Machinable wax is a term for an exceptionally hard synthetic wax mixed with plastic that features great machining properties, quality of finish, and dimensional accuracy. The material is recyclable and reusable, and is used to produce accurate molds, prototypes, and jewelry.
Machinable wax is an extremely hard wax that has been formulated to deliver exceptional machining properties including high resolution detail. Since it is harder and has a higher melting temperature than most other waxes, machinable wax can be machined, cut, or shaped using standard metalworking or woodworking equipment. High quality surface detail and dimensional accuracy are possible. Machinable wax is ideal for verifying CNC machining programs. Machinable wax is often used for precision lost wax casting. It is available in both blocks and cylinders. It features a combination of properties unique to the tooling and prototyping world. Most notable is its non-abrasive, self-lubricating, and self-releasing characteristics, which make it an ideal material for many challenging applications.
The shavings and unused pieces of material can be re-melted and formed back into useable material. This attribute can substantially reduce the cost of using machinable wax over other materials. The self-releasing properties of machinable wax make it an ideal choice to use as a master model. Epoxies and polyurethanes can be poured directly onto the wax surface without the need for sealers or release agents.
3. Silicone Rubber
Silicone rubber is an elastomer (rubber-like material) composed of silicone-itself a polymer-containing silicon together with carbon, hydrogen, and oxygen. Silicone rubbers are widely used in industry, and there are multiple formulations. Silicone rubbers are often one or two part polymers, and may contain fillers to improve properties or reduce cost. Silicone rubber is generally non-reactive, stable, and resistant to extreme environments and temperatures from - 55 to 300 deg C (-70 to 570 deg F) while still maintaining its useful properties. Due to these properties and its ease of manufacturing and shaping, silicone rubber can be found in a wide variety of products, including voltage line insulators, automotive applications; cooking, baking, and food storage products. Reference- Read more.
Moldsil-15 Plus Silicone rubber- (Part-A): Moldsil 15 plus is a room temperature Vulcanizing Silicone Rubber for making strong and flexible molds for excellent reproduction of the master and having superb release characteristics. It is compatible with various master and casting material s. This grade has been specially designed to create molds with long life.
This is a flowable grade, having high mechanical strength and cures with various catalyst options (depending on the application requirements) at room temperature to a flexible elastomer, well suited for detailed and exact reproduction of artifacts, figures, architectural items and similar objects. Moldsil-15 PLUS will reproduce the finest detail of the master and is suitable for a variety of art related and industrial applications such as mold making for reproducing prototypes, furniture, architectural items and sculptures.
Features:
- Flowable type high strength silicone rubber curing at room temperature- Excellent detail reproduction.
- Good mechanical properties - leading to long service Life. It is uitable for deep undercut molding.
- Highly elastic and excellent release properties- for easy de-molding.
- Excellent chemical resistance - compatible with most molding materials with long service life.
- Low viscosity - easy flow and excellent detail reproduction.
Catalyst (Part-B): The choice of catalyst depends on the application method and the speed of cure needed. Moldsil-15 can be cured in to elastomeric products using the following cure options:
1. CAT-24: Slow catalyst,Takes about 24 hours at room temperature.
2. CAT-16: Medium speed Catalyst,Takes about 16 hours at room temperature.
3. CAT-04: Rapid Catalyst,Takes about 4 hours at room temperature
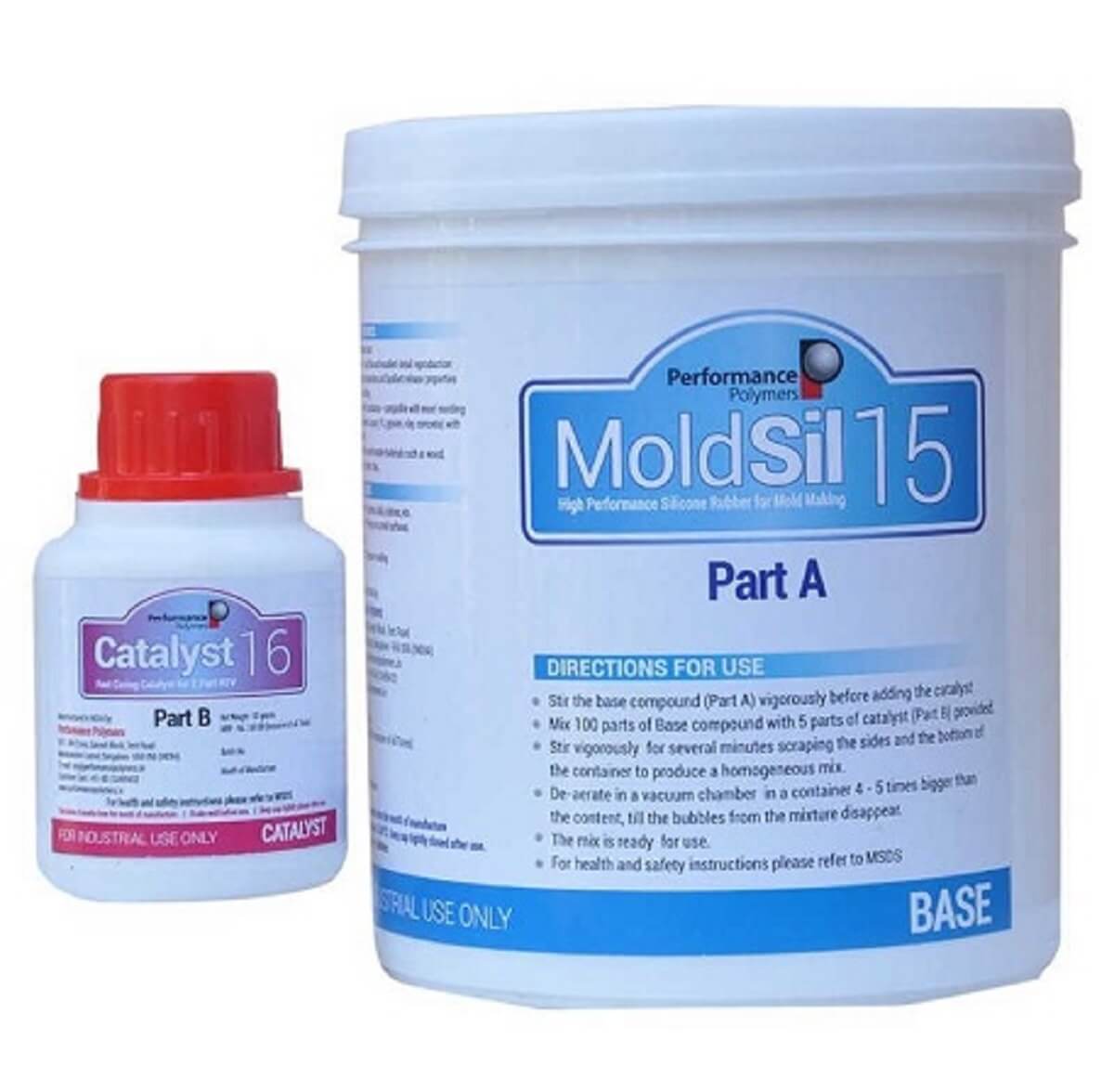 |
Reference
Ecoflex Series Silicone rubber: Ecoflex rubbers are platinum-catalyzed silicones that are versatile and easy to use. Ecoflex rubbers are mixed 1A:1B by weight or volume and cured at room temperature with negligible shrinkage. Low viscosity ensures easy mixing and de-airing. Cured rubber is very soft, very strong and very stretchy, stretching many times its original size without tearing and will rebound to its original form without distortion. Reference- Read more.
Measuring and Mixing - Before you begin, pre-mix Part B thoroughly. After dispensing required amounts of Parts A and B into mixing container (1A:1B by volume or weight), mix thoroughly for 3 minutes making sure that you scrape the sides and bottom of the mixing container several times. After mixing parts A and B, vacuum degassing is recommended to eliminate any entrapped air in liquid rubber.
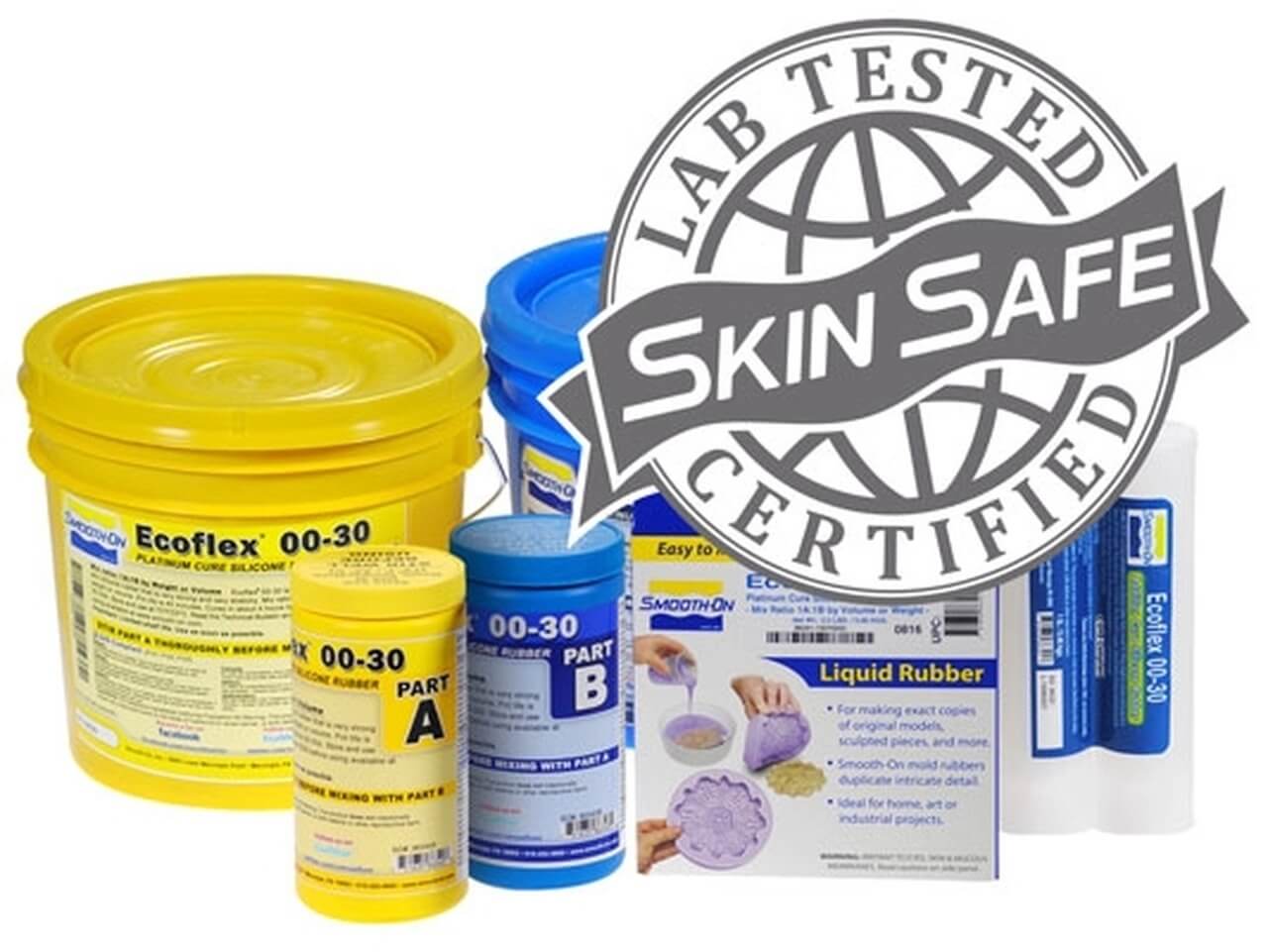 |
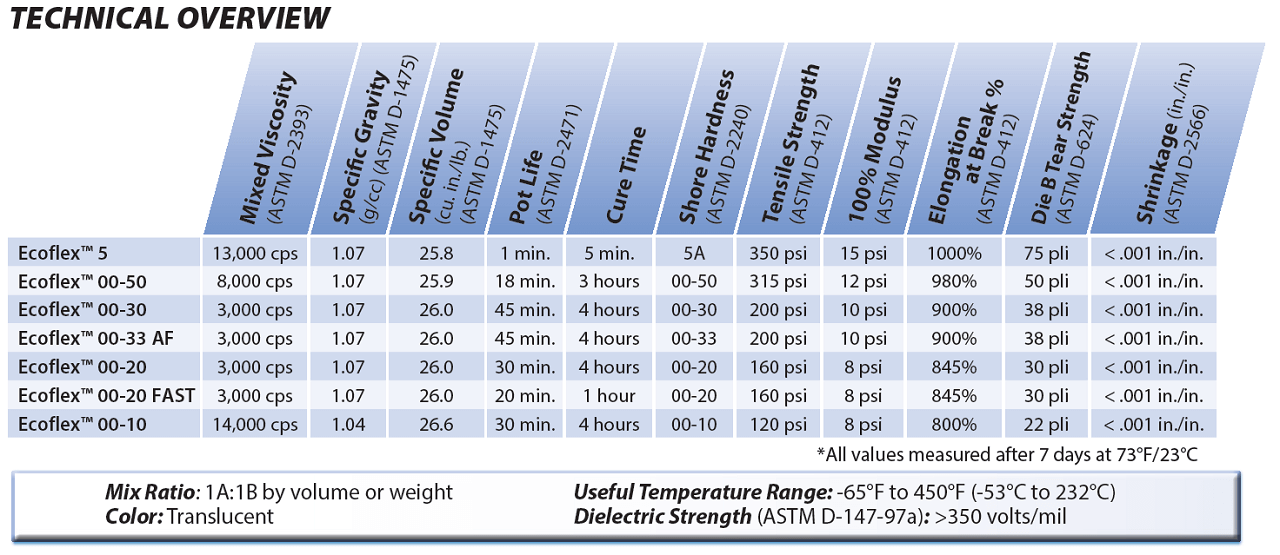 |
Reference for Data sheet of Ecoflex Series Silicone rubber
The Basics of Resin Casting
As the name suggests, resin casting is a casting process that involves the use of synthetic resin. To better understand how it works, you must first look at the synthetic resin used in this casting process. Synthetic resin is any type of resin that is converted into strong and rigid polymers via curing. In other words, it begins in a liquid state but converts to a solid state after being cured.
In resin casting, liquid synthetic resin is mixed with a curing agent- typically at room temperature or near-room temperature. Next, the two substances are poured into a mold cavity. The curing agent then converts the resin into rigid polymers, essentially hardening it. After this chemical reaction has finished, the hardened casting is ejected and removed from the mold cavity. Reference#1- Read more., Reference#2- Read more.
4. Epoxy Resin
Epoxy resin is known for its strong adhesive qualities, making it a versatile product in many industries. It offers resistance to heat and chemical applications, making it an ideal product for anyone needing a strong hold under pressure. Epoxy resin is also a durable product which can be used with various materials, including: wood, fabric, glass, china or metal. It is important to note, however; epoxy resin is not considered to be water resistant. Repeated moist or wet conditions can cause deterioration over time which will affect durability. Reference- Read more.
Casting epoxy resins are suitable for a variety of industrial and art related projects requiring a rigid, clear finished casting. It is mixed 100A:30B by weight (gram scale required) and features a very low viscosity for easy mixing and minimal bubble entrapment.
Details:
- Clear and optically transparent with a glass clear quality.
- It is a low viscous resin made specifically for casting.
- Use 100 parts resin to 30 part hardener by volume (100:30) to ensure a hard finish once set. You MUST follow the instructions accurately. Do NOT change the mixing ratio - this will alter the properties of the resin
- Stir Part A and Part B together thoroughly for at least 3 minutes.
- If cured at 25 degree C this resin should be touch dry within 24hours.
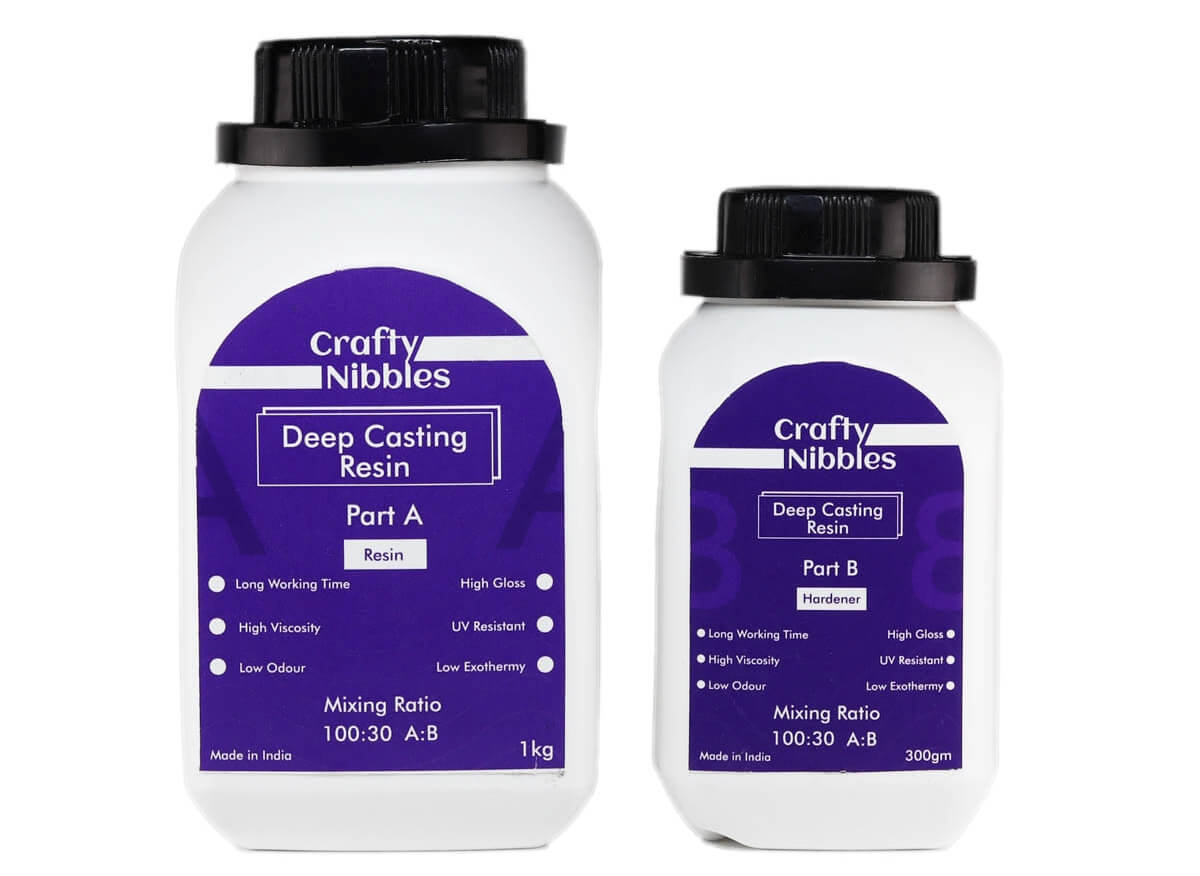 |
Reference
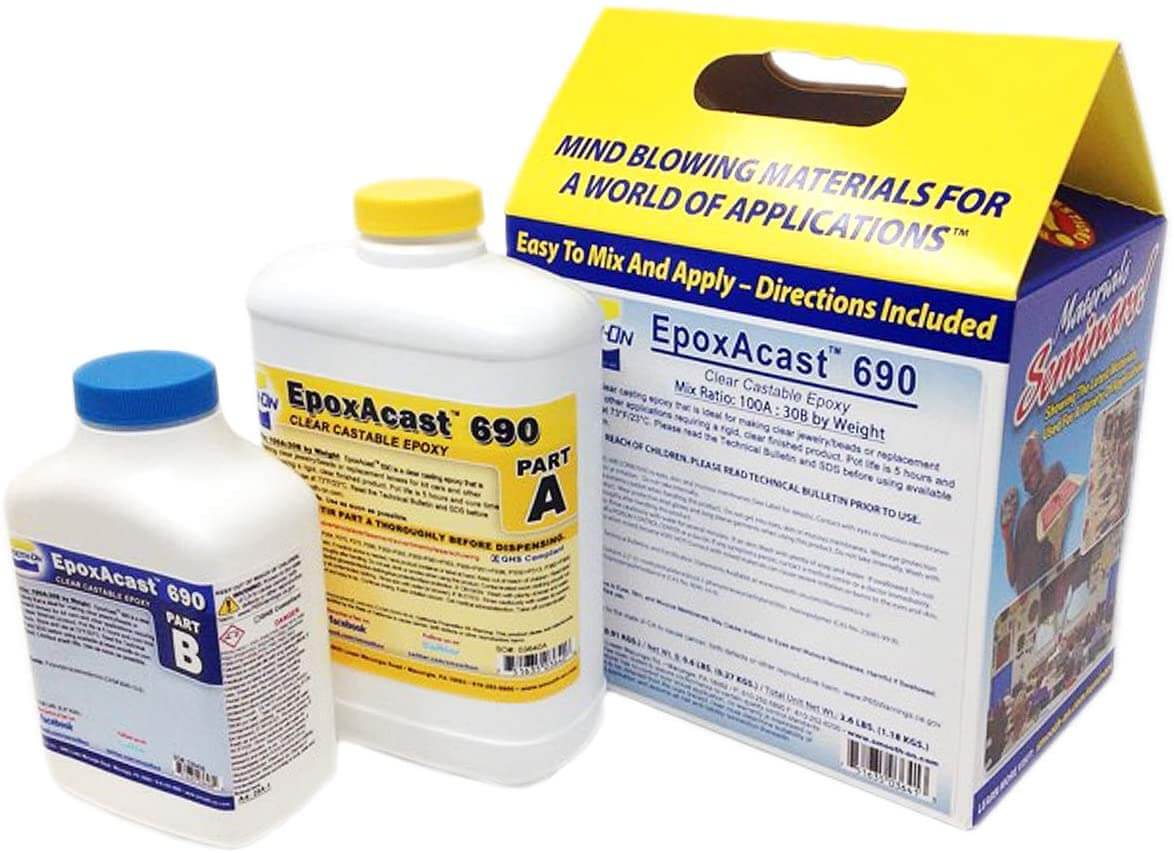 |
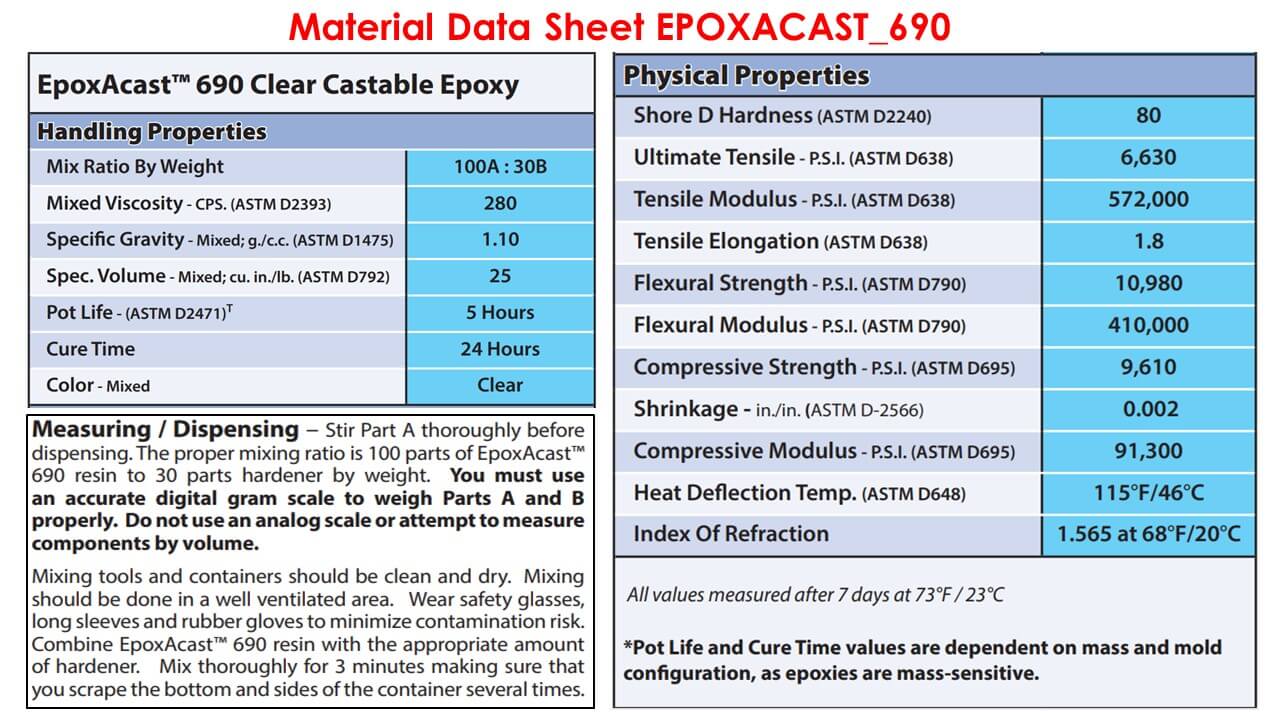 |
Reference
5. Instamold
InstaMold is a temporary mold-making compound that is activated with water. It's perfect for making a quick and perfect reproduction of your treasured memorabilia, including 3D object.
InstaMold is perfectly safe to make a body cast with, and will make a replica which includes the finest of detail. InstaMold does not stick to the original object and once you have your temporary mold you can then make a number of permanent castings using other materials such as ArtPlaster, PermaStone, resin, or wax. InstaMold does not work well with clay. Reference- Read more.
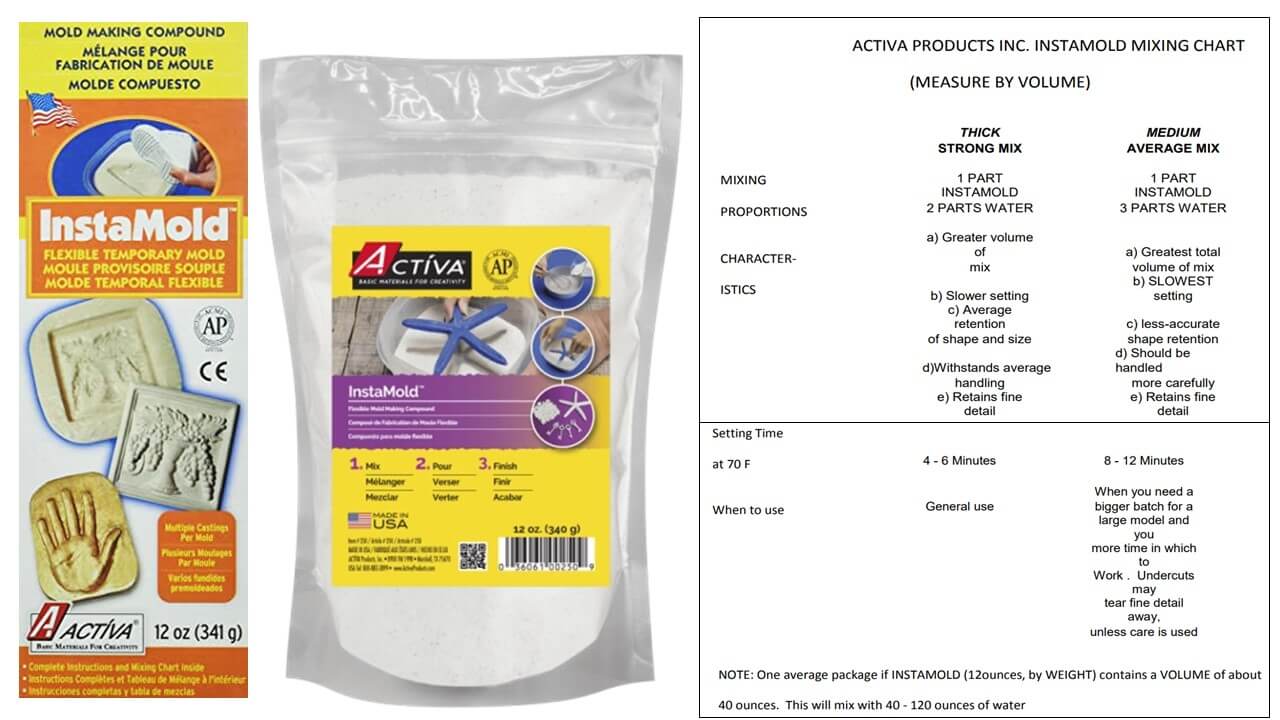 |
Reference- Data sheet for Instamold
6. Hydro-stone gypsum cement
Hydrostone superx gypsum cement is an excellent product for manufacturing solid cast architectural, art novelty and statuary products. Hydrostone superx gypsum cement is extremely hard and has high compressive strength. It has high water absorption resistance while giving extremely fine detail duplication.
It is used primarily in tooling and high quality art object applications. This is an extremely wear-resistant material. It cures Bright White when fully dry. Hydrostone is 40% to 50% harder than regular casting plaster. Works much like plaster in mixing, pouring, and setting. Reference- Read more.
Reference- Data sheet for Hydrostone