Juan Ranera
Fab Academy 2013 Participant
Mechanical design, machine design
The work we have decided to do is design a 3d printer. The reference printer is the
SNAP MTM created two years ago and our work is
remove the superfluous and make it work with the least amount of parts.
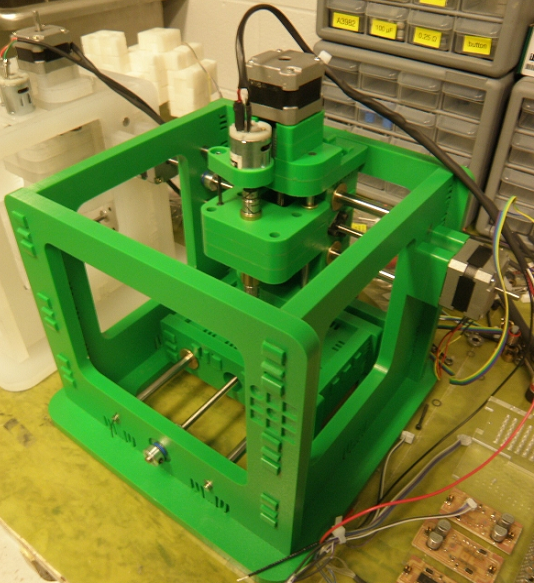
To make this work we will divide the class into several groups and each group will make a different task.
There are 3 main work areas:
Mechanical design: We have to do a change about the previous version. Now we have to move the axes using pulleys and plastic belts instead of drive shafts (rotary to linear motion) proposed in the previous version and this way reduce costs.
Electronic development:
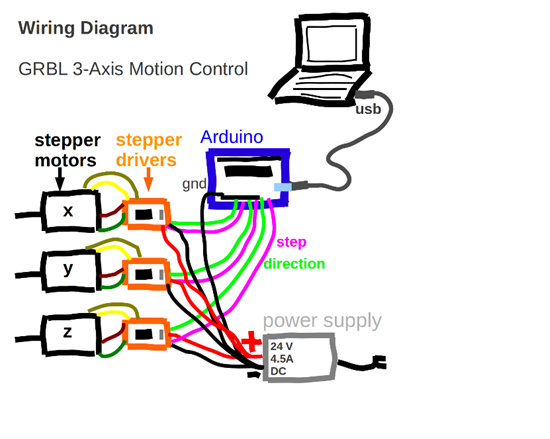
Software:
We have to adapt the older software to the current mechanical modifications.
_________________________________________________________________________________
One of the tasks in which I participated, has been in the manufacture of the belt.
Mechanical design: TIMING BELT
We have to move the axes using pulleys and plastic belts instead of drive shafts (rotary to linear motion) proposed in the previous version and this way reduce costs. Luciano has proposed do the belt and the gear ourselves and I thought it was impossible to do...
At first we design the gear to do the first test.
Material: methacrylate
Width: 3mm
Distance between teeth: 5,49mm
Then we design the belt and we did several tests adjusting the distance between teeth and the size of the holes. We also made some engraves to facilitate bending.
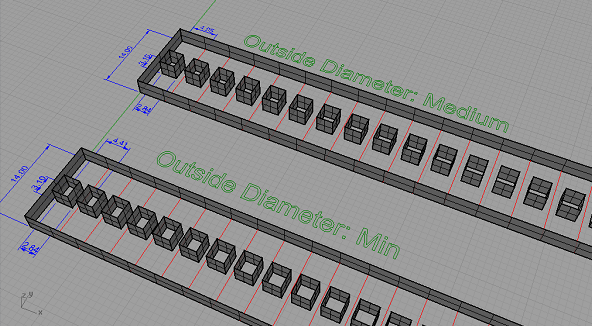
Material: Polypropylne
Width: 0,8mm
Distance between holes: 5,49mm
Note: We cut the belt with Epilog Legend 36EXT and the best configuration after several tests was: Polypropylene (0.8mm)
CUT:
Speed: 40% Power: 75%
ENGRAVE:
Speed: 80% Power: 15%
Finally I was very surprised with the result:
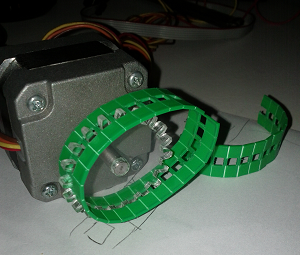