Group Assignment: Molding and Casting
For this week's group assignment we had to review the safety data sheets for each of your molding and casting materials, then make and compare test casts with each of them. To fulfill this week's assignment, we tested the materials we had in our FabAcademy inventory.
Casting Process
Molding is the process by wich you create an impression of an object in some sort of material. Generally, an initially soft material is poured or spread around the object and allowed to harden or set, creating a negative imprint of the object. Moldings can be made in either one piece or multiple pieces. While the type of molding material used depends on the size and shape of that object, some popular options include plaster and silicon. Casting Casting is done once a mold of an object is available. If the mold is made up of multiple pieces, it is put together securely and the casting material is applied. Casting creates an exact replica of the object that was molded, with only some slight sanding needing to be done. Various types of metals are commonly used in the casting process, including aluminum, copper, magnesium, iron, and zinc.
Casting with Silicone
In our FabLab inventory we have two different types of silicone:
Ecoflex™ 00-30
Ecoflex™ rubbers are platinum-catalyzed silicones that are versatile and easy to handle. The mixture is 1A:1B by weight or volume and is cured at room temperature. Ecoflex™ rubbers are suitable for a variety of applications including making prosthetic appliances, cushioning for orthotics and special effects applications.
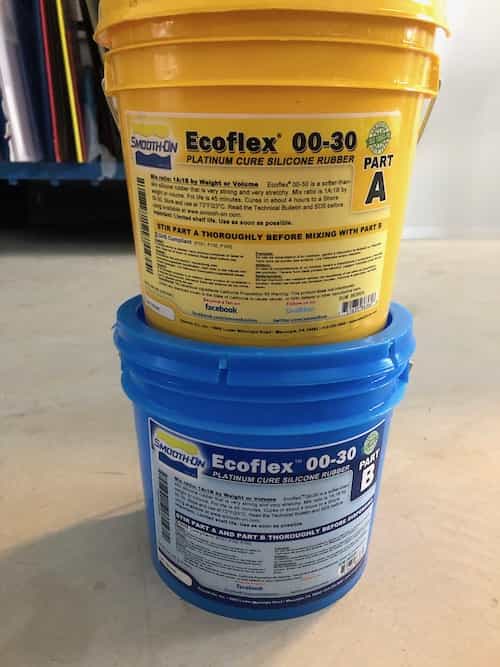
When casting rubbers with Ecoflex™, it is very important that you do so in a well ventilated area. Moreover make sure you wear protective goggles, long sleeves and rubber gloves (only vinyl gloves) to minimize contamination risk. The material should be stored at room temperature (73°F/23°C). Storage at warmfer temperatures will shorten the useful life. Even if the rubber is used at temperatures higher thanroom temperature (73°F/23°C), the working time and curing time will be reduced. The data sheet also states that you should mix for 3 minutes to ensure that you scrape the sides and bottom of the mixing container several times. After mixing it is recommended to vacuum to eliminate any entrapped air. The curing time is approx. 4 hours and the pot life approx. 45 minutes.
Alessandra Crotty used Ecoflex™ 00-30 to coat the steering wheel. She used AltroColor 5036 black to paint the silicone. To speed up the curing process, she also placed it in the oven for 2 hours at 176°F/80°C, which reduced the curing time to 3 hours.
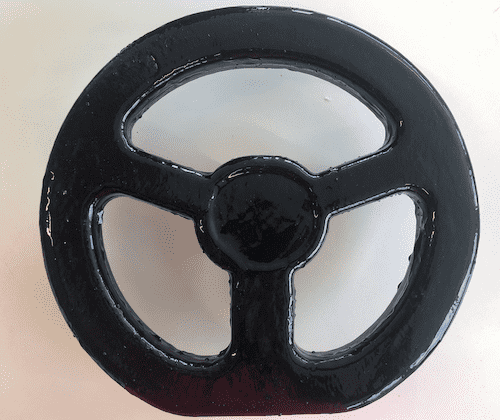
ProtoSil RTV 245
ProtoSil RTV 245 has very good flow properties. It can be used for the production of elastic moulds, especially prototypes. Store the material at temperatures of 15 - 25 °C and keep it in tightly closed original containers. When working with this material, it is very important that the containers you use are clean and dry. The mixture is 100A:10B by weight or volume and is cured at room temperature.


When casting with ProtoSil RTV 245, it is very important that you do so in a well ventilated area. Moreover make sure you wear protective goggles, long sleeves and rubber gloves to minimize contamination risk. The material can react with various types of substances such as organic rubbers, plasticizers, amines and heavy metal compounds. The curing time is approx. 24 hours and the pot life approx. 110 minutes.
We've run some tests using this material. We tried to mix the materials before placing them in the vacuum and mixing them under vacuum, which turned out to be the better way to do it since it eliminates most air bubbles.
Moreover we have also tried to use silicone with different types of molds made out of different materials. Markus Fleischer made a mold out of foam. When we first used foam as a mold, we didn't think about protecting the mold, so unfortunately the silicone stuck to the foam. So he had to destroy the mold to get the negative out of it.
.jpg)
The second time we worked with foam, we protected the mold with acrylic. Unfortunately, this didn't help and we still had to destroy the mold to remove the result.
The use of wax as a molding material therefore proved to be the best choice for casting silicone .
Casting with Resin
In our FabLab inventory we have NEUKADUR ProtoCast 105 as Resin. NEUKADUR ProtoCast 105 has very good flowability, very impact resistant and it's very easy to colour. When casting with NEUKADUR ProtoCast 105, it is very important that you do so in a well ventilated area. Moreover make sure you wear protective goggles, long sleeves and rubber gloves to minimize contamination risk. Store the material at temperatures of 20 - 25 °C and keep it in tightly closed original containers. After use, always clean the cap and make sure it is tightly closed. The mixture is 100A:200B by weight or volume.Note that the density of both materials is different. The curing time is approx. 2 hours and the pot life approx. 30 minutes. NEUKADUR ProtoCast 105 Component A has to be homogenized thoroughly prior to processing.

The data sheet recommends vacuuming component A for 15 minutes before adding it to component B. We casted with and without vacuuming component A and found no relevant difference between the two methods.
According to data sheet it is also possible to mix both components under vacuum. We have also tested this and found that it shortens the pot life of the materials. Alessandra Crotty tried this and did not have enough time to pour the resin into the mold as it was already hardening.
Casting with Epoxy Resin
In our FabLab inventory we have Epoxy Resin 3321.Epoxy resin 3321 is an especially high-quality laminating resin. It has very high strength values and increased heat resistance. Due to its particularly low viscosity, fibres can be impregnated very easily, quickly and completely. Processing in injection processes and under vacuum is also possible. Epoxy resin 3321 is used for the production of high-quality laminates in boat and vehicle construction, for the production of rotor blades for wind generators as well as for the production of industrial laminates and sandwich components.
With the hardeners B1 and B2, a processing time of 0.5 to 2 hours can be achieved. In addition epoxy resin 3321 cures at room temperature. After 7 days it is completely cured. The mixture is 100Epoxy:30B/A by weight or volume and is cured at room temperature.

When casting with Epoxy resin 3321, it is very important that you do so in a well ventilated area. In addition, always wear suitable nitrile or butyl rubber gloves. Wear eye and face protection or a gas mask for respiratory protection as the epoxy produces toxic gases.
We have also found that the best way to vacuum it is to wrap it in plastic film as this is easy to remove. Moreover Epoxy resin doesn't adhere to silicone.