Results: Mechanical Design, Machine Design
This week, we built PachamamaPrint, a 3D printer for peruvian superfoods such as maca. Building this machine was a multifaceted endeavor blending innovation, sustainability, and culinary creativity. From drawing inspiration from Peru's rich culinary heritage to meticulously designing and manufacturing each component, the process was a testament to our team's dedication and ingenuity. Leveraging cutting-edge 3D printing technology and a collaborative spirit, we brought our vision to life, transforming maca—a revered superfood—into enticing and nutritious culinary creations. Through thoughtful design, iterative refinement, and a commitment to sustainability, PachamamaPrint emerged as more than just a machine; it symbolized a holistic approach to addressing nutritional challenges while honoring our cultural heritage and environmental stewardship.
Through collaborative teamwork, we synergized our diverse skills and perspectives, ensuring the seamless integration of design, manufacturing, and sustainable practices, culminating in the realization of PachamamaPrint as a collective achievement. I contributed with the design and manufacturing some components of the machine.
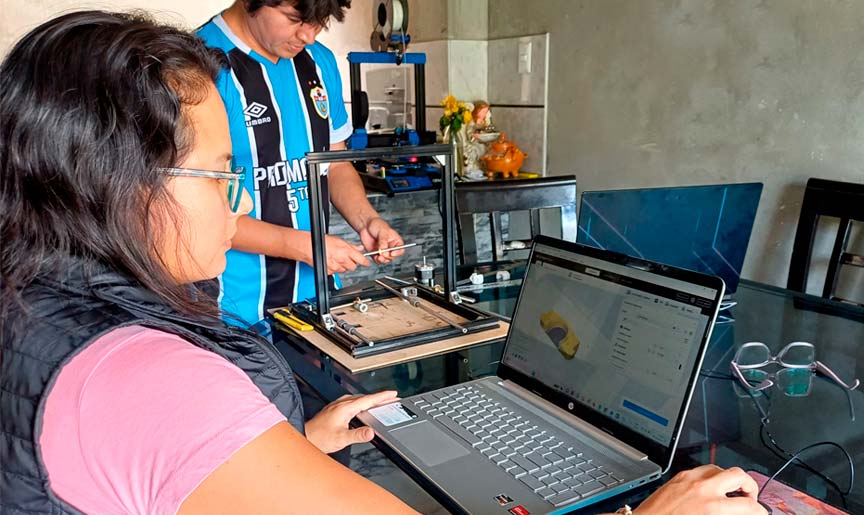
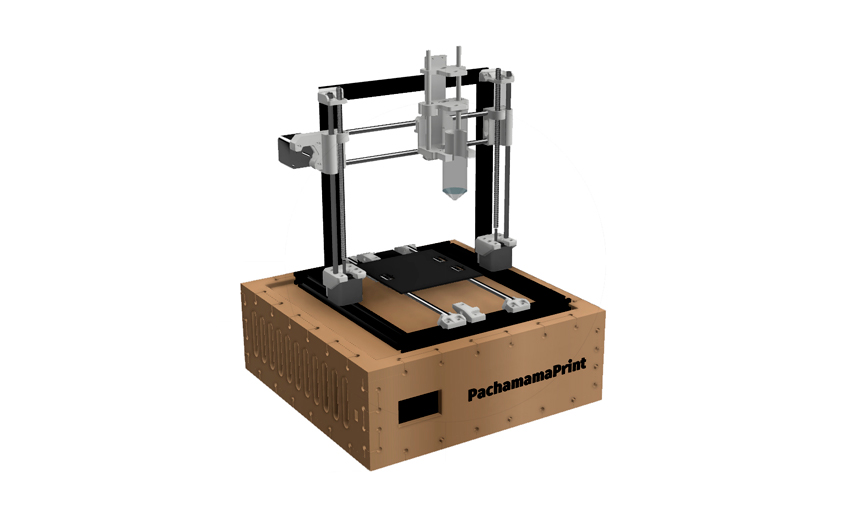
Designing and manufacturing PachamamaPrint
Group Assignment: PachamamaPrint
The group assignment page is here.
Individual Assignment: Design and Manufacturing
Design
In the initial phase of designing PachamamaPrint, I delved into the realm of existing 3D printers, particularly those specializing in chocolate, scouring the market for inspiration. Observing their forms and functionalities, I began sketching out preliminary designs, envisioning a cubic structure that would provide stability and practicality for our intended purpose. Taking cues from the sleek, streamlined shapes of contemporary food printers, I aimed to marry functionality with aesthetics, ensuring that our machine would not only be efficient but also visually appealing.
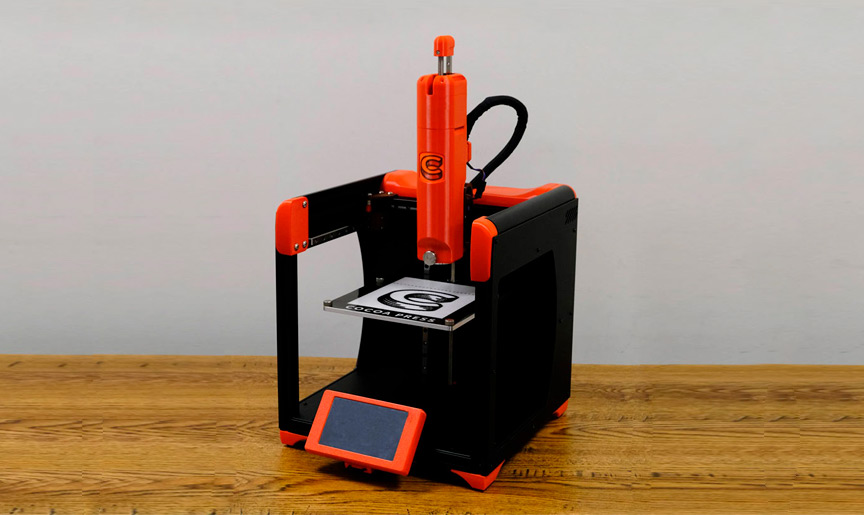
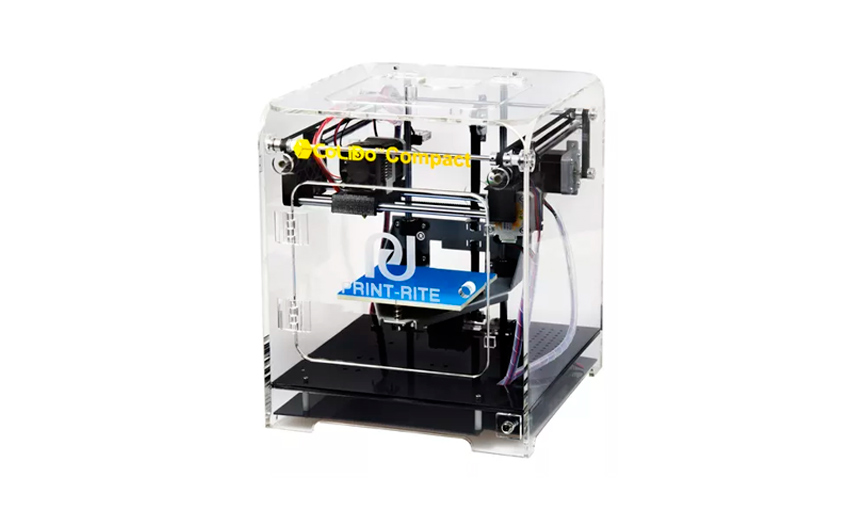
Cocoa Press and Colido Compact 3D printers as structure inspiration
Transitioning from conceptual sketches to tangible designs, I turned to Fusion 360, a powerful CAD software, to bring my ideas to life. Drawing upon components from existing 3D printers, I meticulously crafted each element with precision, seeking to optimize performance and ease of use. Through iterative modeling and refinement, I created a digital prototype of PachamamaPrint, complete with intricate details and realistic textures. Rendering the design allowed me to visualize the final product, refining it further based on feedback and feasibility considerations.
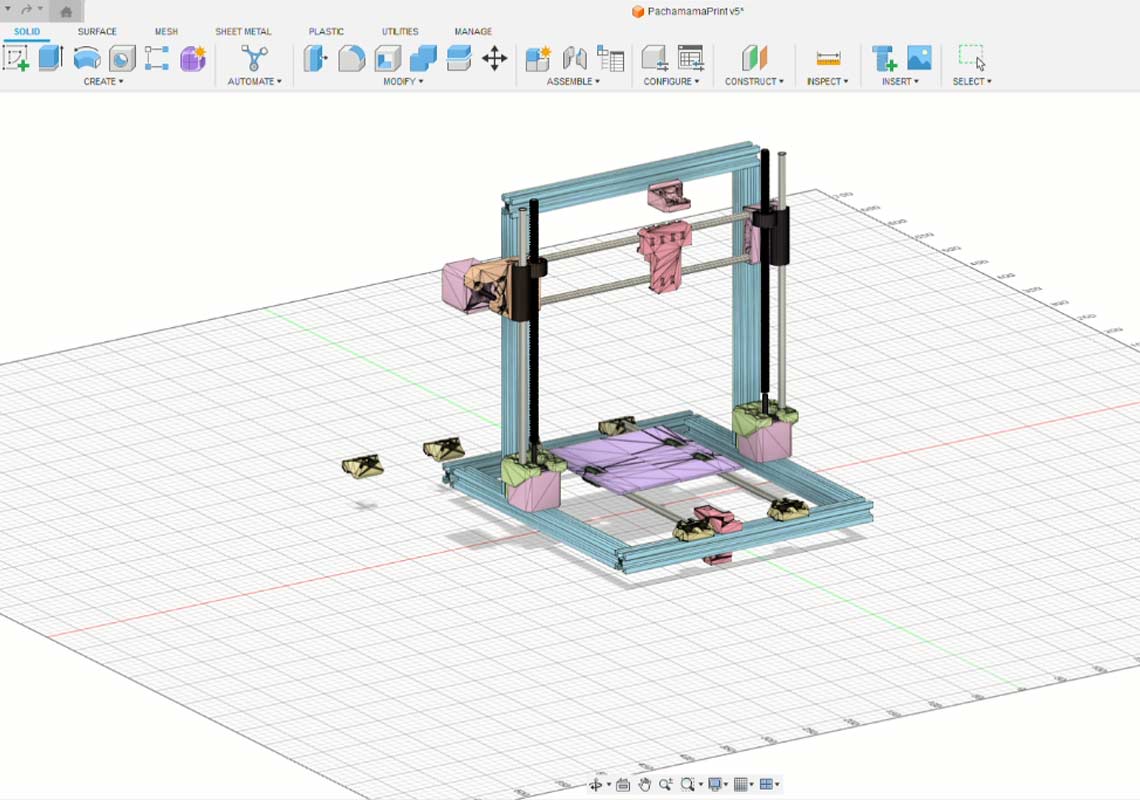
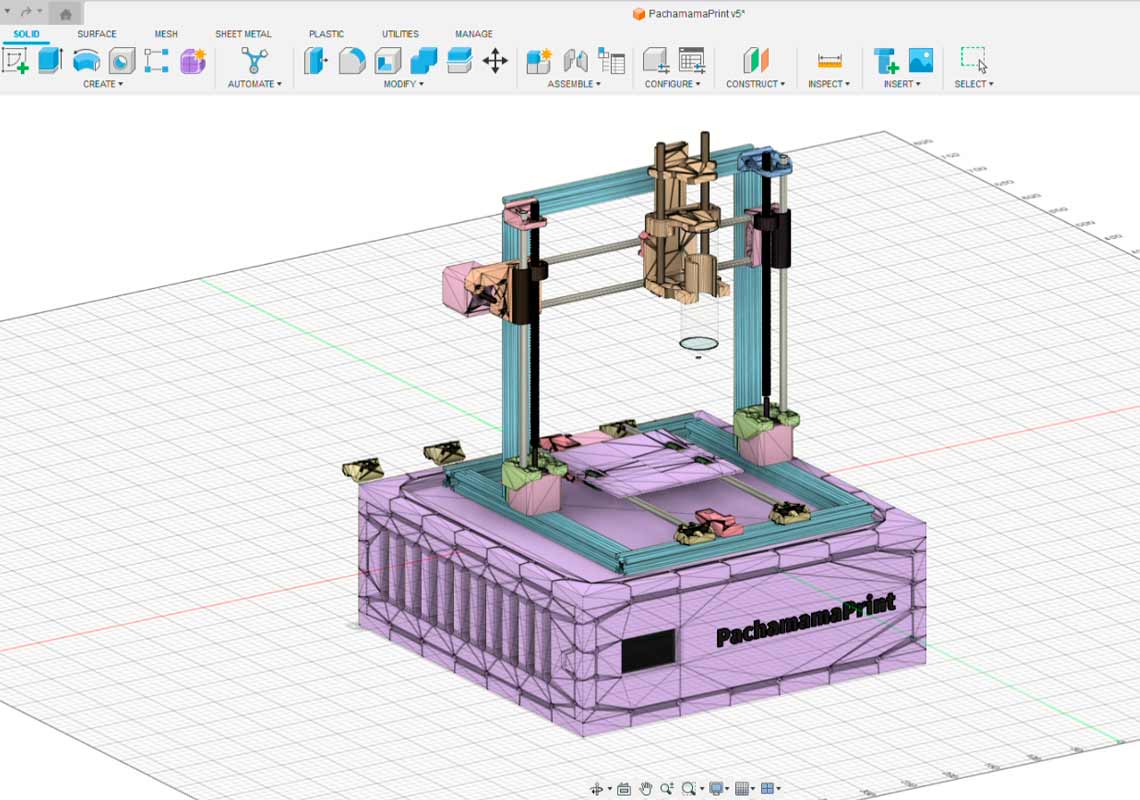
Designing PachamamaPrint in Fusion 360
As our team progressed, we encountered the crucial challenge of adapting our design to accommodate the unique properties of maca and the extrusion process. Collaborating closely with colleagues who conducted ingredient testing, I focused on refining the extrusion component to ensure seamless integration with our chosen superfood. First, I got inspiration on this file. Iterating through various designs and material compositions, we fine-tuned the extrusion mechanism to achieve optimal results, balancing precision with reliability to guarantee consistent output.
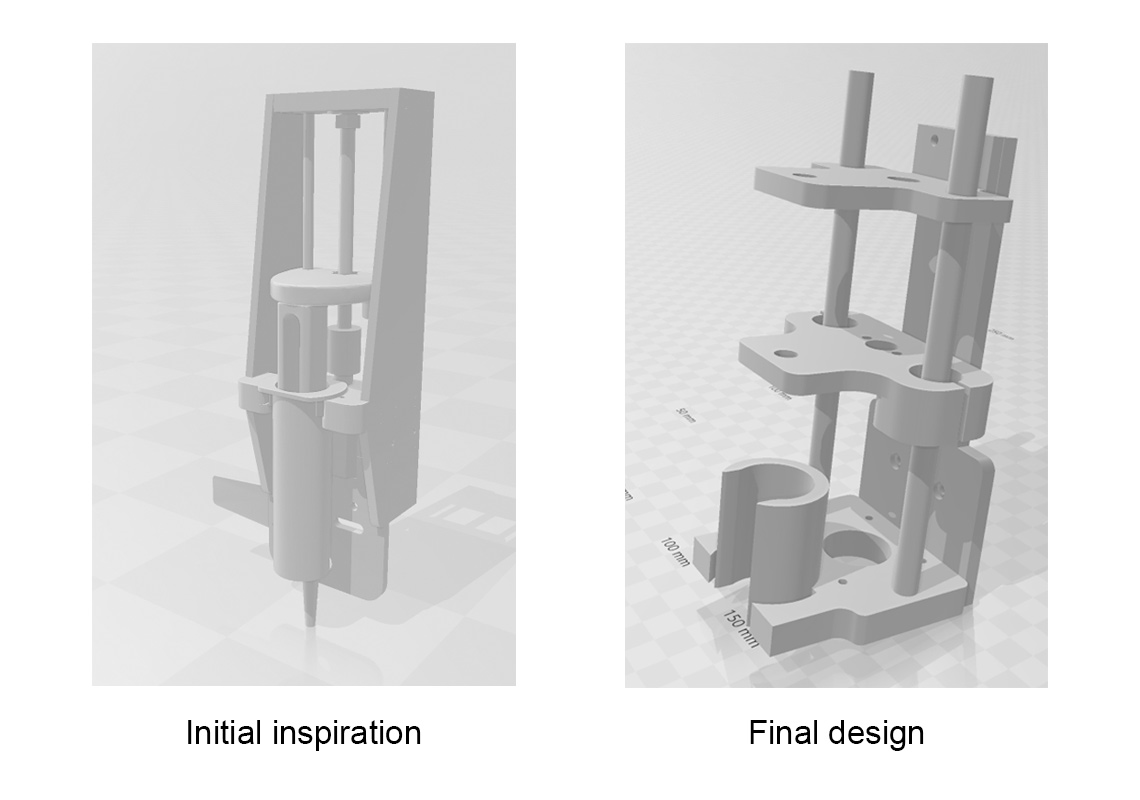
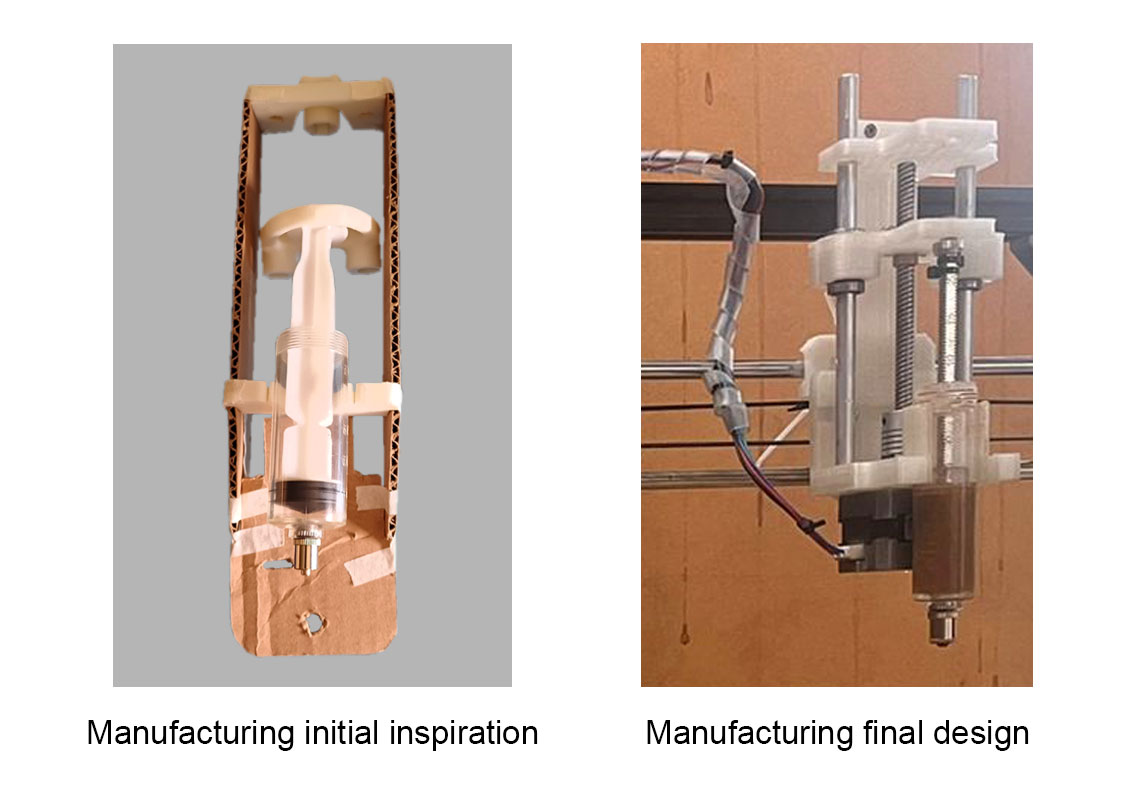
Designing and manufacturing PachamamaPrint extruder
In hindsight, the journey of designing PachamamaPrint was not without its obstacles. Despite our meticulous planning and attention to detail, we encountered unforeseen challenges along the way as described. However, each setback served as a learning opportunity, prompting us to reassess our approach and implement innovative solutions. Through perseverance and collaborative effort, we overcame adversity, ultimately realizing our vision of creating a transformative tool for promoting healthier eating habits and fostering a brighter future for our community.
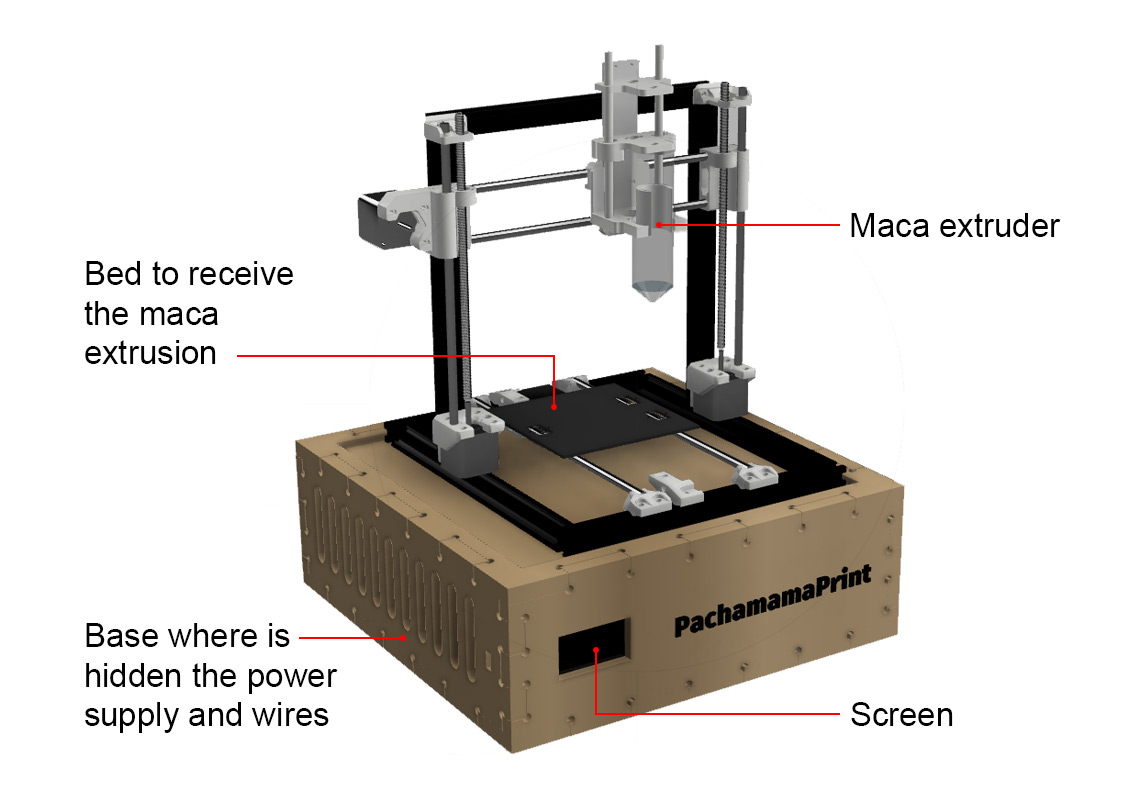
Final design of PachamamaPrint
Manufacturing
With the designs finalized, the next step was to bring them into the physical realm through 3D printing. Utilizing Ultimaker Cura slicer software, I prepared the digital models, generating the necessary G-codes to instruct the printer.
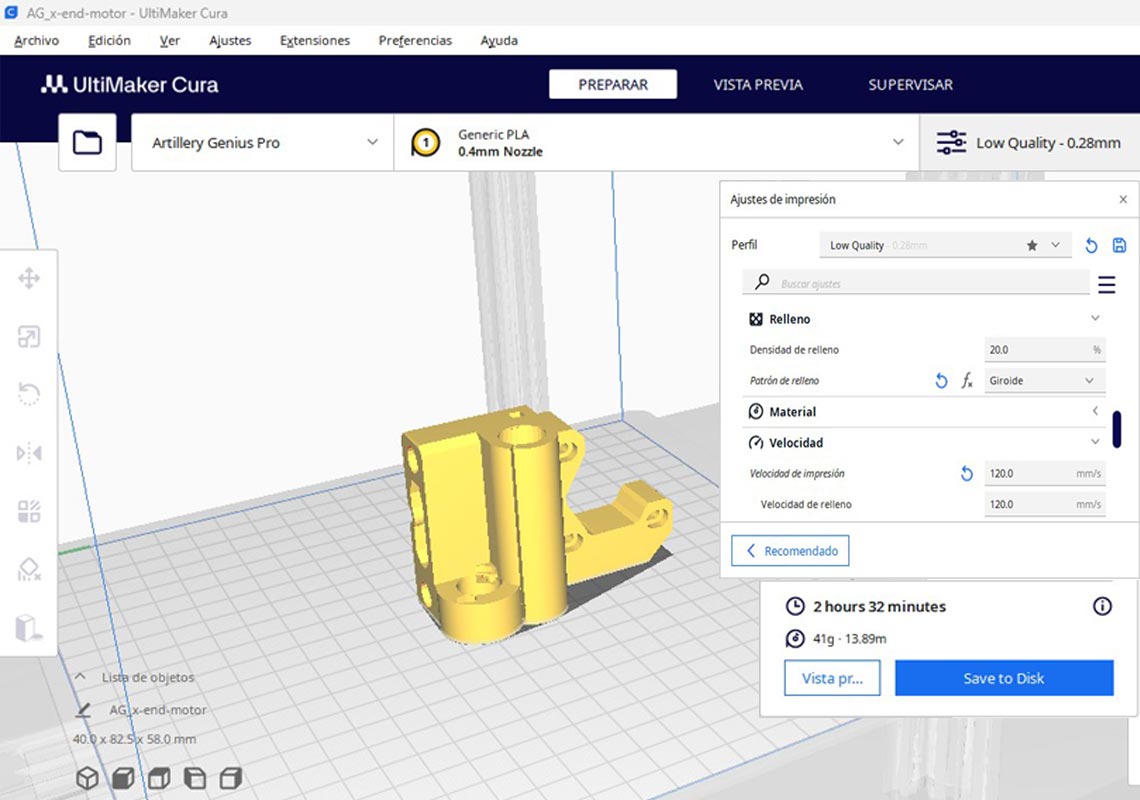
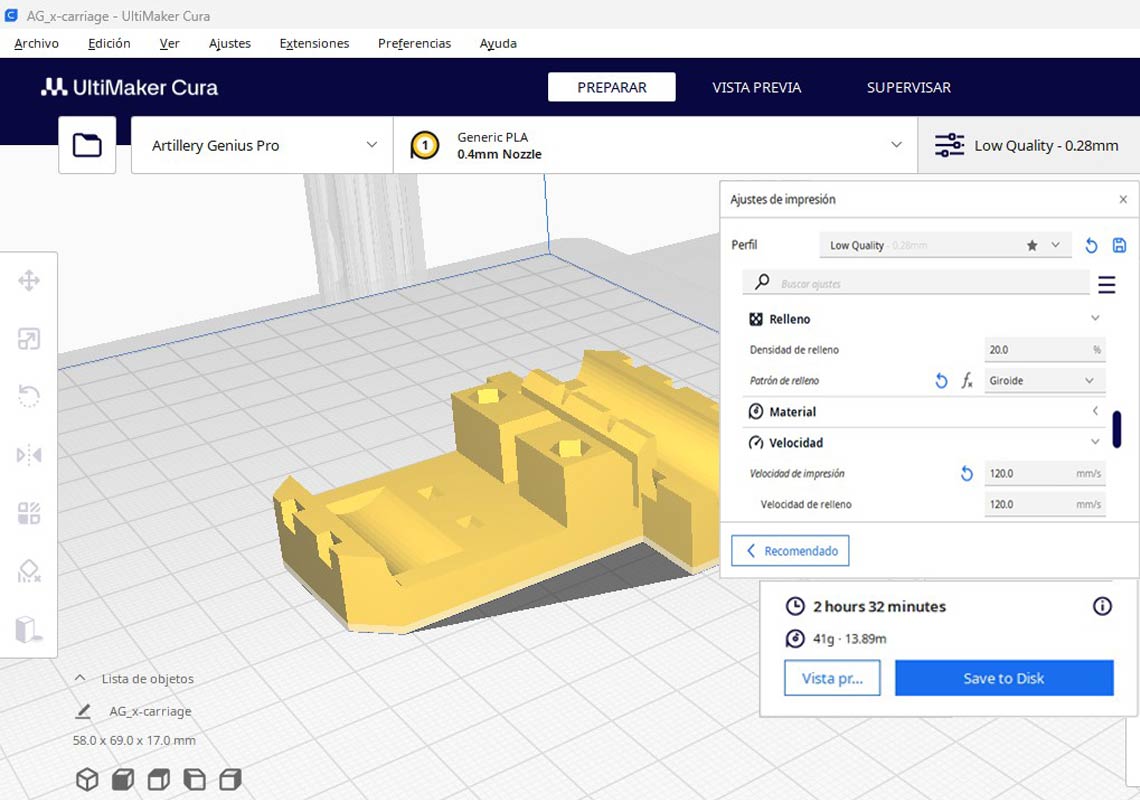
Machine pieces in Ultimaker Cura Slicer
Turning to the Artillery Genius Pro 3D printer, I carefully calibrated the settings and loaded white PLA filament, ensuring optimal print quality. Over the course of several printing sessions (almost a full day), the machine diligently fabricated each component.
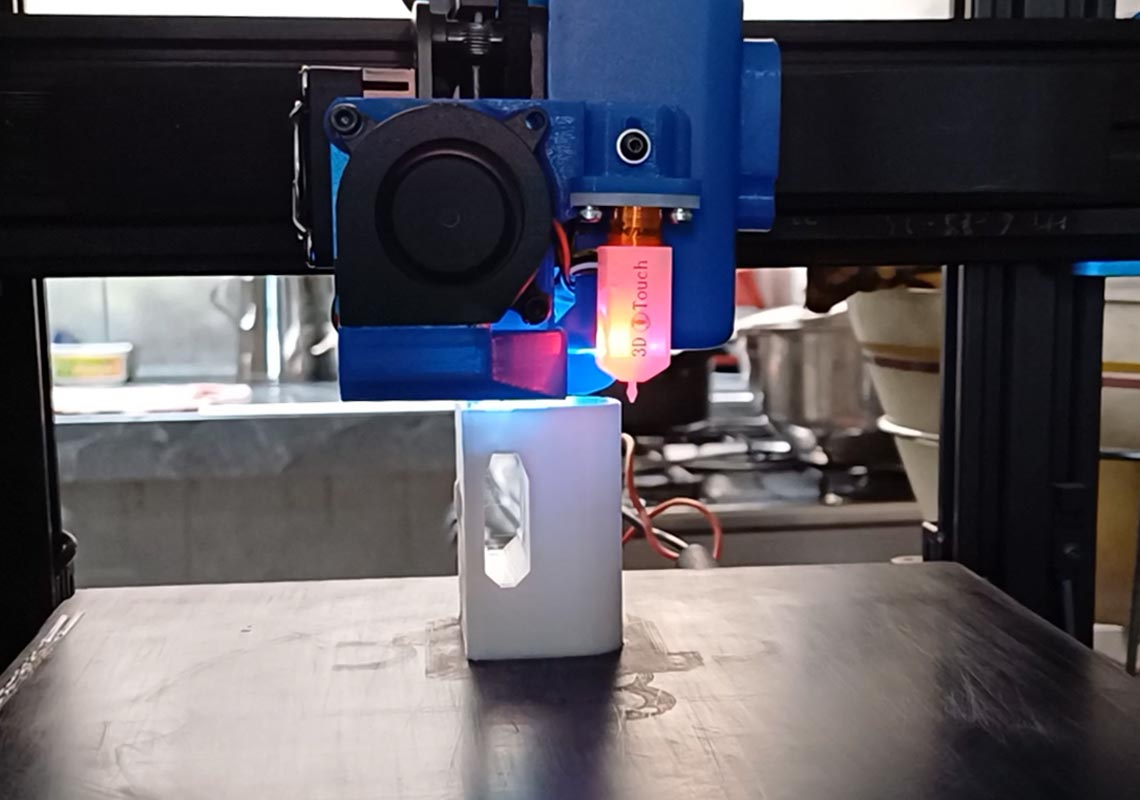
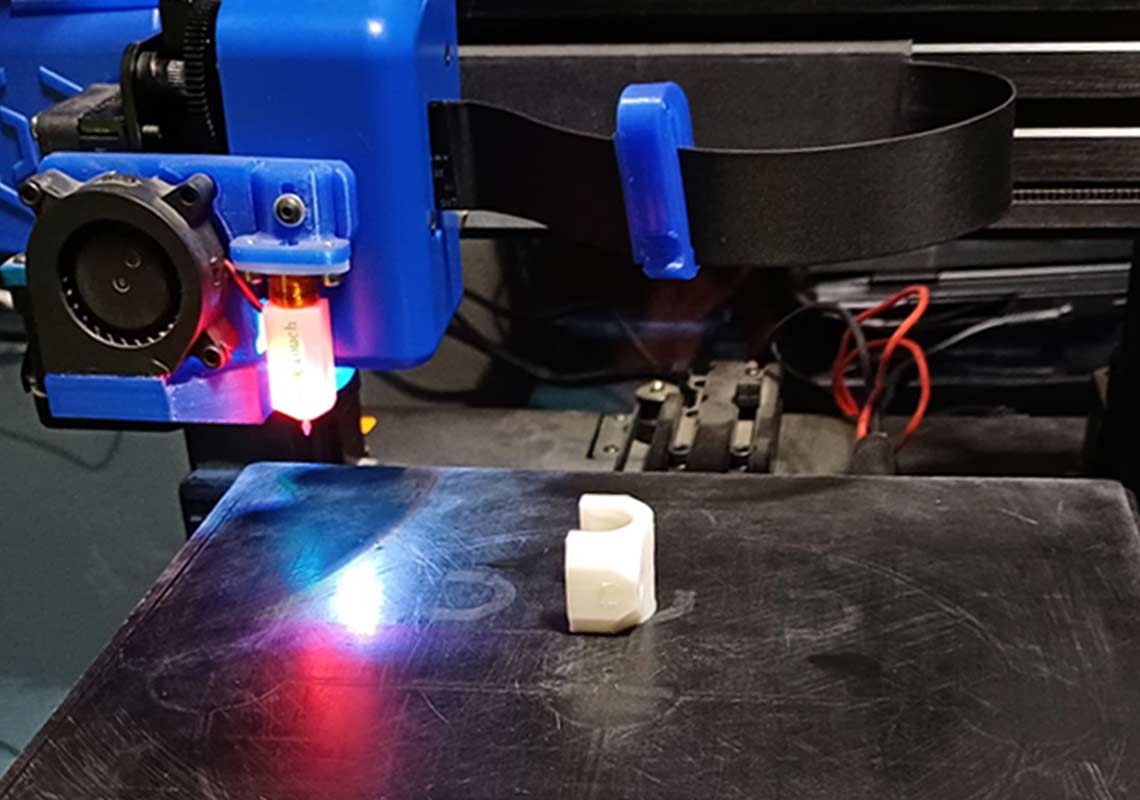
Machine pieces being 3D printed
Through constant monitoring and adjustment, I maintained strict quality control, striving for flawless execution in every print.
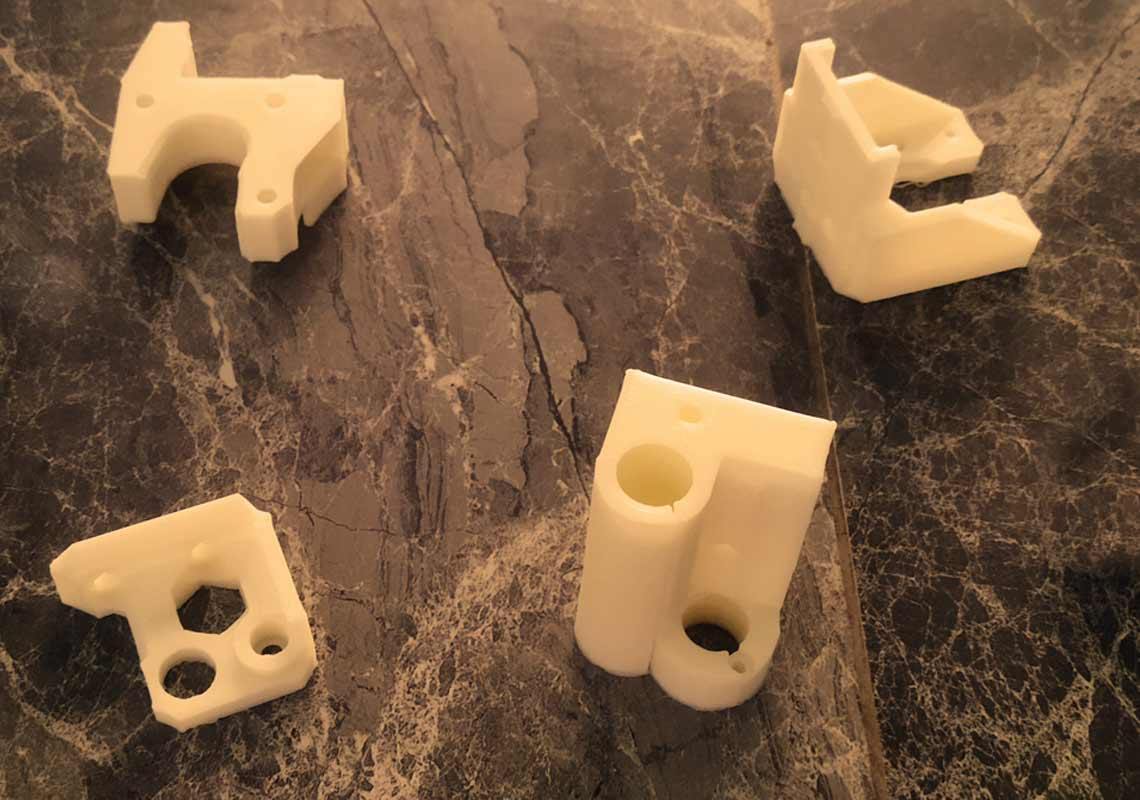
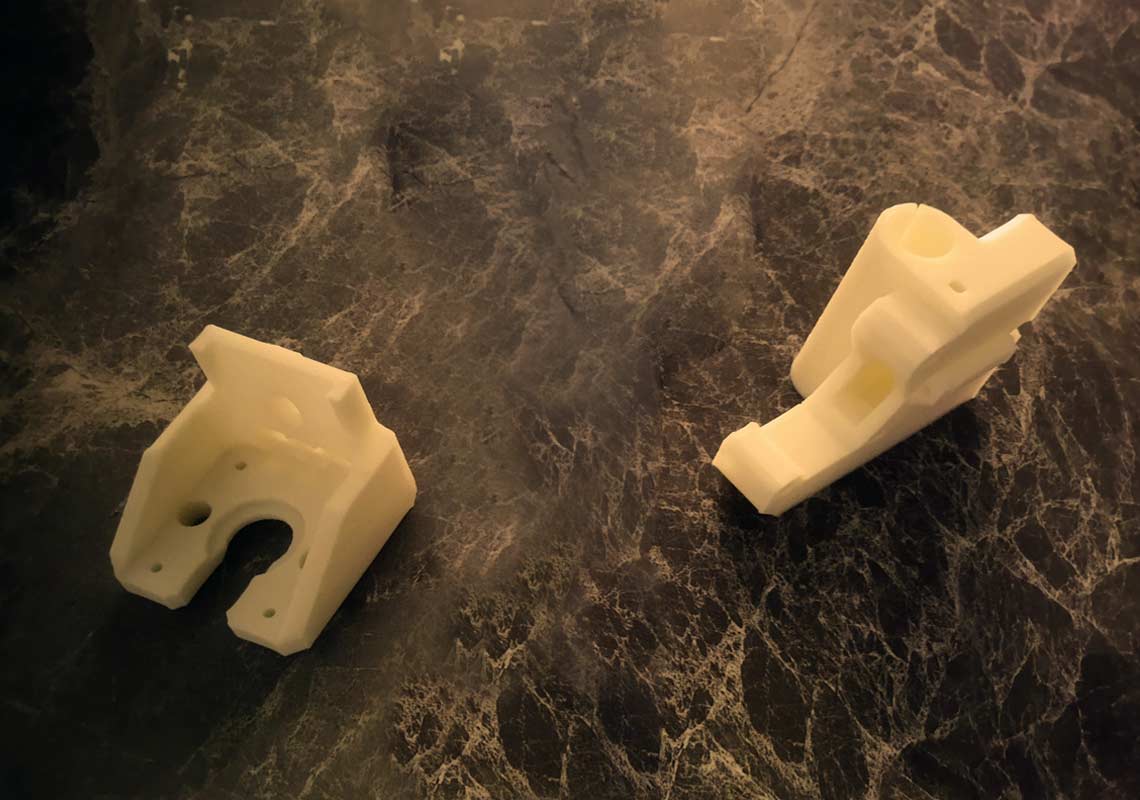
Printed pieces of PachamamaPrint
I did not manufactured a entire new structure because our team adopted a sustainable approach by repurposing components from a disused machine. Recognizing the value of recycling and minimizing waste, we meticulously salvaged and refurbished suitable parts, integrating them seamlessly into our design. This eco-conscious decision not only reduced our environmental footprint but also demonstrated our commitment to responsible machine building practices. By repurposing existing materials, we breathed new life into discarded components, transforming them into integral elements of PachamamaPrint, further embodying our ethos of innovation, sustainability, and community stewardship.
Conclusions
- The journey of building PachamamaPrint underscored the power of innovation and creativity in addressing complex challenges. By reimagining traditional ingredients -such as maca- and leveraging advanced technology, we crafted a solution that not only promotes healthier eating habits but also celebrates our cultural heritage.
- Our commitment to sustainability and responsibility guided every aspect of the project, from design to manufacturing. By repurposing existing materials and minimizing waste, we demonstrated our dedication to environmental stewardship, setting a precedent for responsible engineering practices.
- The success of PachamamaPrint was a testament to the strength of collaboration and teamwork. By harnessing the collective expertise and passion of our team members, we achieved synergy, fostering a dynamic environment where ideas flourished, and obstacles were overcome together.
- To finish this task I thank my fellow students and tutors, especially Vaneza Caycho, Roberto Delgado for the guidance in this process, Ronal Vilca, Silvana Espinoza, Renson Samaniego, and Wilber Giron.