Composite: a Wildcard Week
Week 17
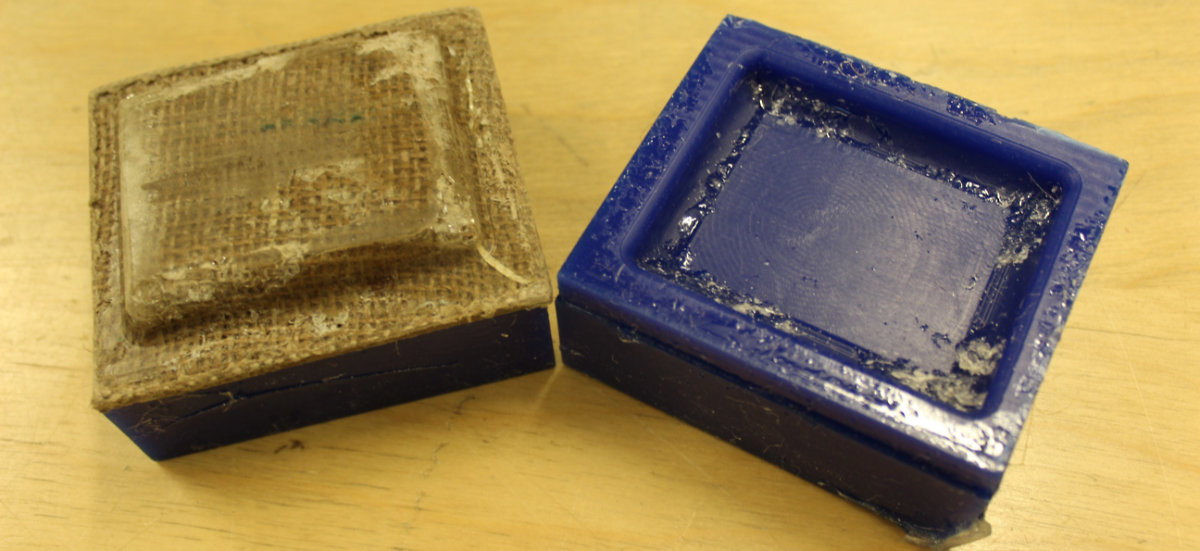
So for this week's assignment, we have a choice of choosing the process that we want to try. I'm very interested with trying out my hand at e-textile, but I will do this later in favor of composite.
This choice is a logical one as I will probably be using composite to create protective boxes for the electronics and the motors for my base. I'm very much interested by this outcome.
The materials
The results will be interesting as I will be using a mixture of resin with jute, all together compressed between a sandwich of molds made of machinable wax and compressed by vacuum.
The molds
For this first try, I will be making a cover of outside dimensions of 2.75" by 2.25". There will be a radius of .125 and a radius of .25" to help the resin and the material flow uniformly inside the mold. This cover will be made in two halves milled in machinable wax.
I made a sketch on paper with all the dimension before I went to the (digital) drawing board. This was very useful as I came up with small details that I haven't thought of before I made my final draft.
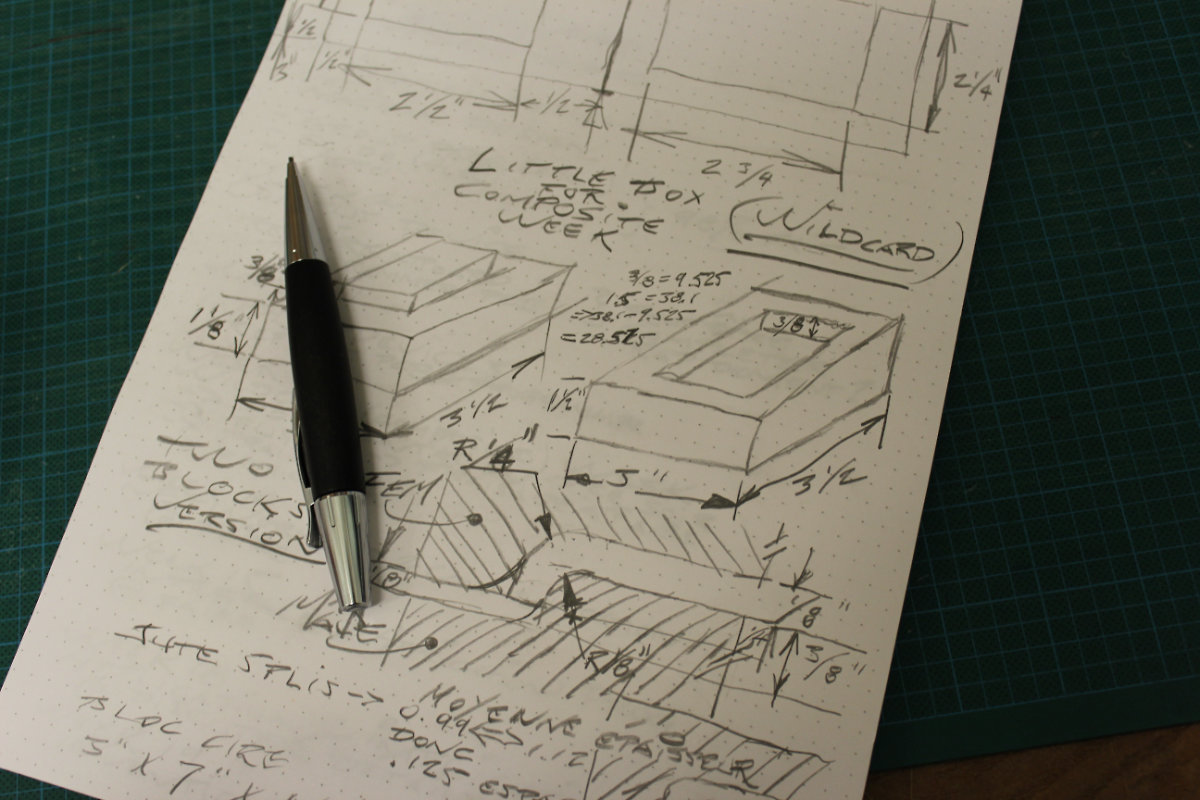
Two molds will be made: a male and a female. The idea is to put the jute on top of the first mold, pour, or more appropriately paint, the resin on top of it, making the first layer. I then put a second layer of jute and paint the resin. I will do this for a total of 5 layers.
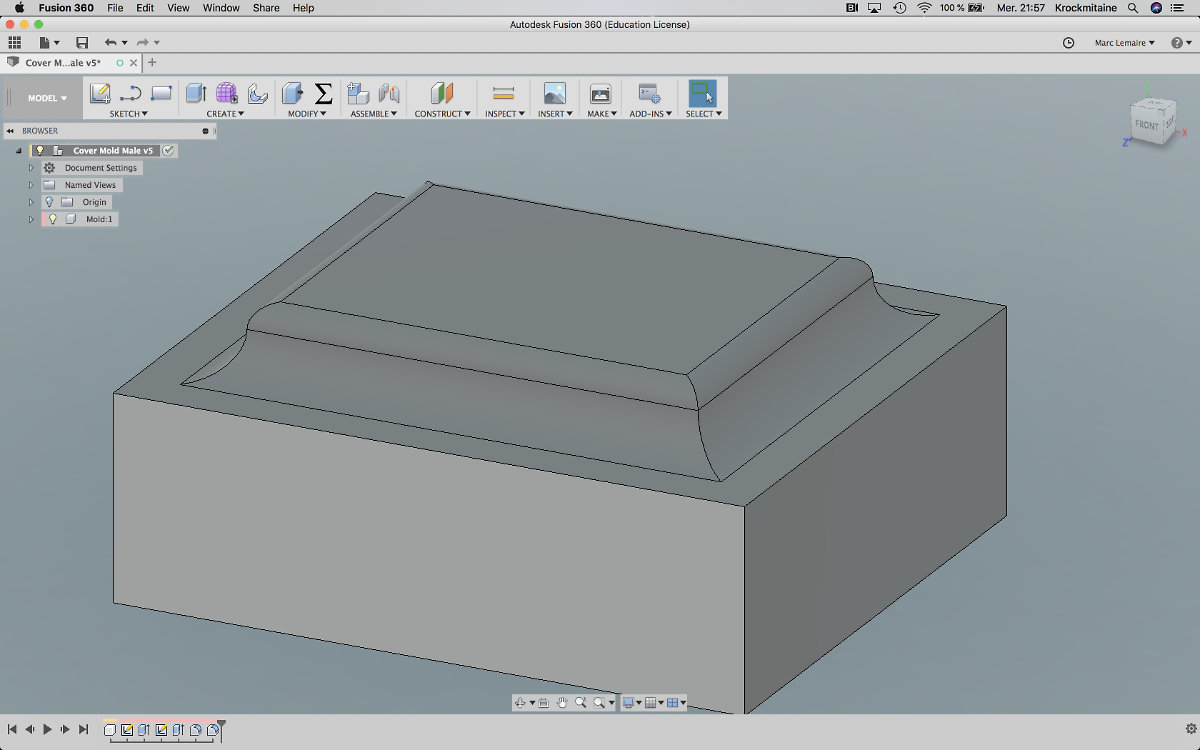
The inner space between the mold will be .125, (⅛"). I've arrived at this dimension after measuring the thickness of 5 layers of dry jute together. As this dimensions averages about 0.99 and 1.12, I added a slight amount for space for the resin to spread and came up to .125, which is easy to remember.
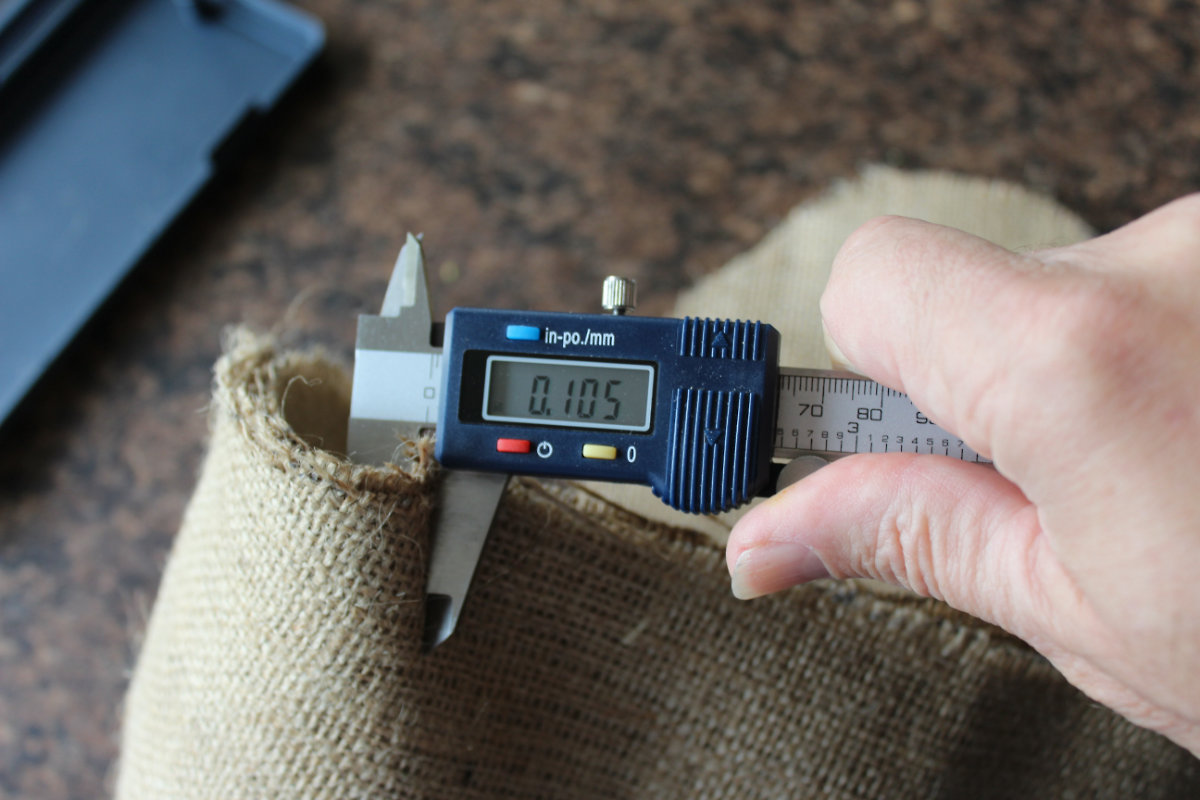
Once this sandwich will be done, the assembly will be put in a suction bag and the air will be pulled out. The atmospheric pressure will compress the two halves of the mold together and squeezed out bubbles from the resin and forcing to adjust to the form, creating the cover.
Safety precaution will be important as I have to read the safety data sheet and the technical data sheet. I wiil have to wear a mask and glove.
Making the molds
Male mold
Making the molds was relatively straitforward. As the process is well described in Week 10, Casting and Molding, I will mainly describes the differences.
This mold involves a change of tool as we received a 1/16" ball end. Since I made many curves, I'm curious of the end results. But I will have to be carefull during the change of tool: I have to stop the machine, unscrew the chuck, change the mill, put the chuck back and continue the operation, all done manually.
I sawed of a block of machinable wax and put one on the table. I made my zero and was ready to start but while checking with me, my instructor noticed that my origin was on the wrong side and my block was wrongly posititionned!
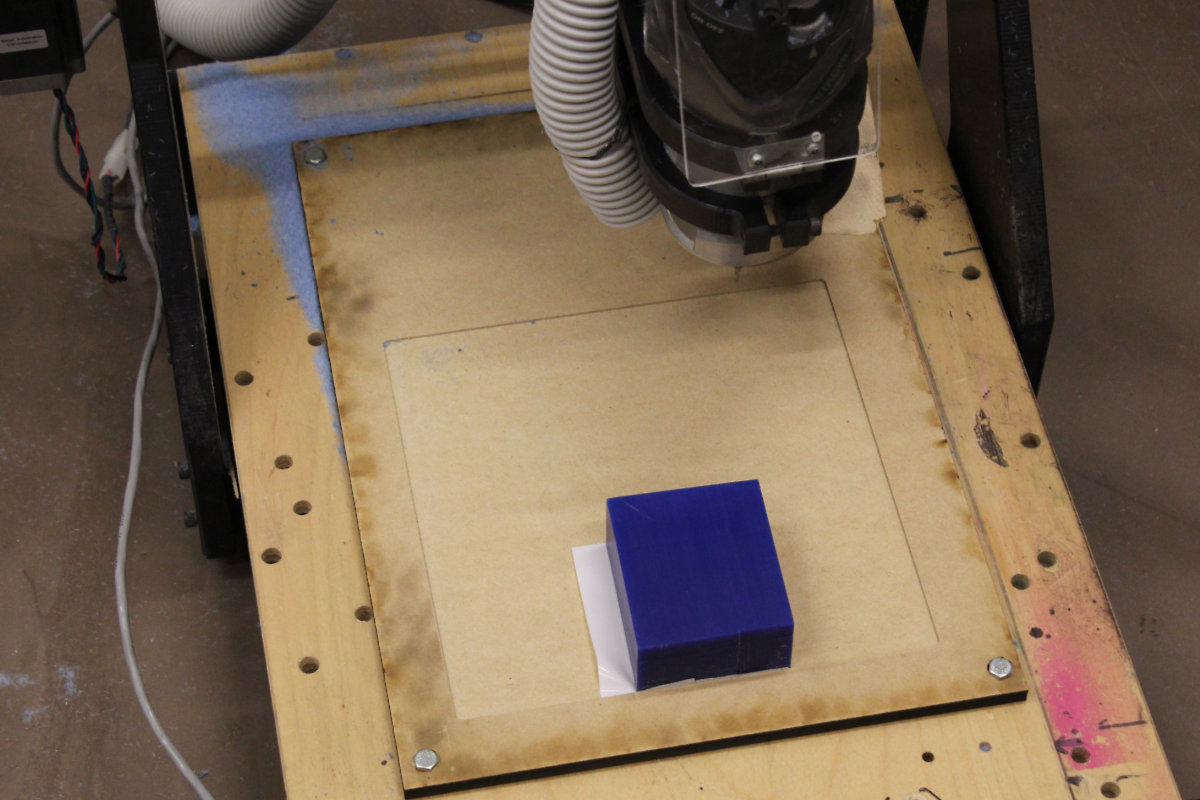
I changed the position of my block, and made another mesurement for the origin. We changed some parameters because we're becoming more expert at machining wax. As recommended by my instructor, I increased the Lead-In, Lead-Out and Ramp Feedrate to 5000mm/min, minimized the stepdown to 3mm to have a nice curve. I also put an offset from the bottom distance to 28.575mm so the mill won't go down any further.
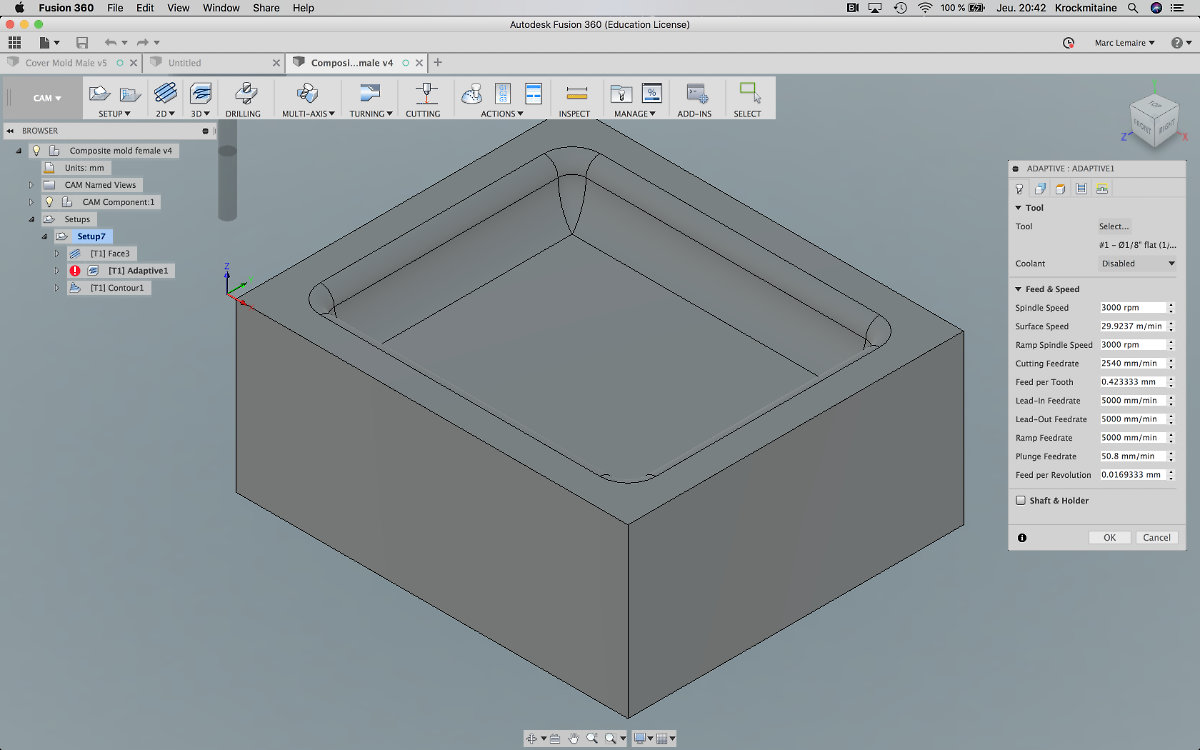
I sended the .nc file to the UGS software and the first stage, the surfacing, seems right. The second file for the milling of the male mold was a little bit more puzzling as I saw that the mold was a little off-center. I checked my file and it was ok. Since this mold need to roughly align to make the cover, I went ahead and continued making the mold. It's only when I changed the mill from the flat ⅛" to ball end 1/16" that I made a mistake: I carefully measured the top of the mill to the chuck. When I putted it back, I made the same measurement but it was done on the wrong surface: I should have measure the top of the mill against the collet of the chuck.
I put the chuck back on the machine, knowing about this mistake but doing it anyway just in case the results were ok. They weren't. The mill was too high. It managed to mill a litlle the sides but essentially milled empty air.
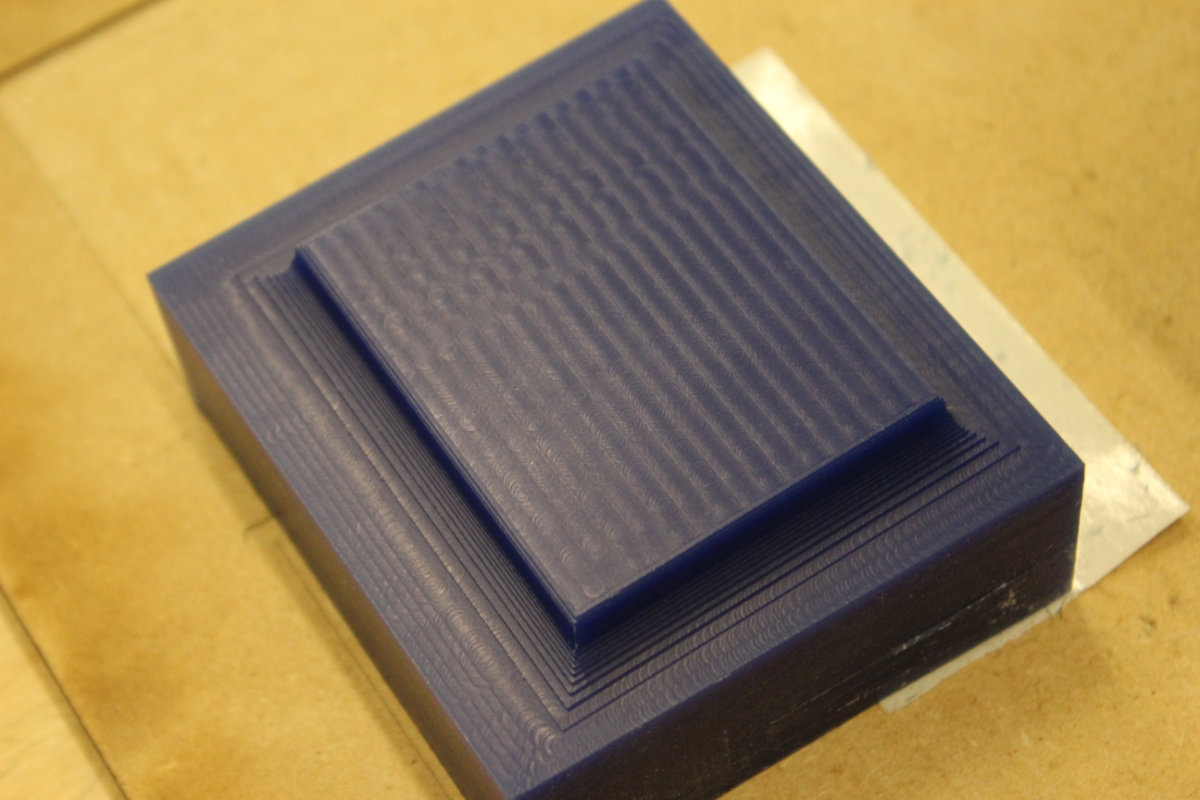
Female mold
Those lessons were applied for the making of the female mold. I carefully mesured the end mill with a caliper while pressing the chuck against the collar and locked the caliper in place.
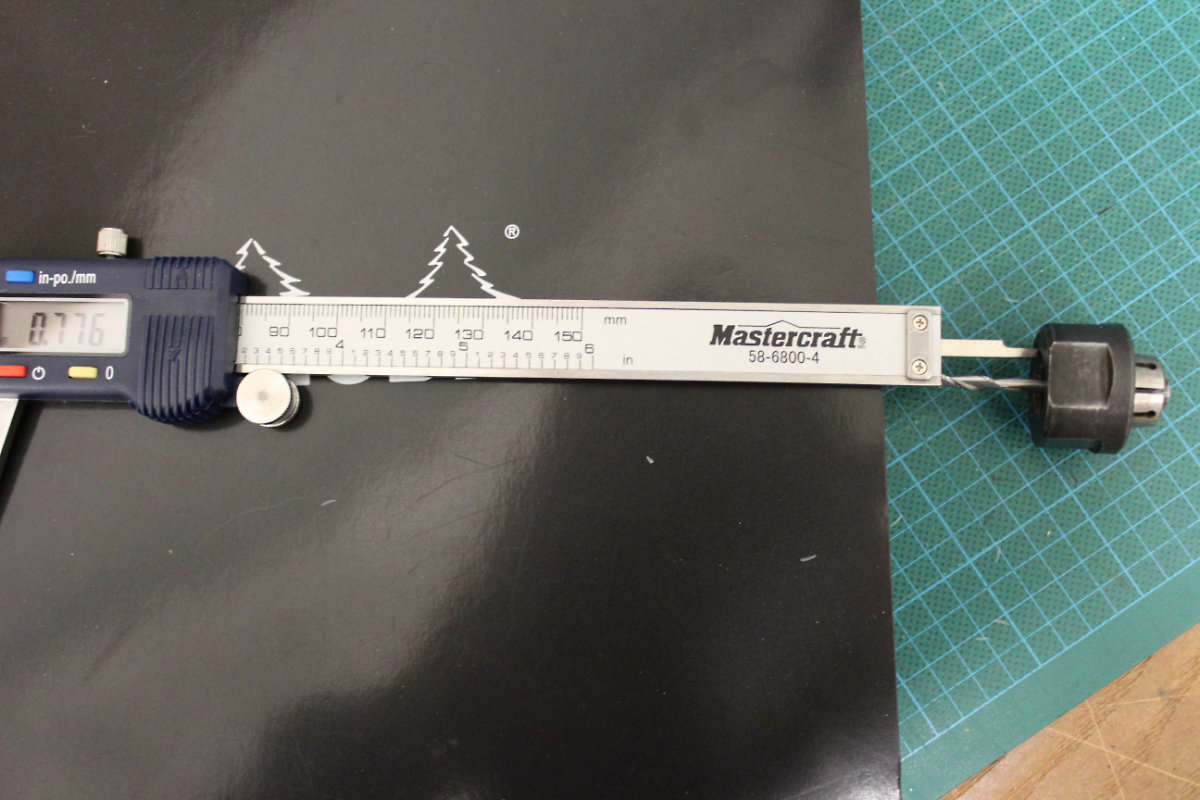
Once the measurement was secure, it was only a matter of patience to manually place the ball end mill to the same height as the end mill. I eventually made it and place the assembly in the chuck of the milling machine.
Those lessons paid off handsomely.
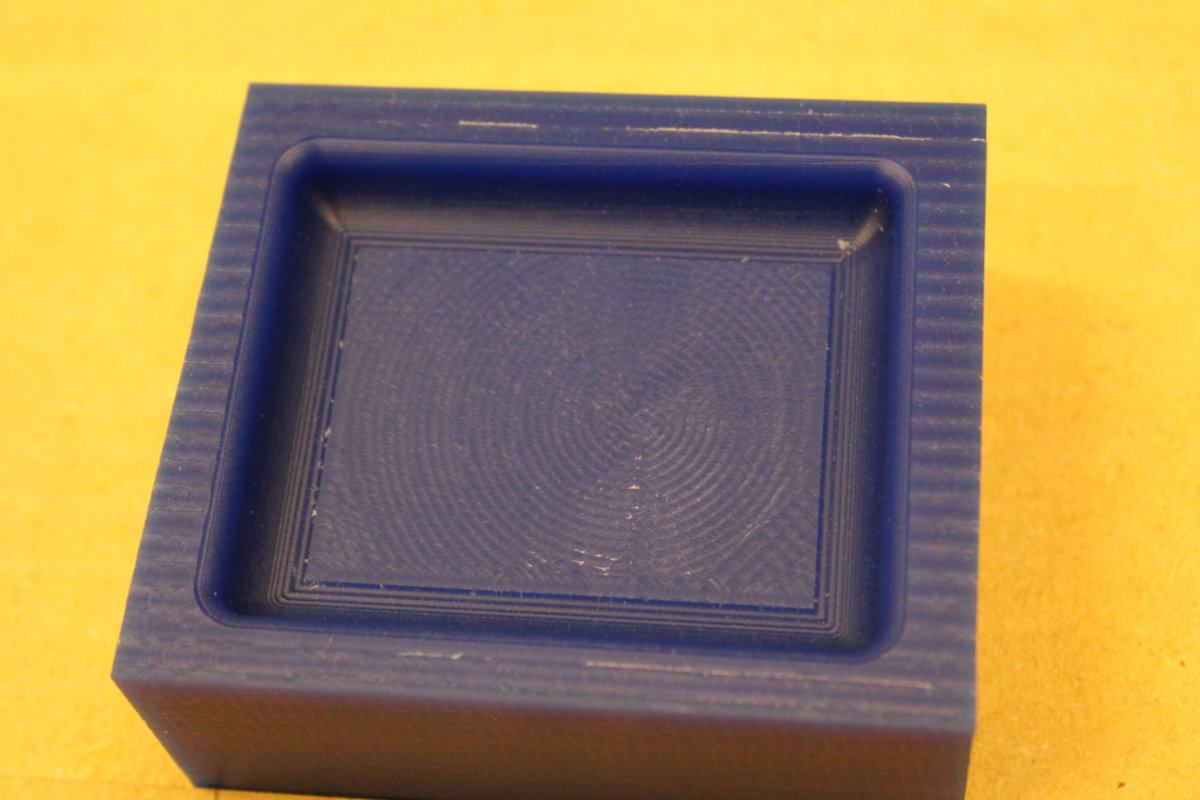
The Male Mold Redux
Having done such a nice female mold, I was obliged to redo the male one, my instructor (or me for that matter) would't have accepted that less than stellar part.
I came in the next morning and went immediately into the shop to prepare the machine. I put the block of wax on the table and started the machine. The operation went as expected and eventually had a complete mold. Those two parts looks amazing and promises to make a nice cover!
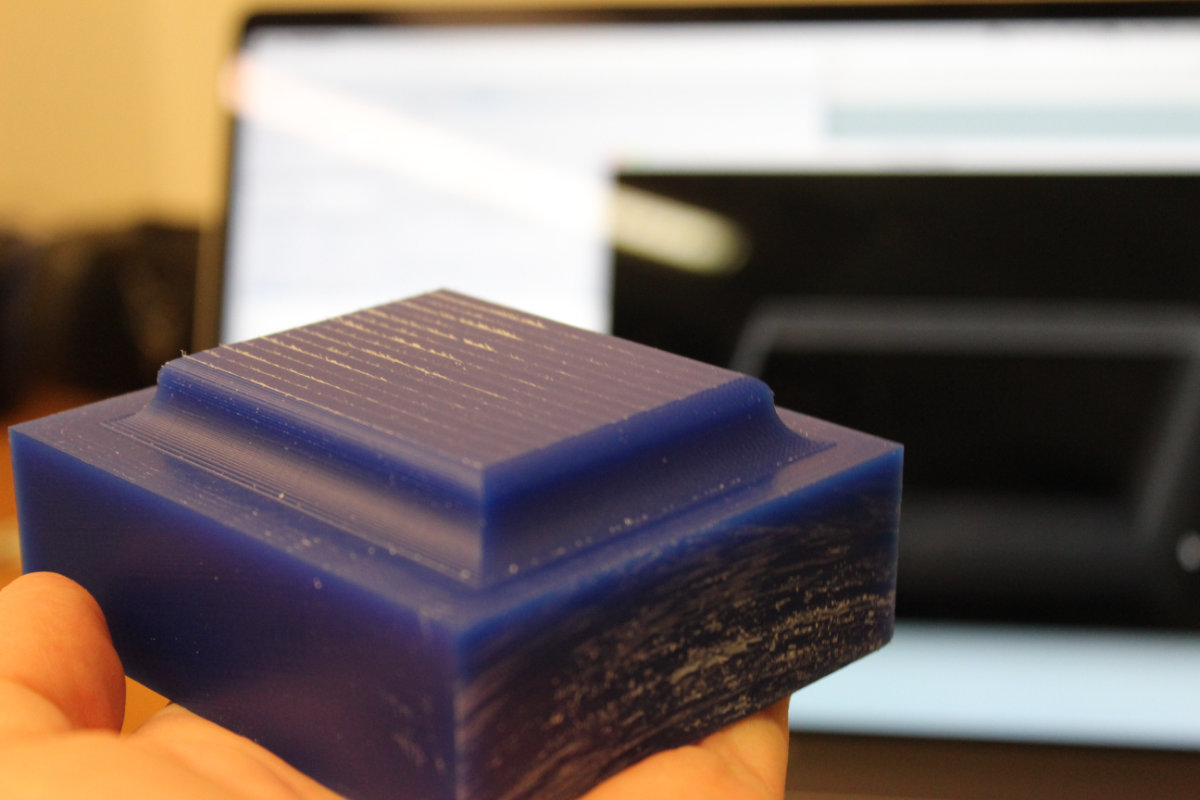
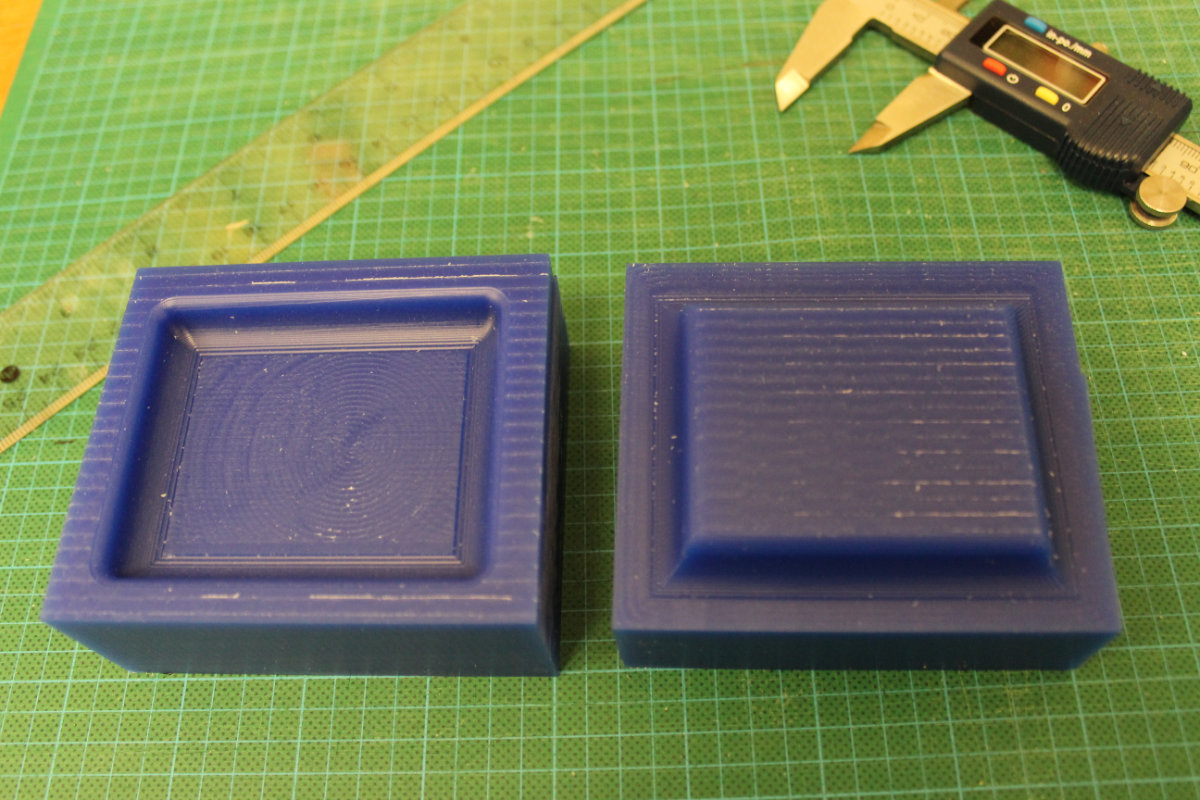
The making of the cover
Now that I have everything under my hand, it was time to prepare the resin for the making of the cover.
The table was setted up for the incoming mess that the process implies: taping a sheet of plastic on the top surface. Also needed are an inexpensive brush, nitrile gloves to protect your hands, a mask and the principal ingredients to making the resin.
Put on the gloves, the mask and your safety glass. I have a good respirator, and during the whole process, I was never inconvenienced.
This epoxy is composed of two parts: the resin is really sticky and the hardener is liquid. Start with "measuring" (dropping it) the resin.
I put a plastic cup on the top of a measuring scale and "measure" (essentially dropping it) the resin into it. The resin is like thick honey and once you begin pouring, it drops really fast. Be prepared to stop pouring before you reached the desired quantity otherwise you'll make a mess.
The hardener is really liquid and easy to measure. Since it's a one on one epoxy, you only need to pour the same quantity as the resin. Once the two are in the same cup, you need to mix the mixture to homogenous state. It's really easy to see when you can stop as there is no resistance and there is no longer any traces of the honeylike resin. And you don't have to worry about a time limit before the epoxy freeses as this is an overnight process.
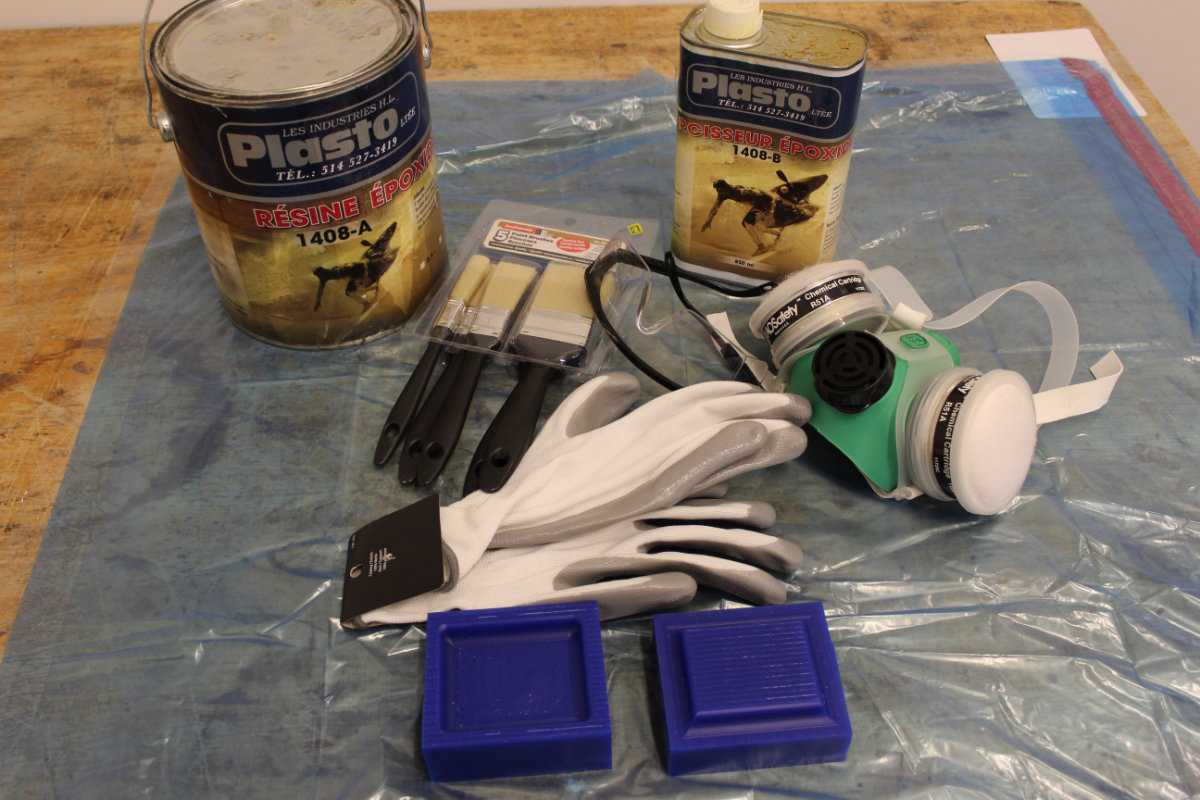
Once I had figured out that the resin was ok, I putted the female mold in front of me, picked up the brush and started to put resin in the bottom of the form. I then placed a layer of jute and dropped some more resin to imbibe the textile. Then another layer of jute and more resin. This job don't requires precision: you paint the resin, you push with your gloves the jute just to be sure that it is fully soaked with resin and you go to the next stage. I was done really quickly.
Once the fifth layer done, I put the other half of the mold on top and pressed. The release of the excess resin from the mold gave me a nice feeling that I have done a good job of soaking the jute. I put everything into the suction bag really quick, to avoid any spillage, and away from the suction hole, to avoid the resin being sucked into the shop vac. The shop vac was turned on and the air was sucked out almost immediately.
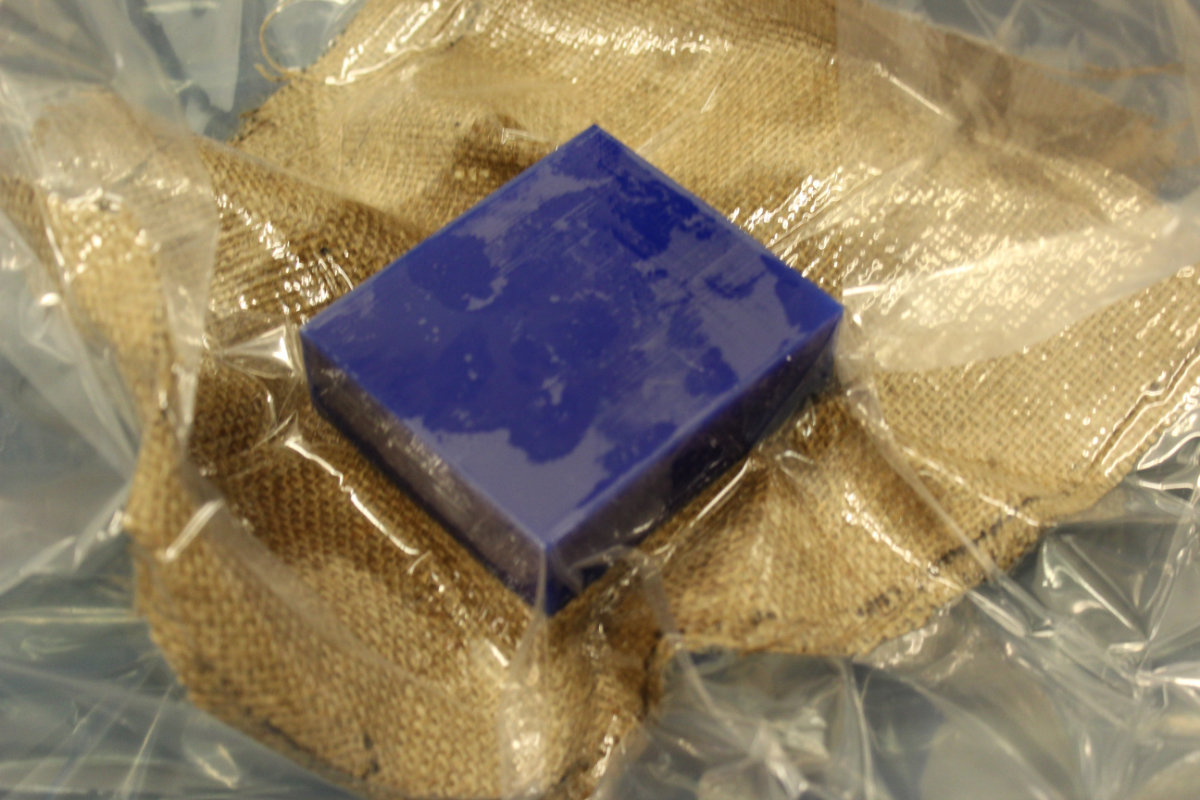
Now that everything is done and there nothing left to do except for the resin to set, I clean up the area and wait for the unmolding.
The unmolding
A little surprise was waiting for me this morning. When I picked up the mold, expecting something rigid, I felt something flexible. Not good. I carefully unscrew the air valve to let the air in. While doing this, I touched the mold: bad idea. Really bad. As I felt the sticky resin on my fingers. Expecting a solid mold, all that I had was an slimy jute with stiky resin that stick to your fingers even after washing your hands many times. I rapidly realised that I made a mistake: wanting to do production last Friday (I was milling boards) I never realised that there was a reason for the different sizes for the resin and the hardener container: proportion! My instructor told me that it was a one on one part but it's actually three to one! It was sticky because there was not enough hardener.
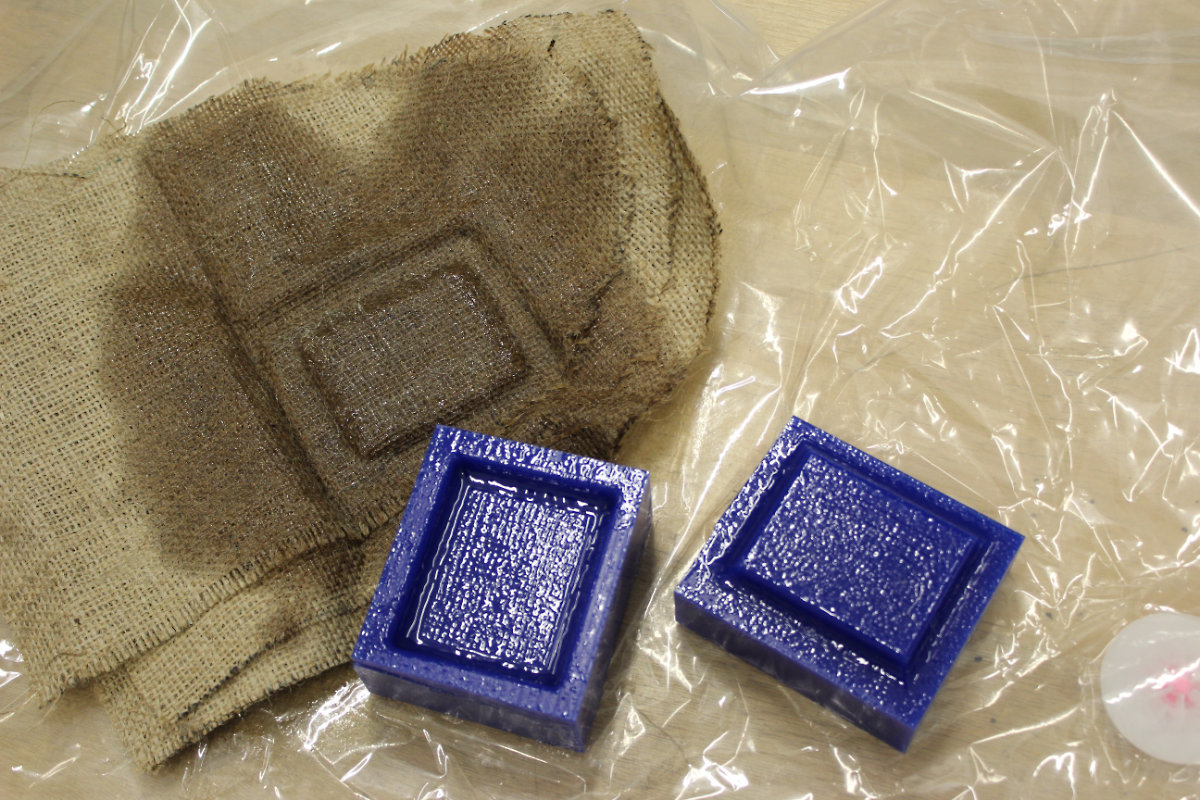
I still need to clean the mold from the resin. Once this is done, I will redo my composite assignment with the correct proportion for the resin.
Can't wait!
Cleaning the mess
The molds were incredibly sticky. So much so that they needed to be clean because the resin was transfering to everything that I touched. I started to use lighter fluid to clean up the surfaces: it was good but eventually, it started to get smelly. I then tried alcool and I was cleaning way faster... without the smell. I tried ethanol and it was a little bit faster, with a slight odor. Once done with my assignment, I will make a thorough cleaning of the molds with ethanol so people will be able to handle the molds.
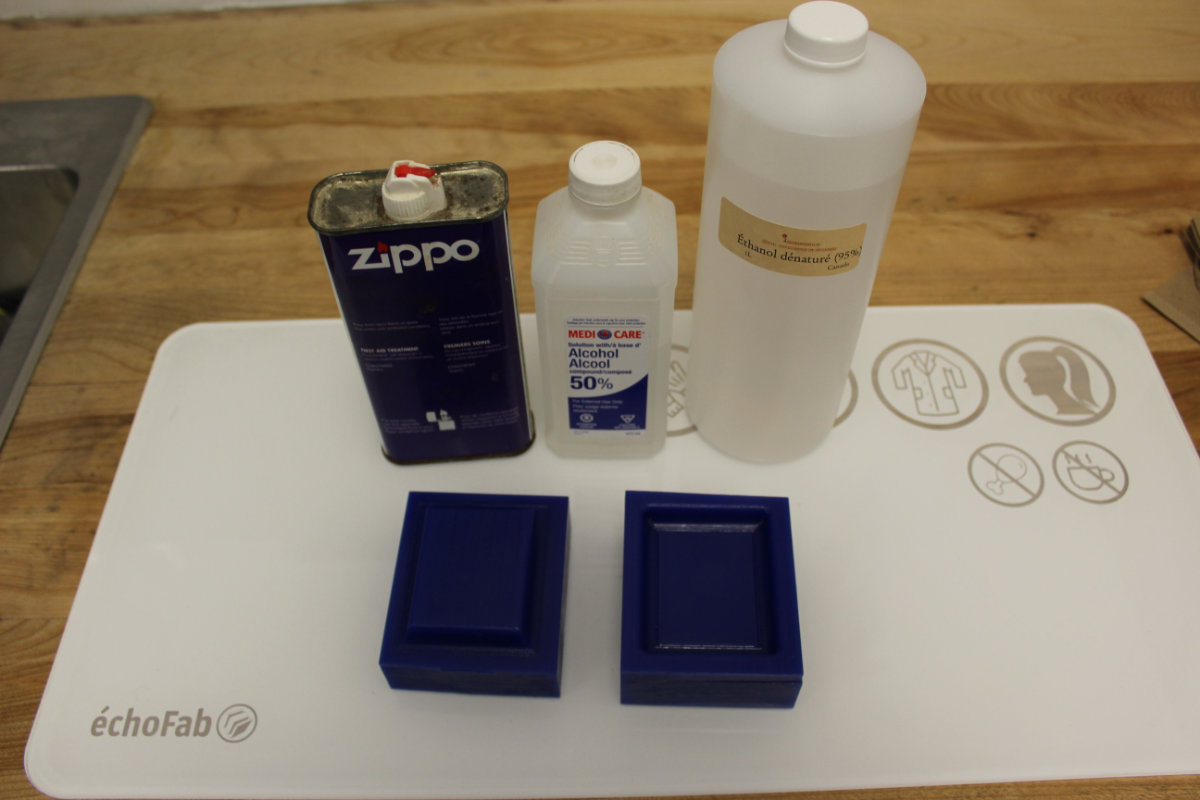
The Second Molding Session
The molding session went as planned. This time I wasn't alone as I helped François Auclair doing this assigment. We had everything on the table and the bags were laid on the floor, ready to be sucked. We measured the mixture for two, weighting 109gr of resin and 36gr of hardener for a total of 145gr of resin (3 to 1 ratio). the whole operation took less than 15 minutes.
The Second Unmolding
When I came in the morning, I took the time to sip the coffee and went to the shop to check the bag. As I touched the border of the jute, I felt that the jute was hard.
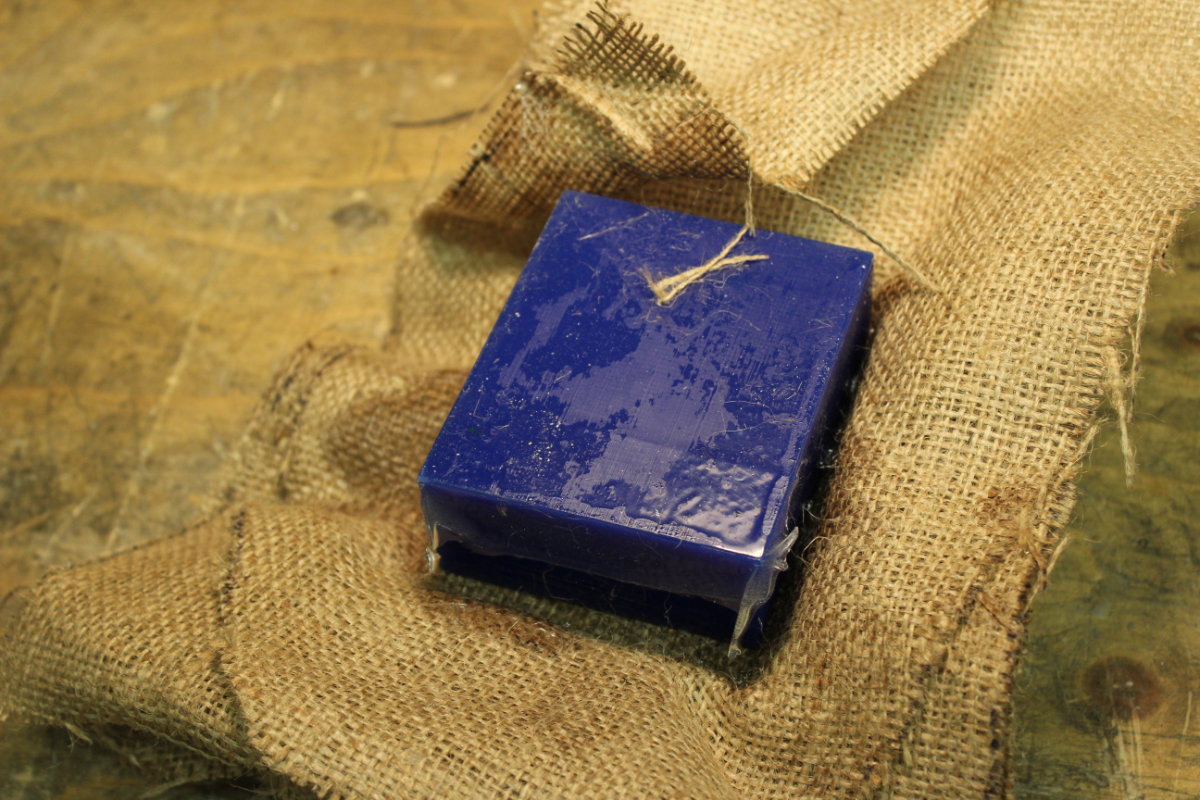
Unbagging the mold was easy, unmolding was surprisingly hard. I took a knife and carefully cutted the border between the mold and the resin. Eventually the part came apart. And I had to do the same to the other half.
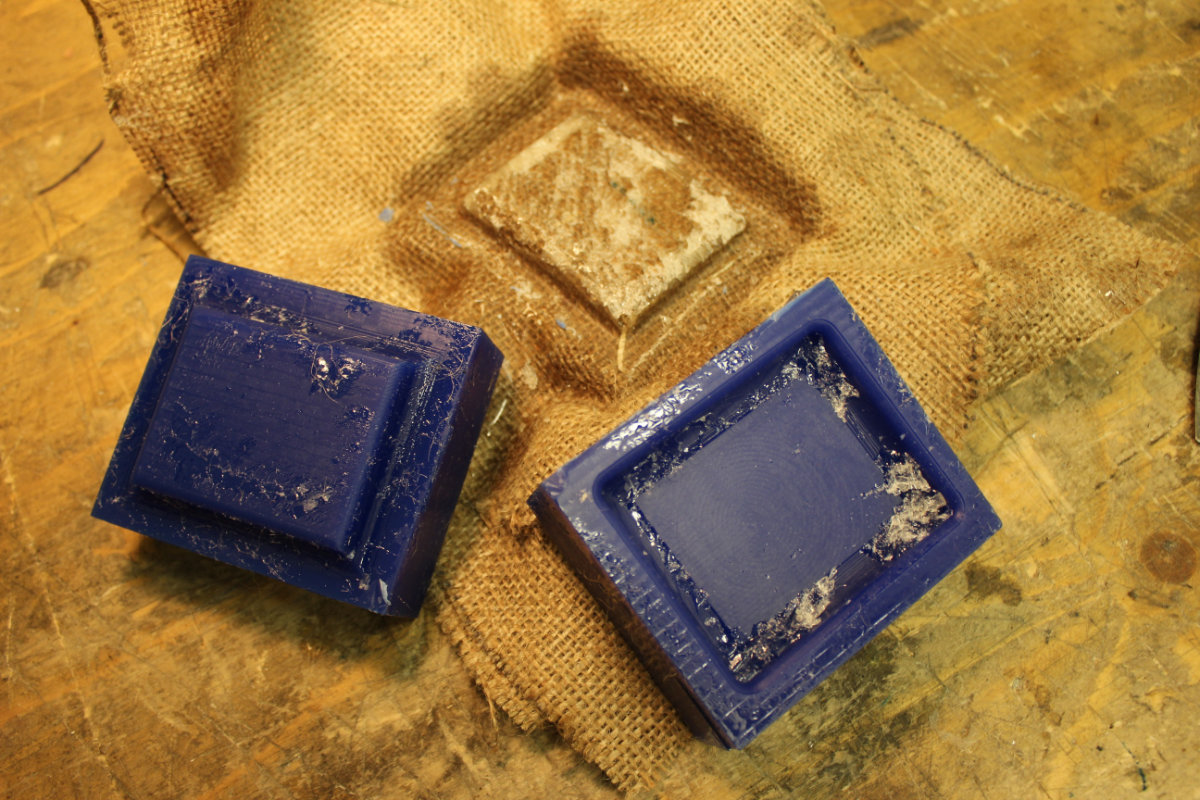
Design failure
Unfortunately, as we had to split the resin into two molds, there wasn't enough quantity to entirely fill the mold and the results were less than stellar. Also, when unmolding, some resin stayed in the mold, breaking a potentionnaly smooth finish.
In retrospect, I would have had more than enough time to mix another quantity and fill the mold and put some release agent inside the mold.
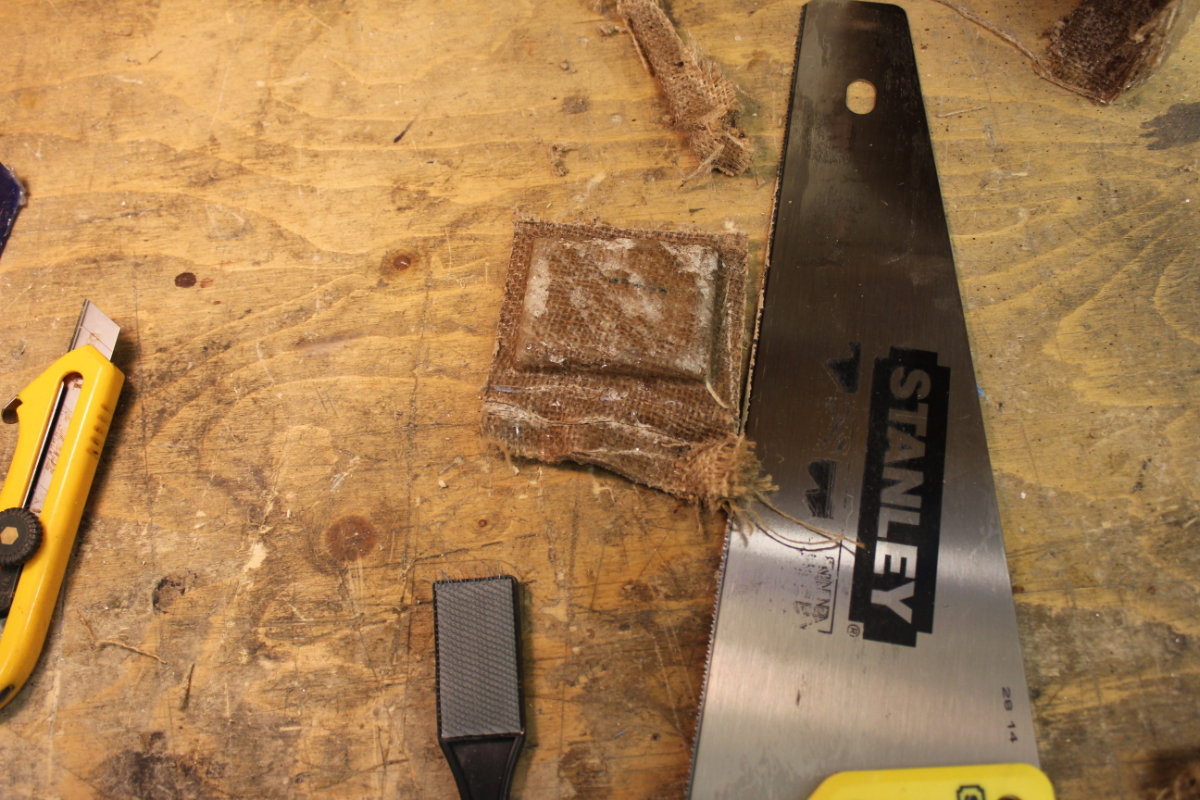
But oh boy, this resin is hard! I started to cut the extra jute with a knife but I rapidly changed that to a saw, just to give an idea of how hard this stuff is. After that, I sanded the edges smooth and was done with my cover.
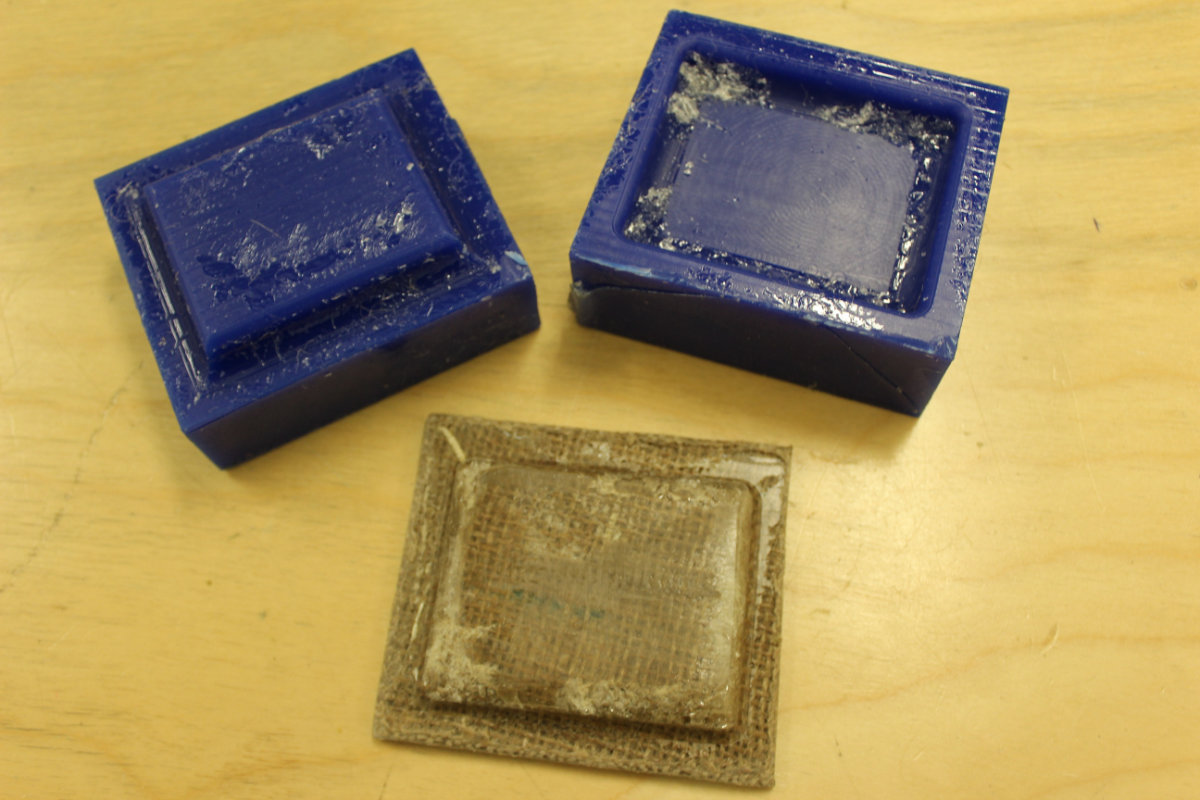
Final thoughts
Although messy, this process is easy to master. I never made resin, and this was my first experience, and not the last. Unkown to me, I have all the necessary equipment in my tool room, including the respirator. Considering this last item, I would recommend for any one who hesitate to try composite resin to not hesitate: it's fun! But protect yourself and buy a good quality respirator (not those cheap paper respirators). You won't regret it as you will not feel dizzy and concentrate to the task at hand.
Also, this is a quick and dirty way to do a mold. It is not for mass production as it is labor intensive, especially the unmolding and cleaning of the part. I was surprised at how much the resin actually stick to the wax, it not often that you see a material sticking to wax. Next time, I would advise to add a releasing agent in the mold.