0 | 1 |
2 | 3 | 4 | 5 | 6 | 7 | 8 | 9 | 10 | 11 | 12 | 13 | 14 | 15 | 16 | 17 | 18 | 19
Kazutoshi
Tsuda
11. composite (Apr 9, 2014)
Design and make a 3D mold, and produce a fiber composite
part in it
I made plant fiber composite materials by adopting an open mold
method in this week.
Cotton
Firstly, I made molds by vacuum forming.
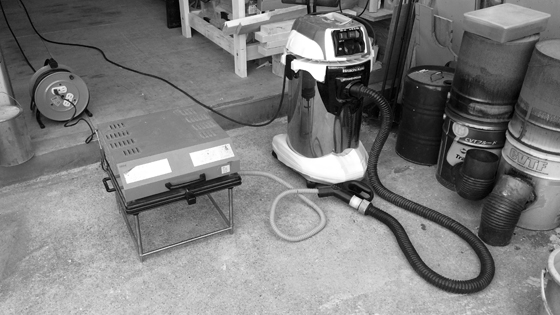
From left to right: extension cable reel, vacuum former,
and vacuum cleaner.
I used the outer surface shape of a pottery bowl as a mold. Last
winter I made the pottery bowl series, with the assistance of an
artist Takako Higashihata in Shigaraki, Japan. I trimmed the
foot ring of the bowl as shown below.
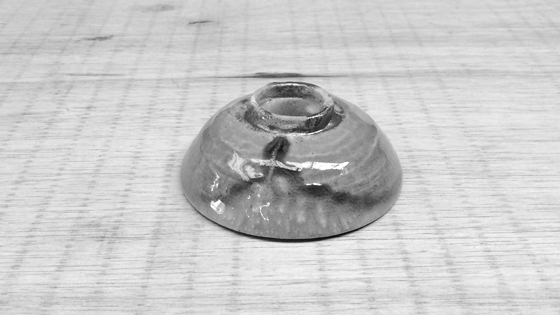
Pottery bowl we made.
Transparent plastic sheet was heated to a pliable forming
temperature (60 Sec, and preheat time is 120 Sec), then formed
to the shape in the mold.
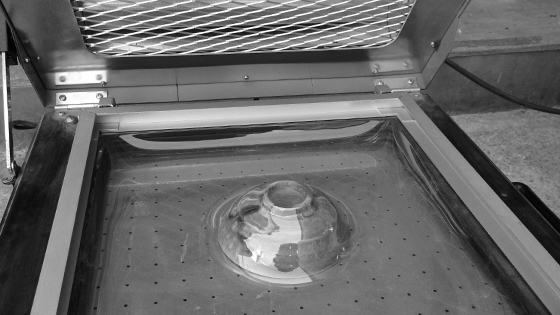
The process of vacuum forming.
As a matrix of the composite, diatomite and powdered resin were
used. Diatomite is a naturally occurring siliceous sedimentary
rock and used as a filtration aid. These particles and water
were mixed with fingers until thoroughly combined, let sit in 30
min, and then mixed to the right consistency.
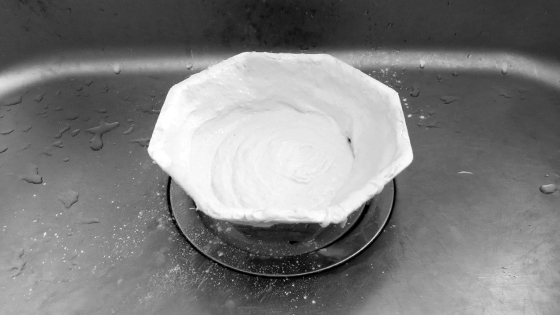
The process of making matrix.
As a fiber of composite, cotton was practiced. The cotton was
made in the field of my family home since it was graft last
season.

Cotton fiber composite in the mold.
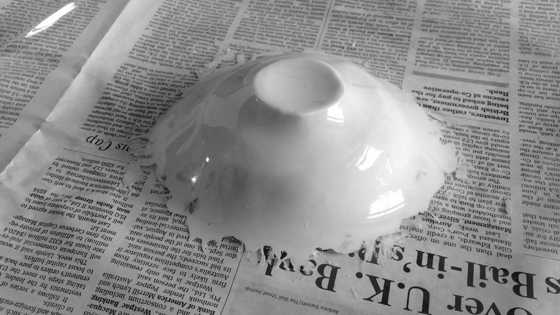
Cotton fiber composite in drying process.
Maybe it is preferred that softer mold (e.g. silicon
mold) and heavy fibers be used for the hard diatomite.
Burlap
I also tried to make another composite by using burlap as heavy
fibers. Burlap sheets were soaked in the mixture of diatomite and powdered
resin.
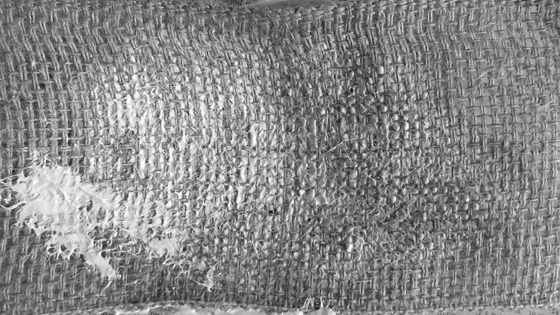
The process of making burlap fiber composite.
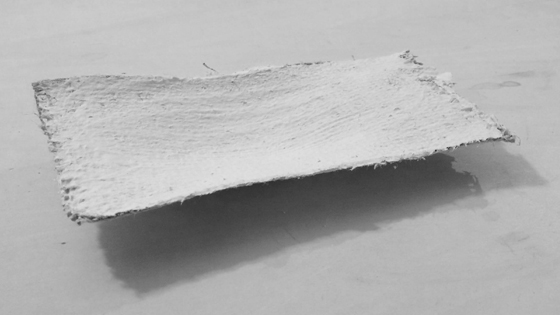
Burlap fiber composite with slightly curved.