Computer-Controlled Cutting
Group Assignment 2021 (Héctor and Gustavo)
The Lasercutter Machine (GCC-Mercury III)
The machine that we have available in our Fablab is the Mercury III. It is a GCC brand laser cutter (GCC website). Use a CO2 laser with a power of 60W.
The CO2 Laser
The carbon dioxide laser (CO2 laser) was one of the earliest gas lasers to be developed. It was invend by Kumar Patel of Bell Labs in 1964, and is still one of the most useful. Carbon dioxitede lasers are the highest-power continuous wave lasers that are currently available. They are also quite efficient: the ratio of output power to pump power can be as large as 20%. The CO2 laser produces a beam of infrared light with the principal wavelength bands centering on 9.6 and 10.6 micrometers (μm).
Cutting and welding
Because of the high power levels available (combined with reasonable cost for the laser), CO2 lasers are frequently used in industrial applications for cutting and welding, while lower power level lasers are used for engraving. It is also used in the additive manufacturing process of Selective laser sintering (SLS).
Principals parameters to lassercutting:
Power parameter (Mercury III)
As it appears in the specifications, the machine has POWER CONTROL adjustable from 1 - 100% (Up to 16 color-linked power settings per job). In the work of characterization of the machine, we have calculated the power and its ratio for the range of materials with which we usually work in our laboratory. Differentiating also in some of the cases between different thicknesses of the same material.
Velocity parameter (Mercury III)
As it appears in the specifications, the maximum speed of the machine is 42IPS. (Inch Per Second). The Mercury III laser cutter machine has SPEED CONTROL adjustable from 1 - 100% (Up to 16 color-linked speed settings per job). In the work of characterization of the machine, we have calculated the speed and its ratio for the range of materials with which we usually work in our laboratory. Differentiating also in some of the cases between different thicknesses of the same material.
Using Lasercutter
To use the lasecutter we need work in CorelDraw. To calculate the kerf parameter we draw two concentric squares
(10mm the smaller, and 30mm the bigger). The line color indicate the cutting order (the firt one is the black color
and the second one is the red color).
Warning: the cutting lines would be set with smaller thickness.
To send the design to be cut or engraved, just press "print",
in the printer selection box choose the laser cutter and from here, configure its parameters
Now we need set the lasercutting parameters in the laser machine configuration:
1º Mode
We choose black and white, since our designs are cut lines and the texts and the engraving are done in grayscale.
With the other methods, you can make engravings with a 3D relief sensation, use the color mode,
in which the software itself assigns each color its equivalent in grayscale to be able to record it,
the mode for raster or stamps, etc.
2º Power and speed
n this window, the power and speed are configured for each color (which indicates the order of making the cuts)
according to the type of material we use.
3º Position mode and others
From here we can choose whether to cut the design from the origin of the laser cutter (fixed in its upper left part, it comes from the factory),
choose a point for the origin on the work table where we want, or indicate that we take the head to a point
(which we will assign as the center point) and from that point it will engrave or cut from the center of our design.
With the other options we can indicate that it makes the engravings using Stucky, matrix, dot filters ...
so that the engraving of the image is not continuous but is textured with these patterns
Making Material Boards
In this section we will talk about our template for characterizing materials.
First we draw up a decagon in which we start from 100% black and we go down from 10% to 10% the percentage of black, until we reach white.
With this we have a gray scale to see how the engraving deepens, depending on the amount of black that we give to the design.
100% Black
60% Black
20% Black
We start drawing in Fusion 360 to make a material caracterization´s parametric design. With this fusion template, in the table of parameterized values, we can adjust the thickness and kerf parameter for each material and the template slots will be adapted.
Later we export to Illustrator in dwg. In illustrator we work the rest of the engraving and cutting parameters.
Here we include a text font in different sizes, to have a sample, and we indicate the cutting and engraving values and dimensions of the template.
We have a generic material parameters board.
Orange Acrylic:
Test two steps:
We made a pass with some recommended parameters, but we could not cut. So, we decided to make a new pass,
with which it cuts the acrylic. With this test we are going to calculate the kerf for 2 passes and compare
with a cutting pass.
1 try: 2.7% speed and 98% power. No total cutting. We need two pass.
10mm -> 10mm - 9.81mm = 0.19mm
30mm -> 30mm - 29.78mm = 0.22mm
10mm hole -> 10mm - 10.31mm = -0.31mm
*** We have calculated the kerf value with our pattern, using the mean with the differences between the real value
after cutting and the theoretical value, for the large square, the small square and the gap between the large
square and the small square. This average value between two, to have the simple value of the kerf
Test one step:
with the new values, for the second attempt, we manage to cut with one pass and calculate the kerf
2 try: 2% speed and 95% power.
10mm -> 10mm – 9.85 = 0.15mm
30mm -> 30mm – 29.81mm = 0.19mm
10mm hole -> 10mm – 10.15mm = -0.15 mm
Kerf= [(0.15+0.15+0.19)/3]/2= 0.082 mm aprx.
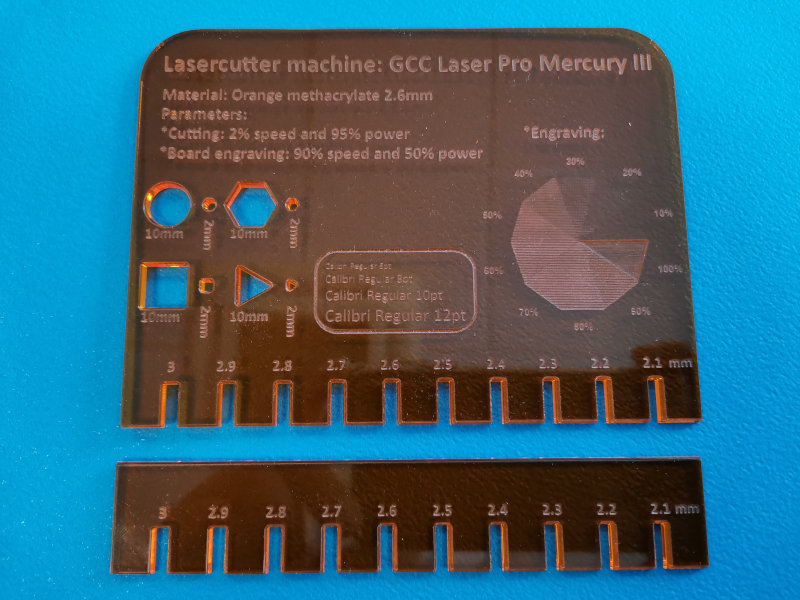
Wood 2.48 – 2.6 mm:
We tested the recommended value, but dropped the power by 5%. We leave the speed the same.
Speed 7% power 95
We do the same measurements for wood:
30mm -> 30mm – 29,80mm = 0.20mm
10mm -> 10mm – 9.85mm = 0.15mm
Hole 10mm -> 10mm – 10.19 = -0.19mm
Kerf= [(0.20+0.15+0.19)/3]/2= 0.09mm
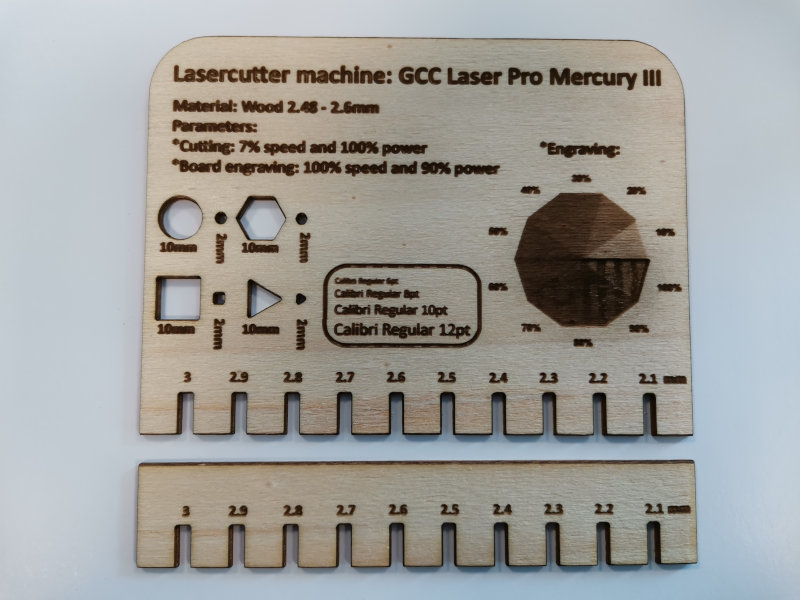
Cardboard 4mm:
We start from a recommended value for a type of cardboard, and we test for our type
Speed 25% power 100% no
Speed 20% power 100% no
Speed 15% power 100% yes
We do the same measurements for the cardboard
30mm -> 30mm – 29,80mm = 0.20mm
10mm -> 10mm – 9.80mm = 0.20mm
Hole 10mm -> 10mm – 10.15 = -0.15mm
Kerf= [(0.20+0.20+0.15)/3]/2= 0.09mm
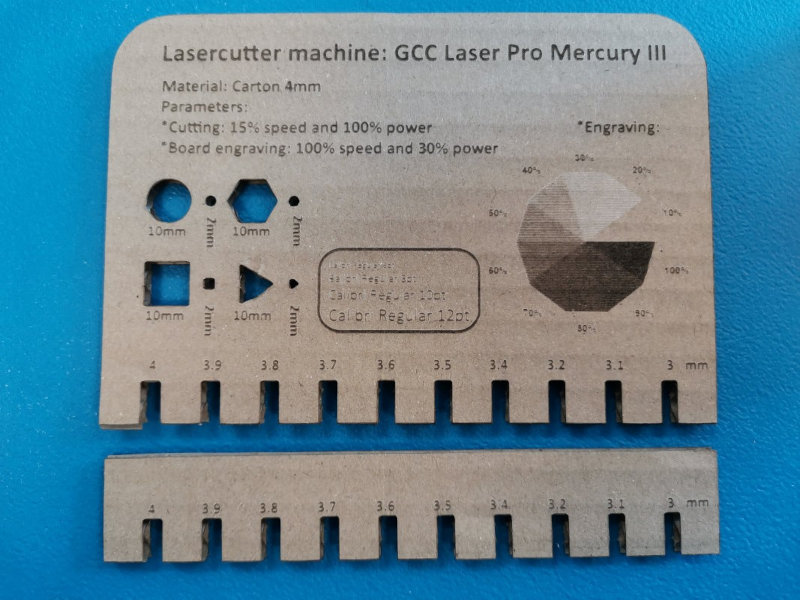
Results
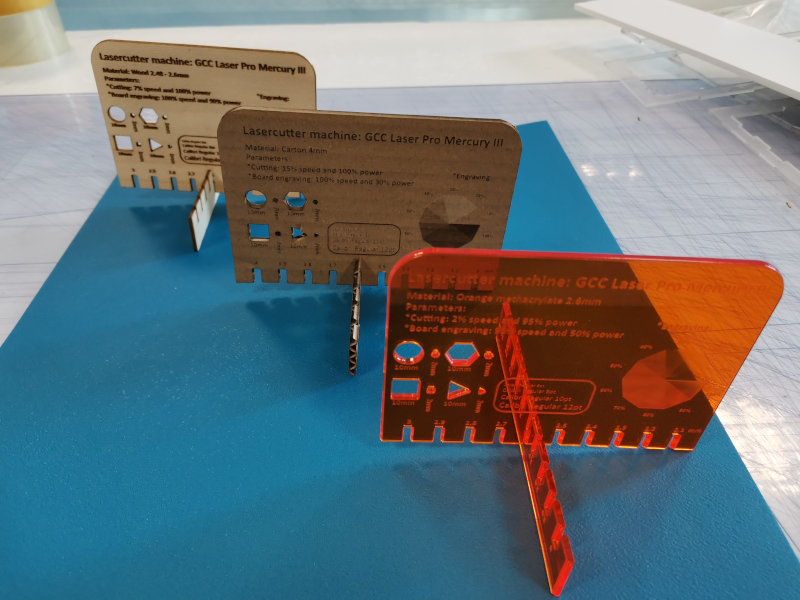
We have cleaned the mirrors and the laser lens to get a better cut. Because we realized that the last cuts we were making, in some points the cut was not clean
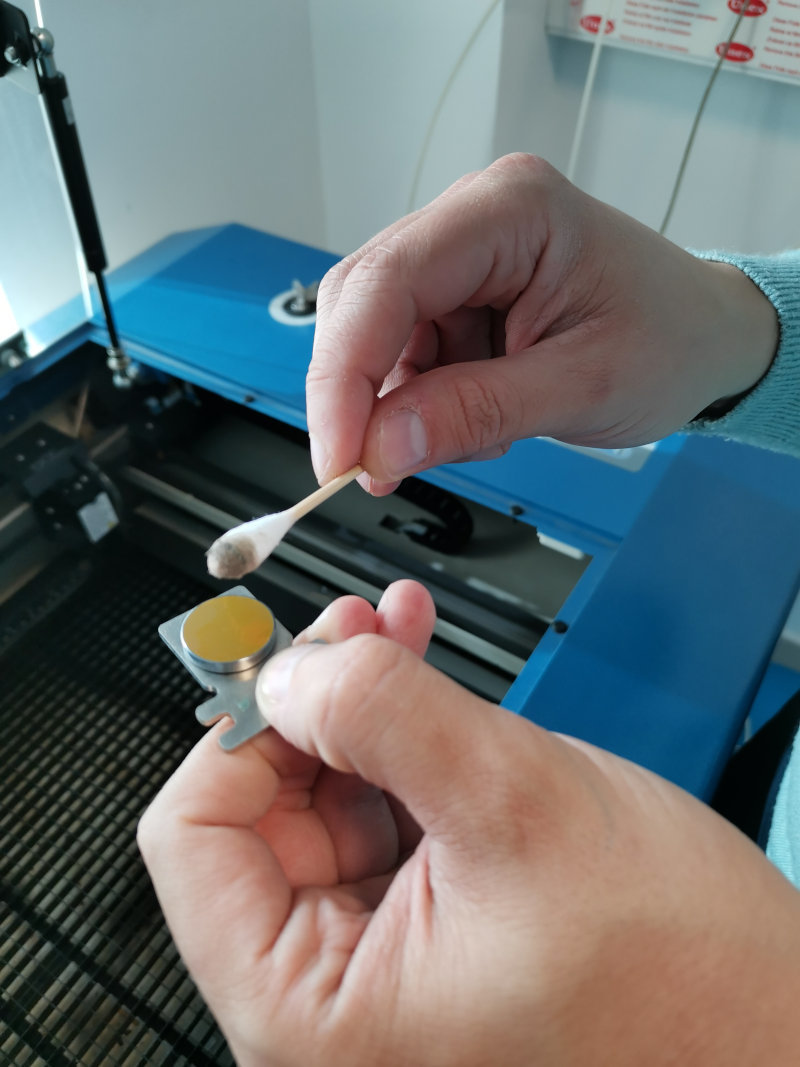