Week 03. Computer-Controlled Cutting
Table of Contents
- WEEKLY PLAN
- GROUP ASSIGNMENT: LASER CUTTER PARAMETERS
- INDIVIDUAL ASSIGNMENT: PARAMETRIC CONSTRUCTION KIT
- VINYL CUTTING
- USEFUL LINKS AND RESOURCES
- FILES
WEEKLY PLAN
Group assignment:
- Lab's safety training
- Characterize laser cutter's focus, power, speed, rate, kerf, joint clearance and types.
- Document work to the group work page and reflect on your individual page what you learned.
Individual assignment:
- Design, lasercut, and document a parametric construction kit, accounting for the laser cutter kerf, which can be assembled in multiple ways.
- Cut something on the vinyl cutter.
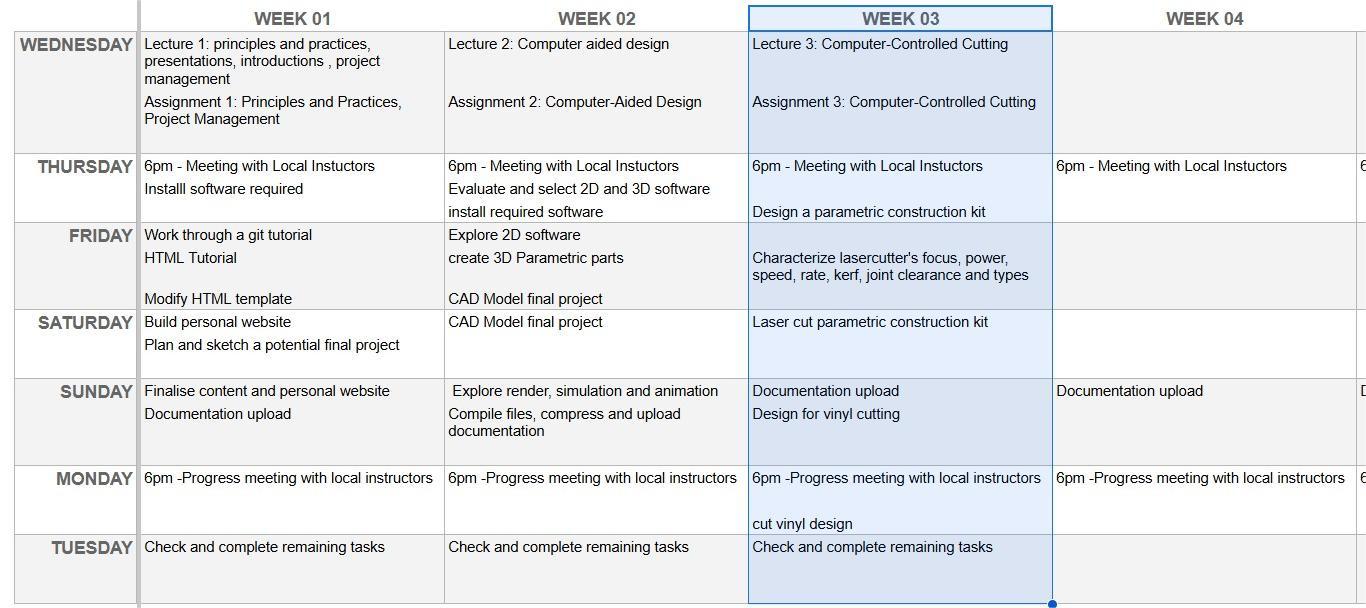
GROUP ASSIGNMENT: LASER CUTTER PARAMETERS
As I am a distance learner at the Fab Lab León, I am completing this part of the assignment on my own and with the laser cutter I have access to.
The model I am characterizing is the AEON NOVA 14 Elite. This is a 100W CO2 laser engraving and cutting machine with a working area of 1400x900mm, scan speeds of 1200mm/sec.
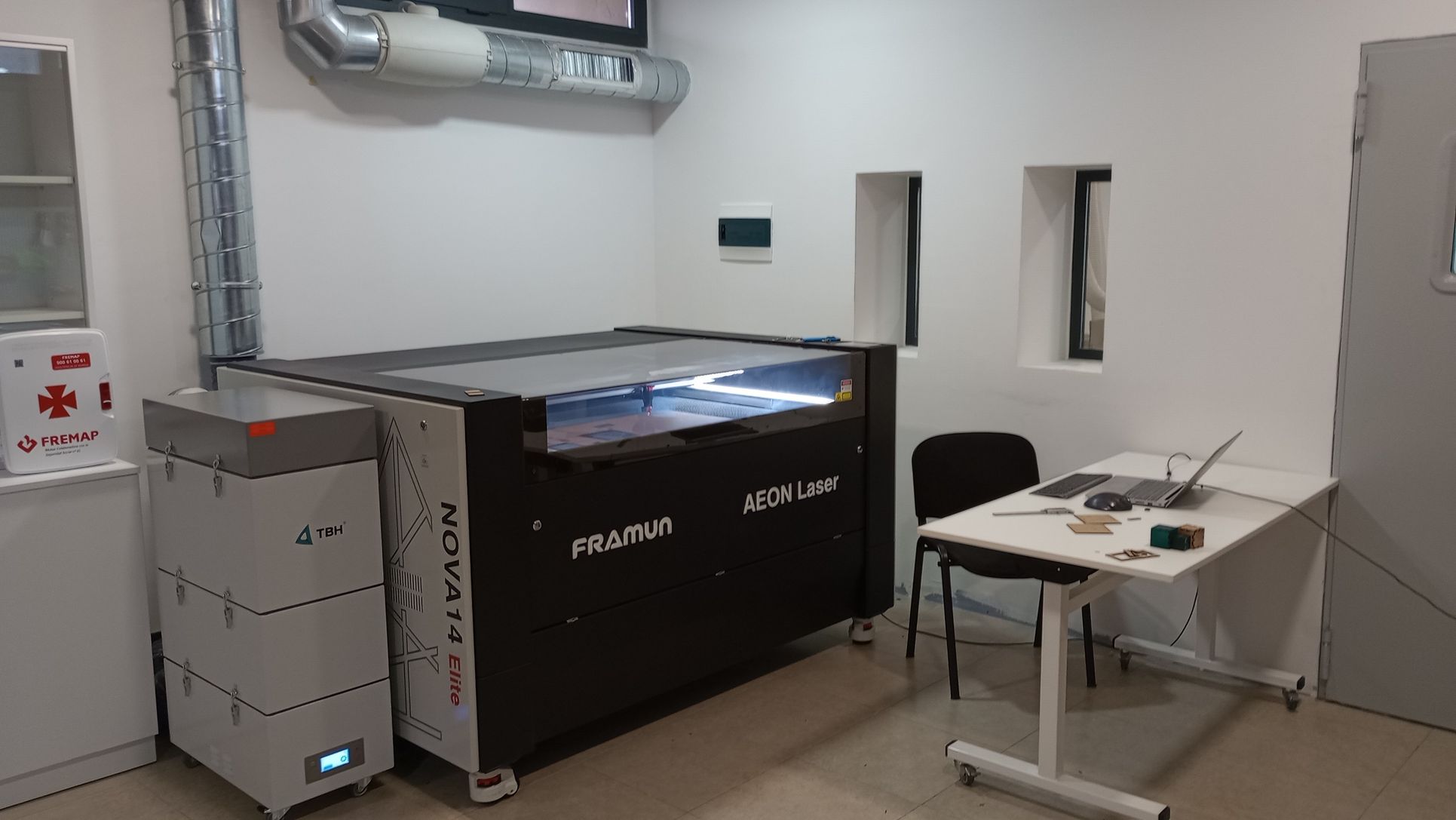
The manufacturer lists a detailed technical specifications for the Elite series on their website. Here I have listed the most relevant specs for the model we have.
AEON NOVA 14 Elite | |
---|---|
Working Area | 1400x900mm |
Laser power | 100W CO2 Glass Tube |
Electric Up&Down | 200mm Adjustable |
Air Assist | 105W Built-In Air Pump |
Blower | 550W Built in Exhaust Fan |
Cooling | Built-in 5200 Chiller |
Engraving Speed | 1200mm/s |
Cutting Thickness | 0-30mm(depends on different materials ) |
Locating Precision | 0.01 mm |
Engraving Software | RDWorks / LightBurn |
Graphic Format Supported | AI/PDF/SC/DXF/HPGL/PLT/RD/SCPRO2/SVG/LBRN/BMP/JPG/JPEG/PNG/GIF/TIF/TIFF/TGA |
The extraction system includes a 280m3/h carbon filter unit made by TBH (link) and local air extraction.
Safety measures when using a laser cutting machine
Check Cutting files:
- Ensure that the work to be cut has been checked for duplicated lines and that the correct settings have been applied
Ensure Proper Ventilation:
- Fume Extraction System: Use a fume extractor or ventilation system to remove harmful fumes, gases, and smoke generated during the laser cutting and engraving process.
Properly Handle and Store Materials:
- Use the Right Materials: Only use materials recommended for laser cutting and engraving to prevent harmful fumes or fire risks.
- Avoid Reflective Materials: Never cut or engrave highly reflective materials, such as mirrors or metals, as they can reflect the laser and cause injury or damage.
Adjust and Test Settings Before Full Operation:
- Test Cuts: Before starting a full job, always run a test cut or engraving on a scrap piece of material to ensure the settings are correct.
- Laser Focus: Ensure the laser is properly focused and aligned before starting the cutting or engraving process.
Never Leave the Machine Unattended:
- Monitor the Cutting Process: Always stay nearby while the laser cutter or engraver is in operation to quickly address any malfunctions or fires.
- Emergency Stops: Be familiar with emergency shutdown procedures in case of an accident or malfunction.
Keep the Work Area Clean and Organized:
- Clear Flammable Materials: Ensure that the area around the machine is free from flammable or combustible materials.
- Emergency Stops: Ensure that the laser working area is clean and remove any debris after the cutting operation
Be Aware of Fire Hazards:
- Keep Fire Extinguishers Nearby: Always have a fire extinguisher rated for electrical and material fires within reach.
Focusing the laser beam
Focusing the laser beam is essential for reducing the kerf and increasing cutting power. There are two methods to achieve this: manual focusing and autofocus. The manual method involves using a gauge, specifically a 5.9mm high piece of acrylic.
This focusing tool is placed on top of the material to be cut, and the table is gradually raised until the gauge touches the nozzle.
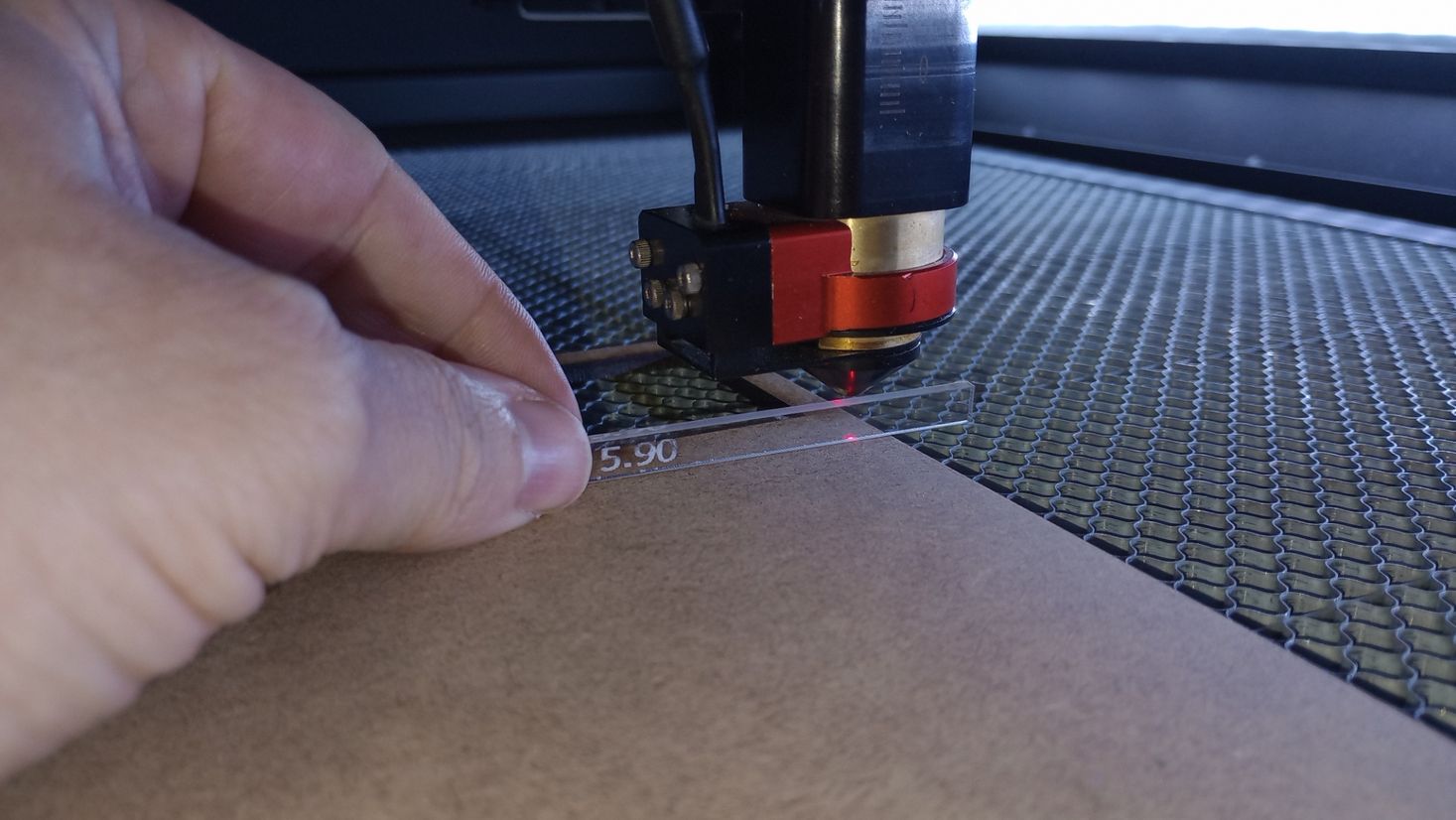
With the integrated autofocus mechanism, the material is positioned beneath the laser head. The bed automatically rises until a built-in probe is activated, at which point the bed lowers by the focusing distance.
Power, Speed and Rate
The output Power and head Speed are the most important settings for laser cutters and they are set as percentage between 0 and 100%.
Laser manufacturers usually provide a list of power and speed parameters for various materials and thicknesses. However, it is often necessary to fine-tune these values by experimenting with different materials and thicknesses. Over time, this approach helps build your own library of parameters.
I have decided to determine the lowest power and speed settings required to effectively cut and engrave the single-flute cardboard 3.8 mm thick I have in stock.
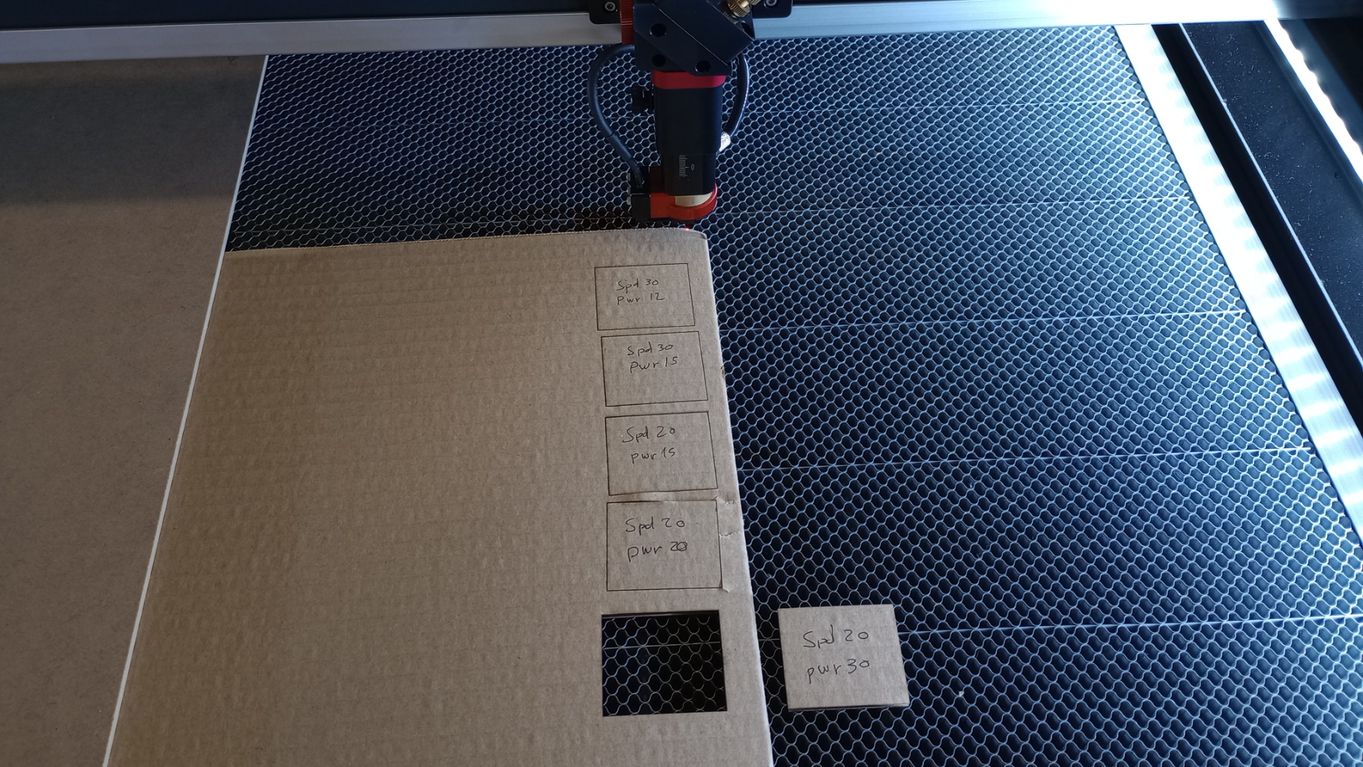
After several tests with cutting, engraving and marking I obtain the following results:
- Cutting: Spd 20/ Pwr 30
- Engraving: Spd 200/Pwr 30
- Marking: Spd 80/Pwr 12