Group Assignment: 3D Scanning and Printing
For this week's group assignment we had to test the design rules for the differnet printer(s) in our fablab.
3D Printing
3D printing or additive manufacturing is a process of making three dimensional solid objects from a digital STL file. It is the opposite of subtractive manufacturing which is cutting out. There are no special tools required. The printed parts are manufactured directly onto the built platform layer-by-layer. These days you can make nearly everything with a 3D printer and you also can use various type of materials. Moreover the time it takes to make a 3D print depends on the size of the model and the settings that you use for printing. Once you have created your 3D model, it needs to be exported as either an STL, OBJ, DAE and AMF file. Then it needs to be imported into a slicing software, which will generate the G-Code for the 3D printer.
Using the Ultimaker
With an Ultimaker you can print a lot of different things, but not everything is possible, as you have seen in my prints. The Ultimaker uses the 3D printing technique FFF (Fused Filament Fabrication), with which layers of melted plastic are placed on top of each other. Therefore complex structures or “overhanging” parts are hard to print. You can use PLA and ABS as materials for 3D printing. Furthermore you can also always try other materials.
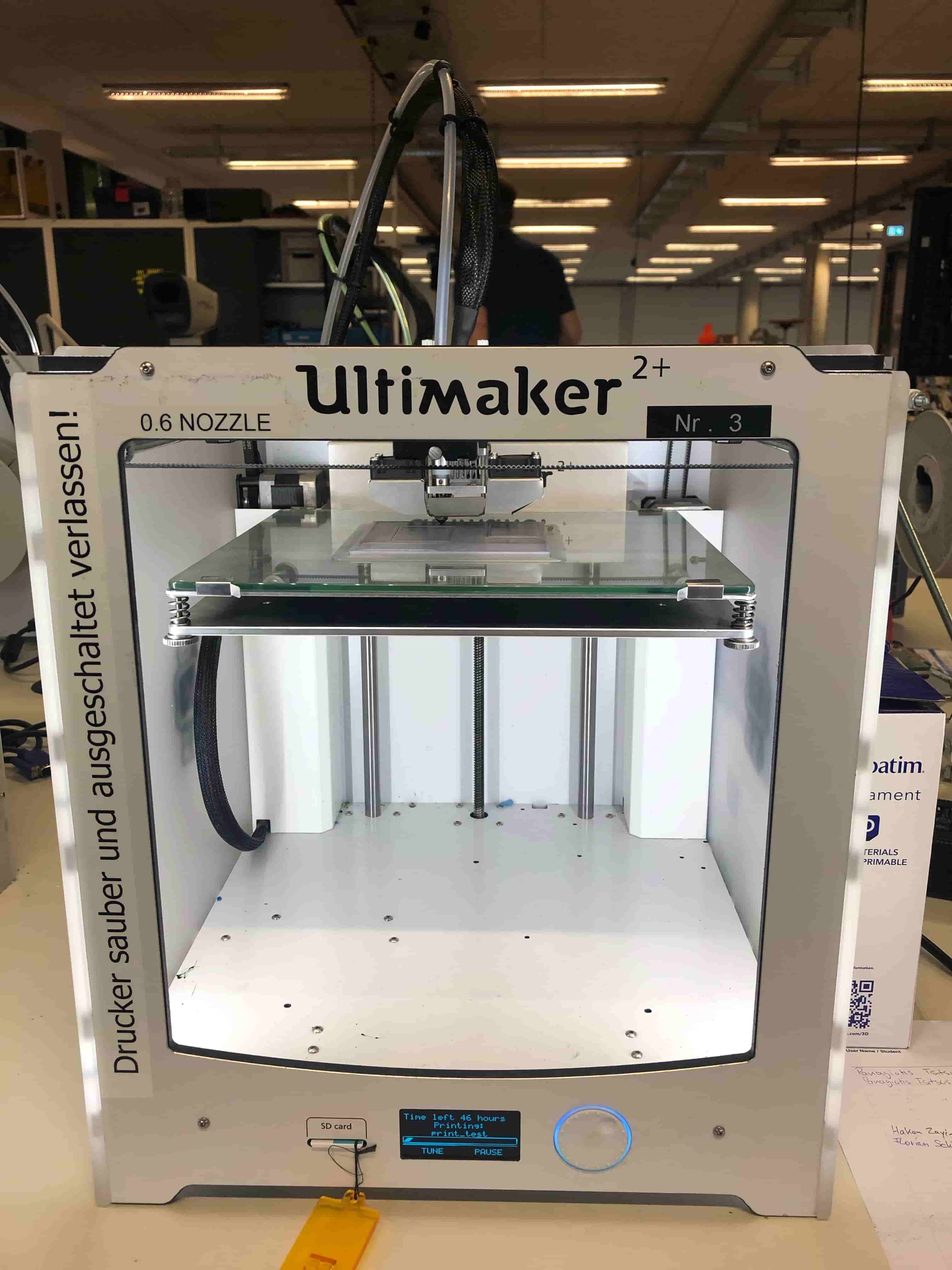
Before you start your print make sure that the surface of the printer is clean. In addition always check if the fillament inside the printer is the same you want to use, otherwise you will have to change it. Now you can start your print by inserting the sd card into the printer and then select the file. The nozzle needs to heat up in order to print, since every material has his one melting point. Before it starts printing it will extrude some fillament, if nothing is coming out the nozzle might be clogged.
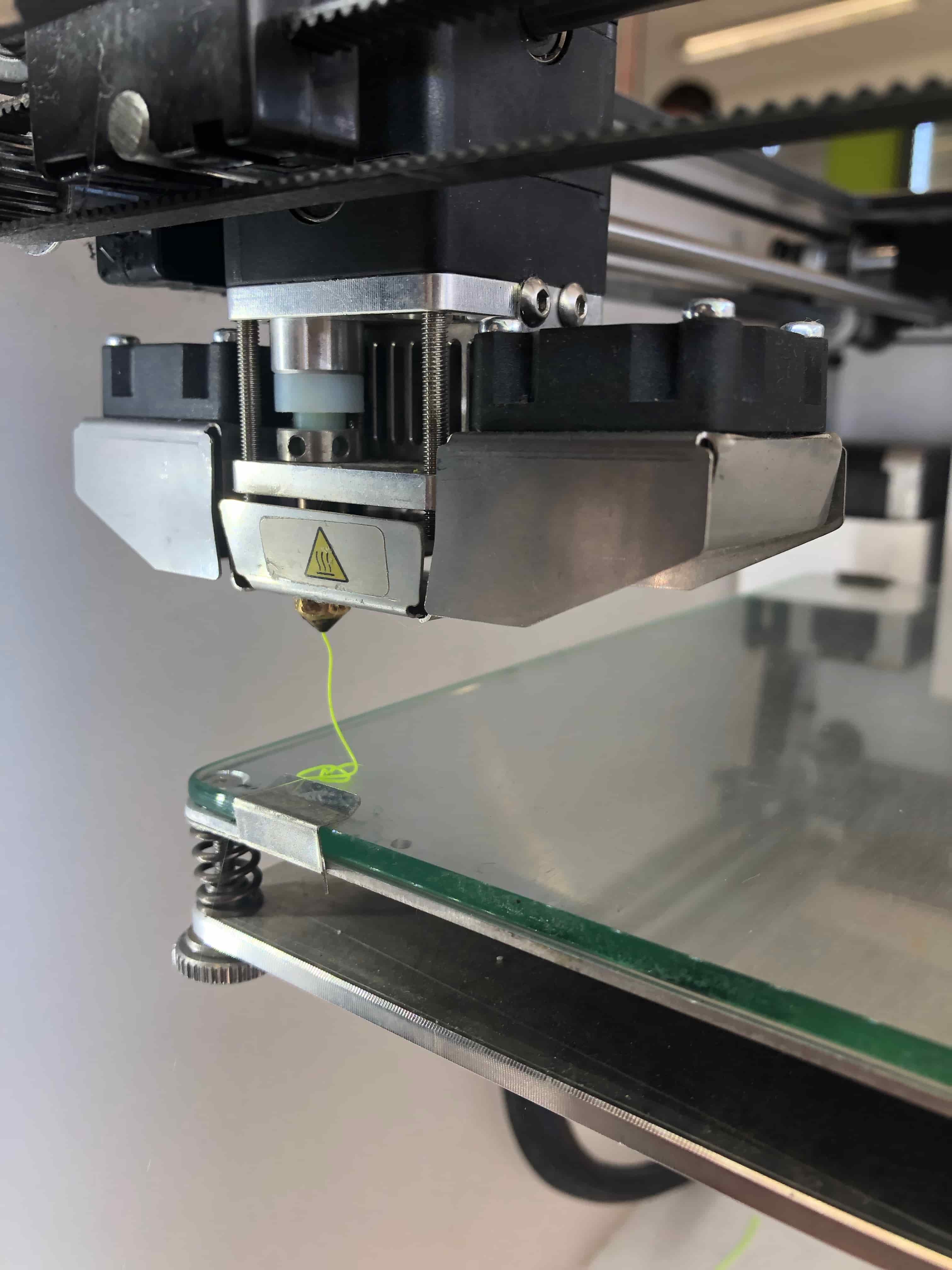
Moreover you always have to check that the first layers are well printed, otherwise you have to abort the print.
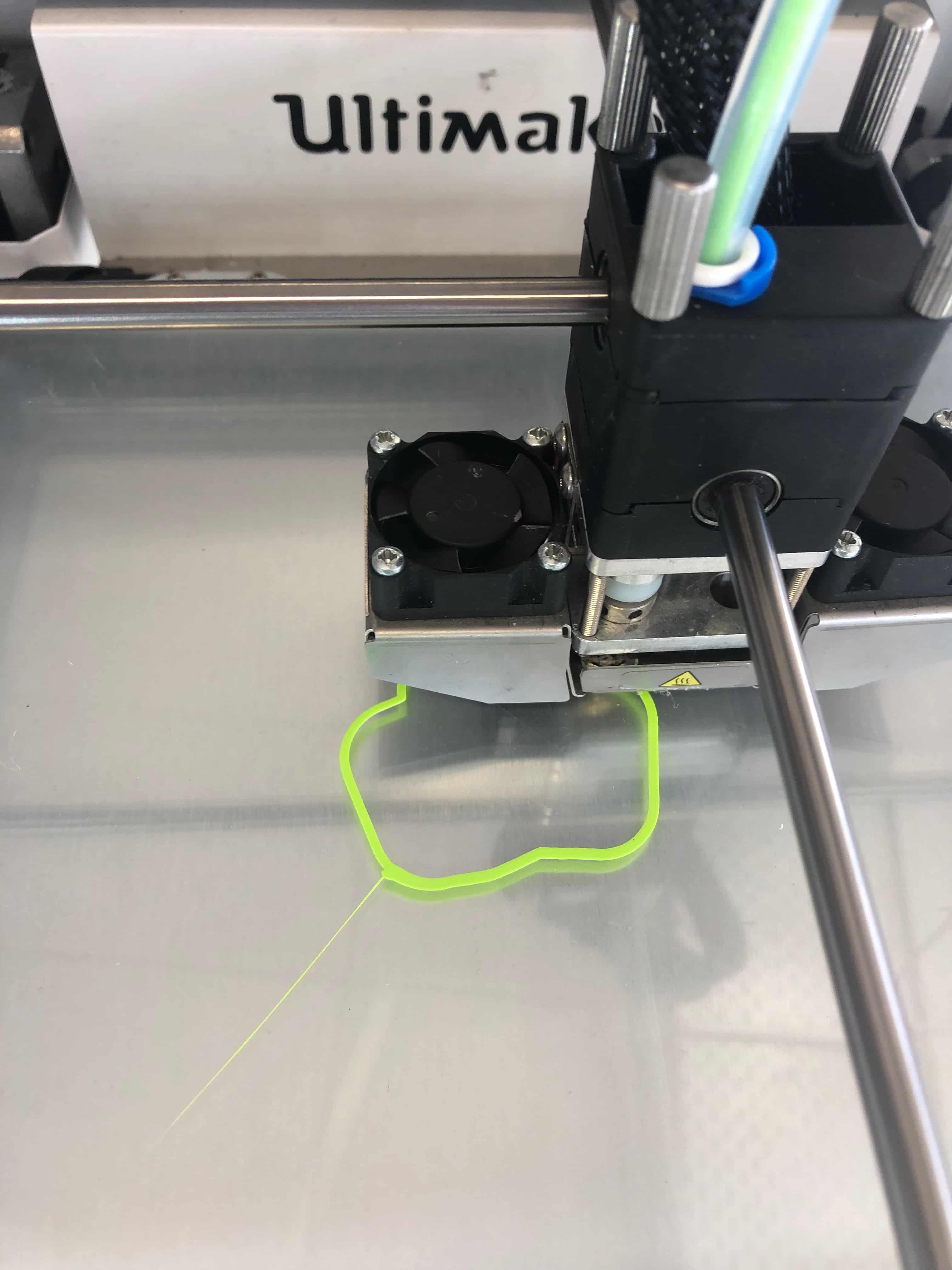
Working with Cura
Ultimaker Cura is an open source 3D printer slicing application. It takes a 3D model and slices it into layers to create the G-Code, which is the code that a 3D printer understands. Cura recognizes STL, OBJ, DAE and AMF file.
On first loading Cura, you’ll be asked to select a printer. Once you have setup the right printer, you can import a model into the software. To import a model, you can either click on the folder icon on the left or select File --> Open File from the top menu.
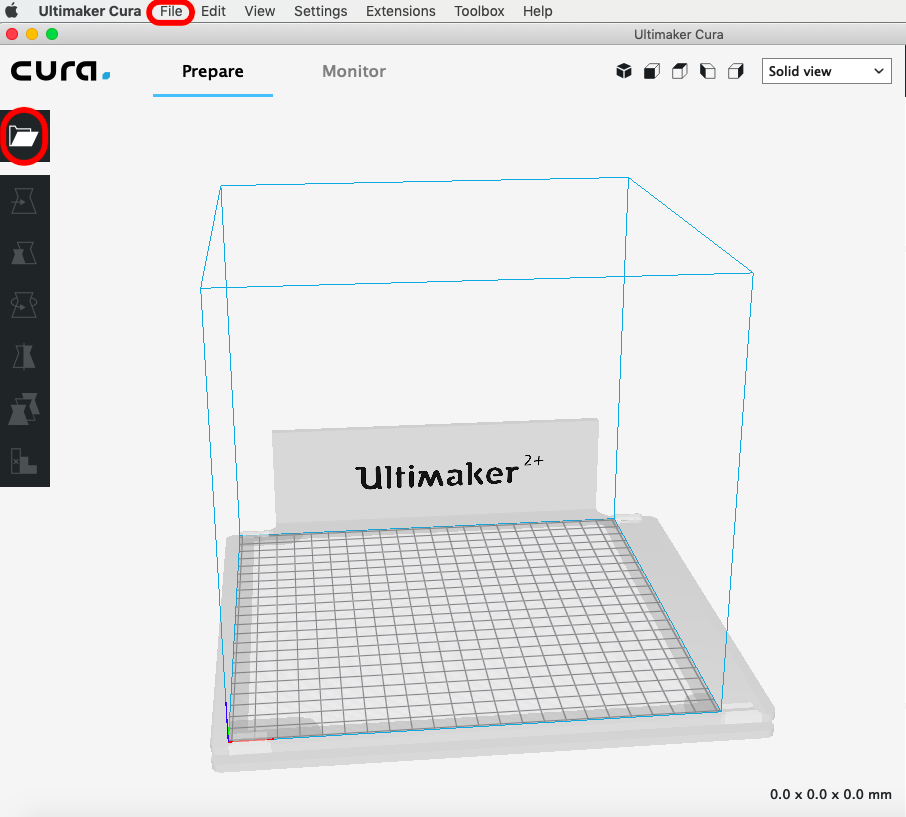
As soon as the model appears on the build area you might have to move it or scale it, in case it's to big. To be able to move the object, you have to select it first. Then the first thing you need to do is, to set the basic settings. Every printer has a different setup, print area, build plate and nozzle size, Cura needs to know these hardware details. Moreover always select the right material, since every material has a different heating point.
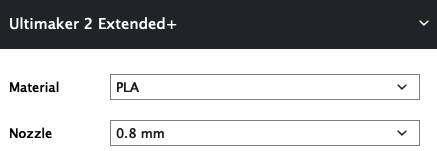
In Cura, there are different ways to view the model (Solid, X-Ray, Layers). Each is useful for different reasons. The default view is the solid view. Everytime you import a new object into the software, you will see it through the default view. It basically shows you the size and shape in comparison to the print platform. Moreover in the right corner you can see the size of your object in millimeters.
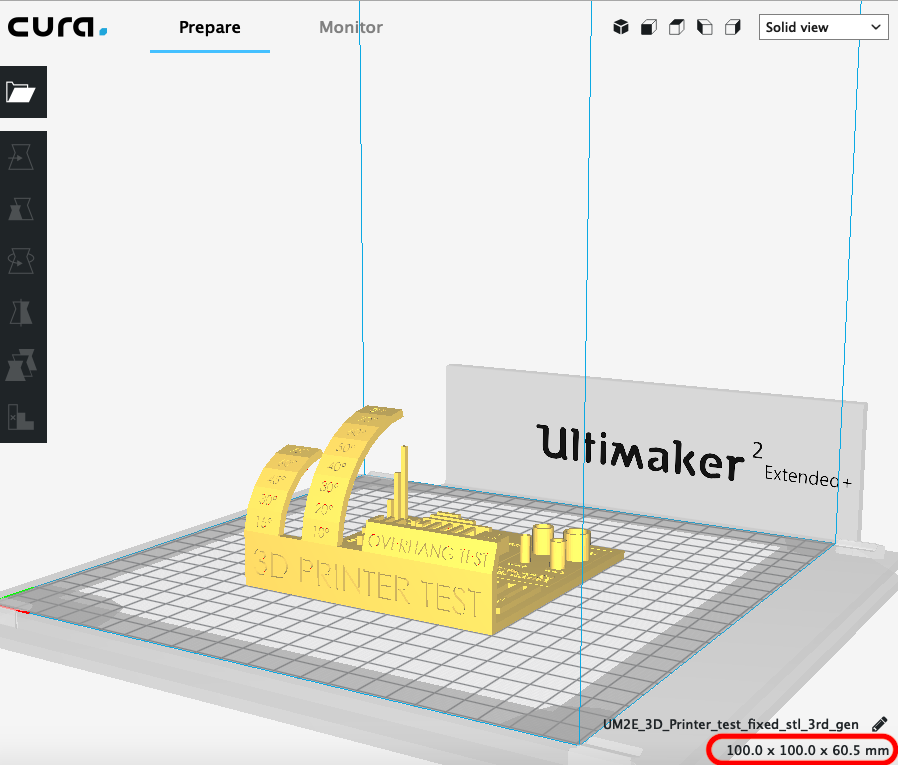
I prefer to use the layers view. This view shows every layer in sequence. It's very usefull to check if there are any problems with the model. If you use support you can change the color scheme into Line Type and you will see where the support starts and ends.
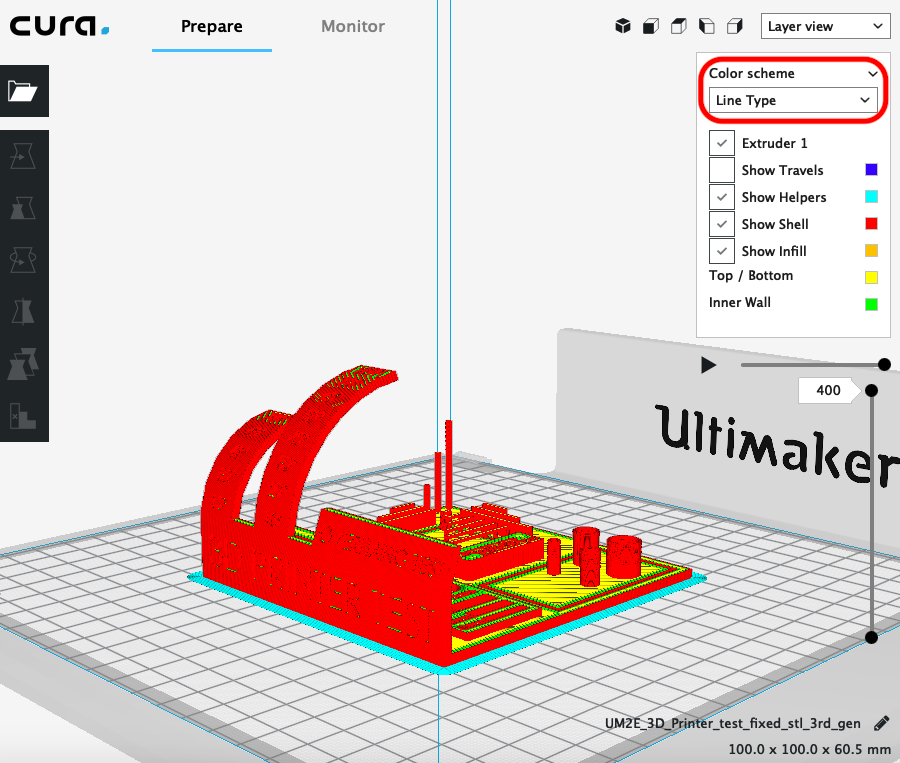
To go through every layer you can use the slider on the right.
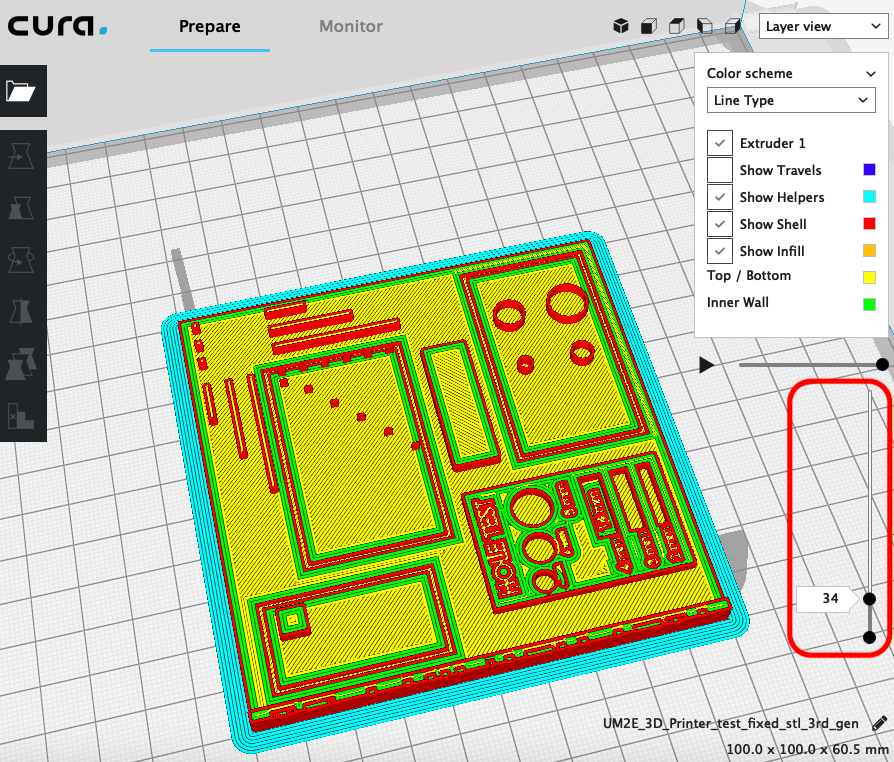
In Cura, you will find all the settings on the side panel. There are many preferences to play with. For my prints I used the following setting categories:
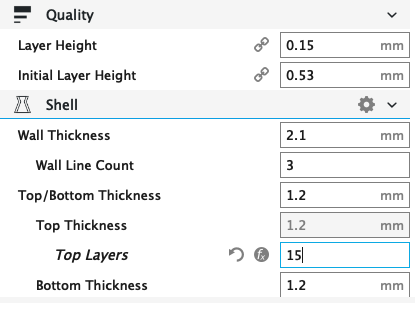
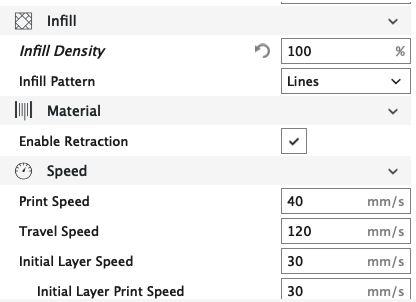
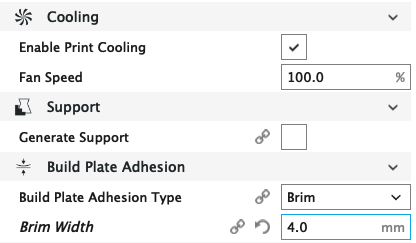
If you would like to know more about the different conditions of the settings you check the Ultimaker Website.
3D test with Ultimaker
We decided to make some tests with the Ultimaker 3D printer. The goal was to discover the importance of the nozzle size in prints. For each test print we used the same settings with different nozzels. We downloaded the design for the 3D test from Thingiverse.

The infill density was set to 100% and the layer height to 0.15mm. We also found out that changing the layer height from 0.1mm to 0.15mm decreased the print up to 1/3. Since the objective was to determine the limitaions of the machine, we decided to print without support.
Underneath you can find pictures of the test with the 0.8mm nozzle. The print took arround 5 hours.
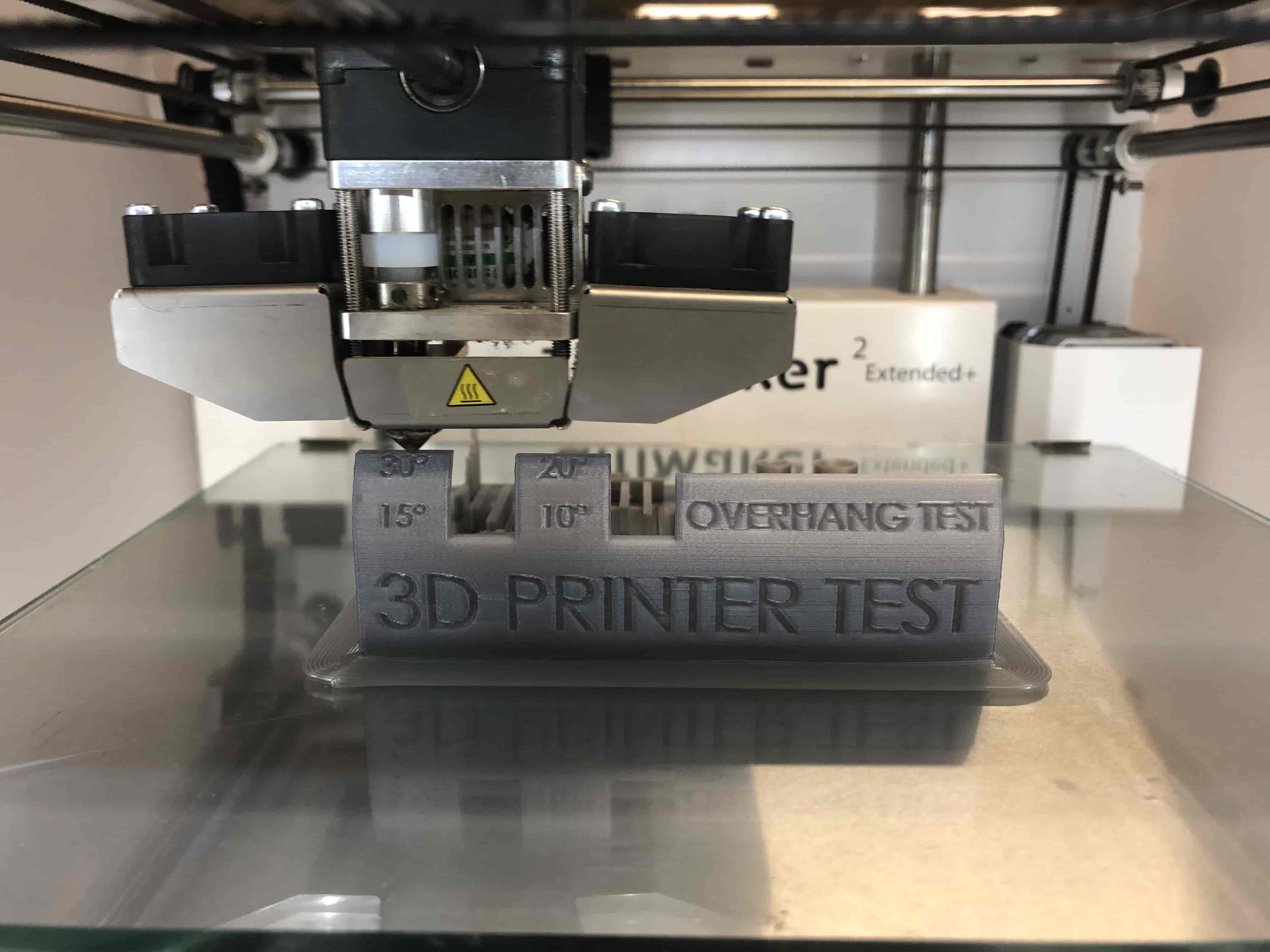
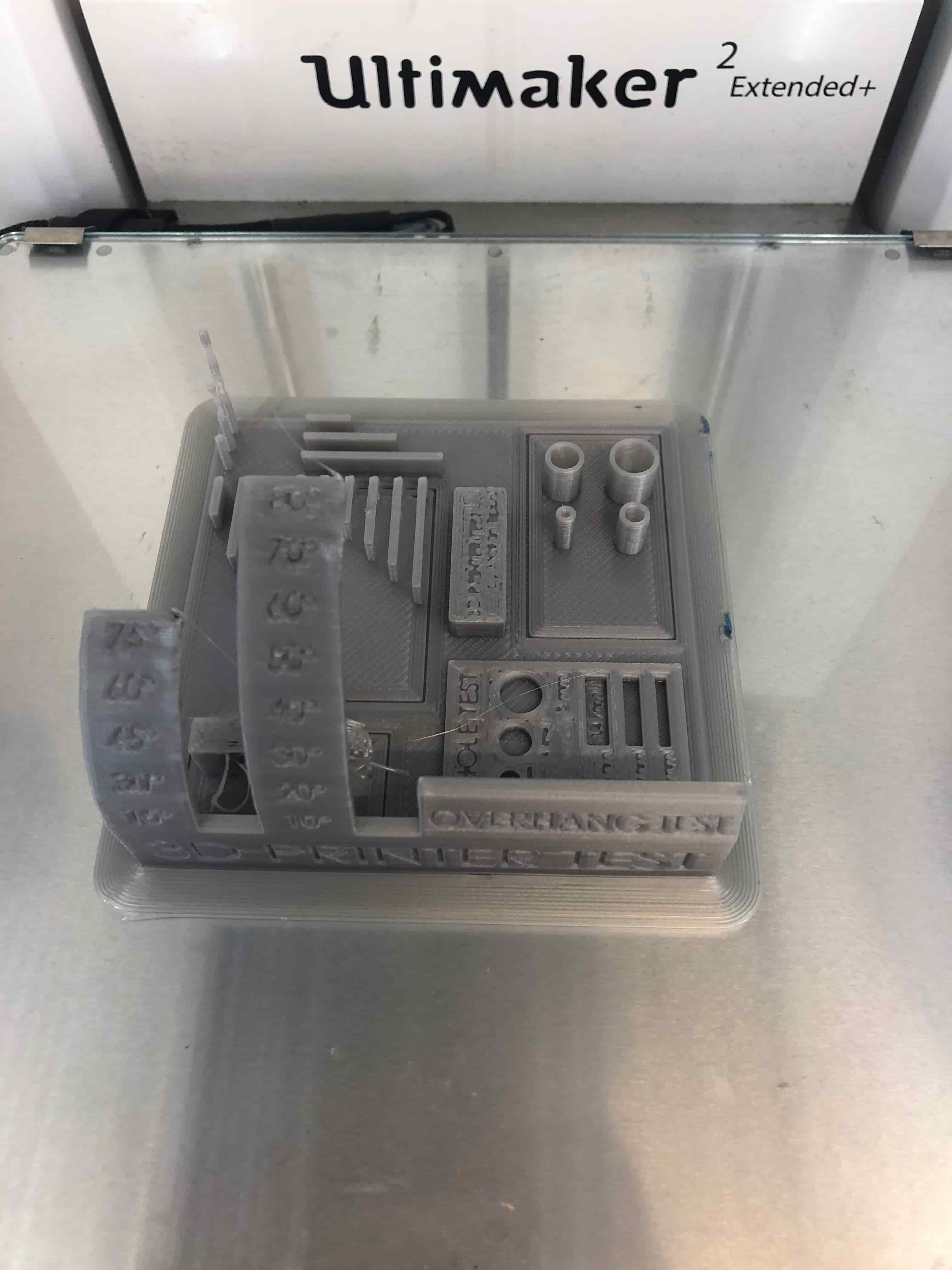
As you can see from the pictures everything with an overhang angle of more than 45 degrees is hard to print without support. Moreover the writing on the top is not readable. Maybe if we would have decreased the layer height it would have looked nicer, but for more detailed jobs you will have to use a smaller nozzle.
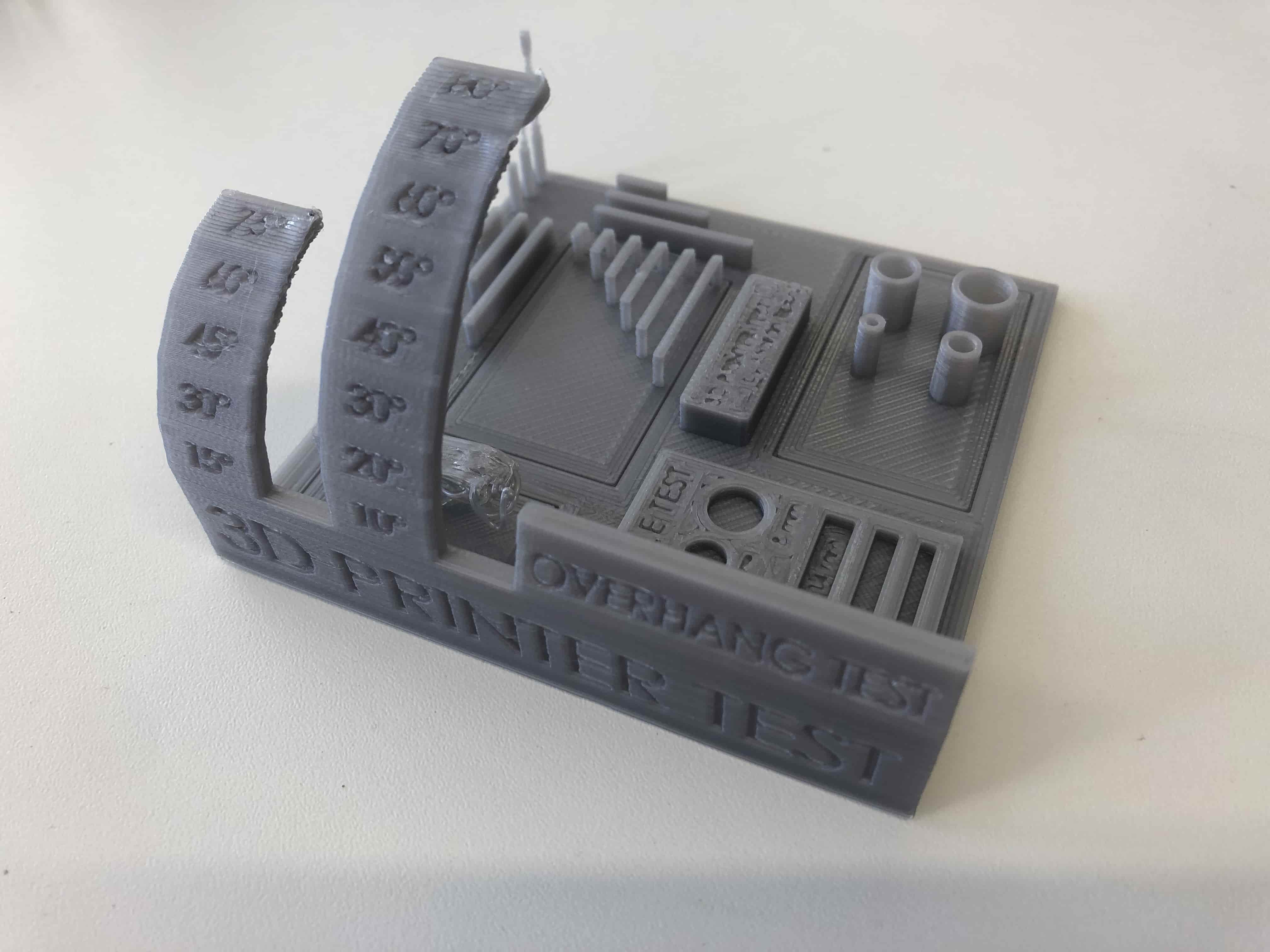
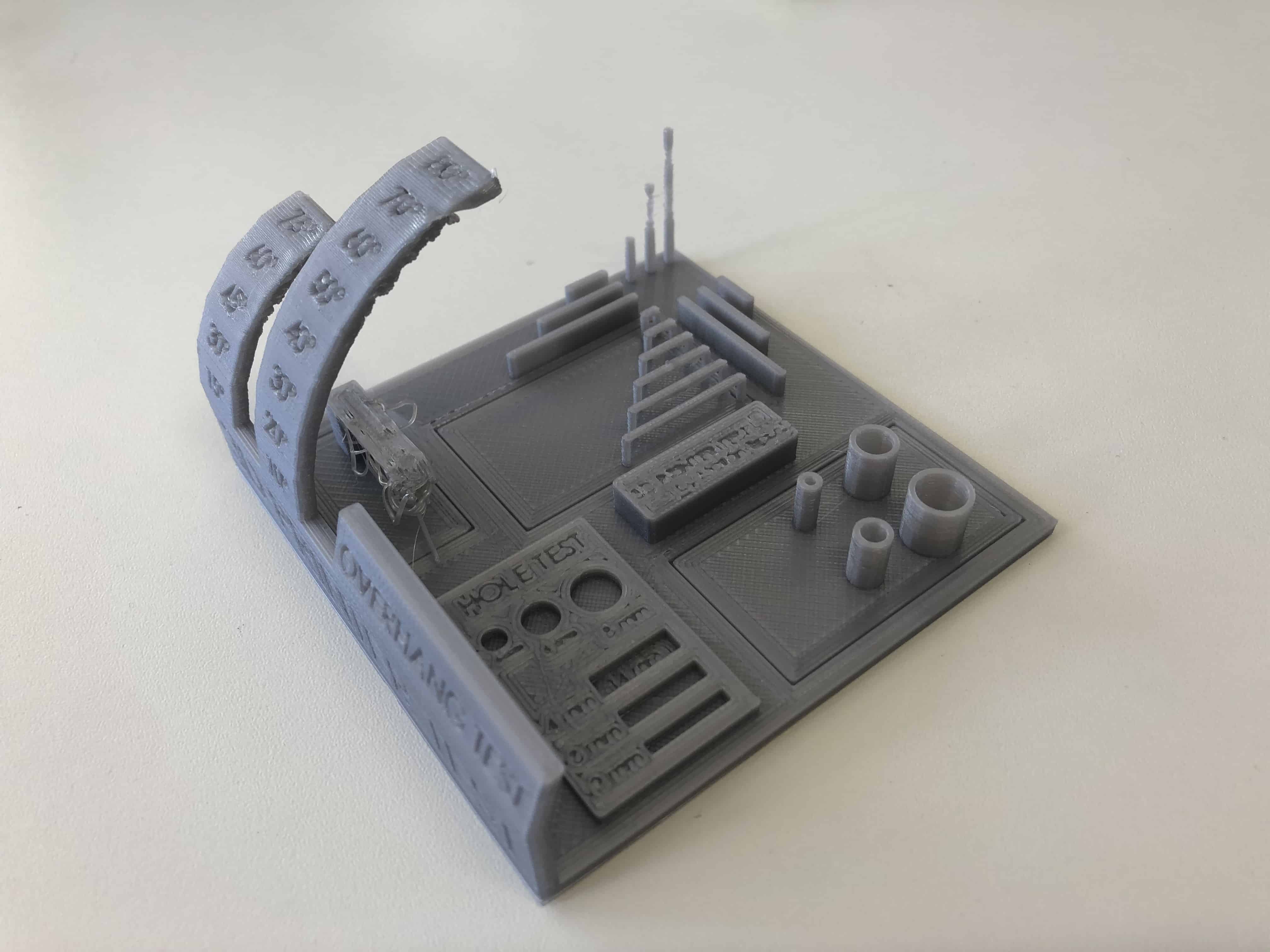
The writing in the front looked in comparison to the others really good and was also readable.