Final Project Requirments
In this week we are assigned to make the final project parts. Describe how the 2D and 3D design of the patقs .What parts for laser cut. In general we are assigned to present the final project using what we learned during the journey in Fab Academy. To show our understanding for the assignments done in previous weeks and make something using Digital Manufacturing.
The Idea
The idea is to monitor the most important parts of the diving equipment. We are aware that the diver underwater must breath from his regulator all the time. He has limited time to stay alive if he stop breathing under water for any reason so I used monitor the diver breath by adding sensors to the regulator and the Tank air.
Assignment Requirments
Computer Aided design
Computer Aided design
In this step I used to design the required parts for the project
BCD Connector
The BCD connector is designed as a port for the hose to inflate the BCD. the hose is connected to the SOV which can be activated electrically to release the air supplied from the tank.
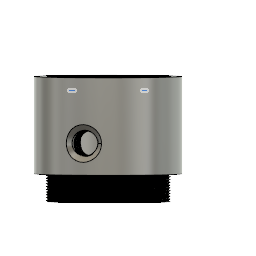
Micro Switch water proof Housing
The micro switch housing is designed to cover the Microswitch and isolate it from water. the micro switch housing consists of the housng, the diaphragm and the cover. The Diaphragm is required for flexible movement of the microswitch mechanical link and isolate it from the water
Regulator sensor cover
The regulator sensor cover is used as a housing for the micro switch housing. It is threaded to be fit for the reglator female thread. The diving reglator has a liver which is acting on the diaphragm. When the diver start inhalation in the closed area, the diaghragm will push the liver which will open the air valve to release amount of air for breathing.
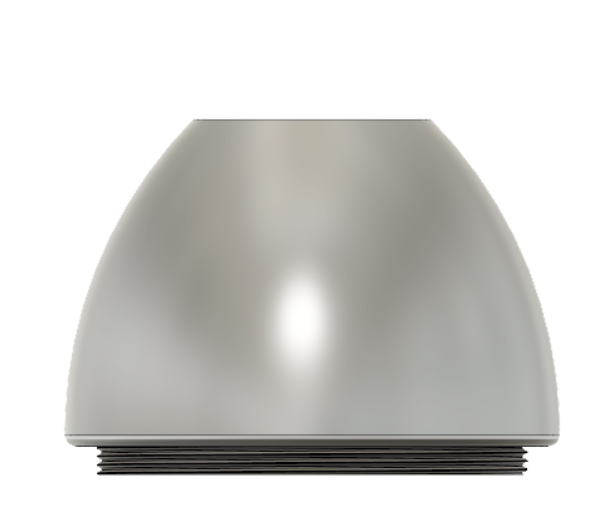
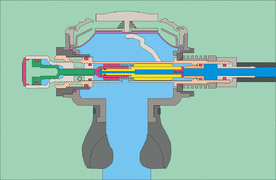
Electronics Box
The electronic box is designed as a water proof container for the microcontroller, batteries and all electronics stuff required for the the project. since the box is not suitable under water and I do not have enough time to modify it. I planned to make another one for the project later after Fab Academy
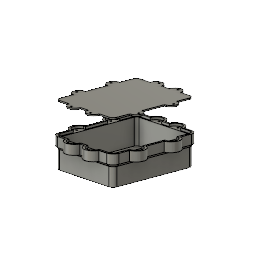
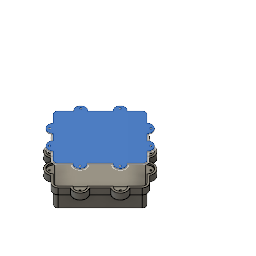
Additive Manufacturing (3D printing)
For the final project I used to manufacture the electronic box, Microwitch housing and the Inflation adapter. Since the electronic box must be waterproofed up to 40 meters I made a box to be ready for the final project presentation and delay the water proof case manufacturing after fab cademy during the development period. I designed the electronic box, Microwitch housing and the Inflation adapter using Autodesk fusion 360.
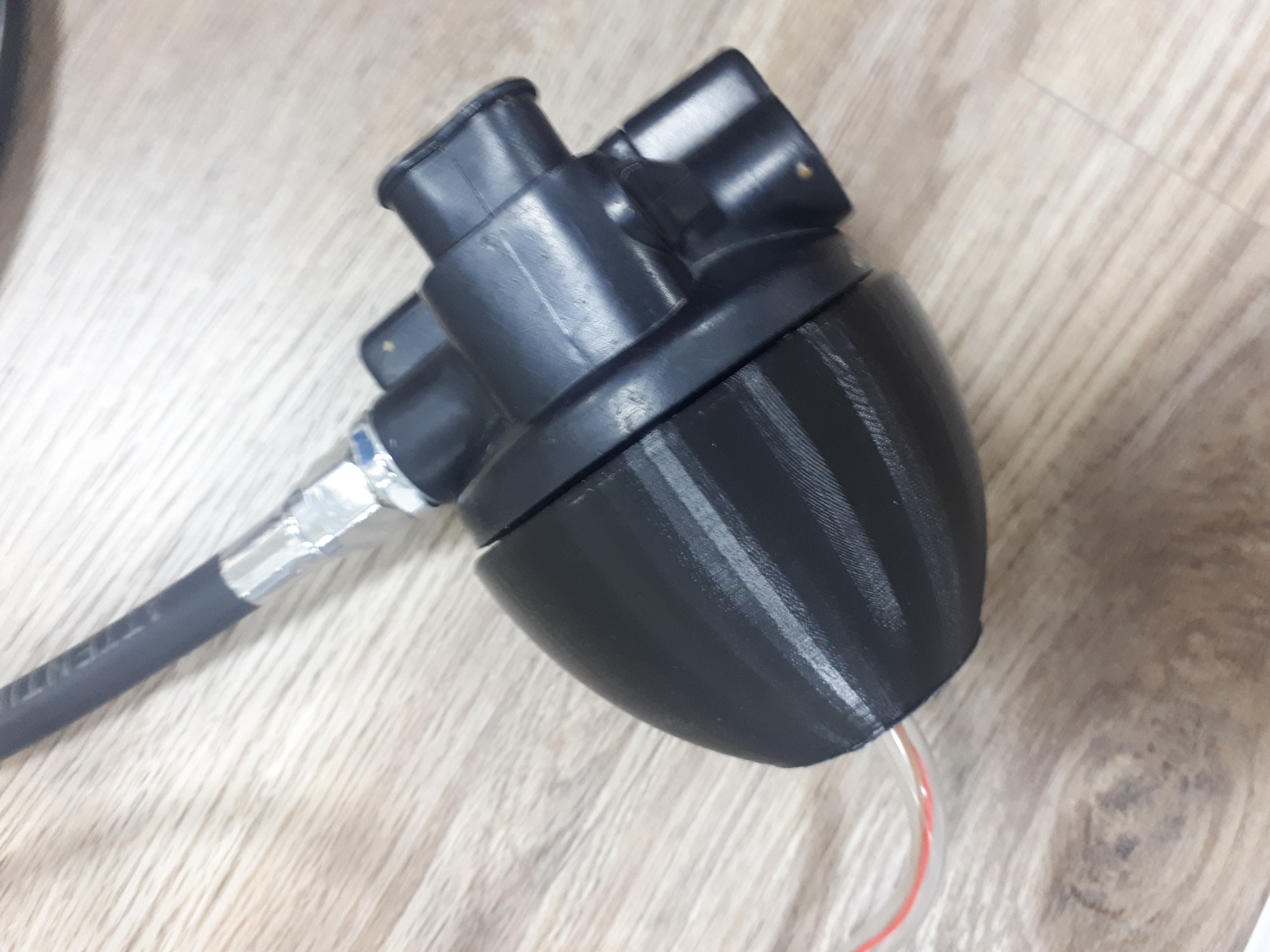

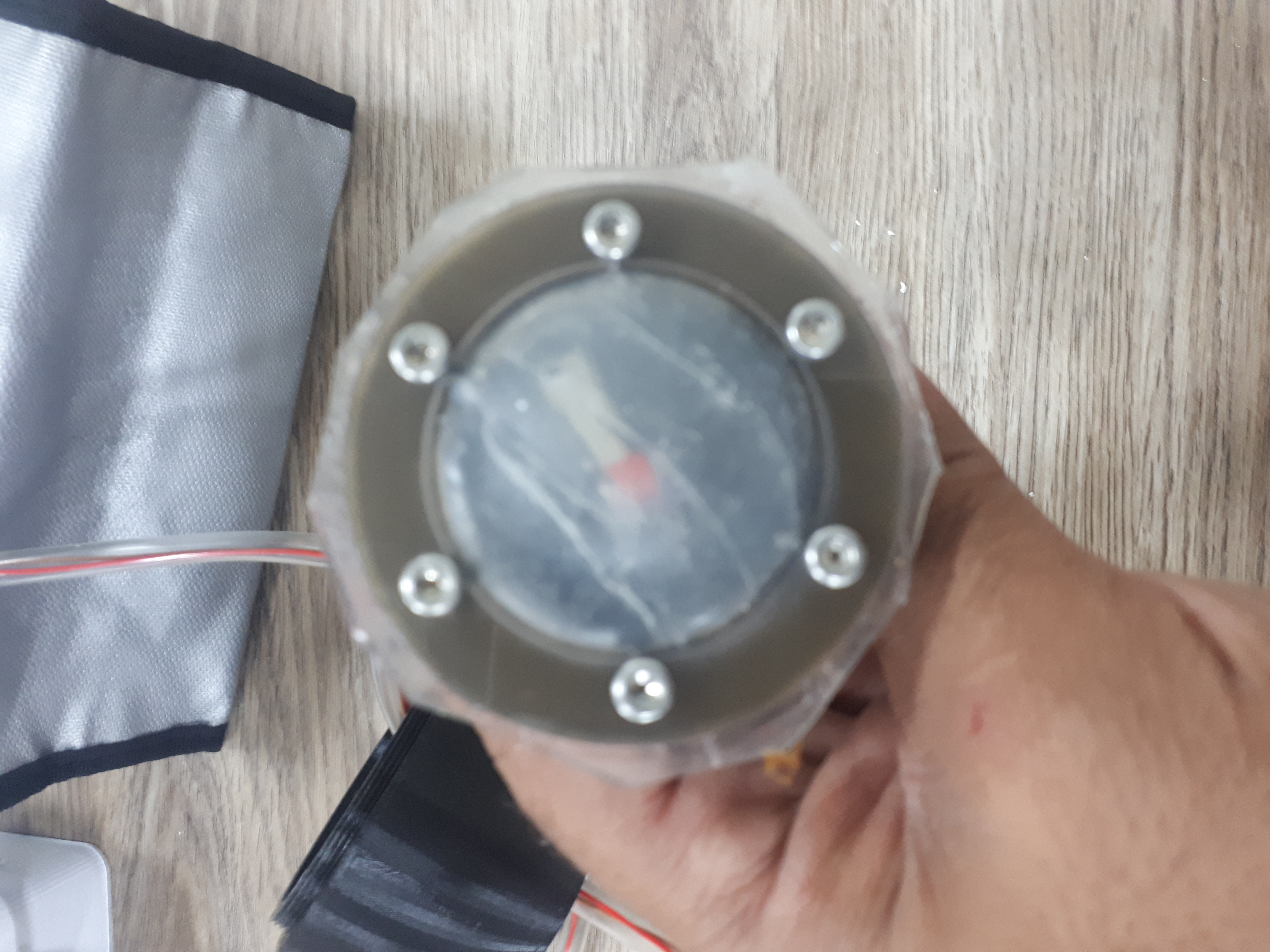
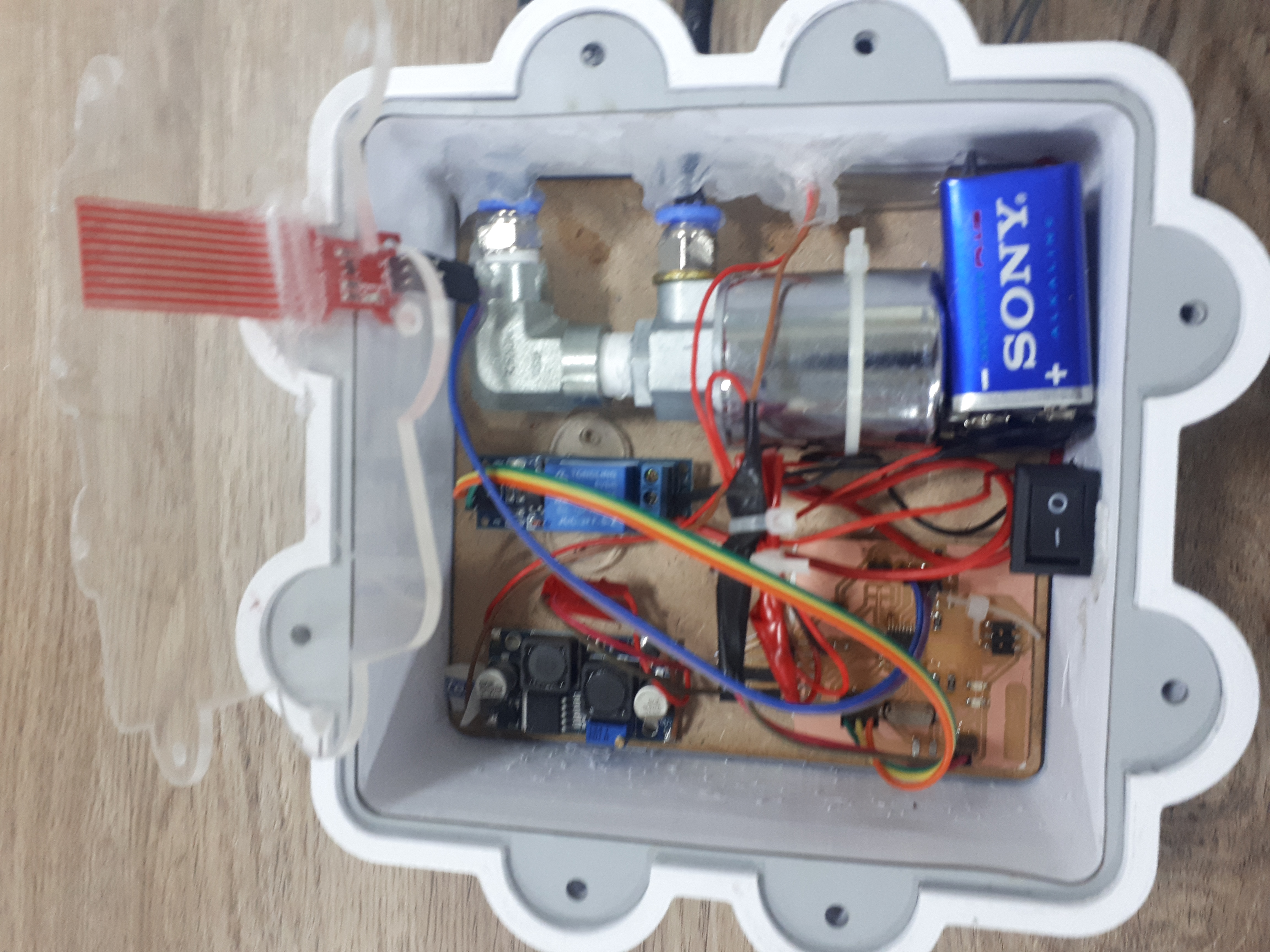
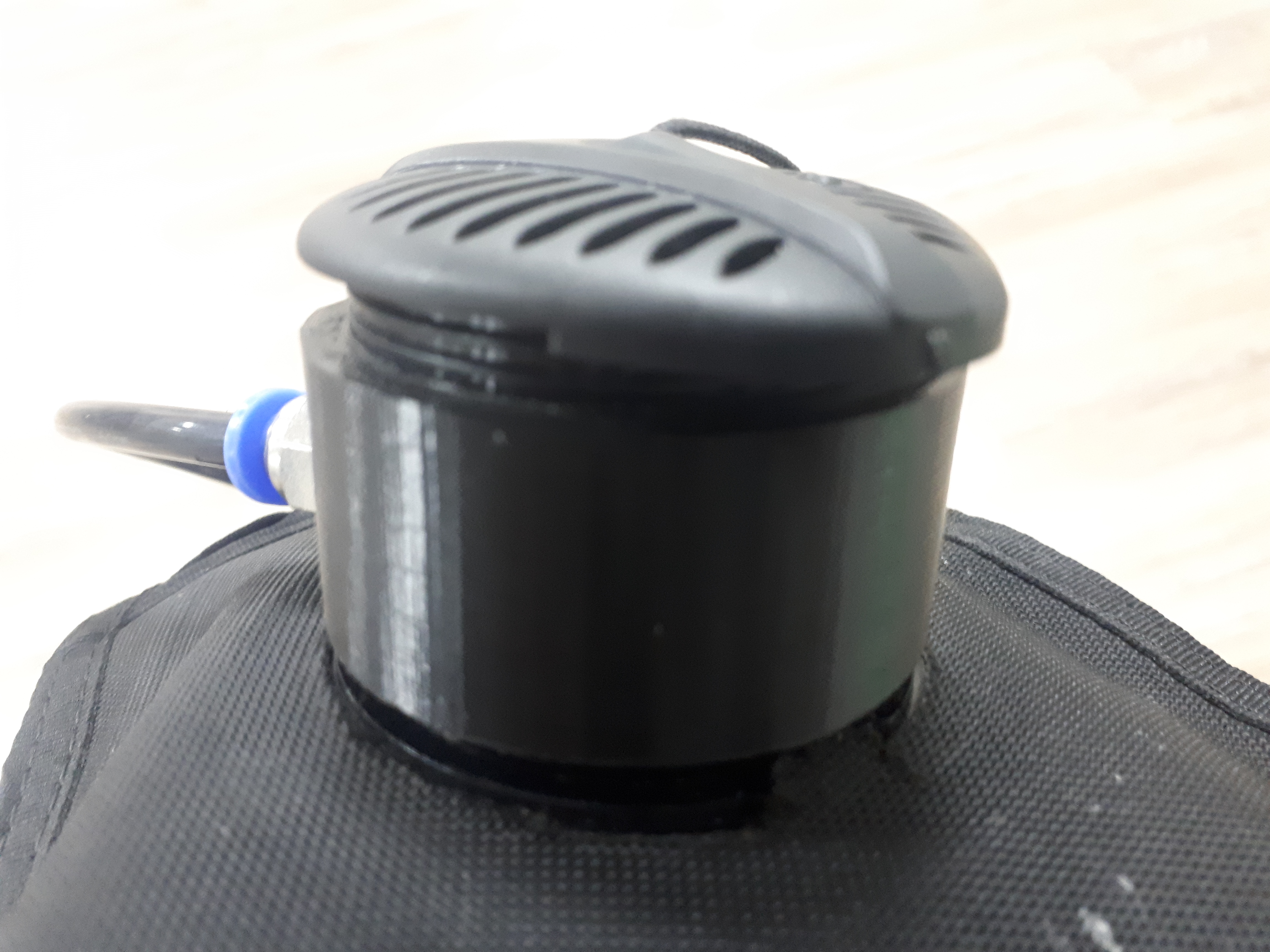
Laser Cutting
In this section I used to laser cut to make the microswitch cover, the box cover and the rubber seal for the electronic box. I used 3 mm acrylice for the covers .
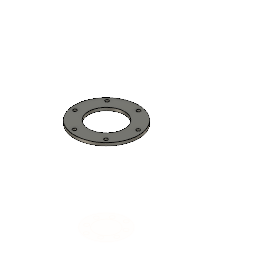
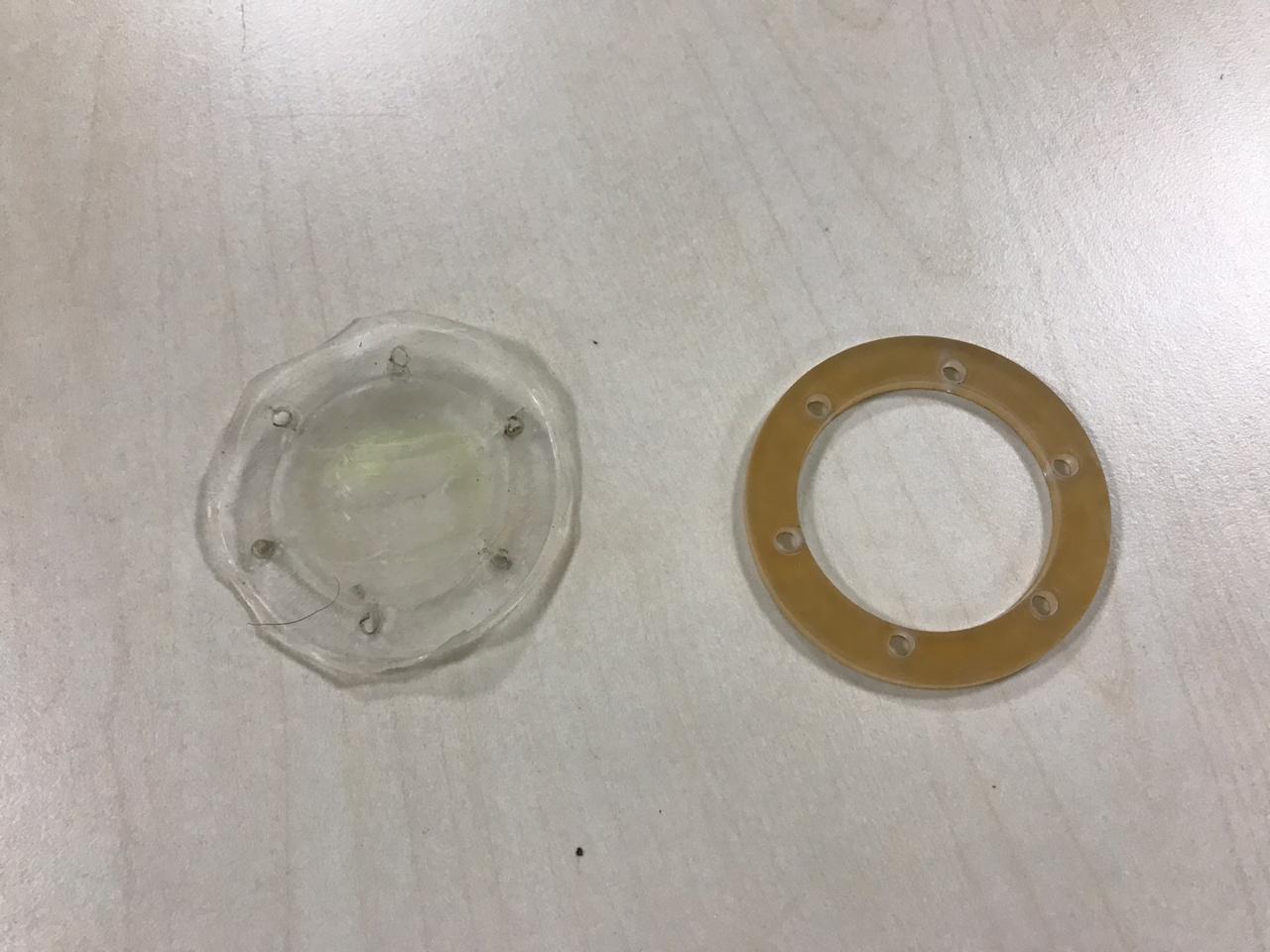
Electronics
In the electronic part, I used to design a micro controller to read the micro switch input and water sensor while the output signals are required for an alarm (LED) and SOV. the water sensor used to allow the system to work only in the water otherwise the system will trip. The SOV required 24 volts power supply so in this case the Relay is required to connect the SOV to the micro controller because the micro controller pin output is 5 volts.
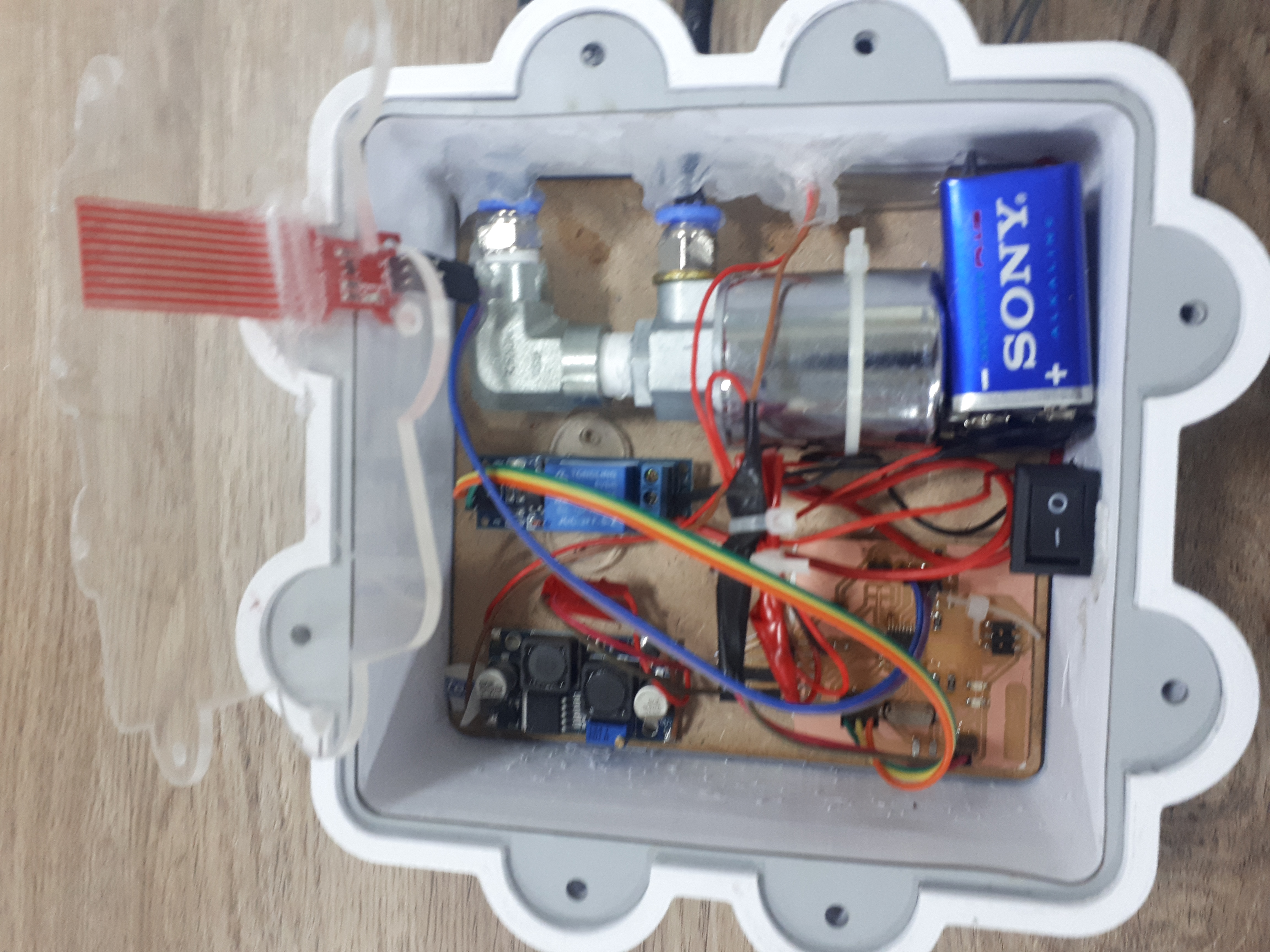
System diagram
The Code
The code for the micro controller is required to Measuer the closed contact time of the micro switch to activate the alarm as an output after 15 seconds and to activate the Solenoid valve after 60 seconds. When the Water sensor send the analog signal for the microntroller and the reading is >500, this will be the confirmation that the diver in the water but if the reading <500 the system will shutdown to save power and tank air.