Week17. Application and Implications
This 17th week was all about applications and implications. In other words, we had to answer a multitude of questions about our final project, in order to define the many things we needed to do. The assignments were as follows.
Assignment
Propose a final project masterpiece that integrates the range of units covered,
answering:
What will it do?
Who's done what beforehand?
What will you design?
What materials and components will be used?
Where will come from?
How much will they cost?
What parts and systems will be made?
What processes will be used?
What questions need to be answered?
How will it be evaluated?
Your project should incorporate 2D and 3D design,
additive and subtractive fabrication processes,
electronics design and production,
embedded microcontroller interfacing and programming,
system integration and packaging
Where possible, you should make rather than buy
the parts of your project
Projects can be separate or joint, but need to show individual
mastery of the skills, and be independently operable
Purpose of the robot
The original aim of my robot was to be able to move around fields, especially corn fields, as this is one of the places where corvids cause the most damage. These birds are extremely clever and quickly get used to the different types of bird killers already on the market. So we need to break up regular cycles by making everything random, sound, mobility... so that corvids can't get used to any of these factors.
Ideally, I'd also like to add camera-based image recognition to the robot, which would enable it not only to wander around fields at random, but also to track crows when it sees them. However, I'm not very far advanced in my work on image recognition and the use of openCV.
In order to delimit a precise geographical area and prevent the robot from going off in multiple directions and being dangerous, the robot needs to have location data. To do this, I used a GPS module to receive its position and let it know where it is. It then has to define a geographical zone from which it can't leave.
To scare off the corvids as much as possible, I also want to add a loudspeaker to the robot so that it can emit randomly changing sounds to make noise and scare the robot.
What already exists?
There are already solutions for scaring away crows, such as gas cannons, scarecrows and the like, but I'm not aware of any robot dedicated to this purpose. On the other hand, while doing some research, I realized that there was a French robot that used the same wheel principle as I do, with bar wheels as I'd like to do. It's the SentiV qui est fabriqué par Meropy. The difference between my robot and that of this brand is that their robot has a camera on top to monitor the crop once it's developed, whereas my robot will be more interested in external factors that differ from the crop.
Where do I stand?
For the moment, I've made a small prototype in miniature format to test my software, but it wasn't a great success, as the small motors I used didn't have enough torque to make my wheels move, so I couldn't test how well it worked. To steer it manually, I use a joystick. My remote control and my robot work with an esp32, so I use the espNOW protocol, a communication protocol using wifi functionality. On the software side, I also manage to receive gps coordinates with my circuit.
Concerning the PCB, I have a version that's quite satisfactory, I've made outputs for various functions, motor control, UART communication (GPS, possibly an IMU), an output for a loudspeaker, I2C communication ports (which don't work very well at the moment).
As for the final version, I've started work on a chassis so I can fit all my components, and I've also made a plate so I can fix my electronic components and avoid short circuits like I did with the first prototype. I've got my motors and I've made a support to fix them on. I found some axles to hold my wheels.
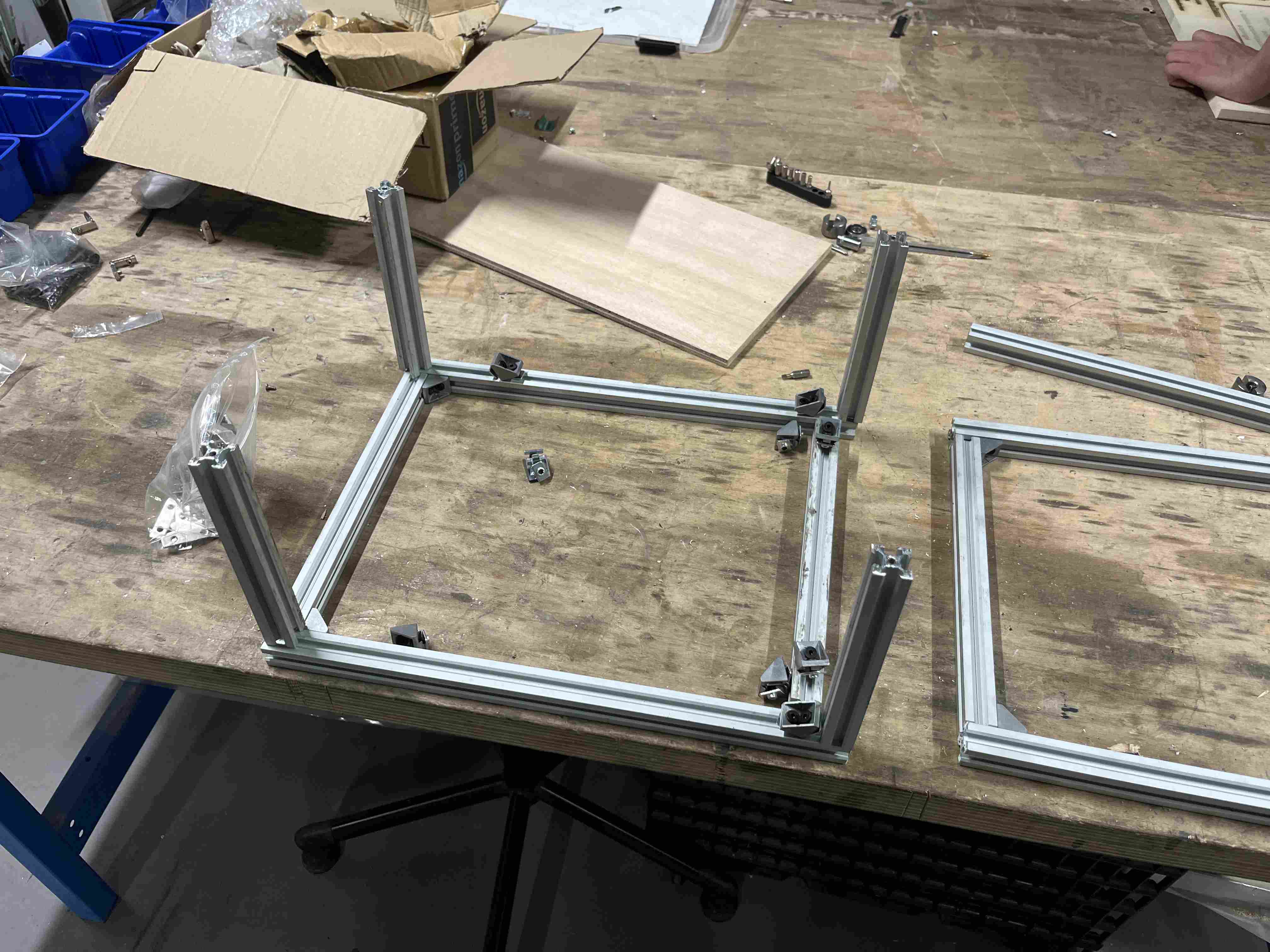
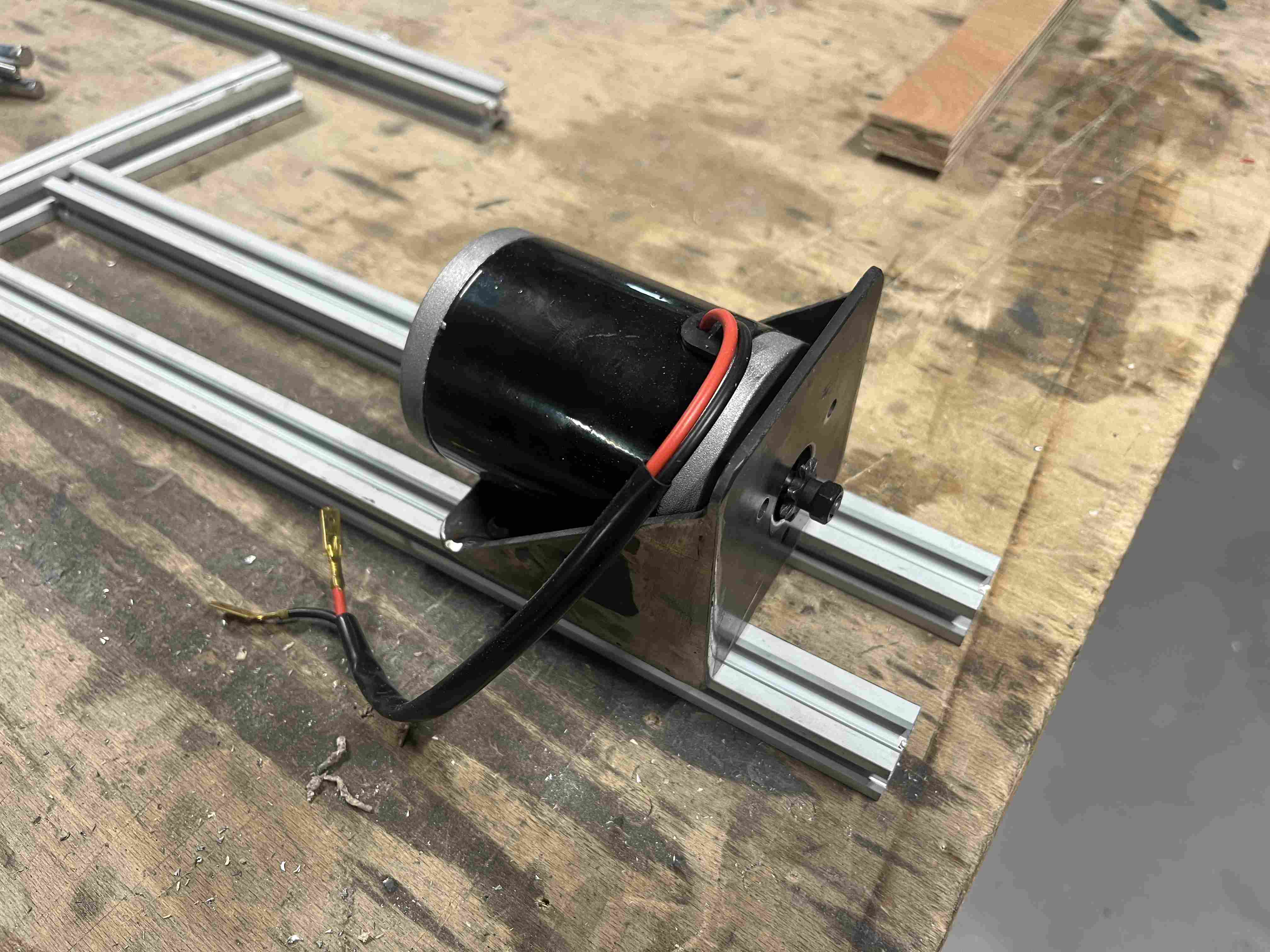
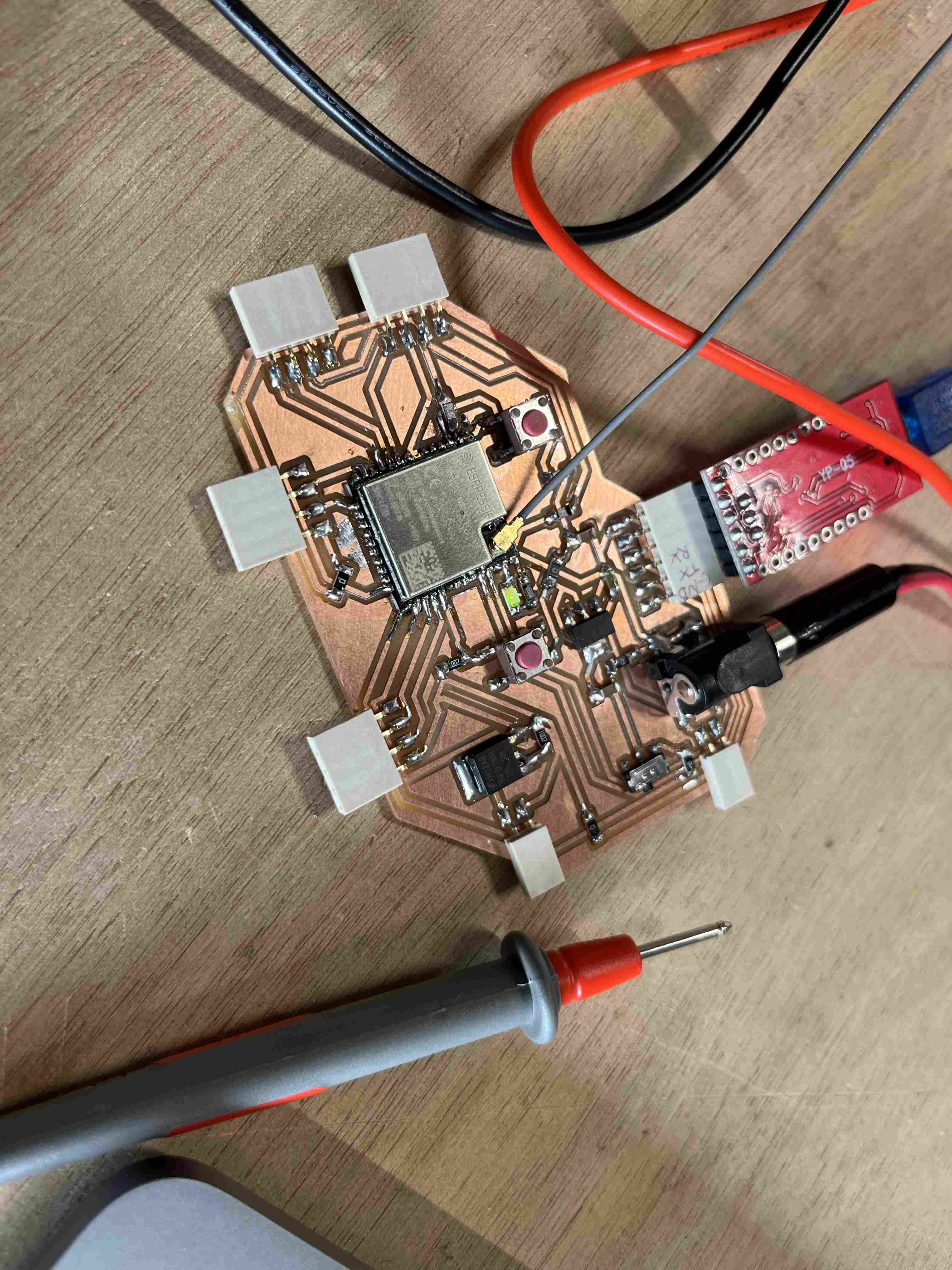
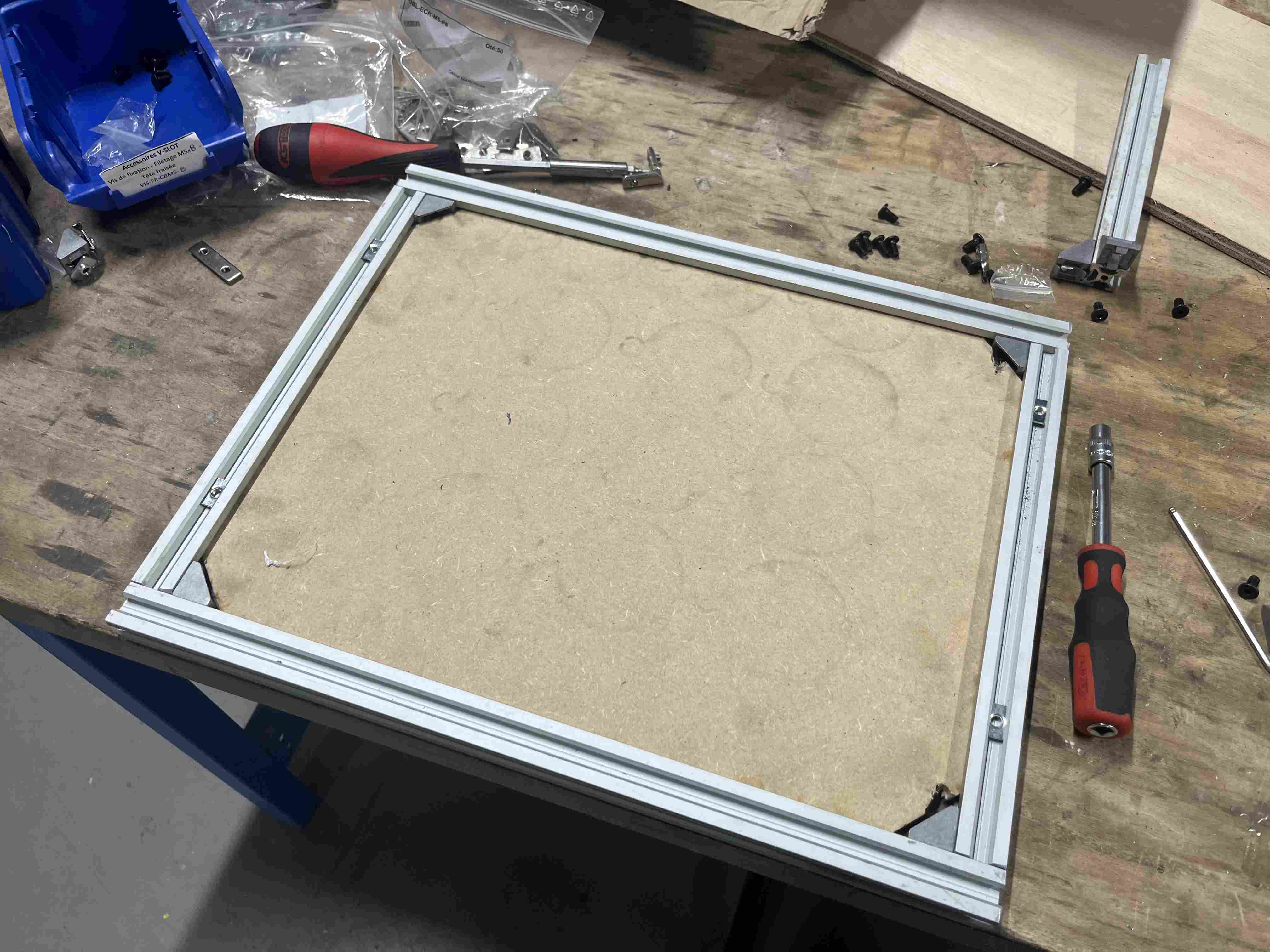
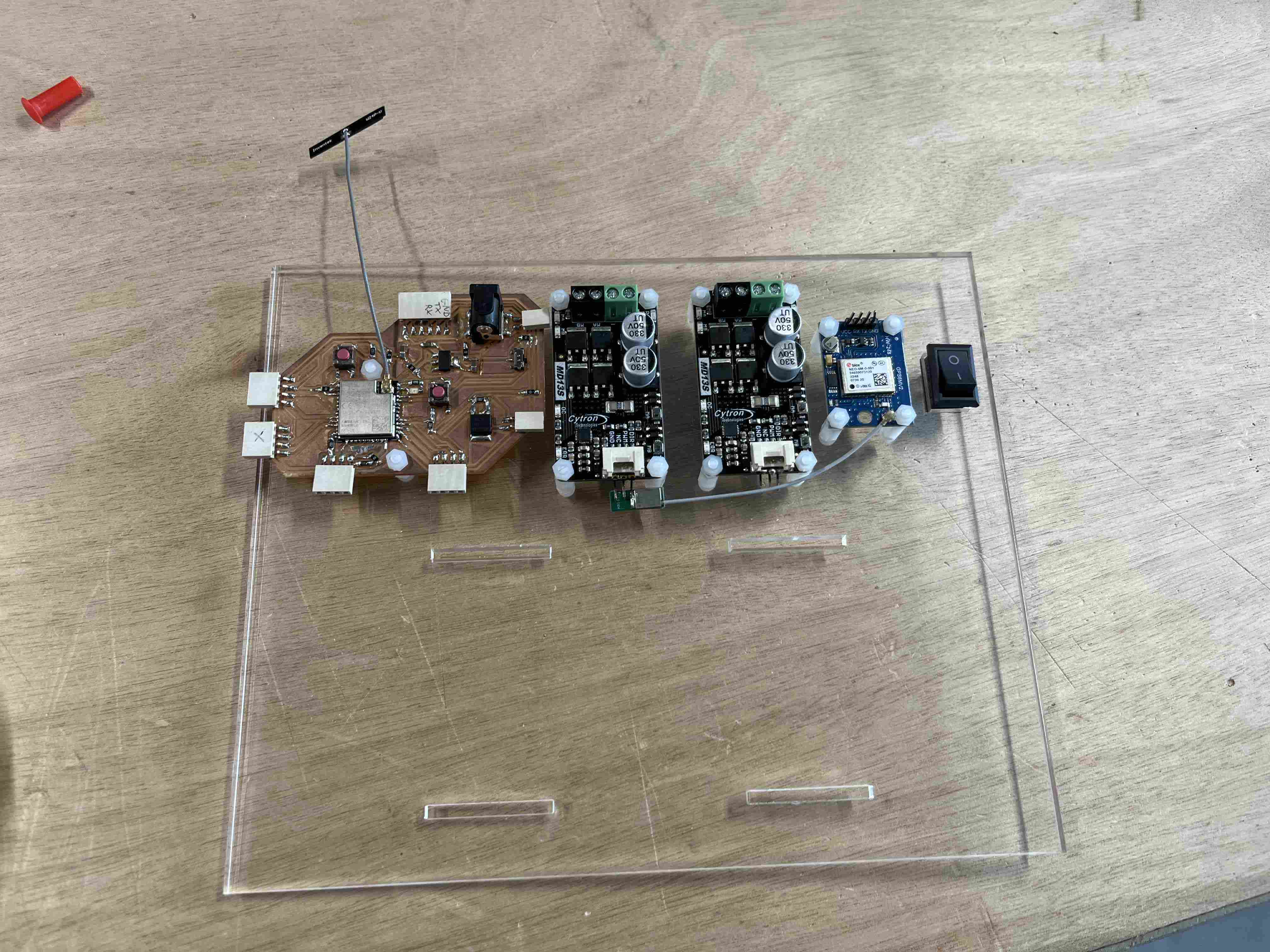
What's left for me to do?
I still have a lot of work to do. First, in order to test it, I need to finish the robot at actual size. To do this, I need to finalize my chassis, finish assembling and wiring everything. I've also got a lot of work to do on my wheels and drive, as I haven't yet completed the full-size wheels. I need to choose the materials I'm going to use to make the poles and I need to make the support that will hold them, I need to fix my motors and find a way of reducing the torque of my motors so that I can drive my wheels. The solution I've come up with so far is to use a bicycle gearbox pinion and put a very large sprocket on my wheels, which will enable me to reduce the force and get it moving without too much trouble. However, with this system, we'd have to move the wheels away from the motors, so I'd have to make bearings to hold them in place.
As far as the software is concerned, I've already got a lot of bricks, but I still have to combine them all, so that I can control my robot with the remote control or in automatic mode, with the possibility of leaving it autonomous and having it work randomly using the GPS. There are still two points where I don't have much to go on: the use of loudspeakers. Last but not least, I'll have to work in depth on image recognition and mastering OpenCV.
Components
Components | Provenance | Price |
---|---|---|
PCB | Manufactured at agrilab, components mainly from Digikey | |
Motors | Amazon | €26.23 each |
Driver | Seed Studio | €16.70 |
Neo 6M GPS Module | Amazon | €8.50 |
Steel | Local supplier | |
Battery | Recovered from old drone | |
Profiles | Local supplier | |
PLA | Unknown source - recovered stock | |
Poles | Undetermined |
Processes used
In order to build my robot, I used many of the tools available at Agrilab. First, I used the Roland milling machine to make my PCB. I then used soldering irons to assemble the PCB. I used the laser cutter to cut out the support plates, for my robot chassis, for my electronic support... I used 3D printing to create different parts on both sides. I also used different software to operate each machine and to program my robot.