Electronics Production | Week 05
Group Assignment #2: Electronic Production
Objectives of this Group Assignment:
Types of PCBs
PCB Fabrication (Process, Material, Machine and Tools)
Machining (Milling) for PCB Fabrication
Material, Machine and Tools used in PCB Machining (Milling)
Material:
Machine:
Tools:
Generate the tool path for tracing and cutting:
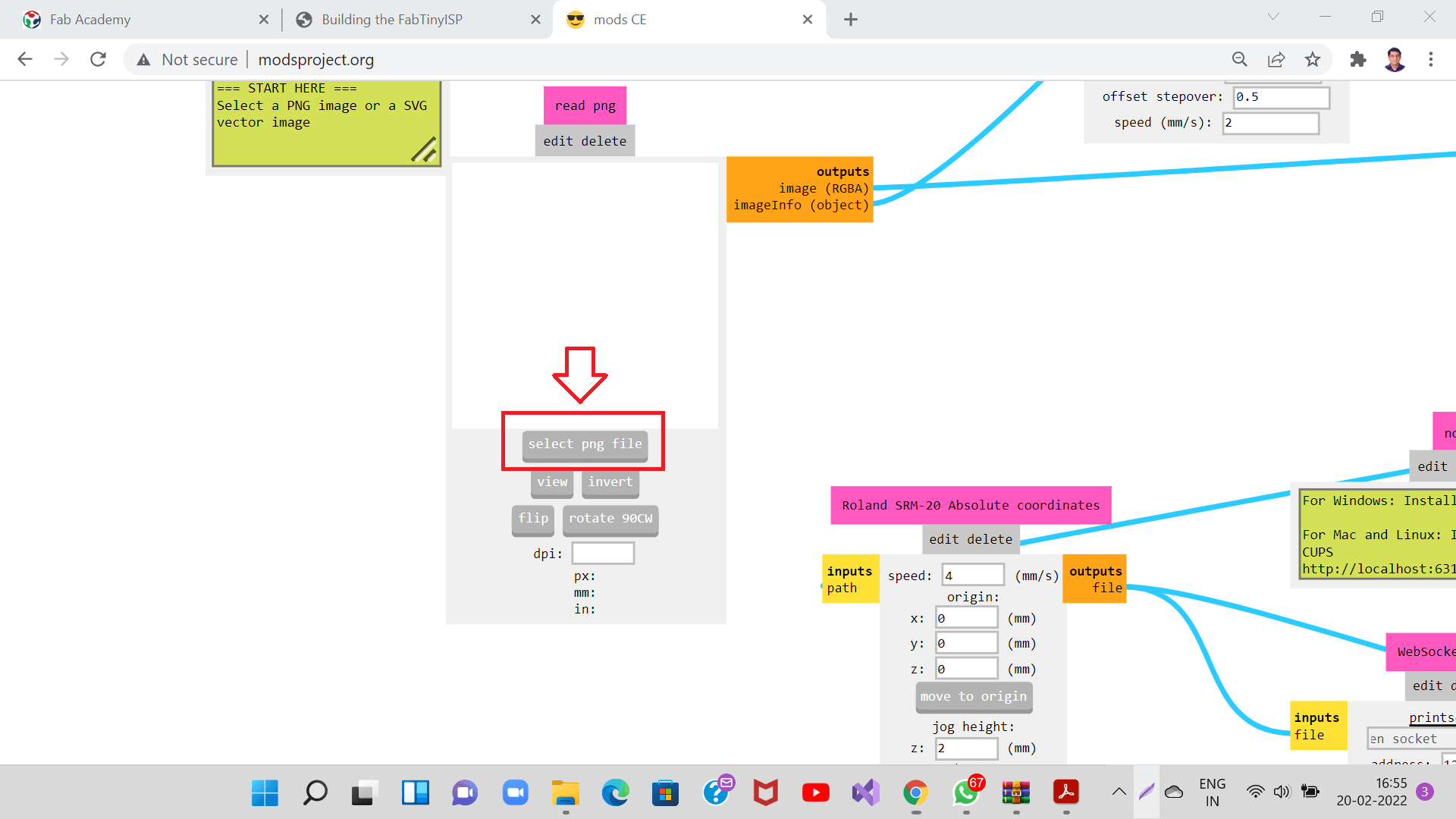
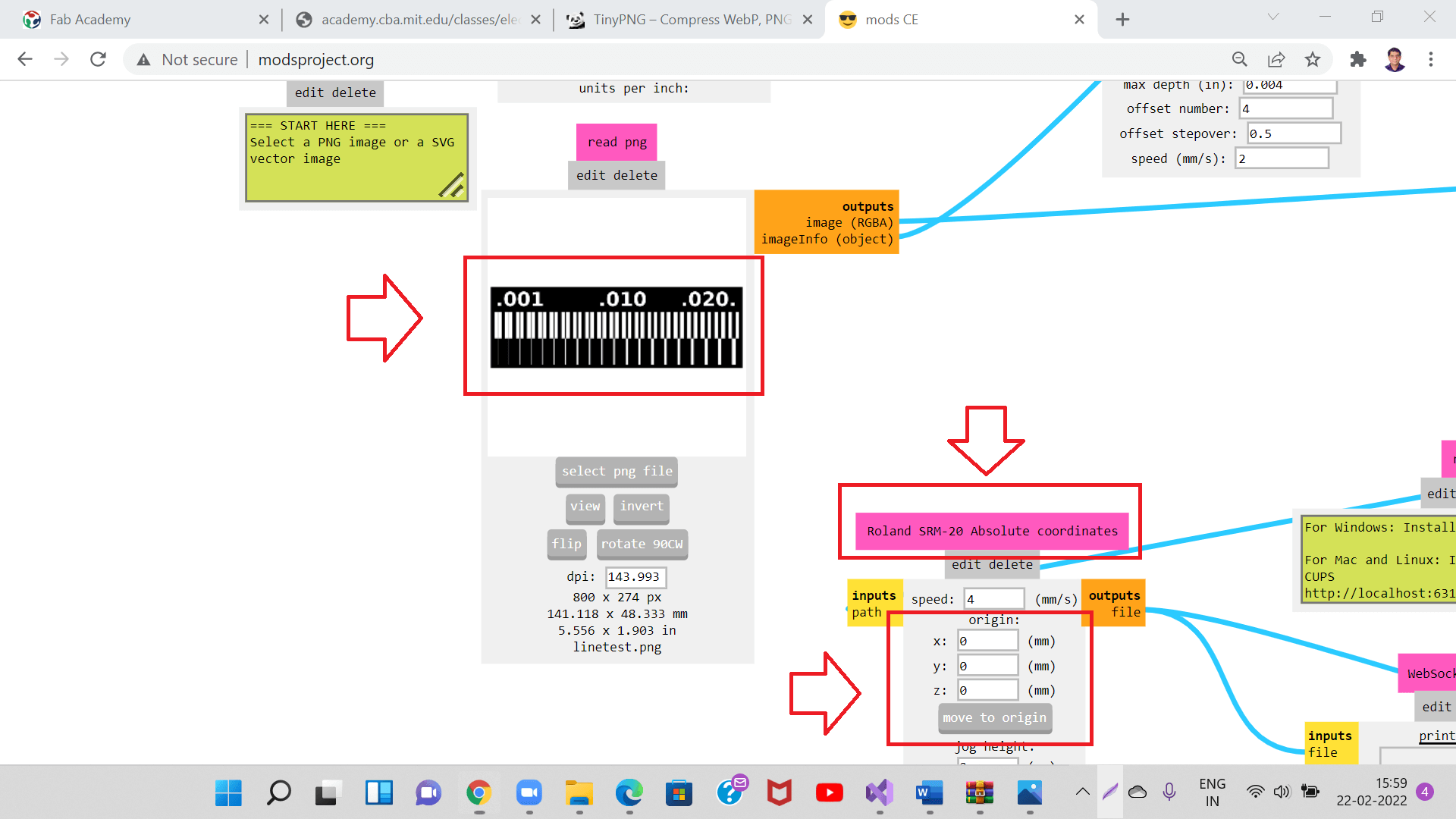
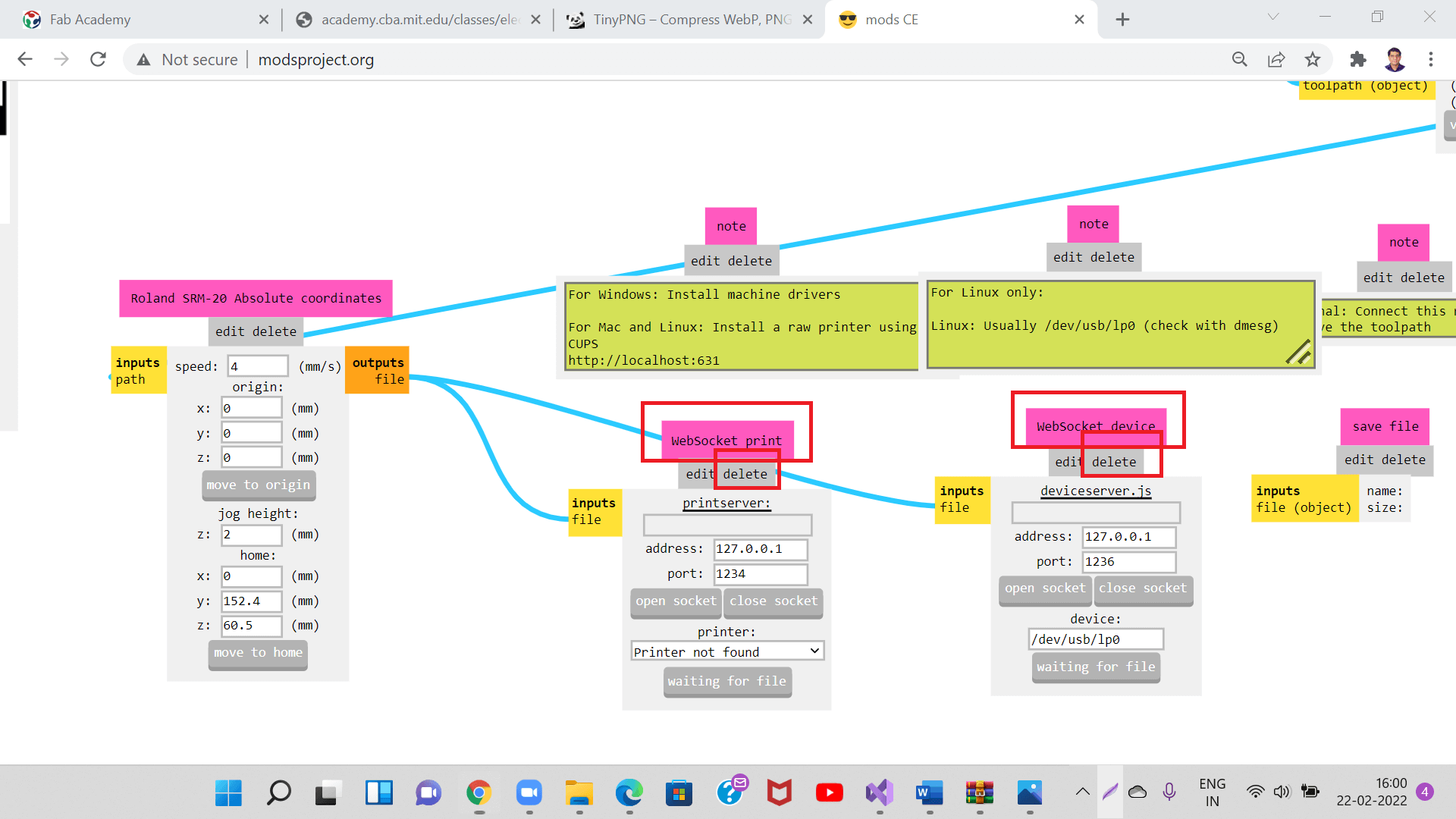
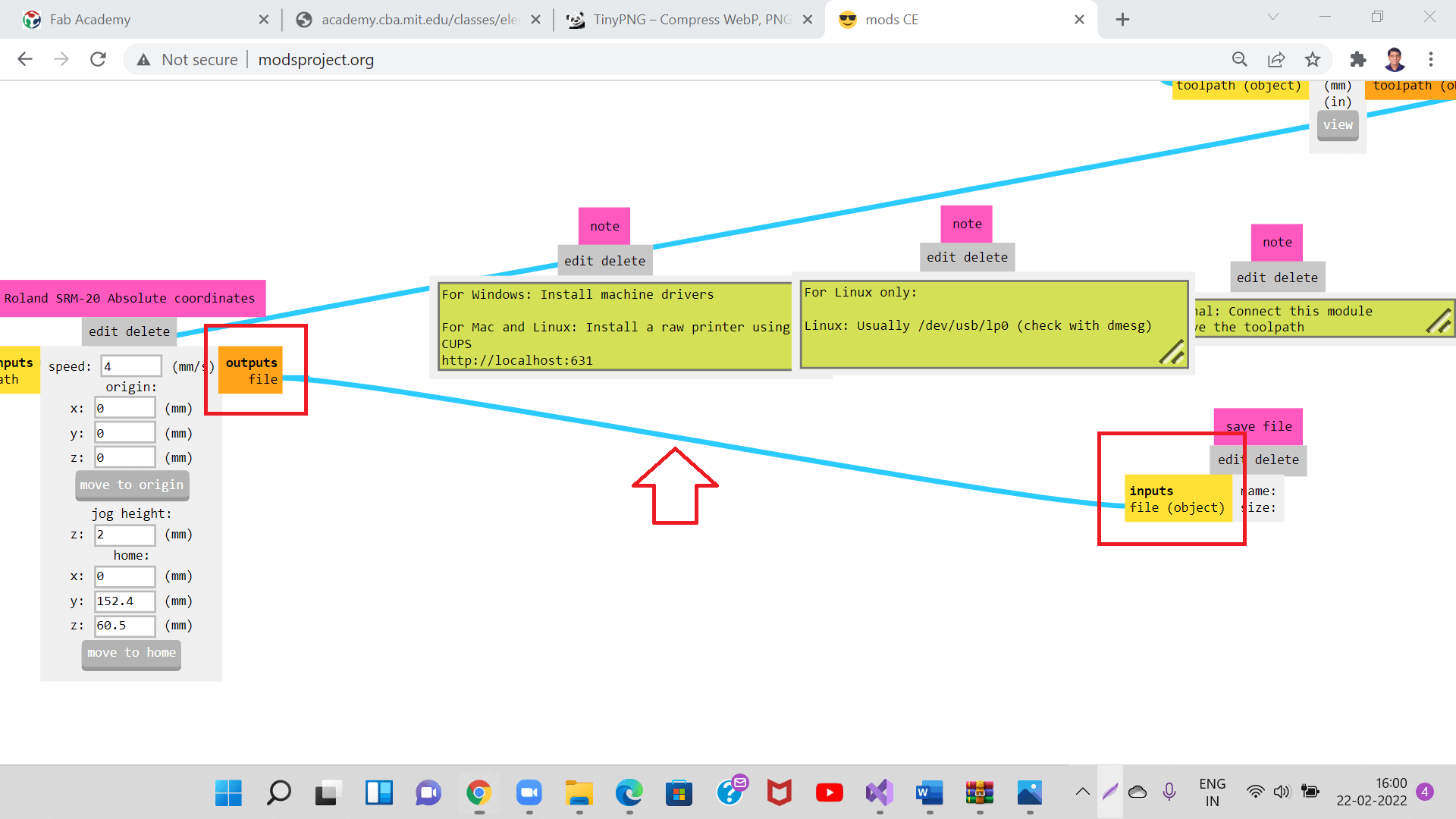
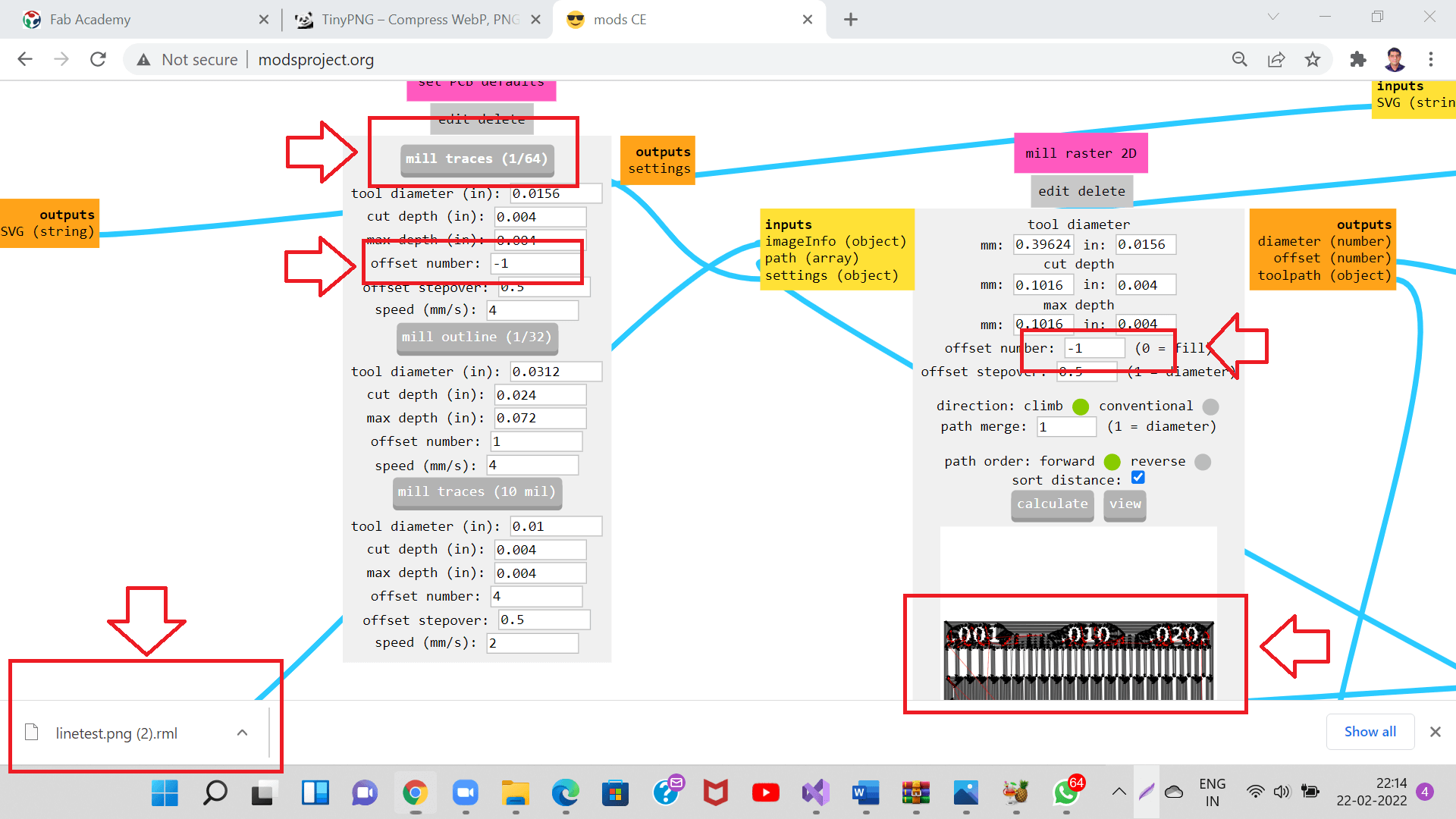
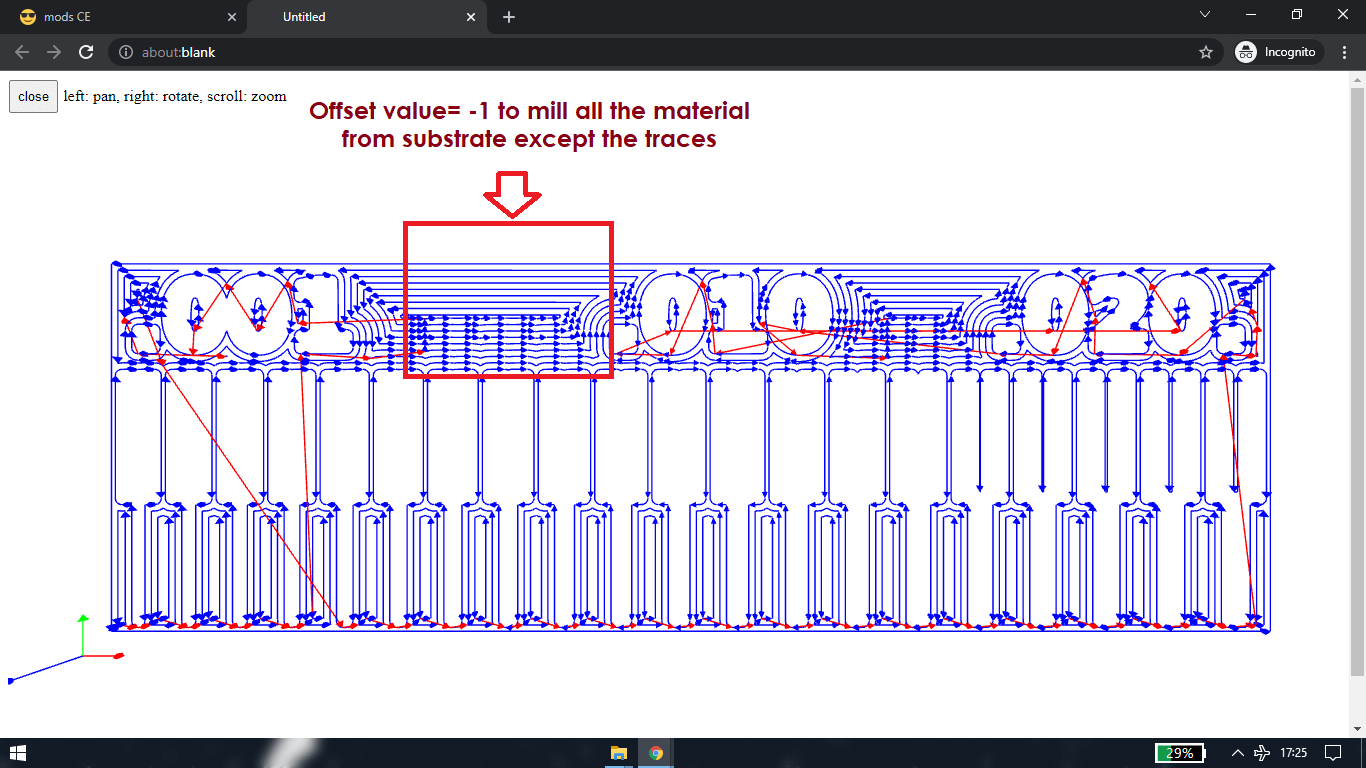
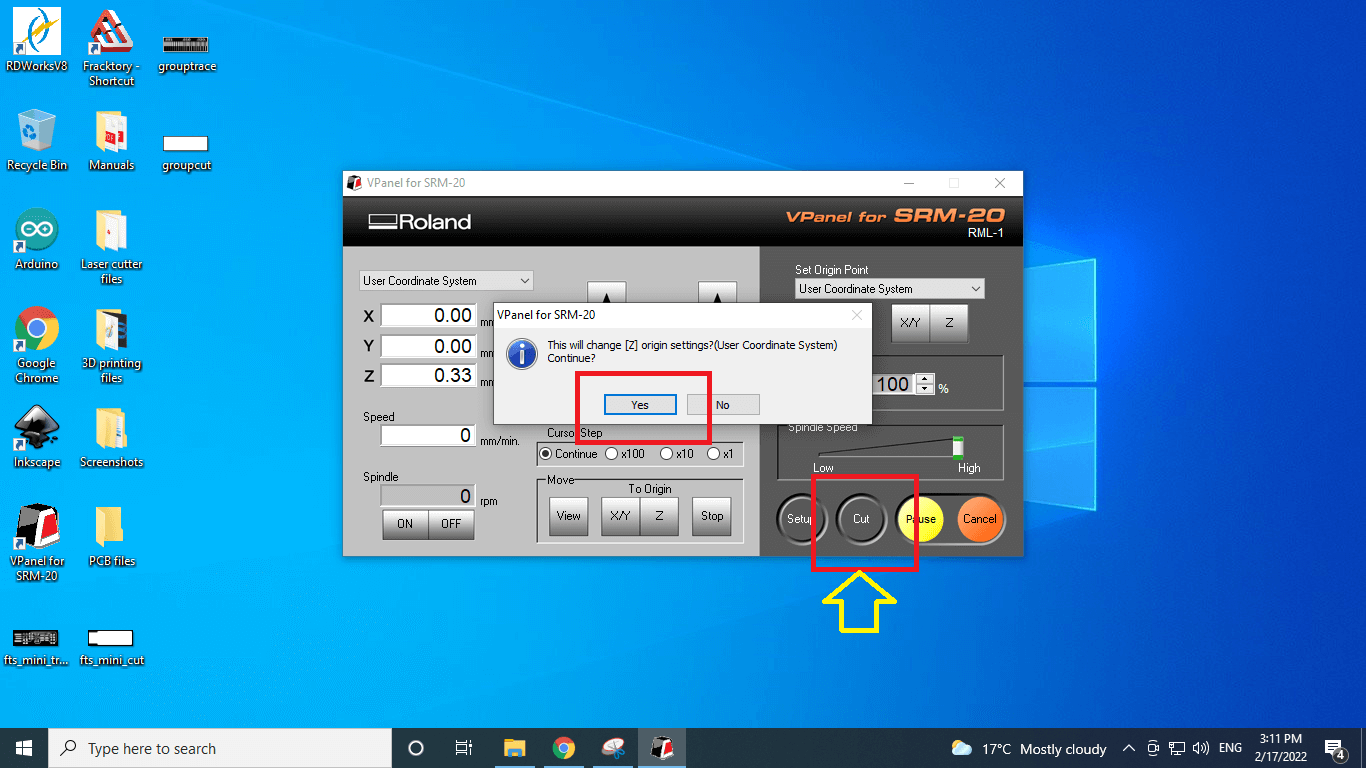

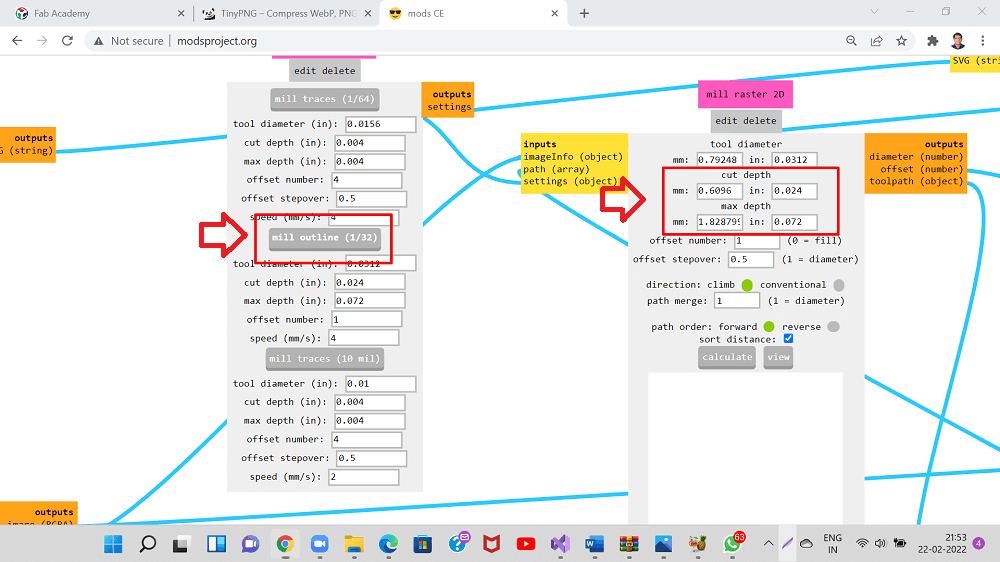
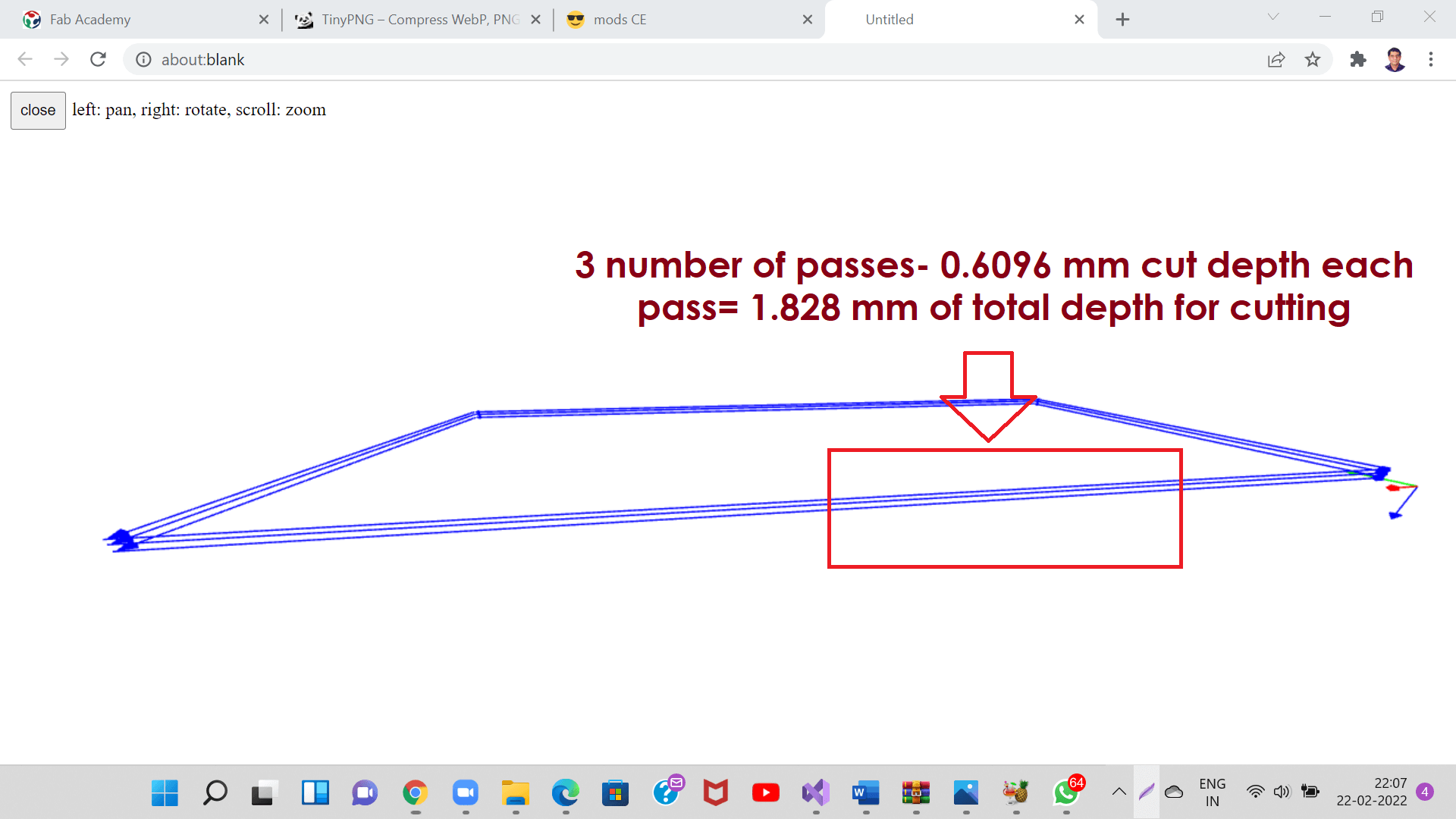
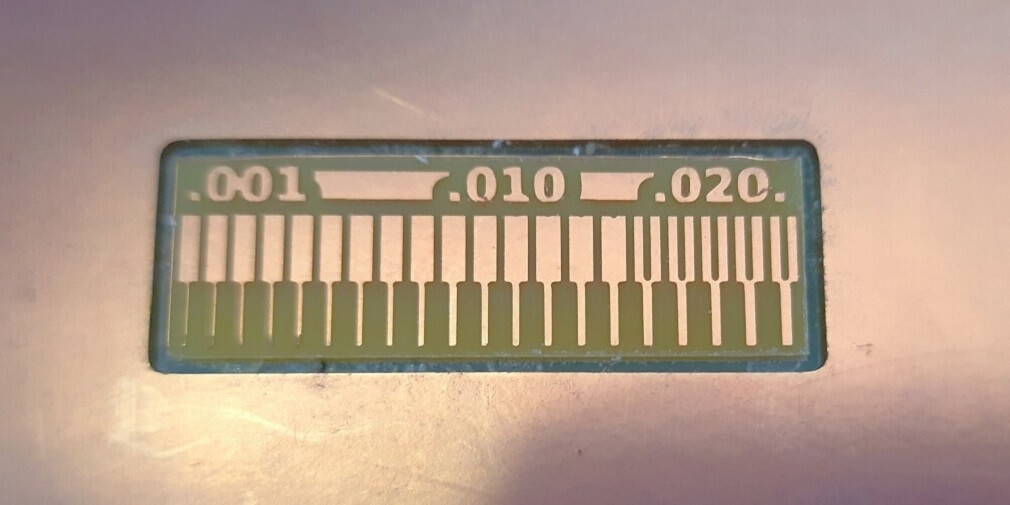
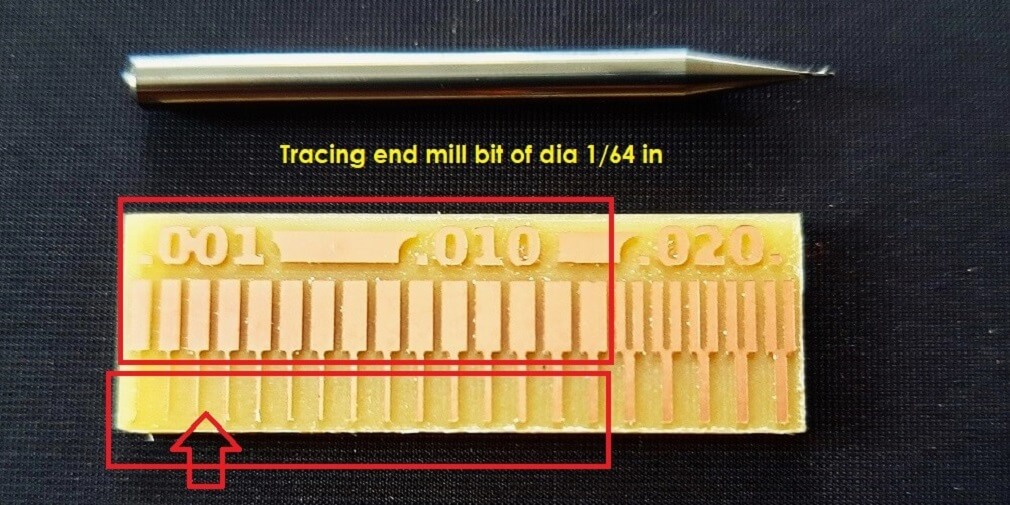
Files from Brian:-
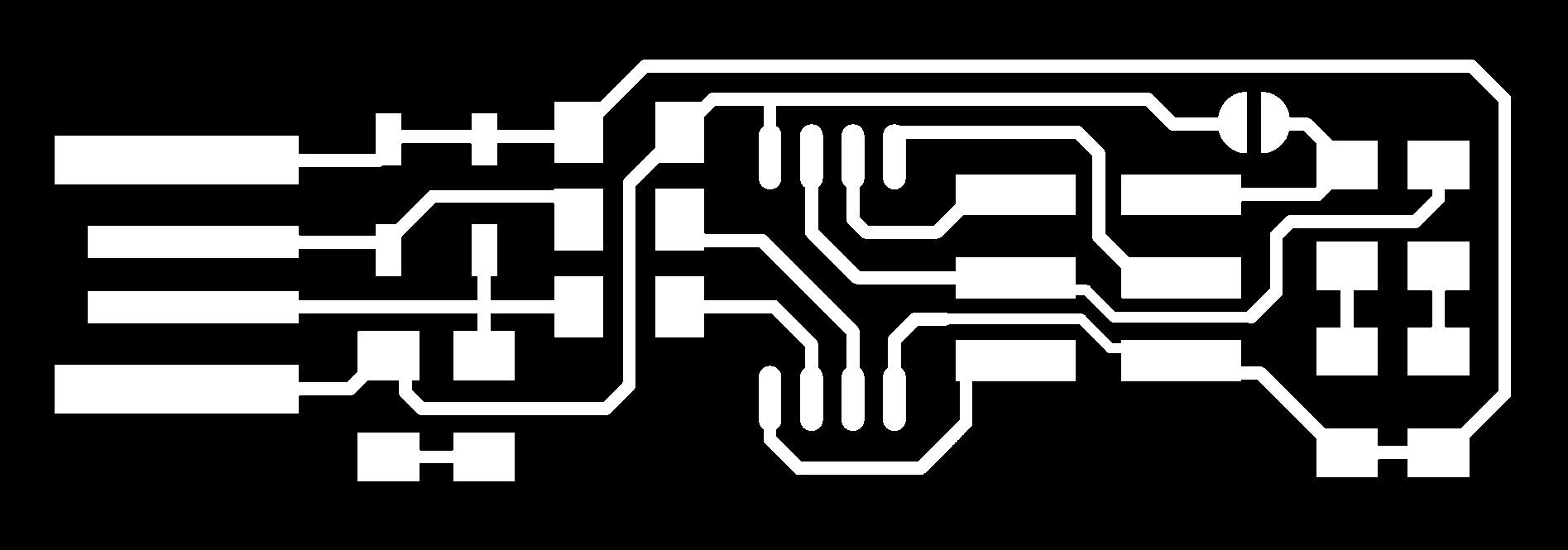
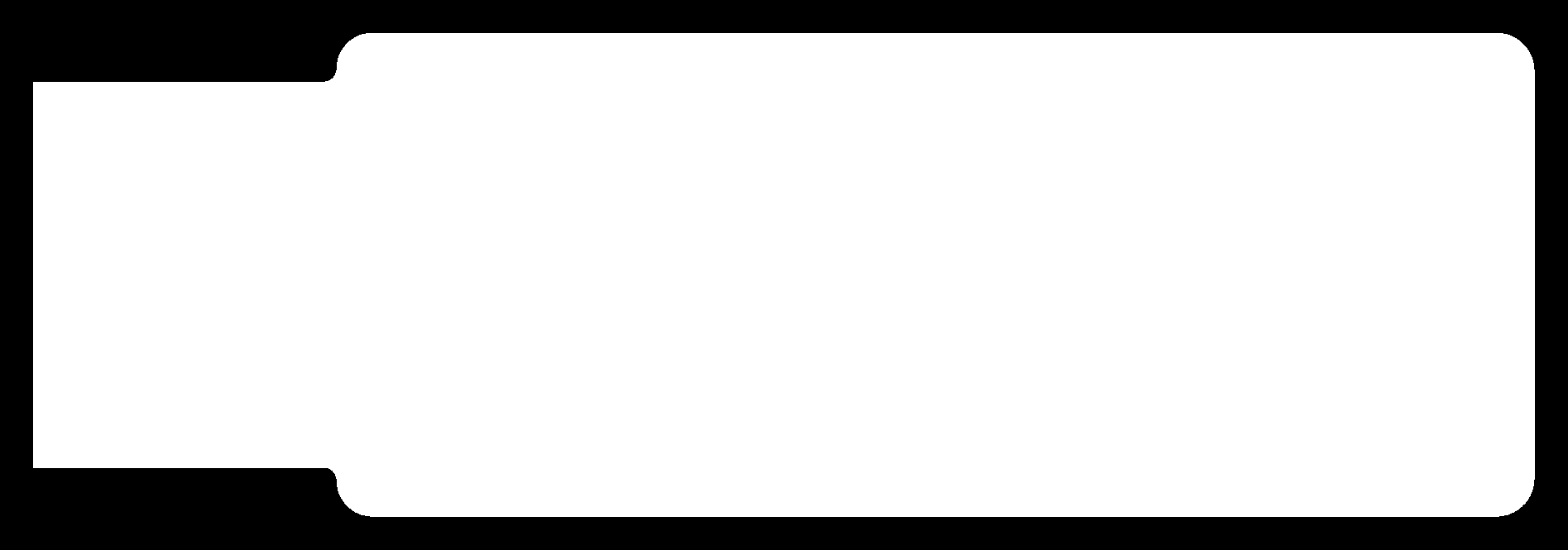
Fab modules:-
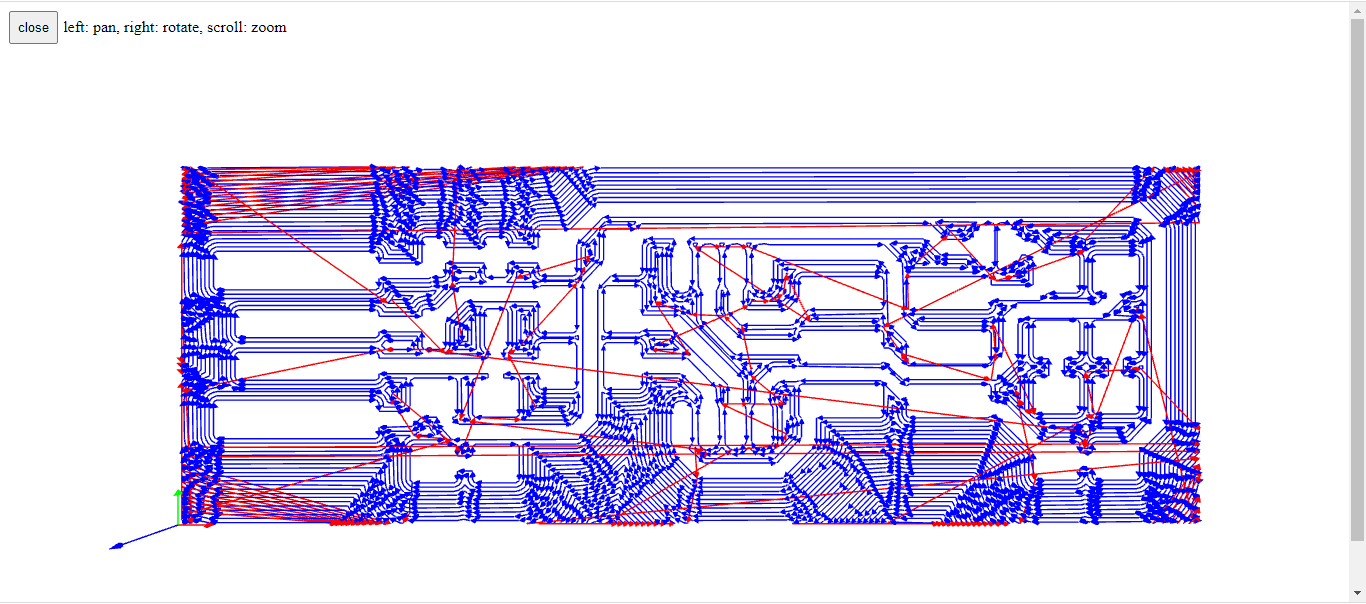
Download .rml file
Specifications and system requirements of SRM-20
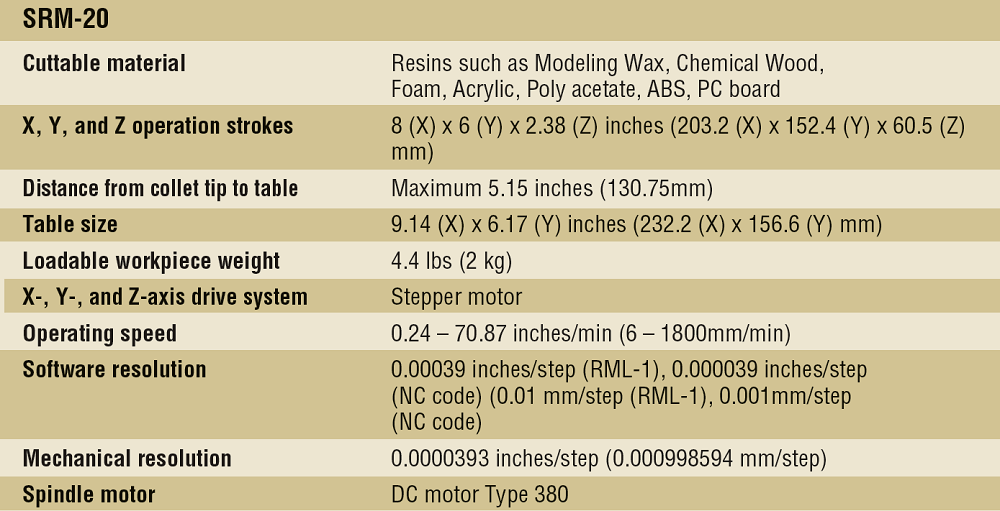
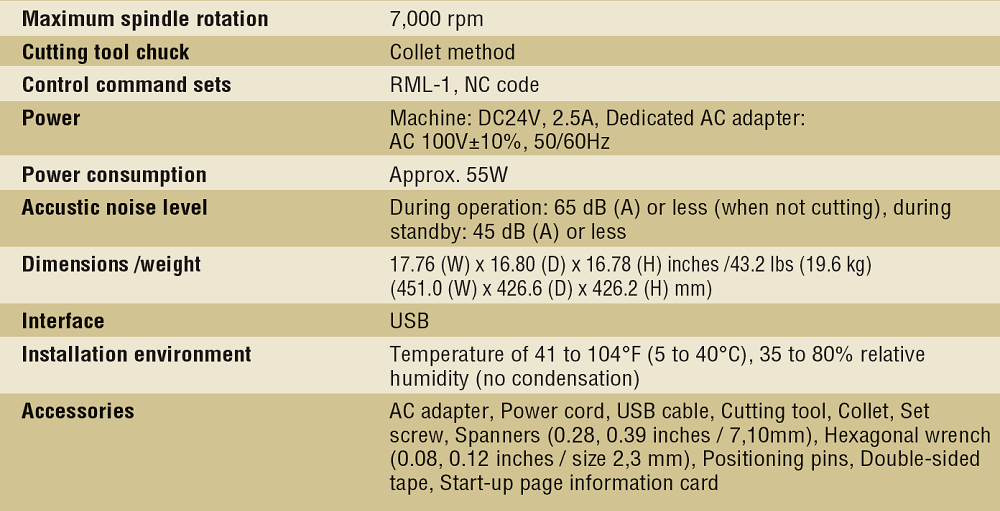
Upload File Vpanel:
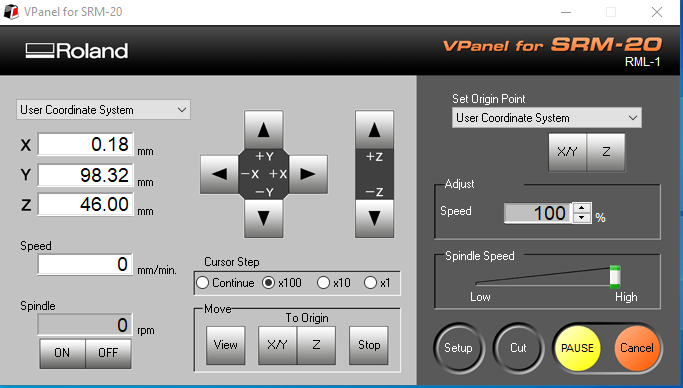
Explain VPanel
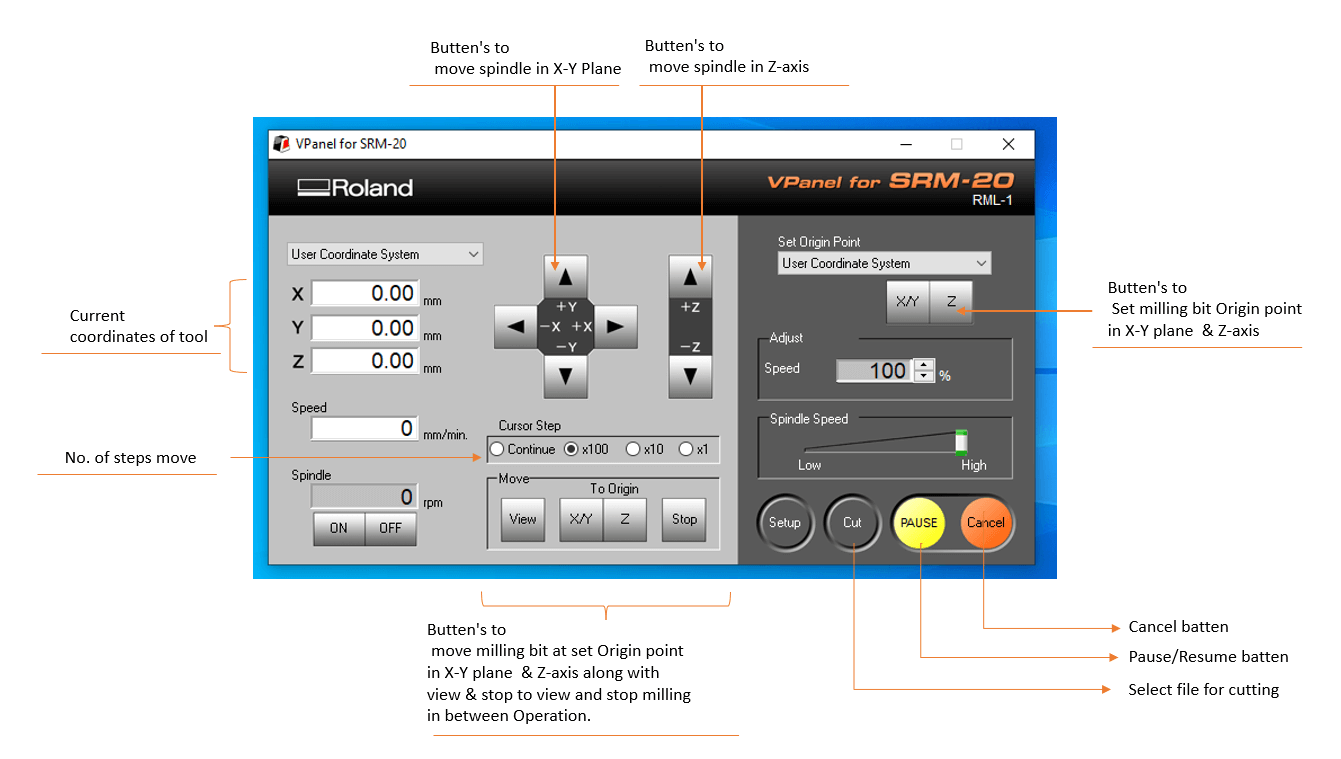
Upload Cut File VPanel
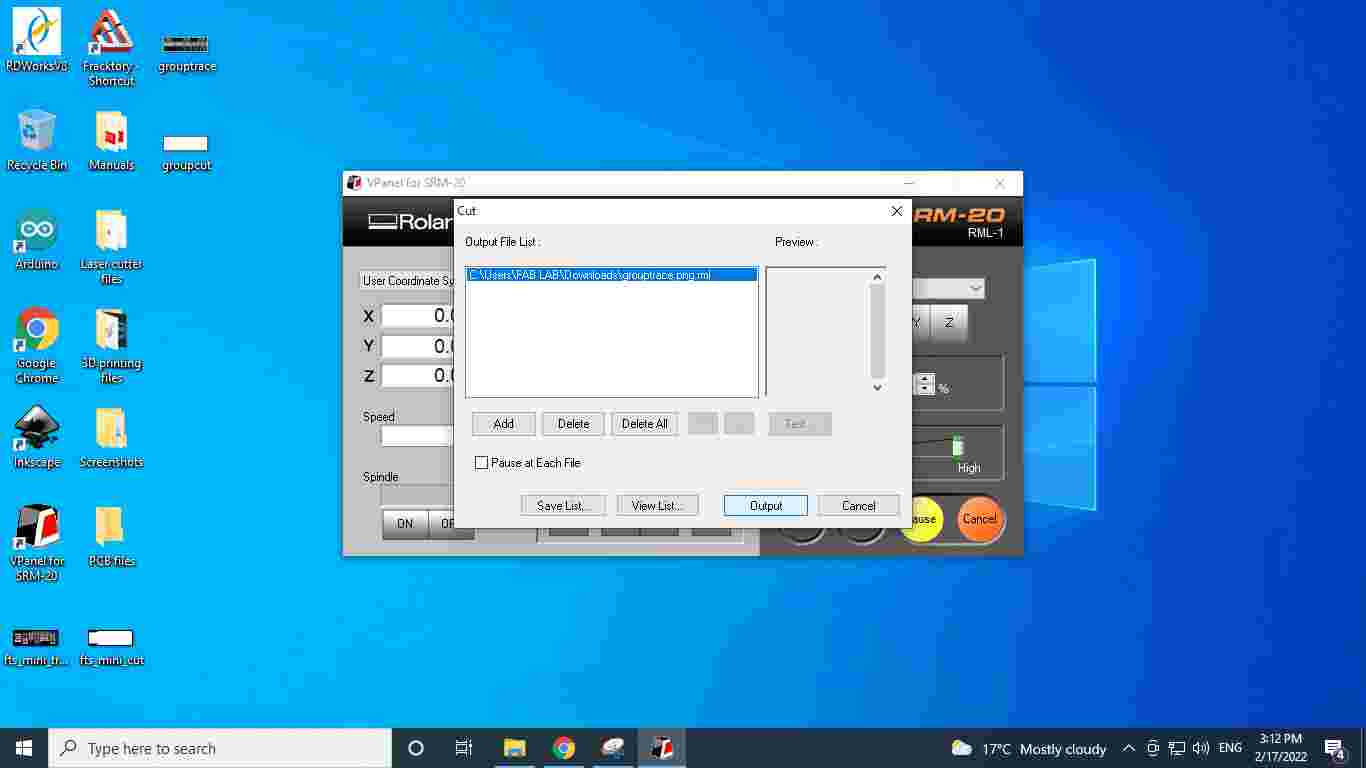
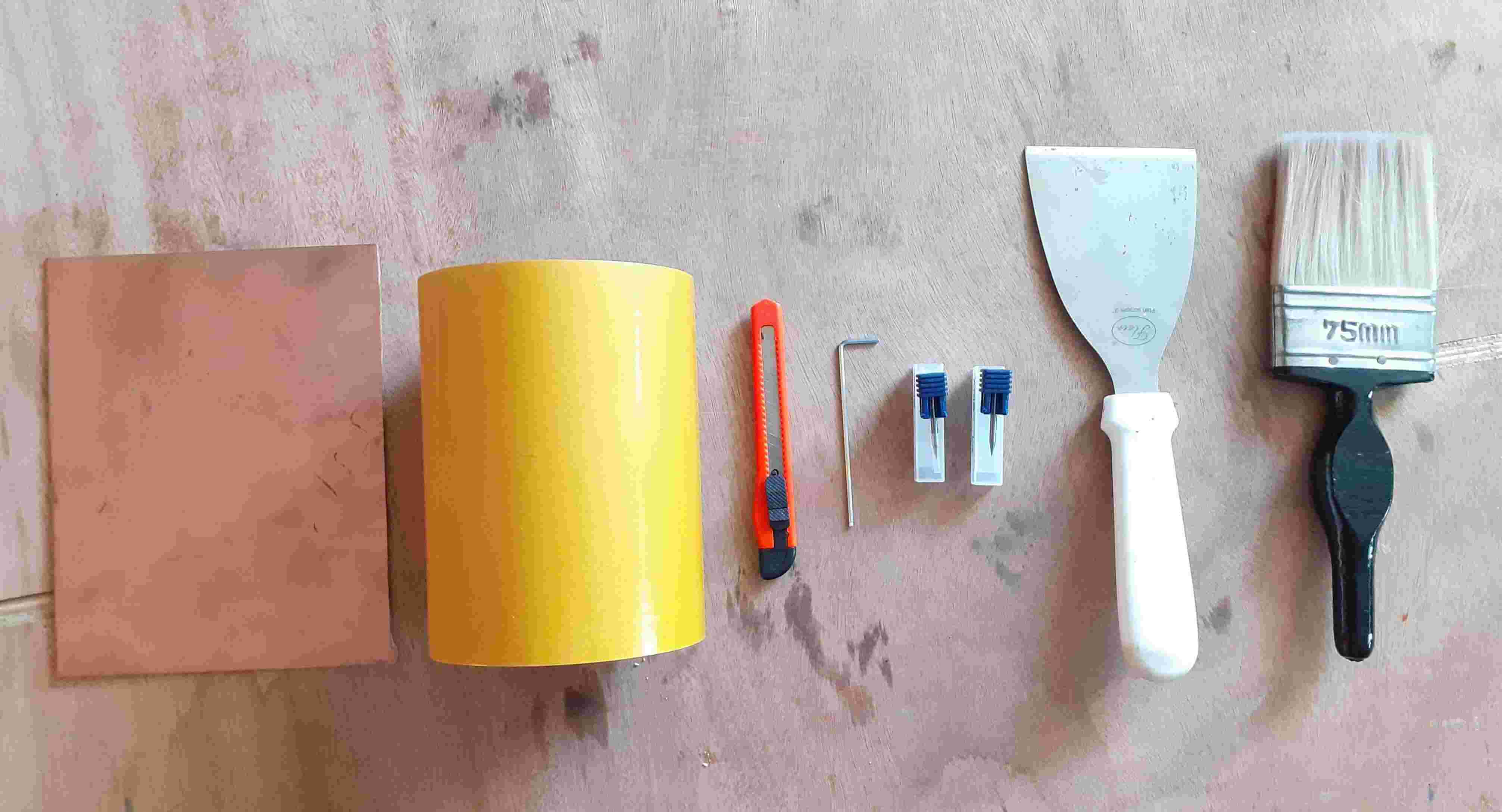
Pre-prepartion for milling
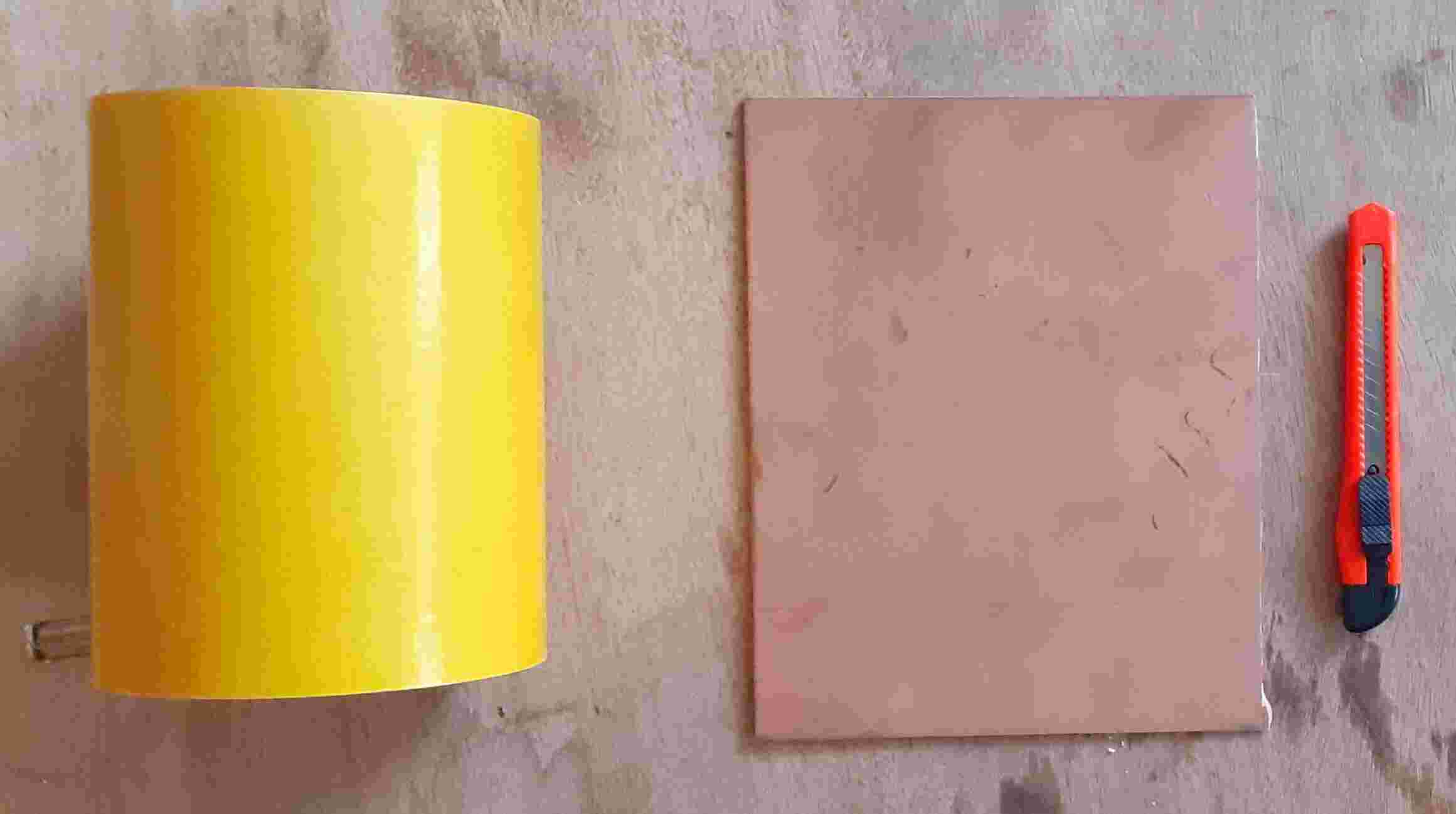
Material Thickness Check
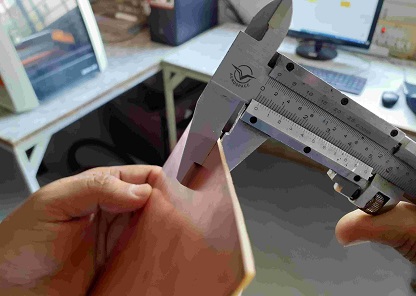
Use Bit
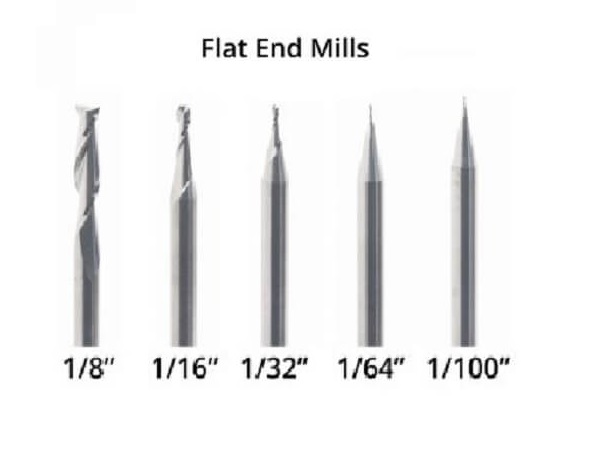
1/64
1/32
sacrificial layer
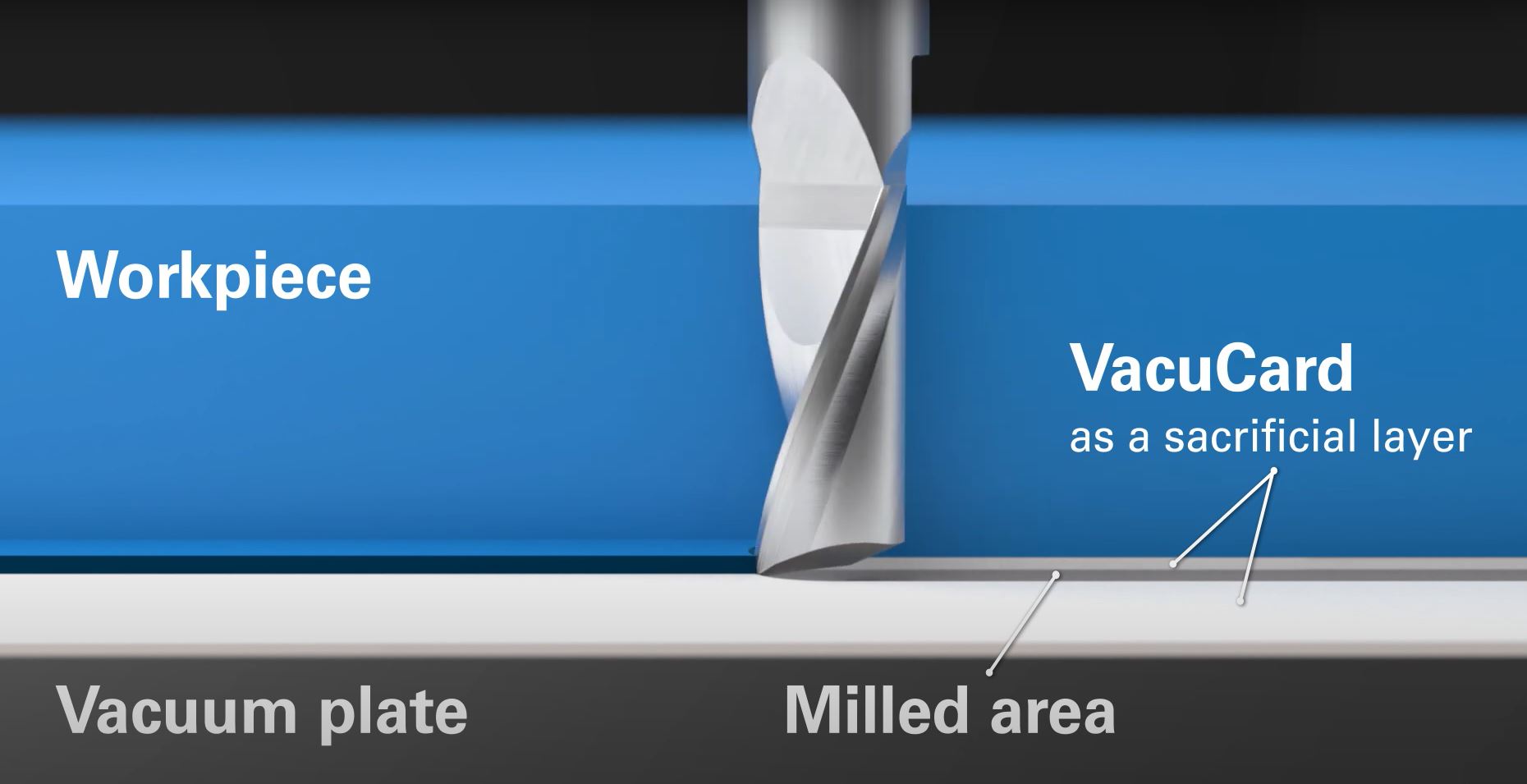
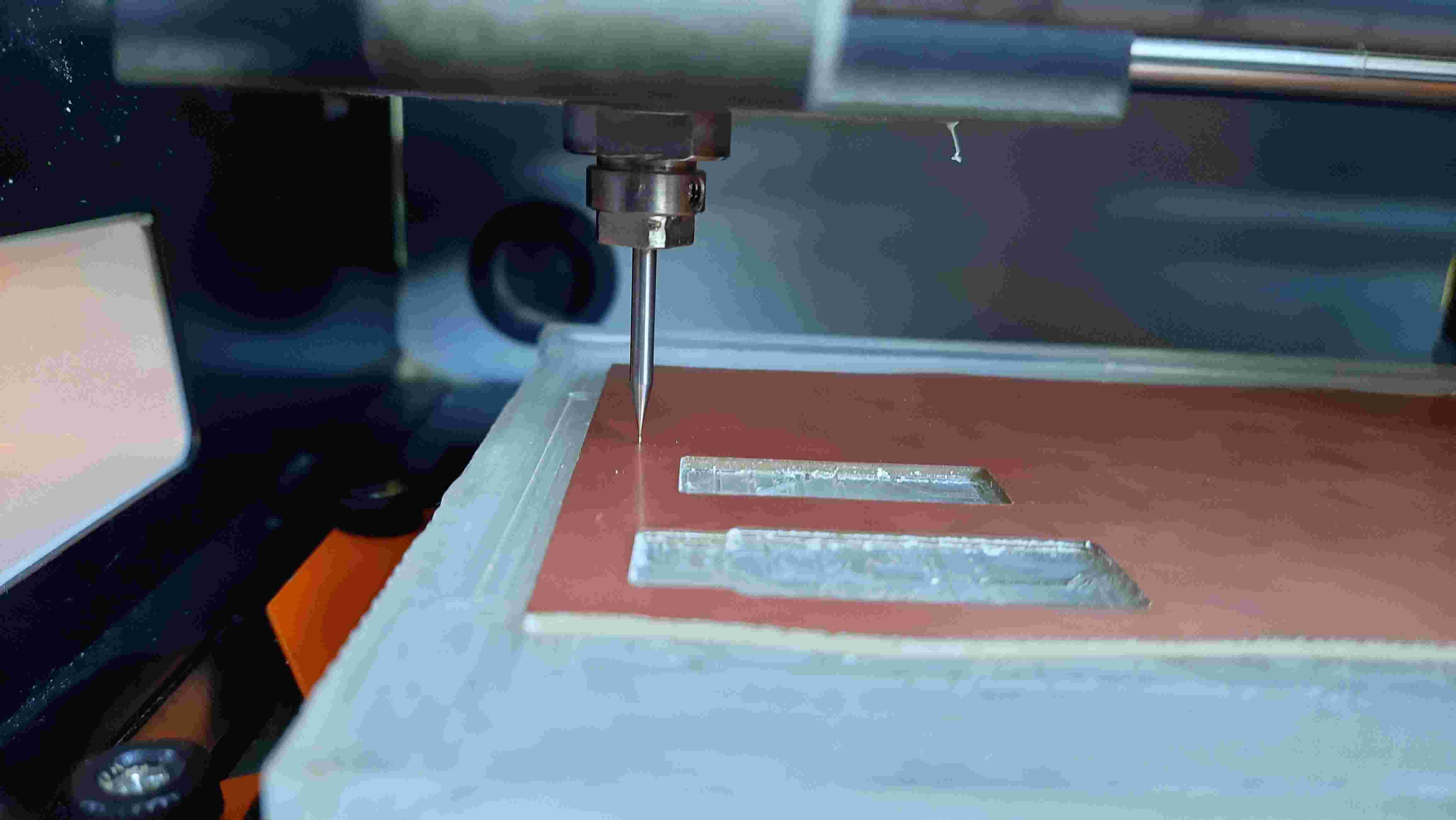
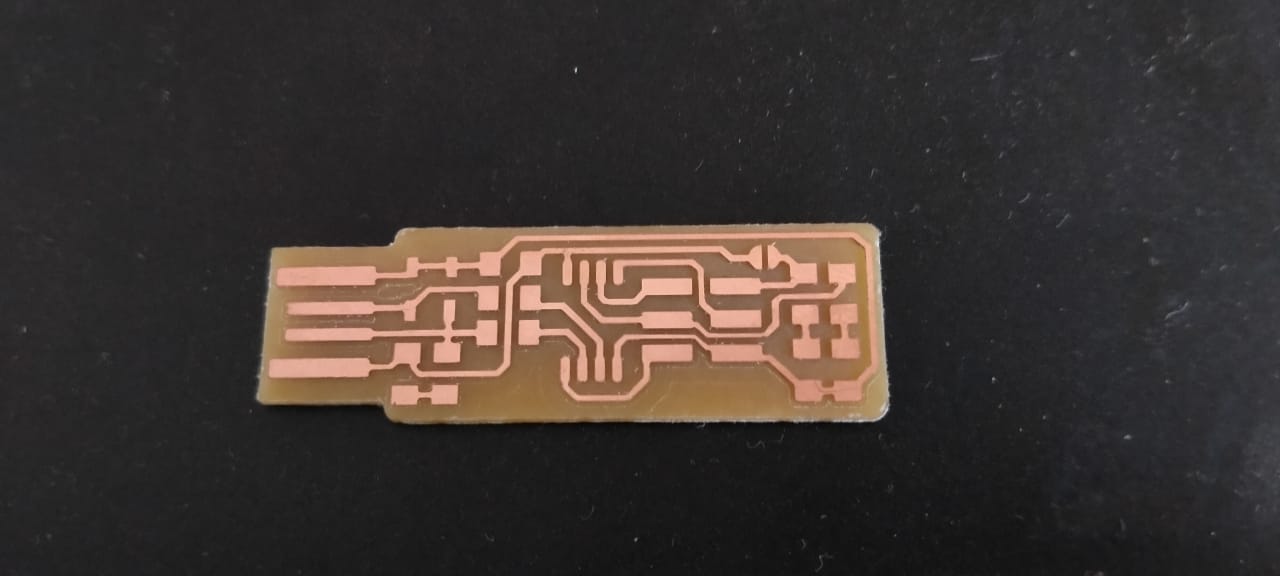
What is Solder?
Filler:
Flux:
Soldering Iron Rod:
Hot Air Gun:
Exhaust Fan:
Desolder Pump:
Twisers:
Magnifying Glass:
Light lamp:
What is the FabISP?
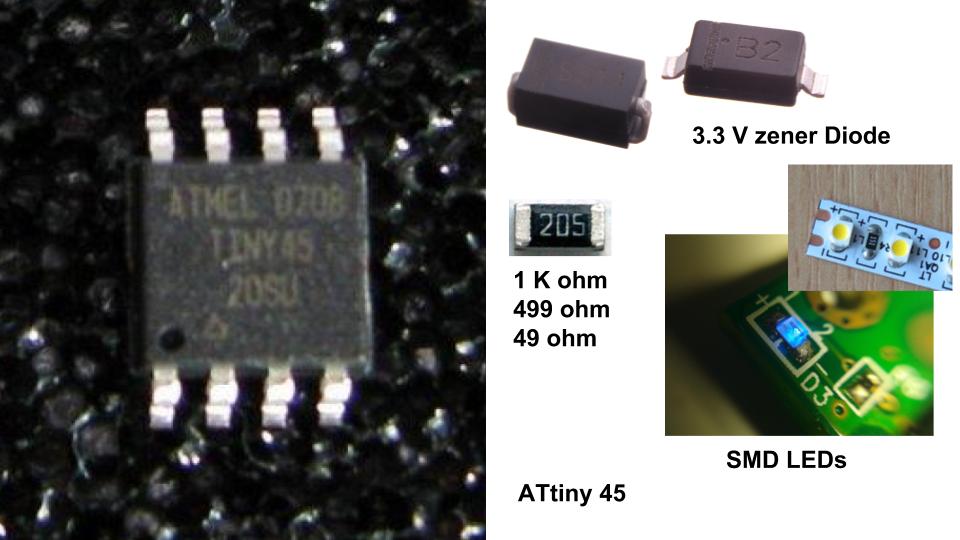
Components of circuit:
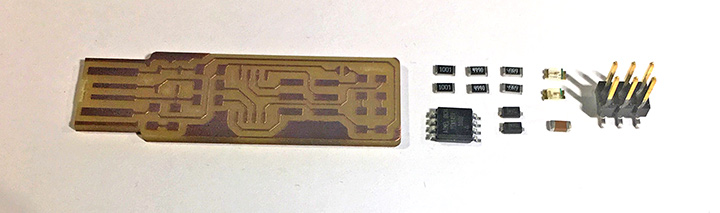
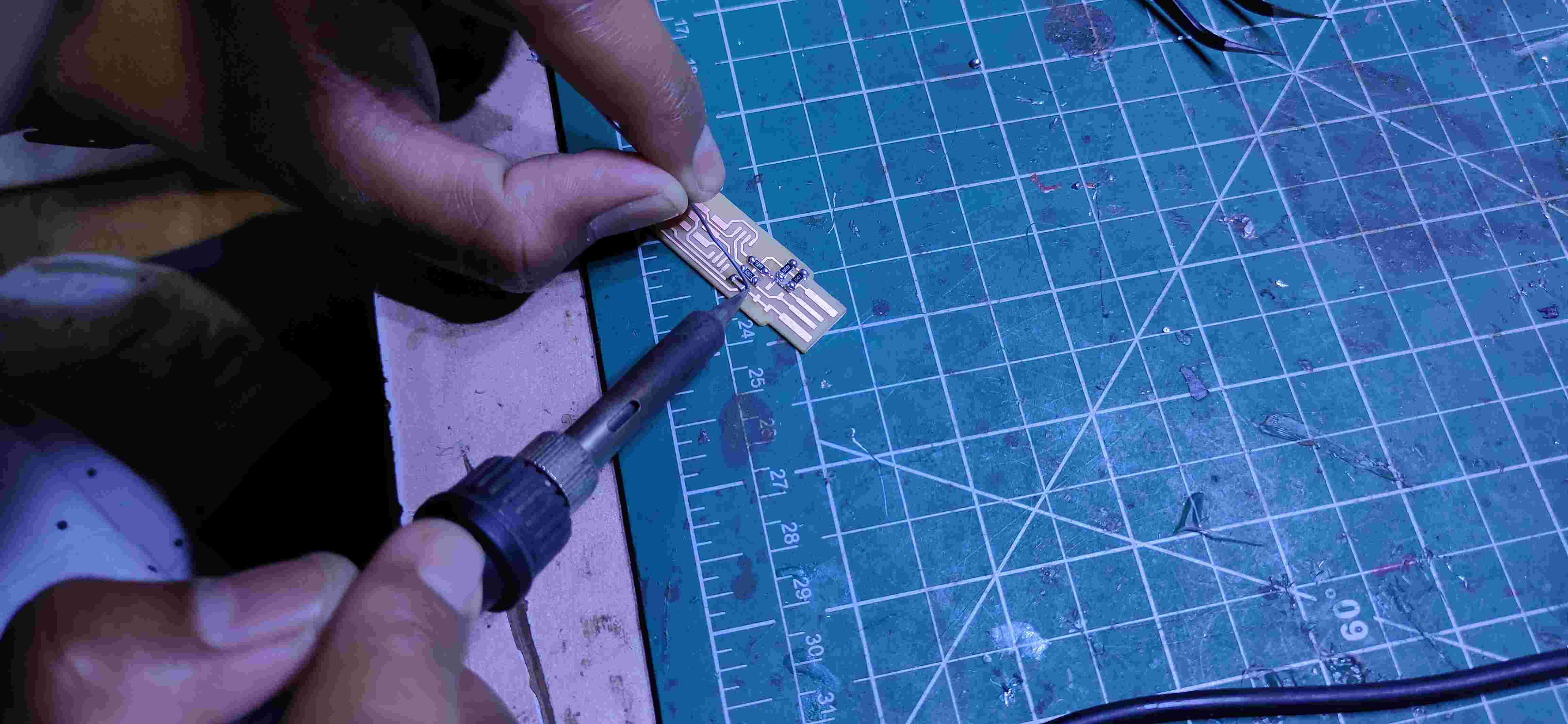
Checked Circuit
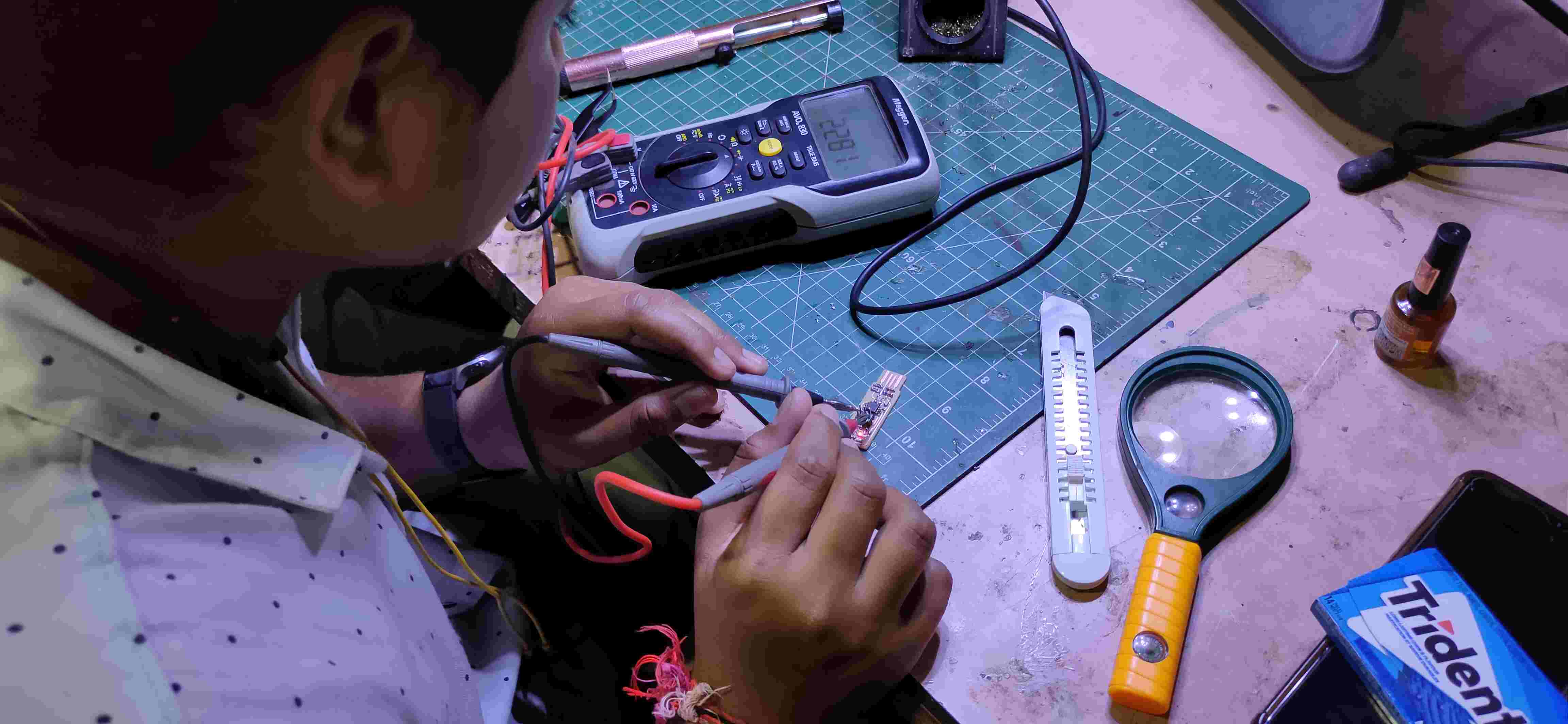
Finally Soldering Complaint
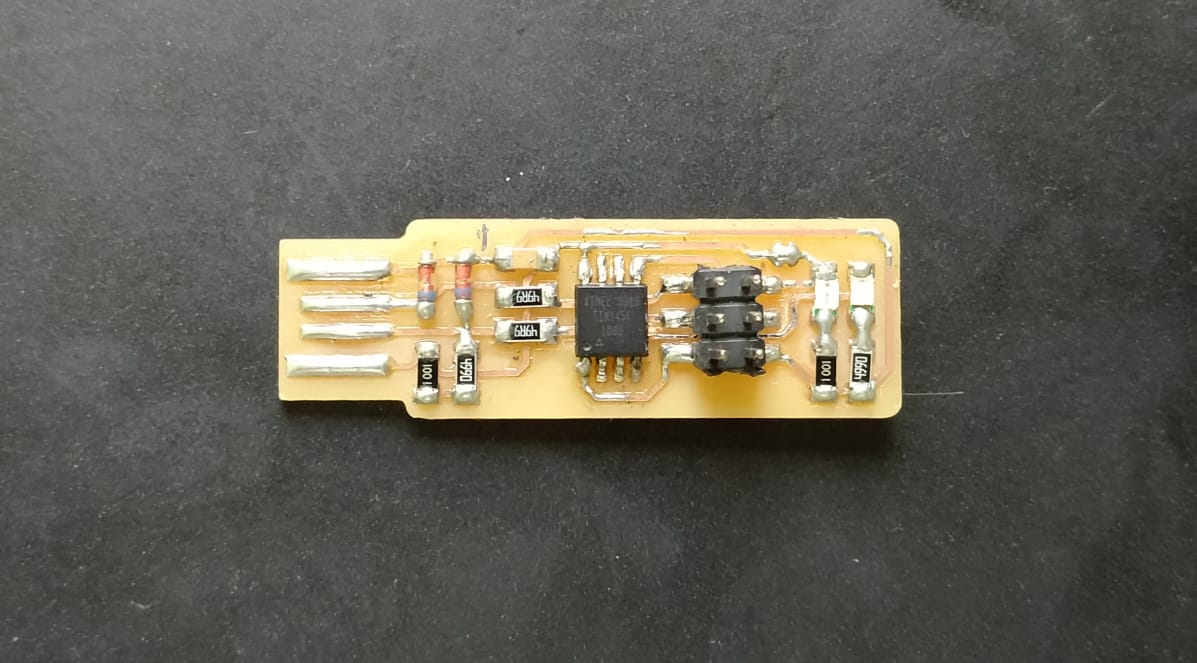
Installed GNU Make:
Updated Path:
Edited Path to add the below 3 values:
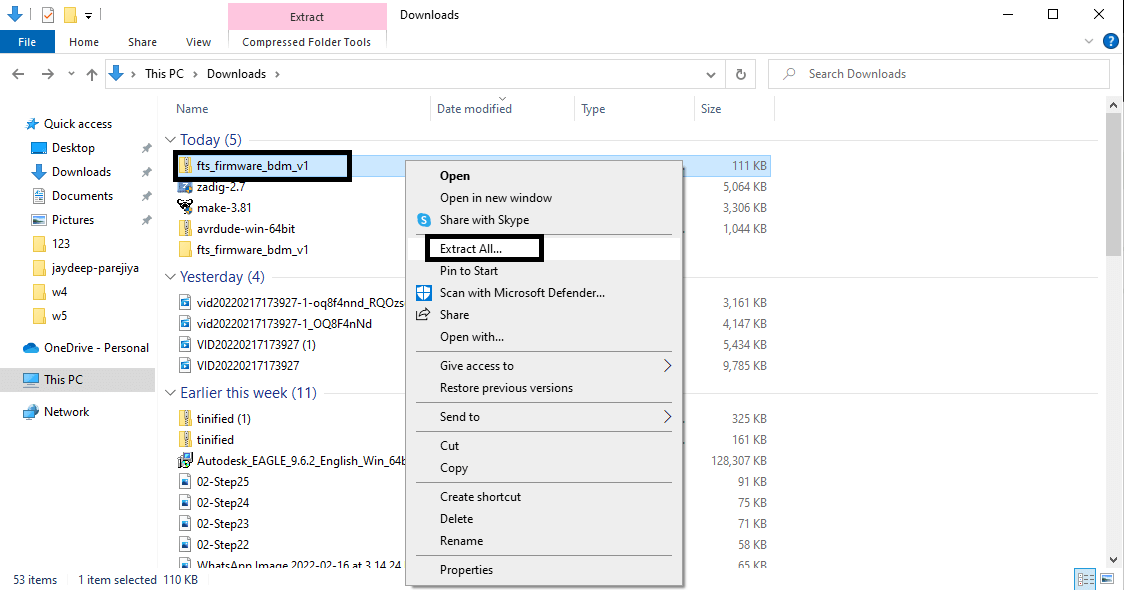
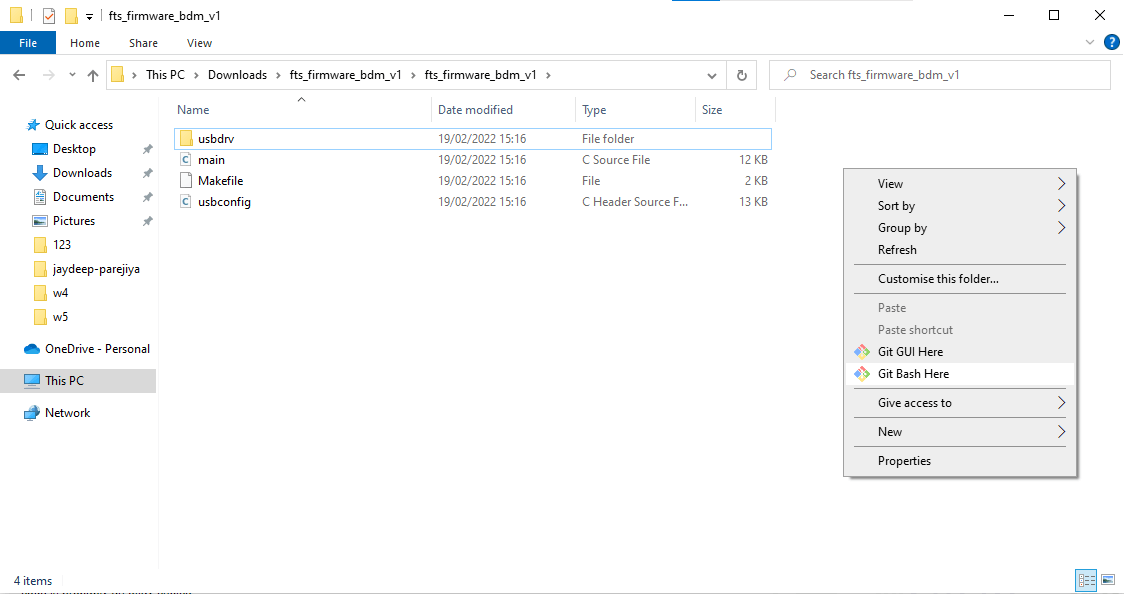
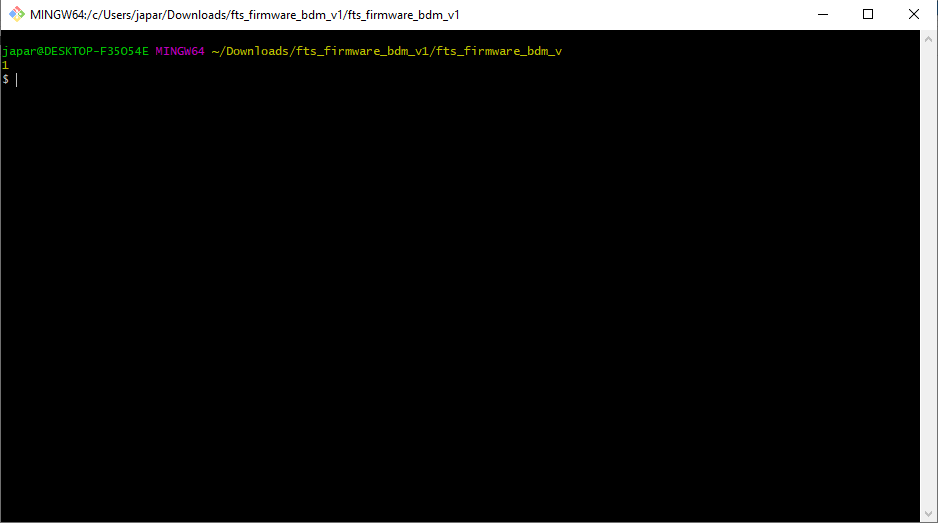
$ make
$ make flash
$ make fuses
$ make rstdisbl
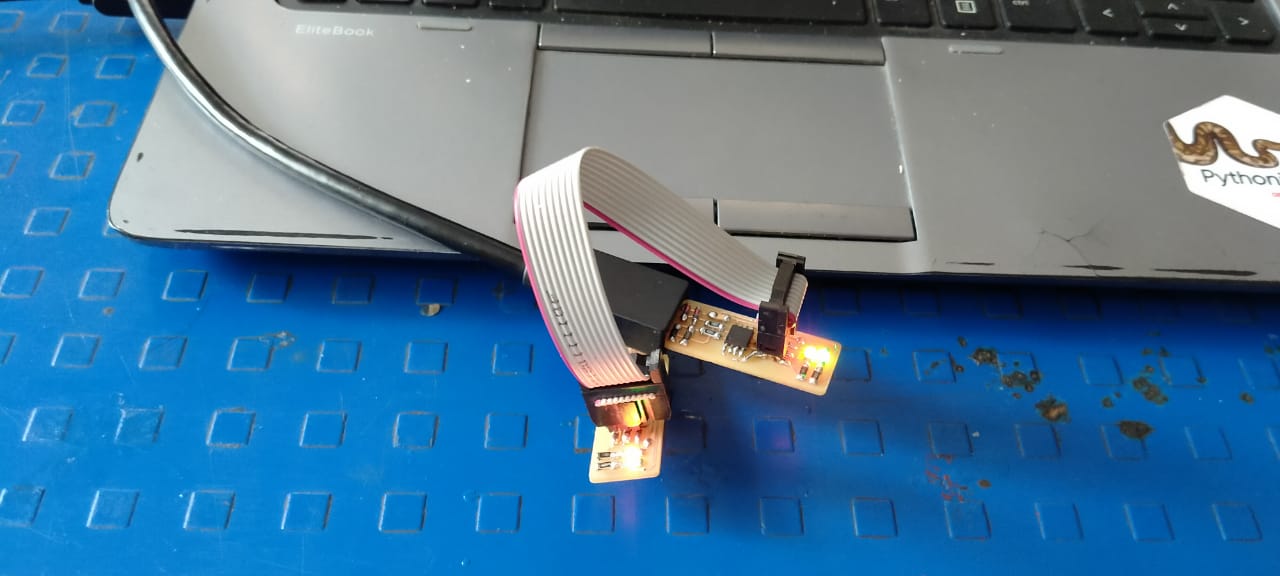
Download Source Code:
break 1/64 end mill
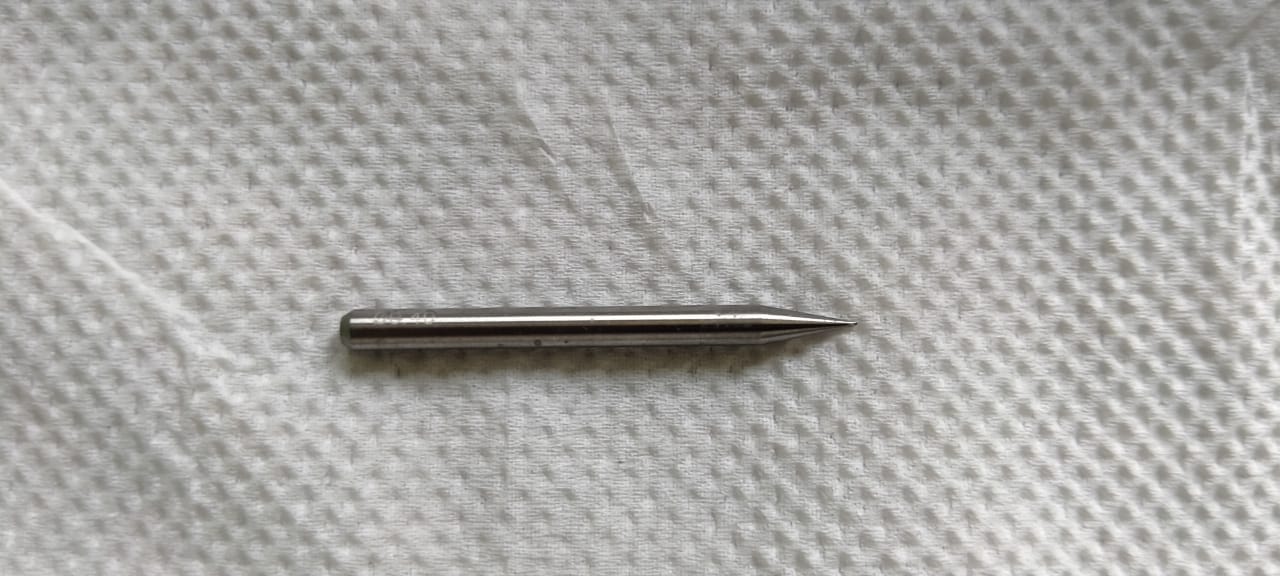
Refernces Link
Buildling the FabTinyISP by BrianGNU AVR ToolChain on Windows 10
Atmel ToolChain Download
« Computer Controlled Cutting | Week 04 3D Scanning and Printing | Week 06 »
Safety Switch by Parejiya Jaydeep is licensed under CC BY-ND 4.0