Introduction.
In this week I met and was able to make use of the scanner and 3d printing, I am really excited because for the first time in my life I could make use of a 3d printer, it is fabulous as by means of the computer-aided design object ideas can be materialized, it is required of course design knowledge but it is something that anyone can learn. I could make two 3d prints a sphere inside a cube and it was great.
Group assignment.
- test the design rules for your 3D printer(s)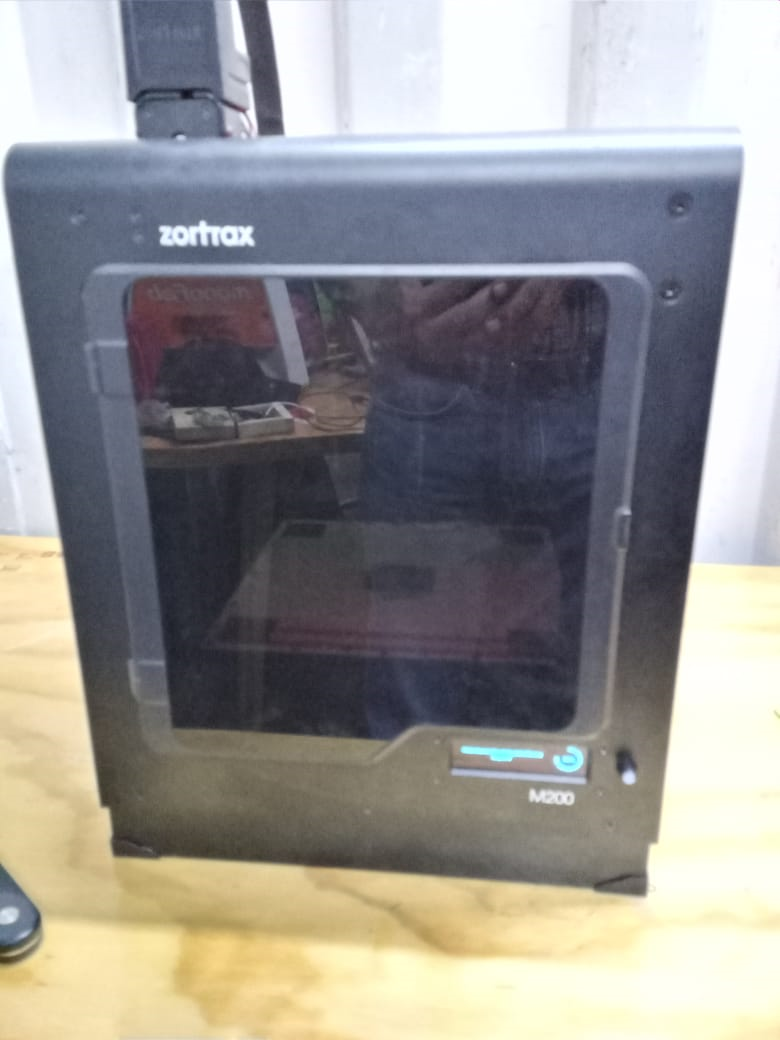
Zortrax 3D printers operate at high temperatures and have easily accessible movable
components,
therefore, you must be particularly careful when handling or operating the devices. While
operating
the printer, it is extremely important to avoid situations that may lead to burns or
interference in
proper functioning.
Do not leave the machine unattended during the print job - check it periodically for proper
functioning in order to avoid potential accidents or breakdowns. Turn off the printer once
the print job is finished.
Keep the printer away from heat sources, fire, flammable materials, humidity as well as
water and other liquids Place the machine away from any equipment emitting radiation.
All service and maintenance activities, as well as the operation of the device, require the
use of safety gloves included in the Starter Kit. It is also recommended to wear safety
gloves when removing the print.
A special room dedicated only to 3D printing is recommended and ensure adequate
ventilation in it. At the same time, it is not recommended to stay in a room where the 3D
printer has been used for a long time. Vapors released during the printing process do not
represent a direct hazard, but they can have negative effects when combined with long-term
accumulated dust particles.
Specification for Zortrax M200
Device
Software
Printing
Temperature
Electric specifications
Installation
Some key steps to start printing with ABS is the correct installation of a thermal plate that prevents its movement using perforated plates, this guarantees a perfect maintenance of the models during printing. Installation is easy, it has magnetic points that are intuitively inserted into the plate. With two connectors they allow the calibration and heating of the tray, these remain visible and must be handled with care, with the time of use we will know if it is a point in favor against after printing several objects. Do not forget about the `protection: gloves, glasses supplied by Zotrax.Then you just have to insert the reel support and guide the cable that feeds the print head, as well as the filament guide that will allow the ABS-Z to reach the extruder. Now you simply have to connect your printer to a power source and press ON.
Software
Z-suite, the brand's software, has a simple and intuitive interface. Only manufacturers and strong supporters of Open Source can be a bit disappointed. Because it can do almost everything ...Among its conventional options is to add, delete, view, flip the model, move, rotate, scale automatically. Something new within the applications is the cut, not the slicage, it really serves to cut the pieces of the pattern to help remove the supports or print larger pieces. This function offers many possibilities that make the task easier if you need to use other software.
In printing, the fundamental thing is: coil type, layer thickness (there are 5 options), speed (2 options), recharge (4 options), fan percentage and, finally, being able to choose the angle at which they will be placed. the supports and the volume they will have. Within the Zortrax M200 software there are also some advanced settings available. Like the location of the seam, where you can choose the same point or do it randomly. This allows you to eliminate the unsightly line on the back of prints when the layer always starts in the same place.
For testing I use the # 3DBenchy model
provided in STL file format, which is an industry
standard for 3D printing. This surface tessellation language describes and represents the
surface of a computer generated object (CAD file).
An STL file is a shrink wrap representation of a 3D model, covering its surface with many
small triangles. # 3DBenchy's high-resolution STL file has exactly 225,154 triangles that
cover the shape of the ship and deviate less than one thousandth of a millimeter (0.00003937
inches).
The # 3DBenchy.stl file is designed and QA for 3D printing. Its topology is 100% waterproof
and does not contain mesh errors such as collector areas, inverted normals, holes, etc.
STL files can be saved in ASCII or binary format. To save disk space, the # 3DBenchy.stl is
provided as an 11.3 MB binary file.
Every 3D-printing process can be varied to yield different results regarding printing-speed, layer height, surface smoothness, material consumption, etc. In most tests #3DBenchy has been printed according to the following generic settings for extrusion-based 3D printers (FFF).
- Scale: 1:1 (unmodified in size, from bow to stern #3DBenchy.stl measures 60.00 mm).
- Layer height: 0,2 mm
- Infill: 10%
- Print speed (extrusion): up to 50 mm/s
- Print speed (travel): up to 150 mm/s
- Print nozzle diameter: 0,4 mm
Calibration
The Zortrax M200 calibration is semi-automatic, 5 colored squares serve as calibration zones. When you start leveling, the machine takes over, and after many twists and turns it gets close to the print head with the required distance from the heating plate. If it is too close or too far, the printer prompts you to tighten or loosen a screw present at the bottom of the plate, after which the automatic calibration restarts.individual assignment
- design and 3D print an object (small, few cm3, limited by printer time) that could not be made subtractively
Considering that the design should not be able to be created using another type of technology, such as laser cutting or cnc cutting, I thought of designing a cube and putting a sphere inside it, those cuts in the corners of the cube I think can not be done another way, only with 3d printing.First I create a sketch. Second in the create menu, select rectangue-> center rectangle.
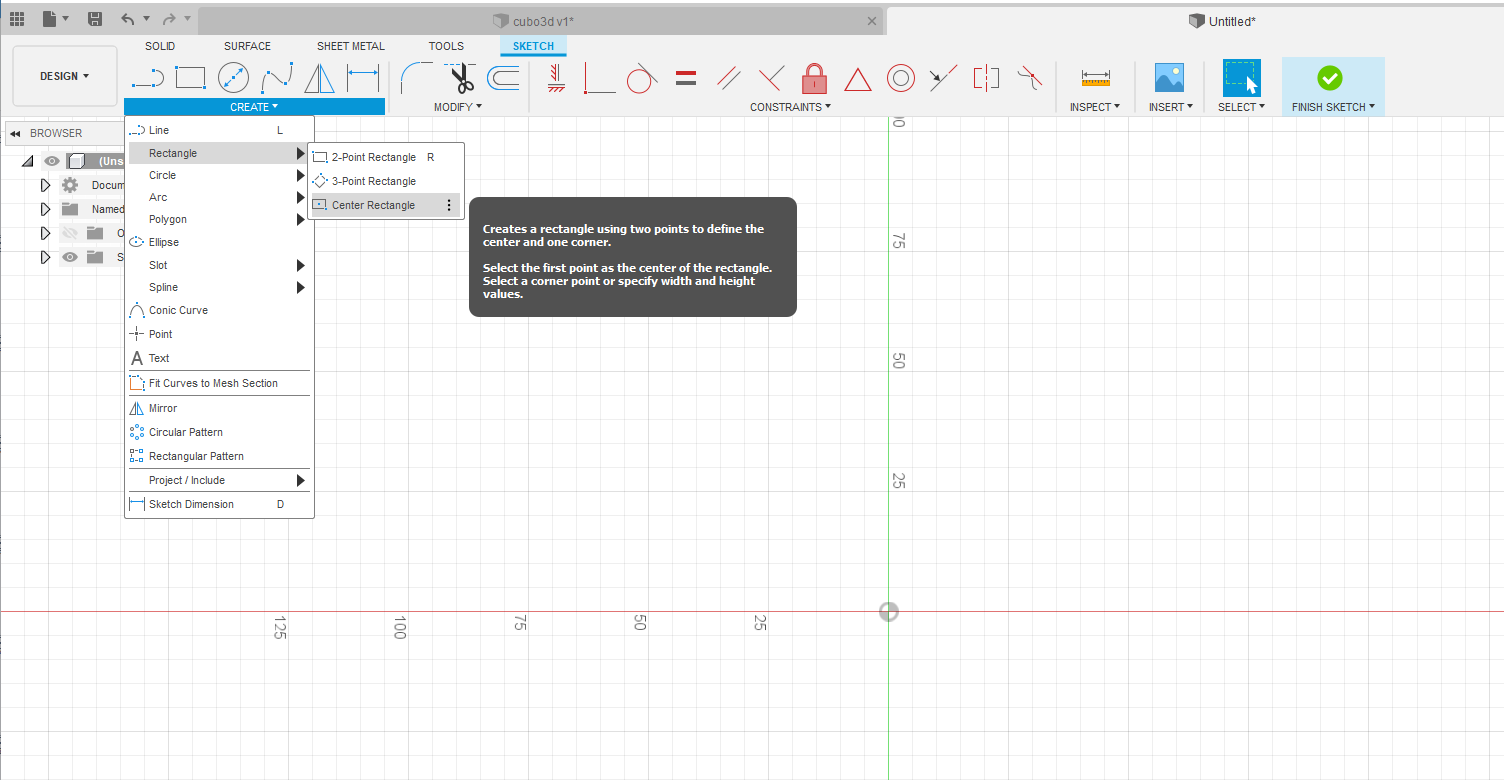
Third gave square measurements and I click finish sketch.
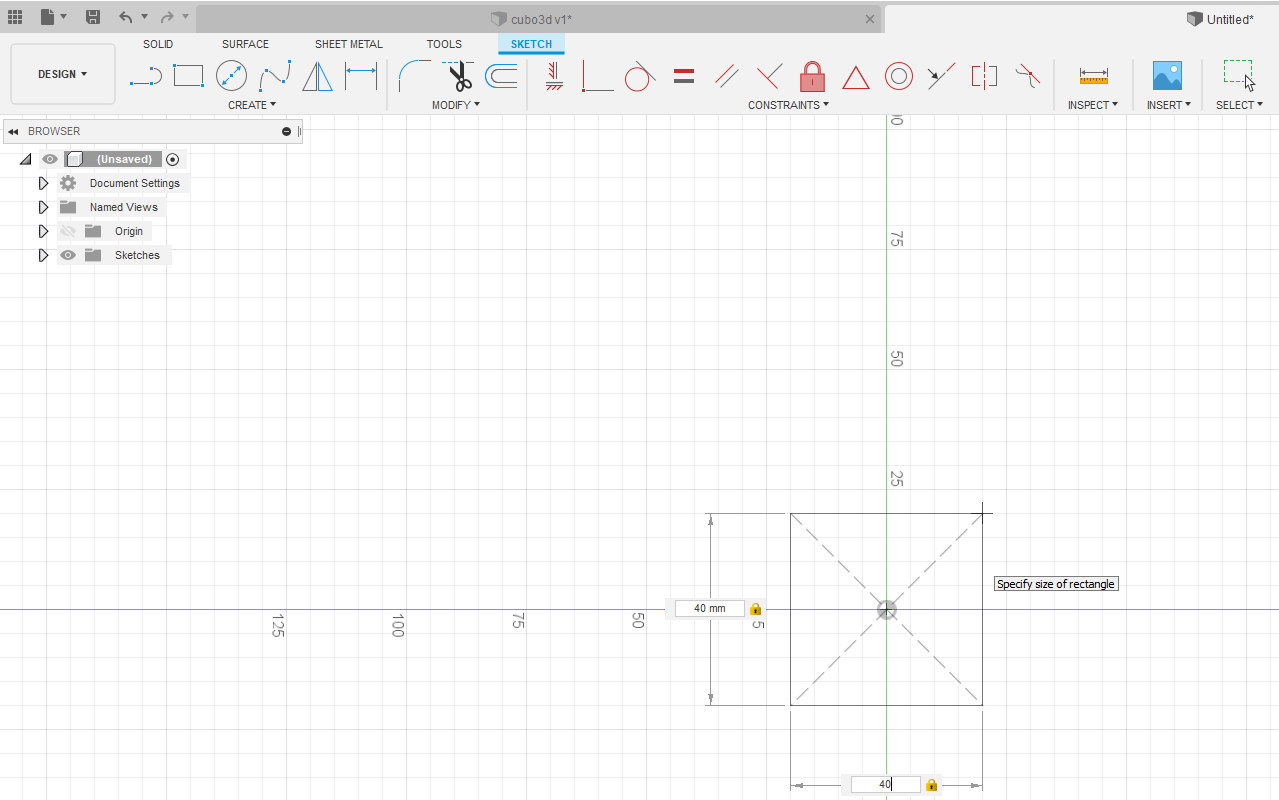
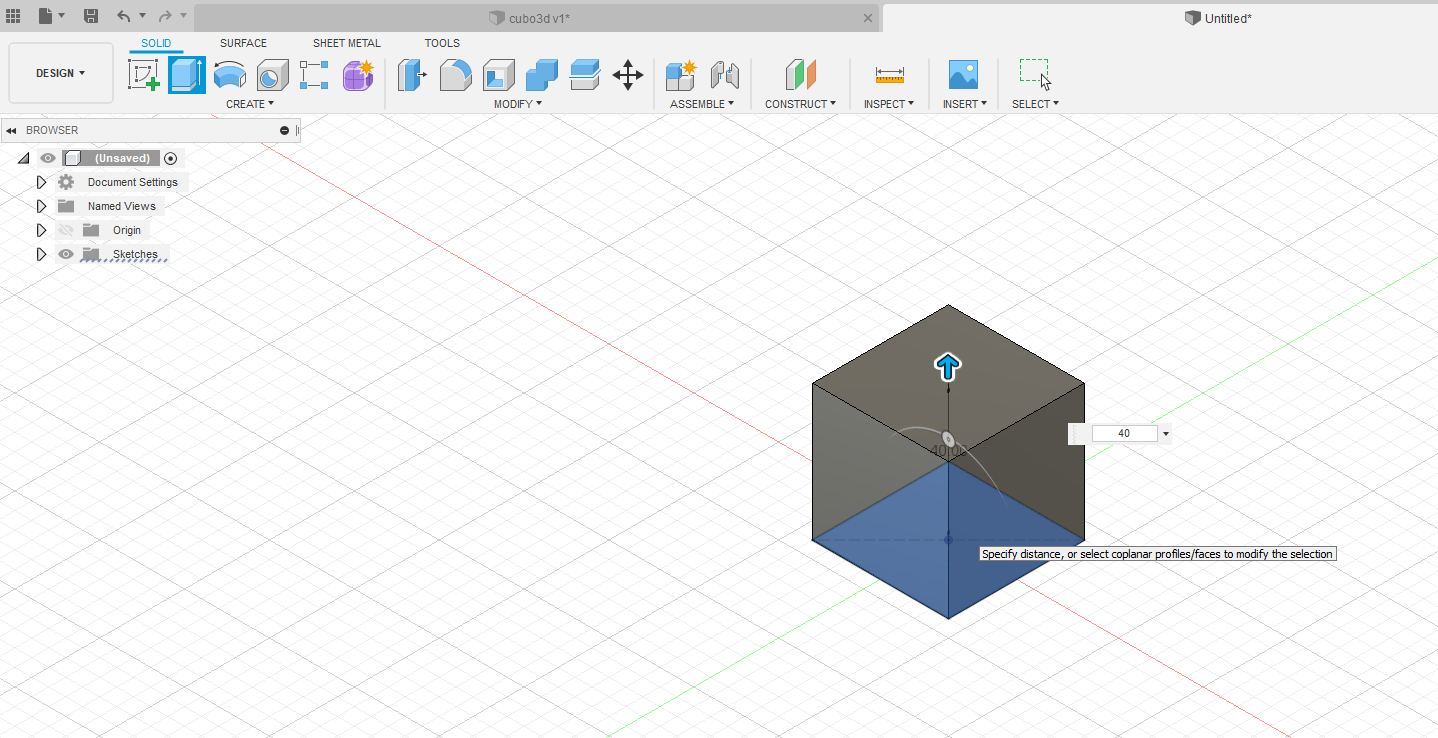
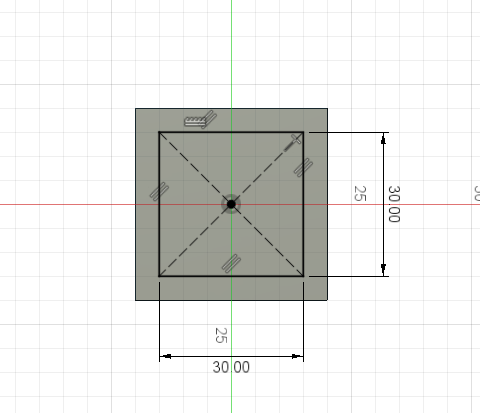
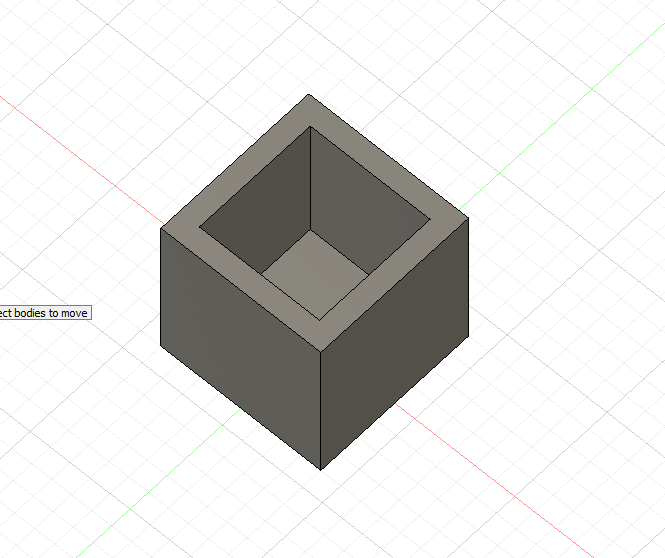
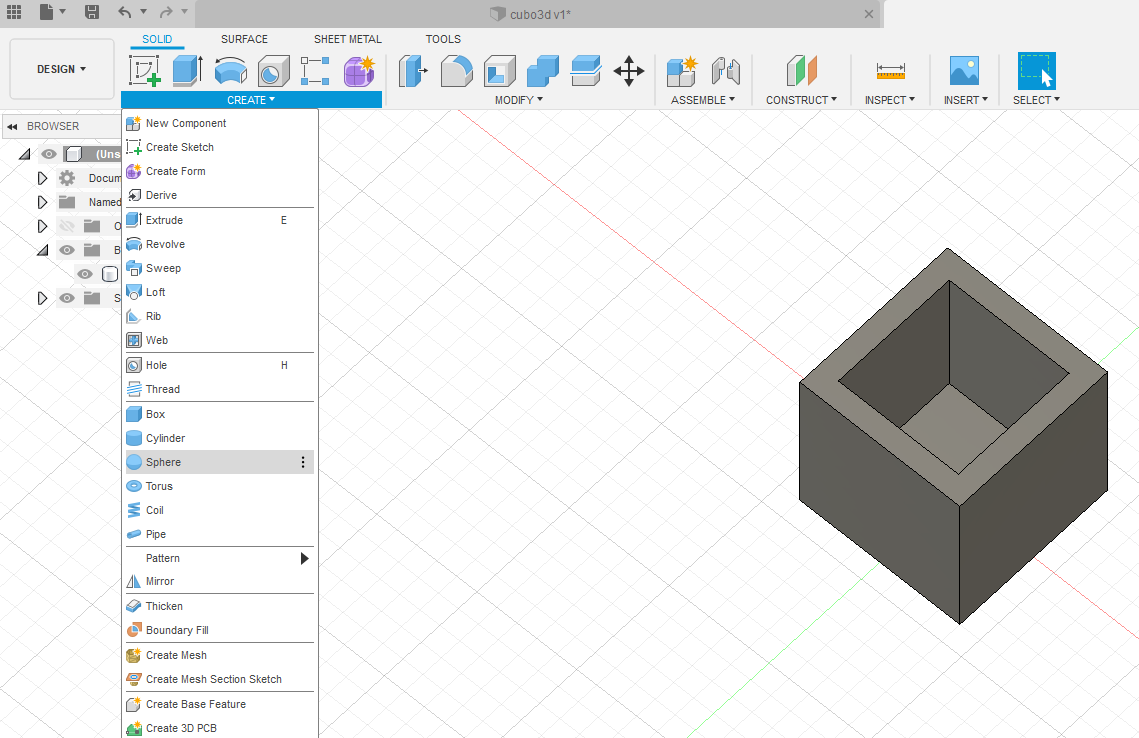
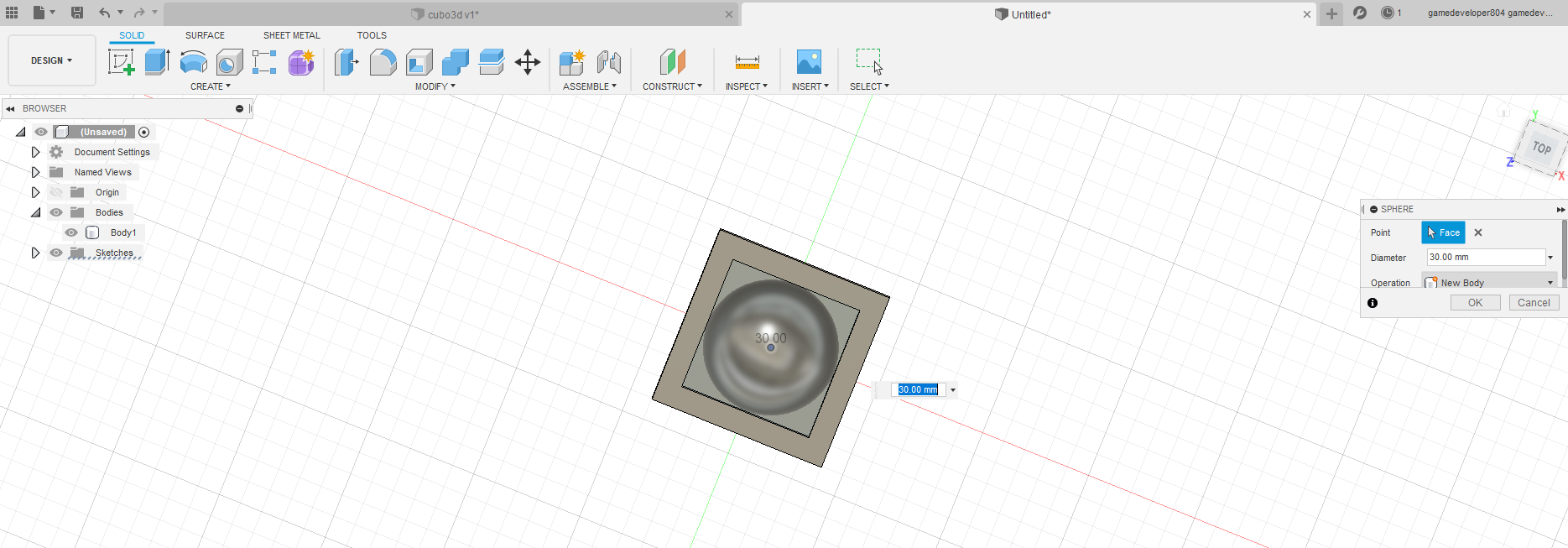
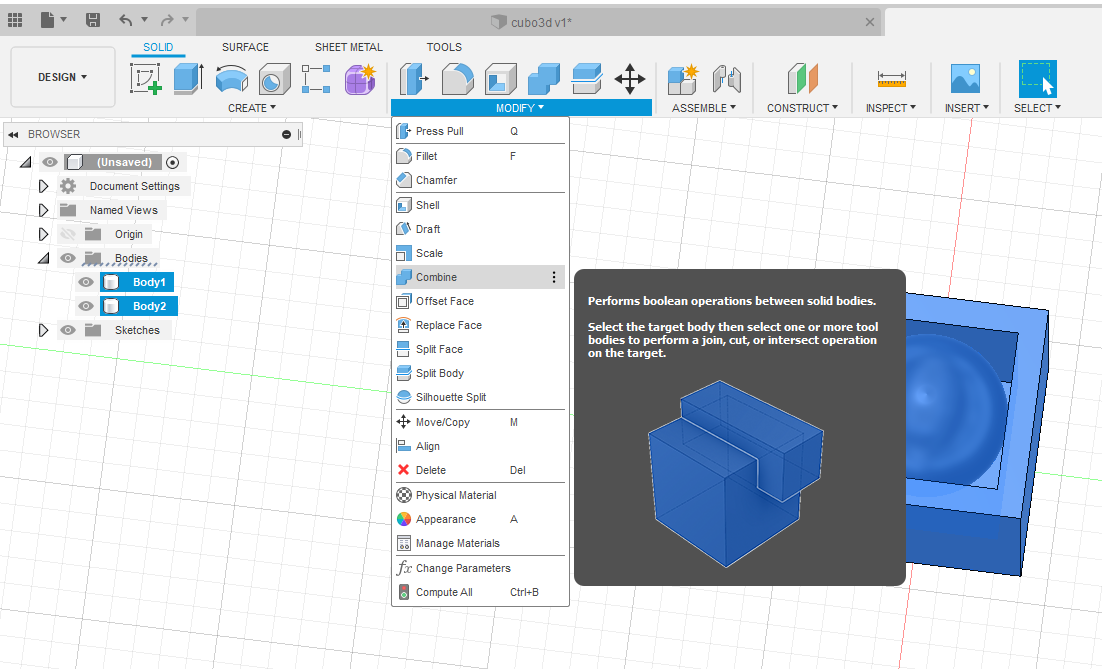
The 3d design consists of a sphere contained within a cube, the space that remains of the circular parts of the sphere on the walls of the cube, I think it would not be possible to do it by subtraction.
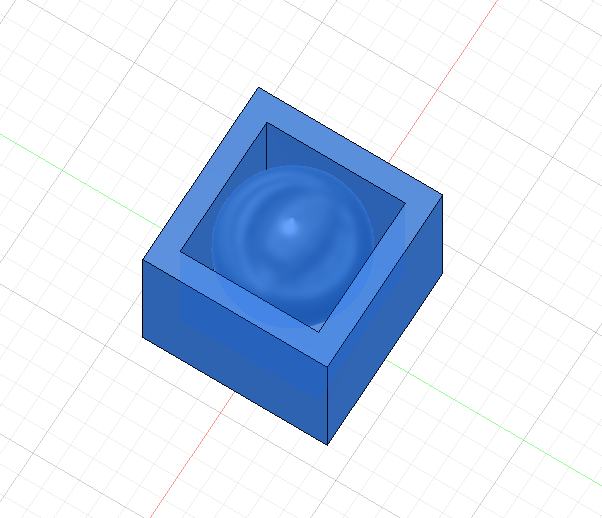
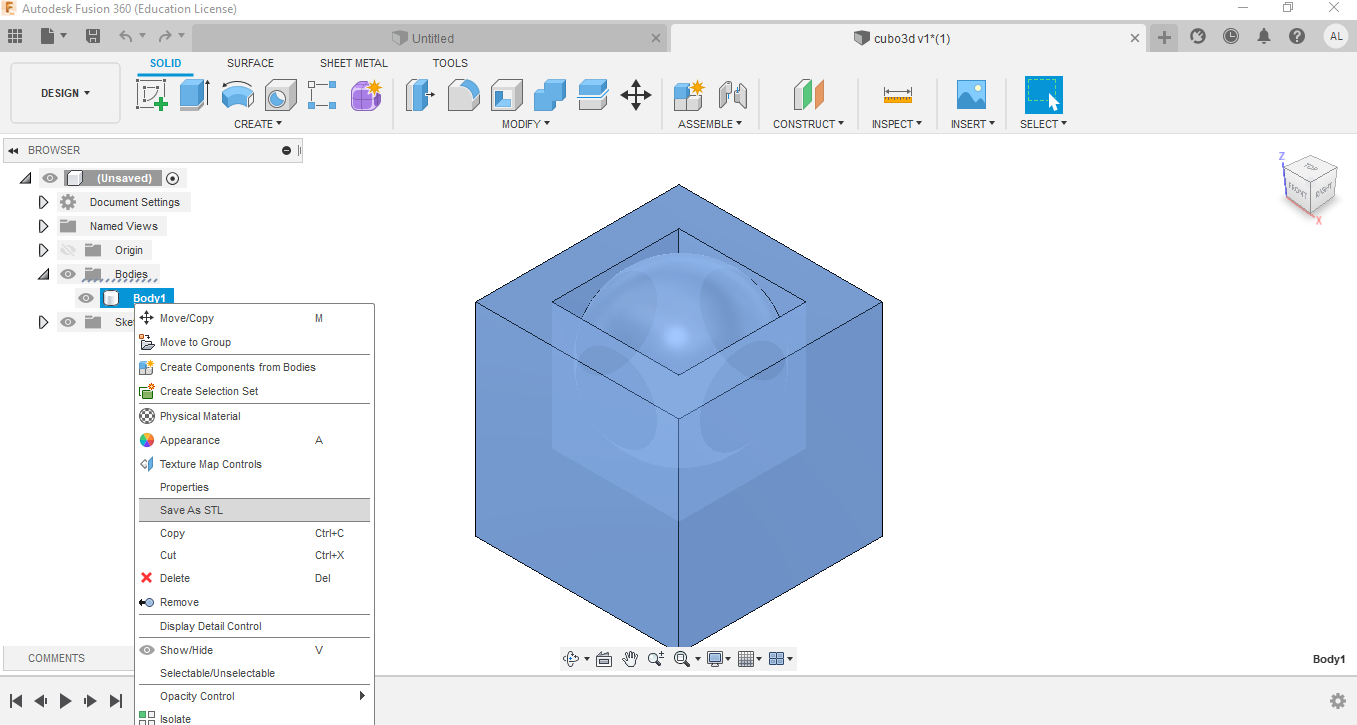
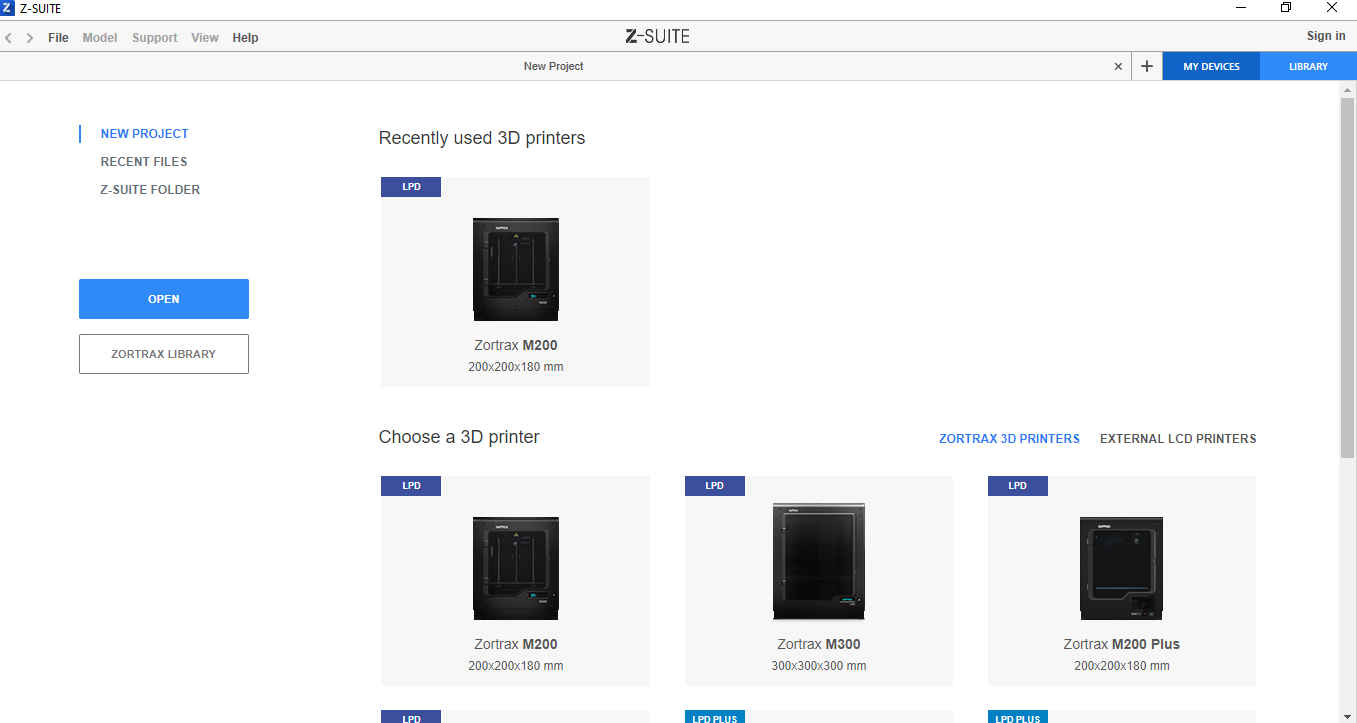
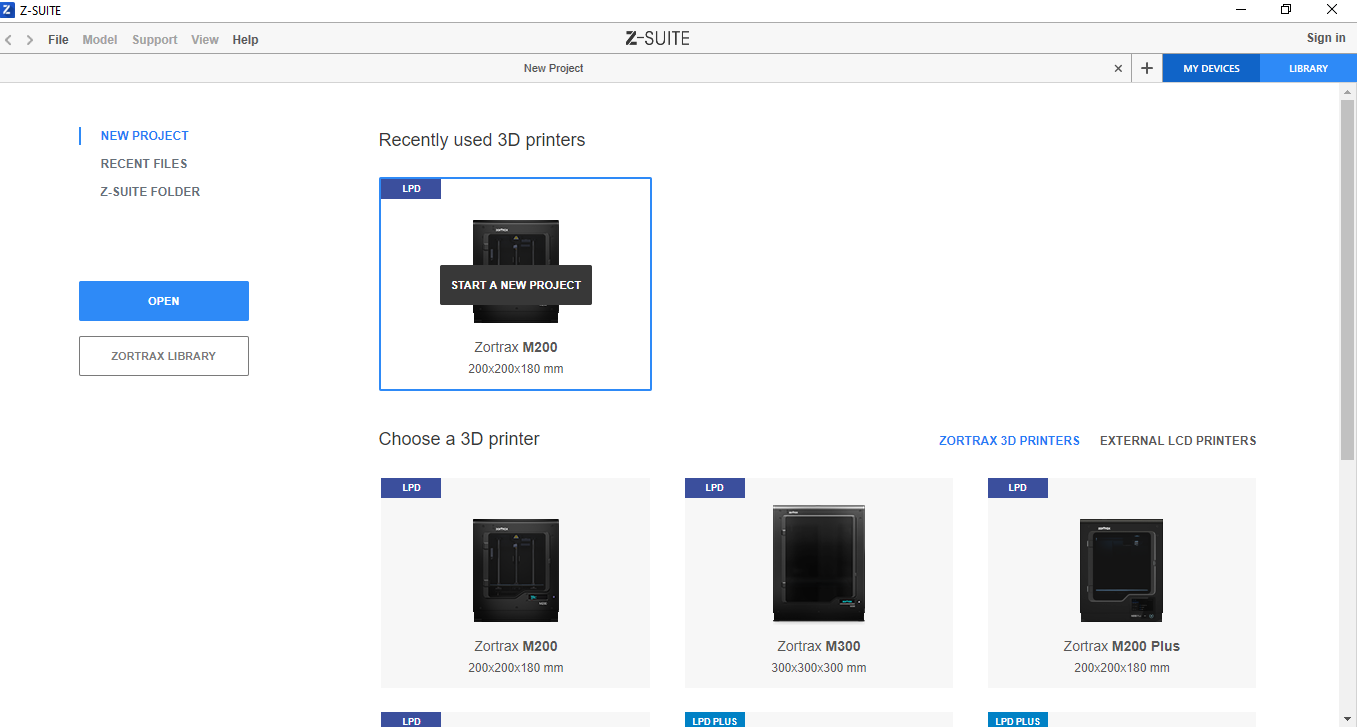
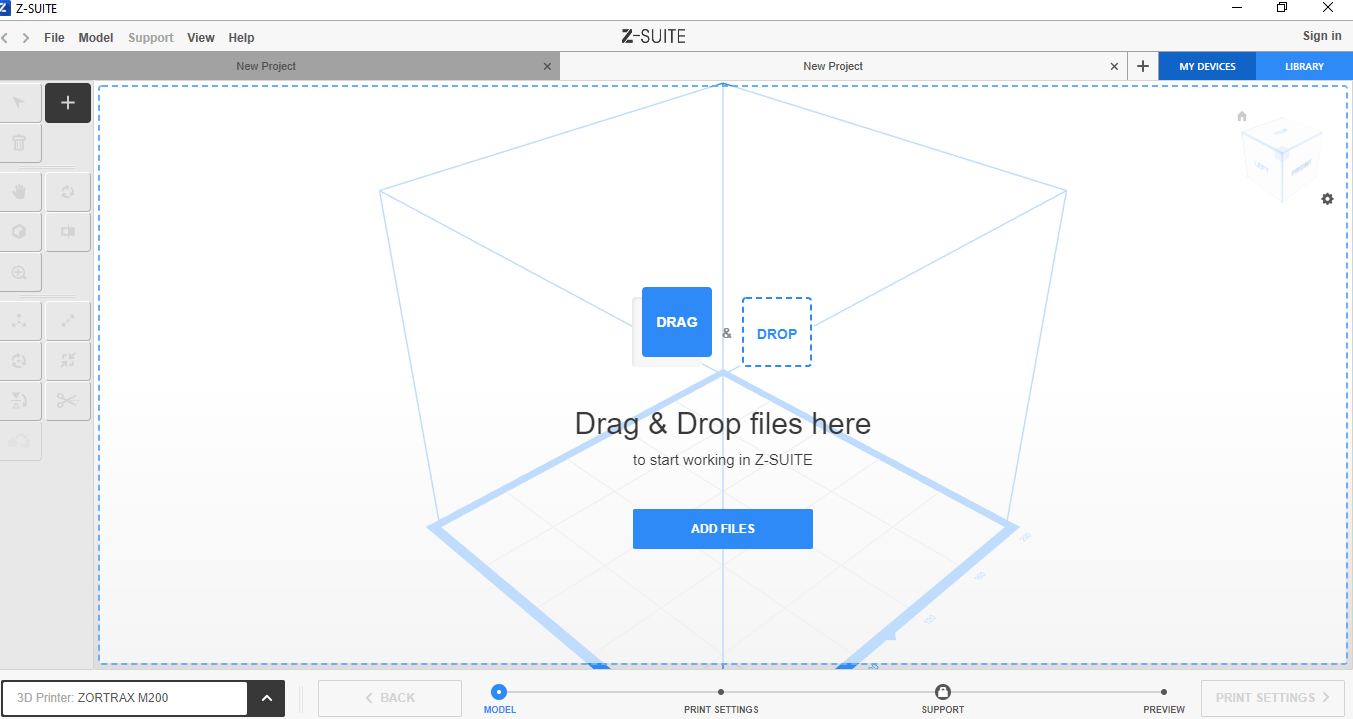
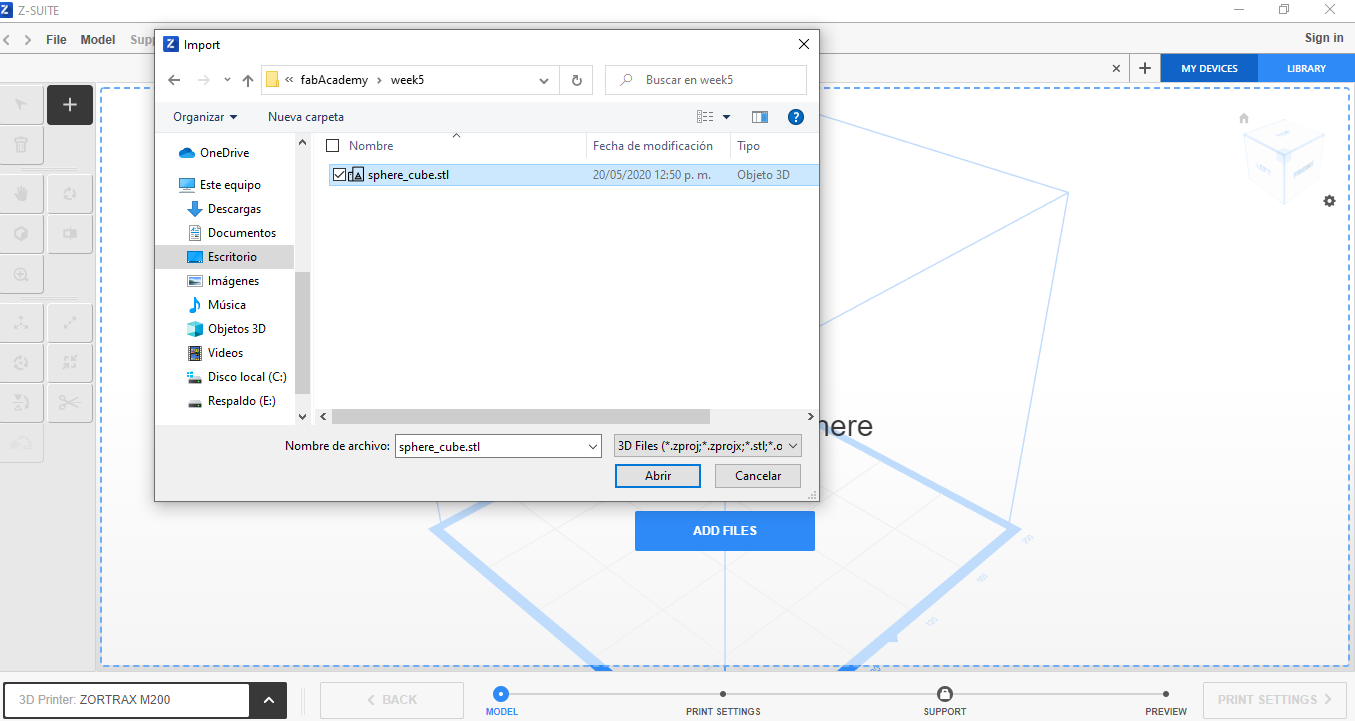
As you can see in the left panel there are several options that allow, among other things, to add another model, apply zoom, it is a matter of testing what each one does.
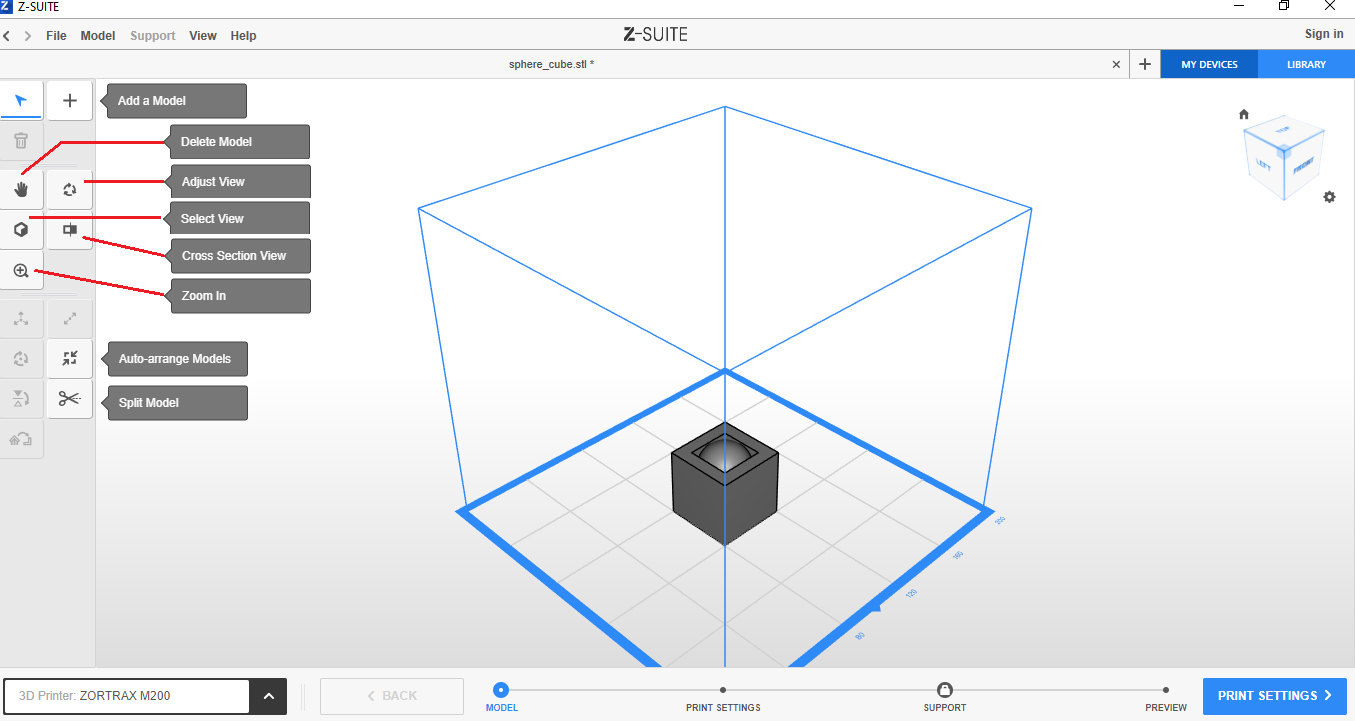
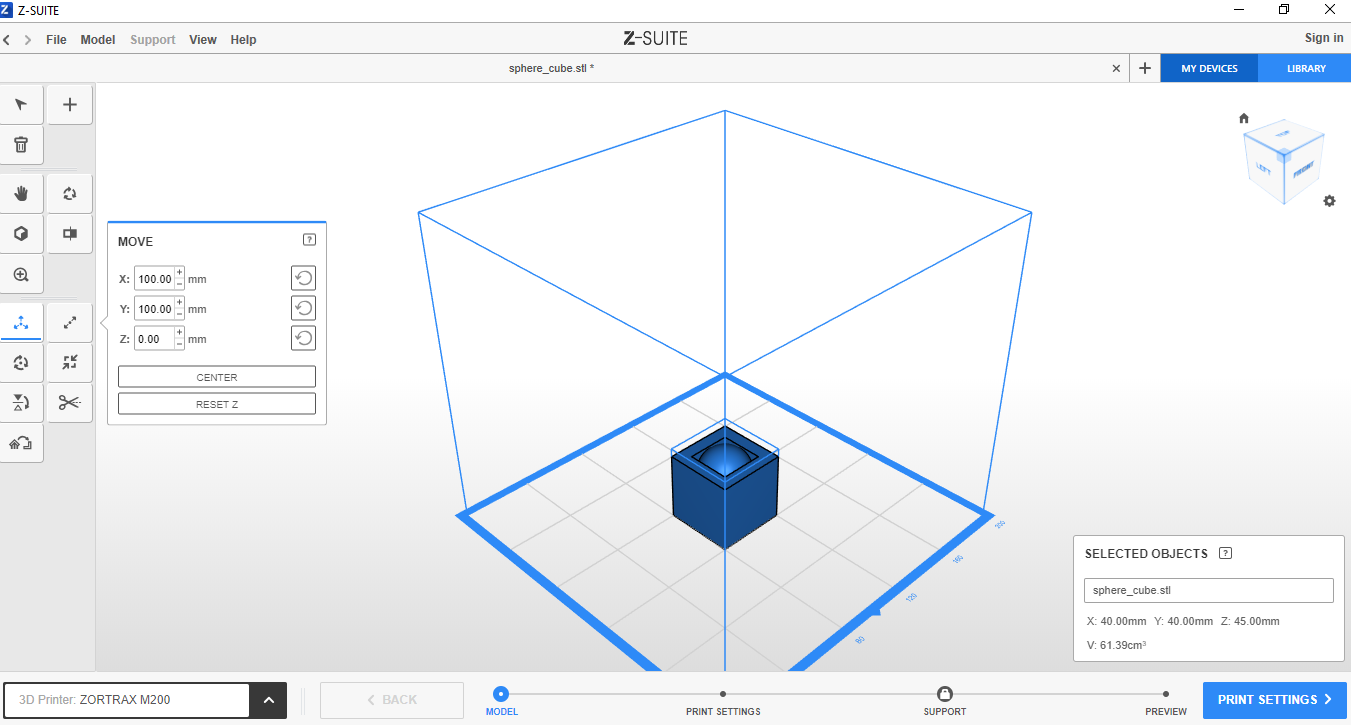
When the model is selected, you can see the size of each axis.
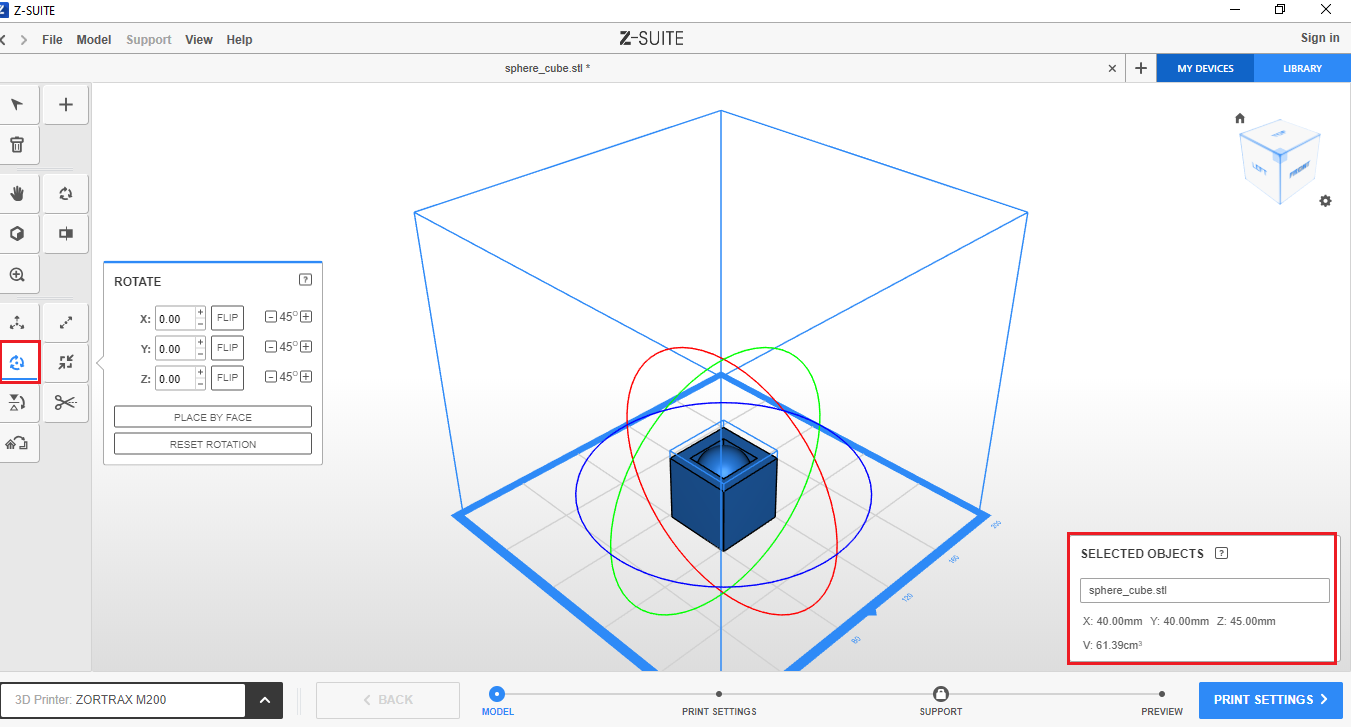
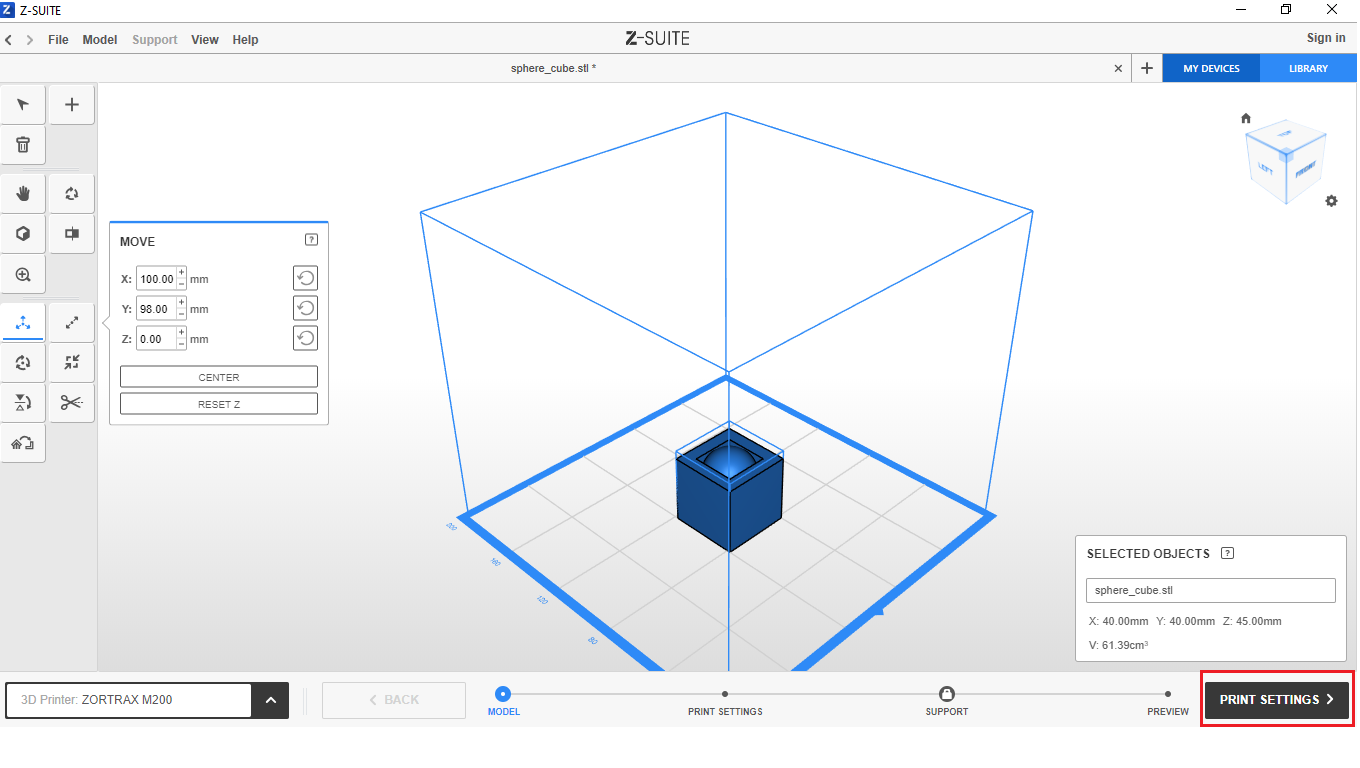
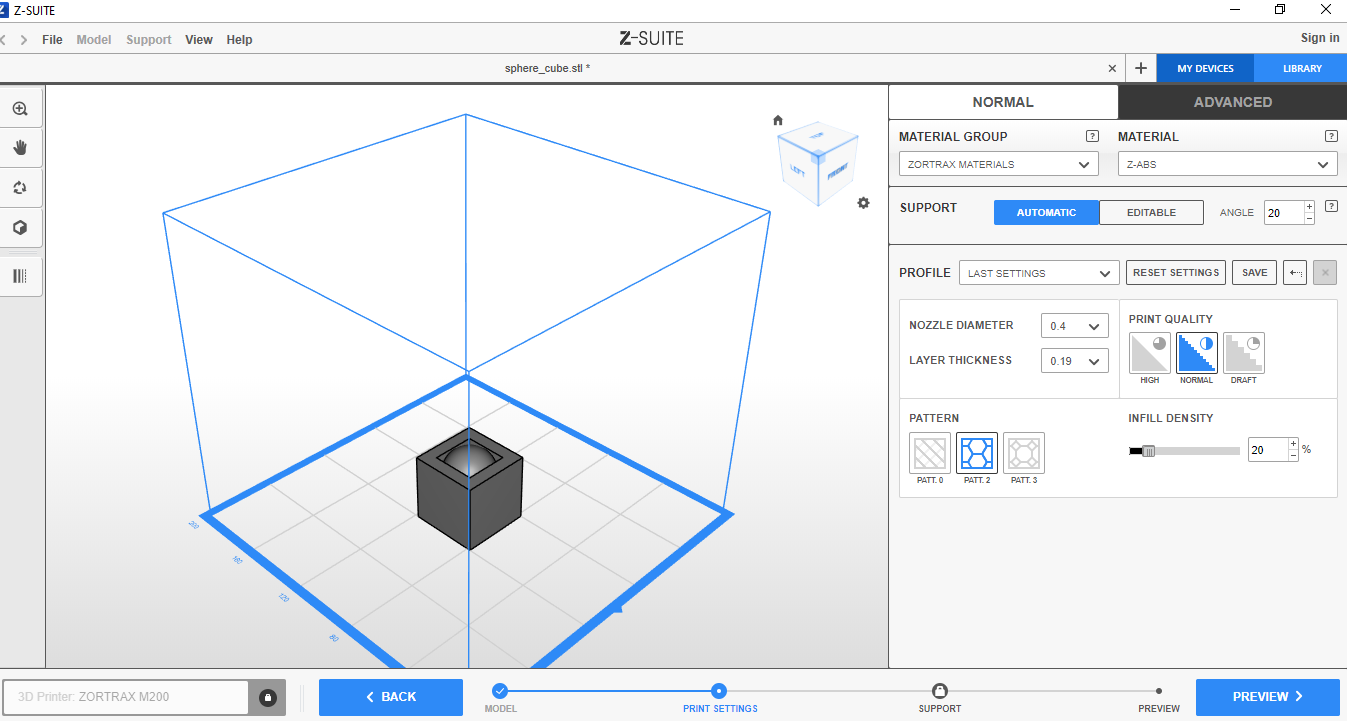
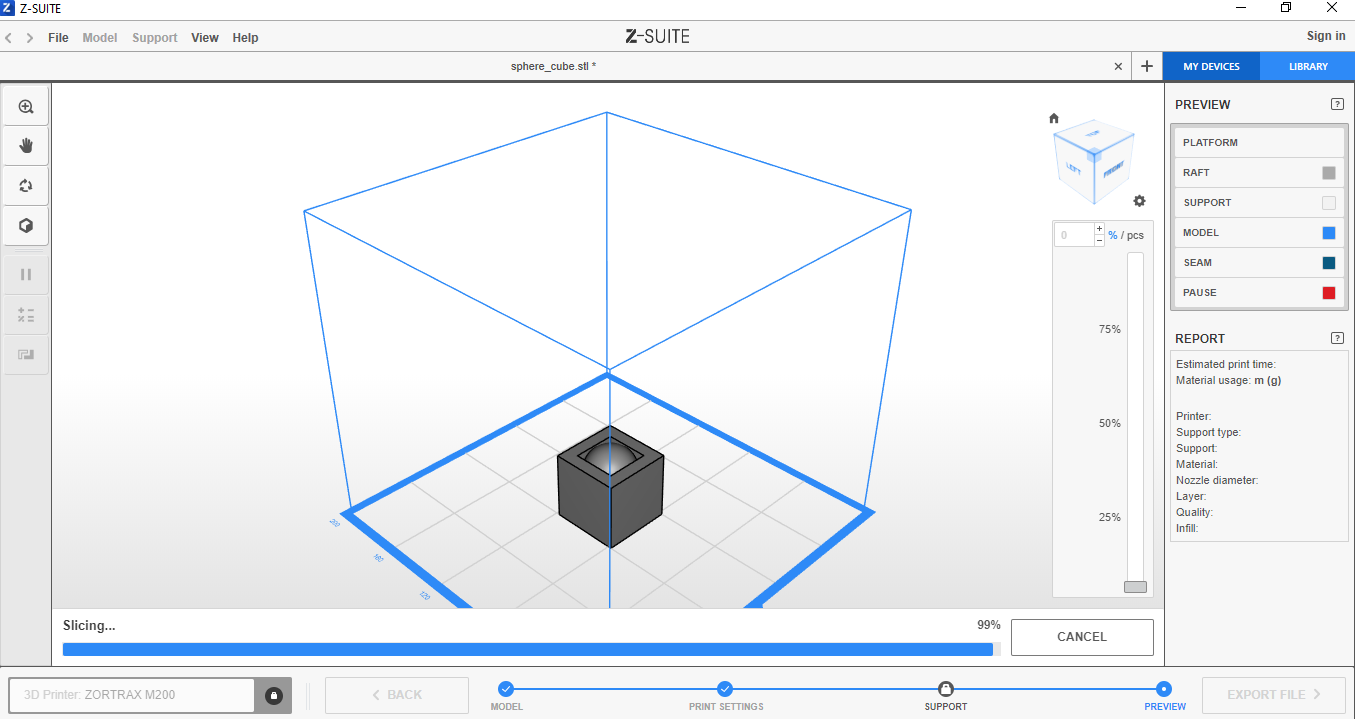
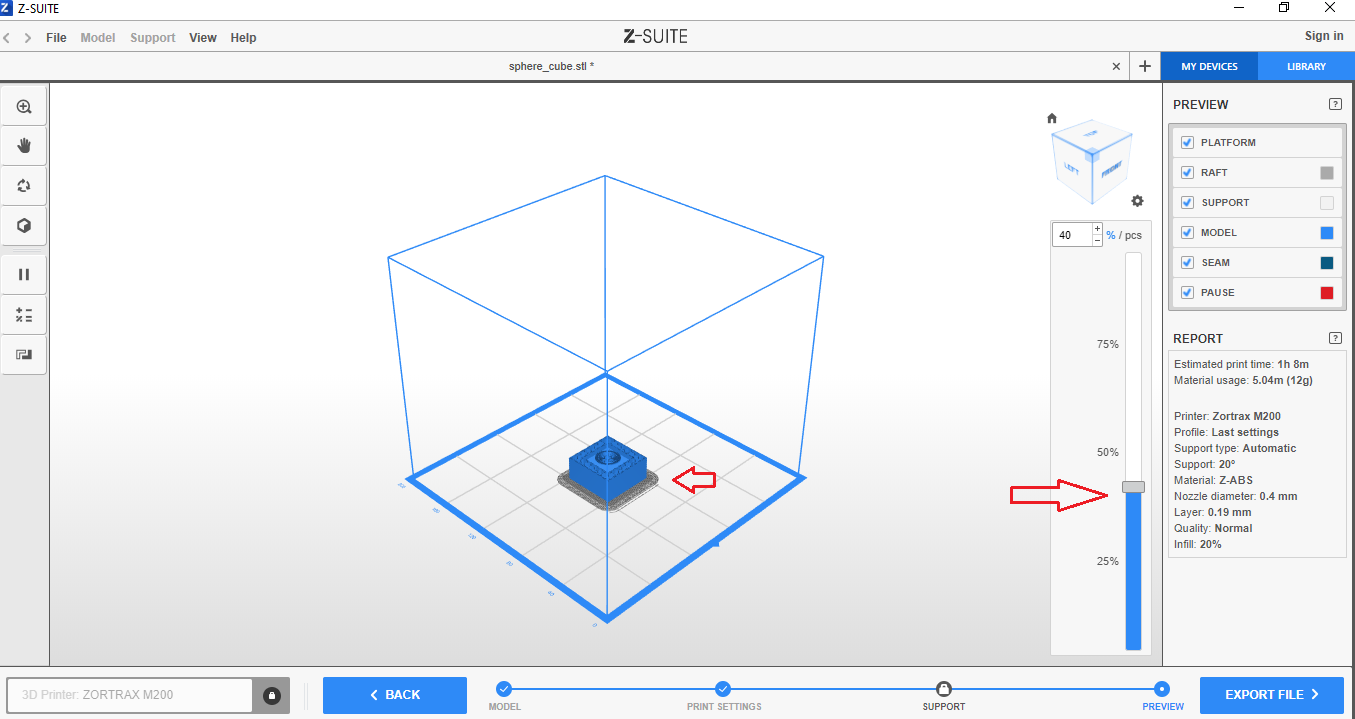
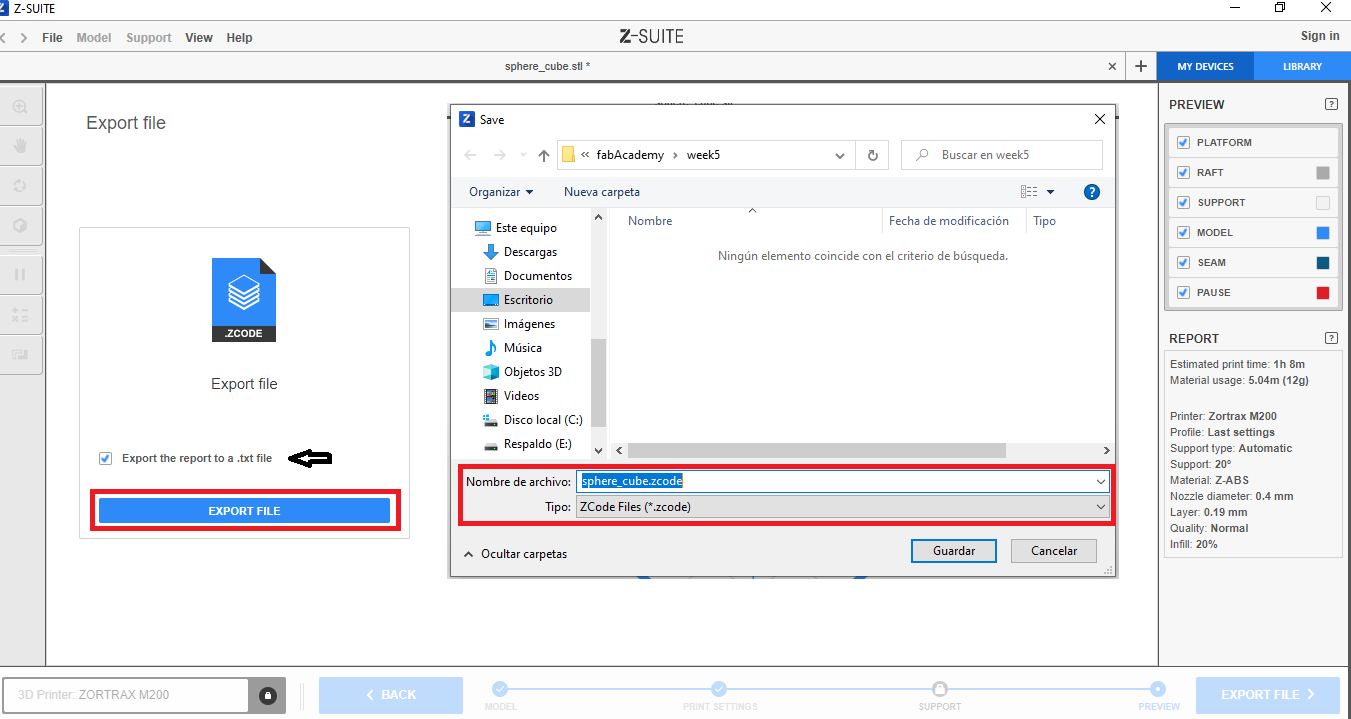
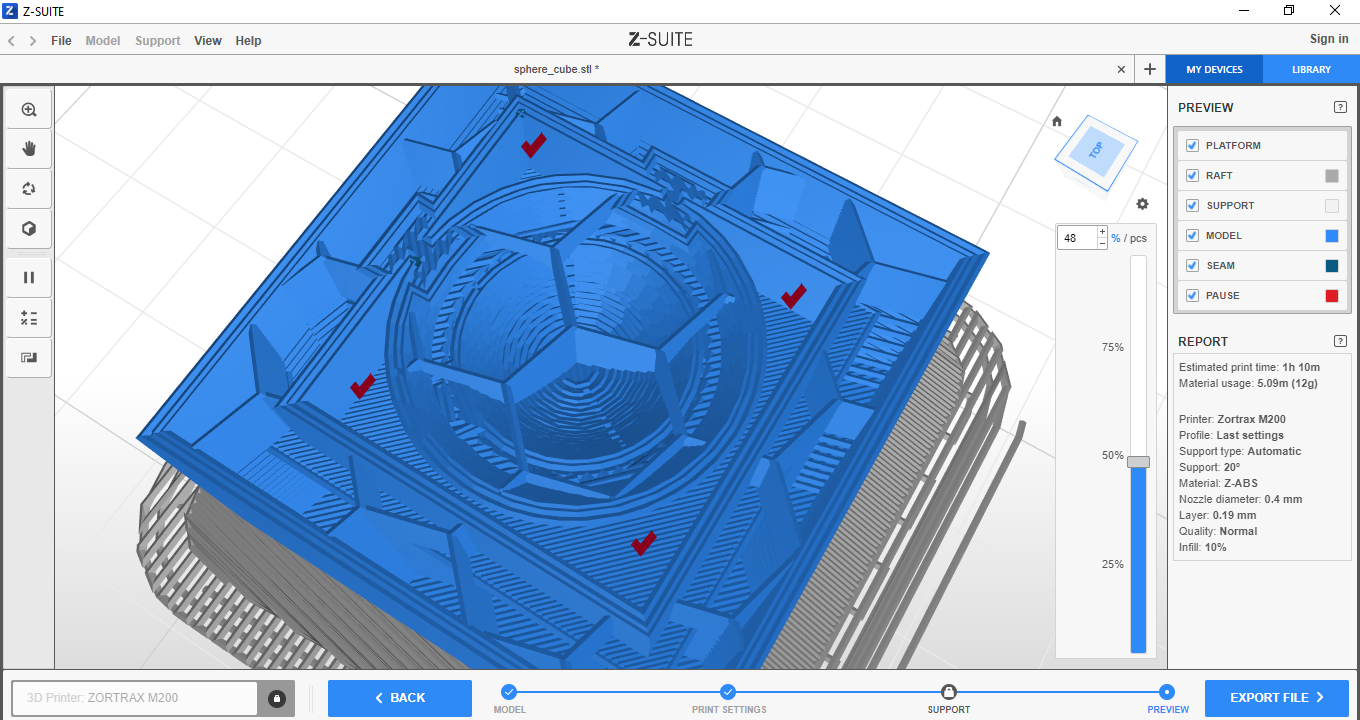
That file is now copied to a memory to be later inserted into the printer to select the file and start printing.
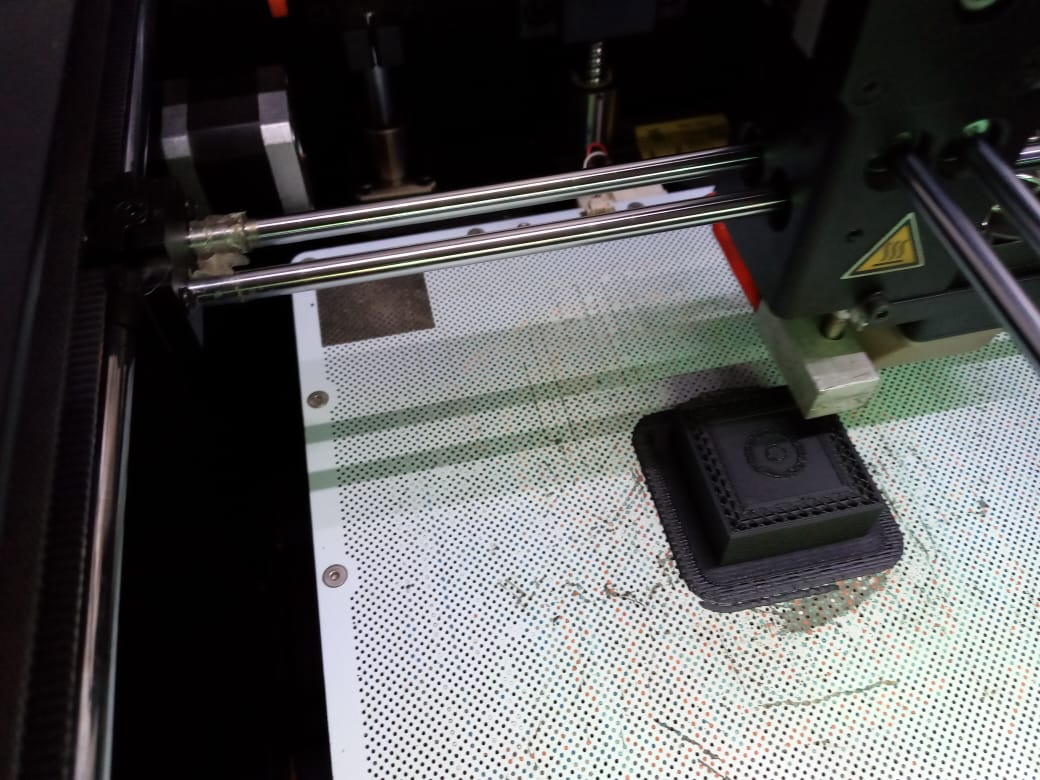
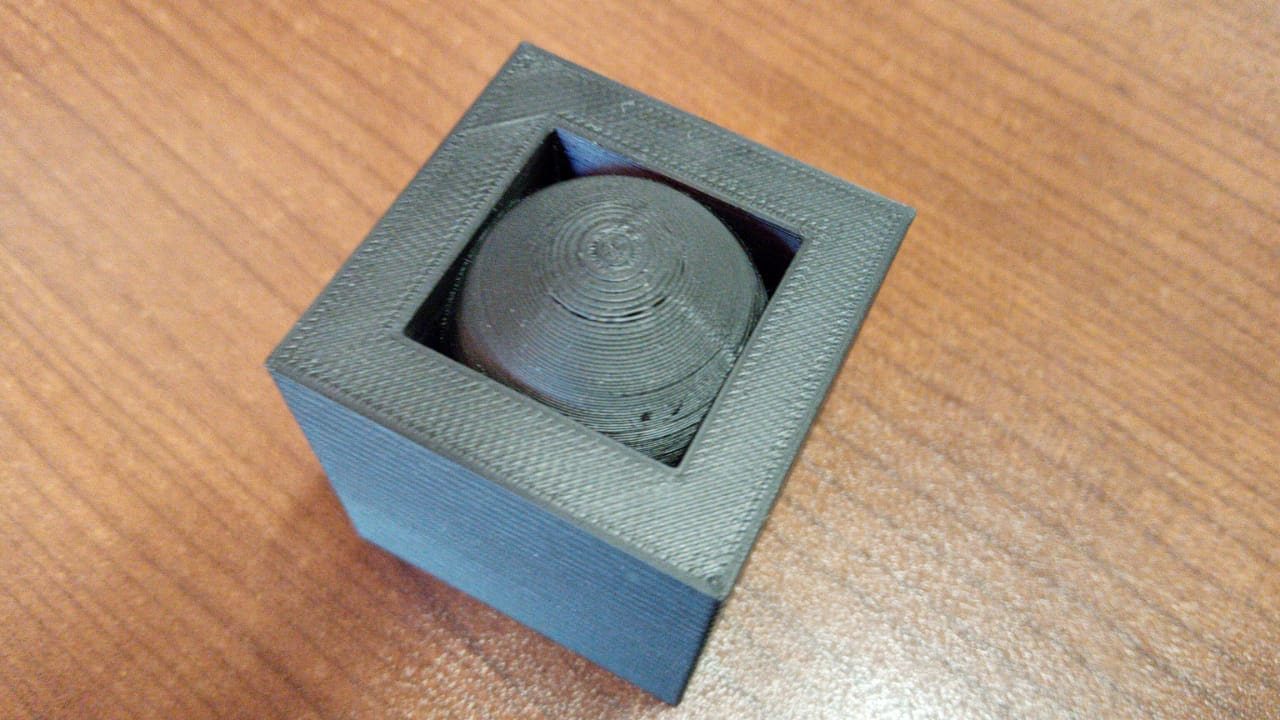
As the sphere is not visible, I am going to redesign the cube but now without walls, only the outline so that the interior can be appreciated.
Extrude the first face
Extrude the second face
Extrude the third face
I add the sphere and placed it inside the cube (press the letter m), then I selected the 2 sketches and with the combine tool I integrate them as an object.
Now I'm going to save the object in STL format, to print it.
Open the z-suite software again and carry out the steps previously described to send the cube to print again.
The print is ready, same design same size, but the cube is now open.
- 3D scan an object (and optionally print it)
To start the 3d scan it is first necessary to download the skanet software To do the 3d scan use the kinect for this reason the software is downloaded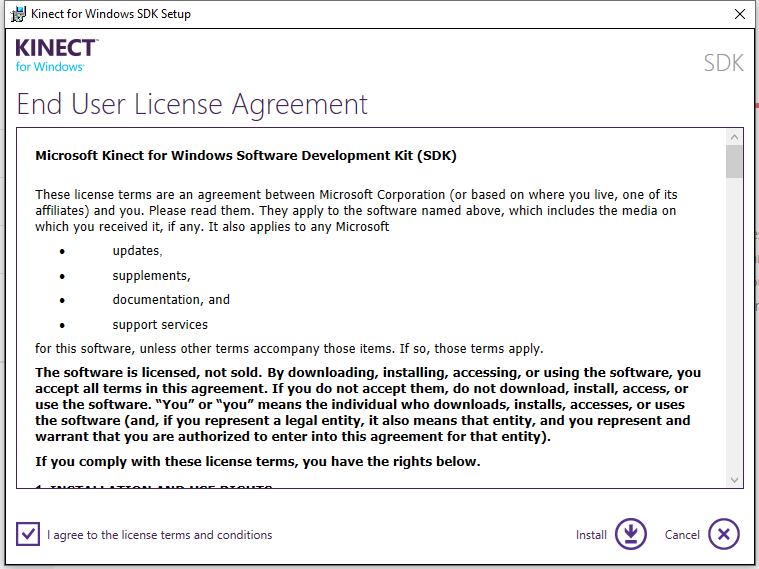
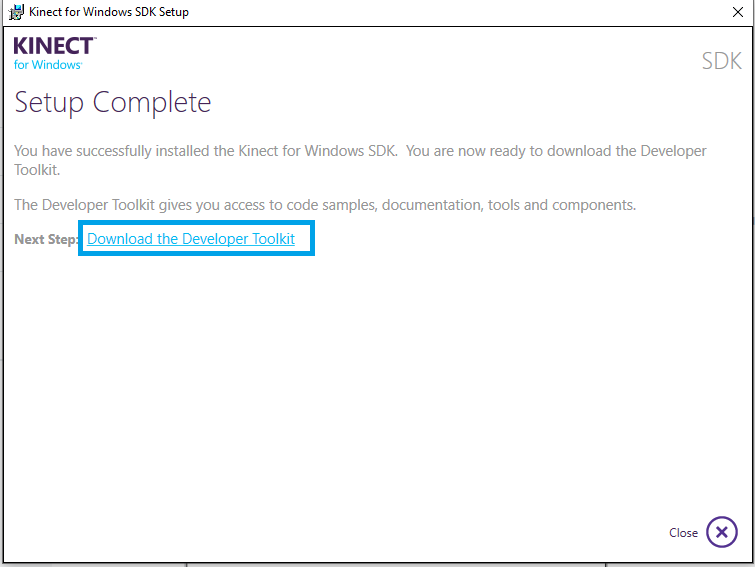
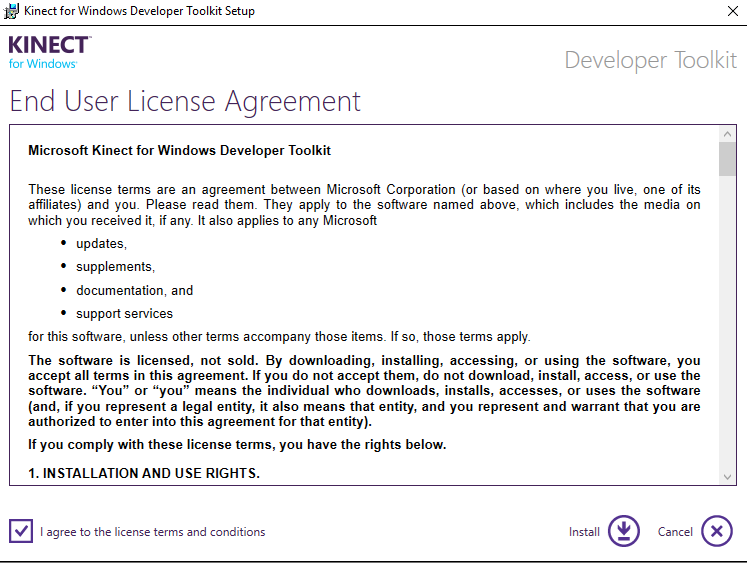
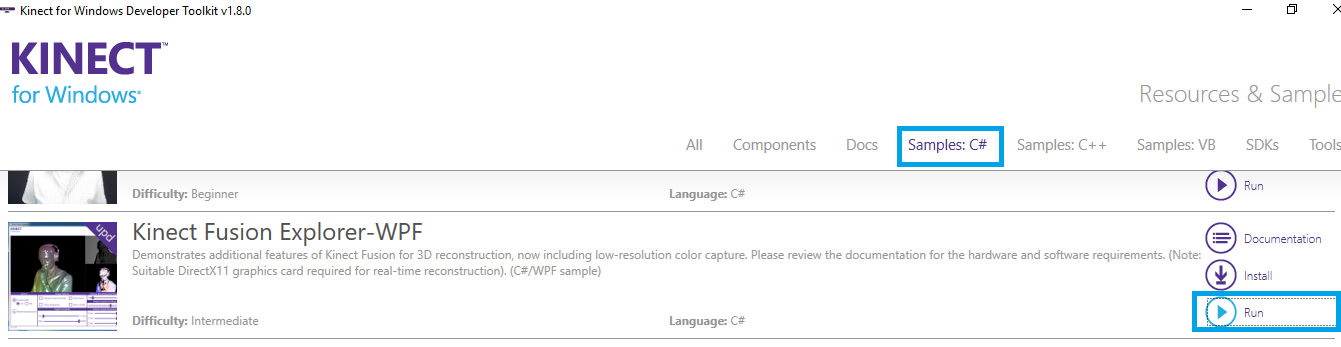
Select sampleC # and in kinect fusion Explorer-WPF click on run, this action opens a window where the image that is being captured by the kicnet appears. Select sampleC # and in kinect fusion Explorer-WPF click on run, this action opens a window where the image that is being captured by the kicnet appears. With this a test is performed to see if it detects the kicnet.
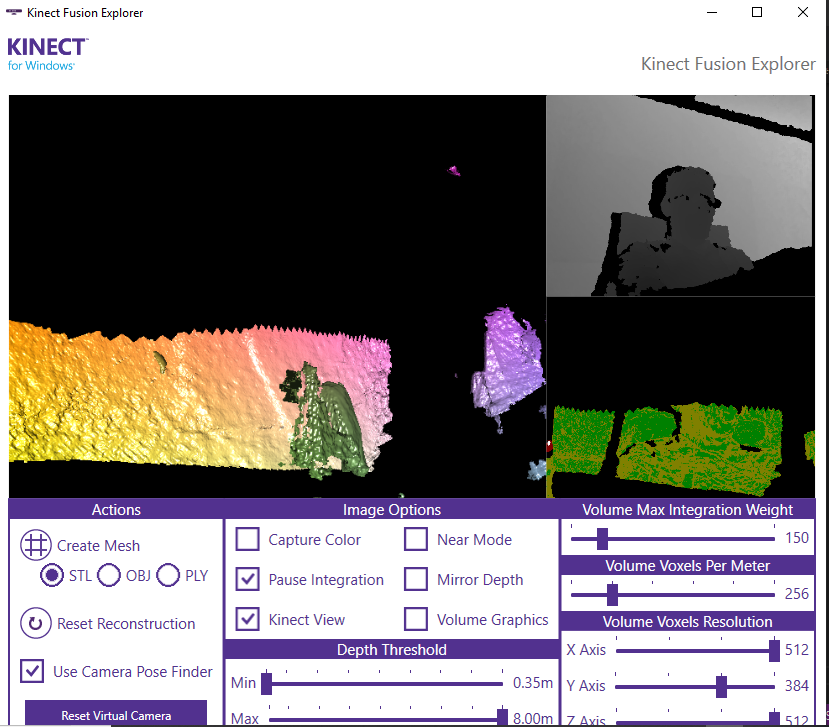
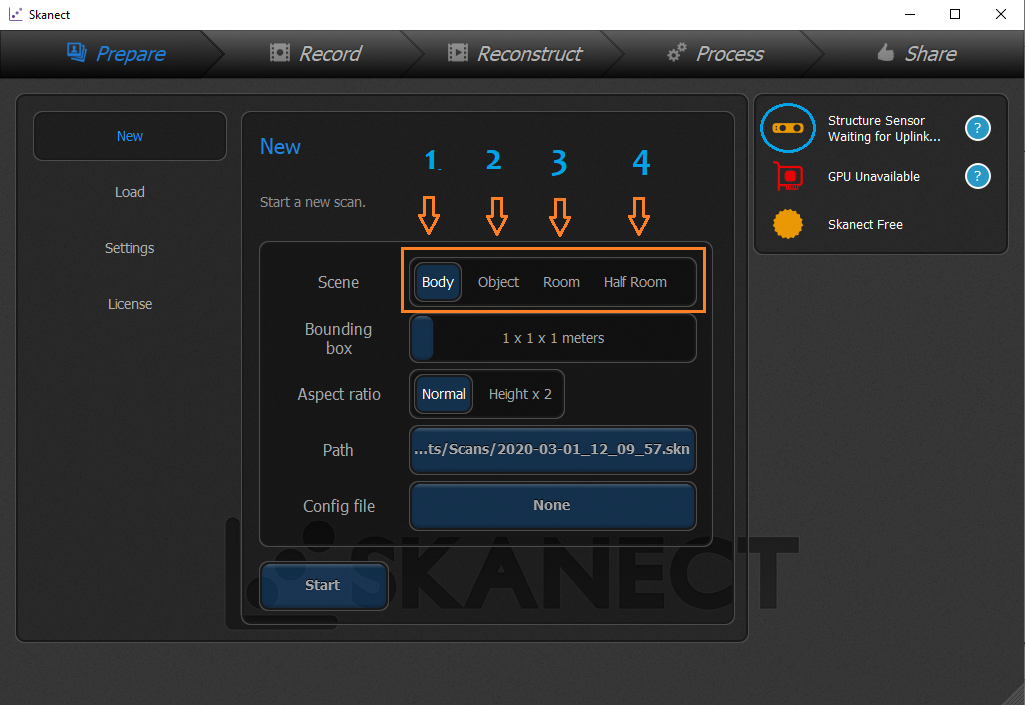
Once the sensor is recognized, the image capture must be started (record), this step requires a lot of patience, the first scan was done with the help of two people, the software operator and the one that moved around me With the kinect in his hands.
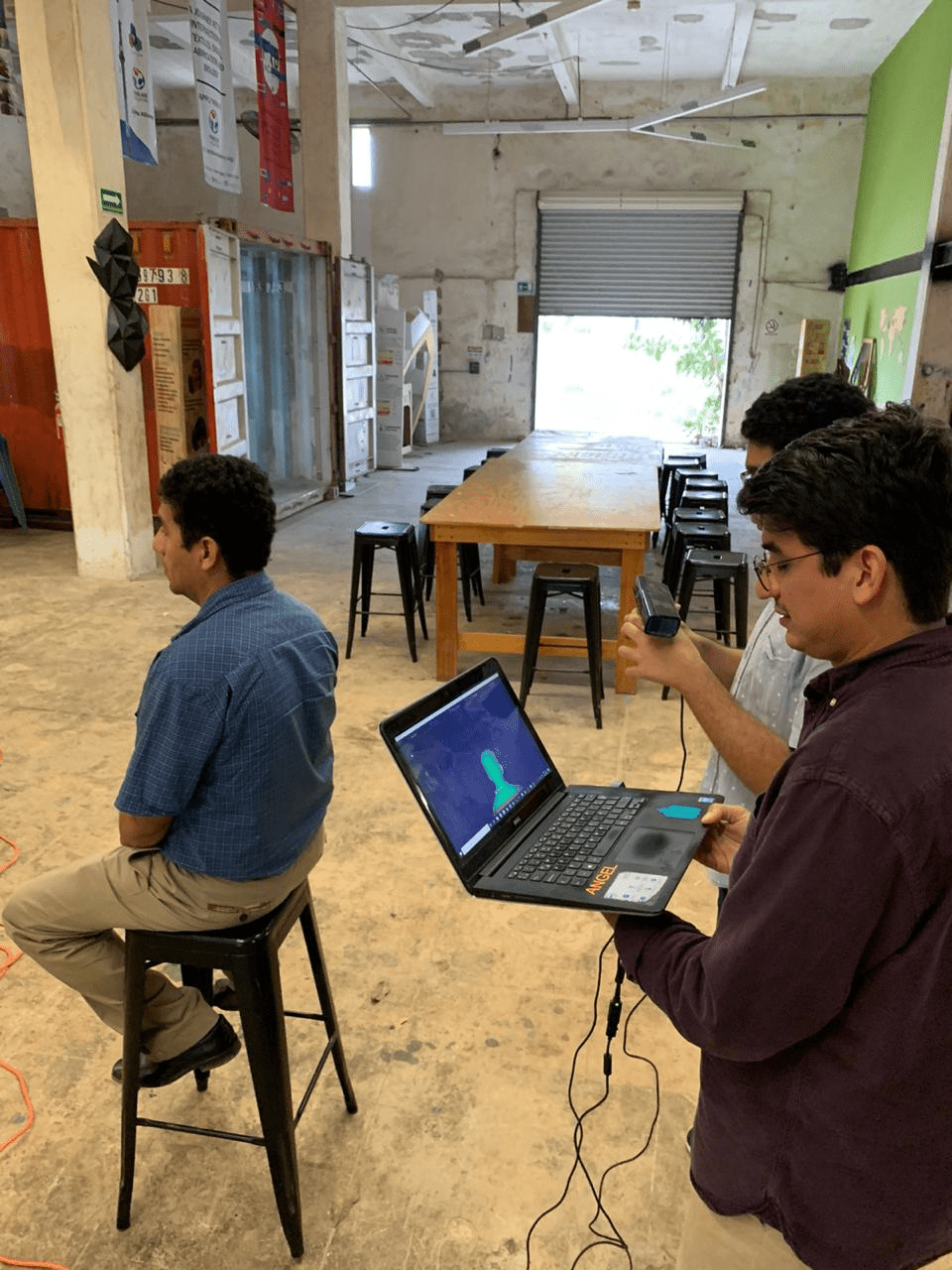
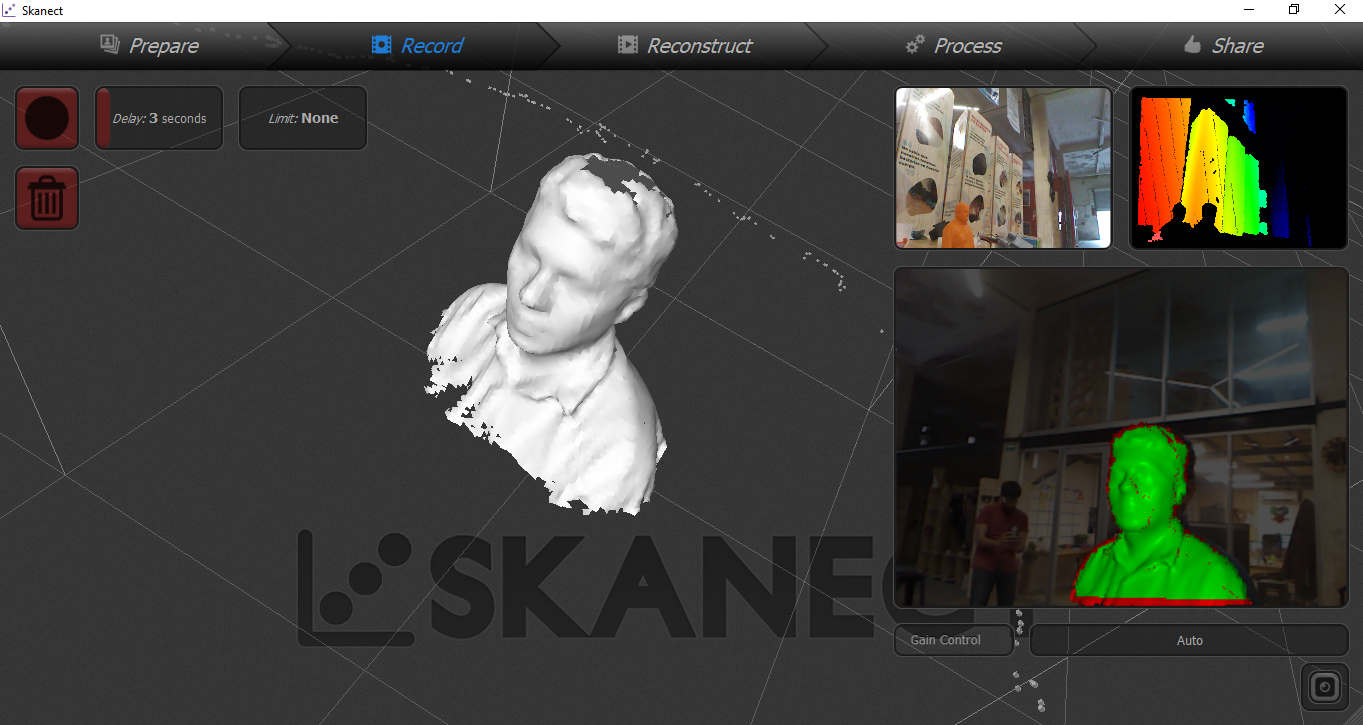
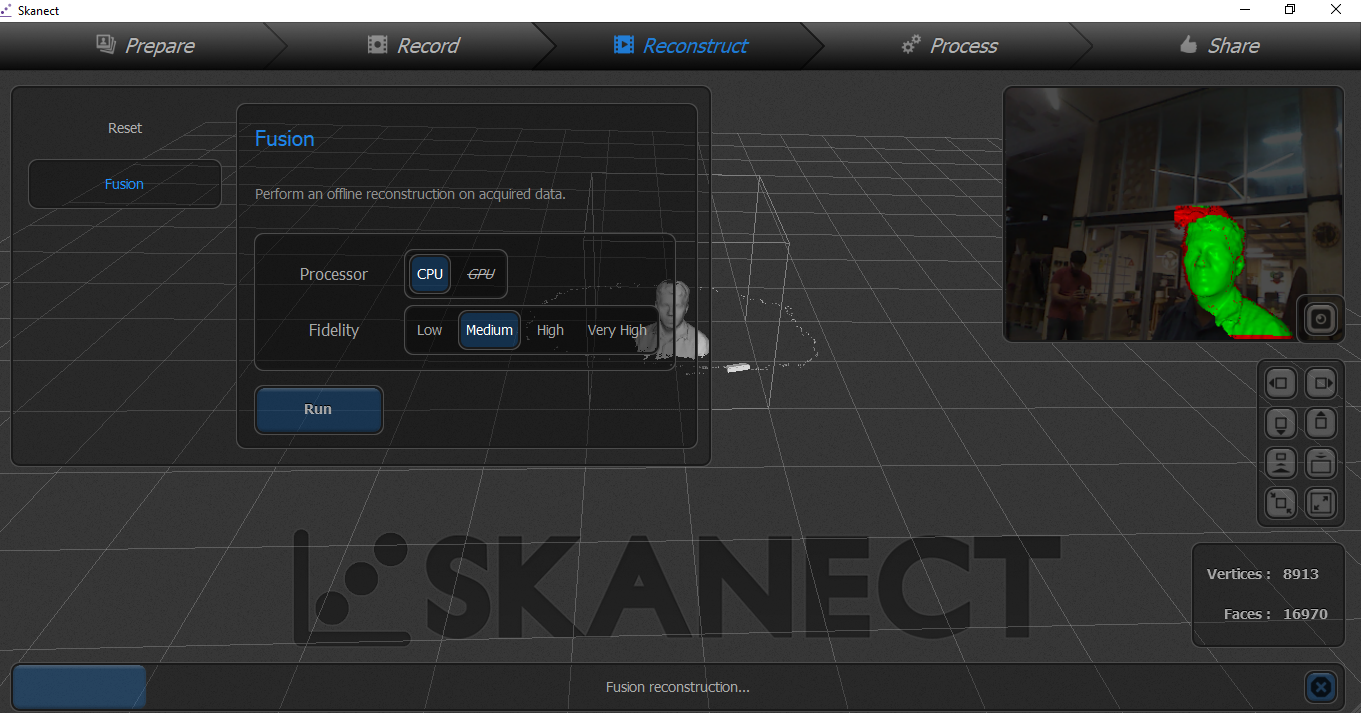
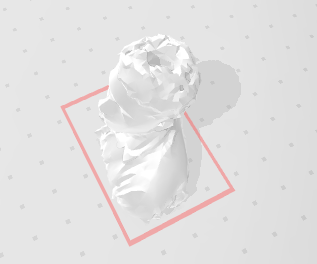
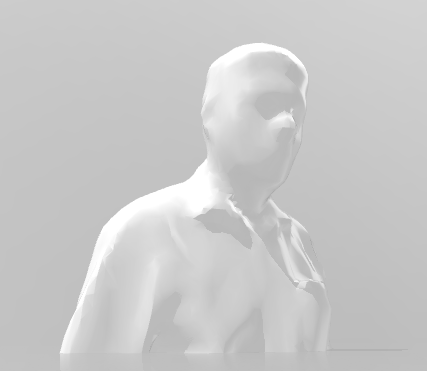
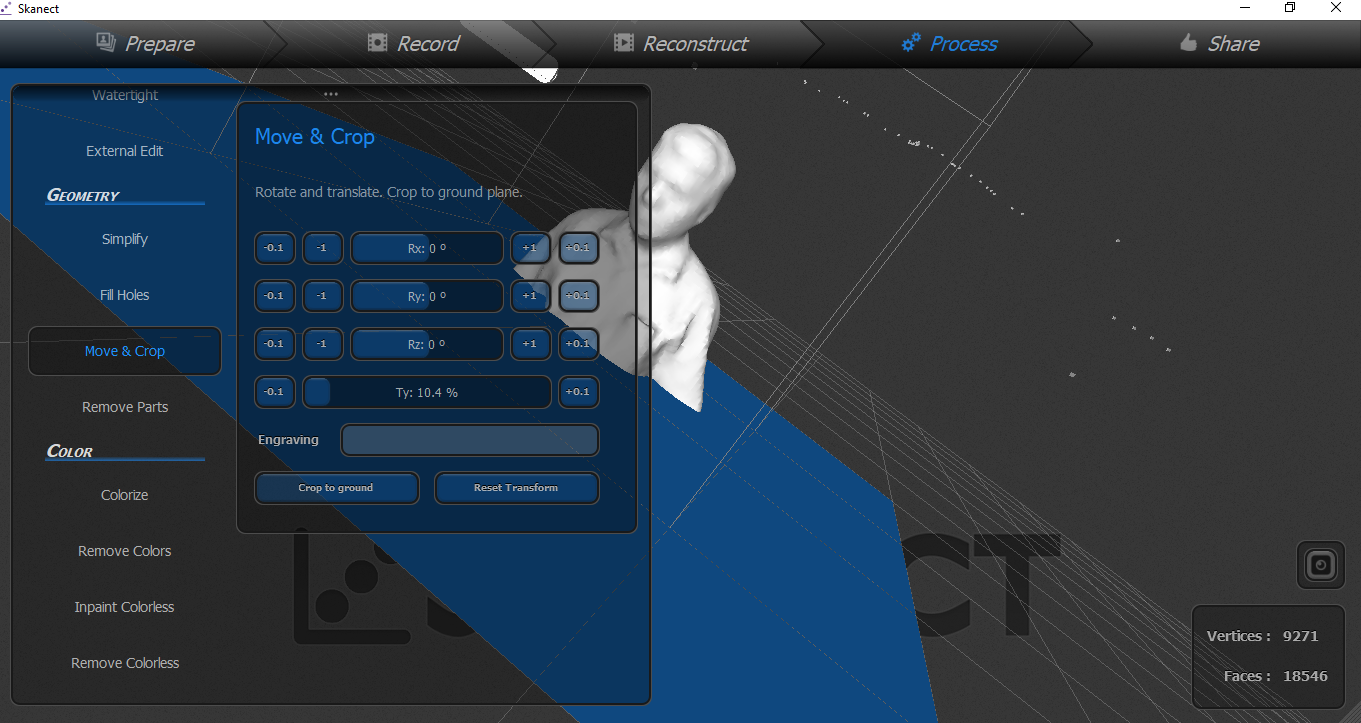
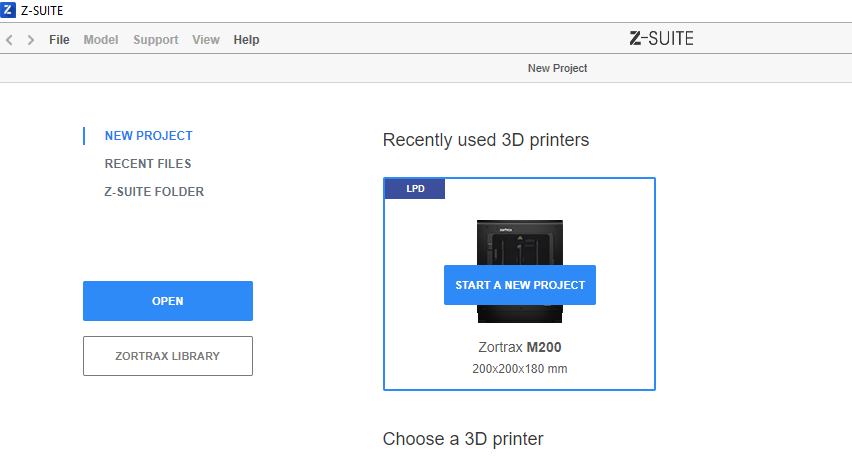
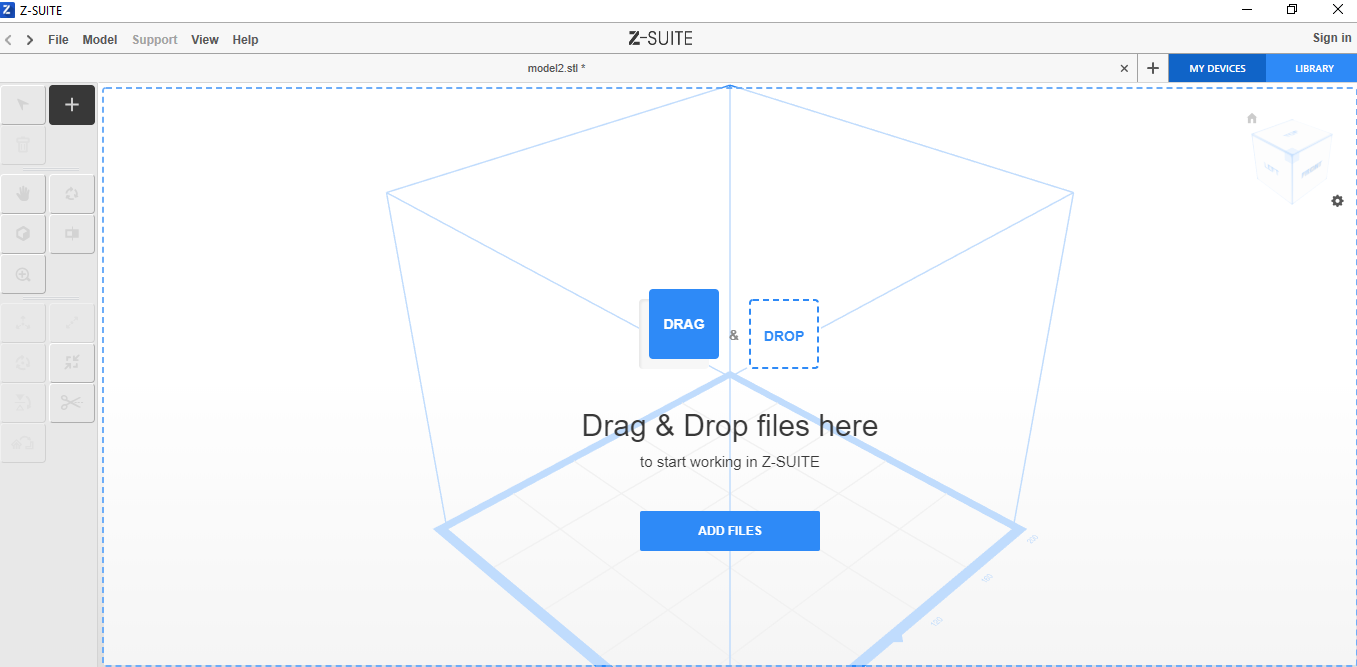
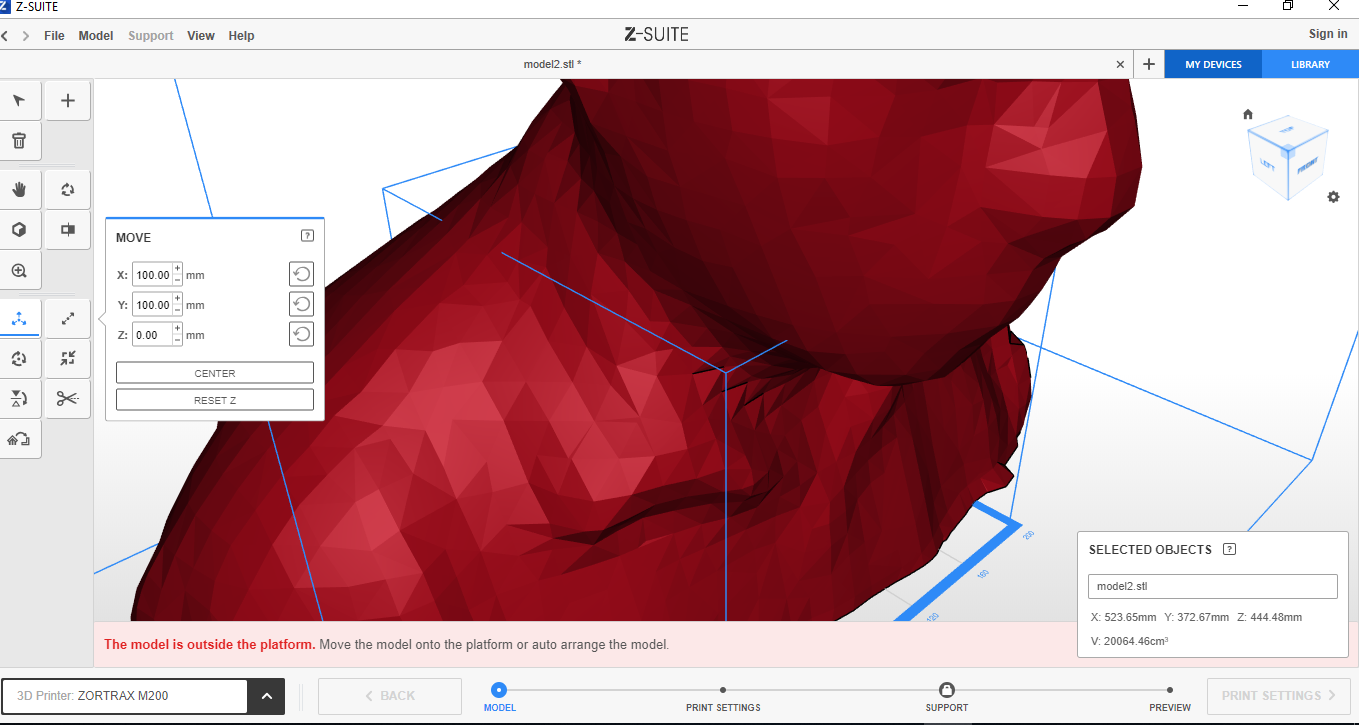
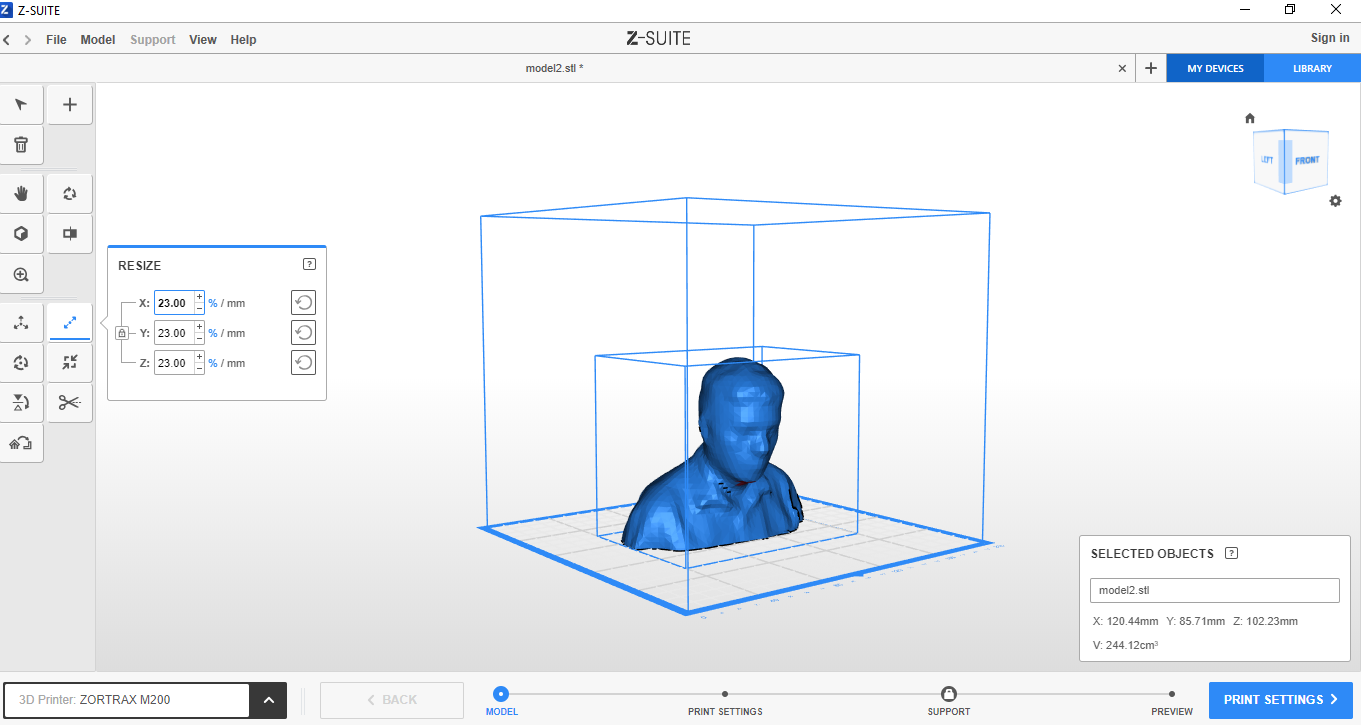
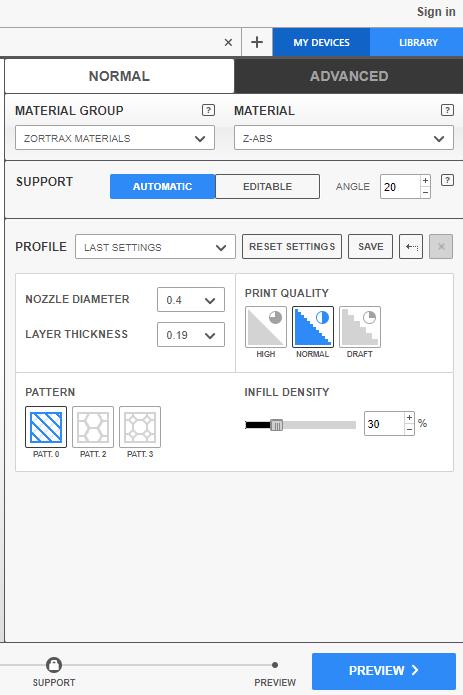
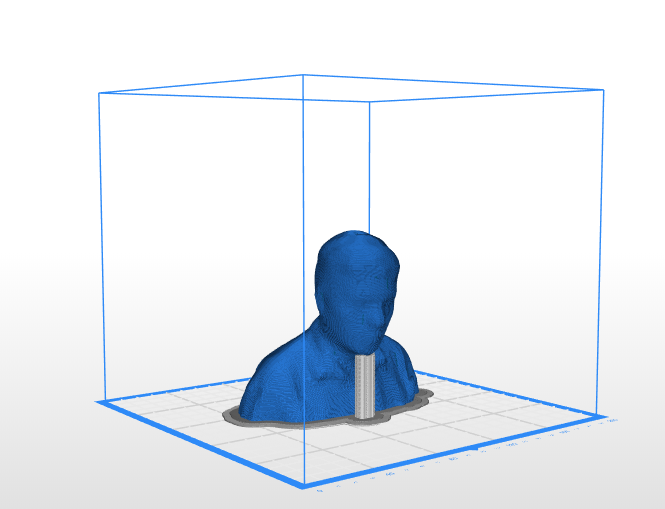
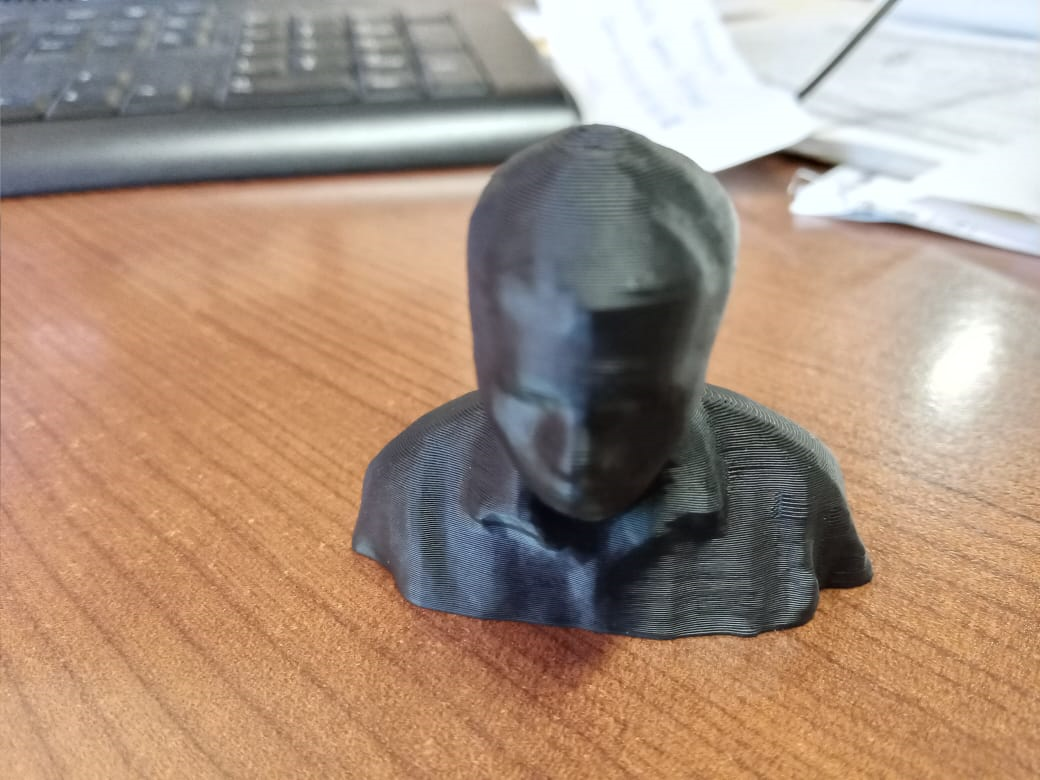