Week 10: Machine Design
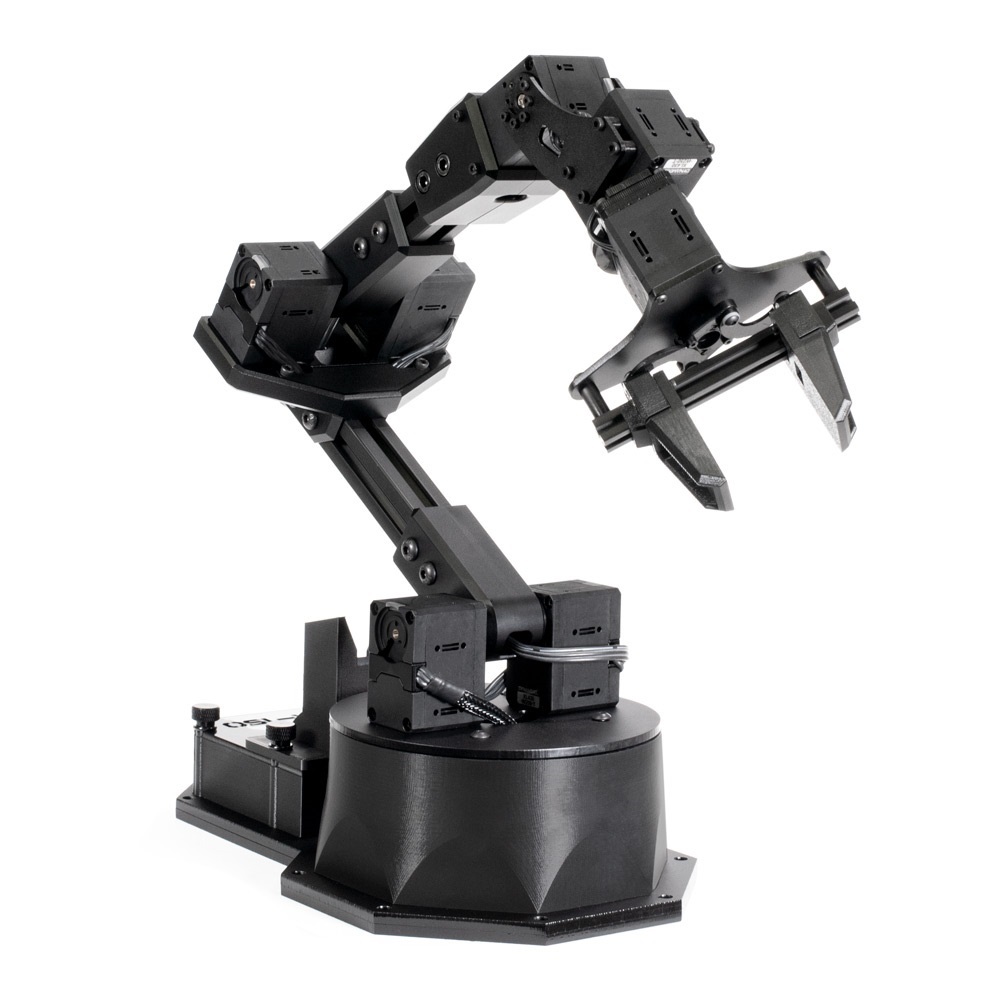
Group Assignment
- Design a machine that includes mechanism + actuation + automation + application
- Build the mechanical parts and operate it manually.
- Document the group project
- Actuate and automate your machine.
- Document the group project
Individual Assignment
- Document your individual contribution.
WEEK 11 WORK ORGANIZATION
Group Assignment
This week group assignment was to design and make machine. our group i made by 9 participants and we have selected two machine types : one is Arm robot and other one is laser cutter machine.the group work is documented on FabLab Rwanda web pageMy Contribution
My task was to make a study on needed stepper motor to be used for both cases , propose stepper motor available and make a stepper motor drive for both assignment.Selected Stepper Motors to be used
in FabLab Rwanda , we have only NEMA 17 and NEMA23 stepper motors and we have to adopt to use them in our assignment. so i had to explore them with all their characteristics before making their controllers or drivers
NEMA17 AND NEMA23 SPECIFICATIONS
NEMA 17 Stepper Motor Technical Specifications
Specification | Value |
---|---|
Holding torque | 40 N·cm |
Step angle | 1.8° |
Current per phase | 1.5 A |
Resistance per phase | 2.4 Ω |
Inductance per phase | 3.8 mH |
Detent torque | 2.2 N·cm |
Rotor inertia | 34 g·cm² |
Weight | 0.28 kg |
Length | 47 mm |
NEMA 23 Stepper Motor Technical Specifications
Specification | Value |
---|---|
Holding torque | 120 N·cm |
Step angle | 1.8° |
Current per phase | 2.8 A |
Resistance per phase | 0.9 Ω |
Inductance per phase | 2.5 mH |
Detent torque | 5.5 N·cm |
Rotor inertia | 480 g·cm² |
Weight | 1.2 kg |
Length | 76 mm |
From the laser design we did in solidworks , we decided to use TWO NEMA 23 ON X axis because the have used heavy MDF material without best fixing techniques which can cause mis-allignment in x-axix movement, so we decided to use two nema17 stepper motors on x-axis to be sycnhronized togather
Our Design
For Y axix , we decided to use NEMA17 becuse the laser Head is not heavier
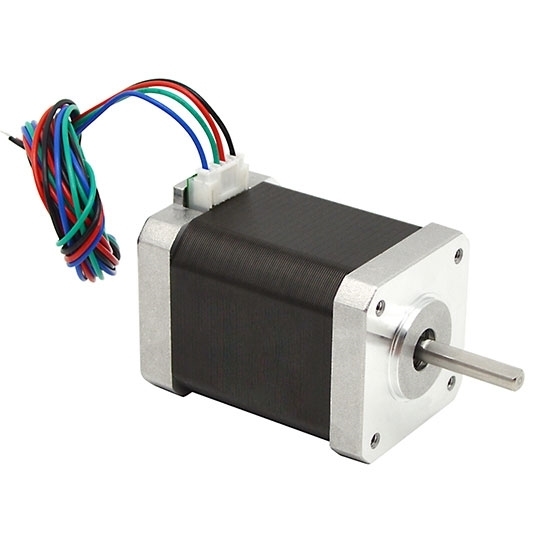
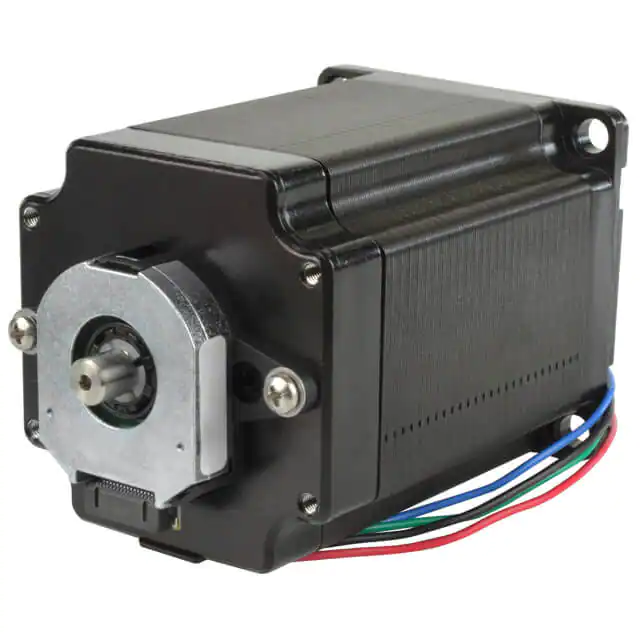
Design Stepper motor driver
I had to look around and find the available stepper motor driver chip mostly used and available to our local store and i found ony A4988 stepper motor driver and drv8824 driver . the following are their specifications
A4988 vs DRV8824 Stepper Motor Driver Comparison
Specification | A4988 ![]() |
DRV8824 ![]() |
---|---|---|
Maximum current | 2 A | 2.5 A |
Maximum microstep resolution | 1/16 | 1/32 |
Input voltage range | 8 - 35 V | 8.2 - 45 V |
Output voltage range | Same as input voltage | Same as input voltage |
Logic voltage | 5 V | 3.3 V or 5 V |
Number of stepper motors | 1 | 1 |
Thermal shutdown protection | Yes | Yes |
Over-current protection | Yes | Yes |
Adjustable current limiting | Yes | Yes |
Dimensions | 20 mm x 15.5 mm x 10 mm | 20 mm x 15.5 mm x 5.5 mm |
From the power perspective, both A4988 and drv8824 , produce current lower that 2.5 A where NMA 23 CONSUMES 2.7 a PER PAHSE. here we have used NEMA17 for A4988 because it is what we have .
for NEMA23 , we suggested the use of coomercial drivers like TB6600
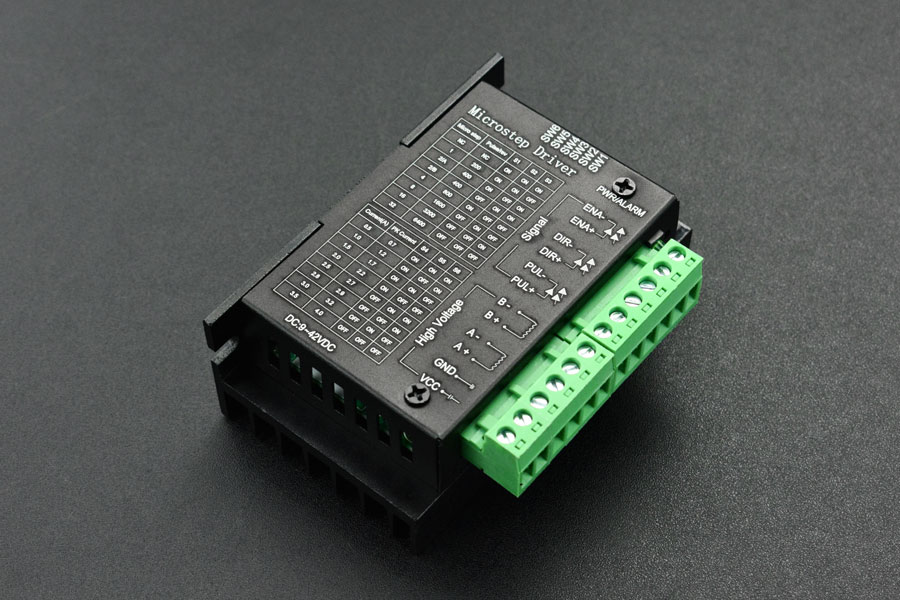
TB600 stepper motor specification
Parameter | Specification |
---|---|
Input Voltage | DC 9-40V |
Output Current | 0.2A - 5A |
Microstep Resolution | 1, 2, 4, 8, 16, 32 |
Pulse Frequency | 0-20kHz |
Overheat Protection | Yes |
Short Circuit Protection | Yes |
Dimensions | 96 x 56 x 33 mm |
This driver can provide up to 5A which is adequate current for our NEMA23 stepper driver
Microcontroller Connection For TB6600 STEPPER MOTOR DRIVER
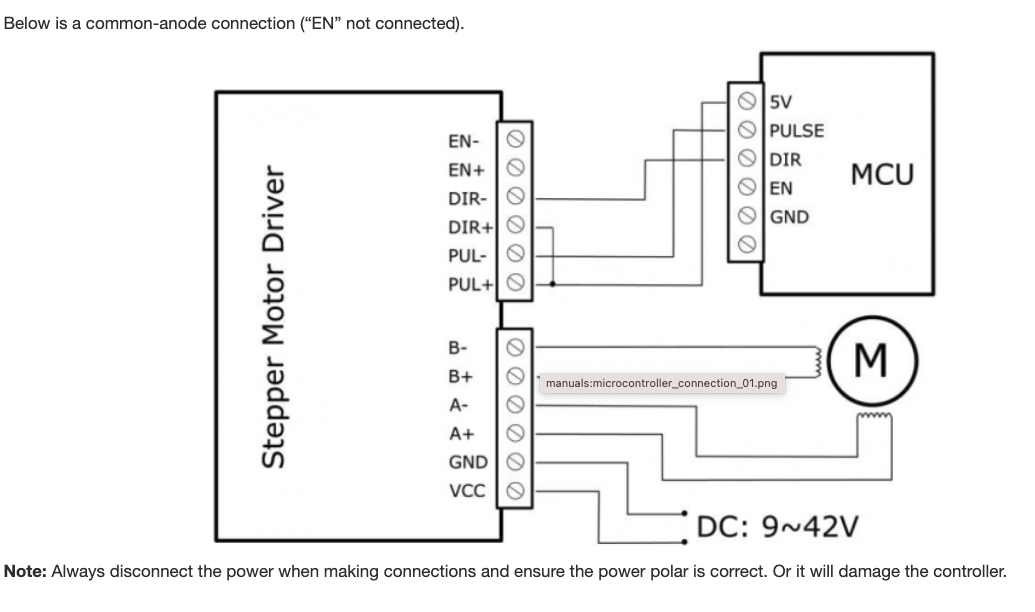
Team member working on different tasks
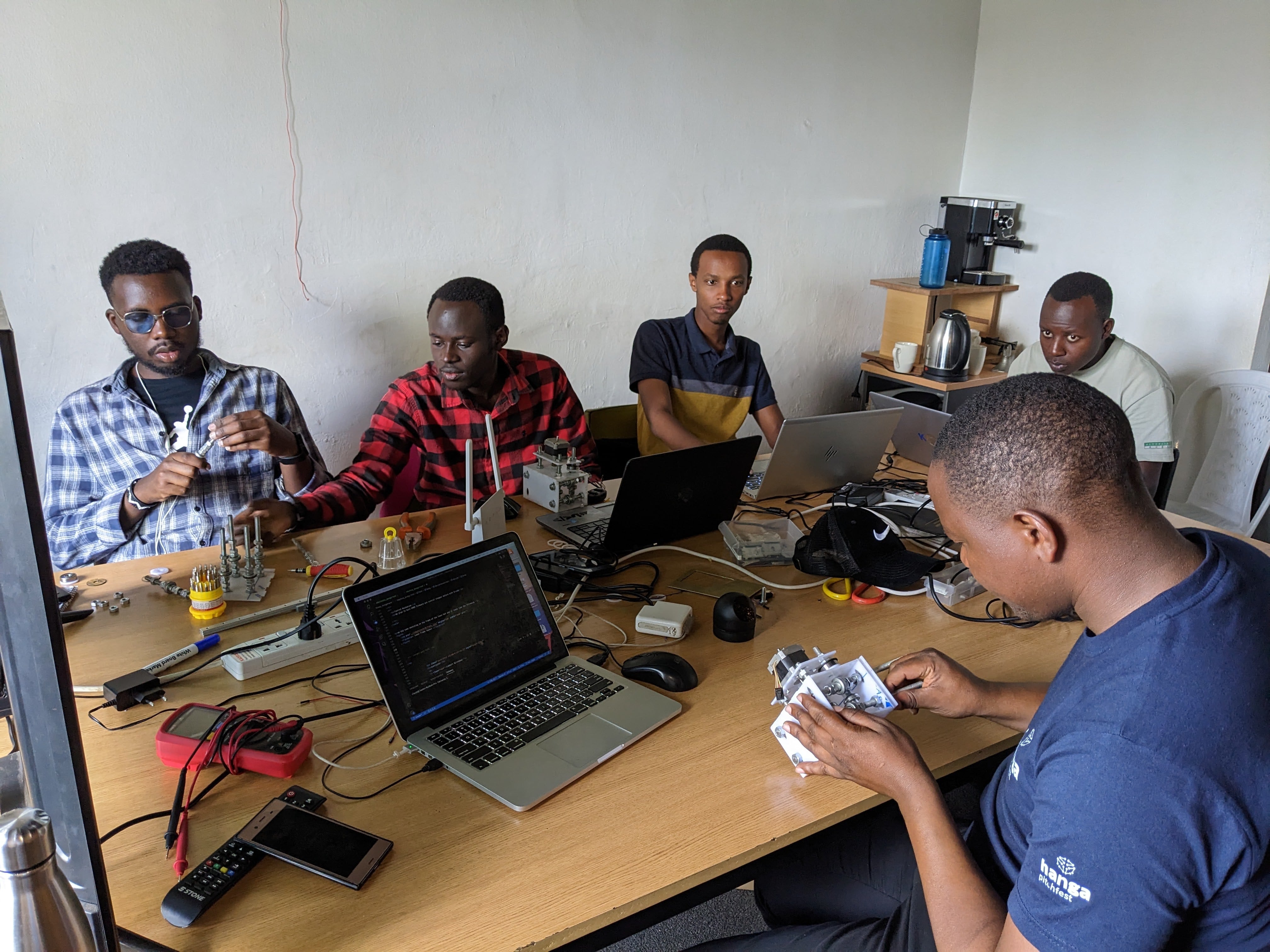
Designing Motor Controller for Our Arm robot
The arm robot will use only NEMA17 stepper motors so i had to desifn the driver board based on A4988 DRIVER in order to controll the robot movement
Making of Stepper Motor control Board
To be able to control stepper motors, motor control board is needed . we made a control board based on A4988 stepper motor drive BOARD
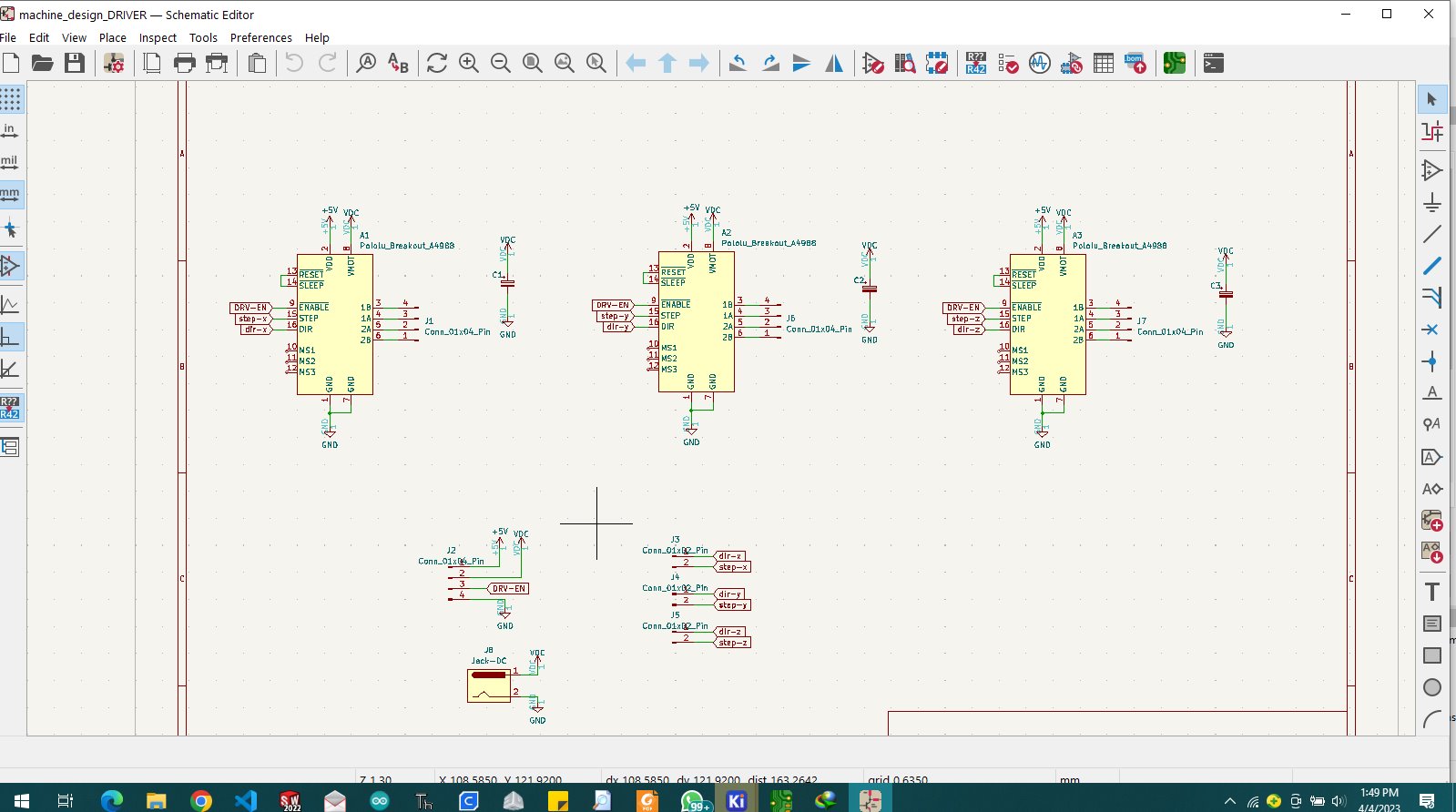
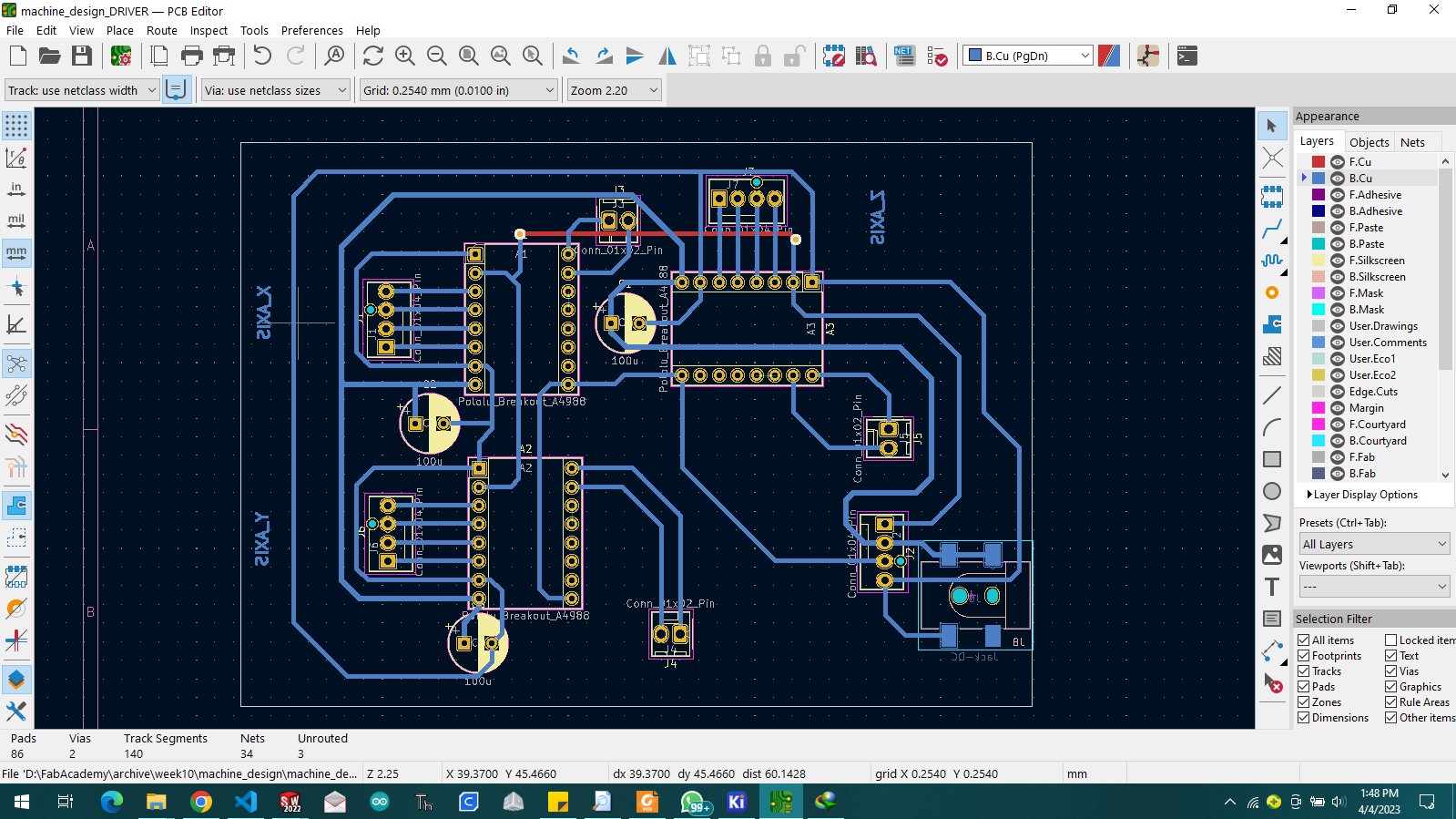
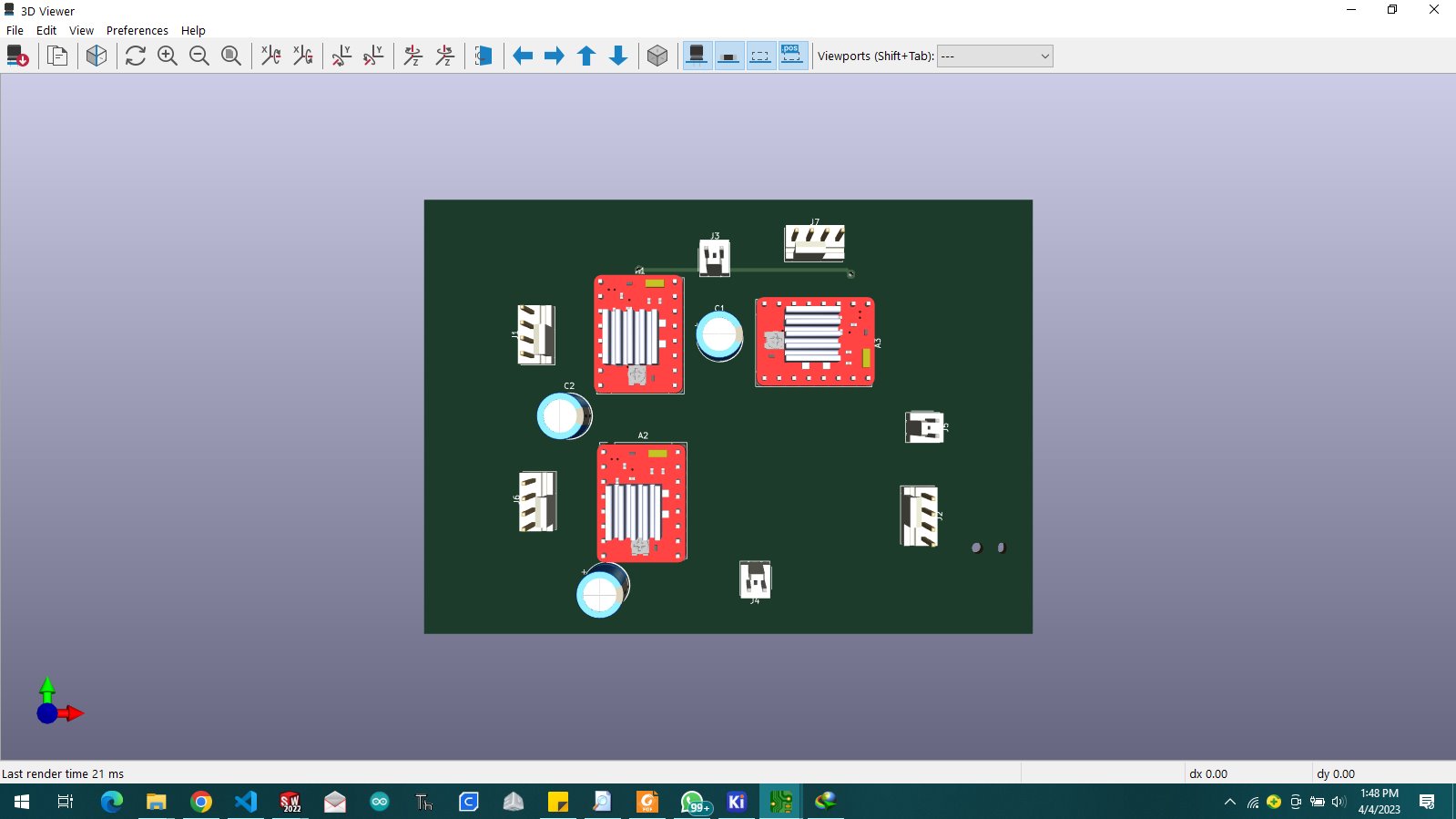
Testing the Soldered stepper Motor Driver on NEMA17 Stepper motors
we have flashed GRBL Firware in Atmega328 mcu we send g-code from PC to the MCU and the stepper motor starts providing the current to the motors