10. Molding and casting¶
Group assignment :
- Review the safety data sheets for each of your molding and casting materials
- Make and compare test casts with each of them
Individual assignment :
- Design a mold around the stock and tooling that you’ll be using
- Mill it (rough cut + (at least) three-axis finish cut)
- Use it to cast parts
Group assignment¶
Link to ULB Group : link
For the group work, I analysed the products available to me. We received Crystal Clear resin, RTV Silicone, but also classic and phosporescent colorants and a release agent.
Crystal Clear resin datasheet¶
Transparent casting and coating. Two component colourless epoxy system.
W241: Recommended maximum casting thickness 100mm
W242: Max. recommended casting thickness 10mm
Colour: colourless
Viscosity at mixing: 650-950
Density: 1.10-1.14
Mixing ratio: 100:45
Potlife with W241: 75-95min
Potlife with W242: 35-45min
Demoulding time with W241 : 36-48h
Demoulding time with W242 : 18-24h
Danger
H315: causes skin irritation
H317: May cause skin allergy
H318: Causes serious eye damage
H411: Toxic to aquatic organisms, causing long-term adverse effects
P261: Avoid breathing dust/fume/gas/mist/vapour/air
P273: Avoid release to the environment
P800: Wear protective gloves/protective clothing/eye protection/face protection
P305+P351+P338: In case of contact with eyes: rinse cautiously with water for several minutes. Remove contact lenses if present and easily removable. Continue rinsing
P310: Call a poison control centre or doctor immediately.
Silicone RTV¶
RTV silicone is suitable for the reproduction of figures, artefacts and similar objects. It is a 2-component material consisting of RTV and RTV hardener. Curing at room temperature.
Technical data with RTV hardener
Colour: White
Hardness Shore A:25
Demoulding after 24 hours at 23° CPréparation du matériel
Potlife: 36-60min
Mixing ratio by weight: 100:5
Tensile strength: 2.8
Elongation at break: 380%.
Tear strength: 2.0kN/m
Linear Shrinkage: <0.8
Relative density: <0.3%.
Relative density: 1.08
Viscosity: 20.000-25.000 mPa
Individual assignment:¶
Design on Fusion 360¶
I have made a name tag for the fablab. It is small but complete enough for the demonstration. After looking at the time estimates for the machine, I decided to make the part on the “big” digital milling machine.
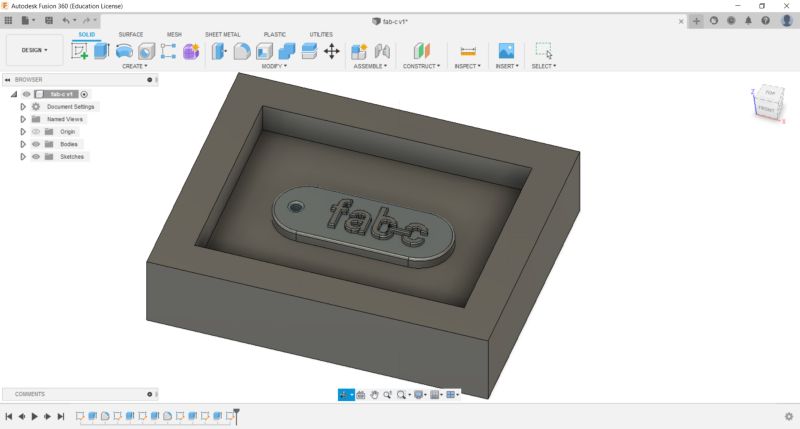
First step, roughing with a 3mm milling cutter
- Optimal load : 1.2mm
- Minimal cutting Radius : 0.3mm
- Maximum Roughing Stepdown : 1mm
- Fine Stepdown : 0.1mm
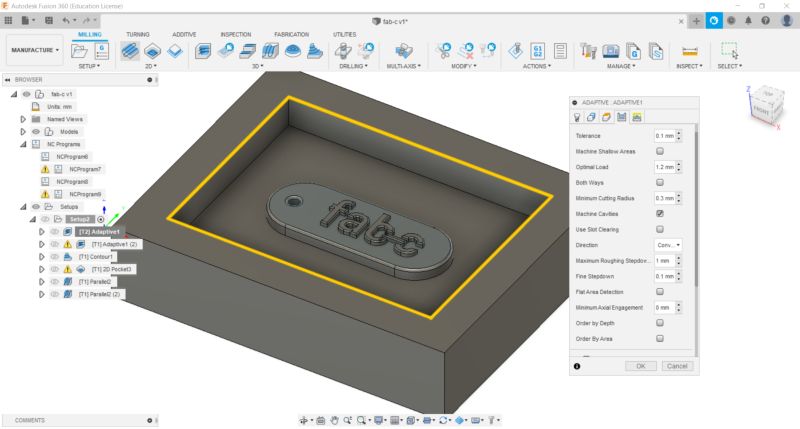

Then roughen with a 1mm milling
- Optimal load : 0.4mm
- Minimal cutting Radius : 0.1mm
- Maximum Roughing Stepdown : 0.5mm
- Fine Stepdown : 0.05mm

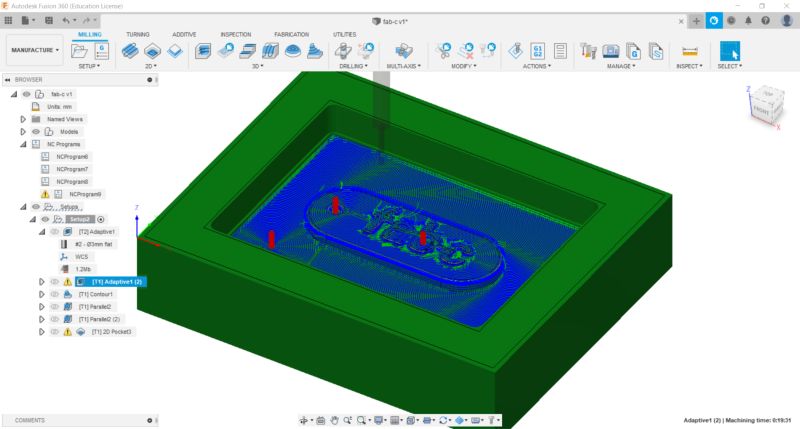
With a 0.6mm milling
Contour
- Maximum Stepdown : 0.2mm


Pocket for b and a : 0.6mm
- Maximum Stepover : 0.57mm
- Finishing stepdown : 0.1mm
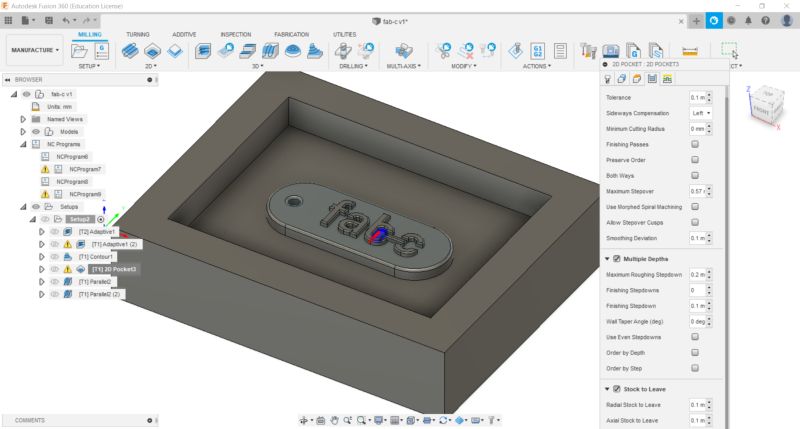
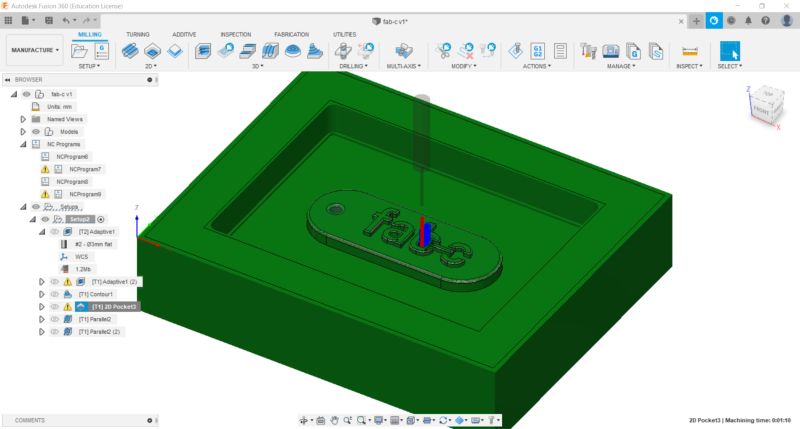
3d surface finish with 0.6mm milling
- Stepover : 0.1mm
- Maximum Stepdown : 0.2mm
- Nb Stepdown : 1
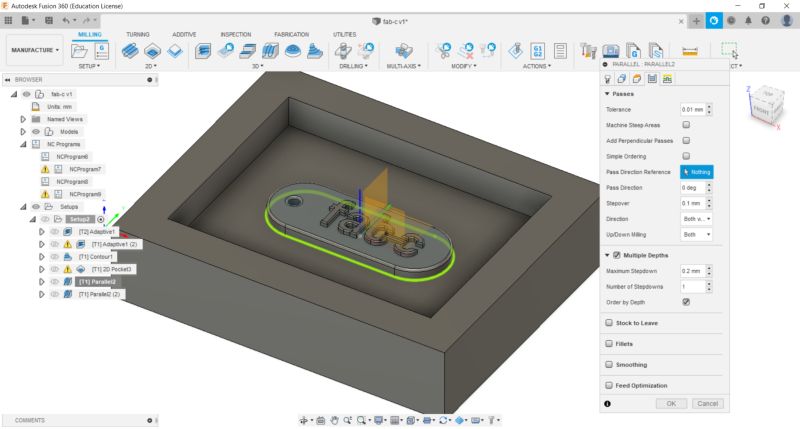
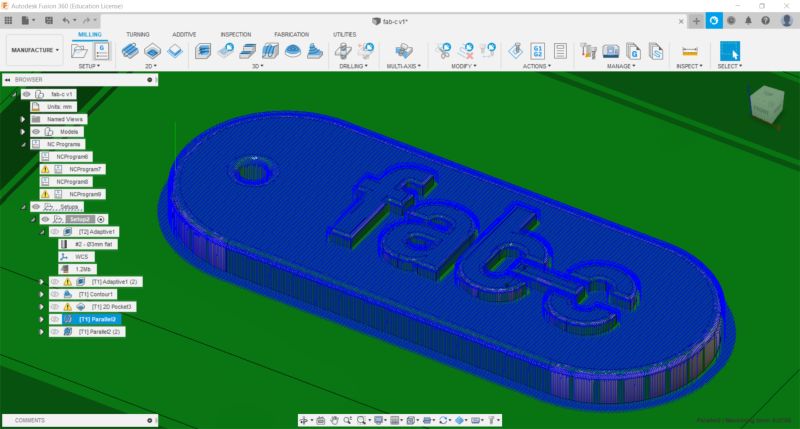
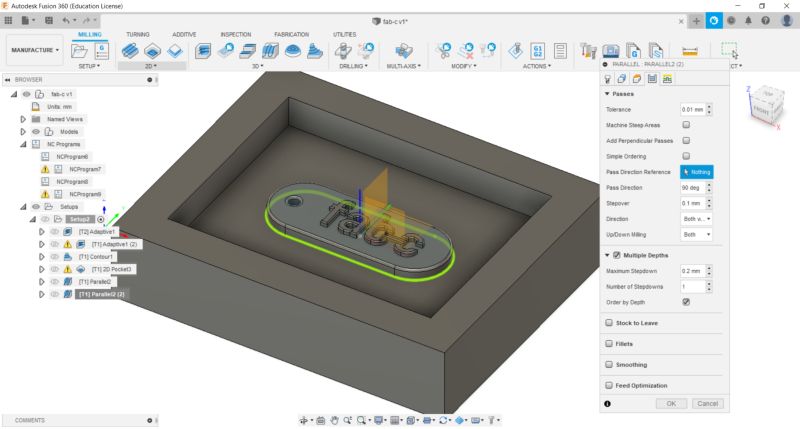
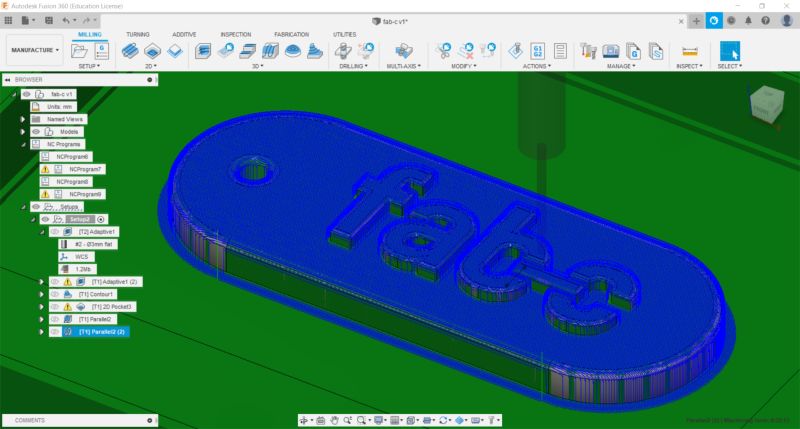
Download :
Work in CNC Mekanika¶
A first pass with a 3mm milling
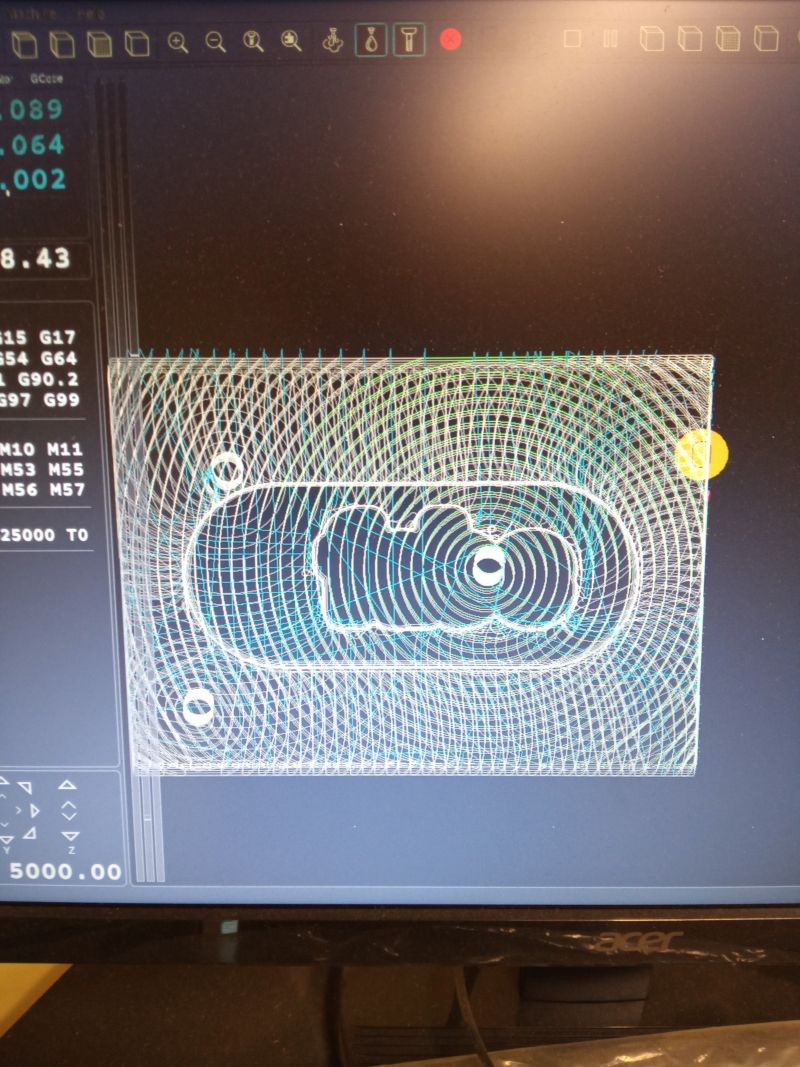


A second pass with a 1mm milling
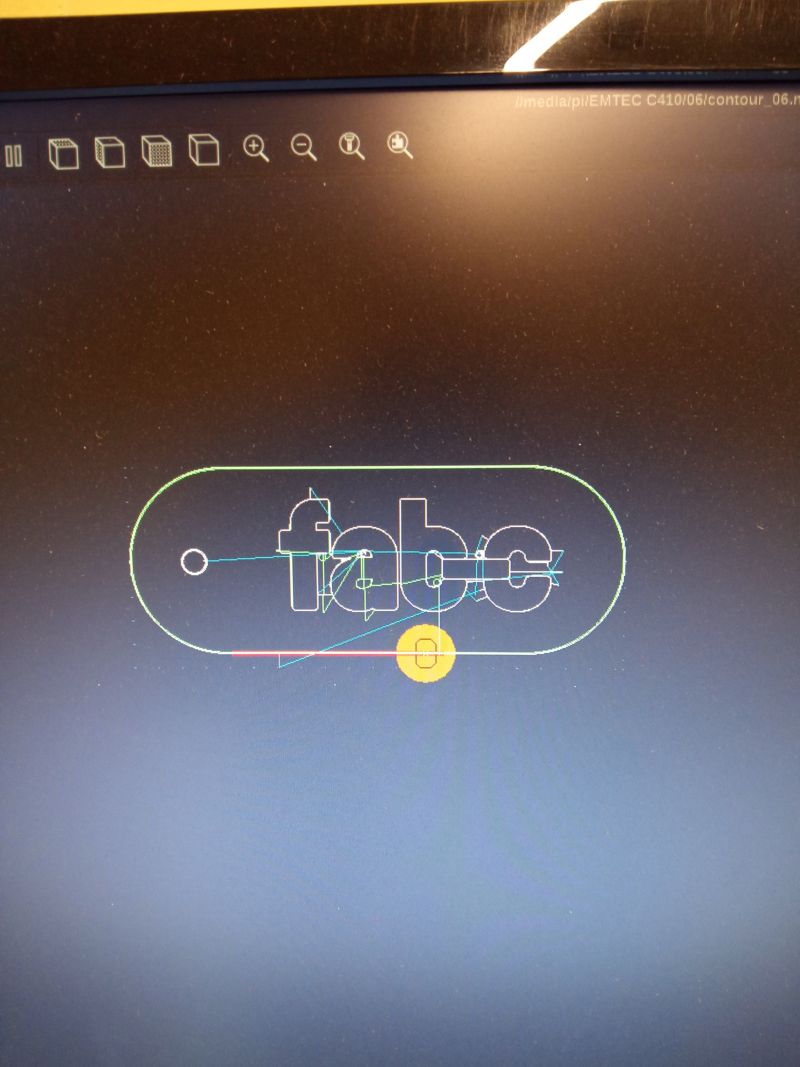
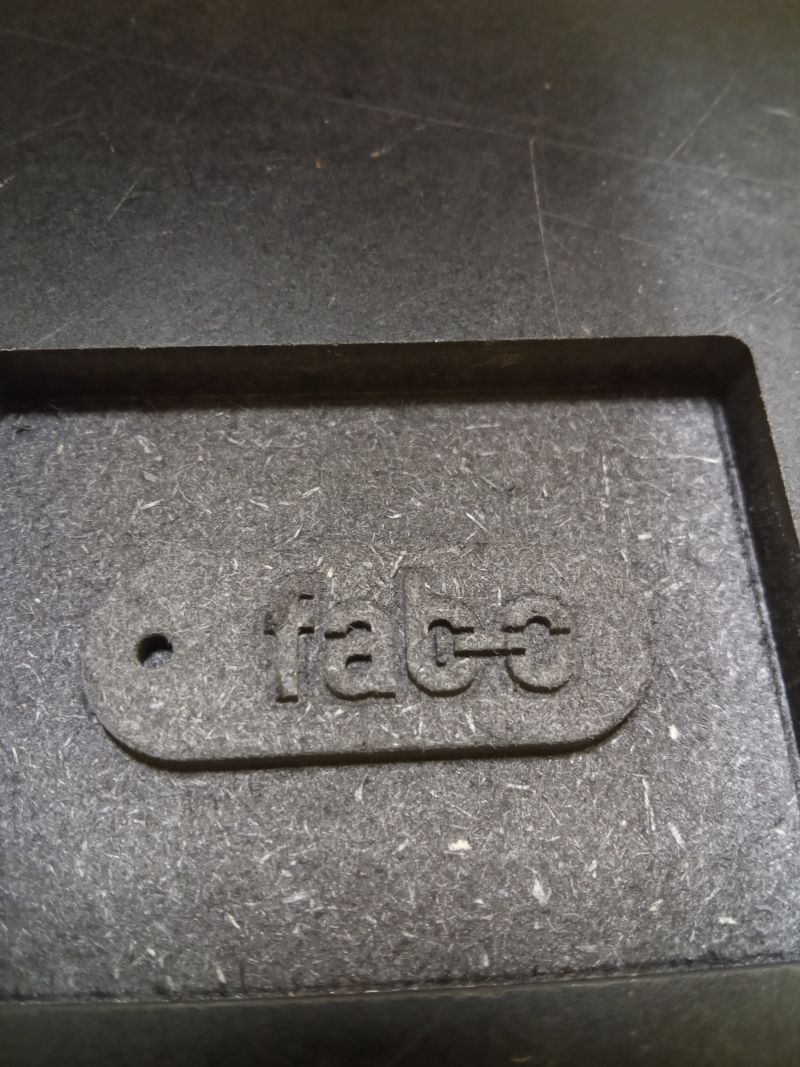
We finish with a 0.6mm milling

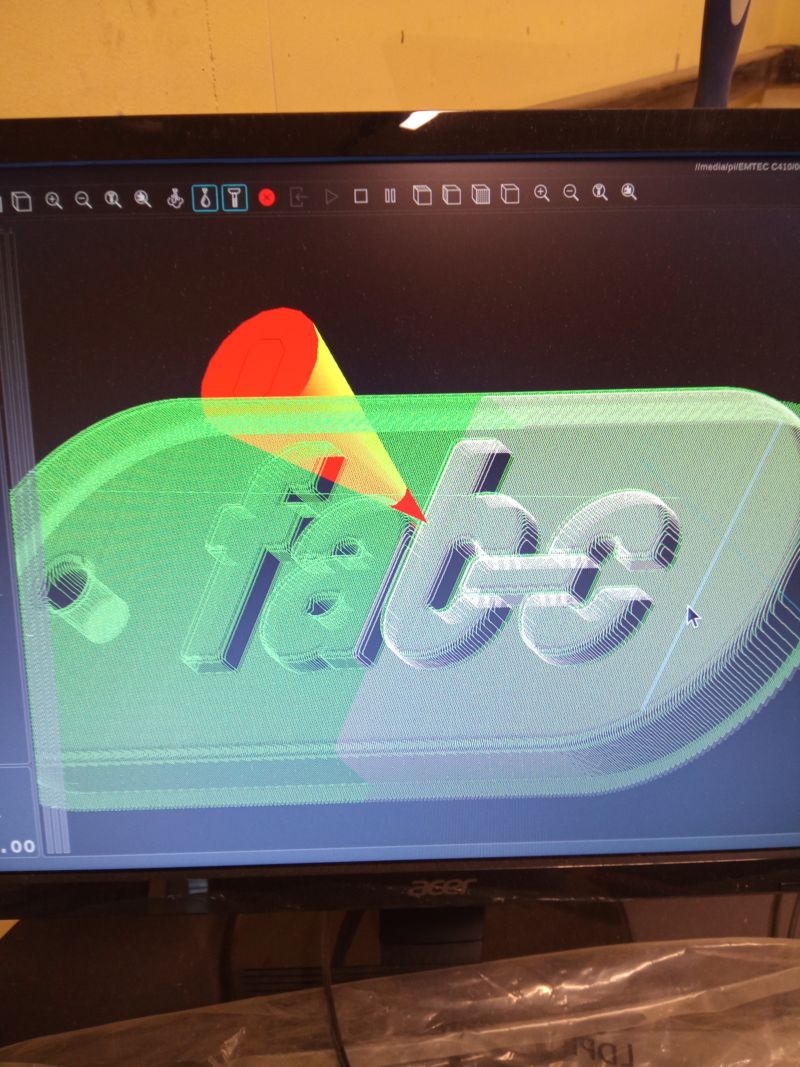

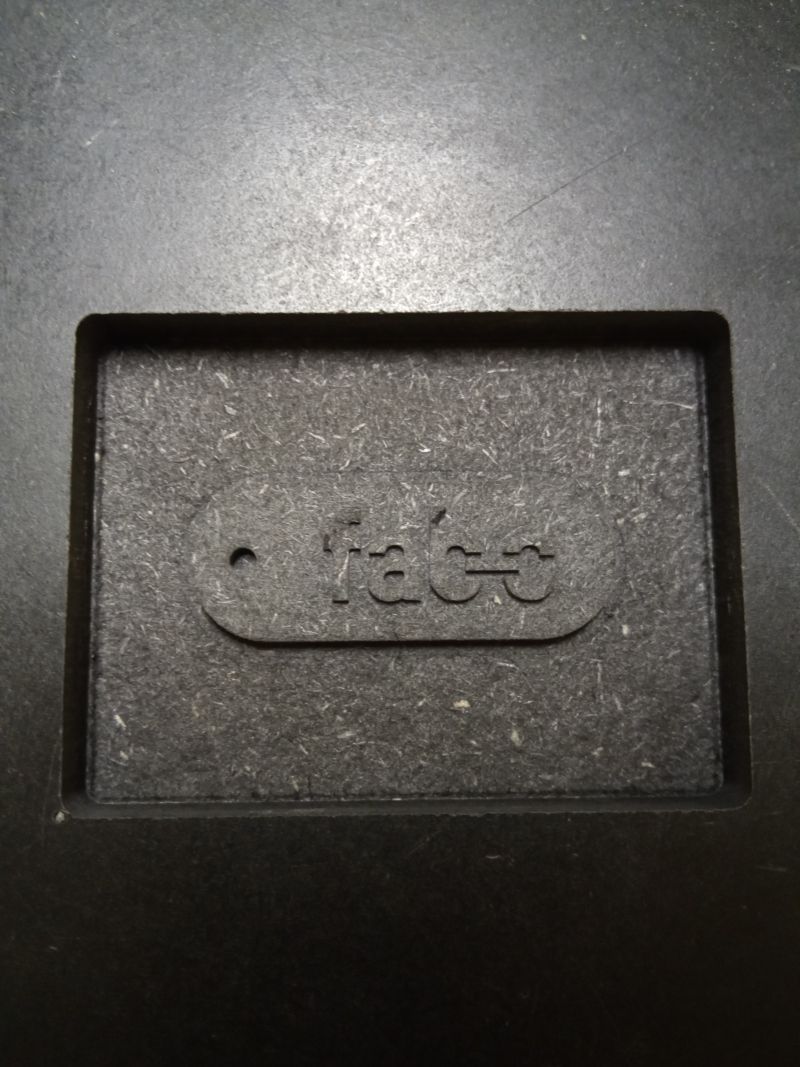
I am quite happy with the result
Mould creation¶
Let’s go for the casting of the part.
Preparation of the material
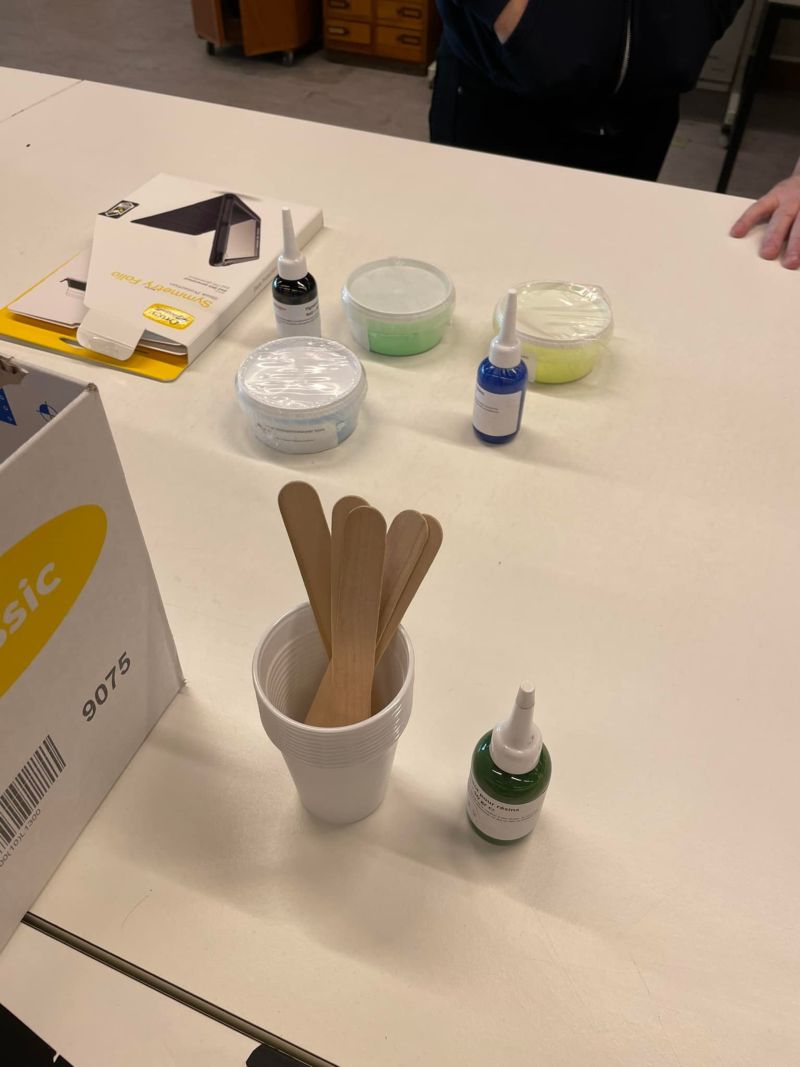
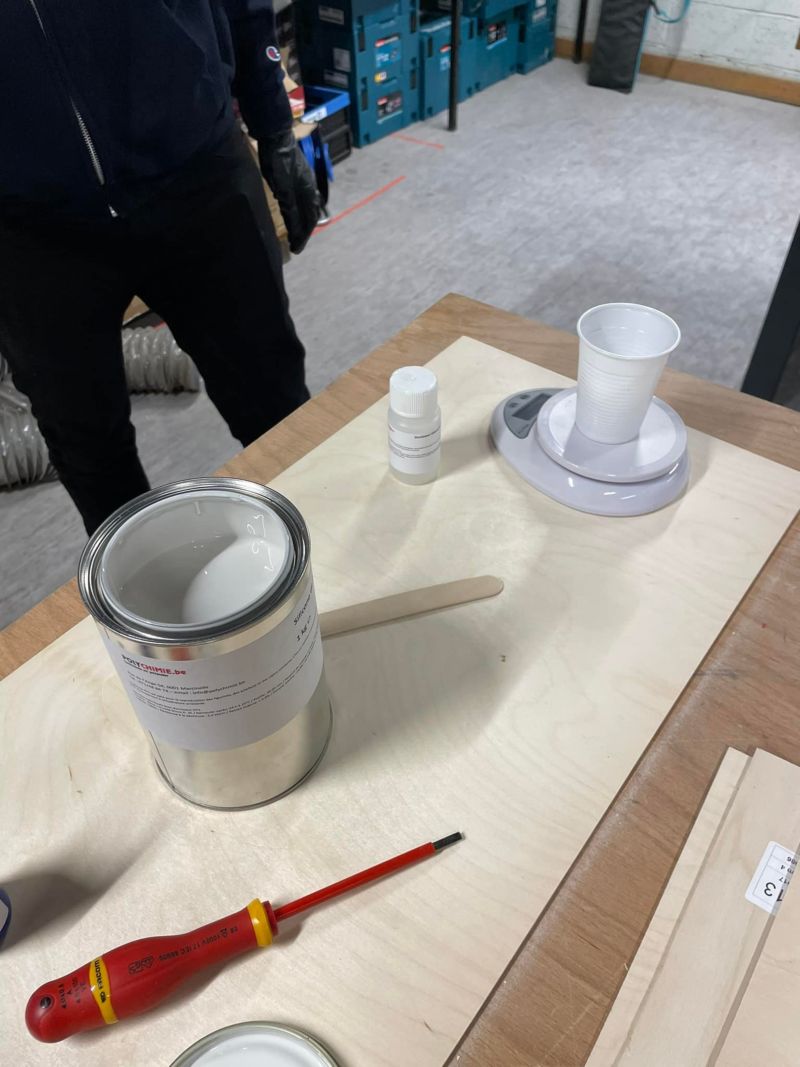
Weighing is extremely important. The ratio of 100:5 must be respected.
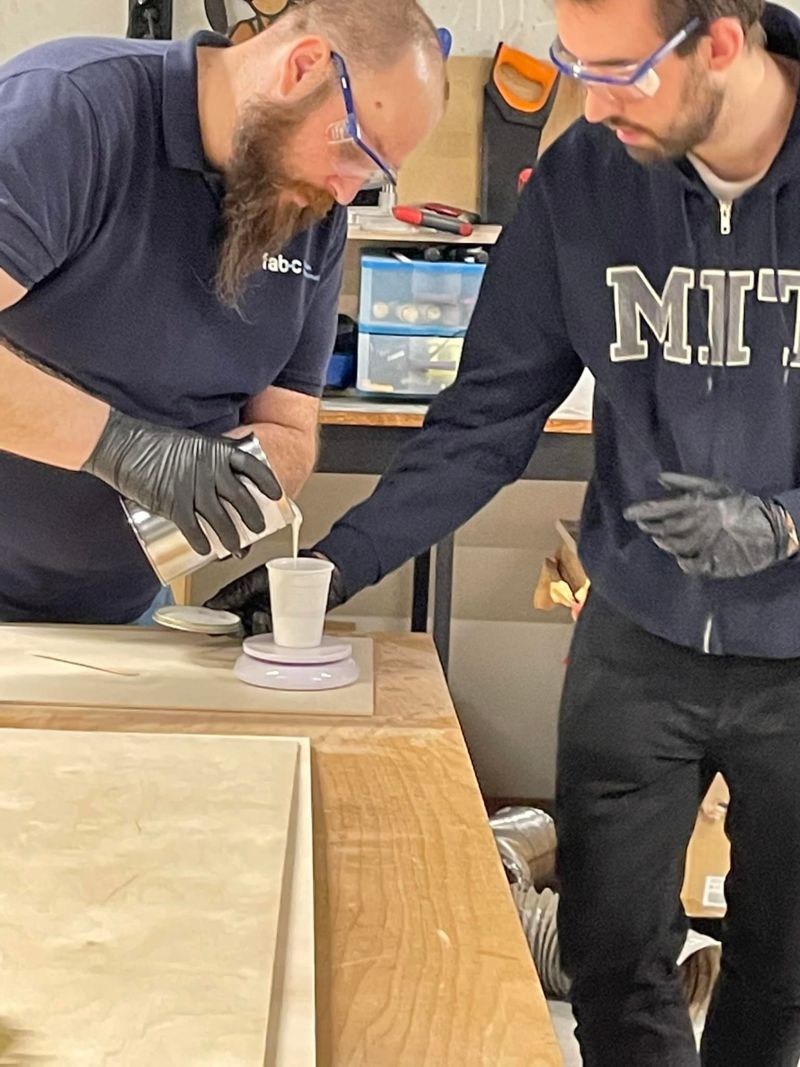
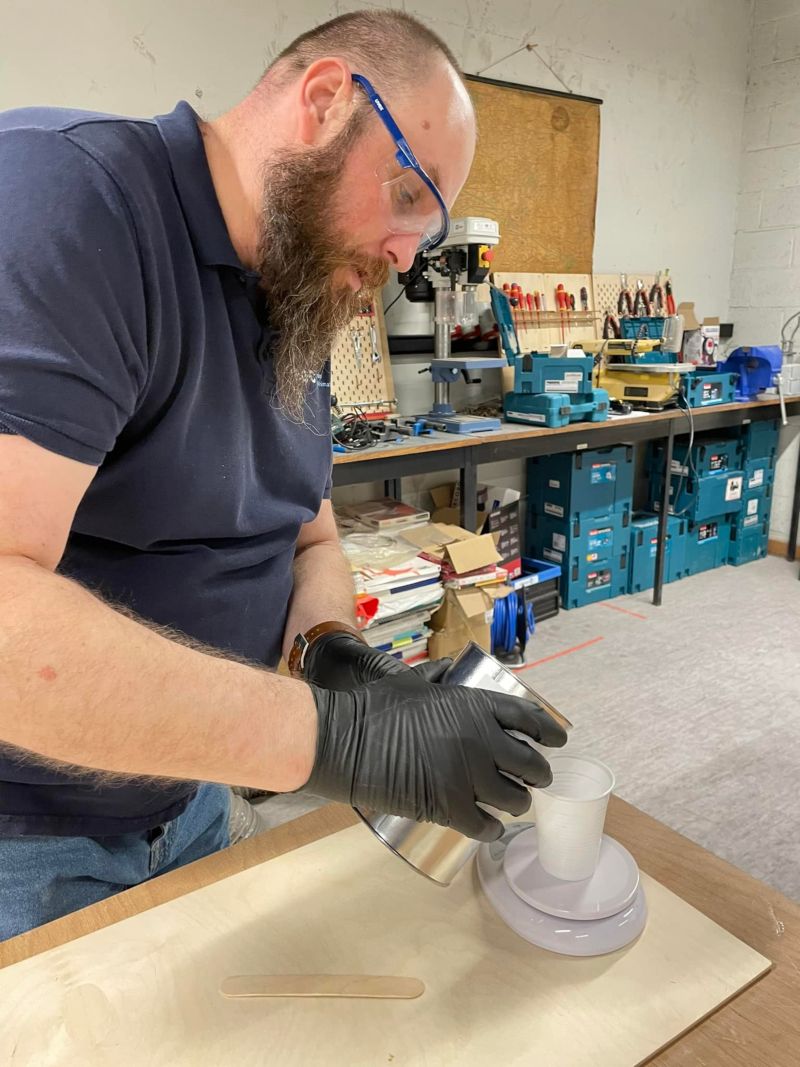
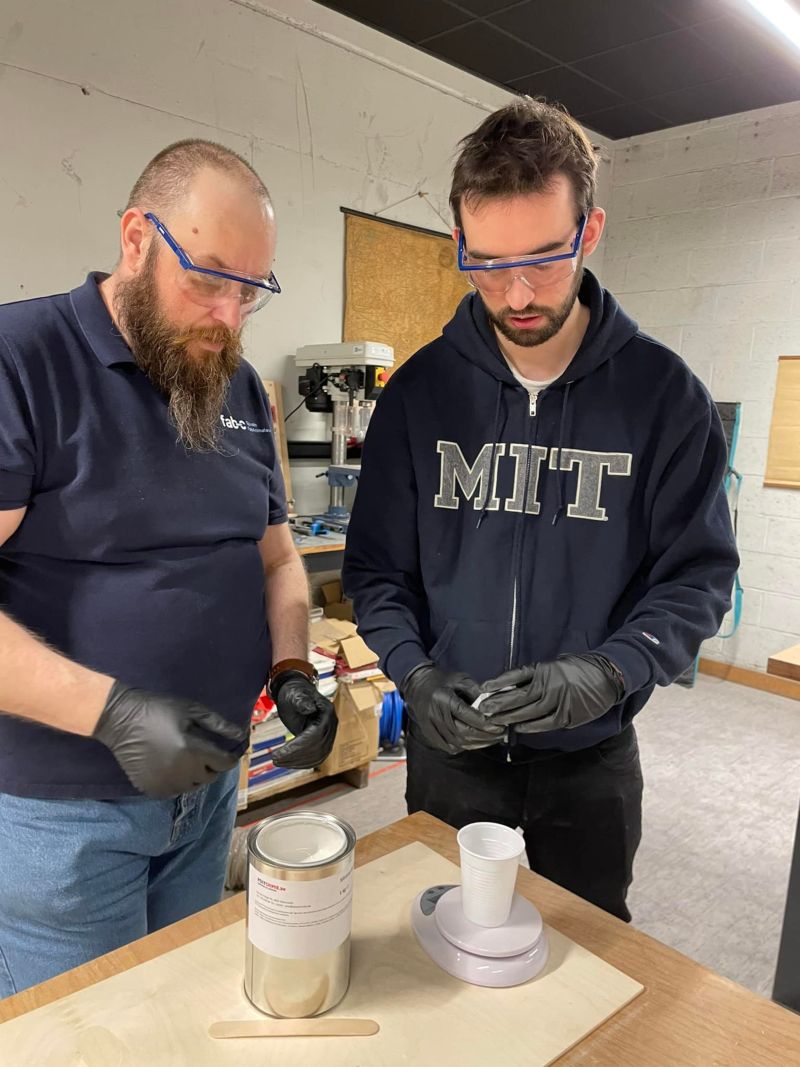
Mix for a few minutes without making bubbles
Spray is applied to facilitate demoulding in the final phase
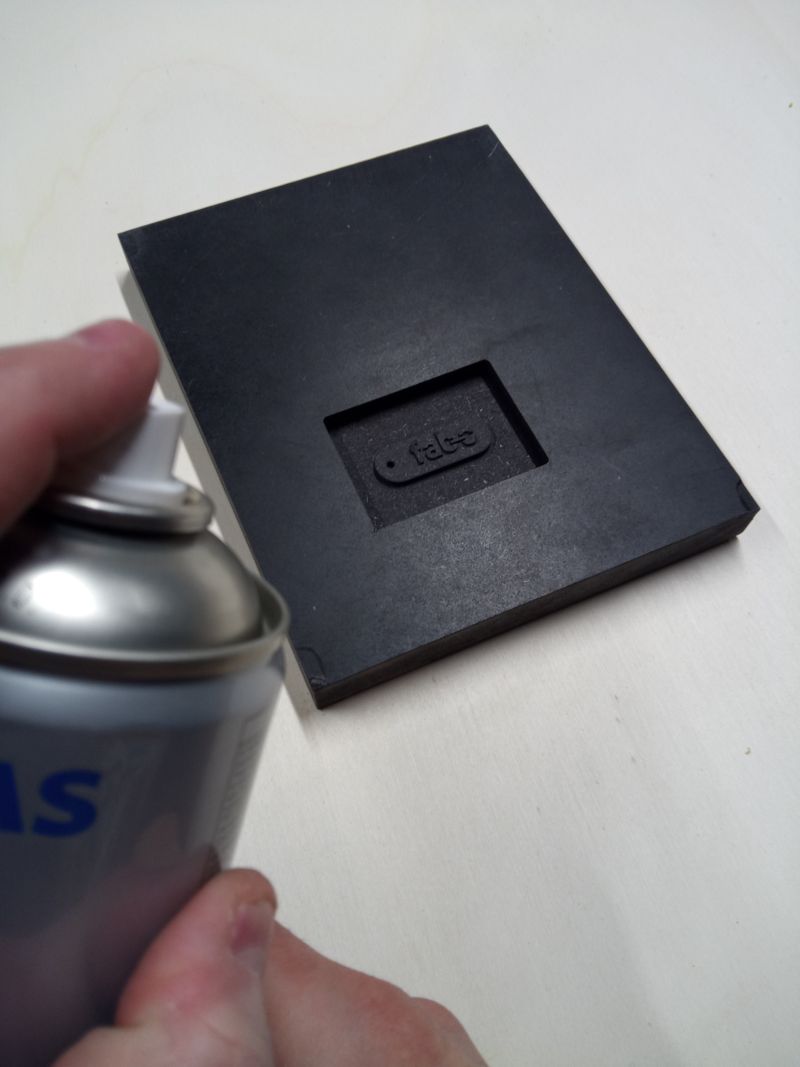
The silicone must be cast to make the mould
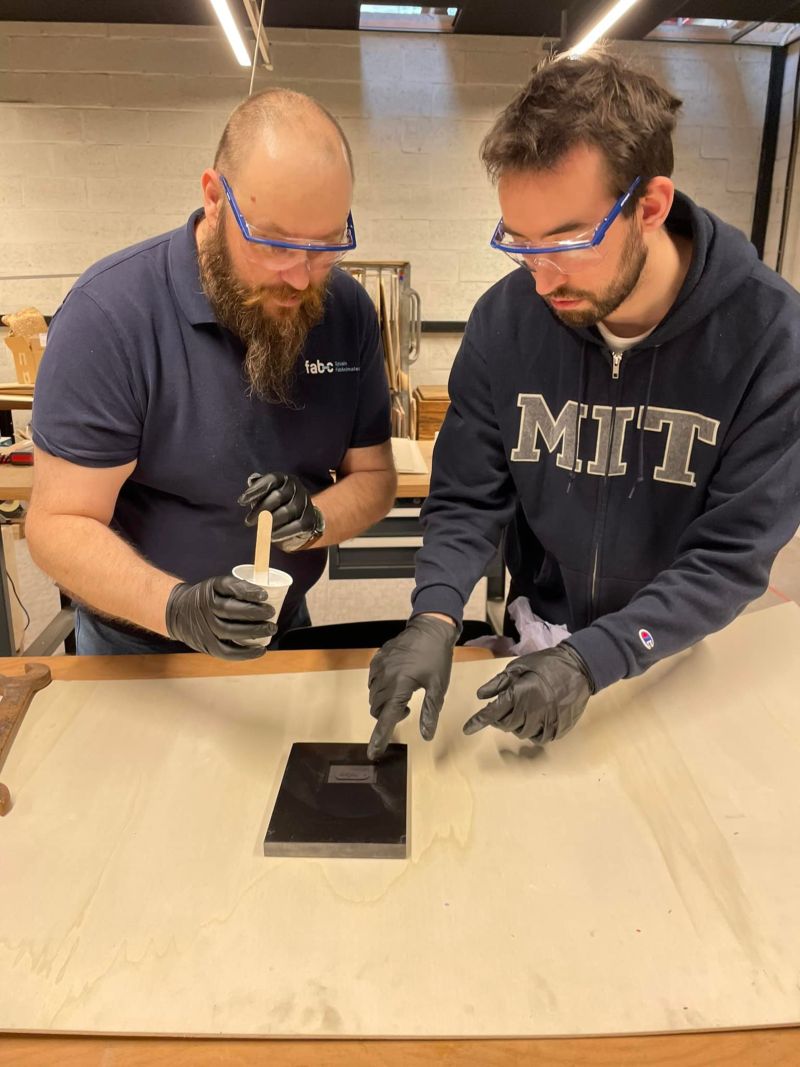
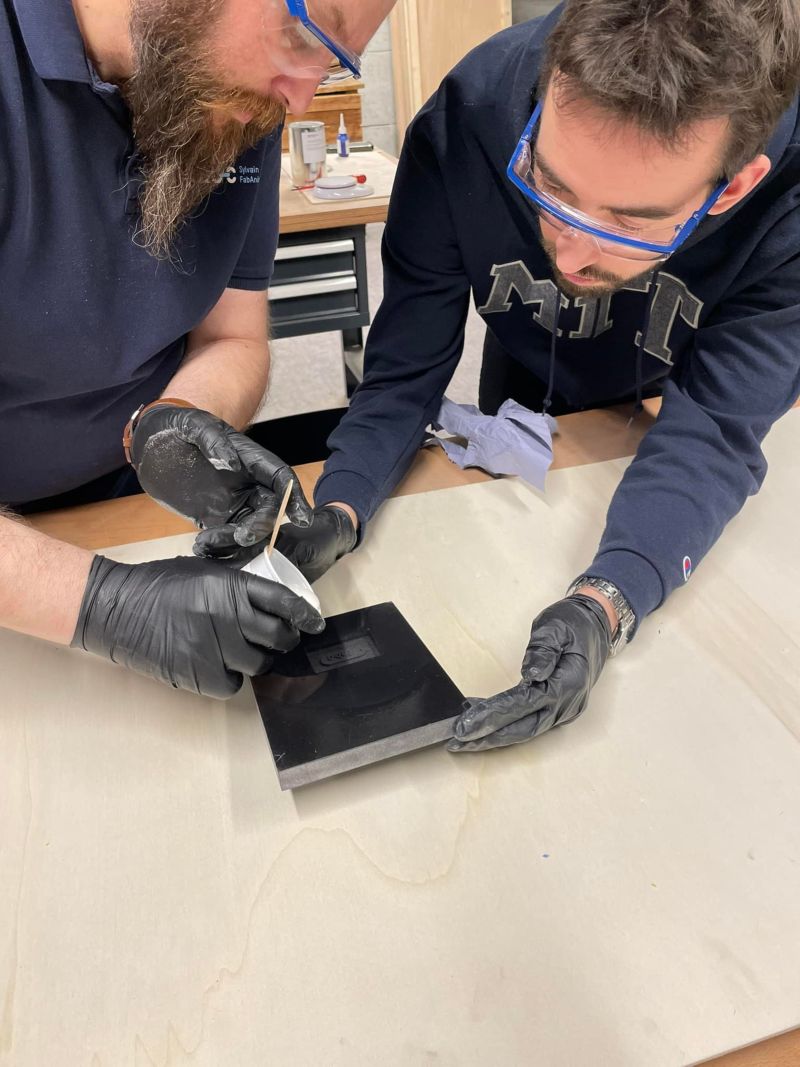
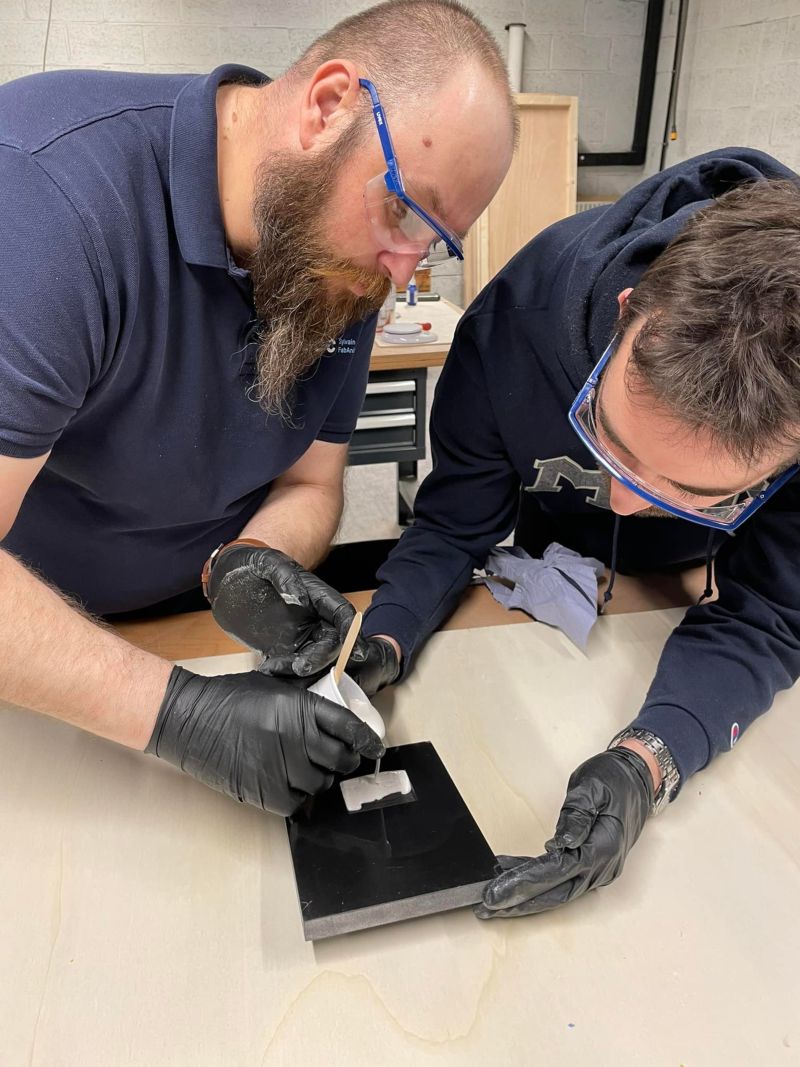
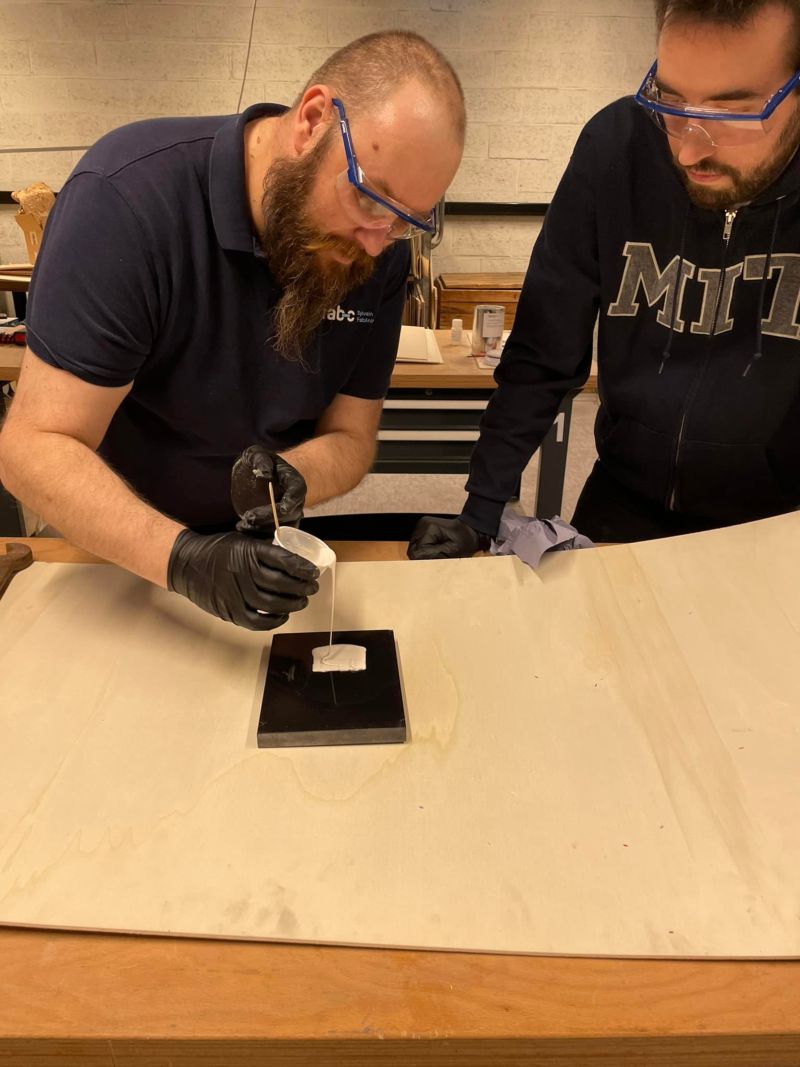
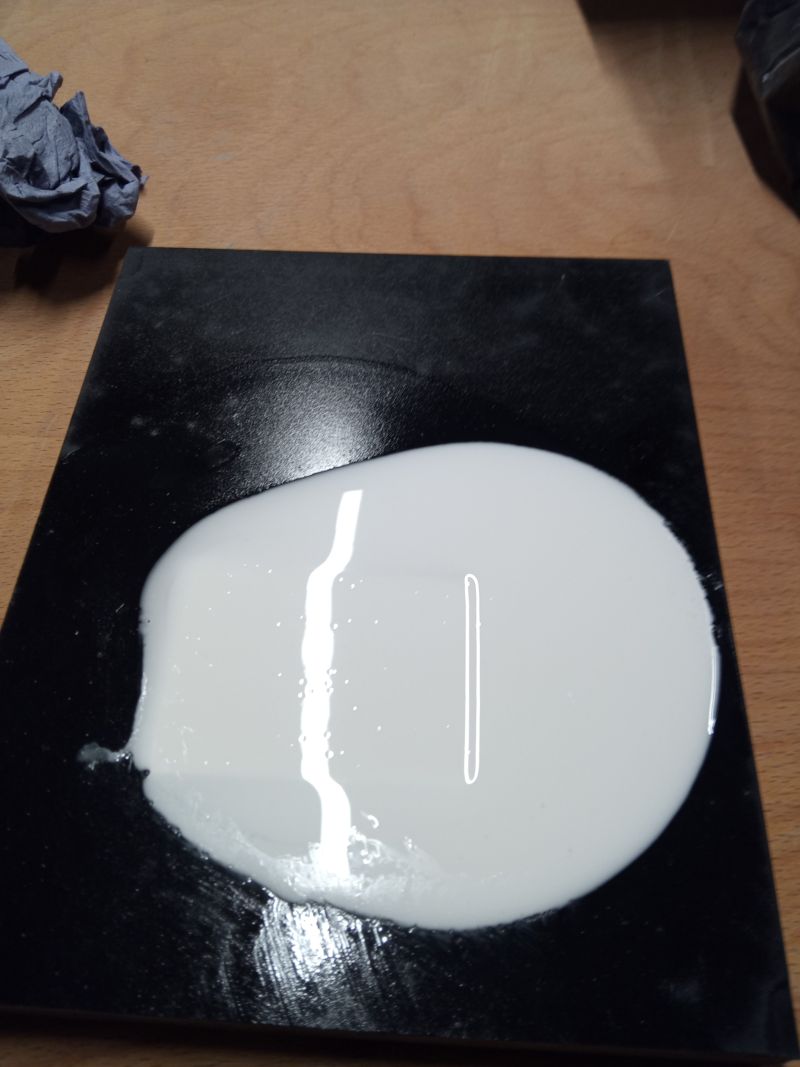
We wait about 24 hours to see the result

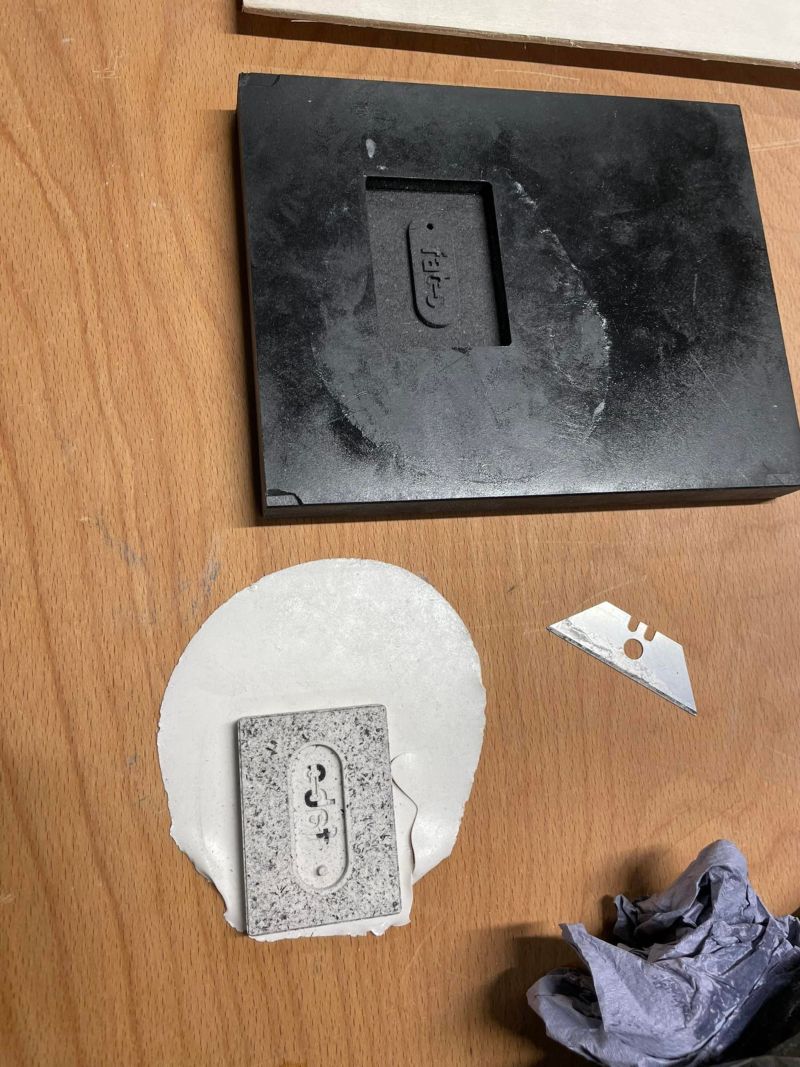
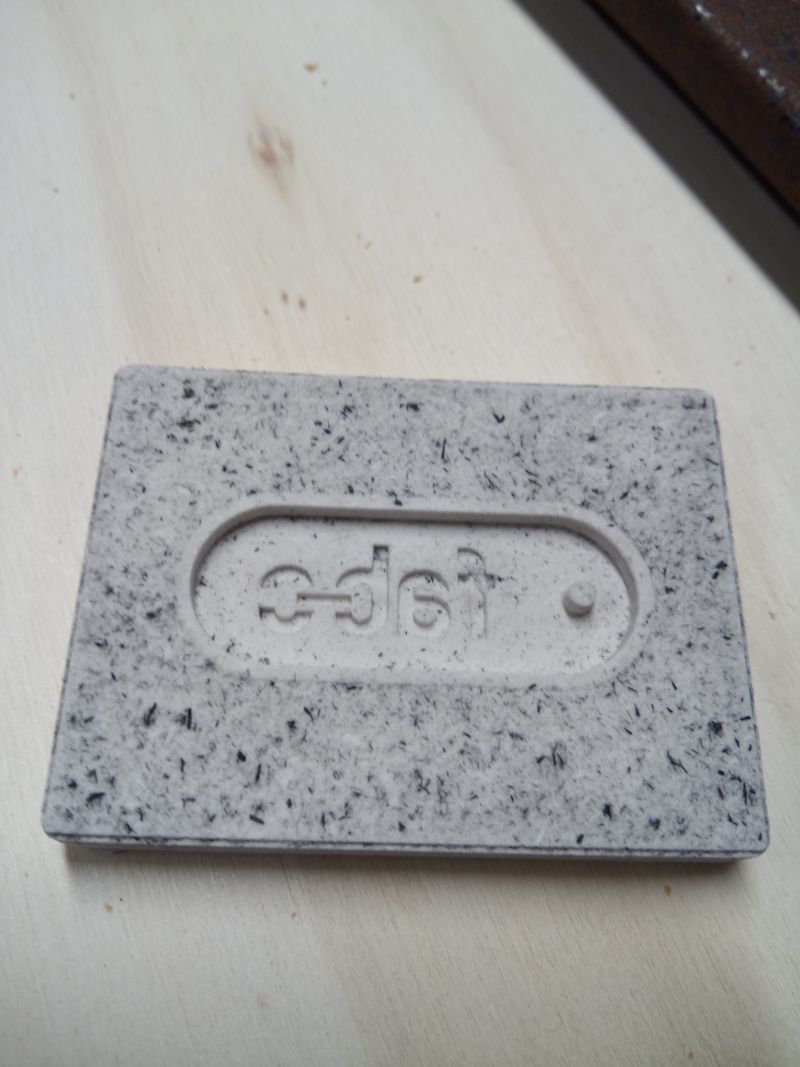
Creating resin parts¶
Danger
obligatory protection
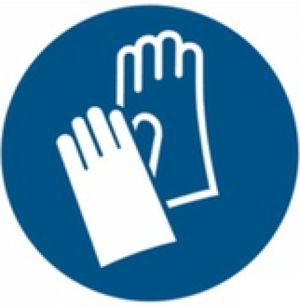
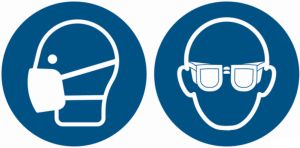
Weighing is extremely important. The ratio of 100:45 must be respected.
we start pouring
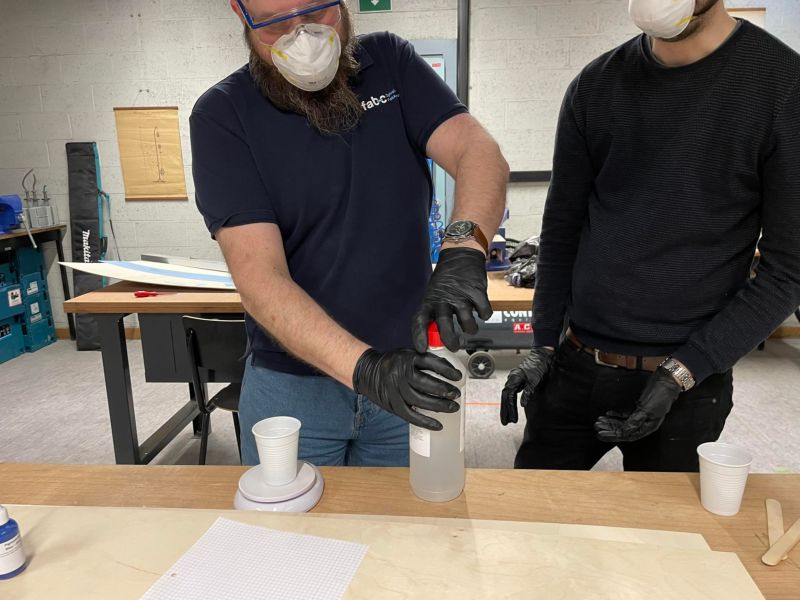
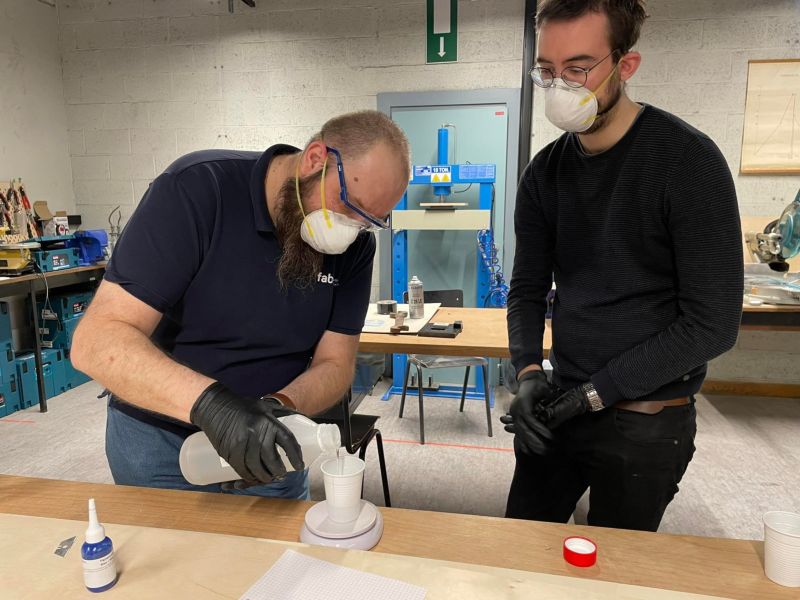
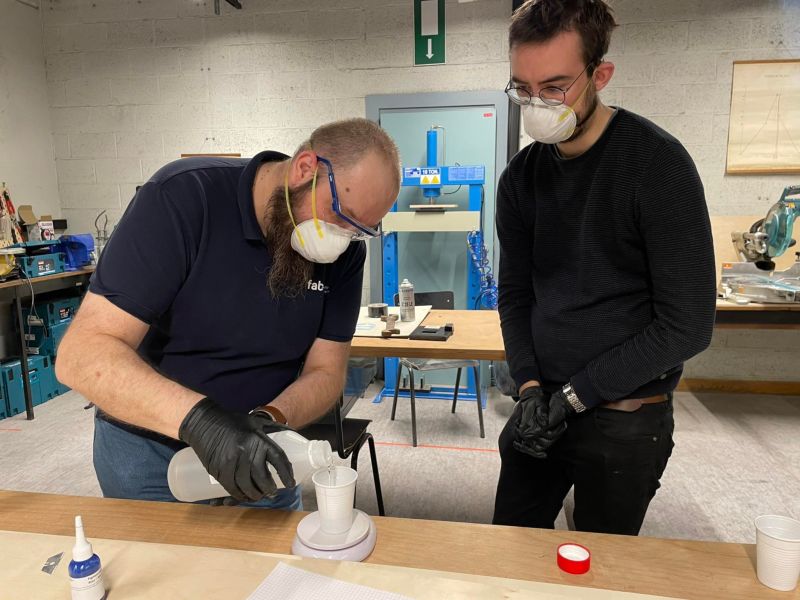
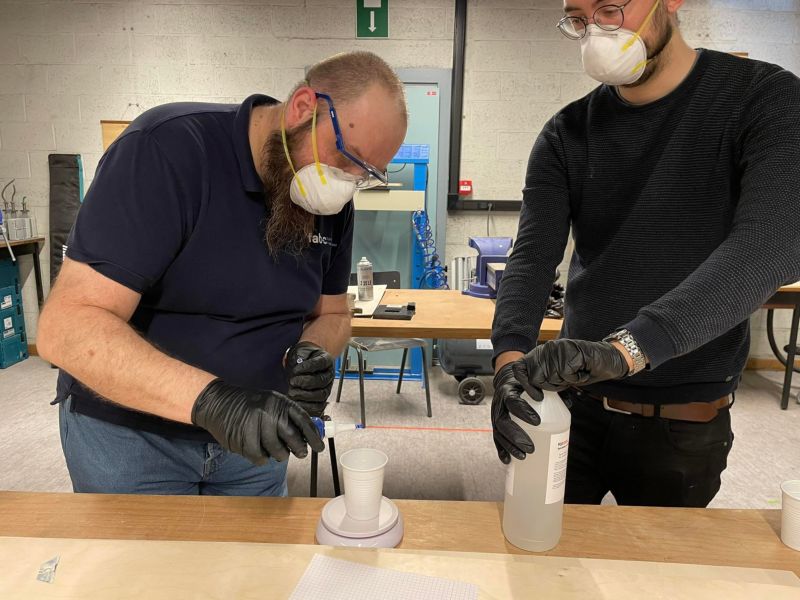
A few drops of dye are added
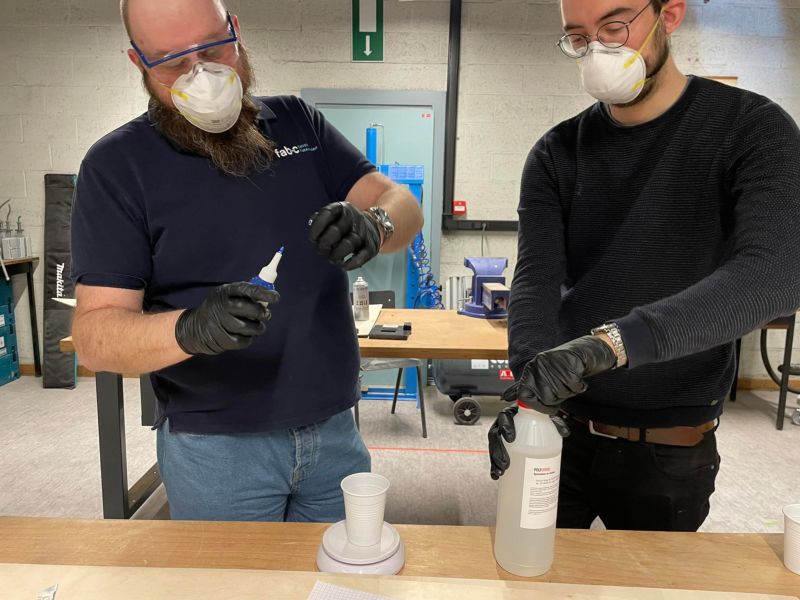

We add the second component
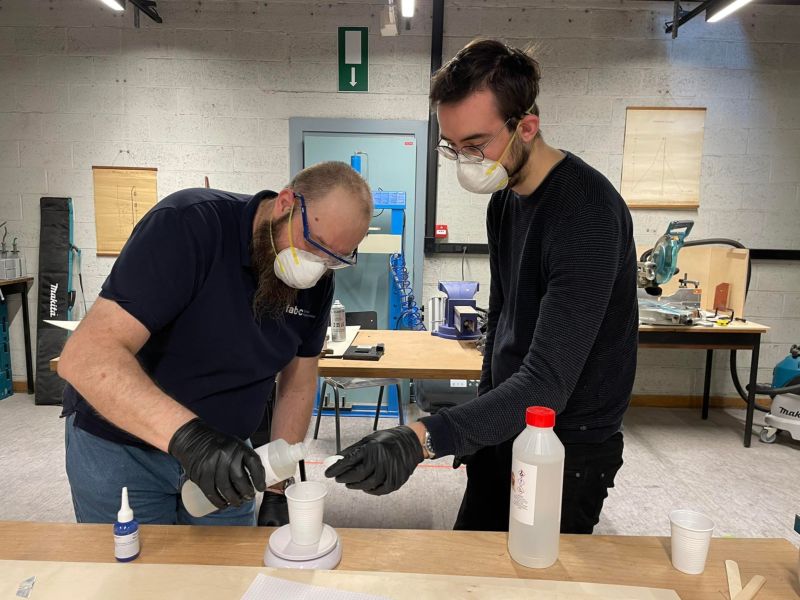
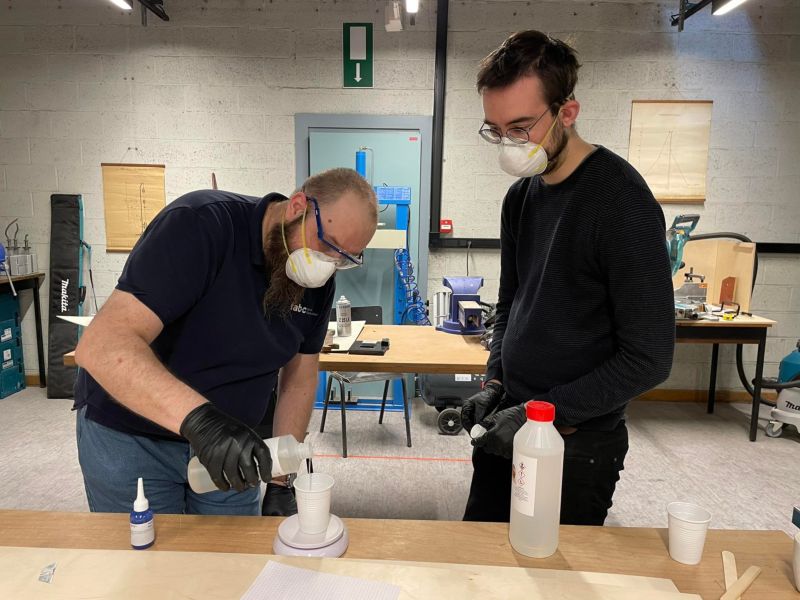
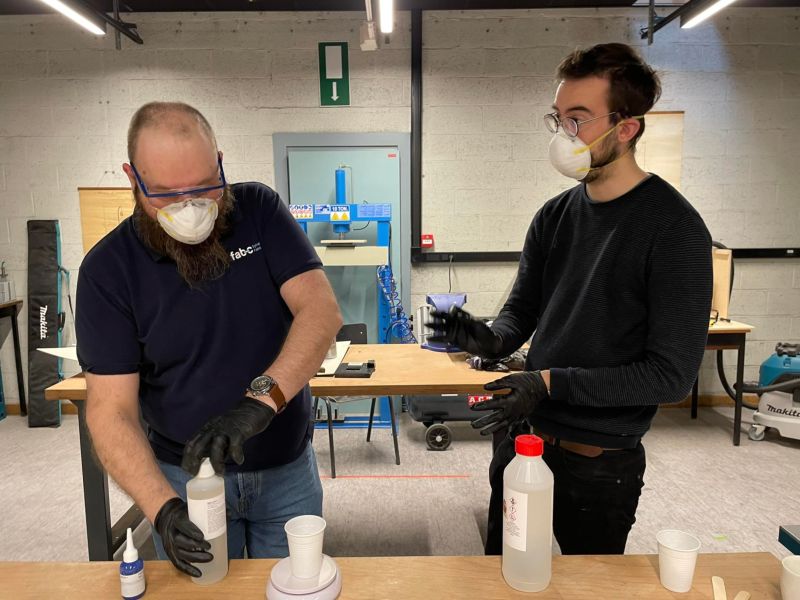
Mix well to avoid bubbles
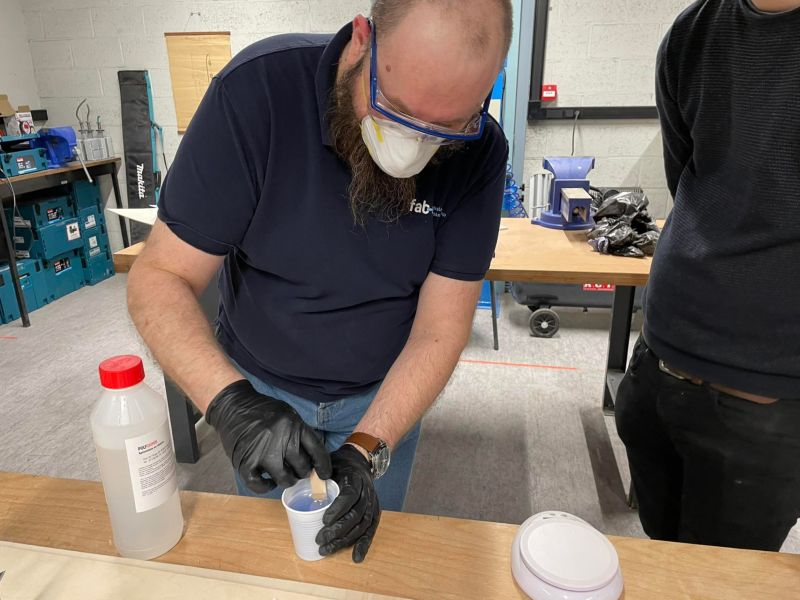

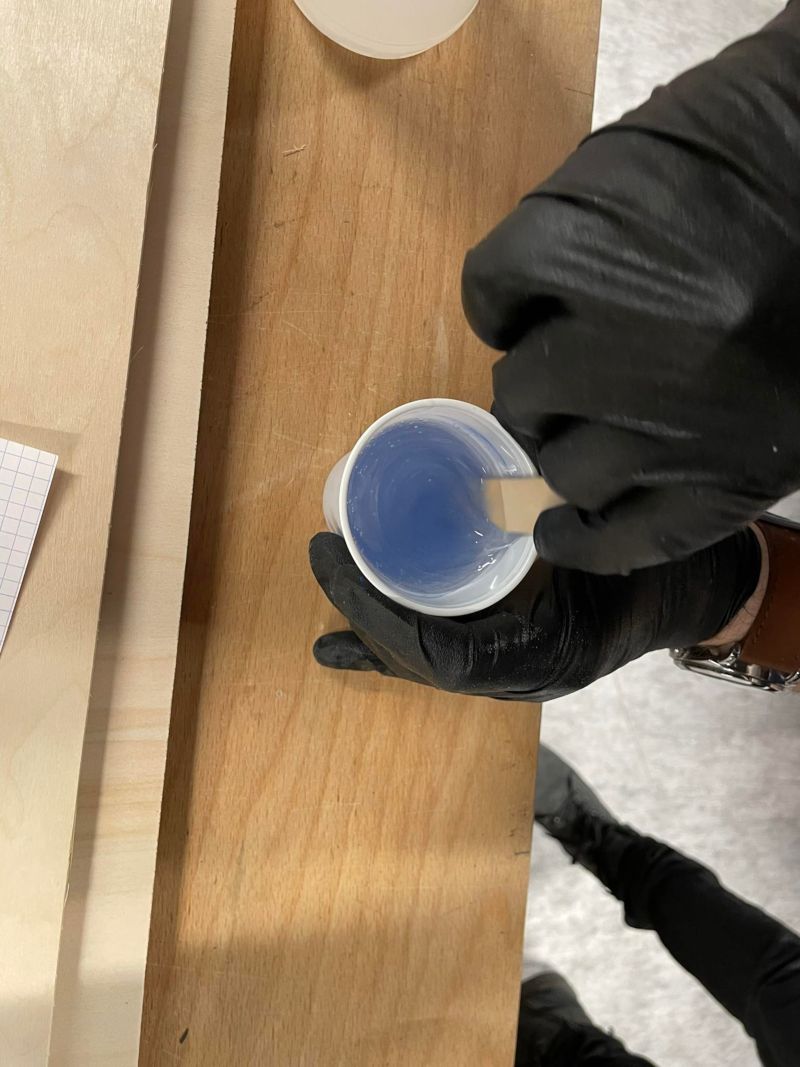
We prepare the parts to be moulded and we cast our mixture
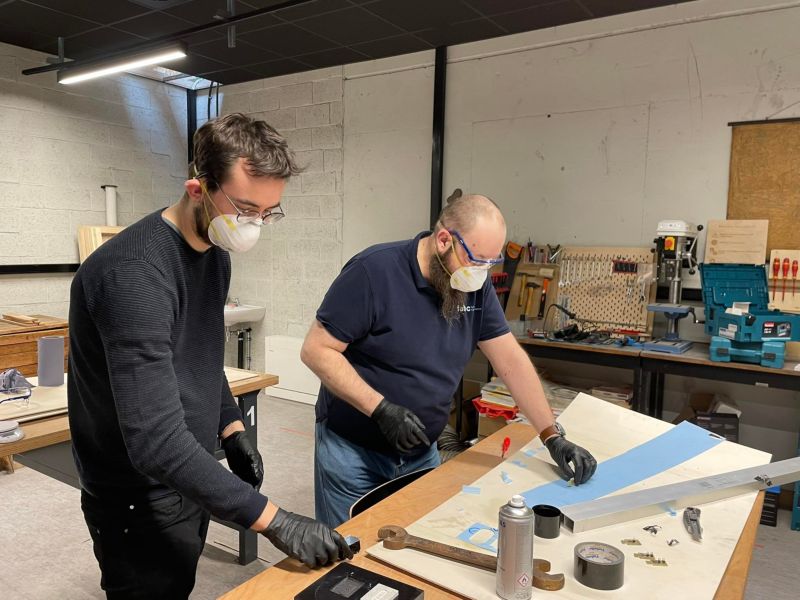
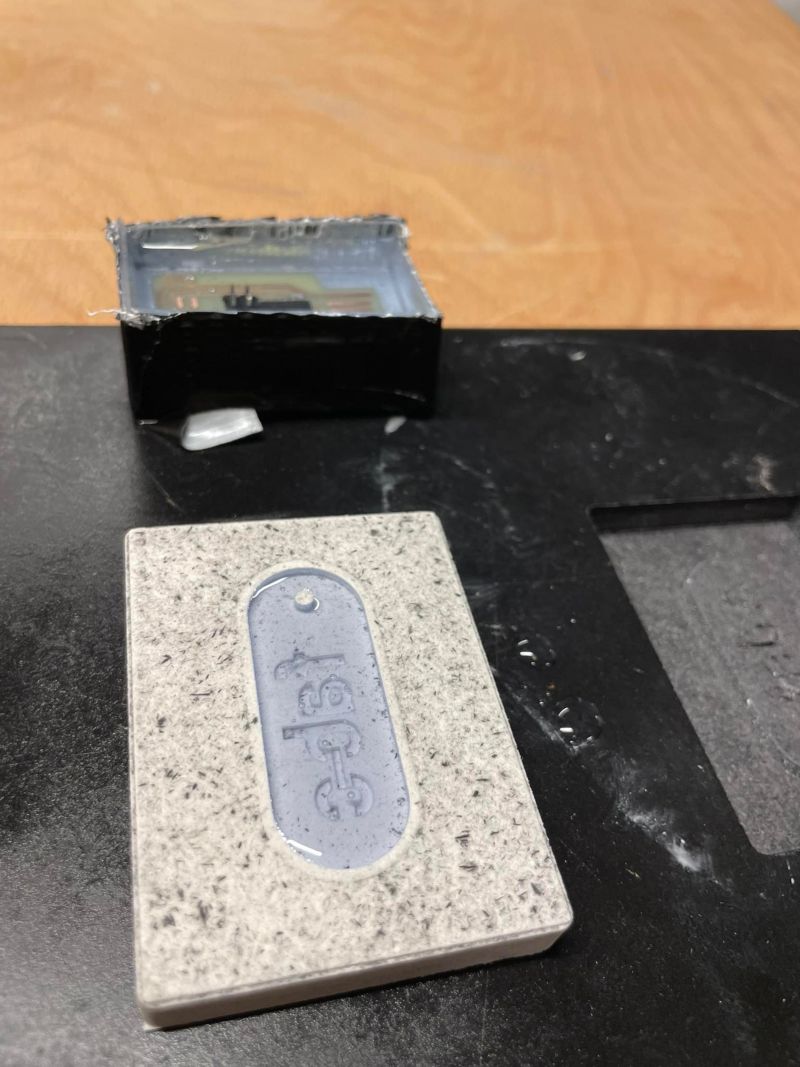
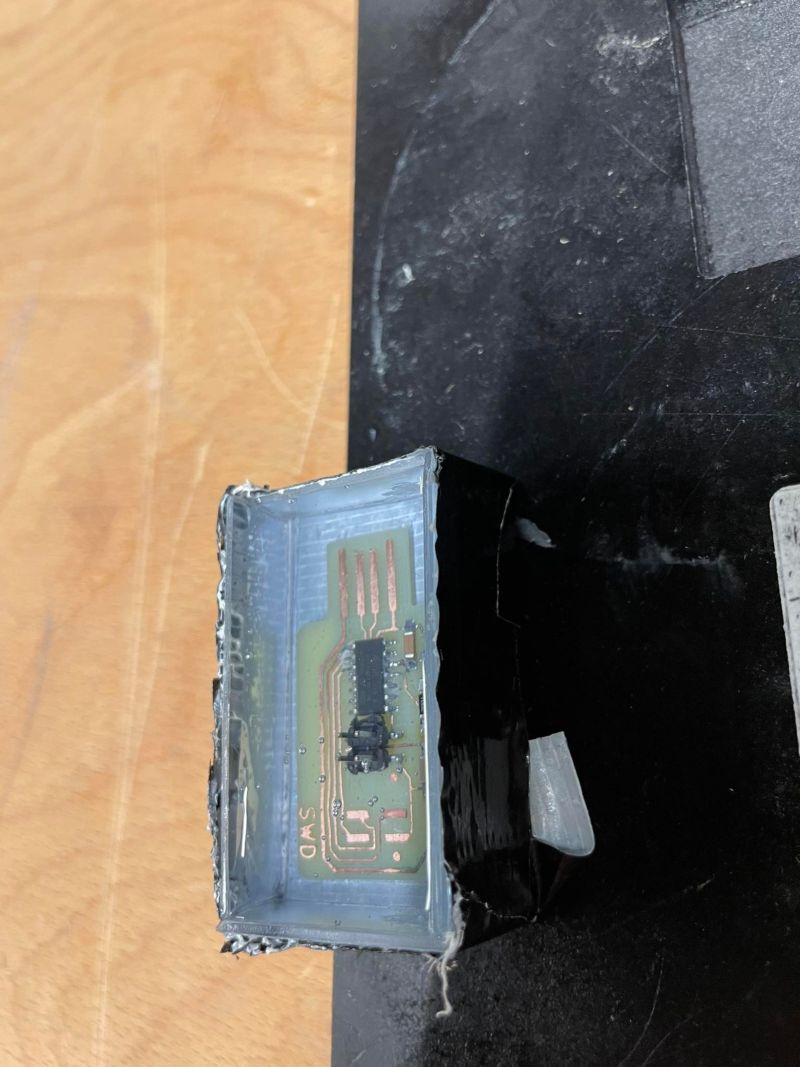
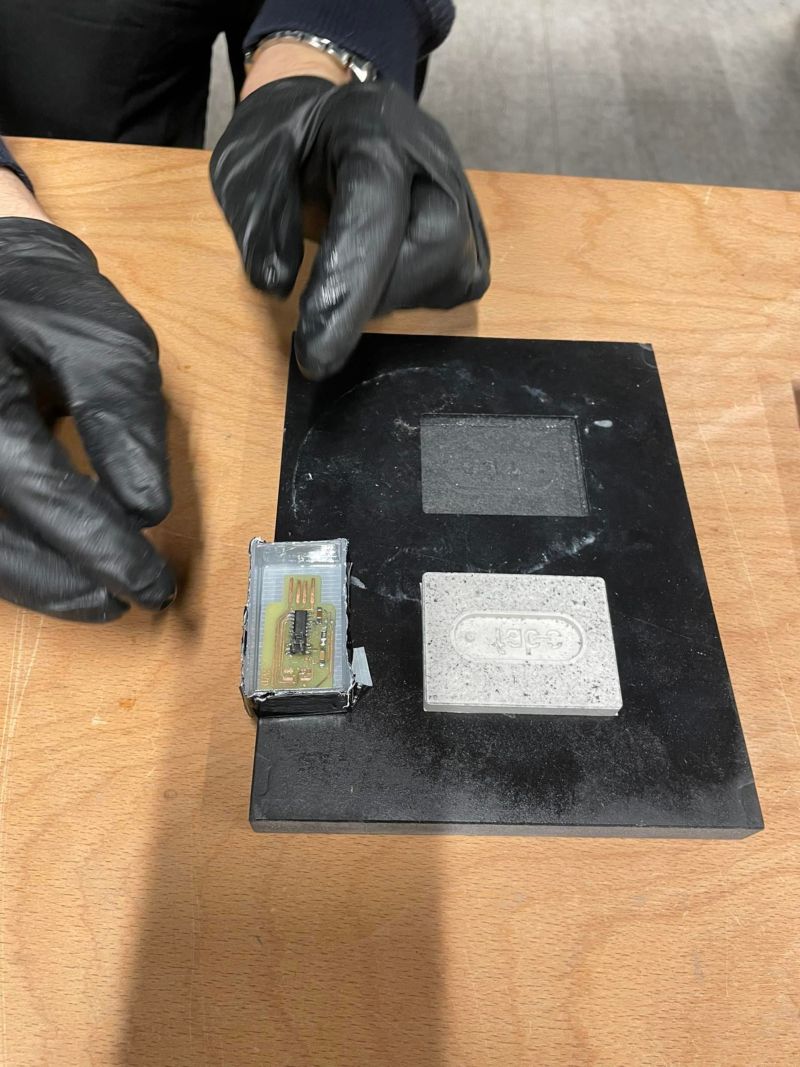
We heat to make the bubbles disappear.
To remedy the bubbles, several solutions are available to us:
1 - Pour really slowly without any sudden movement (not the easiest)
2 - Use a vacuum box (we don't have one at the fablab)
3 - Heat the resin until the bubbles disappear. (this last option was used here with a "thermal stripper")
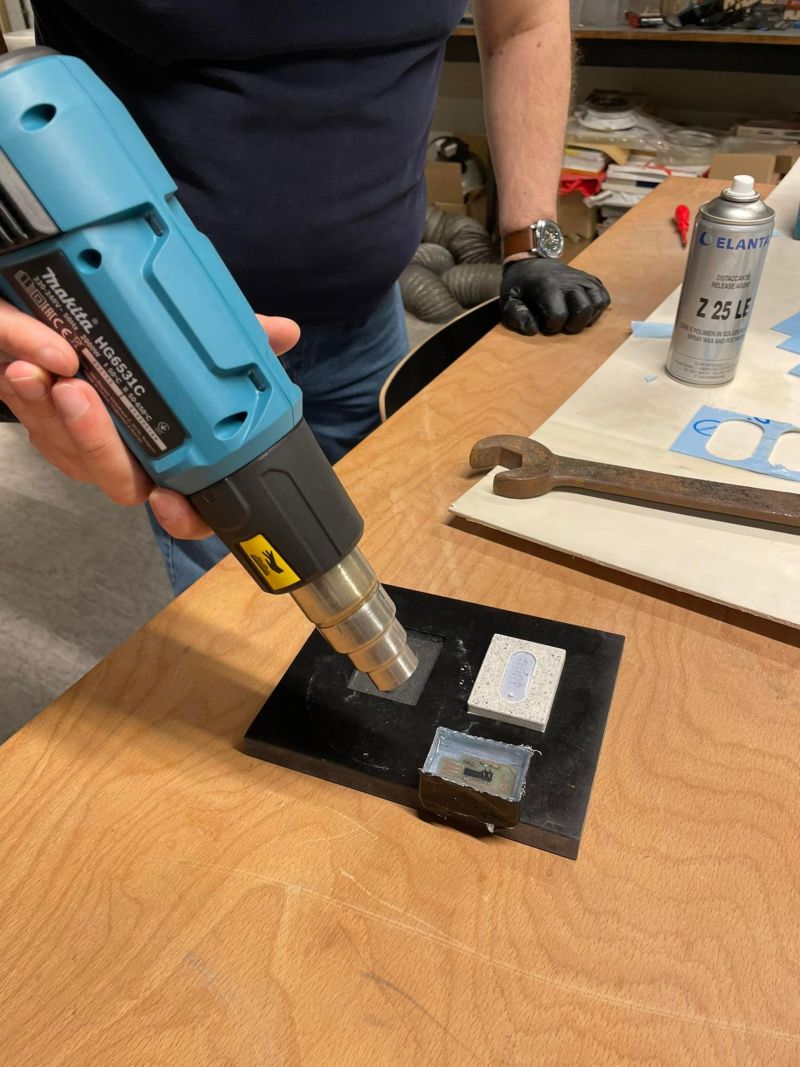
Final Result¶
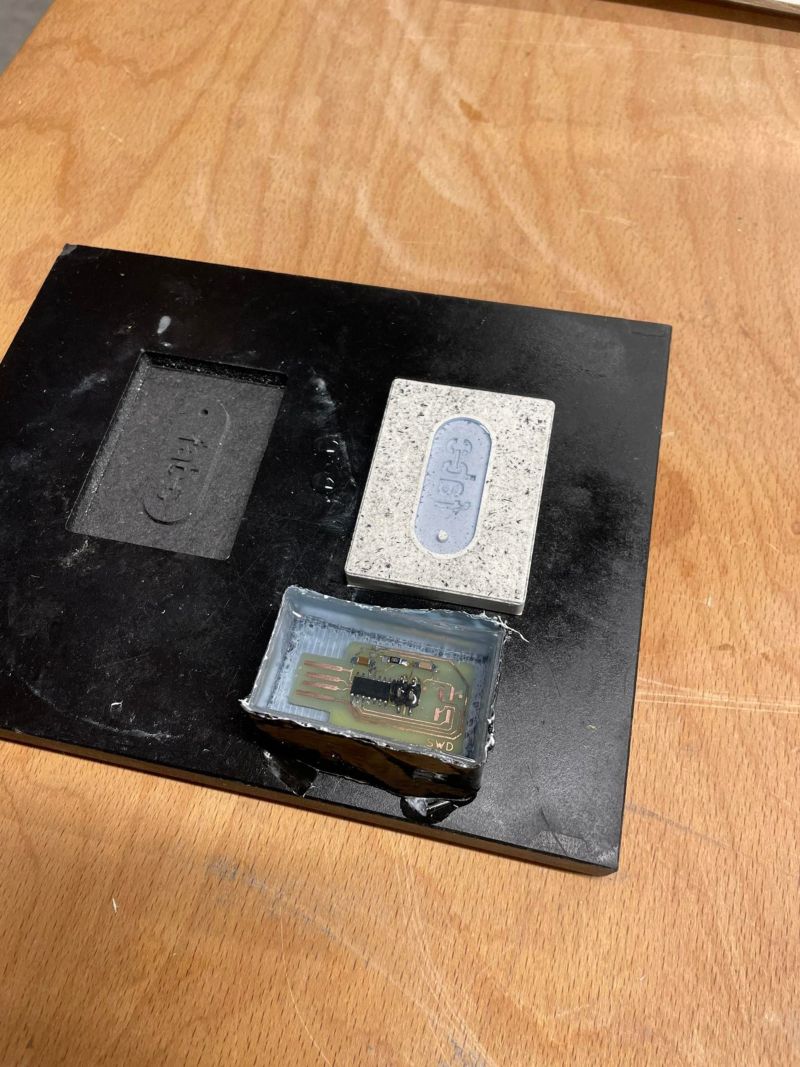
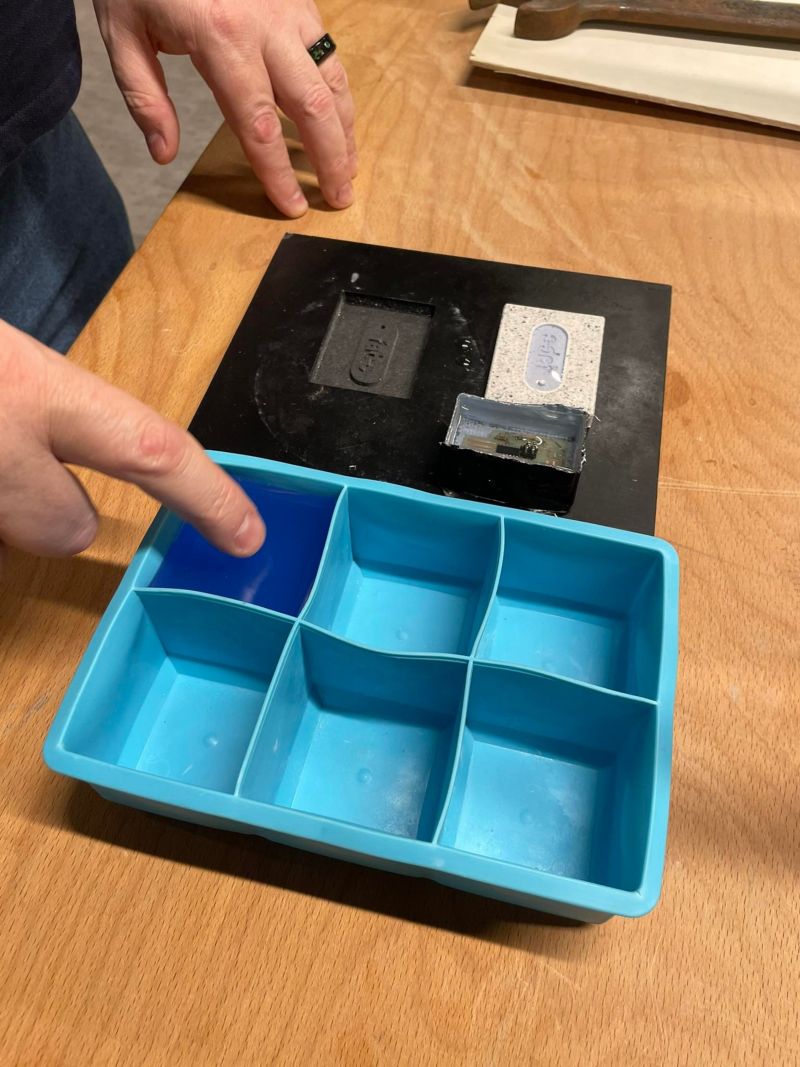
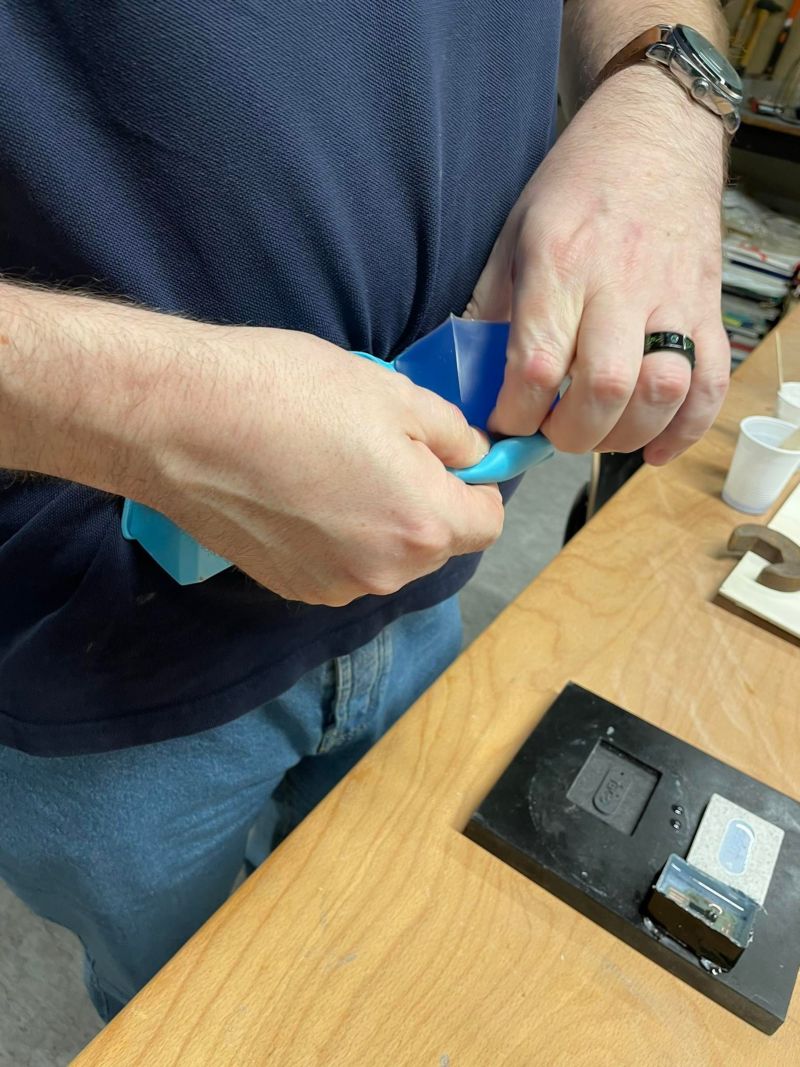
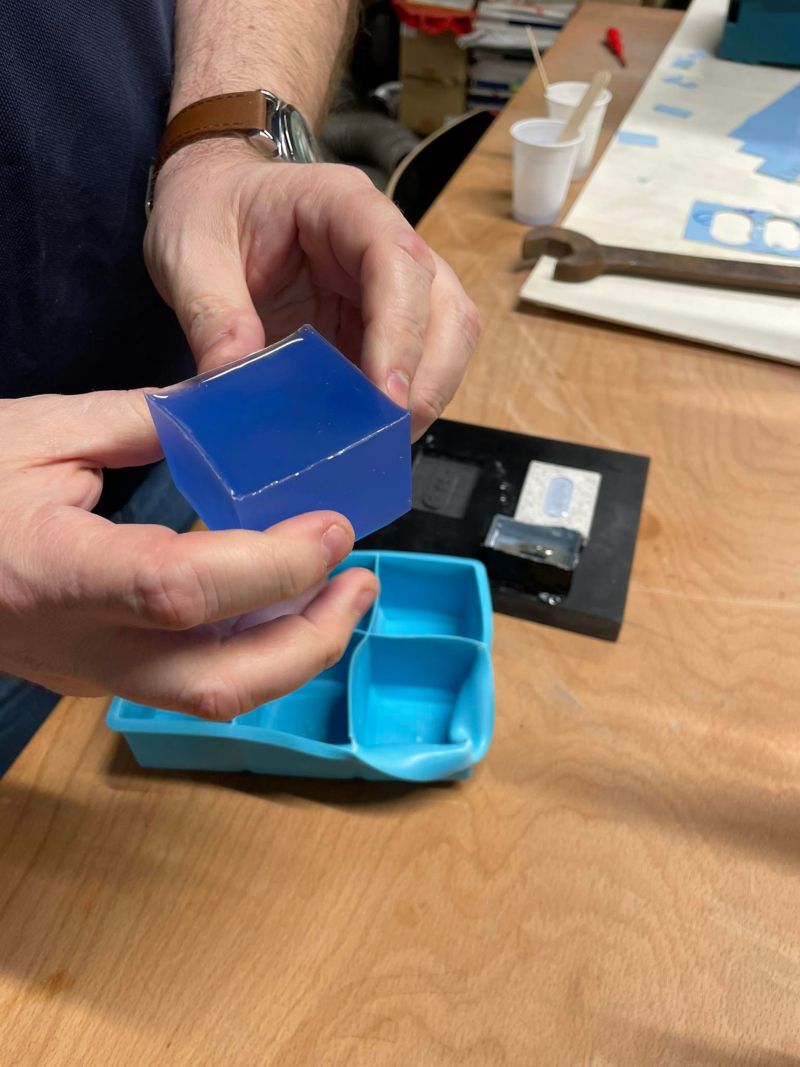
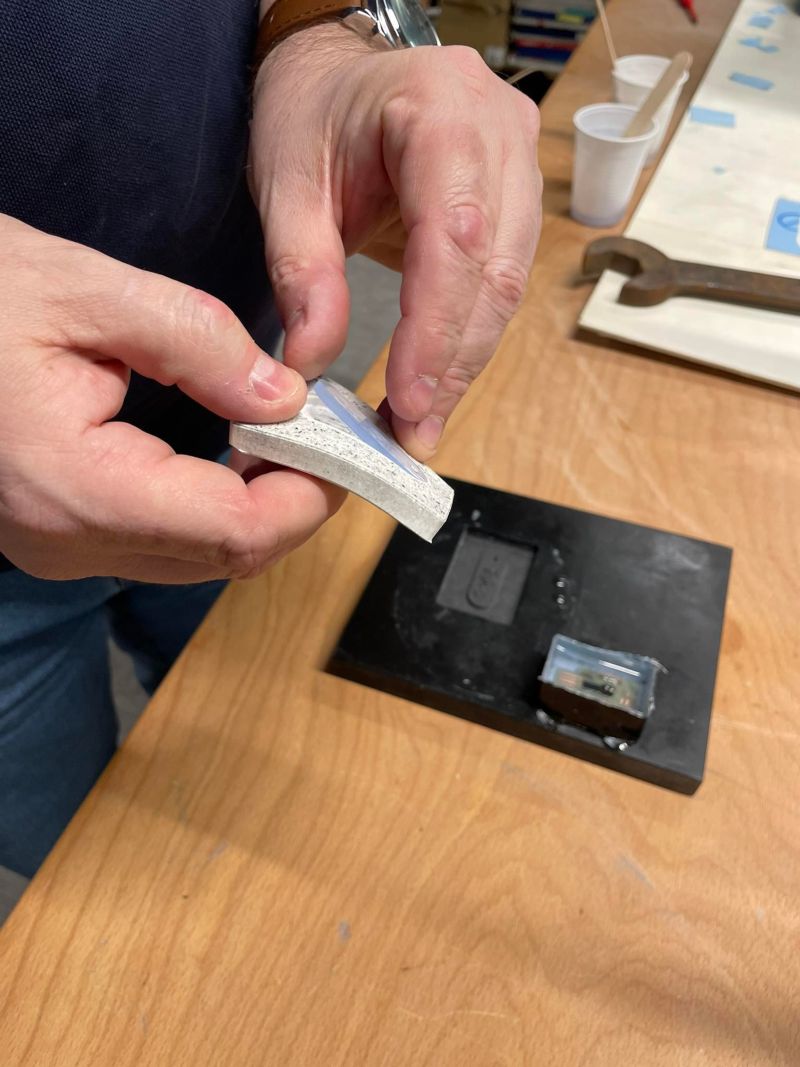
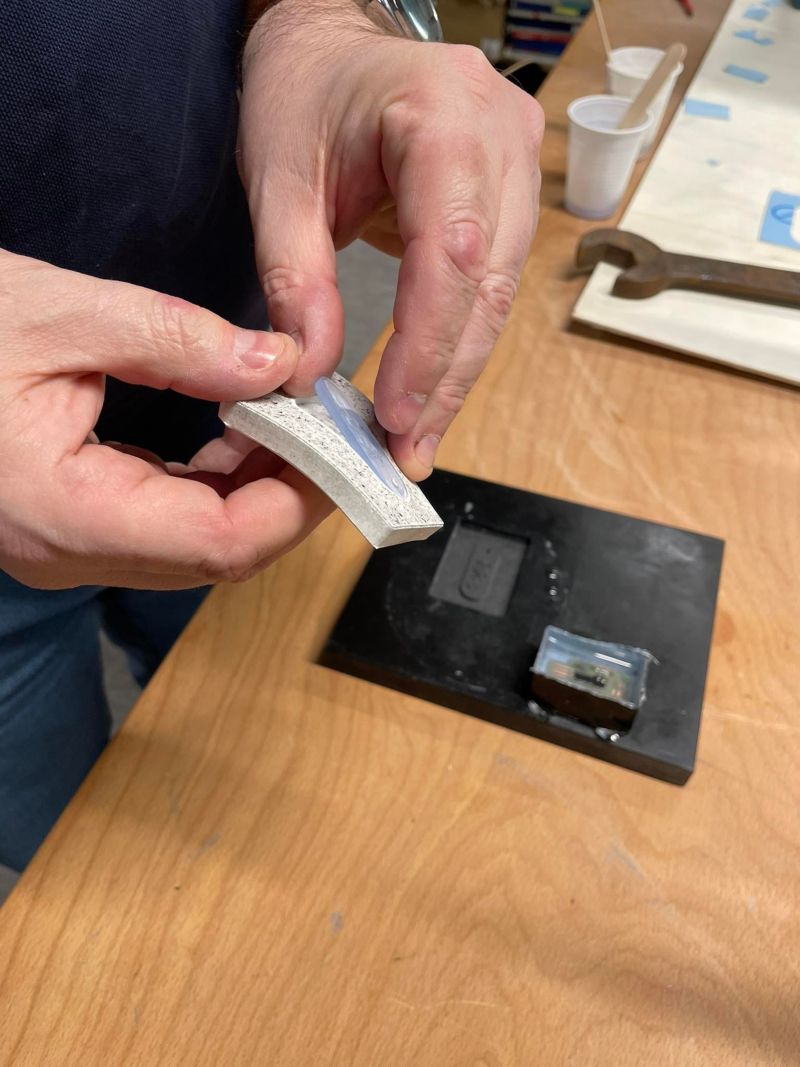
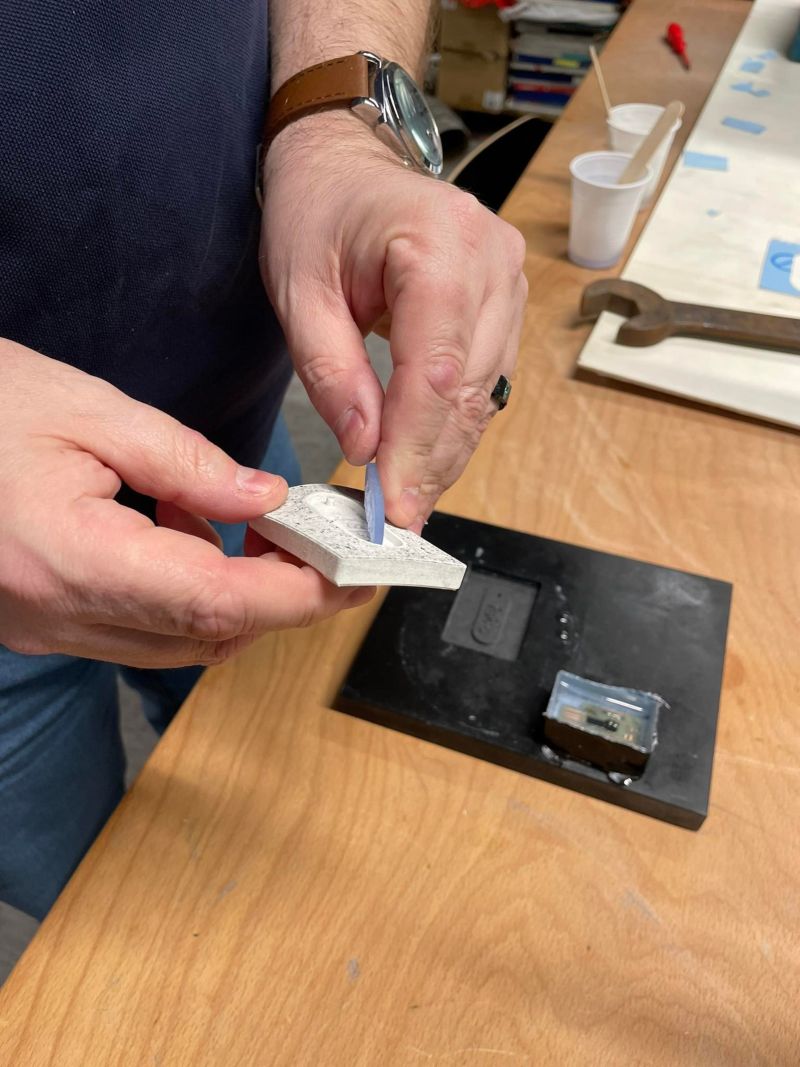

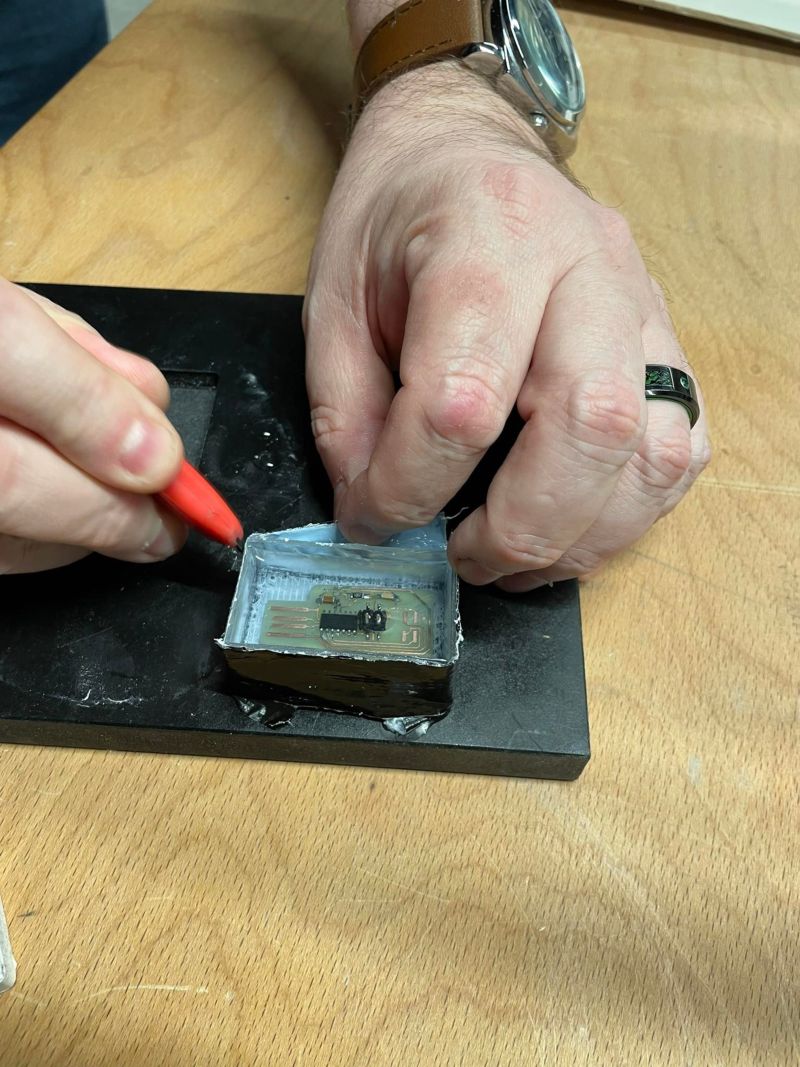

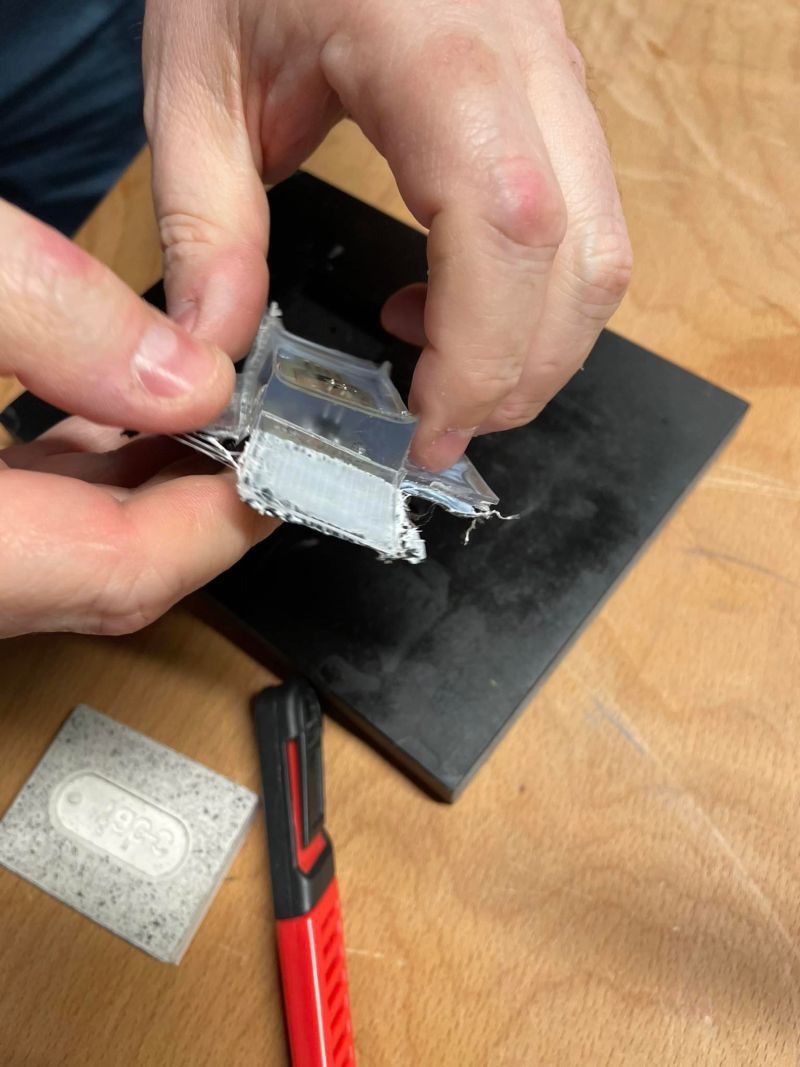
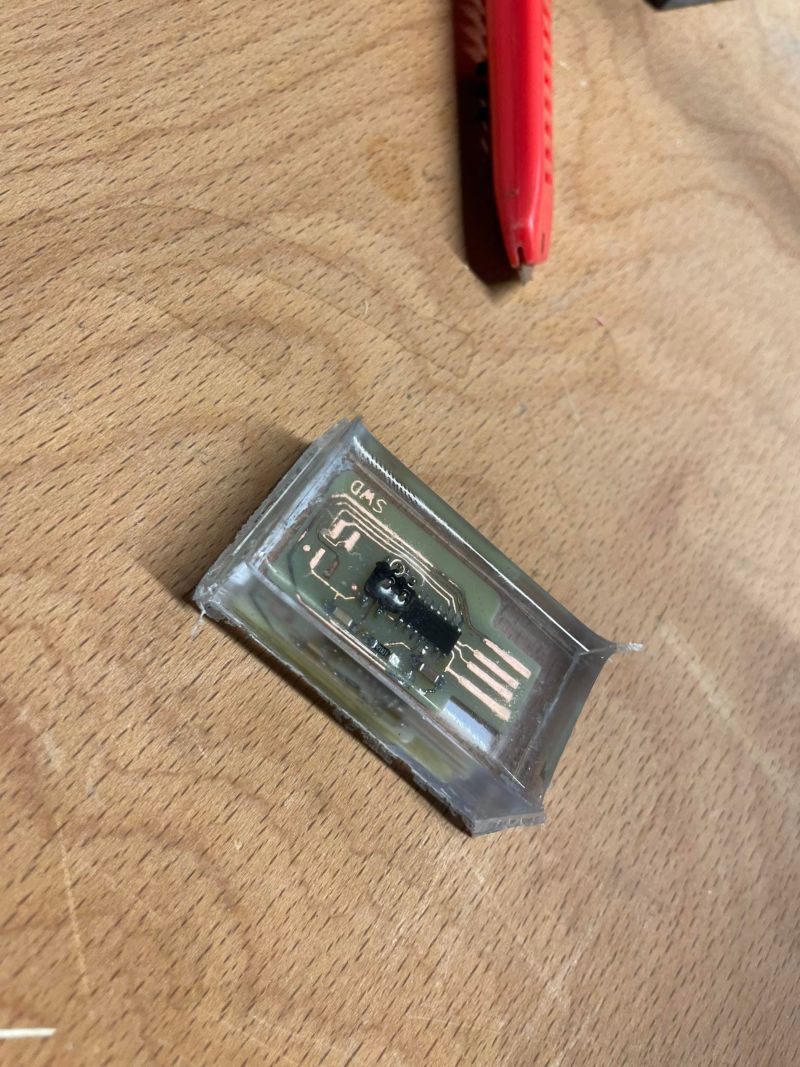
Bonus¶
In an art shop, I found some silicone moulding compound. It is ready in 5 to 10 minutes and the mould can be used 50 times.
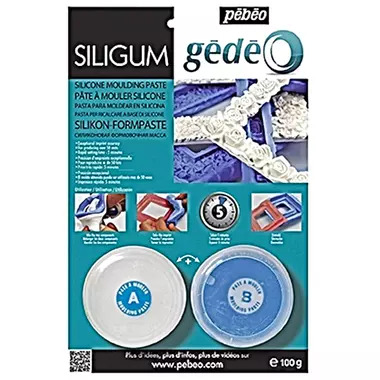
Mixture, 1/1
So I made several moulds to carry out several tests. The first one, with a phosporescent powder, the second and the third with different dyes and the last one with wax



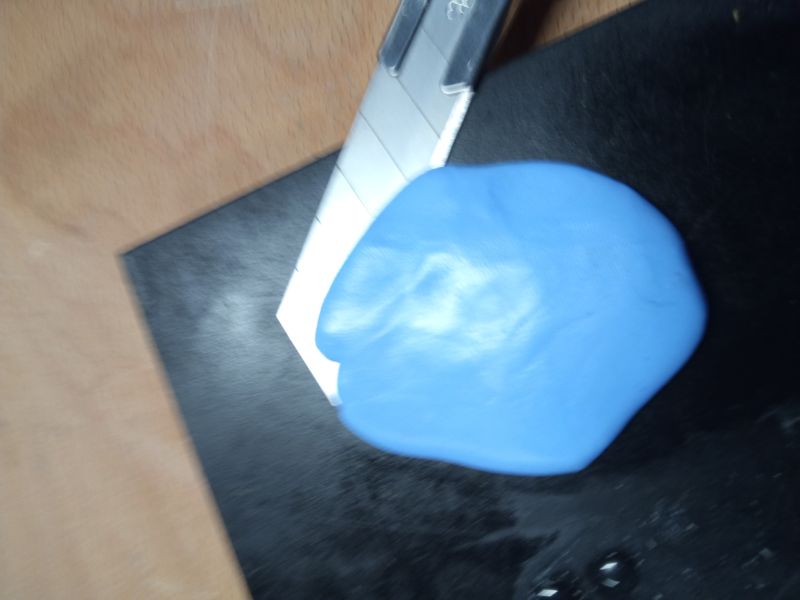
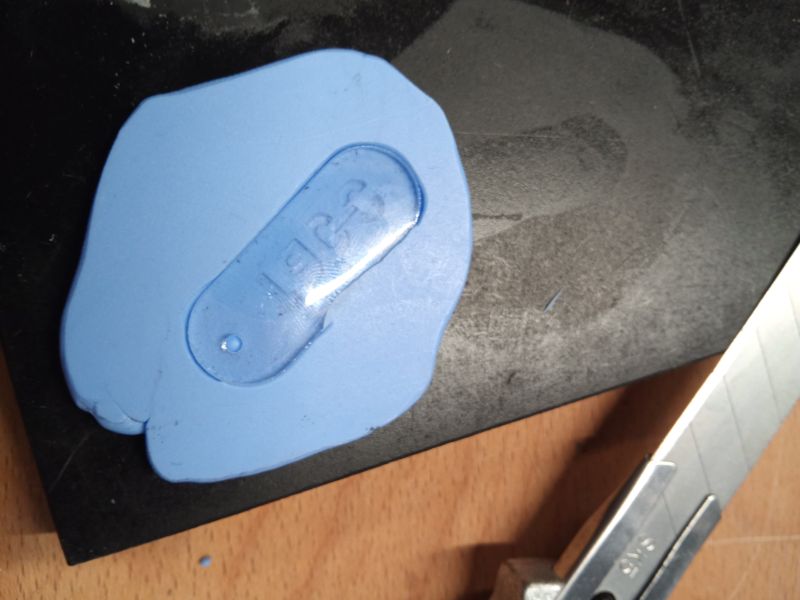
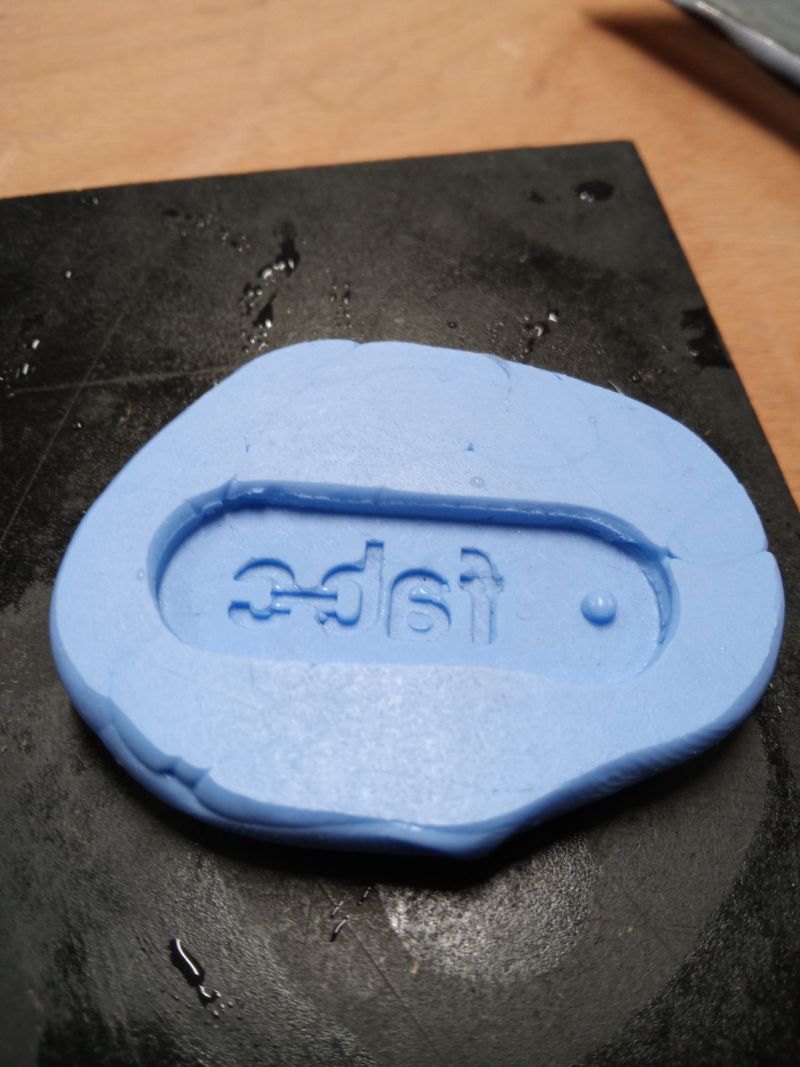
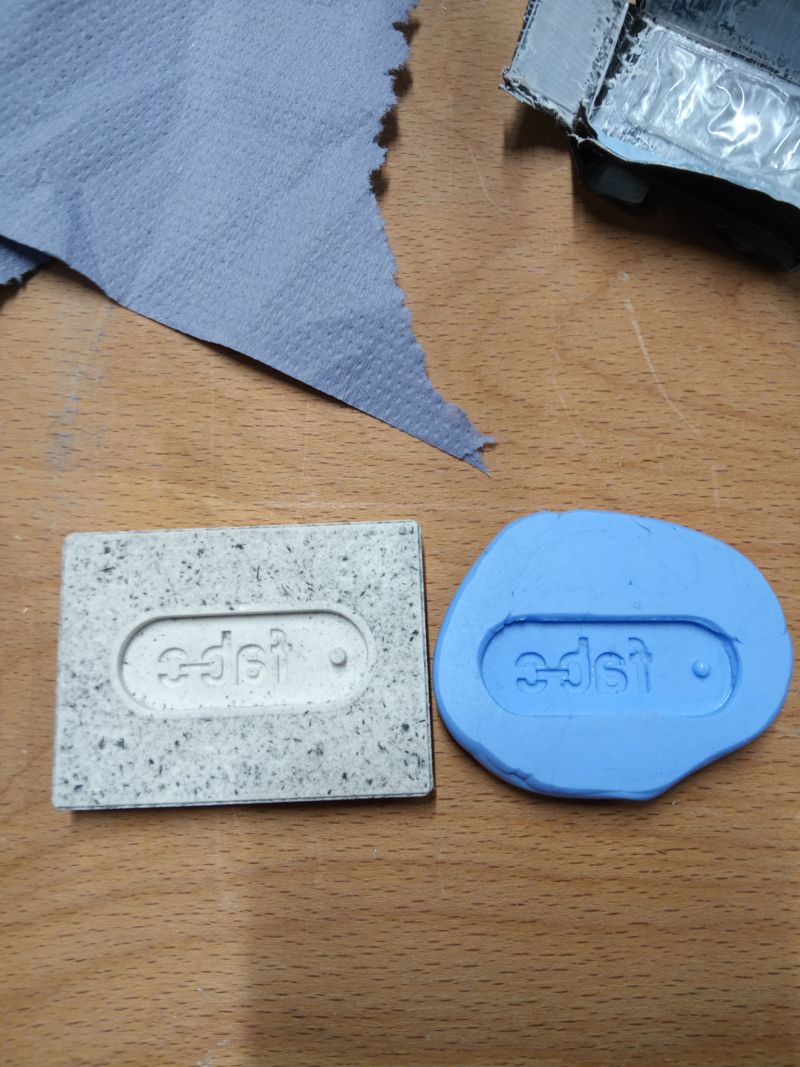
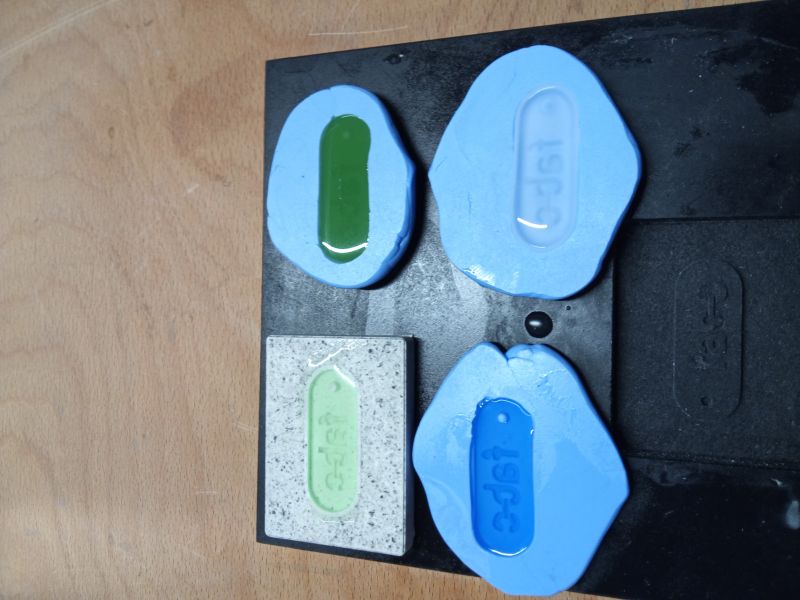
Result¶

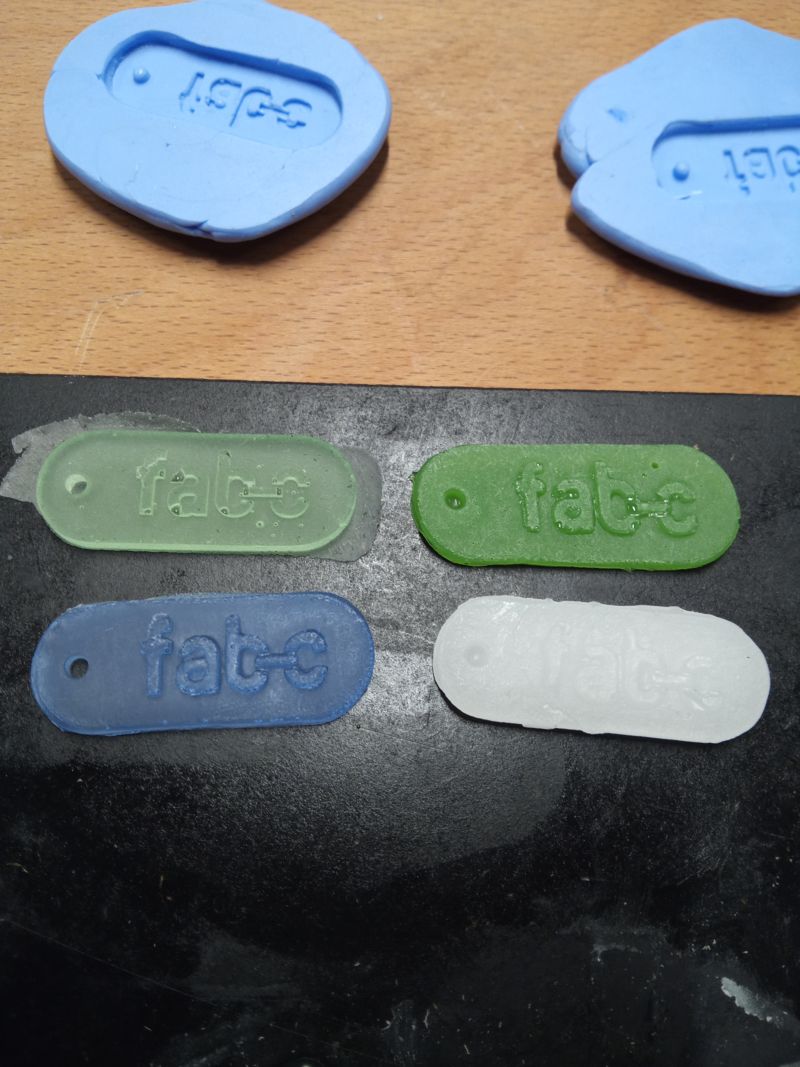
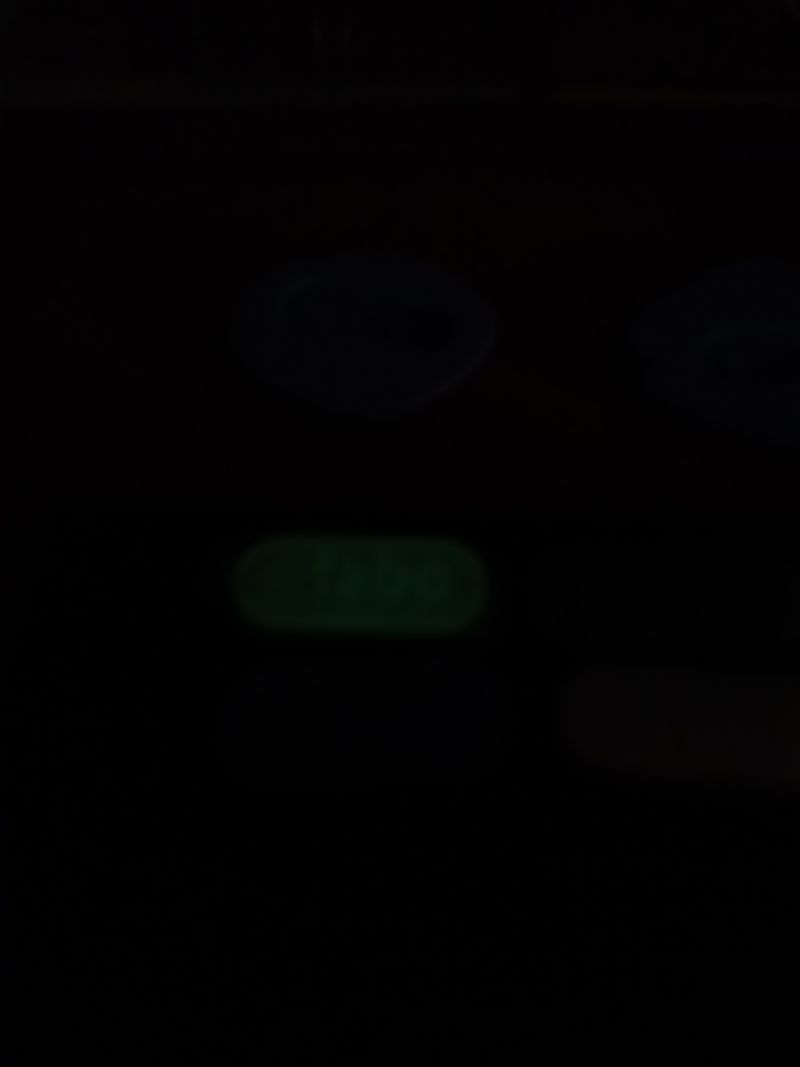