Making the auto peeler
I worked with Marta Cortes Orduna, Peetu Virkkala, Behnaz Norouzi and Heidi Hartikainen. For all the process of machine designing and building, see our group website.
Project overview
Idea came from the suggestion of building a mini lathe from one of the FabLab staff. We thought it is too complicated to position the bit according to 3D design. So we simplified the mechanics using the same principle of movement. The machine we make is auto peeler which removes skin of fruits or vegetables. For instance an apple will be attached to the rotating pole and moves one direction. When the blade touches the apple the skin will be removed.
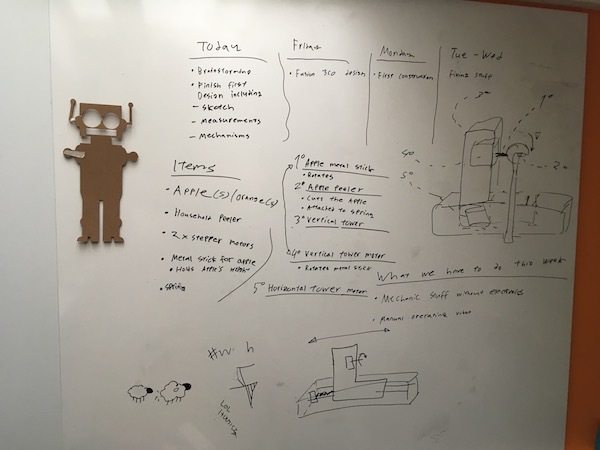
Own contribution
3D designing of the joint part
I designed the joint part to connect the stepper motor and the rotating pole together. First we measured the diameter of the axle of the stepper motor and the pole using the calliper.
I used Fusion 360 for designing. I drew hexagon in sketch mode. Hexagon will be easier to grab and attach the axles. Following the advice of the FabLab staff, I drew a hole which diameter is 0.1mm smaller than the axle of stepper motor. I stopped the sketch and moved to model mode. I extruded the hexagon and made the hole up to the half of the height. I selected the other surface which does not have hole and drew another hole for the rotating pole.
Working on the blade
We decided to use thin metal plate as a blade. I watched a couple of videos of the peeler to find out the good angle toward the object. We tested and decided to attached the blade on the piece of MDF which has some flexibility so that the blade will remove the skin when it touches the surface of the apple.
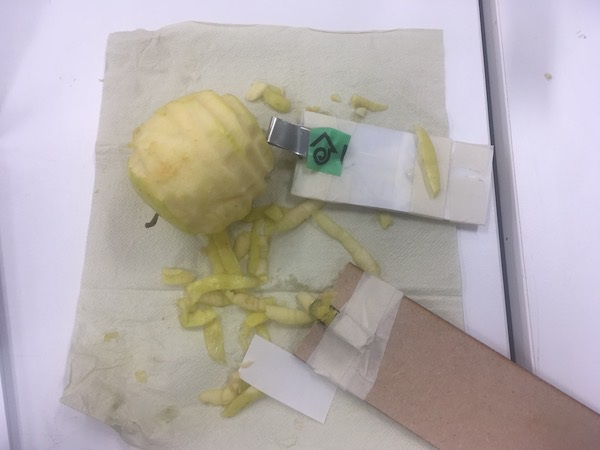
We calculated the distance and the height of the blade. I drew the simple holder in Inkscape to keep the blade on the certain position. We cut the holder with laser cutter. It worked okay.
3D designing of the peeler
Bas suggested to design a 3D model of the machine to see the whole image. I used Fusion 360 to design the model. Since we decided to recycle materials which were used in previous year, we already had most of the parts ready. I measured the parts and made the 3D model.
Here is the video of this week's outcome.