Molding and Casting
Group assignment
In this week we will use two different types of pourable materials:
2- Smooth-Cast™ 305 liquid plastic.
Before dealing with those materials I had to go trough the datasheet for each material to look closer how to use them and what to avoid.
For the OOMOO™ 25 silicone rubber , to get the best results:
1- Safety : to have safe use we should wear gloves and goggles to protect the skin and eyes from the liquid rubber. Also to make sure the working is well-ventilated(“room size” ventilation).
2- Preparing the mold: including to make sure the mold is well cleaned and free from any unwanted particles, sometimes a sealing agent “barrier coat” like clear acrylic lacquer is sprayed onto the mold surface.
3- Applying A Release Agent: Although not usually necessary, a release agent will make demolding easier when pouring into or over most surfaces, applying a release agent will prolong the life of the mold.
4- Shake well: before using the materials we should make sure to shake the bottles well to make sure the material is homogeneous.
5- Mixing materials: It should follow the manufacturer instruction about mixing ratios, we should mix thoroughly, making sure that you scrape the sides and bottom of the mixing container several times. Mixture should have a uniform color with no color streaks. If we observed color streaks, we should continue mixing until they are eliminated.
6- Shelf life of product: we should make sure to store the material in warm temperature(23°C) and close the lids of the material well after using, this will help to prolong the shelf life of the unused product.
7- Pot life: also known as working time, it is about 15 min, this means that once the two components of the silicone rubber are mixed together, we will have approximately 15 minutes to pour or brush the material into the mold before it begins to set.
8- Pouring: pouring the mixed OOMOO™ 25 silicone rubber should be slowly over the model, making sure it covers the entire surface. it is important to try avoid trapping any air bubbles. The liquid rubber should level off at least 1/2” (1.3 cm) over the highest point of the model surface.
9- Clean up: we should clean up any spills or drips with a paper towel or cloth. Dispose of any unused or excess silicone in accordance with our local regulations.
10- Curing: We should let the silicone rubber cure at room temperature. It usually takes around 75 minutes to fully cure, but the curing time may vary depending on the temperature and humidity of the environment.
11- Demolding : Once the silicone has fully cured, we can remove it from the mold or application. But we have to be gentle and careful removing so we do not damage the mold or the cured silicone.
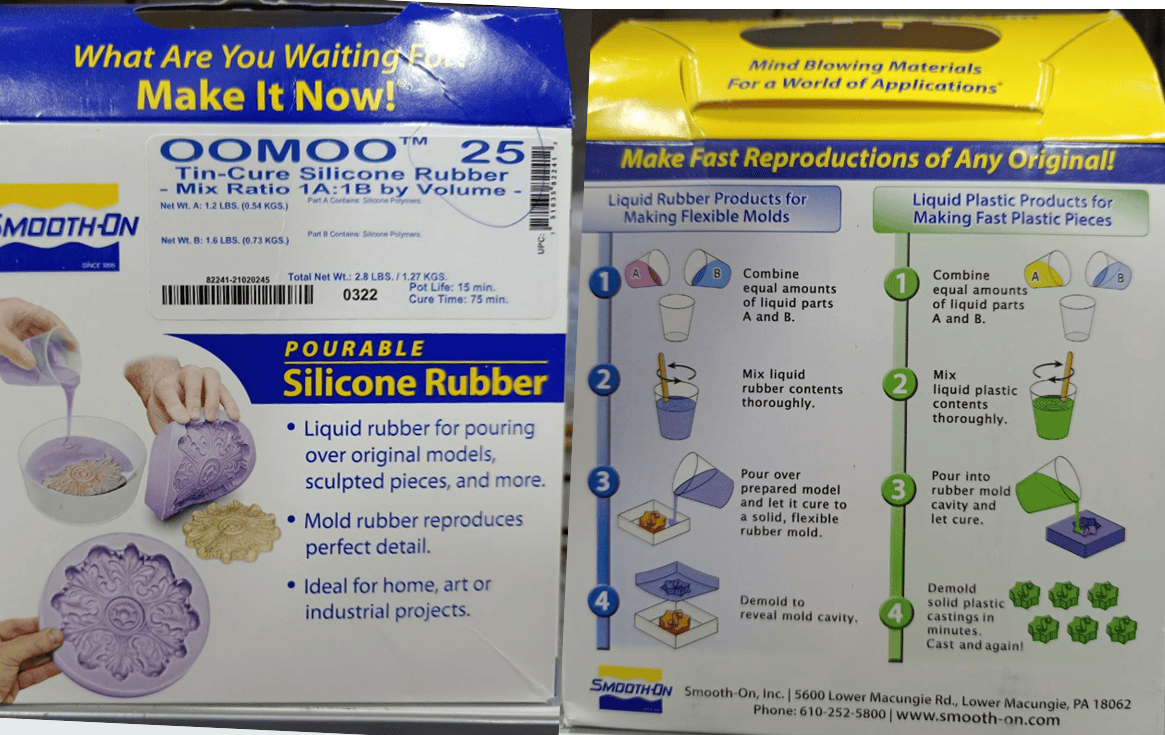
For the Smooth-Cast™ 305 liquid plastic, to get the best results and safe usage:
1- Safety : to have safe use we should wear gloves and goggles to protect the skin and eyes from the liquid rubber. Also to make sure the working is well-ventilated(“room size” ventilation).
2- Preparing the mold: including to make sure the mold is well cleaned and free from any unwanted particles, sometimes a sealing agent “barrier coat” like clear acrylic lacquer or small layer of vaseline is sprayed onto the mold surface.
3- Applying A Release Agent: Although not usually necessary, a release agent will make demolding easier when pouring into or over most surfaces, applying a release agent will prolong the life of the mold.
4- Shake well: before using the materials we should make sure to shake the bottles well to make sure the material is homogeneous.
5- Mixing materials: It should follow the manufacturer instruction about mixing ratios, we should mix thoroughly, making sure that you scrape the sides and bottom of the mixing container several times. Mixture should have a uniform color with no color streaks. If we observed color streaks, we should continue mixing until they are eliminated.
6- Shelf life of product: we should make sure to store the material in warm temperature(23°C) and close the lids of the material well after using, this will help to prolong the shelf life of the unused product.
7- Pot life: also known as working time, it is about 7 min, this means that once the two components of the liquid plastic are mixed together, we will have approximately 7 minutes to pour or brush the material into the mold before it begins to cure.
8- Pouring: pouring the mixed Smooth-Cast™ 305 liquid plastic should be slowly over the model, making sure it covers the entire surface. it is important to try avoid trapping any air bubbles. The liquid plastic should cover all mold areas.
9- Clean up: we should clean up any spills or drips with a paper towel or cloth. Dispose of any unused or excess liquid in accordance with our local regulations.
10- Curing: We should let the liquid plastic cures at room temperature. It usually takes around 30 minutes to fully cure, but the curing time may vary depending on the temperature and humidity of the environment.
11- Demolding : Once the liquid plastic has fully cured, we can remove it from the mold. But we have to be gentle and careful removing so we do not damage the mold or the cured plastic
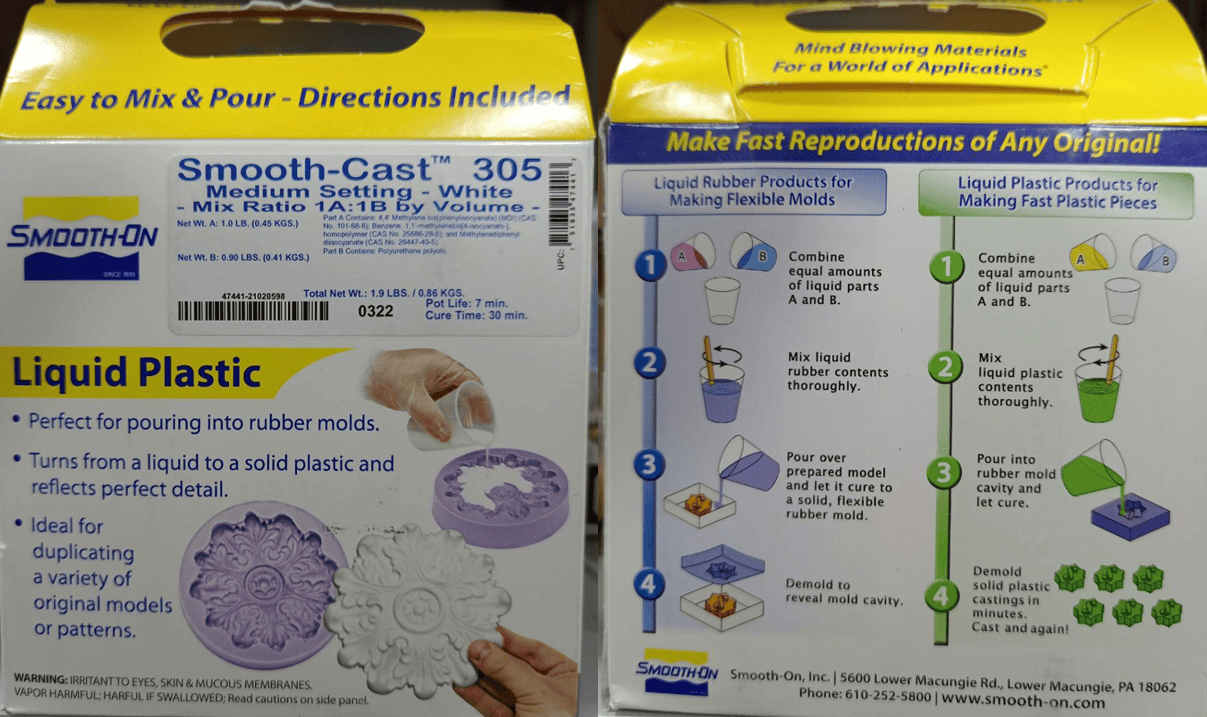
After we go through and learned about the materials we will use, we designed a half sphere mold using fusion 360 and then machined using shopbot and and we silicon and liquid plastic with some colors in a small cups as samples for material.
We fixed the wax block and run the roughing and finishing files as week07, the result of the mold:
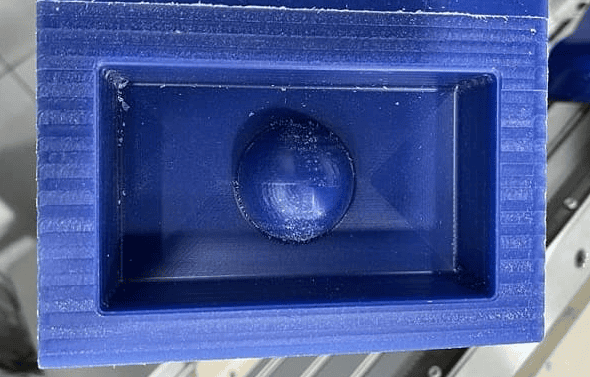
We cleaned the wax mold, and prepare it for casting, we did the silicon casting as I mentioned below in the individual assignment part, the curing time took around 130 min.
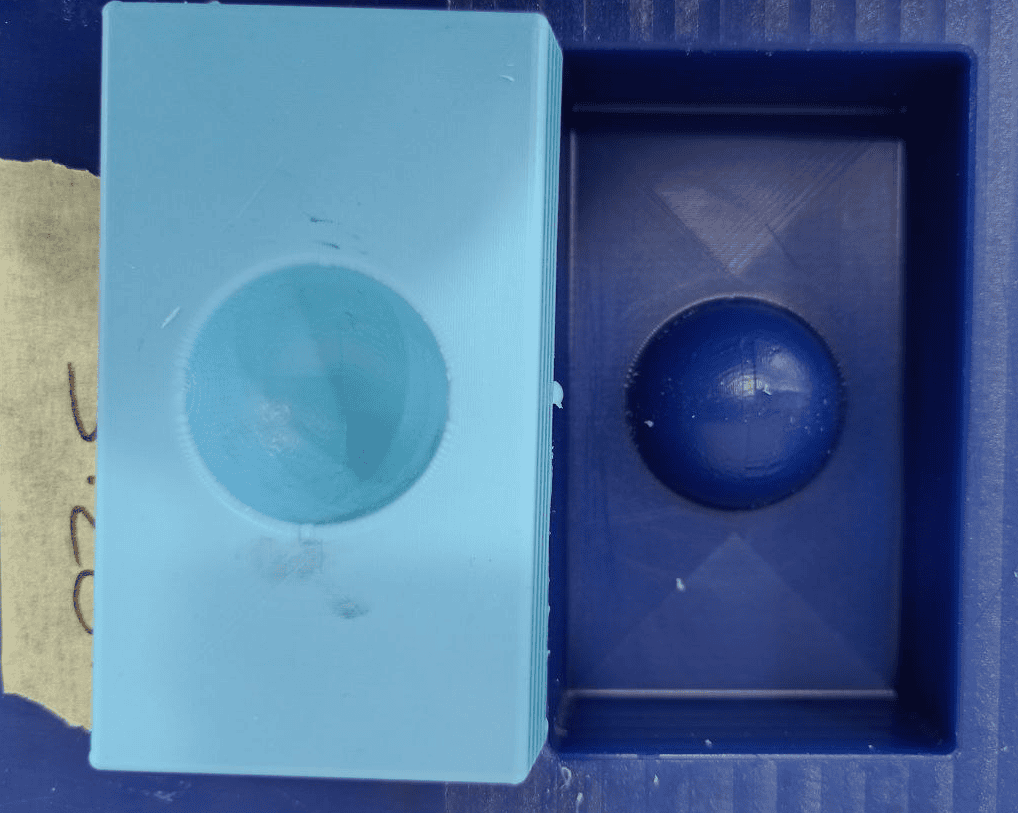
We also wanted to test the liquid plastic material, but we wanted to add some colors, we used SO-Strong™ liquid urethane colorants, we made sure that the colors was compatible by going through the datasheet, and those colors were safe to use with any Smooth-On liquid urethane rubber, urethane plastic or urethane foam except Smooth-On silicones.
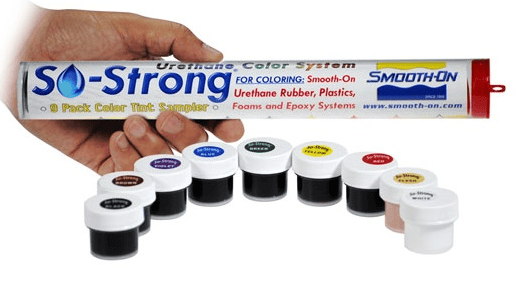
The recommended mixing ratios are between 0.01% - 3% of the total weight (Parts A + B mixed), so we added the color to part B and mix thoroughly then we combine Parts A and B into a mixing container and mix them well before pouring. (this step also explained below in the individual part).
The result of testing was great, all of them cured after around 22 min, we noticed that the liquid color after mixing without adding any colors was pure white.
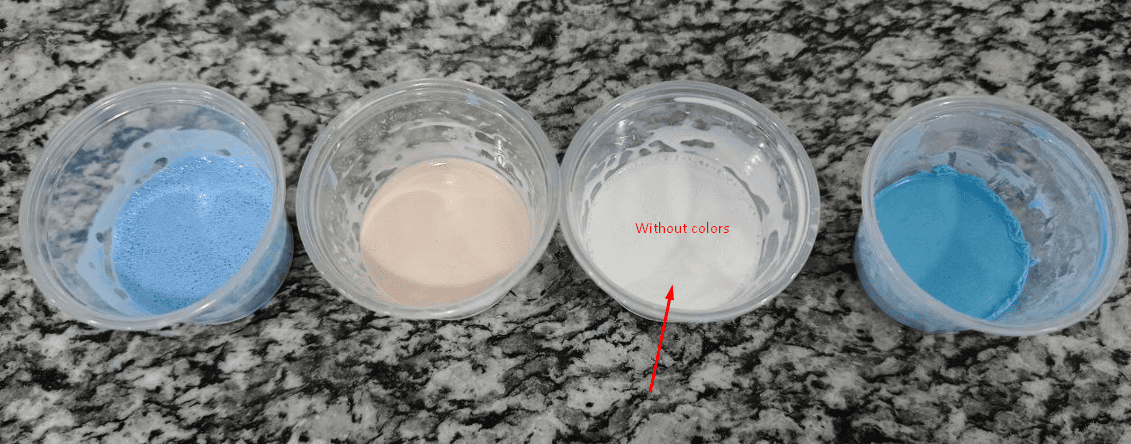
As a result, we recommend always to go through the datasheet for any material and stick with the manufacturer recommendation to have a safe use and good results!
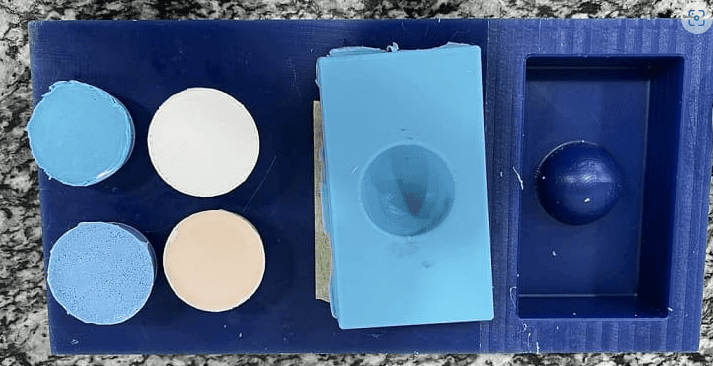
Individual assignment
For this week, I want to make a mold to produce a rectangles of plastics, those rectangles will be used as a game challenge for different ages!
I designed the mold using fusion 360, first I made a 2D rectangle then using extrude I set the height of the piece 70 mm(heigh of the machineable wax stock), then I made the corners as a fillet to make the removal of the silicon from the mold after casting easier.
Worth to mention that the extrude was not straight, because it is advisable to avoid sharp corners or angles of 90 degrees so I set a tapered angle equal to 5 degrees before extruding:
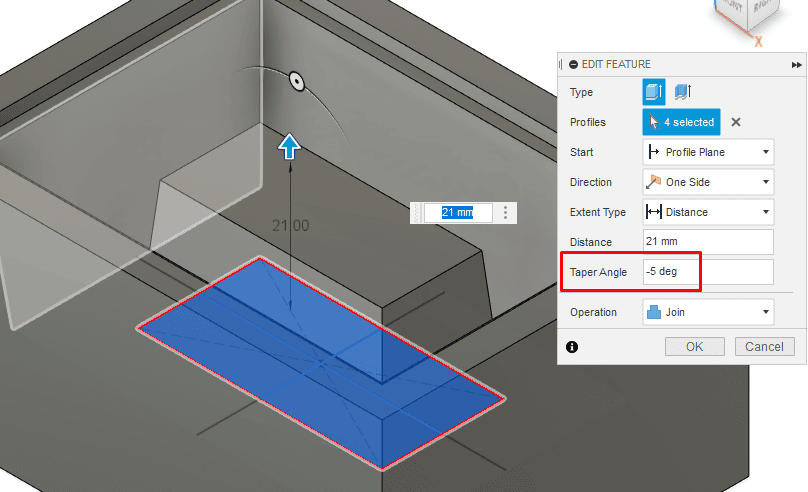
The video below summarize the designing process:
After designing I exported the model as .stl (as I mentioned on week05) then I opened the vcarve program to import the model and prepare the cam for the machine (more details on week07).
To import the 3D model to vcarve, from drawing list I set the job size dimensions, then I set the material as blue plastic as follows:
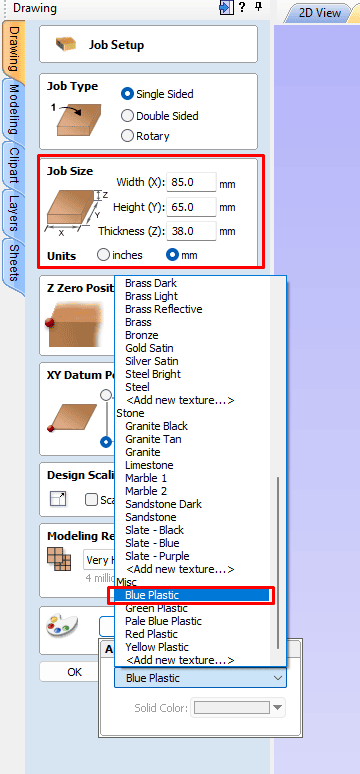
Then from modeling list, I chose the model, I set the initial orientation, centered the model then position and import:
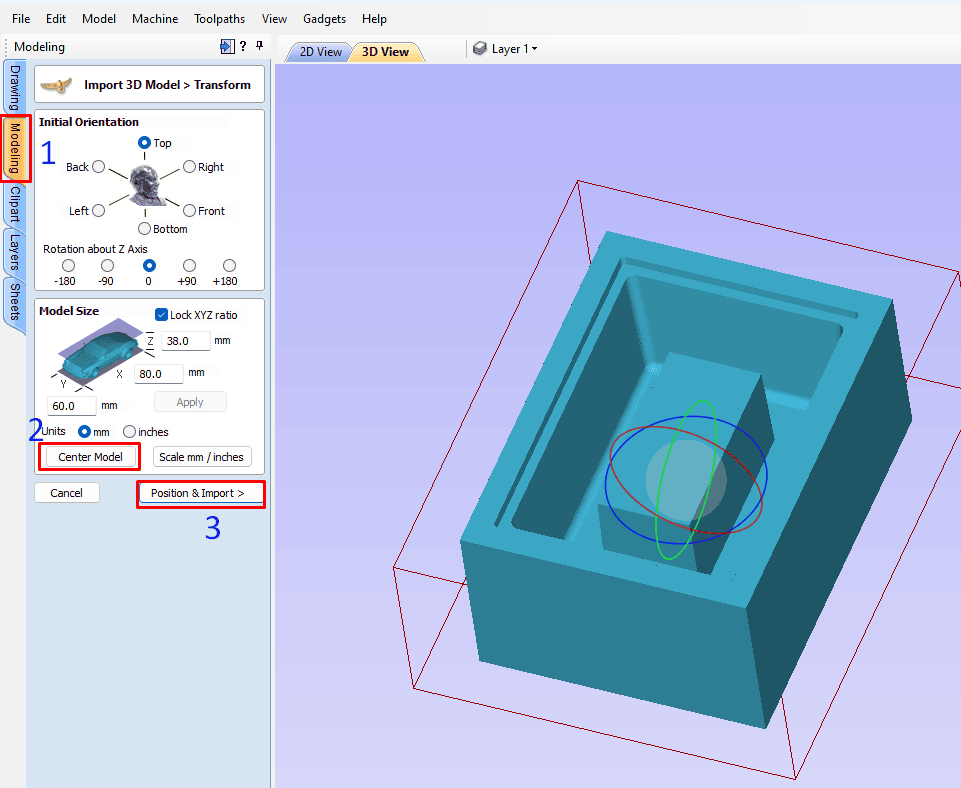
Last thing was to position the model relative to the jop workpiece, so I set the depth below top, then imported the model:
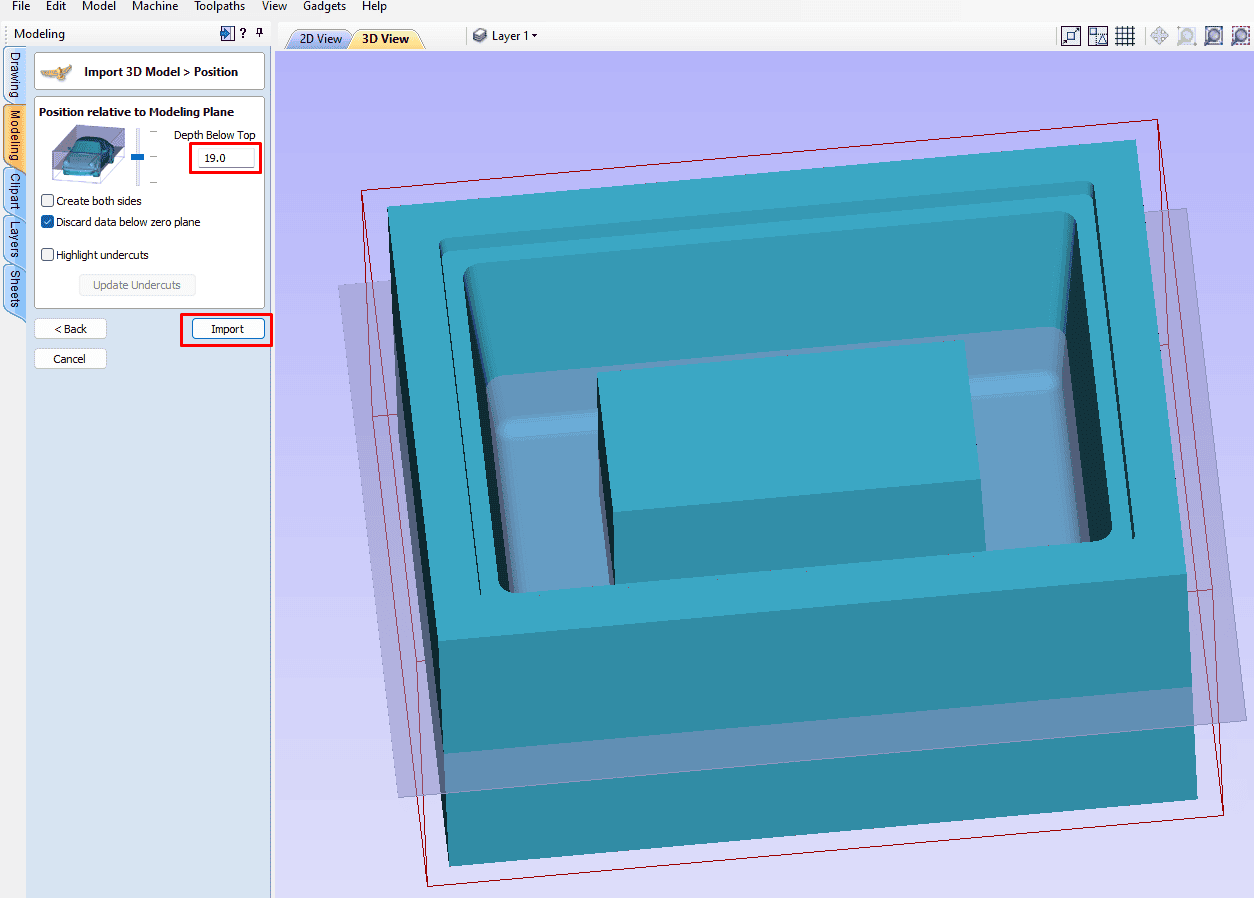
Now it is the time to make the toolpath, the toolpath will be divided into two steps:
1- Roughing toolpath: during this operation the cutting tool will remove large amounts of material from the workpiece at high feeds and speeds with no worries about the surface finish for this step.
2- Finishing toolpath: during this operation the cutting tool will remove any remaining material and achieve the final desired surface finish.
For roughing operation, I opened the toolpath tab, then I have chosen the 3D roughing operation:
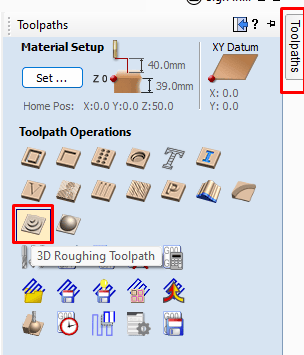
I have used the 1/4 inch flat endmill double floats with the following settings:
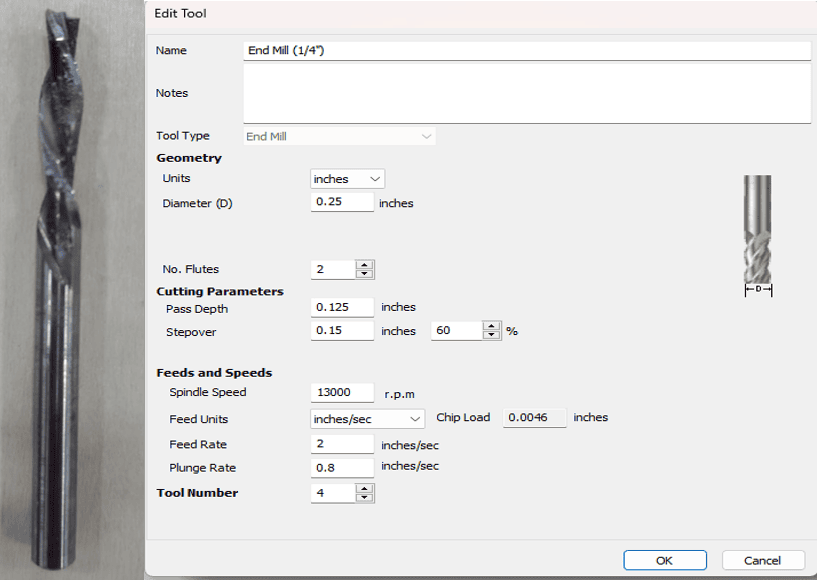
The machining Limit Boundary: for this operation I have four types:
1- Model boundary: The combined boundaries of all the components in this job are used. This is the area of the composite model which has components on it. Note: this is not the boundary of the selected models.
2- Material boundary: The boundary of the entire material block is used.
3- Selected vectors: Selected vectors are used as the machining boundary.
4- Selected levels: The combined boundaries of all the components on the specified level. This is similar to Model Boundary, but only specific to the named level.
For the remaining parameters, I set the machining allowance to be 0.5 mm, this means the toolpath will remove 0.5mm extra from material, and when we start the finishing toolpath it will start by 0.5 mm above the surface, this will help to get better surface finish.
Roughing strategy: for this operation I have two types:
1- Z-level: the toolpath will be move like steps, starting from the top layer to the last layer.
2- 3D Raster: the toolpath will follow the shape of the workpiece this will help to get closer to the final shape.
The ramp distance will be equal to 14mm (usually it is 2-3 times tool diameter), while the safe z will be equal to 40 mm.
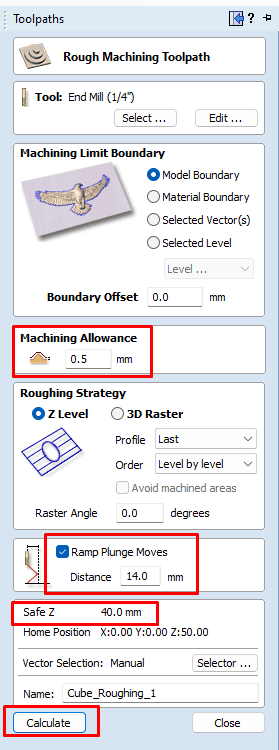
After calculating, the result shown below, it is notable how the steps of the roughing toolpath looks like:
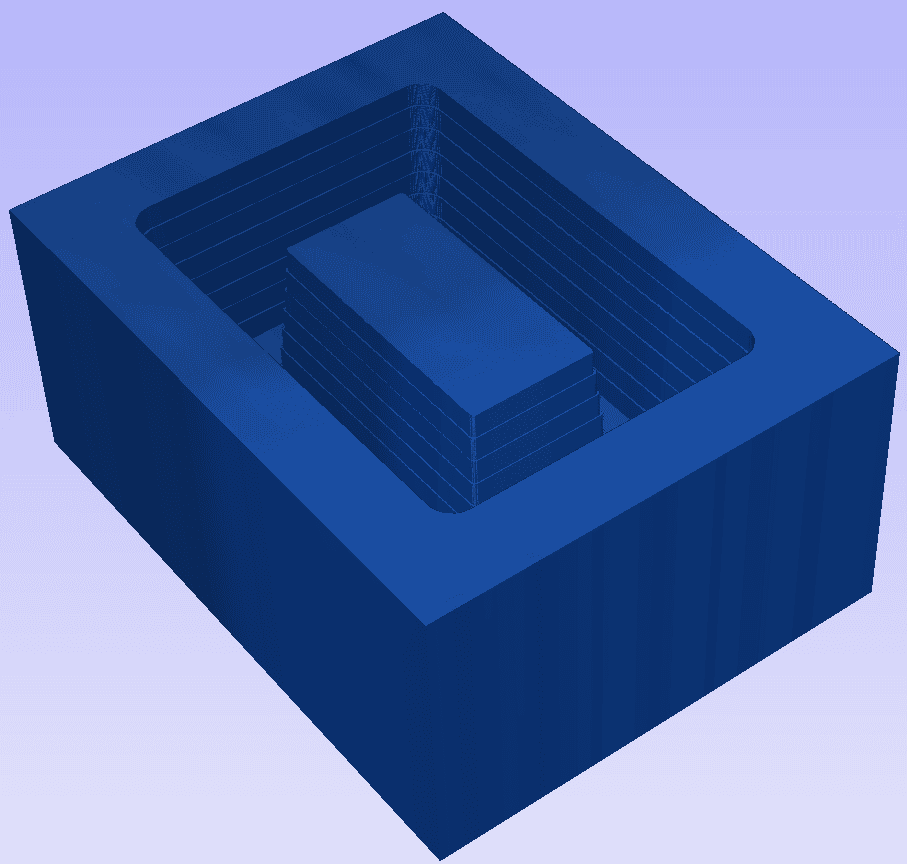
For finishing operation, I opened the toolpath tab, then I have chosen the 3D Finishing operation:
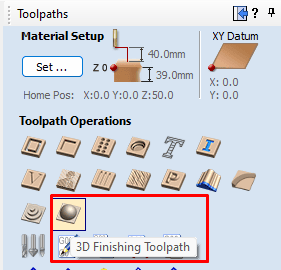
I have used the 1/4 inch tapered ball nose with the following settings:
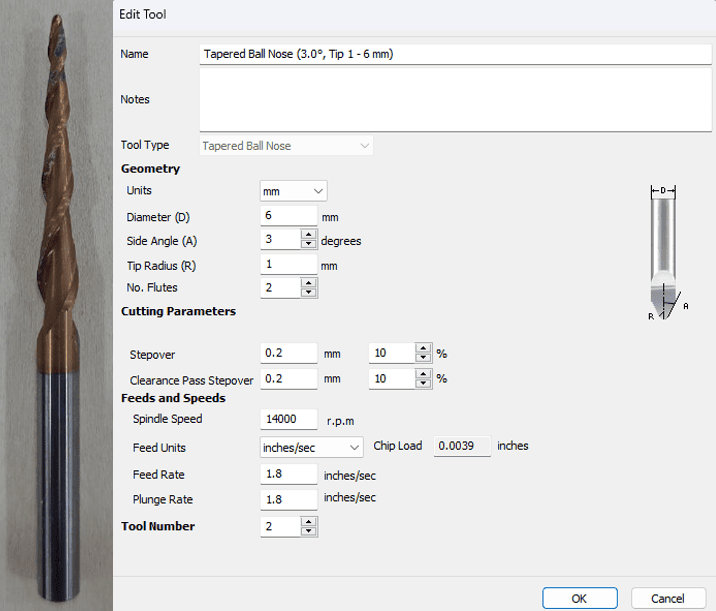
I have chosen the model boundary, while the safe z will be equal to 40 mm.
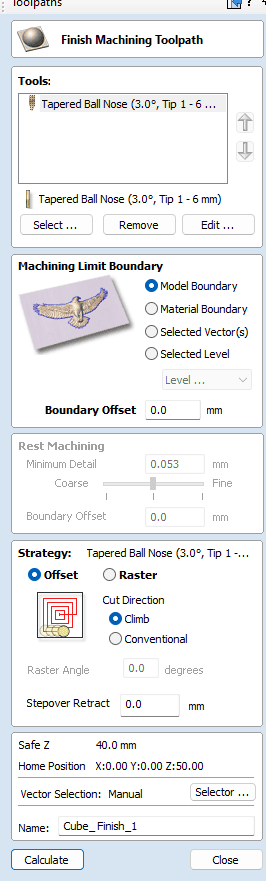
After calculating, the result shown below:
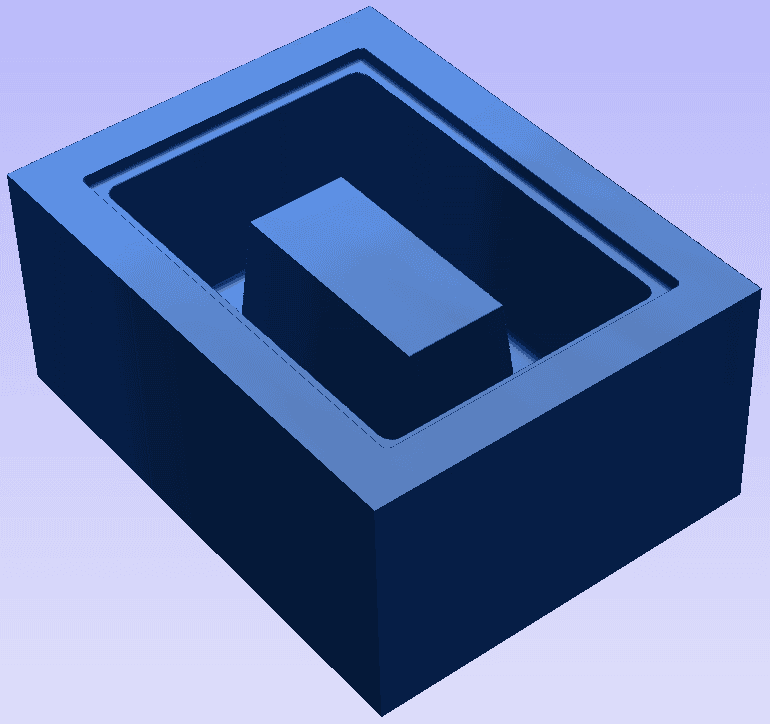
The roughing and finishing tool path:
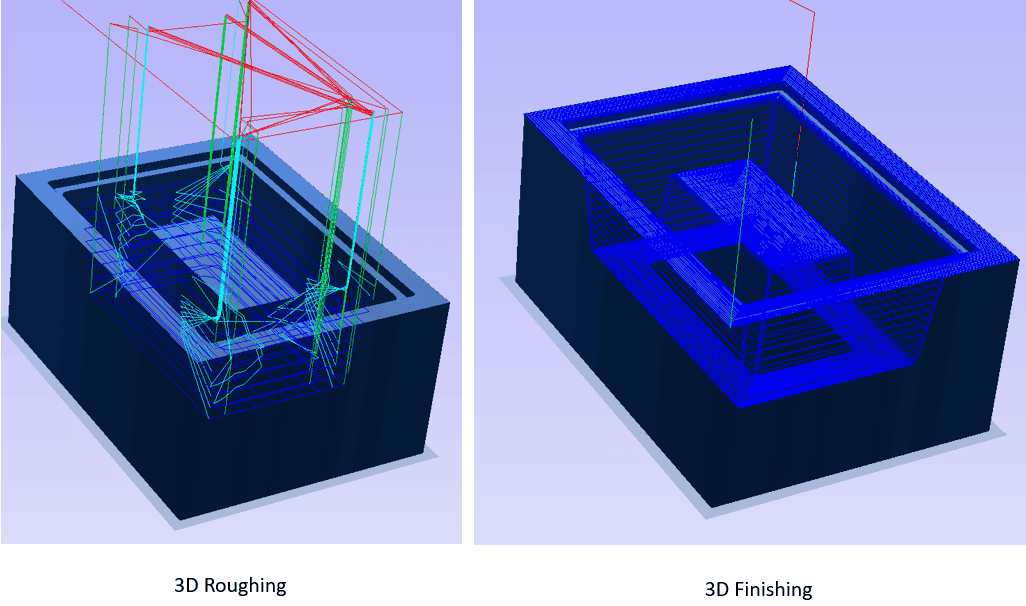
After calculating, I saved the toolpaths to send them to the machine:
I prepared the wax block and fix it to the sacrifice bed, then I changed the tool to the roughing endmill then I zeroed all axes as week07:
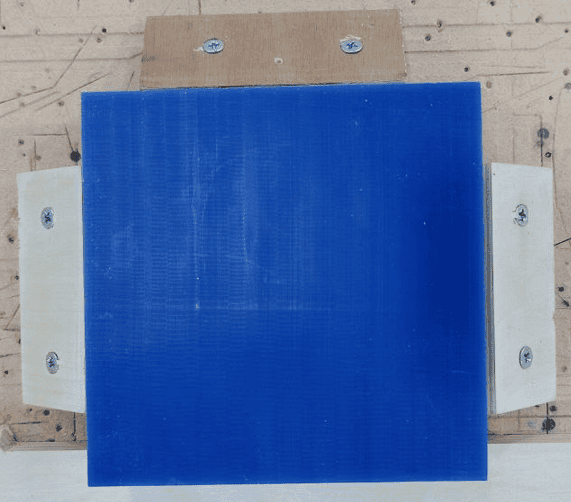
Unfortunately, The vacuum was not able to suction all wax machined in the deepest points, so the machined wax on some areas milted and stuck and this cause to not have a good quality on the surfaces, anyhow I tried to remove the remaining wax manually while trying to avoid scratching the mold itself.
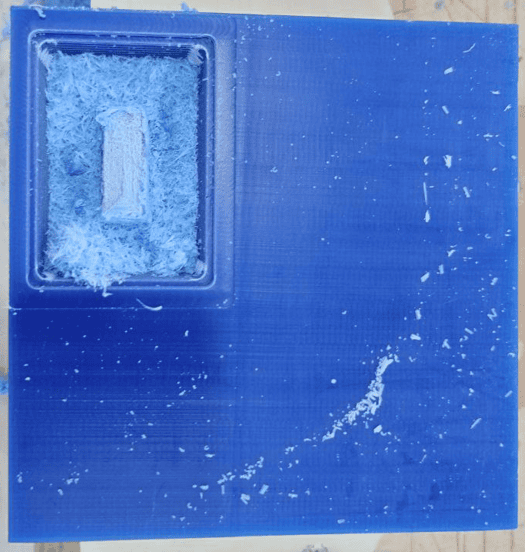
For the next step, I have changed the endmill to the finish endmill then re zeroed the z axis and run the finishing toolpath, I tried as much as possible to clean the mold after milling, the result is shown below:
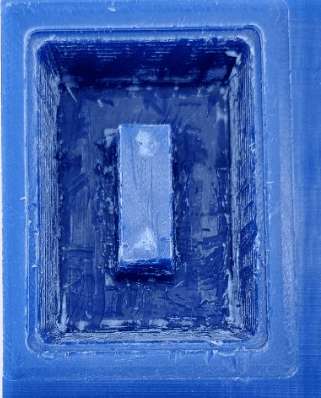
To prepare the mold for casting, I followed this procedure:
1- I prepared the mold, silicon rubber, electronic scale and some cups.
2- I put the cup on the scale and I zeroed the scale to the weight of the cup so it will not included in the mixture weight.
3- For the mix ratios, it will be by weight, each 1 gram from part A, I will put 1.3 grams for part B, so I weigh 75 grams from part A and 98 grams from B.
4- I mixed them will, with trying to make the stir slow to avoid introducing air bubbles to the mixture.
5- After mixing, I poured them in the mold slowly and I shake the mold well to make the mixture take the whole shape and to make the bobbles escapes from the mold.
6- I wait for 75 min for curing as mentioned in the datasheet, it was almost cured but still a little bit sticky, I think because it was a bit cold, so I have waited another 30 min just to have safe removing without damaging the mold or the casted one.
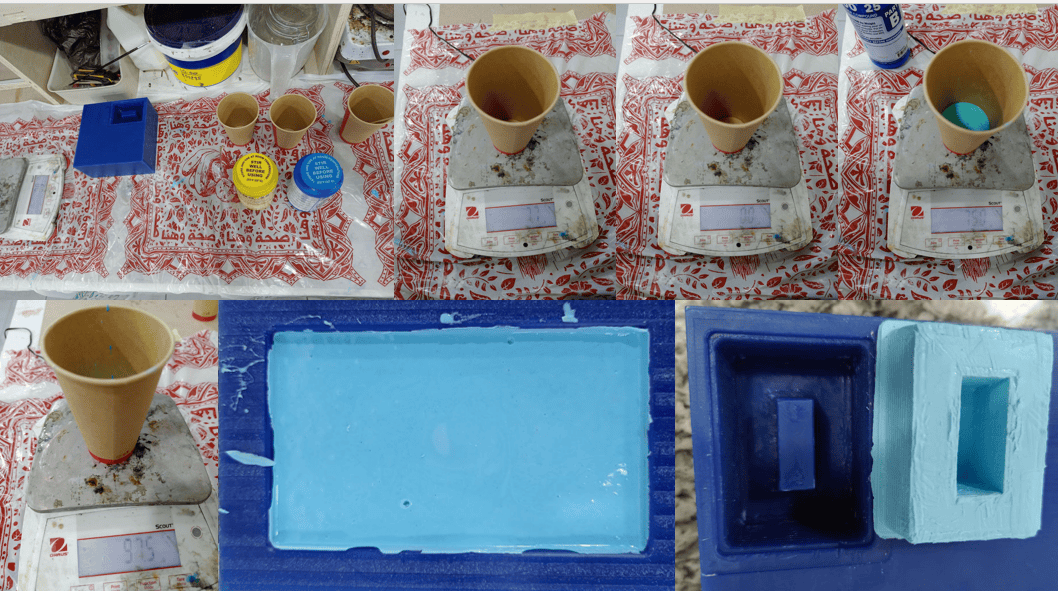
To prepare the casting with liquid plastic:
1- I prepared the electronic weight scale, silicon mold and some cups.
2- To have precise measurements, I used a syringe, making sure that each part should have it is own syringe, this is important to not contaminate the parts bottles.
3- I zeroed the scale on the the cup, the weight ratio was each 1 gram from part A, I will put 0.9 grams for part B, so I weigh 7 grams from part A and 6.3 grams from B.
4- Before mixing, I used a small drop(0.2 grams) of the liquid urethane colorants then I mixed them properly.
5- I poured them into the mold, and I waited for 25 min to have it fully cured, I noticed that the black color became dull a bit (turned to gray), I think it should to increase the amount of the color, up to 3% of the total weight.
6- For the other parts I repeated the same procedure.
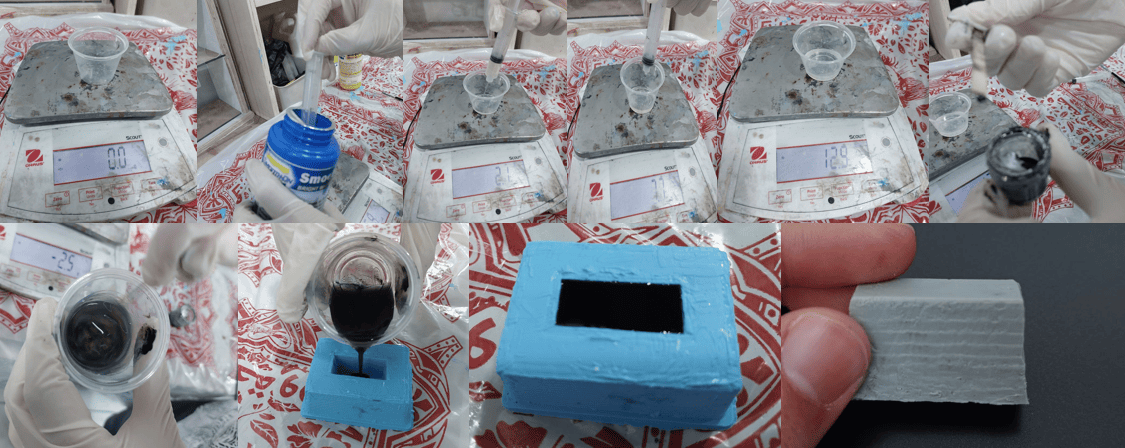
till now I made those, planing to make more in the future to make games more challenging!
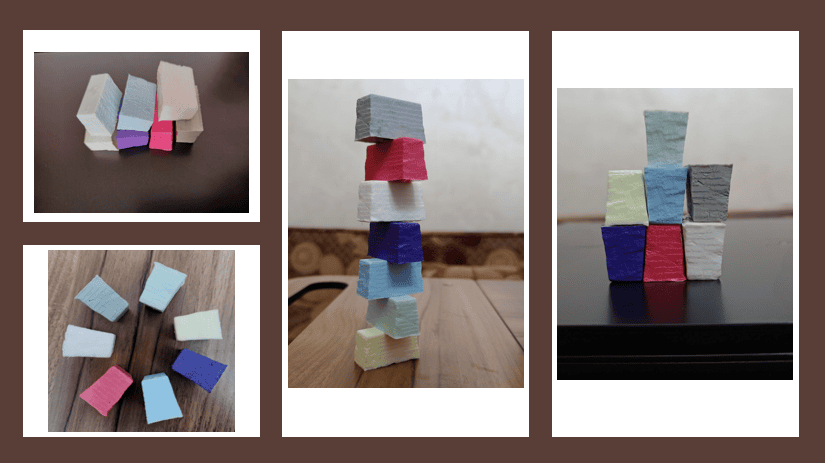