Week 02. Computer-Aided Design
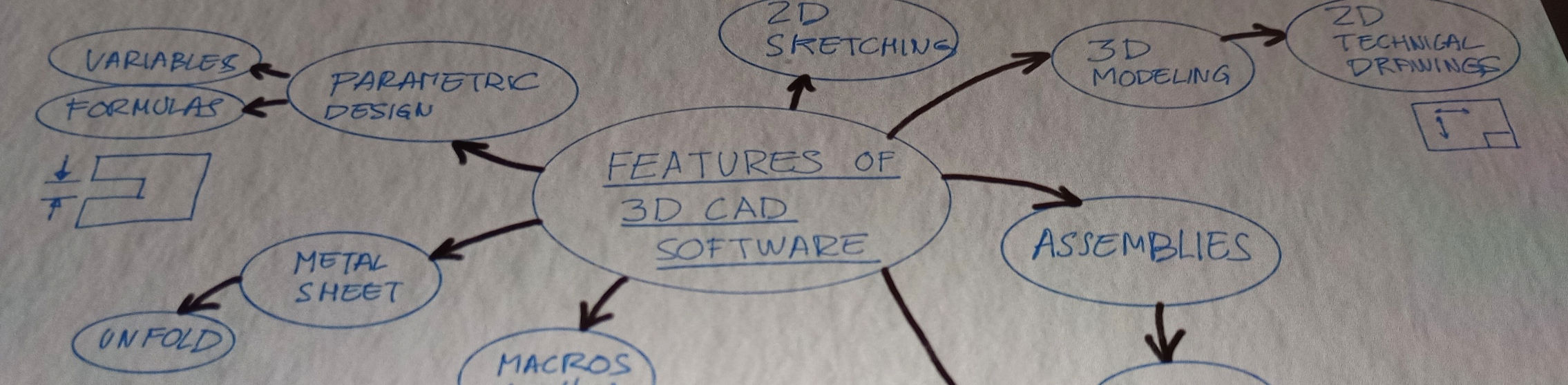
Table of Contents
- WEEKLY PLAN
- COMPUTER-AIDED DESIGN
- CAD MODEL OF FINAL PROJECT
- RENDERING AND ANIMATION
- IMAGE AND VIDEO COMPRESSION
- USEFUL LINKS AND RESOURCES
- FILES
- REFLECTION
WEEKLY PLAN
- Model (raster, vector, 2D, 3D, render, animate, simulate, ...) a possible final project.
- Document how to compress image and video files.
- Demonstrate and describe processes used in modelling with 2D and 3D software.
- Upload documentation to the class archive
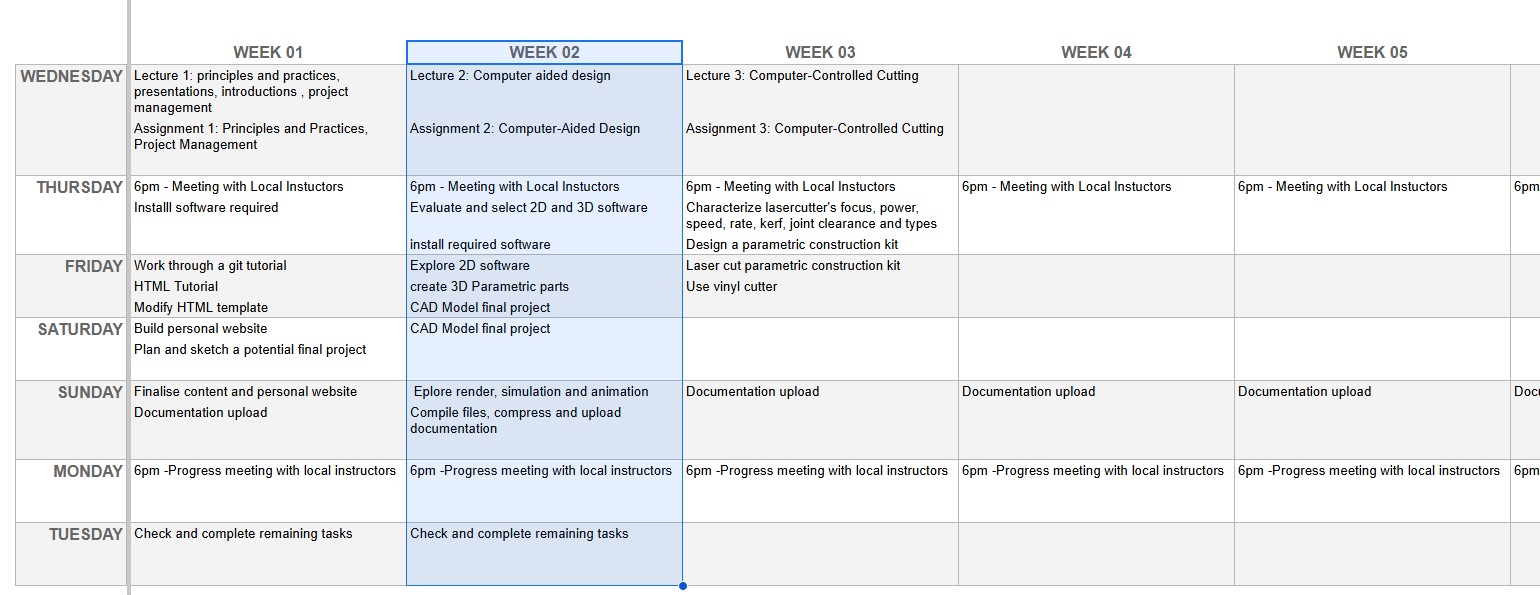
COMPUTER-AIDED DESIGN
2D DESIGN SOFTWARE
PROCREATE
Procreate is a raster graphics app designed for the iPad, enabling users to sketch and create digital art.
I have utilized Procreate to hand-draw a potential logo design that could serve as a brand identity mark for my final project, which involves designing and constructing a dual-axis solar tracker.
In Procreate, you use a stylus pen, and the app offers a variety of brushes and layering tools.
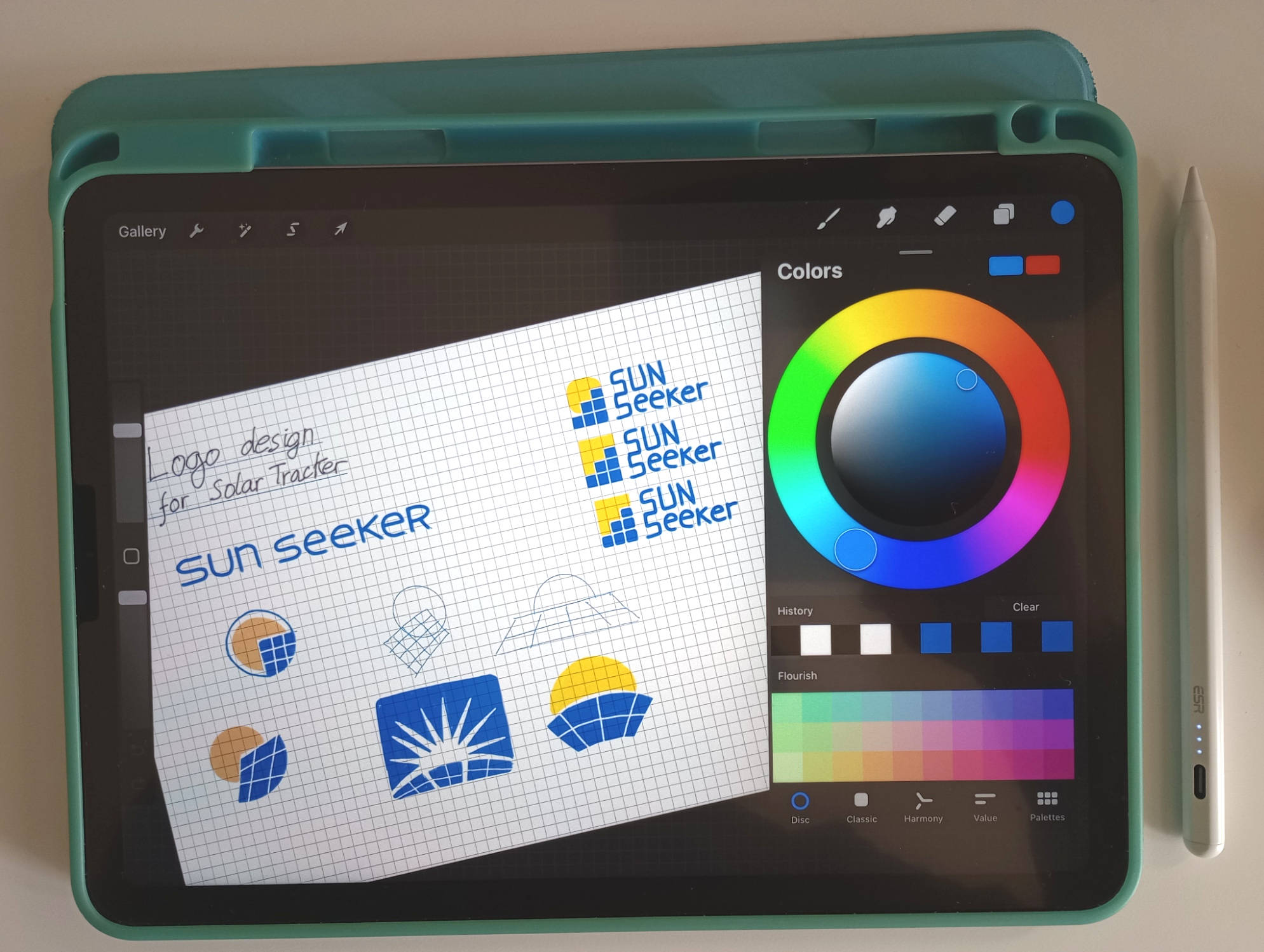
INKSCAPE
I exported the designs from Procreate as JPEG files and imported them into Inkscape. Inkscape is a free, open-source vector graphics software used for creating illustrations and artwork. Since it works with vector graphics, the designs can be scaled without losing quality, a common issue with raster graphics.
I decided to use Inkscape to replicate one of the designs I sketched in Procreate. I employed the grid and snap features to draw simple shapes that were evenly spaced. Additionally, I used boolean operations to join or intersect shapes, allowing me to create more complex designs. The text tools were also used to adjust the font and line spacing.
Although I didn't use this feature in my project, Inkscape can vectorize bitmaps. The vector paths generated in Inkscape can be utilised for 2D digital manufacturing processes, such as laser and vinyl cutting.
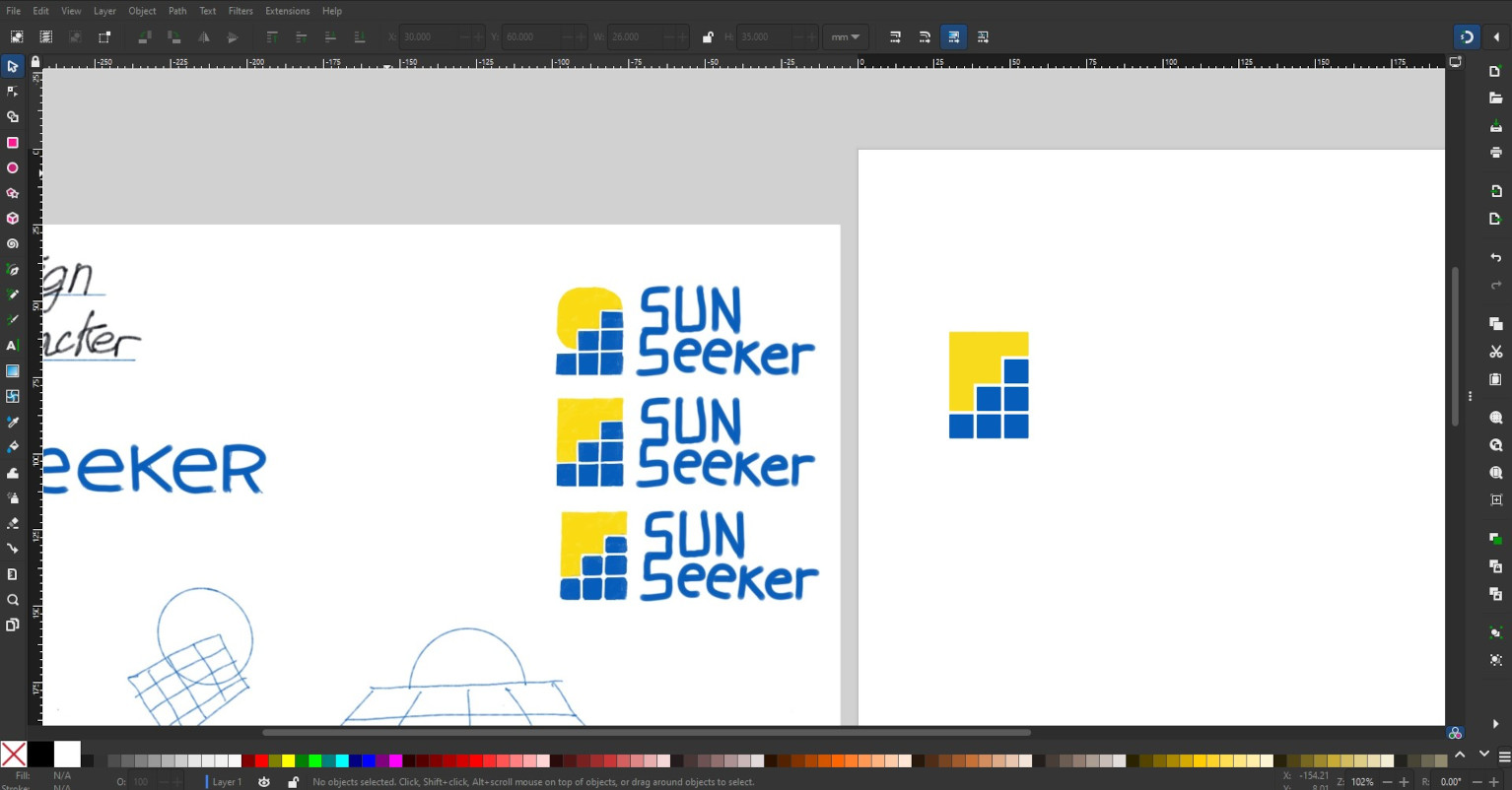
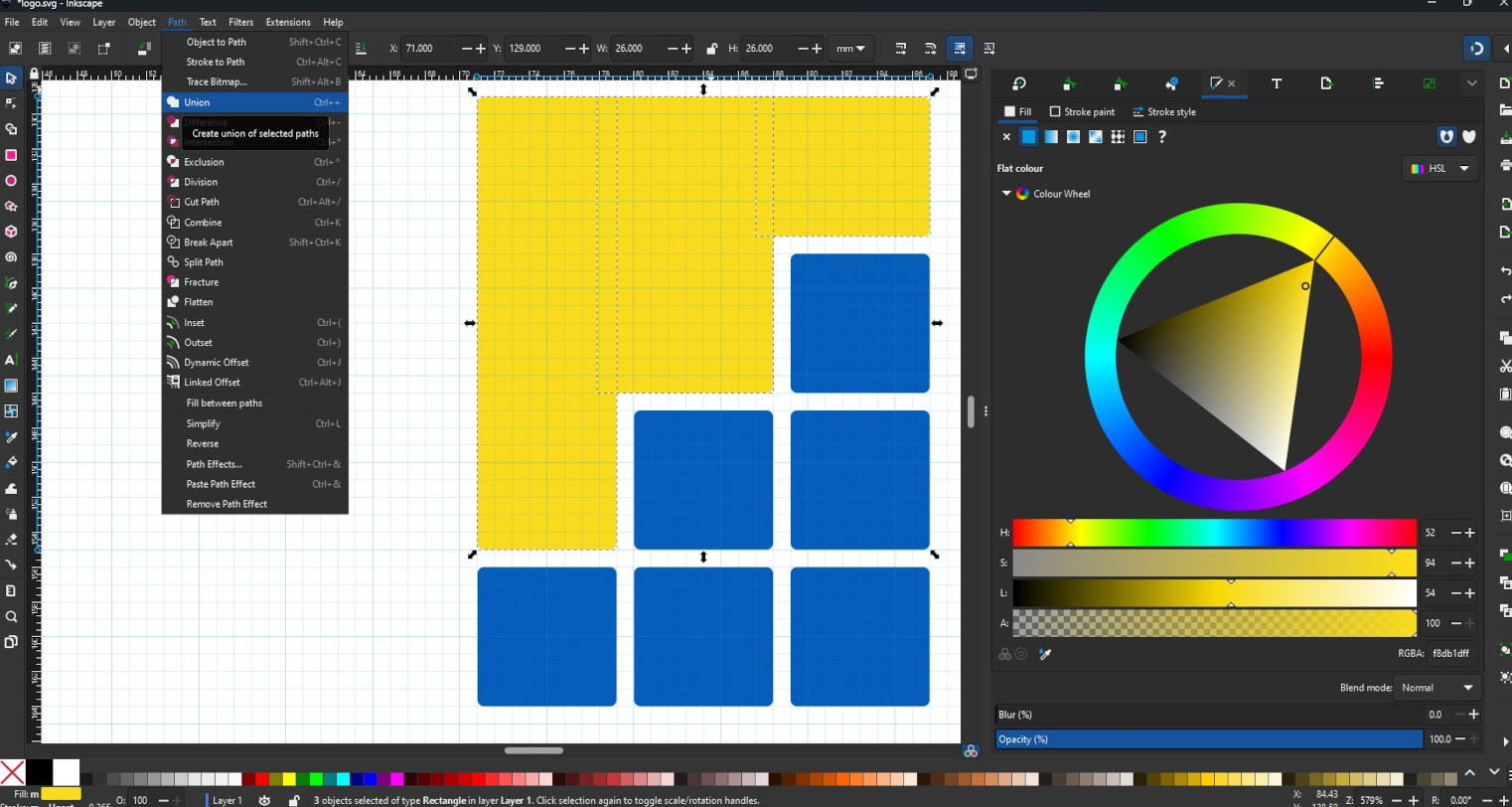
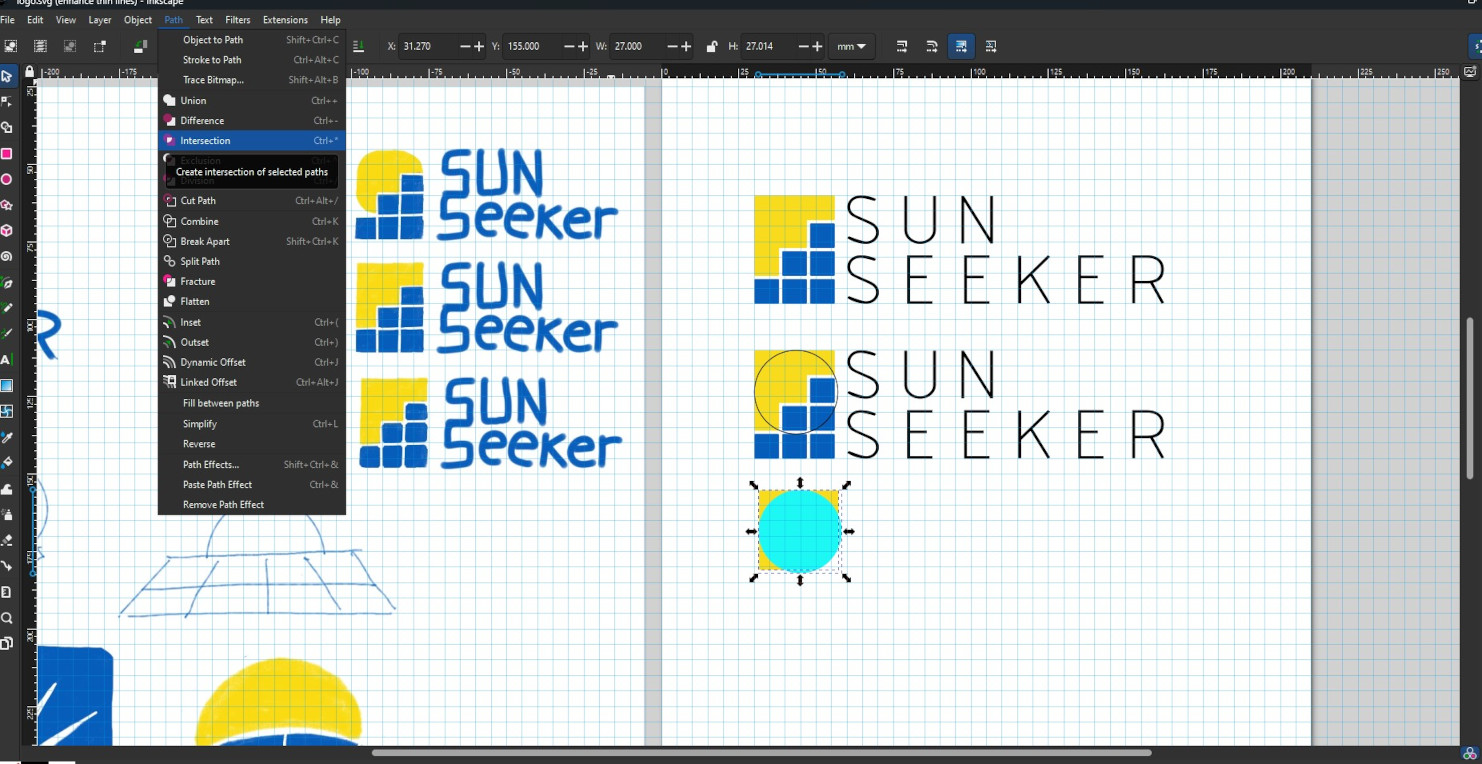
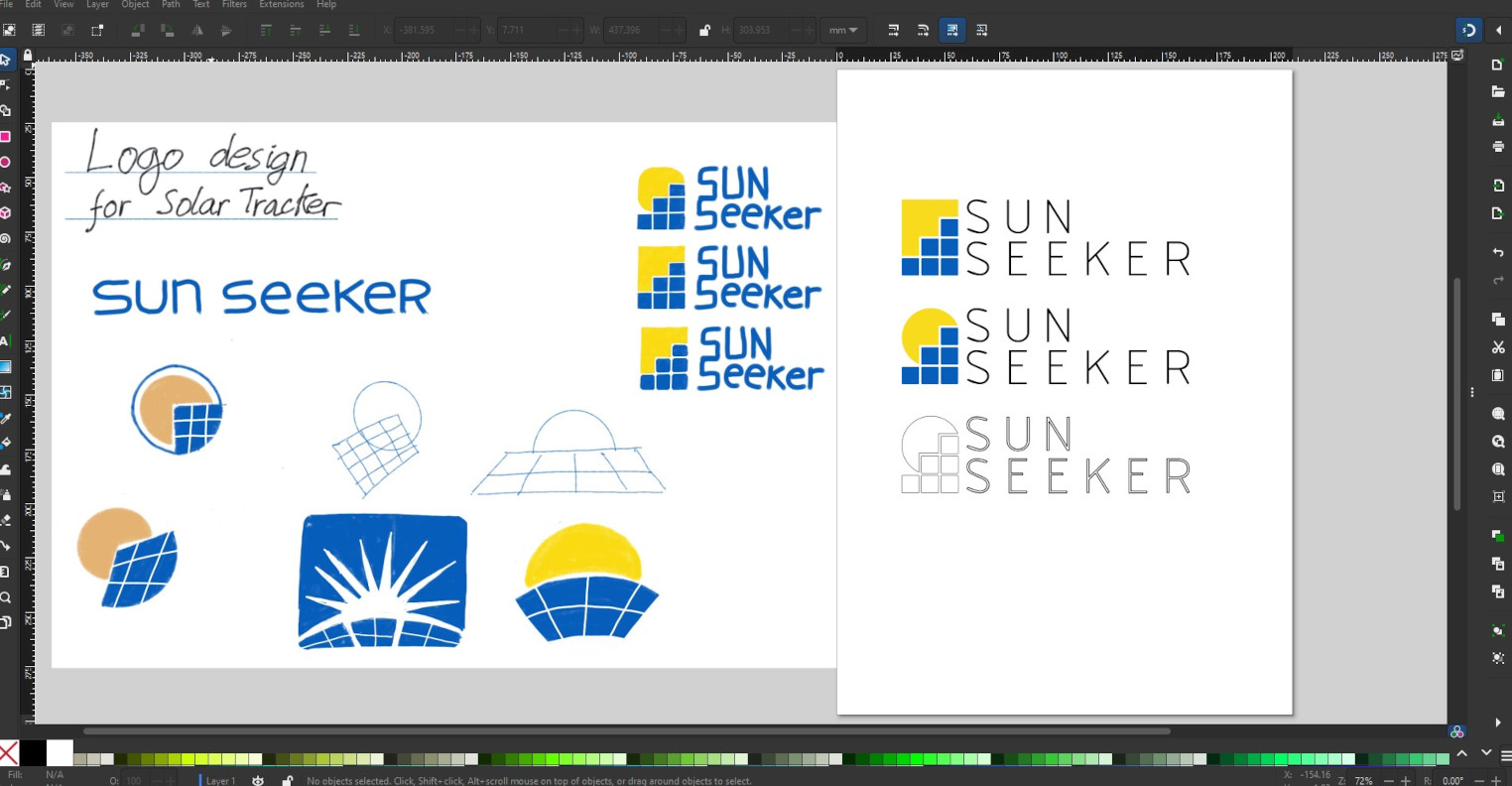
FREECAD (2D)
FreeCAD offers a useful 2D drawing environment with tools for creating precise drawings that include dimensions and constraints. There are two workbenches available for 2D drawing: Draft and Sketcher. While they share similar tools, each has its own unique features, which can be somewhat confusing. For instance, in Sketcher, you can select elements using a selection window, whereas this option is not available in Draft. Additionally, you can select and drag elements in Sketcher, but in Draft, you must use the move command.
I explored the Draft Workbench in FreeCAD to study the ideal fixing points for a linear actuator designed to move a solar panel from 0 to 90 degrees.
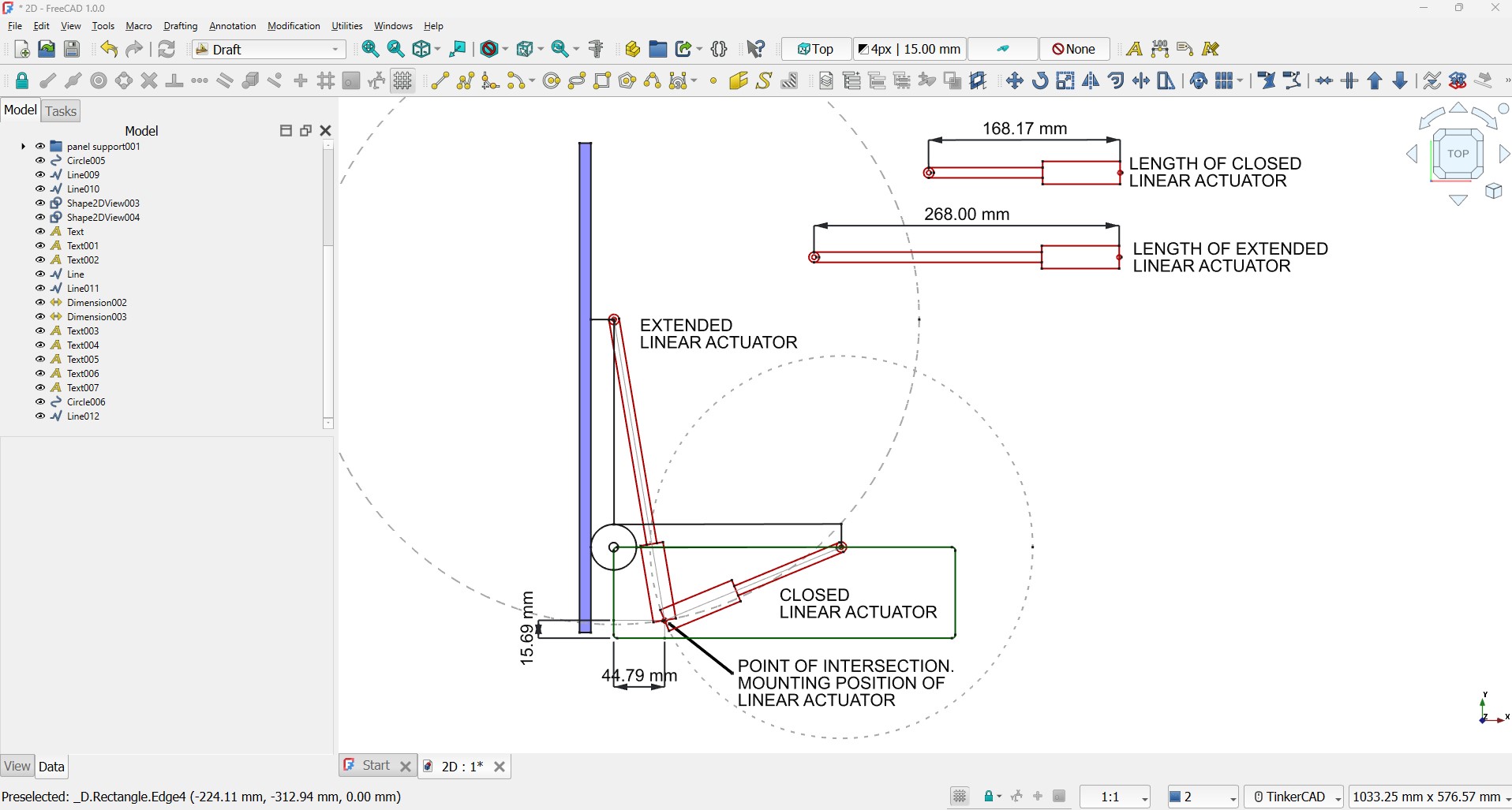
3D CAD SOFTWARE
To evaluate different 3D CAD software I am going to model a part that is going to be used in the 3D model of my final project. This part is a linear actuator, but since I still haven´t decided on the size and model, I am going to try and create it as parametric part. I will also add a joint to represent the sliding movement of the rod.
As a reference I am going to use the data sheet from linear actuator Actuonix L16.
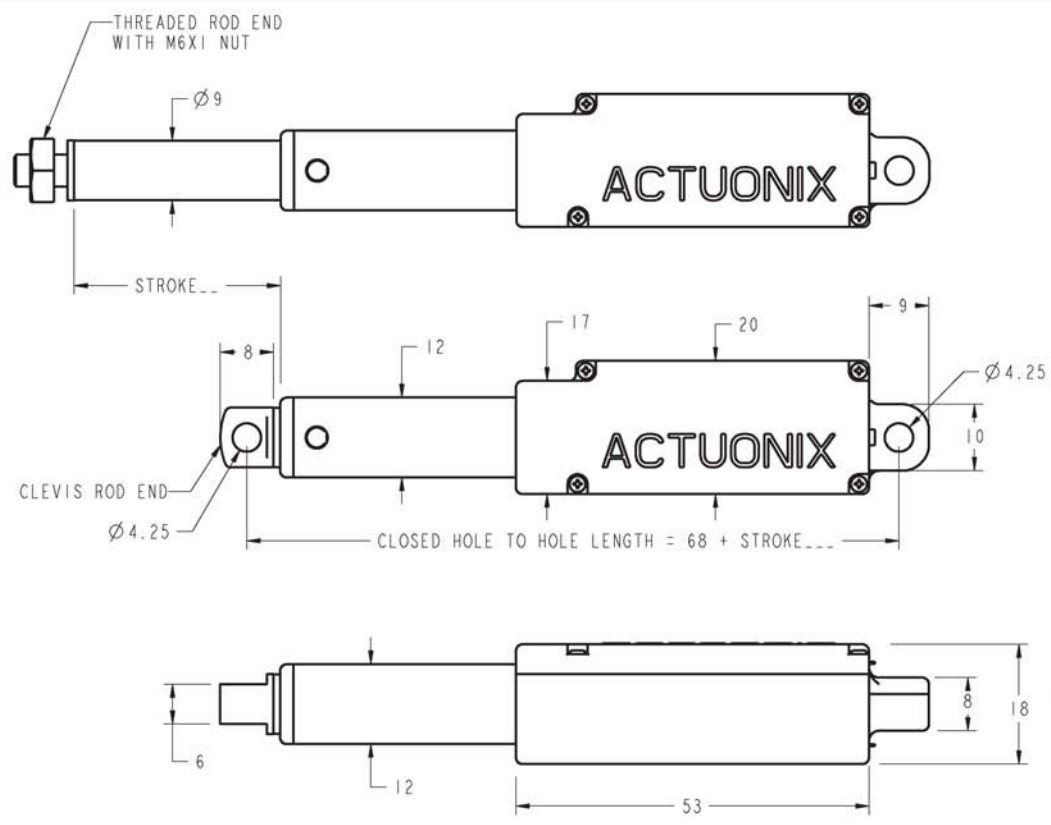
ONSHAPE
Onshape is a cloud-based CAD software that includes tools for sketching, 3D modelling, assembly design, joints, drawings, simulation and renderings.
When creating a sketch, you can use a table to set variables such as actuator body length, thickness, and stroke distance. These variables can then be used in the dimensions, allowing for easy modifications of the design by changing the value of the variables.
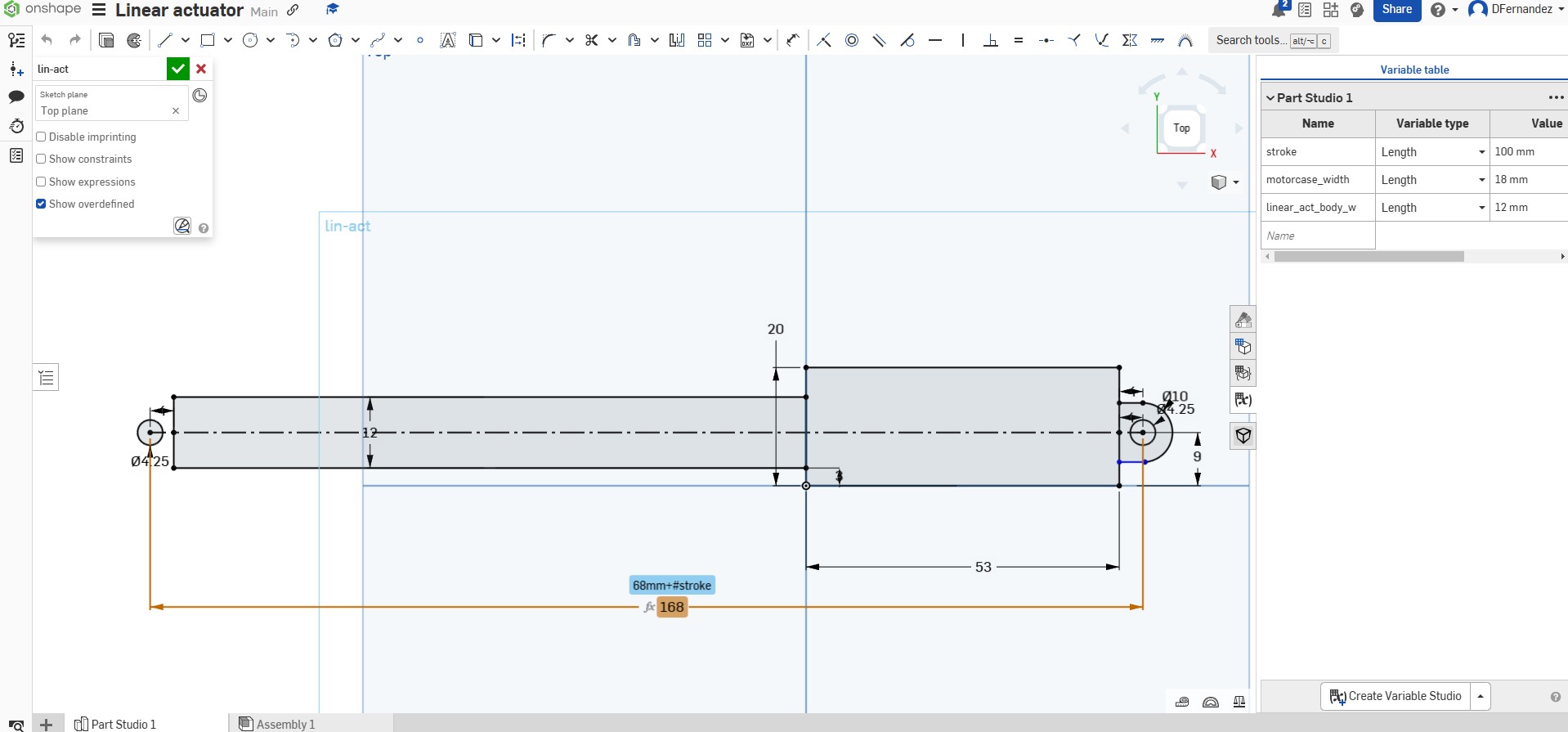
When extruding the geometry from the sketch you can also use variables.
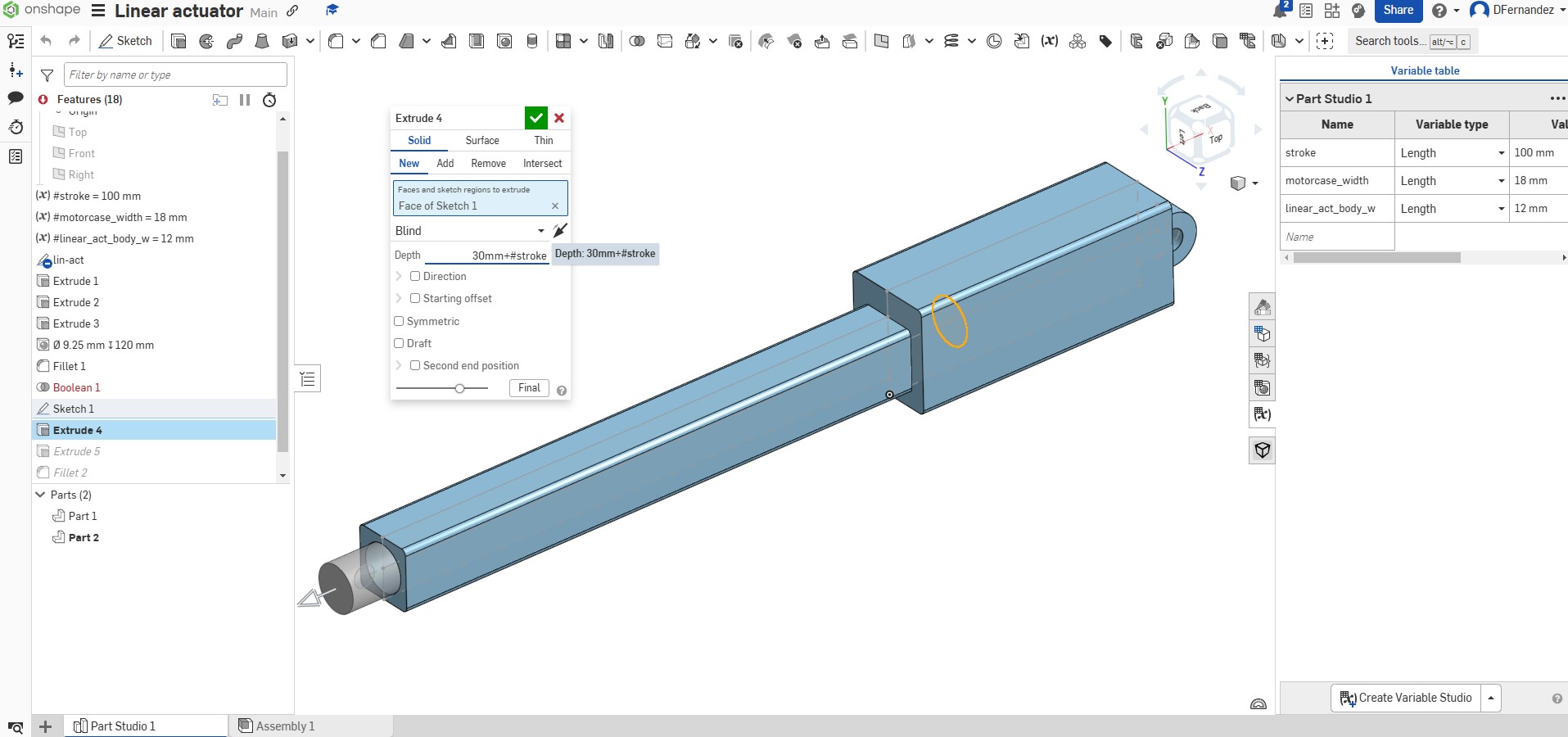
To apply joints, you must first create an assembly. There are various types of joints available; in this case, I will use the Slider Mate joint.
The maximum movement of the rod can be defined by a variable, which means that not only the dimensions of the linear actuator change, but the stroke length of the joint is also updated accordingly.
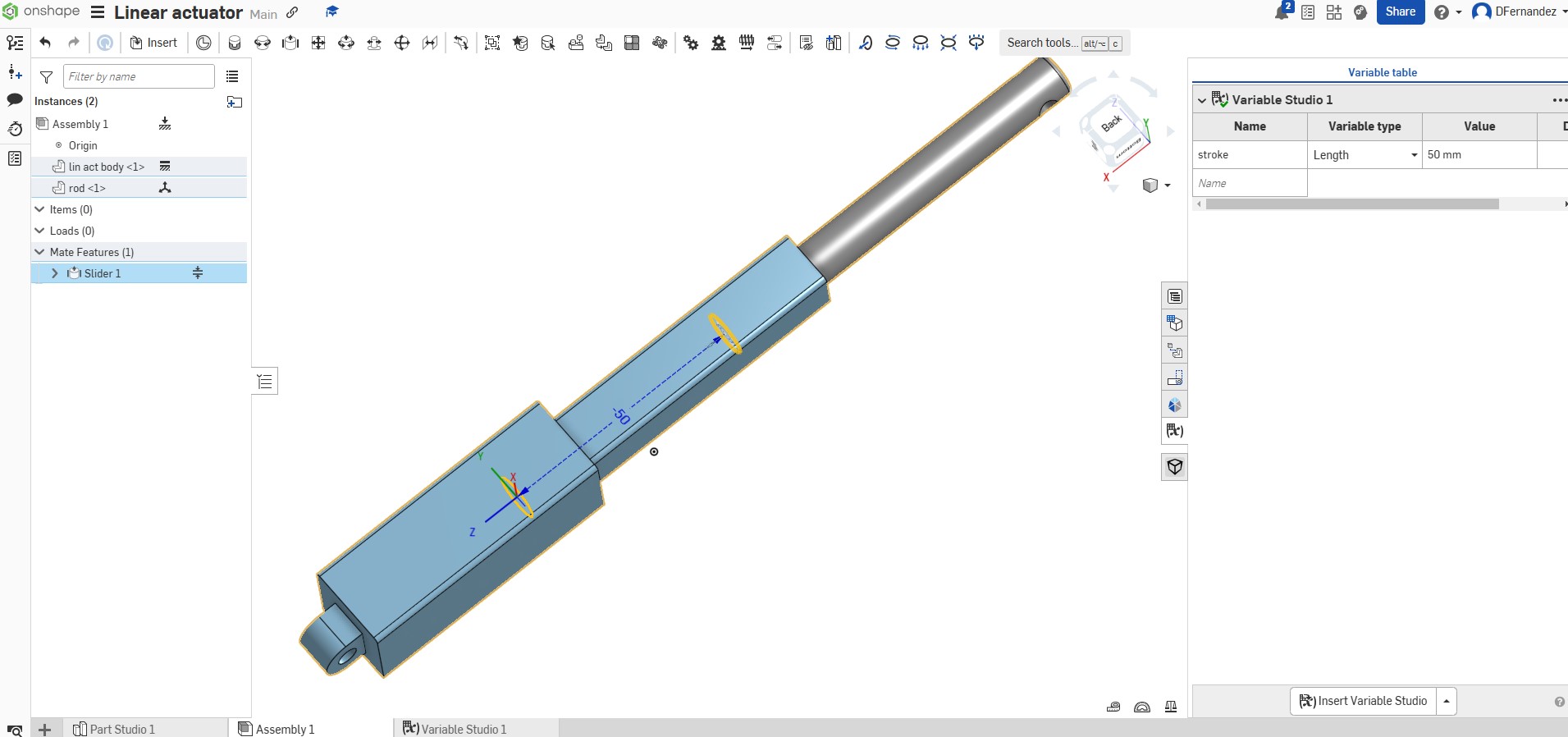
Overall, using Onshape was a seamless experience, and although I was not that familiar with this software, I didn’t require any tutorials.
FUSION
Fusion is another cloud-based CAD tool that offers features for product design, engineering, and manufacturing.
The workflow for creating the parametric design of the linear actuator closely resembles that of Onshape.
First, I created a sketch incorporating constraints and parametric values.
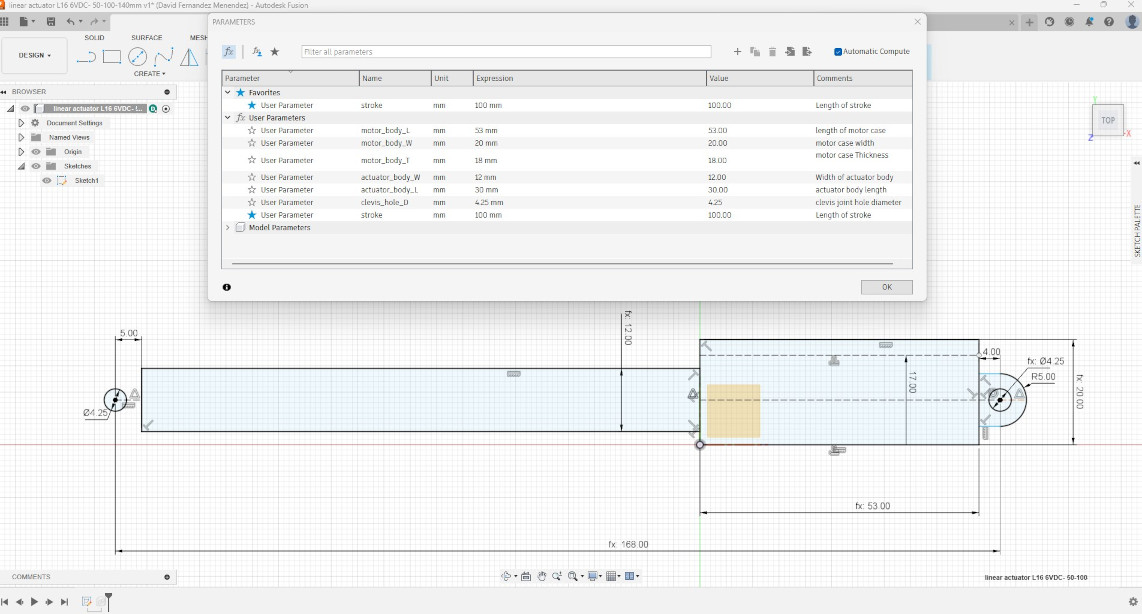
When extruding the sketch I can also make use of parametric values.
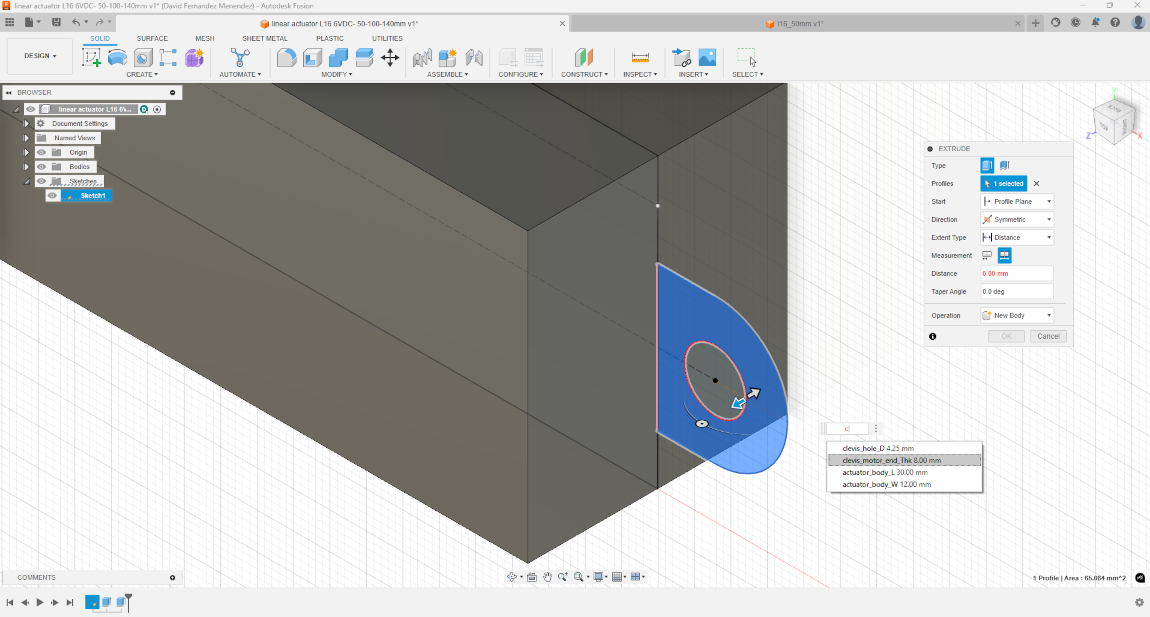
And when applying the Slider joint I could define the maximum motion limit using the stroke variable.
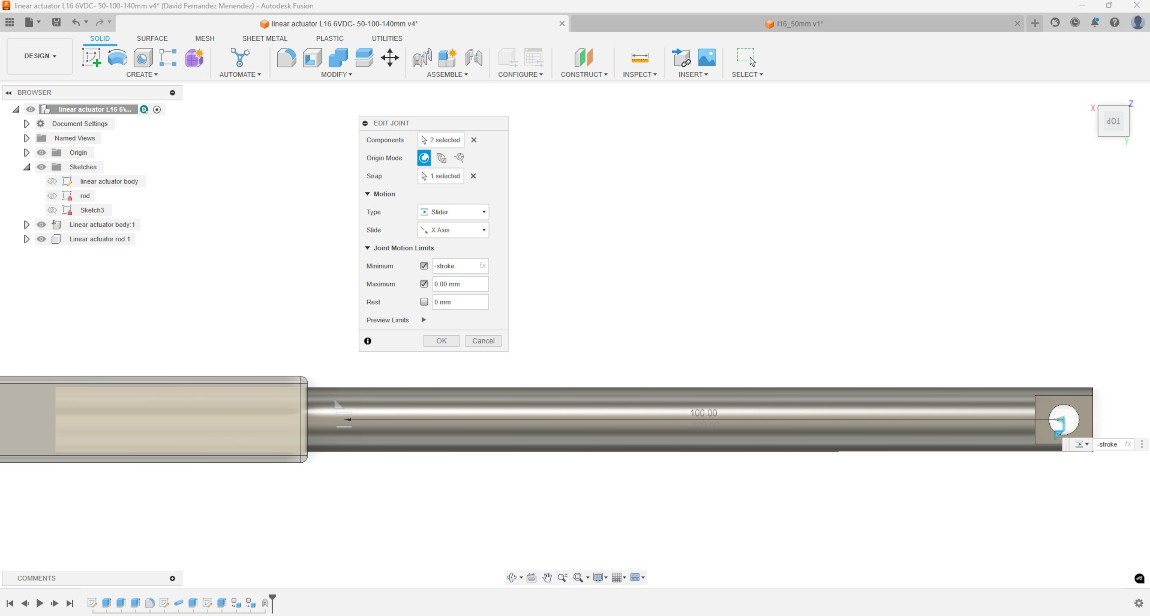
Additionally I found a Add-in that allows you to create parametric text that can then be embossed on the design. In this way I managed to make a parametric design that changes the dimensions of the linear actuator, modifies the motion limits of the joints and updates the engraved text to show the stroke length of the actuator.
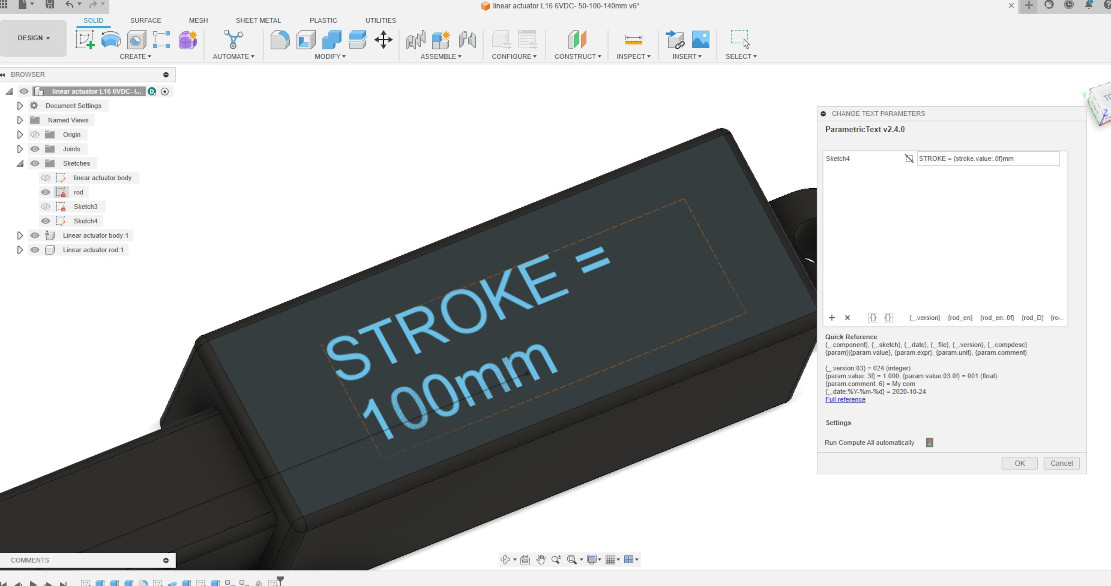
The following video shows how easily the design can be modified changing the parametric values.
Fusion provides a viewer that can be shared via a link or embedded on a website. This allows everyone to visualize the design in a 3D environment and even animate it.
I have previous experience using Fusion, which in this case has proven to be a powerful CAD tool. It integrates many functionalities that I will utilise later in the course and for designing my final project, including rendering, 2D drawing generation, animations, and analysis.
TopFREECAD
FreeCAD is an open-source, parametric 3D modeling software. Having previously used the 2D drafting environment, I am now exploring the parametric and 3D modeling capabilities of the software.
I used the Sketcher workbench to create geometry by applying constraints and the parametric variables defined in the Spreadsheet. This process took longer than with other software I evaluated because applying constraints was not as intuitive, and I encountered an error when trying to create a solid. The issue arose because the areas were not fully enclosed; it appears that the two rectangles need to have overlapping coincident edges. This is not required in Fusion or Onshape.
It would also be beneficial to see the areas filled with color when they are closed and ready to be extruded as it happens in other CAD platforms.
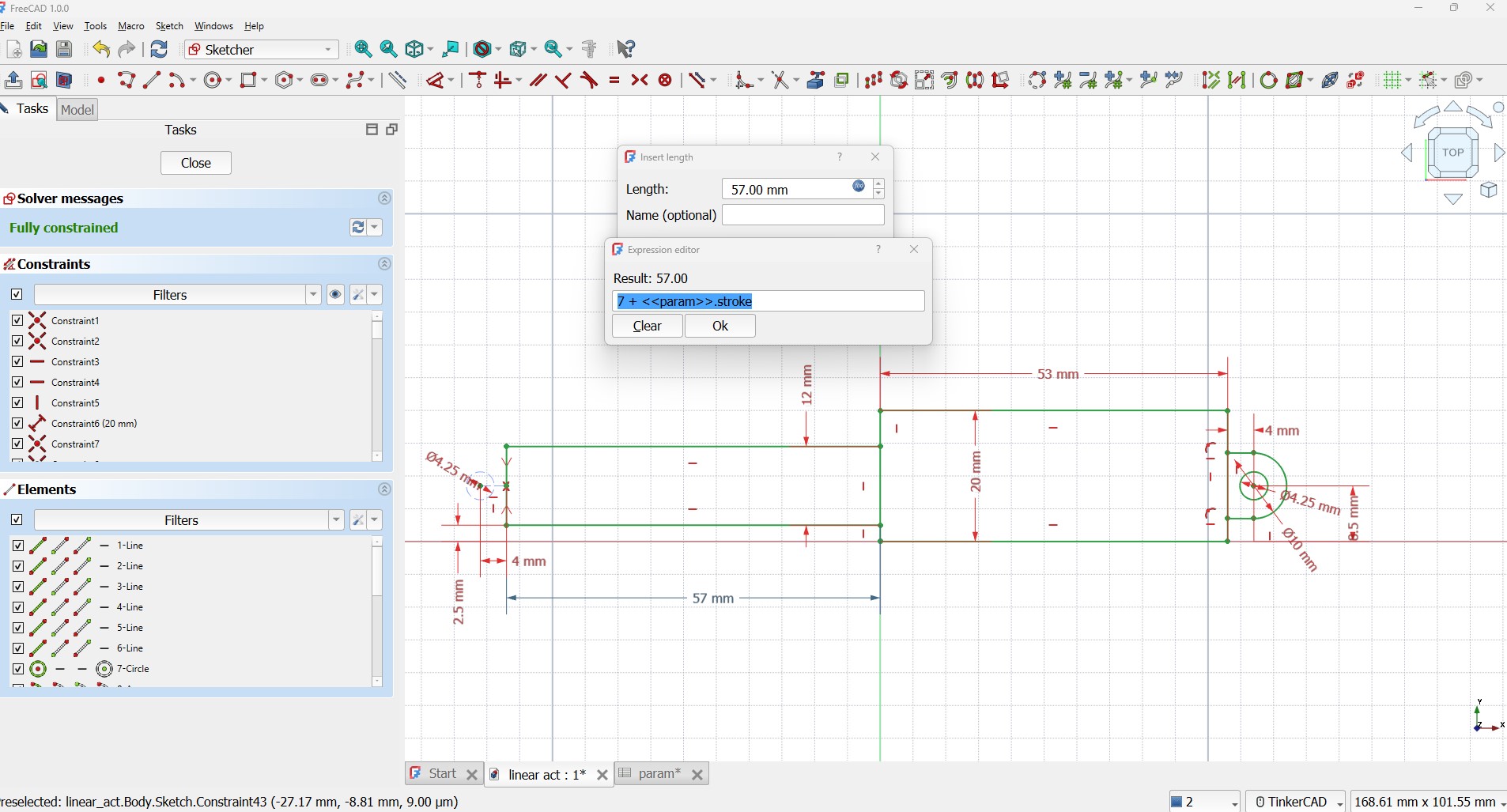
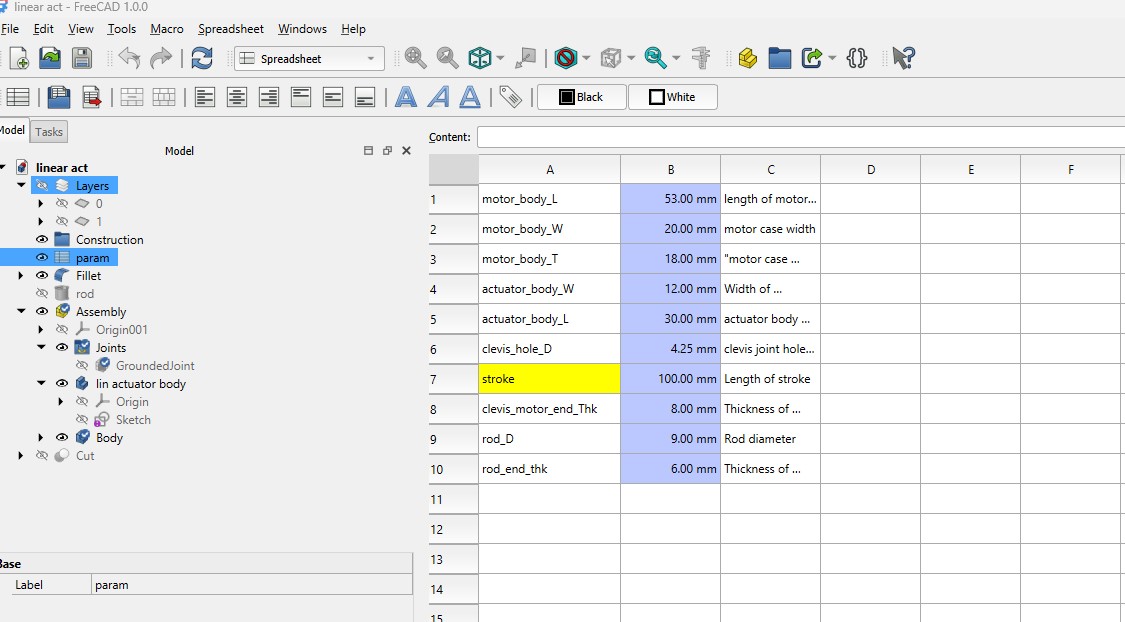
When extruding a 2D geometry, you can apply parametric values to define the depth of the extrusion. However, I discovered that it is not possible to extrude different areas of the same sketch, which means I cannot apply varying thicknesses as I was able to do before. This is quite cumbersome, as I would need to create 3 separate sketches to achieve the same solid that I previously generated using other software with just 1 sketch
Additionally, I am a bit confused about the use of the Part Design and Part Workbenches. I find myself switching between these two workspaces too often.
In the Part workbench, I create another extrusion to make a hole for the rod. Then, I use a Boolean operation to remove one part from another.
I then moved to the Assembly Workbench to create the slider joint, but I encountered some additional problems. I was able to ground one of the parts, but when I attempted to create the joint, I couldn't select the contact faces from the grounded part.