3D Scanning and 3D Printing
For this assignment the intent was to scan an object and to print another one that could not be made by traditional (substractive) methods.
3D Scanning
For this section a makerbot Replicator 2x was used.
The object to print was my version of the popular
object commonly known as "chained ball”. The object
consists of a ball trapped in a twisted cage that
allow it to move but not to escape. Below you can
see the model of the object in Solidworks.
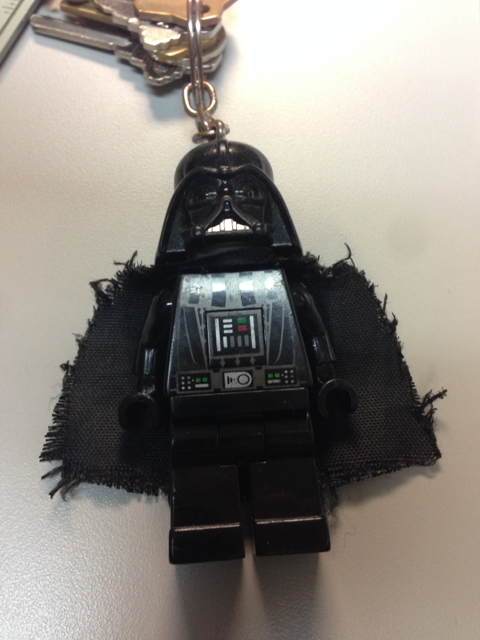
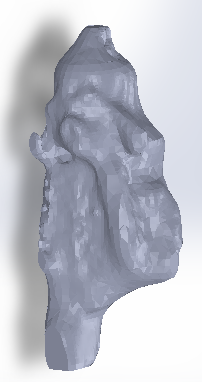
A second attempt was digitizing a traffic cone that had been 3D printed. The result was much more satisfying but unimpressive for being such a simple geometry.
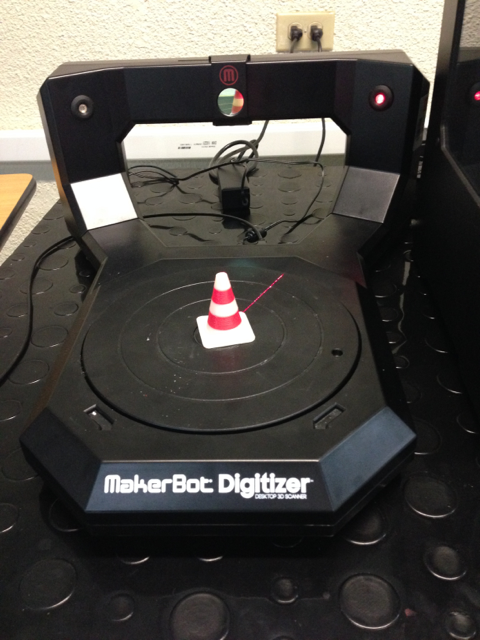
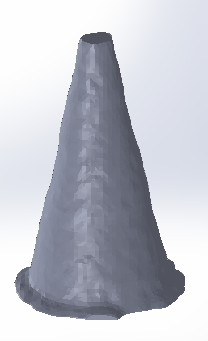
The next attempt was to digitize another object that was more complex and larger. This piece had some difficulties for being a bit shinny and for having the light source right above it.
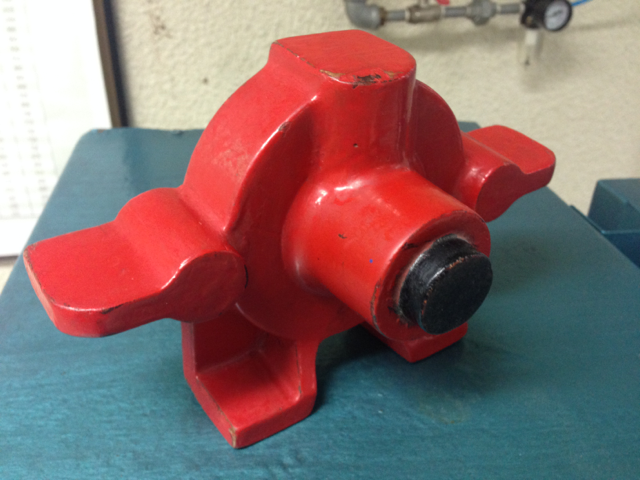
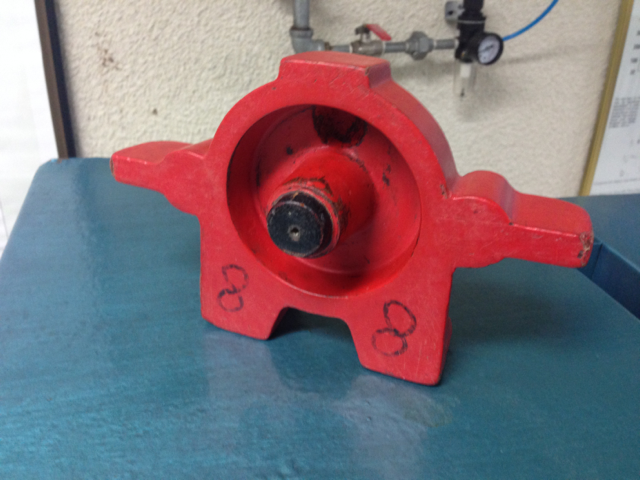
The first trial was problematic once again, the light reflected on the flaps produced discontinuities on the 3D model, and the dark section of the axis was not captured that well.
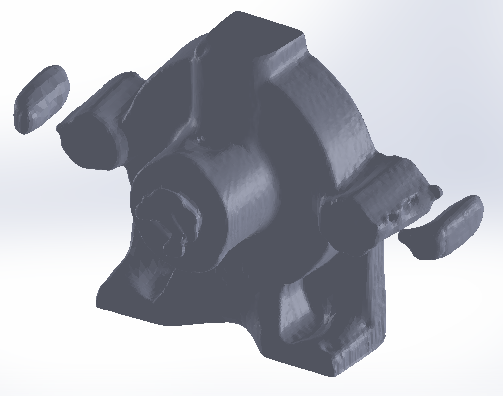
A second trial was performed shutting down the
light that was shinning right above the scanner and
after seeing some persistent errors, a multi view
scan was created by scanning the piece once again
laying down. The scanner then uses information from
both scans to recreate the piece more precisely. The
result improved significantly.
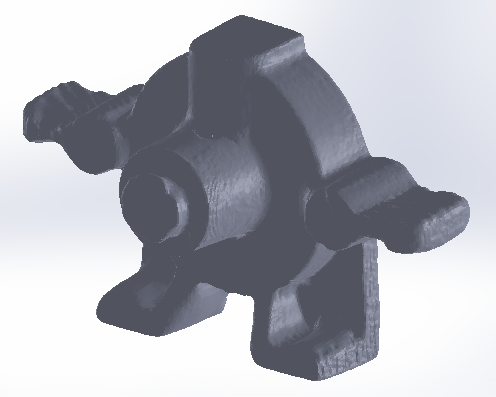
3D Printing
For this task a makerbot Replicator 2X was used. The object selected was my version of the popular object commonly known as "chained ball" which consists of a ball traped in a cage where it can move but it cannot escape.
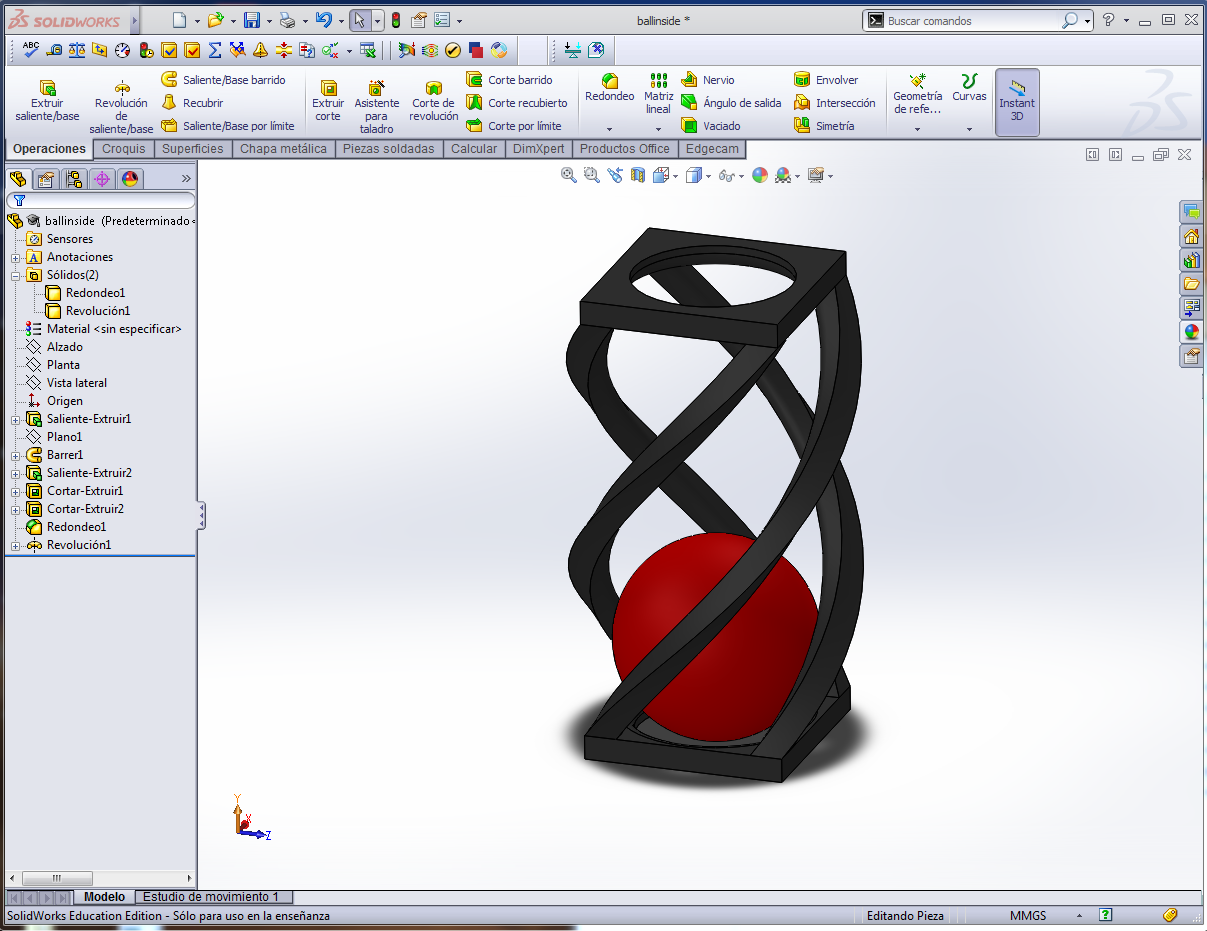
Next, the model was exported as stl format and imported into the makerware software which is the software that comes with the printer. In order to print in two colors, each solid of the object (ball and frame) needed to be exported independently. Later in makerware, each solid was imported and a color/extrusion head was selected for each one.
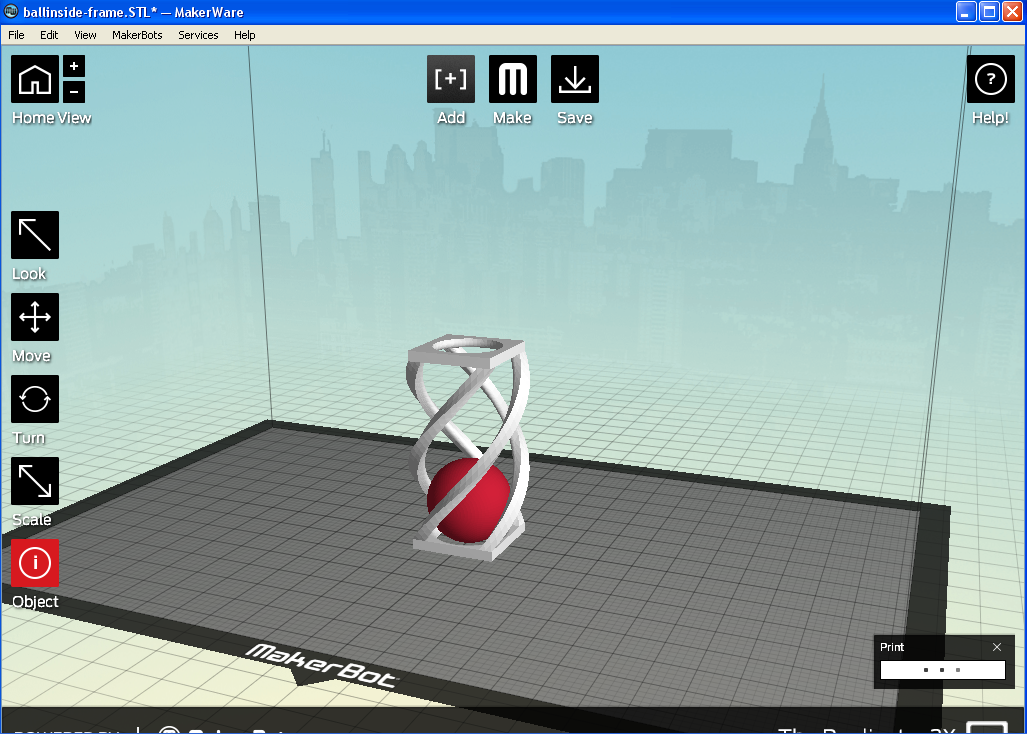
The next attempt was to print it directly. Two challenges appeared: first, when printing the ball without any support, the small base created by the first layer started moving while printing subsequent layers. This resulted in a crappy base that did not resemble a ball. Second, the extrusion of one of the materials stopped after a few layers and it was unclear what was happening.
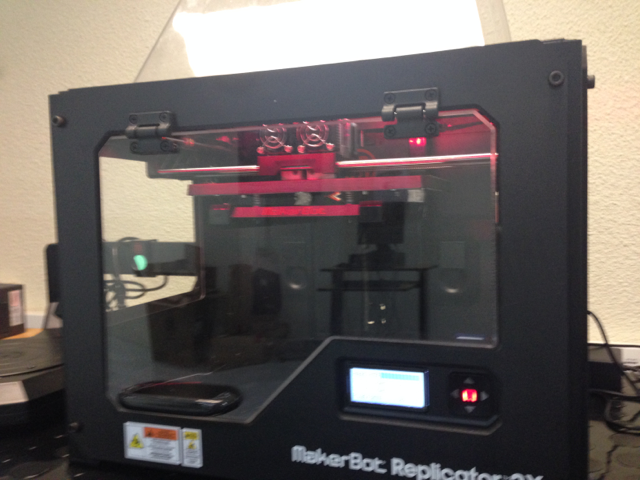
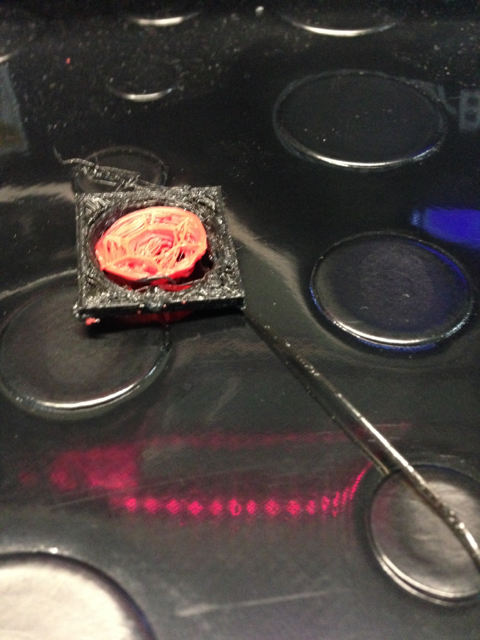
After many iterations checking the temperature settings and making sure that the material was being fed correctly it was decided to switch the black filament for a white one that had worked better for other pieces. It turned out that the black filament was PLA instead of ABS which made a big difference, specially because the settings in the printer had it as ABS. Additionally, a support frame was used to be able to reproduce better the intended geometry. The software also allowed to simulate the print before sending it to the printer and to add some patterns to guarantee that the extrusion heads were indeed printing.
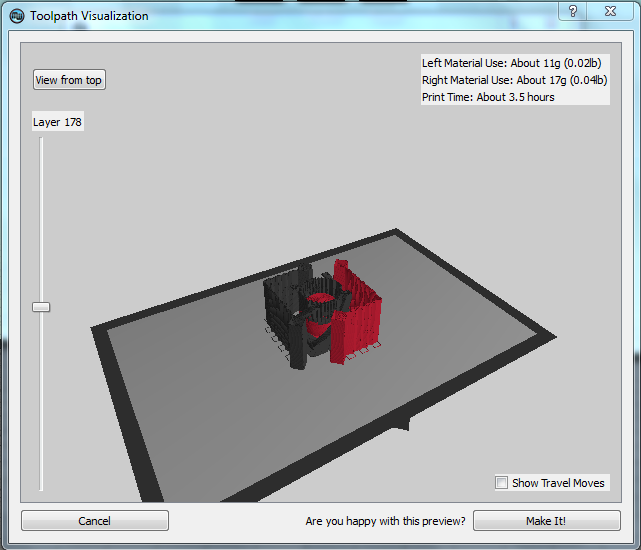
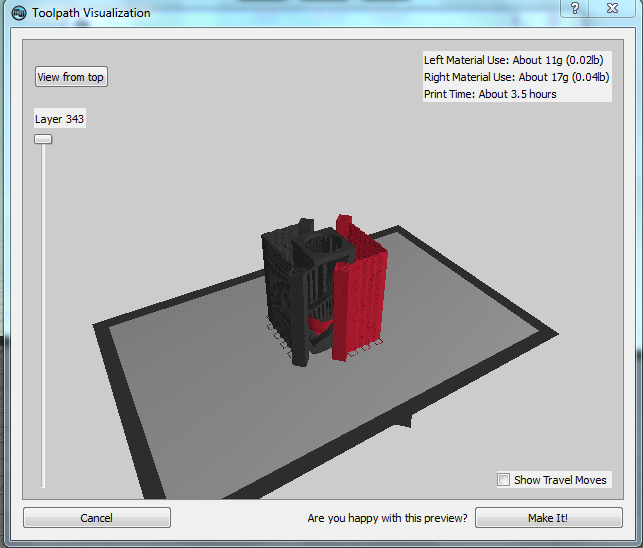
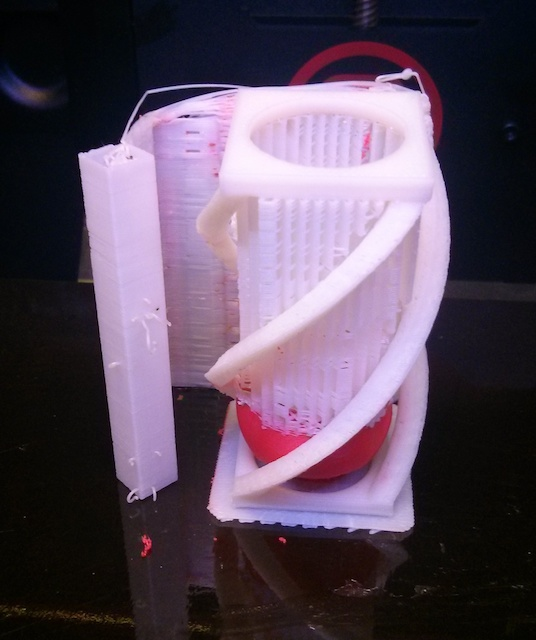
Next the challenge was to remove the supporting material from the printed piece. Although it was time consumming and had to be done very carefully so the intended piece was not damaged, the final outcome was very satisfying.
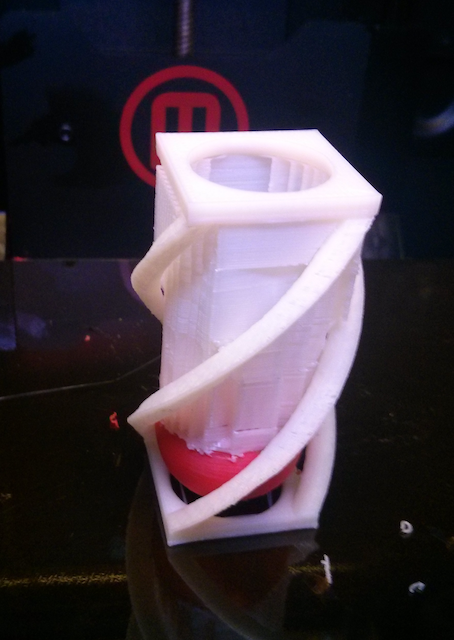
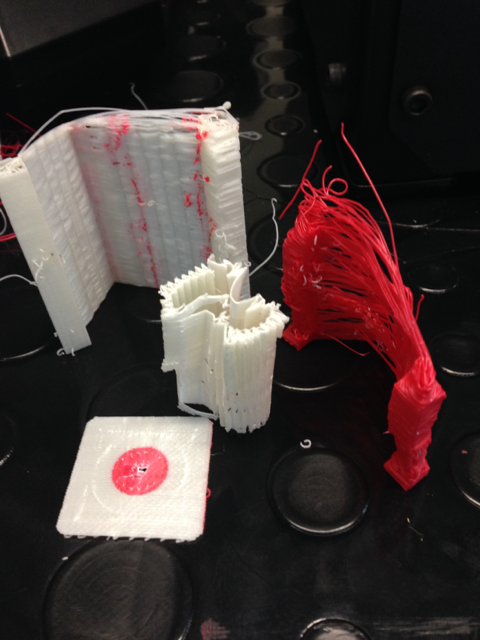
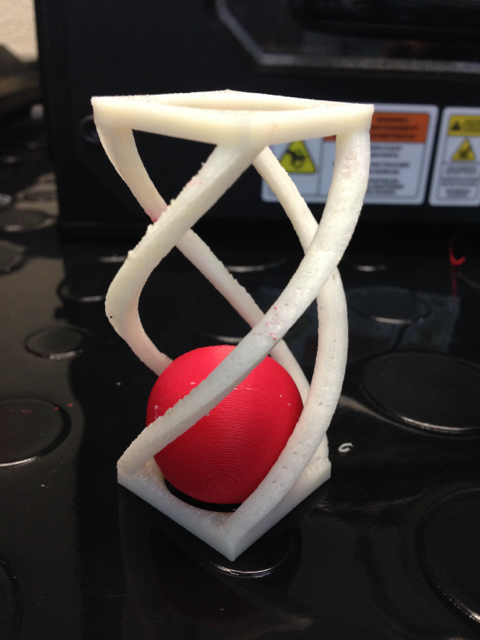
Progress
- Project Proposal
- 2D and 3D Model
- Laser Cut
- Circuit Making - FabISP
- 3D Scanning and Printing
- Electronics design
- Make Something Big
- Embedded Programming
- Molding and Casting
- Input Devices
- Composites
- Output Devices
- Networking
- Mechanical Design
- Interface
- Applications
- Invention
- Project Development
- Project Presentation
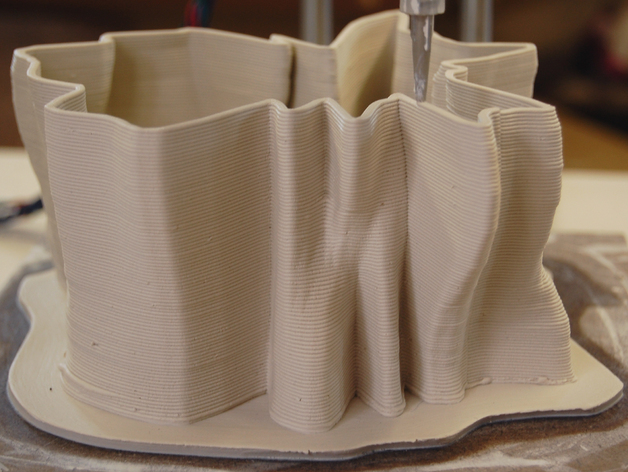
Alvaro J. Rojas Arciniegas, PhD
Assistant Professor Department of Automatics and Electronics - UAO
+57 (2) 318-8000 ext. 11384
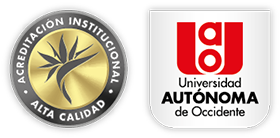