"Hi everyone ,Week 16 Wild card week.
- Design and produce something with a digital fabrication process (incorporating computer-aided design and manufacturing) not covered in another assignment, documenting the requirements that your assignment meets, and including everything necessary to reproduce it. Possibilities include (but are not limited to):
Individual assignment
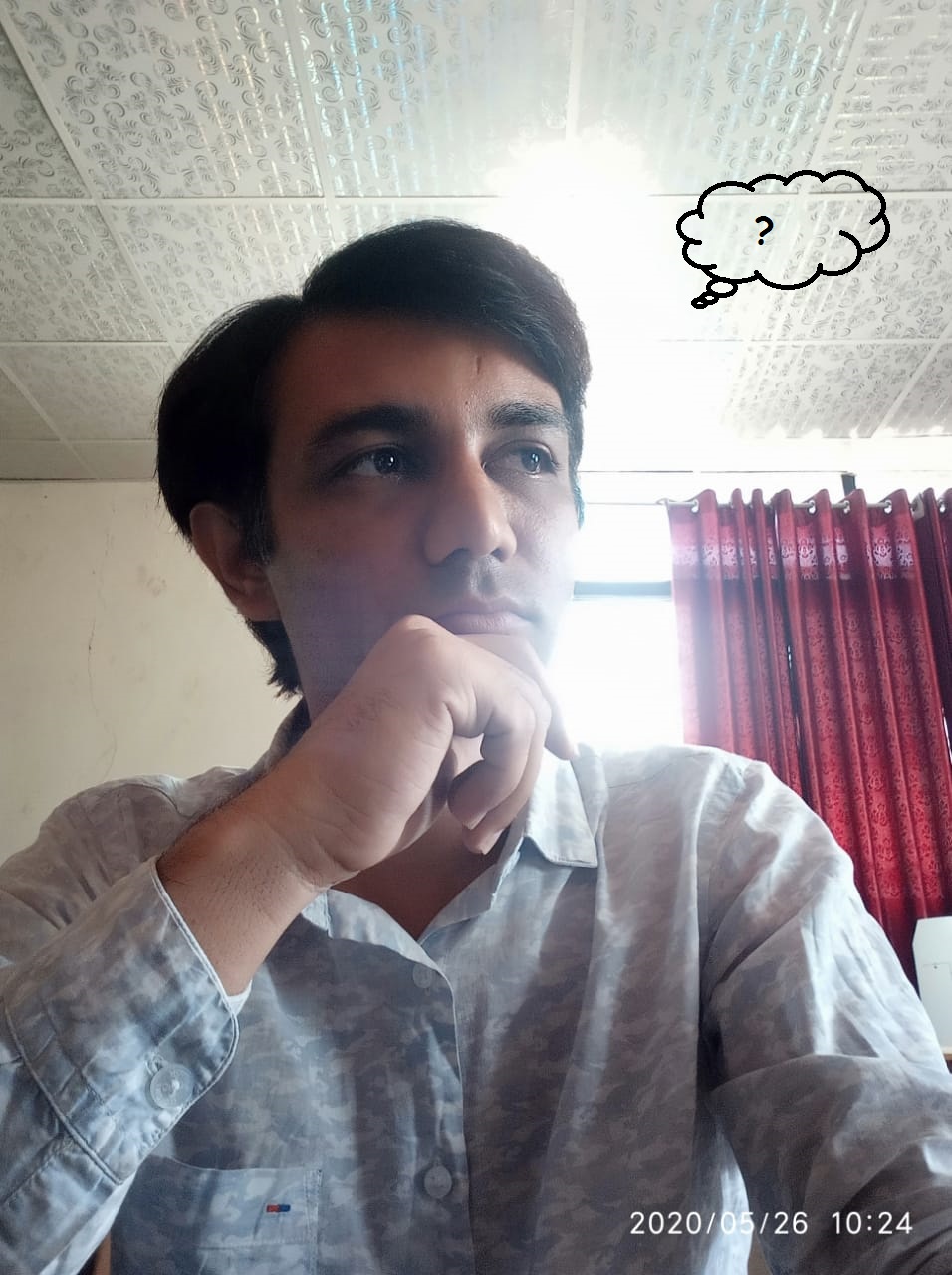
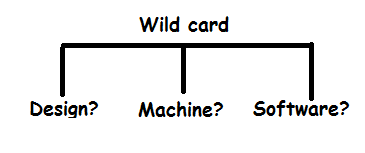
While thinking about wild card week what should i design? which machine and software we should used?.When i was thinking over this i got an idea which i didnt tried yet.So i decided to take this idea to explore more, this wild card week.
Since in last 14-15 weeks ,i went through different assignments and exploring different ideas but during this time lots of ideas came and some of them i worked amd others were left.But one of the idea which i wish i could exercise that makes me realy happy.The ideas was to design and make Table lamp and one moobile stand which we usyally found in our day to day life.To explore these two idea wild cardweek is better options for me.
Design
Table Lamp
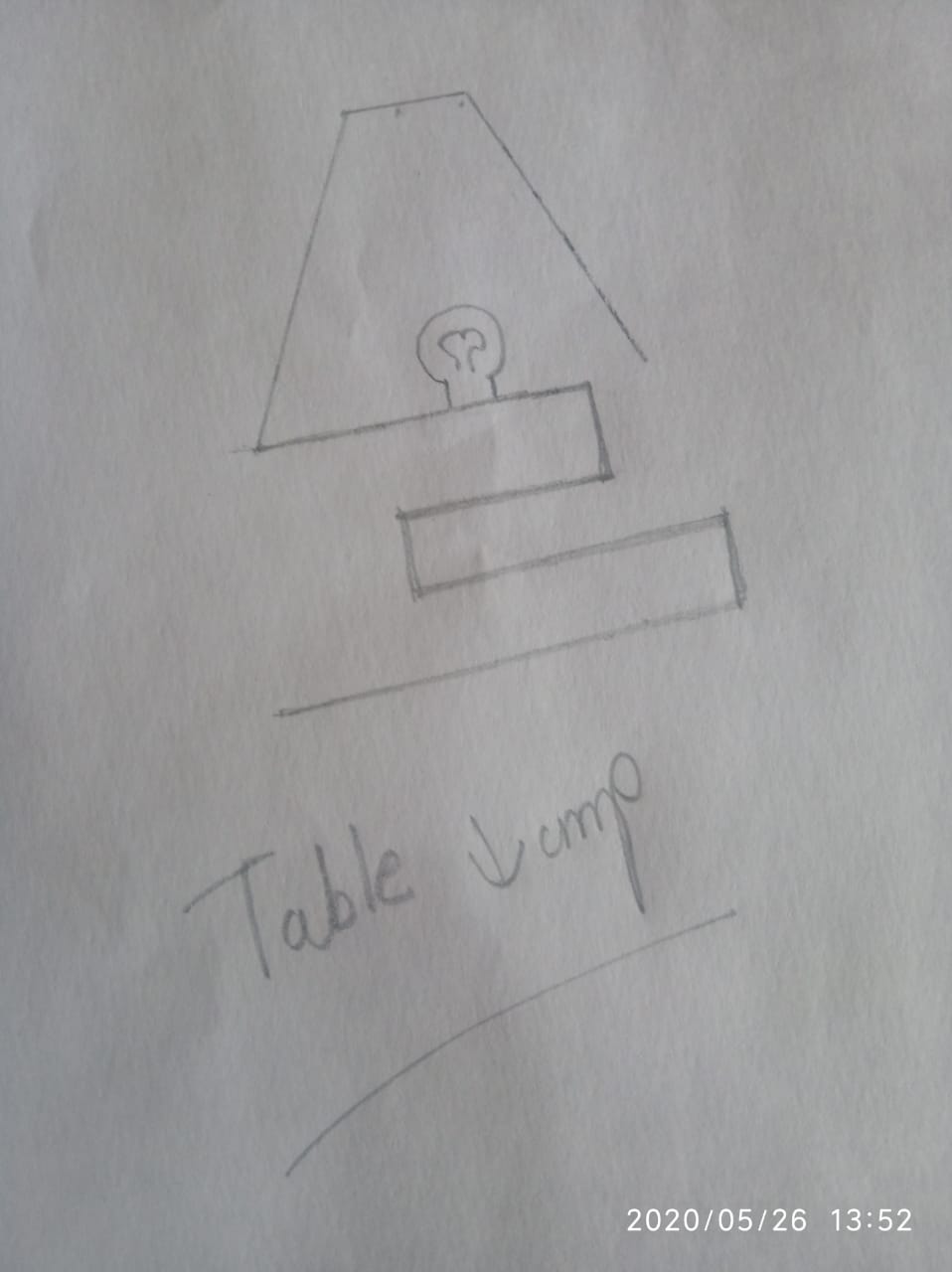
This is what actually i am talking about.i.e.Table lamp.I want this kind of Table lamp at my home as well.There are so many design of table lamp availables but while designing mine i took care of my problems which i faced quite.Accordingly i make certain changes in the design.So i hope i will make it happen.
Mobile stand
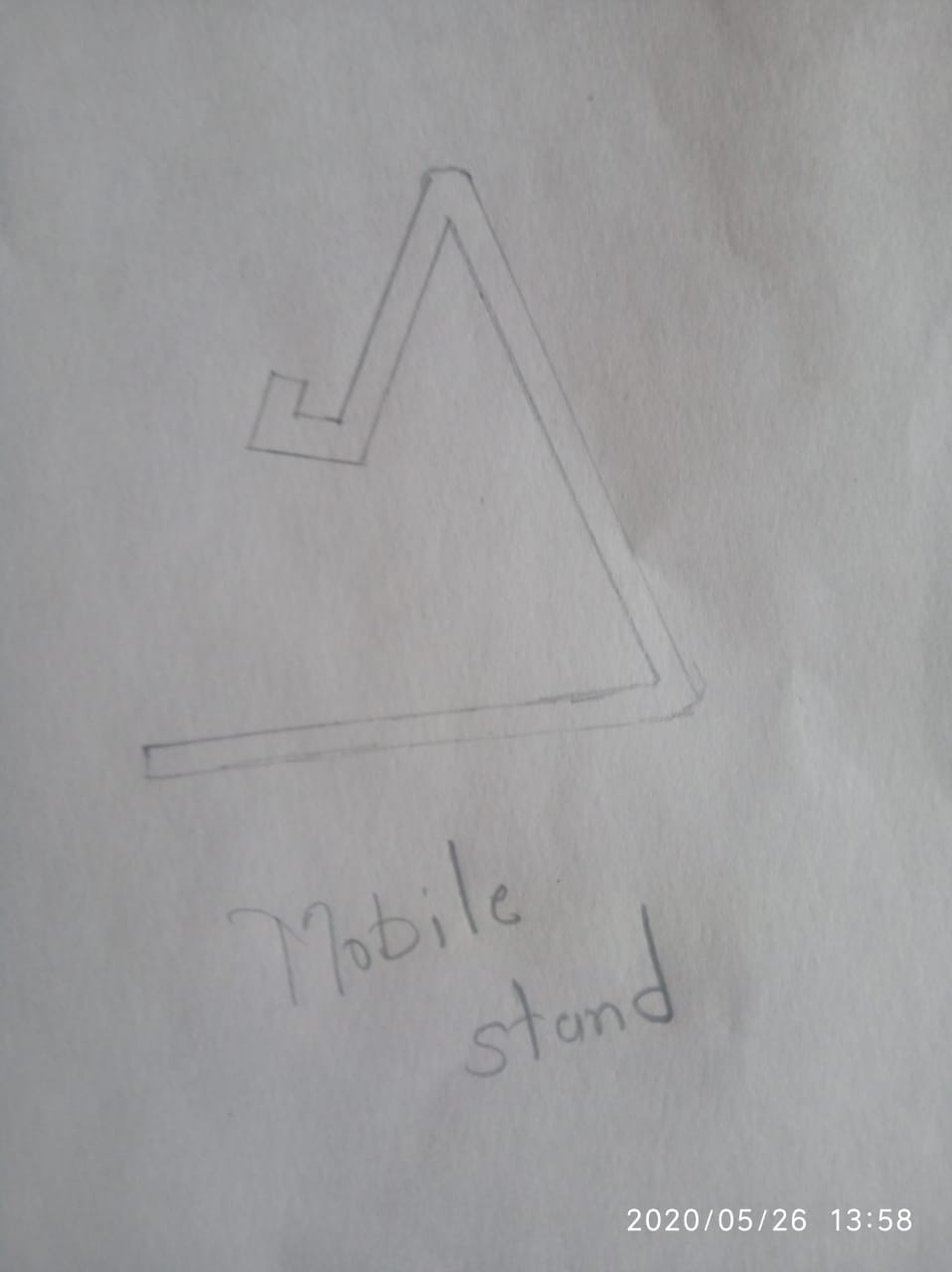
This is a mobile stand which i wish everybody wanted to have with them.Idea is simple but simple ideas always make big impact.As we used for differnt purposes like video call meeting or to watch movie.So in both situation we cant hold a mobile for a hours so its better to have a stand to hold a mobile .So its is quite usefull for most of us.
Machine & Software
Plasma cutter
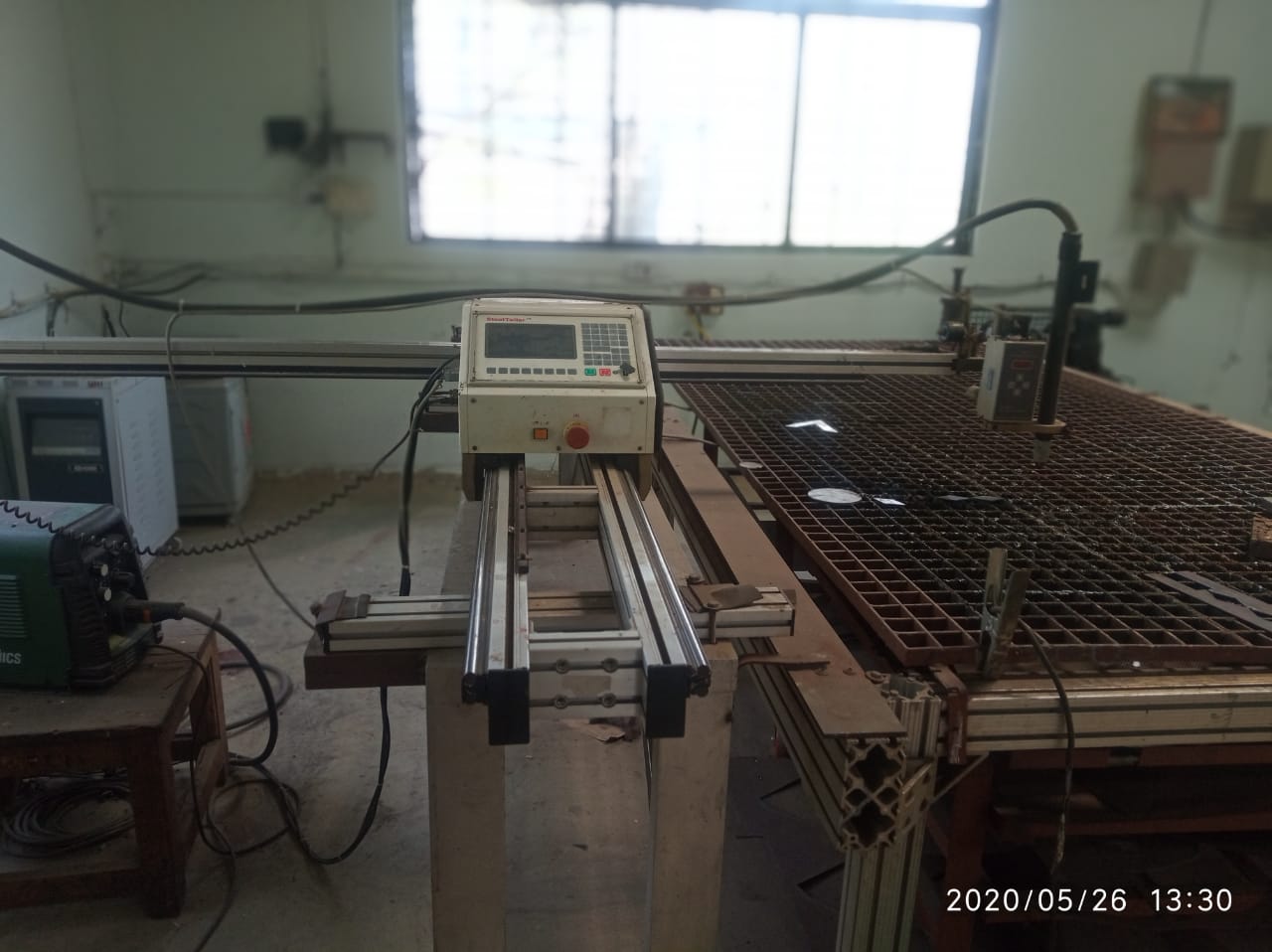
Solid work
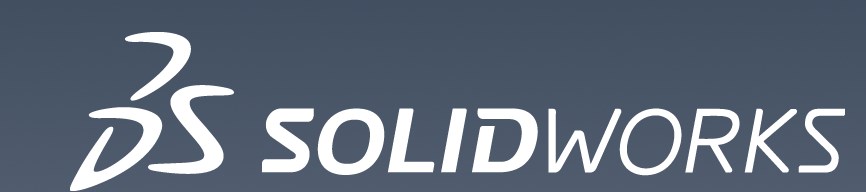
After i figured out above now i am ready to work on these.So first i am going to design above sketch in solidwork,then used Fastcam to generate g-code and then used this g-code to run plasma cutter to cut my design.So i catagories my steps as below.
Step 1.Table lamp design in solid work
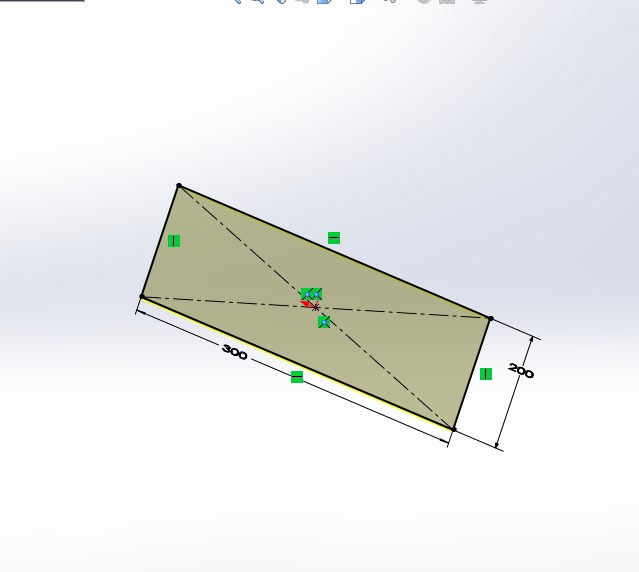
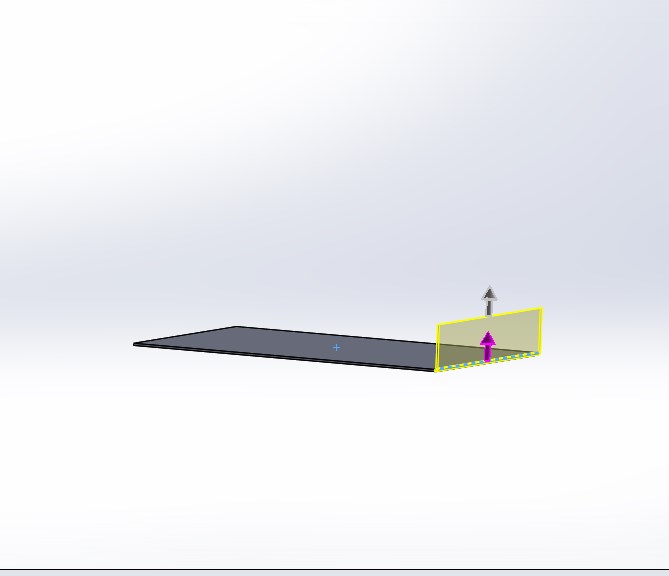
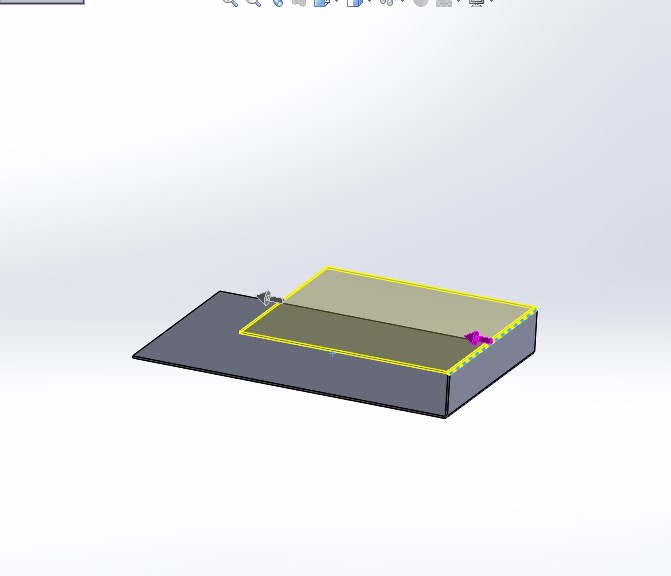
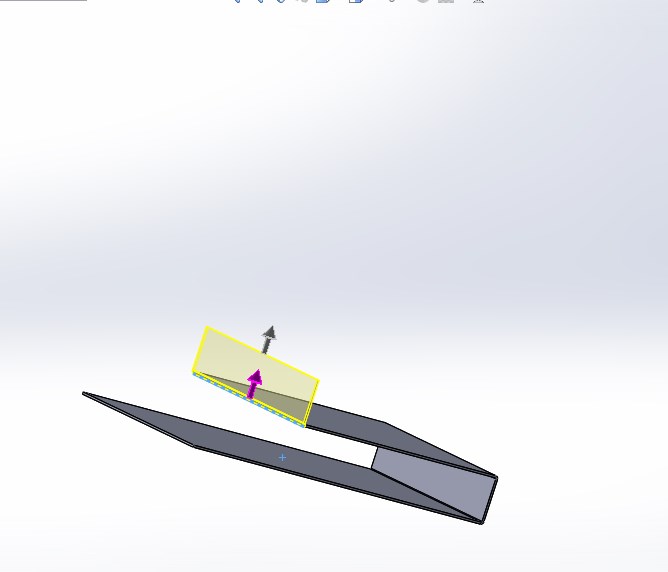
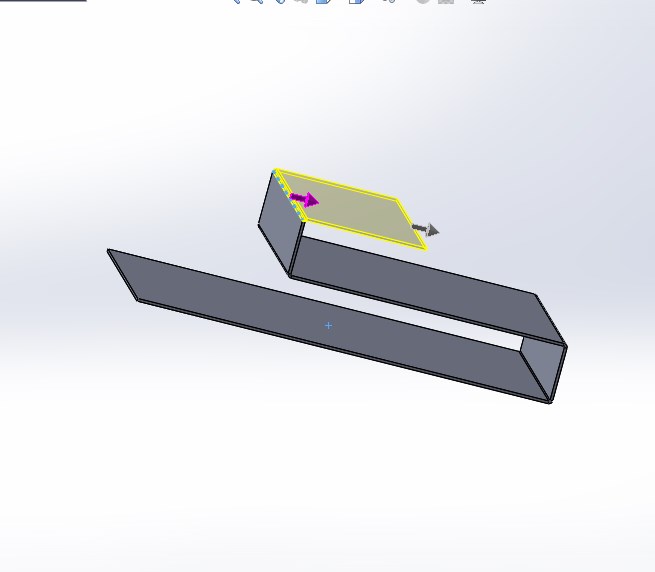
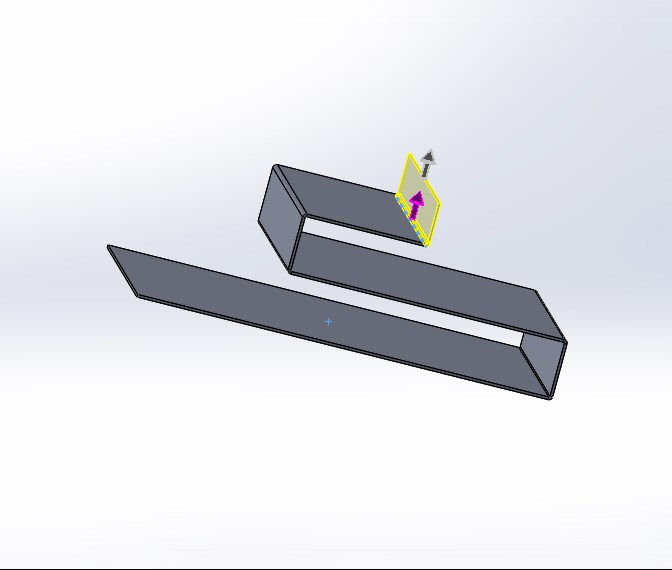
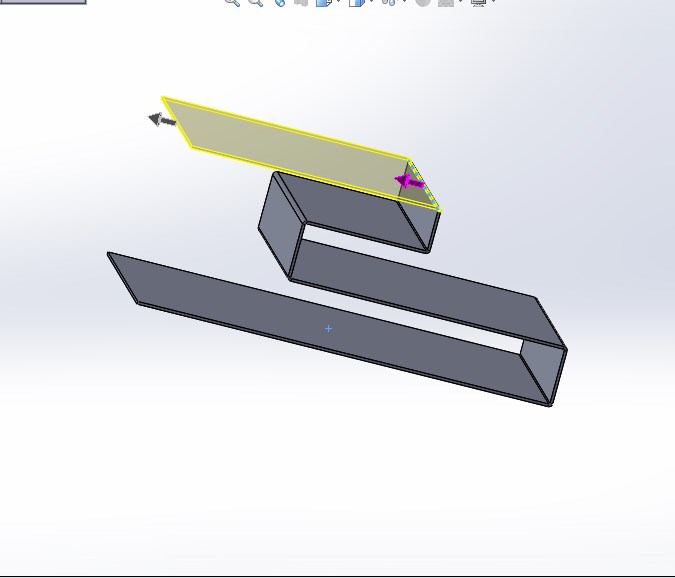
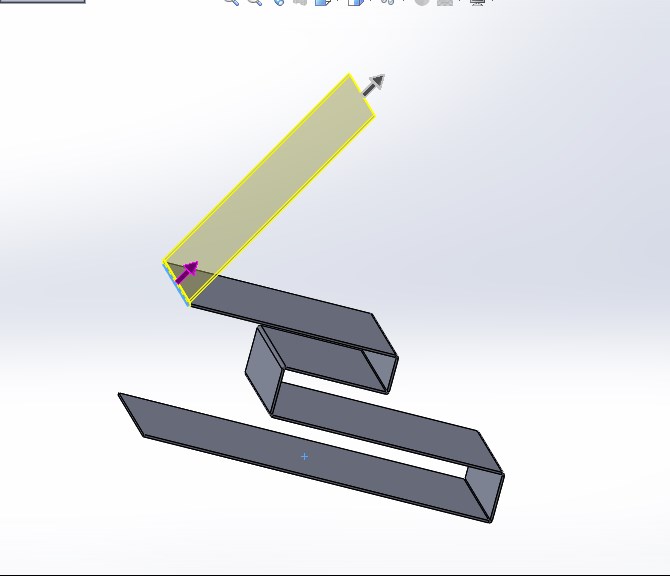
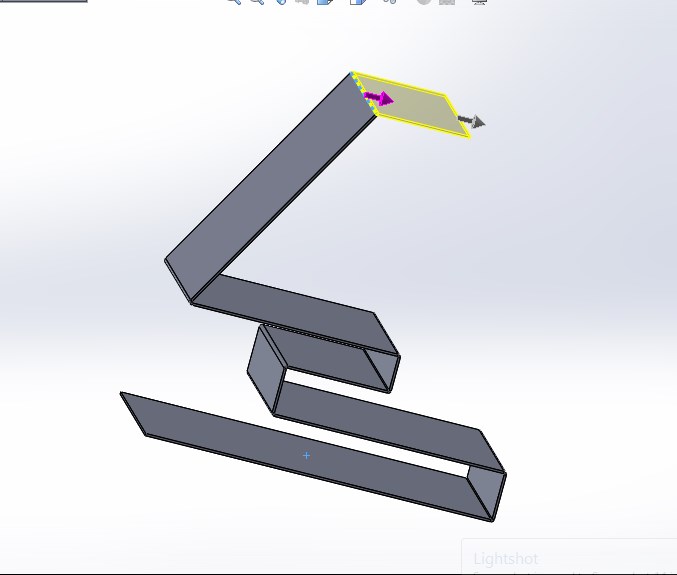
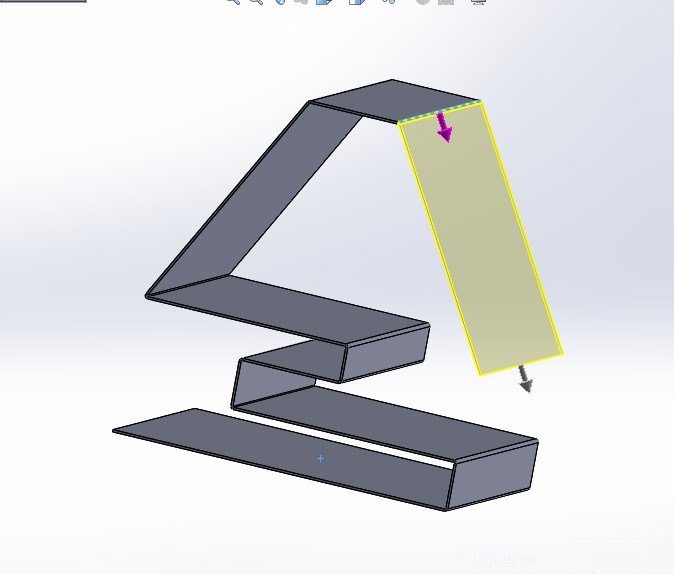
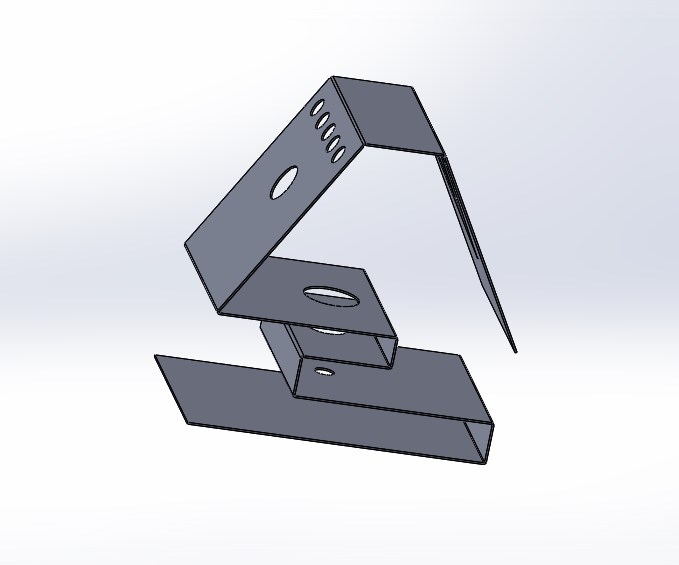
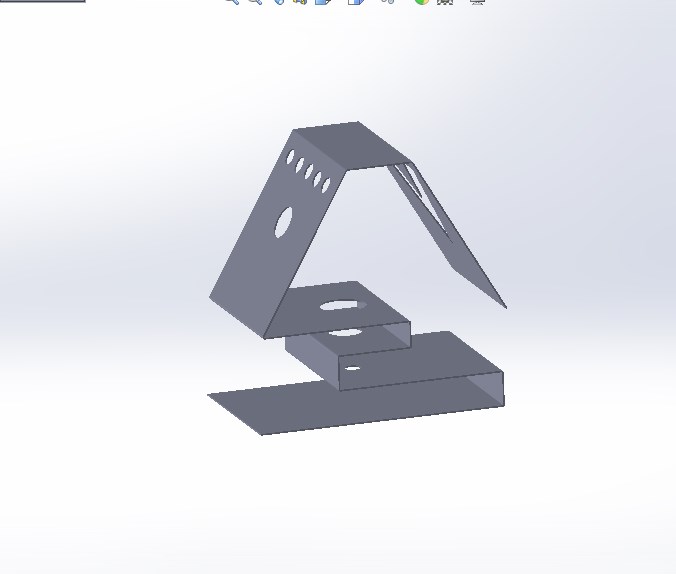
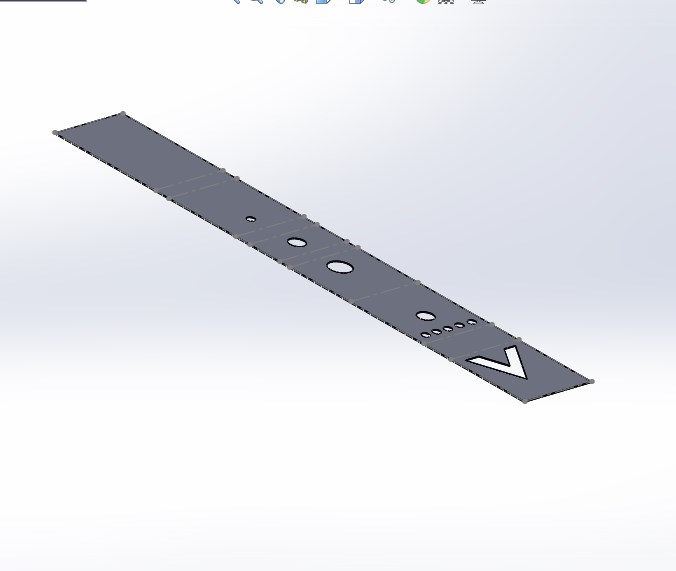
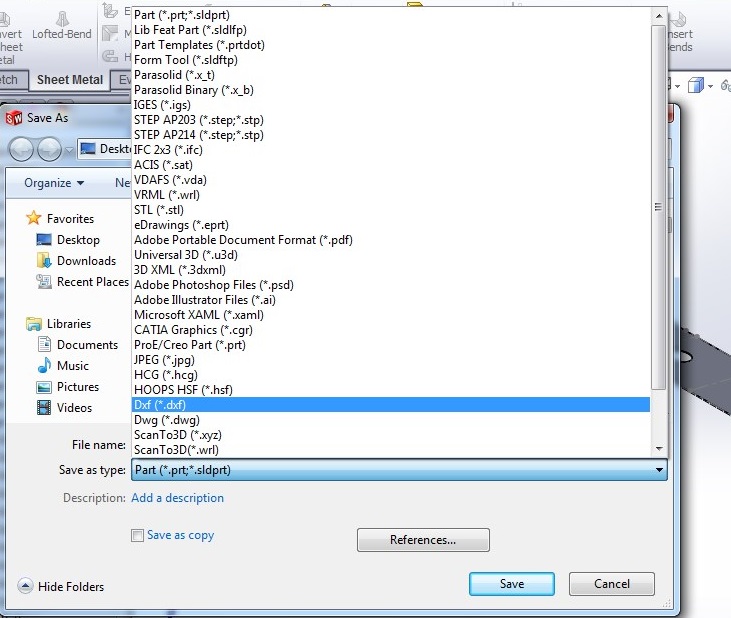
Step 2.Procedure to Convert DXF file into .TXT file
Once i am ready with dxf file which is generated using solid work software now its time to convert this dxf file into g-code.For that i am using Fast CAM software which will do this task.The procedure to operate FastCAM software is given in video.
Step 3.Cutting sheet metal on plasma machine
About plasma cutting machine
The plasma cutter machine which we are having in our Fab lab is Smart IIporable table CNC cutting machine.Basically this machine based on F4 concepts i.e.Friendly in transportation, frieindly in installation ,firindly in operation,friendly in maintenance.The cutting area is 1500 x 3000mm and table structures are more precision.This is a dual drive system,taht can handle more weight.This machine comes with high precision dual shaft linear guide
plasma cutting machine parameters
Type | Smart II plasma cutting machine |
Input voltage | 110/220 V |
Input Frequency | 60/50 Hz |
Input power | 200 W |
Controller | LCD 7 ˝ color screen controller ( remote control is optional) |
Effective cutting range | 1500 (crosswise) X 3000 (lengthways) mm |
Max cutting speed | 4000 mm / min |
Cutting thickness | Plasma cutting: depends on plasma power |
Cutting mode | plasma |
Cutting software | FastCAM |
Cutting mode | plasma |
How plasma cutter machine works
Plasma cutting is a process in which electrically conductive materials are cut through by means of an accelerated jet of hot plasma. Typical materials that can be cut with a plasma torch are steel, stainless steel, aluminium, brass, copper and other conductive metals
Take a Hands on the plasma cutter machine
Now its time interact with machine and test it, understand different parameters as i mentioned above.So our operator helped me to understand these parameters of this big machine.I have given detailed below:
Points to be discussed with machine operator
Me:What type of material is ?
Operator:Its a metal sheet of "CRCA".
Me:What is CRCA?
Operator:Its a Cold roll closed annealed".Its a method of treating steel below its recrystallization temprature.Due to this method we will get a thickness of material uniform.Also the material get hardened
Me:What amount carbon is in material we used?
Operator:The carbon content is moderate
Me:What is thickness of metal sheet which we will be using?
Operator:0.8mm for sure
Me:What is the air pressure we set?
Operator:The air pressure is 7 bar
Me:What is current we set for 0.8mm sheet?
Operator:We set a generator current to 25A
Me:What about the voltage for generator?
Operator:Its 320v three phase supply
Me:Can you tell me about the Nozzle Selection?
Operator:The nozzles number should match with
Cutting process
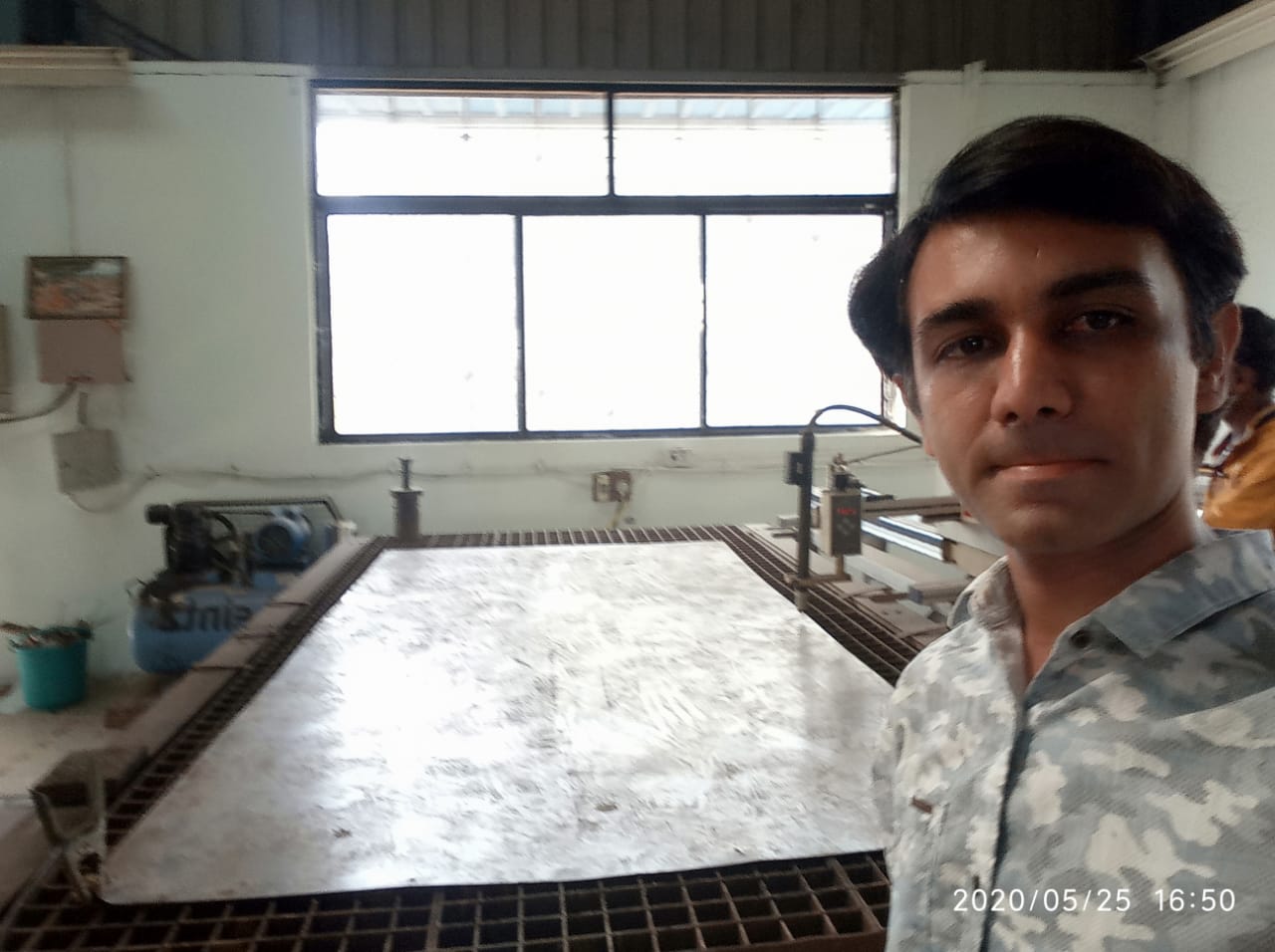
When i entered into The operator whoh gave us idea about plasma cutter and its explain different parametaers.So after understanding the different parameters of plasma , now i am ready to run plasma cutter.So first i put mild metal sheet on the plasma platform.
Now i am ready to upload g-code into plasma cutter machine.I have attach procedural video of it.After doing initial settings ,i had taken dry run test just to ensure whether it takes proper path or not.
During interaction with instructor i came to know that kerf for the plasma is very very small if you looking for a biggerstructure.On the other hand in laser cutter i need to take care of kerf value.
But still i need to make sure for that i just test 100mm x 100 mm square design and check the what exactly the value of kerf.In the side image you can see the value of kerf for plasma is around 1.26mm which is very very small.
Parameters | Value |
Air pressure | 7 Bar |
Current | 25A |
Kerf | 1mm |
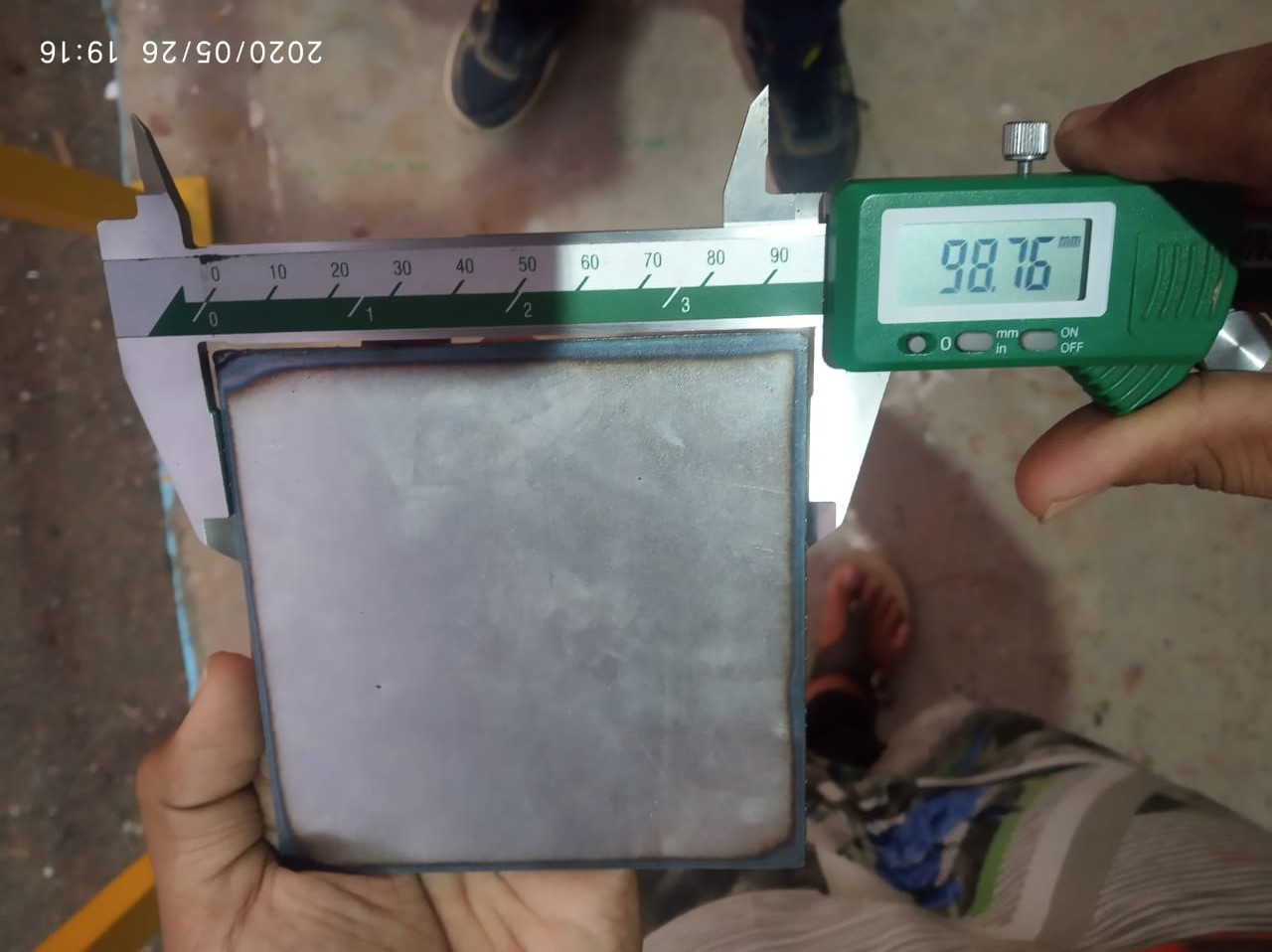
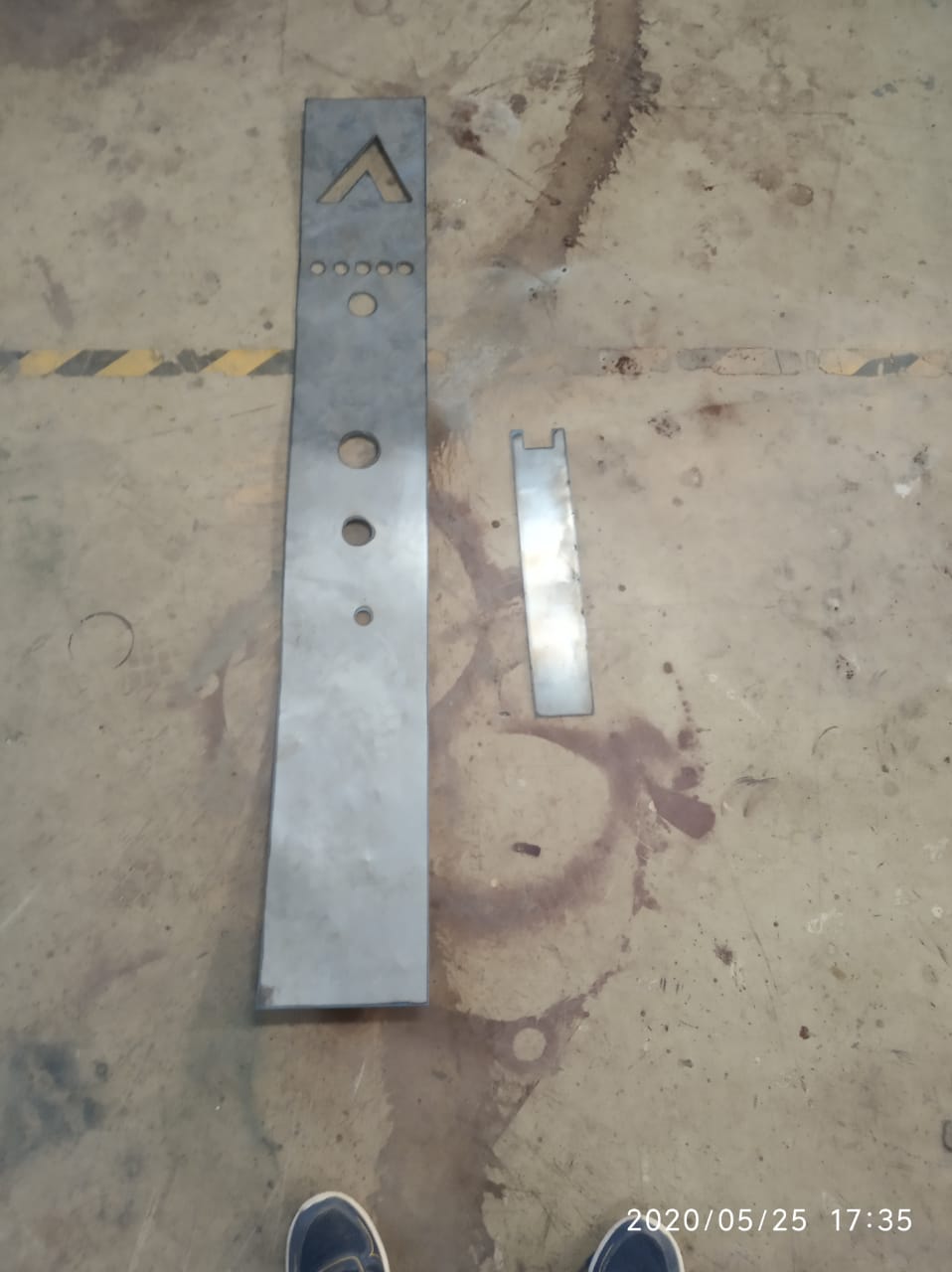
These are my cutting flattend sheets.Now i need to bend it using bending machine considering metal sheet doesnt bend too much and it should maintain shape.
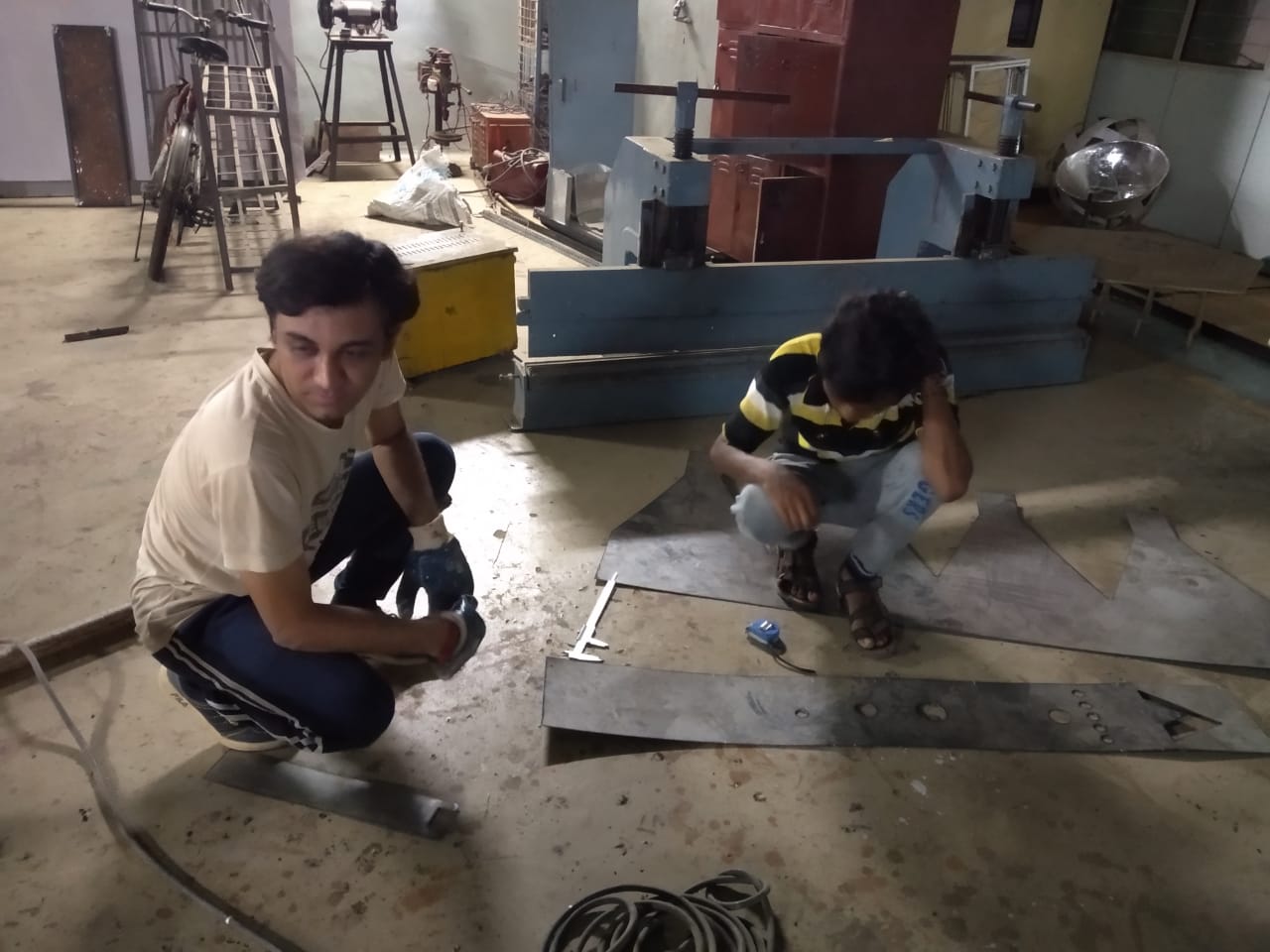
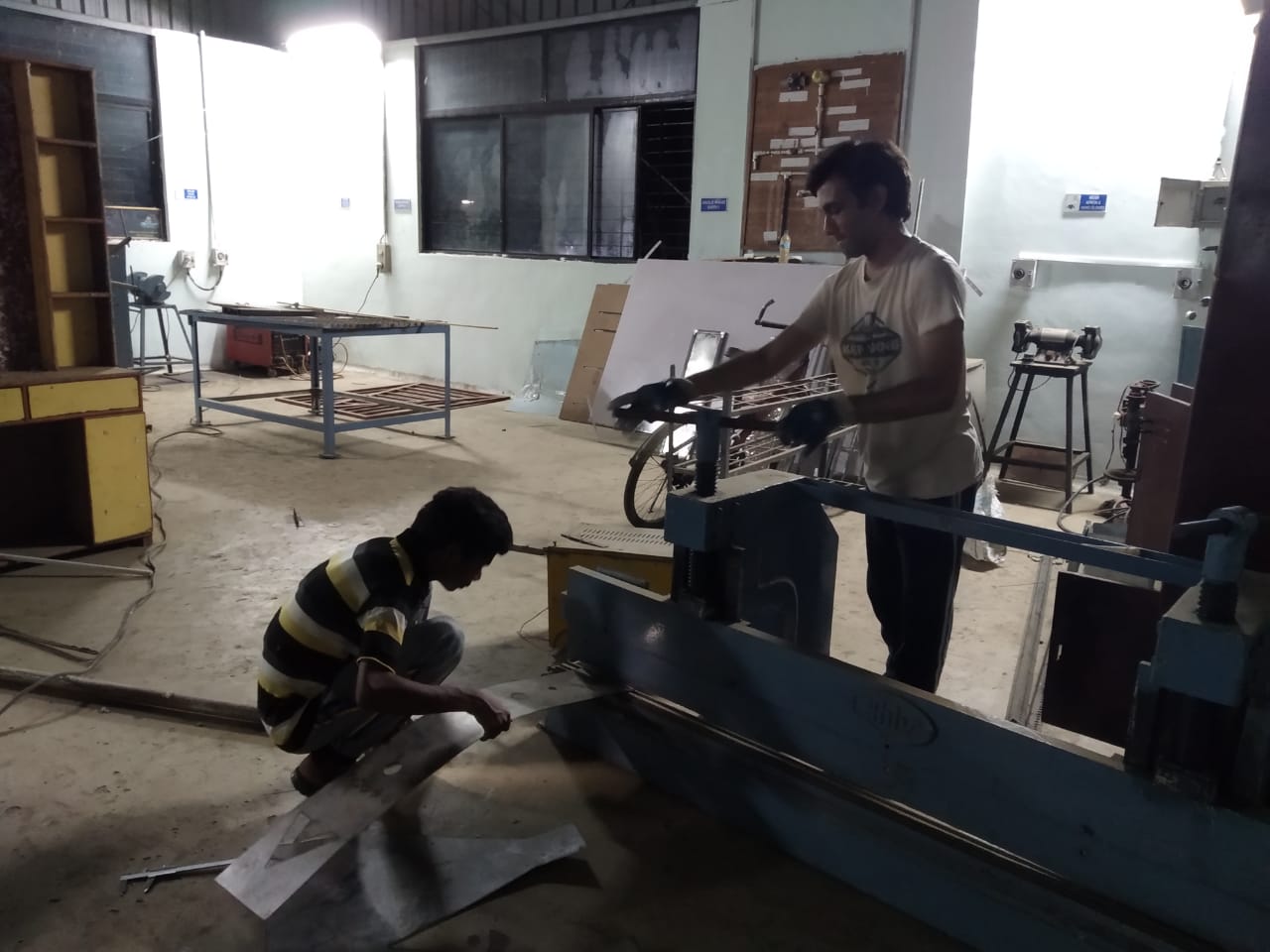
Gallery
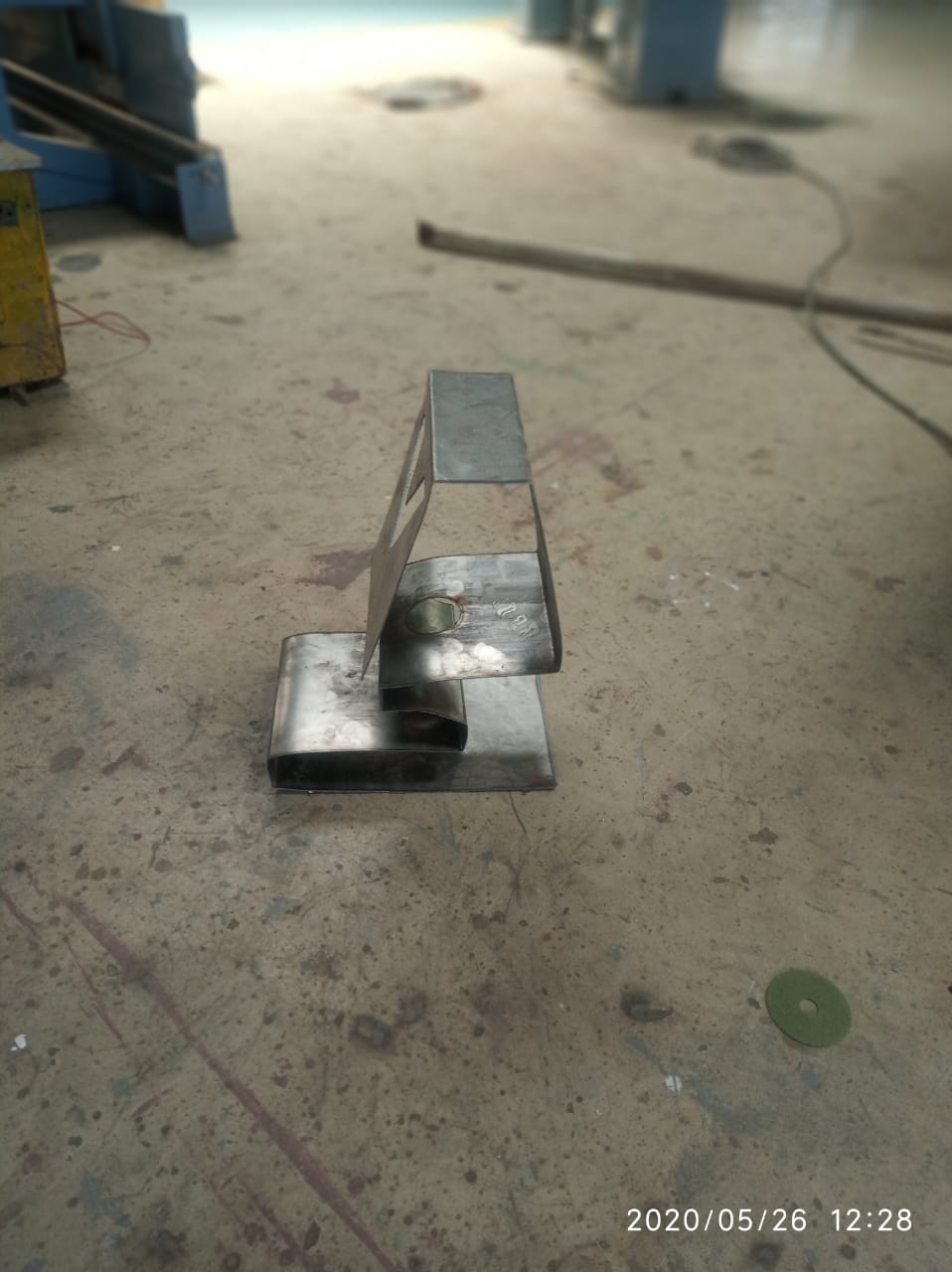
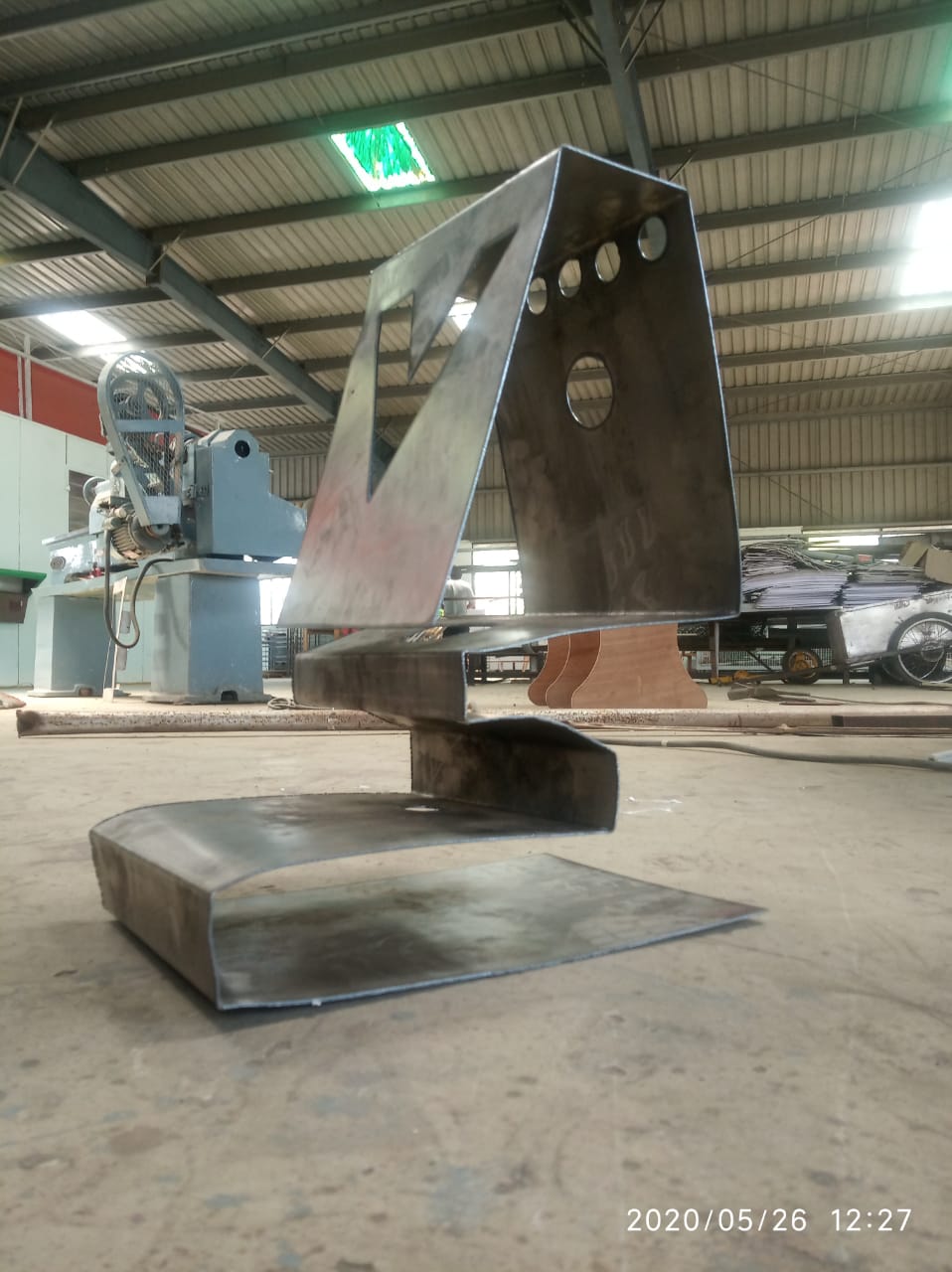
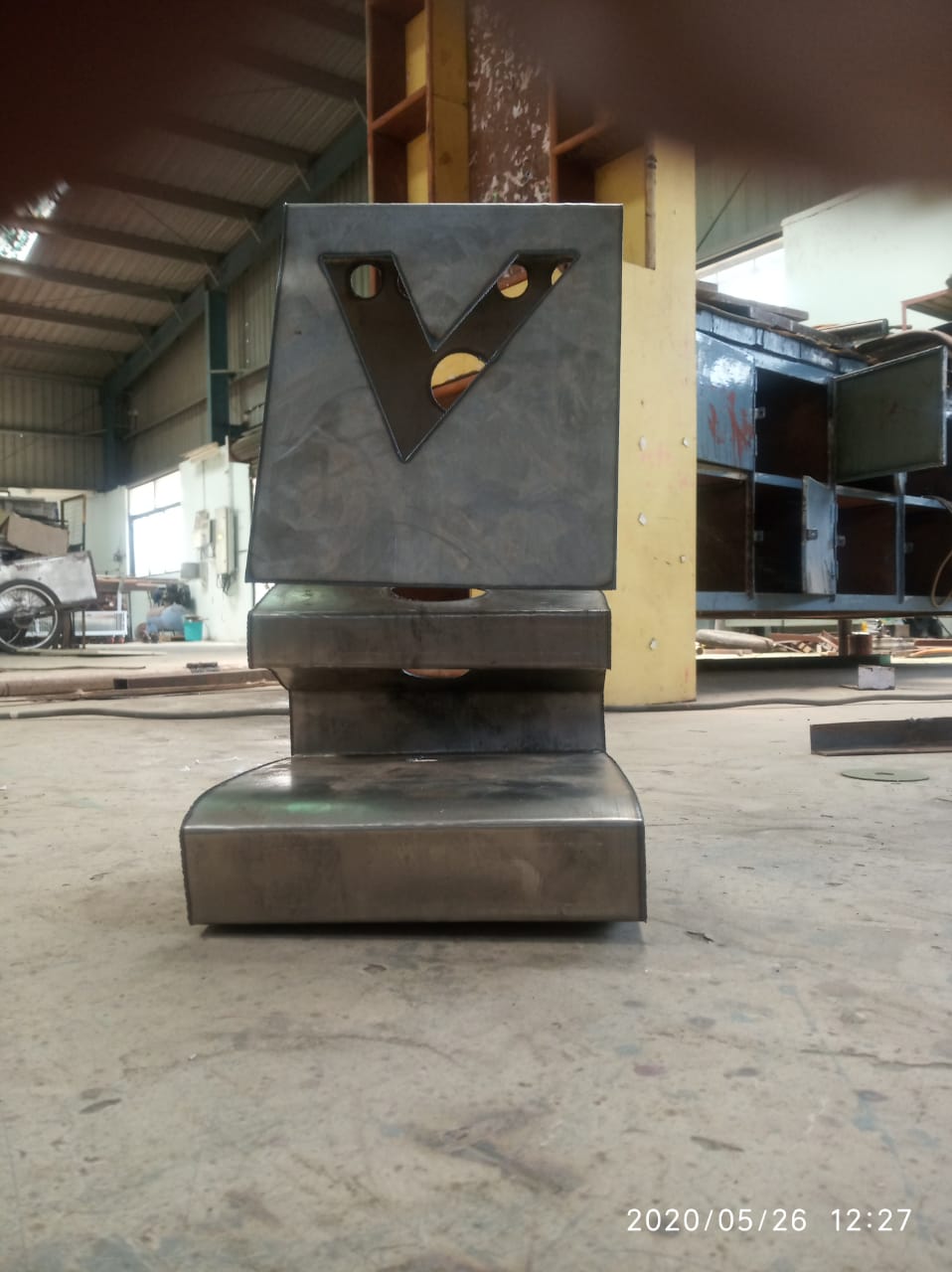
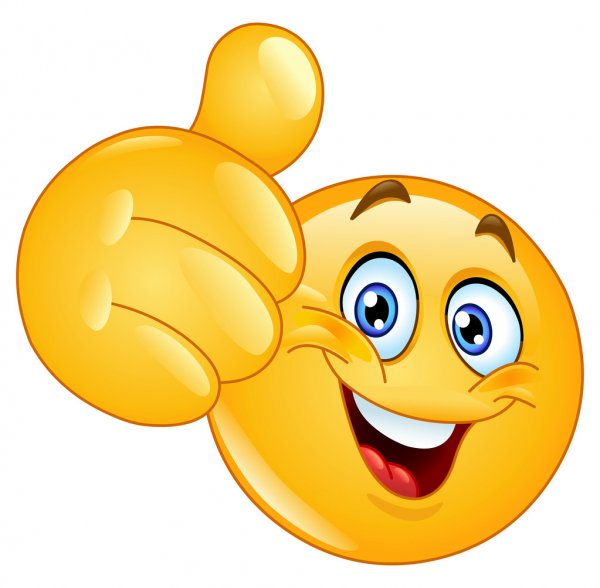
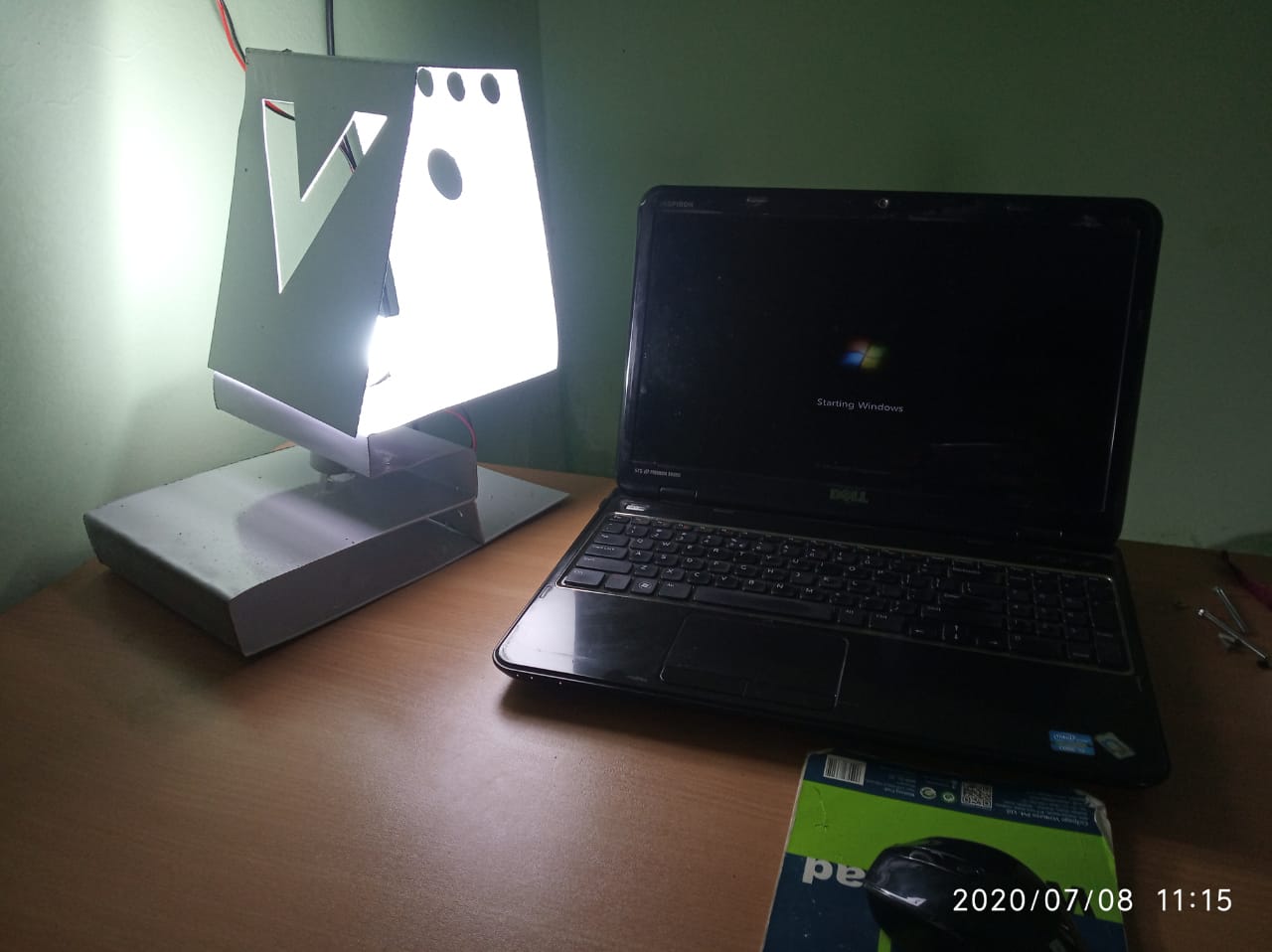
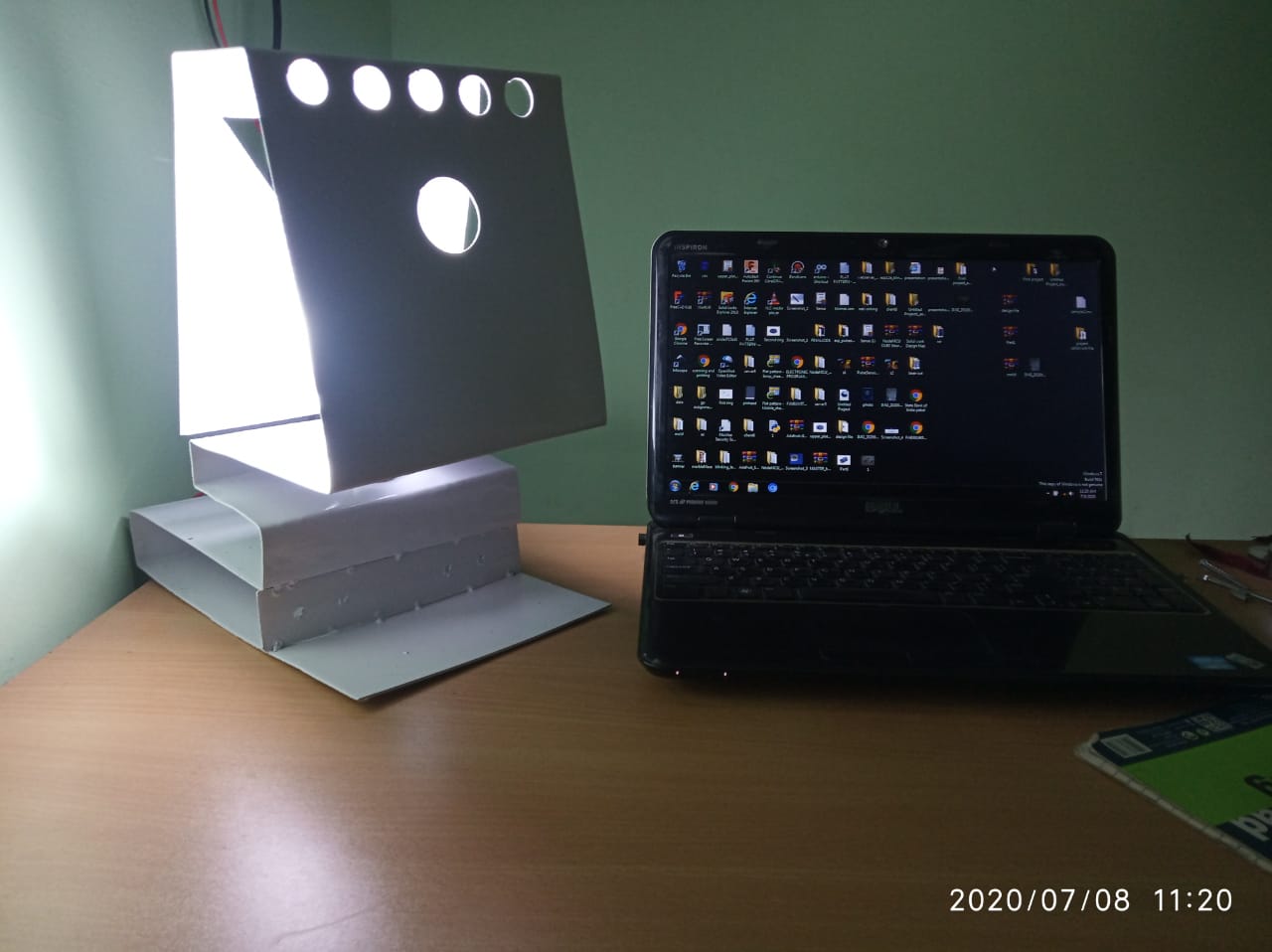
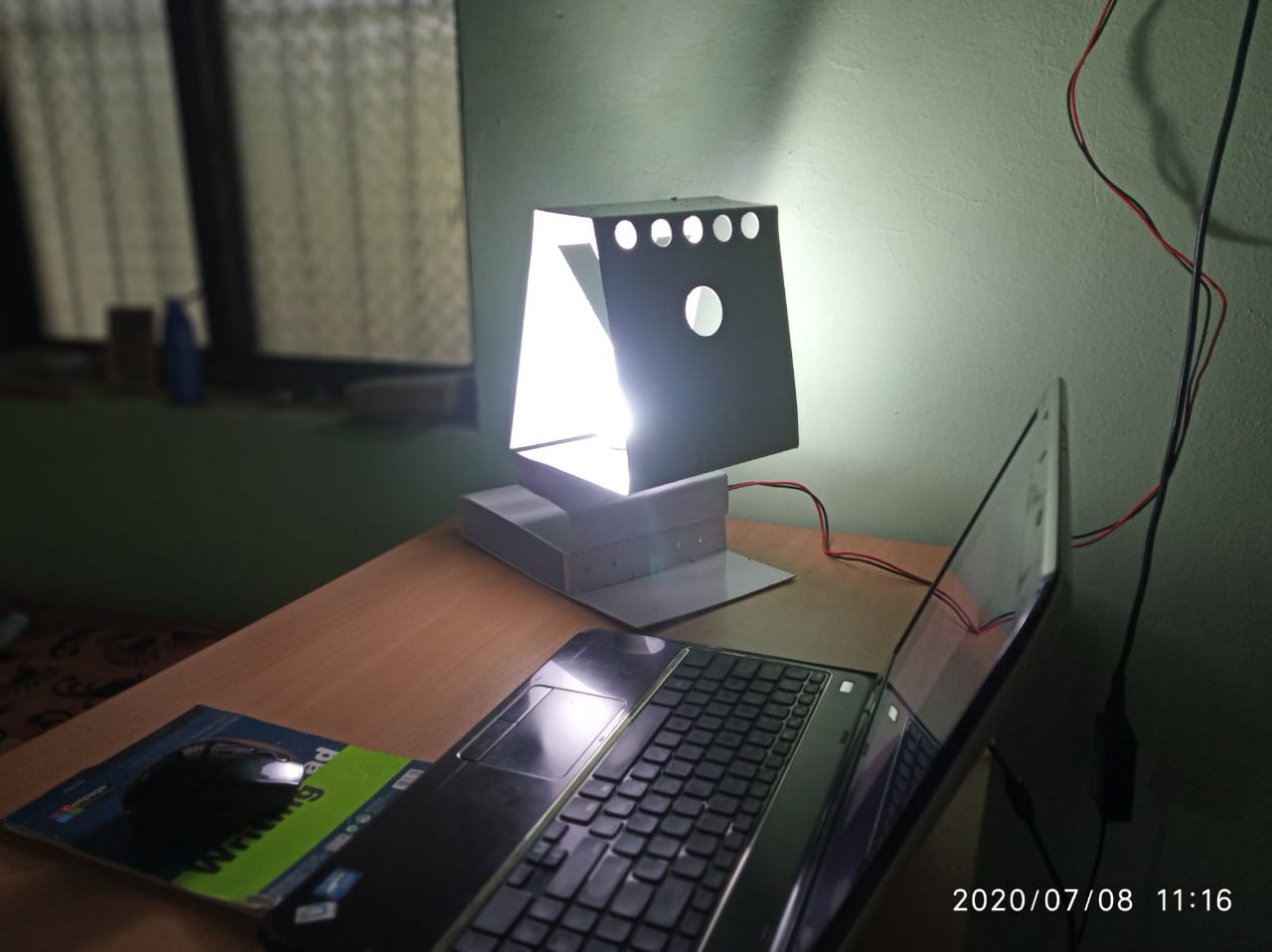
Learning Outcomes:

Cattle Health Monitoring System by Vikram Ingole is licensed under a Creative Commons Attribution-NonCommercial-ShareAlike 4.0 International License.