Week 3
Computer controlled cutting
Week 3 - Assignments
• Cut something on the vinylcutter
• Design, lasercut, and document a parametric press-fit construction kit.
Vynil cutter
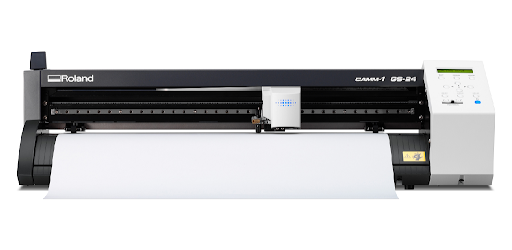
Roland Camm-1 GS-24
For the Vynil Cutter assignment, I decided to design a logo for my River Turbine Final Project.
I used Inkscape to do the design of the logo and for the material i used heat press transfer textile film.
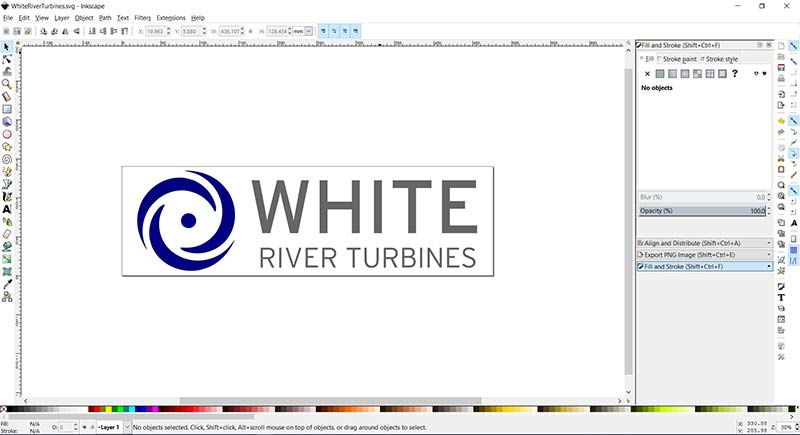
To prepare the graphic for the Roland_GS24 vinylcutter we have to outline the stroke and i usually use pure red RGB color
We also need to set the stroke thickness to 0.02 mm or else the Vinyl cutter will not register the line.
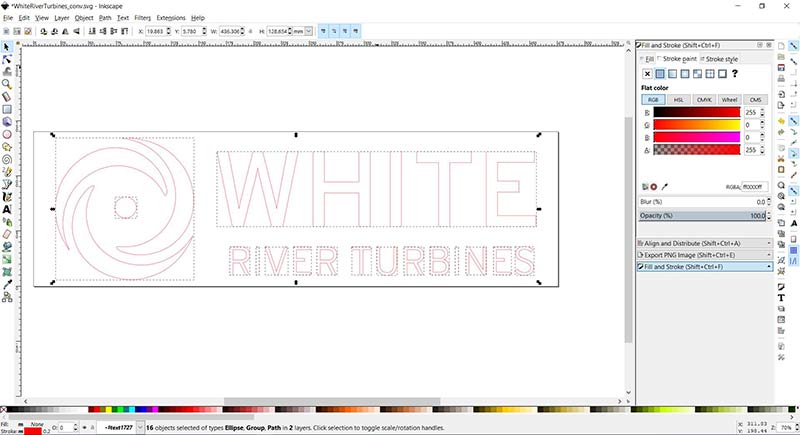
When you are cutting on heat transfer textile film you need to mirror the graphic before saving but for ordinary vinyl you do not need to mirror
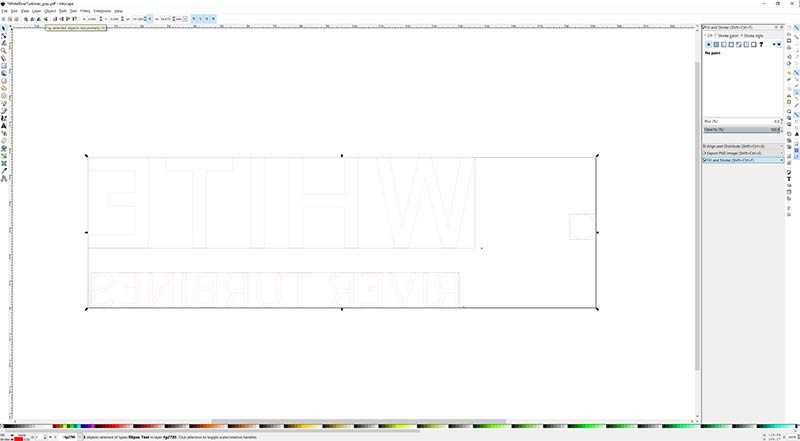
When there are multible colors in the design like my logo then you have to save one file for each color.
Before you save the file you have to convert all text to outline .
The file format sould be PDF
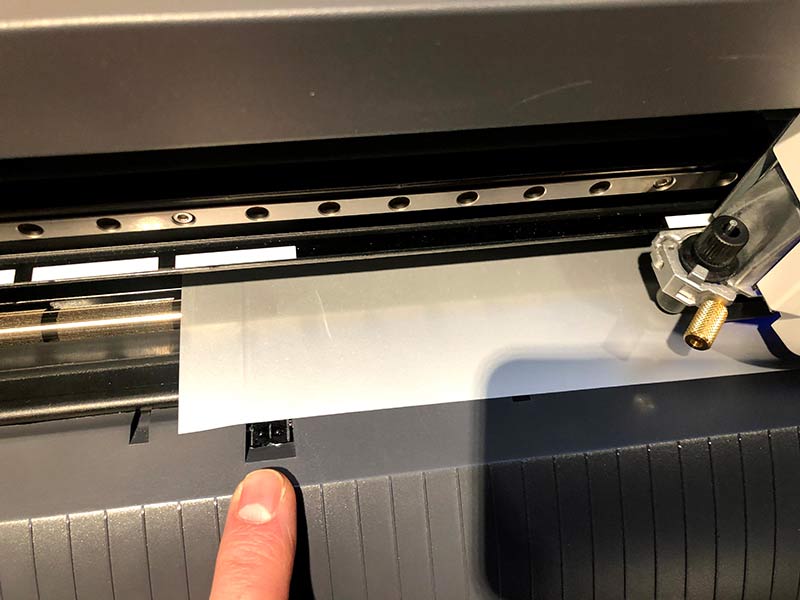
When you put the material in the machine you have to make it go cover the sensor
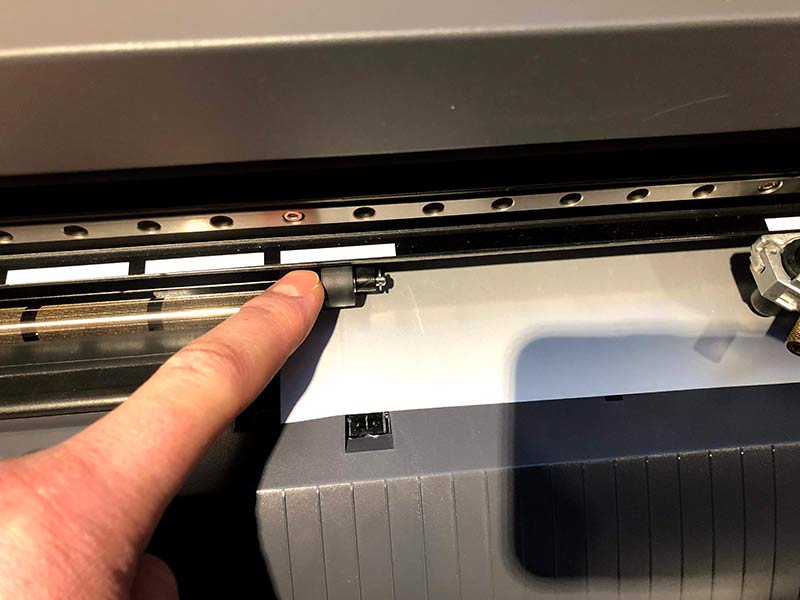
Sett the rollers over the white stripes
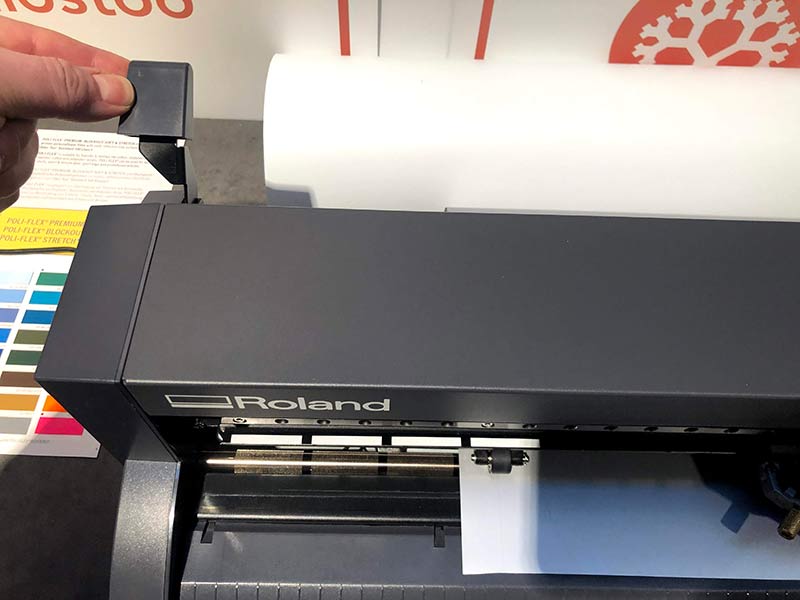
Pull up on the handle
Turn on the machine. Press down and select Roll and Press enter. Then the machine will mesure the with of the roll.
On the screen select Get from Machine. Then you only have to set the length.
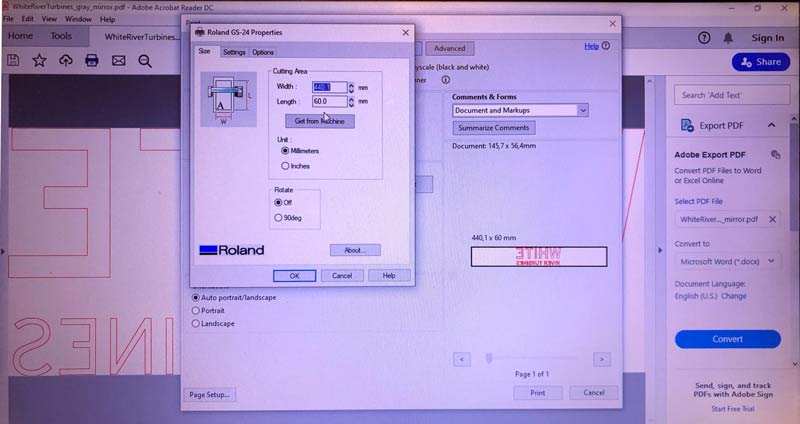
Peel the film from the vinyl
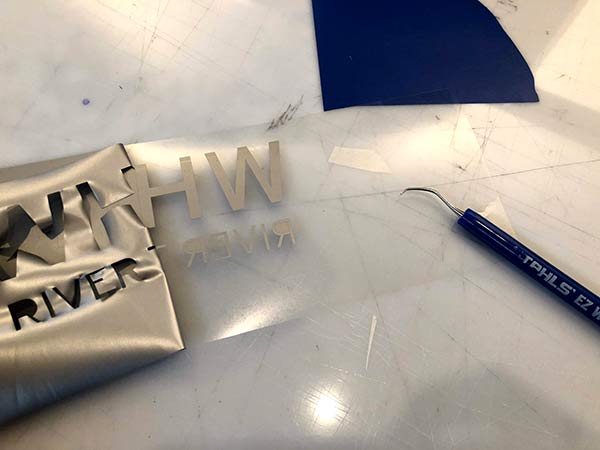
Press one color at a time and peel the trasparent protection film after each pressing
Here I am pressing the gray color
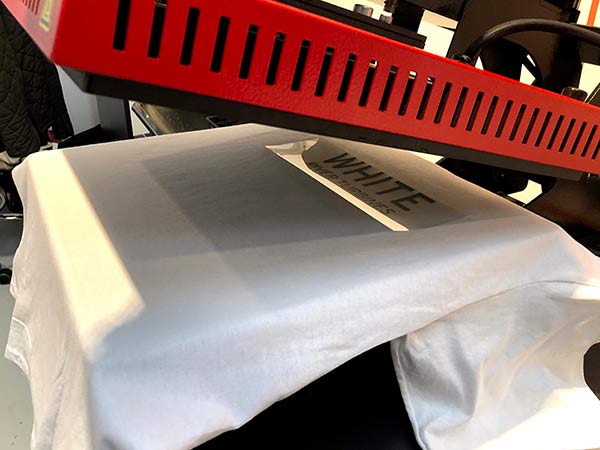
Here is the T-shirt ready

LASER CUTTER
KERF
Kerf is defined as the width of material that is removed by a cutting process. It was originally used to describe how much wood was removed by a saw, because the teeth on a saw are bent to the side, so that they remove more material than the width of the saw blade itself, preventing the blade from getting stuck in the wood.
When talking about CNC shape cutting with typical cutting processes, kerf is the width of material that the process removes as it cuts through the plate.
Over the years I’ve heard some people use the term when referring to the angle on the edge of the part, but that would be an incorrect use of the word. The “cut angle” on the edge of the part makes measuring the kerf width sorta tricky, but for consistency, the word “kerf” should only be used when talking about the actual cut width.
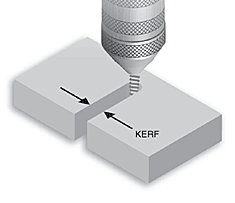
The laser cutter machine
The model of laser cutter machine we have in ours Fablab is a 100w laser 1390 from China.
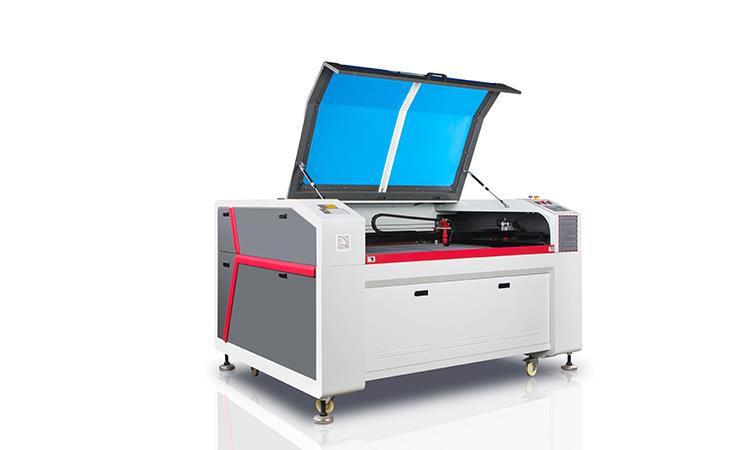
To control the laser i use Rdworks V8 laser software
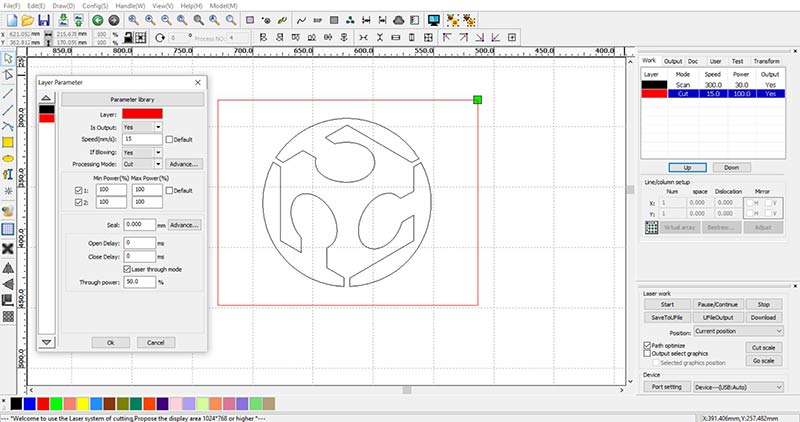
Laser Kerf test
To test the Kerf on my machine i made a Kerf Laser file in Rhino
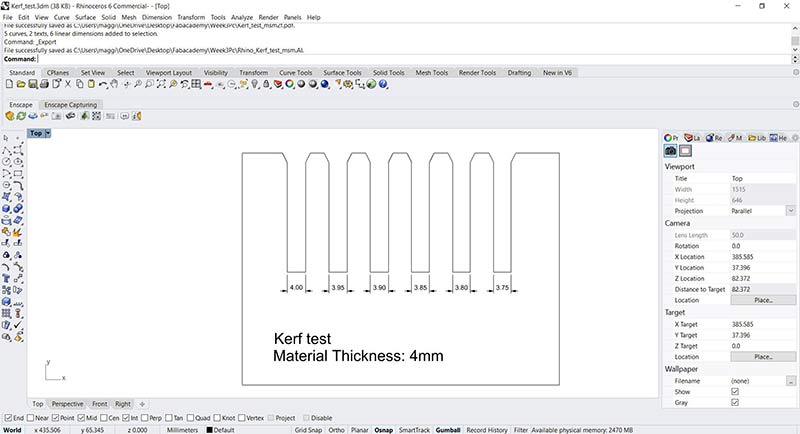
Exported the file from rhino as a illustrator .ai format and opened it in Rdworks V8.
The file format that i usually use for the laser is .ai and .dxf
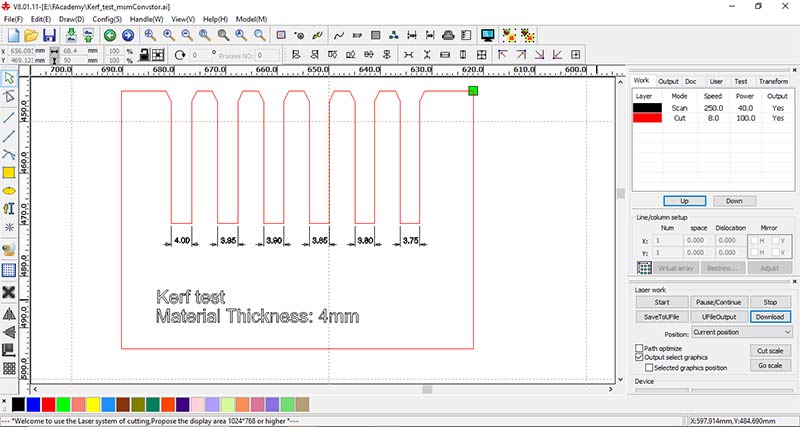
Here i can control the speed and power of the laser. I define where i want to cut with red color and use black color for the Scan(Raster)
Download to the machine and select the file one the laser control box
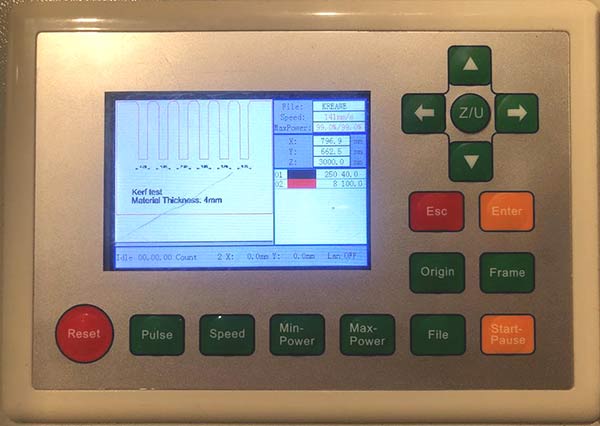
After that you push the ORIGIN button to make that you new zero position and then you can push the FRAME button to see the size of your project on the material.
Here is the Kerf cutout test
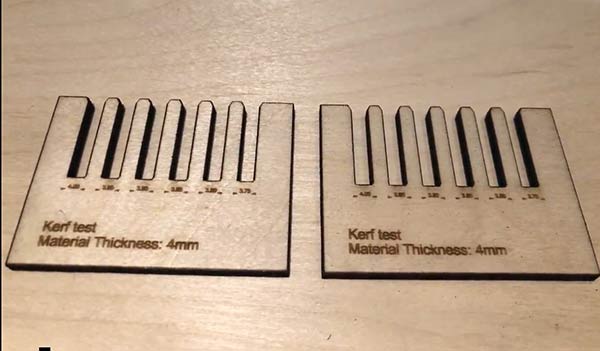
I put the to picese to gether and found out that the best fit was 3.8 mm so my laser Kerf cutout with is 0.2 mm or 0.1 mm from center line in both directions
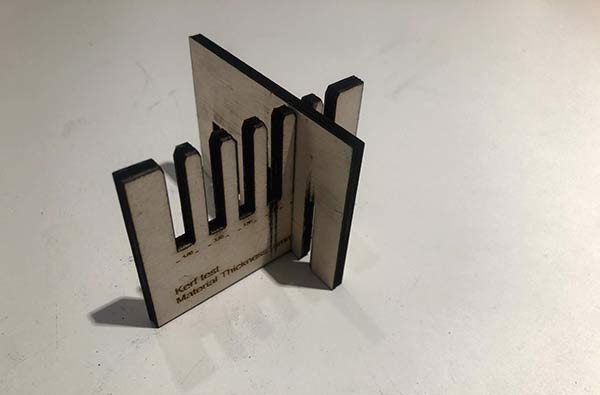
PRESS FIT kit
One of the Assignments this week was to make a press fit kit.
I decited to make mine in Rhino.
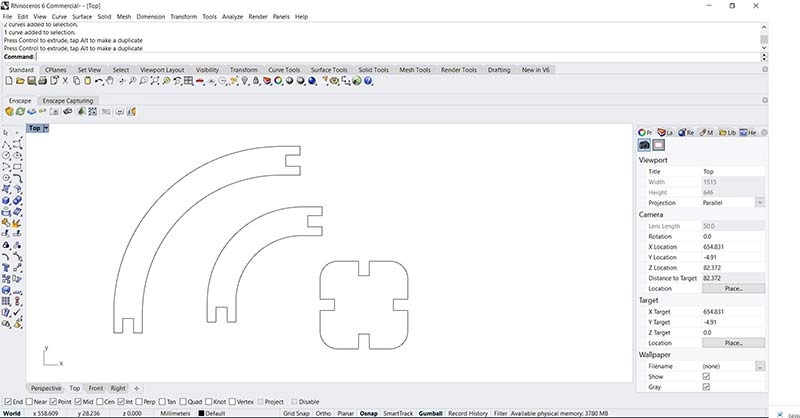
I extruded my design in Rhino and made a 3D drawing of the Press fit kit

I then used my laser to cut the kit out on cardboard
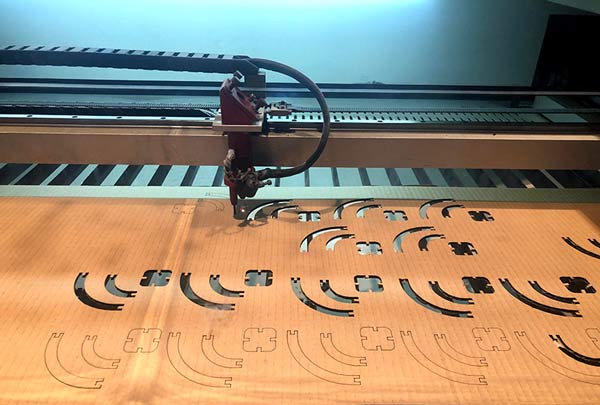
Finally i played a round with the kit and made a few variations
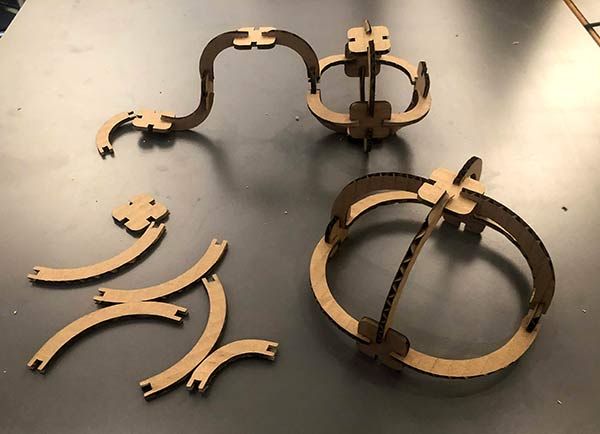
Final Project
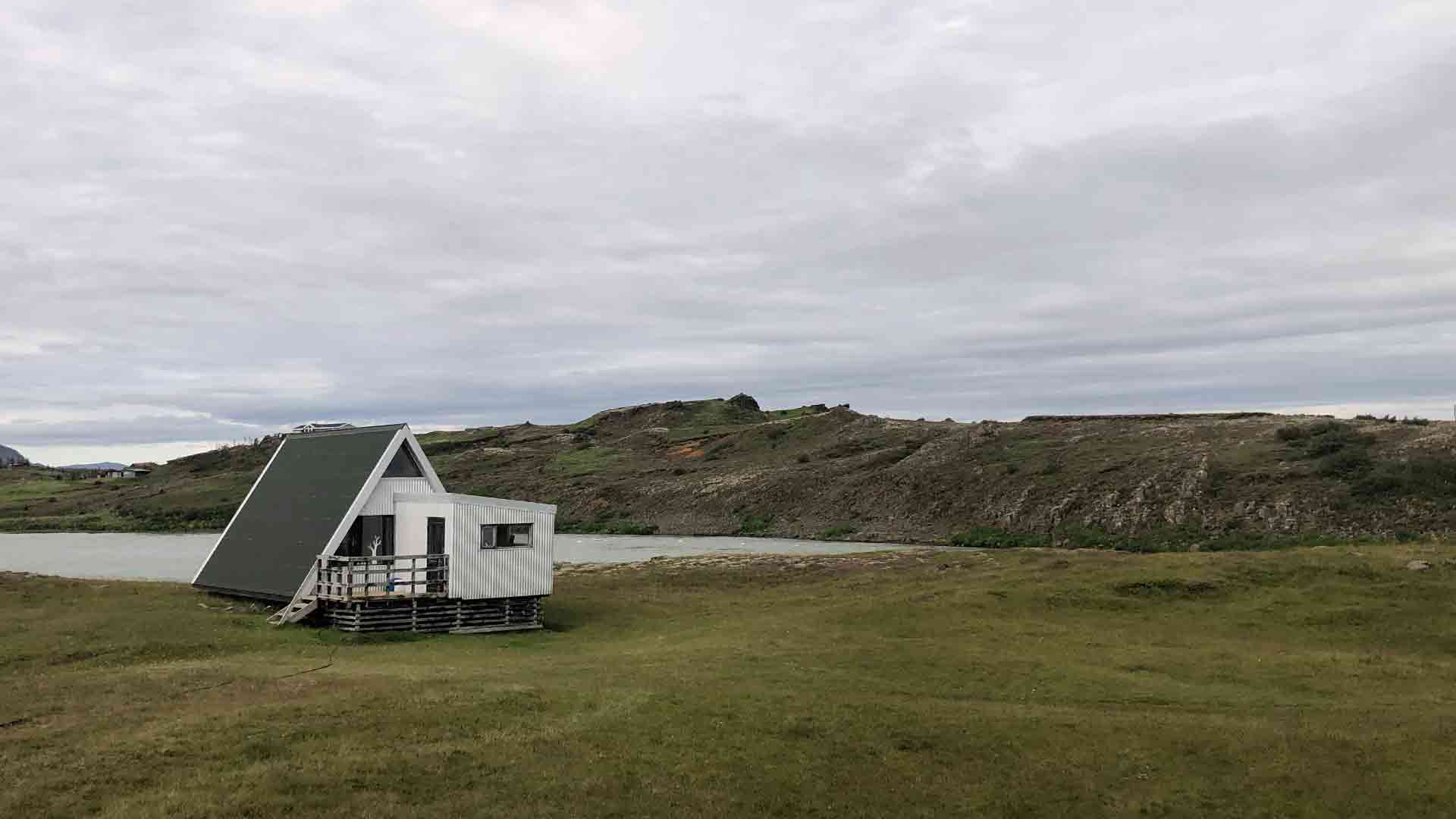
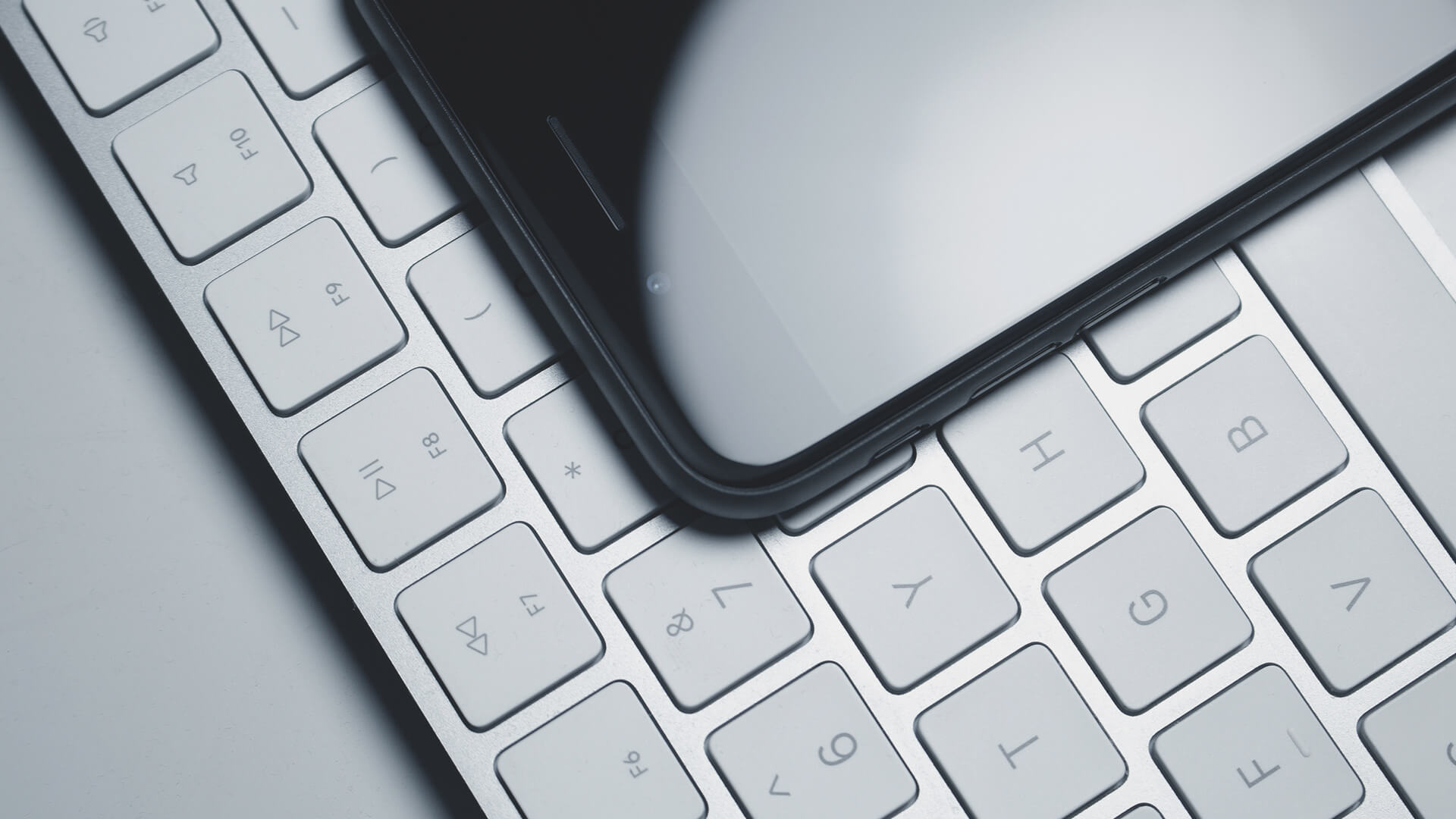
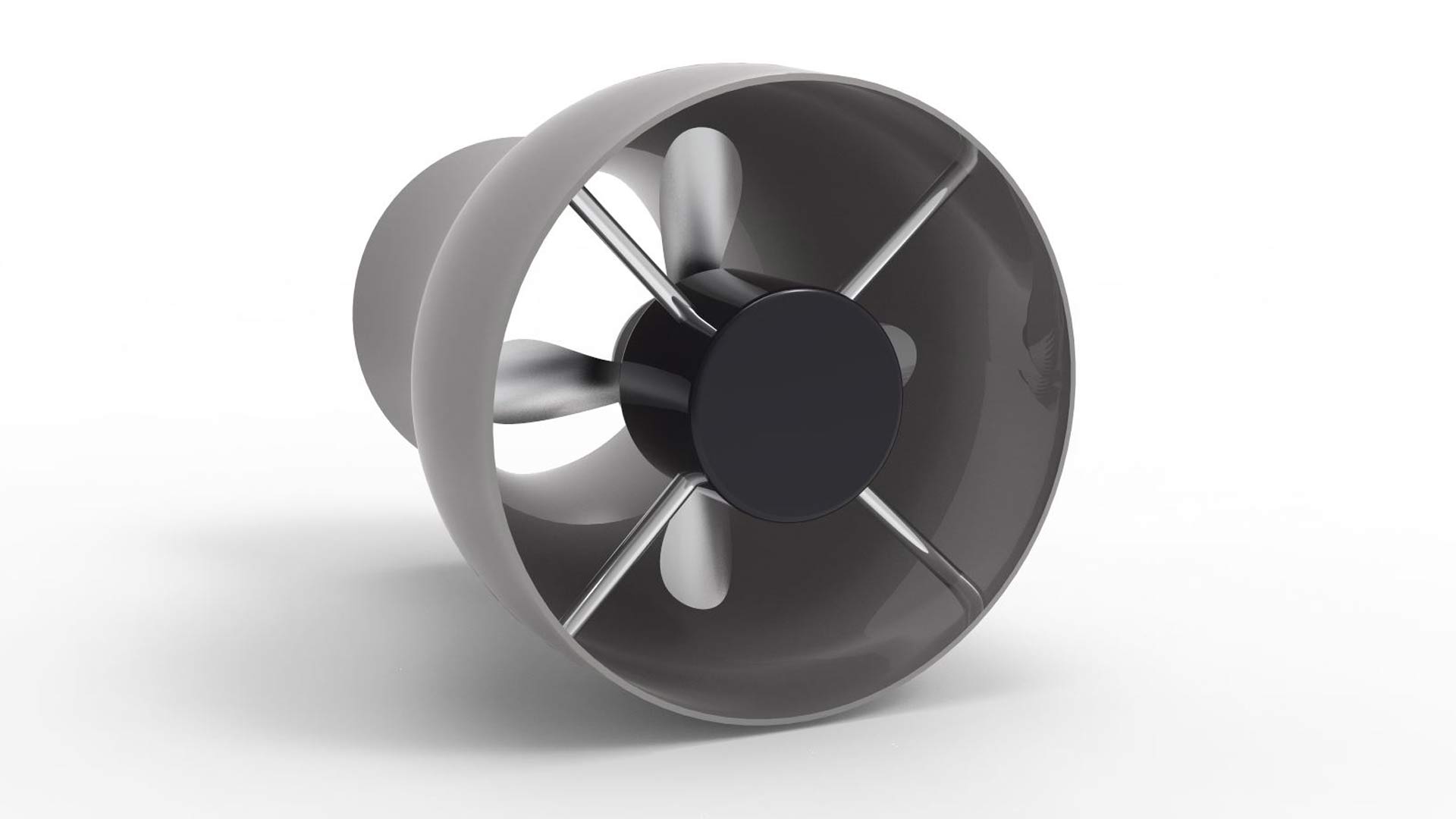
The portable water turbine
I have a little fishing hut by a river in a rural part of south Iceland. This hut is quite primitive with no running water and almost no electricity. When I say almost, its because I have solar cells on the rooftop to engine a few lights to help over the darkest hour. As for other equipment, I have a gas stove to cook and a gas heater to keep warm and prevent the hut from molding. Some might say that this hut is to primitive to use but for me its quite the opposite. Sometimes the only therapy you need is to get away from the hectic everyday life and experience the peace and quiet, and that is what I get in my hut.
That said, of course here are some aspect of my hut that I would like to adjust. The solar cell for example does not function as it could due to scars sunlight in the winter time in Iceland. That, combined with the long dark days, makes it hard to rely on solely.
Like I said before, the hut is situated by a river. In Iceland we have a long history of harvesting rivers and streams for electricity. Iceland gets about 71% of its electricity this way and another 22% from geothermal harvesting. These facts are part of the Icelandic culture and shape the way we think about our nature. Therefore, it was a natural step to try to harvest the river by my hut to make my own electricity with some kind of a water turbine.
But I didn’t want to stop there. As much as I love my hut, I also enjoy traveling through the wilderness of Iceland, by cars, horses and on my feet. And as much as I enjoy the peace and quiet, I also know that the weather in Iceland can change rapidly and you should always have a fully charged phone or an emergency locator of any kind. This, as well as the fact that the Icelandic wilderness is full of rivers and water streams got me to the idea to find a way to make a small, portable water turbine, efficient enough to charge a phone, a radio or similar.
ABOUT ME As a trained pilot and graphic designer working for a furniture manufacturer, I have always been fascinated by how things work. I am a craftsman by nature and have a deep need to understand “the material” and its capacity. Being married for over twenty years, a father to three kids and living in the countryside has also been the theme for most of my adult life, making me inclined to always try to find practical ways to better my surrounding for the benefit of the whole. My Fab Academy project regarding a portable water turbine originates from these elements and will hopefully benefit others as well.Final project
Developer: | Magnus St. Magnusson |
Category: | Electric generating device |
Skill: | Electric, 3d design, 3d printing, CNC mill |
Date Post: | 04 February, 2020 |
Tags: | Electric Turbine, Electric generation |
Magnús St. Magnússon © 2020| v1
Madefor FabAcademy