Computer-Aided Design
Week 02
5th-12th February 2014
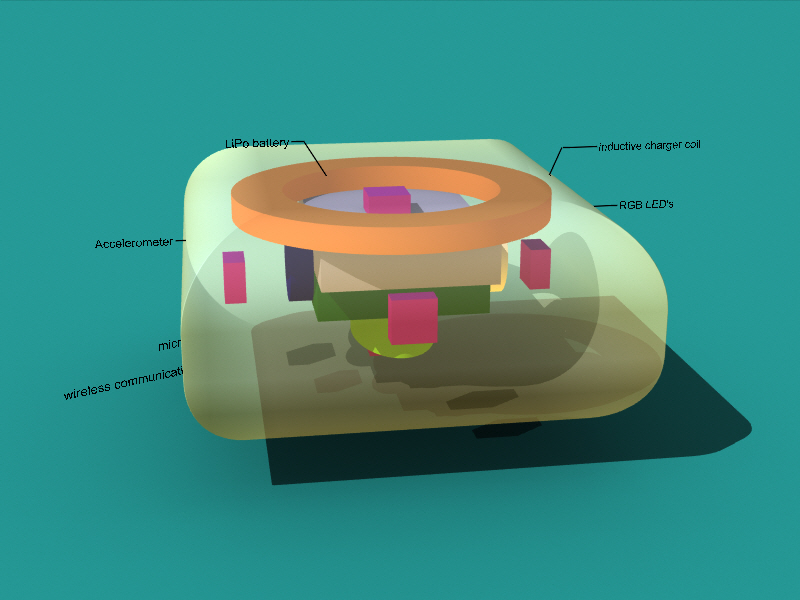
This week's assignment was to model and render a sketch of the final project. For the object that I will try to build, the final shape is not as determining as the electronic functionality. I've therefore sketched out a basic bounding volume for all the components that need to fit inside.
As this was my first reasonably extensive use of Rhino, it took some time to get used to the new toolset. Rendering was particularly tricky, but overall, in about a day of doing tutorials and poking around I arrived at a somewhat decent result.
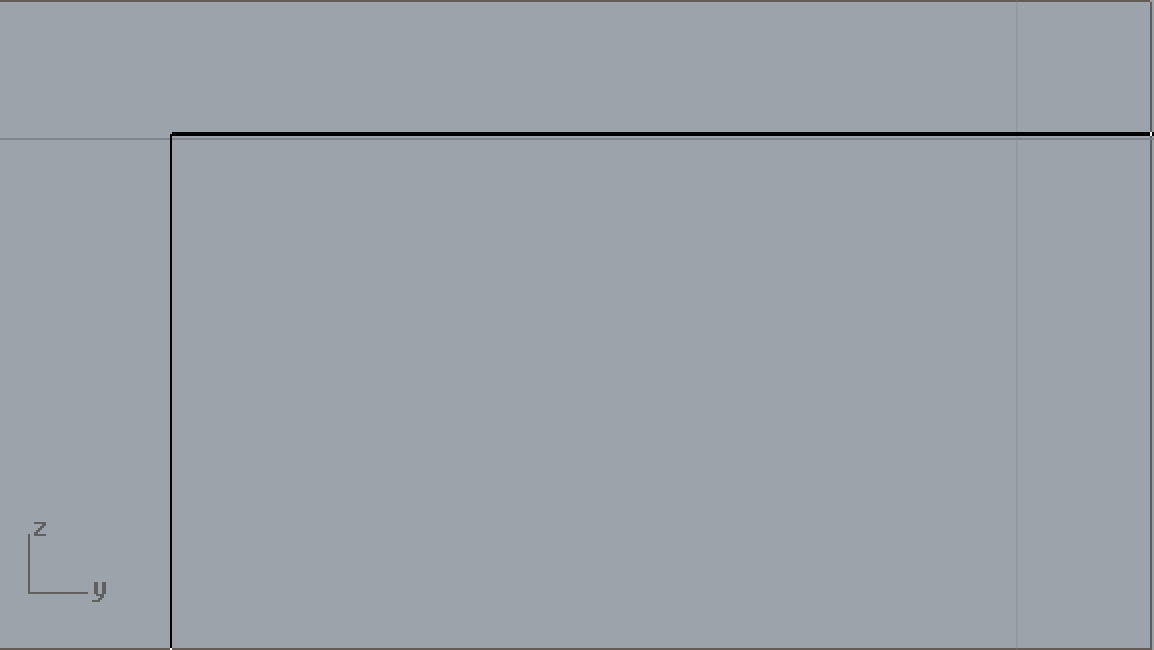
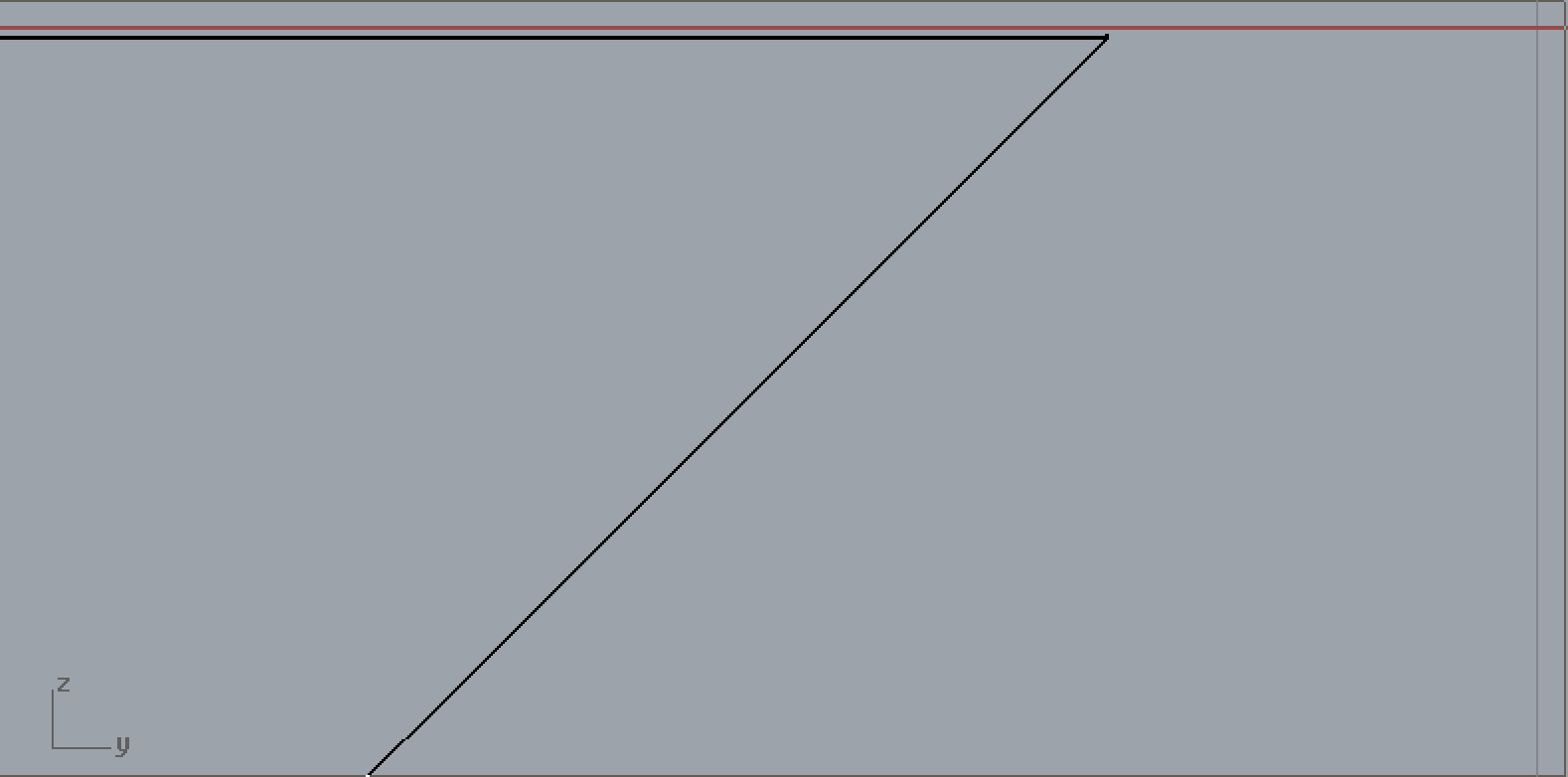
First trouble of working with Rhino started showing when I was trying to mill a precision mold on Modela. Generating precise watertight models in Rhino requires particular attention to the scale and tolerances settings. Even though I tried to re-draw the model multiple times, religiously tracking every snap, I was still getting lines and surfaces that would not align properly. After spending some time trying to resolve this, I decided that maybe it's time to give Solidworks a shot.
This was A VERY GOOD IDEA. Even though I had to spend some extra time learning the interface and getting used to the new workflow, but it immediately felt so much cleaner and more precise and just more fit for the kind of job I needed to get done.
Solidworks model can be downloaded here: