For composites I wanted to keep things as simple as possible. I designed a simple batman logo in sketchup and exported it as .stl. Imported this in Meshlab and exported it as a .dxf for the shopbot.
I used a 1/4 straight 4 flute millingbit on the foam on 30k rpm. The tool went through like butter and milling was done in about 15 to 20 minutes.
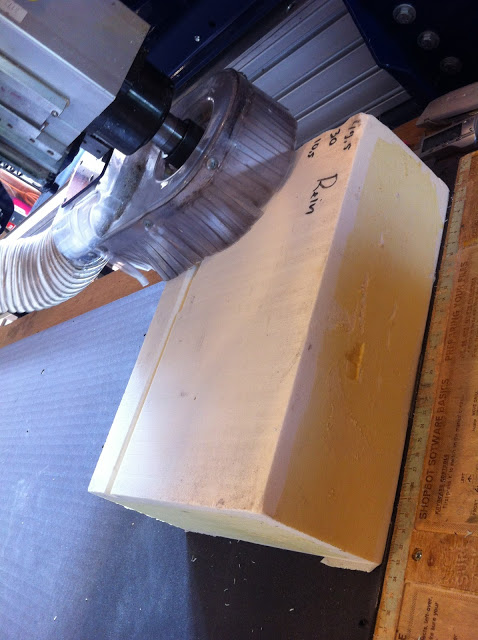
After milling I cut off the excess material and used Gesso to cover the foam.
After the Gesso had dried I used vaseline as a release materical and then I cut up strips of cotton fabric and layered it on the model. I then mixed up some smoothcast 310 and started to poor it over the fabric while using a piece of wood to fill all the nooks and crannies. Next I covered the entire thing again with another piece of fabric and poored the leftover smoothcast on top of it. Then I covered the vacuumbag with vaseline and vacuum sealed the model. After about an hour I pulled the model from the bag as it was not completely vacuum sealed to cure it outside the bag. On the box it says 3-4 hours curing time at 23ºC but it's over 26º here now and the leftover material had already set.
After another hour of curing I decided it was time to pull the mold off the foam. It was really hard and it seems the resin bonded to the foam at some places. It would have been a good idea to wrap the entire thing in shrinkwrap before putting the fabrics on. I had to use a plethora of flat head screwdrivers and knives to get the thing off. In the end I broke off a couple of pieces of foam. Other parts came off very easy. Especially the flat parts. Alex suggested that for a next time instead of the 90 degree angle to use a 45 degree angle so the composite will come of easier.
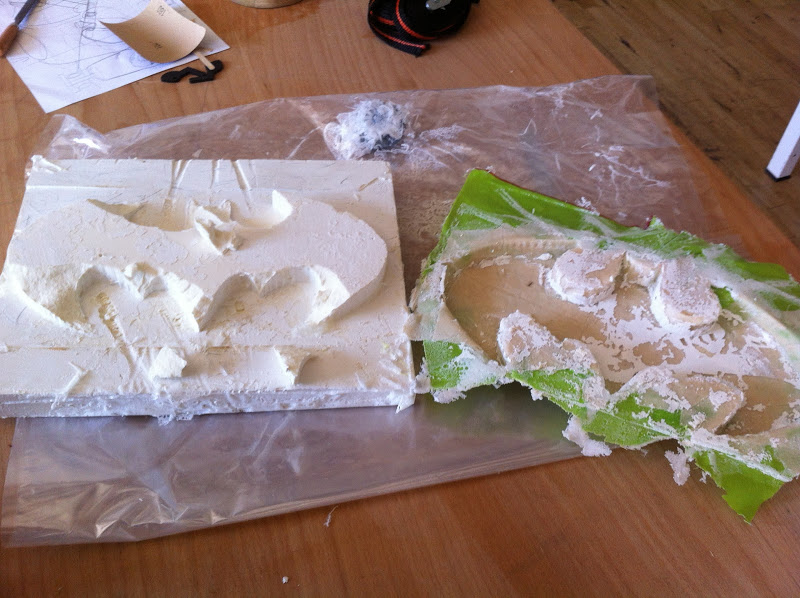
A thing of interest is that the resin will bond the gesso to itself but not everywhere. It flakes off here and there. Pro tip: sealing the positive mold with mold release or something that will not bond to the resin but be able to go completely flat to the positive mold.
top