Wildcard Week
This week the challenge was to produce 'something' with the digital fabrication process (for my methodological logic, the 'something' was too much printing π ) and that has not been covered in the previous weeks.
That piece of information, together with the examples found in the week's guide, the team of colleagues we performed some experimentation with biomaterials.
To do so, we resorted as a source of information to the site materiom.org , from where we took the following:
Conductive and non-conductive bioplastics
Since agar-agar (an ingredient that allows elasticity) was not available, it was replaced by gelatin as in the recipe for the conductive gelatinous bioplastic.
The mixture was placed in some available molds and containers.
To accelerate the setting of the gelatin, one of the containers was placed in the refrigerator for 30 min, obtaining a much faster setting compared to another one of similar volume that was left at room temperature.
One of the molds, where a considerable volume of mixture was deposited to obtain a thicker block of bioplastic, was left in the refrigerator overnight until the following day.
On day 2 of the experiments, the strength and flexibility of the materials obtained were observed. With a thin sheet and the thicker block, the laser engraving was tested, obtaining the following result:
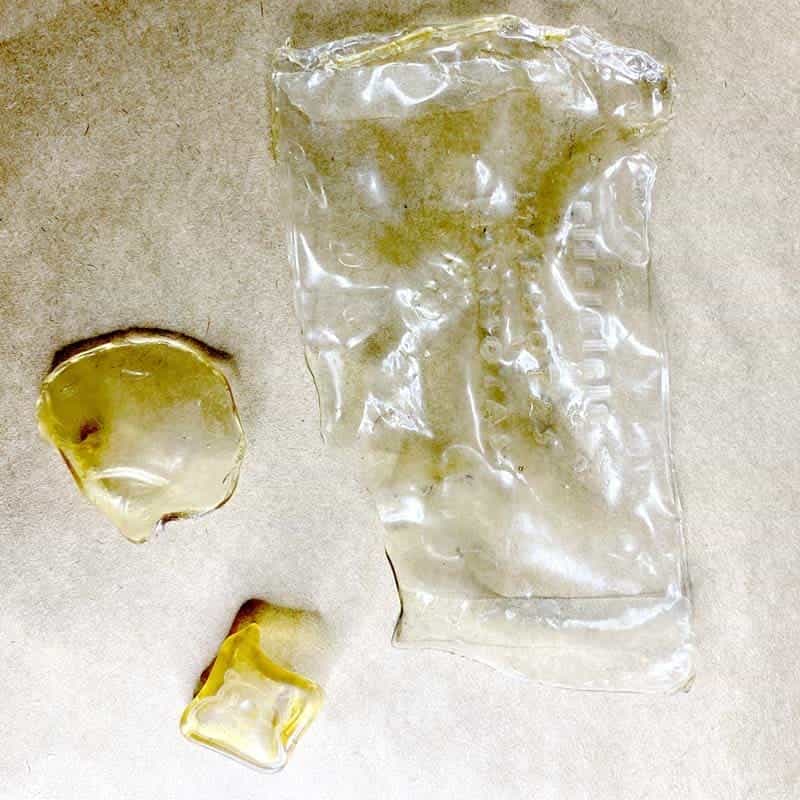
For the conductive bioplastic, the base of the above mixture was added salt. The mixture was poured into a rectangular mold, to obtain a sheet of approximately 5 mm. This mold was also kept in the refrigerator for at least 12 h.
On day 2, the film was removed and it was observed that it captured some details of the container used.
To verify the conductivity, we connected the foil to the oscilloscope to feed and verify the voltage conducted by the foil.
Then, we made the connection between the foil and the circuit I had made during the computer controller-cutting week with copper foil, which has three LEDs. The result was successful! Although we also concluded that it would be necessary to increase the amount of salt to improve the conductivity of the foil.
Compost
Another product made was the mix to obtain a block that could be machined on the CNC machine. We used the recipe:
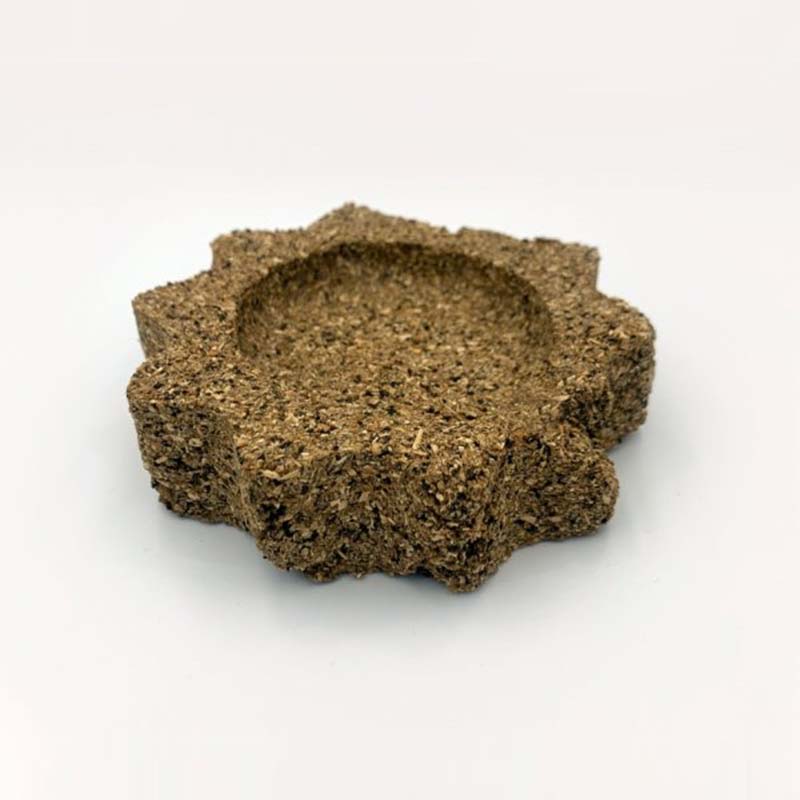
The changes made were: oak sawdust for local wood sawdust available at FABLab; rooibos tea for yerba mate (Ilex paraguariensis), and cornstarch for cassava starch.
The sequence suggested in the recipe was carried out; we obtained the mixture that was distributed in different containers that served as molds (one quadrangular, one spherical, one hexagonal and one circular) in different proportions.
This mixture remained at rest for two days, at room temperature inside the laboratory and in a place where the sun shone to evaporate as much liquid as possible and obtain the blocks.
The result was diverse, but not as expected: the binder ingredient (cassava starch) was not successful (perhaps it will be necessary to try another quantity in the mixture), which caused the molds obtained to crumble (the hexagonal one) or break in the thicker ones. Only the ovoid mold showed a slightly better compaction.
We can conclude that although it did not result in machinable blocks, they can be used as germination compost π±.
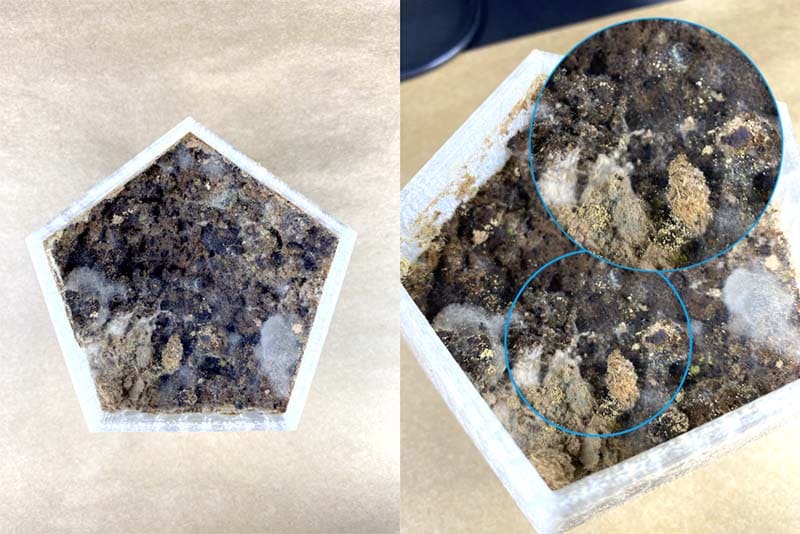
Recipes
I remind you that this experience was based on the recipes listed at the beginning, which can be found on the Materiom website. In addition, we support the bioplastic experience in the documentation of Silvia Lugo, in week 6 of Fabricademy.
And that we modified some ingredients because they are not available in stores.
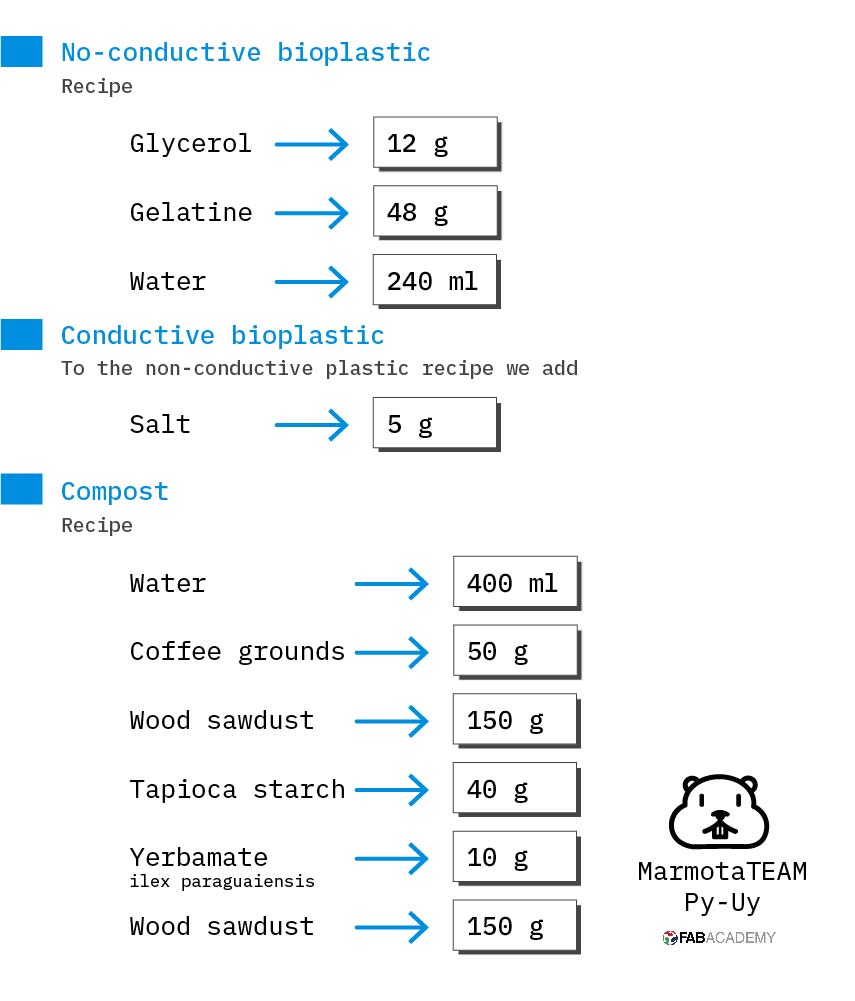
What I learned
π I found Materiom to be a very interesting source of reference for the production of composites.
π― To produce bioplastics with locally available ingredients.
How I learned it
By the assistant of the local instructors. ππΌ
By tutorials.