Individual Assignment
Design and produce something with a digital fabrication process (incorporating computer-aided design and manufacturing) not covered in another assignment, documenting the requirements that your assignment meets, and including everything necessary to reproduce it. Possibilities include (but are not limited to): composites, textiles, biotechnology, robotics, folding, and cooking.
Individual Assignment
Defining Composites
The definition of a “composite” is two or more materials that are different physically or in their chemical properties. When combined together remain separate and distinct at some level because they don’t fully merge or dissolve into one another.
The two main components within a composite are the matrix and fiber. The matrix is the base material while the fiber is what reinforces the material. On top of the fiber reinforcements and matrix, composites can also include core materials, fillers, additives and surface finishes to provide unique performance attributes.
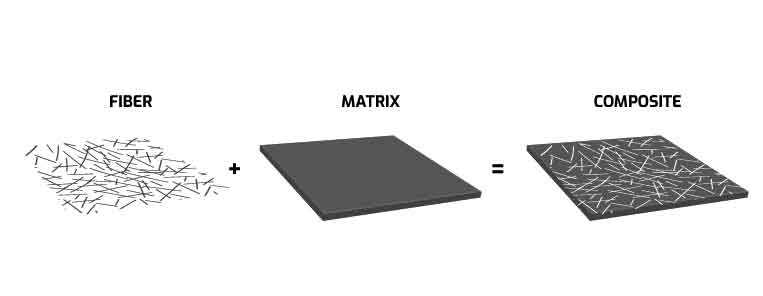
Some the benefits of composites:
Lightweight
High strength
Small to large part geometry – styling/design – sculptural form
Long-term durability
Design:
For the desigin I used FUsion 360 Software.
In this week’s assignment I wanted to design and explore the folding techniques. I wanted to check how the software slicer for fusion 360 and the folded panels option works.
I used canson paper 150gsm weight the purpose is that from a 2D flat paper we can create a 3D shape using only glue. This technique helps us provides us with many ideas and options especially that it is lightweight and doesn’t require a lot of material.
In Fusion 360 I started by creating a form and changing the surfaces and modifying the form until it became an interesting shape.
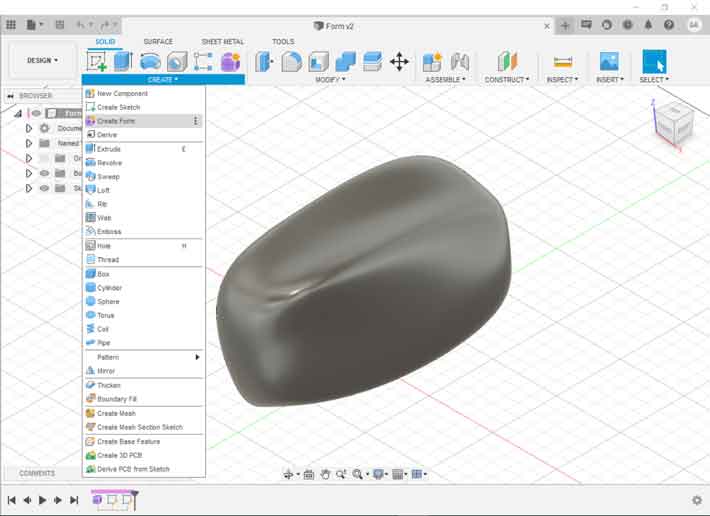
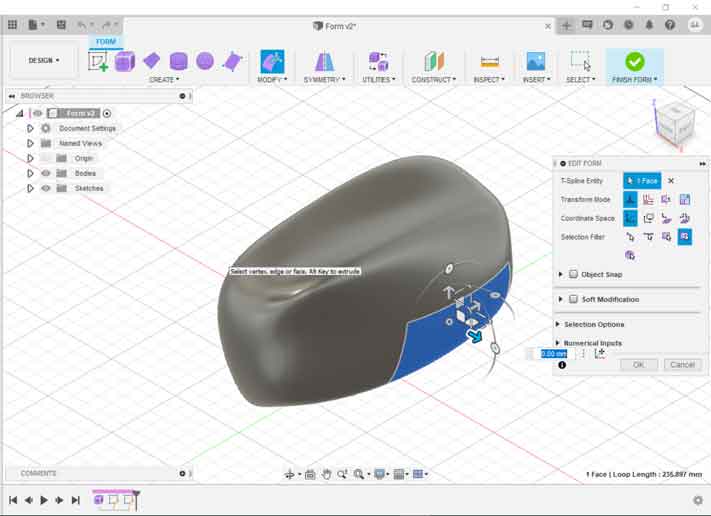
Then I exported the file as stl format.
Slicer for Fusion 360
In the slicer I opened the stl file then chose the technique I want to use which is folded panels and assigned the size of the material I am going to use.
As we can see that the slicer turned the form into a geometrical angular form in an interesting way.
I also assigned the number of vertex counts so that the form is not complicated a lot for folding.
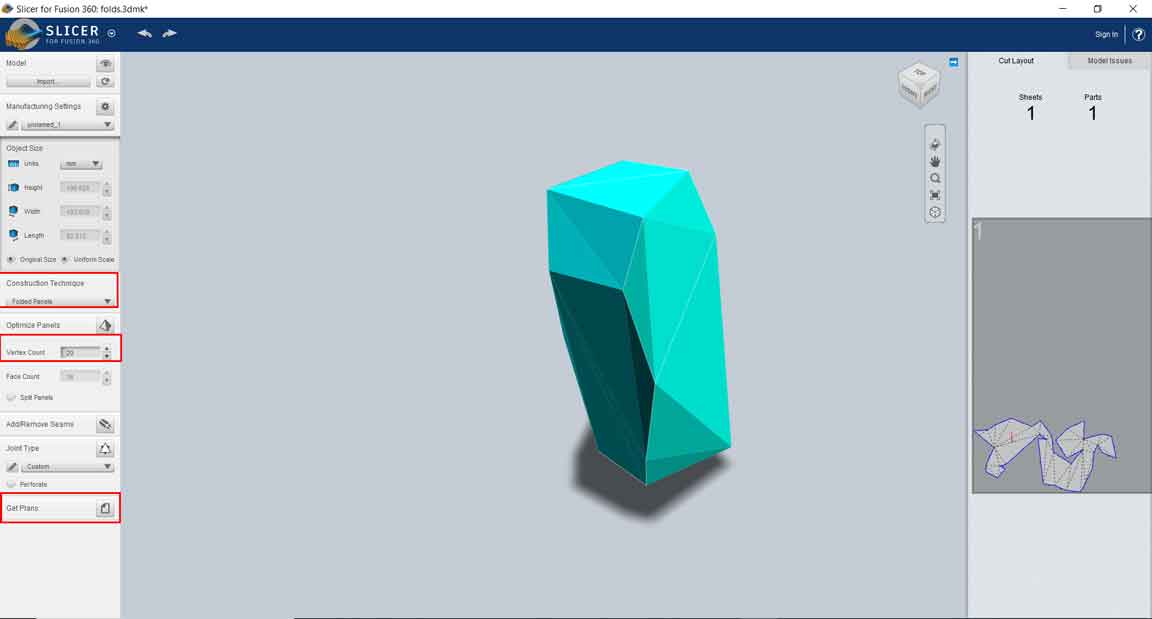
Then after setting all the option I chose get planes and chose the option as .dxf AutoCAD file in order to laser cut the folds.
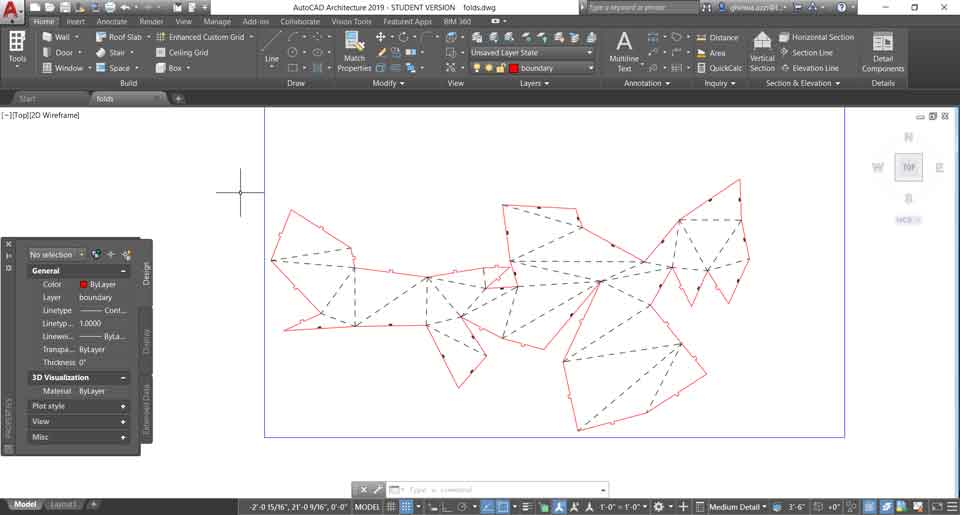
I used the VLS3.60 laser machine and below are the options I used to cut the material.
In the file I assigned the black lines to lightcut option and the red lines to cut option.
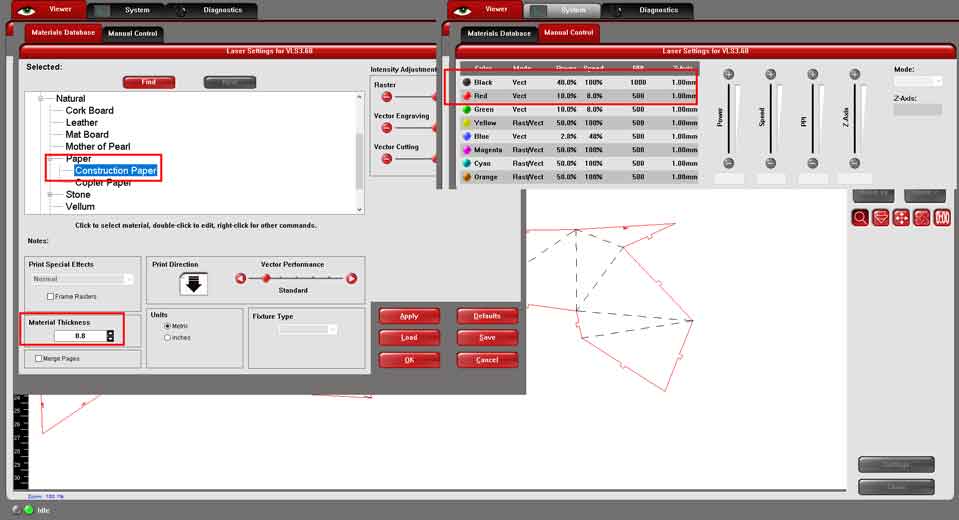
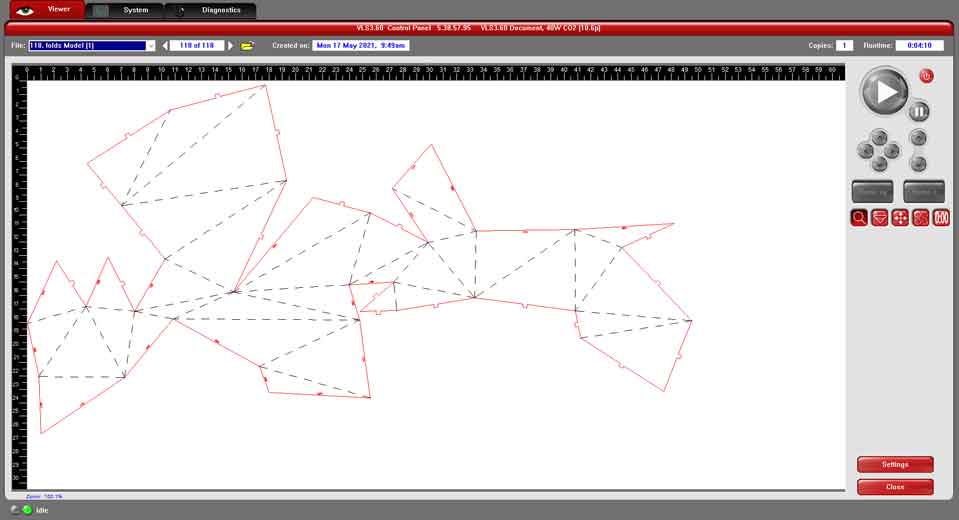
Assembeling the Model
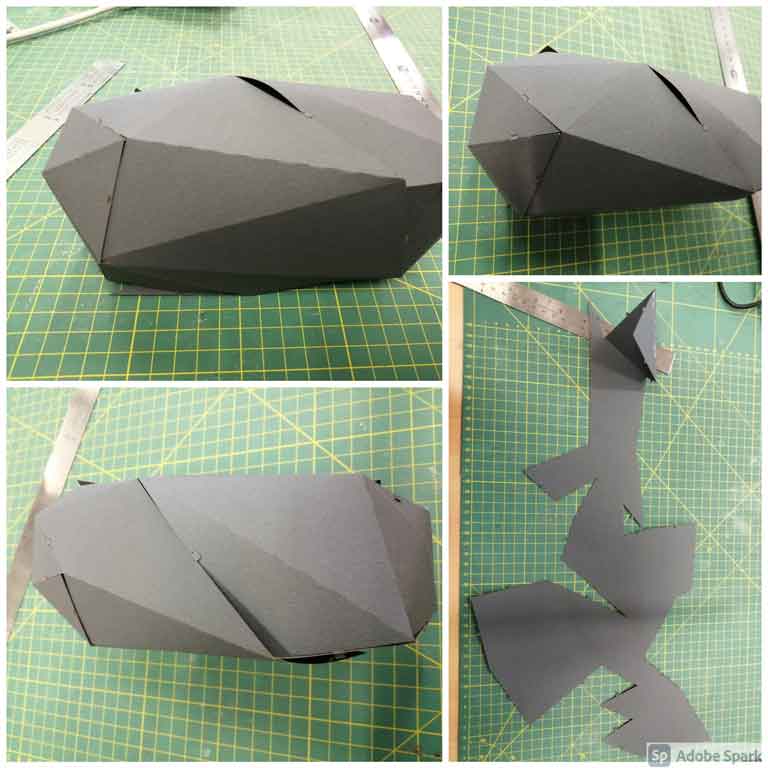
Then I decided to coat the model wtih fiberglass sheet and epoxy resin.
Safety and Technical Data Sheets:
Safety:
- Use with adequate general ventilation and/or local ventilation to keep exposures below established limits.
- Safety glasses with side shields or chemical splash goggles.
- Wear liquid-proof, chemical resistant gloves (nitrile-butyl rubber, neoprene, butyl rubber or natural rubber) and full body-covering clothing .
Technical:
- Mixing Ratio: By Volume - Resin/Hardener 3.44:1
- Working Time / Pot Life: 40-60 min at 23-25ºC
- Curing Times: Hard Cure: 24 h - Full Cure: 72 h
- Shelf Life: 1 year unopened / 6 months opened (approx.)
Fiberglass Cloth Rolls
Fiberglass refers to a strong, lightweight material that consists of thin fibers of glass that can be transformed into a woven layer or used as reinforcement. ... Fiberglass is commonly used in aircraft, boats, automobiles, swimming pools, storage tanks, roofing, pipes, cladding and casts.
I covered the folded model with fiberglass and after the whole model is covered I mixed the resin adding to it yellow colarent.
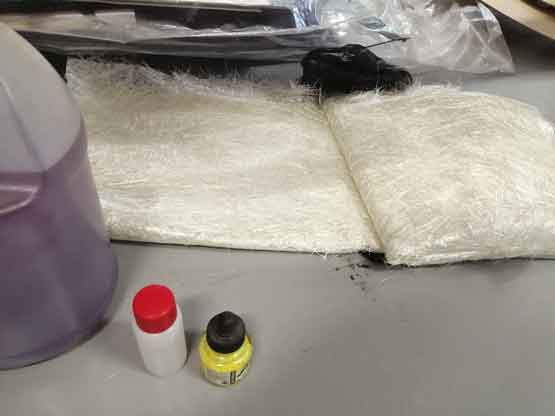
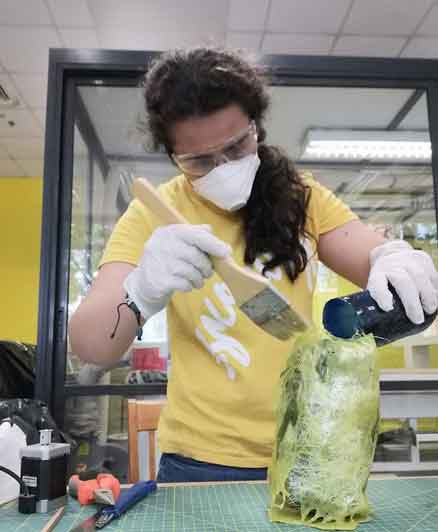
Final Result:
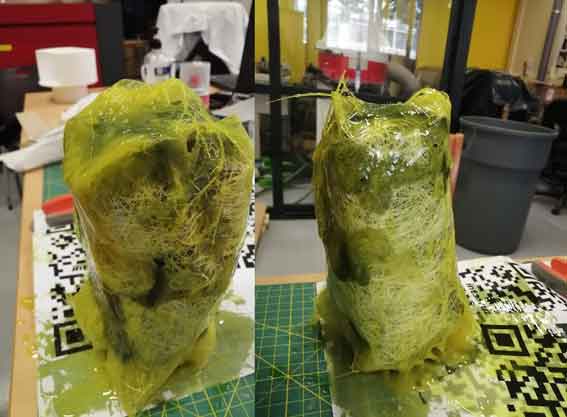
The final result did not end up as I wanted since the fiberglass was a bit thick to the take the form of the folds.
This work is licensed under a Creative Commons Attribution-NonCommercial-ShareAlike 4.0 International License