Mechanical Design
Week 15
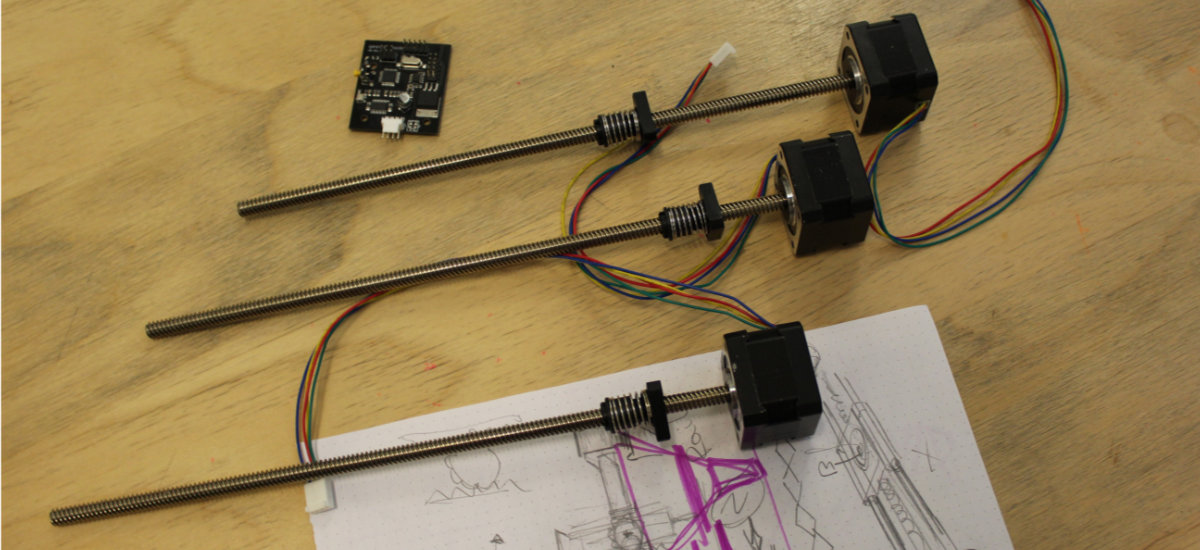
This week and the next are special because we must work as a team and develop a machine that can be controlled electronically. Right after Neil's presentation, we settle down (Alec, George and me) and start designing a machine.
First brainstorm
We came with a first idea of making a turntable-like machine in which we would be making circular drawing on paper, similar to a vinyl cutter. We manage to get a few idea of what the machine would do. George made a rela quick design on the computer of the turntable in action with an arm, with the motor, swinging in and out of the circle. We tried other ideas but these we dismissed.
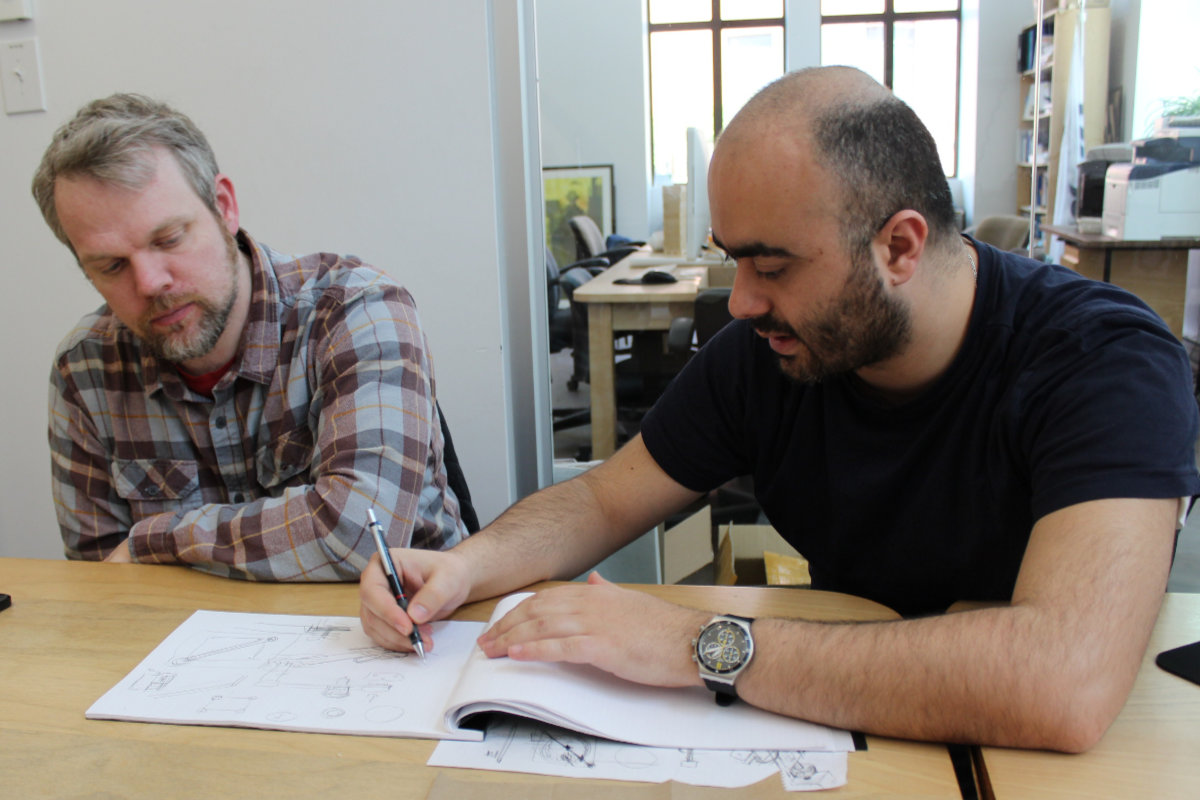
We then change the plan for a new machine that instead of being rotary, the platter would actually be a convoyer belt with a rolled paper and a funnel containing both sand and glue that we would deposit on the surface of the paper to make multimaterial artistic shapes.
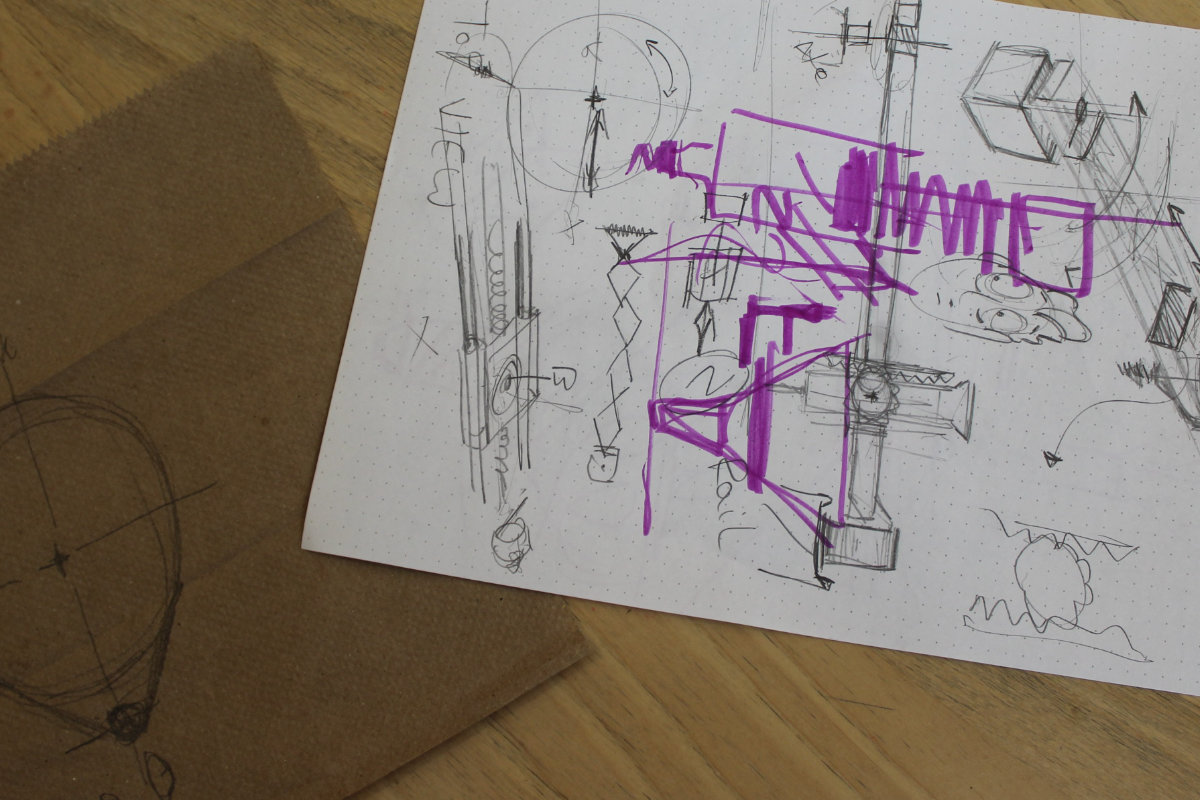
We then decided who would make what. I decided to focus on making the motor controls, of which we need three: two linear motors and one rotational. I would also make the appropriate research to ease the making of the machine.
A first surprise
Suddenly, George came with an old contraption that came out of a junked printer. It looked like what we needed for a quick start but I felt uneasy about it. Sure, there was a motor, but this one was a DC instead of a stepper motor. Also, the opposite bases were unequal, which meant some tinkering for to make the base equal. And the moving part doing the linear mouvement had a shape useful for a task that is entirely different from what we had in mind and would need some attention. And last, the maximum width was 8 ½" standard, but narrow. A starting point that need some work, but how much?
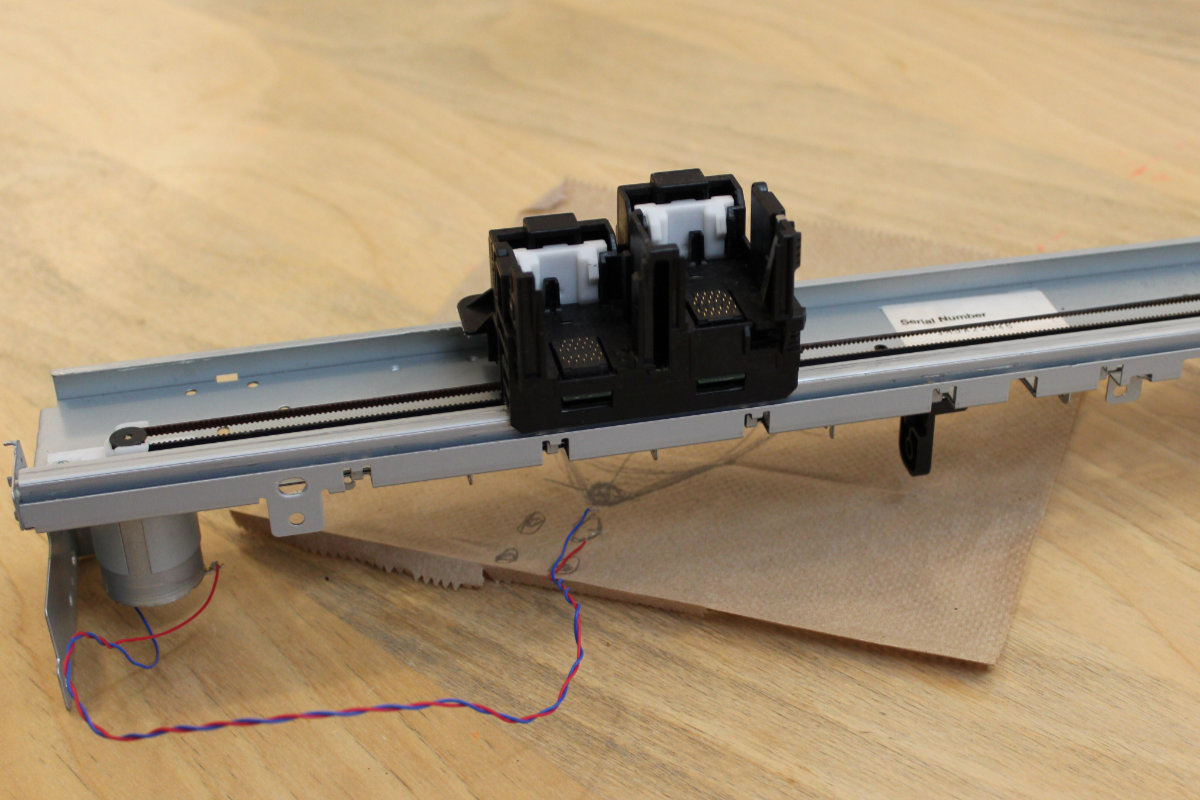
The second surprise
While exchanging ideas, Mathieu came to me and gave me a circuit board telling me to check up on this one. I asked some questions about it and he told me that this was a Gestalt Node that can control a stepper motor. What's more, we had a kit comprised of three stepper motors with a long mechanical screw. My first discovery was Fab Academy website that gave the impression that this board was lacking in support. After talking about this problem, I was told that there was some doc and I redoubled my effort to find some and started to get some nuggets about this system. The main problem is the the GitHub depot where the code is, has a link to a website that says that it will be available in November 2013. Also, you get a link to a master's dissertation! Not a good start. I eventually understood that this dissertation is important and is required reading.
But once I started to use the author's name, Nadya Peek, I started to get more and more useful links that I put in here. So yes, it looks like there's information on how to use Gestalt Nodes but it is scatterred everywhere and there's no central repo to help people get started. I hope that this site will be helpful.
Gestald Node
The main advantage is that this system was designed for rapid prototyping with simplicity in mind: the use of cardboard for making the frame, a stepper motor, a screw, two guides and create a motorized module. One module can be added to the next and the motors are daisy chained to the next. But there's a two problems: first, the rotary stage, considered important by the author, has no page reference. This module is important to our concept (or other projects). Also, the dropbox containing the cut files refered to in the [m]MTM website is now a 404. I guess we'll have to make do with the motors.
This is a very interesting concept and let's see where this will led us to.
The building of the linear stage
As I came at the lab, Alec had cutted the file for the linear stage. With an X-acto knife I carefully removed the part from the cardboard. Alec warned me that the original file were not to scale and he had to guesstimate the scale. I started to make the assembly and eventually came up to a wall: the parts don't fit together. I tried with many configuration but whatever I do, the holes for the aluminium and the motorized shaft don't align. We'll have to fix this.
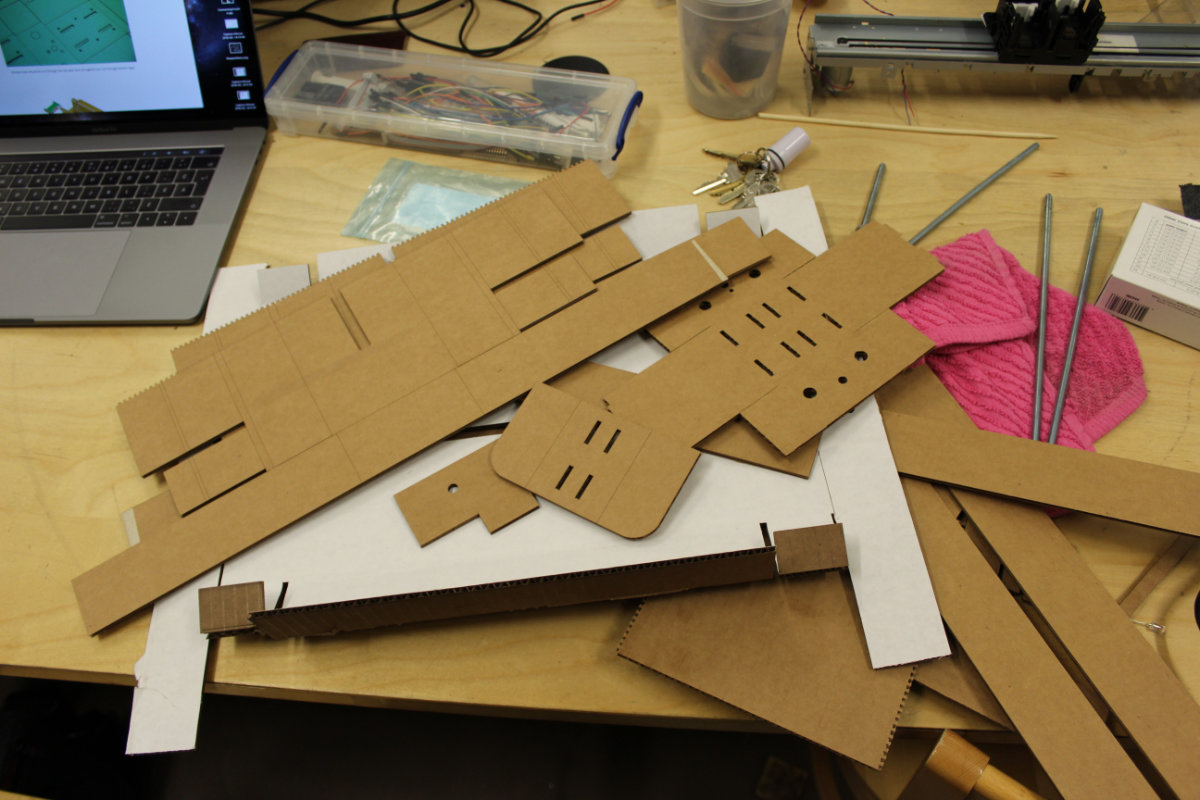
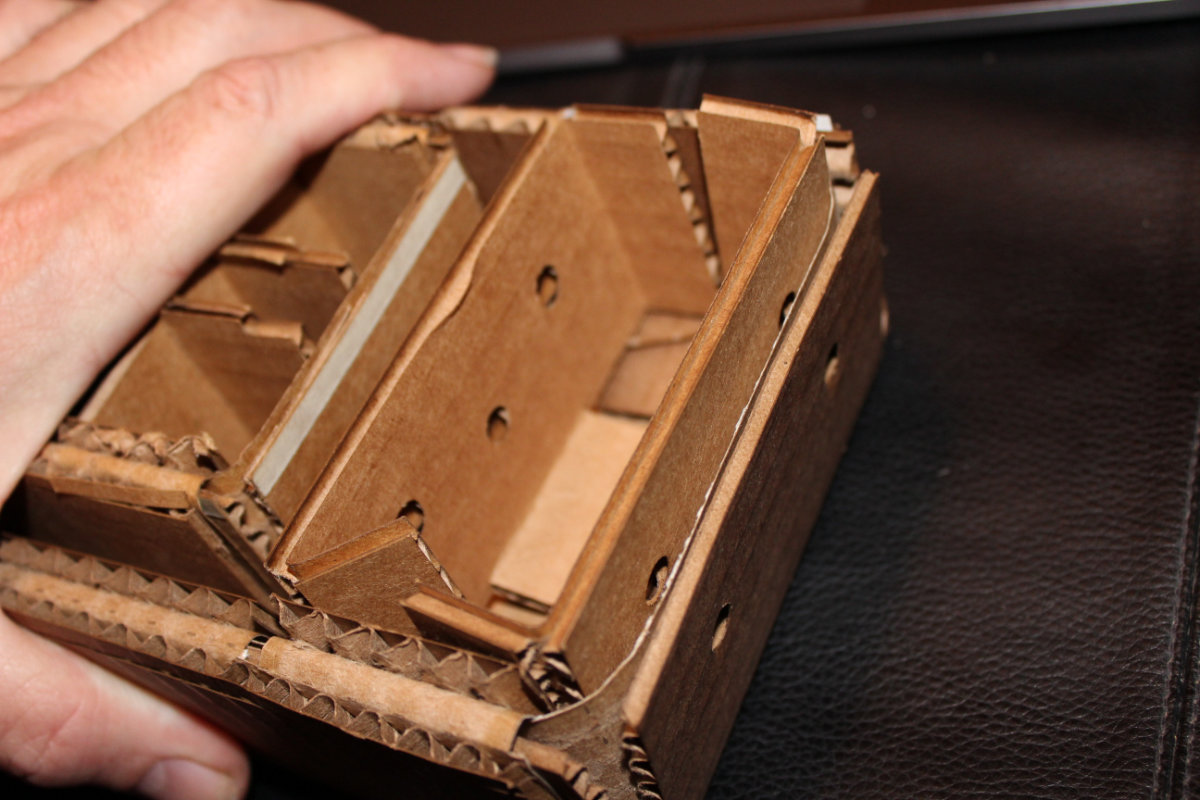
Fabnet
My first task is to get the node working. I carefully read the documentation and found that I need a module that connect the computer to the first node. I found this module at the Fab in a box website. It's a small module that uses a FTDI connector but the order of the wires are mixed up. Since we had FTDI cables with the connector, I was a little uneasy about cutting that connector for the Fabnet board and limit the usage of the FTDI wire exclusively to the Fabnet board. Mathieu came up with the idea of soldering jumper wires (with appropriate colored wires I might add) to the board instead and having the best of both world... I should have thought about that!
Since the mill was configured for pcb, I prepped a copper board and put it in place. I picked up the Fabnet trace from the website and push it to fabmodule. As my previous job, I configured the cut speed to 6mm/sec and, for once, put a -1 to get a clean board. The time to get it done was estimated at about 35 minutes.
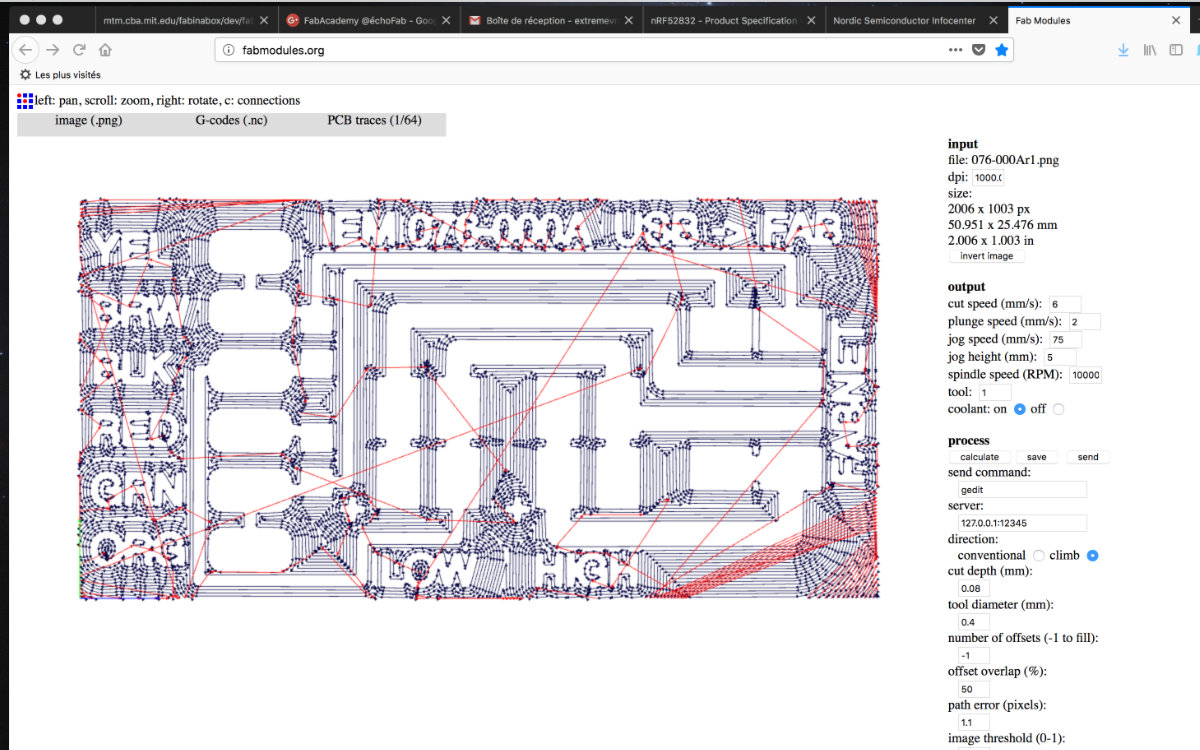
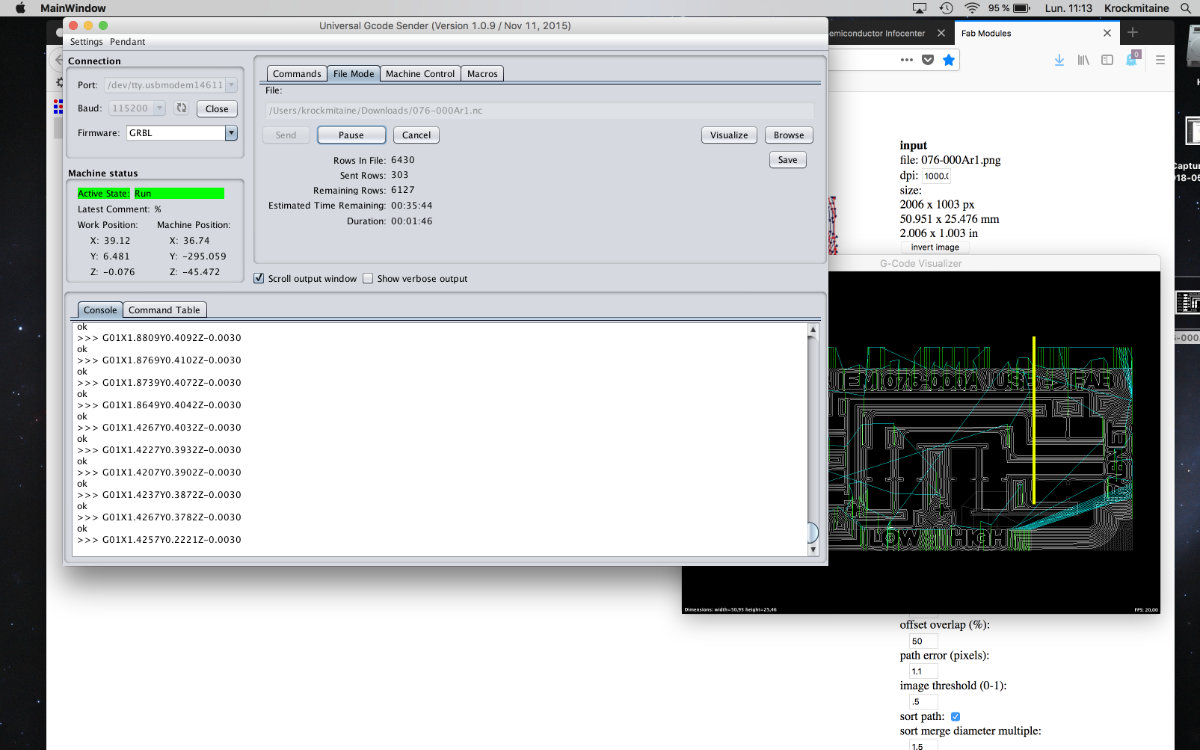
The board was done with no problem and came out really nice.
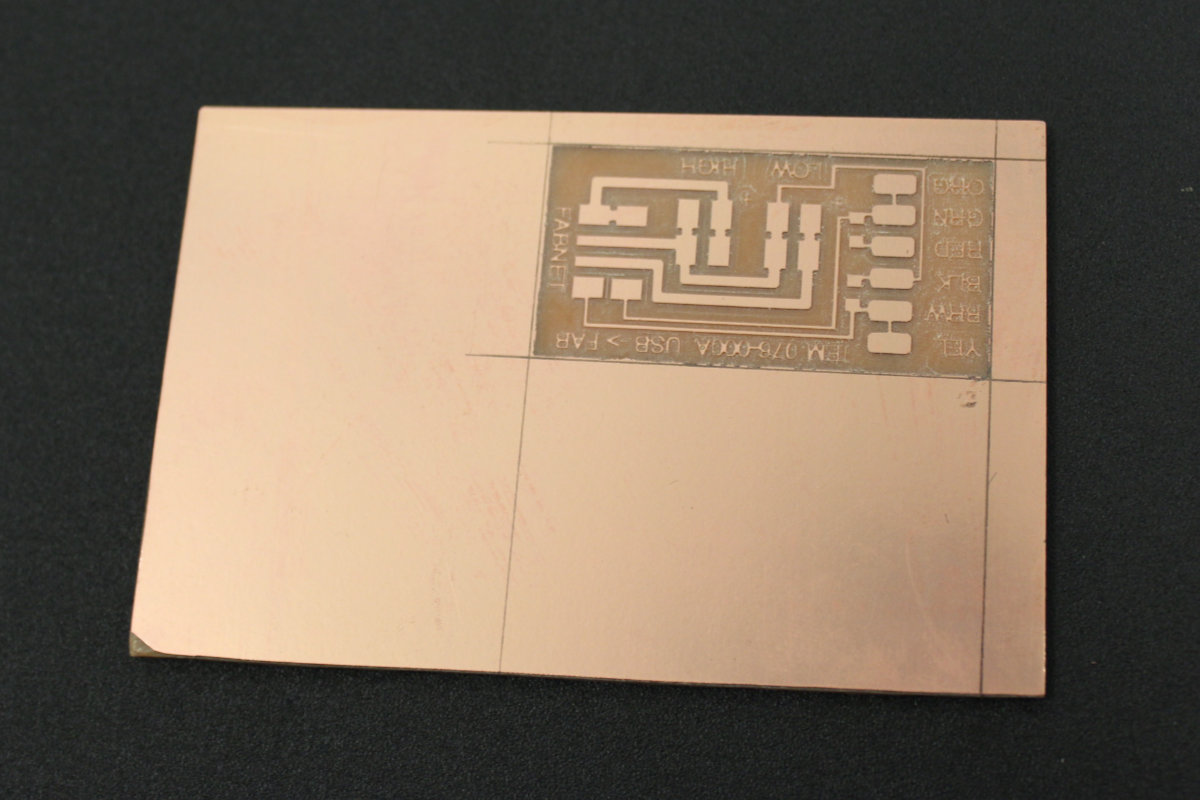
The soldering is really simple; two resistors plus the six wires to solder. I almost lost the board when I tried to solder the first wire: somehow, the solder did't stick to it. Try as I might, I couldn't get it done. As a solution, I decide to change the wire because cutting it down implied to cut all the others in order to have the same lenght. I did it just in time because the copper pad was starting to peel off the base. The other wires were easy to do as the header pins.
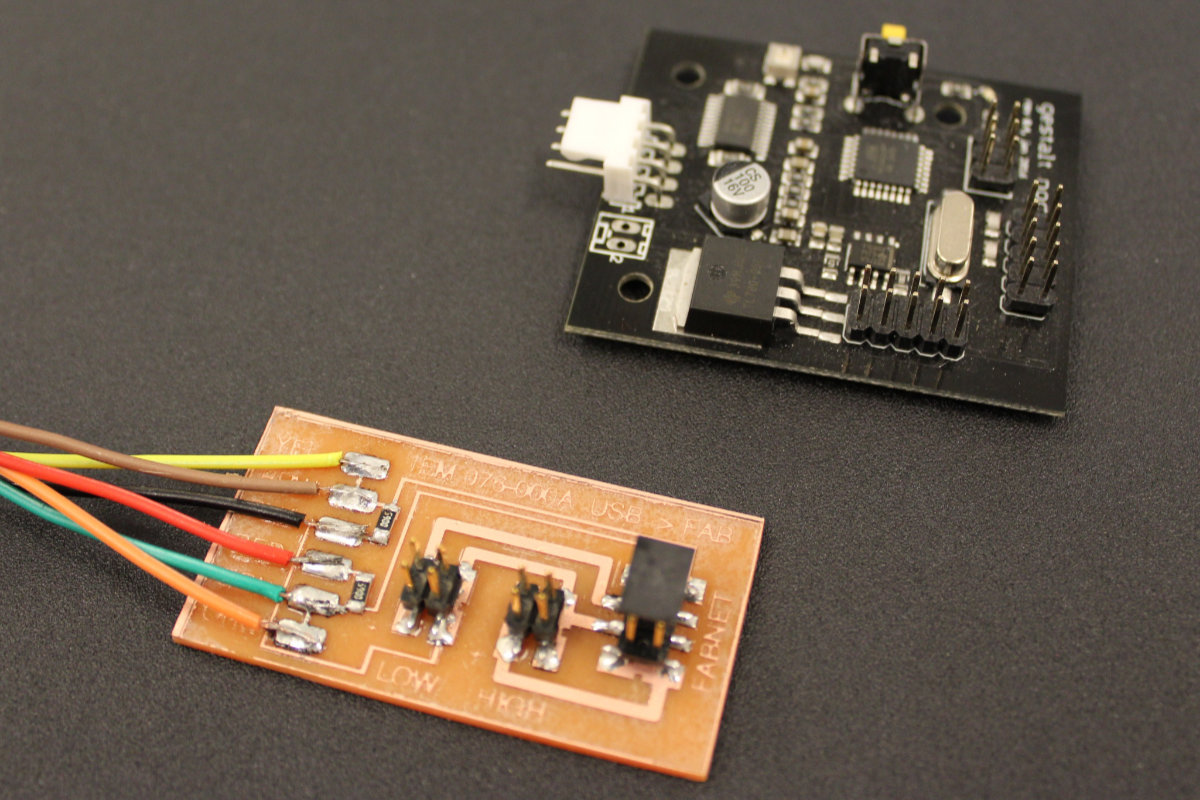
Oups...
Although I was careful with the soldering of the pins, double checking that the male was at the appropriate place, only when I tried to connect the FTDI pins that I saw that I made a mistake: somehow, I chose a female-female connector! I had no choice but to put back the soldering station and correct the situation.
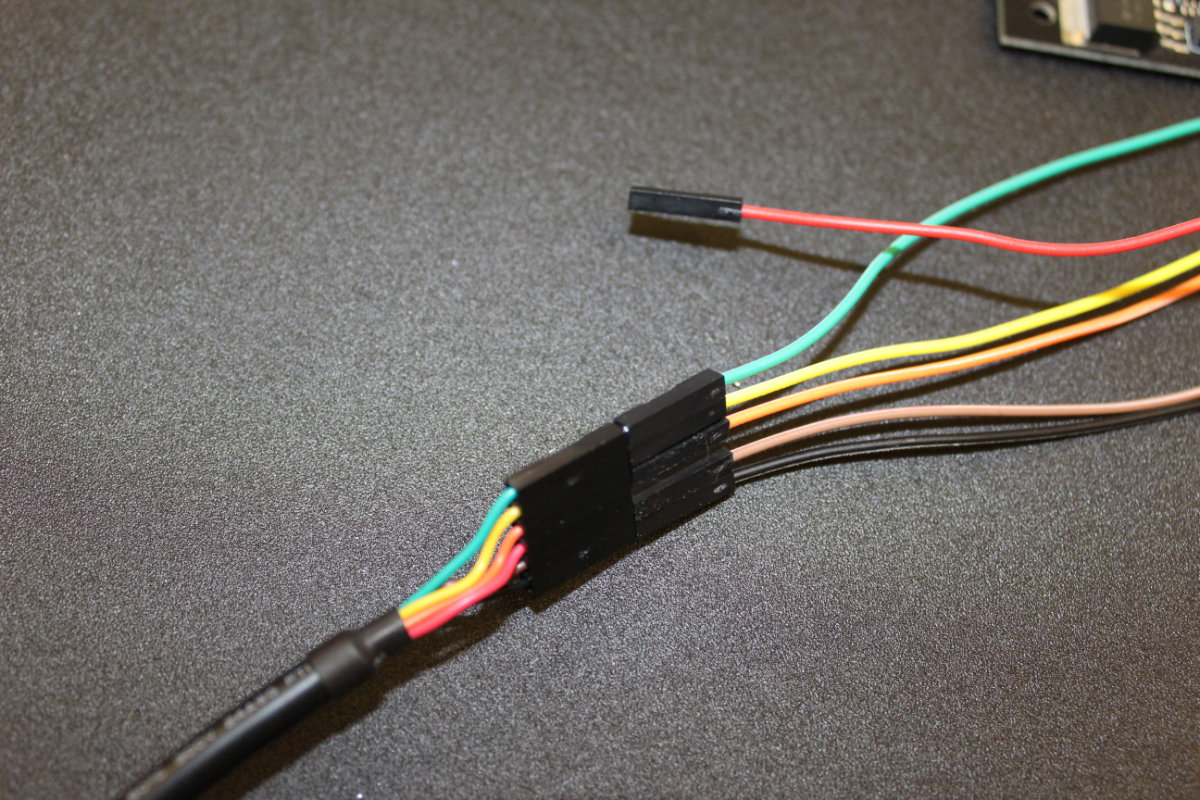
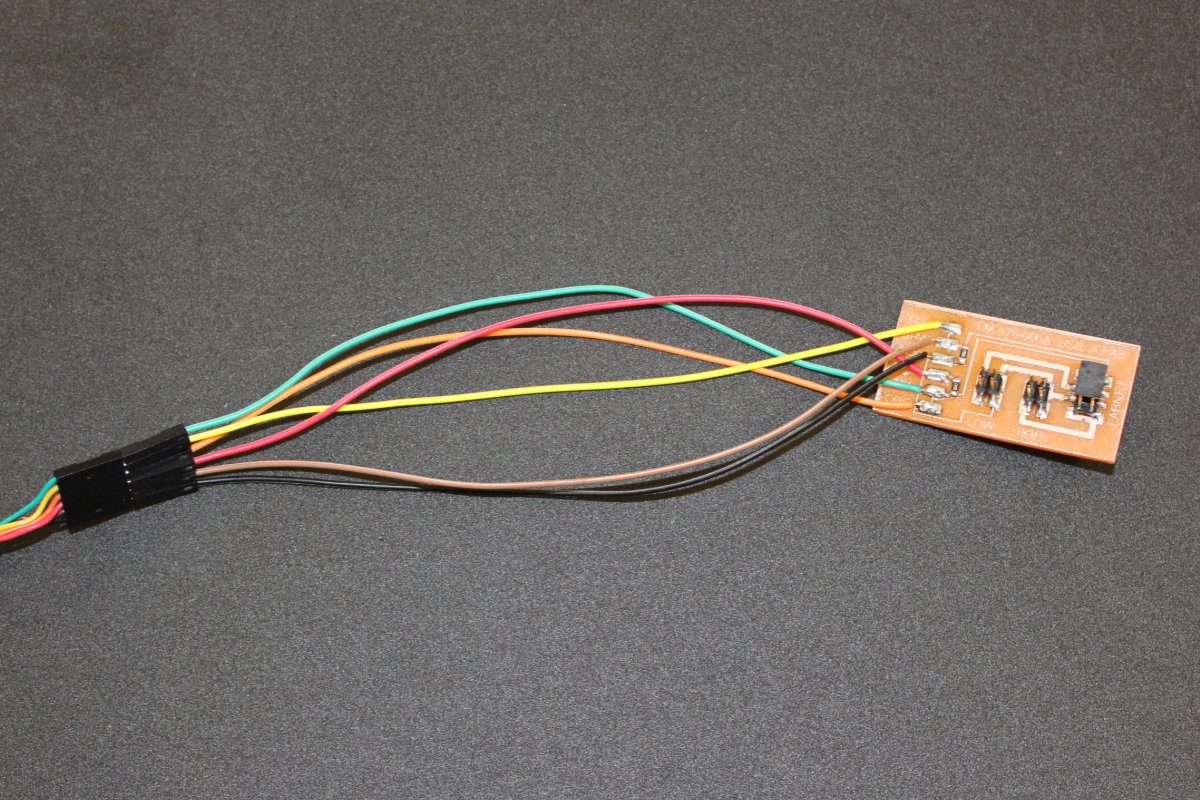
The problem with the transformer
Since I need some electrical juice to power the modules and the motors, I need a separate power source to feed the Fabnet module. I found a 7.5 DC transformer in the bin cut the adapter and for the heck of it, measured the voltage and be sure of the polarity of the wire -before- soldering the connector wires. To my surprise, the reading came out at 11.9 volts! Way too high. I went back to the box because there was another transformer without any purpose in life, this one universal. At 7.5 volt setting, the voltage reading was at 11.4! I checked all the different voltage but they were all off the scale. My investigation was interrupted because of a meeting with my regional mentor. As he told me, one strange reading is ok, but two, you'de be better off checking your instrument. Indeed. Next step, I will check the instrument with the regulated DC power transformer that we have at the lab.
The problem with the cable
During the meeting with my regional mentor, he pointed out that the first ribbon connector had two switchover cable that must be configured. Since this one is not documented, I ask questions about where I should get the schematic for this one. Alas, it seems that this cable is not documented yet.
The problem of scattered documentation
After reading Getting up with Gestald Nodes, I found out that those problems might not be problems after all. The 11.4 volt output is really near the recommended 12V needed for driving the stepper motors. In the same web page, we find the documentation related for the connection between Fabnet and the first Gestald Node. Although I read about Bas's board, I didn't quite understood the need of it until I learn that I must reverse some wires between Fabnet and the first node. Bas's board eliminates this problem.
Gestald Nodes really need a central deposit to help users and future fab academicians.
Configuring the first node
As I noted earlier, the first thing that I done when I went back to the lab was checking the multimeter that I was using against a regulated power supply. The reading were correct so it was the transformer that is giving out more juice than the specs printed on the power supply. But this voltage was what I needed so I went along, soldered the tips of the wires with connectors and added heat shrinks tube to go over the solder contacts once this is done. I no longer use electrical tape to do this. I've learned my lesson the hard way.
Once this was done, everything was set to power up the Gestald Node. Since I didn't had accesss to ribbon cable, I picked up connector cables instead. Before lunch, I made an initial setup with no power. When I came back I carefully checked the wiring and correct a misconnection that I made. Once this was done. I check again and finally powered my setup. Contrary to what was expected, nothing happened, no led blinked to acknoledge that it was under tension. Since it was a test, I turned off the power supply and then installed the necessary software. I followed the instructions given in the Getting Started With Gestald Nodes page. I installed the Pygestalt, edited the singlenode.py
file with my device ID. I powered the GNode again, typed python singlenode.py
and nothing happened. Next I read that I needed the pyserial, I followed the instructions and the install went smoothly. So now at last I had everything. I powered the board, typed in python singlenode.py
again. The terminal sended me the following message:
FABNET: error opening serial port /dev/tty.usbserial-FT90ZRJN
FABNET: serialInterface is not connected.
As I was trying to debunk the problem, I touched the wires, they were hot, and George warned me that there was smoke coming out of the power supply! I pulled it out, it was really hot, from the power bar. Once the smell abated, I realised that my power supply was junk. Fortunately, there was another one in the box and made the same modifications as the first one. Once done, I retrace the previous steps that I made, made the connection while touching now and then the power supply in case it was overheating. Nothing was wrong. But I was still getting no connection. I remade the whole setup, checking all the connections, checking if the board was receiving the appropriate 5 and 12 volts (success) and I still had the serialInterface in not connected
message at the terminal. I talked with Mathieu about all my verification process, the fact that the led never lighted up, and we came to the same conclusion: the Gestalt Node board was dead.
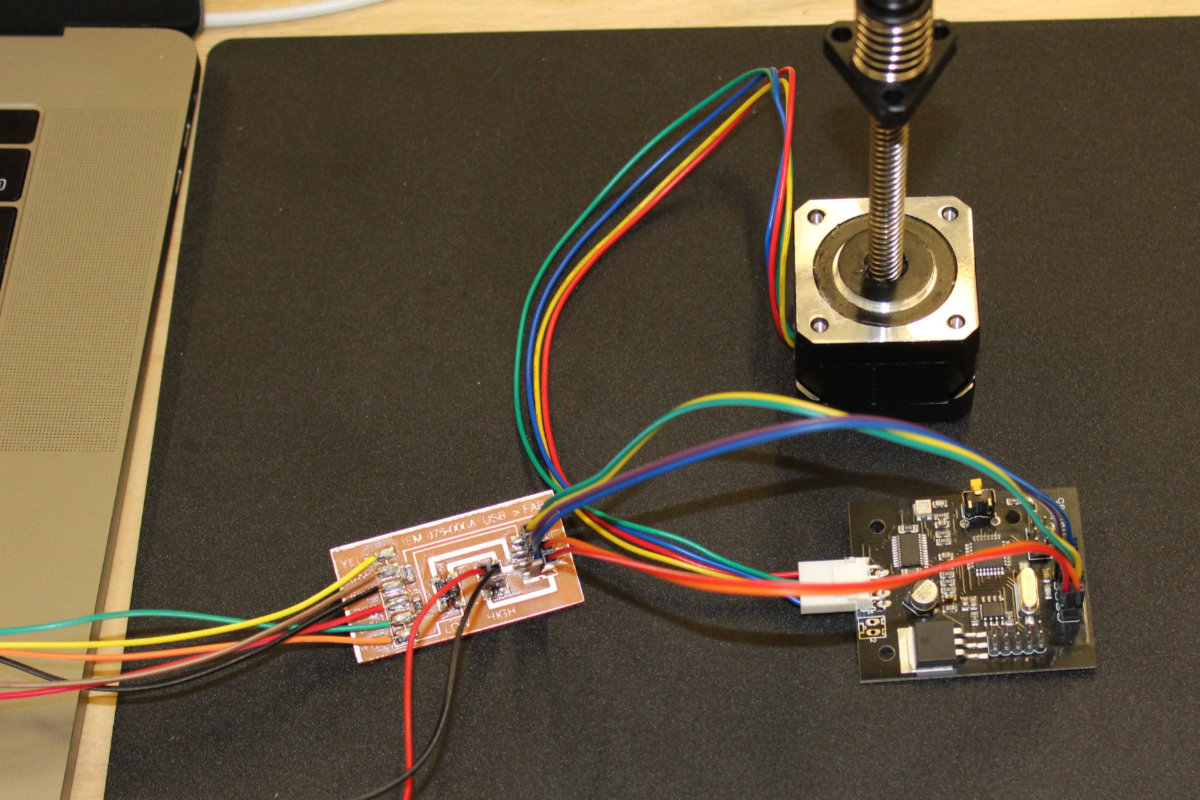
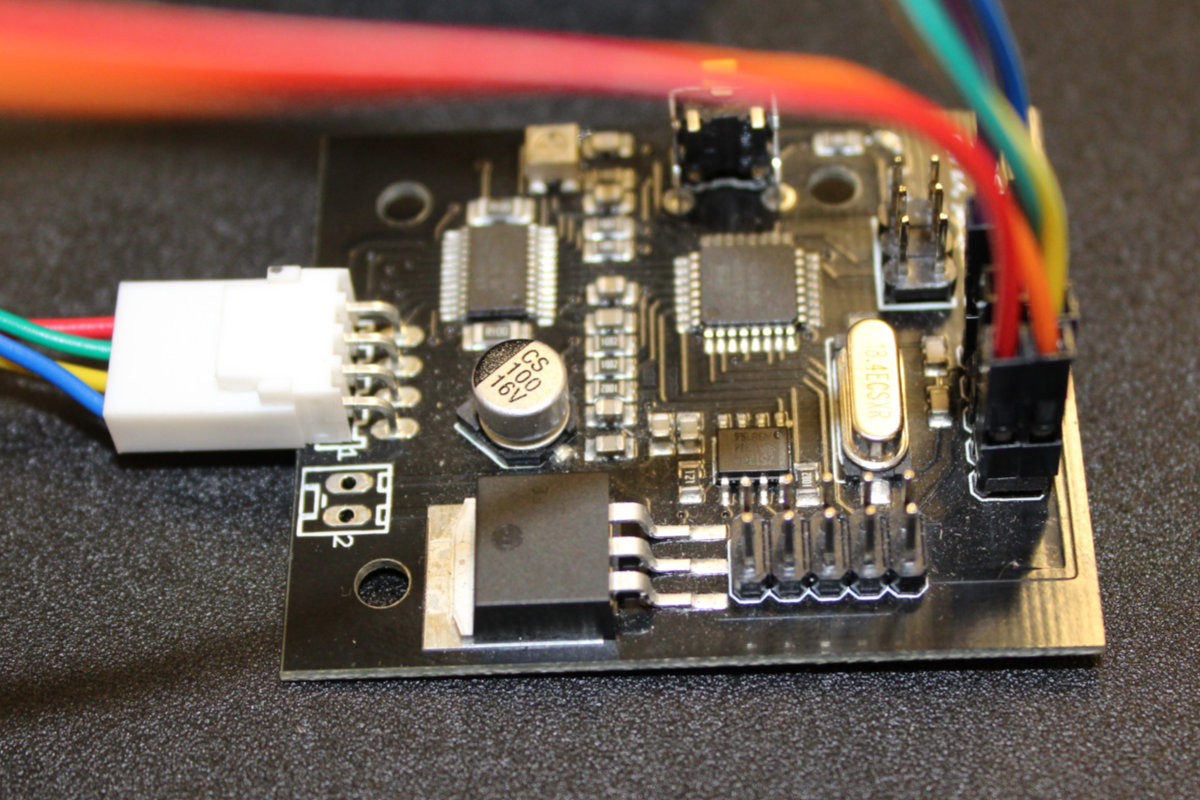
While waiting for the Nodes...
My work had stopped once the Gestalt Node was declared officially dead. In the meantime, I helped Alec while he was building the machine. Including George, who was working on the effector, we stayed late in the evening, slowly progressing.
The roller assembly
My main contribution of the evening was the building of the roller assembly. I built a first iteration of the roller with some laser cutted disks made from 6mm plywood. I found a stainless steel shaft and hammered the disk into it. It made perfect alignment but at the cost of breaking the wood around the central hole. I then put some black tape to create a high coefficient of friction so paper would hold unto it. That version was rejected because the diameter was too small and the paper wouldn't even grip the roller. For the next design, Alec came up with the idea to put elastics into grooves to make a better grip for the paper.
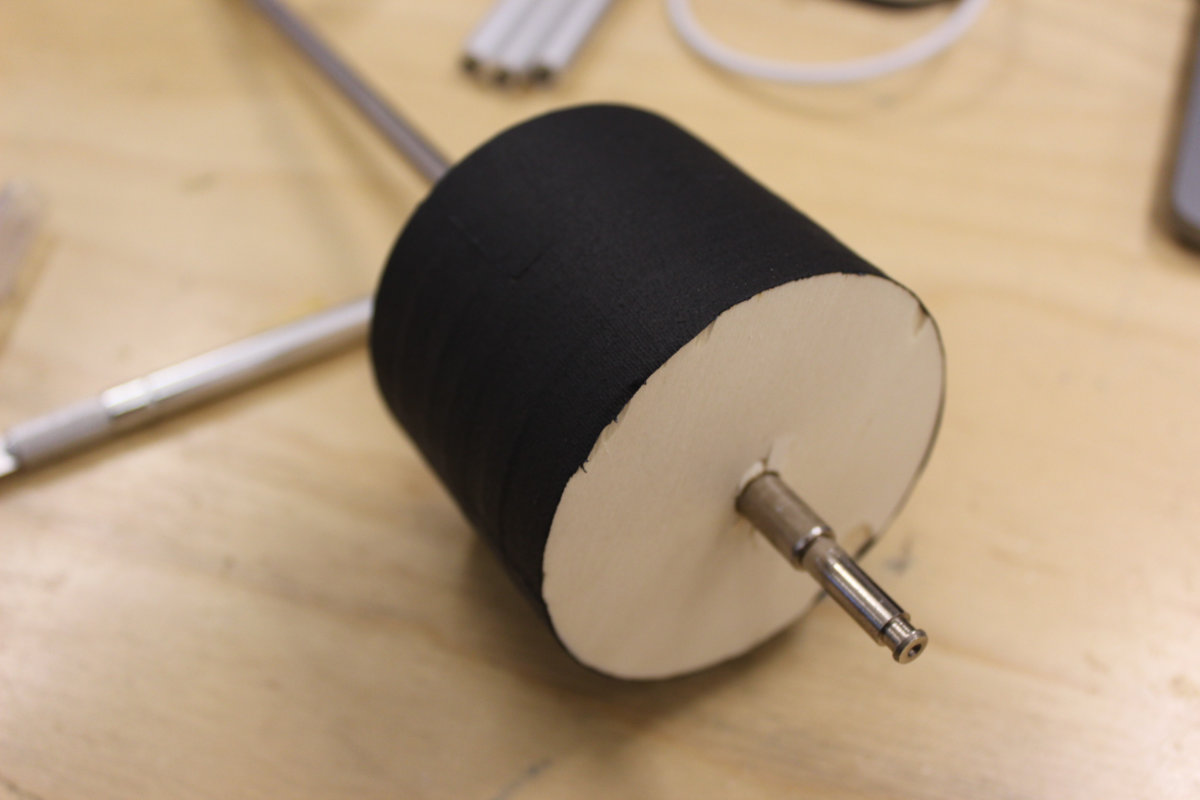
With a description of his needs, I calulated the differents radiuses of the disks. I made a serie of disks (2 disks of 92mm dia. and 1 90mm dia.) I glue them all together with the help of the steel shaft and tested it on the shaft of the machine. To say that this initial test was a success would be an undestatement. We forced this roller in the shaft with the intent of testing the usability but instead we embarked in a battle to remove the roller without destroying the machine. We released a collective sight of relief when the roller came out of the shaft, but we were tired and had to fix this problem. I made four holes of different diameter to test the fit on the shaft and laser cut them. From my test, I found that the optimal dimention was 7.79mm diameter, which, I would later find out, correspond to the steel shaft that I was using for aligning the wooden disks.
Once ready, I made a series of 90mm and 92mm on the laser cutter and went to the tool shop. I glued the wood disks together to make the roller assembly, letting them dry. Once dried, I used the shaft in a vise and put the roller assembly into the shaft for the next operation. This was my setup to put the rubber band in the grooves. This operation proved to be a struggle as the rubbers bands that Alec provided was for use in an industrial setting, not for regular use. Moreover, they had a smaller diameter than the grooves and had to be force feeded into the grooves. I had to find a solution because I couldn't place one rubber in the grooves with my hands. Eventually, I founded a offset screwdriver and used it as a guide, forcing the rubber to pass over the wood disk diameter and into the groove. That no rubber band ever broke is a testament of the solidity of the material.
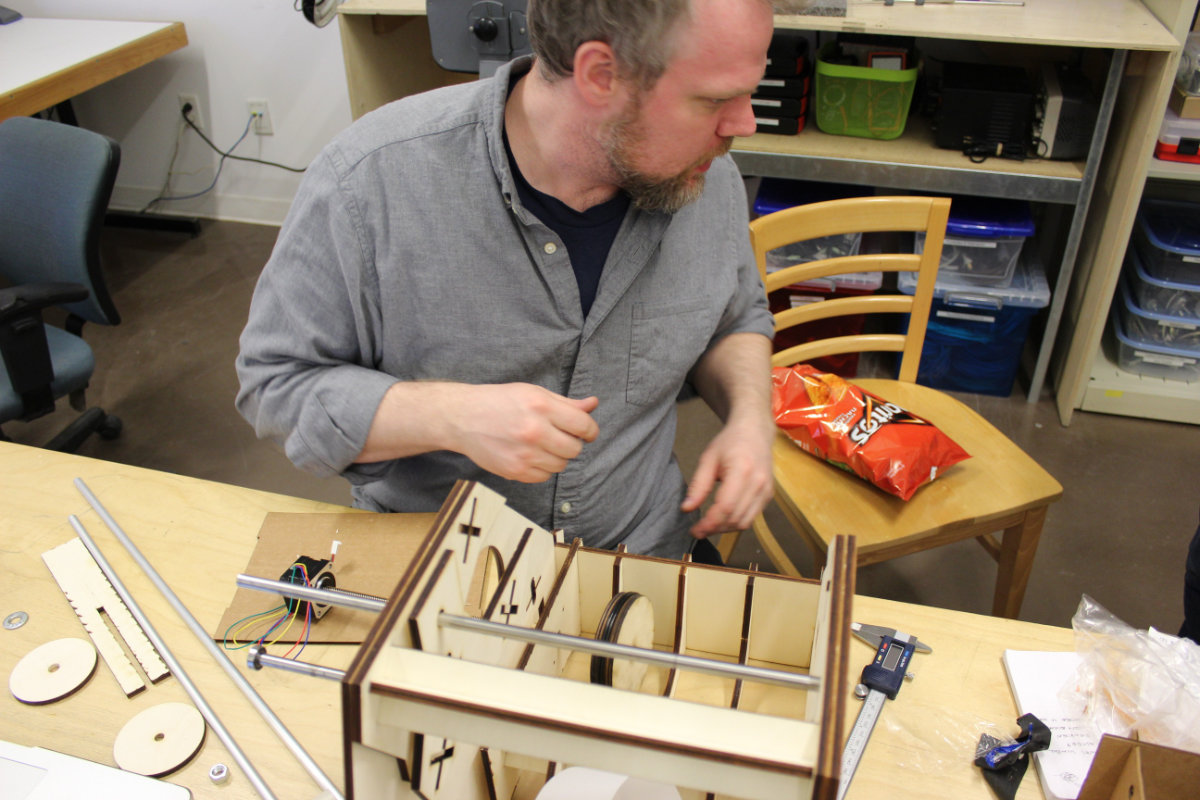
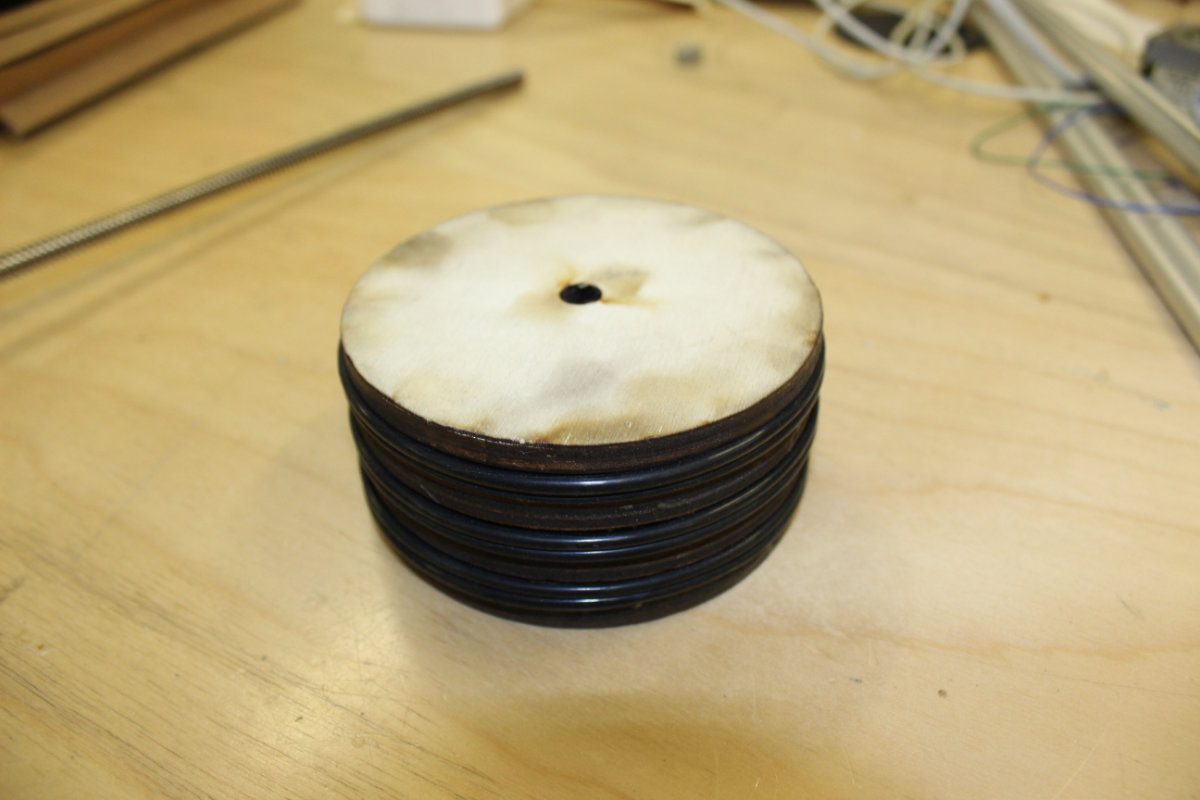
After that we made a test to see if the paper would come out and the test was positive.
Tasks that I've done
For the first part of this assignment, I've done many task toward the completion of the machine, some of them intangible (brainstorming, testing ideas) others not. My contributions are described bellow:
- Evaluation of the old printer head;
- Research the Gestald Node;
- Building the Linear Stage;
- Milling the FabNET board;
- Soldering the components;
- Evaluating the Gestald Node board;
- Assembling the prototype roller assembly;
- Design of the rollers;
- Laser cutting wood disks for the rollers;
- Gluing the disks together;
- Assembling the final roller with the rubber bands;
- Taking pictures of the team working for documentation.