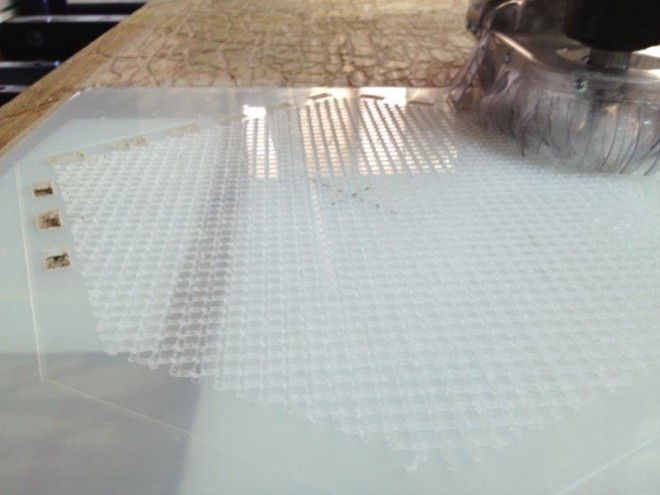
The Assignment for this week is: make something BIG …
As part of my final project I designed and made a controller box for the Penta-Tone. The Penta-Tone is built out of five playing units (which were designed and made by Ida Vass – My partner for the final project) and a control box. The control box contains some electronic components and the shape of it was designed by Ida and it is part of the general design for the complete project.
Designing and making the Controller box:
I got from Ida the outlines for the box as it needed to fit to the end units she designed.
I used Rhino to model the box. I think that was one of the most challenging missions for me in this project and I could hardly believe it when I finally came out with an actual box with its notches and everything … it took me days!! to figure it out, but I learned so match from the process, and when I tried to rpeplay the designing process all over again for the sake of documentation it took me just hours …
Planar Curves –>
We used teeth connectors to connect the box faces. We decided to use the ShopBot to cut the box’ so we needed to adjust the joints. We made “Dog Bone” shapes at the inner corners of each connector. The diameter of the shape was in accordance to the diameter of the milling bit we used (up-cut, double flute, 6 mm).
As the box was completes I “unfolded” it so I can prepare it for cutting (3D Rotate on rhino).
From a Model to Machine:
The Cap:
I exported it to a 2D file (.dxf).
The TOP layer was engraved 3 mm deep.
We used bridges on the frame to hold the cap and prevent it from moving while milling
The Box:
I exported the model twice, becouse the box parts needed to be cut in two phases. The first phase was a 3D milling of the edges with its angles. The second phase was 2D cutting of the frames.
For the 3D milling I exported the model as a .stl file.
For the 2D cutting I exported the model as a .dxf file
Making the box:
I was very happy with the outcome (even though the controller came out a bit taller then the end units – but I think it even nicer).
And one more cutting exercise:
I used the scanned 3D model of my face from previous modules and adjusted it to the milling machine.
I used the ShopBot editor to scale the model and make it shallower (I had to adjust the model to the size of the milling head).
I used foam as the material for milling.