15. Mechanical design¶
Group assignment
- Design a machine that includes mechanism + actuation + automation
- Build the mechanical parts and operate it manually
- Document the group project and your individual contribution
Documentation |
---|
1.LaserCutFiles.dxf |
2.3DPrintFiles.stl |
3.Fusion360Archive |
This week I’m going to Design and Fabricate the mechanical parts of an automatic knitting machine.
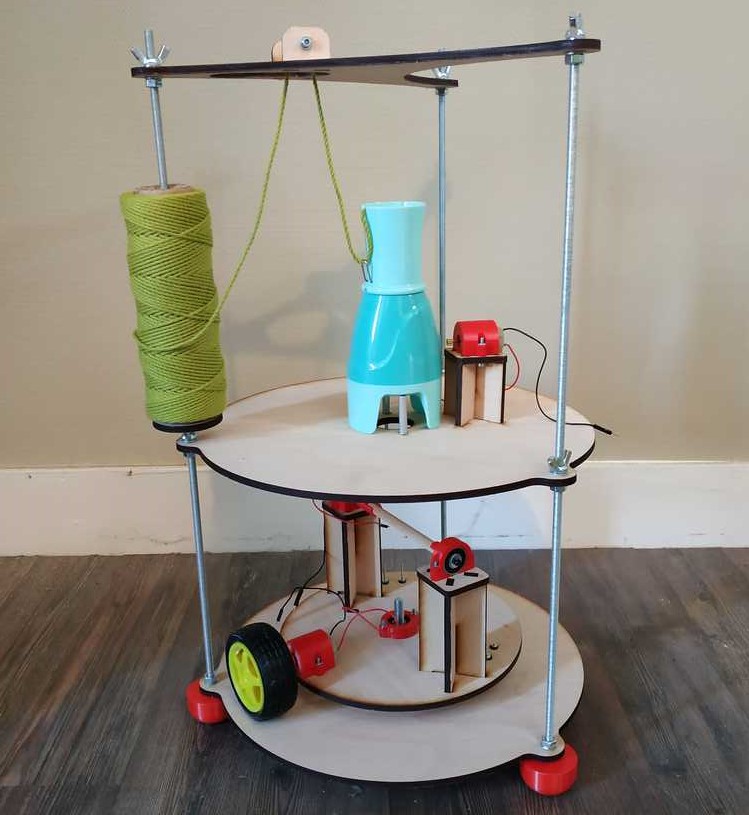
Context¶
This year, I’m the only remaining student of the fabacademy at fablab Digiscope. However we are running at the same time a fabricademy cycle and Camille is a student of this year cycle. As part of her project she’s working on motorising a mechanical knitting machine (also called french knitting machine). We can find her documentation here.
Here’s a video of how to operate the machine :
We decided to join forces to go further into the design and make a machine that will automatically knit a yarn and roll the created thread on a spool.
Camille will focus on the knitting part and I will focus on the spooling part and we will then join our two projects into one machine.
The spooling system¶
Constraints¶
By observing the video above we can see few important caracteristics of the machine.
- We need to add a weight to the thread. This force on the thread is an important feature.
- We can see that the thread rotates along its axis as it goes down so we will need to counter this effect to not damage it.
I need to make a system with two degrees of freedom :
- One rotation along the shaft to spool the thread
- One rotation along the thread to avoid any damage
As we can see on the video, one rotation of the knitting machine is equal to one rotation of the thread.
I wanted to do it as much as possible using the tools available in the lab so I’ll use standard parts, 3D print the casing of those parts and laser cut the machine.
Design 01 : the mecanical approach¶
The design¶
Inspired by Da Vinci machines I wanted to make a fully mecanical mecanism in order to have just one motor to control both rotations.
I’ve designed a system where one motor can rotate a wheel that will make the spool to roll on it.
NOTE : To make the spur gears I used an add in in Fusion 360.
Here is a view of the mecanism with the different parts.
The mecanism works this way :
- The gear on the motor rotate the big gear
- Due to the rotation of the gear, the wheel roll causing the shaft to roll to spool the thread and it starts a second rotation
- The shaft is linked to one wheel and a bearing on the other side to rotate in one direction
NOTE : The wheels are linked to the body of the machine on the top part with the same hole pattern.
I was confused a lot by making this design and I was not sure if it would work or not so I decided to make the machine and see what are the potential problems to make some adjustments.
Making the machine¶
Cutting the parts¶
I made the body of the machine using 10mm thickness plywood and the wheels and gears using 5mm plywood for a first try.
For the 10mm thick plywood I used the following parameters on the epilog fusion M2 :
- Speed 2
- Power 100
- Frequency 50
- Pass 1
then
- Speed 15
- Power 100
- Frequency 50
- Pass 6
For the 5mm thick plywood I used the following parameters on the epilog fusion M2 :
- Speed 6
- Power 100
- Frequency 50
- Pass 1
Assembling and testing the mecanism¶
I then assembled the parts, It feet the way I expected to :
![]() |
![]() |
Making it was a great learning experience because I was able to see directly all the issues with this design :
- The wheels don’t have enough room to rotate in the box
- The design of the wheels is not good, they just want one thing it’s to go off tracks
![]() |
![]() |
To sum up on this first design, here are the good aspects :
- It’s a constraint design and we don’t need gravity to operate it
- It needs just one motor to make the two rotations
Here are the bad aspects :
- To work the design of the wheels need to be done better
- We assume the speeds of the two rotations are proportional which is not the case
After this experience and thanks to a great brainstorming with our fabmanager, Jonah, I’ve decided to go back from scratch and make a mecanism with two motors to better control each rotation.
Design 02 : simplifying the mecanism¶
The design¶
The idea this time is to use a motor to rotate a platform.
- A wheel linked to a motor will rotate the platform
- A shaft will be placed in the bearing in the middle of the platform in order to guide the rotation
- There are two freewheels to keep the platform level as it moves
On the platfrom I added another motor for the shaft of the spool
- A 3D printed part is connected to the motor
- A 3D printed part is connected to the bearing
- To place the shaft we just have to snap it into the 3D printed parts. This way we can easily remove it once it’s done.
Making the system¶
Equipement needed¶
To assemble the machine I need :
- To laser cut some parts
- To 3D print some parts
- Two 608zz bearing
- Two freewheels
- One wheel
- two DC motors (from arduino starter kit)
- A 8mm wooden rod
- M3x20 bolts
- M3 washers
Preparing the parts¶
I’ve cut the platform usin g a 5mm thick plywood plank. I used the following parameter on the epilog fusion M2 :
- Speed 6
- Power 100
- Frequency 50
- Pass 1
I’ve printed the parts using an Pursa MK3 :
- Material PLA
- Infill 15%
- Brim ON
- Support ON
I’ve designed my cases with a footprint to fit a nut in it. To bond the metal part with my plastic part I heated the nut using a soldering iron.
![]() |
![]() |
Then I assembled everything as shown below
Here are some photos of the assembly
![]() |
![]() |
![]() |
![]() |
![]() |
![]() |
The wooden part are designed as a press fit kit. It’s a snug fit, I used a hammer to make it fit properly.
![]() |
![]() |
![]() |
![]() |
![]() |
![]() |
Here’s the whole platform assembled
Then I thought of the design of the whole machine to fit Camille’s part as well.
The machine¶
Concept¶
We wanted the machine to be modular with three levels. each level being connected to another one using 6mm threaded rods :
- Level 01 will be a platform with the spooling system on it
- Level 02 will be the knitting system
- Level 03 will be a level to give strengh to the overall machine and give tension as well on the thread
NOTE : For this machine the second level is an existing machine modified for our need but it could be a model made in a fablab. The fact that the levels are independent means it’s easy to change the knitting system for another one (with more needles for example).
Level 01 : The holding platform¶
The level 01 is a very simple design. It’s a platform to hold the spooling system. It has a hole in the middle to connect to the bearing of the platform and it has three holes to hold the rods to connect the different levels on the sides.
I cut the part in the lasercutter in 5mm plywood using the same parameters as before. Then I mounted the rods (I used 50mm long 6mm threaded rods) with nuts. I put a whasher on each side to protect the wood.
I’ve 3D printed some feet for the machine to be more stable
![]() |
![]() |
I then used a 60mm long 8mm bolt to connect the platform to the spooling system
![]() |
![]() |
Level 02 : The knitting system¶
On this platform we put :
- The kitting machine
- The motor to operate it
- A spool holder for the yarn
- Holes to connect to the rest of the machine
More information on the design :
- The knitting machine is screwed to the platform
- We will use the rods as guides for the yarn, we just designed a platform to hold the yarn
To assemble this level we need :
- To laser cut some Parts
- To 3D print some parts
- M3x20 bolts
- M3 washers
- M6 nuts
- M6 washers
- Two M3 threaded rods
- Two aluminium tubes
I have cut my 3mm rods and my aluminium tube
- 2 x 60mm for my threaded rods
- 2 x 40mm for my aluminium tubes
To screw the knitting machine, I removed to screws at the bottom of the machine and replaced it by the two rods. I placed the tube of aluminium around the rods.
![]() |
![]() |
The motor and its platfrom are the same design as before so the assembly is the same.
To assemble this level to the rest of the machine placed some nuts on the 6mm rods 200 mm above the previous level.
![]() |
![]() |
NOTE : I made a mistake taking the dimensions, my motor wasn’t in front of the machine, so I adjust the lenght of the platform of the motor.
Here’s a photo of the platform assembled.
Here’s a photo of the platform mounted.
Level 03 : The tension system¶
The purpose of this level is to :
- Give strenght to the whole machine
- Give tension to the yarn before it goes to the machine
NOTE : Here again the fact that the hight of the platform can be adjusted is good because it means we can have big or small yarn, we can adjust the hight of the level.
Here again a simple design, we will need to assemble this level :
- To laser cut some Parts
- To 3D print some parts
- M6 nuts
- M6 washers
- M3 threaded rod
- Aluminium tubes
Here again I cut my M3 rod about 85 mm and my aluminium tube about 58mm, I’ve laser cut the different parts and assembled everything.
![]() |
![]() |
I then mounted the platform on the rods using nuts and washers
Final assembly and tests¶
Here are photos of the whole machine assembled.
![]() |
![]() |
![]() |
To test the spooling system, I’ve plugged a 9V battery to the motor connected to the wheel.
NOTE : At full speed we can see some vibrations but everything stand fine. We will need to control the speed of the platform to get less vibrations.
At this point everything seems fine, we are ready to go further.
Ce(tte) œuvre est mise à disposition selon les termes de la Licence Creative Commons Attribution - Pas d’Utilisation Commerciale - Partage dans les Mêmes Conditions 4.0 International.