Moulding And Casting
Assignment
In this week we are assigned to to design a mould by milling machine and casting an object
Procedure
3D Design
I used to design a traditinal pottery object which used used to drink Water.
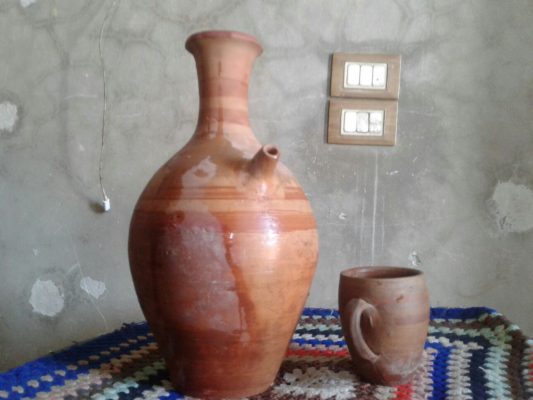
To design this obejct I used to sketch 2D design then I used the revolve tool to convert the sketch to 3D object using 180 degrees angle since I need the half of the object. I duplicated the object to make the double side mold. I made holes so when the mold used for casting the sides should match perfectly.
My fault is the letters is very small so I used a 0.8 mm milling bit but I think while casting the liquid will not cover the letters area
After the the design is done we need to shift to manufacture setting in fusion and set the milling settings. we need to select the milling bit size depend on the the area to enter such as the letters fault previously. I adjust the speed of the spindle for milling to be 50% for seafety reason and to avoid of breaking the milling bit.
Here the milling bit selection. we need a vernier caliper to take the measurements of the milling bit diamensions. we use rough milling to clear the whole area quickly. The rough milling bit is 6mm then we use the finishing rounded head milling bit depends on shape for the funal mold shaping. we need to take care of the smallest area of the design to use the proper milling bit.
Let's Start Milling
we use Wax block to make the mold. we cut the wax block as per the size of the mold design
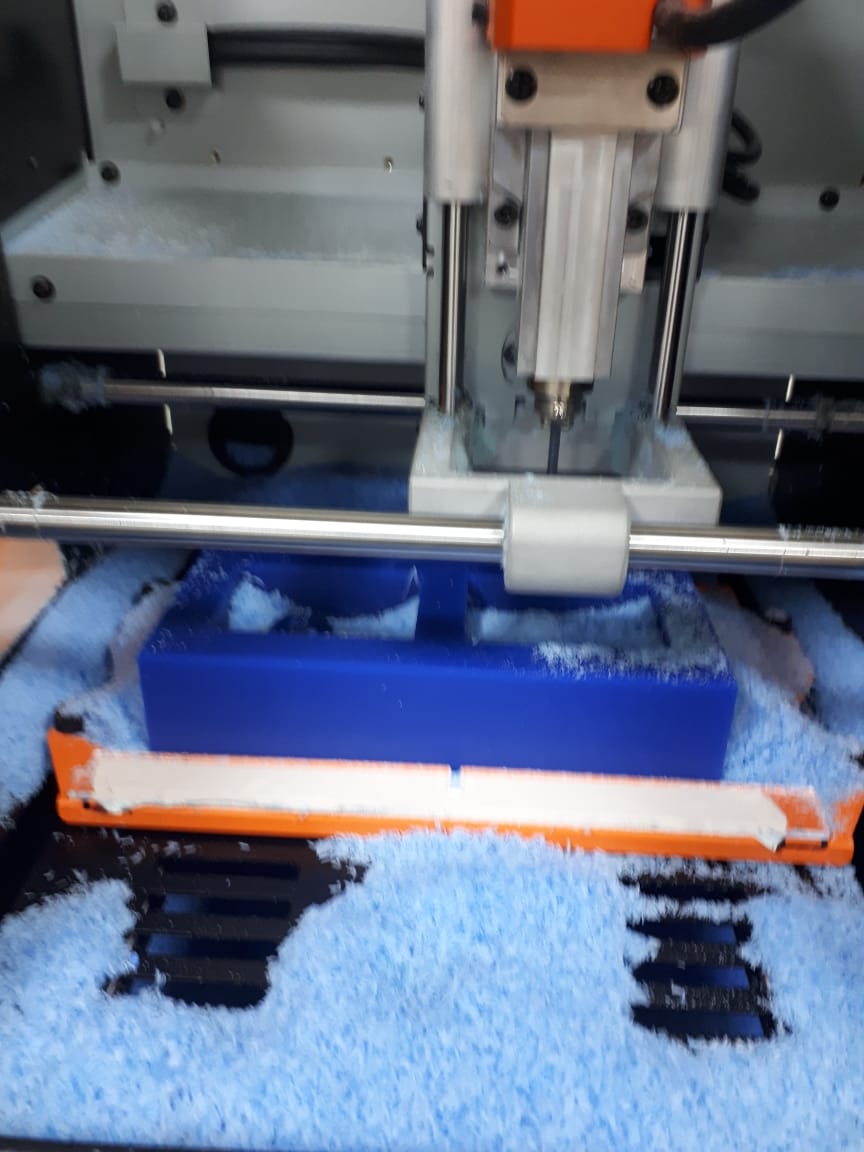
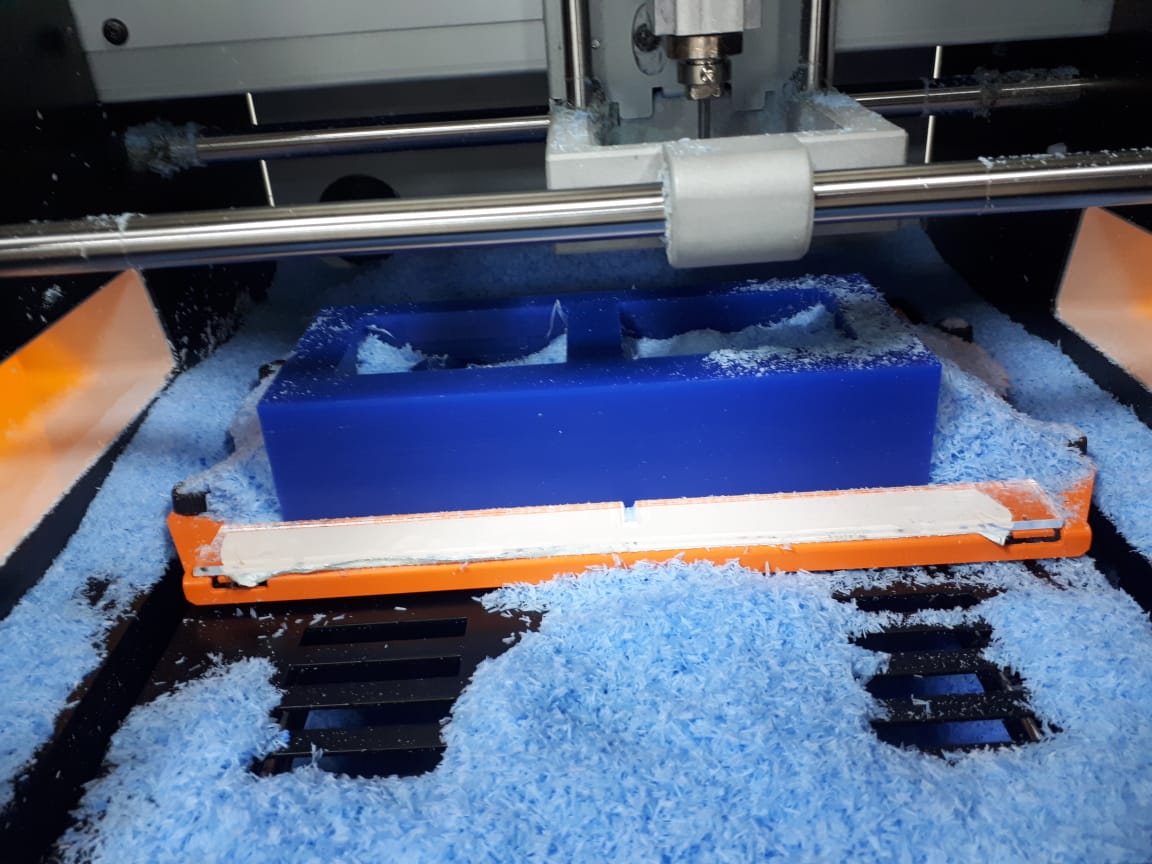
Now the mould is ready we can start casting. Remember to wear Safety glasses and muzzle before working on chemicals and you can find a note written in tha data sheet regarding safety requirments before start casting. We need to measure the Volume of the liquid by filling water in the mould. Read the manual before start mixing Part A and B becuase the capacity of part A required a specific Capcity of part B depend on the manufacture specifications. you cannot cast plastic material on plastic mold. If you like to cast plastic you should use rubber mold. the cast required long time to dry at least 24 hours.
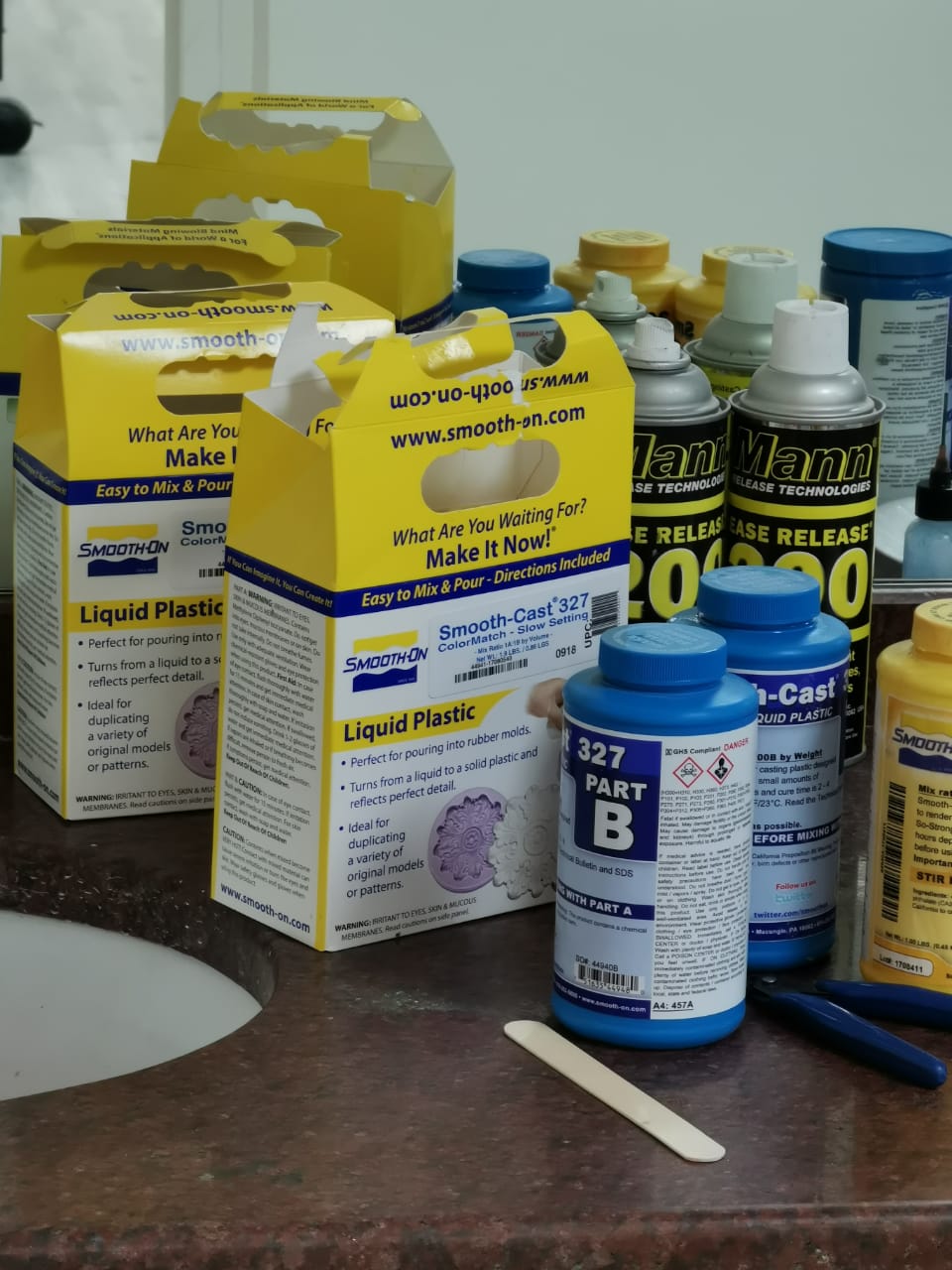

Part A required 3% of part B. since Part A weight = 143.8g Multiply by 3% = 4.314g.
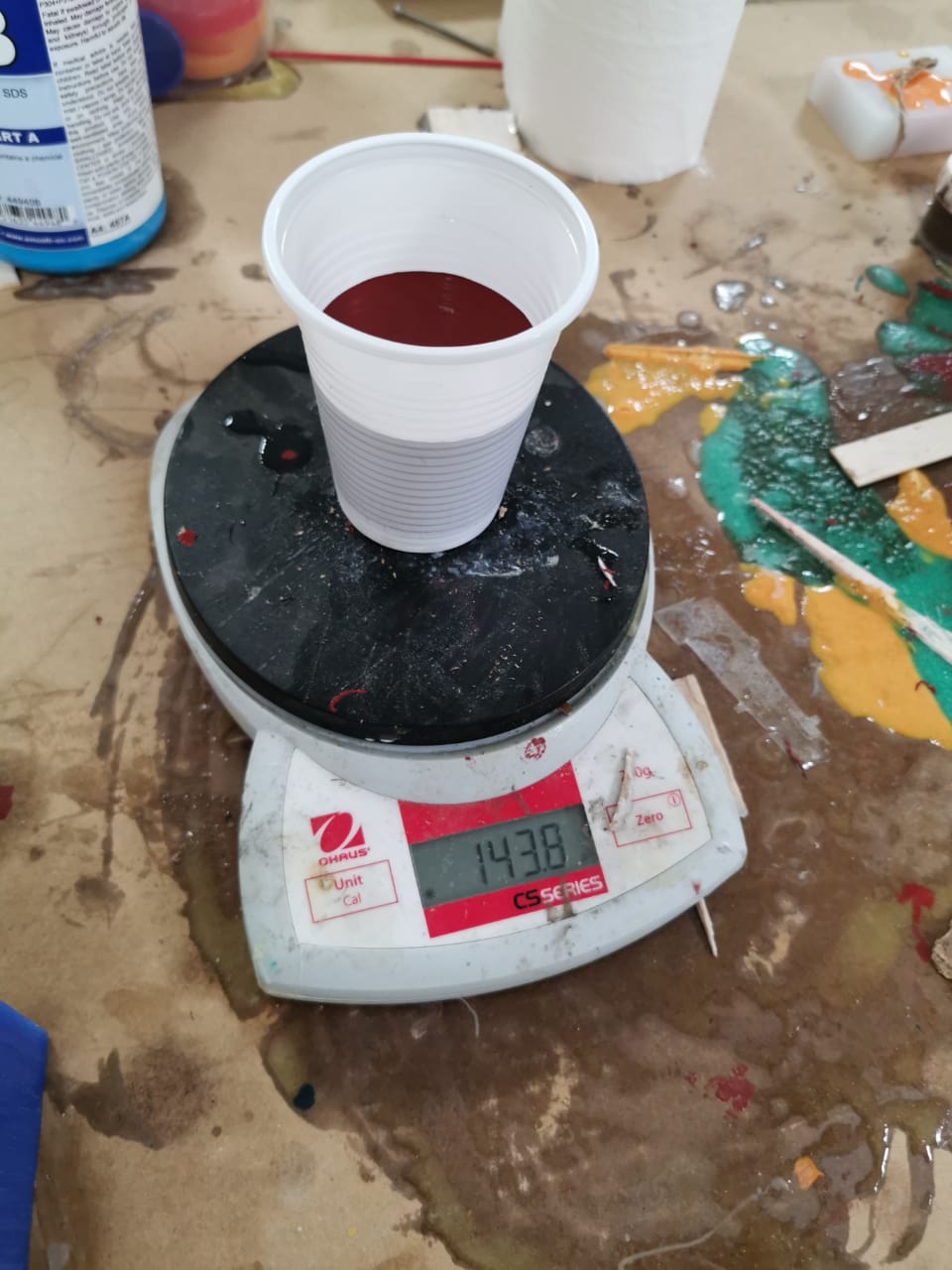
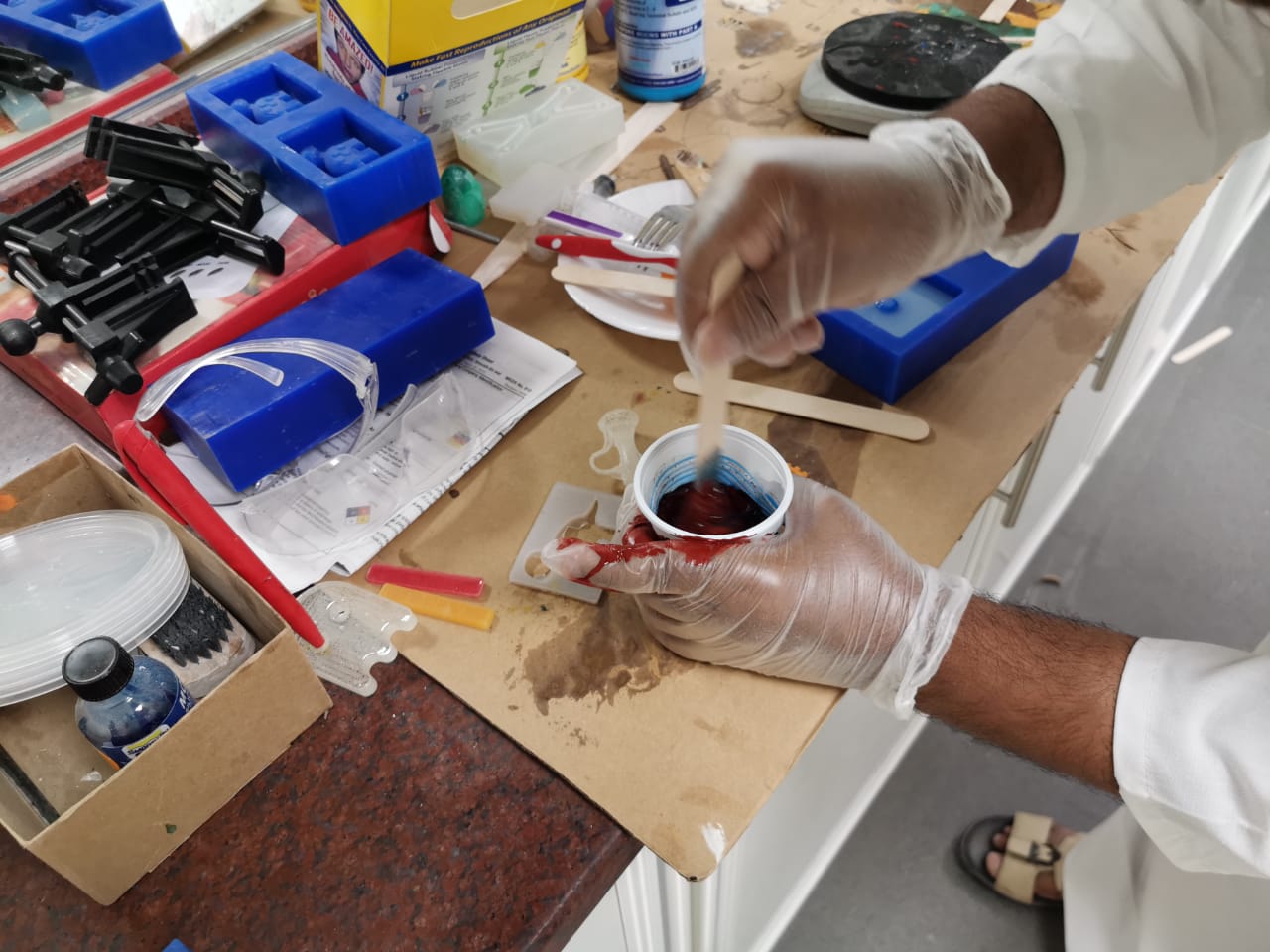
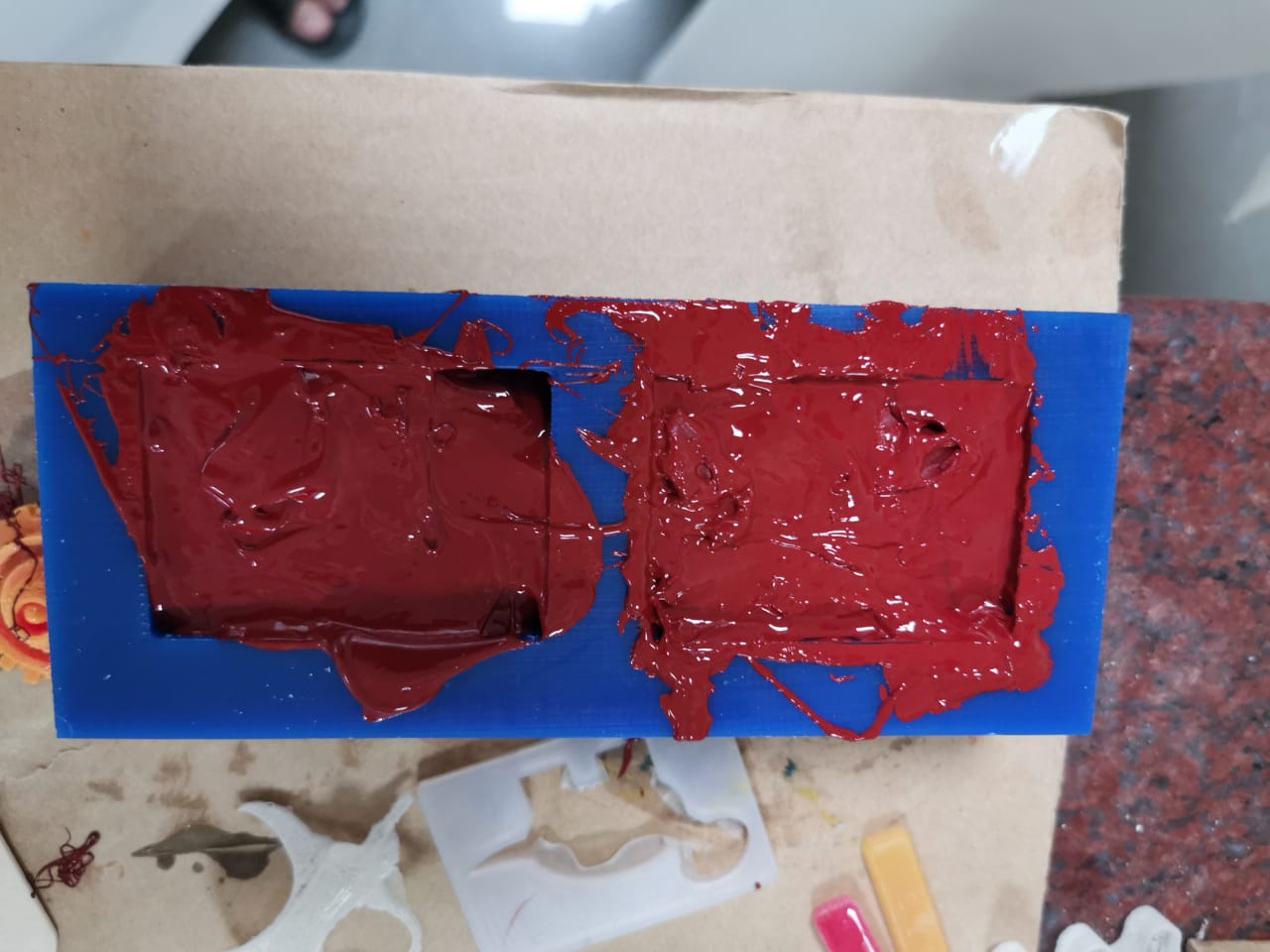
here the final product
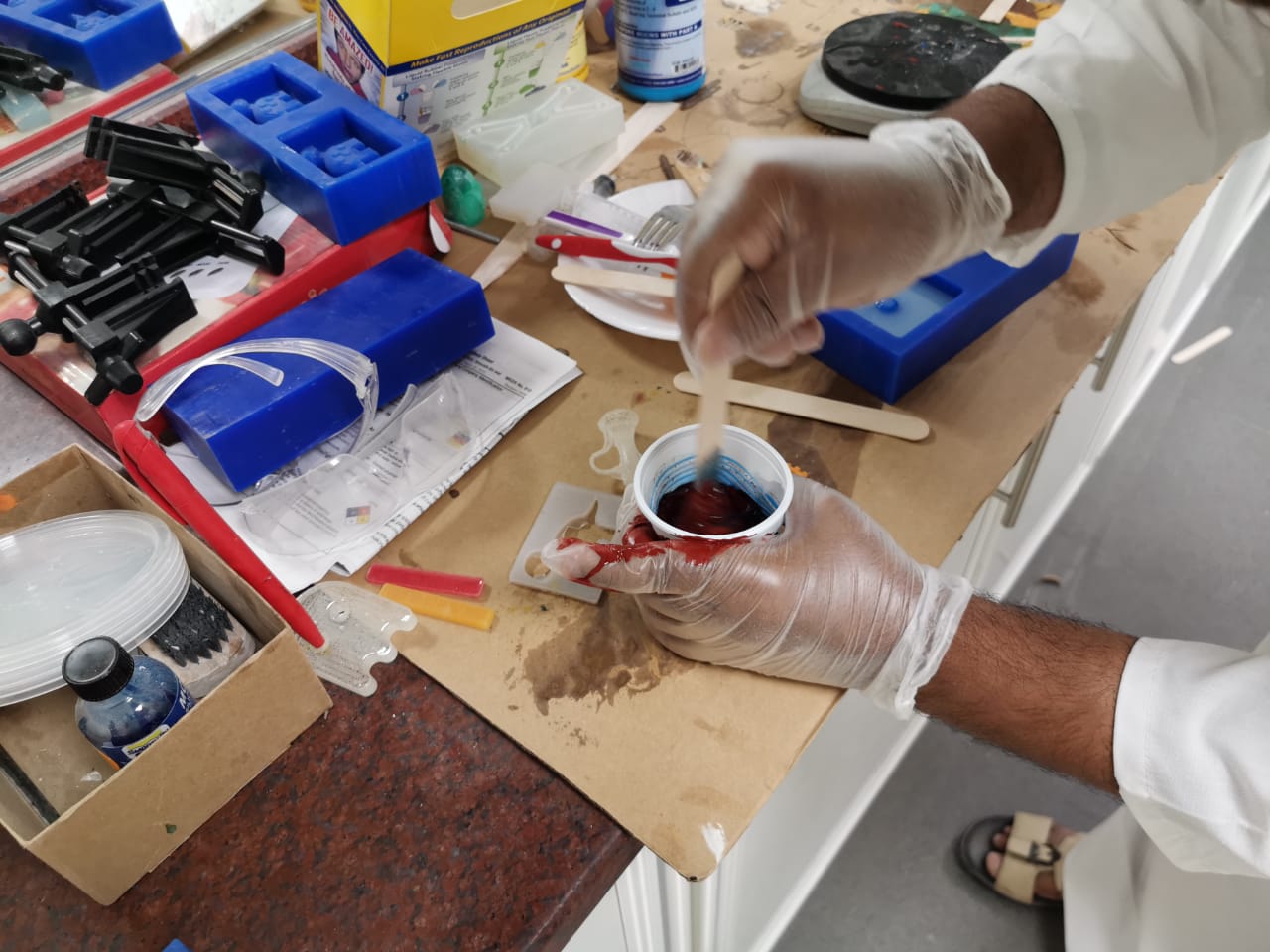
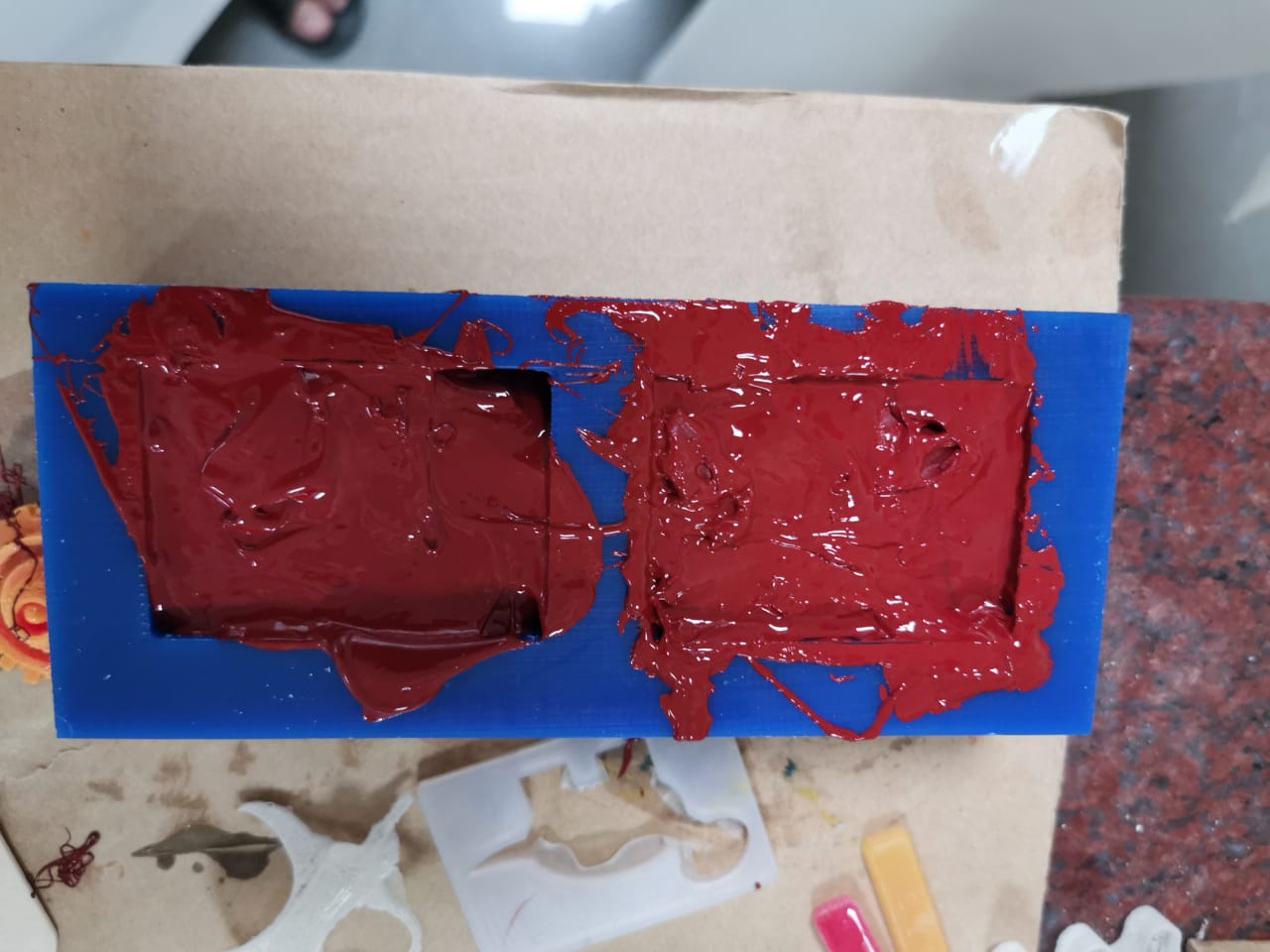
Tick Tock Tick Tock >>>>>>>> 24 Hours>>>>> Here the final Product
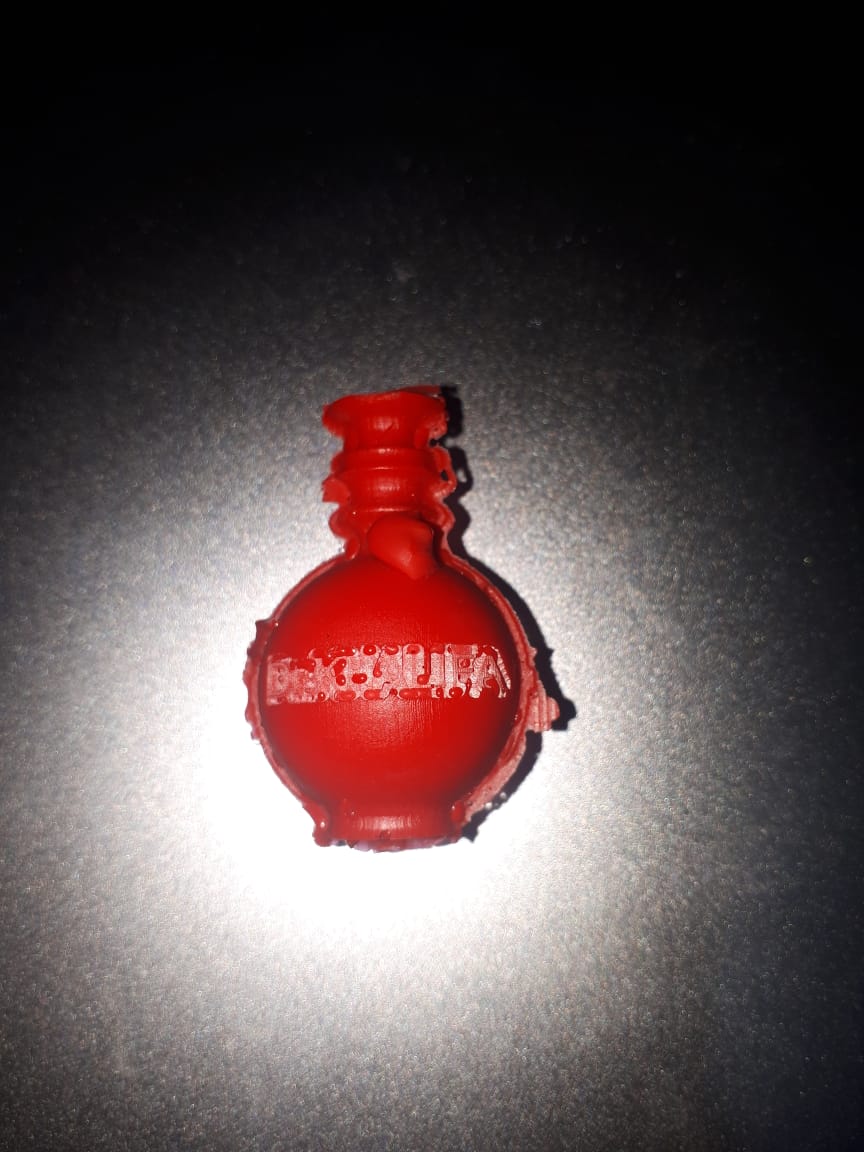
Files
Software
Autodesk Fusion 360
Vpanel for SRM-20