Week 17 - Applications and Implications, Project Development
Assignment
Propose a final project masterpiece that integrates the range of units covered.
Your project should incorporate:
2D and 3D design
Additive and subtractive fabrication processes
Electronics design and production
Embedded microcontroller interfacing and programming
System integration and packaging.
Where possible, you should make rather than buy the parts of your project.
Projects can be separate or joint, but need to show individual mastery of the skills, and be independently operable.
See Final Project Requirements for a complete list of requirements you must fulfil.
Project: Bionic Hand
What will it do?
My project is a bionic hand that replicates human finger motion using servo motors. Currently, the control input is based on flexible resistive sensors worn on a glove, which change resistance when fingers bend. These resistance values are read by a microcontroller and wirelessly sent to another microcontroller that controls servos on the hand.
Originally, EMG sensors were intended for control, but due to poor signal quality in the first set, they were replaced with flexible sensors. A future integration with more reliable EMG sensors is planned to enhance physiological control.
Who has done what beforehand?
Projects like Motorized Bionic Hand and InMoov, and other DIY bionic hands have used Arduino boards, servo motors, and EMG signals to control hand movement. Most combine signal processing and actuation on a single board.
In my project, I chose to design two custom PCBs—one for reading signals from flexible resistors and one for servo control. This modular approach helps me better understand each part of the system and makes future upgrades, like EMG integration, easier without always reopening the hand setup. I also use ESP32 boards for wireless communication between the glove and the hand.
What will you design?
Enclosure
- Arm-mounted sensor case
- Palm and finger structure of the hand
Electronics
- Custom PCBs for signal acquisition and servo control
- Power distribution system for battery and voltage regulation
Mechanical
- Articulated 3D printed fingers
- Servo mounts and tendon routing system
What materials and components will be used?
Item & Description | Quantity | Price/Unit | Source | Notes |
---|---|---|---|---|
ESP32 wroom microcontroller | 2 | Frw 8,000 | https://nyerekatech.com/shop/esp-32s-esp-wroom-32/ | One for EMG sensors, one for servo control on the fingers |
Servo motors | 5 | Frw 3,800 | https://nyerekatech.com/shop/sg90-9g-mini-micro-servo-motor/ | One for each finger |
3D Printing Filament (PLA) | 1 | Frw 50,000 | https://nyerekatech.com/shop/light-blue-pla-filament-1-75mm-1kg-roll-for-3d-printer/ | For printing the hand and enclosure |
Lepo Battery | 1 | Frw 10,000 | https://nyerekatech.com/shop/3-7v-dtp-654065-lipo-battery-2000mah-rechargeable-battery/ | Powers the EMG sensor in the arm case |
5V 2A Power Supply | 1 | Frw 5,000 | https://nyerekatech.com/shop/5v-3a-dc-power-supply-220v-ac/ | Powers the servo motors with a 5v |
Plastic Cord (Fishing Line) | 2 | Frw 2,000 | Connecting finger tips to servo motors and tendon | |
Xiao ESP32-C3 | 1 | Frw 20,000 | https://www.nyerekatech.com/shop/seeed-studio-xiao-esp32c3/ | Controlling flexible resistor on mounted on the glove |
Glove | 1 | Frw 5,000 | To help attach the flexible resistor properly | |
Flexible Resistors | 5 | Frw 20,000 | To help Determine the finger movements |
What parts and systems will be made?
- 3D printed bionic hand, including palm and articulated fingers
- Sensor enclosure for arm-mounted EMG setup
- Custom PCB for EMG signal processing
- Control board (PCB) for servo control
- Power management system to control and supply both microcontrollers and servos with power
What processes will be used?
- CAD for mechanical design (SolidWorks)
- 3D printing
- PCB design and milling
- Soldering and circuit assembly
- Embedded programming (Arduino IDE)
- Wireless communication between microcontrollers(ESP-NOW)
What questions need to be answered?
- Can the microcontrollers reliably communicate fast enough for responsive finger motion?
- Can the flexible sensors reliably detect each finger's movement?
- Can future EMG sensors be easily integrated into the current system?
- How to minimize power consumption while maintaining functionality?
What problems need to be solved?
- Calibrating resistance values to servo movement angles
- Smooth and proportional control of servo motors
- Improving mechanical durability of finger joints
- Efficient use of battery power for extended usage
How will it be evaluated?
The bionic hand should:
- Respond in real time to EMG signals
- Accurately move individual or grouped fingers
- Run for a reasonable duration on battery power
What tasks still need to be completed?
- Finalize CAD design for arm enclosure
- Integrate EMG sensor with microcontroller
- Design and build the power management system
- Calibrate and fine-tune servo response to flexible resistor
- Conduct user testing and evaluations
What has worked?
- 3D printed finger prototypes with tendon actuation
- Basic communication between ESP32 modules
- Flexible sensors controlling finger servos
What has not worked yet?
- Reliable EMG sensor input (awaiting replacement sensors)
- Stabilization of signal for real-time movement
What have you learned?
- Practical use of CAD and digital fabrication to match human anatomy
- Designing reliable circuits using custom PCBs
- Real-time wireless data communication using ESP-NOW
- Substituting sensor types while maintaining system architecture
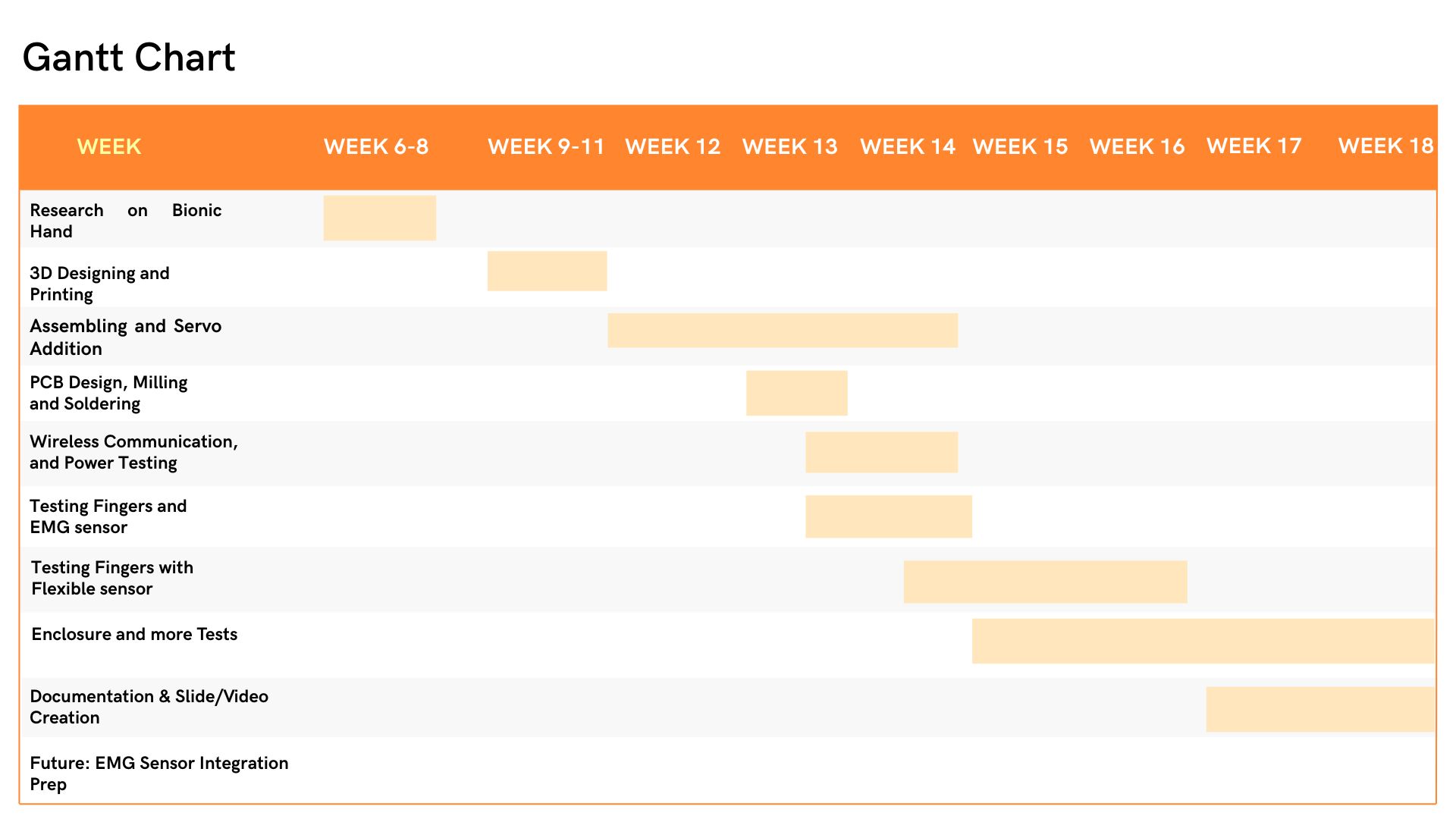
This content was paraphrased and refined using Grammarly AI.