Reflection
This week is definitely a challenging one but one that I have been looking forward the most. This is the first time I learn how to design electronic circuit and learn a new software specifically design for electronic design. Therefore this is definitely not the smoothest week and I definitely stumble to multitude of problems along the way. However, the fact that now I can design my own PCB outweigh all the troubles I faced.
Components Availability in Indonesia
As described in my assignment, it's fairly hard to come by SMD components especially the headers. Components like resistor, capacitor, transistor, diode, LED, etc are not common, but still can be purchased from some seller in Tokopedia (Indonesia's version of Ebay). However, no one sells SMD headers at all here. Purchasing from overseas is the only option, but Indonesia's regulation regarding custom is vague at best, making it so hard to source goods from overseas.
Considering this reason and our goal to use as many components sourced as locally as possible, I decided to use THT headers instead. Even these headers are not widely available neither, but at least there are few dozens local sellers that sell them online.
Beside that, I have to get a little creative too just like what I did back when soldering my Quentorres. In this design, I need to use 2x7 SMD female header for mounting the XIAO. Instead of bending a pin like last time, I used 2 right angle female headers, slightly trim the pin, and solder them side by side.
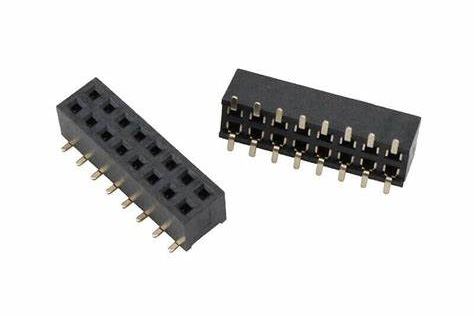
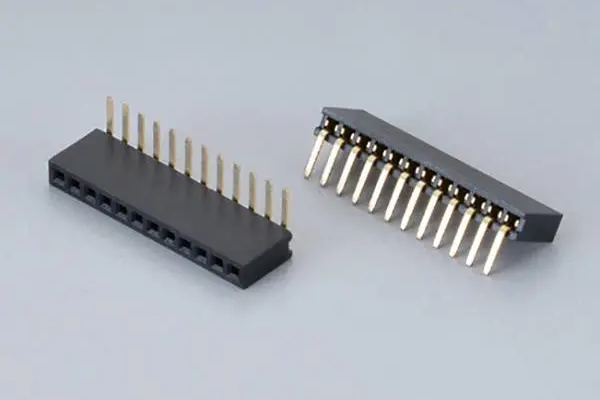
End Mill Availability in Indonesia
Just like SMD headers, small end mill is very hard to come by and it is unreasonably expensive. Like in my electronic production week, this week I insist on using v-bit end mill instead for milling my traces. Another big reason is because I see many people achieved excellent result with similar setup (3018 cnc machine + v-bit end mill). One of our goal in Bali is to attract more people to do what we do here and to achieve it, I think it is very important to figure out a workflow that keep the cost barrier as low as possible.
V-bit for Traces
I milled my Quentorres traces with v-bit and it turned out really well. However, I notice that on subsequent milling operation by my colleagues that with same milling bit and settings, the results may varying from slight difference to rather extreme. The worst one has the copper tracks width as hairline thin and even completely milled altogether.
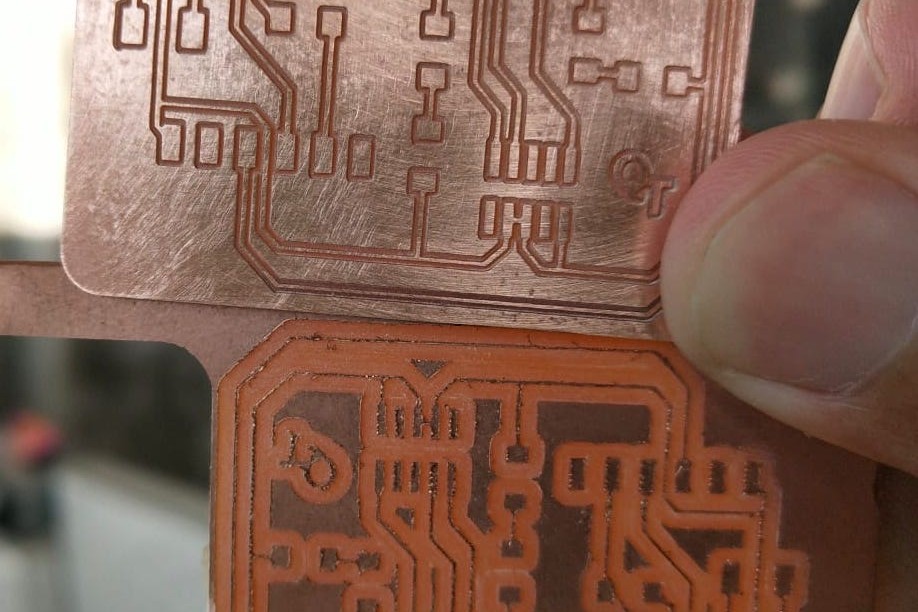
My suspicion is the v-bit tip got duller after each milling operations resulting in the actual cutting diameter getting wider and milled more copper than it necessary. This is due to the deeper the v-bit cuts, the wider the cutting diameter will be like shown bellow.
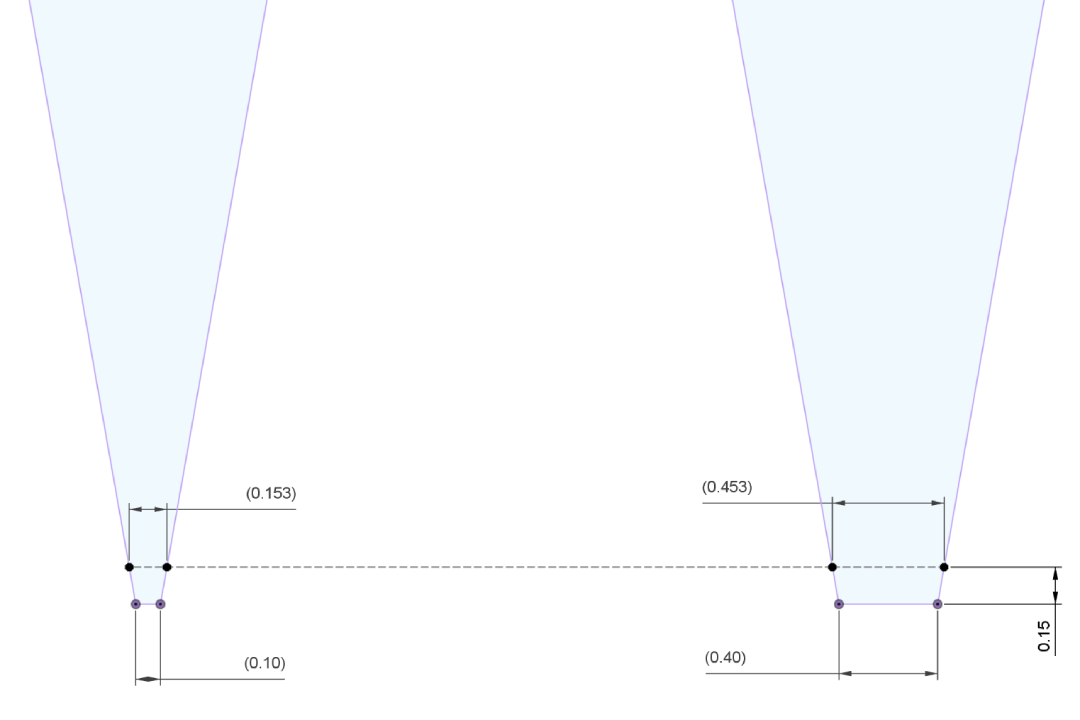
To mitigate this, I improvised a workflow that give me a good result but require more steps. However this workflow makes it possible to mill PCB successfully with slightly dull v-bit in my multiple attempts, so I think it's worth the hassle.
- When generating the g-code for the traces, instead of using the v-bit calculator, I straight up input 0.4 mm as the tool diameter and use 0.1 mm or even slightly smaller as cutting depth.
- Be sure to use height mapping feature in Candle or autoleveler in UGS.
- Start milling your traces. The setting that we used on step 1 will most likely caused some copper not cut all the way through. Once the milling is finished, do not remove the PCB from the jig! Inspect the results and take note where all the copper lines that didn't get cut through. Lighting an LED below the board helps a lot in this step.
- Duplicate and edit current .nc file. Remove all the lines that got successfully cut through, leaving only the one that need additional milling. Lower the Z value on those lines.
- Run the new .nc file. Repeat step 3 and 4 until you successfully milled all your traces.
0.8 mm Corn Teeth End Mill for Drilling
In the middle of this week, both of my colleagues have accidentally broke both of our 1/32" end mills. This force us to look for an alternative that available in Tokopedia. Imperial end mill is almost non existent here, so we try to look for metric one.
We found a reasonably priced 0.8 mm 2 flutes carbide end mill, IDR 85,000 / USD 5. However, I saw a 0.8 mm used corn teeth end mill in the same store priced at IDR 5,000 / USD 0.3. It got me thinking, the drilling and cutting operations are relatively shorter and require less precision compared to trace isolation. If the used corn teeth bit can do the job half as good compared to the new straight end mill, we could save so much cost considering how small mistakes can easily break this bits regardless how new they were.
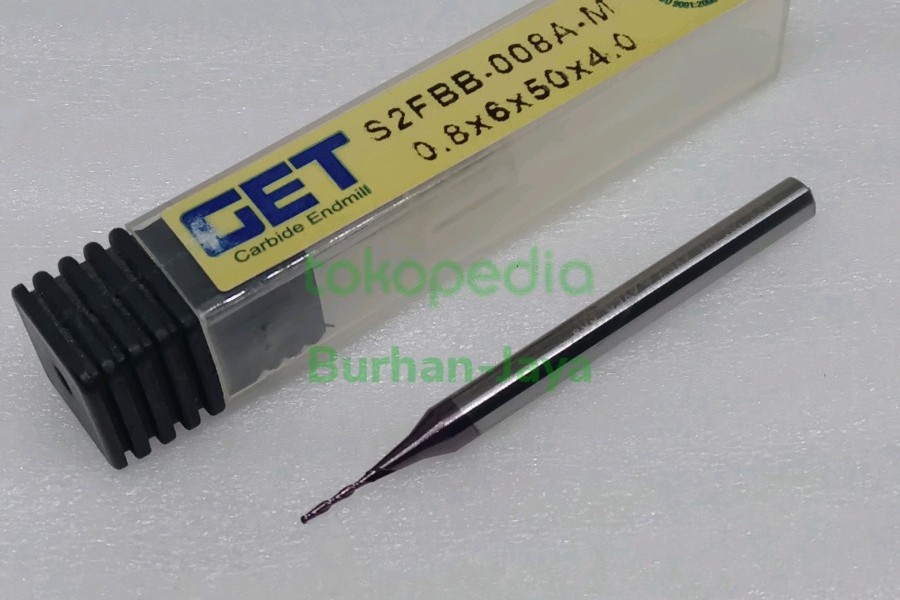
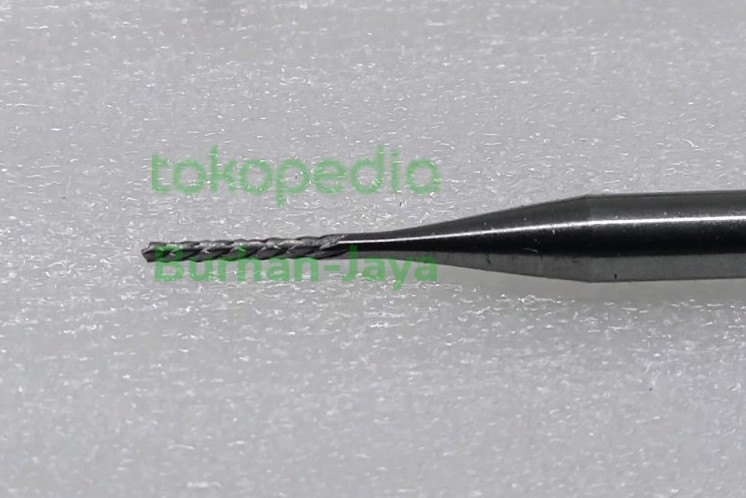
My bet pays well. I purchased few of this bits and used it to mill my development board. I did not notice any differences both on the milling operations and the result compared to our old 1/32" end mill. Then my colleague proceed to break one of them right away!