3. Computer controlled cutting
This week started to use Lazer cut Machine, also group assignments. For modular joinable details decided create parametric detail by Fusion 360, but processing thought that it in this case would be problematic make fully parametric sketch, so decided to use Grasshopper. Final aim was to create physical press-fit kit.
Also Group Assignments started.
Documentation
- Chosed plane, created and trimed circuls.
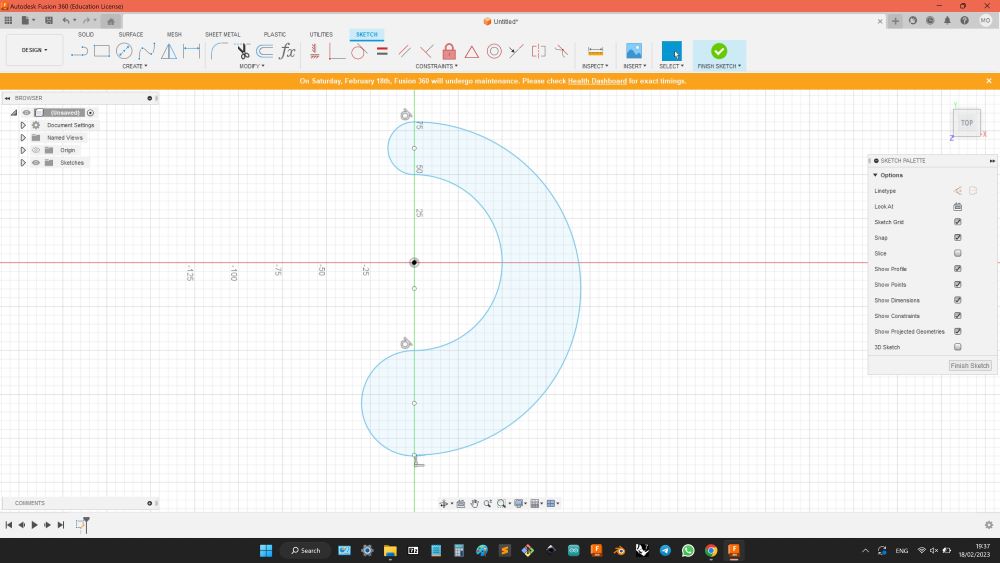
- Constrained circles origins.
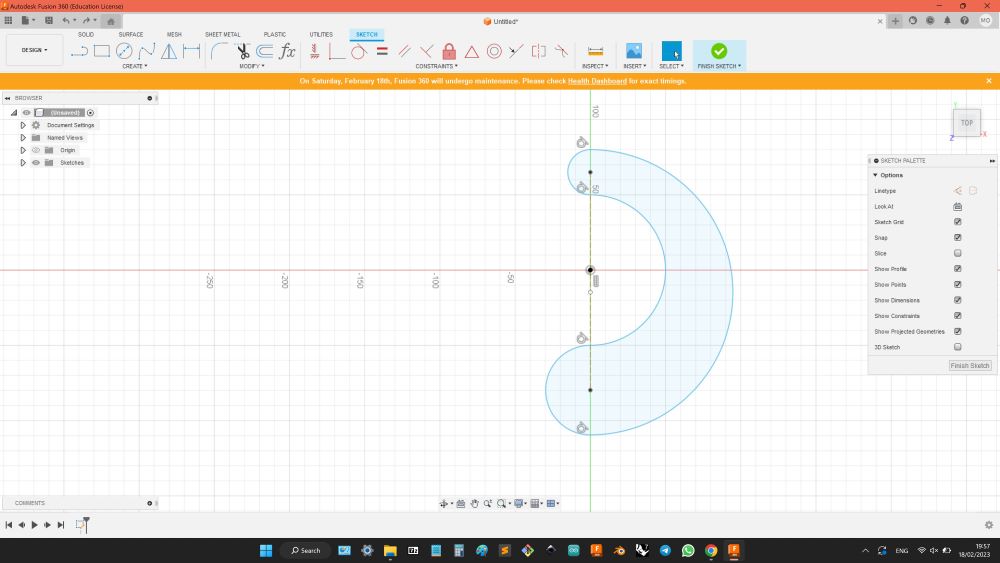
- Added parameters for size control.
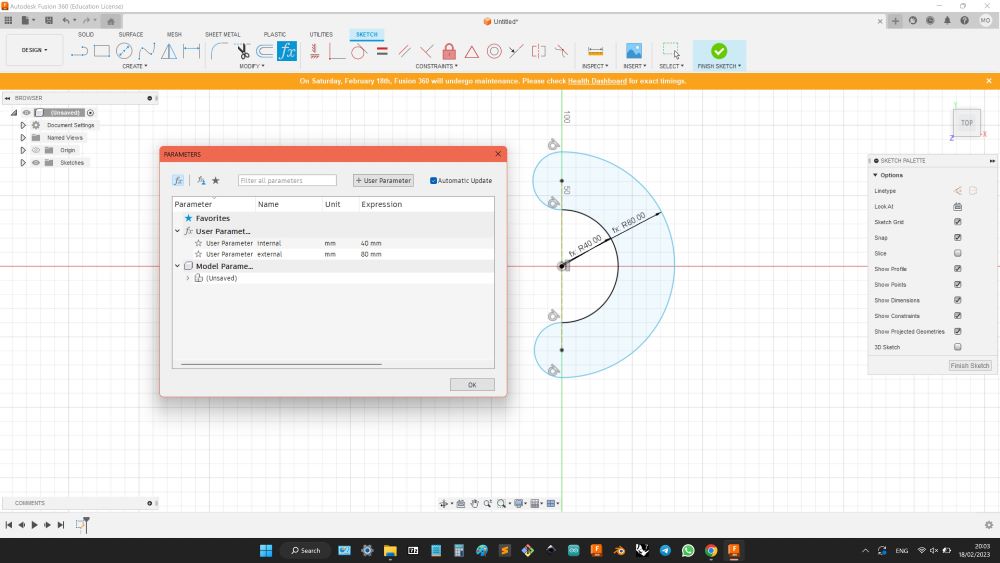
- Thought that manage it better in Grasshopper.
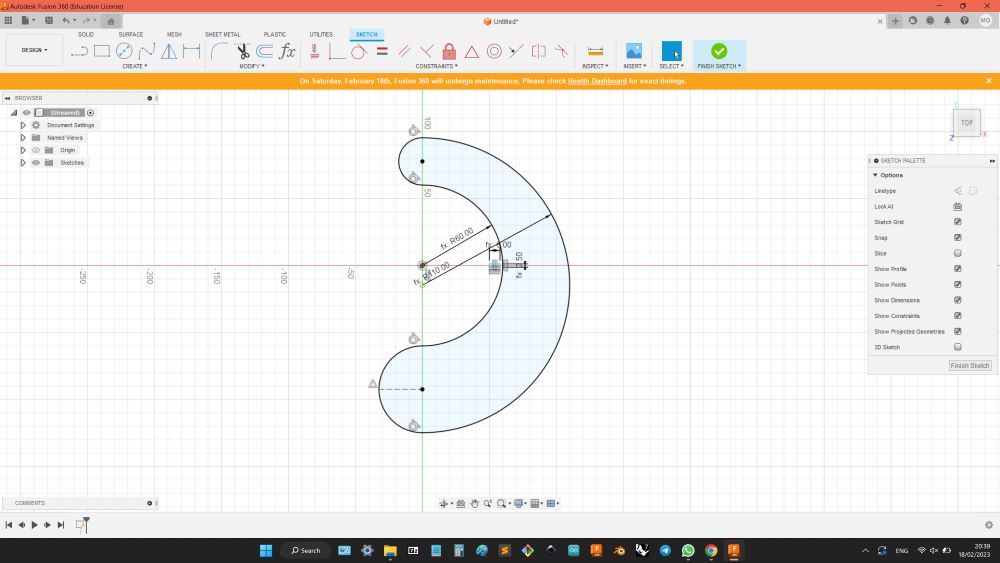
- Created two circules, moved smaller one.
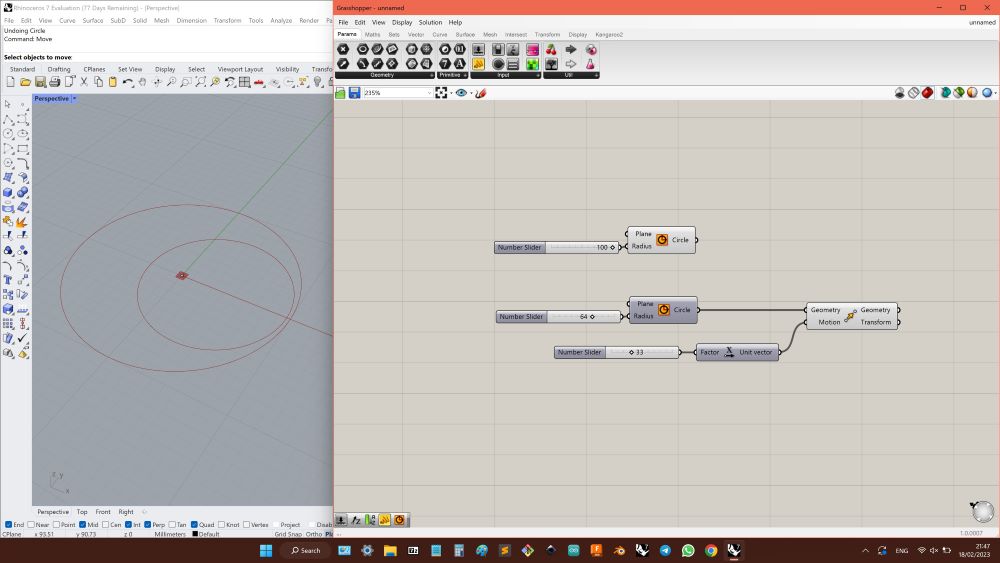
- Tried few input/output conections variations, trying define points for curve split.
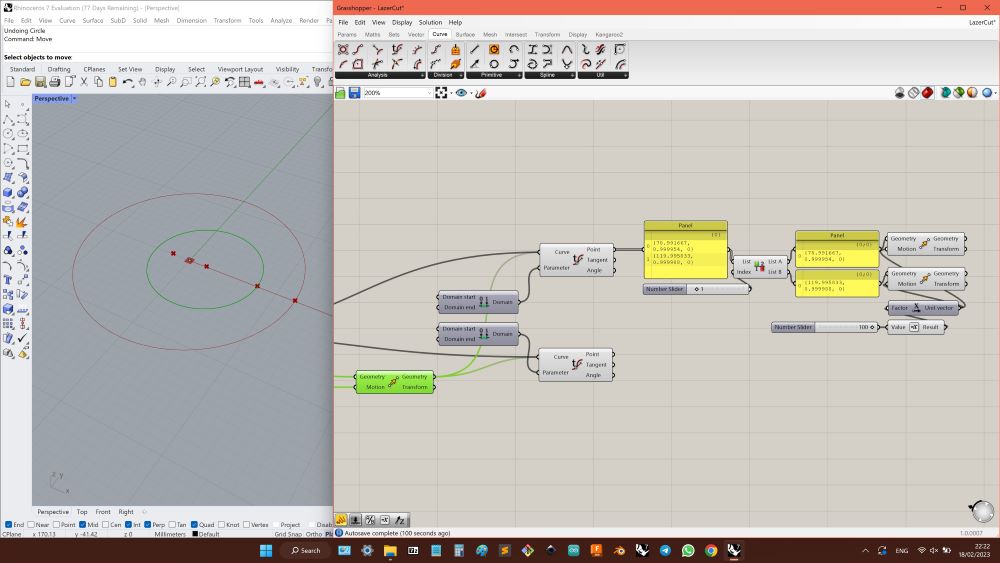
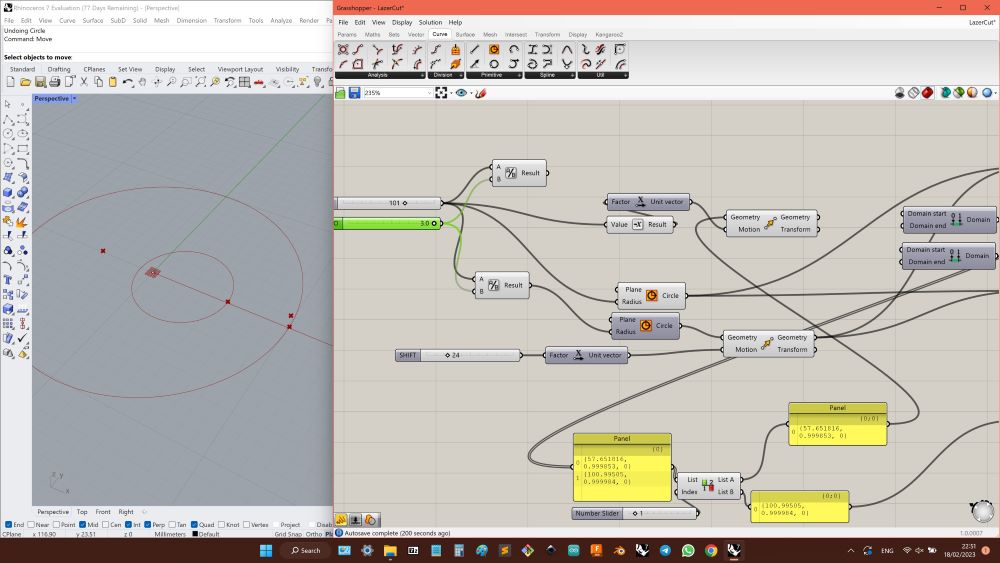
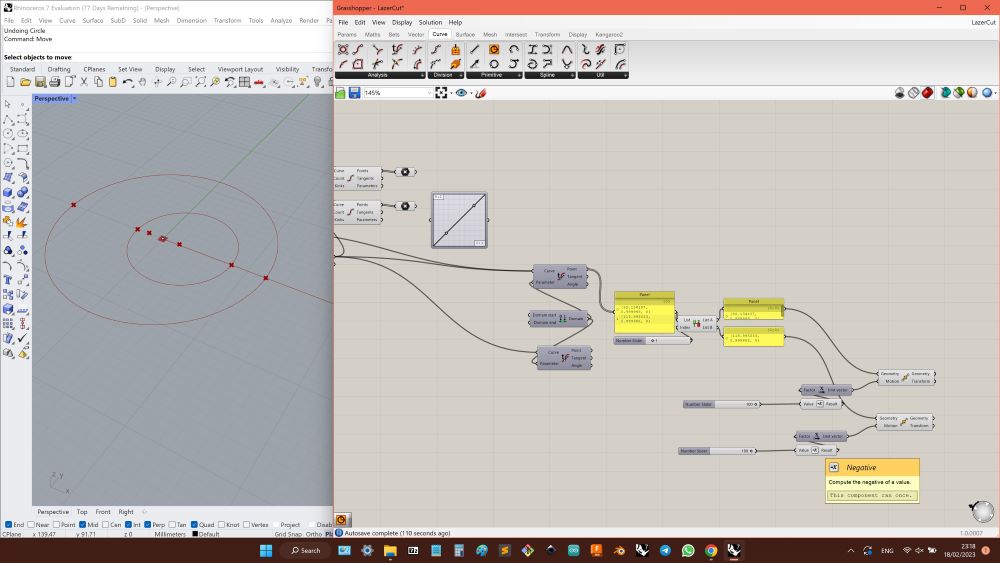
- Eventualy decided to use division of curves on equal segments.
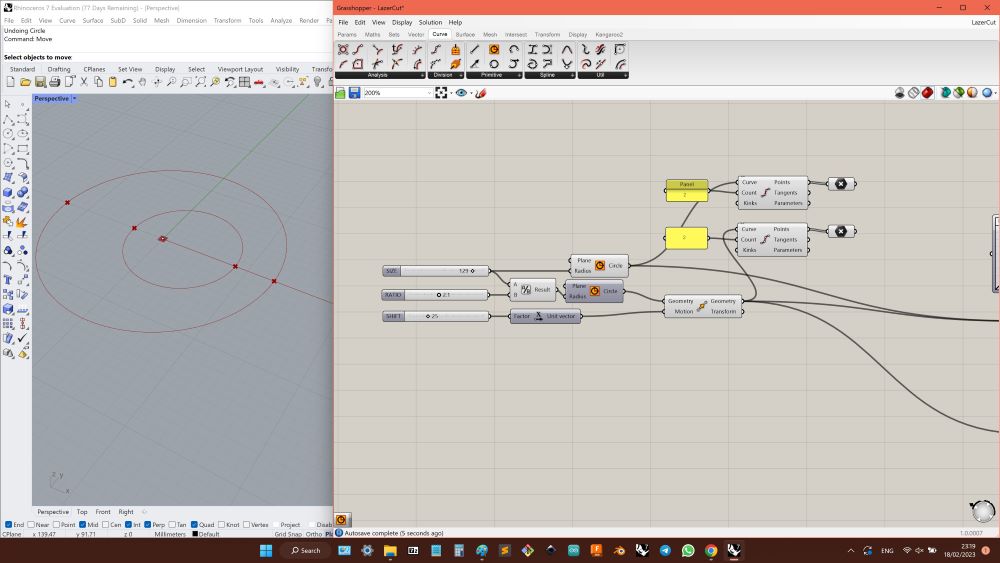
- Created tangents circles, surfaces and splited them, differentiate each demanded area.
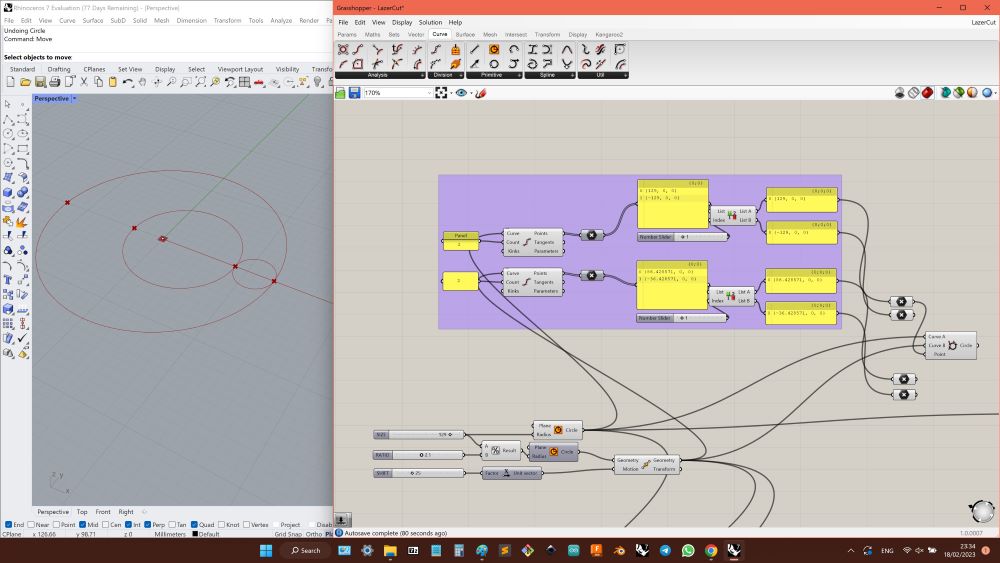
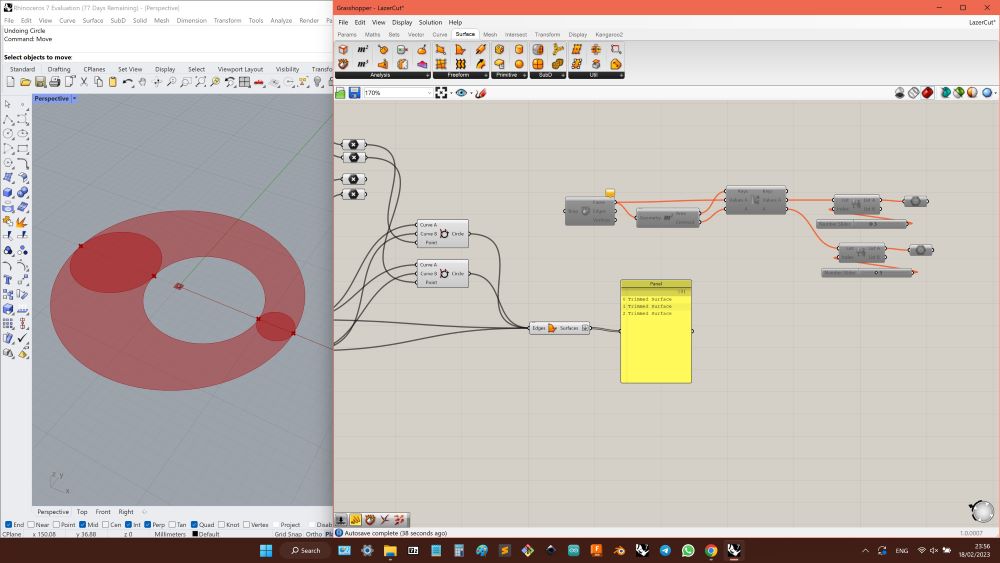
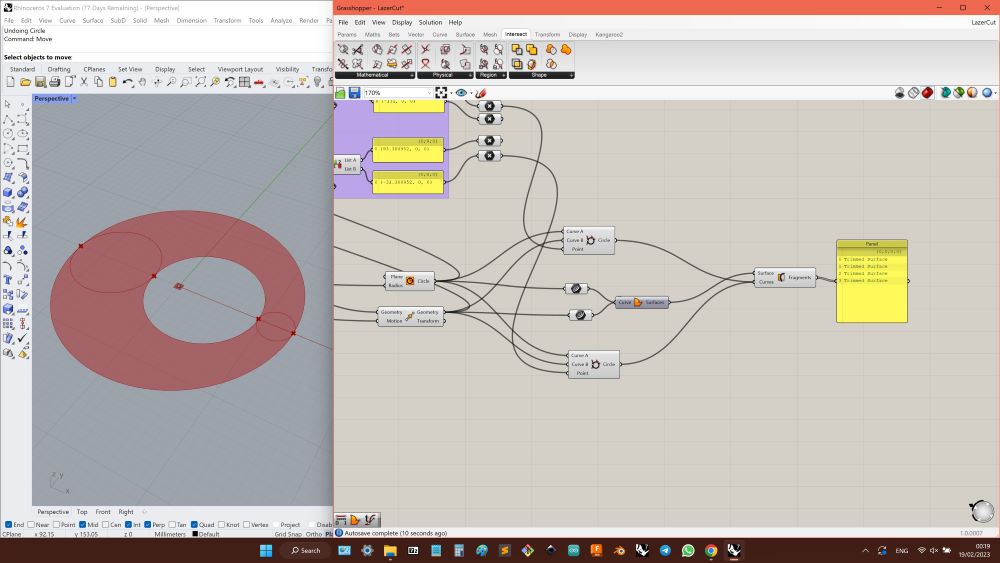
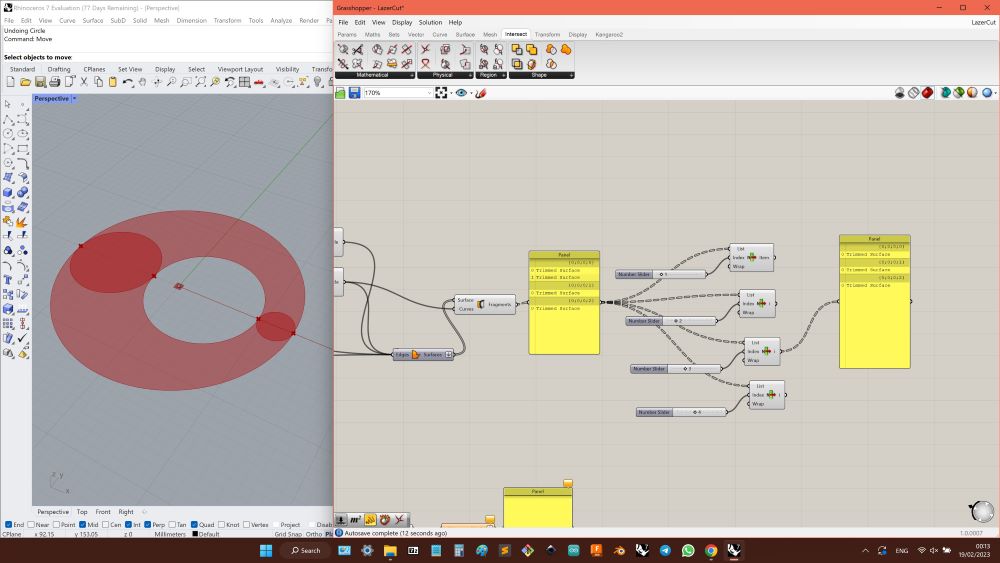
- Started create volume, realised that need 2D for Lazer cut.
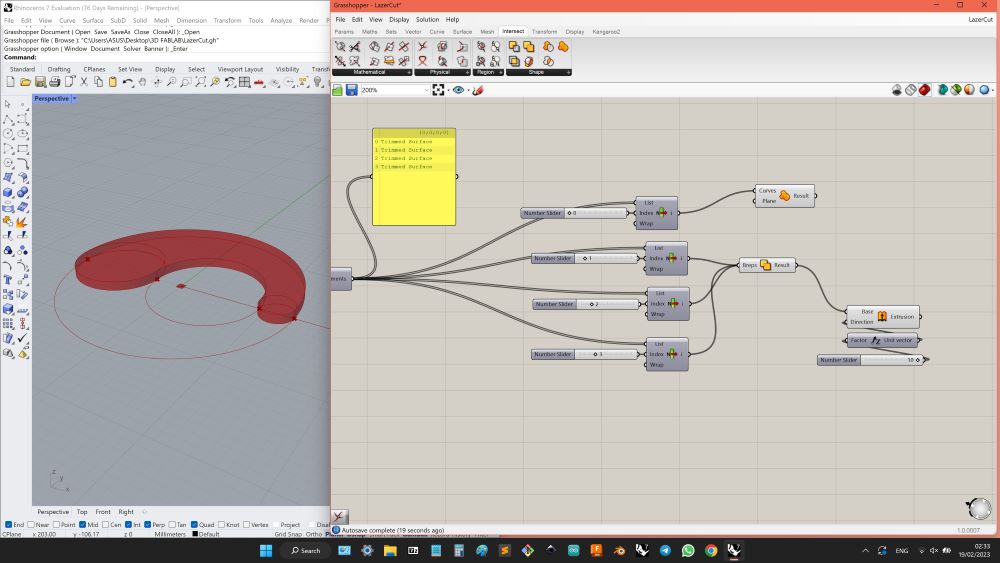
- Devided contour of shape, defined planes and rectangle.
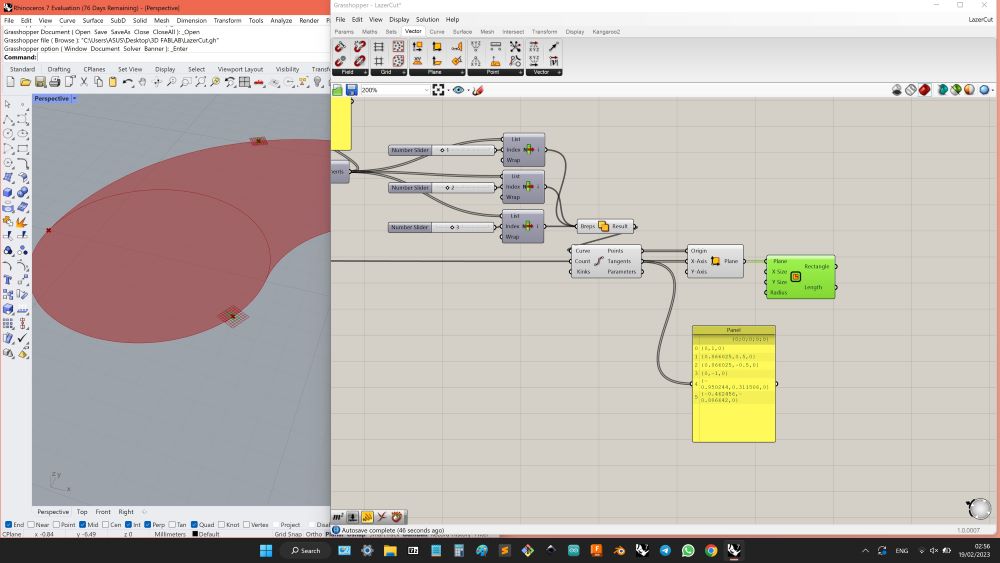
- Rotated plane by defining by tangents direction.
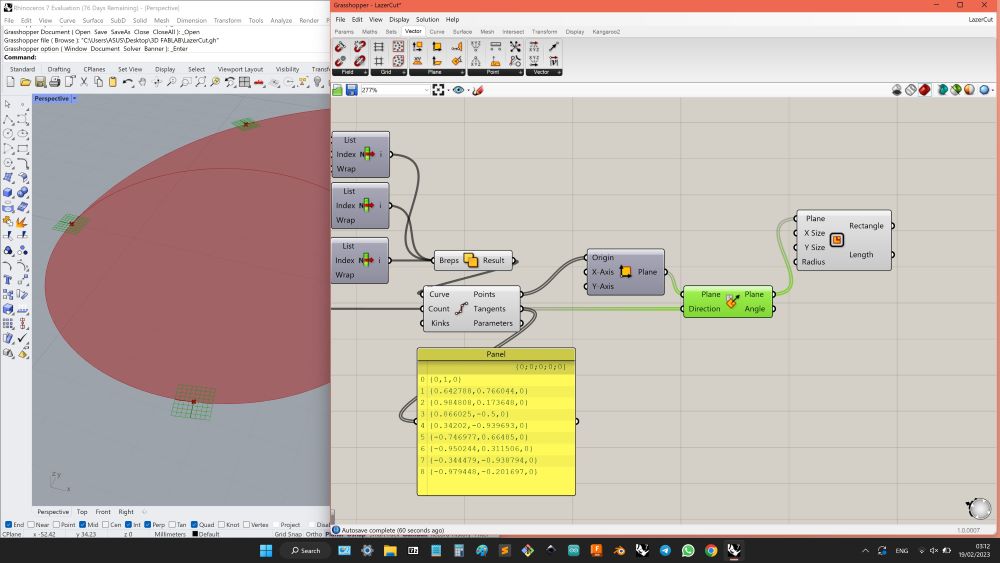
- Defined rectangle sizes and placement by domains.
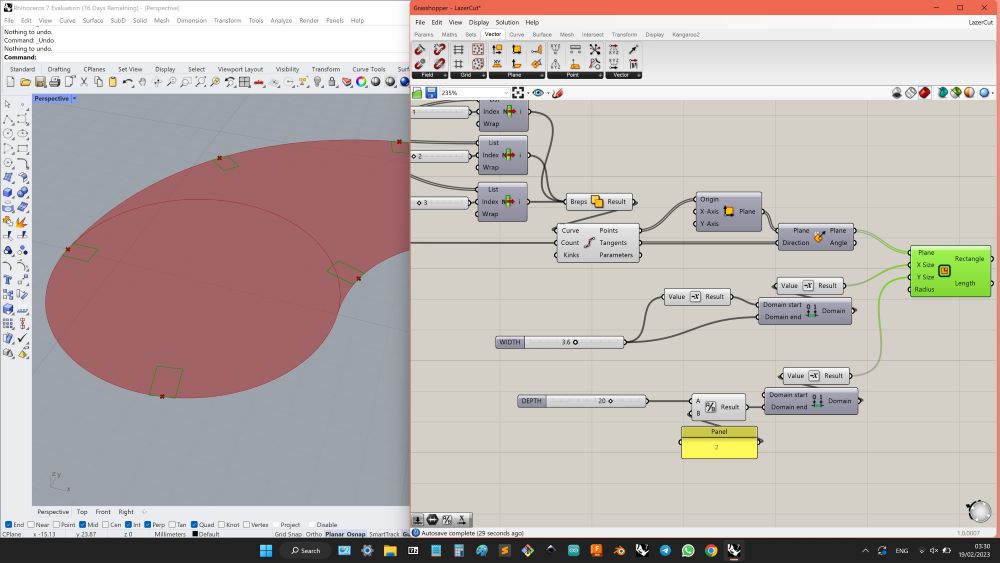
- Did Boolian deference rectangles from contour, line splited not correctly, because of curvature.
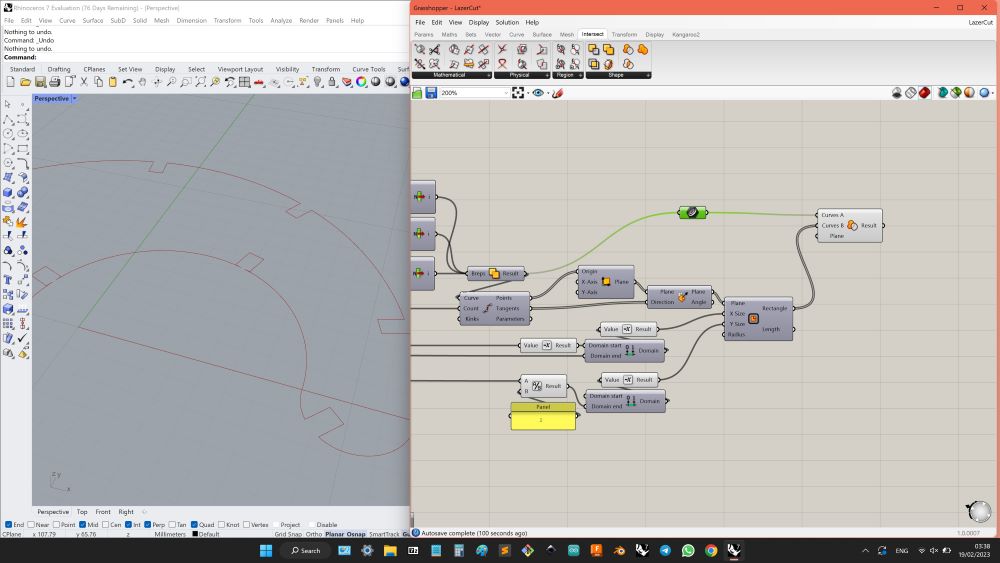
- Defined points on rectengular corners, chosed closest 2 (same distance), splited list.
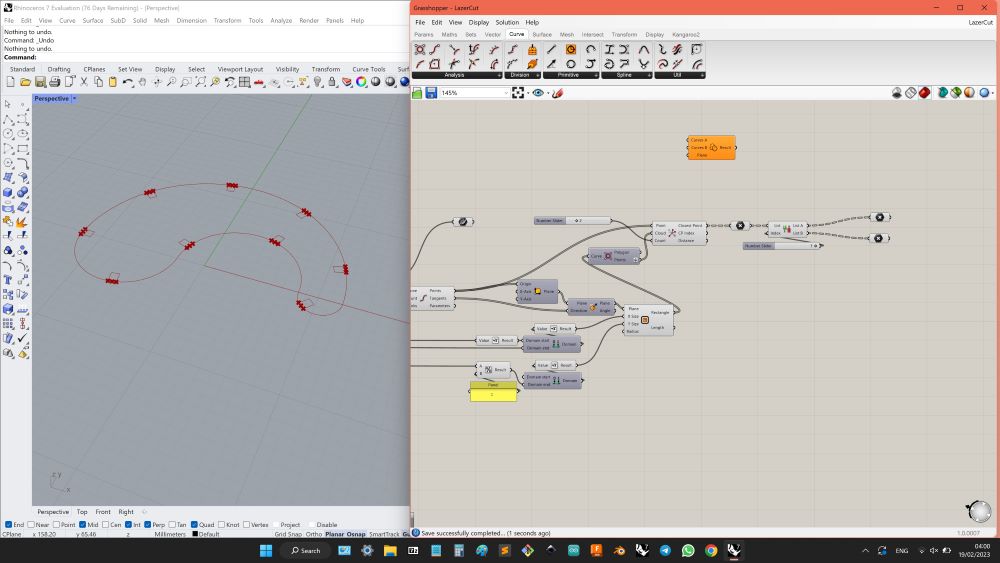
- Started search the way to determine poins on contour.
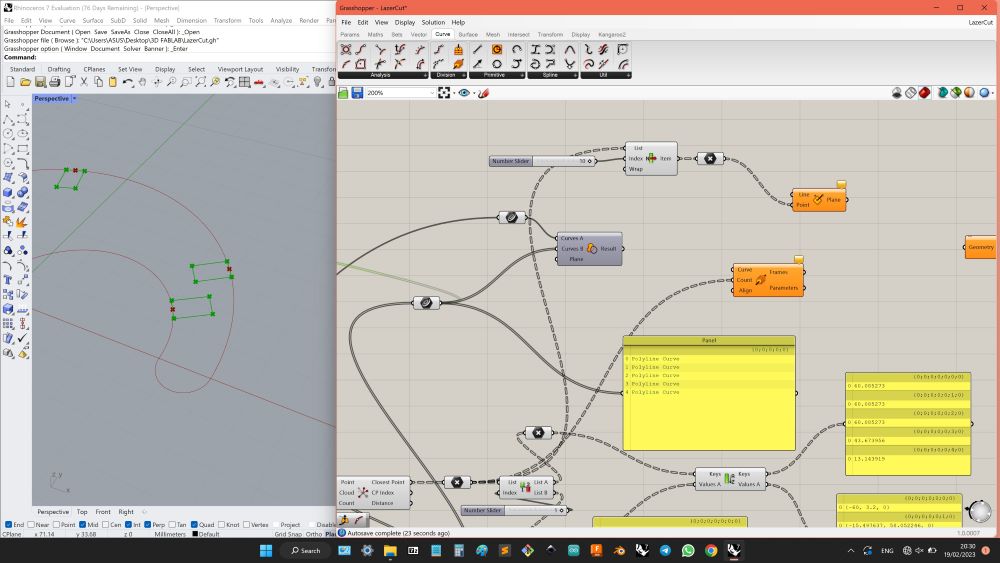
- Splited rectangulars on segments.
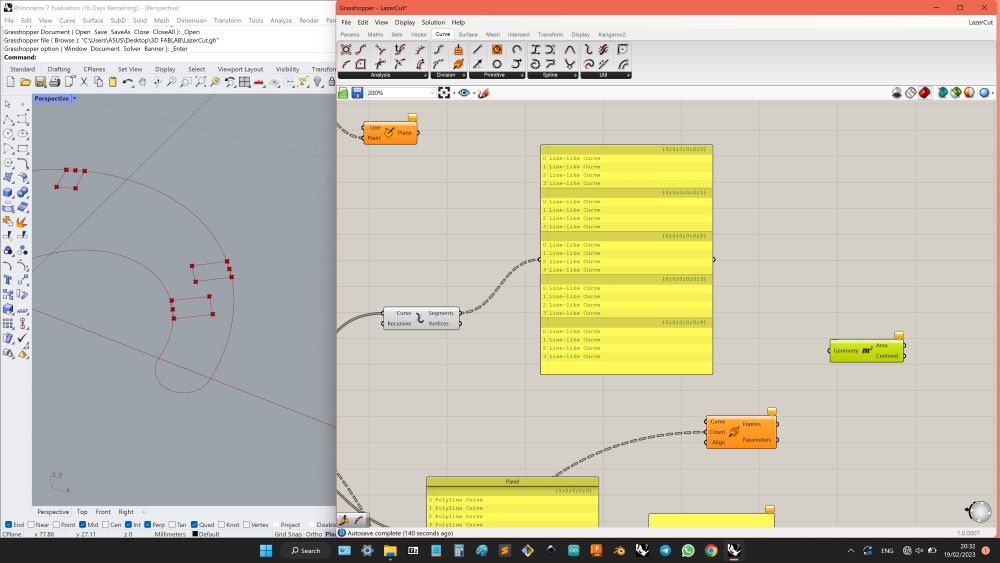
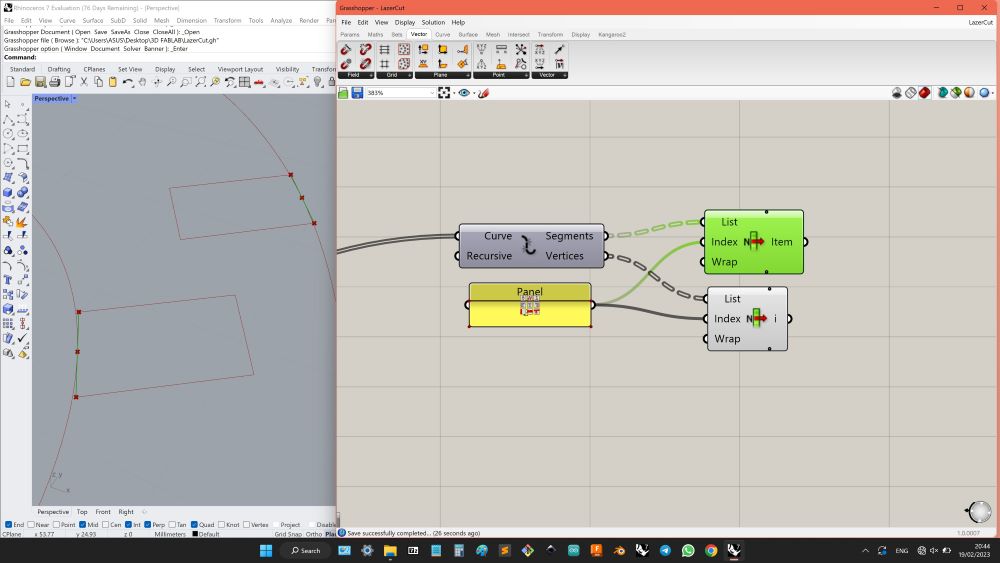
- Created frames in end points of closest to contour segments.
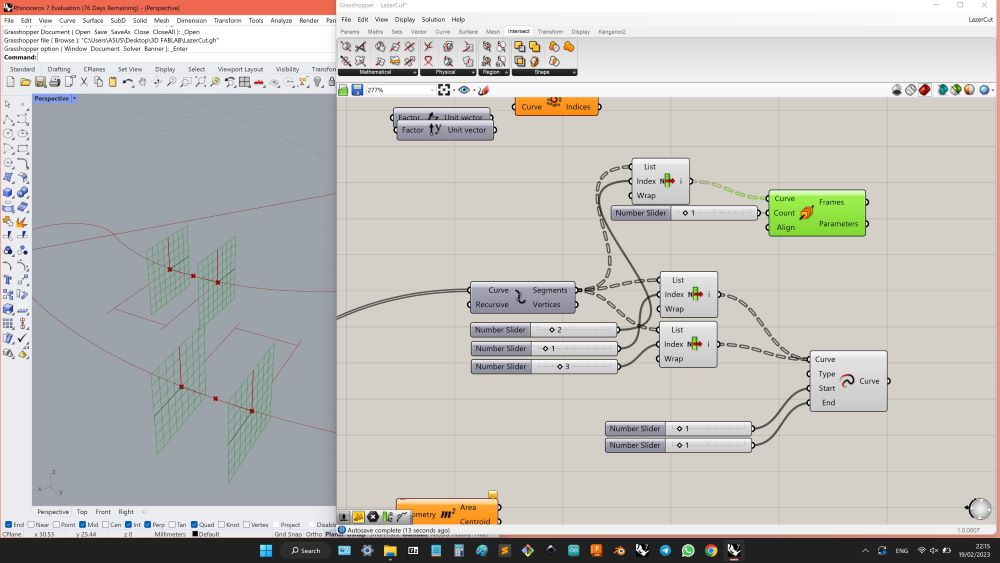
- Defined intersection points of frames with contour.
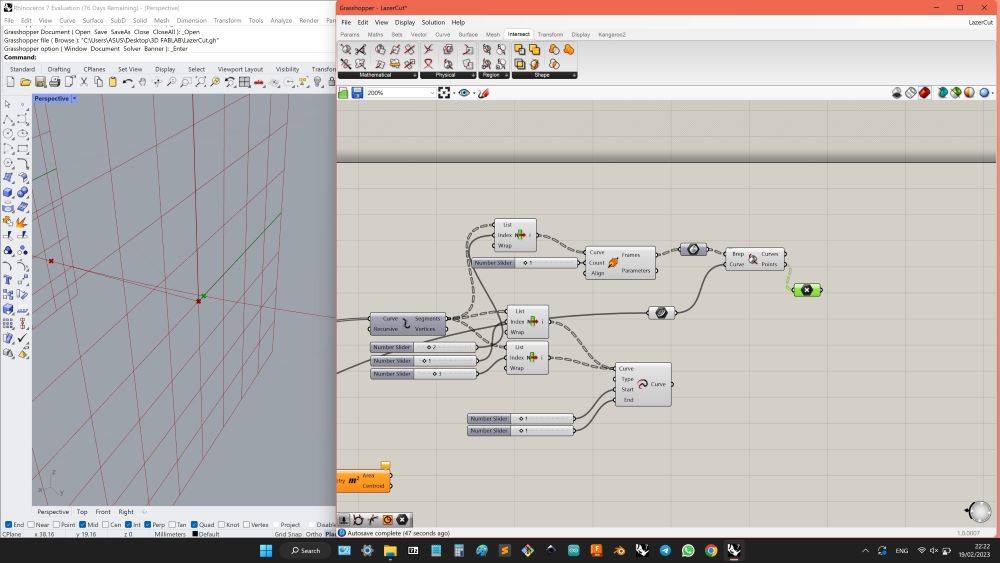
- Mirrored frames by dublication, for intersection of both concave / curved contour parts.
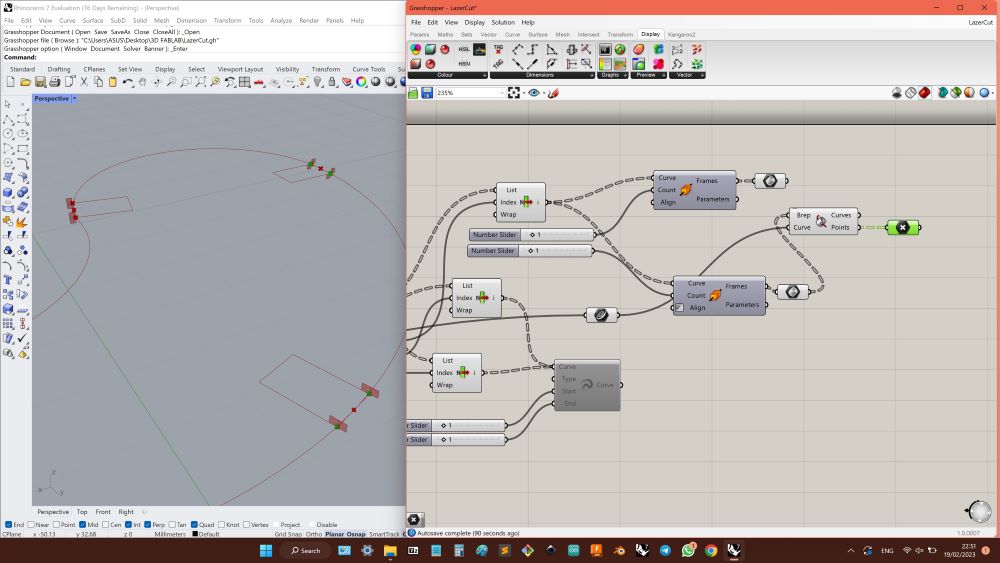
- Tried to understand how arrange rectangle properly.
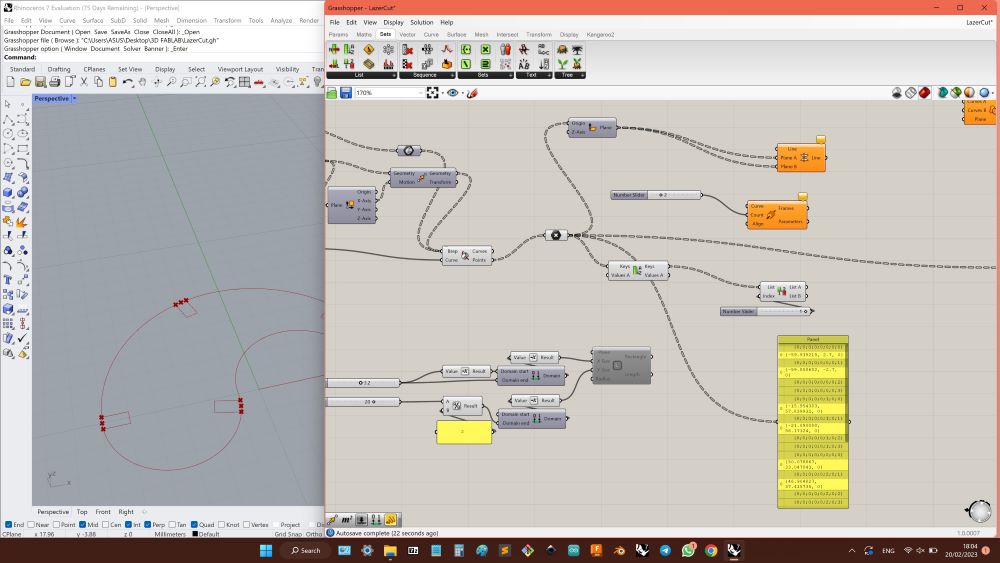
- Decided that best way is create line and find midpoint to determine it as new rectangle origin, dispatched list of intersection points to use them for start and end line points, started work properly only after flatening of points tree.
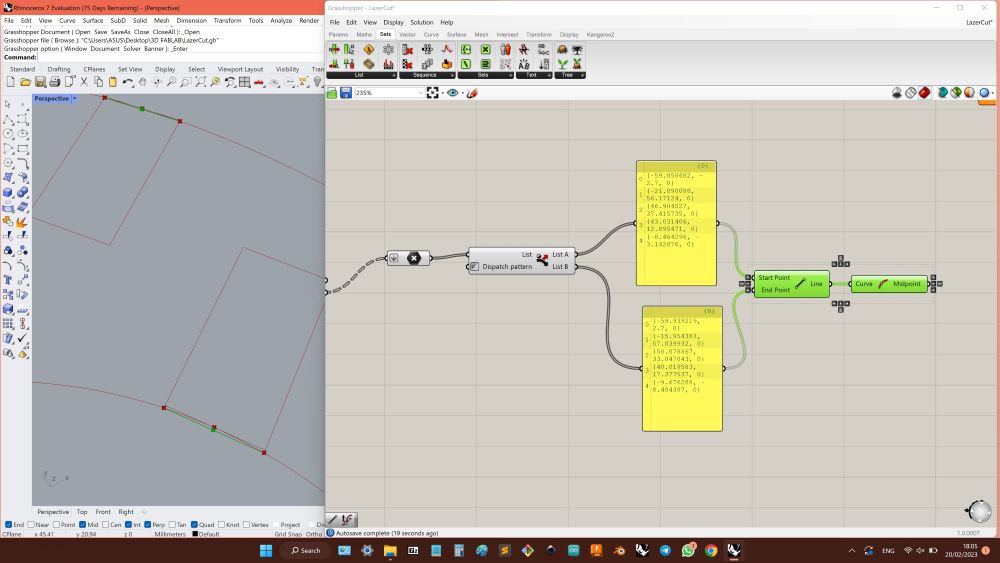
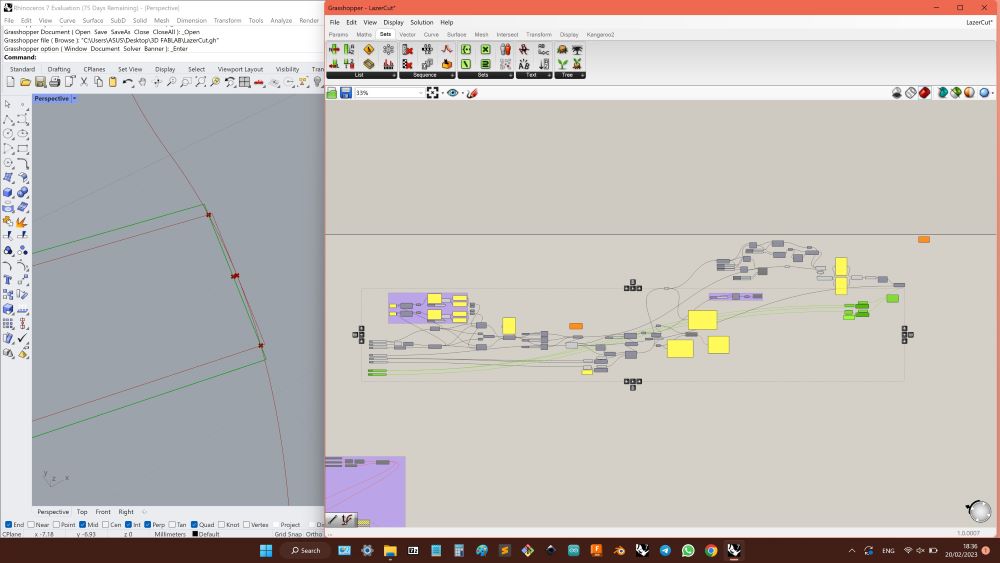
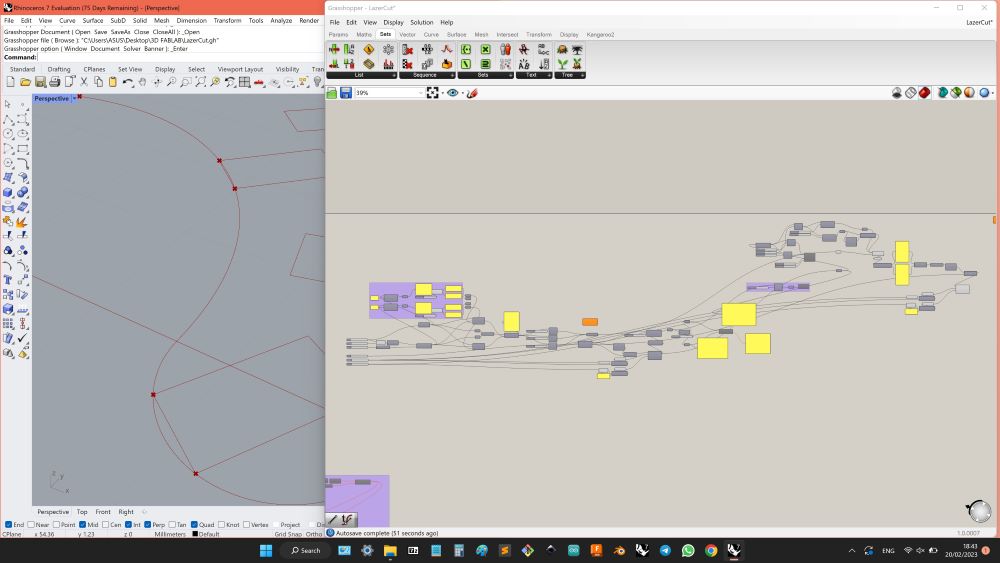
- Tried boolian difference, still did not work properly (worked only on concave part) even with aligned with contour new rectangales.
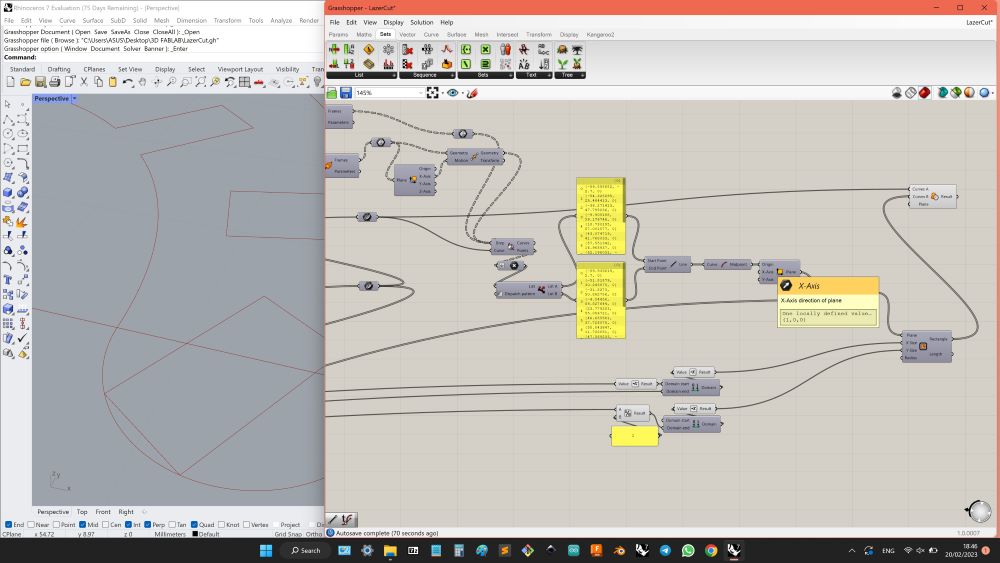
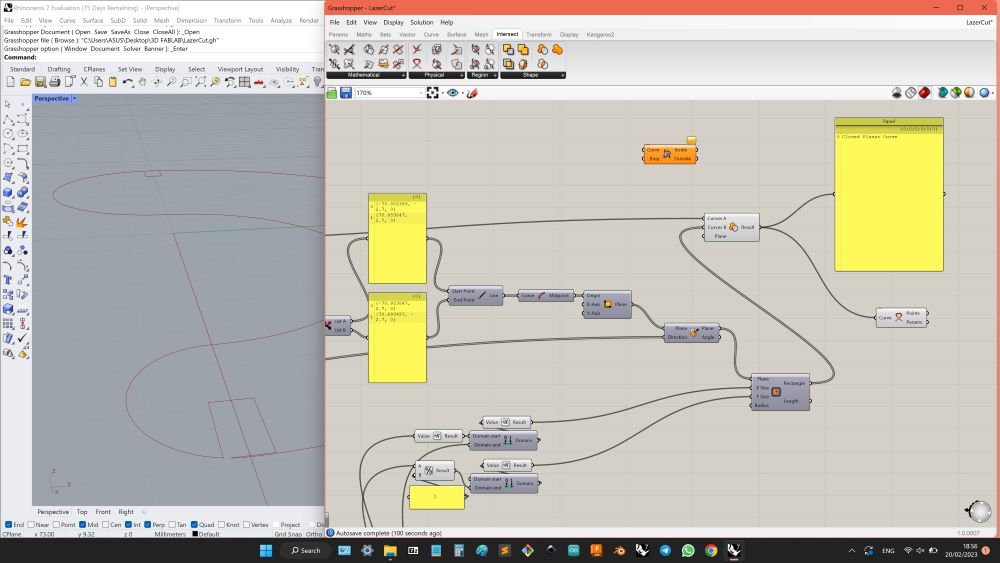
- Tried few ways to determine elements for trim.
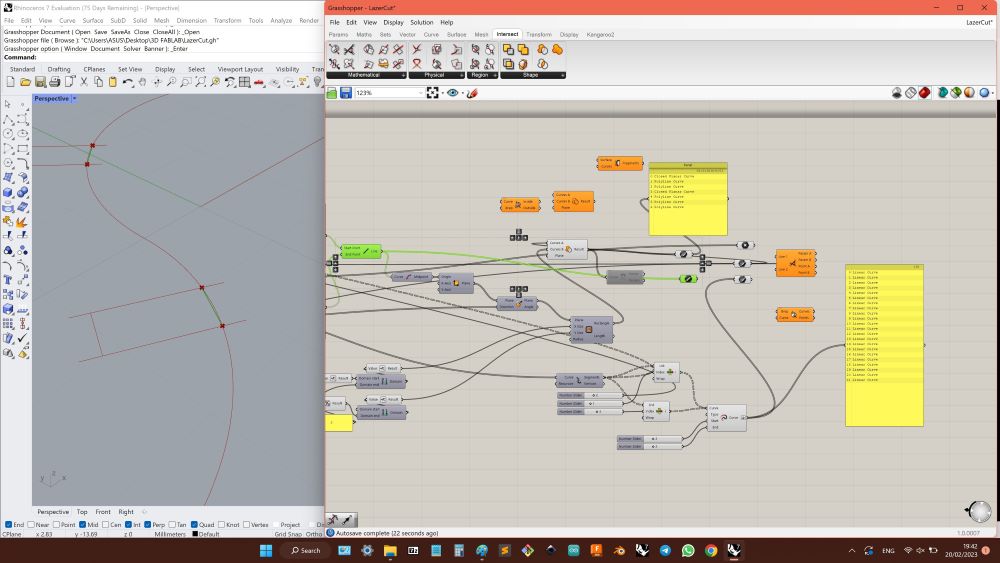
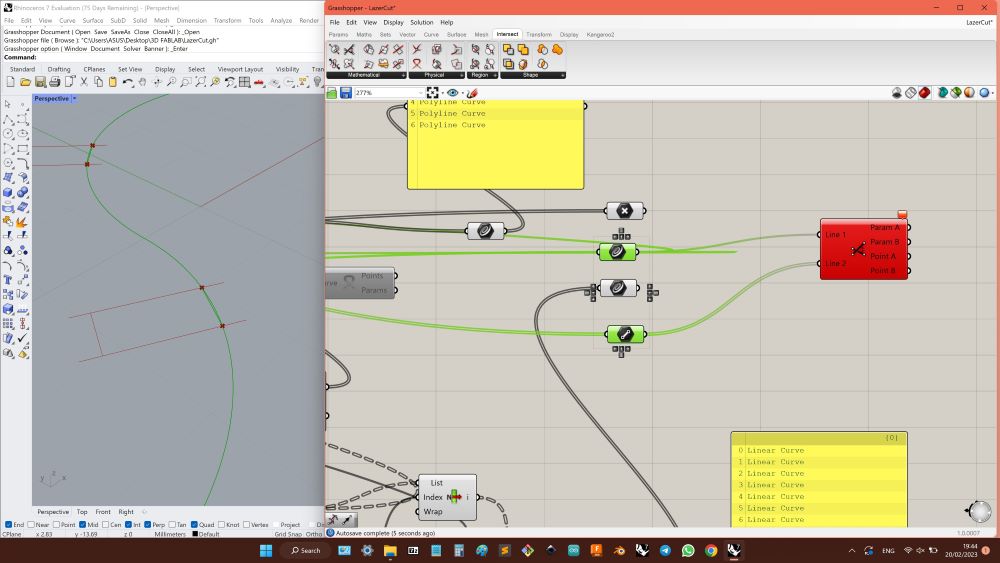
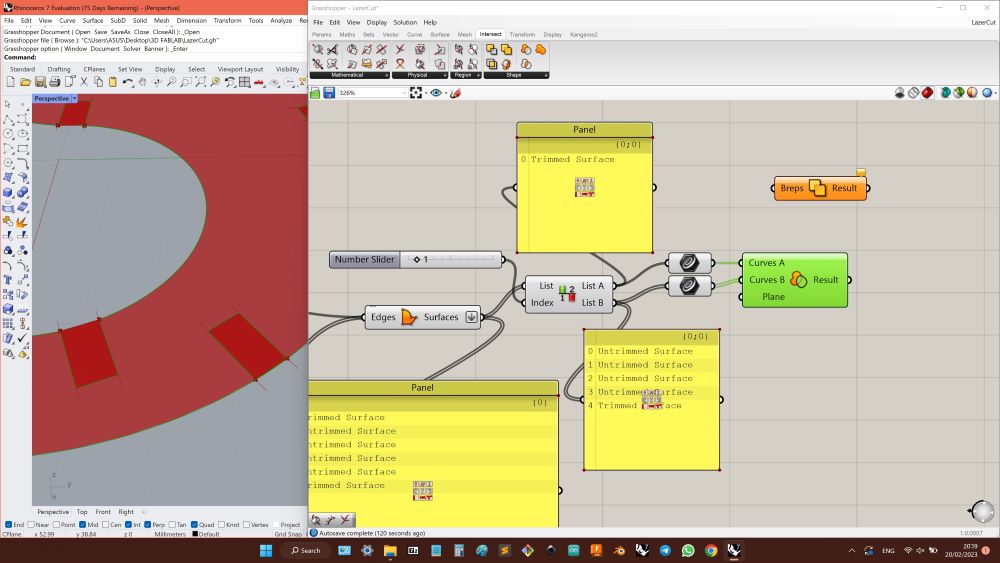
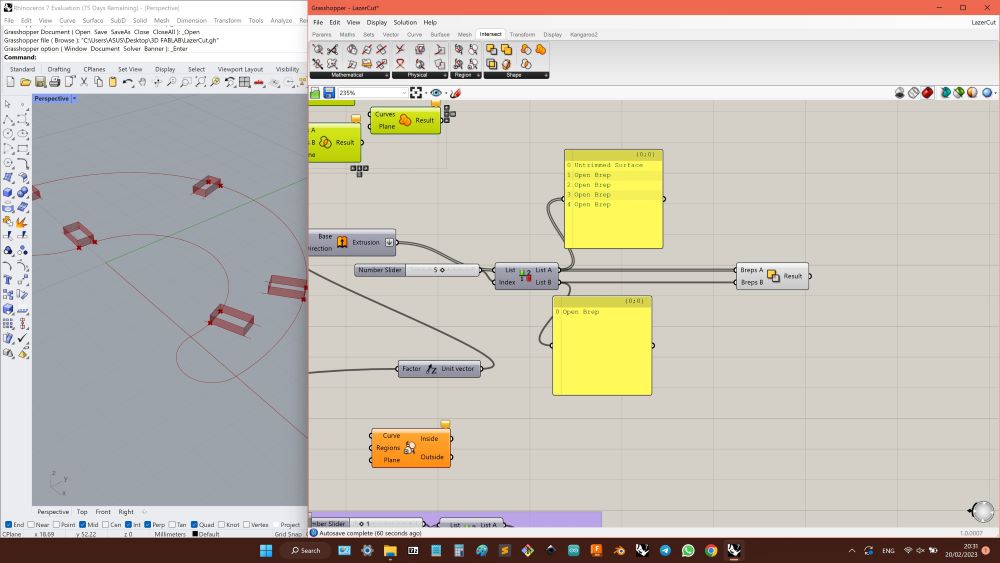
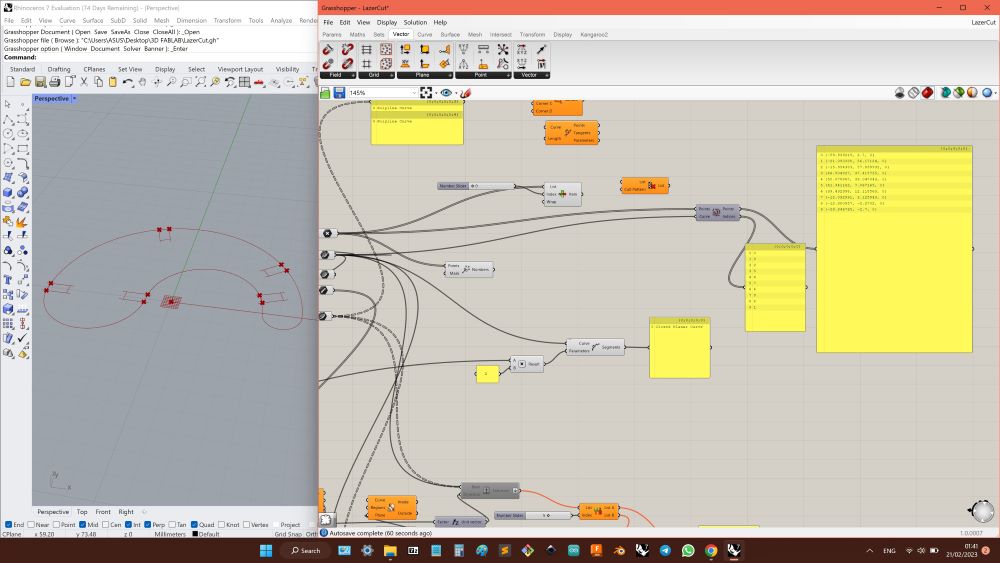
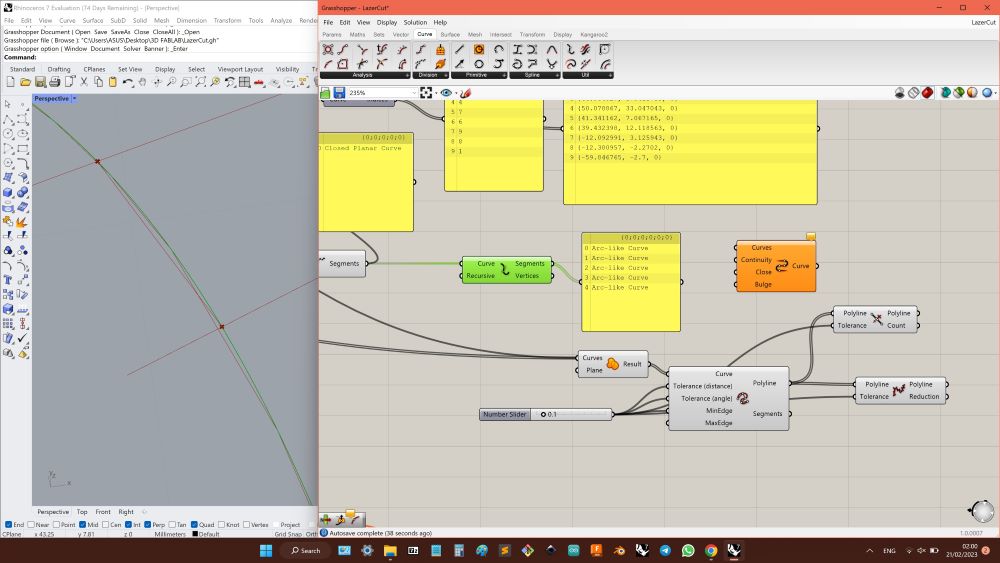
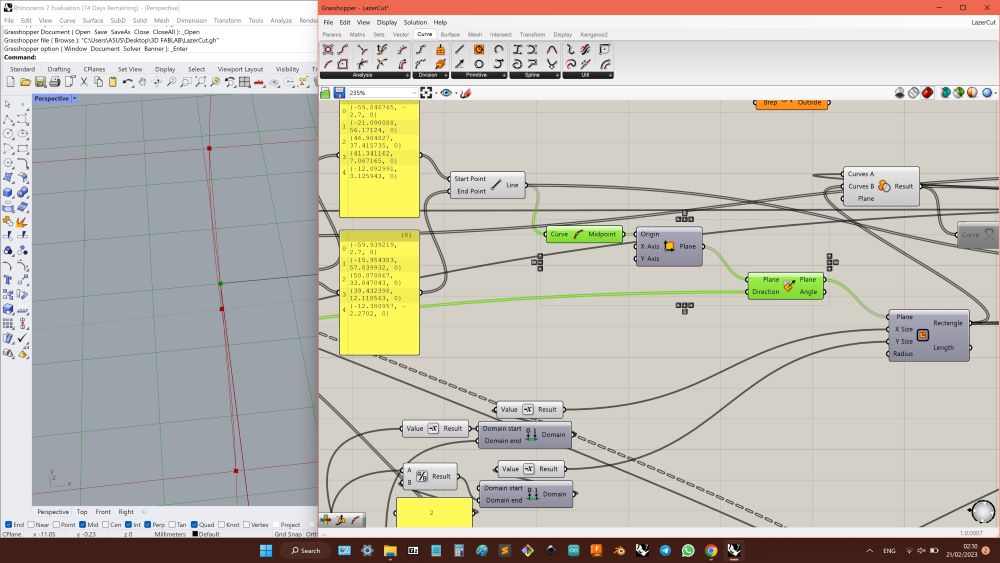
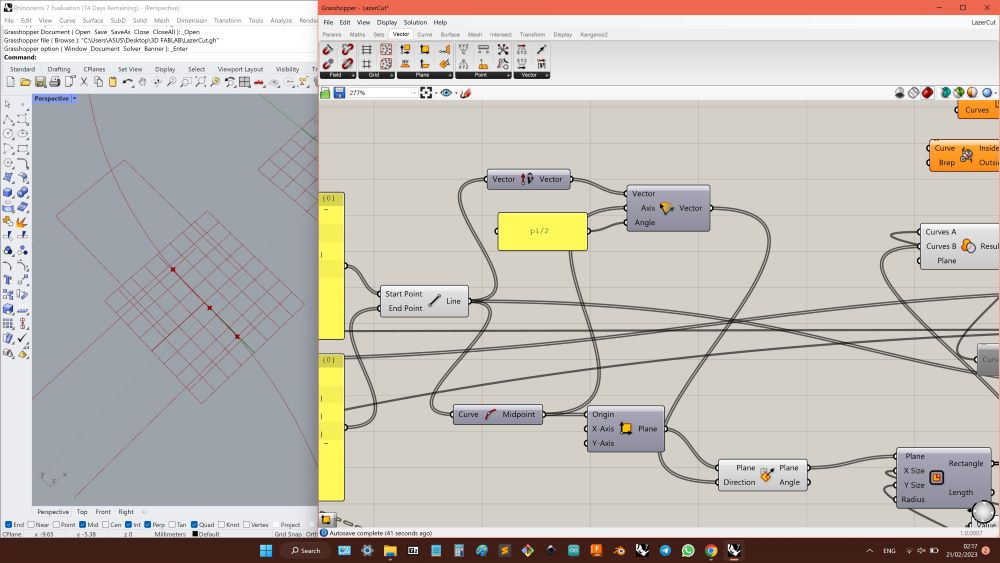
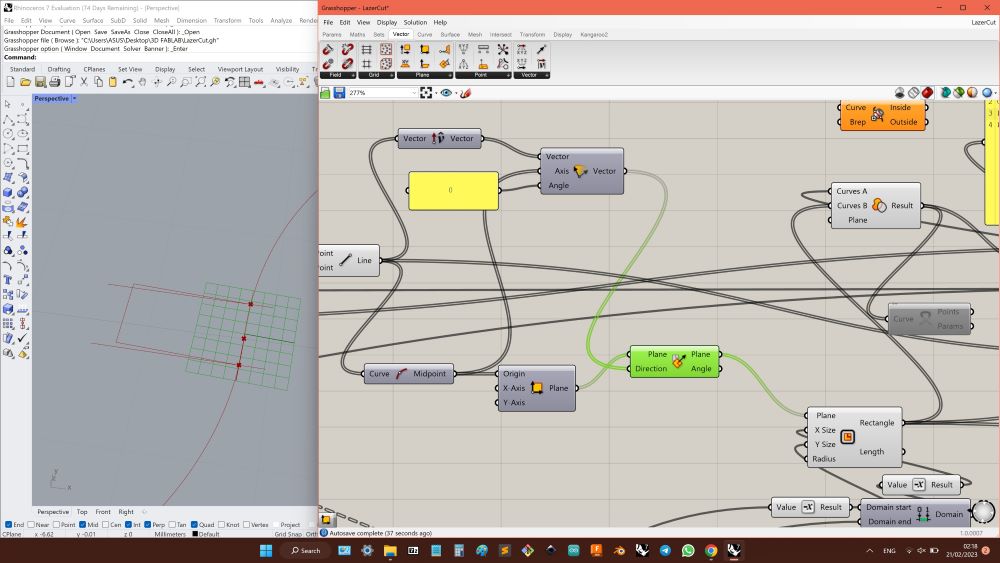
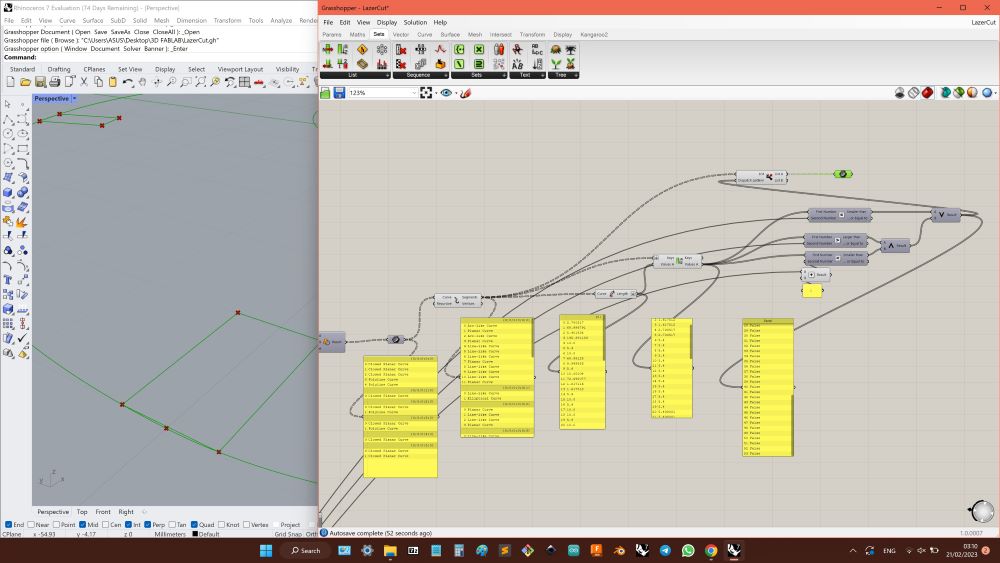
- Found way to split contour accurate, framing it by area aligned with rectangles.
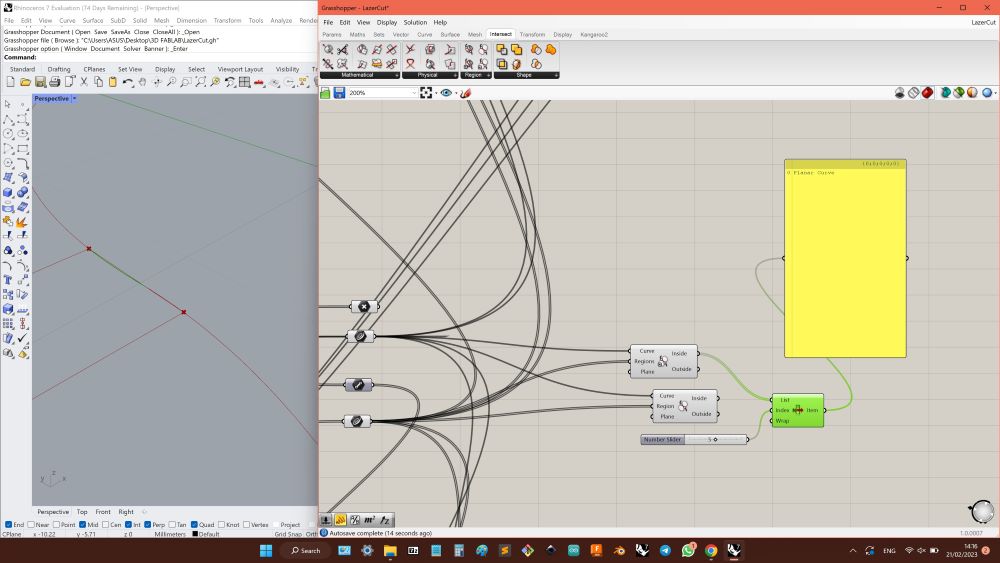
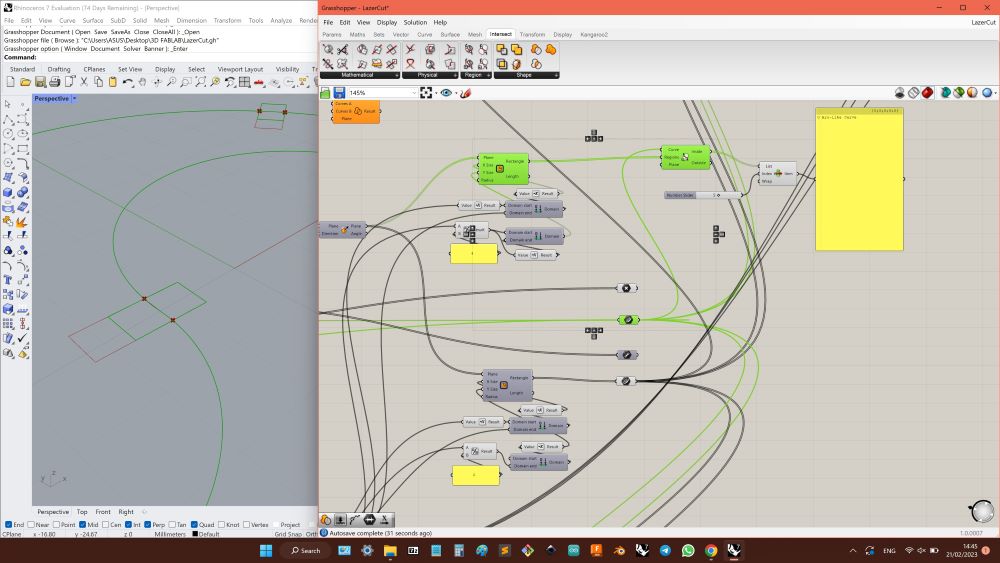
- Selected demanded curves and lines, joined, tried to fillet engeles, but it worked only with 90 degrees angles.
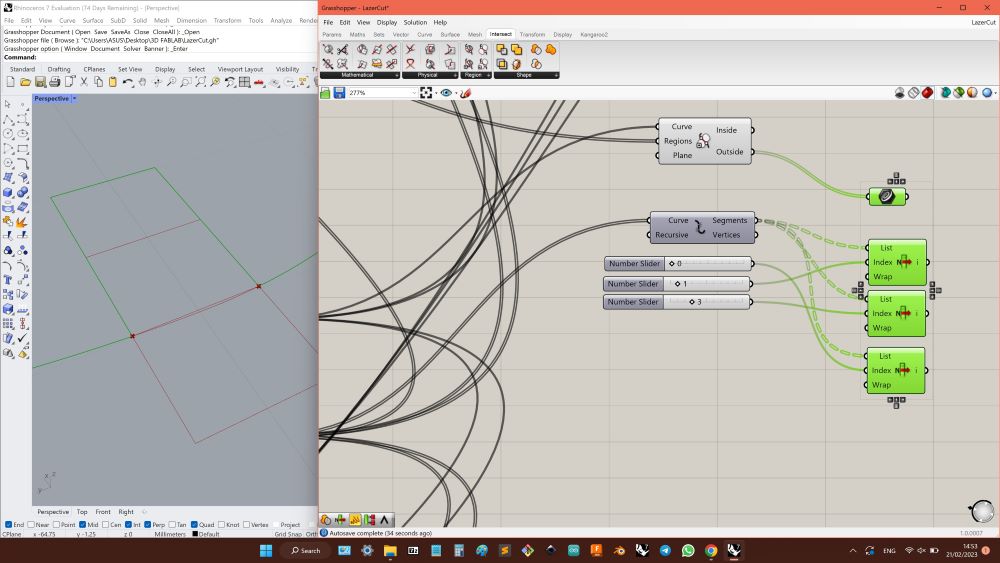
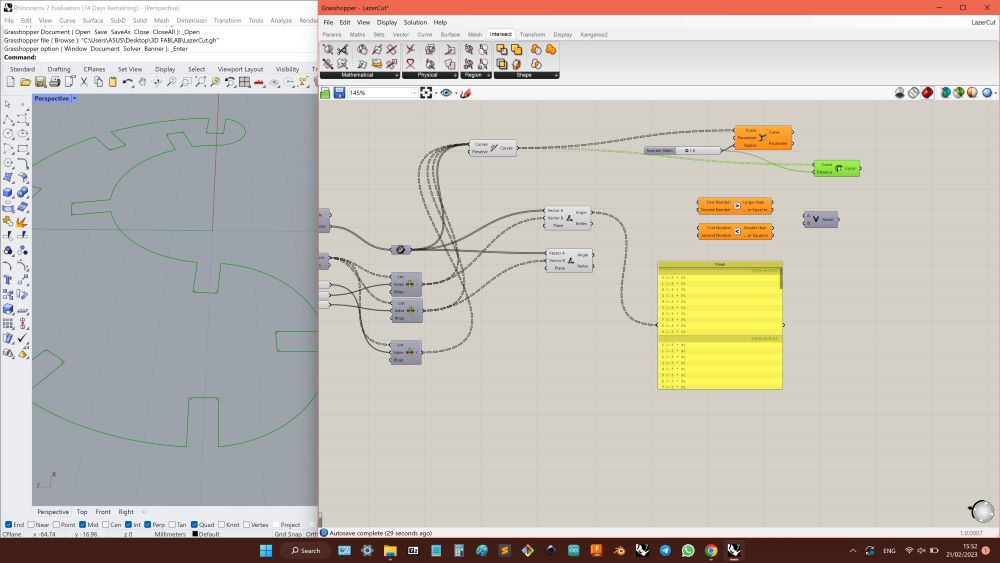
- Desided to use same tactic of lines intercection for fillets points determination, but faced problem of points lists organisation. Tried different manipulations with lists and data trees, but did not succeed in dispatching points for start ana end points input.
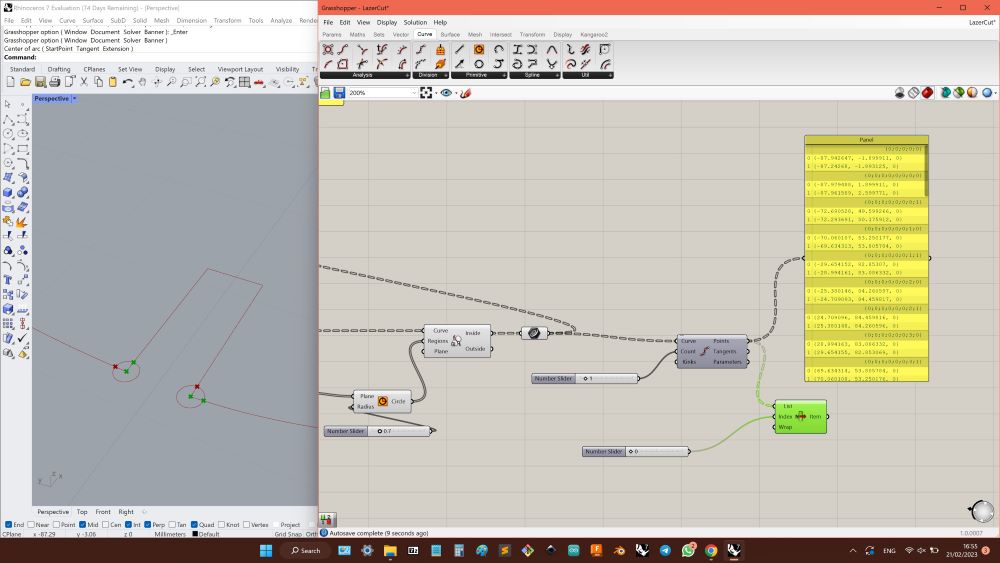
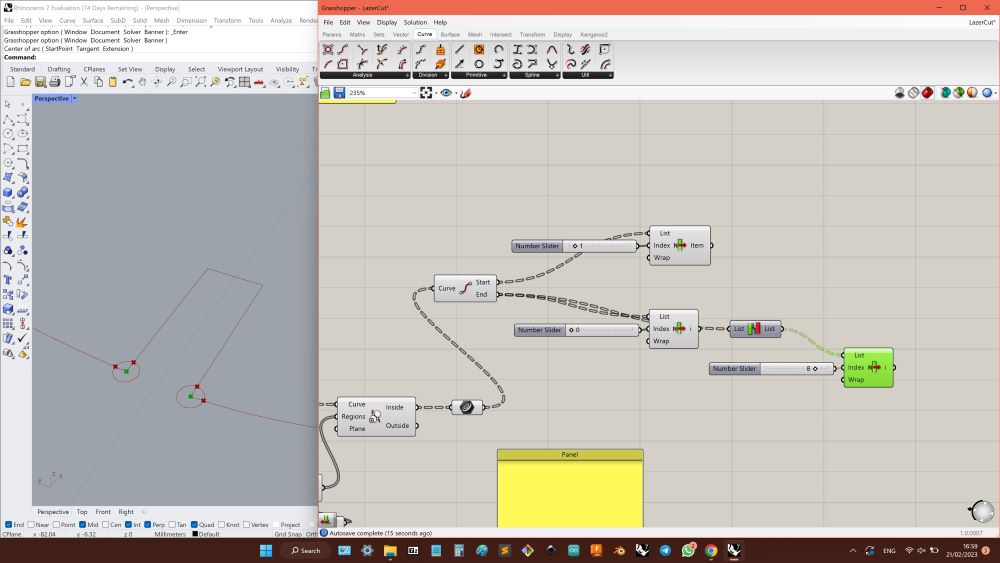
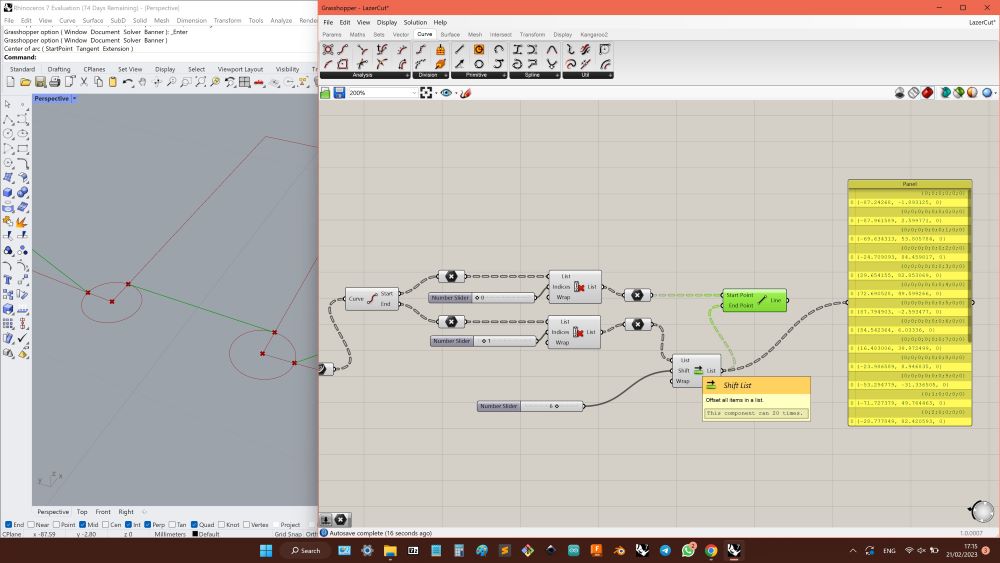
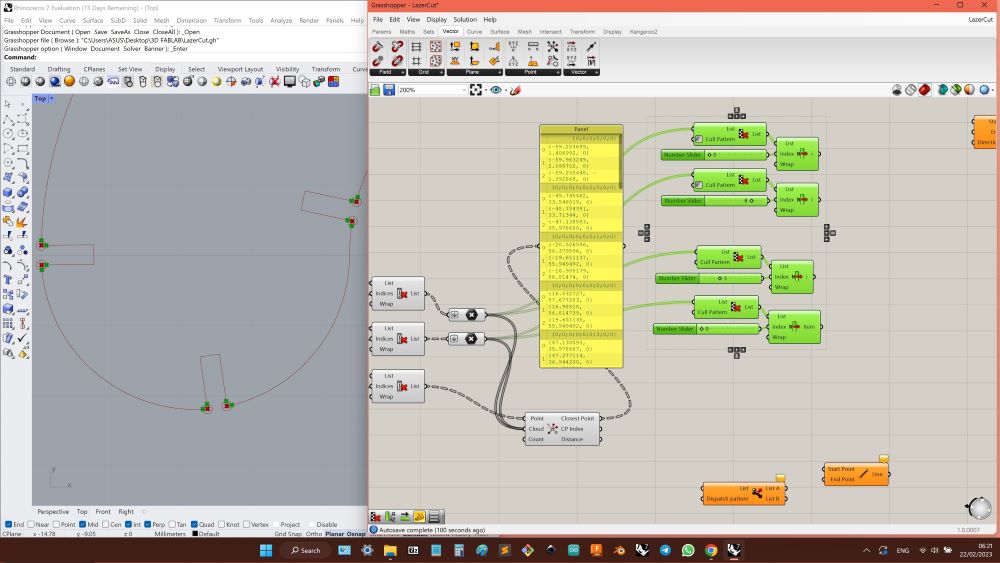
- Probably need try to create internal contour and use closest point function.
Cut process
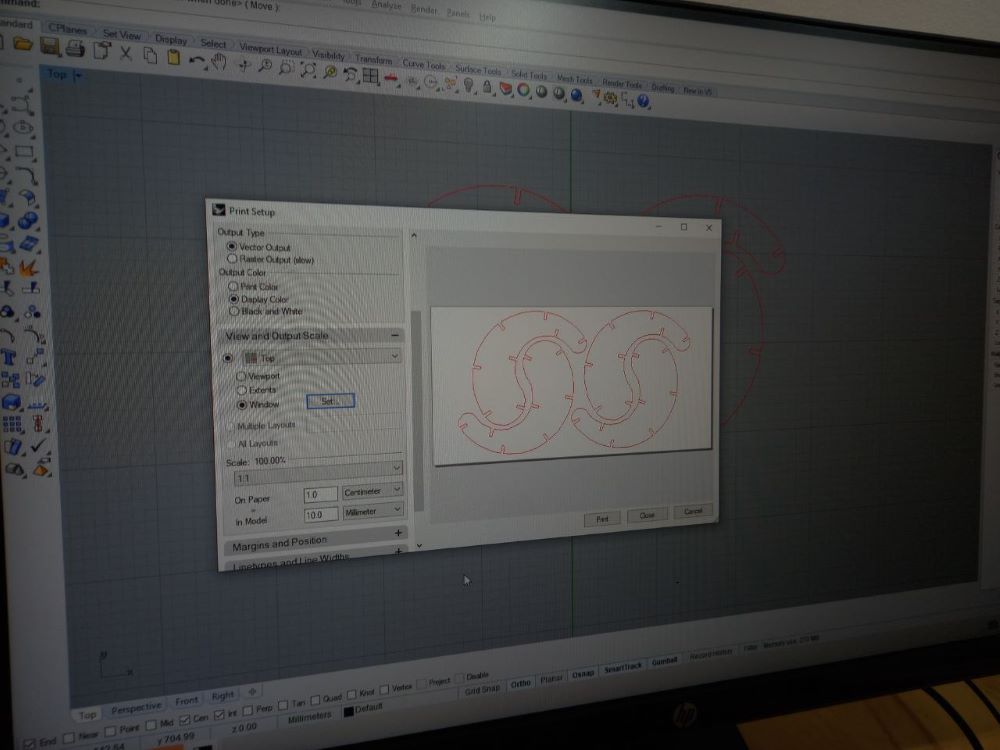
- In result decided bake contour and do "Fillet Edge" manualy
- By "CTRL" + "P" opened window to set details with workingzone projection, "Print" to use soft for Laser.
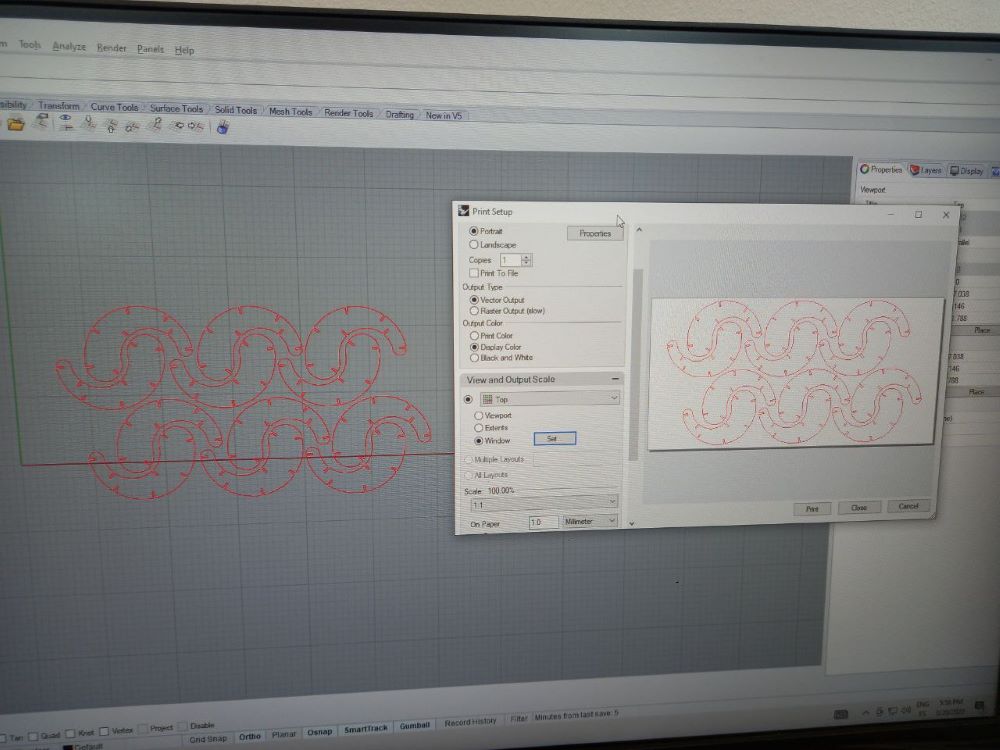
- But width of joints was wrong at Grasshopper, also used small laser, so till fixing reduced the size of details.
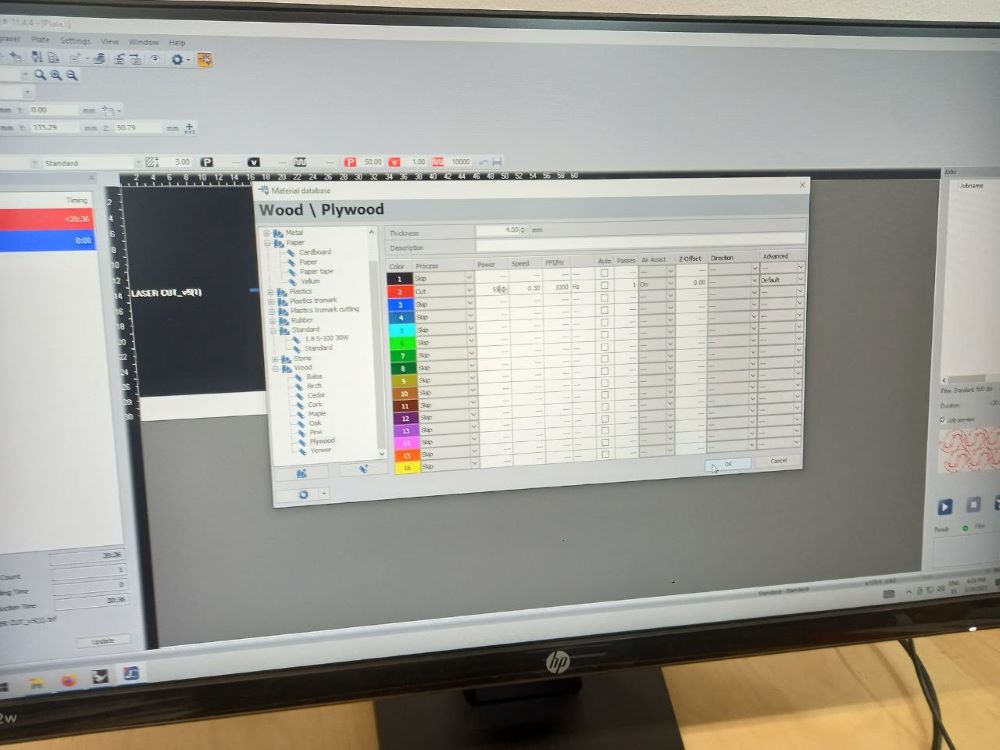
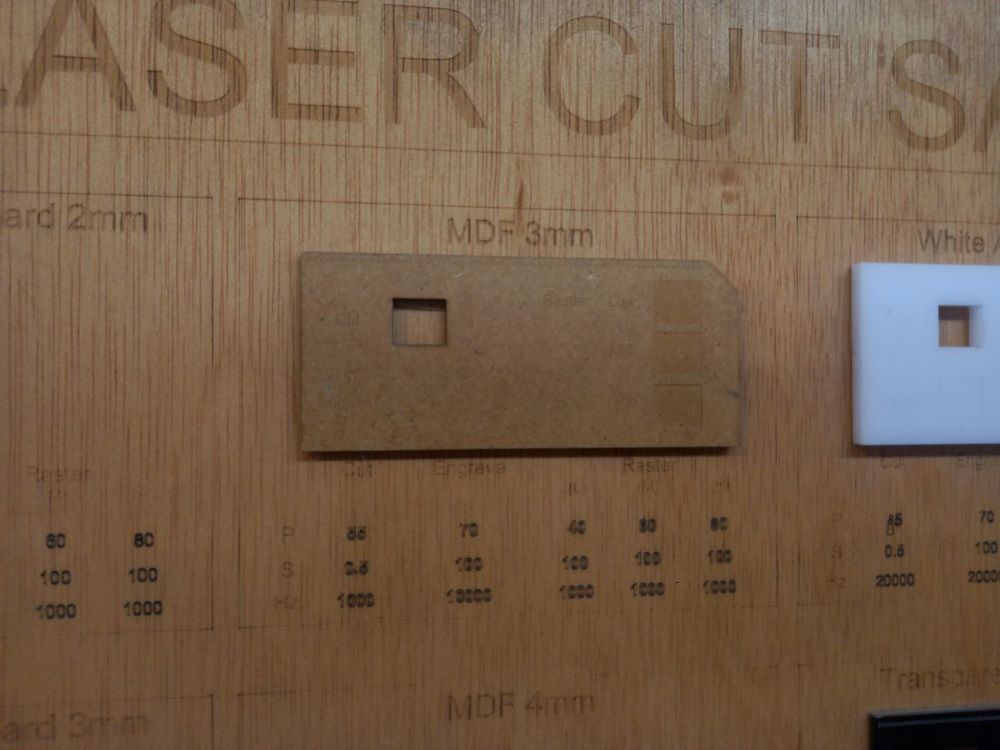
- Set cut properties.
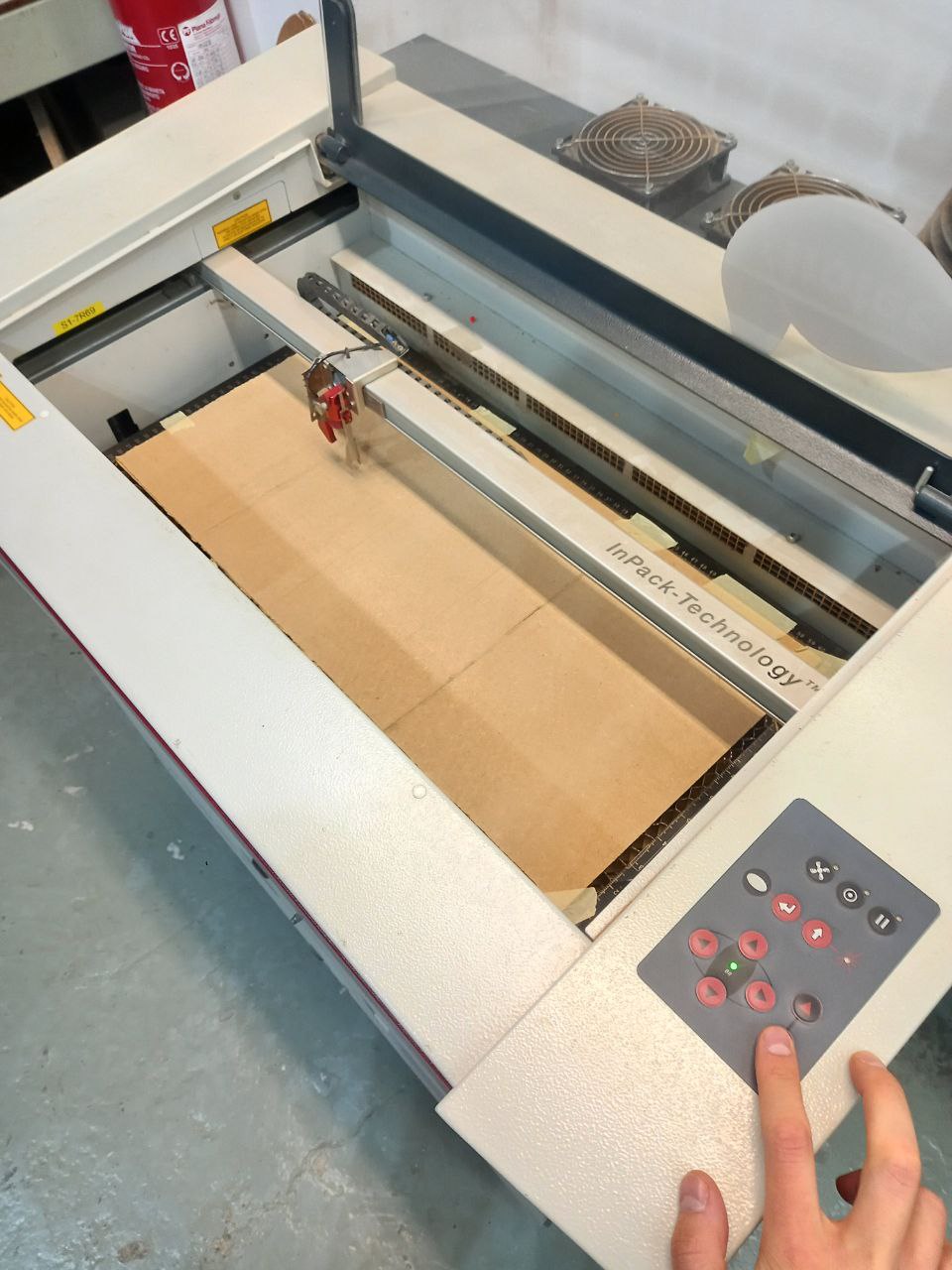
- Defined Z-axis of origin by callibration tool.
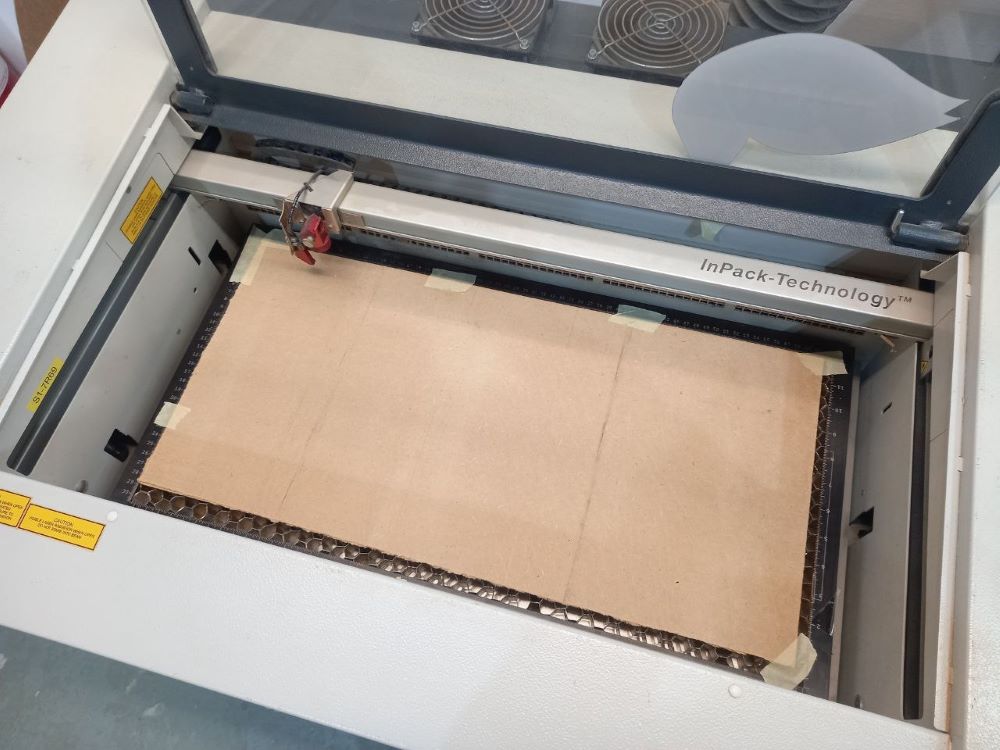
- Used tape to make material more plane.
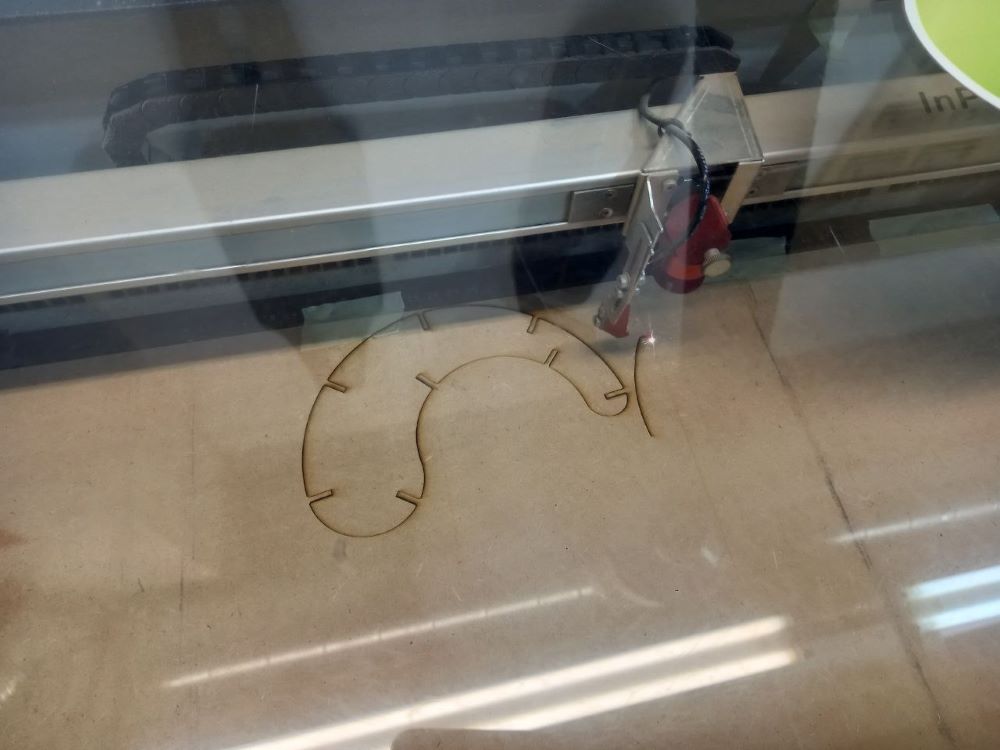
- Laser started.
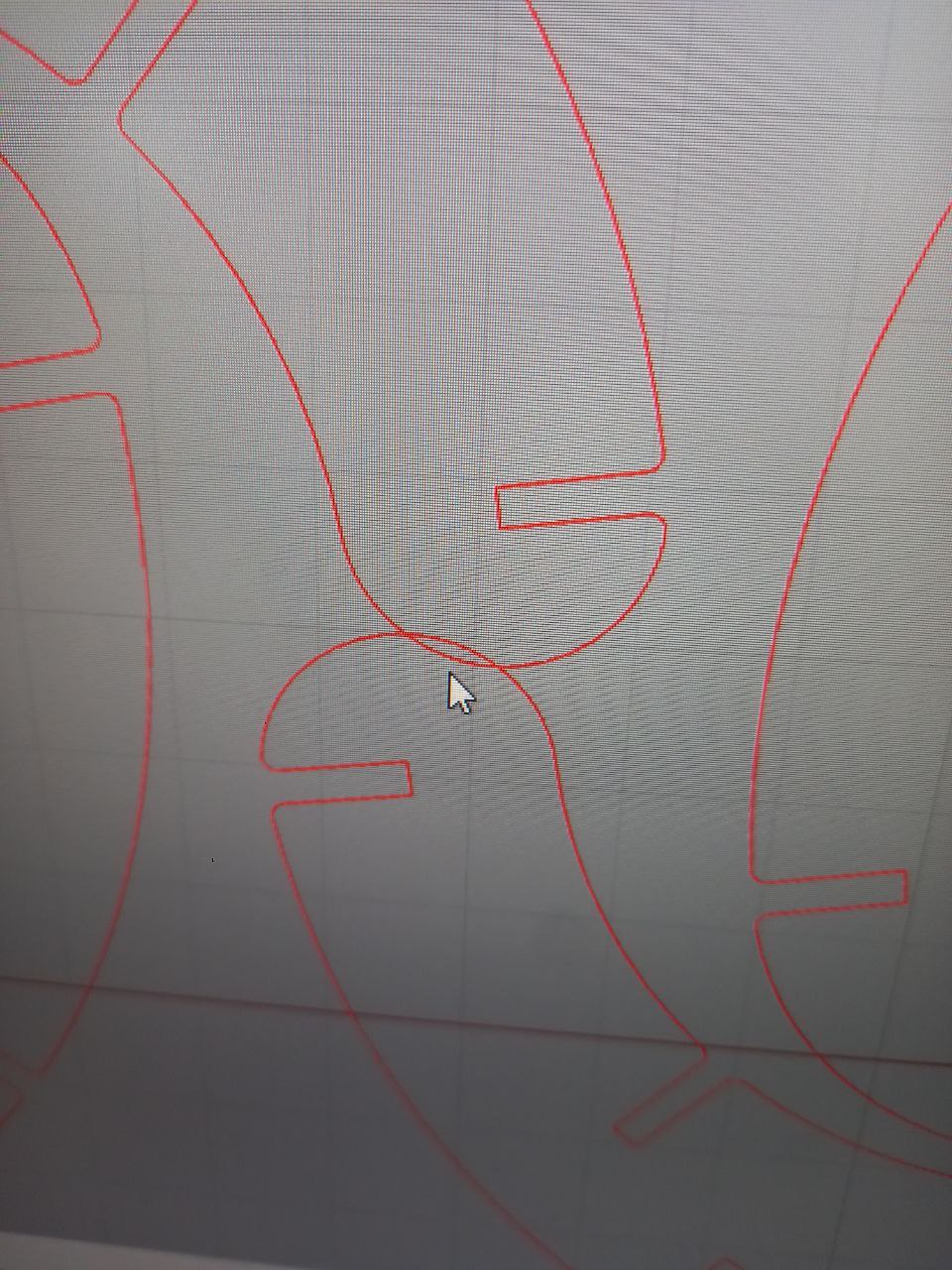
- In process explored that little bit intersected details during stuffing.
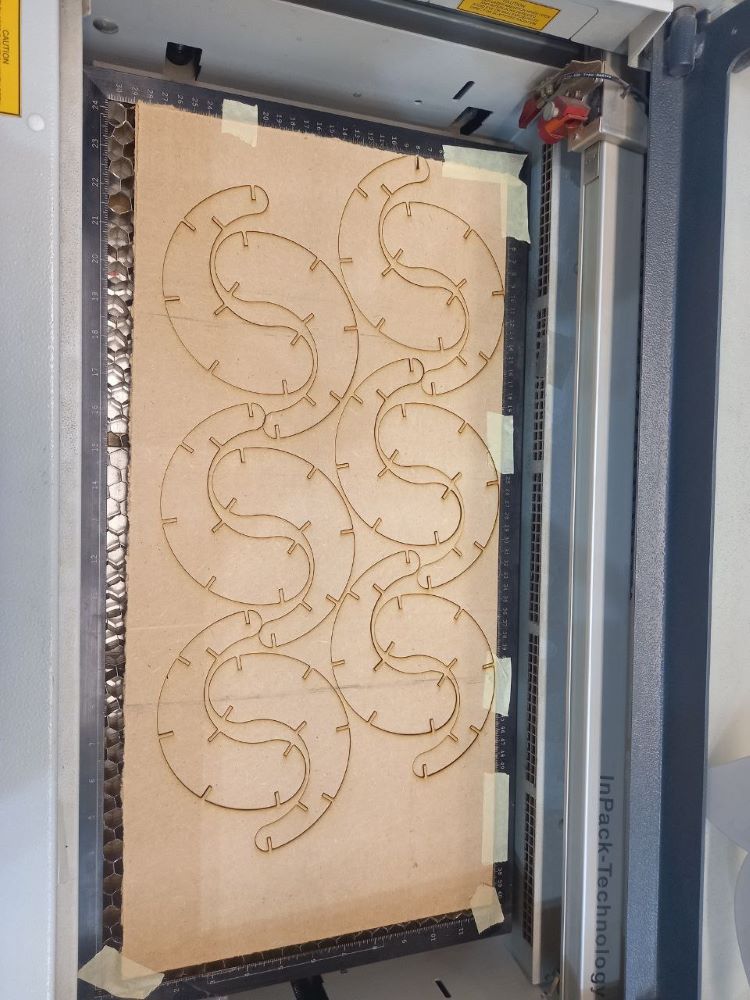
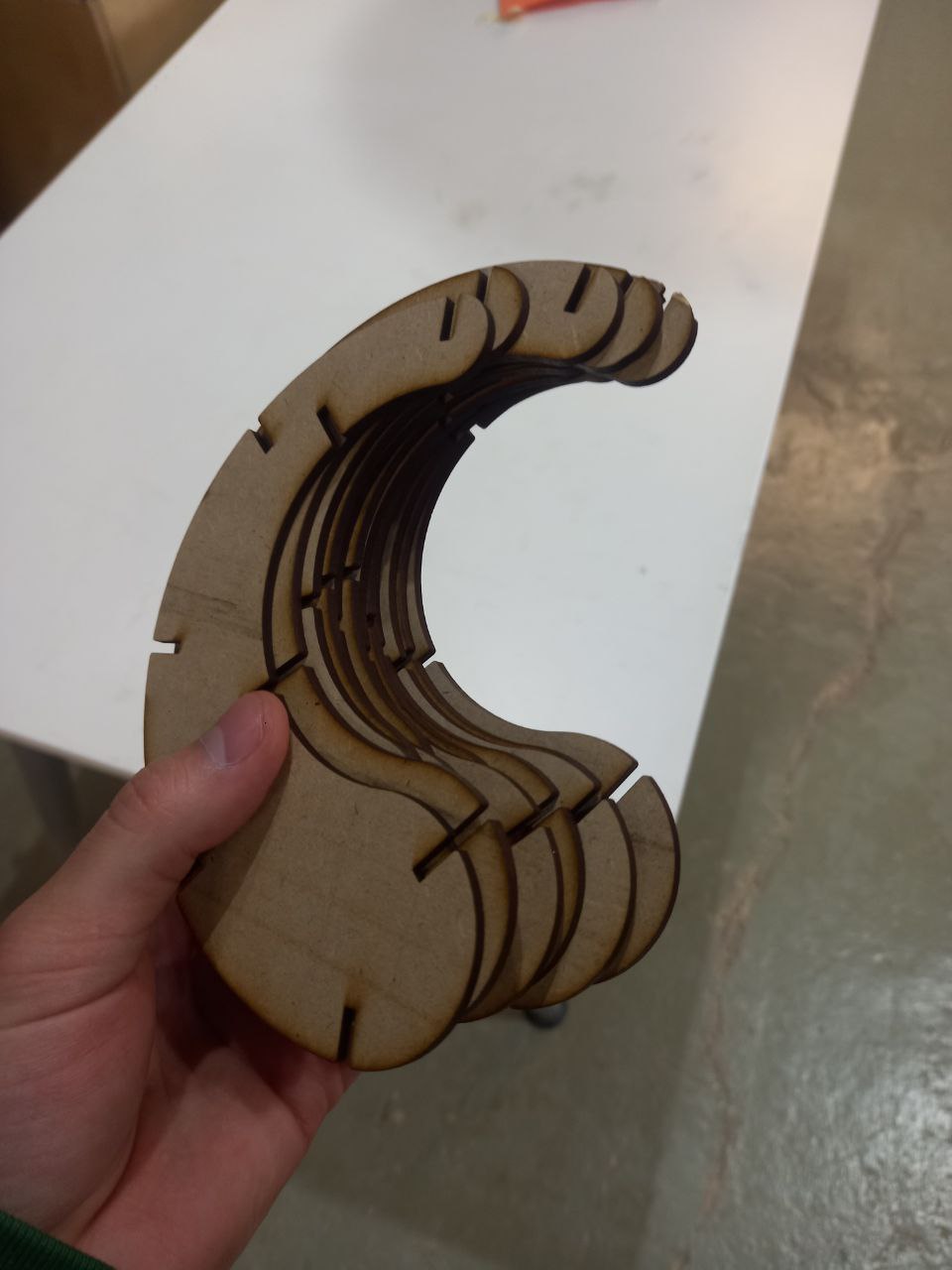
- Complite.
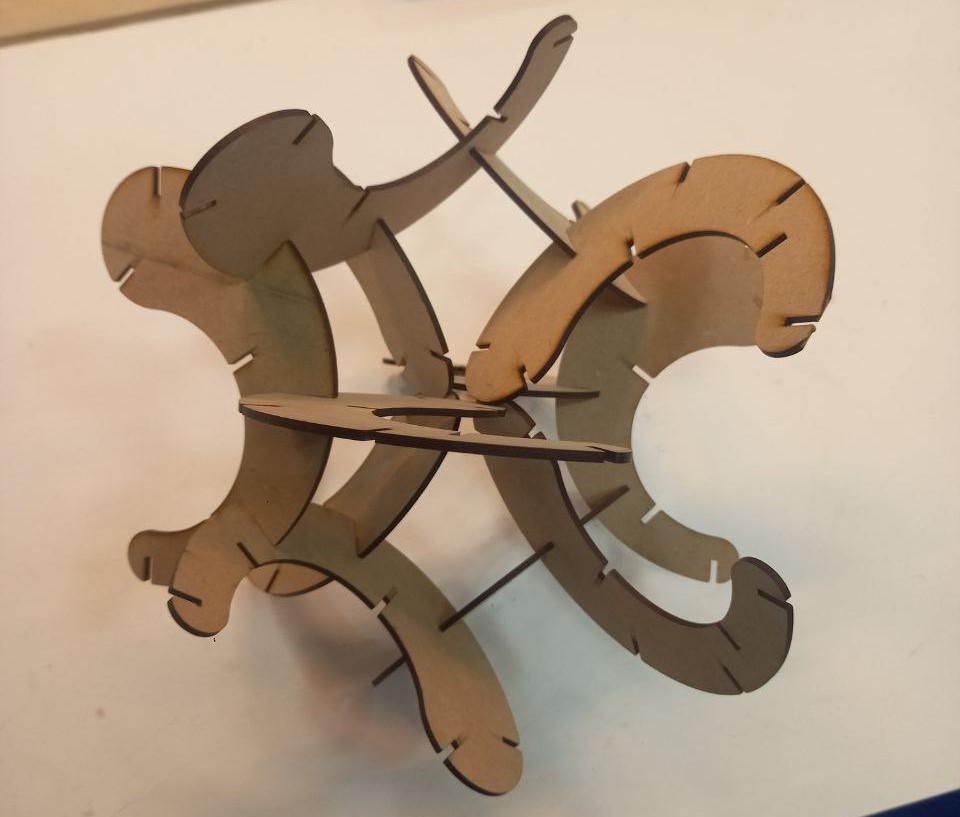
- Actualy parametric frames are too extinctive and not cuclutated for full form potential realisation.
Ploter
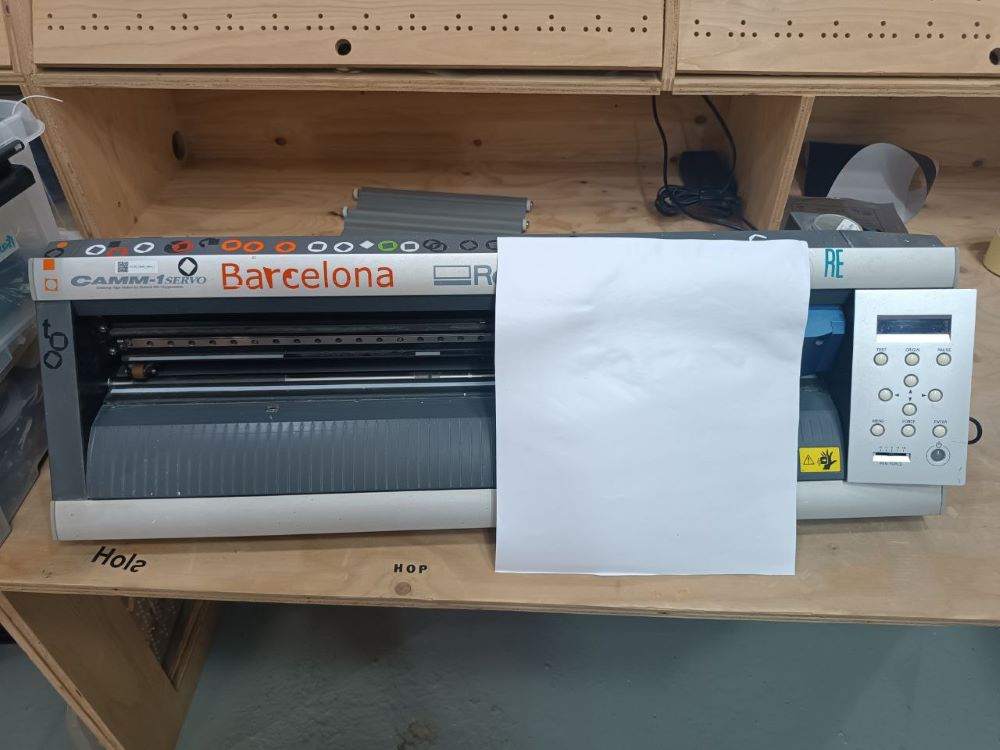
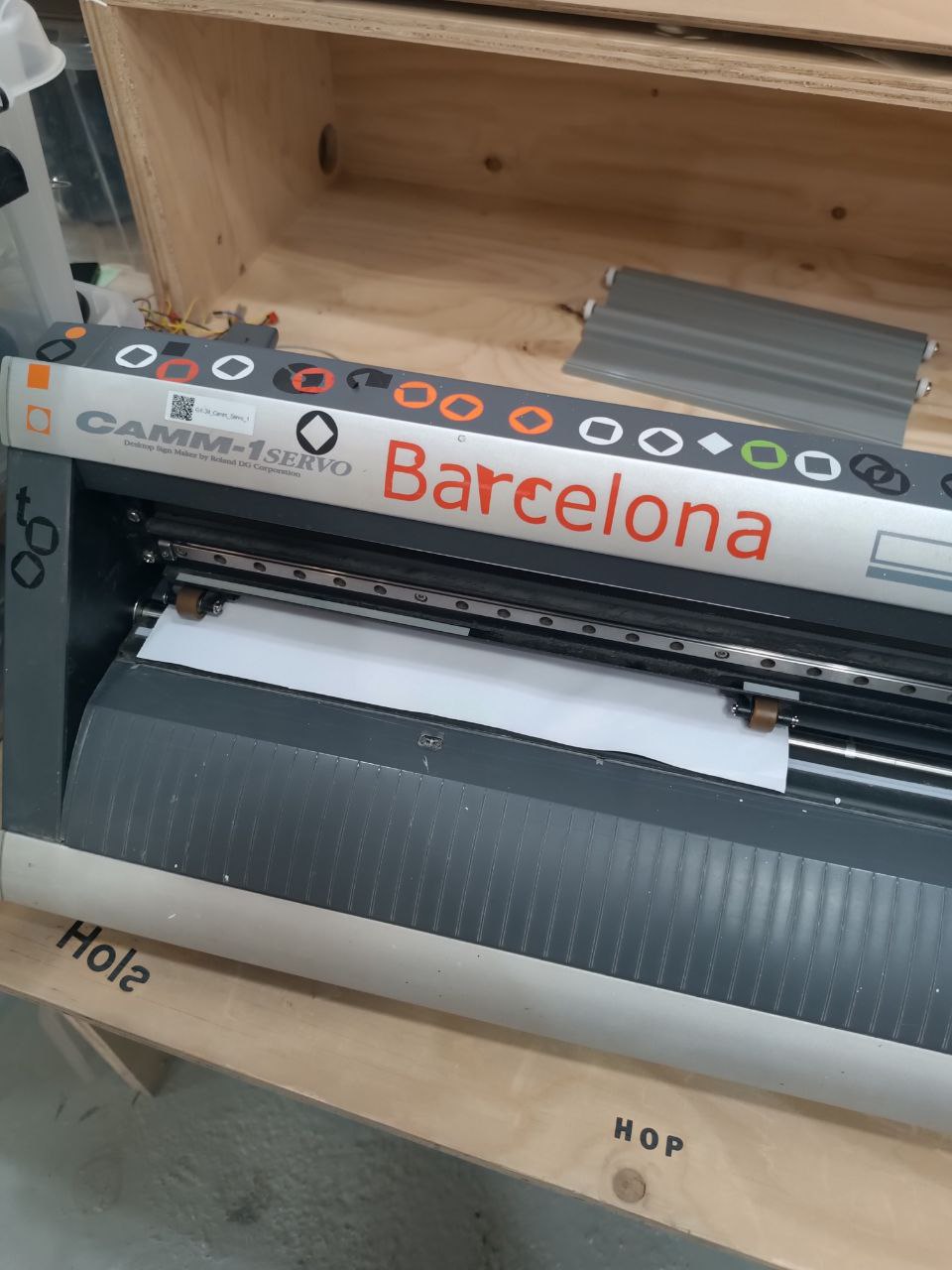
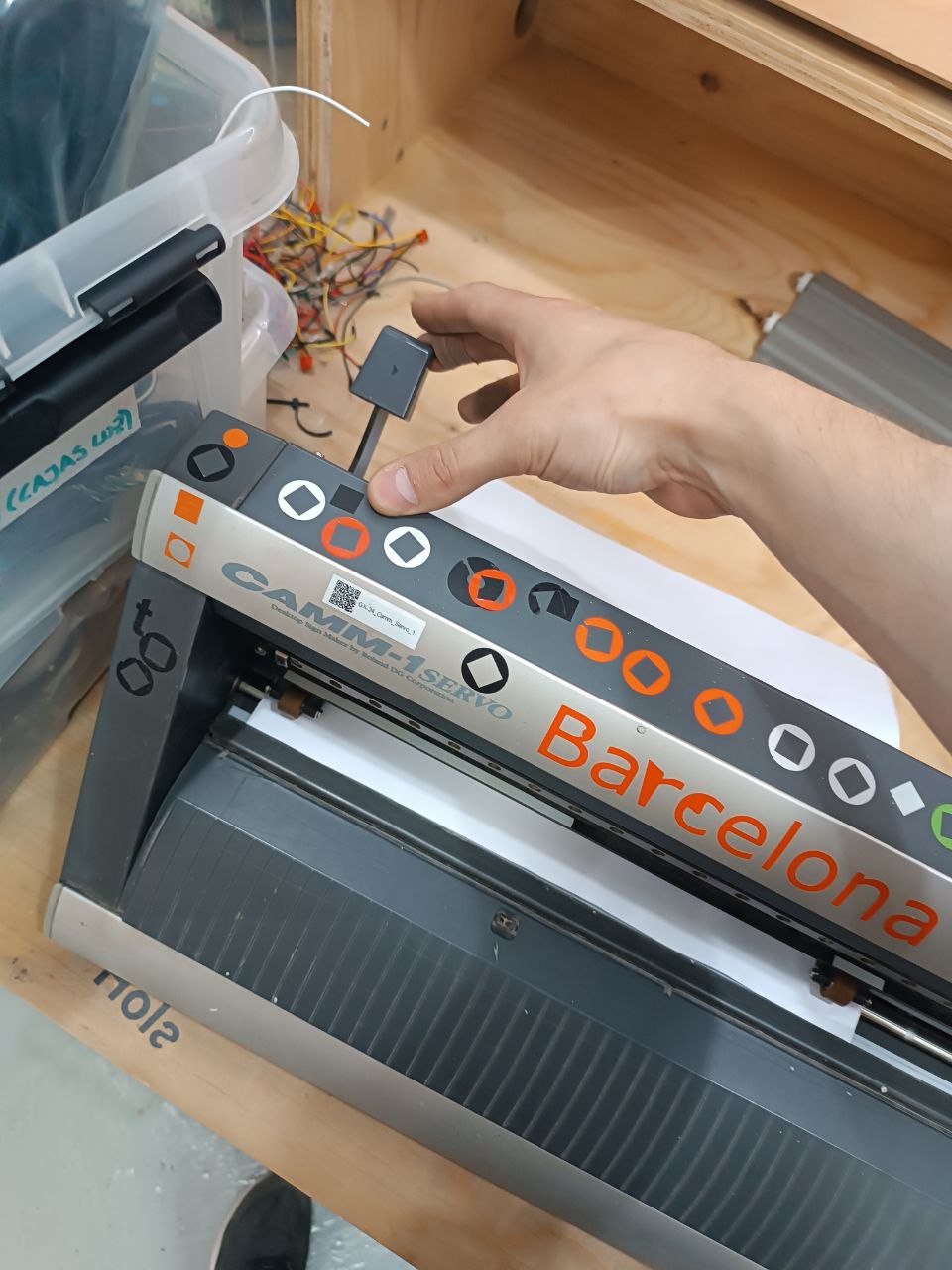
- Placed vinyl film, aligned rollers with white marked zones, fixed.
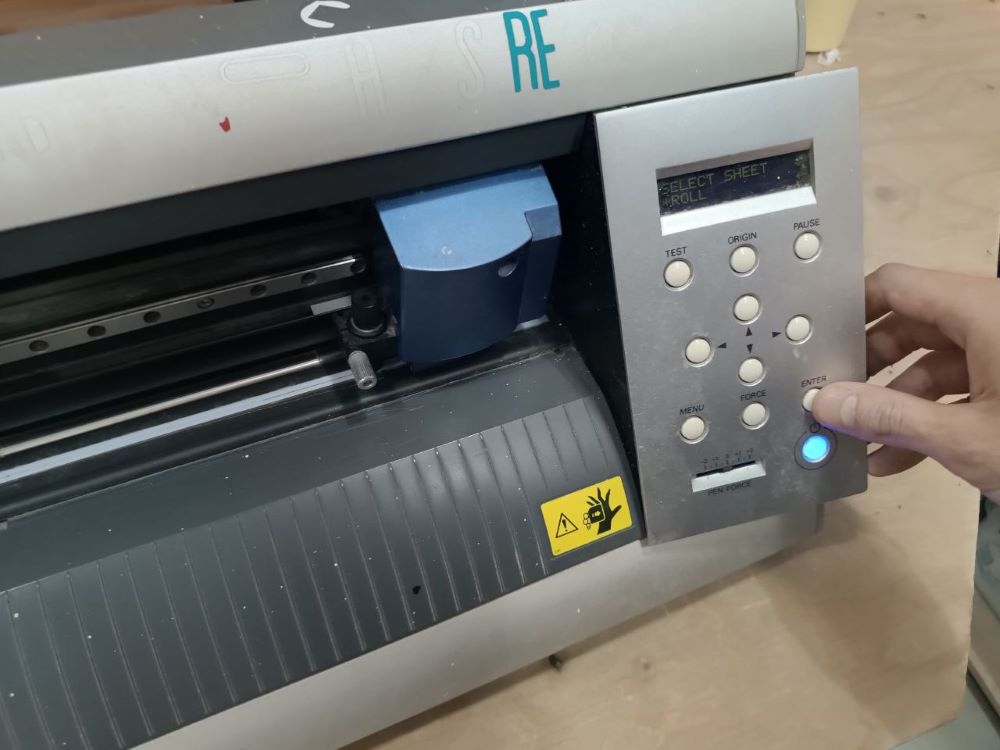
- About second continuty push needed for on/off button, also for enter button to home blade.
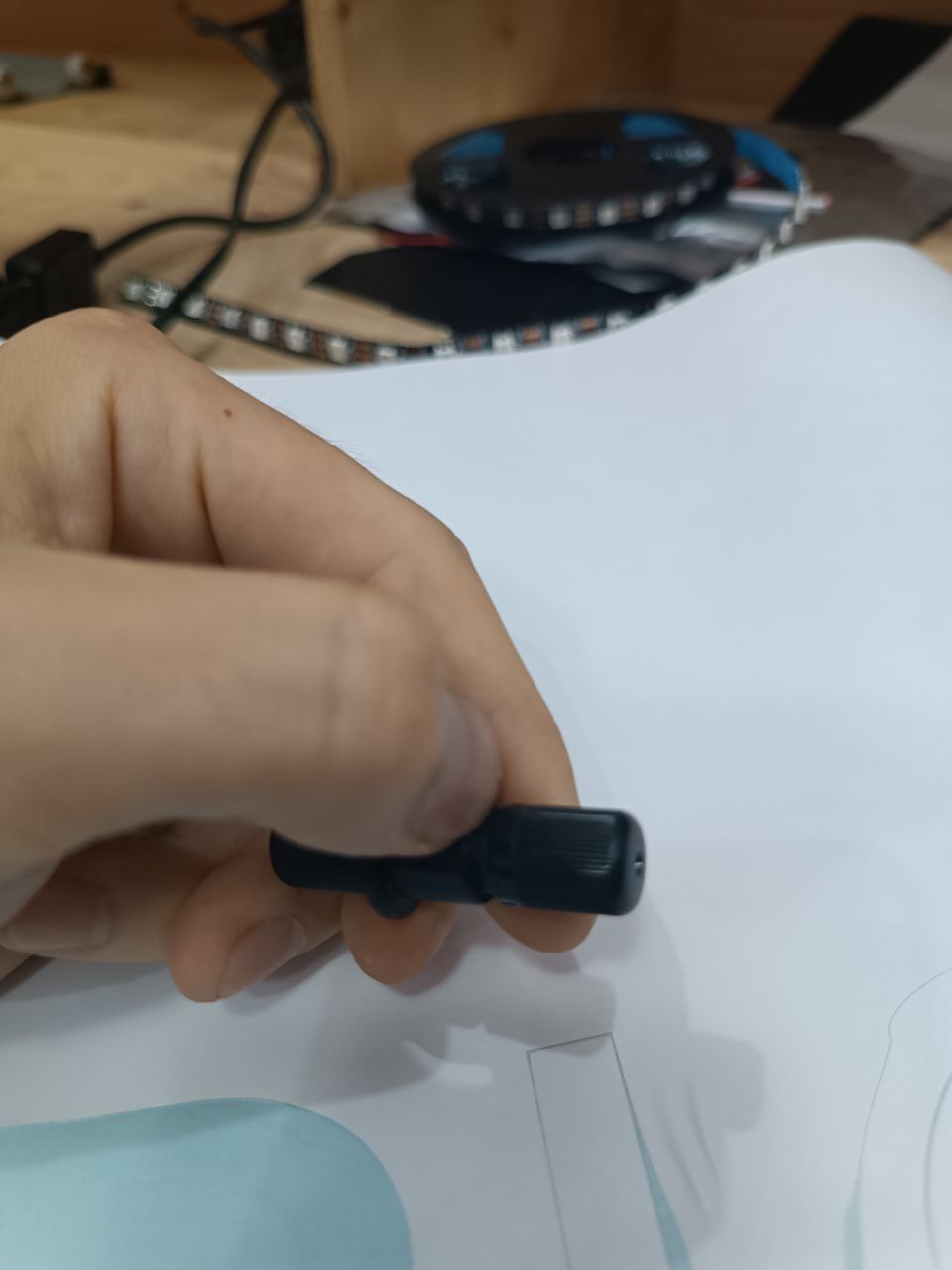
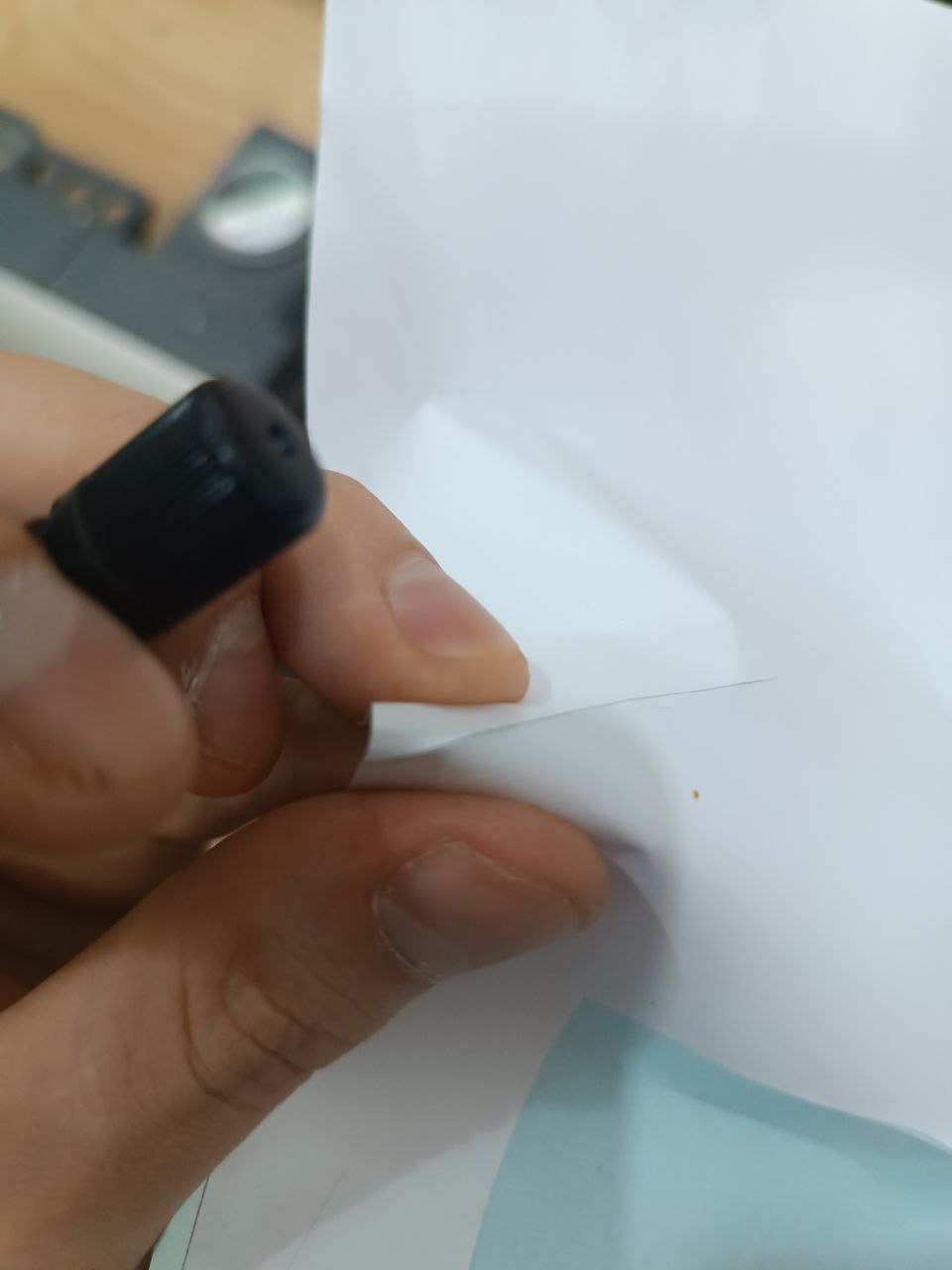
- Setted blade length by rotating sleeve, have to cut vinyl film, but not cut through base sheet, done.
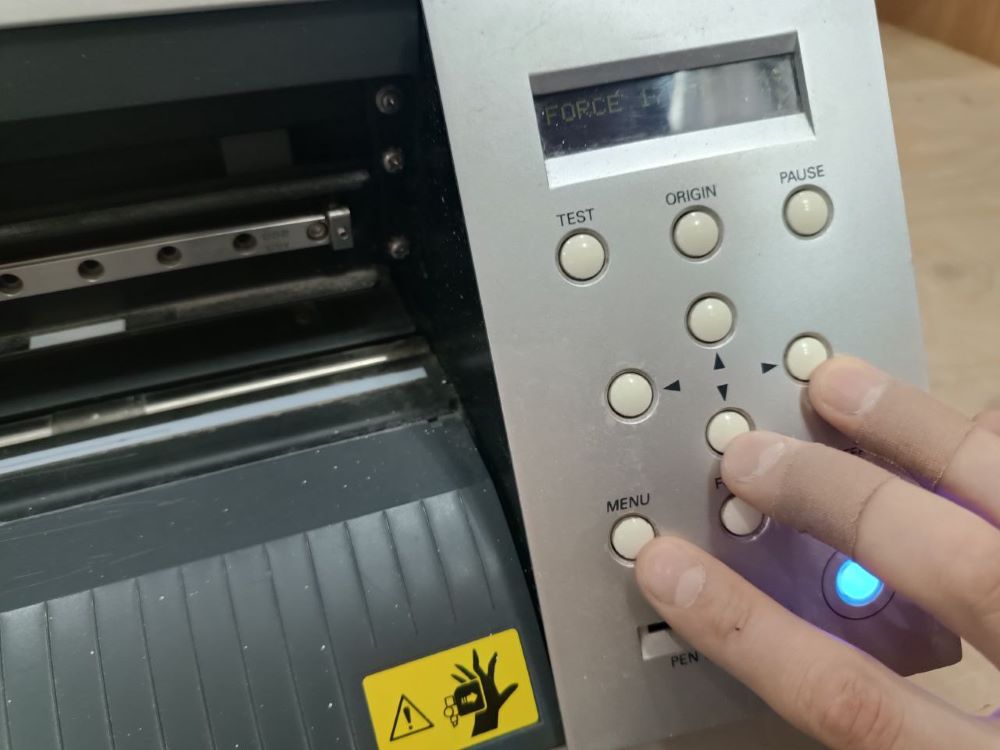
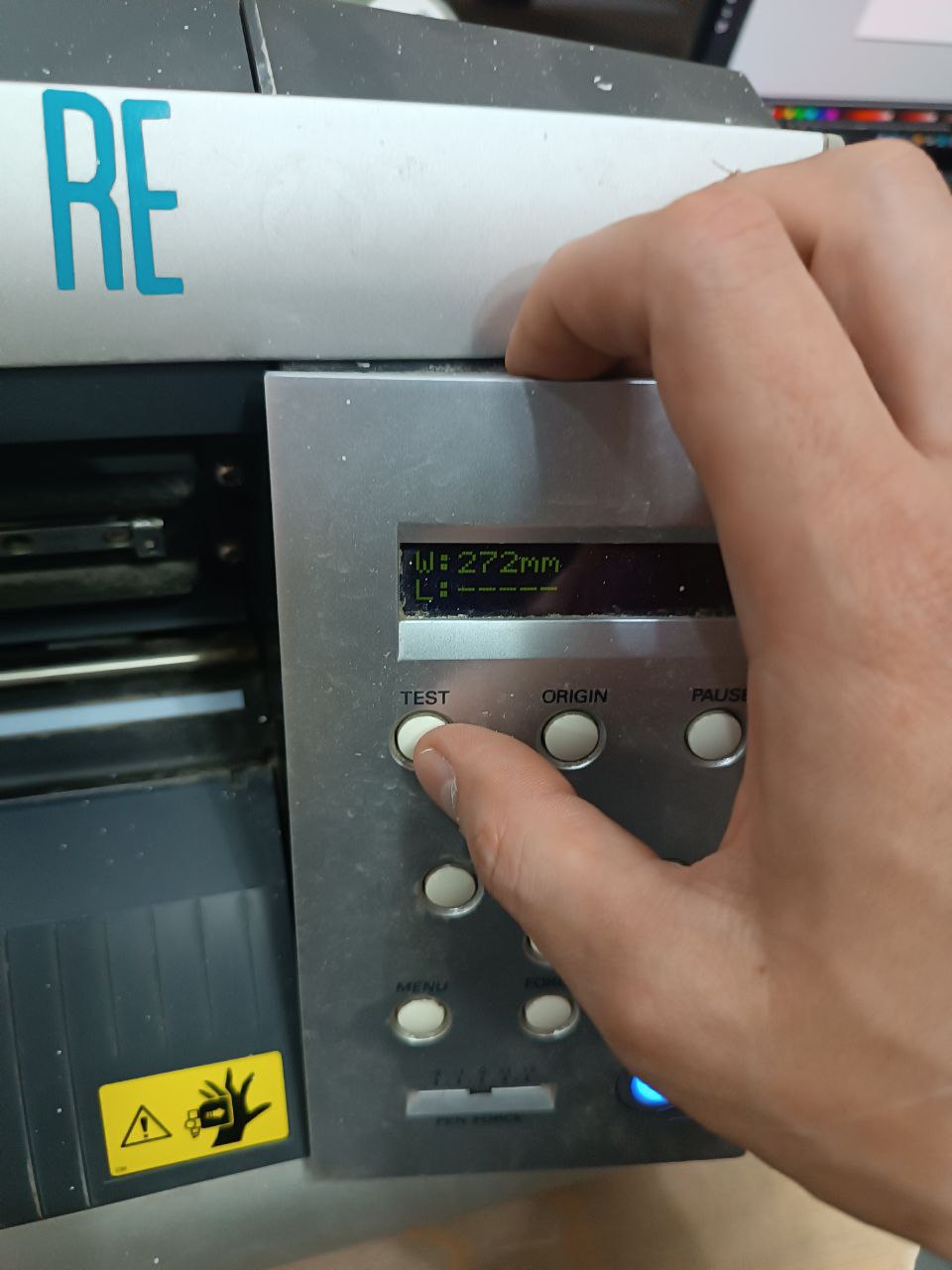
- Setted force (depending on material) and speed (depending on detalisation) by menu and arrows buttons.
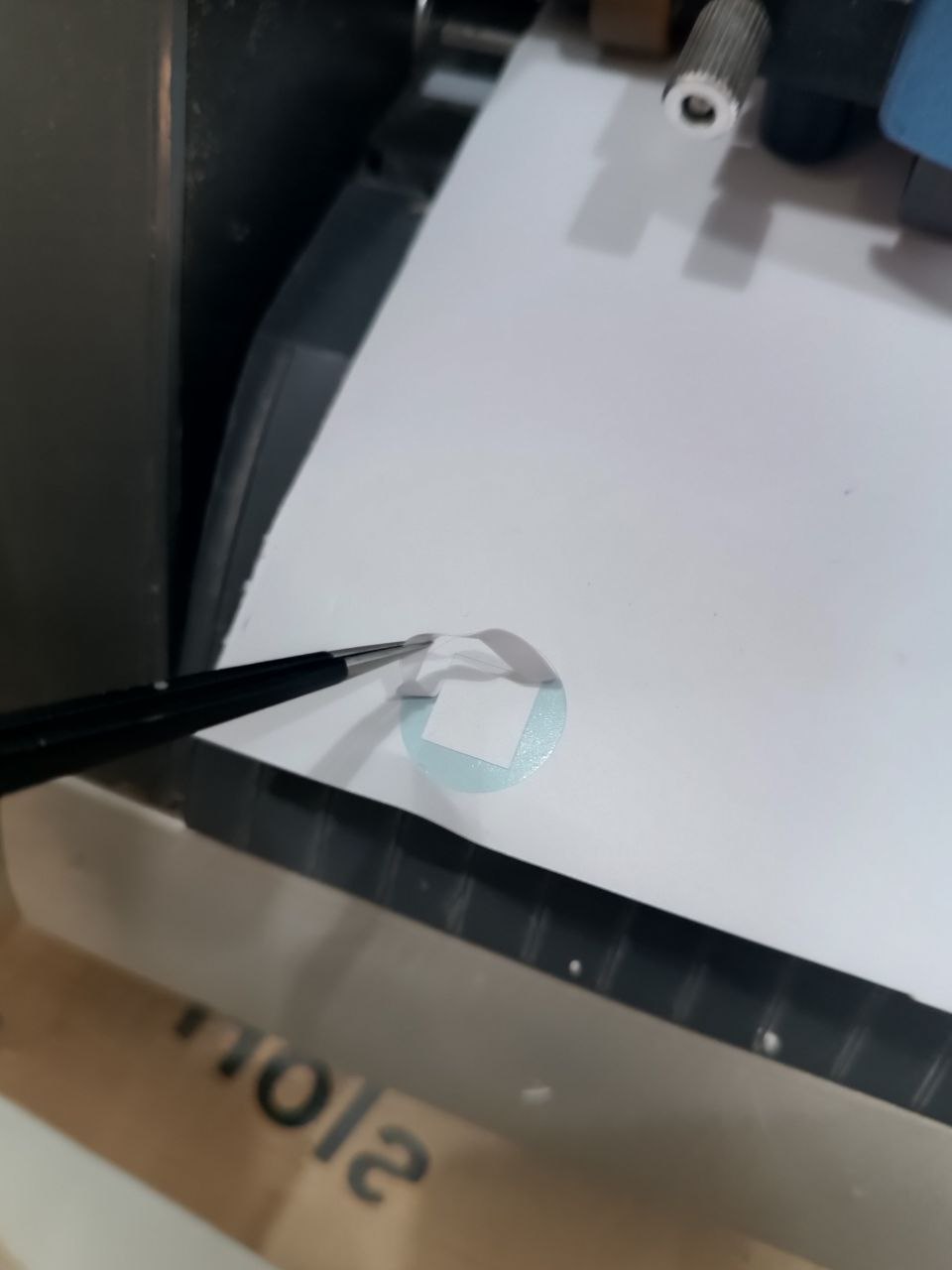
- Special button for test, blade setted well.

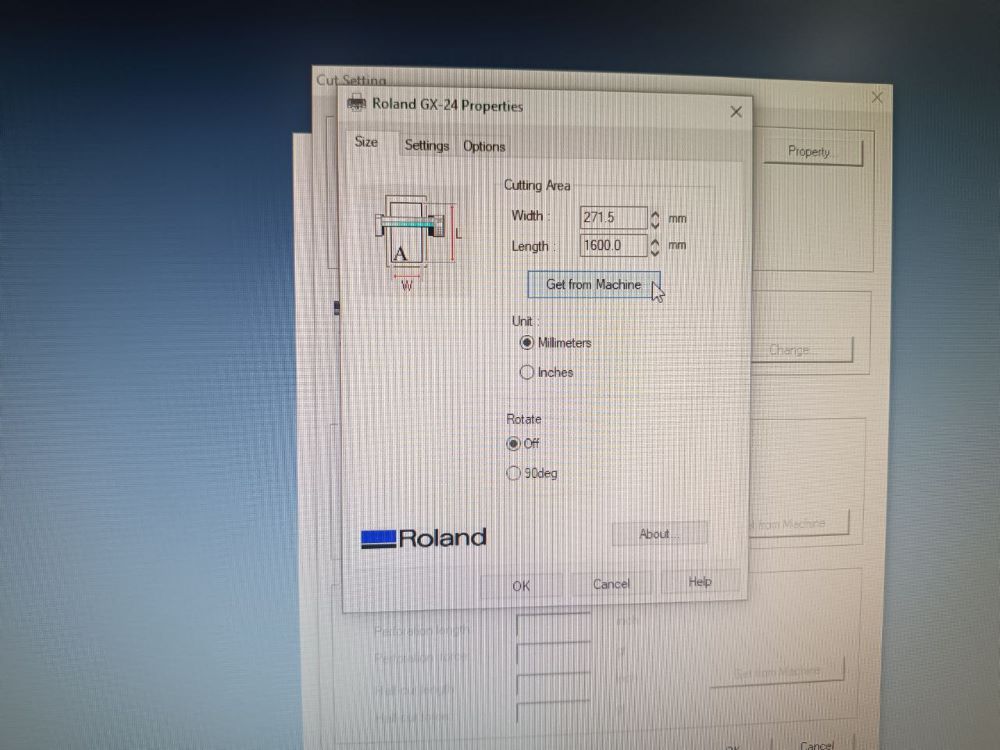
- Working scene should be defined, could be defined automaticly.
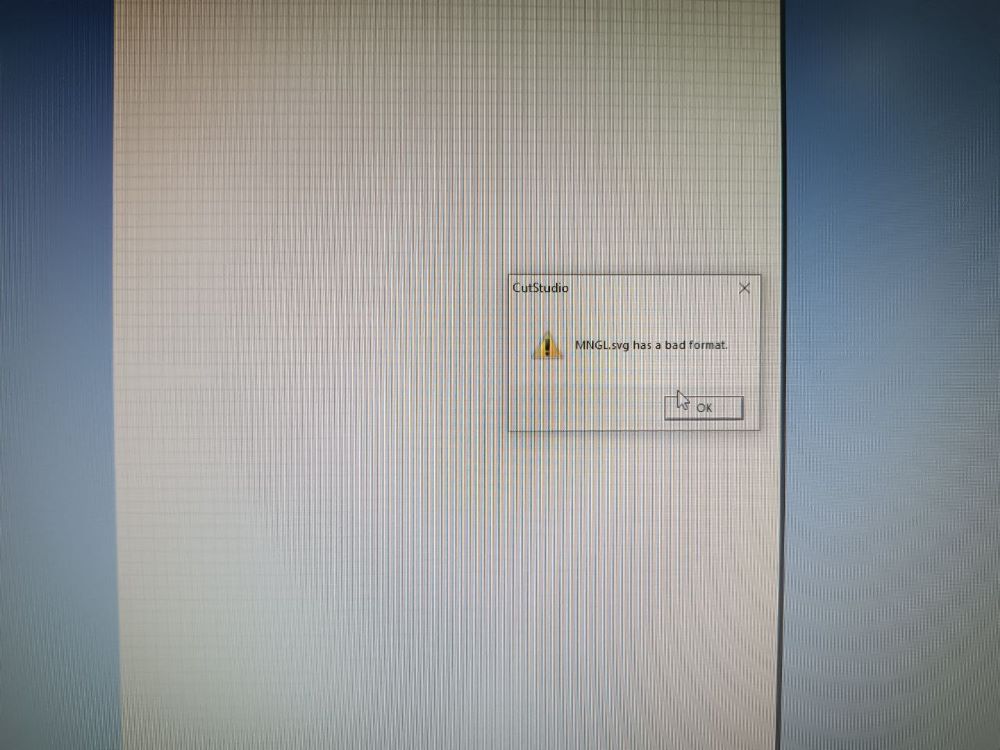
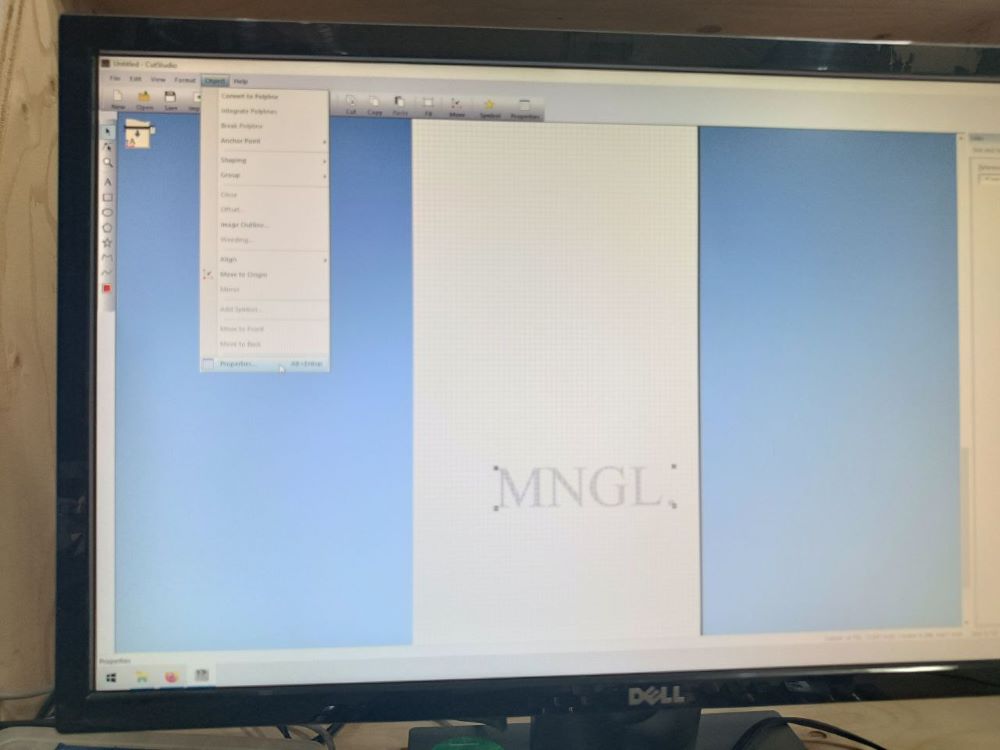
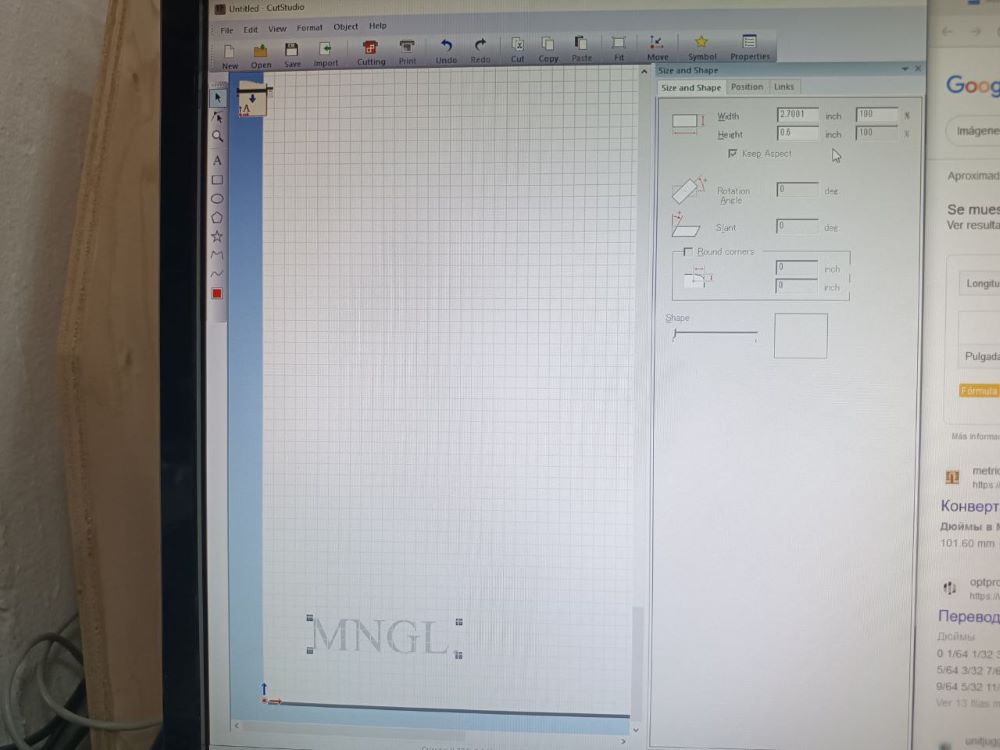
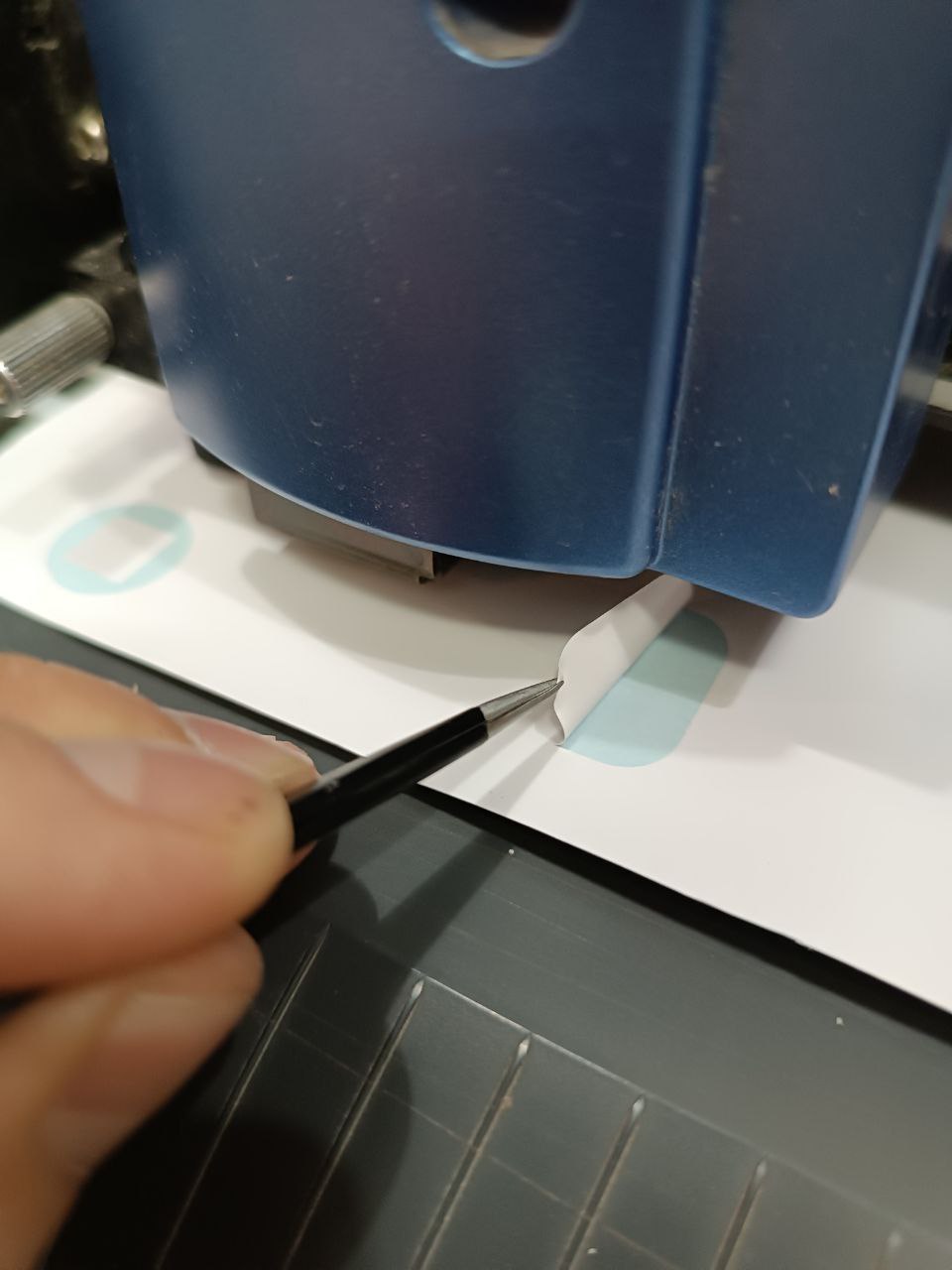
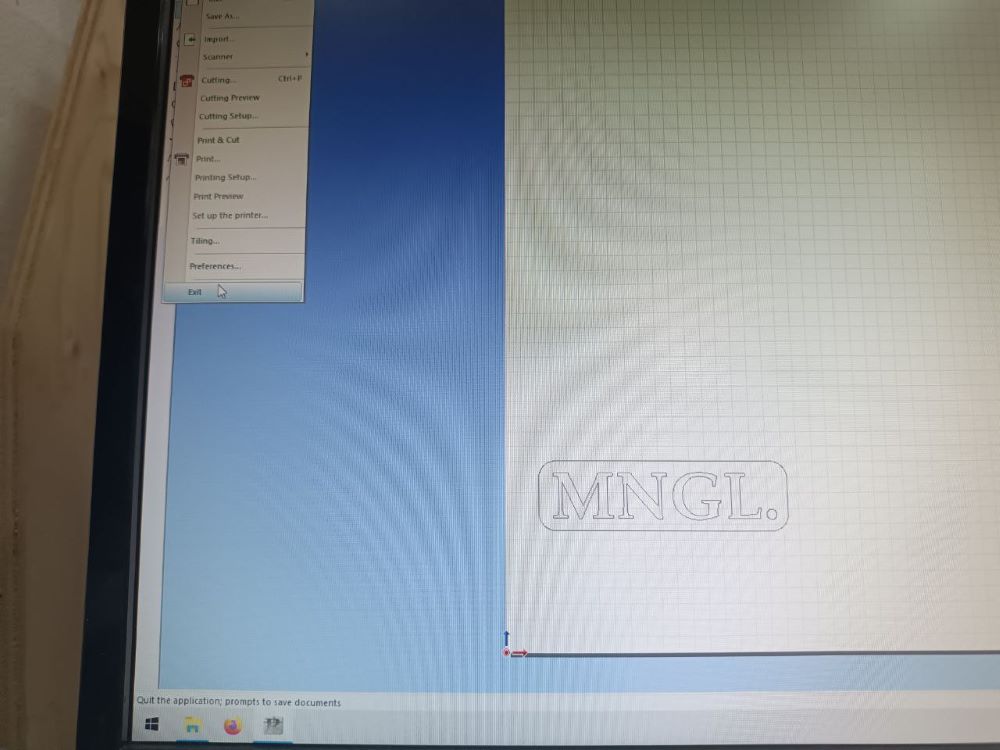
- SVG format did not suit, so exported PNG from Inkscape, but first setted resolution was to small, then too big, eventually defined size in object properties. But after cut found out that PNG did not, so just used Studio Cut text tool.
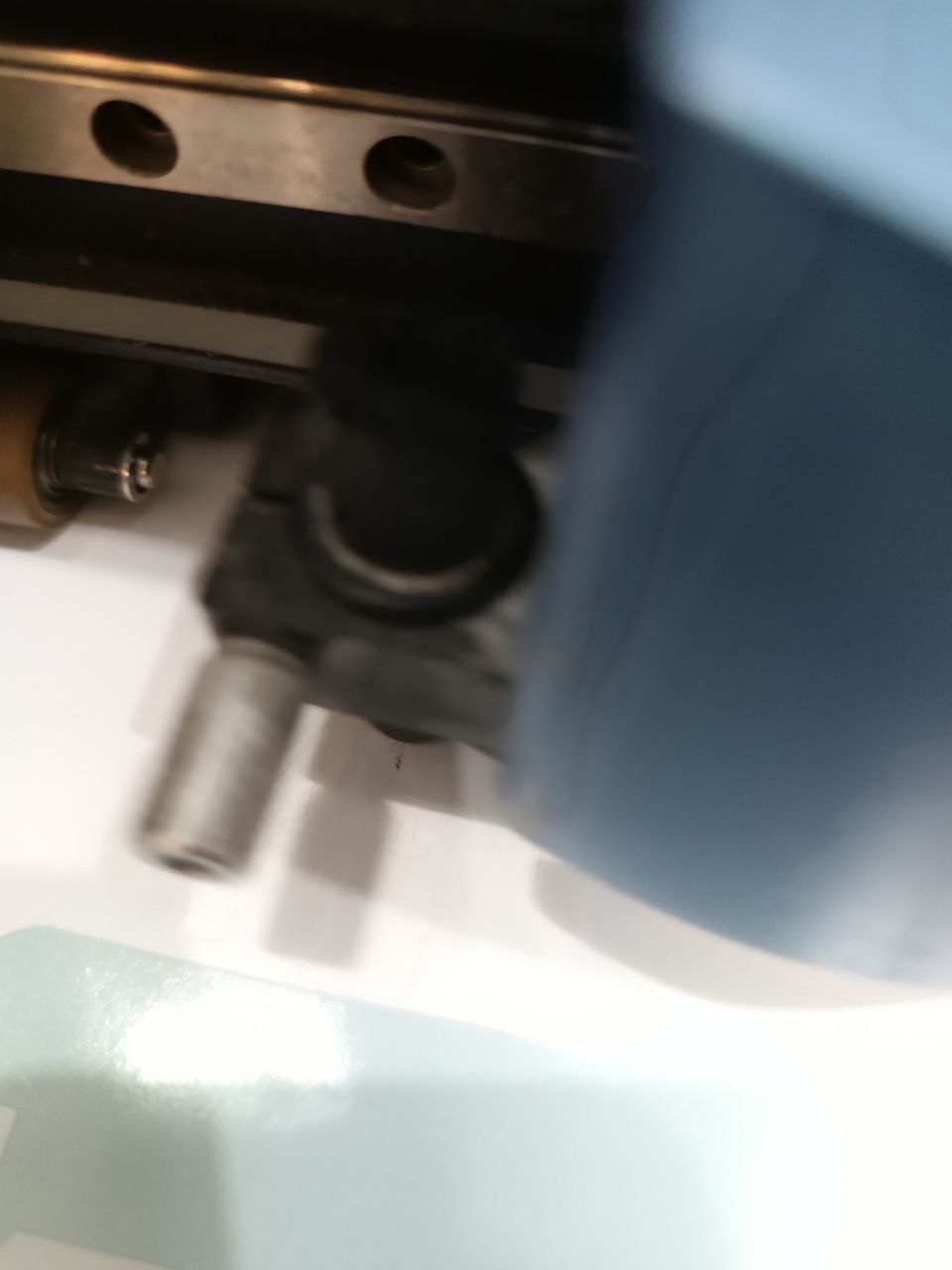
- Cut.
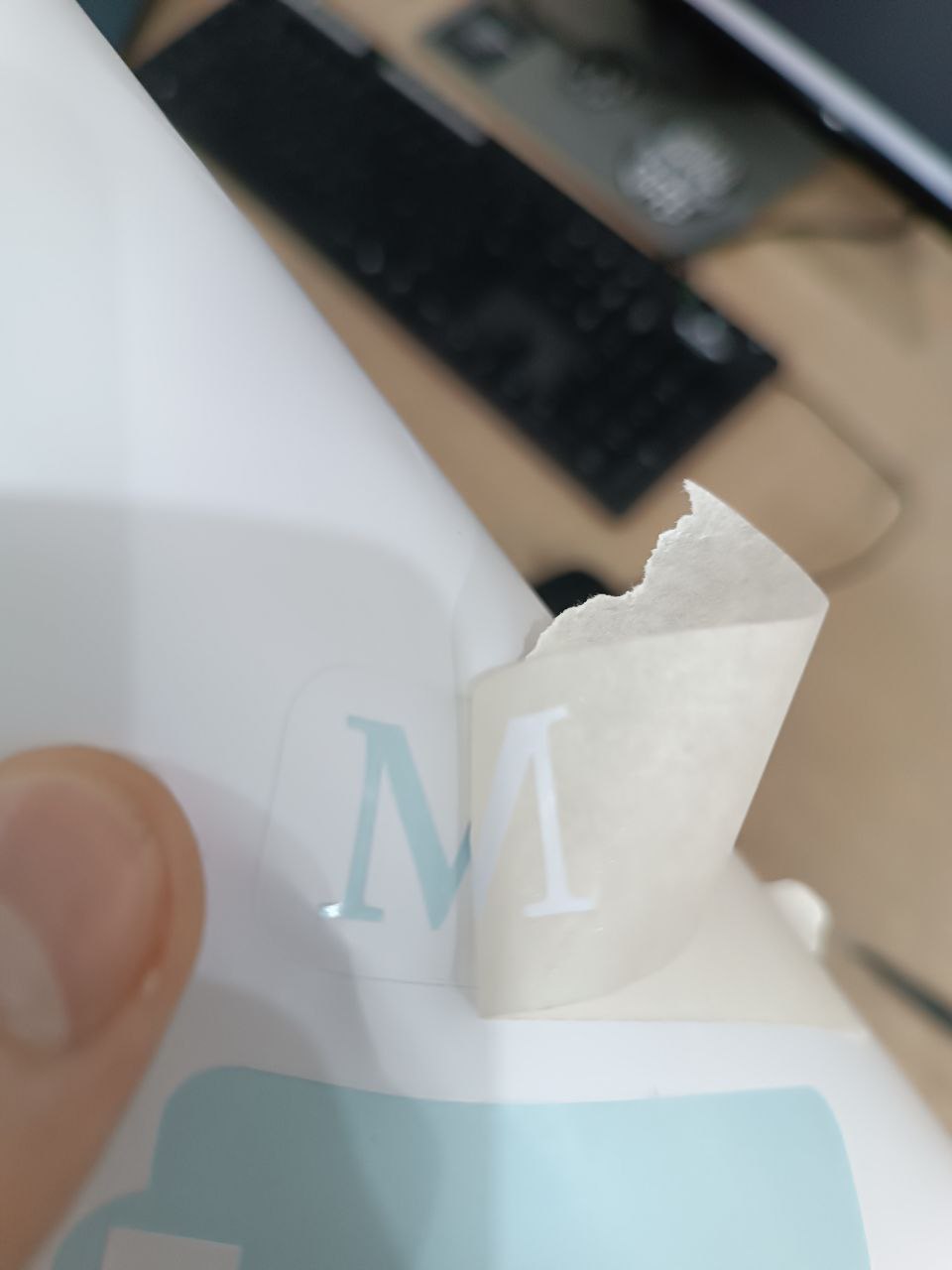
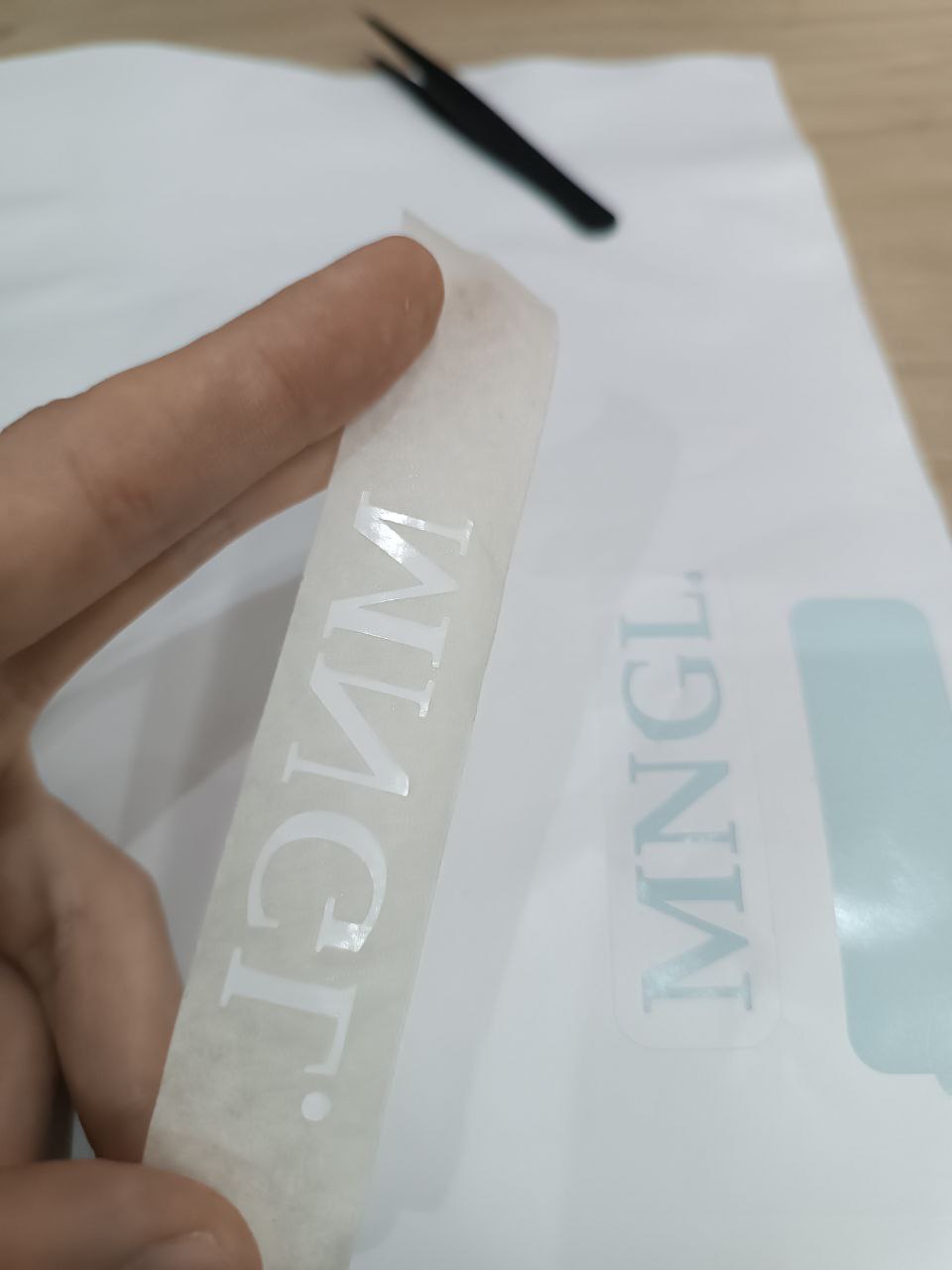
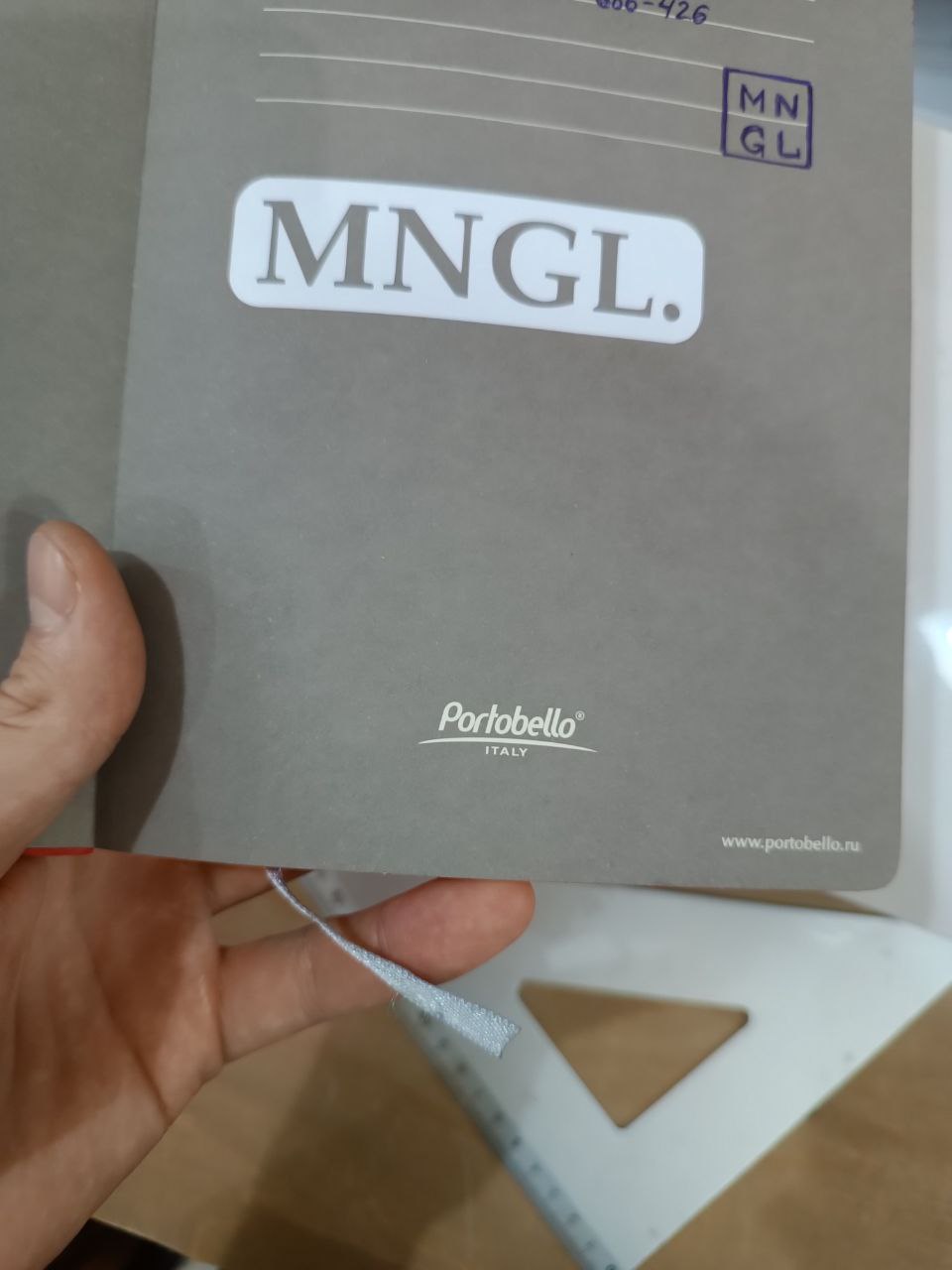
- Used tape to separate elements grouped.
Summary
- Think it is userful and convinient machine, once would like realize its potential for paper (plastic, so on) half-cut volume shaping.