Composites (and 3D printing)
In this assignment we decided to explore the benefits of composites associated with 3D printing by analyzing the improvement in tensile strength of a hollow probe of ABS filaments (printed in a makerbot replicator 2X) filled with clear silicone sealing. In this case the filaments of ABS printed on the makerbot create the fibers of the composite while the silicone acts as the matrix.
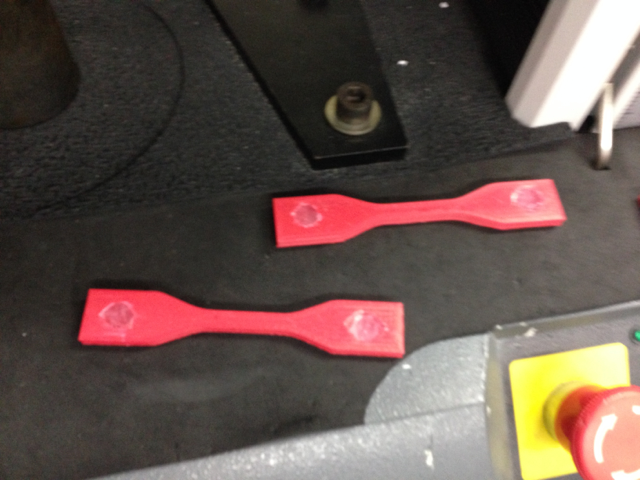
The probes were taken to a universal testing
machine that allowed us to examine the tensile
strengh of the material by pulling the probe until
braking point and recording the load applied.
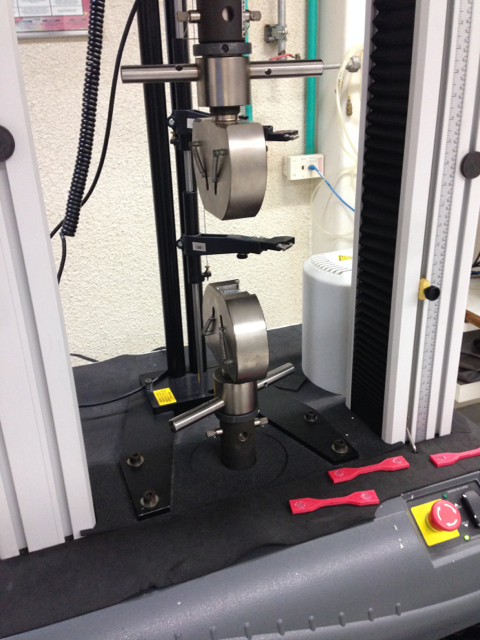
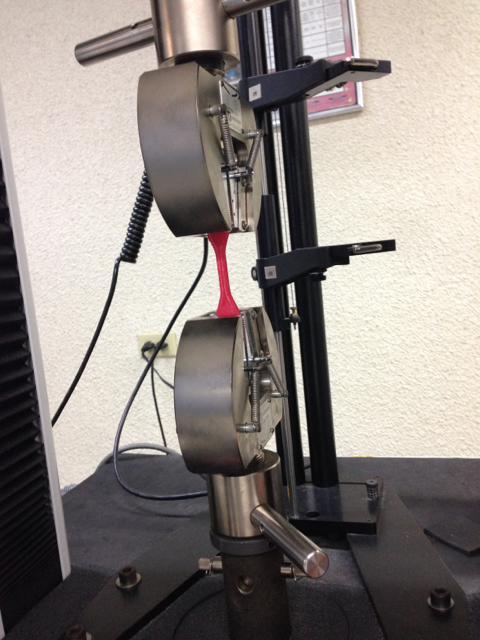
The way the probes were printed led to interesting
behaviors during the test. The filaments on the
edges tend to stay together and separate from the
top and bottom faces fairly quickly.
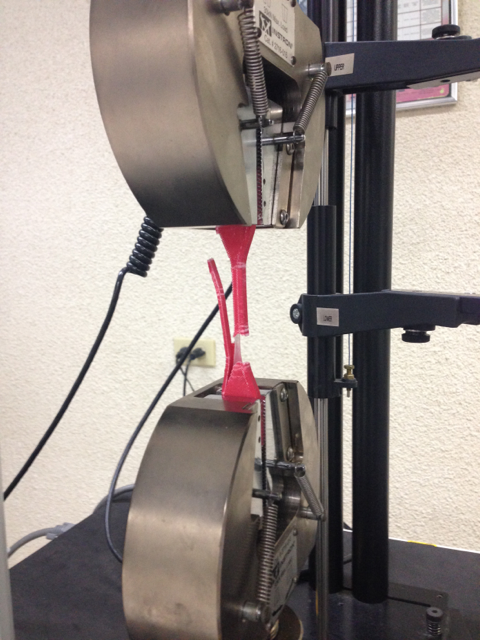
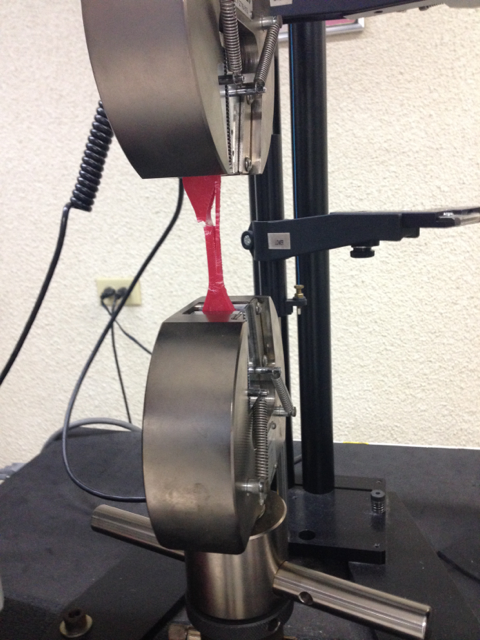
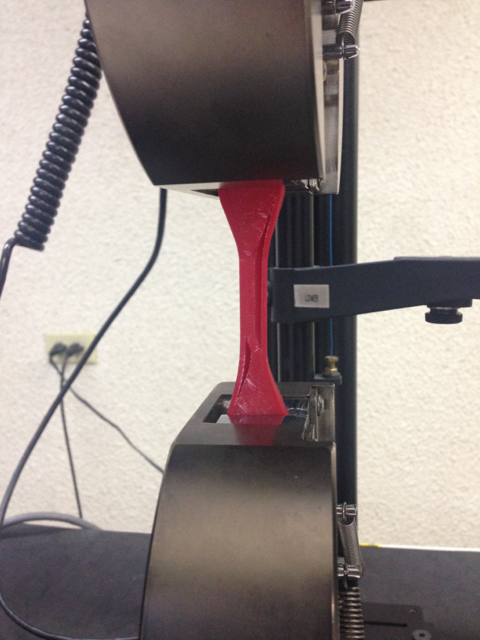
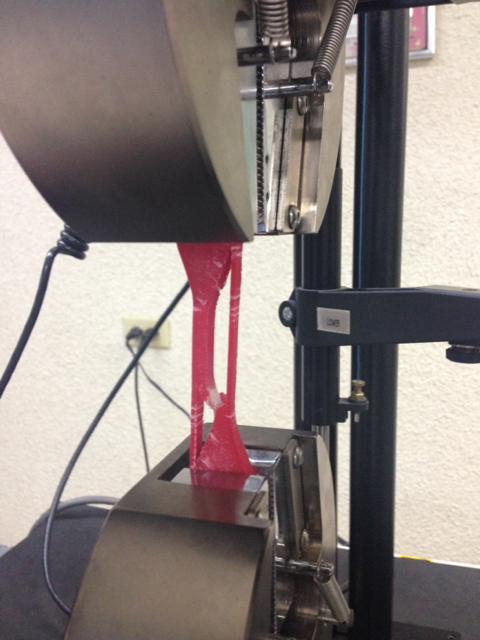
3 probes were made and notice that in all cases the
ABS failed first on the top and bottom faces that on
the sides and the clear silicone is still expanding
until the breaking point for it is reached.
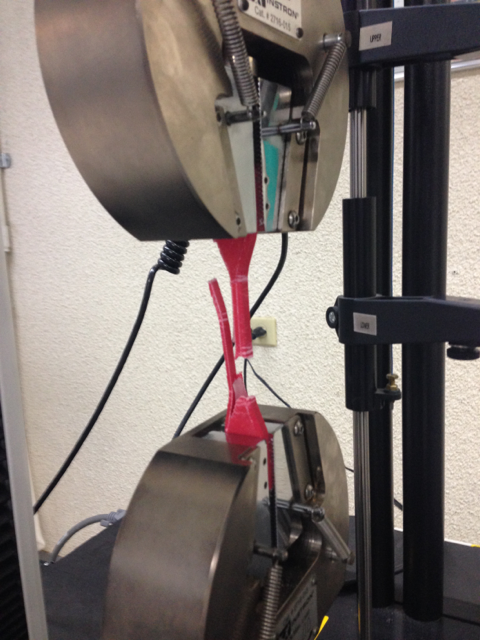
To compare the performance 3 solid probes were
printed and put to the test. These probes behaved
different; the sides did not separate from the body
because of the pattern used to print the part was
constant all along. However, the probe broke quickly
without much deformation.
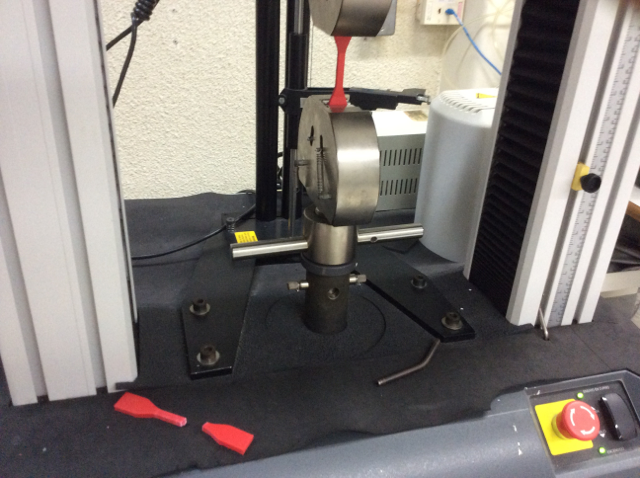
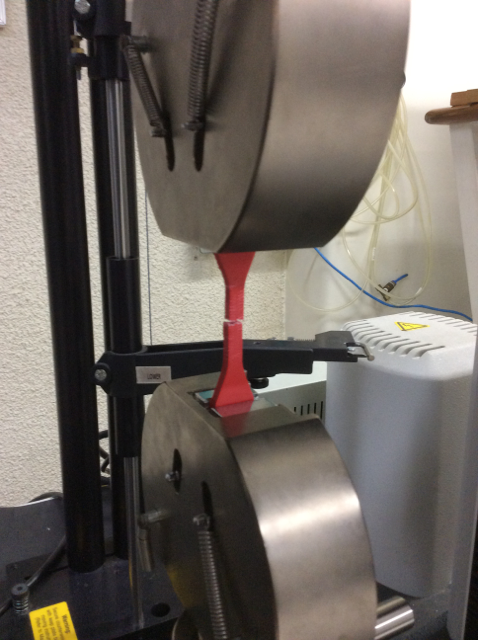
The maximum load supported by the probes was
registered as follow:
Composite Probes
#1: 0.70004 kN
#2: 0.70232 kN
#3: 0.65122 kN
Average: 0.68452 kN
Solid Probes
#1: 0.72271 kN
#2: 0.70877 kN
#3: 0.74304 kN
Average: 0.72484 kN
showing a similar performance for both cases, with
a slight advantage from the solid probes. More
elongation was observed in the composite probes due
to the side walls separating from the top and bottom
faces, straightening and finally breaking, while the
solid probes simply broke after certain elongation.
This is representative of the observations where the
solid probes had better structure while the
composites separated easily by faces. Looking
further into the structure of the composite probes
one finds how only a few filaments were really
surrounded by the clear silicone and those provided
a true composite behavior.
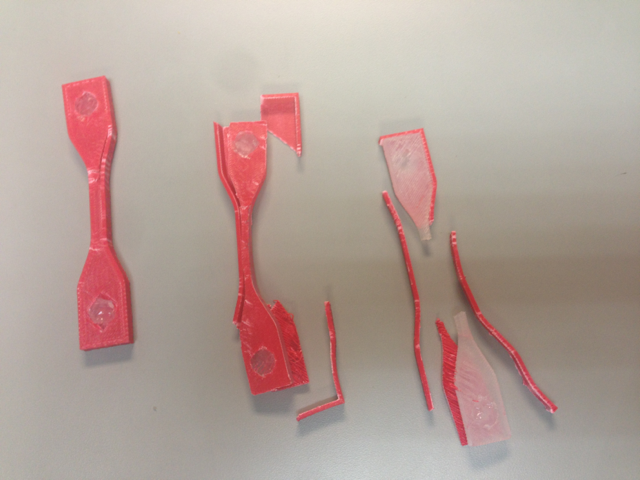
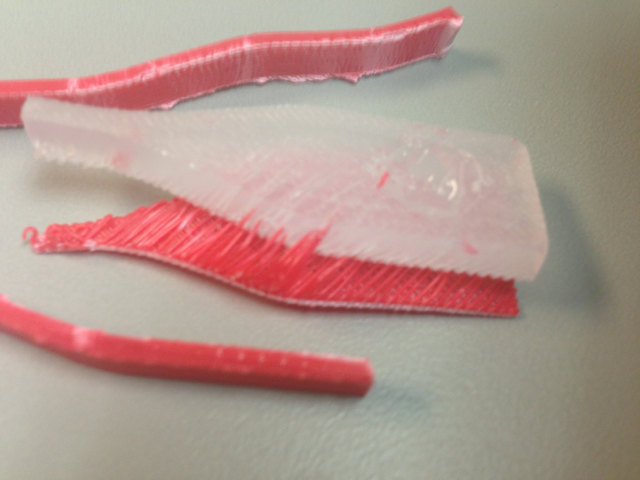
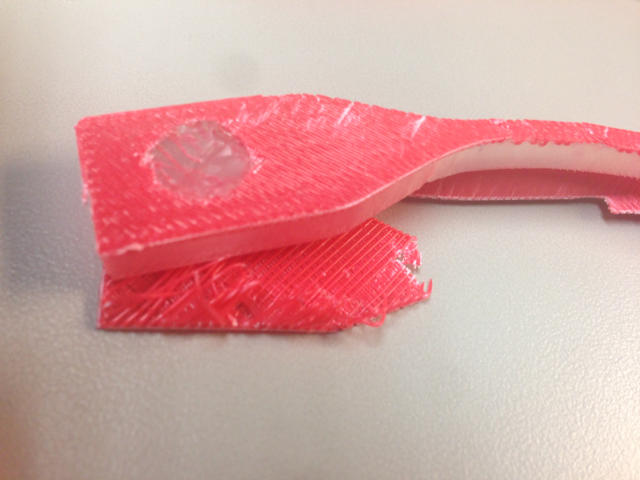
Two conclusions can be extracted from this
experiment. First, in order to create composites
with 3D printed filaments one needs to print an
internal structure that would allow for filling it
up with the matrix while providing enough fibers to
allow for good interaction between fibers and
matrix. Second, 3D printing may be an alternative
for creating molds that can be filled with resins
and later peel off the printed case since the walls
and faces are fairly uniform and separate cleanly
from the clear silicone.
Progress
- Project Proposal
- 2D and 3D Model
- Laser Cut
- Circuit Making - FabISP
- 3D Scanning and Printing
- Electronics design
- Make Something Big
- Embedded Programming
- Molding and Casting
- Input Devices
- Composites
- Output Devices
- Networking
- Mechanical Design
- Interface
- Applications
- Invention
- Project Development
- Project Presentation
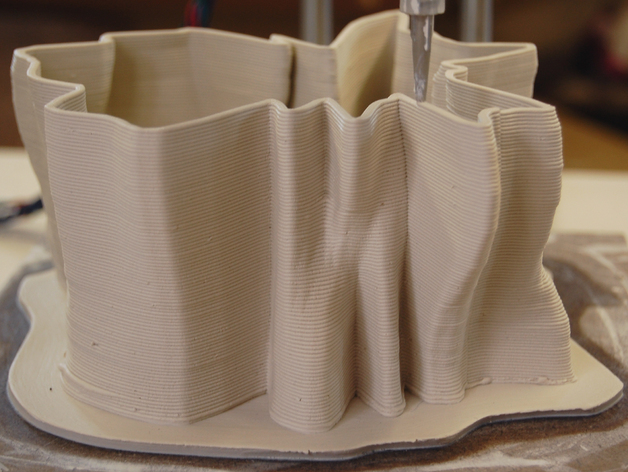
Alvaro J. Rojas Arciniegas, PhD
Assistant Professor Department of Automatics and Electronics - UAO
+57 (2) 318-8000 ext. 11384
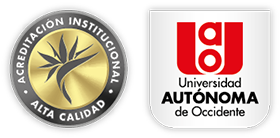