Materials Used
Overview of selected materials
This project utilized a carefully selected range of materials to optimize both the functionality and aesthetics of the prototype:
- PLA: Primarily used for printing the propellers and other minor components. Its ease of use and mechanical properties make it ideal for parts that require precision and a good surface finish.
- Aluminum: Chosen for the main structure of the prototype, providing strength and durability without adding excessive weight. Aluminum ensures a solid foundation that supports all system components.
- Acrylic: Used for the prototype’s bases, offering rigidity and a professional appearance. This material is transparent, allowing visibility of internal components and facilitating maintenance.
- Red Vinyl: Applied over the acrylic to enhance the design and add an aesthetic touch. This vinyl gives the prototype a striking and customized finish, aligning with the overall design of the project.
- Other Materials: Screws, nuts, and various adjustment tools were included to assemble the prototype securely. These small elements are essential for ensuring the stability and functionality of the model.
- Sealant: Applied in areas where moisture and dust protection are needed, the sealant ensures that the electronic and mechanical components of the prototype remain isolated from external factors, preserving their functionality and performance over time.
Properties of PLA for 3D-printed components
PLA
Polylactic acid (PLA) is one of the most popular materials in 3D printing due to its ease of use, low toxicity, and suitable mechanical properties for low-impact prototypes and functional parts. This polymer is derived from renewable resources such as corn, cassava, and sugarcane, making it a sustainable and environmentally friendly option. Unlike other plastics, PLA is biodegradable under specific industrial composting conditions, helping to reduce its environmental impact.
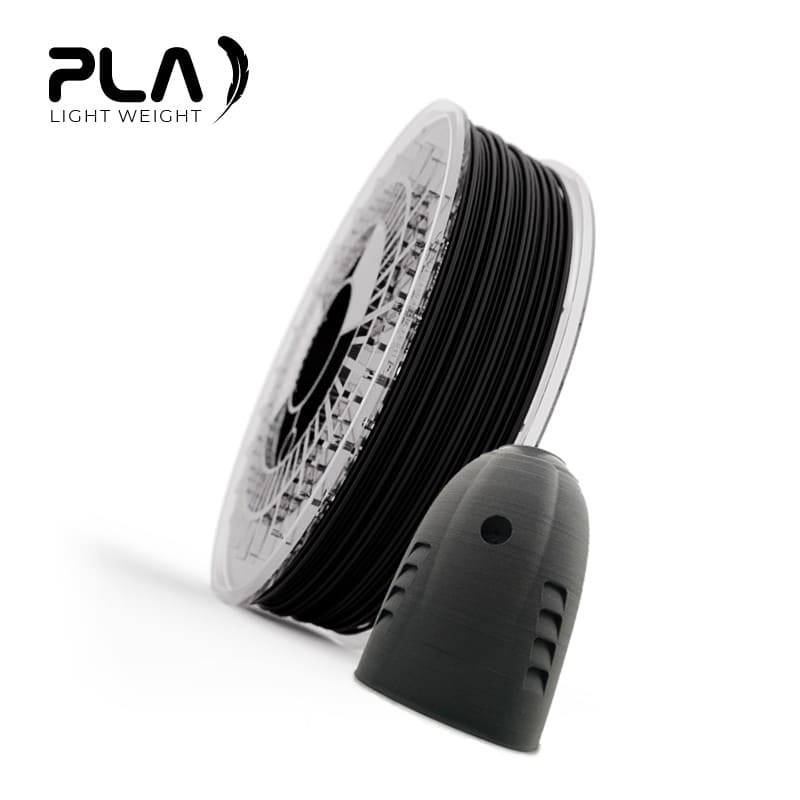
PLA has a relatively low printing temperature, typically between 180 and 220220 degrees Celsius, which reduces the risk of warping and makes it easier to print complex parts. Additionally, PLA has good bed adhesion and does not require a heated bed, making it ideal for low-cost or desktop 3D printers.
Advantages and limitations of PLA
Among the advantages of PLA is its low shrinkage during cooling, allowing for parts with high dimensional accuracy. This is particularly useful in digital fabrication projects where precision is necessary for assembling multiple parts. However, PLA has limitations, such as low heat resistance, making it unsuitable for applications requiring high durability in high-temperature environments.
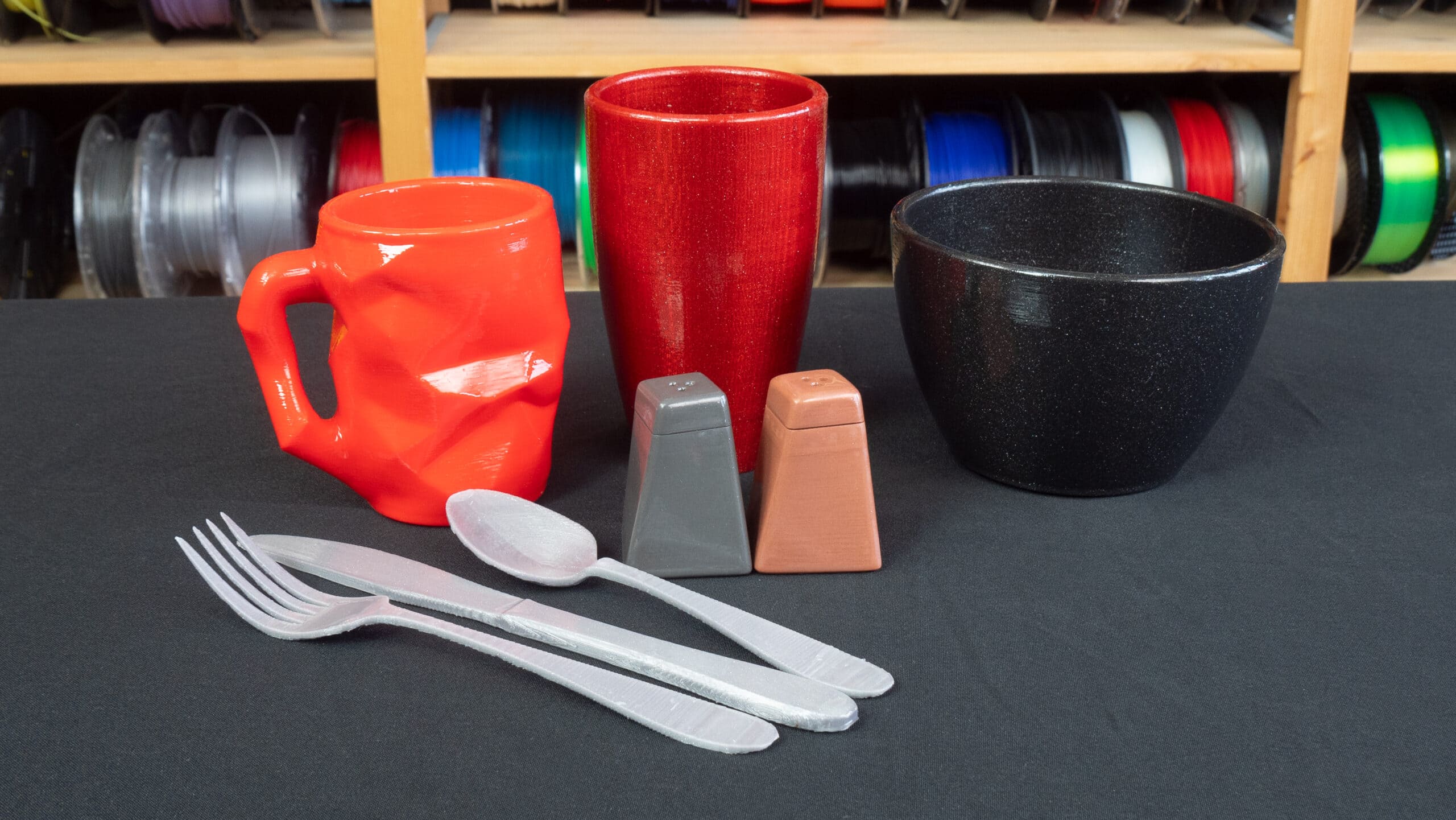
Applications of PLA in prototype manufacturing
In this project, PLA was primarily used for printing propellers and other non-structural parts of the prototype. Its easy availability, low cost, and suitable mechanical properties make it ideal for creating components that will not be exposed to high loads or temperatures. Due to its low shrinkage rate, it was possible to achieve precise parts, which are essential for the correct assembly of the prototype.
Benefits of aluminum in structure
Aluminum was selected as the primary material for the structural framework of this prototype due to its remarkable combination of strength, lightweight nature, and corrosion resistance. Using aluminum profiles and tubes allowed us to create a sturdy yet adaptable structure, essential for a functional wind energy prototype. The specific components made of aluminum include 2mm profiles for the main structure and tubes for the support and energy generation mechanism of the propellers.
Aluminum Profiles for Main Structure
The 2mm aluminum profiles were used to form the main structural framework of the prototype. These profiles provide excellent support for the entire assembly, ensuring that the framework is stable and resistant to bending under load. Due to aluminum's high strength-to-weight ratio, these profiles allow for a solid foundation without adding excessive weight, making the structure easier to transport and assemble.
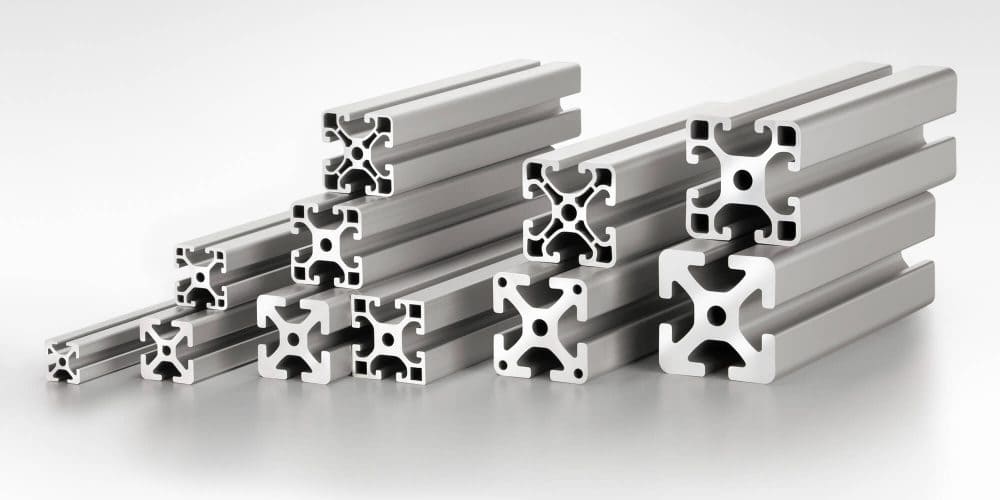
Aluminum Tubes for Propellers and Energy Generation
The aluminum tubes play a crucial role in supporting the propellers and facilitating energy generation.
Each propeller has a central opening where it is threaded onto an aluminum tube. This allows multiple
propellers to be stacked along the length of the tube. The tube's high rigidity and durability ensure that the propellers
remain securely attached and rotate smoothly.
The aluminum tubing used was 5/16 inch or 7.9 mm.
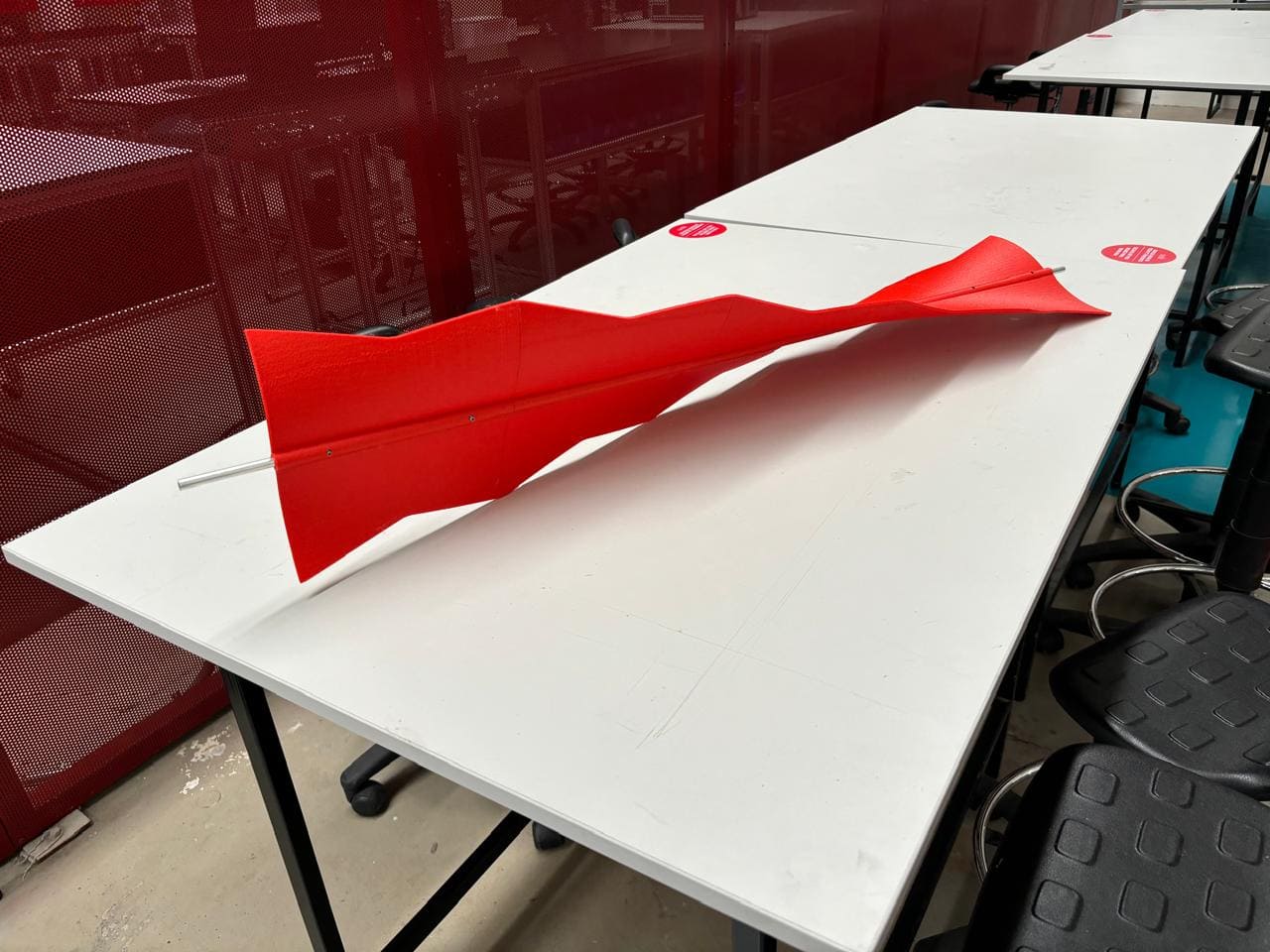
Properties and Advantages of Aluminum
Aluminum is widely used in industrial and engineering applications due to its favorable mechanical properties:
Property | Aluminum | Steel | Plastic |
---|---|---|---|
Strength and Durability | High tensile strength, ideal for load-bearing structures | Higher tensile strength but heavier | Low tensile strength, suitable for lightweight, non-load-bearing parts |
Corrosion Resistance | Excellent, forms a protective oxide layer | Varies, often needs coating | Not affected by corrosion, but susceptible to UV degradation |
Lightweight | Low density, one-third that of steel | Heavy, may require additional support | Very light, but not as strong |
Ease of Machining | Easy to cut, drill, and shape | Moderate; requires specialized tools | Easy, but can deform under heat |
Recyclability | Highly recyclable, sustainable | Recyclable but energy-intensive | Varies, some types are recyclable |
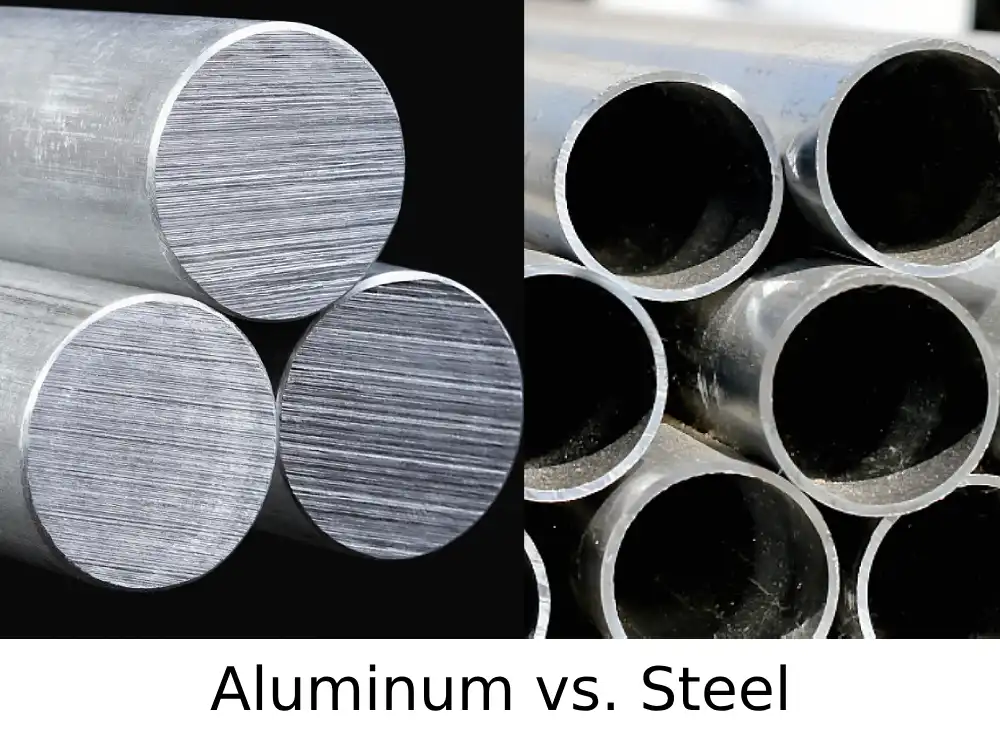
Aluminum's combination of these properties made it the perfect choice for creating a robust and efficient structure in our wind energy prototype. Its application in both the profiles and tubes highlights its versatility, providing stability to the main structure and facilitating the rotation of the propellers for optimal energy generation.
Acrylic Support Structure
Acrylic was chosen as a key material for the project's bases and support panels due to its rigidity and professional aesthetics. This material provides the necessary stability for the propellers and other system components, as well as allowing clear visibility of the internal workings, which facilitates maintenance and adjustments.
The design of the acrylic bases enabled efficient integration of motors and wiring, maintaining a clean and organized look. The transparency of acrylic also contributes to the overall aesthetic of the project, allowing internal parts to be visible and making it easier to monitor each component.

The acrylic pieces were precisely cut to fit the prototype’s specific dimensions and requirements, ensuring a perfect fit with other materials like aluminum and vinyl.

Vinyl Finish for Enhanced Aesthetics
Red vinyl was applied over the acrylic to enhance the prototype’s aesthetics. This detail provides a visually appealing and professional finish, aligned with the overall design of the project. Additionally, the vinyl serves as an extra protective layer, safeguarding the acrylic surfaces from potential scratches or damage.
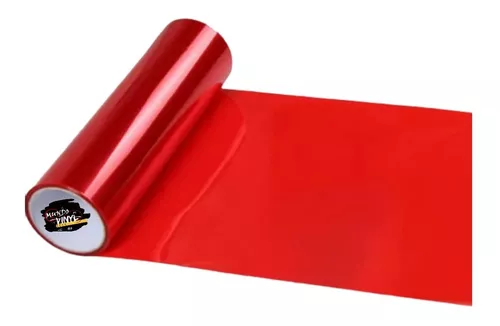
Assembly and Adjustment Elements
In addition to the main materials, assembling the prototype required the use of screws, nuts, and adjustment tools. These small elements were essential to ensure the stability and functionality of the model, allowing each piece to be securely assembled and facilitating future adjustments and maintenance.

Sealant Application for Protection
Sealant was applied in areas where moisture and dust protection are needed, ensuring that the prototype’s electronic and mechanical components remain isolated from external factors. This measure preserves the functionality and performance of the system, preventing potential damage caused by environmental conditions and enhancing the prototype's durability.
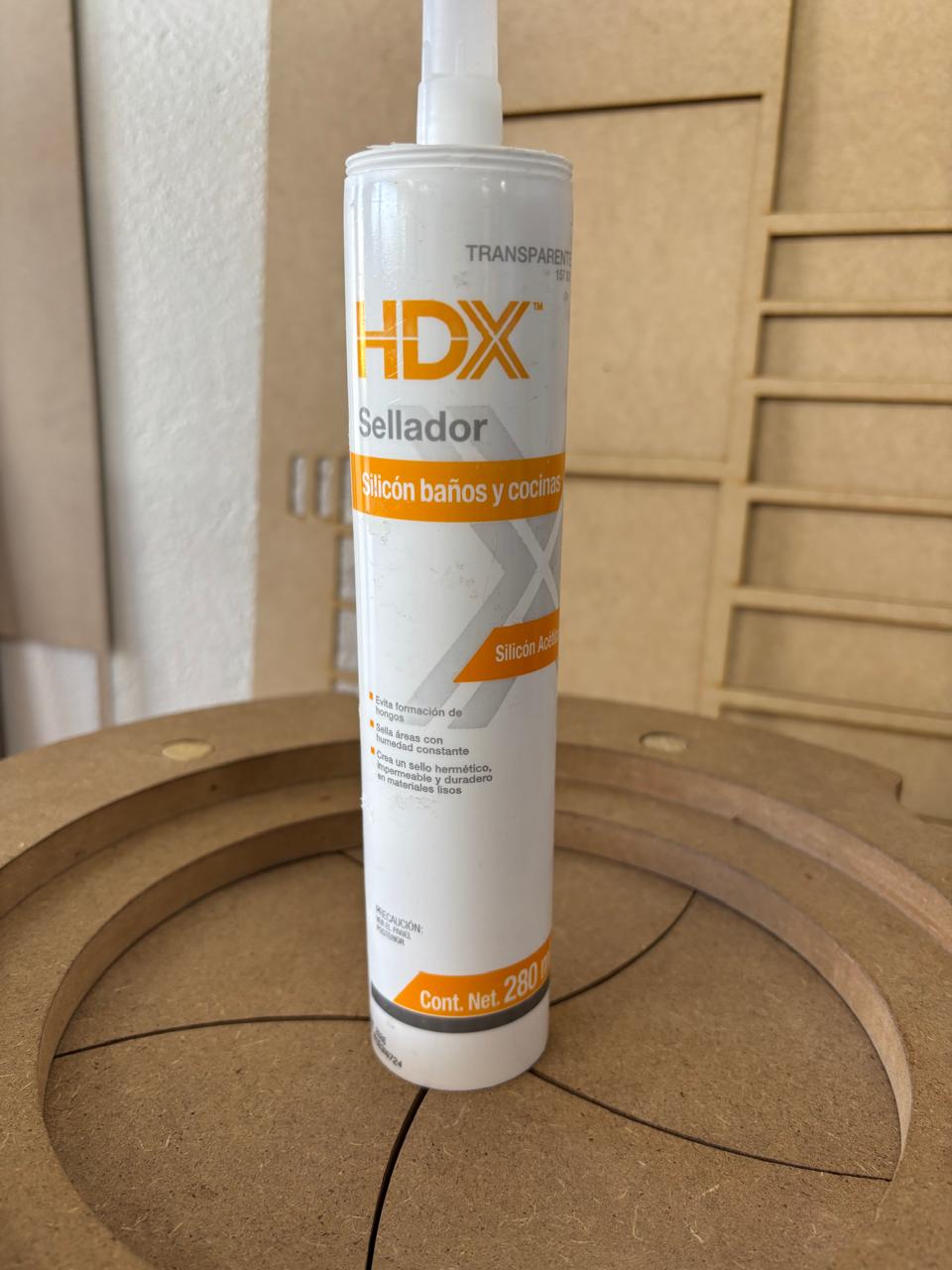
Features:
Resistance to Extreme Temperatures
Maintains its physical properties over a wide temperature range, approximately -60°C to 250°C.
Flexibility and Elasticity
Highly elastic and flexible, making it ideal for applications requiring absorption of movement and vibrations.
Weather Resistance
Resistant to moisture, ultraviolet radiation, and ozone, providing durability in harsh environmental conditions.
Electrical Properties
Acts as an excellent electrical insulator, widely used in the electronics industry.
Chemical Inertness
Inert and stable against a variety of chemicals, suitable for industrial and medical applications.
Biocompatibility
Odorless, non-toxic, and non-staining, making it safe for food contact and medical uses.
Justification for material selection in sustainable design
The material selection in this project was based on sustainable design principles, aiming to minimize environmental impact without compromising the functionality and durability of the prototype. Today, sustainability in product design is essential to reduce the carbon footprint and promote responsible practices in manufacturing and resource consumption. Aluminum, PLA, and acrylic were strategically chosen for their physical properties, recyclability, and market availability.
Aluminum has proven advantageous in structural design due to its high strength-to-weight ratio, allowing for robust systems without adding excessive weight. This characteristic is particularly relevant in applications where energy efficiency and durability are crucial (Rodriguez & Liu, 2020). Furthermore, aluminum is highly recyclable, which significantly reduces energy and resource consumption compared to producing virgin materials (European Aluminium Association, 2021). With its corrosion resistance, aluminum ensures an extended lifespan, avoiding frequent replacements and contributing to long-term waste reduction.
On the other hand, PLA was chosen for its biodegradable nature and lower environmental impact compared to conventional plastics like ABS. Unlike petroleum-based plastics, PLA is manufactured from renewable resources, such as corn starch, making it a more sustainable option (Auras et al., 2004). Additionally, PLA is suitable for 3D printing, enabling the production of precise and custom parts with minimal material waste, which is essential in sustainable digital fabrication.
Acrylic was selected for its transparency and rigidity, qualities that facilitate visual inspection of the prototype's internal components. Although not biodegradable, acrylic has a long lifespan and is recyclable, making it a suitable choice for applications requiring durability and resilience. Its use is justified by the possibility of reusing or recycling acrylic parts at the end of their life cycle (Tsai, 2019).
Together, the choice of these materials reflects a comprehensive approach to sustainability, considering both direct environmental impact and the life cycle of each component. This material selection not only optimizes the prototype's performance but also promotes responsible design practices, aligning with current sustainability goals and the commitment to a greener, more conscious future.