Wildcard Week
For this week's assignment we had to design and produce something with a digital fabrication process (incorporating computer-aided design and manufacturing) not covered in another assignment. I choose to create a composite, since it's also beneficial for my final project. For the final project I am creating a Electric GoKart in cooperation with Hakan Zayin. To fulfill this week's assignment I fabricated the steering wheel of the GoKart using a composite material.
Composites
A composite is a material made from two or more constituent materials with different physical or chemical properties. The different materials that create the composite function as either the matrix or the reinforcement. When these are combined, they produce a material with characteristics differences from the individual components. The reinforcement is the material that provides strength, rigidity and the ability to carry a load such as fiber, wood or fabric. The matrix is usually a viscous material that hardens to give shape to the composite and to protect the reinforement from damage such as epoxy, wax, resin or even melted plastic.
Computer-Aided Design
To create the design I used Autodesk Fusion 360. To get a full introduction on how to use Fusion 360 got to the Computer-Aided Design assignment. Below you can see the finished design of the steering wheel.
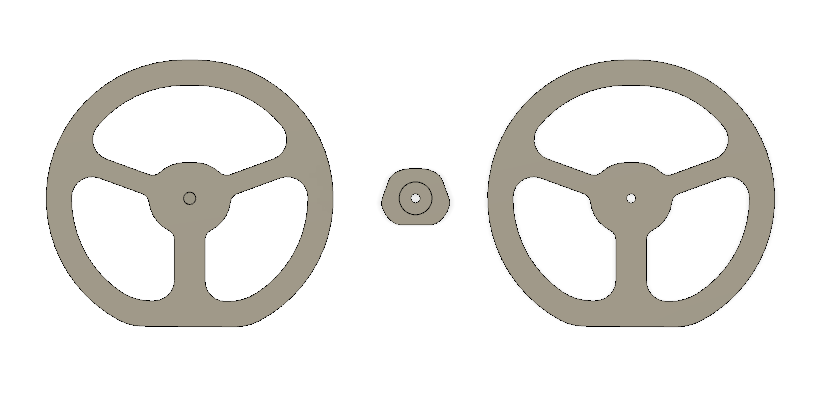
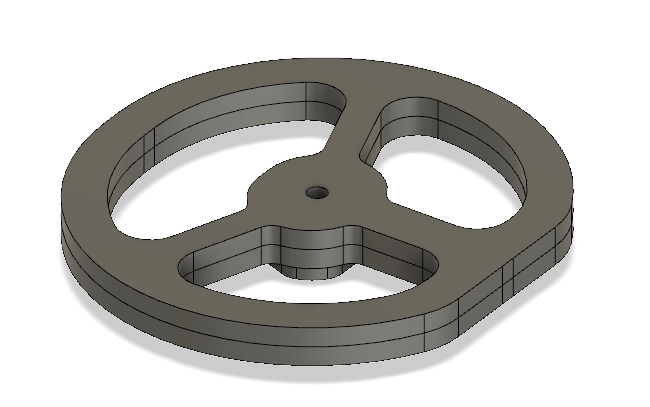
After exporting the file, I had to import it into Rhino to create separate layers for each job. Moreover I also checked if I had double lines by exploding them and then joining them again.
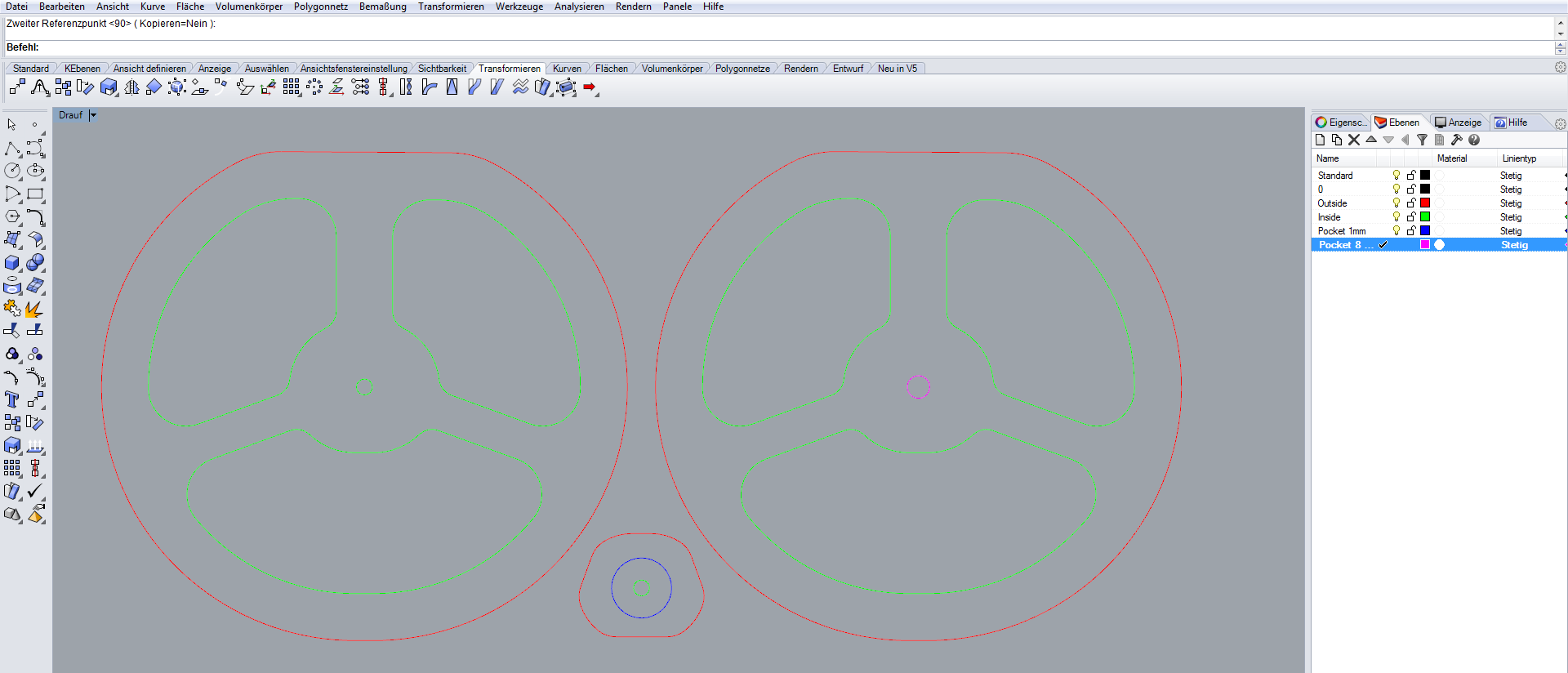
The Reinforcement
As outside reinforcement I used poplar plywood. There are many benefits that come with using poplar plywood. Poplar plywood is known for its extremely light weight, for its maximum moisture resistance, bending strength and durability. It can be used for building furniture, door and windows frames. Moreover it is also suitable for usage in humid areas, since its moisture resistance. Because of its relatively low weight it can be used to build high structural stresses in shop and interior fitting, shipbuilding, bathroom furniture and also in vehicle construction.
Next I used the CNC machine to mill the parts. To get more informations on how to operate the CNC machine go check the Computer-Controlled-Machining assignment. The video below shows the outside cut, done with a 6mm flat end mill.
To create the fillit I used a 20mm ball end mill. I also used the same 2D Design for the inner and outer cut and only changed the end z to 5mm.
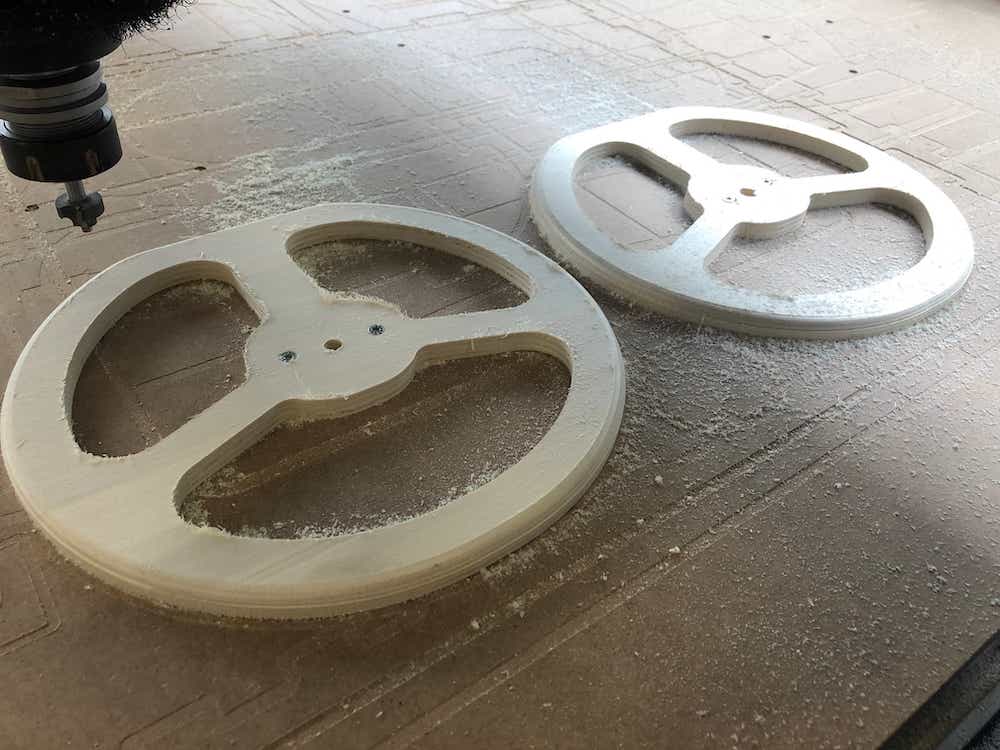
Underneath you see the final outcome of the CNC machine process.
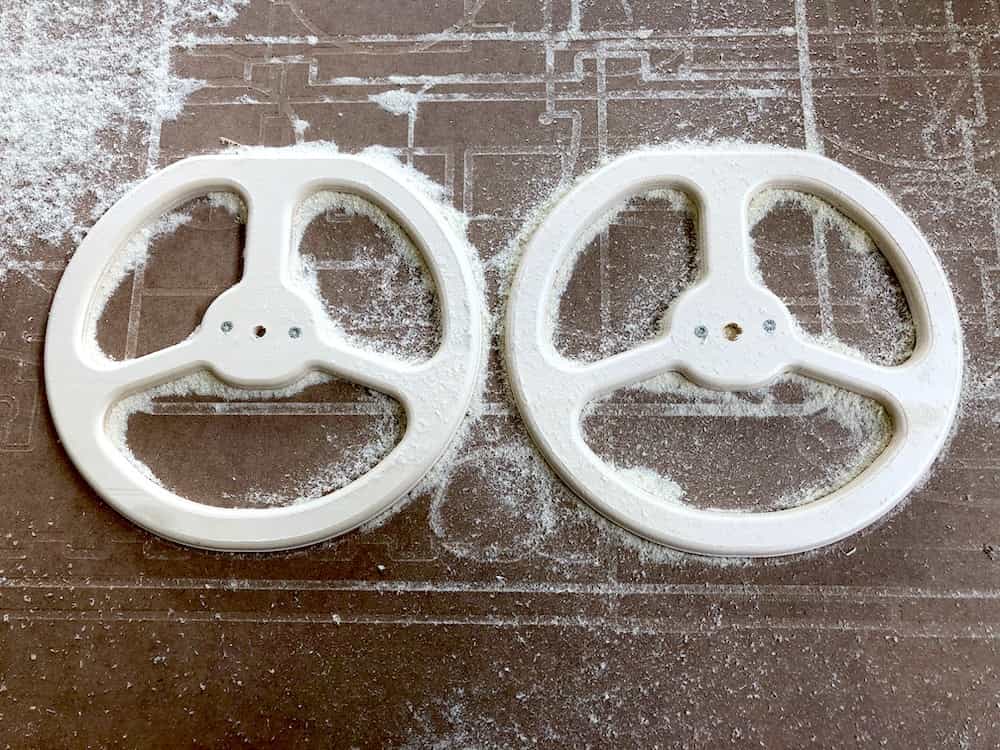
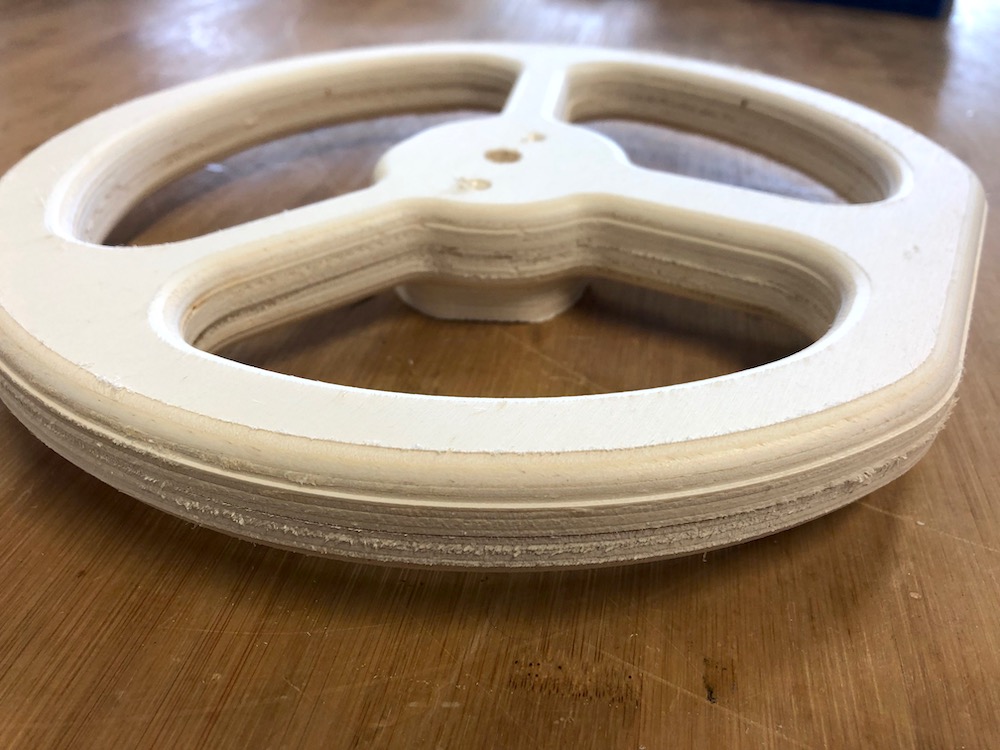
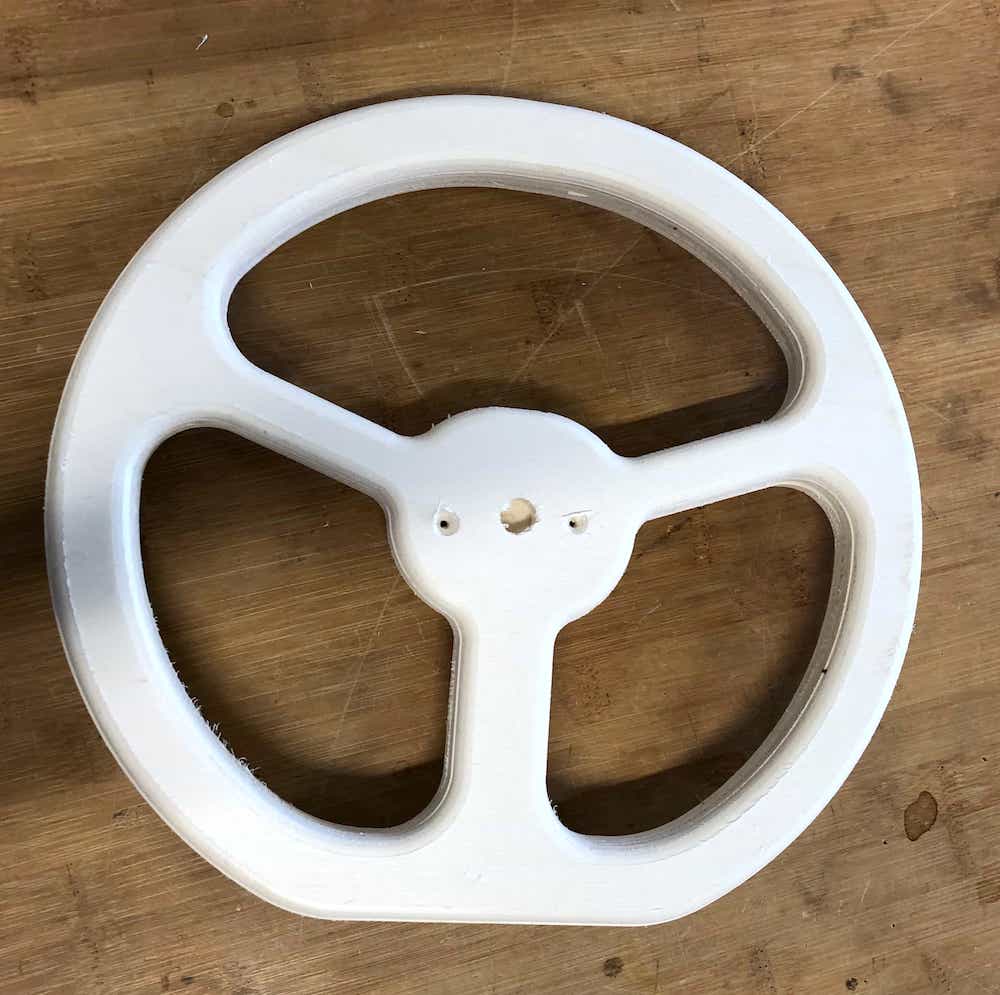
The second reinforcement I used was Jute. Jute is environmentally friendly and also the most affordable fibre in comparison to glass fibre or carbon fibre. The jute plant is easy to grow and requires litte water and fertilzier. Jute fibre is made out of two components a part is cellulose (major component of plant fibre) and another part lignin (major component of wood fibre), which makes it quit strong and durable. Therefore it has a wide range of applications. It can be used to make things such as rope, chair covers or rugs. It has even been considered to use jute in combination with sugar to build aeroplane panels. Instead of using carbon fibre-reinforced synthetic plastics to build aerplane panels, it has been discovered that the use of a combination out of jute fabric and epoxy resin improves it's mechanical properties.
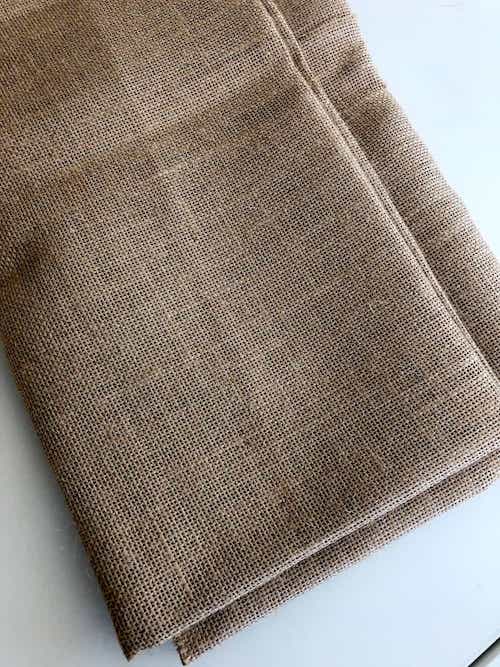
To cut the jute I decided to use the Epilog Zing Laser Cutter to get a perfekt cut out of the steering wheel. The idea is to sandwich the jute between the two parts of poplar plywood and then add the matrix to secure the materials. I had to experiment a bit to get the right vektor settings. The settings I used are:
When I first used these settings, it started a fire, because I used cardboard as a underlay. But luckily, I was always paying attention, so that I was able to extinguish the fire quickly and easily. This once again showed me how dangerous these machines actually are.
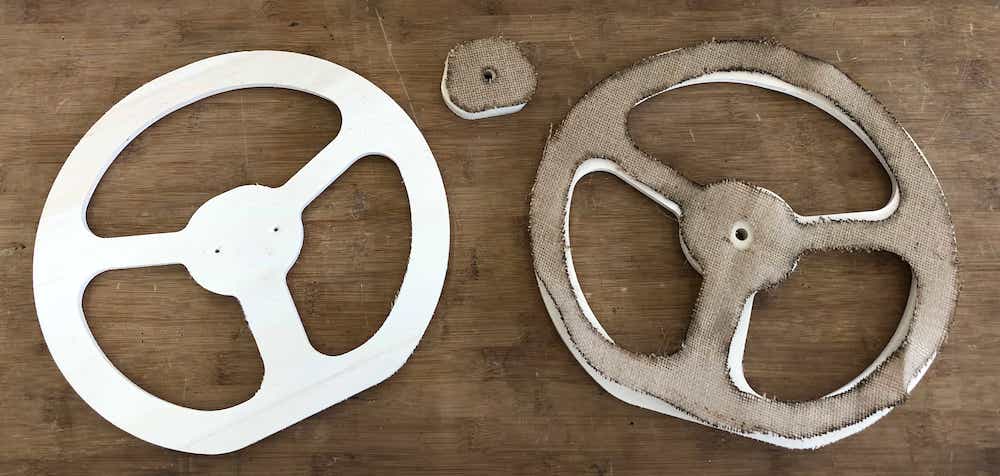
The Matrix
As Matrix to create the composite I used epoxy resin because of its reactivity that enables it to bond well to fibres. Due to its particularly low viscosity, the reinforcing fibres can be impregnated very easily, quickly and completely. Processing in injection processes and under vacuum is also possible. In the FabLab we have Epoxy Resin 3321. With the hardeners B1 and B2, a processing time of 0.5 to 2 hours can be achieved. In addition epoxy resin 3321 cures at room temperature. The mixing ratio by weight is: 100 Epoxy resin 3221 to 30 of hardner B1/B2.
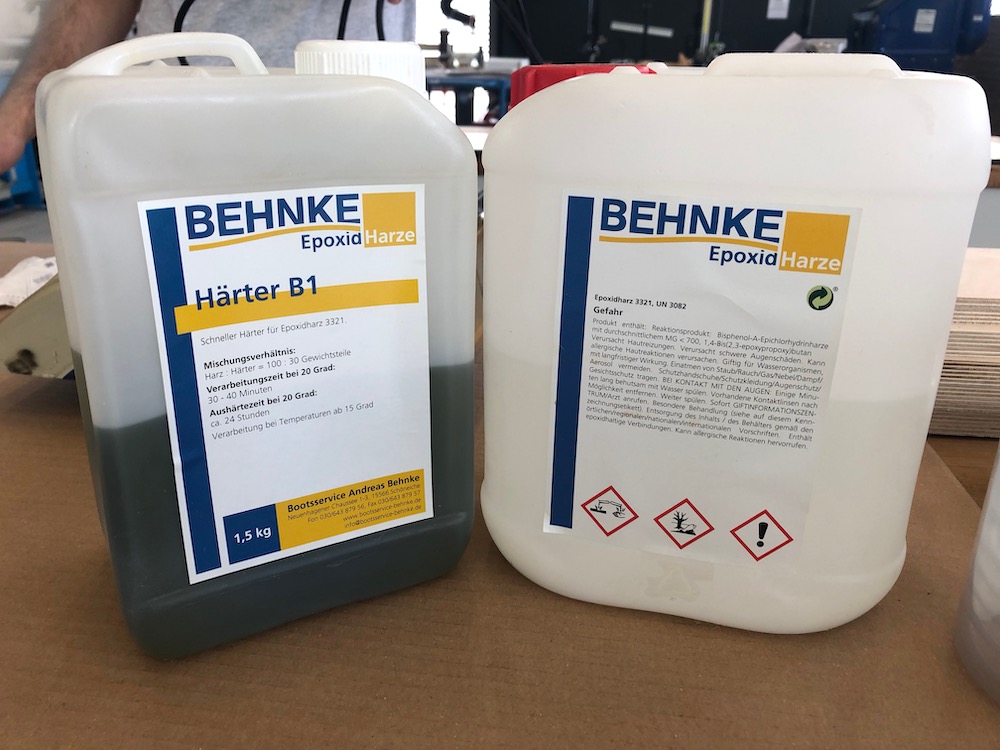
Please wear gloves and a mask during this process.
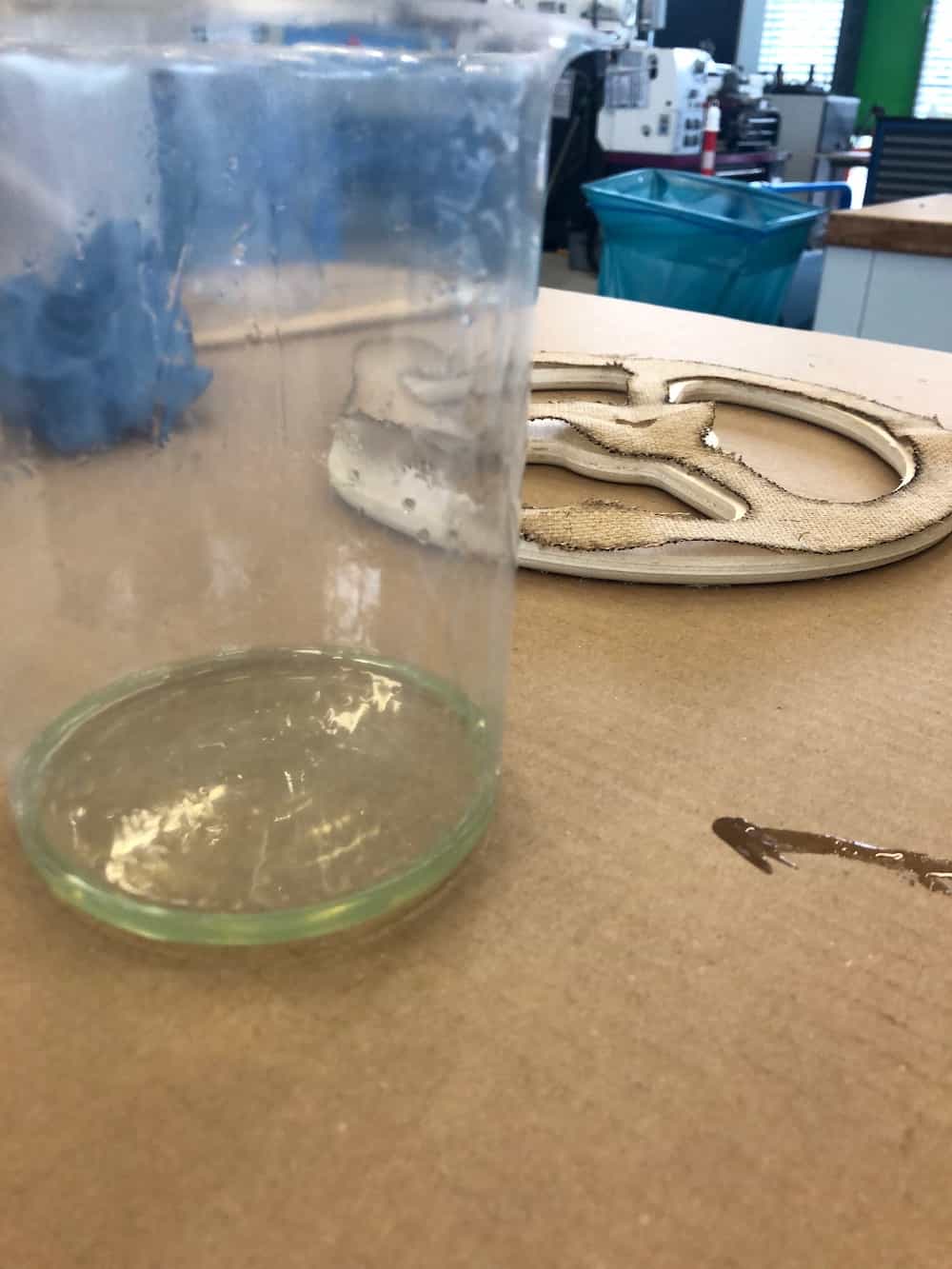
I used a brush to cover the fibre and poplar plywood with epoxy resin.
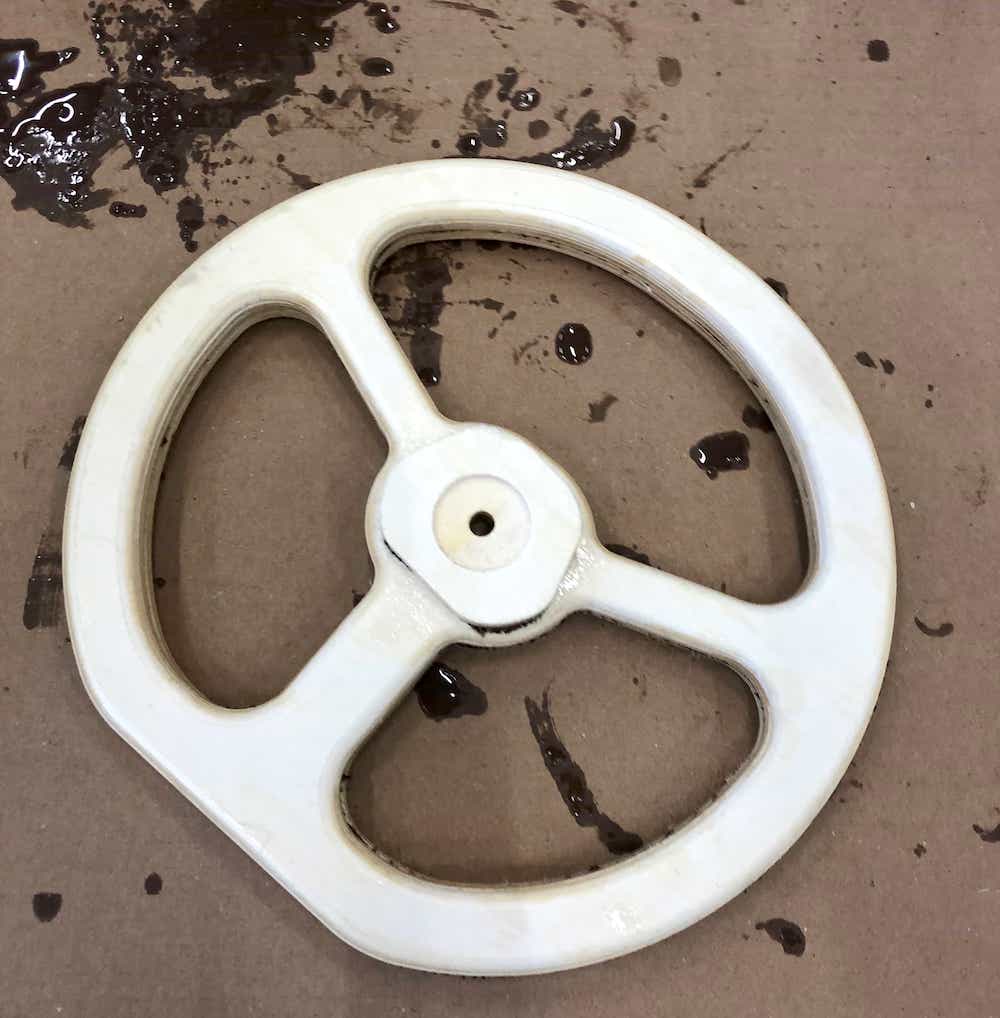
Next I wrapped the composite in cling film. In this way it prevents the epoxy from flowing out of the composite while its under vacuum. The cling film is also really easy to remove and does not react with the epoxy resin.
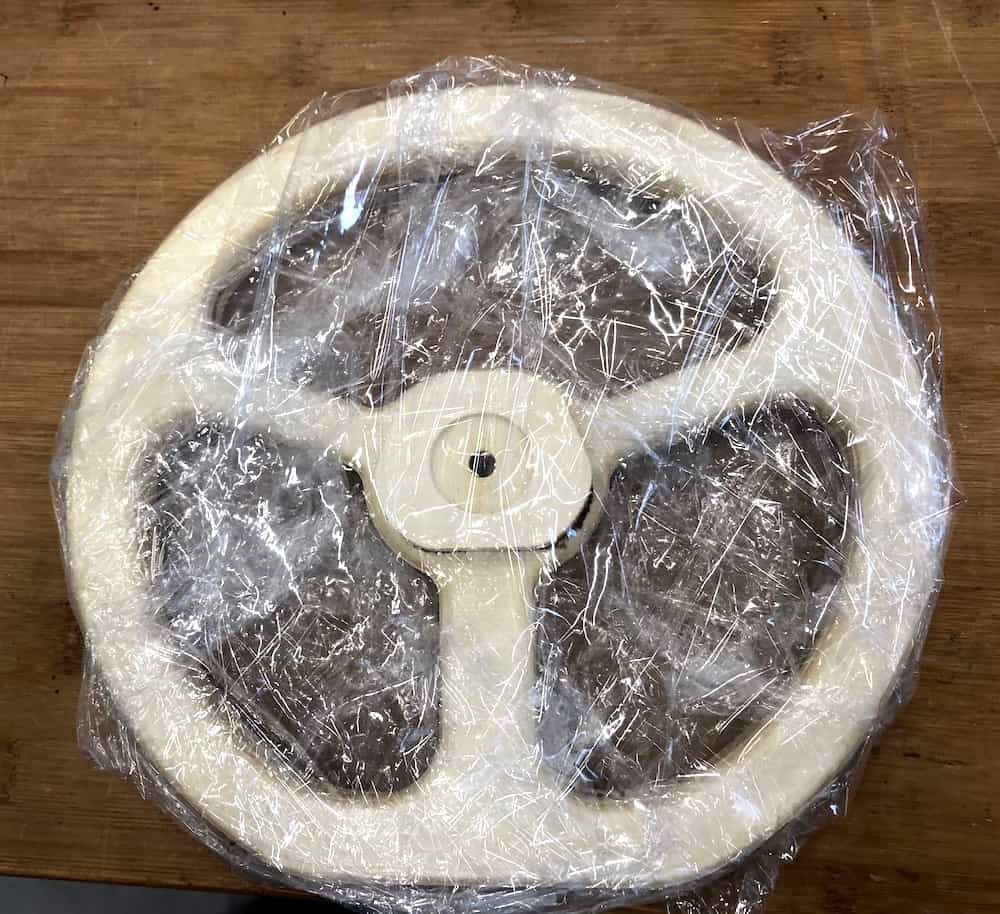
Pressing the Composite
I used a sheet of cardboard as underlay to prevent that some of the epoxy resin gets on the bed of the vacuum machine. I left the composite over night under vakuum.
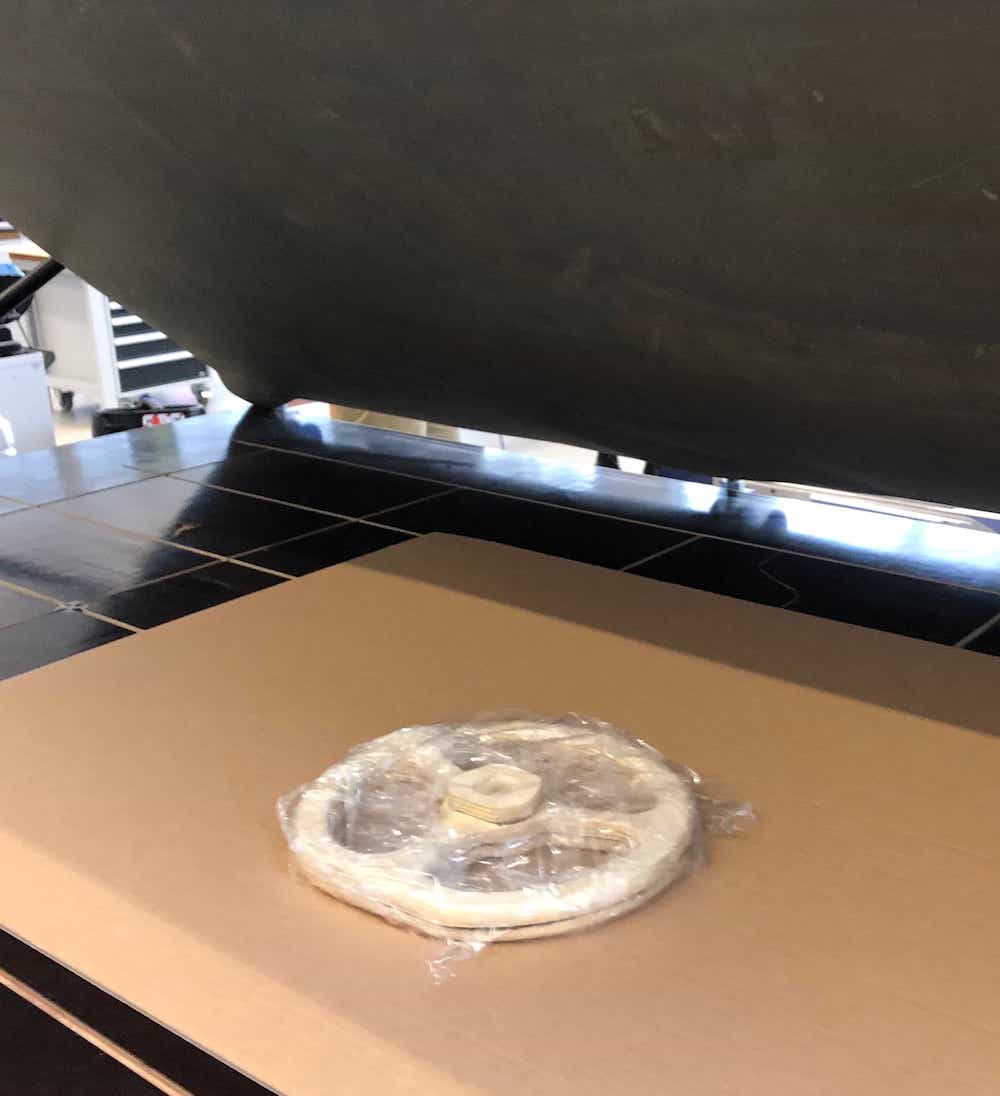
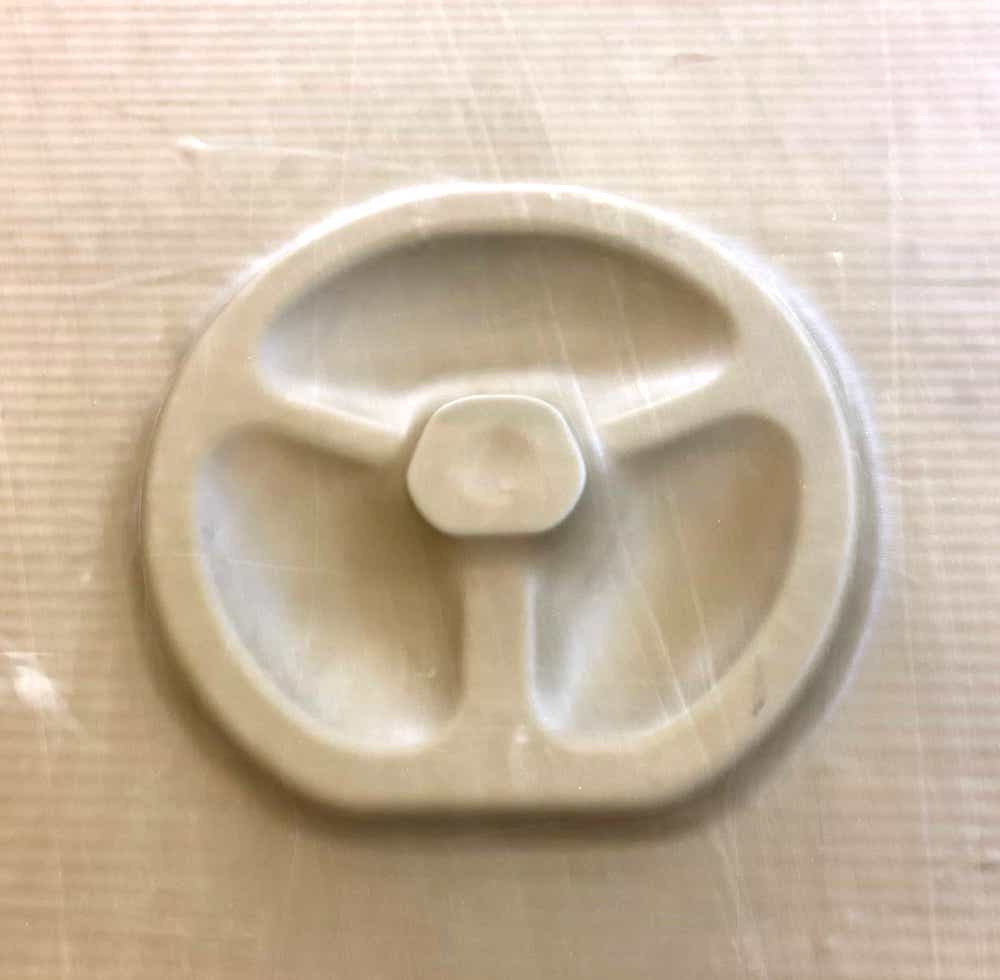
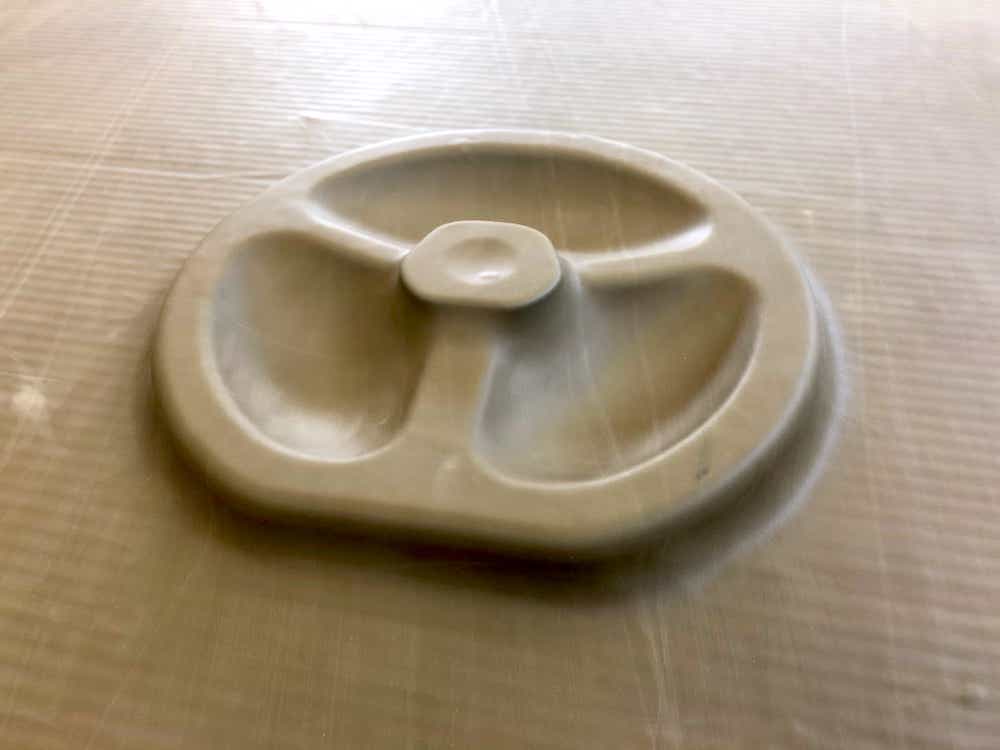
The next morning it was completely cured. The steering wheel can now withstand a lot of pressure without breaking. That was exactly the goal, since the steering wheel is the only thing you hold on to when you have an accident. It's extremely robust when compared to what it's made of (extremely light poplar plywood and jute).
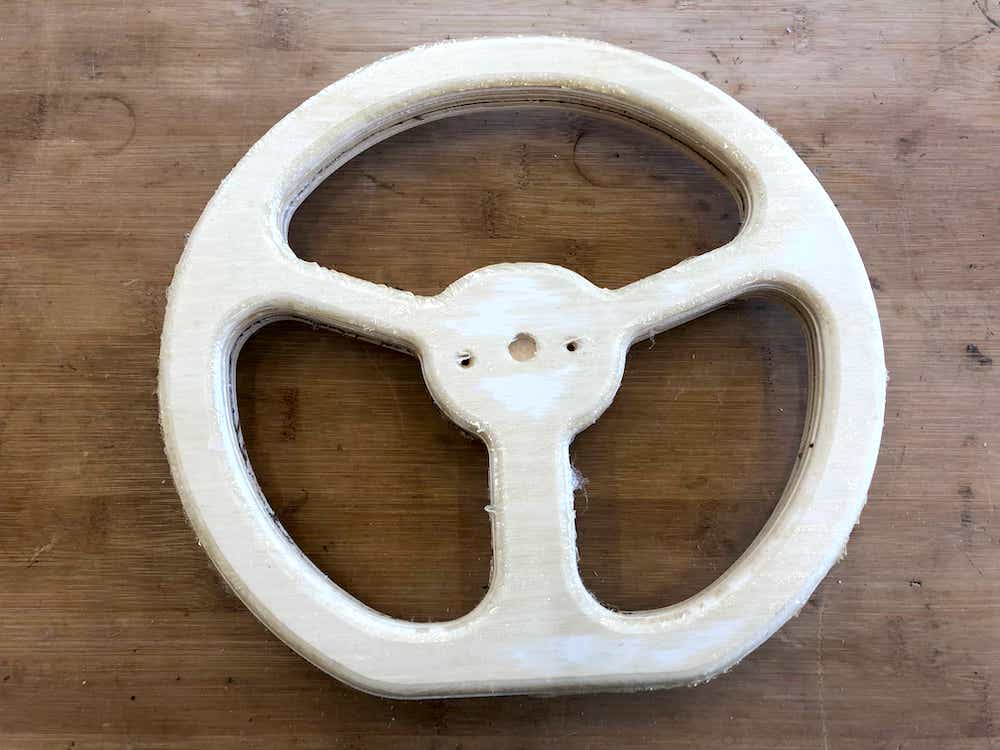
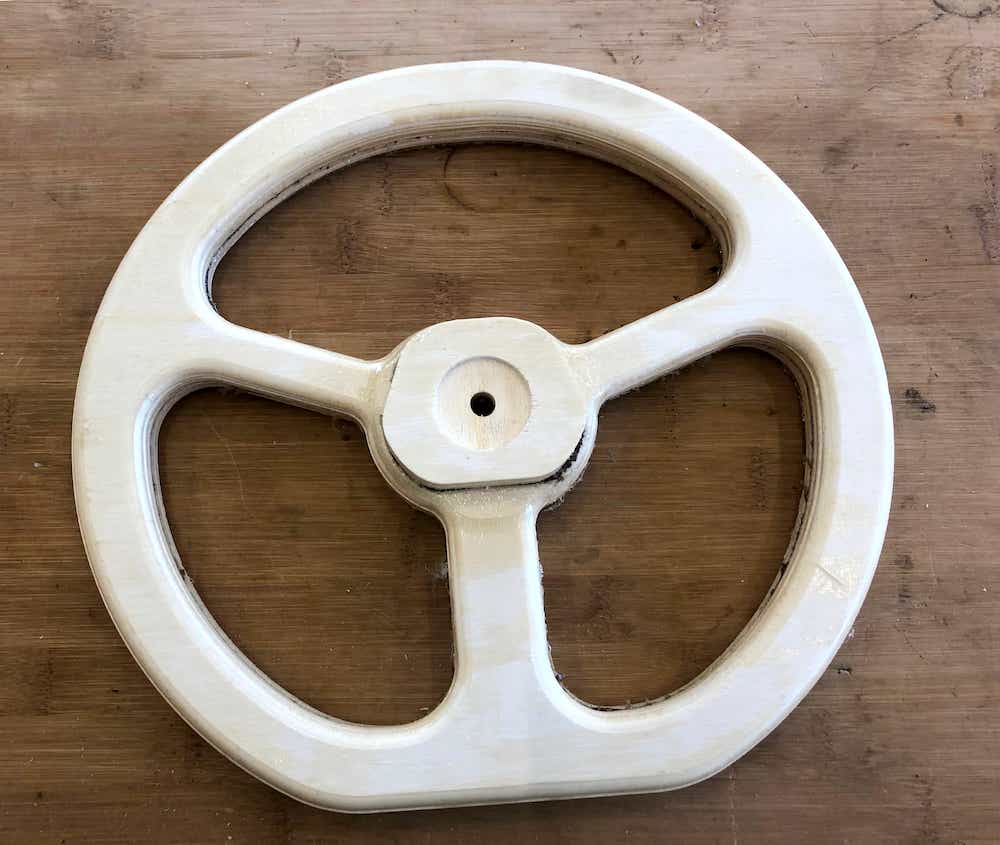
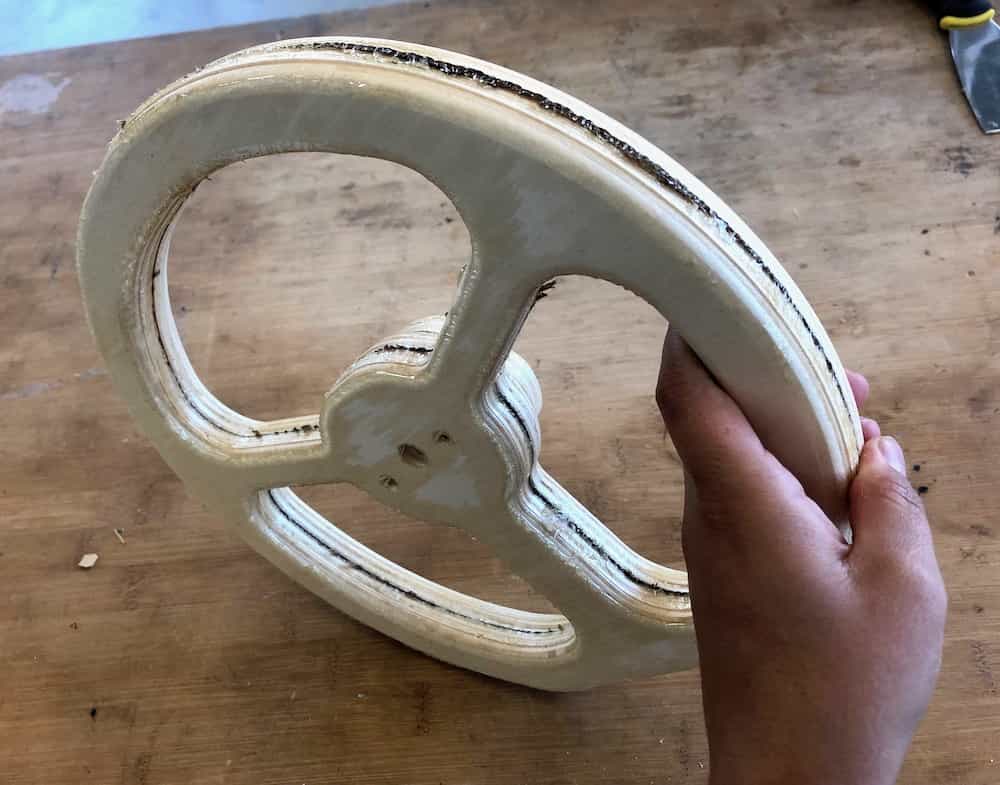
To follow the progress of the Go-Kart check the Final Project page.