Molding and Casting
Molding and casting are fundamental processes in manufacturing, art, and various other industries, allowing the reproduction of objects with good precision.
Group Assignment
The Kannai team as usual was divided into two and i worked with Ahmad Tijjani Ishaq The task is to review the safety data sheets for each of your molding and casting materials, then make and compare test casts with each of them compare printing vs milling molds Our group assignment page
Individual Assignment
All source files can be found Here at the side bar.
Assignment for the week is to design a mold around the process you’ll be using, produce it with a smooth surface finish, and use it to cast parts extra credit: use more then two mold parts
Molding This is the process of creating a negative impression or mold of an object, which is then used to reproduce multiple replicas.
Casting is the process of pouring a liquid or semi-liquid material into a mold to create a solid object.
To complete my assignment i follow the following steps.
- I first did a 3D design of my possitive mold using fusion 360. My design is a
bangle with a heart at
the center dedicated to my fiance.
- I first made the design of the desired finished part. I made the front and back surface seperate first
- Then i used the combine tool to make the negative mold of the parts and also included the lapping space for the two halves
- After that i used the combine tool again to get the possitive mold of the whole parts
- Then i exported the stl file
- Next i used the mods site. i chose program, gcode, mill 2.5D stl which is used for the rough cut.
- Then i generated the 2.5d gcode and repeated same process for mill 3D stl for the finish cut
- With my gcode's ready i proceed to cut my mold using the Genmitsu milling CNC. I
use the following:
- Material -- machinable Wax
- Toolbit-- 1/16 bit for finish cut
- Toolbit -- 1/8 bit for Roughcut
- With the milling completed, i kept the pieces from the milling operation for recycle purpose
- A table was prepared for the casting process so as to avoid messing up the place. Also Safety wears was used for protection
- With that done, next i mixed the silicon Mold Star™ rubbers part A and B together in a mixure of ratio 1A:1B in a cup and stir till its well mixed
- Then i cut acrylic material and place at the edges of the mold and then poured the mixure in it. i waited for 25 minute for it to dry
- having casted our first part with silicon. I used this as a negative mold for my
final cast which is ceramic, I made a stand
to keep it in place before i could pour the ceramic mixture in it. i also added
baby powder in the mold with the help
of a brush.
I used The Smooth-Cast™ 300 Series of liquid plastics that are ultra-low viscosity casting resins that yield castings that are bright white and virtually bubble free. - After waiting for 15min, the cast solidifies and set.
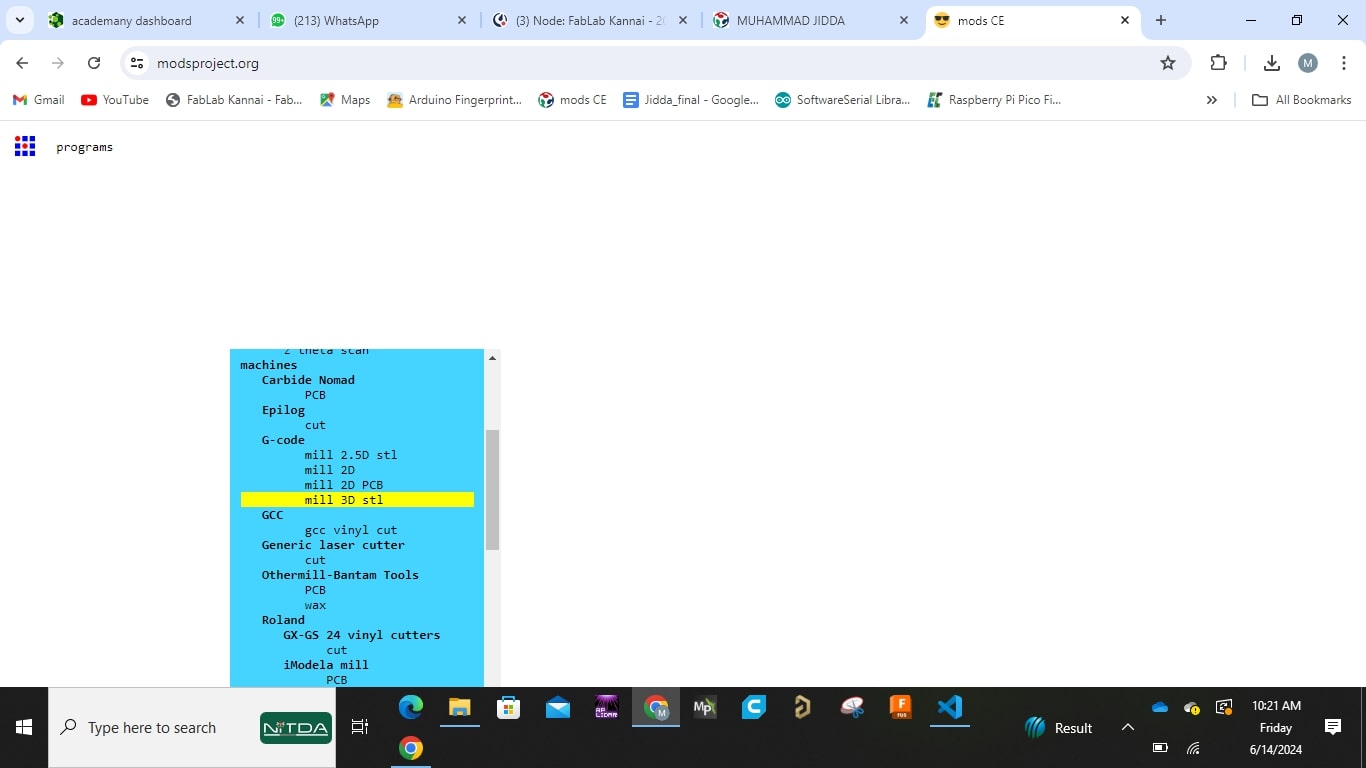
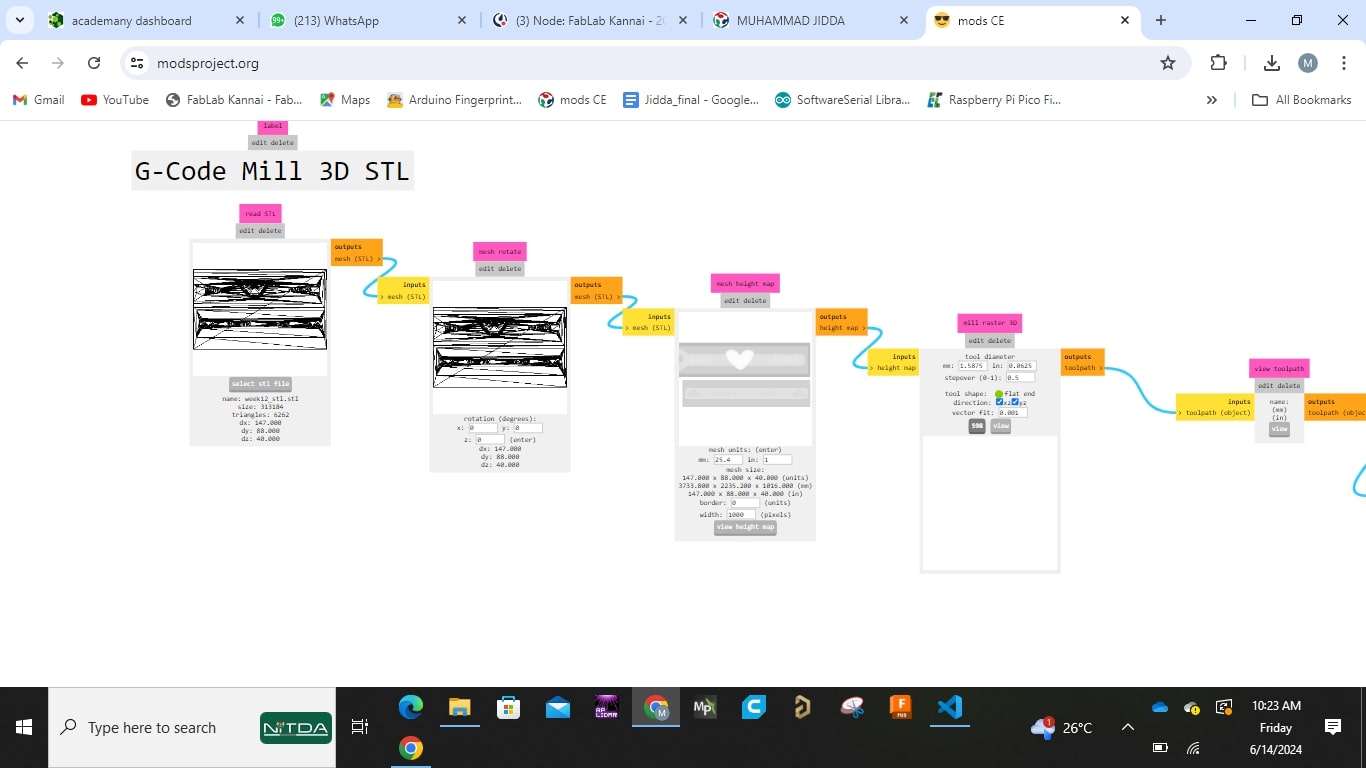
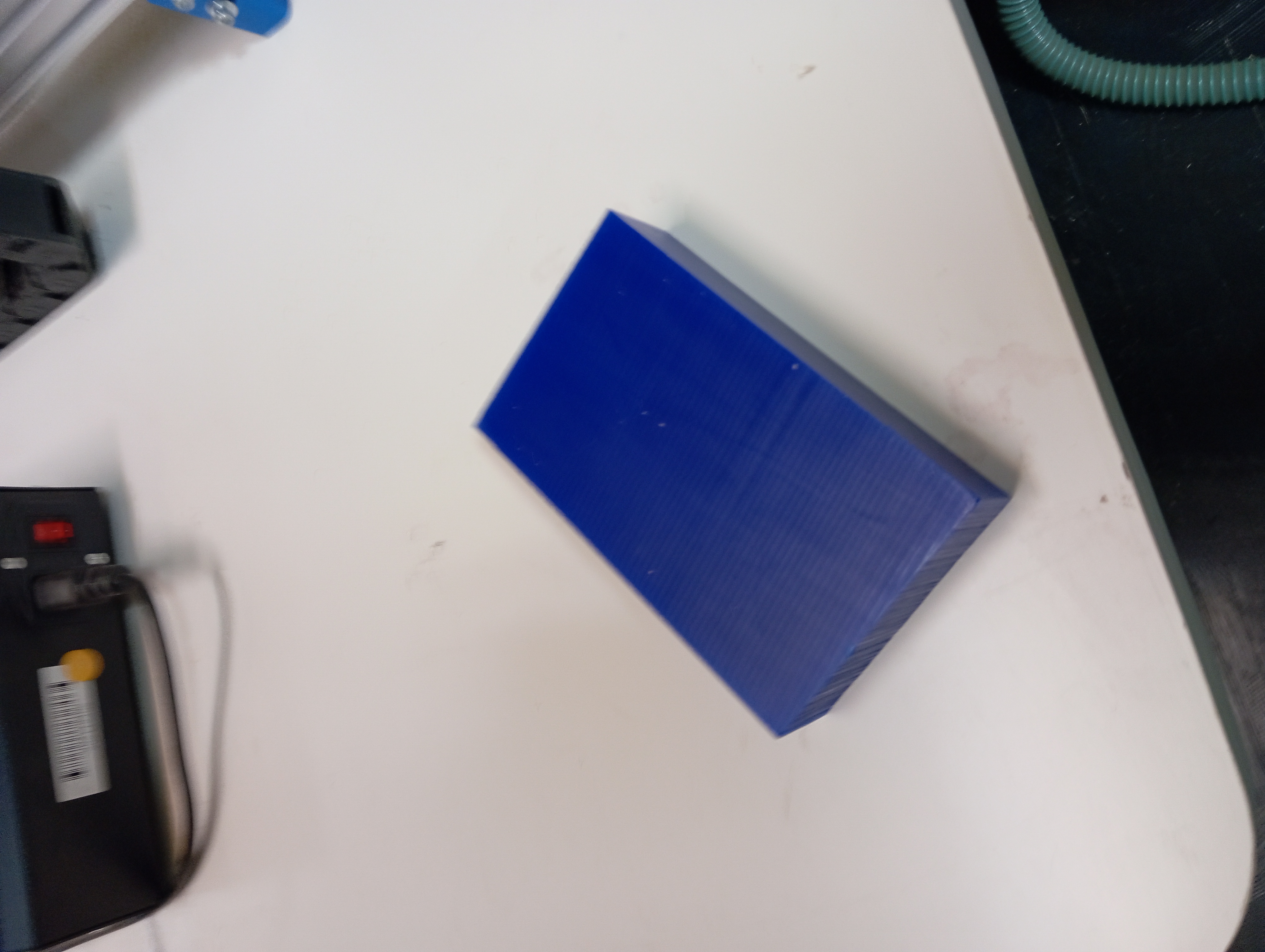
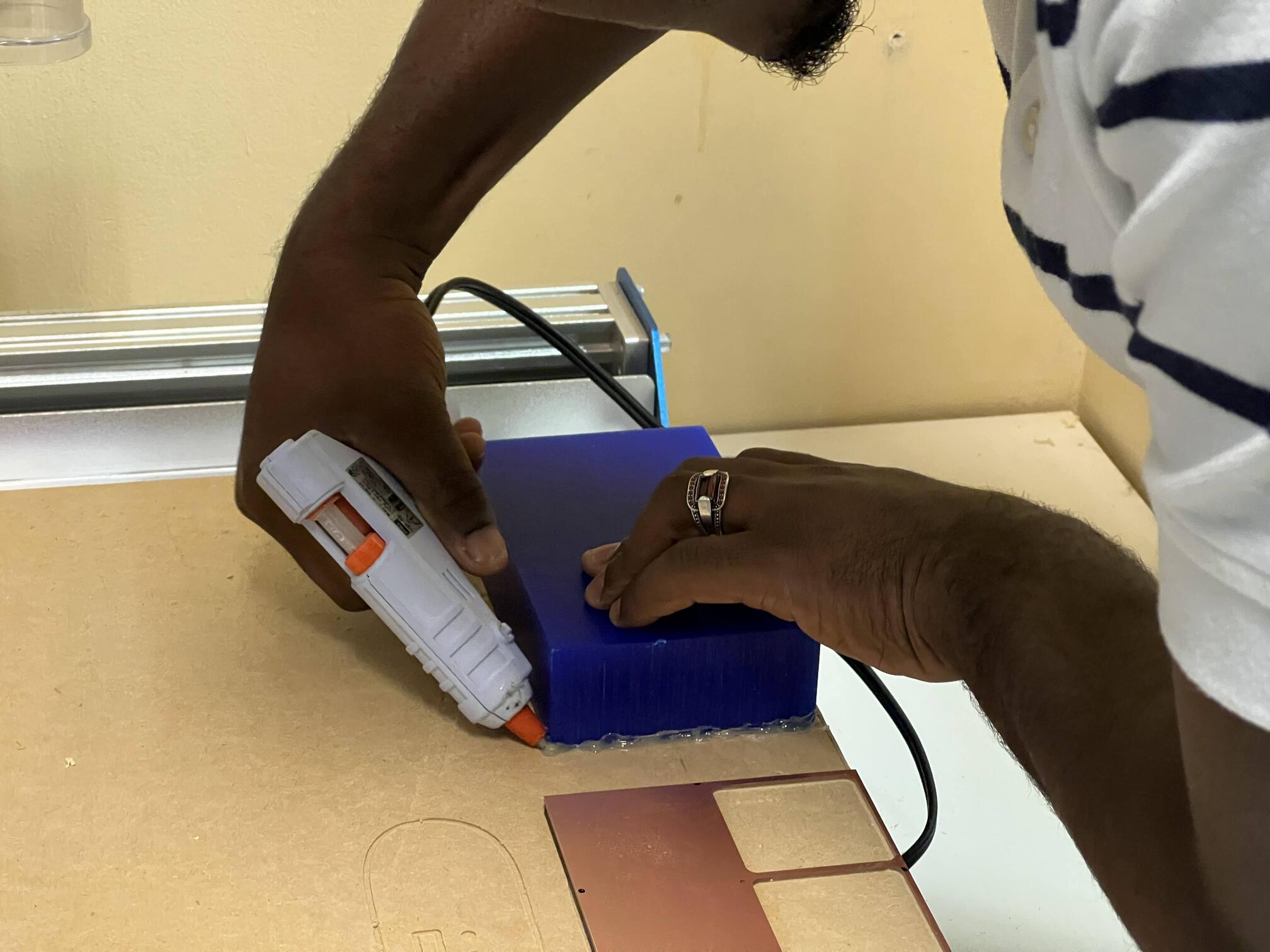
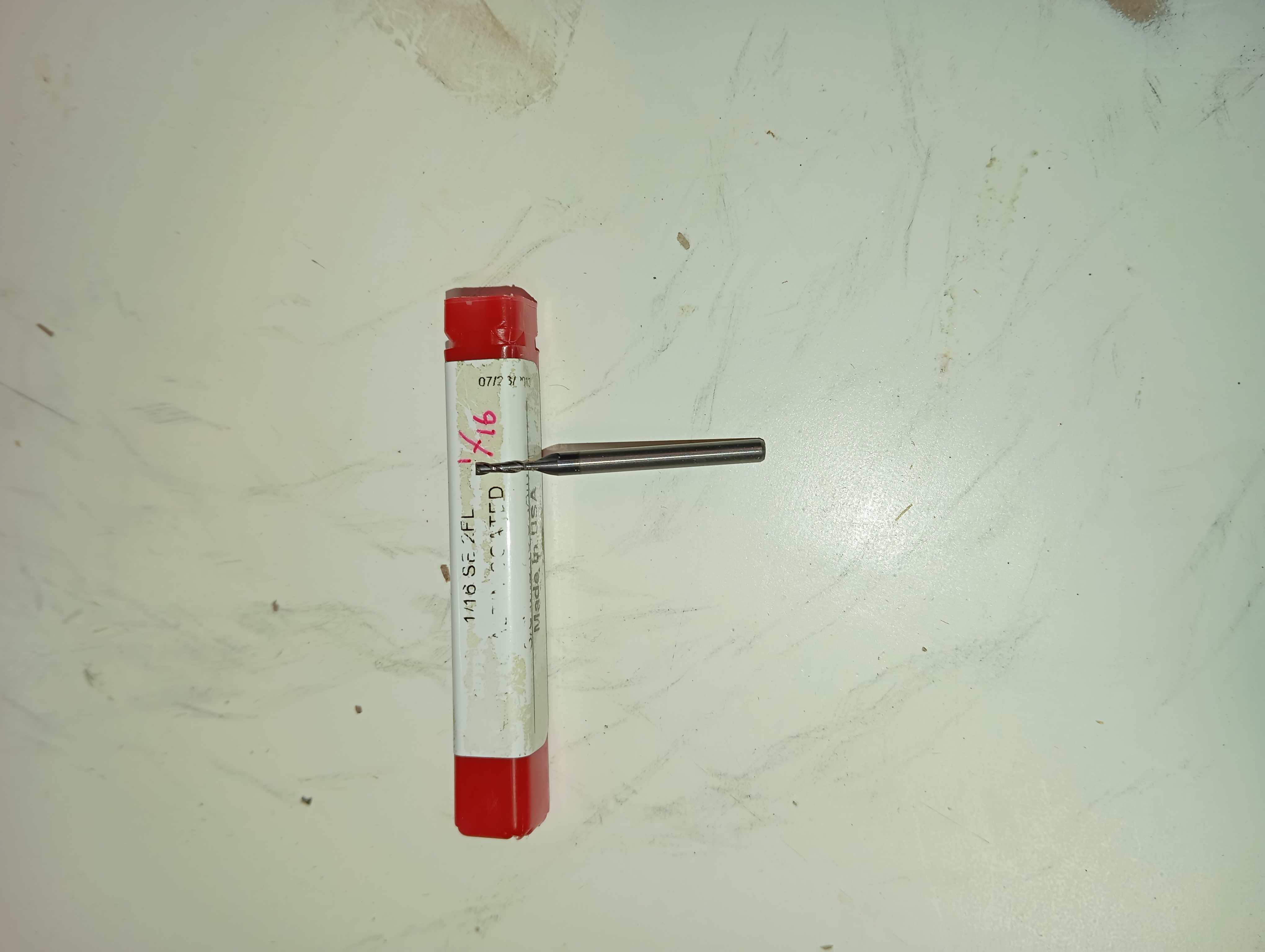
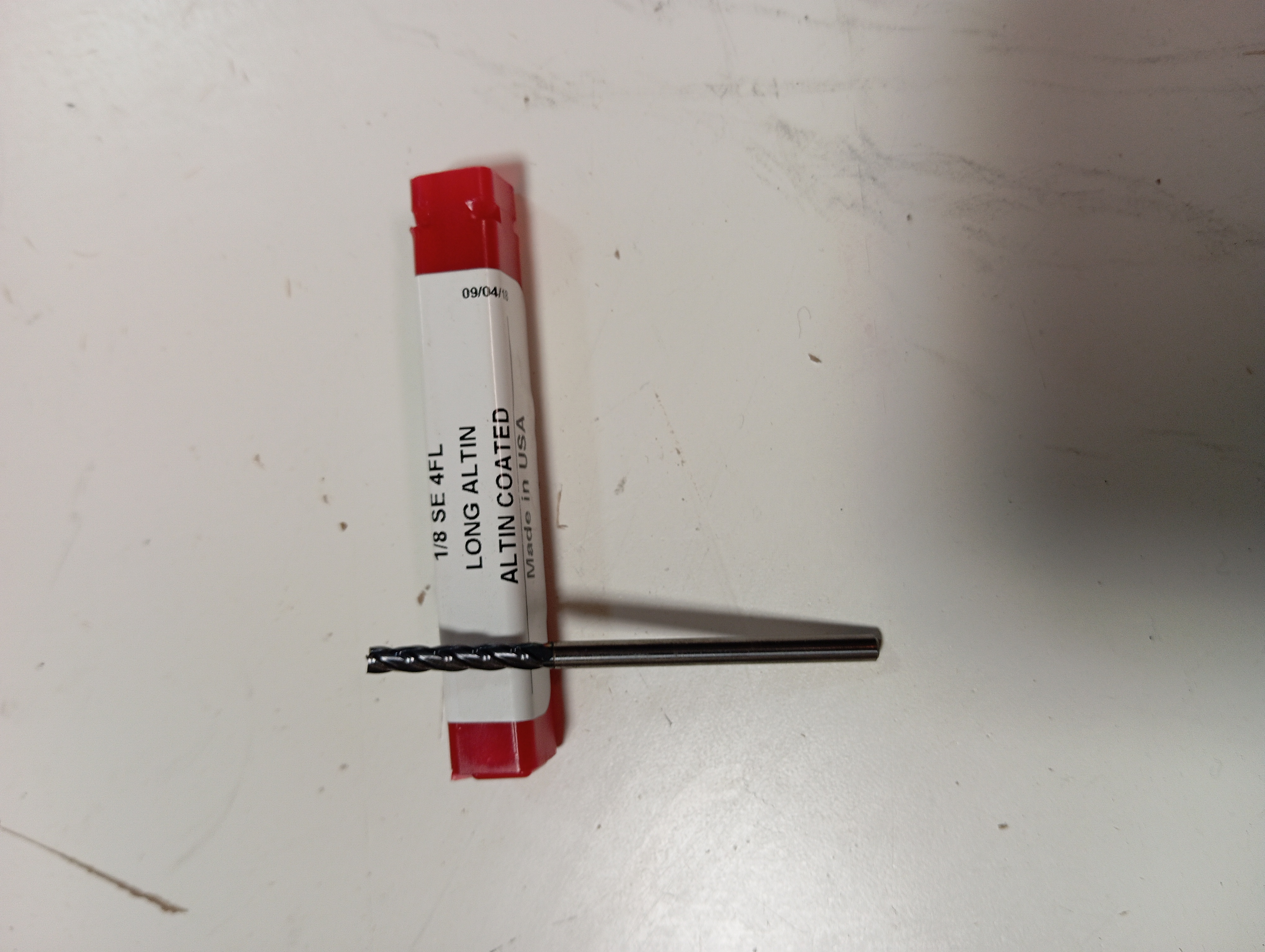
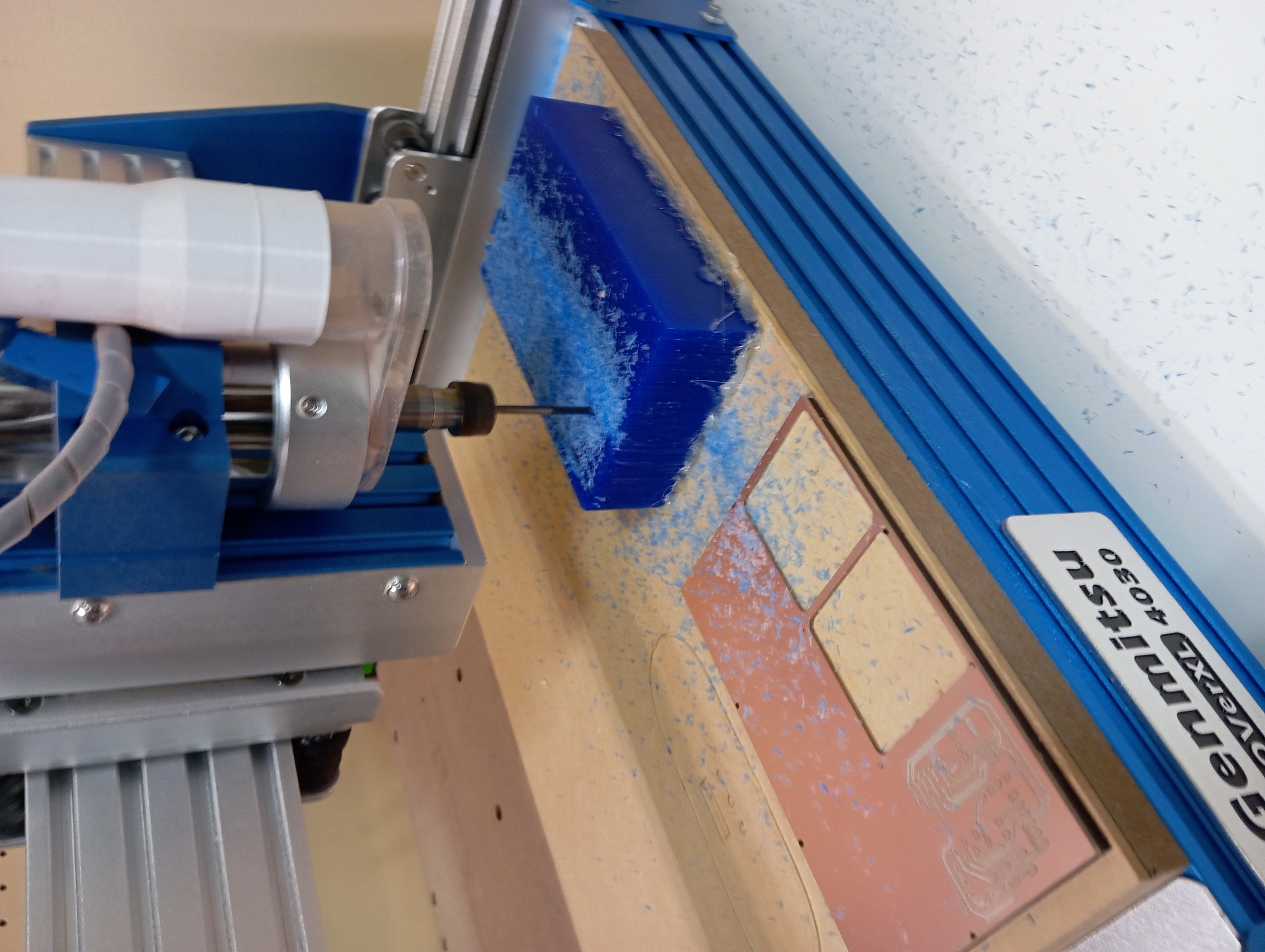
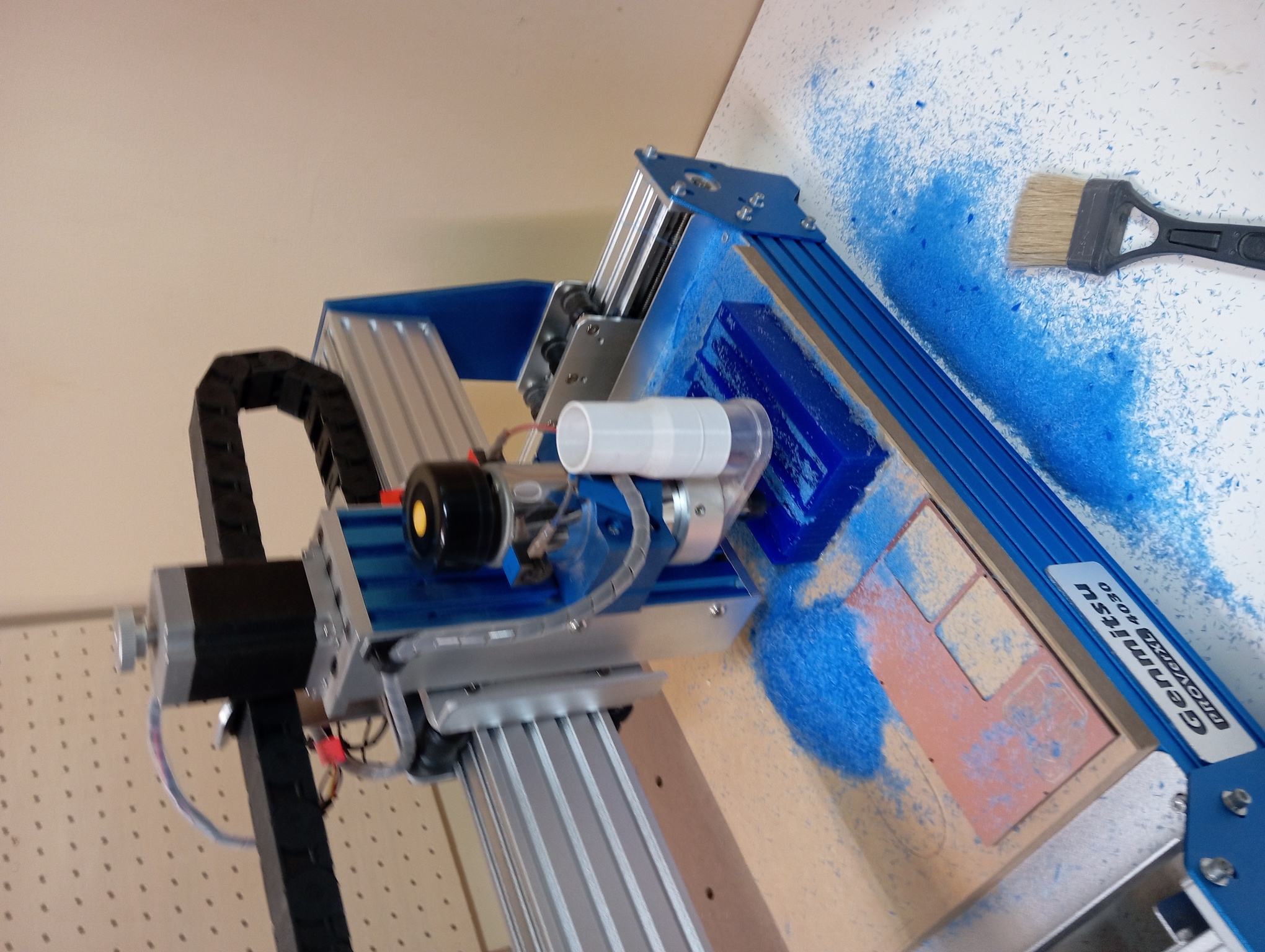
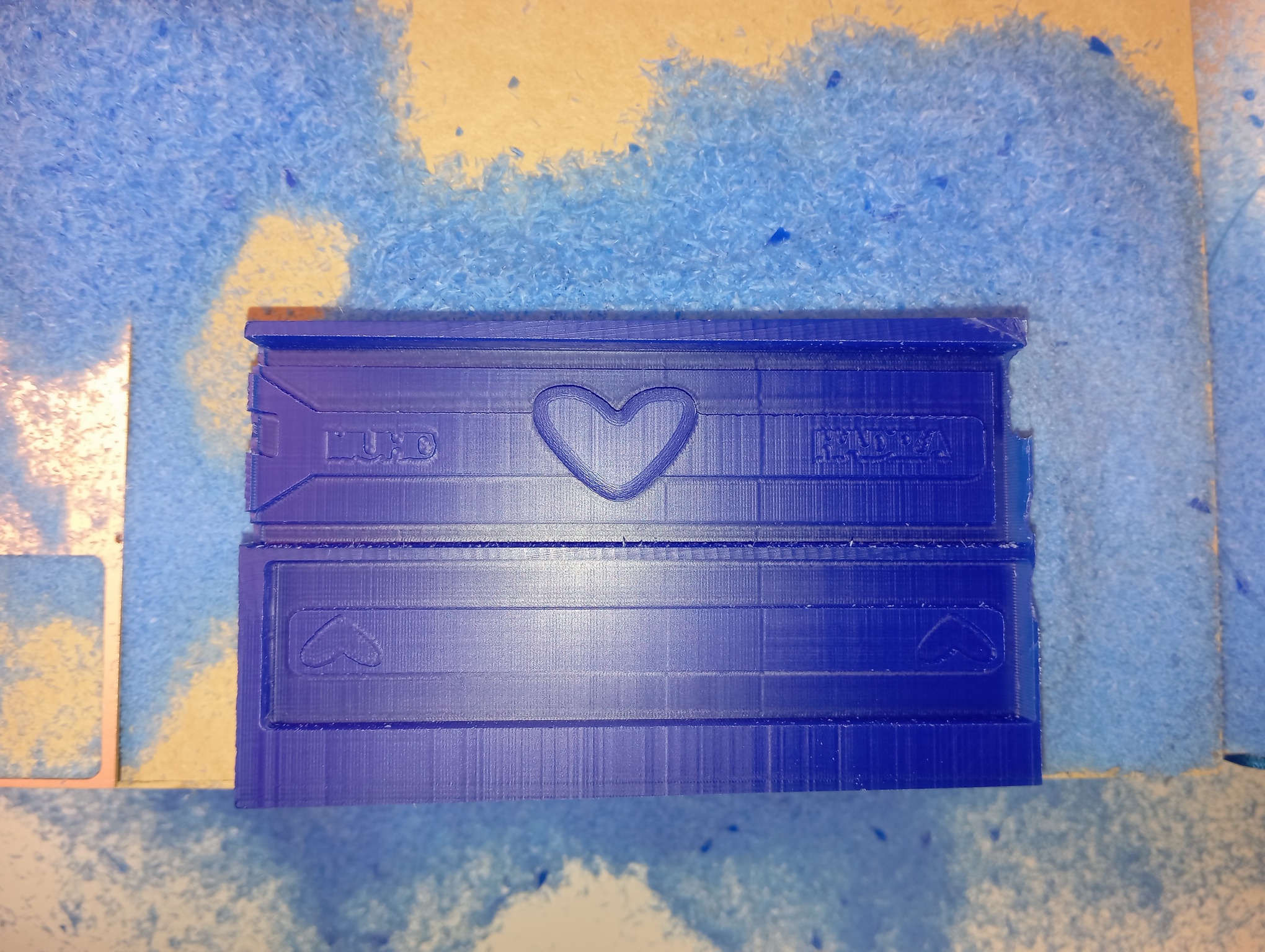
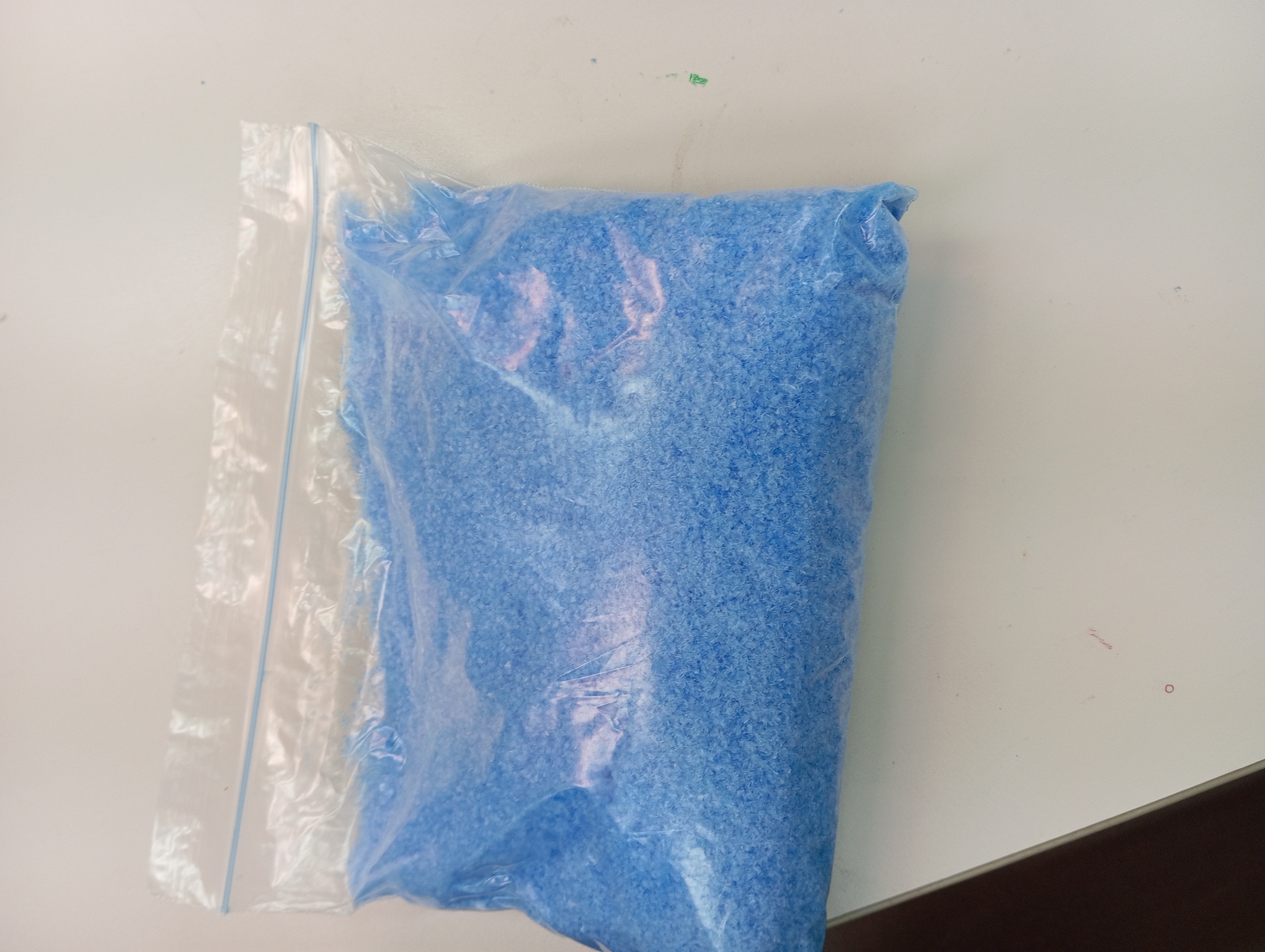
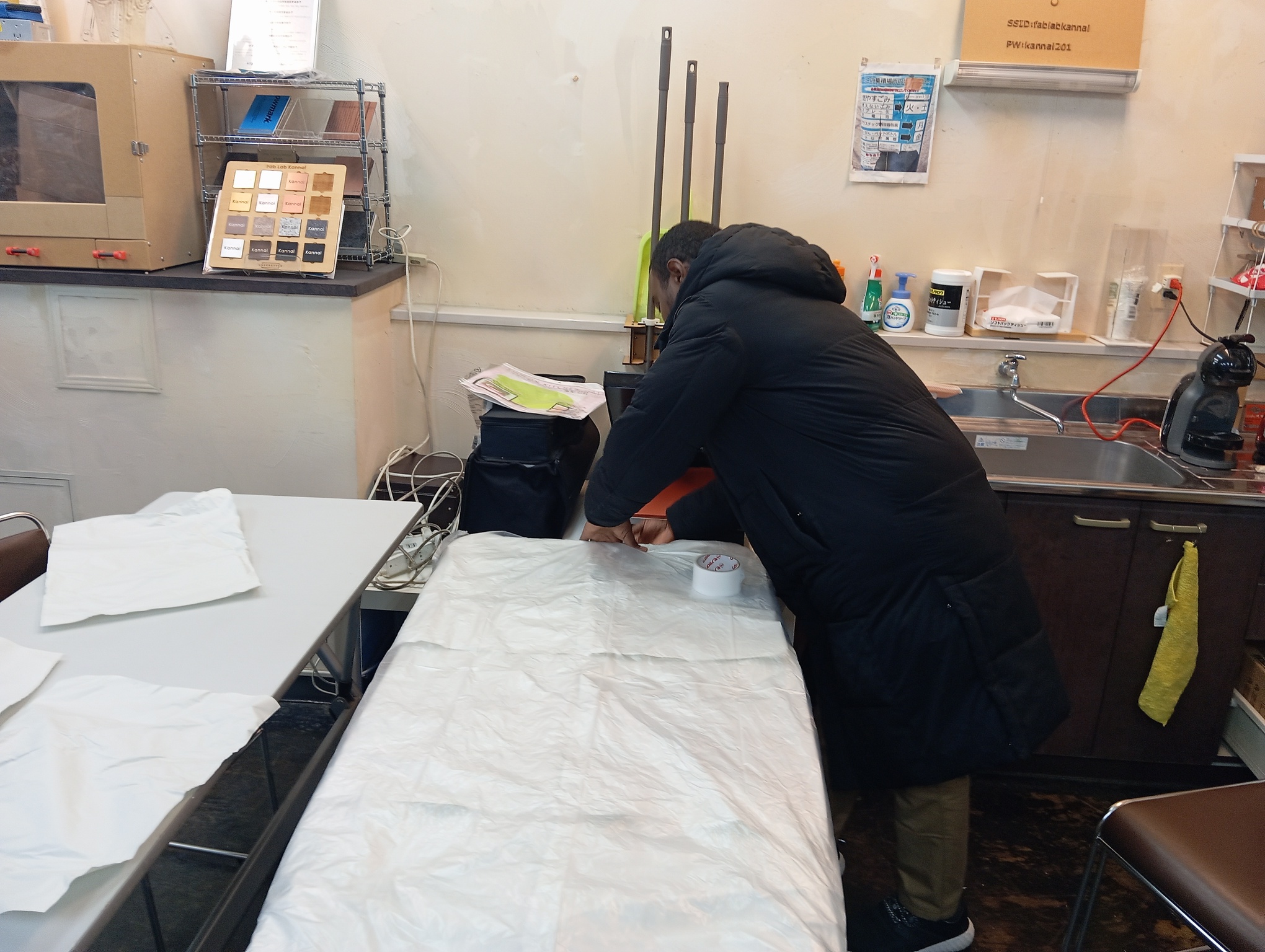
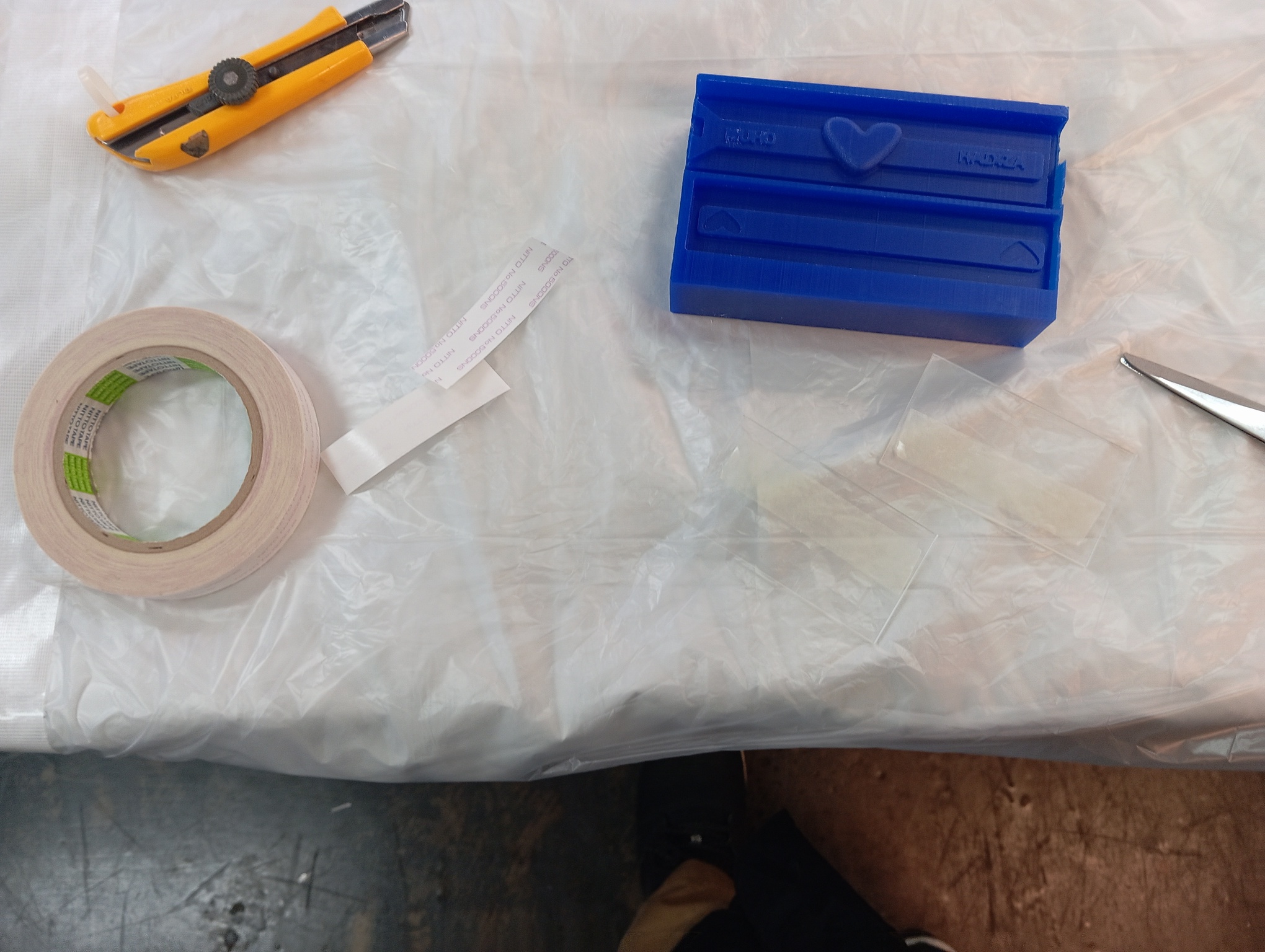
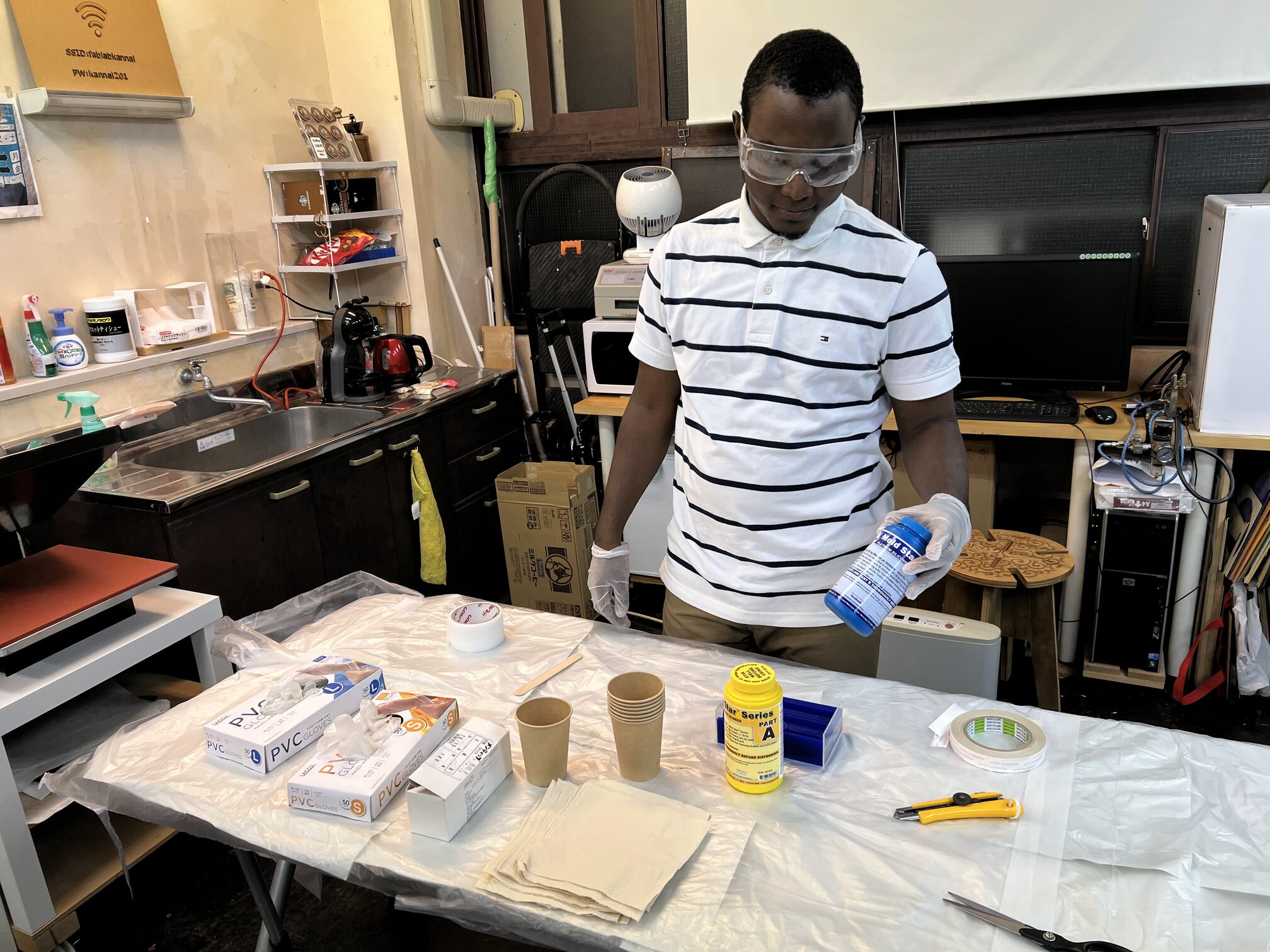
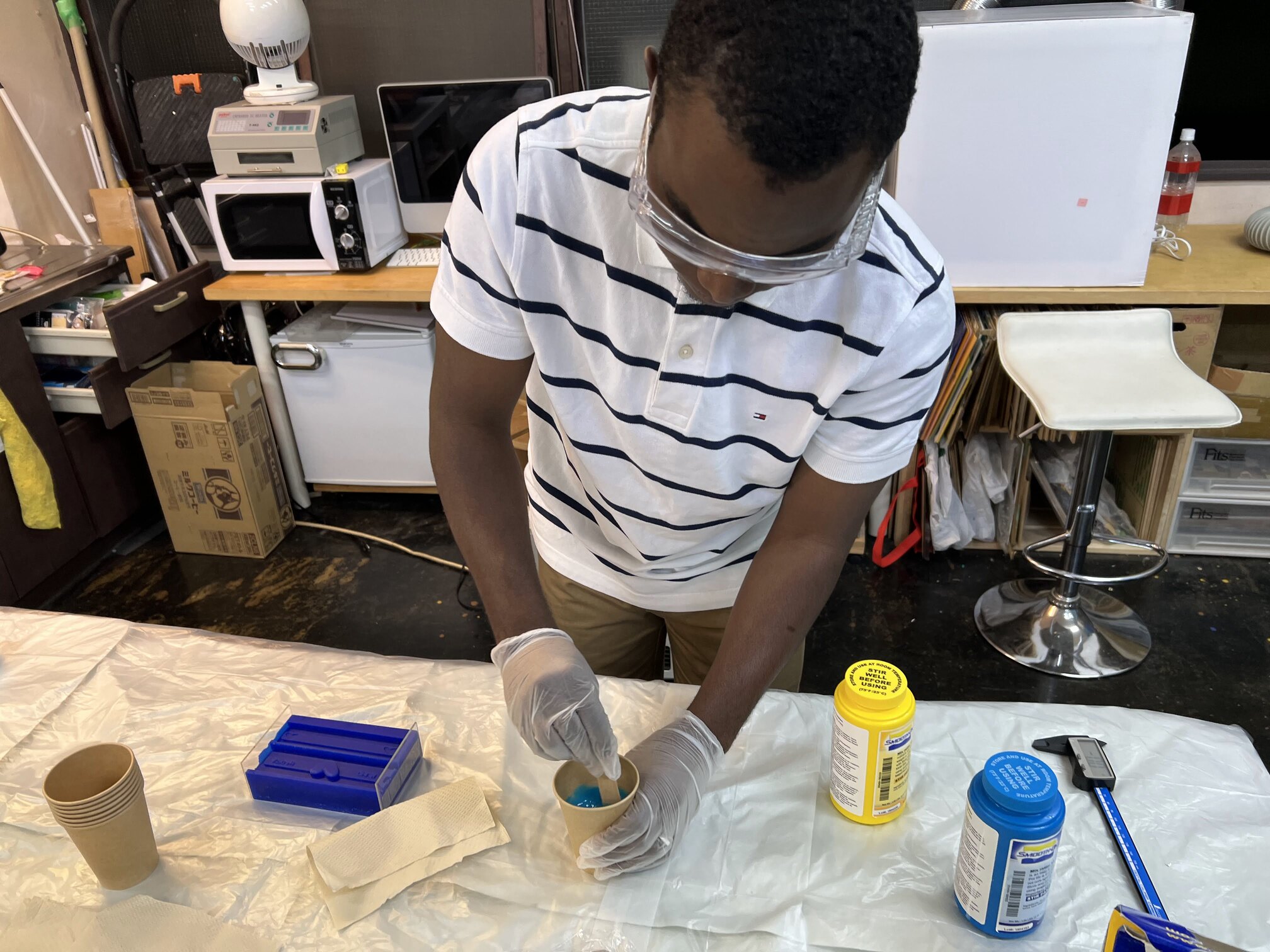
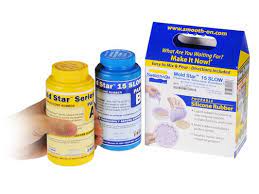
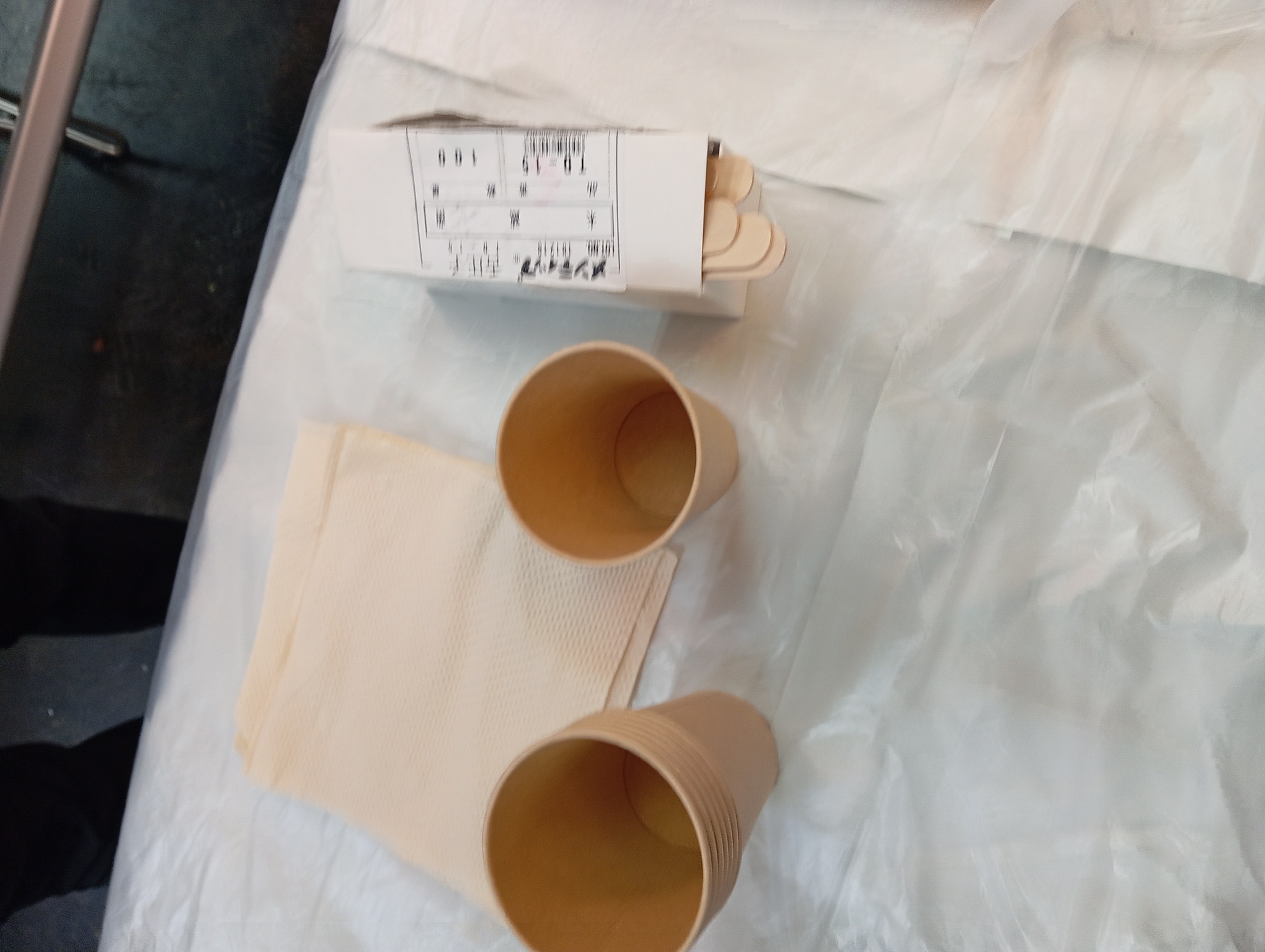
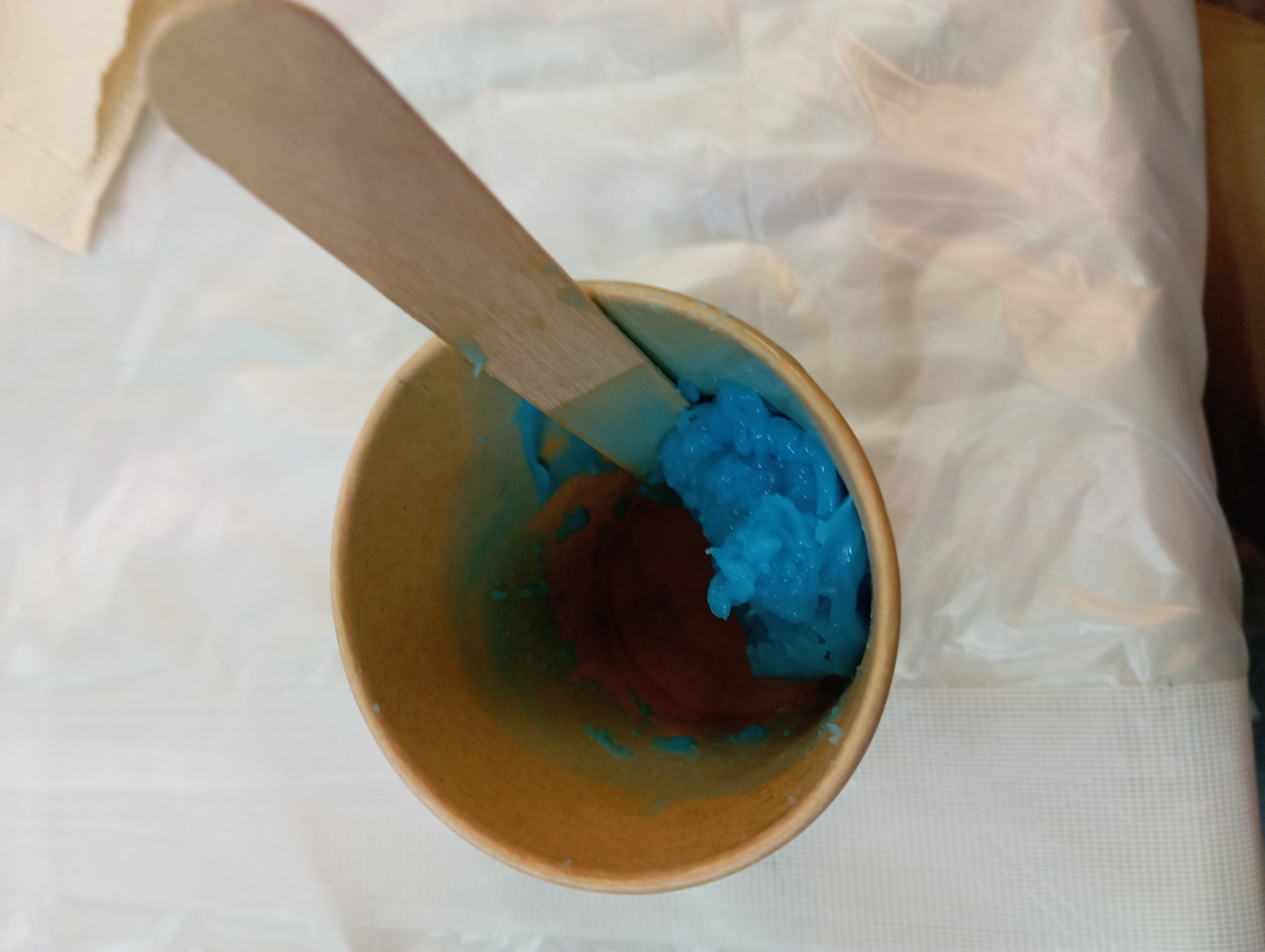
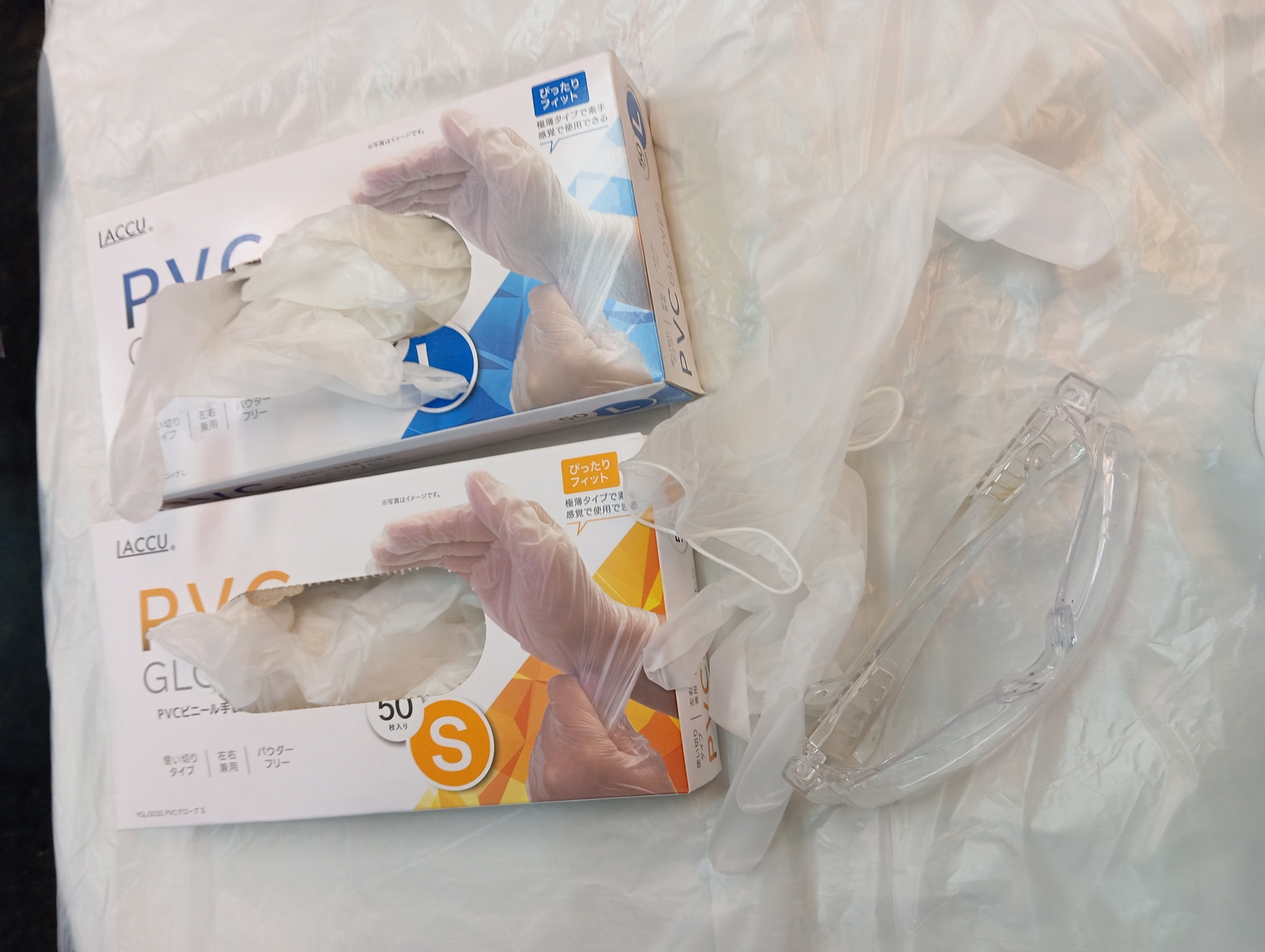
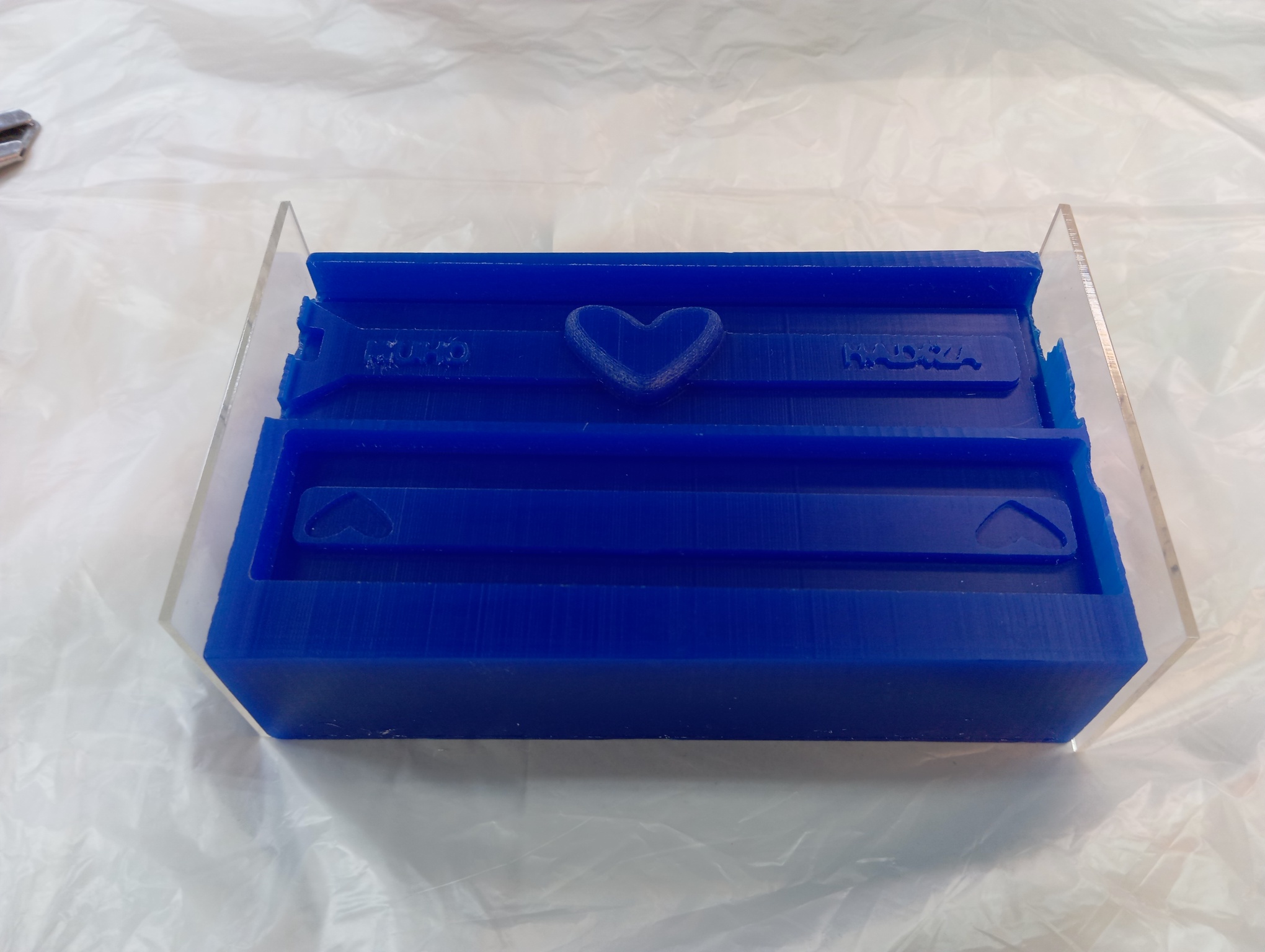
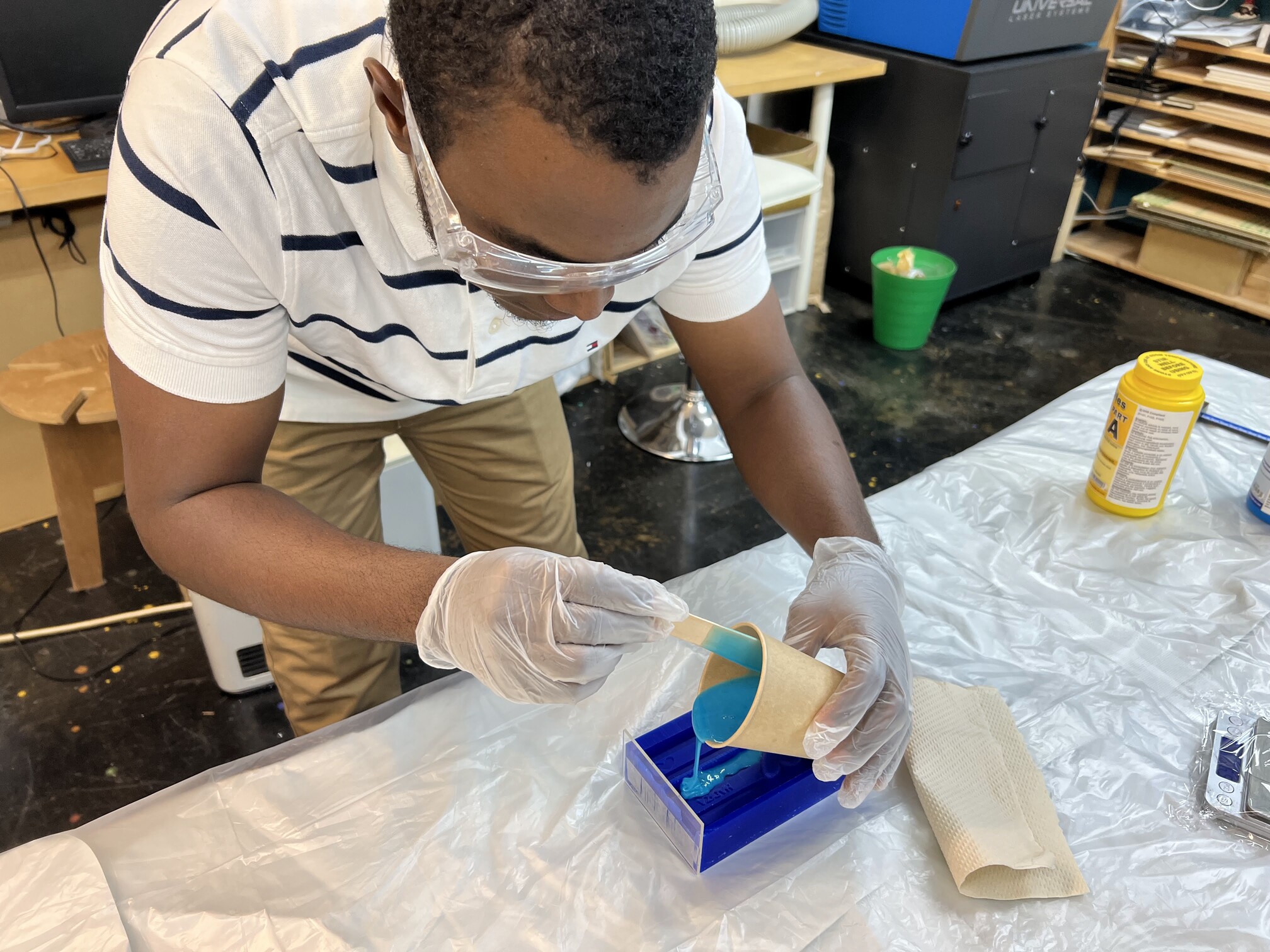
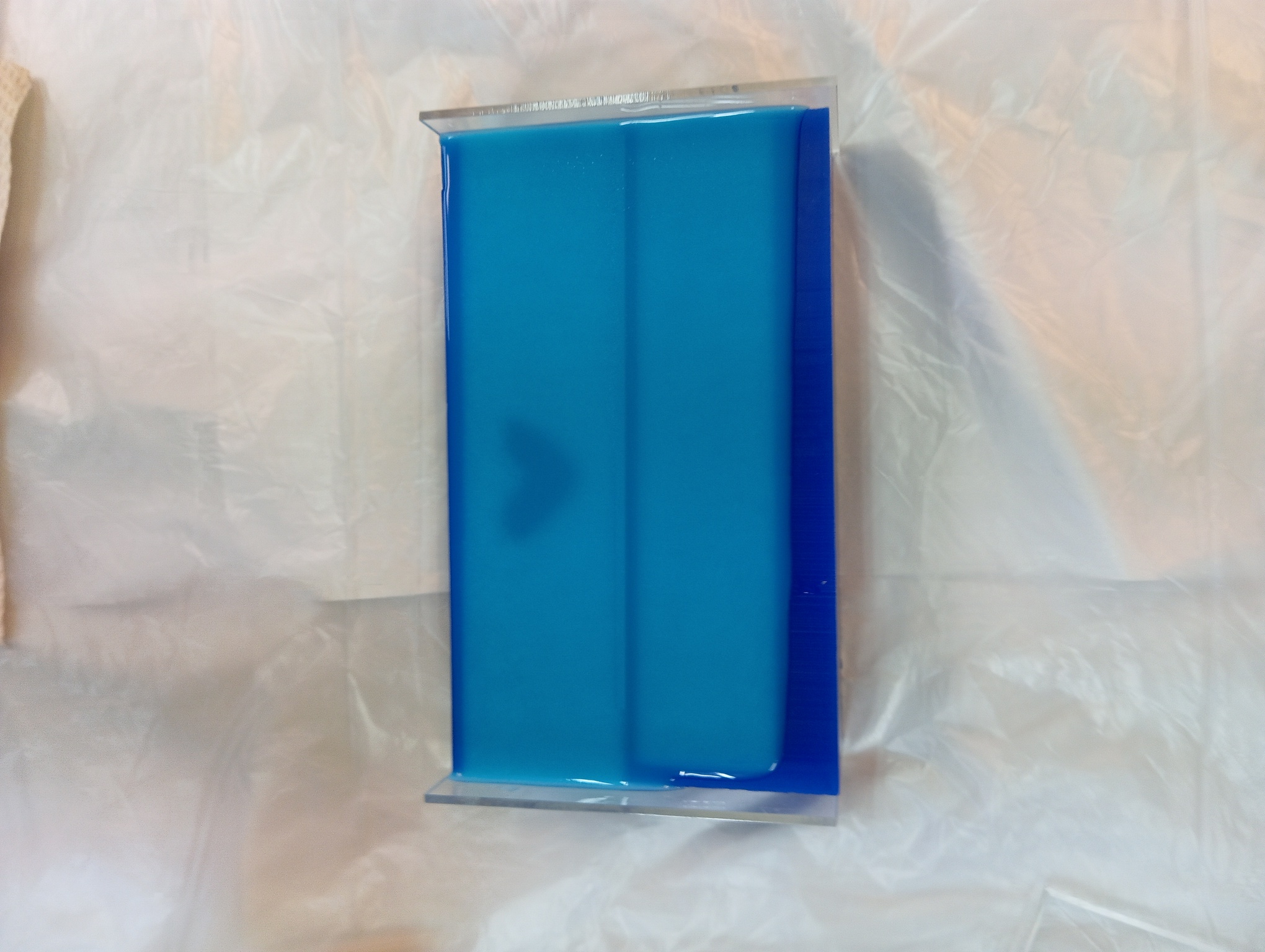
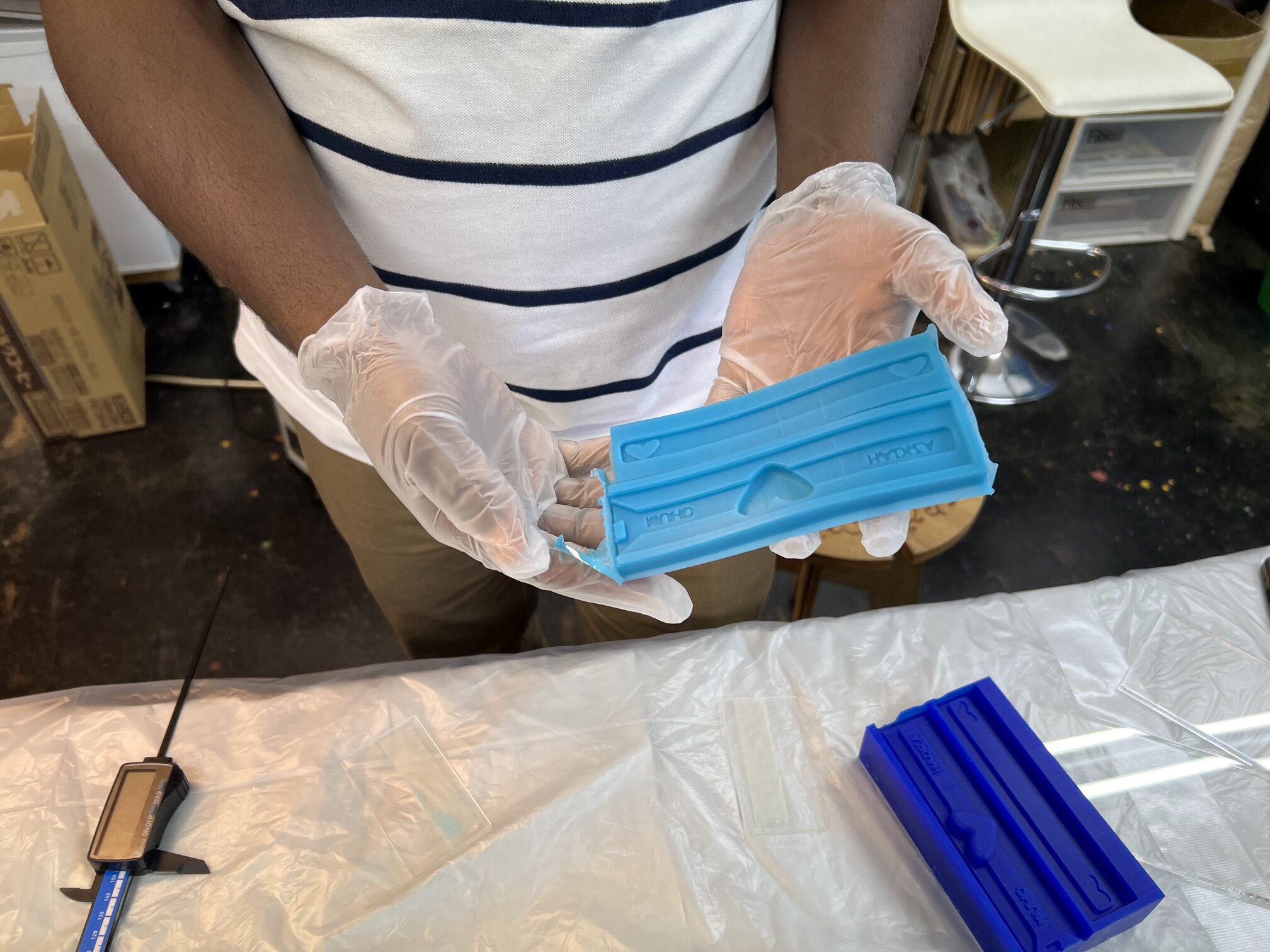
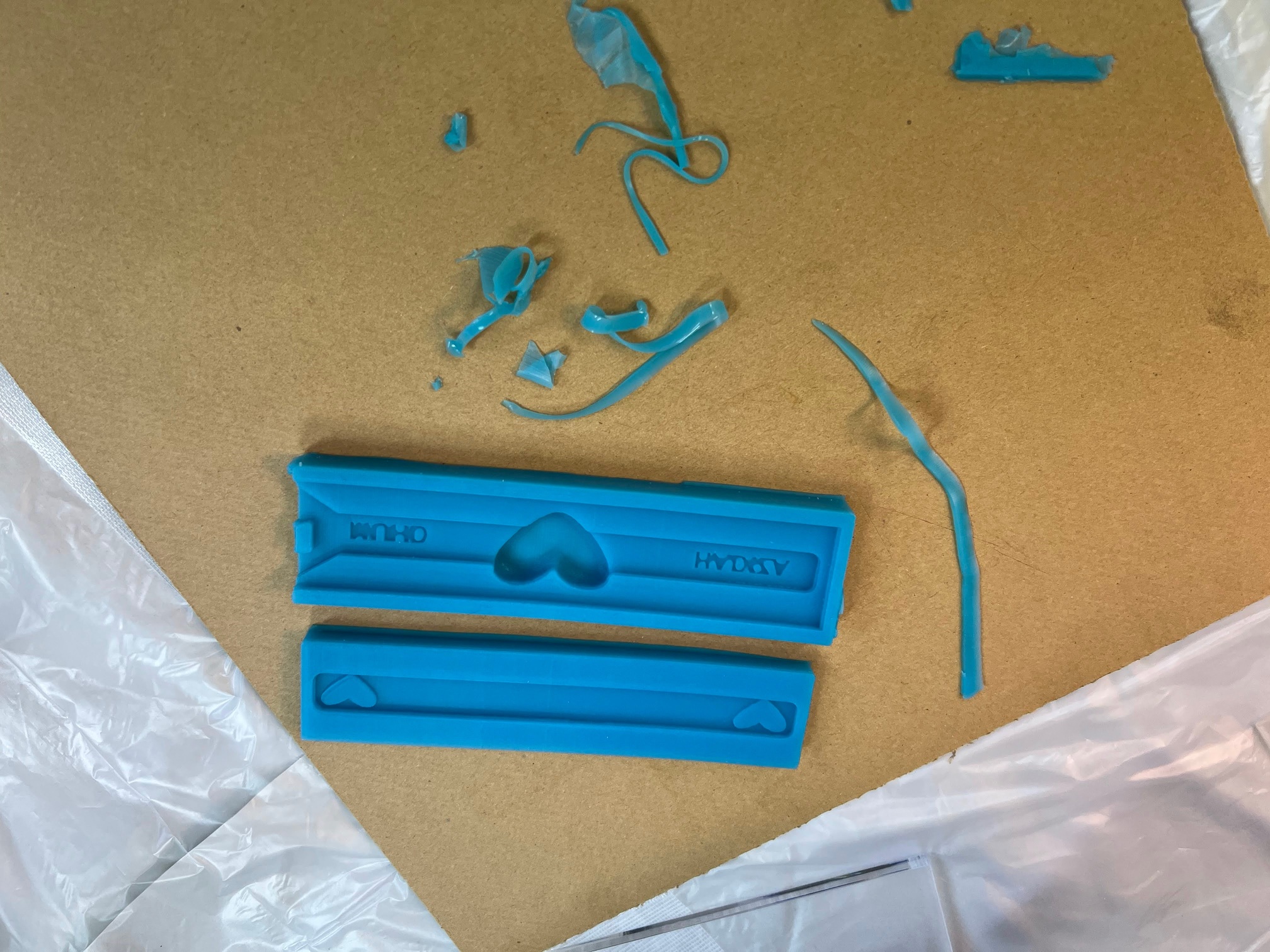
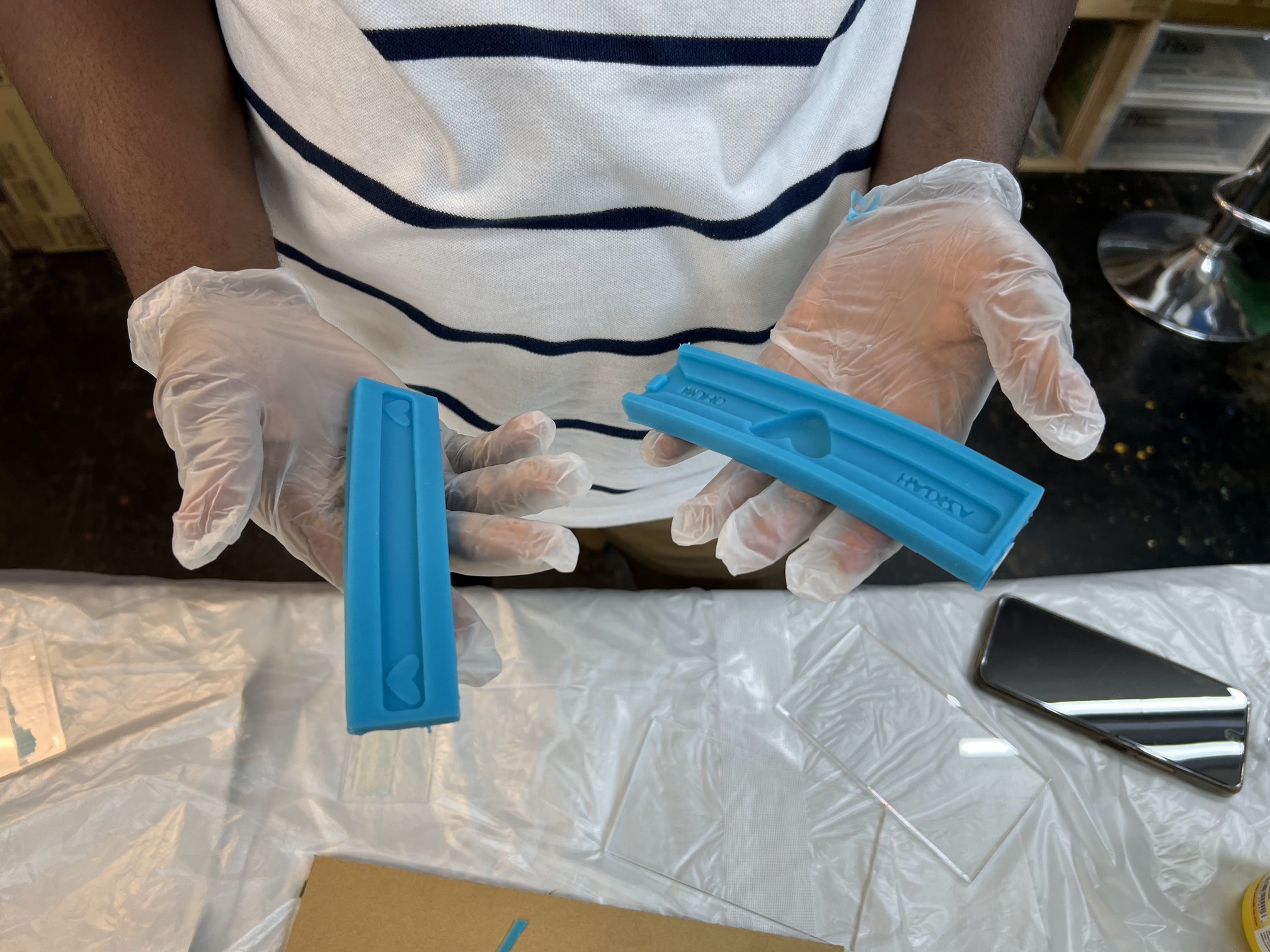
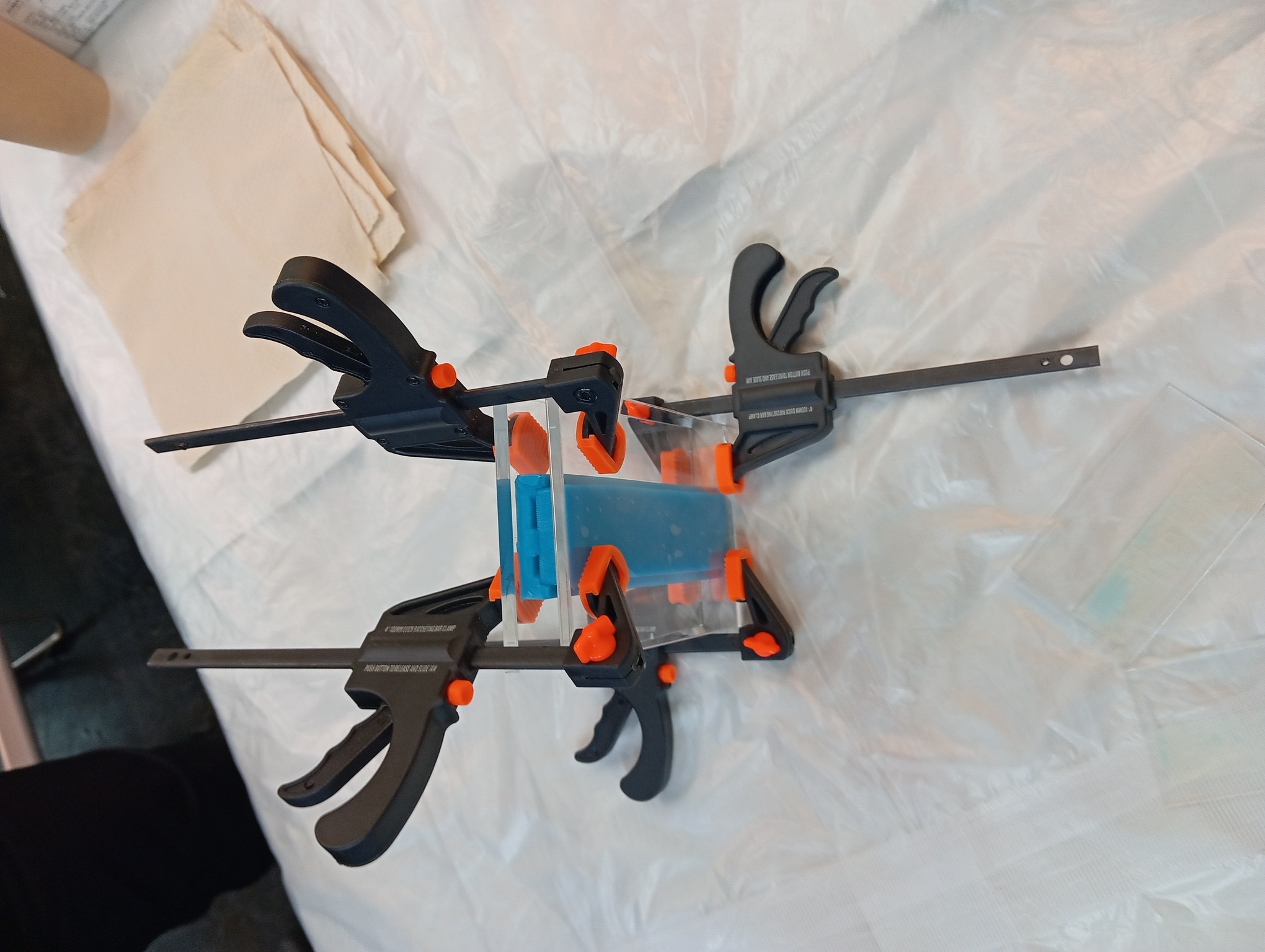
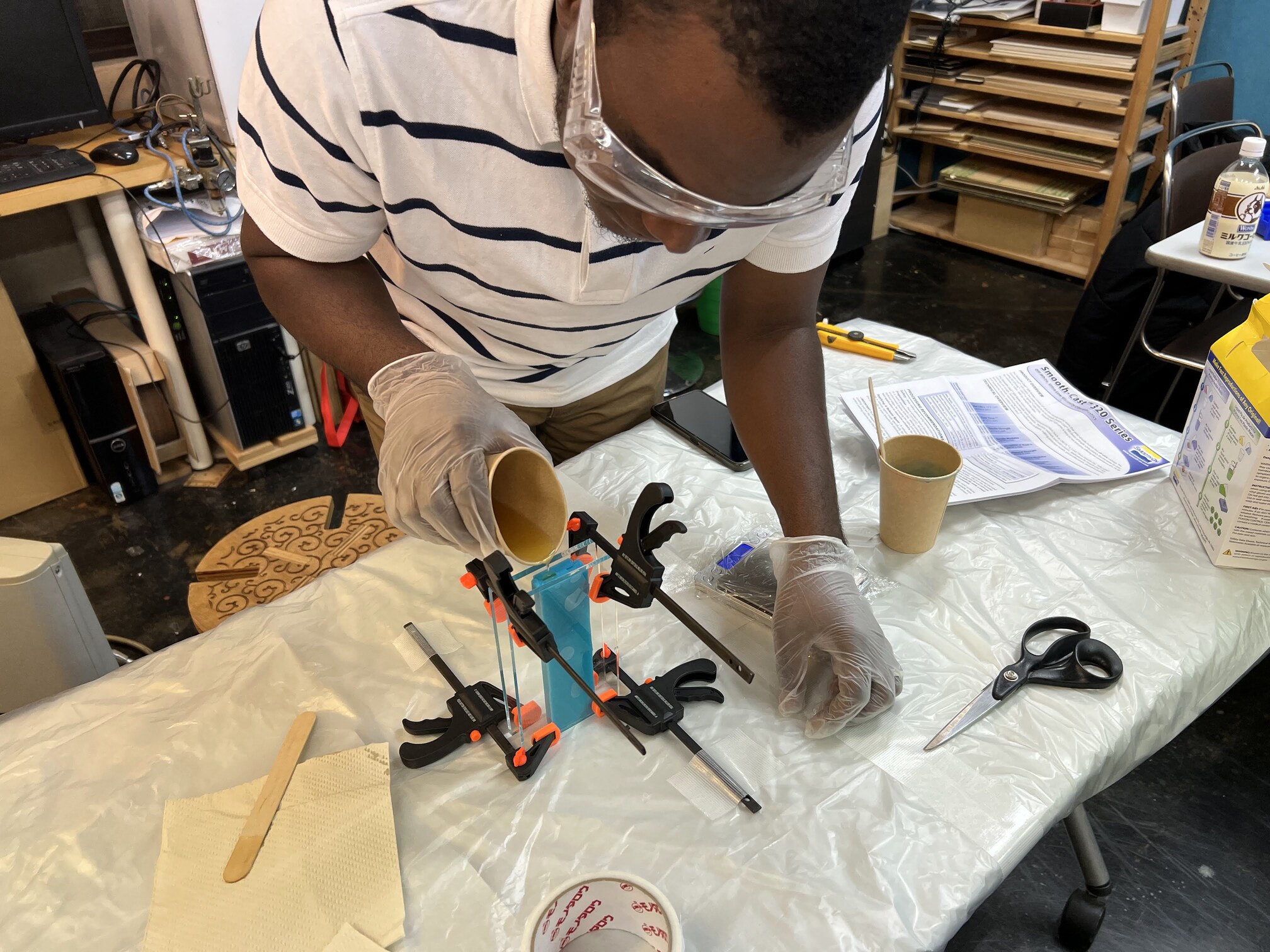
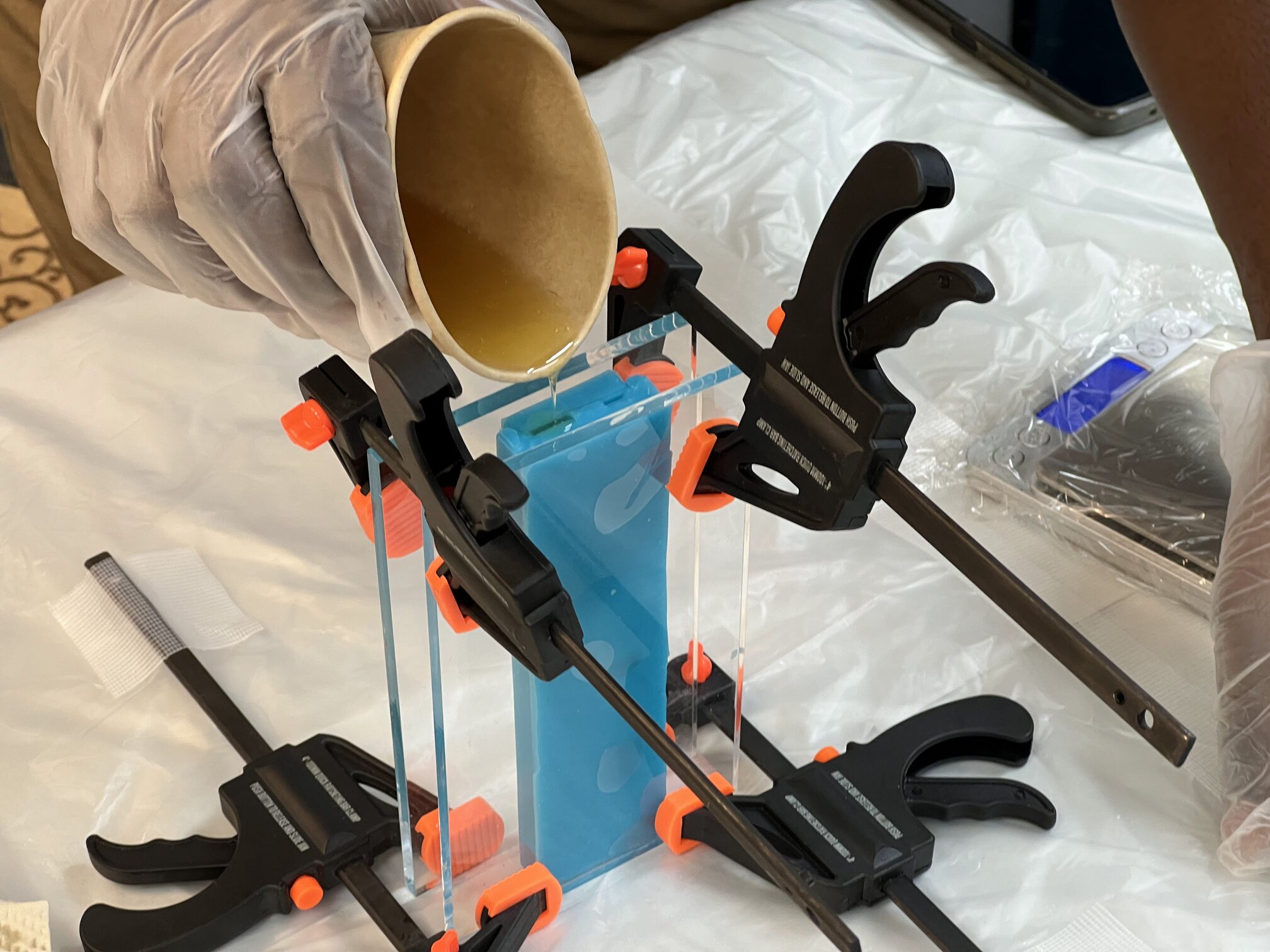
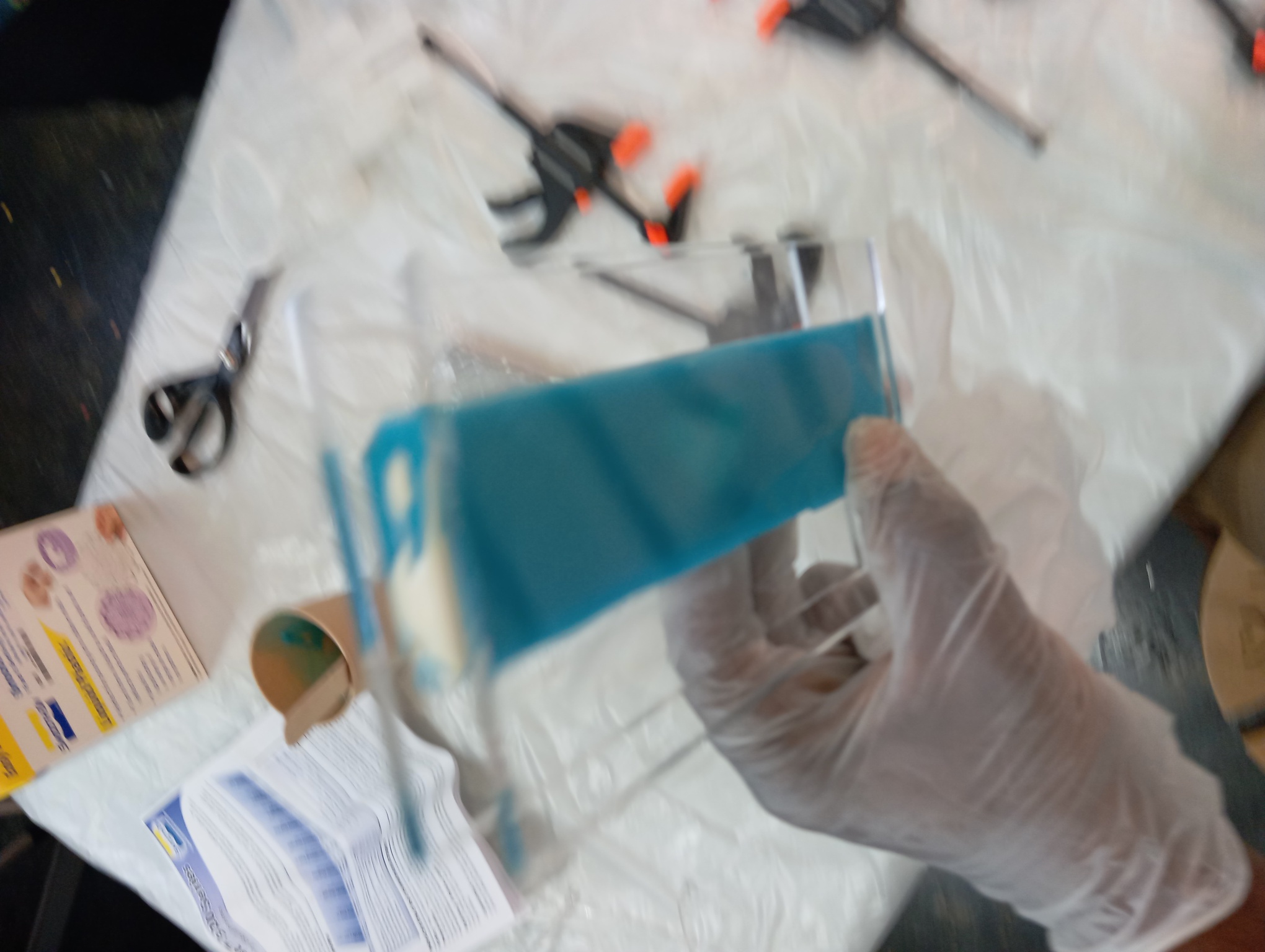
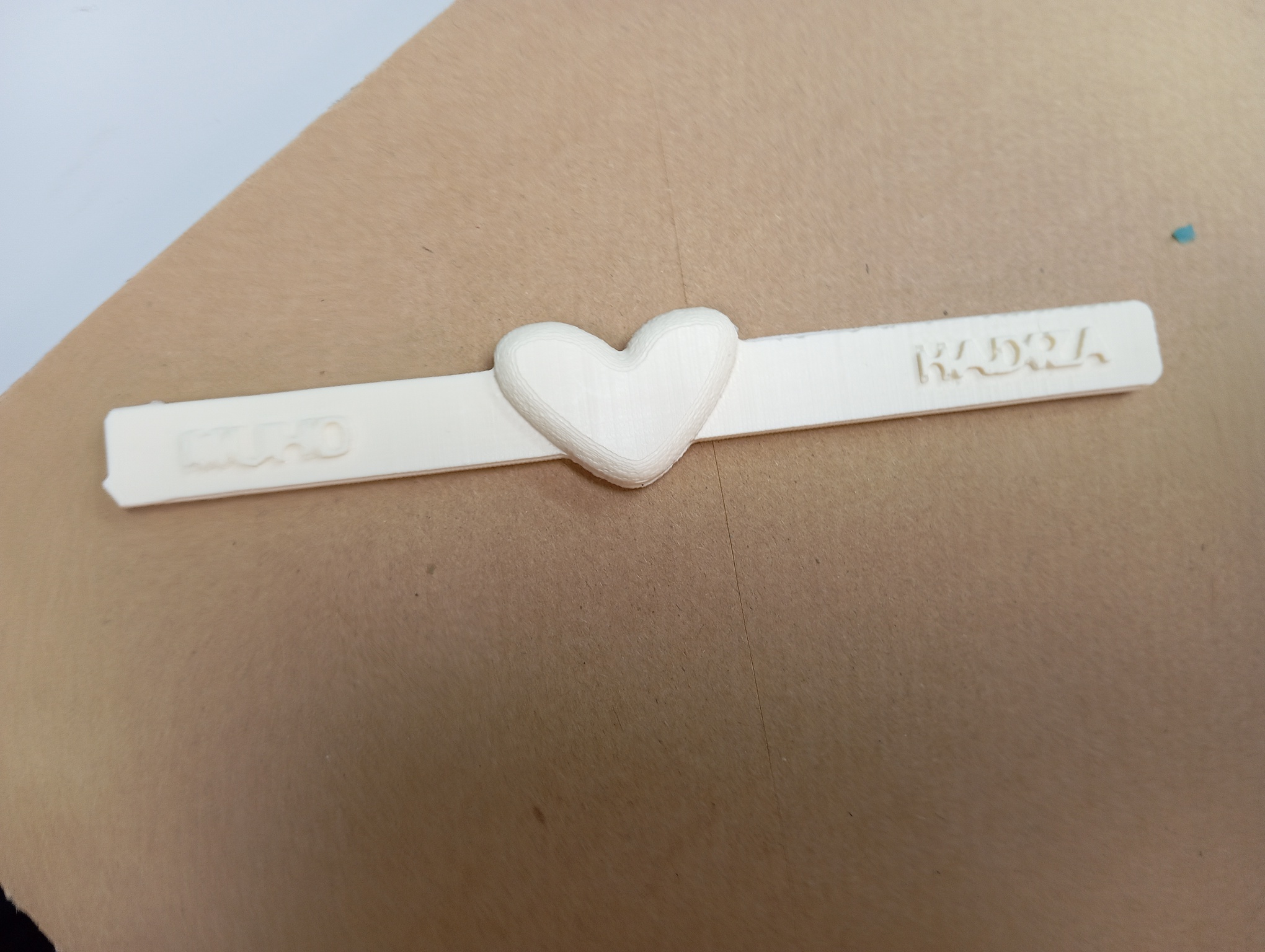
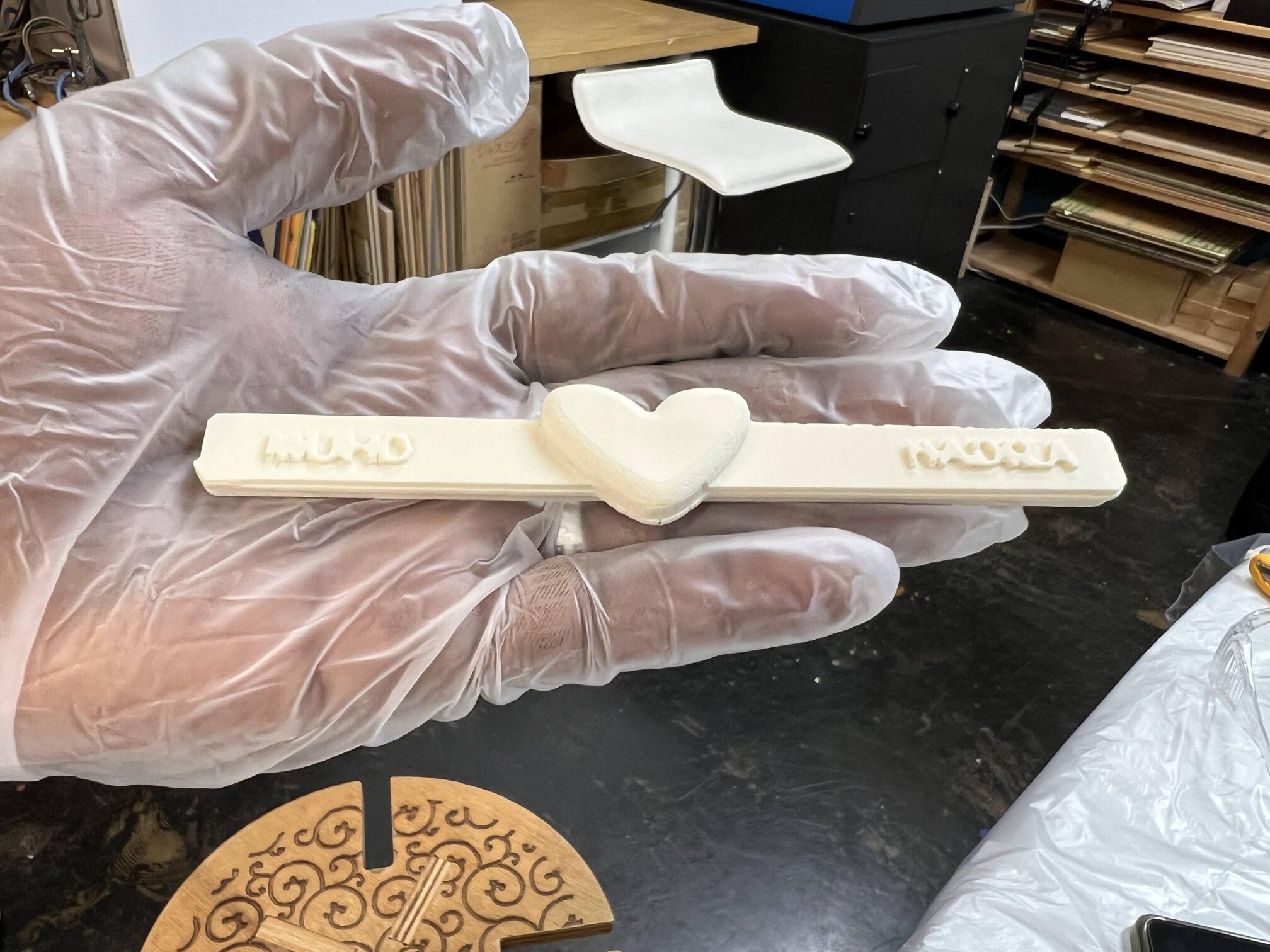
With this i have come to the end of my weekly activity
All source files can be found Here at the side bar.