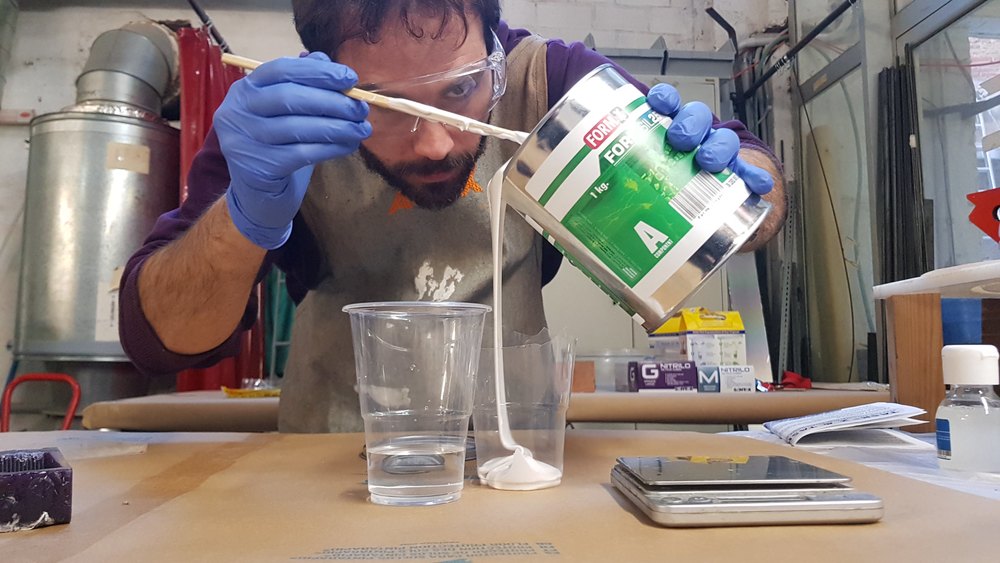
Molding and Casting
Week 10 - Molding and casting NOTES
Here you will find my work description during this tenth week
General info
Class notes
Molding types
- Injection molding
- insert molding (See Bas exemple)
- Soft molding (See this excellent assignment)
- Multiparts molds (see hypercude exemple)
- Registration like this
Vendors
Materials
- Amaco flexwax
- Machineable wax (reusable)
- Rigid foam (for big molds)
- Activa
- Clear Rubbers(?), epoxies,
- Silicon (OOMOO High res)
- PDMS (very hogh res atomic size)
- Latex (not recommanded)
- Plaster (calsium sulfate)
- Drystone
Recommandations : strat with OOMMOO then Drystone
Bismuth Alloy Talk powder helps surface tensions
- aluminium (be carefull)
- glass molding with wet wood
- Food safe -chocolate, candies
Additives
- glass peers ?
- fibers
- dies for colors
Processing
-
The first thing you should do is pick your material and test a little cast to check that mold and cast are compatible (testing)
-
Mixing silicon OOMOO is 1 to 1 (no lost) non need to mesure hydrostone (be carefull at the state change)
-
Pouring it : Be carefull to not trap air, avoid bubbles, shake it (vacum chamber or overpressure, shear, learn to mix resin
-
curing Reactions ! bad: mixing too much material, starts heating (can melt the container)
Pot life (time to cast),
-
demolding flexible mold are easier to remove
-
storage Be carefull at the material working temperature
Google image : smooth-cast color match
clear workspace, clean containers
Safety
Story about Clear / epoxy (crystal clear extremely toxic)
- Always Read the SDS Safety datasheet
- Wear gloves
- Eye protection
- Cloth protection
Disposal
Machining
Much higher surface resolution
3 axis machining
Rough cutting (use 2 axis at the same time) finich cutting (use 3 axis)
tooling Xtra long shaft micro endmills long neck micro endmills (combination of both - very fragile) ball end mills
it’s important to design the mold around the tool
We have to design around the tool
Idealy the flute diameter match the shank
flat end mill for material removal (rough cutting) ball end mill for finish cutting
BUT a flat endmill and ball endmill can make a smooth surface if you move using the 3 axis at the same time
be carefull of collisions
Sofwares
VCarve Fusion has 3 axis cam fabmodules (using gradient or STL) mesh->RolandMill->wax rought cutting mesh->RolandMill->wax finish cutting
We need a in hole to fill and a out hole
google “How to read SDS” tutorial on cba
Rigid mold to flex mod to cast
Good to see :
Troxes johathan bobrow - automatiles nano imprint lythography
Stay in touch
Hi, I'm
Joris Navarro, from Perpignan (France), a proud dad, a fab director/manager, a teacher, a ceo, a FabAcademy student, but not only. Click here to know more about me.
Check my work for FabAcademy on FabCloud GitLab
@joris.navarro.
Want to say Hi ? Please send me a message.