wk.12-Composites
Designing the shape
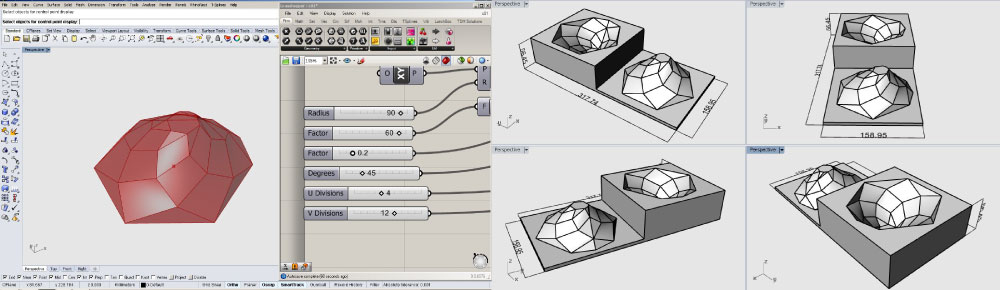
I started this assignment with the design of element, i proposed a panelized shape for the exploration the formal possibilities of my final project "interactive dynamic lamp " (in this case i explored the shape the superior part of the lamp), I developed the element in the Rhinoceros3d software, with the Grasshopper plug-in and his complement WaveBird (complement for the panels generation). . I forced me to project two models systems "positive and negative", take this election because i seemed that this system would get a much detail in the final shape.
Cut process generation

Created the 3d model of the piece, I proceed with the configuration of the cut process in the "Shopbot" software "Patworks 3D", where i've selected in first place by recommendation of the local instructor, the work material (high density polyurethane), after this i put the parameter for an optimal milling of the object designed, following the step by step of the software interface, for the cut process i used 2 milling tools (1/2 inch for the roughing process and the 1/4 for the finish).this for the speed in the process execution, i used in the first tool the following parameters, pass depth=0.5, stepover=0.125 or 50%, spindle speed=12.000rpm, feed rate=5.0 inch/sec, and plunge rate=1.0 inch/sec

In the second tool i configure the parameters this way, stepover=0.1125 or 45%, spindle speed=12.000rpm, feed rate=5.0 inch/sec, and plunge rate=1.0 inch/sec.
Work material #1

In the same way that the previous steps by recommendation of the local instructor, the team worked with the "high density polyurethane", because this material is very smooth for the milling machined, rigid and his composition (if one do prepare correctly) is not heavy. This product is formed by two substance, "Polyol" component A, and "Isocianato" component B, the substance is prepared with a mix in the equally proportion of the two previous components.
Polyurethane mix preparation

In this sequence of pictures, the "fab team" prepared the polyurethane in equally four parts, (each one of 250g approximately), "but if you're interested in more specifications, you can download and check this spreadsheet with the proposed formula for the mix dosage"

After of the mixing process, the team poured the substance in the formwork (the material of the formwork was plywood with raincoat layer). I think and suggest that the pouring process is made efficiently in the formwork corners, because the material can fill the entire piece.
"Human counterweight"

As curious aspect, the chemistry reaction of the substance "the polyurethane" is very powerful, by the so fast growth of the foam, and as it was able to lift and support six people.
“Milling horror”

I thought that my polyurethane high density mix was going to work perfectly, but i realized that the preparation had errors, because in the milling process, the piece to machining haven't the correct density for the desired definition. and his fixing in the work surface, resulted in a difficult and tedious process, that resolved with the screws in the edges of the element and with double sided tape in the bottom.
And why the wood was the best option?

By the result of the previous piece to machining, i decided used a material that i worked in anterior locations, and that know how functions, for this the "fab team" shared with me the decision of machining all the pieces again in the wood block. "this process resulted with the improvements in some detail of the final molds".
Cut process of the surface cuirass

I did the cut file using the rhinoceros command "smash and unroll ", this command allows me obtain the exact shape in a plane of all to cut surface, and after this I extracted all the contours or edges for the laser cut process.(i ordered the file in layers and colors by the sequence to the assembly elements). I selected how work material for this process the wicker because is a inexpensive material and of easy consecution.

After the previous process the "fab team" prepared the resin mix (mixing the compound A and B in equal amounts), for his application in the wicker surface.(i recommend apply two layer for each part).
Final piece

This is the result of the two molds used, and i think that elements worked really good for a reliable shape and accord with the digital model "not so exact for the election for the milling process" but if for the mold machining result.