computer-controlled cutting
- Assignment: design, make, and document a press-fit construction kit
- Best Width
- I used shina-plywood(シナ合板) which is plywood made of Tilia japonica(シナノキ) on the face and Dipterocarpaceae(ラワン) in the middle.
- In this case, the press-fit joinery width should be plywood thikness - 0.3mm. So, for instance, I used 2.8mm shina-plywood then 2.5mm width was the best.
- I tested the width by making pieces shown below with changing its width.
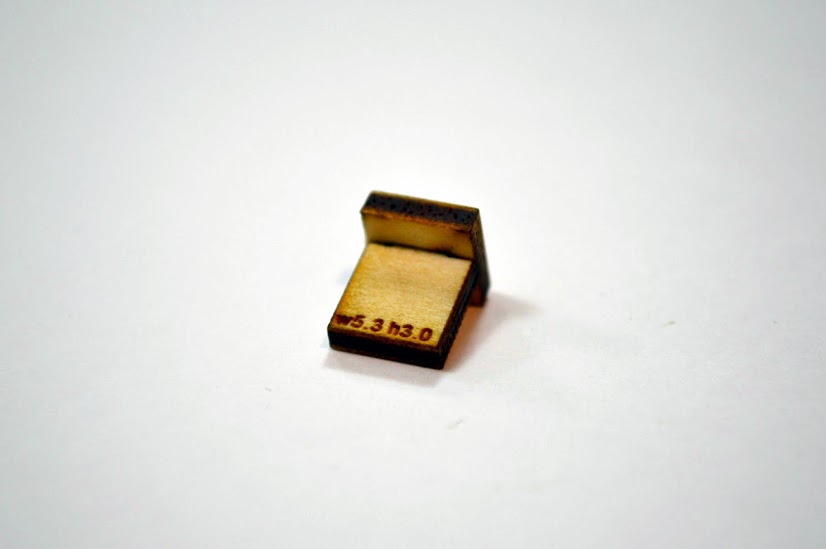
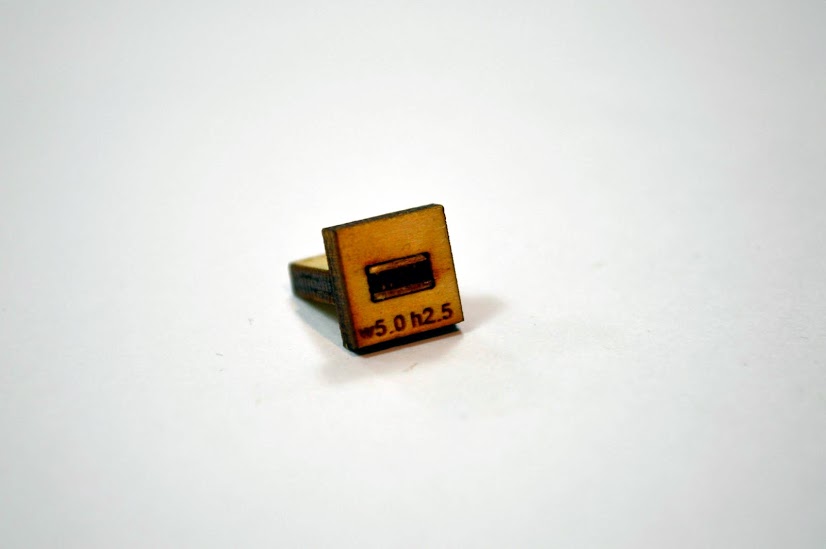

![]()
- I described the result here.

- I also described the result of MDF I tested before.

- Frequency
- A lasercutter is a digital machine. I mean it lases intermittently, actually.
- Frequency on the Epilog driver and PPI on the UNIVERSAL driver mean how many times the lasercutter lases in a fixed period of length. PPI stands for Pulses Per Inch, which means how many times it lases in one inch.
- Here is the result of testing frequency of an Epilog.
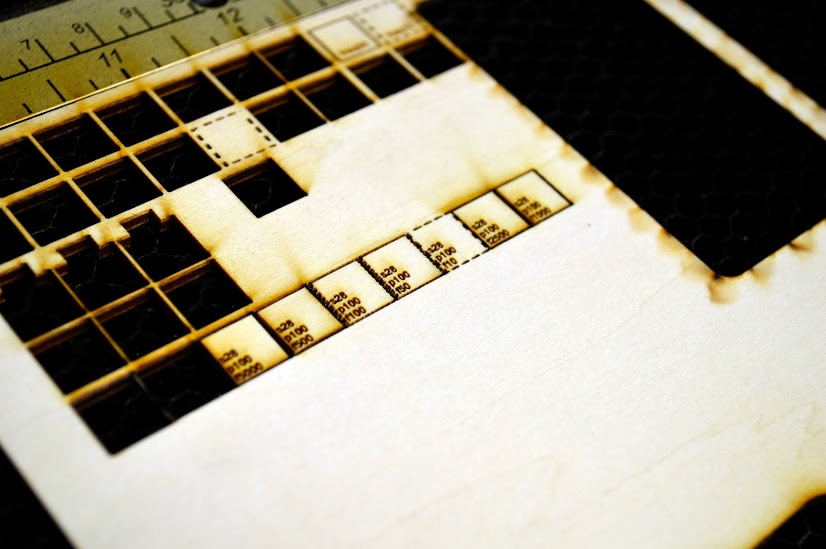
- (above)the face / (below) the back



- (above) the back of frequency 50 (right) and frequency 10 (left)

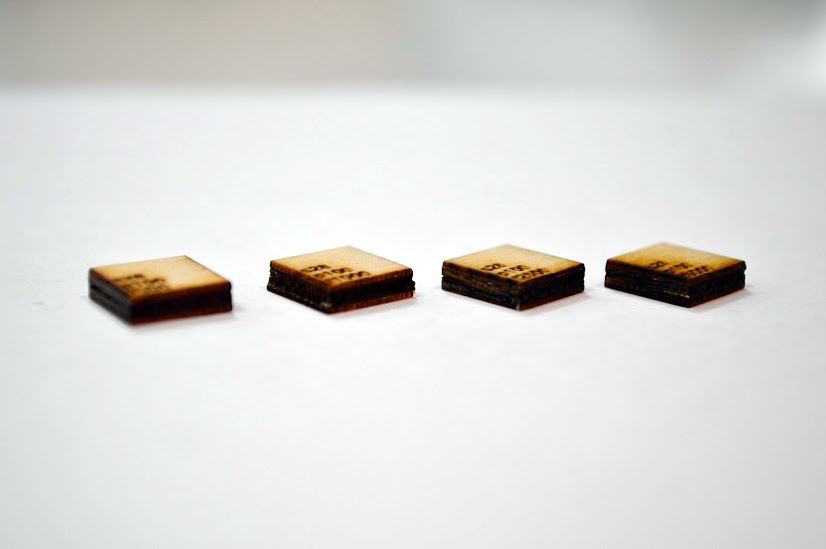
- Power and Speed
- Speed 22 / Power 100 / Frequency 500 seems the best for shina-plywood 2.8mm thickness with an Epilog laser. (It was sold for 3.0mm thickness but I found it 2.8mm actually by measuring with a caliper)
- If the speed value is too low or the power value is too high, your material will get this kind of burnings on the back.

- To avoid this, you should
- 1. cover its back with a masking tape then the burnings will be on the tape and peel it off after lasercutting or
- 2. leave space between the honeycomb table of the lasercutter and a material with some blocks or something or
- 3. find the best parameter!!

- (above) This is the back of the plywood when I tried speed20 / power 100 / frequency 400.


- (2 photos above) These are also the result on speed20 / power 100 / frequency 400. It is very useful, each of the parts were not dropped on the honeycomb table so you can pick the whole of it from the table at once but also you can take the parts off very easily and smoothly.

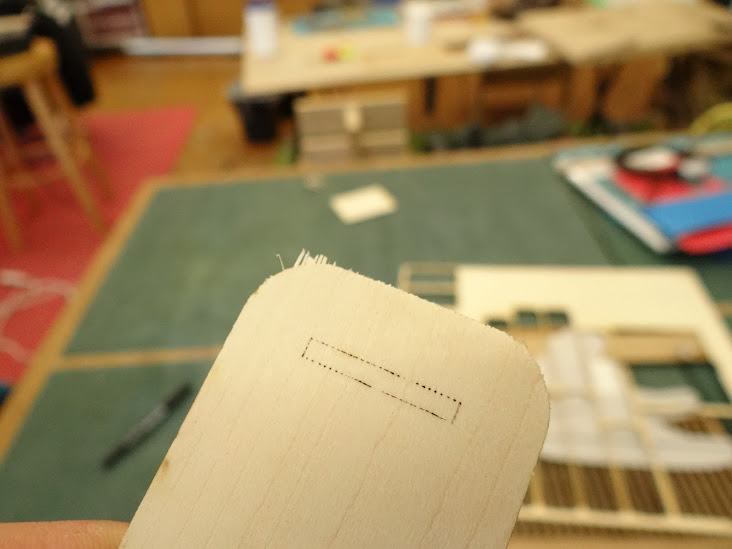
- (2 photos above) However, these are also the result of the same parameter. It was cut less deeper so I needed to use a (manual) cutter to take it off.

- (above) I guess this is the reason why it was happened. The laser beam comes from on the left of top and reflects on two mirrors then goes onto a material.
- When the place to cut is near to the left of top, the distance the laser beam runs is short, when the it is far from the left of top, the distance is long so that it needs more energy then the beam gets weaker.
![]()
![]()
![]()
- What I made this week

- A box (shina-plywood 2.8mm-thickness)


- A simplified model for structural test (mdf 5.5mm-thickness)
- The bar parts are simplified models of a latch needle(メリヤス針).
- A latch needle is a needle used for knitting machines.
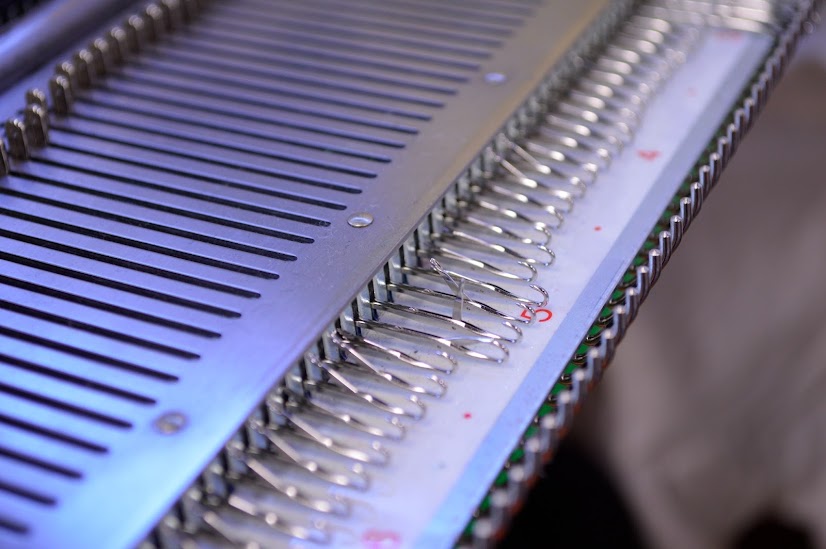