A section view of
the bottom support of the rotation axis, with the bearing, the
brass rod and the acrylic pipe. To design this I use the
parameters mentioned above, if I need to change a component, or
put some tolerances I don´t have to redraw nothing, just change
the EXPRESSION value of the parameters I already use.
A section view of
the solar cell support that will be 3D printed.
In every stage of the model, If you
need to change something, with parametrics and constraints is
much more easy than other softwares.
Cheking the base
3D model in Slicer, this software convert your 3D models into
different forms of construction techniques, in this case we
use the Interlocked Slices because I want to make it with
corrugated cardboard.
I want to fit
this components into the base, so here I made some drawings
in the image to show it to Paulina so I can explain better
my idea and wich components to fit in.
A drawing
direct into the slicer image to indicate where I need the
space to fit those components.
investigation
a place to re-connect
position of the
sun
Path of the sun
here in the Universidad Anáhuac México
Different methods
to choose the right angle to set up your solar panels
path of the sun
in summer and during winter
the incline I
choose for my panels is 16.9º
this is a table
with the altitude and azimuth of the sun in its path right
above the University
I made this to
visualize the path of the sun mention in the above table, with
this I be able to define the position of the solar cells and
time spending in that position during the day, the next day,
at 6:30 AM they return to the initial position
IHere we can see
the recomended high of the leds and angle of light of public
luminairies
I choose the 5vcc
and 160mA for the project, because of the batteies and the
servo
The connection of
the solar panels should be in paralel to maintain the Voltage
of 5V but sum de Amp, in this case 160x4=640mA
production
a place to re-connect
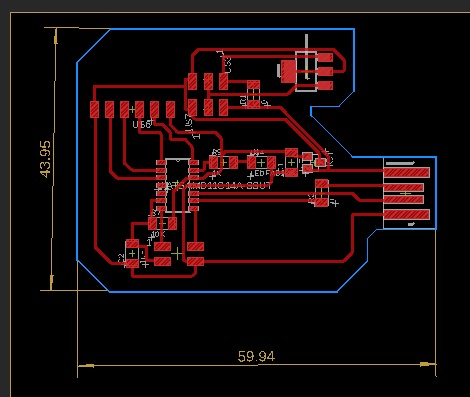
Image of the PCB
with components and traces ready to export it to a PNG image
My redesign of the
SAMDINO, the Hugodino, this PCB its the one who´s going to
control my project
PNG image of my SWD
PCB
PNG image of my LDR
PCB
Opening UBUNTU to
open MODS
Opening MODS
The PNG image of my
PCB, always import a PNG image of the PCB and of the outline if
need it
Here I´m about to
change the offset so I obtain better clearance between traces
Setting the offset
on 8
Setting the origin
to start milling
Settings on MODS
Putting some double
adhesive masking to the coper plate to stick it to the sacrifice
bed
The copper plate
stick to the sacrifice bed
The MODELA just
finish milling my SWD
All the components
that our PCBs need are here in little boxes
This PCB is for the
LDR and those are the components I need to put on it
The list of the
components I will weld at my Hugodino board
My SWD board
previously to start welding the components
A shot of the SWD
finish, with this I will program my Hugodino board
The leafs covers in
Autocad, this drawing is in a DWG format. Here I´m choosing the
color of the layer so the laser machine knows if it is a cut or
just engrave.
This is the setting
panel of the laser machine, here we put the size, the proporties
and the scale
The custom
properties initial panel
Here I´m going to
select the material that I´m about to cut, in this case is
"cartulina ilustración" or ilustration board.
This must match the
layer color I choose in order to cut or engrave, in this case
the red color will cut with a 75mm speed and a 35 of power
settings
Laser machine
display, here we can see the name of the archive display and we
can select different functions like level up or down the
material in order to had the right separation between the laser
nozzle and the material.
My pieces already
cut, it is recomend to put some paper below the cardboard to
protect the downside face of our pieces.
the "Z" pieces that
fit in the base, al the pieces has a "code" number so you know
in wich place they fit.
More cardboard
pieces
Te base almost
finish with the cardboard pieces
All the pieces
of double corrugated cardboard that forms the base in
place
once you have your
object ready to print, export it in .STL format, so you can
import it to the 3D printing machine software without problem.
Sample of one
object imported.
When in Advance
settings, first, be sure to choose the right material, in this
case could be ABS or PLA, then you can set up the support, the
layer thickness, the speed in general or for the outside or
inside face of your object.
If you need to
rotate the object into a better position to fit better the print
process you can do it with the rotation menu in X, Y or Z Axis
and you can dcecide the angle need it and then you can click the
Stick object to bed to be sure it is in the right position.
The Gcode is
already export and in this screen you can se the printing layers
with the slide that you can find at the right of the screen, the
one who has the 223 number, you can go up or down.
Here you can see
that is printing the support that atache the object to the bed
of the machine, over this will start to print your final piece
Once printing just
wait and from time to time just check if everything is fine.
Cardboard leafs and
the perimeters printed in 3D some in ABS and others in PLA. I
did this to check settings, printing time, texture and quality.
The axis of
rotation and the solar cells support printed in 3D
electronics
a place to re-connect