- For CAM Design, we used ArtCAM version 9. We performed the following steps:
- Open the artCAM and create a new model
- Set the size of the wood sheet that you will work on, in my case it was Length 2440 mm x Width 1220 mm.
- Go to FILE -> IMPORT -> Vector Files and choose the DXF files we exported in Autodesk Fusion 360. Cleck OK and ensure that the DXF is centered and adjusted well in the sheet and accept t ojoin the vector lines in case they are not connected.
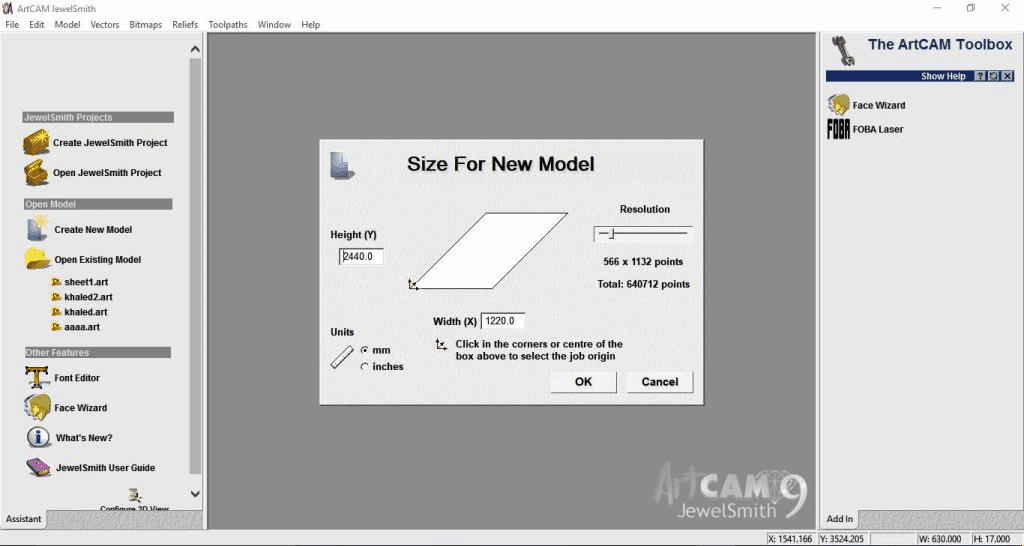
- Select the vectors you want to create toolpaths for, Create a tool path, choose PROFILE and use the following settings:
- Select the cutting direction as OUTSIDE, Finish Depth = 20 mm, The sheet thickness is not unifor and it ranges from 17mm to 18.5 mm, we chose 20 to ensure that all the parts will be cut properly.
- Select Profile tool as wood cutting drill bit with diameter = 6mm, choose stepdown to be 6.7mm (this will make the full cut performed on 3 paths), plunge rate = 100 mm/sec.
- Give the toolpath created a name and click on the NOW button.
- change the cutting direction to INSIDE for the pockets and then repeat the above steps.
Problems Faced and How we solved them?! - When one of my colleagues did his task on the machine before me, I noticed that in some areas the cut was not clean and it did not cut fully, The cutting took a long time and there was 4 paths with one path to cut only 1 mm depth.
To avoid that: I increased the cut depth to 20mm and I increased the plunge rate to 100 mm/sec. I also made the stepdown 6.7 mm to ensure it will cut the 20 mm on 3 steps not 4.
- Go to toolpath menu -> save tool path -> arrange the toolpaths and start with the inside pockets first then the external cuts, choose machine output to be MACH2 mm then save.
- My task required 2 sheets so I did the same steps as below for the second sheet.