Make something BIG
This week was all about manufacturing something 'BIG' in terms of that the built object should be bigger than the usual ones we built with e.g. the lasercutter.
But mainly the goal was to explore the dimensions and abilities of our CNC-milling machine and use its 2.5D ability. For my final project I am planning to build an interactive
crib that I can put underneath my christmas tree the next years. Therefore, I decided to use the CNC mill for the house of my crib.
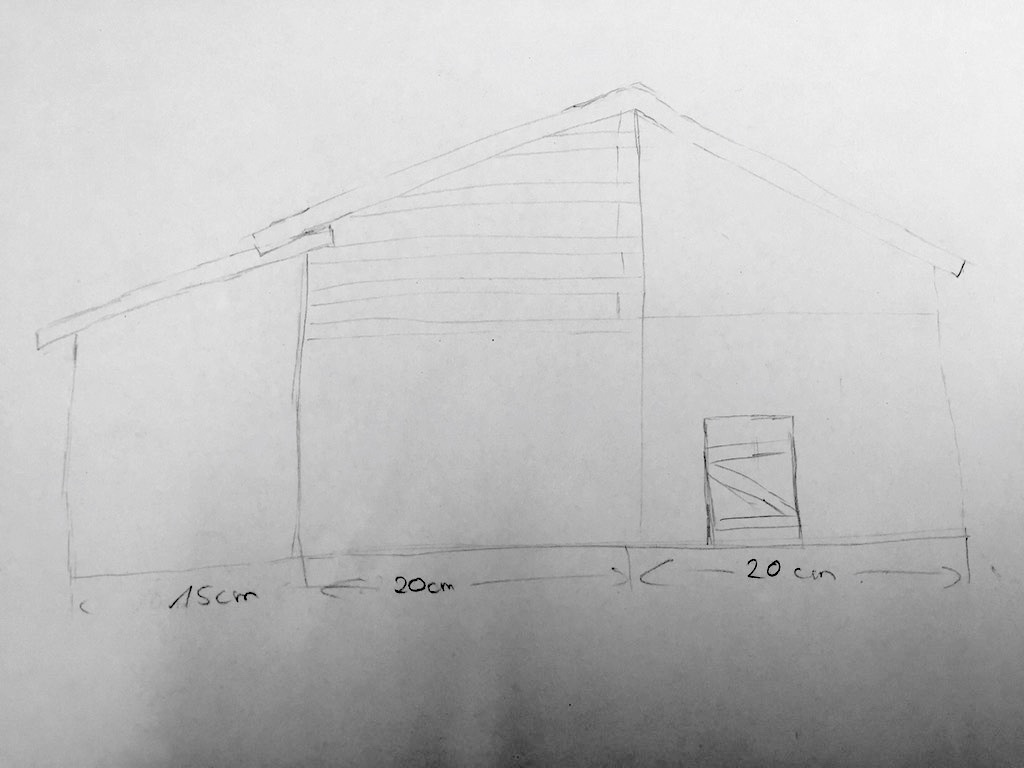
Sketches for the design and dimensions of my crib.
Again, we were asked to do a group assignment: testing our mill. You can find
the documentation on the
Group project page.
CNC machine: Stepcraft
In our lab we have a
Stepcraft 840 CK. As this machine is relatively new it took me longer than for the
other machines in the lab to understand how to make it work. At the moment we mostly mill wood and foam with the CNC-machine but we plan to mill other materials in the future as well.
We hope to have this finished during the next weeks.
Stepcraft milling machine.
Design with Fusion360
I did design the house for my crib with Fusion360. Mainly because we use Fusion360 to generate the needed gcode for the stepcraft software to mill. I have not worked with Fusion360
before, thats why I took some time to just play around with the tool. I also used
this tutorial page
to get a deeper understanding how to design with the software. After around an hour I felt started working on my house design.
Playing around with Fusion360.
Start design house. I started with drawing the full shape of the house by the outline of it. Afterwards I divided it up into the several walls of the house by adding
a lines that define the joints where the final pieces need to fit together.
Then I cut off at these line joints to achieve all final pieces and added the line joints to all places that need to fit together accordingly.
Basically I copied the line (that forms the joint) at the according place and connected it to each piece that fits to another one.
Finished 2D walls plus joints to assemble them.
Impression of designing the joints.
After designing in 2D use the 'Extrude' feature to change the objects into 3D. I used the 'Extrude' feature to receive 3D walls. This way the z-parameter
of my house can also be considered later on. It also opens up the possibility to add a pattern onto my walls if I decide so later on.
CAM processor of Fusion360
After a few cycles I was able to use the Cam processor myself. At first it did look quite complicated but in the end only around 10 clicks are necessary to prepare
the object to be processed into gcode. One thing that is really important to take care of. When designing your objects in Fusion make sure that the Z-axis is pointing into the top direction.
Usually this is the default but somehow in my design the Y-axis was pointing to the top. This complicated the CAM process a lot because the coordinate system was wrong.
To prepare the gcode for the milling follow these steps:
1. After designing your model you need to prepare the object to be generated into gcode for the milling machine. First of all, you need to change from the 'Model' view into the 'CAM' view
(see picture a.). Now your tap should look like this:
a. Change from the 'Model' view into the 'CAM' view.
2. Now you need to define your setup, i.e. define what you want to mill. I used the 2D options that Fusion provides.
Click on the this button
to choose between the 2D options. I chose a '2D-Contour'.
3. After your have chosen an option what you want to drill you need to set some more attributes. Therefore, double-click on 'Setup' in the tree
on the left of the Fusion interface
.
4. This dialog pops up when double-clicking 'Setup'. You need to set the coordinate system accordingly to the coordinate system
of your CNC mill. There is no always correct solution for that. Always make sure to set it correct. To set the axes click on the combobox next to the term 'Orientation'.
5. After you have defined the axes you need to set your attributes for the '2D-Contour'.
Therefore, double-click on '2D-Contour' in the tree
on the left of the Fusion interface
.
6. You need the follow the tap from left ot right in the dialogue that pops up. In the first you need to make sure that the correct
drill head is selected. If not select the correct on by clicking on 'Select'. Speed and other values are set then automatically.
7. In the second tap you need to choose
the lines you want to cut. I did choose the bottom outer line of my house walls.
8. In the third tap you need to select your bottom of the model. This assures that the machine later knows how deep it
has to mill.
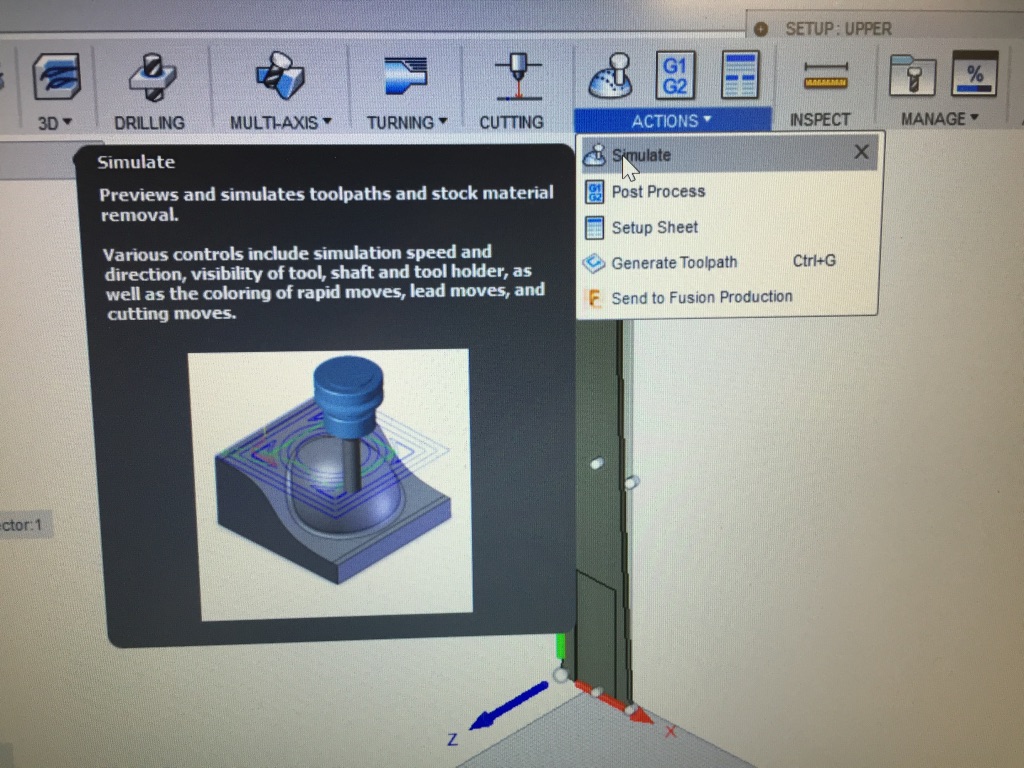
9. Now you can simulate your drilling process. Click on the 'Actions/Simulate' (seen on the upper picture) and start the siumlation by clicking on
the play button (seen on the lower picture).
10. Finally, you need to postprocess your model to generate gcode. Click on 'Simulate/Post Process' and save the file on your computer.
UCCNC software Stepcraft
For the stepcraft machine we have a special software to move to drilling head and start milling. The interface of the software when opening it you can see on the picture underneath.
As you can see that interface is quite unclean and could need some redesign in terms of design laws.
View of Stepcraft software with an opened file.
To be able to start milling follow these steps:
1. Load the file you saved on your computer before into the software by clicking on the button 'Load file'

.
2. Start moving your drill head with the arrow keys on your keyboard to a position where the zero coordinate of your model is. Then click the button 'Zero All'
3. Check whether the object fits onto your plate in the milling machine. To check it fix your material in the machine with the help of screws so it does not move around during the mill process
(as seen as an example in the picture underneath)
The grey bars and the screws help to stabilise the material.
4. If the object fits onto the material move your drilling head onto the material in the Z-axis and press 'Zero all' again.
5. Move your drill head up again. Around 1cm from the material is fine. This is to be able to turn on the drill head without leading it to directly mill into the material.
6. Press the button 'Cycle Start' to start your mill process
During the mill process you can observe the status of the process in the stepcraft software.
Stepcraft software during mill process.
Machine Setup: Parameters
-
I used a feed rate of the value 300 to mill my housing. I chose that value as a faster one made a mill tool break in an earlier usage of the machine.
-
I used a nut milling head with 4mm diameter.
Milling process
Turn on the drill head by reaching into the machine. Additionally, turn on the vacuum cleaner.
After back wall of house has been milled.
Milling side walls. In the picture on the top right you can also see one of the screws and rails that
hold the milled piece in place. This is necessary as during the mill process the force on the milled material is quite high and would move
the material. Moving the material would destroy the model.
Second attempt to mill the side walls. This time I tried using the idea of dogbones to assure that the joints fit
because without dogbones the mill produces round corners. Those round corners are a problem when assembling the house. The dogbones were realised by just adding drill holes in the CAM process at all the corners
of the joints. For future designs I will add dogbones directly into the design file. Adding drill holes this time saved time for the fabrication process.
Finished walls with round corners.
Assembling the house
Closer look at the round corners. I did use a file as a postprocess option to make the walls fit together smoothly. Filing was only necessary for the part
of the crib that did not have the dog bone holes.
Filing the jags to make them fit smoothly.
Without the filing and without the dogbone method the joints did not fit.
Joints fit after filing.
Joints from the outside.
What I learned about Joints
General fact: Producing objects that can be assembled and fit tightly is not the easiest process. You need to plan during the design process how you want the object
to look like in the end and accordingly choose the suitable joint type.
-
To be able to connect parts I usually use finger joints, e.g. when using the laser cutter. The problem with finger joints when using the CNC mill is that the mill head cannot mill rectangular inner corners.
It will always produce round inner corners. But round corners are not able to produce fitting parts.
-
One solution to produce tight fit parts is using dog bone joints.
I found the following website concerning more elegant dogbones. The picture underneath gives
very interesting information about dog bones design. When I used dog bones I just made use of a big round hole at the inner corners to produce fitting crib walls.
But dog bones can look differently. You can design them nearly invisible. A very interesting fact to keep in mind for the future.
-
While searching for ways how to produce a tight fit with a CNC milling machine I came across different types of other joints, e.g. blind joints, half blind joints, through joints
etc. Even though flexures
are not the classic joints flexures still open up the opportunity to form 3D objects by producing bendable material. More types of joints and information you can find
here
How I used dogbones
So-called technique of dogbones that I used after my first attempt of milling did produce round corners.
Dogbone joints do fit but there is still improvement possible in terms of the dogbones size. Concerning more elegant dogbones
I did read this website.
Dogbone joints from the outside.
Final walls of my crib.