Week 11: Composites
Goal: design and make a 3D mold and produce a fiber composite part in it.
Step 1: mold design and manufacturing
This week in my assignment I made the seat and backrest of a chair with a glass fiber composite.
The chair fabricated is based on a Charles and Ray Eames design, but I adapted the original to digital fabrication with laser cut and CNC router machine in MDF planks (natural and black).
|
|
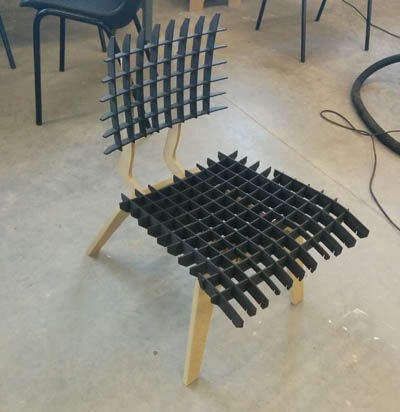 |
When de CAD design is made (using Rhino), I drill the mold in polyurethane foam.
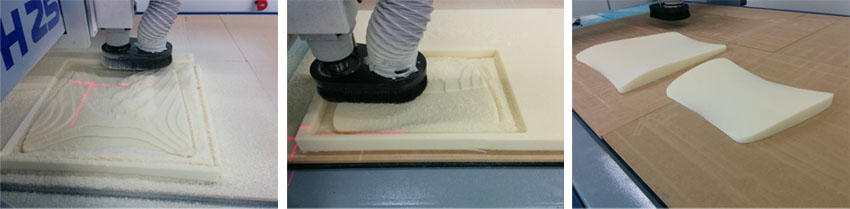
Step 2: preparing the fiber glass
For adapting the Fiber Glass to the curved surfaces and prevent bubbles I make a pattern with the fiber glass as I would do with clothing to make a suit.
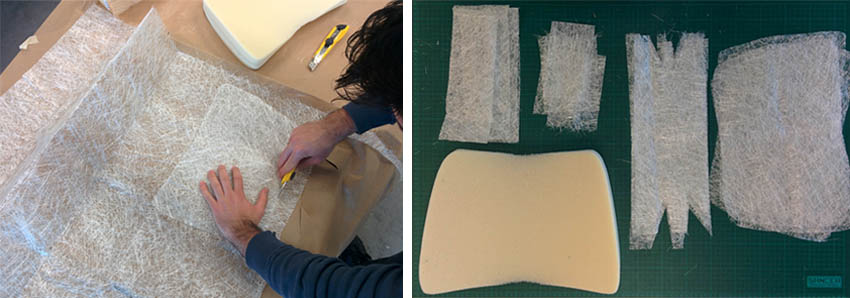
Step 3: preparing the composite
I used a polyurethane resin purchased from Feroca that is already accelerated. It has two components, one is the polyester resin and the other one is the catalyst that will make the resin solidifies. The proportion of catalyst to be added is 1.5 % of the resin used . Working time before the resin catalyze is about 20 minutes.
To apply the resin I used a brush. First I put a layer of resin on the polyurethane and then I put the fiberglass over it and give another layer of resin, being careful to avoid bubbles. I'm putting several layers to give consistency . In my experience I have seen that is better many small dimensions pieces of fiber instead of one large to improve the adaptation to curved surfaces .
I worked on two pieces, inthe first one(the seat of the chair) I've only applied composite on one side , while the second piece, the back, I have done on both sides . The problem when applied on both sides is when you support the piece to apply the second side, the first one will take off and bubbles appear, so you must be very careful and apply all the resin holding the piece with a hand , still in points where it has been held small bubbles appear . May be better to apply only on one side and wait until the resin is dry and then apply the resin in the second side . Despite that the result wasn't bad.
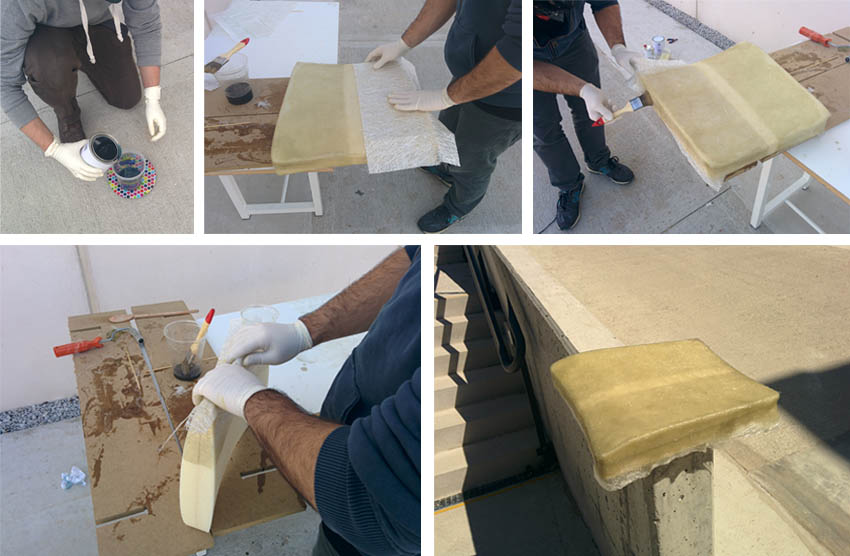
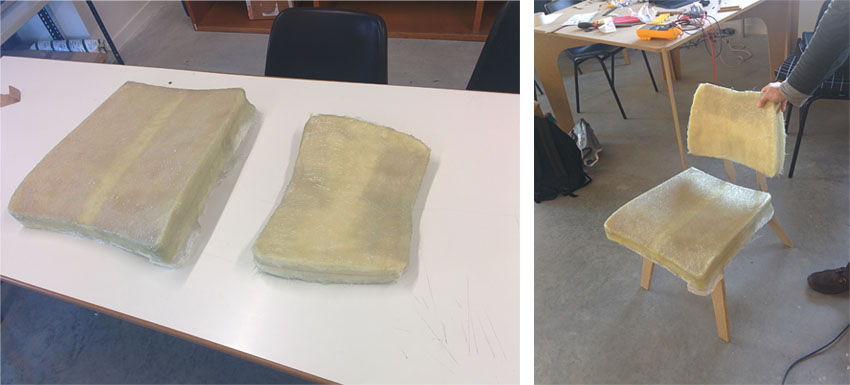
|