Molding and casting
Let's go!
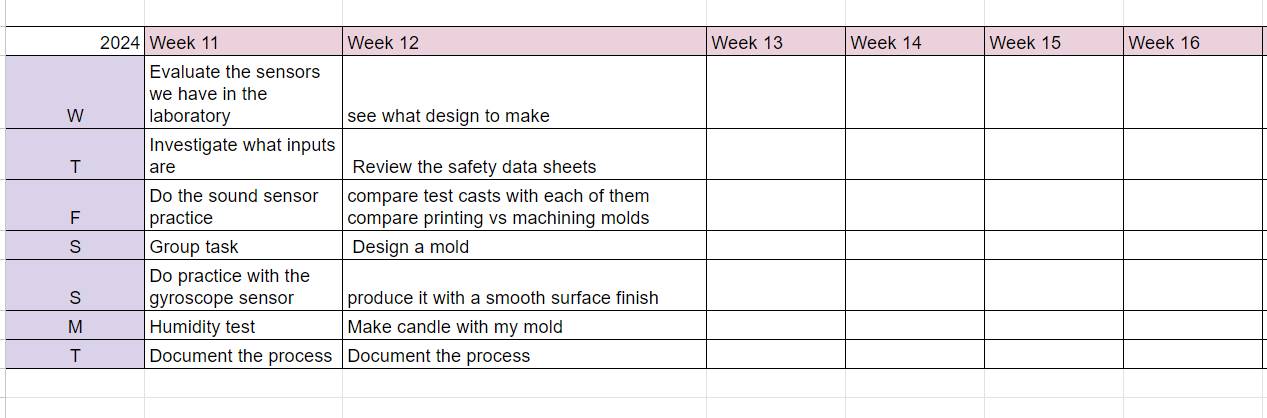
This week I am very excited, it is something I have wanted to do for a long time, to be able to create my own molds.
WEEK GROUP
Design Board Safety data sheets for each of your molding and casting materials Designed and created your 3D mold Safely made your mold and cast the parts Final files:
Conclusions
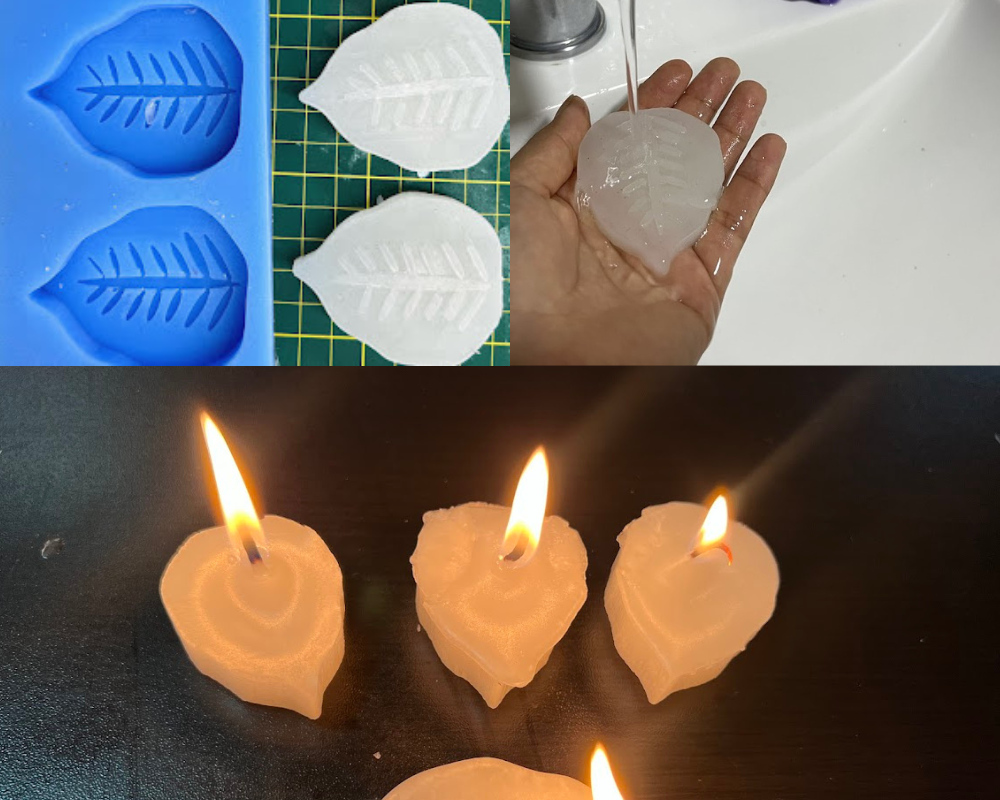
Assignments
-
Group assignment:
- Review the safety data sheets for each of your molding and casting materials, then make and compare test casts with each of them compare printing vs machining molds Individual assignment:
- - Design a mold around the process you'll be using, produce it with a smooth surface finish, and use it to cast parts
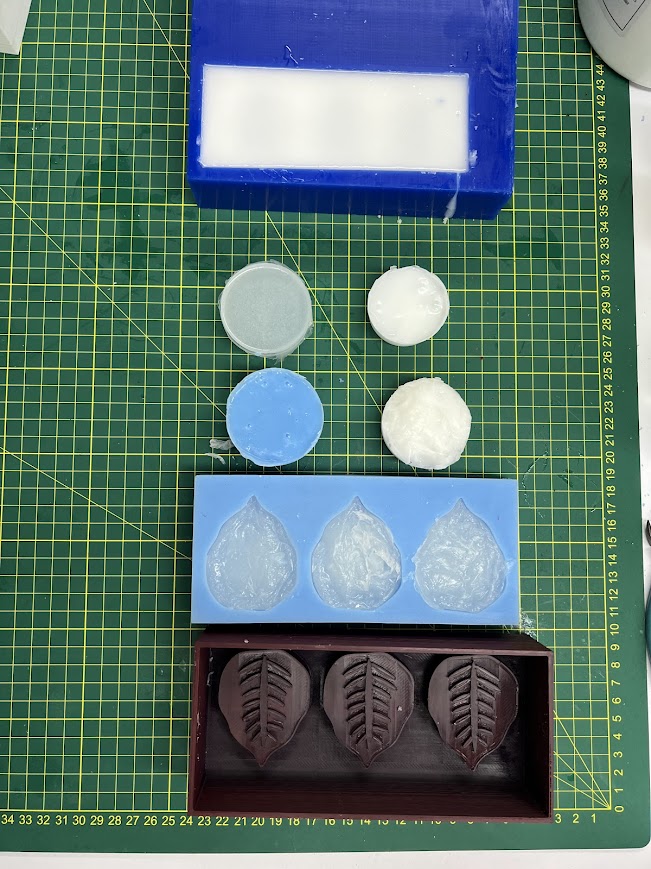
Group assignment
In the group assignment we explored various types of materials, some of the silicones we used did not have a data sheep as such, but the supplier gave us a summary of the instructions, other suppliers did have one, and they sent them to you by WhatsApp clearly indicating what you did. the purchase and send the purchase receipt. There are several companies where you can buy, for example, this silka and silcon peruREVIEW THE SAFETY DATA SHEETS FOR MATERIALS
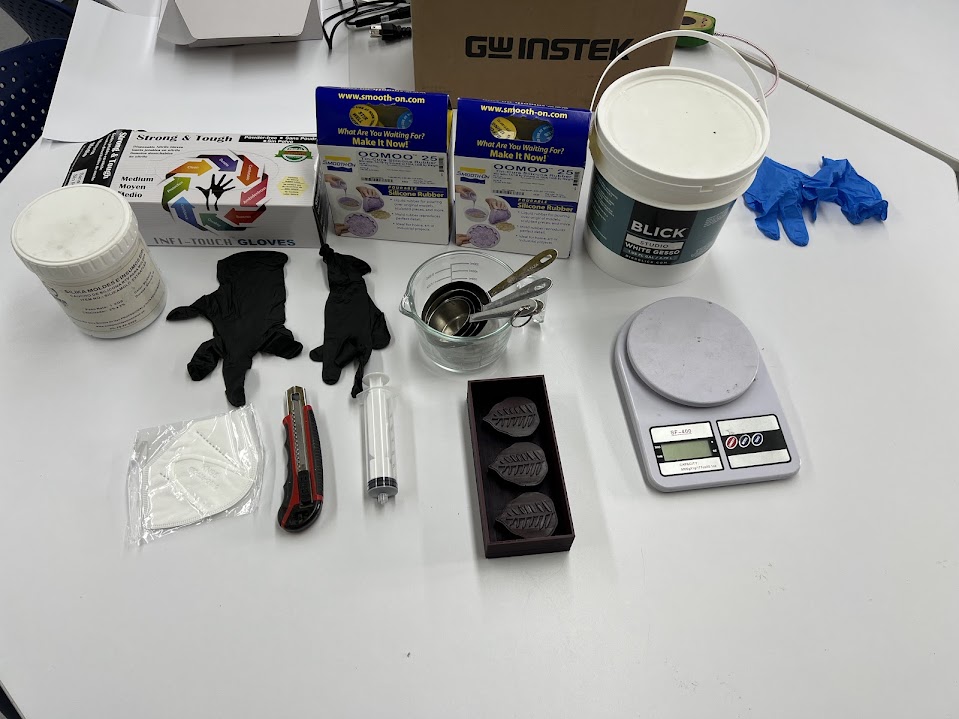
First, my classmates and I reviewed everything we had at home and in the laboratory, I brought a silicone that I had a while ago when I took a digital experimentation course where we did sofrobotic, so I took it to test.
Now I show you everything we found
- Balance
- Syringe
- Containers with measurer
- Gloves
- silicones as many as you can try
- Face mask
- Cuter
- Mold made by you
SILICON OMMO 25 - SMOOTH ON
DATA SHEET
PDFThe first thing we did with my group was to look for the materials in the USCUR laboratory, something very sad was finding the silicone, to be exact OMMO 25 from SMOOTH - ON, the one with the yellow knob was hard, there was no way to use it and there were several failed batches, We were very sad, but it didn't stop us from continuing with the other materials we brought.
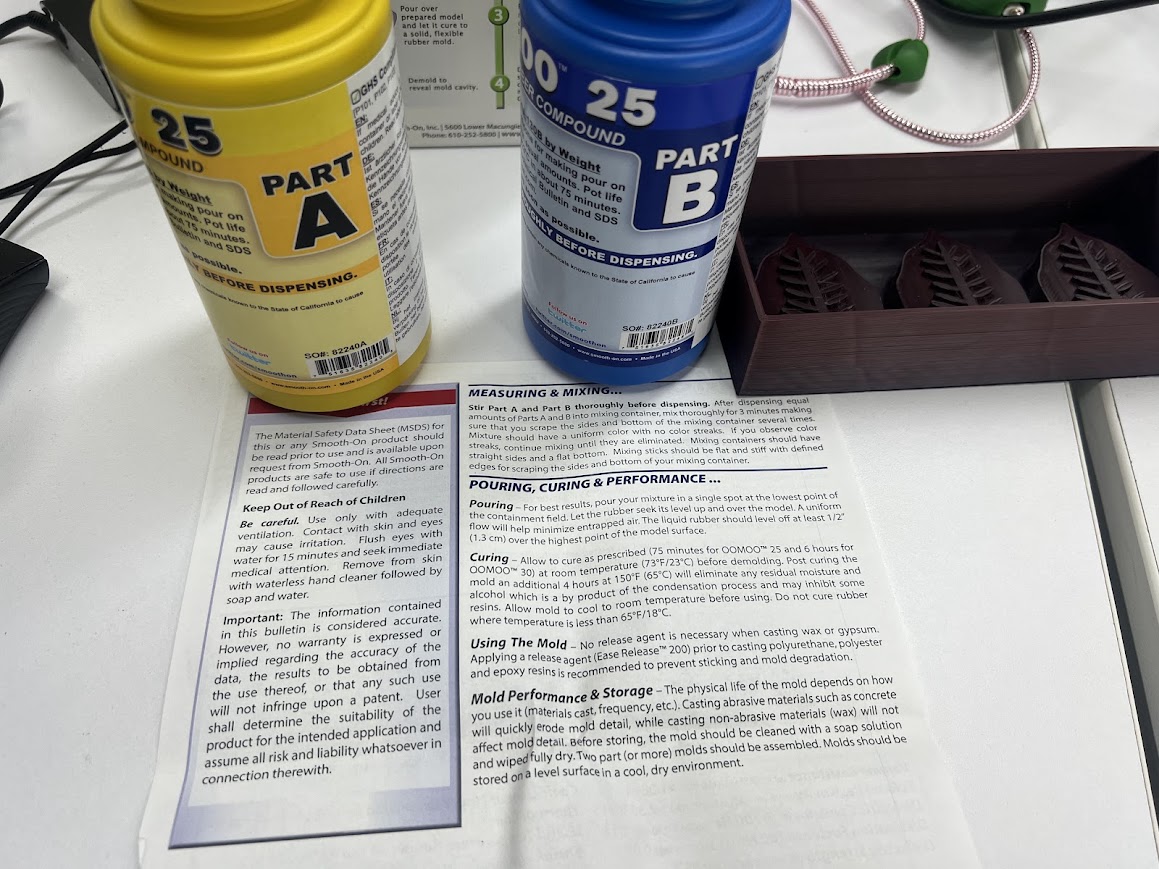
SILICON RTV F20 PLUS
DATA SHEET
PDFSPECIFICATIONS
- Cure at room temperature within 4-8 hours, but all perfomance will act perfectly when it cure within 2-hours.
- Good fluidity and ecellent operation
- Good resistance to weather, temperature, aging, acid.
- Excellent tear strength, comfortable duplication times
- Firstly, after your previous work of dealing with the original model, take some liquid silicone rubber, add 2%~3% cuing agent of the amount of silicon and mix them evenly.
- Then after vacuum-pumping the mixture, you can pour it into the mold frame.
- . The silicone mold will cured in 2~3 hours
- Base and Curing Agent Mixture (100:3 by weight) in 25 °C (77F) testin
- MIX RATIO INSPECTION METHOD A:B VALUE 100:3
- POT LIFE INSPECTION METHOD : 25°C VALUE: 40-50 mins
- Demold time INSPECTION METHOD : 25° C VALUE:8-12h
- Shelf life 12 months with original unopened package
The following silicone consists of 2 parts A Silicon and B Curing agent, a white liquid which is the silicone and the curing agent. Curing time is 4 to 8 hours. It has good tear resistance and excellent temperature resistance. Here is a summary table of the data sheets provided by the seller and the PDF to download.
We started weighing to achieve the proper ratio between silicone and curing liquid according to the data sheets.
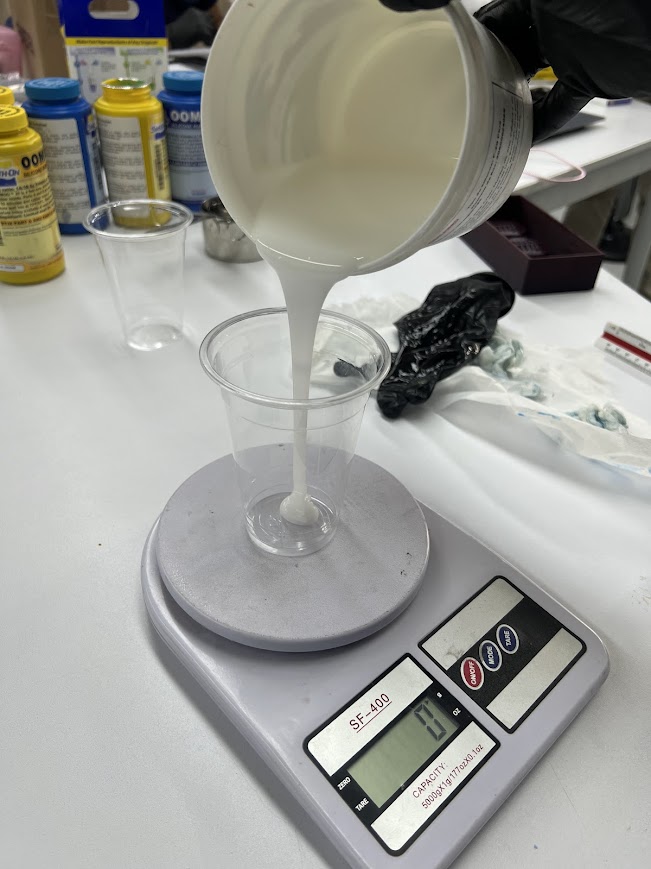
We weighed the silicone to ensure precise measurements, allowing us to calculate the exact amount of catalyst needed for mixing.
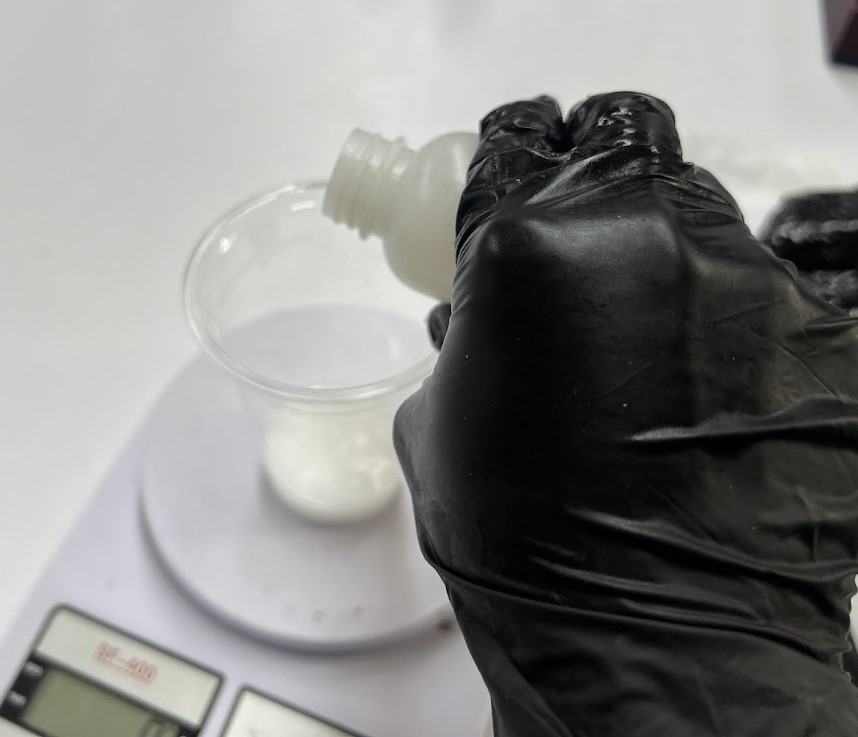
We measured and mixed the materials according to the proportions outlined in the technical datasheet.
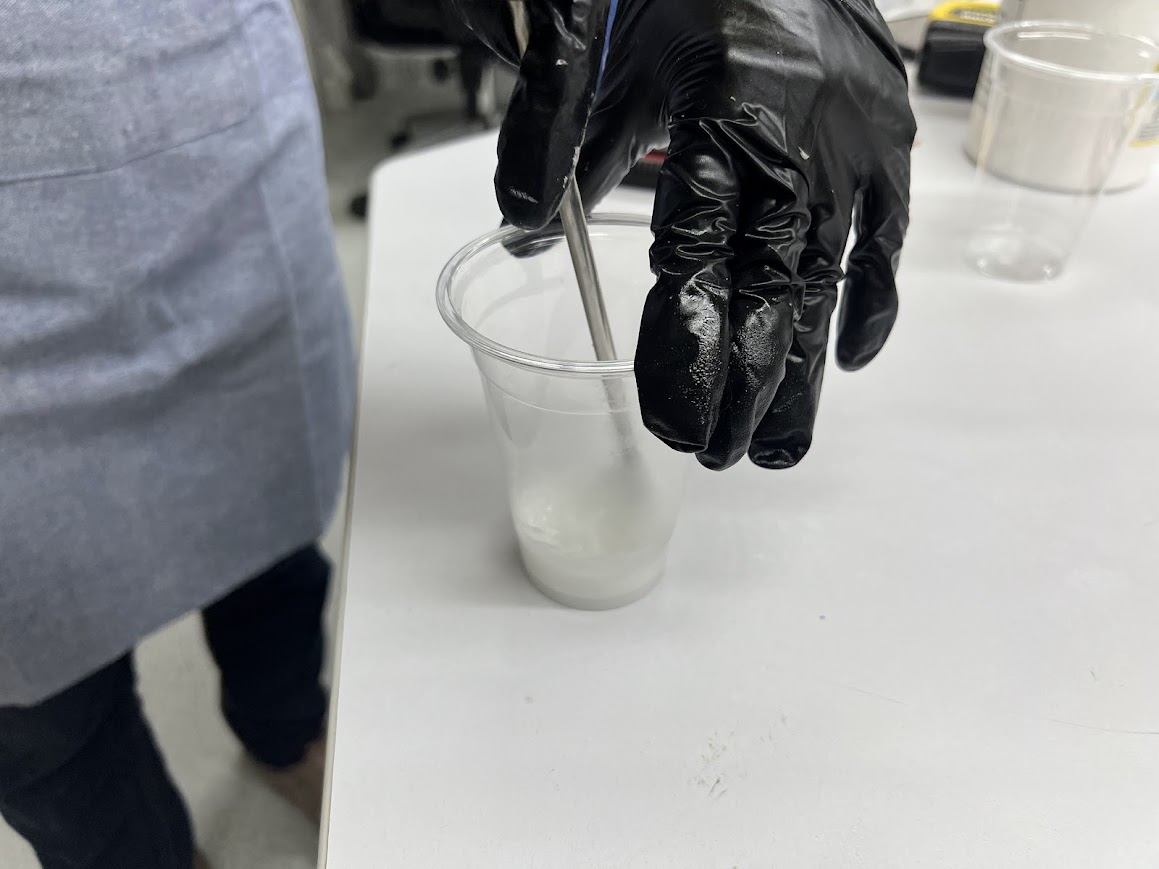
We moved the two materials slowly to prevent the formation of too many bubbles.
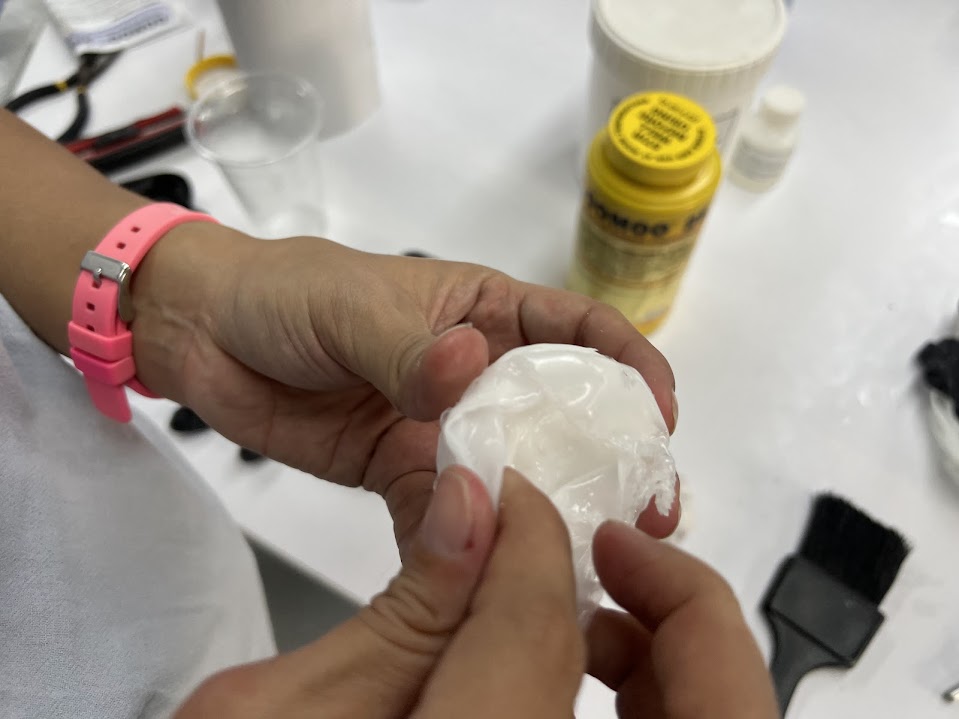
We can observe the result of the first test, which yielded a silicone mold that is more robust, with some excess material around the edges due to leftovers in the container. However, we were able to remove these excess parts to assess its consistency and strength.
PLATINUM RTV SILICONE HARDNESS 30-1 FOOD
DATA SHEET
PDFGiven that we're using PLATINUM RTV SILICONE HARDNESS 30-1 FOOD, safety is still a priority. While this type of silicone is not as toxic, we'll still adhere to safety protocols by wearing gloves, a mask, and safety glasses. This precaution ensures that we're protected from any potential hazards during the work process.
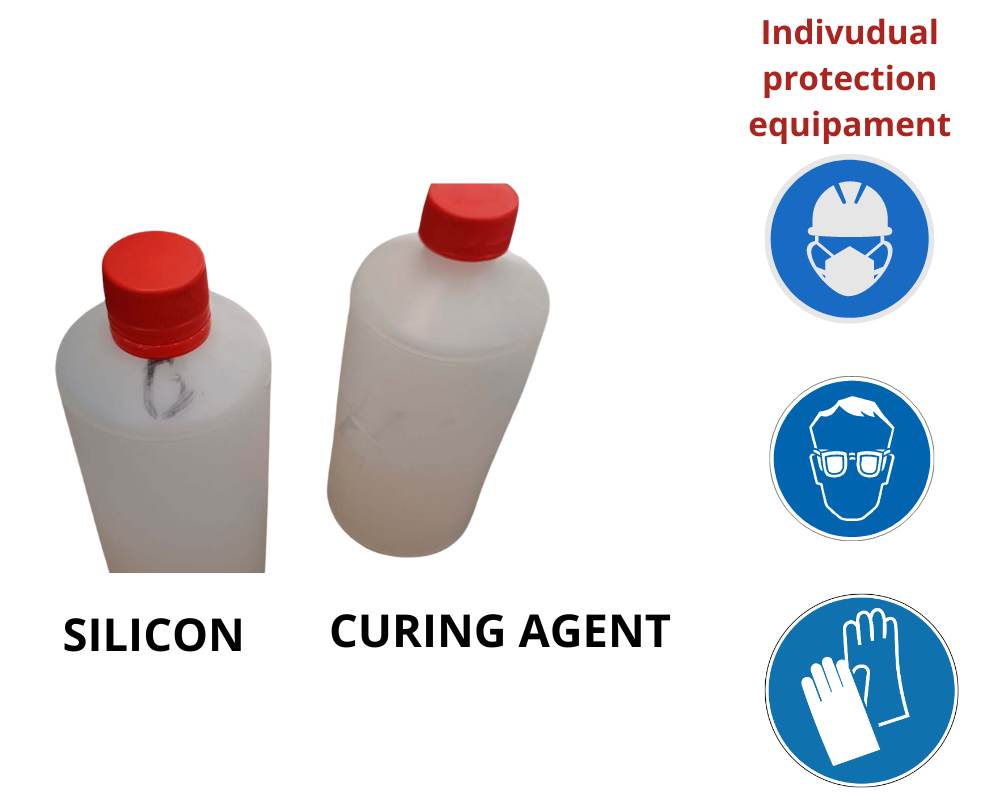
RTV EXTRAFLEX SILICONE RUBBER
DATA SHEET
PDFWith RTV EXTRAFLEX SILICONE RUBBER, full protection is required, including safety glasses, a respirator mask, and gloves.
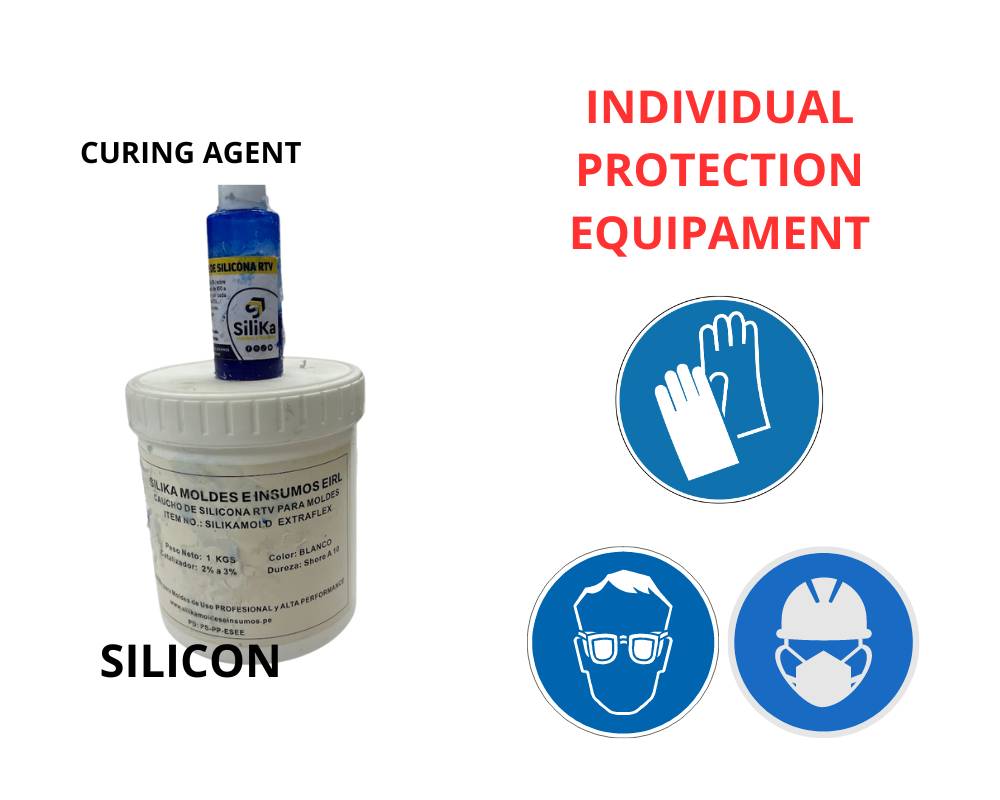
The first thing we did with Hans was to measure out the portions we were going to use for the tests.
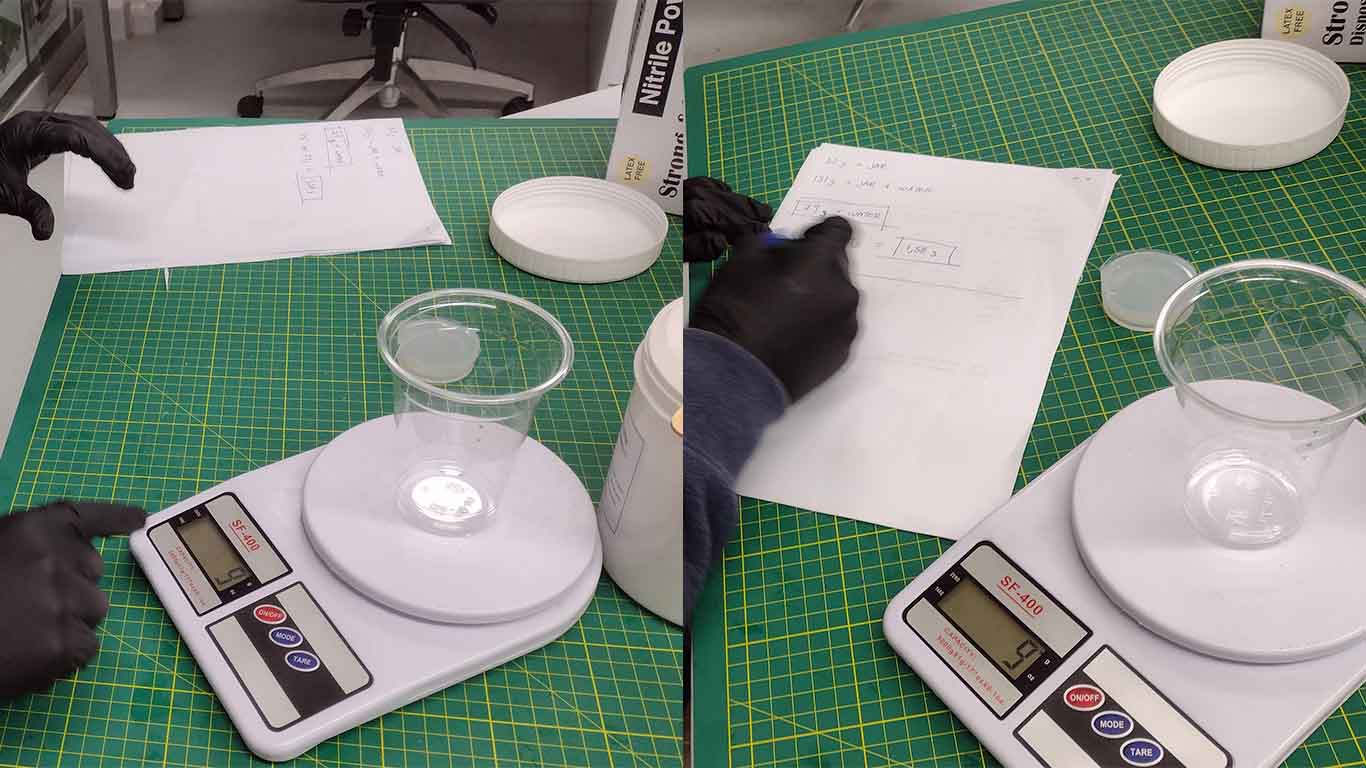
We measured out the silicone to the same quantity as the other molds, and then added 1% of catalyst to ensure it would dry within 6 to 8 hours..

SILICON F10 PLUS
DATA SHEET
PDFIndividual assignment
DESIGN MY MOLD
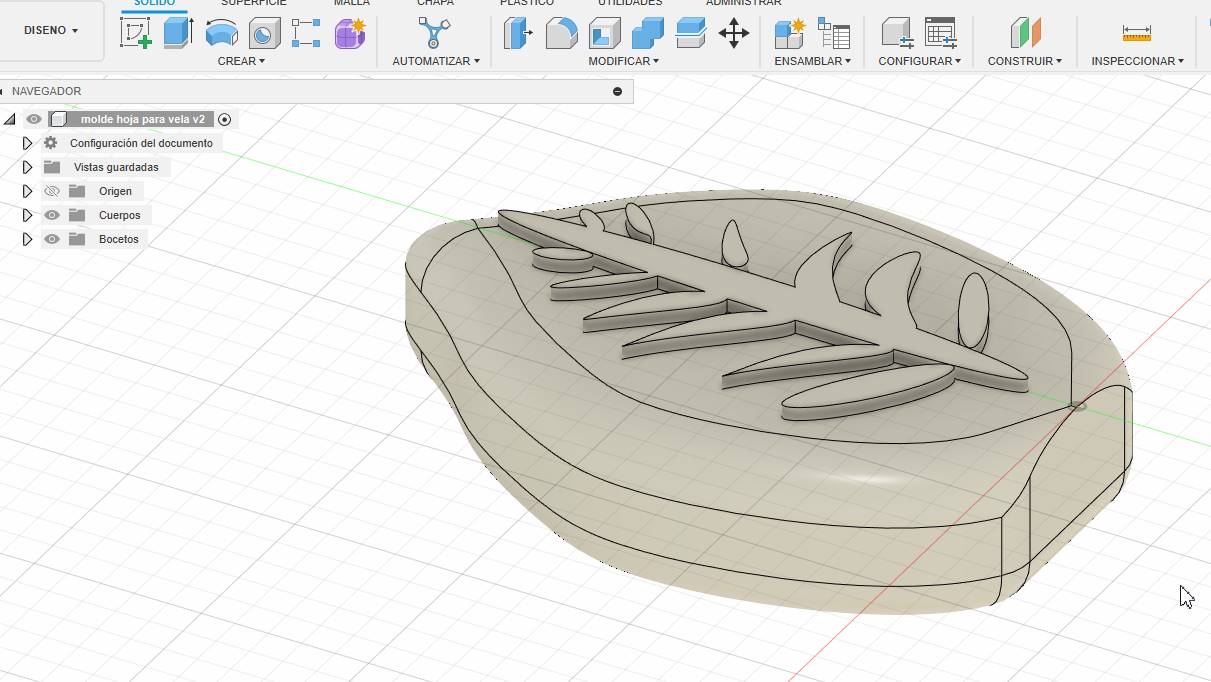
"Design My Mold" began with my initial design, which evolved and changed over time. You'll see many versions of my molds as they progressed.
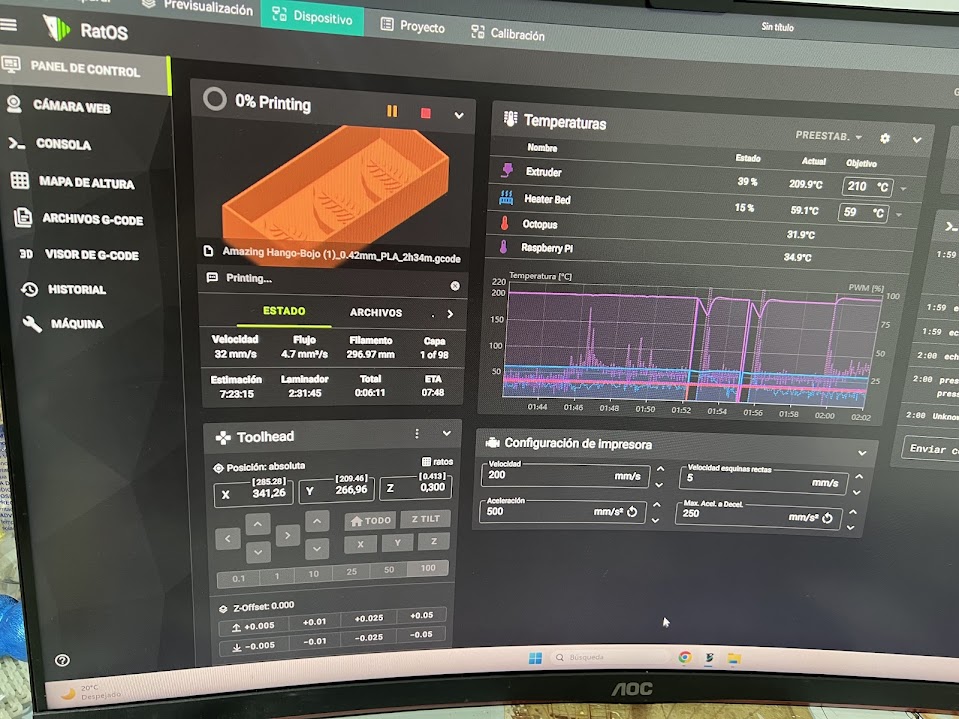
Here, we need to slice it in Orca. We can observe that the printing time is 7 hours and 23 minutes, with a material consumption of 296.97mm.
SILICONE MOLD
I'm glad you loved the outcome of the silicone mold. It's fantastic to see how the detail and smooth finish will allow you to replicate your soaps and candles accurately. Sounds like a total success!
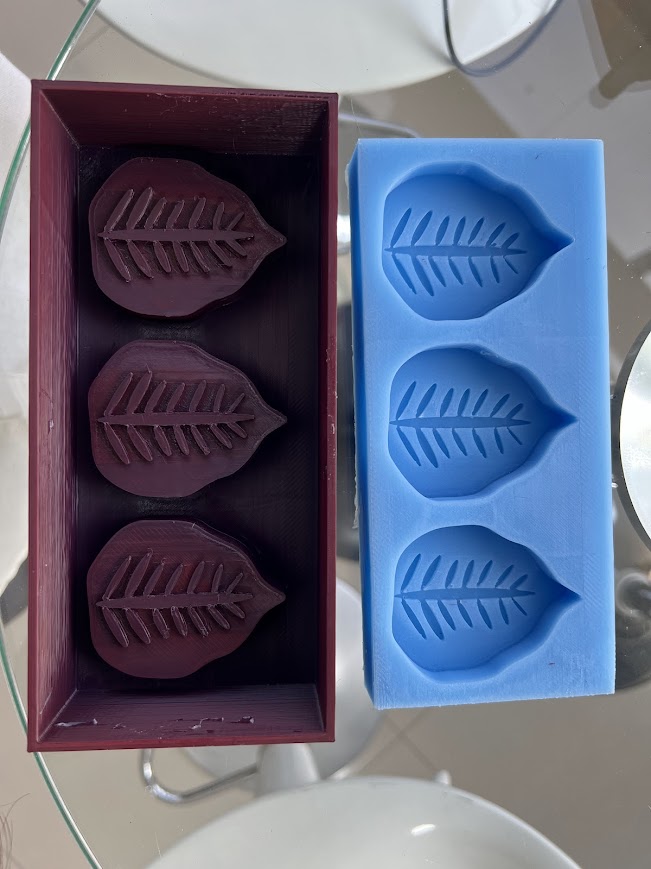
CASTINGS
Now, for casting, one crucial aspect is the products you can create from your molds.
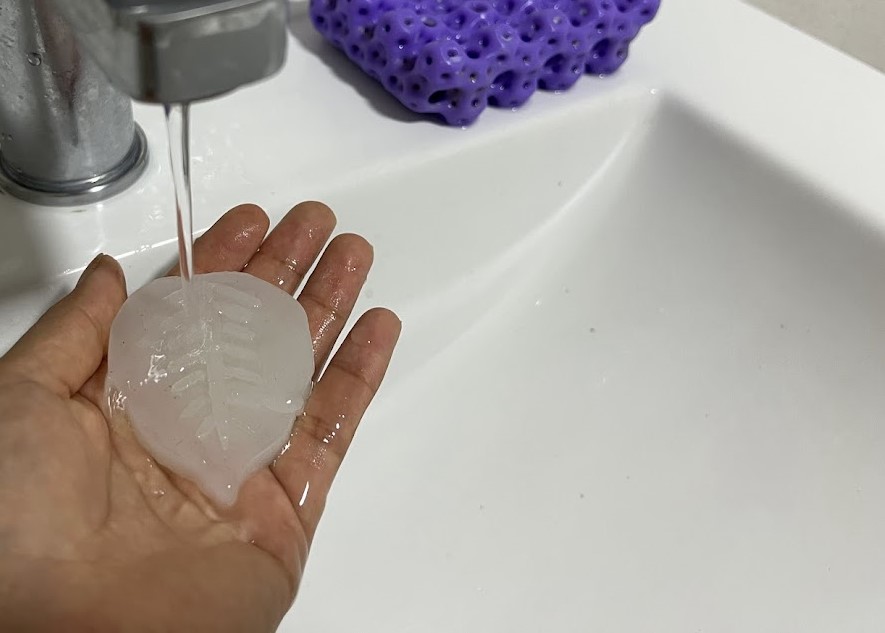
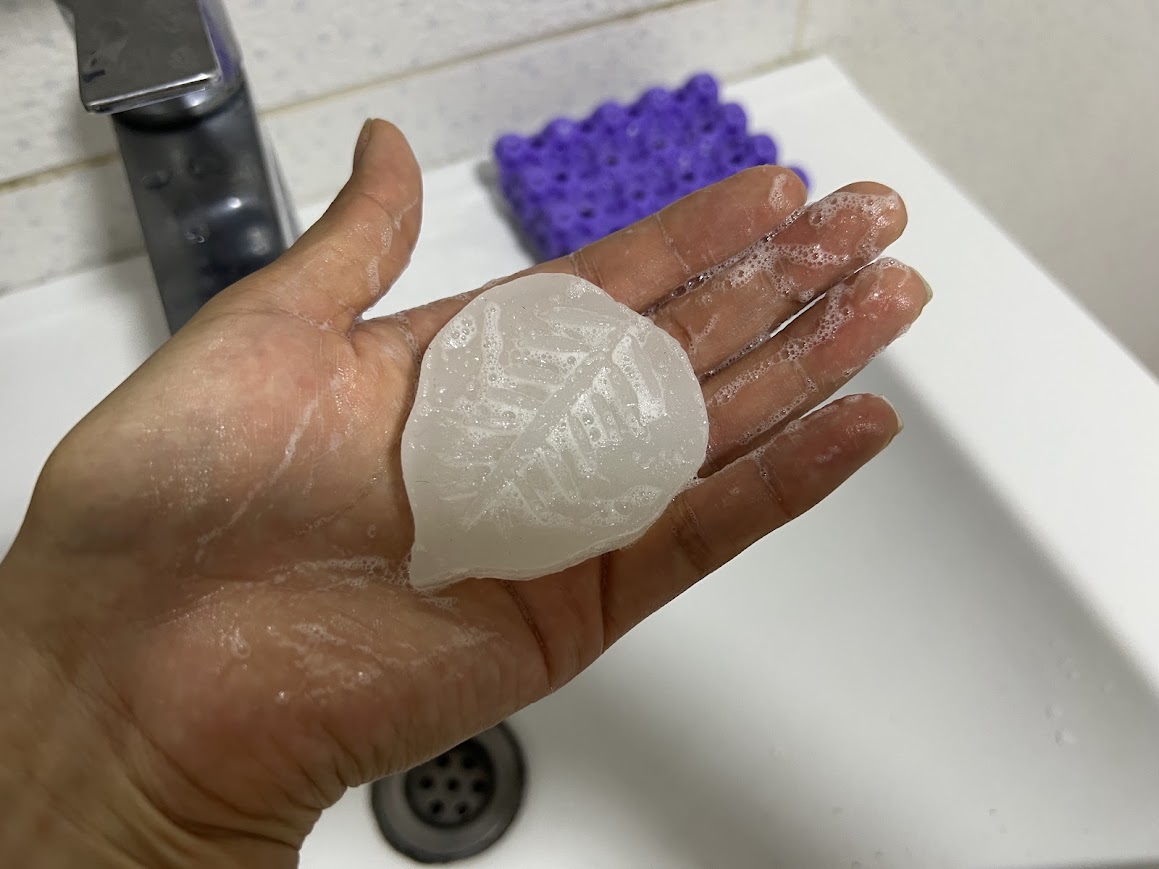
The soap lathers up really well, now everyone's using it!
MILLING MY MOLD
In this part my colleague Hans made an inventory of all the things that were going to be needed to make the mold, and saw that the best thing would be to work with the SHOPBOT.
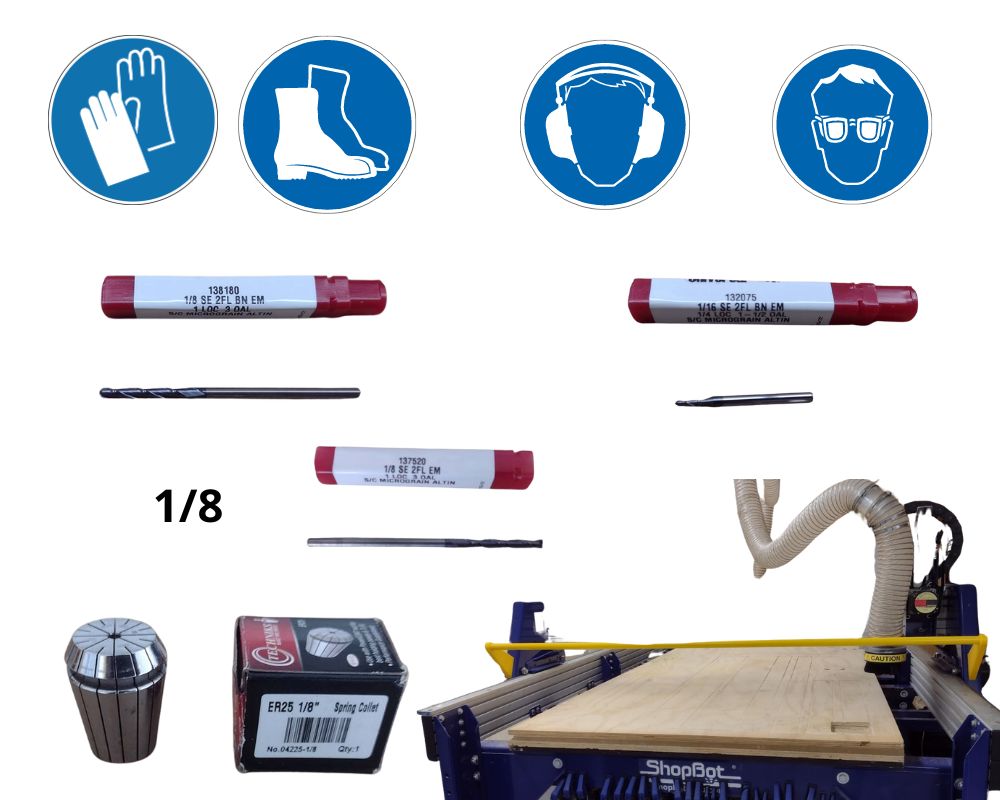
To finish use a 1/8" milling cutter.
CONFIGURATION TO MILLING ROUG WITH MODS CE
MILLING MY MOLD
After obtaining the MILLING file, we proceeded to configure the SHOPBOT for milling. hans installed the 1/8" round nose cutter and adjusted the Z axis, Hans assisted me in this process, providing guidance on calibration and cutter installation. While there were some initial errors, we continued to practice and refine our technique.
SILICONE MOLD
The main thing is to understand how to use the oscilloscope and then obtain accurate measurements. Recently, we performed tests on a servo motor using the Miniware DS213 Portable Mini Oscilloscope. During these tests, we focused on key aspects such as frequency, amplitude and voltage, with the aim of understanding its behavior and verifying its correct operation. Using the oscilloscope, we were able to observe in detail the waveform generated by the servomotor, which allowed us to analyze aspects such as stability, response to different commands and consistency in its operation. This information was invaluable to ensure that the servomotor was operating within the expected parameters and to identify any anomalies that might require attention.
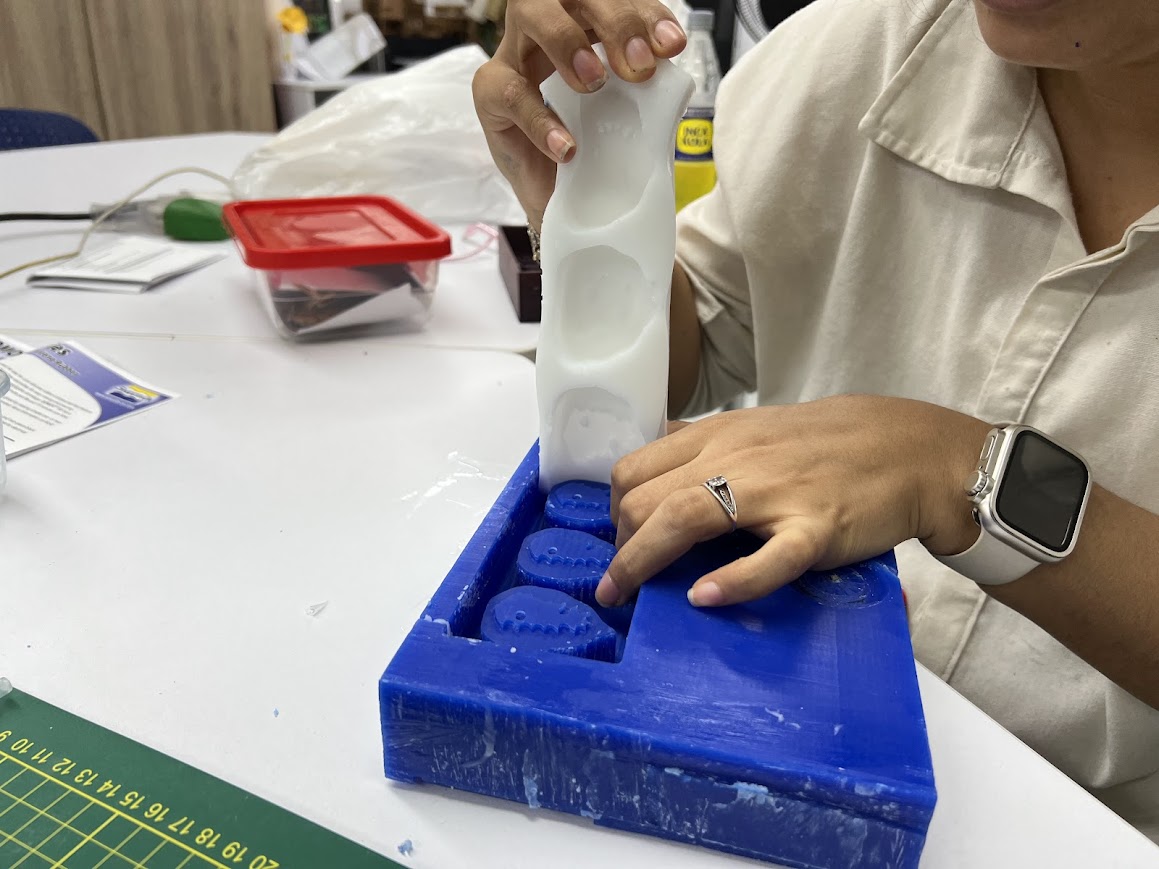
In summary, the use of the oscilloscope allowed us to perform extensive testing and obtain accurate measurements, giving us greater confidence in the quality and performance of the servo motor.
Final result
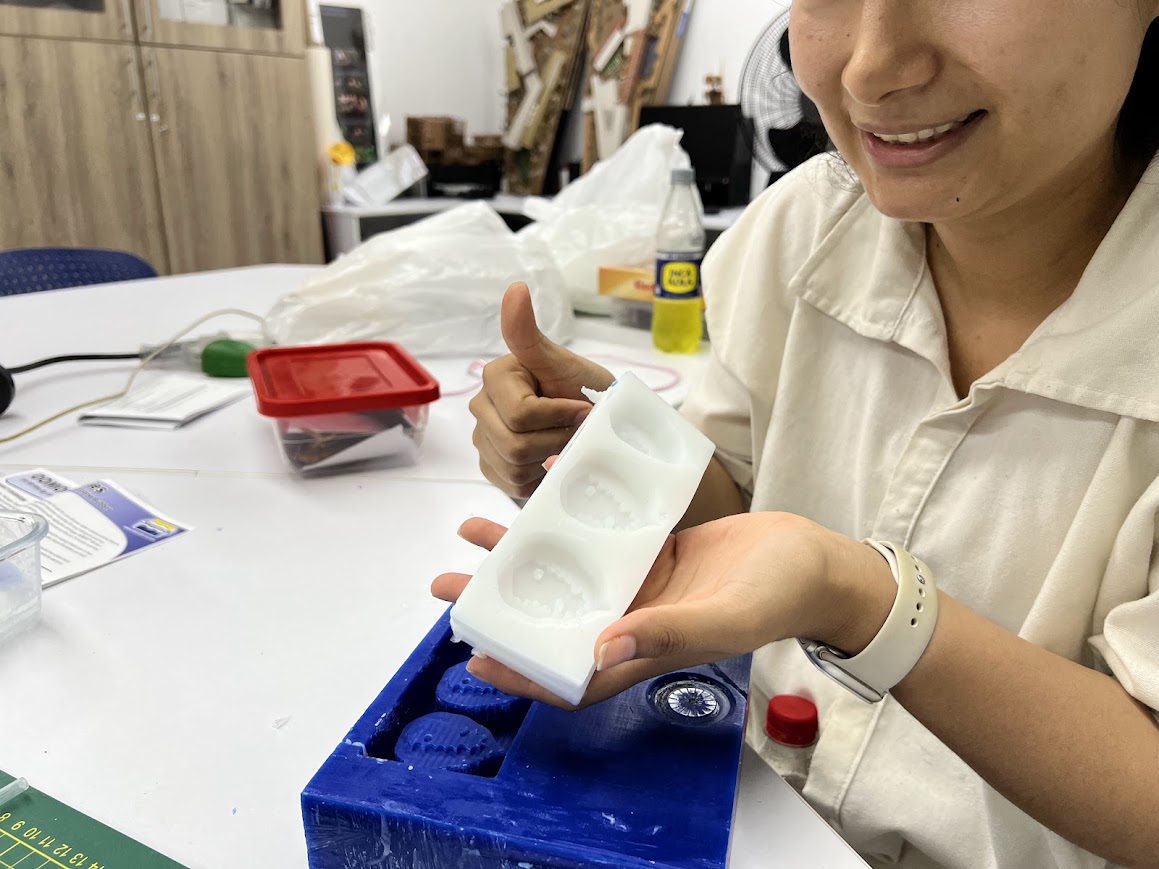
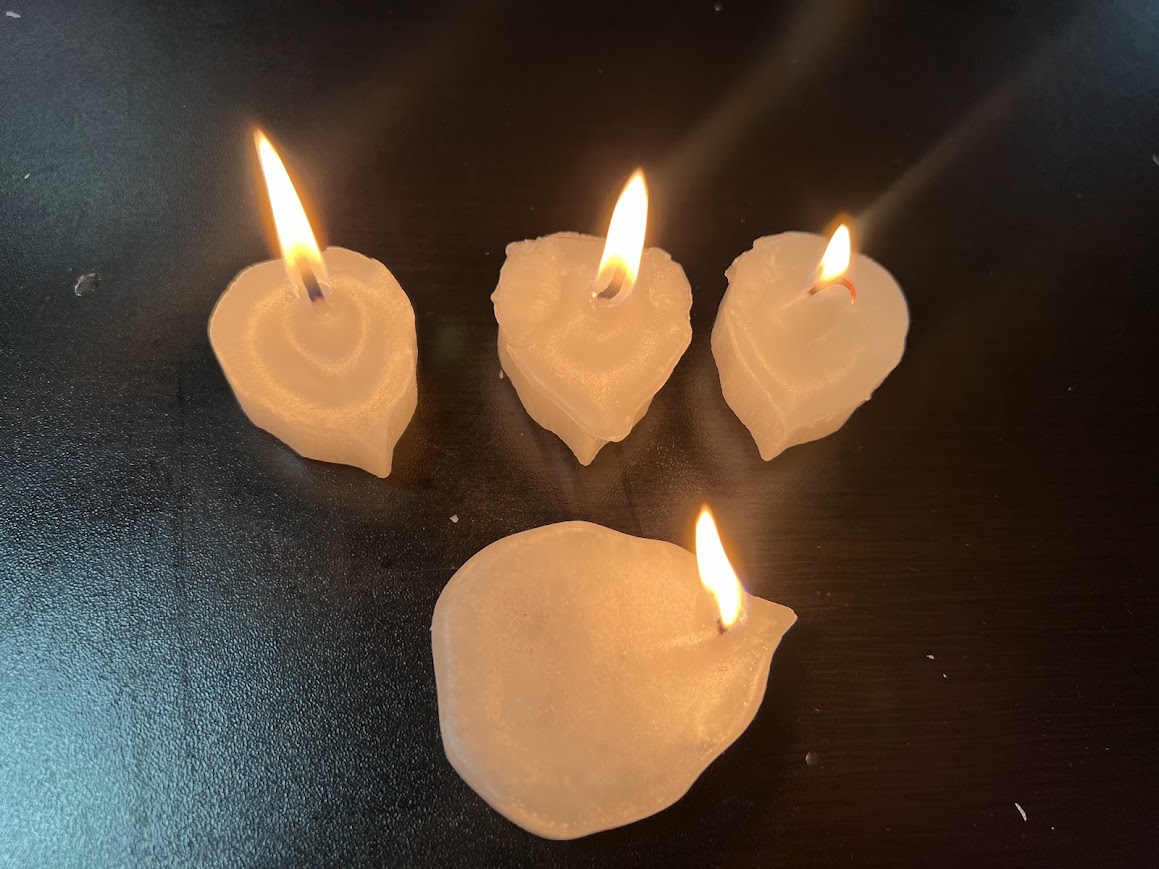
CONCLUSIONS
This week's task has been quite a challenge for me, since I entered a new field that I was completely unaware of: working with molds. Despite the setbacks I faced during the week with the material, we managed to make considerable progress. As I mentioned, we had hard silicone that was no longer useful and we had to buy others. Consider this, if it has been stored for more than a year, it is probably already hard.
In conclusion, this week has been crucial for my learning in mold-making and the proper use of silicones. Understanding the technical specifications of these materials is essential to achieve quality molds that are durable and suitable for our projects.
It is crucial to consult the datasheet of each silicone to avoid wasting time and materials through trial and error.
Described problems and how you fixed them
This week's task has been quite a challenge for me, since I entered a new field that I was completely unaware of: working with molds. Despite the setbacks I faced during the week with the material, we managed to make considerable progress. As I mentioned, we had hard silicone that was no longer useful and we had to buy others. Consider this, if it has been stored for more than a year, it is probably already hard.
Regarding the finish of my mold, I admit that I would have liked to obtain a more polished finish on the machine molds. I think we could achieve even better results if we do more research on how to improve the finish of the wax bar on the CNC machine.
On the other hand, I really enjoyed the process of working with the molds and the various characteristics and configurations that we must take into account. It is fascinating to discover the wide variety of silicones available and how each one of them has a specific function, whether for objects or food.
Regarding aspects to improve, we identified some key points. For example, we ran into difficulty achieving 90 degree angles in some cases, which affected the final shape of my piece. It is clear that we need to explore more strategies to address this challenge and ensure that we can reproduce more accurate ways in the future.
Despite the obstacles encountered, this project was extremely interesting and enriching. I learned a lot and, although I experienced a certain amount of anxiety, I am encouraged to continue expanding my knowledge about working with molds and to achieve perfection in making them with our machine.