Week 12: Molding and Casting
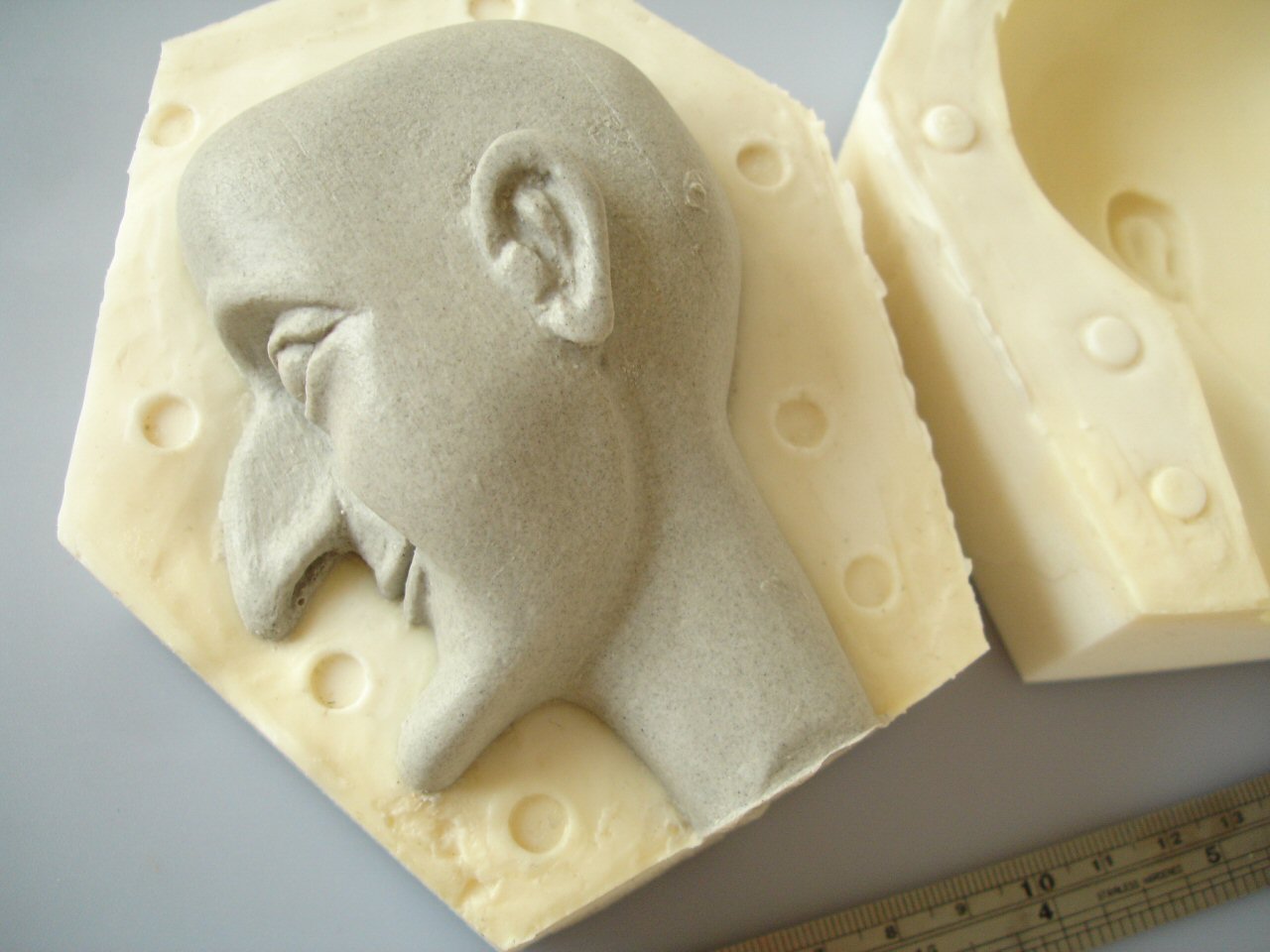
Group Assignment
- Review the safety data sheets for each of your molding and casting materials
- Make and compare test casts with each of them
Individual Assignment
- Design a mold around the stock and tooling that you’ll be using, mill it (rough cut + (at least) three-axis finish cut), and use it to cast parts.
WEEK 13 WORK ORGANIZATION
Group Assignments
Designing a Mold
my thinking was around to make a something that can be a layout of a given watch or smart watch. i want to make a smartwatch in the future the reason why i designed a part that looks like a watch
The design process was done using solidworks
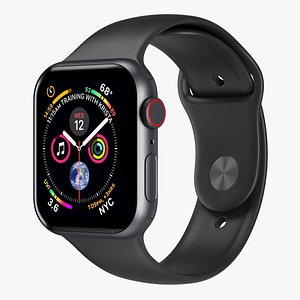
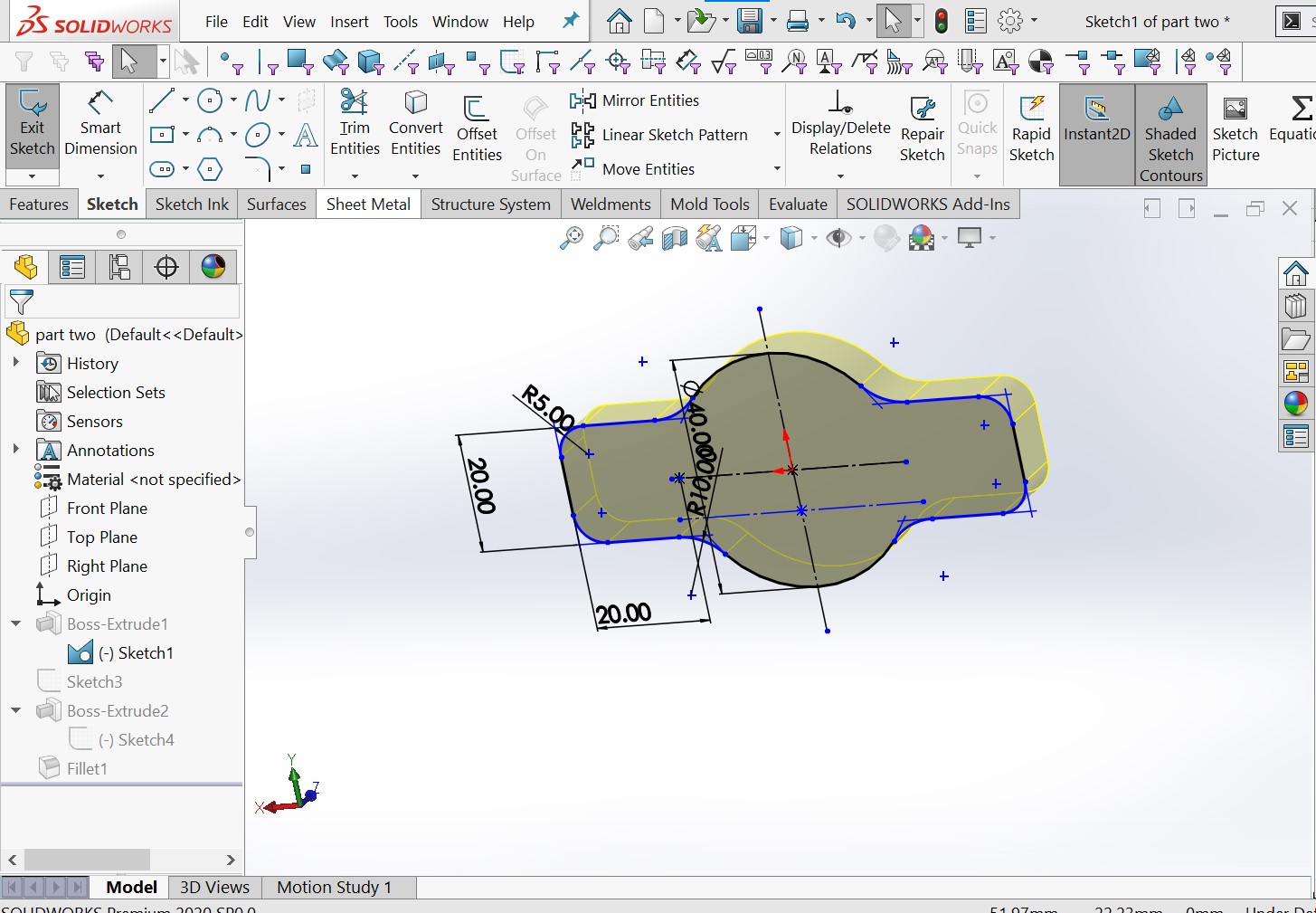
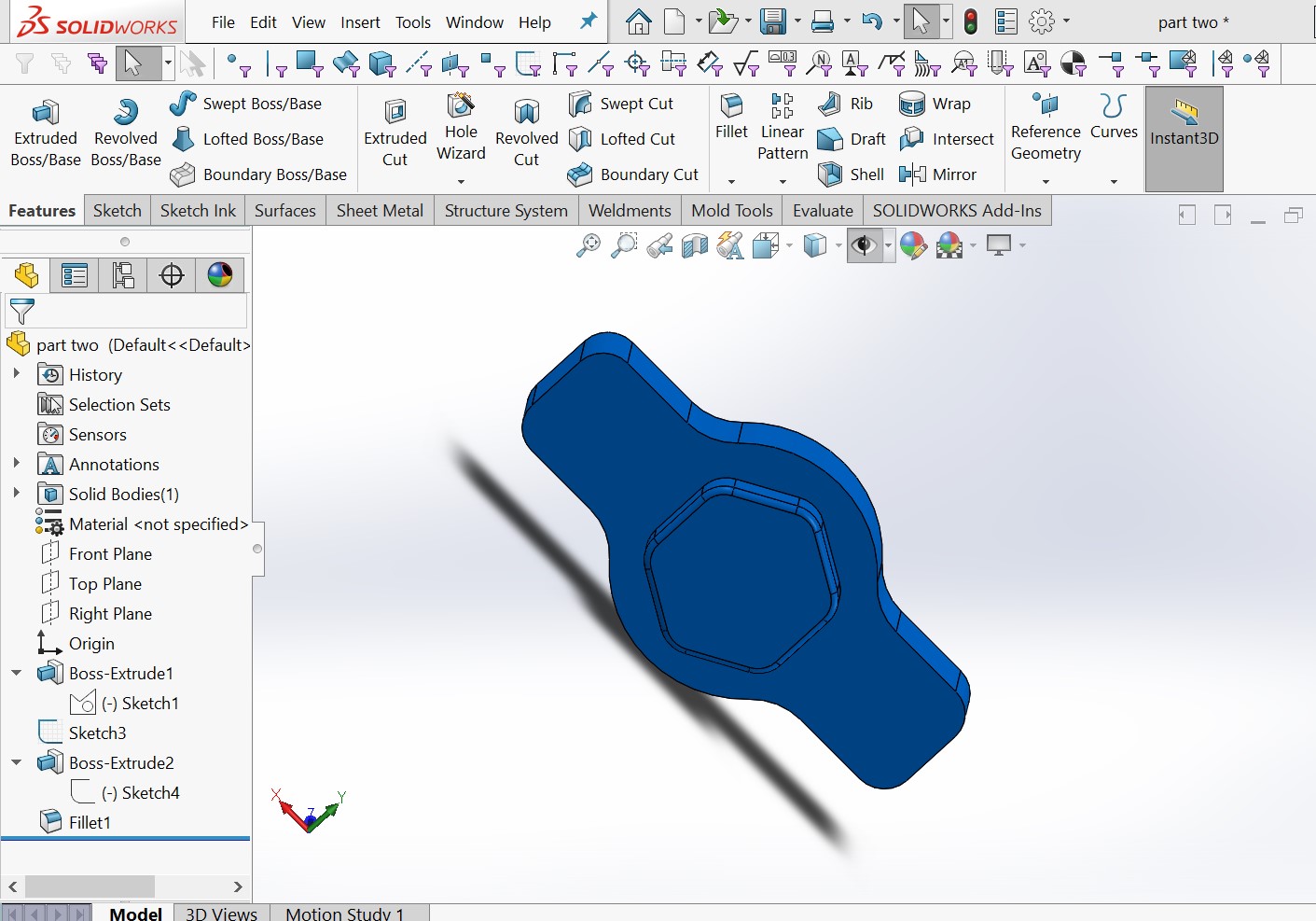
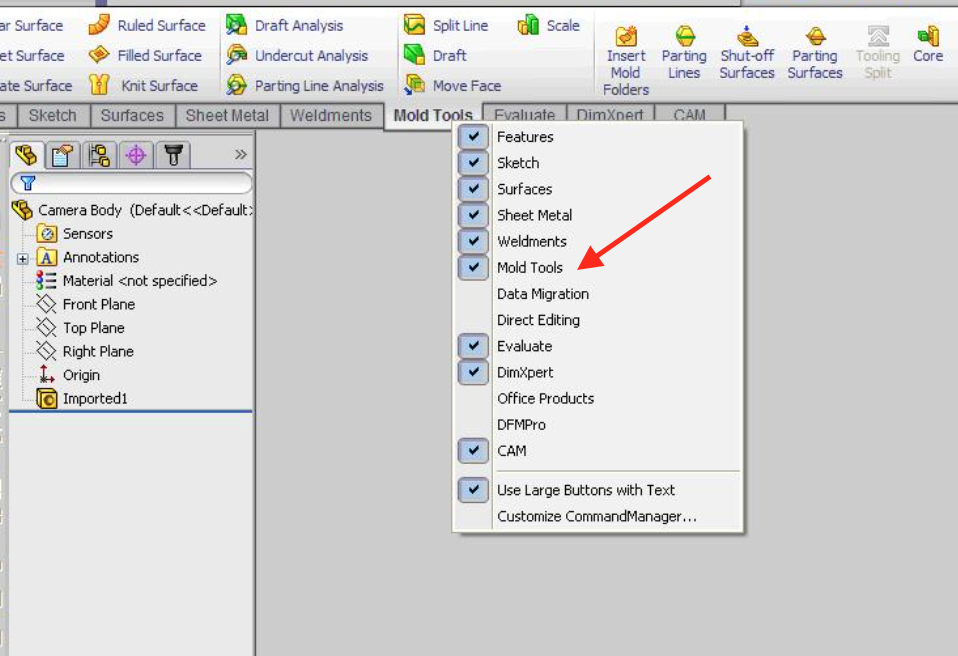
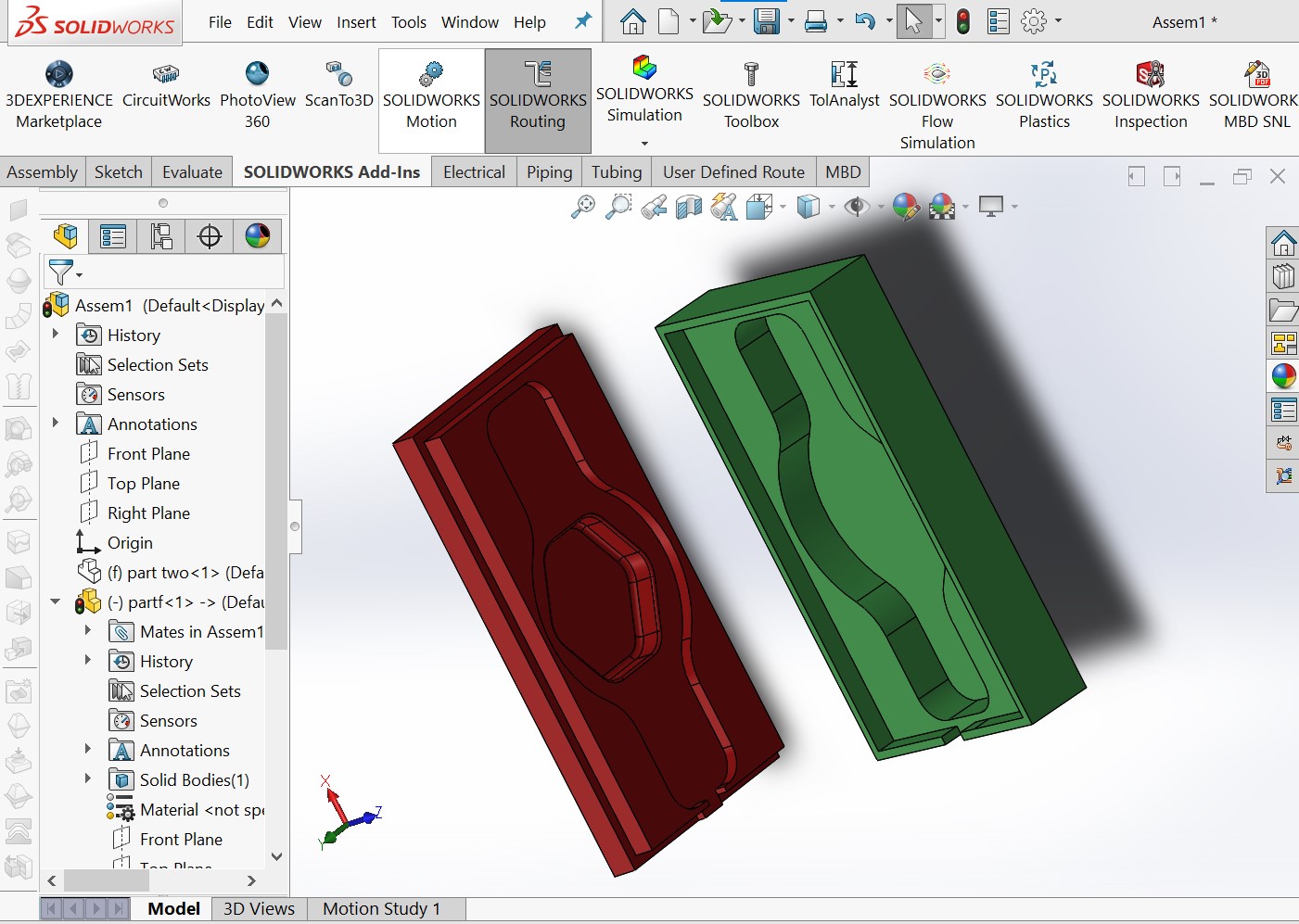
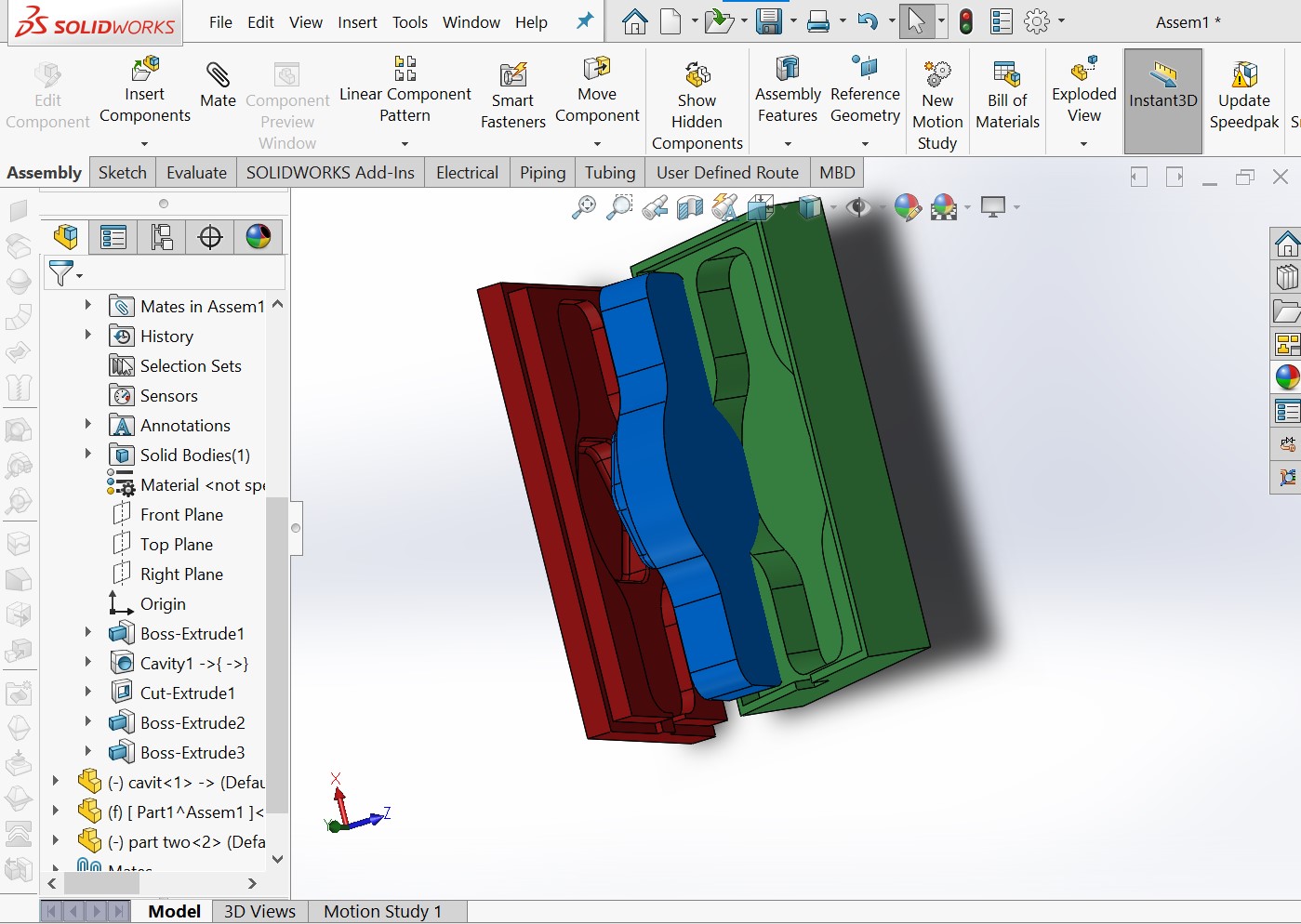
EXport mold design in Vcarve pro before Milling Process with CNC
After design i have to mill the mold with cnc router and i have used vcarve pro software to create toolpath
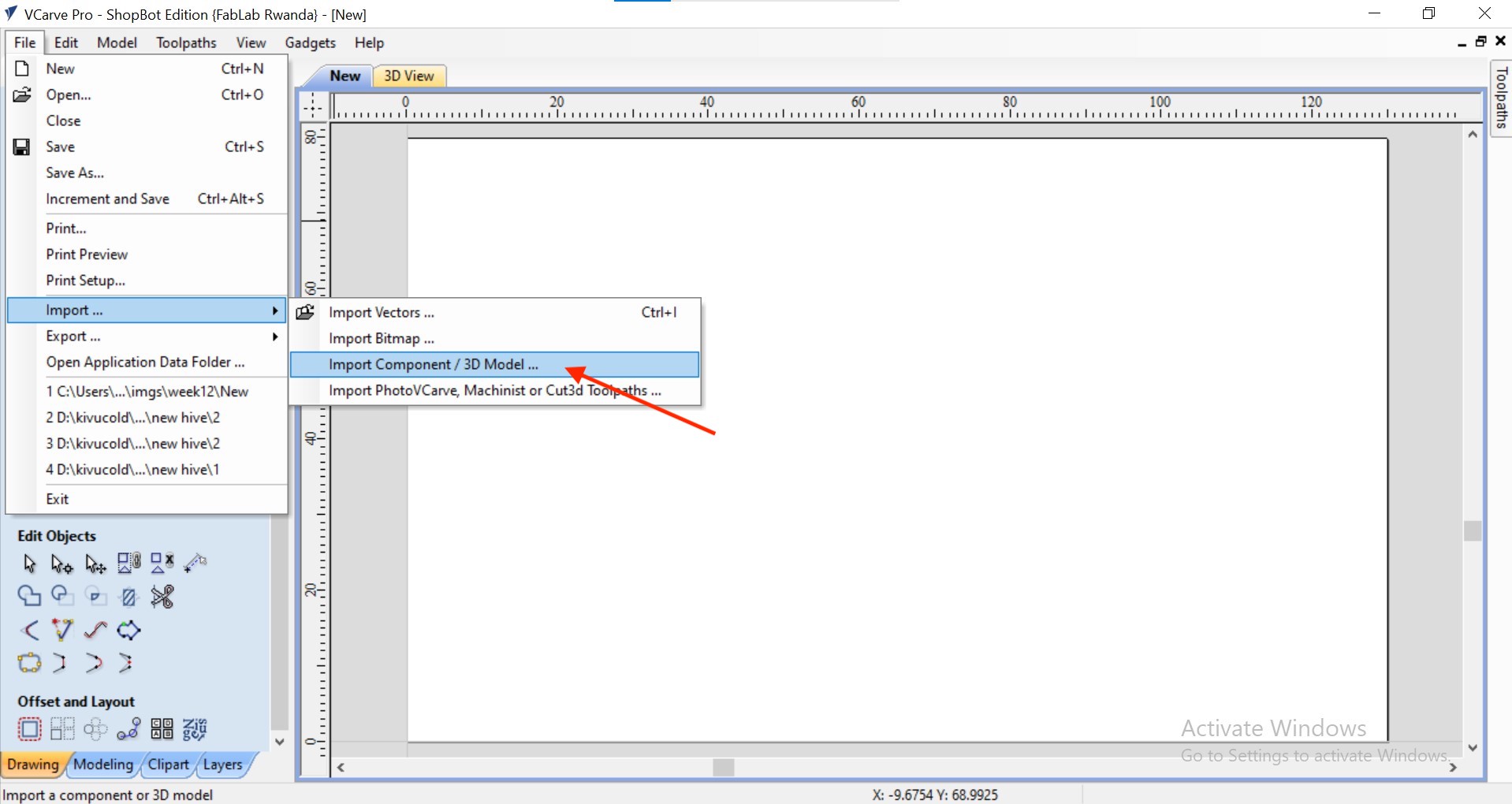
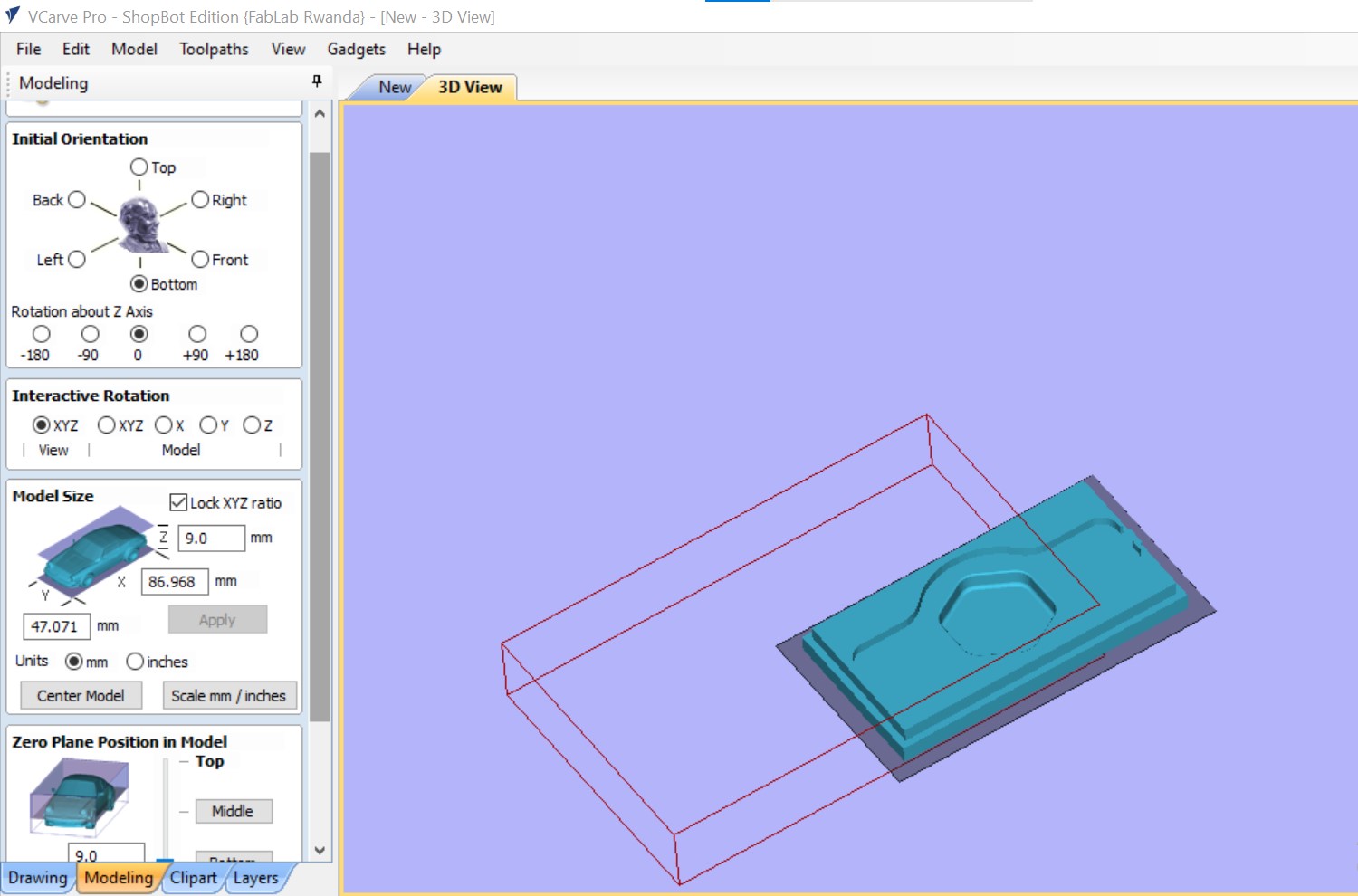
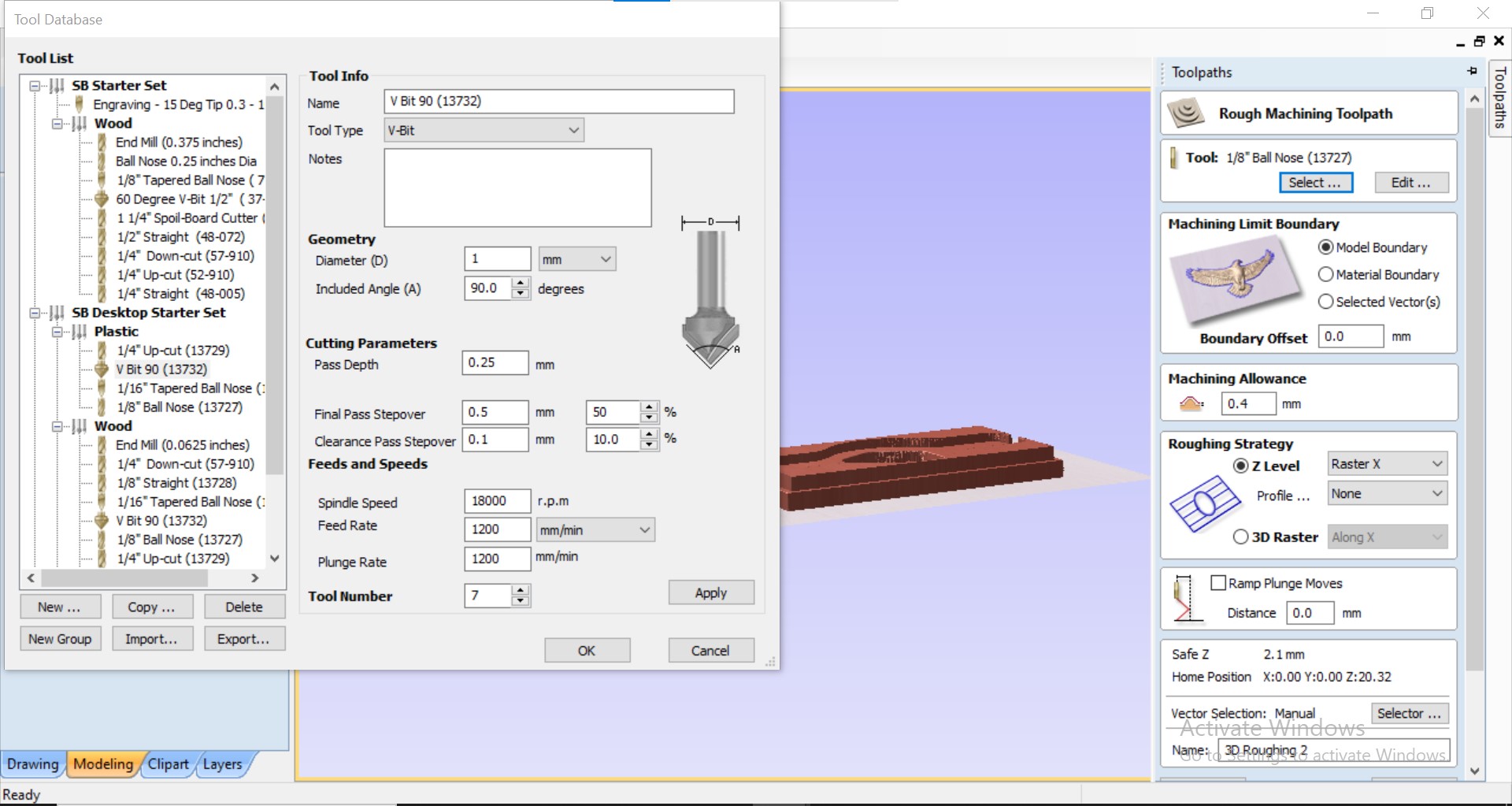
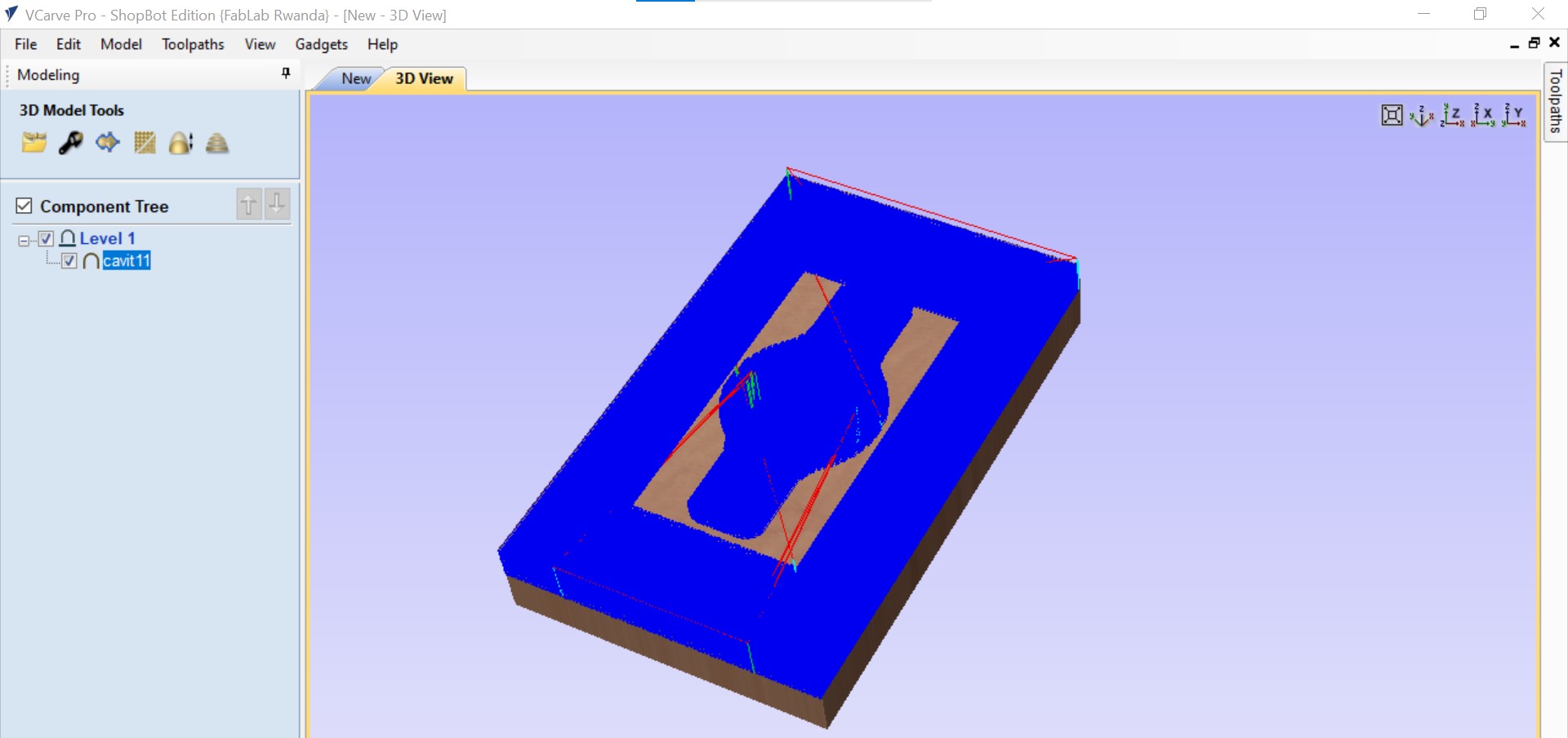
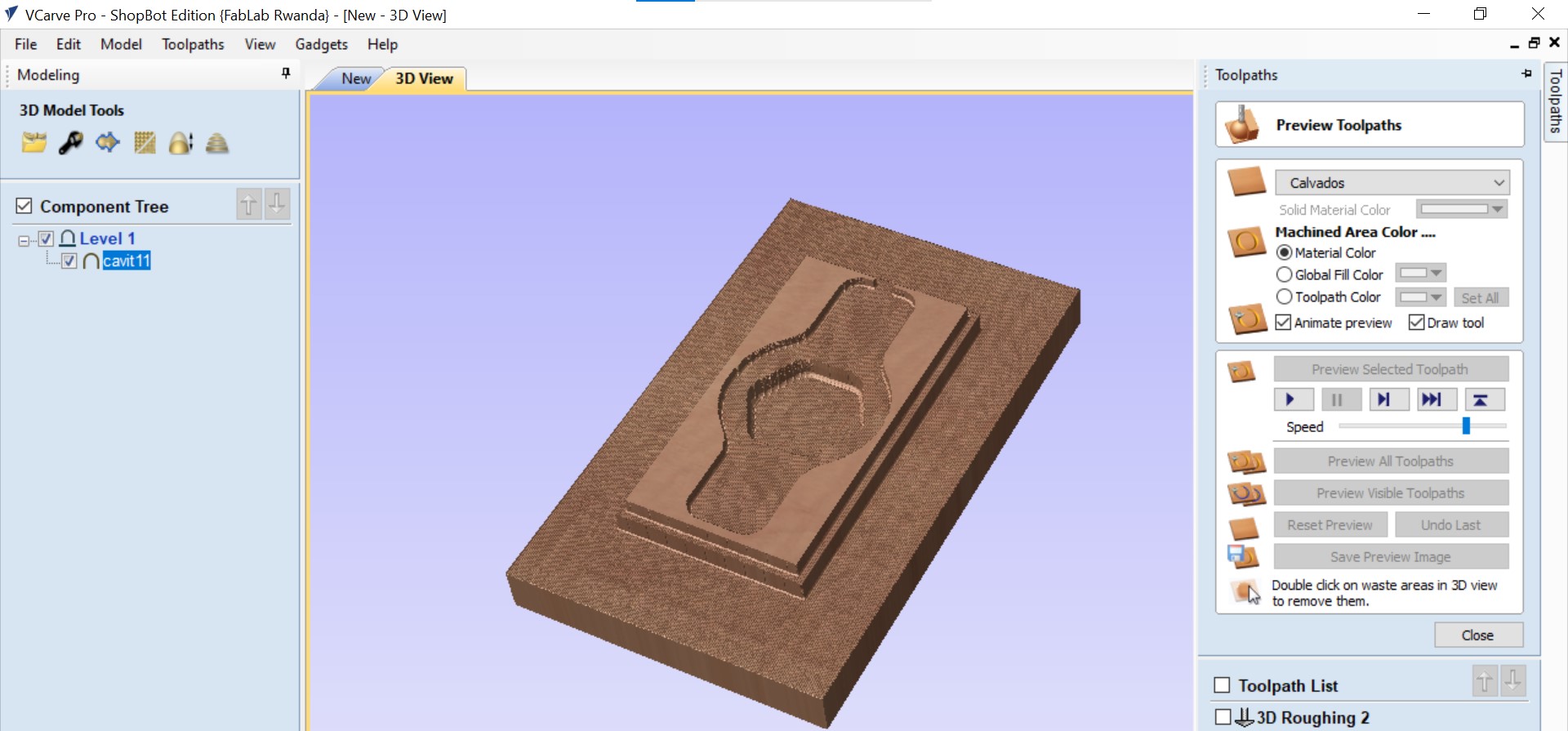
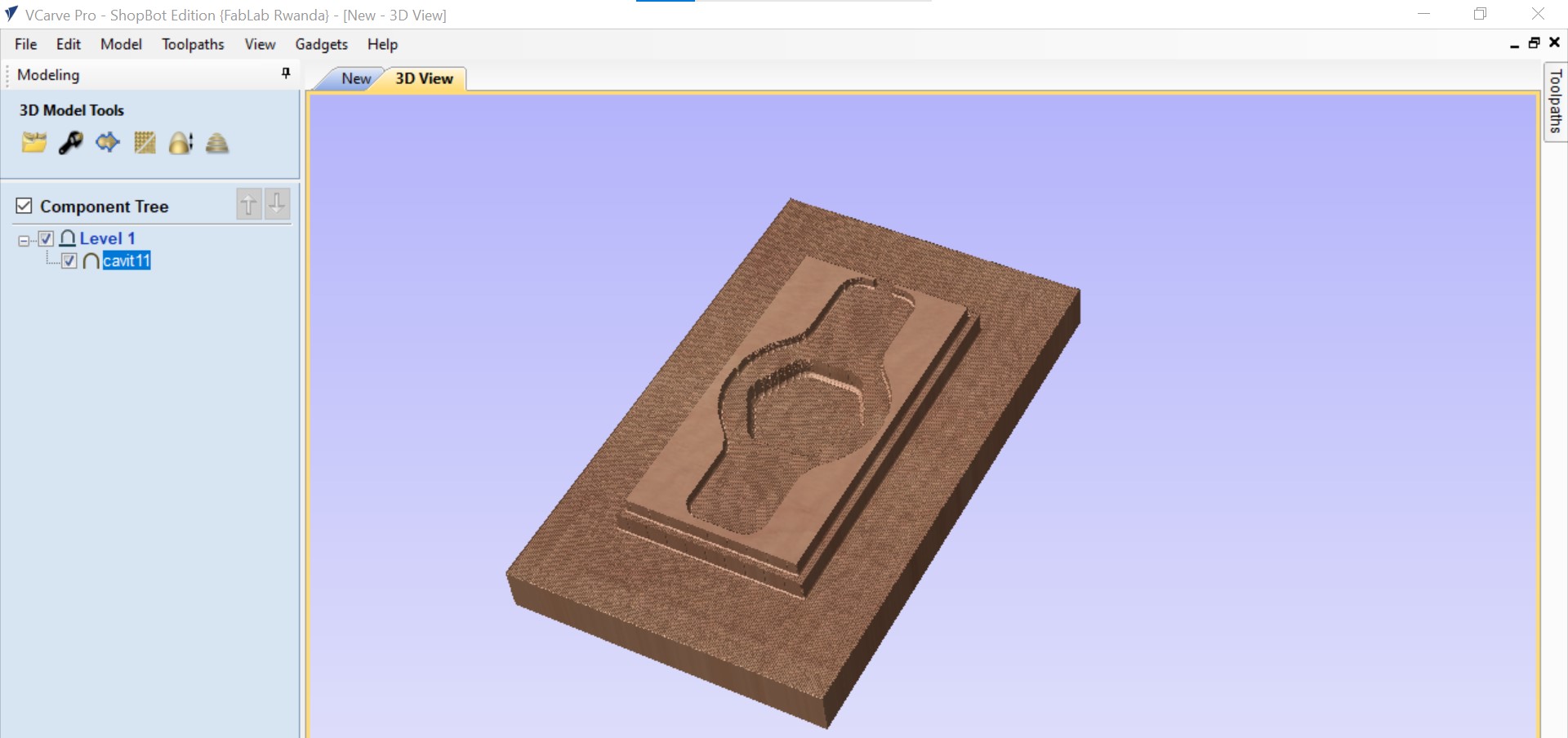
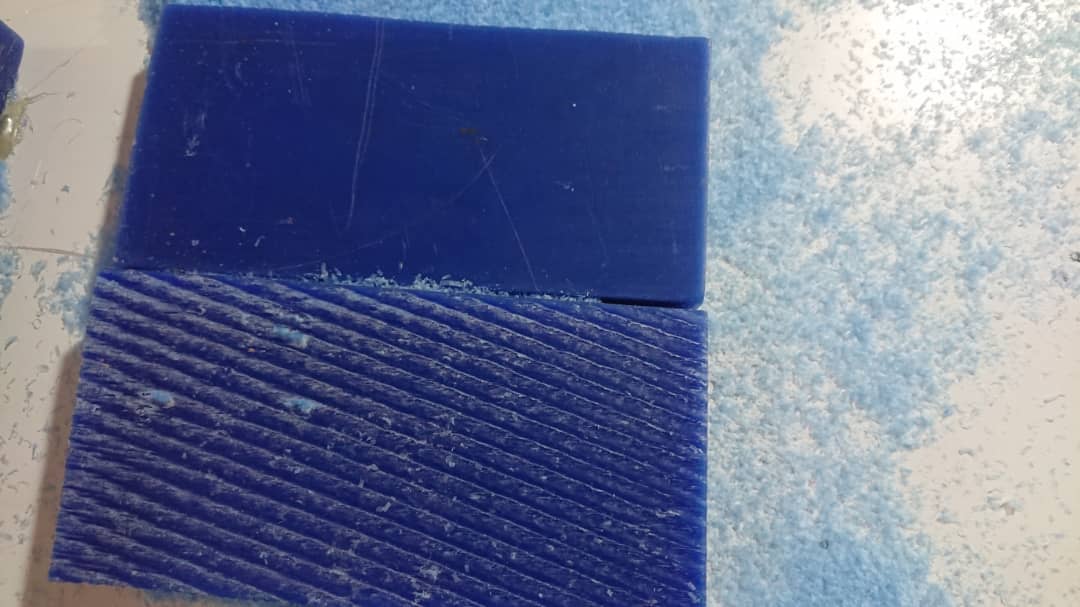
Milling process => levering
The issue is that the works are not levered . they have been used by others. so ihave to use cnc to cretae equal level surface on my wax materilas.
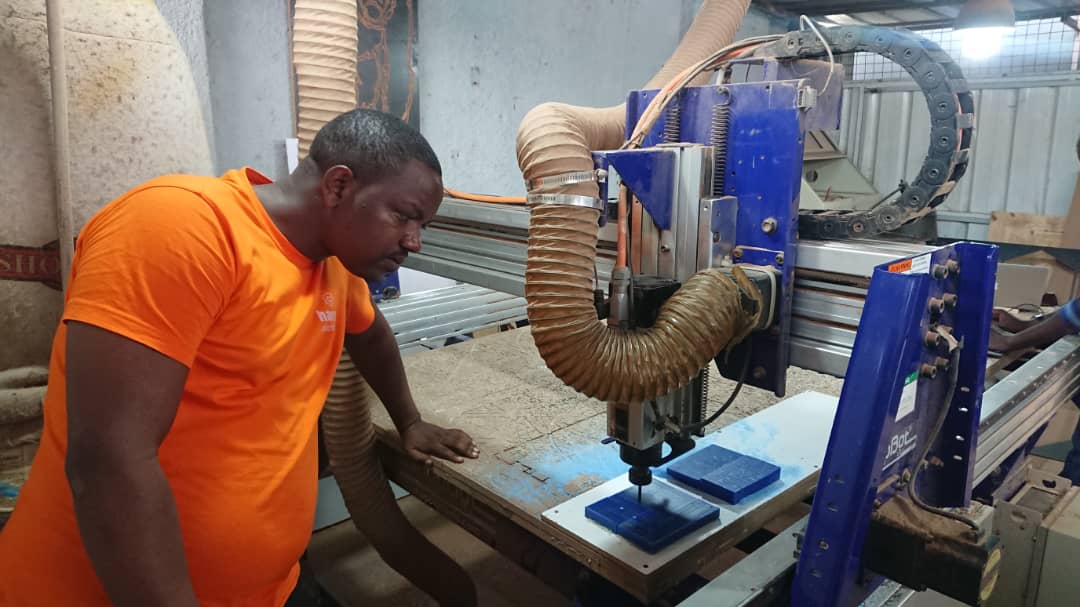
Leveling wax with cnc by milling its surface little bit
ROUGHING IN CNC MACHINIG
according to runsom.comRoughing in machining is the process of removing large amounts of material from a workpiece in preparation for semi-finishing and finishing operations. It involves using large feed rate and cutting depth to remove the excess material as quickly and efficiently as possible, often leaving a somewhat rough surface finish.
The purpose of roughing is to remove as much material as necessary to get the workpiece close to its final shape, while also minimizing the amount of time and energy required to do so. It’s usually the first stage in the CNC machining process and allows for more precise and efficient finishing operations later in the machining process.
Benefits of roughing
- Time saving
- Cost effective
- Saving materials
- Extended tool life
in my CNC Machining, i used 6mm End mill for roughing unfortunately i forgot to take heroshoot for that. i took a heroshoot for finishing only and i demonstrate that after
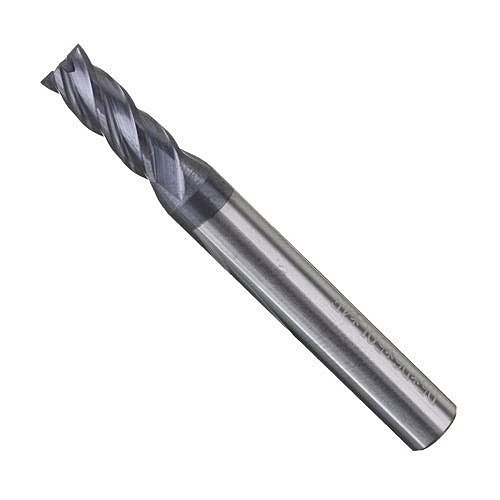
FINISHING IN CNC MACHINING
Finishing in machining refers to the process of giving the final surface finish and dimensional accuracy to a machined part or component. It’s a crucial method to improve the mechanical properties of the final product, such as performance, function, durability, electrical conductivity, smoothness, corrosion and wear resistance, and appearance.
Finishing usually takes place after roughing operations on workpieces in CNC manufacturing projects and is used to achieve final dimensions in terms of flatness, thickness, roughness, tolerances, and surface finish by removing any necessary excess material and completing the manufactured component.
Benefits of finishing
- Aesthetics
- Improve functionality
- Precision
- Easee of cleaning
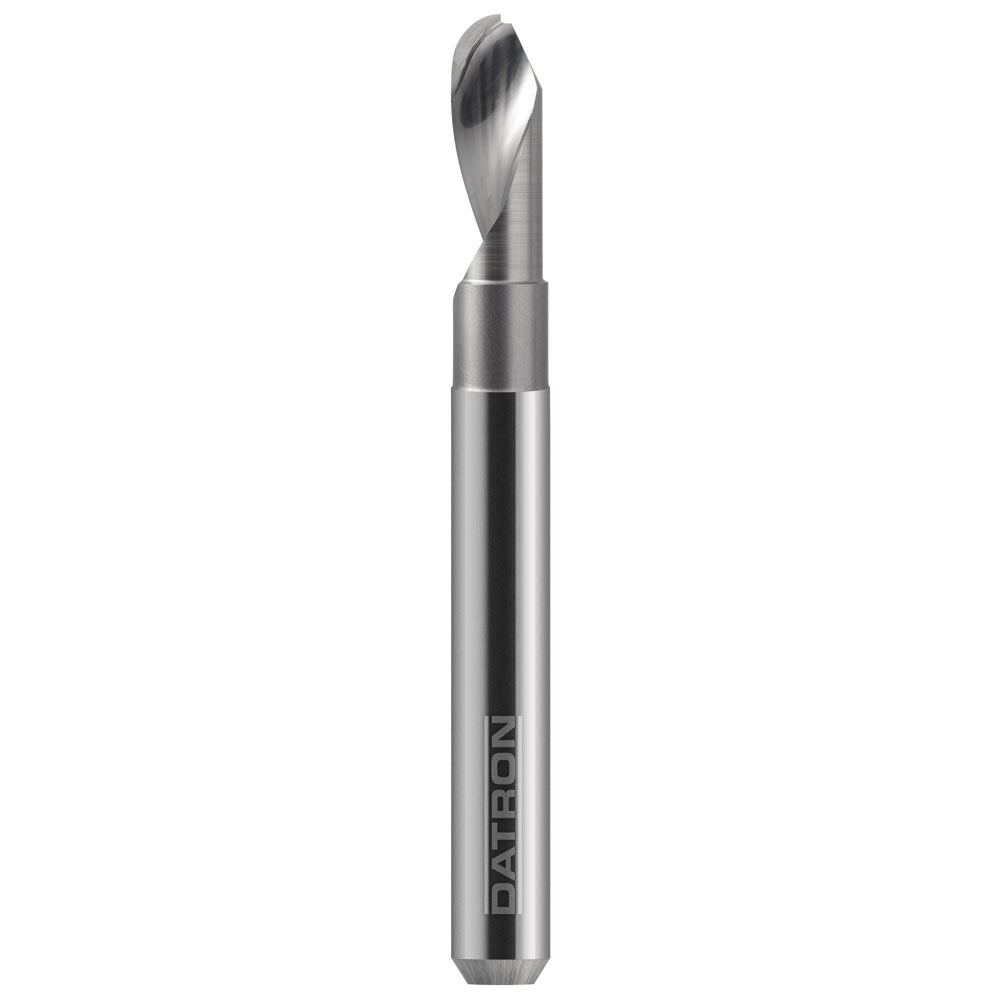
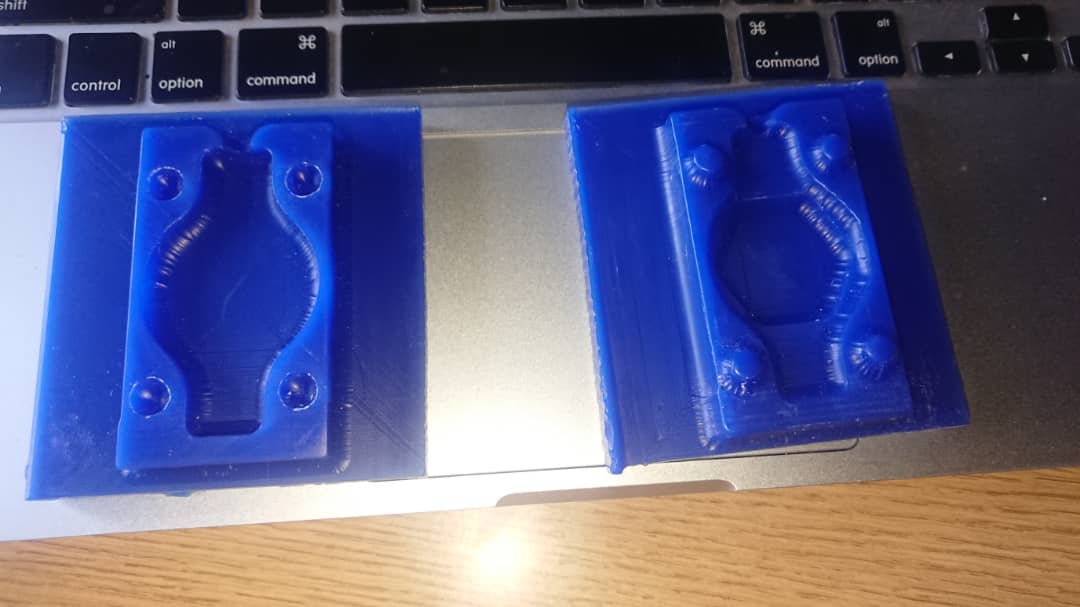
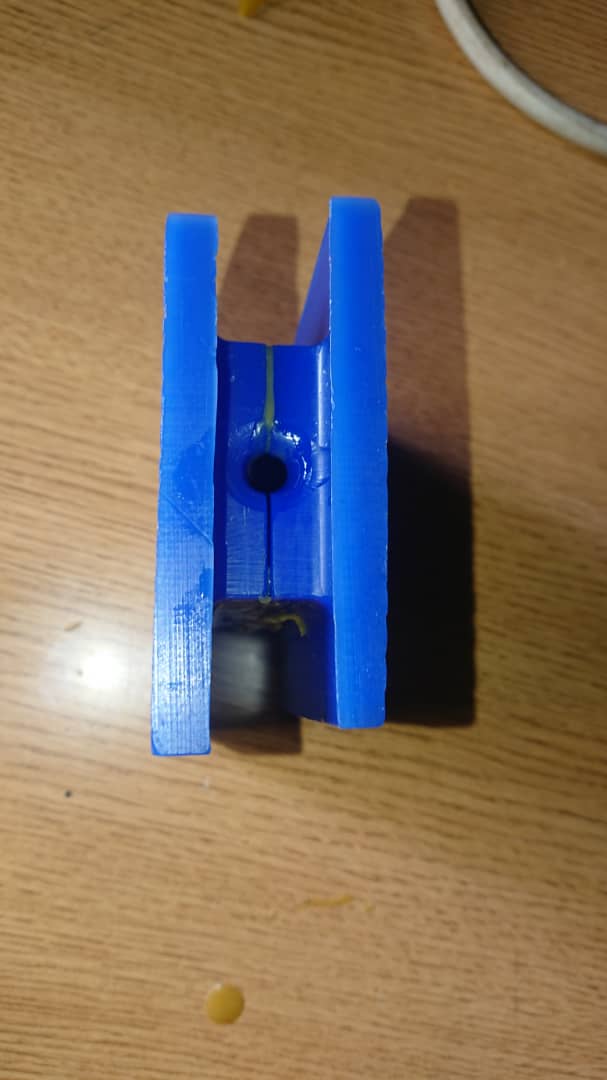
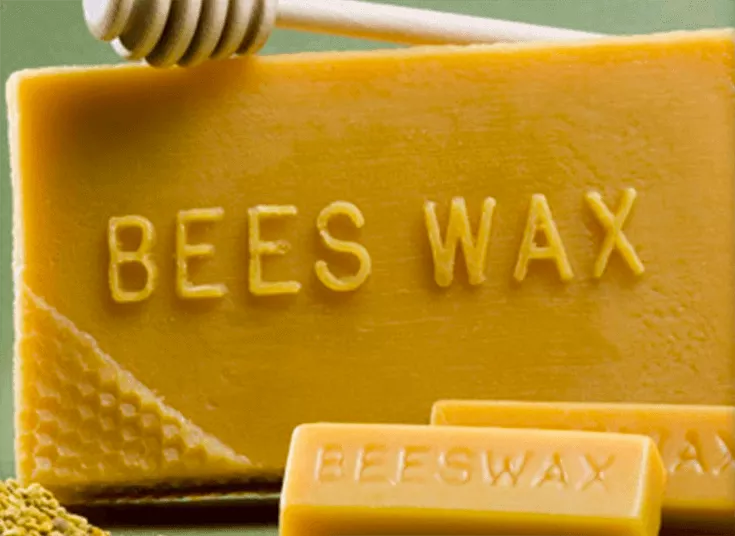
Beeswax is a natural substance produced by honeybees. It is a waxy material secreted by worker bees from glands on the underside of their abdomens. Beeswax is used by bees to build honeycomb cells, where they store honey, pollen, and raise their brood.
Beeswax has a low melting point, which makes it suitable for creating molds for various purposes.
things that can be made with bees wax
BEE WAX PROPERTIES
Property | Description |
---|---|
Malleability | Beeswax is easily malleable, allowing it to be shaped and molded into various forms. |
Low Melting Point | Beeswax has a relatively low melting point (62-65 celcius degrees), making it easy to melt and work with using gentle heat. |
Emollient | Beeswax has emollient properties, making it effective in moisturizing and softening the skin. |
Fragrance Retention | Beeswax has the ability to retain and release fragrance, making it useful in scented products like candles and cosmetics. |
Waterproofing | Beeswax is water-resistant, providing a protective barrier against moisture when used in various applications. |
Combustibility | Beeswax is combustible and burns with a clean flame, making it ideal for candle-making. |
Thermal properties of bee wax
Property | Value |
---|---|
Chemical Formula | C15H31COOC30H61 |
Melting Point | 62-64 °C (144-147 °F) |
Boiling Point | 204-209 °C (399-408 °F) |
Flash Point | >93 °C (>199 °F) |
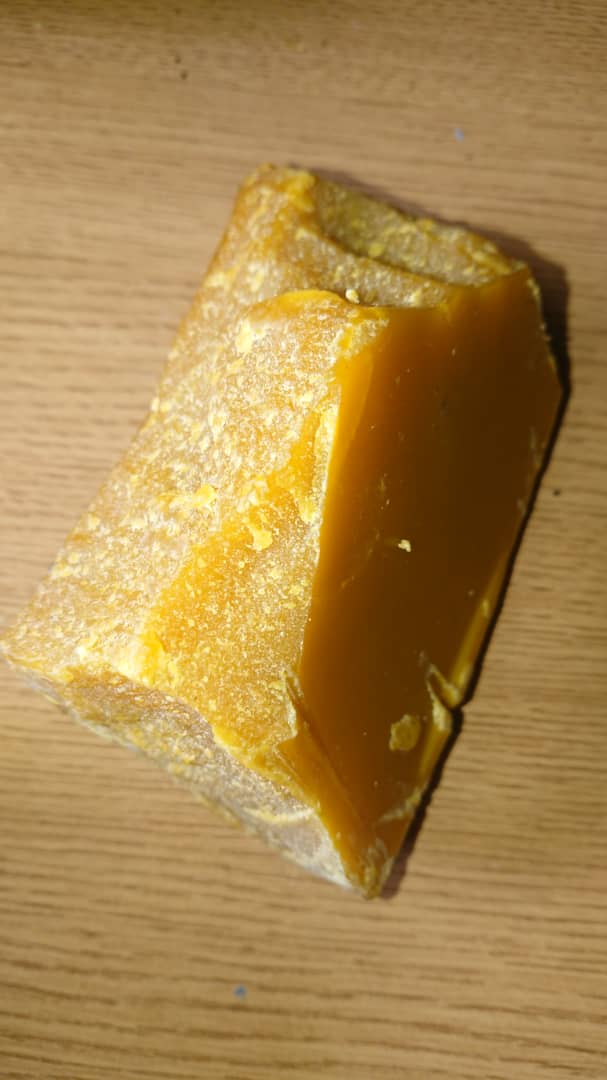
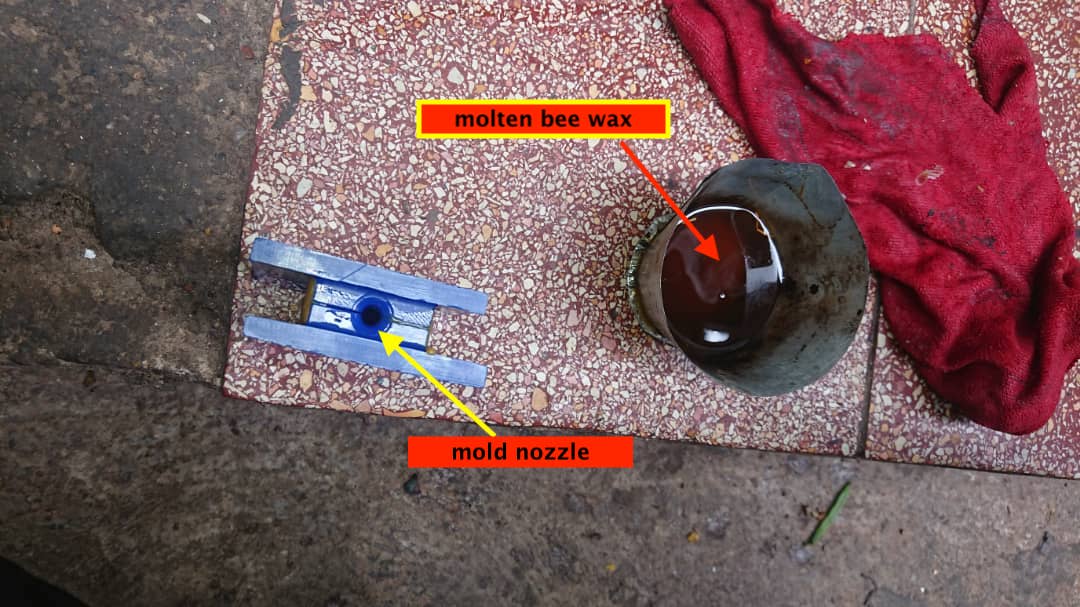
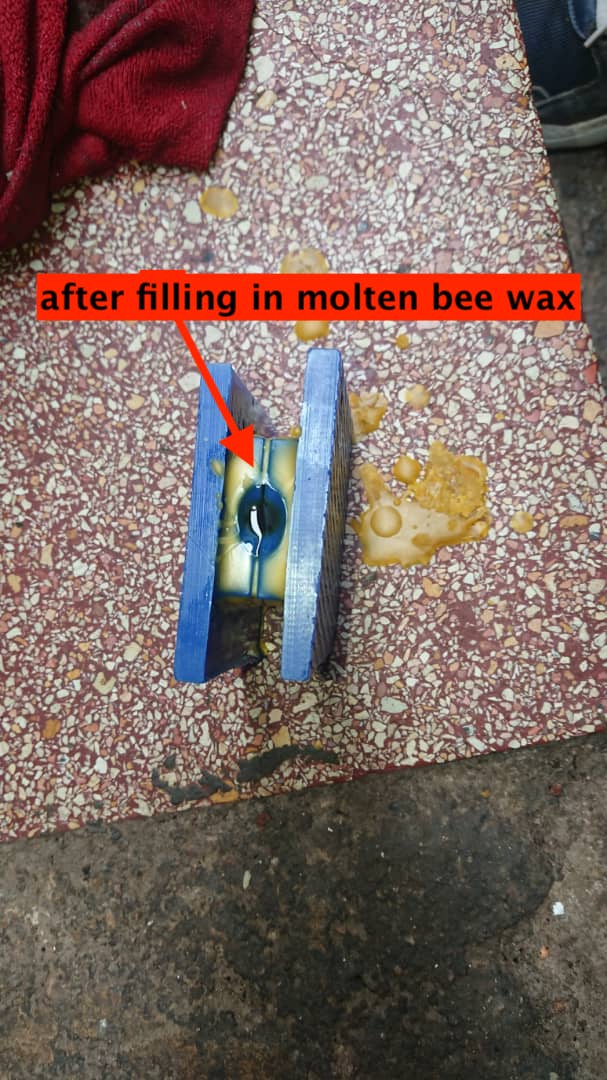
Results
after waiting around 2 hours i have opned the mold and release my material
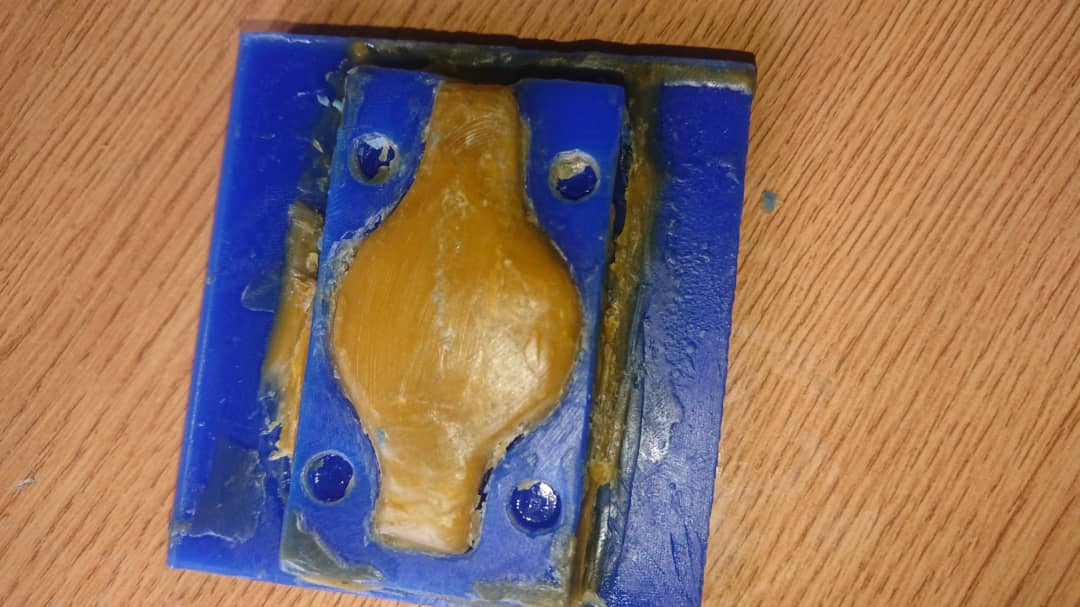
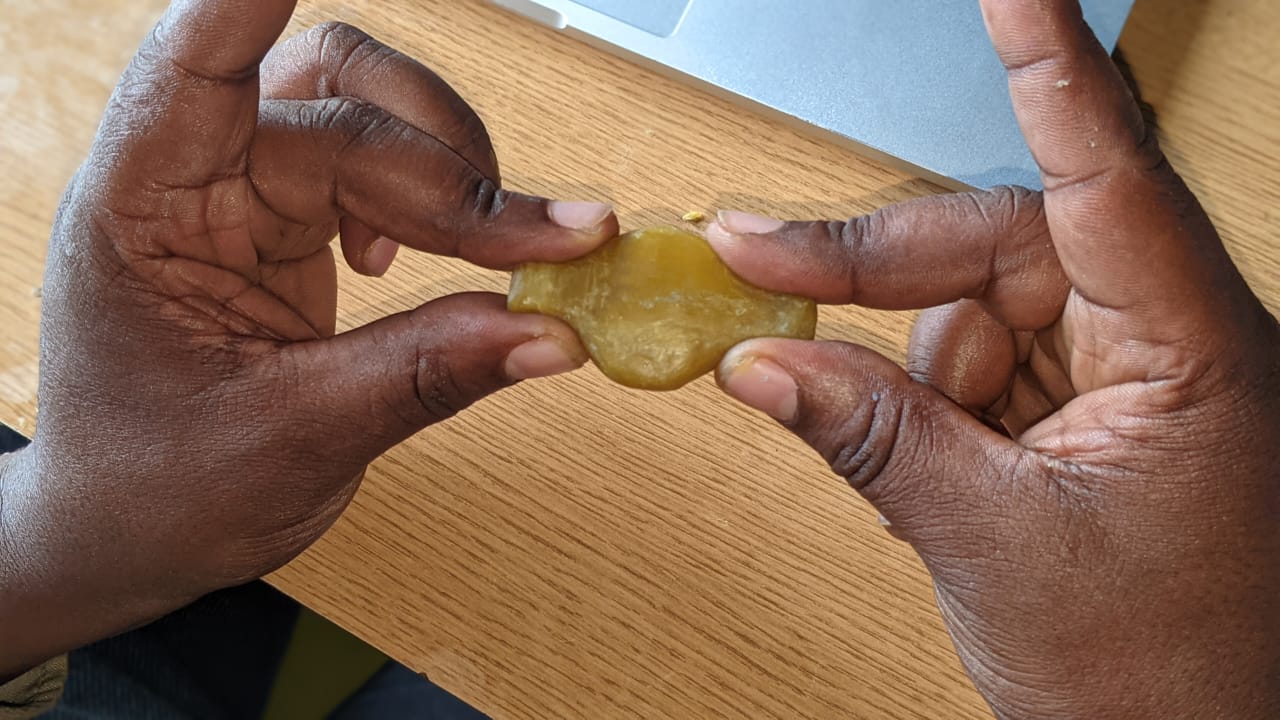
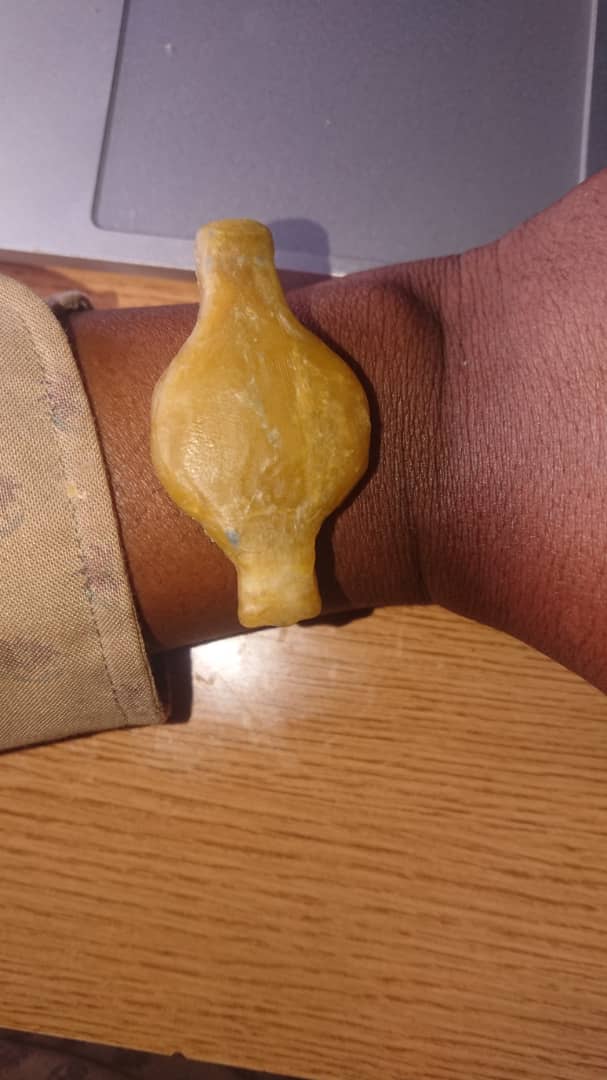
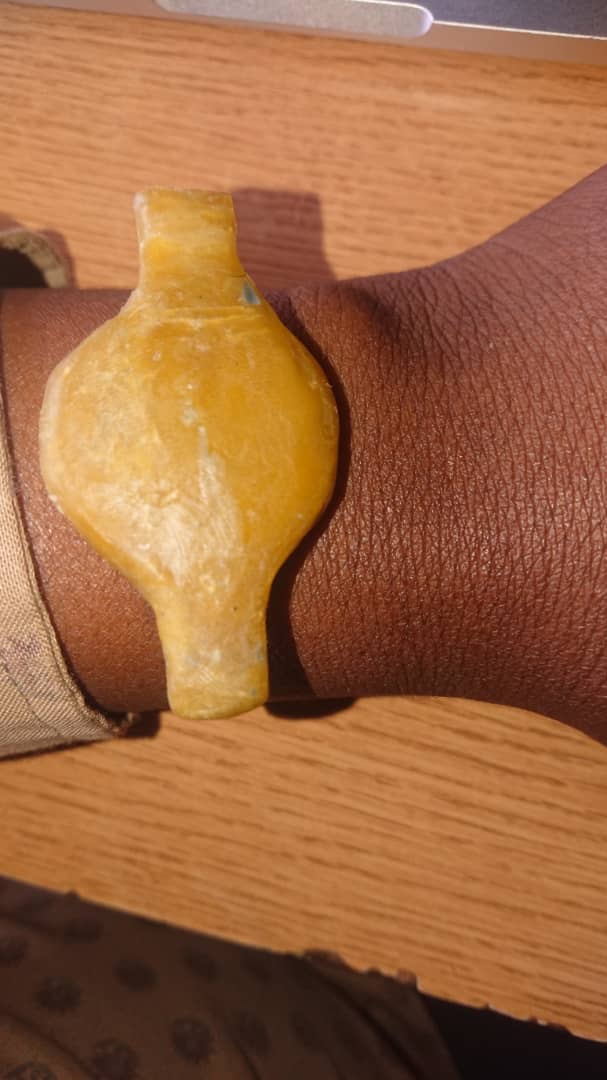