12. Molding and casting
This week we searched 3D milling for mold creation and casting.
Documentation
Frame print
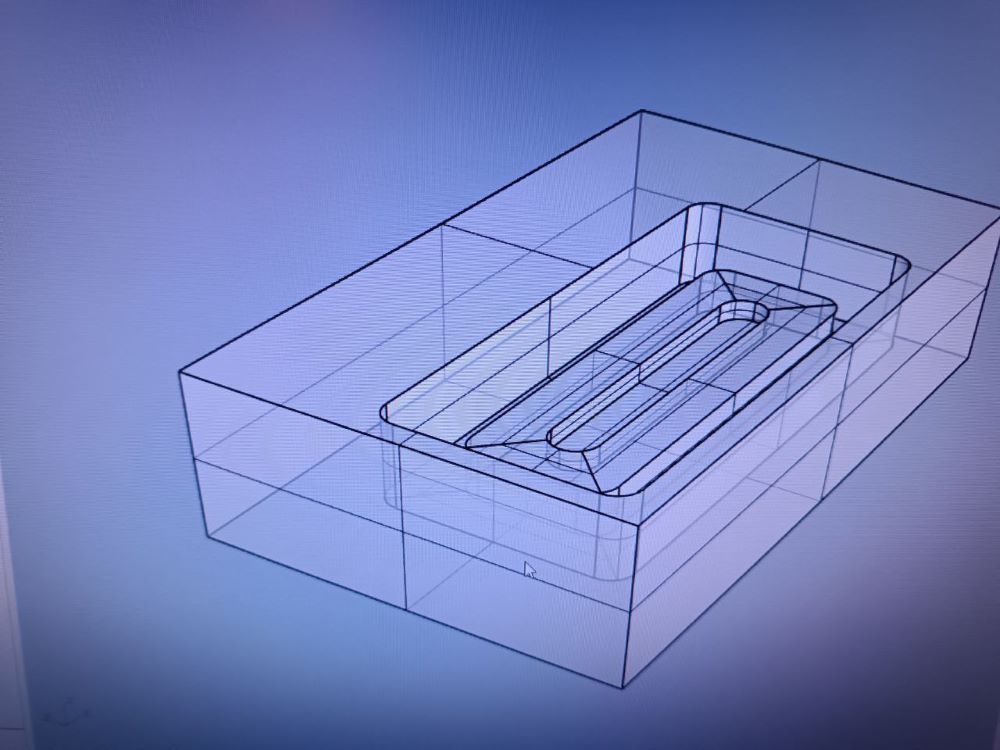
- Created model in Rhino. Used Modela Player 4 soft for tool path creation.
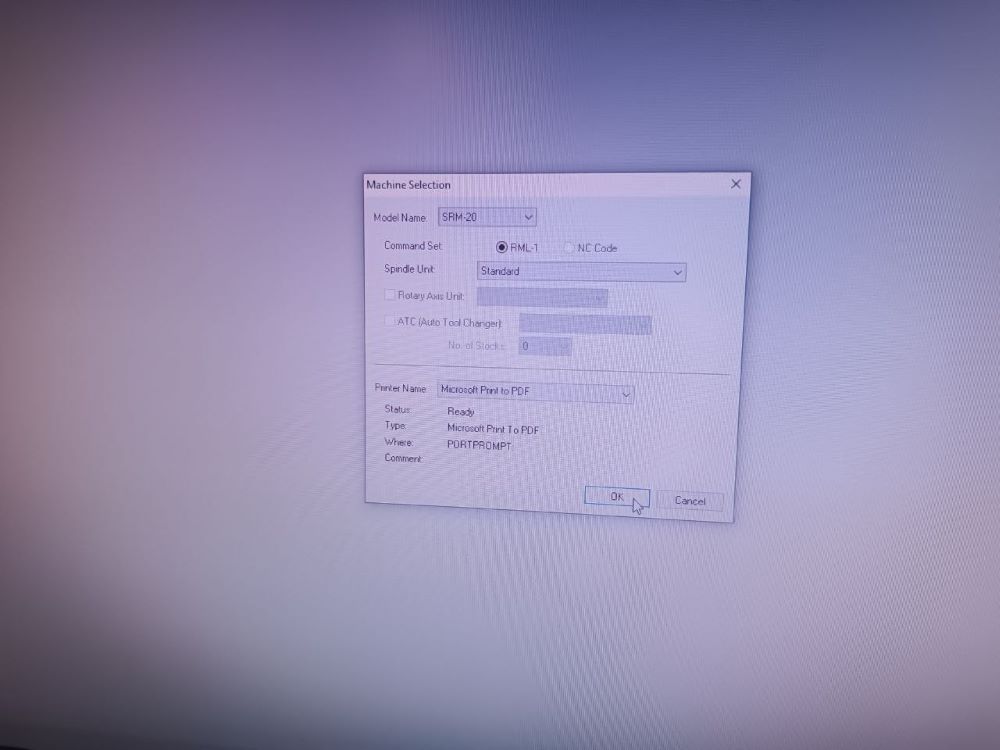
- Choosed machine.
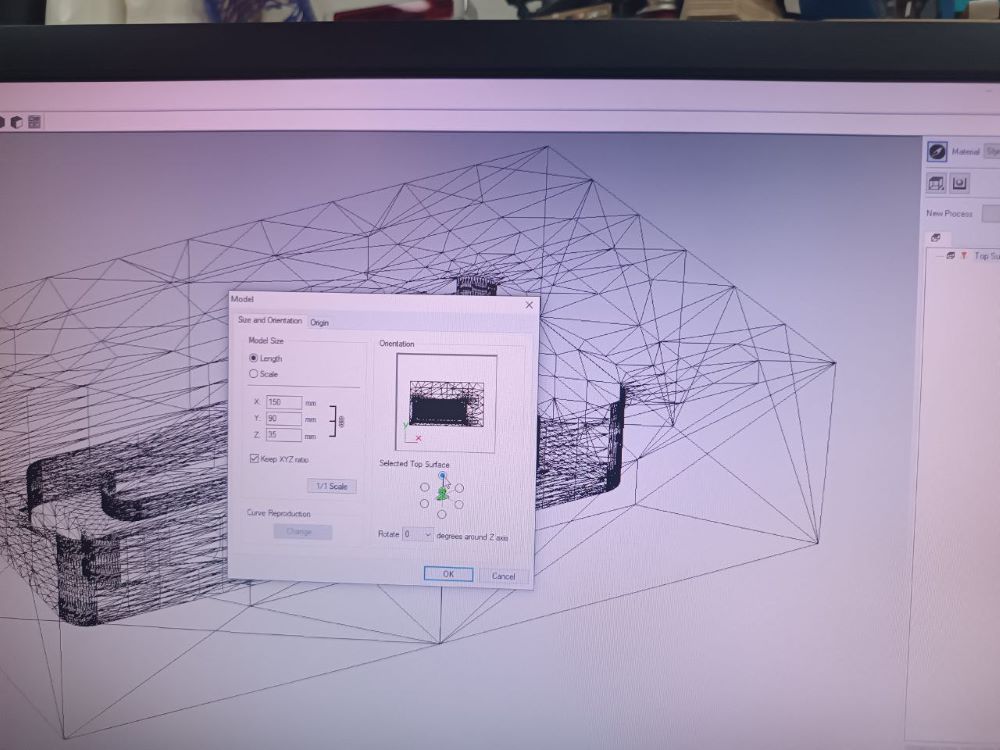
- Defined orientation and material size.
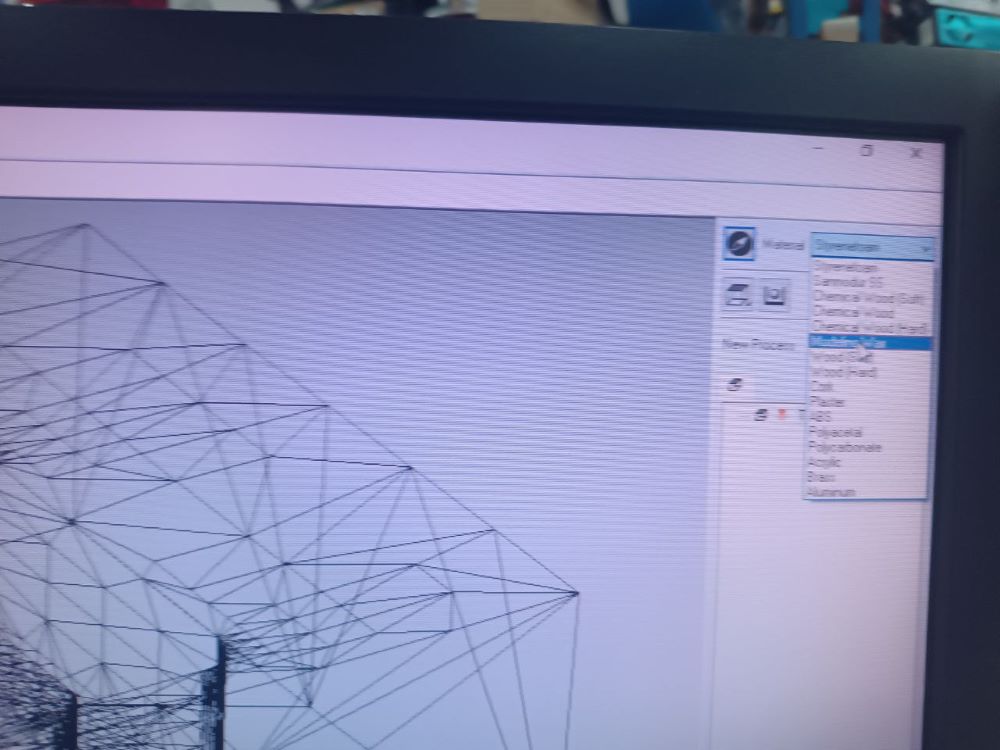
- Defined mateial (modeling wax).
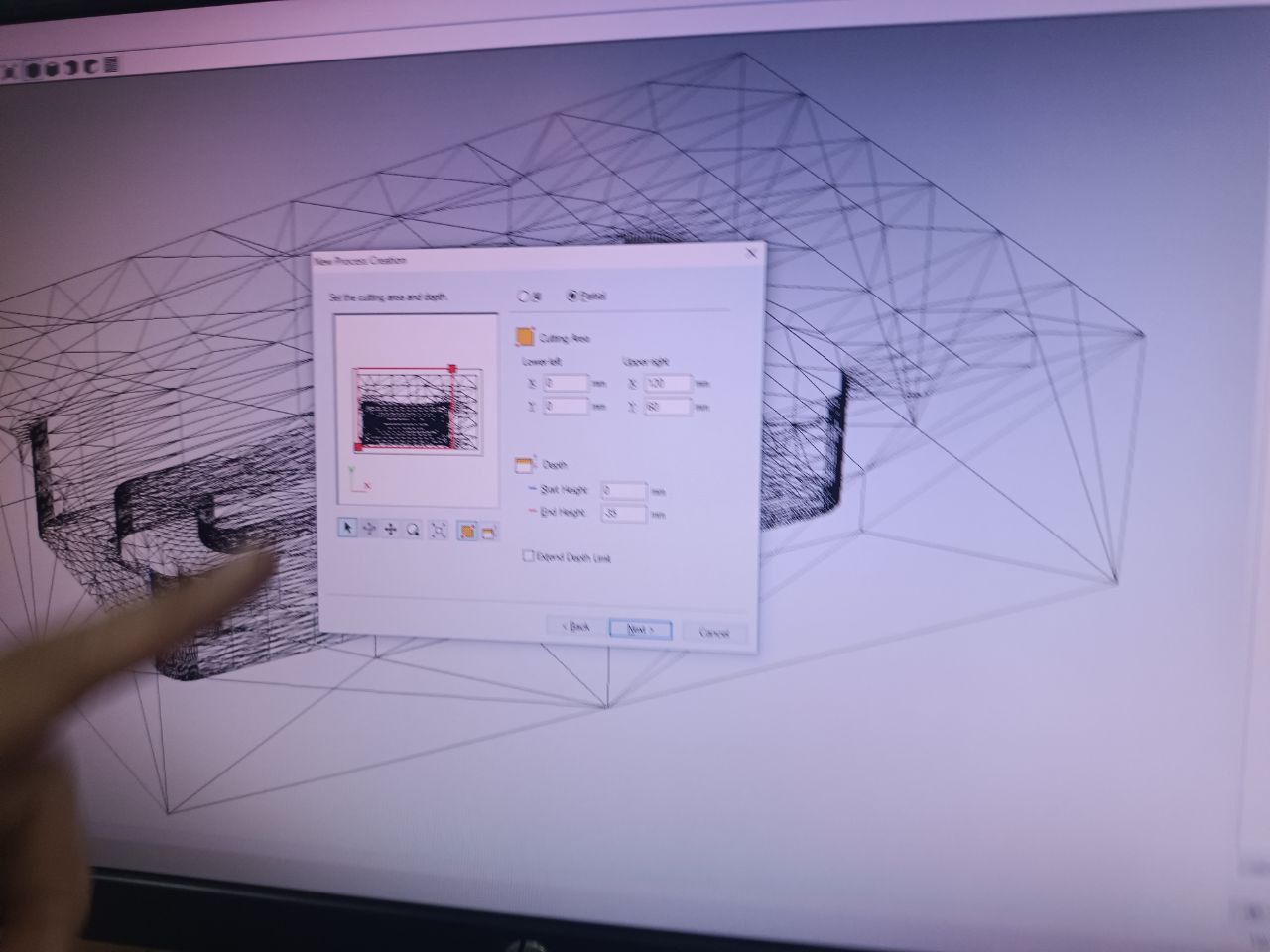
- Defined cutting area (if not, it will prosess all model area) to save time.
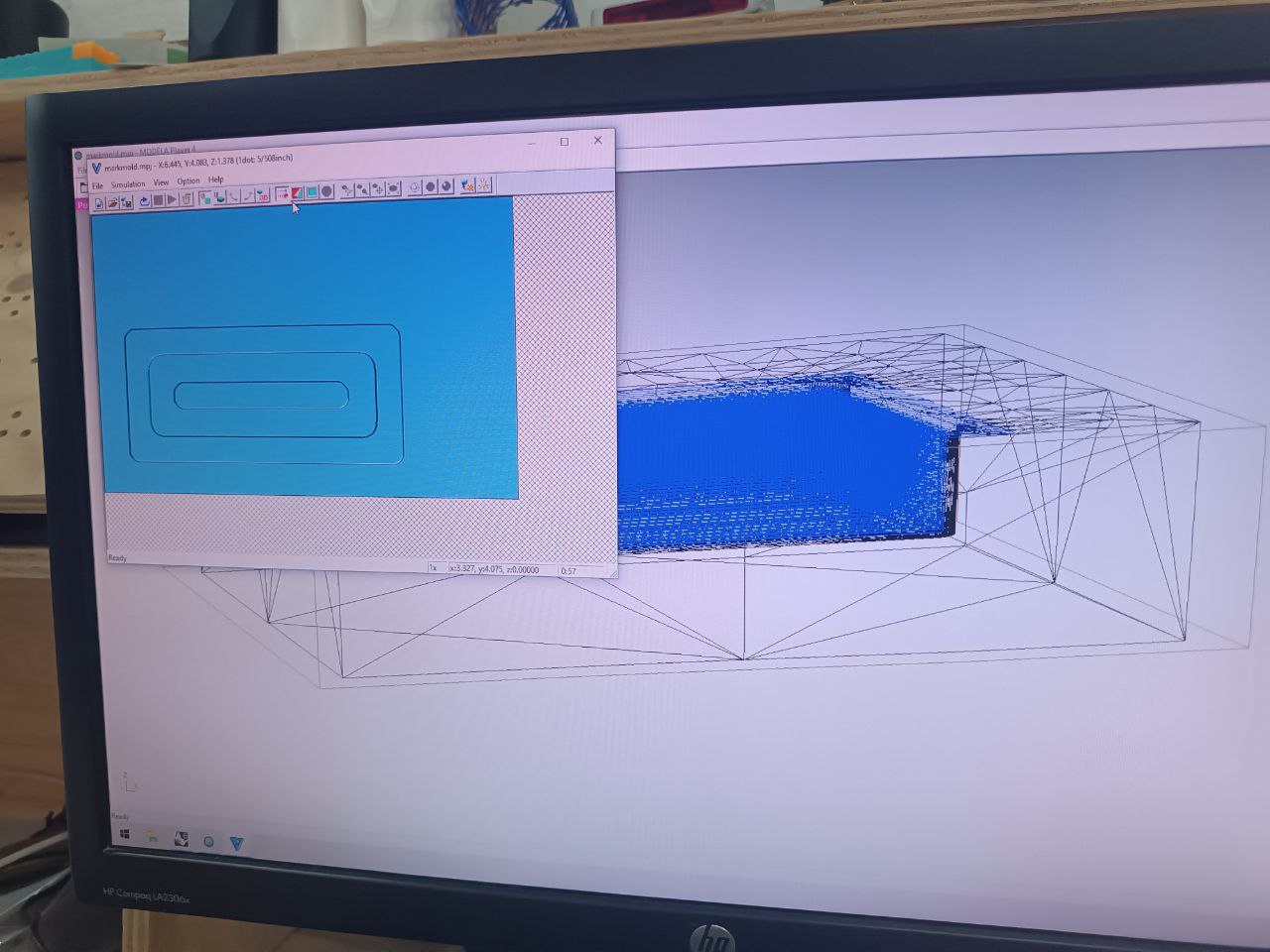
- Checked simulation.
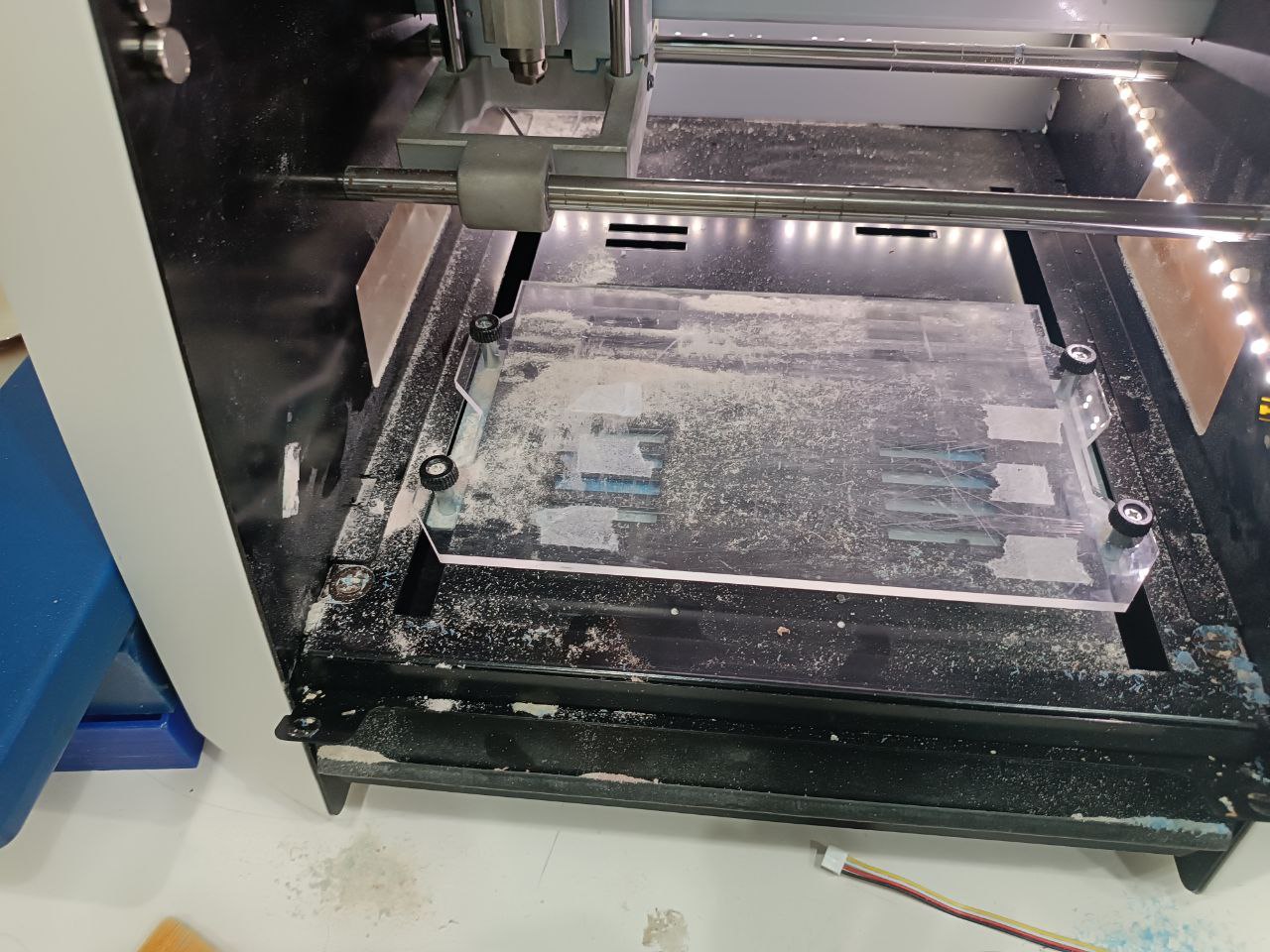
- Changed base (one for boards cut is too thick).
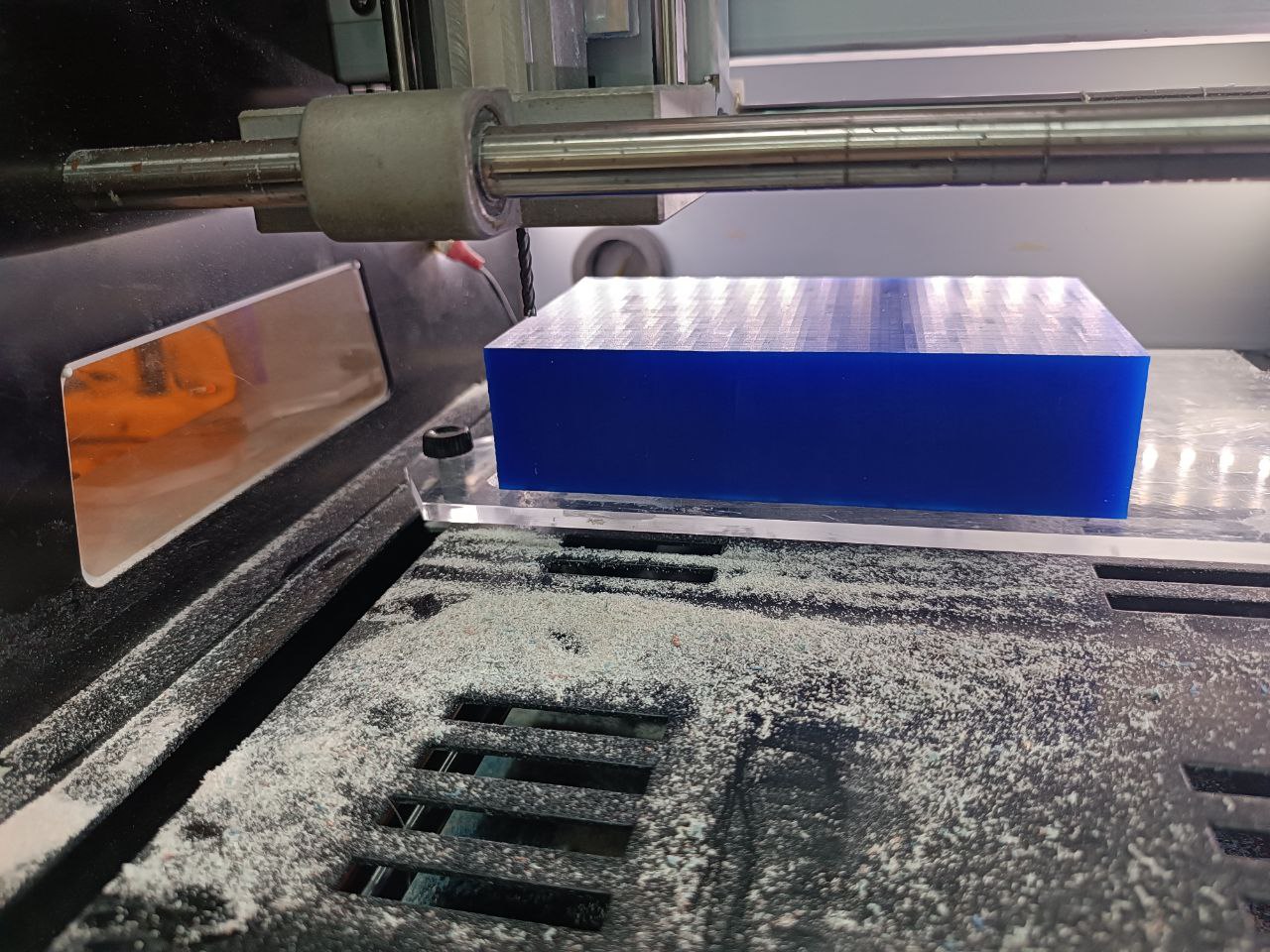
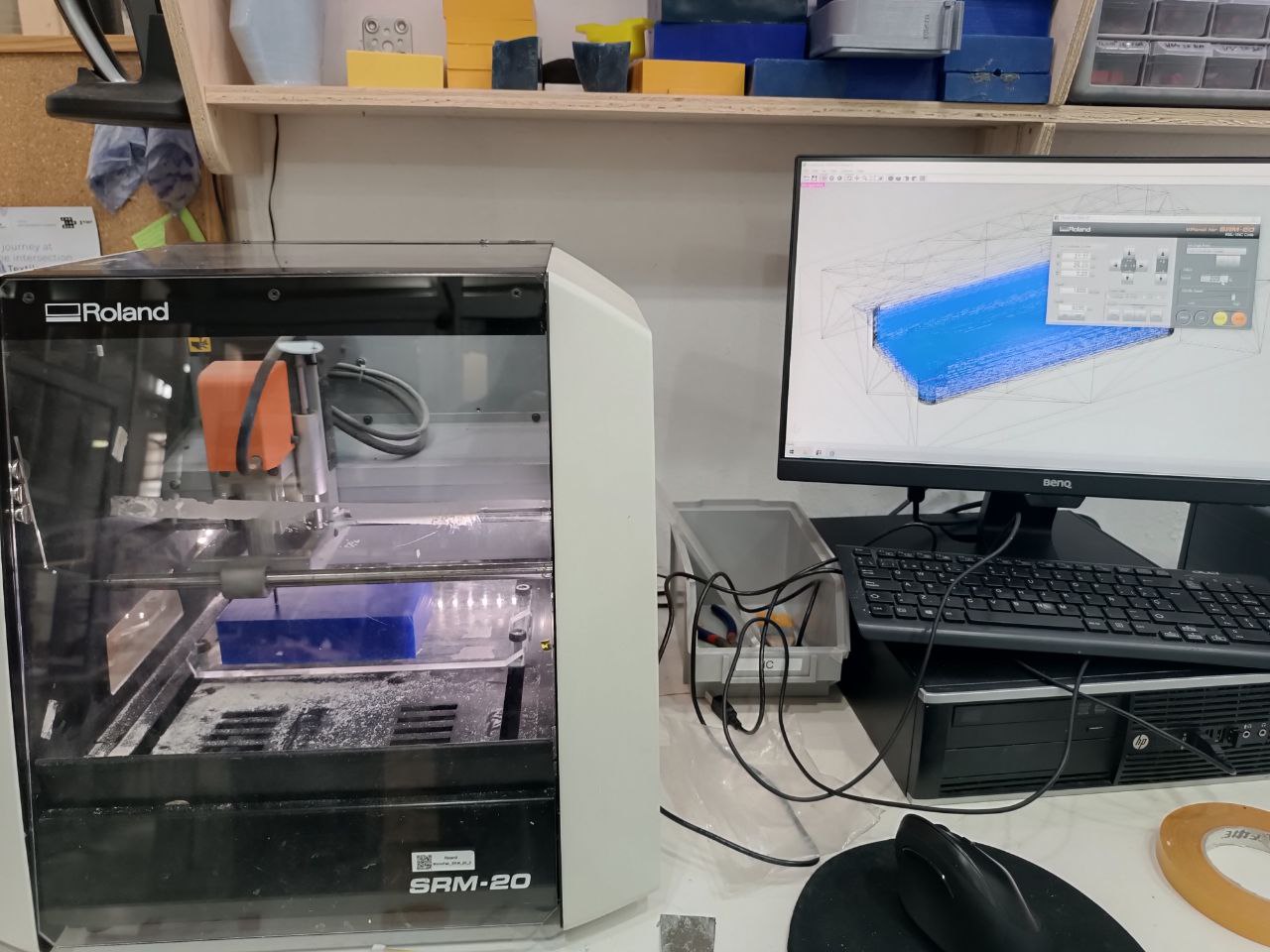
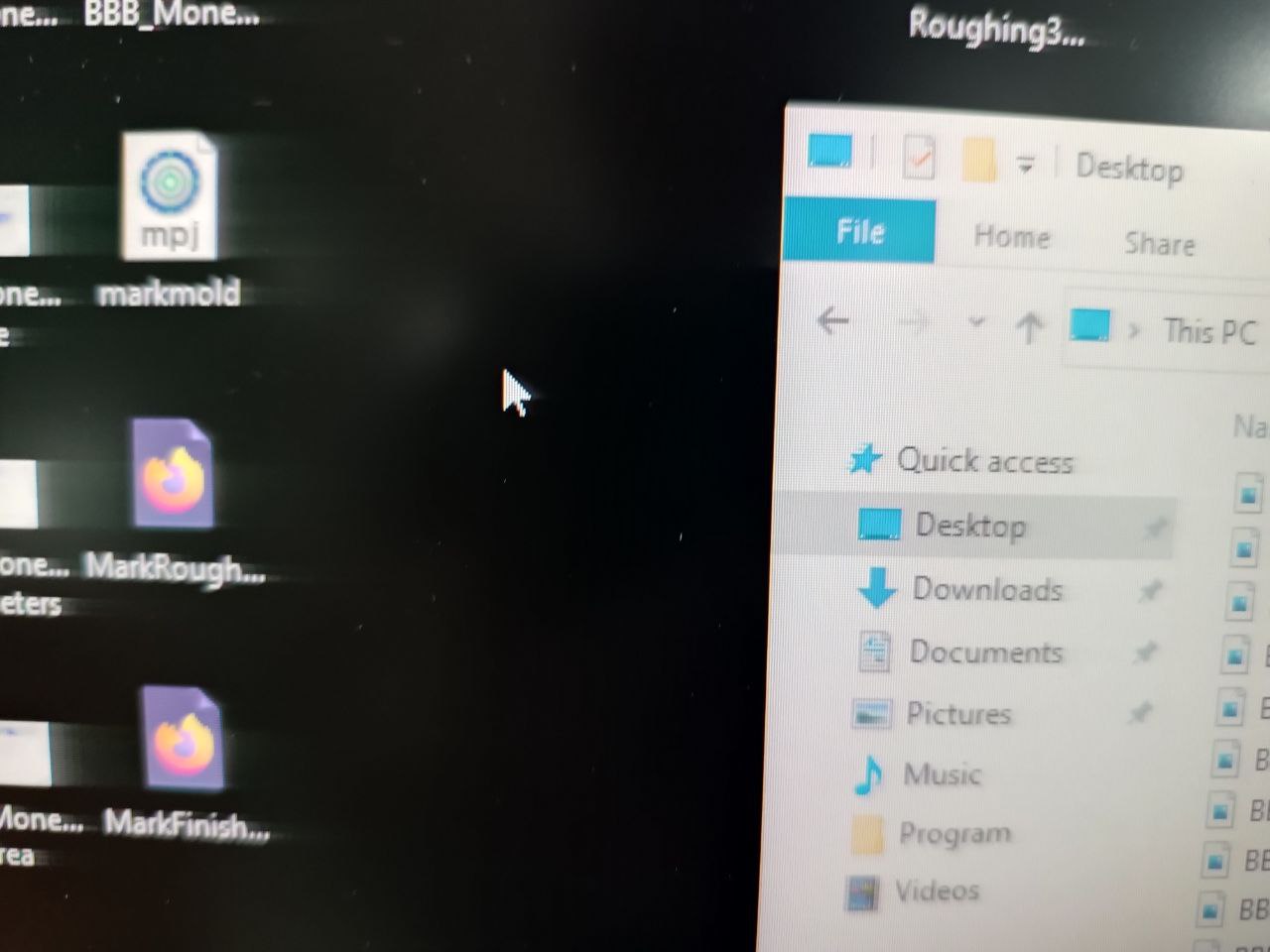
- Defined XY, Z origin.
- For some reason machine did not cut, in result the reason was, that I did not crerated PRN file (type of gcode) and tried import file of Modela Player 4.
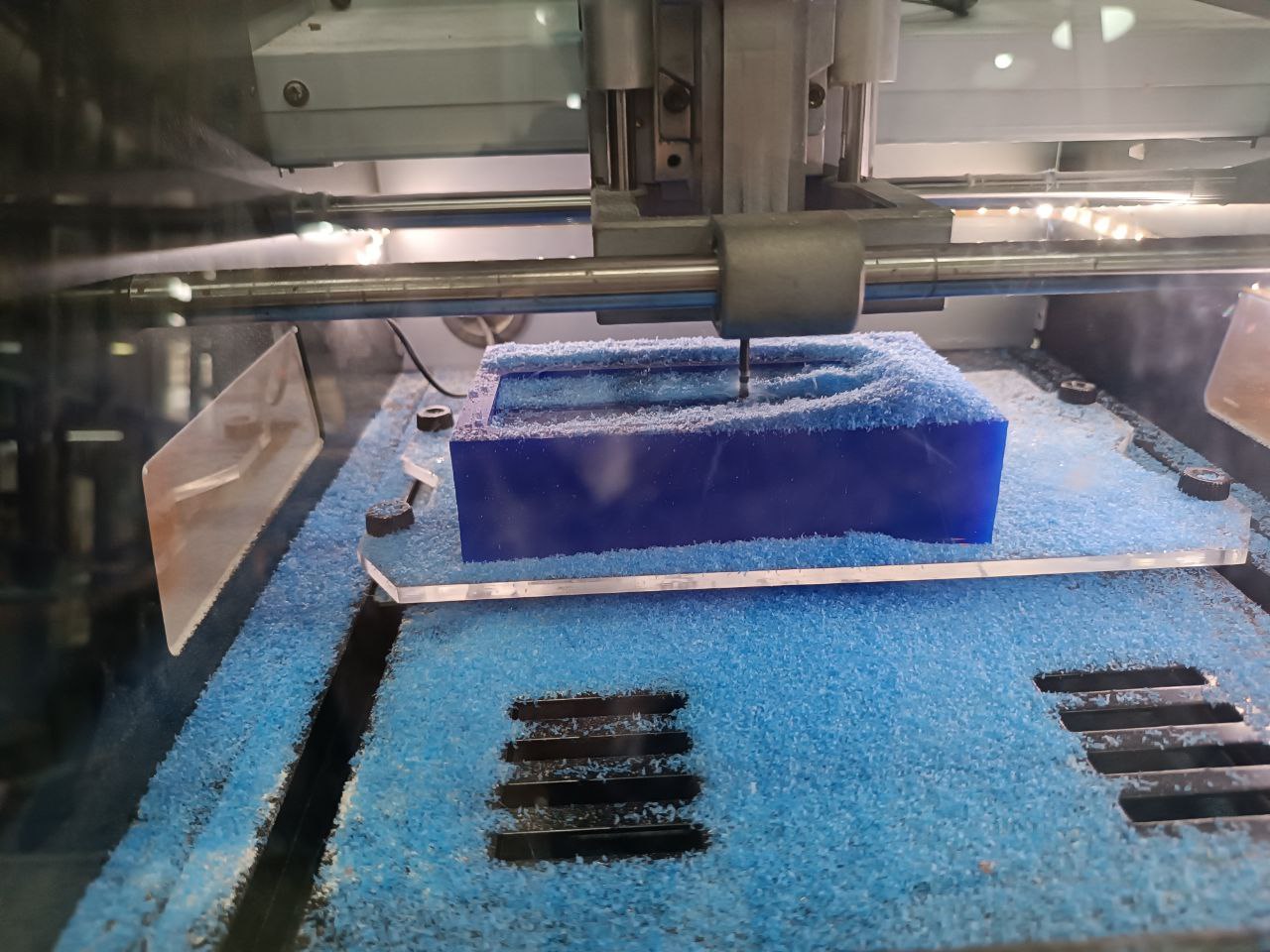
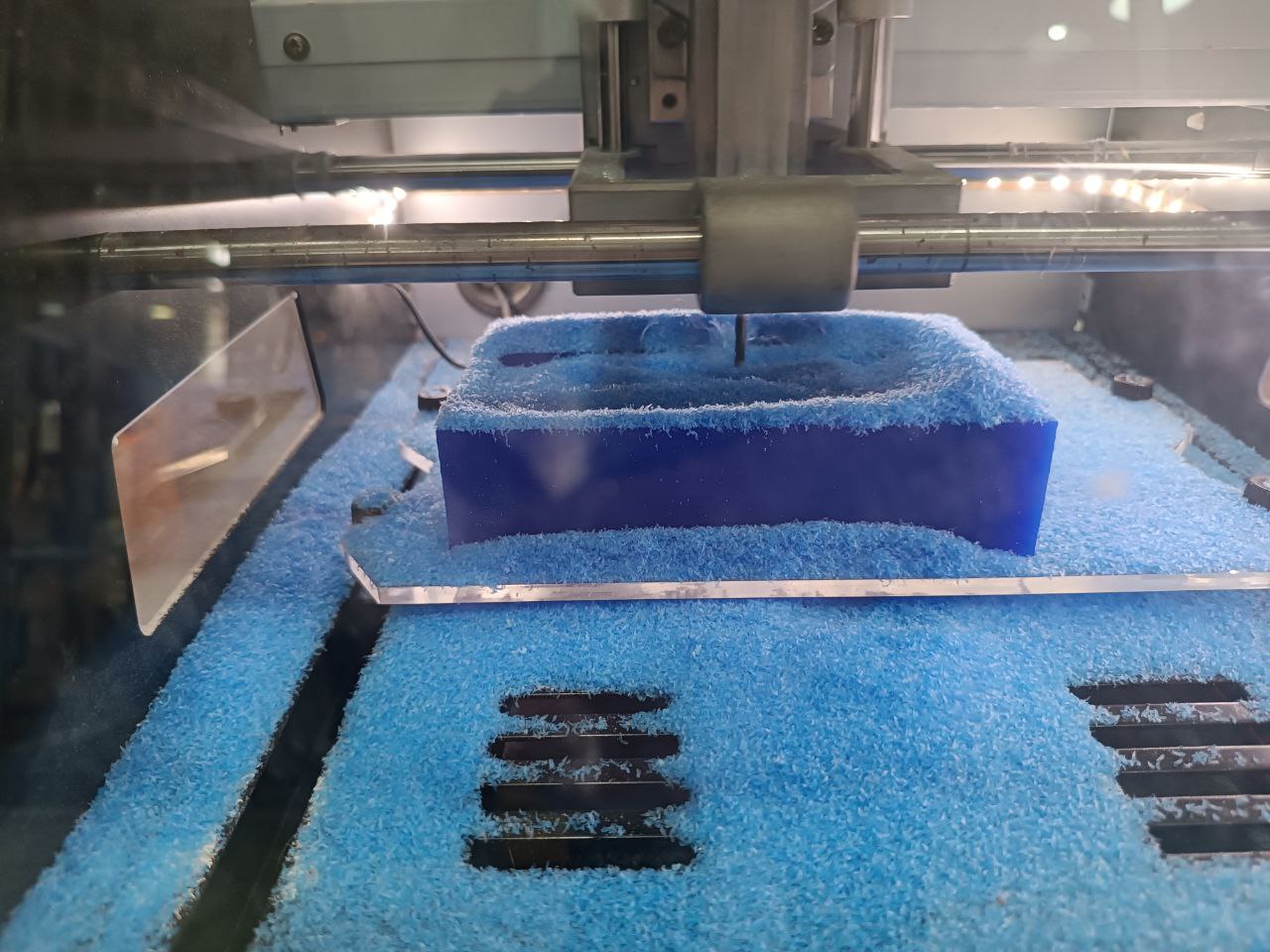
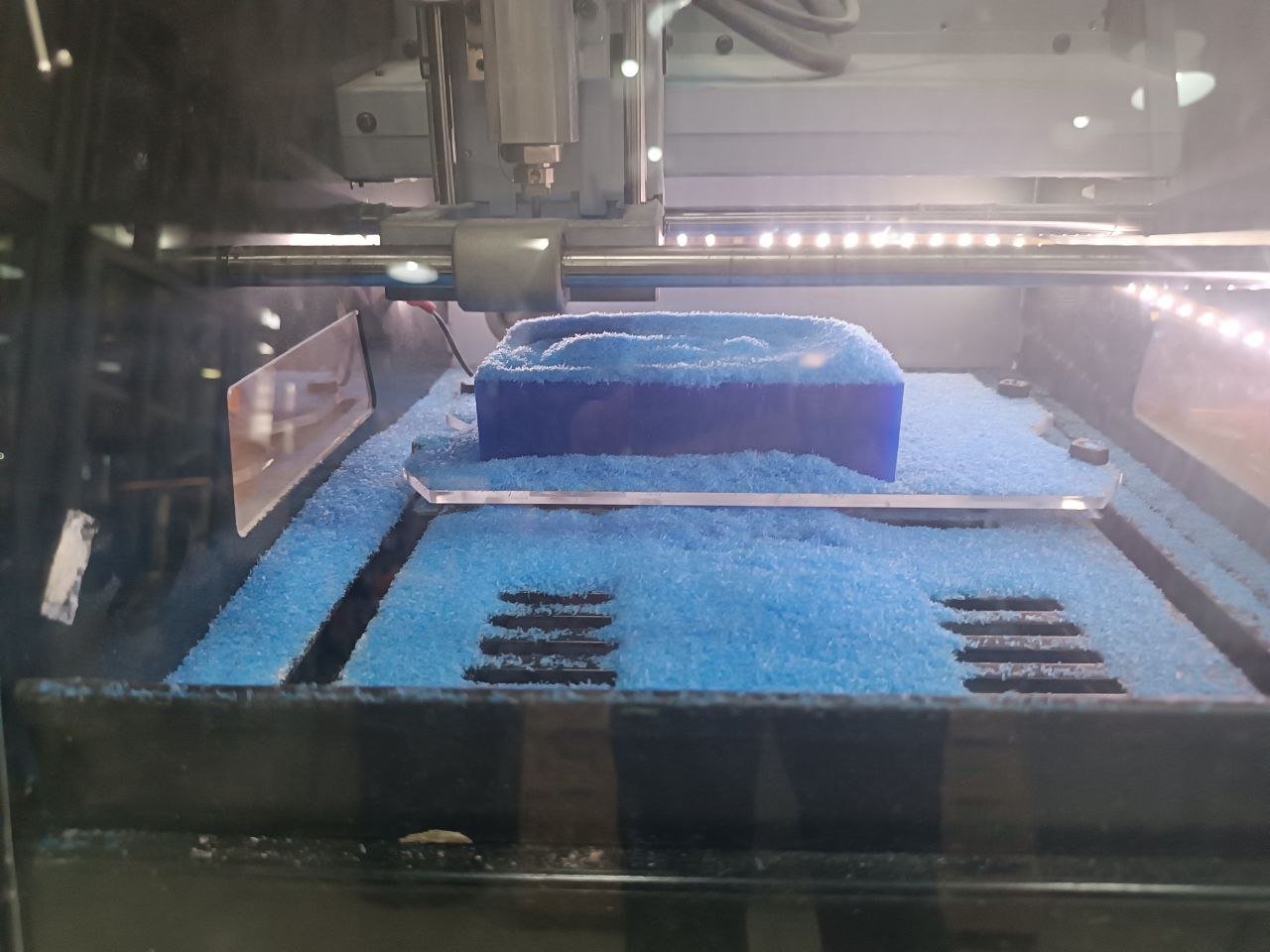
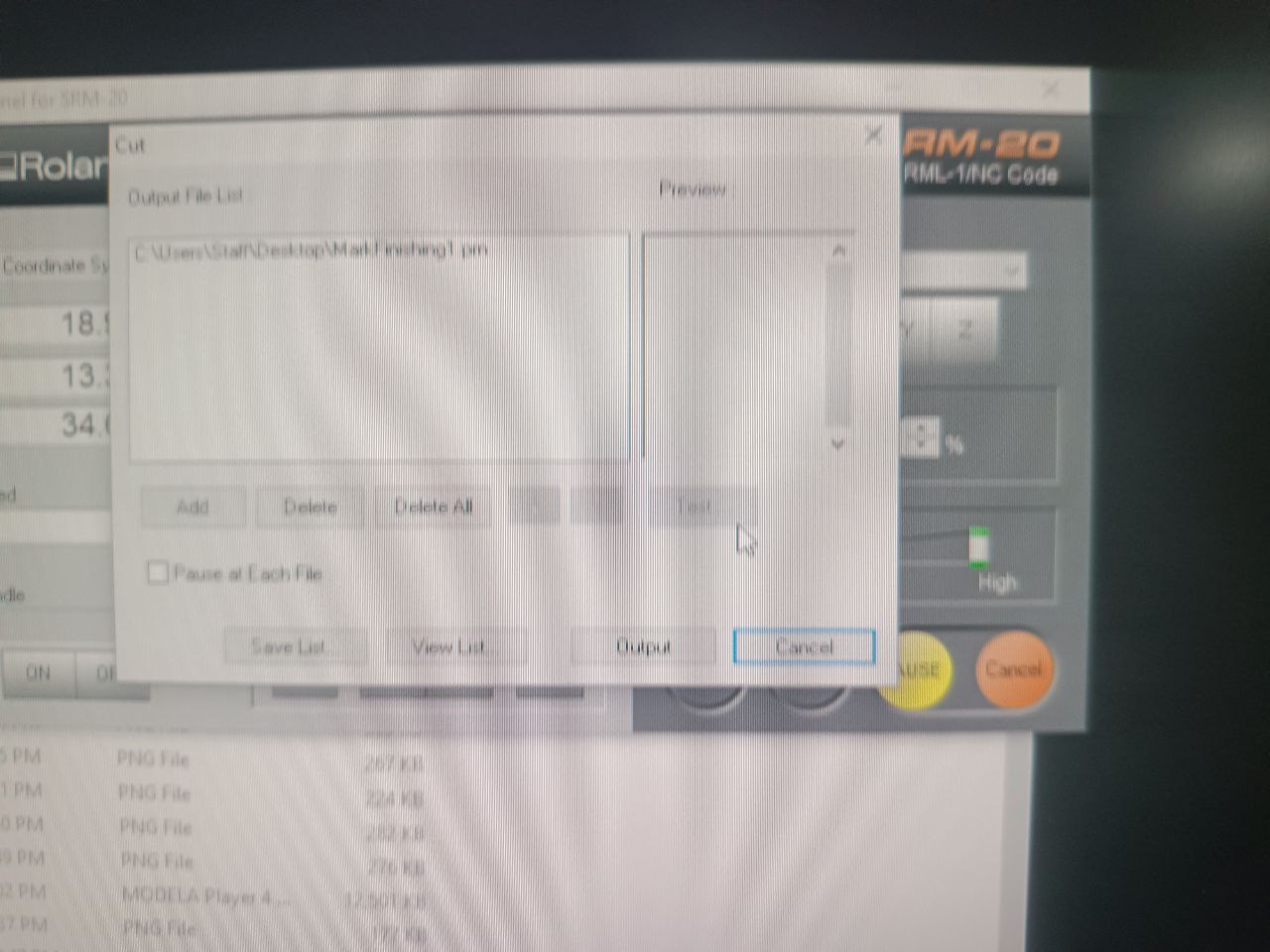
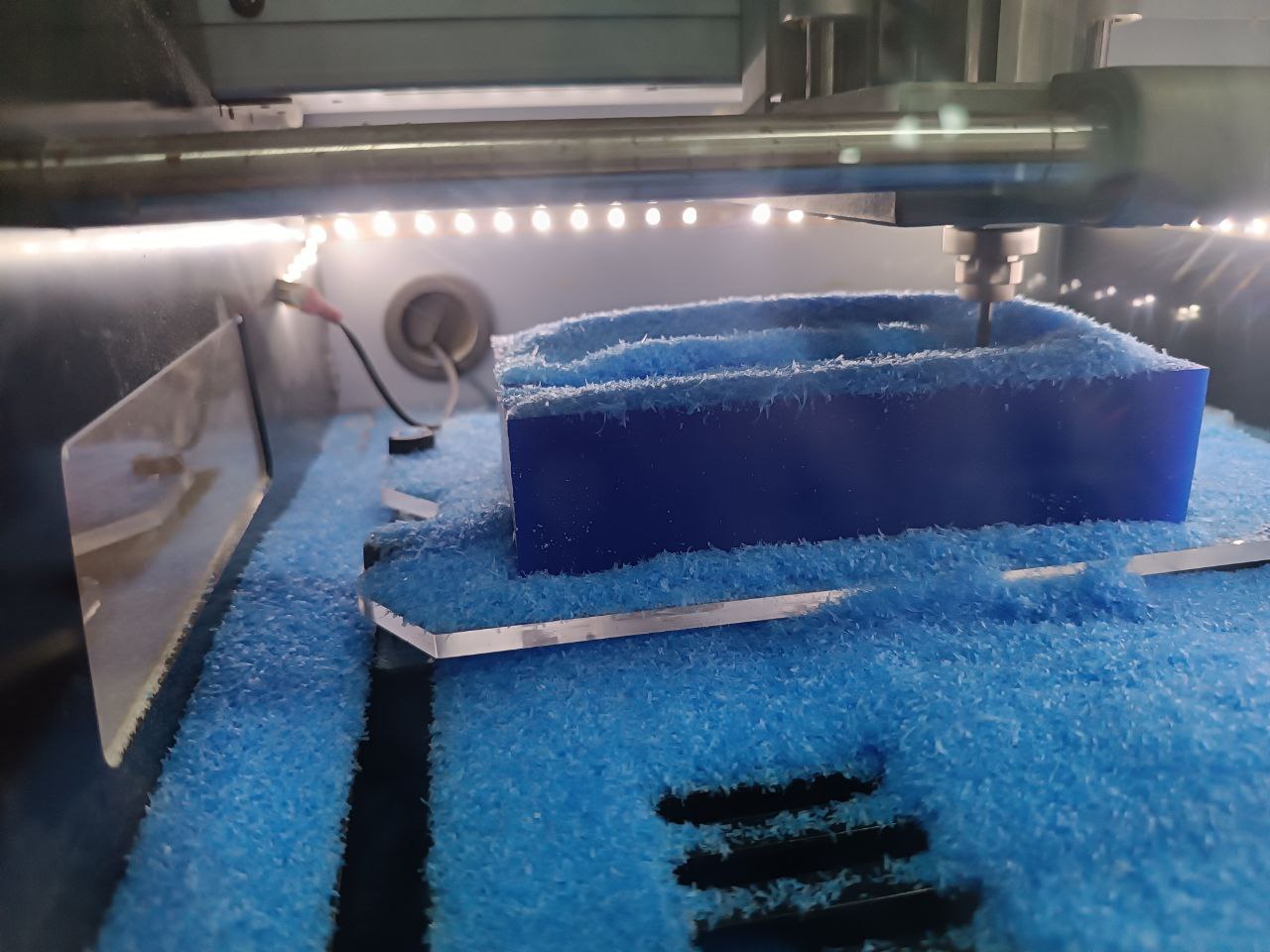
- Eventually it initialised and cut.
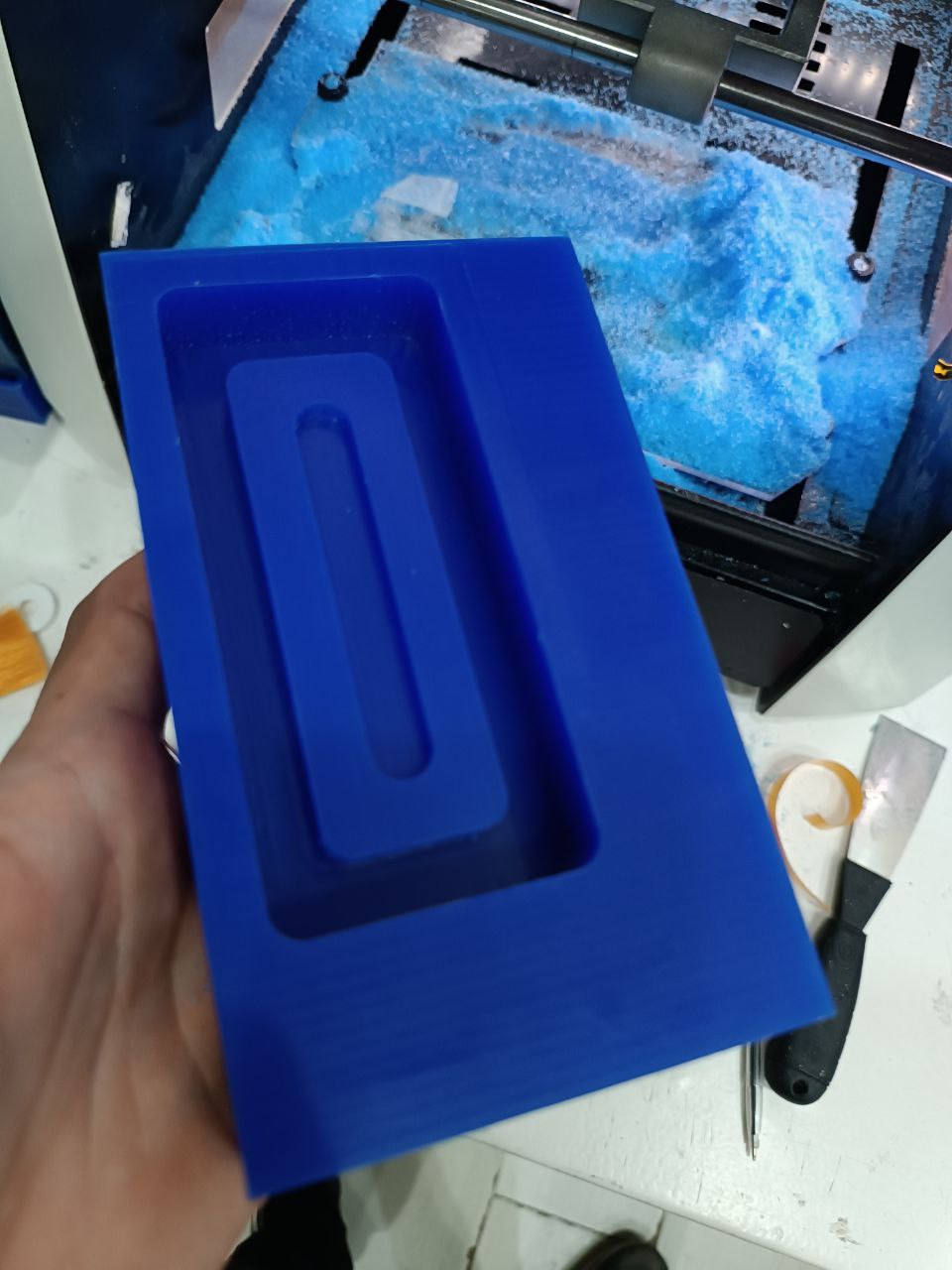
- It was done. But trying to save time, I made shape to easy, not suitable for 3D prosessing .
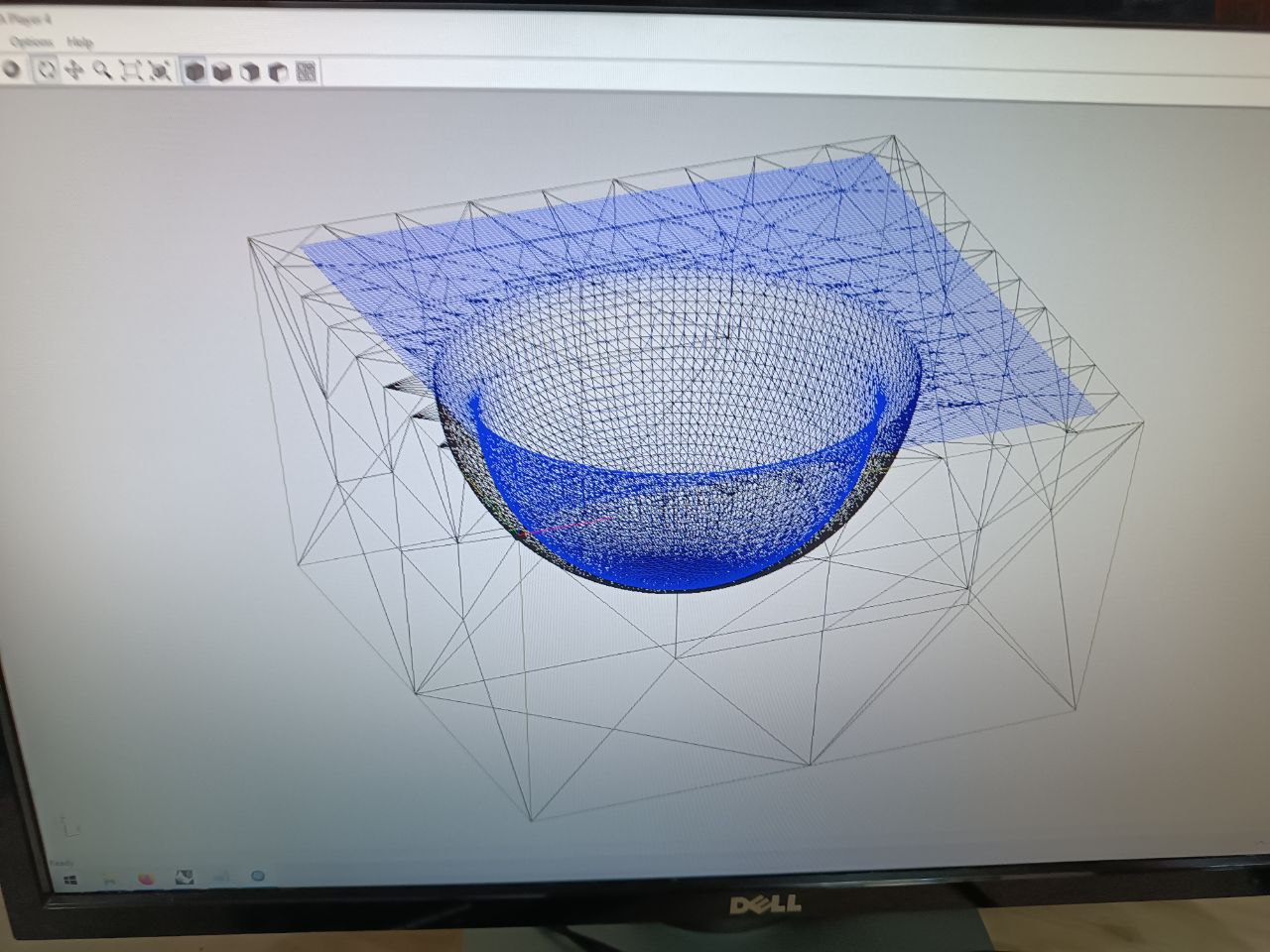
- So enother semispherical shape was done for casting LED inside silicone.
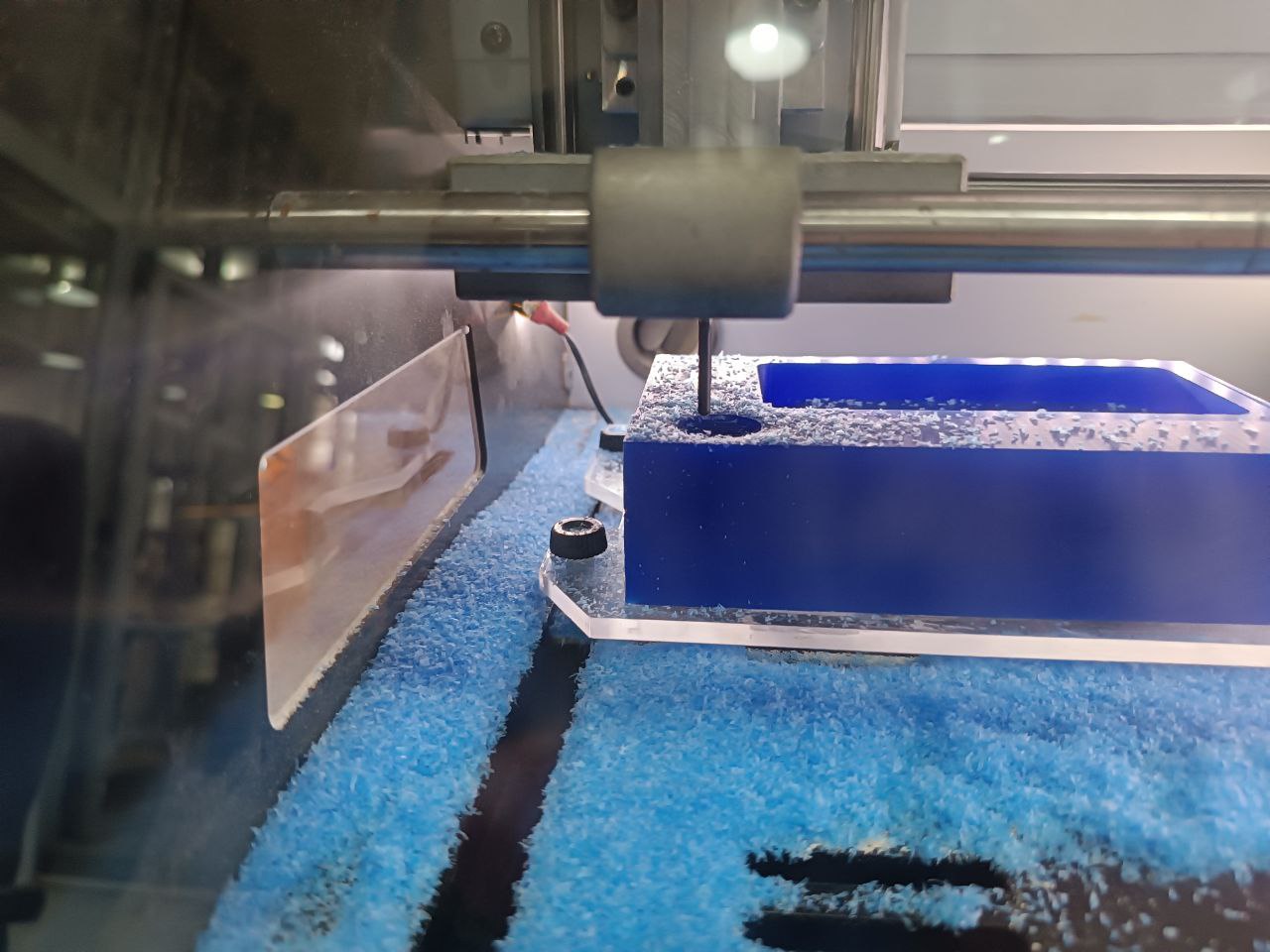
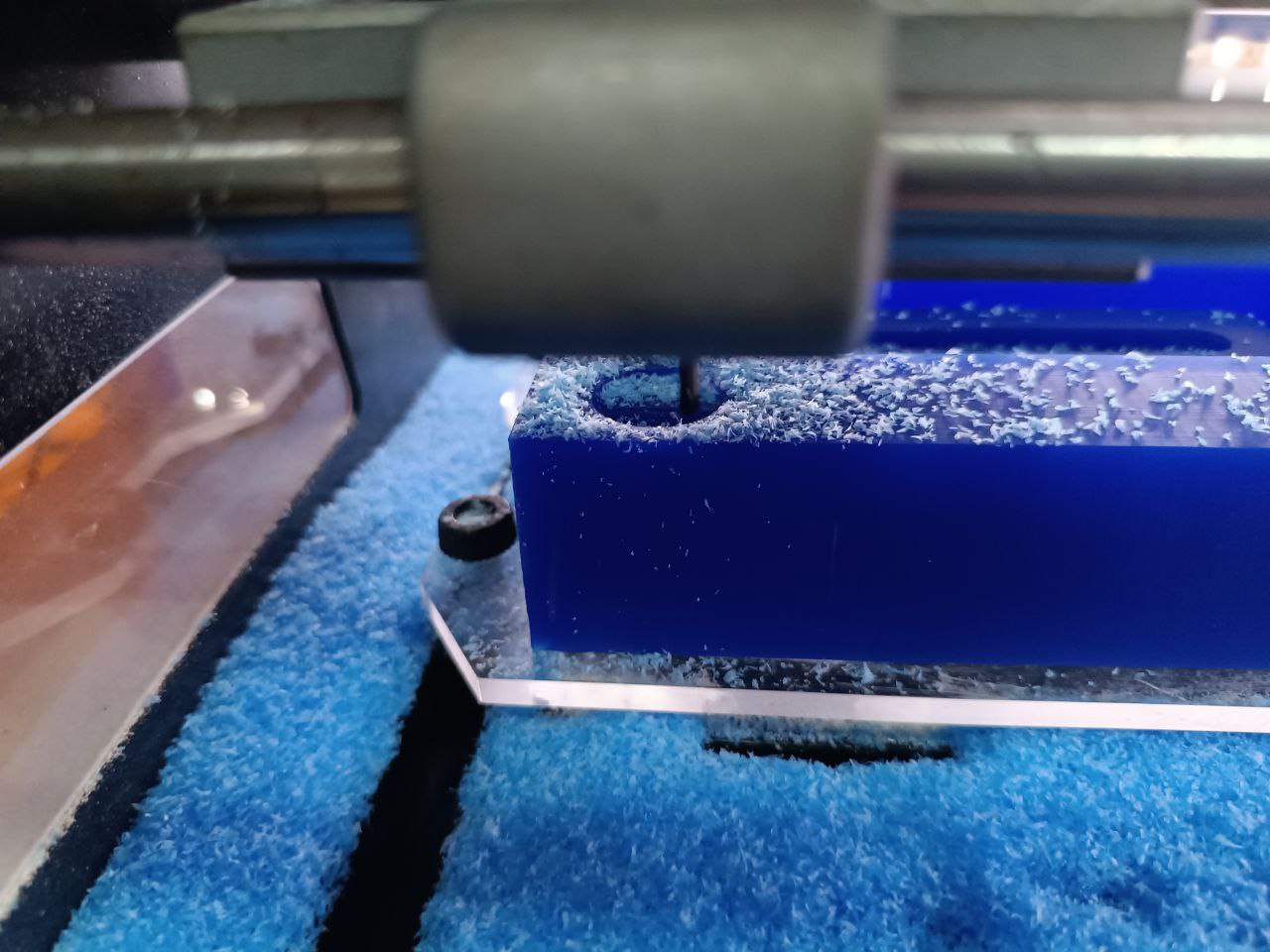
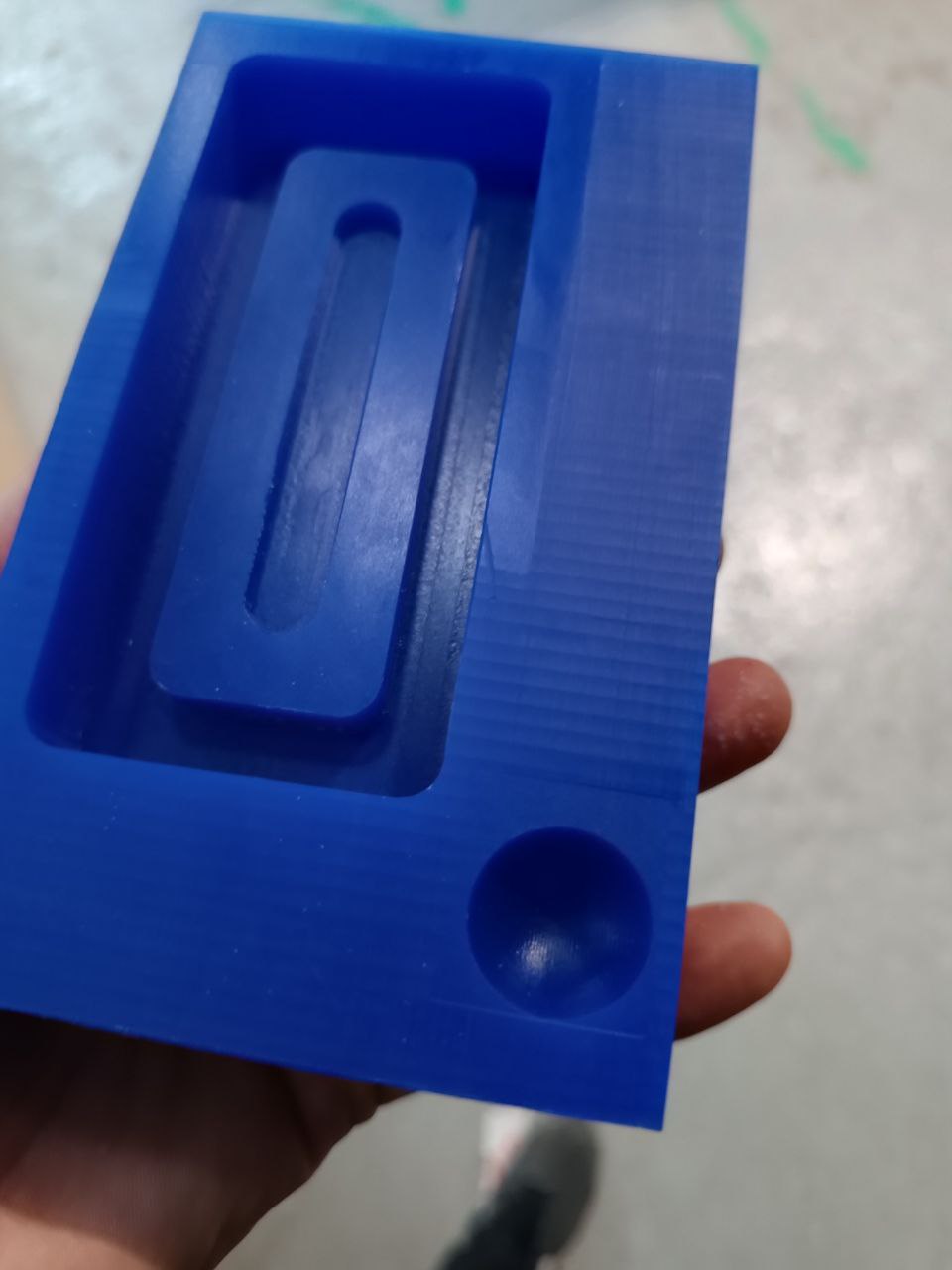
- Done.
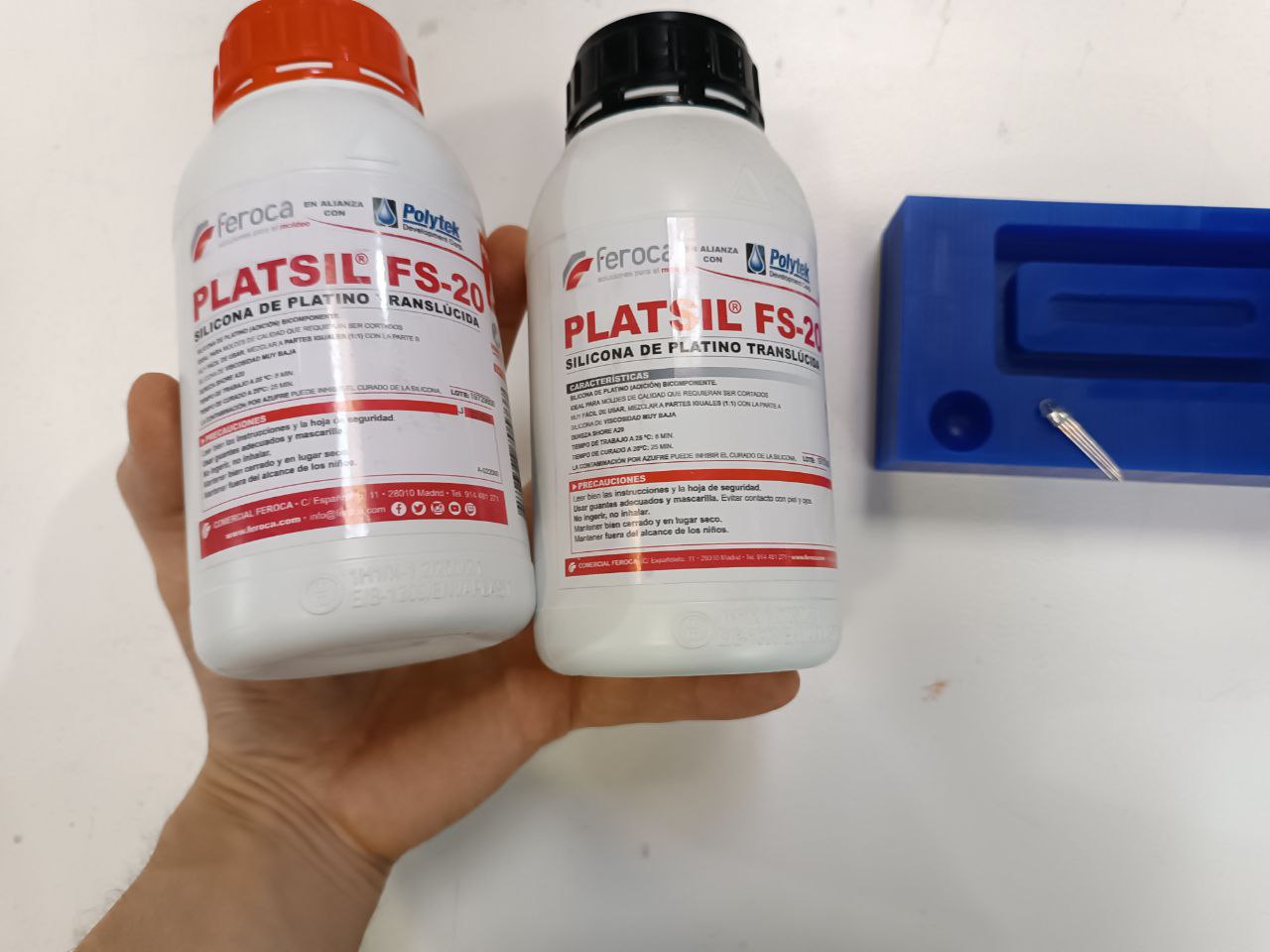
- Used fast solidifing silicone.
- Datasheet
- Quick full cure, in the region of 20 to 25 minutes.
- Working time of around 8 minutes.
- Low viscosity, high tear strength.
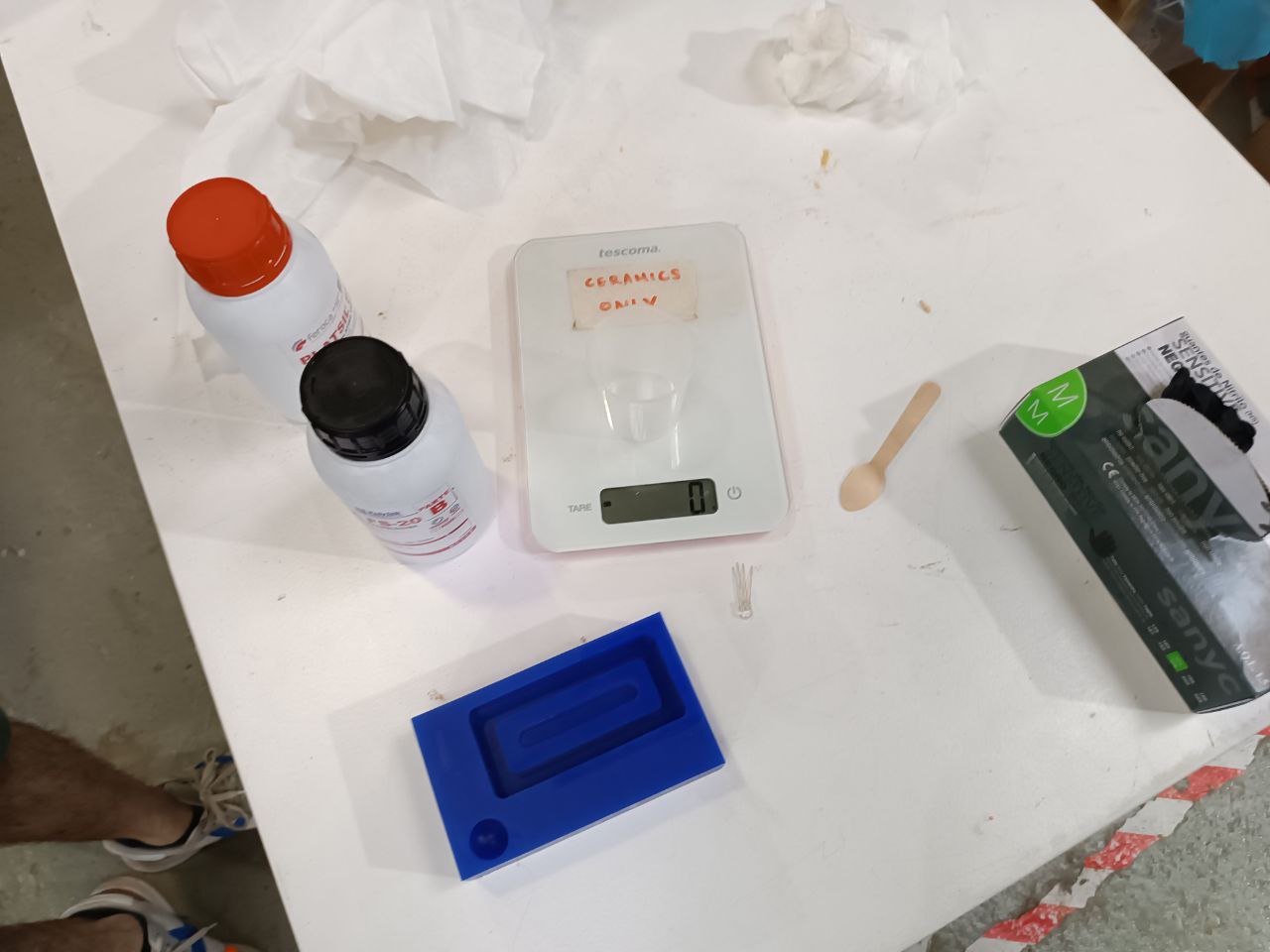
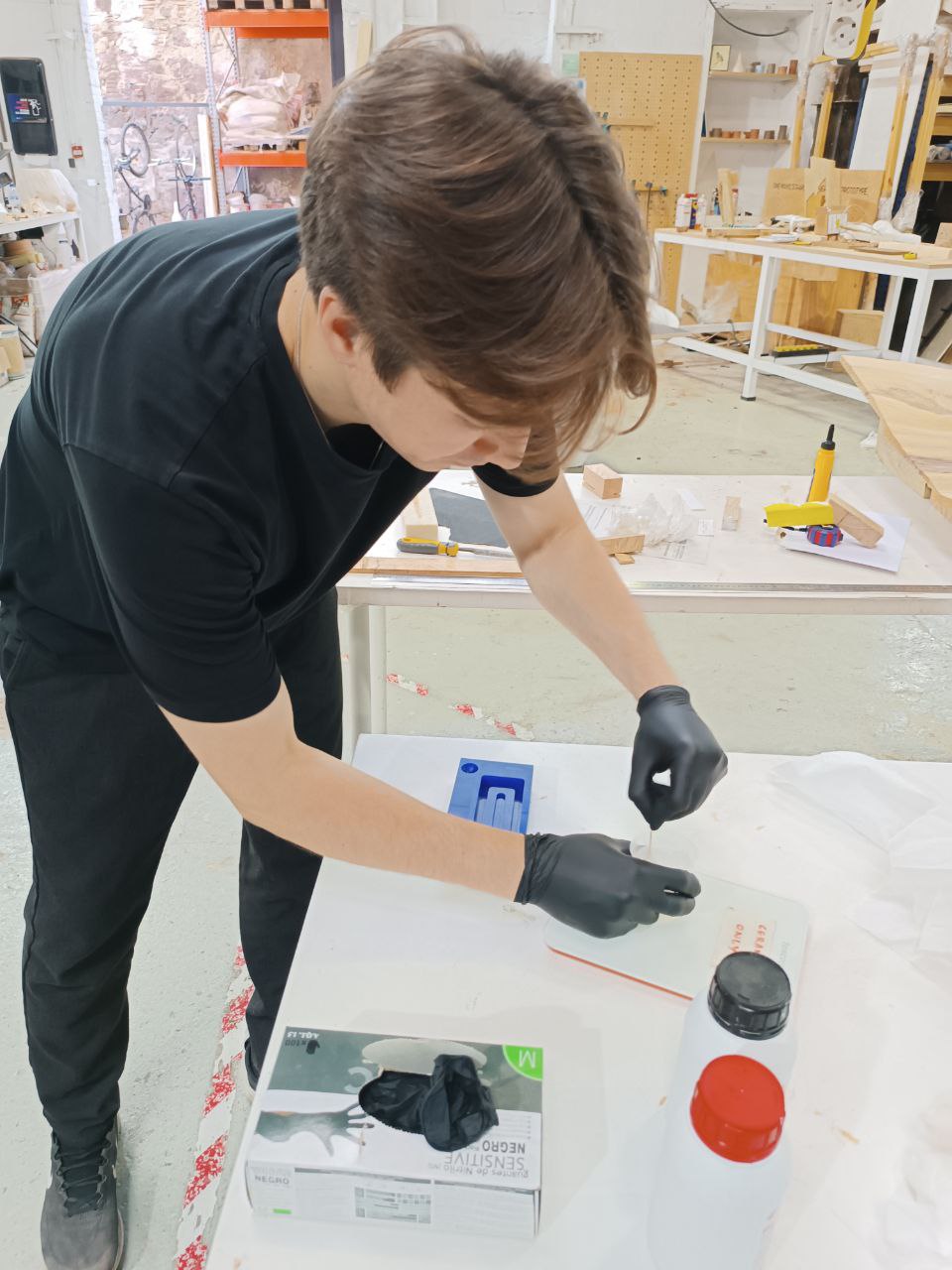
- Exectly that one need to be mixed 1:1.
- Mixed well, needed evenly mass for well solidifing (that is why better mix components in one container, then put them in two and tancefuse from one to another, to avoid leaving part of material on walls and breack the proportion).
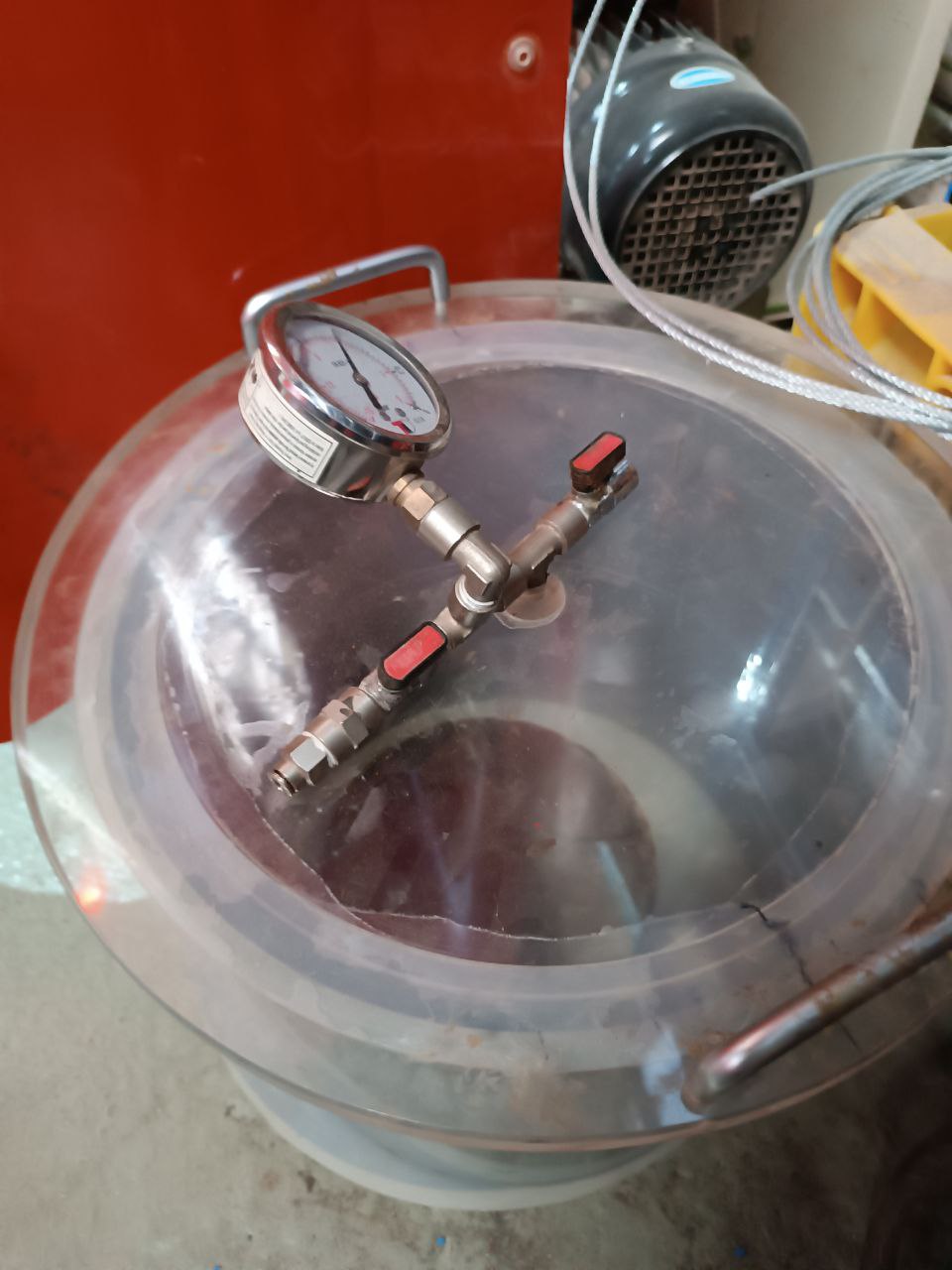
- Usually for erasing bubles used compression container to pump out air, that involves flow up of bubles from silicone mass.
- But in this case would just knock mold bottom on table (it is far not so efficient as compression, but helps to make face surface smoothier).
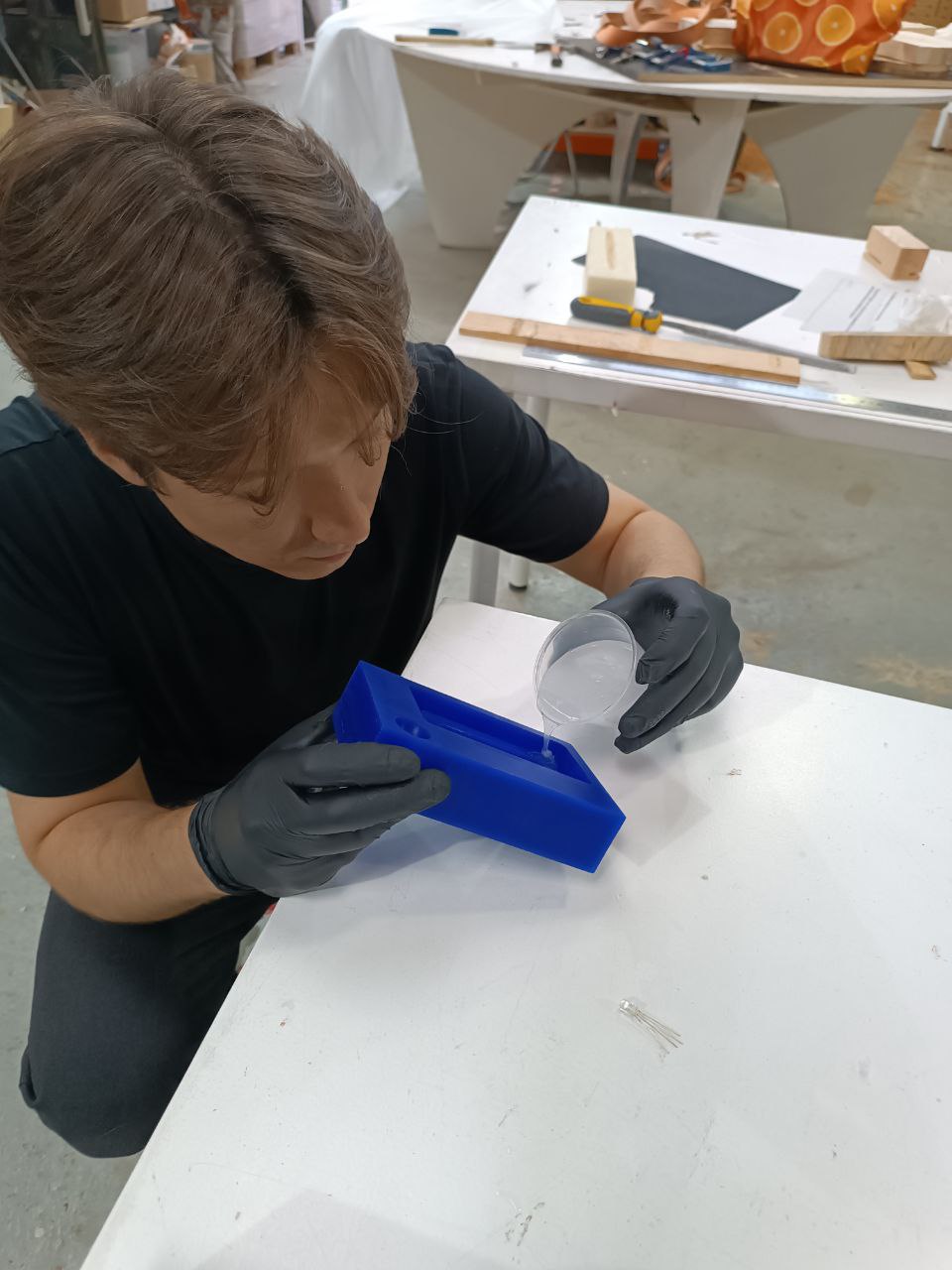
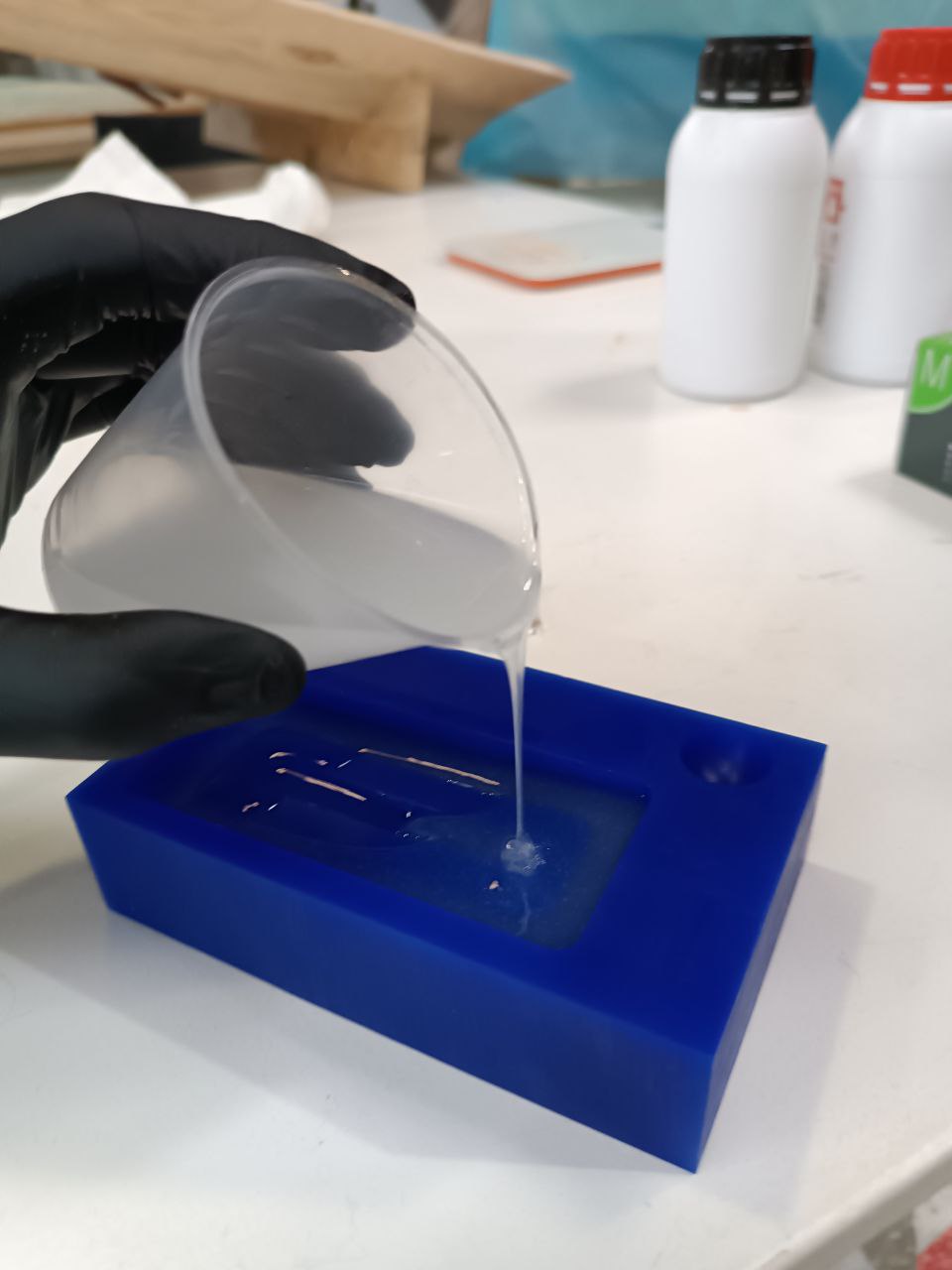
- Started infilling mold (flow should be thin as possible, to create less bubles, also after starting, better to direct silicone falling on sillicone and let it flow, then on material of mold, to create less bubles on face surface).
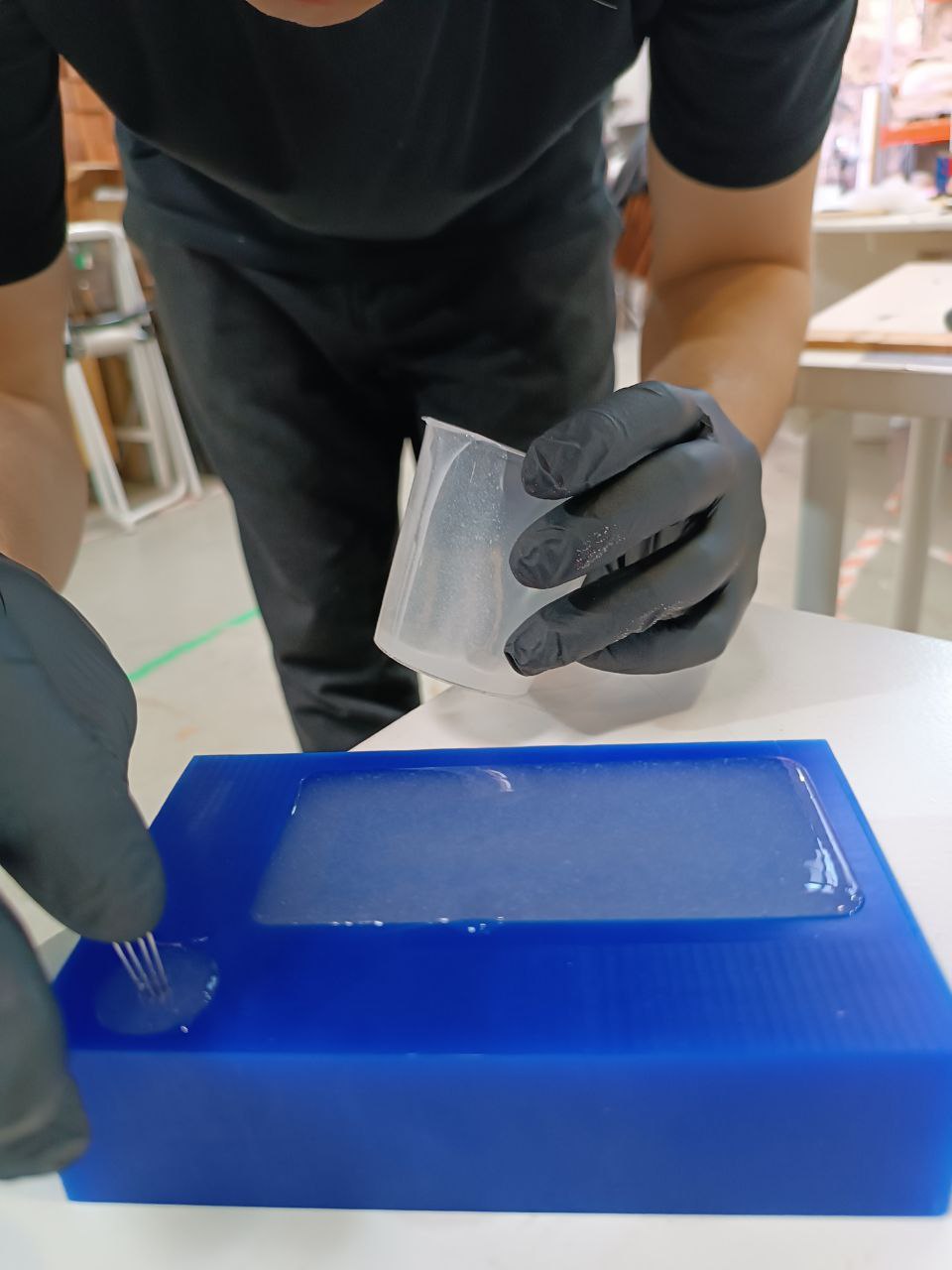
- Placed LED.
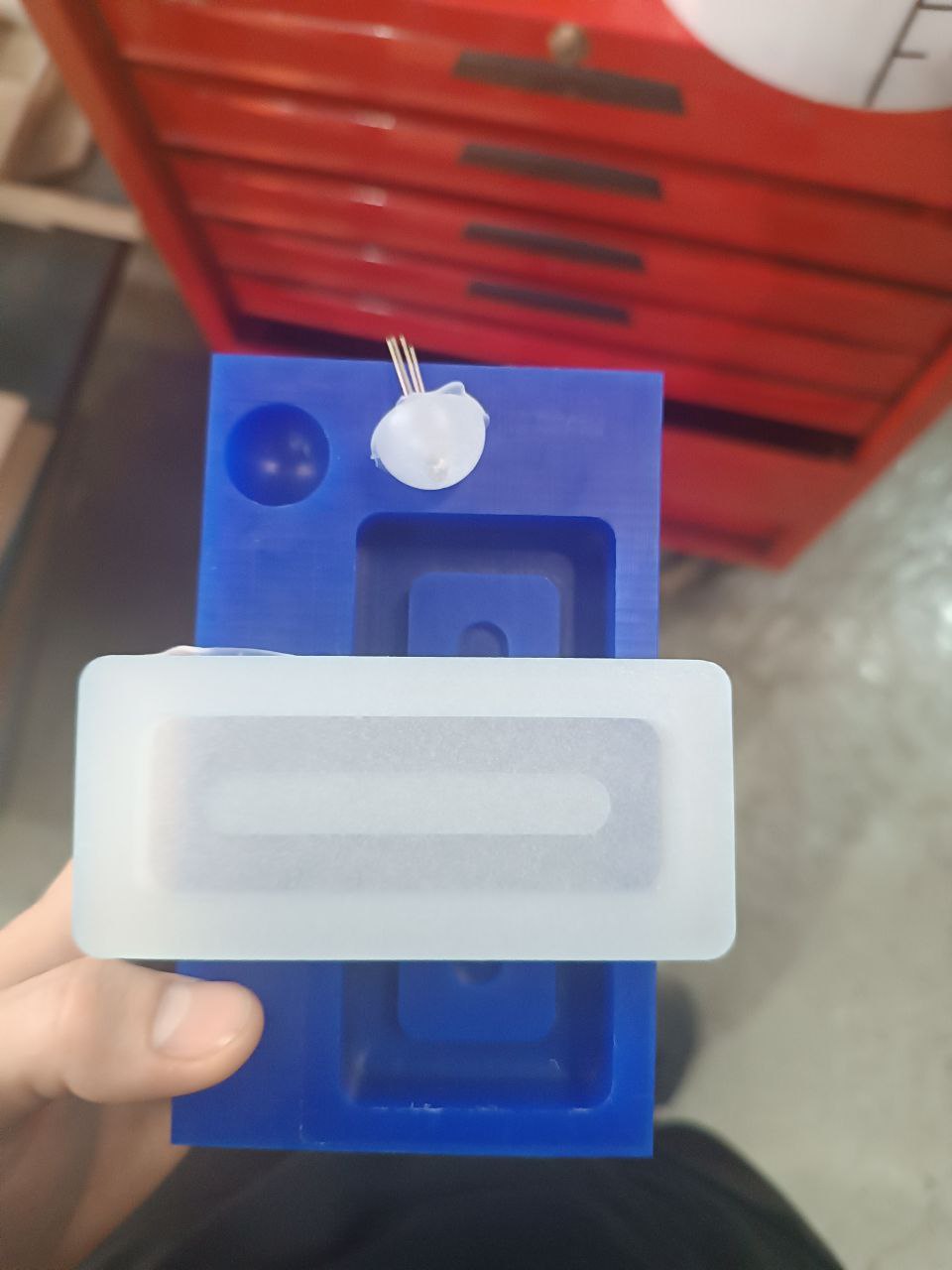
- Casted well.