Week 8 | Computer Controlled Machining
There was a mess in my lab because of electronics and it's constant use. We needed some place to keep it at one place and it should also look neat and tidy. So made something for keeping all the things at one place and also it is easy to work when all the things are placed together. We could keep all the electronics and other important things at one place so it becomes easy to work. The design is in Rhino.
In the design there are pockets in place of slots and cutting on the edges for fixing the square pieces.
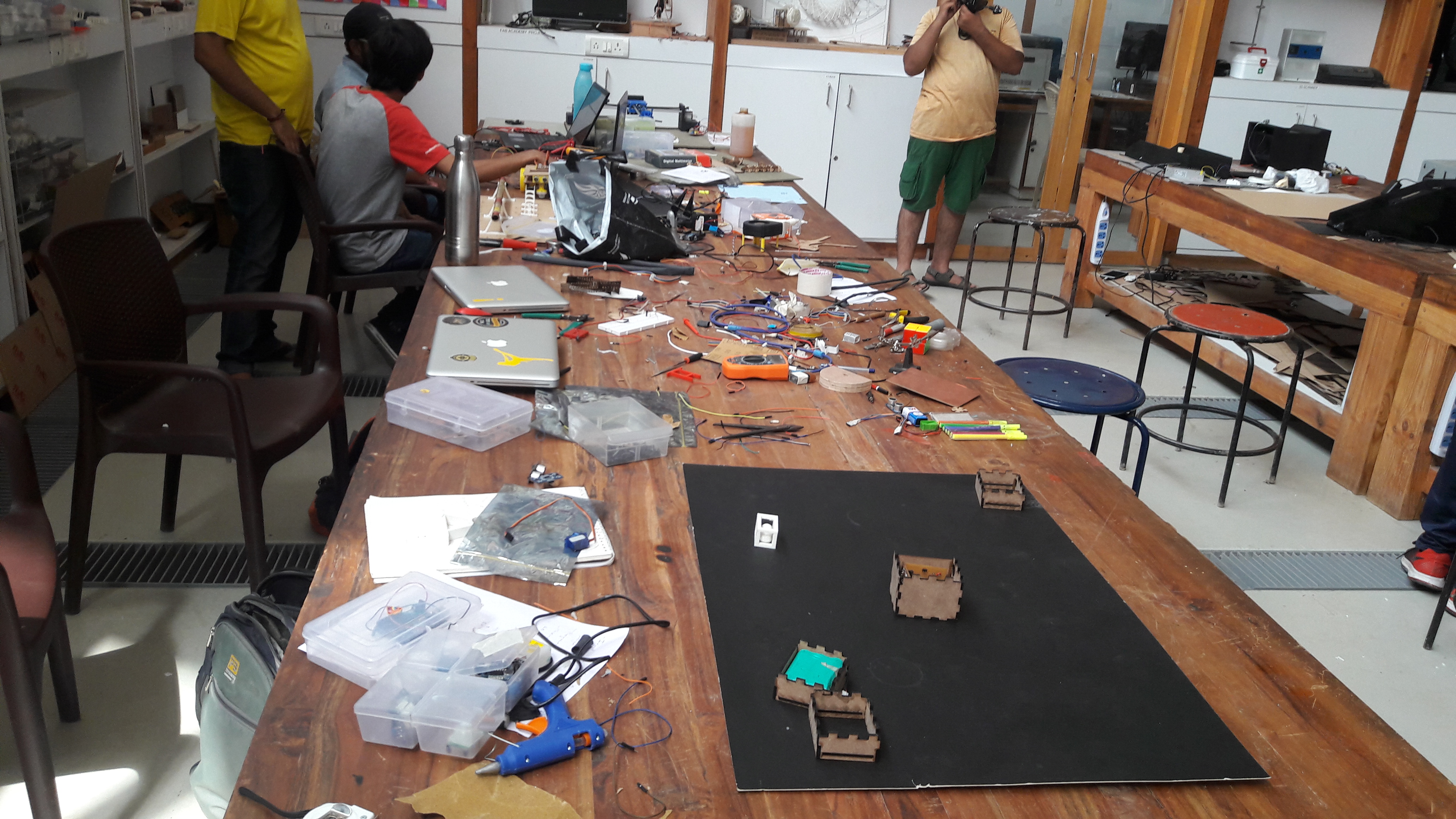
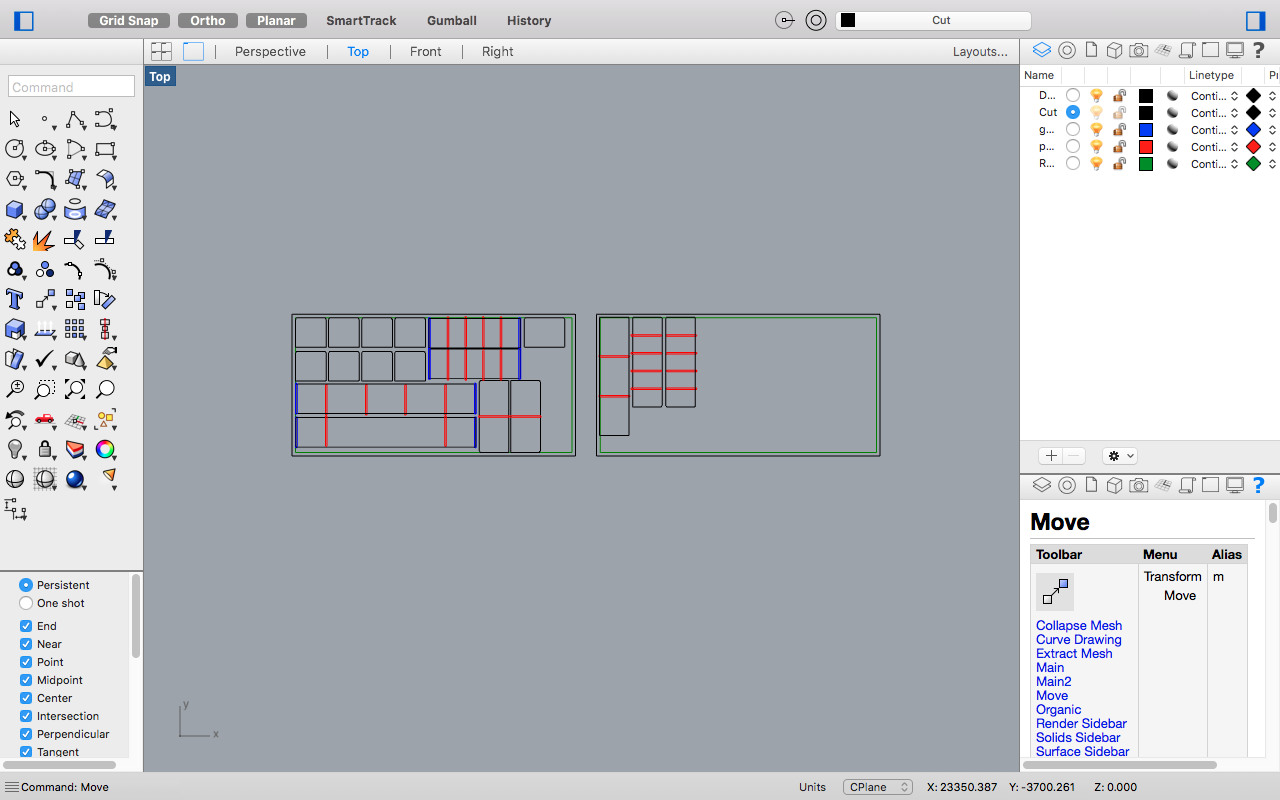
Part works editing
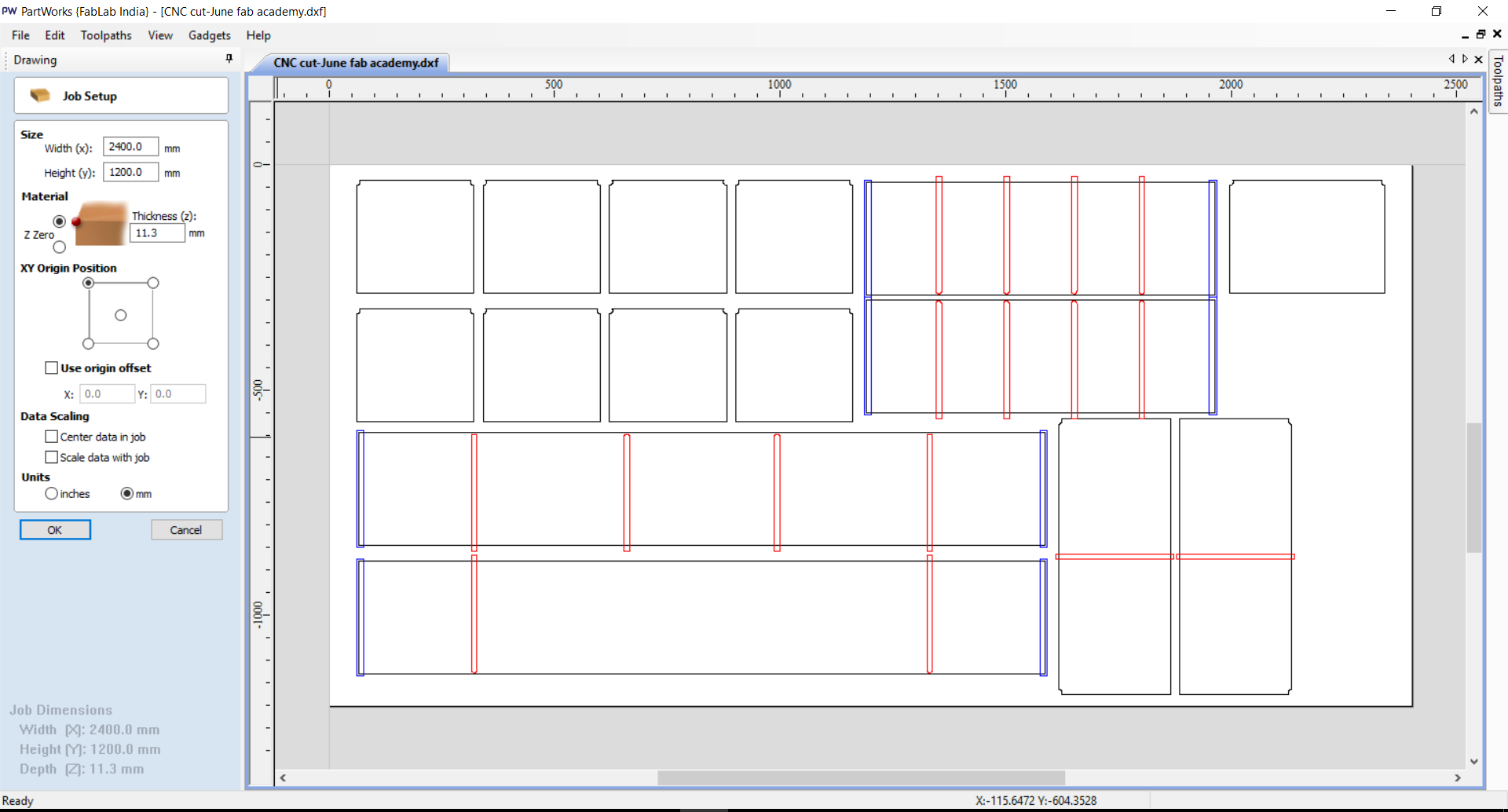
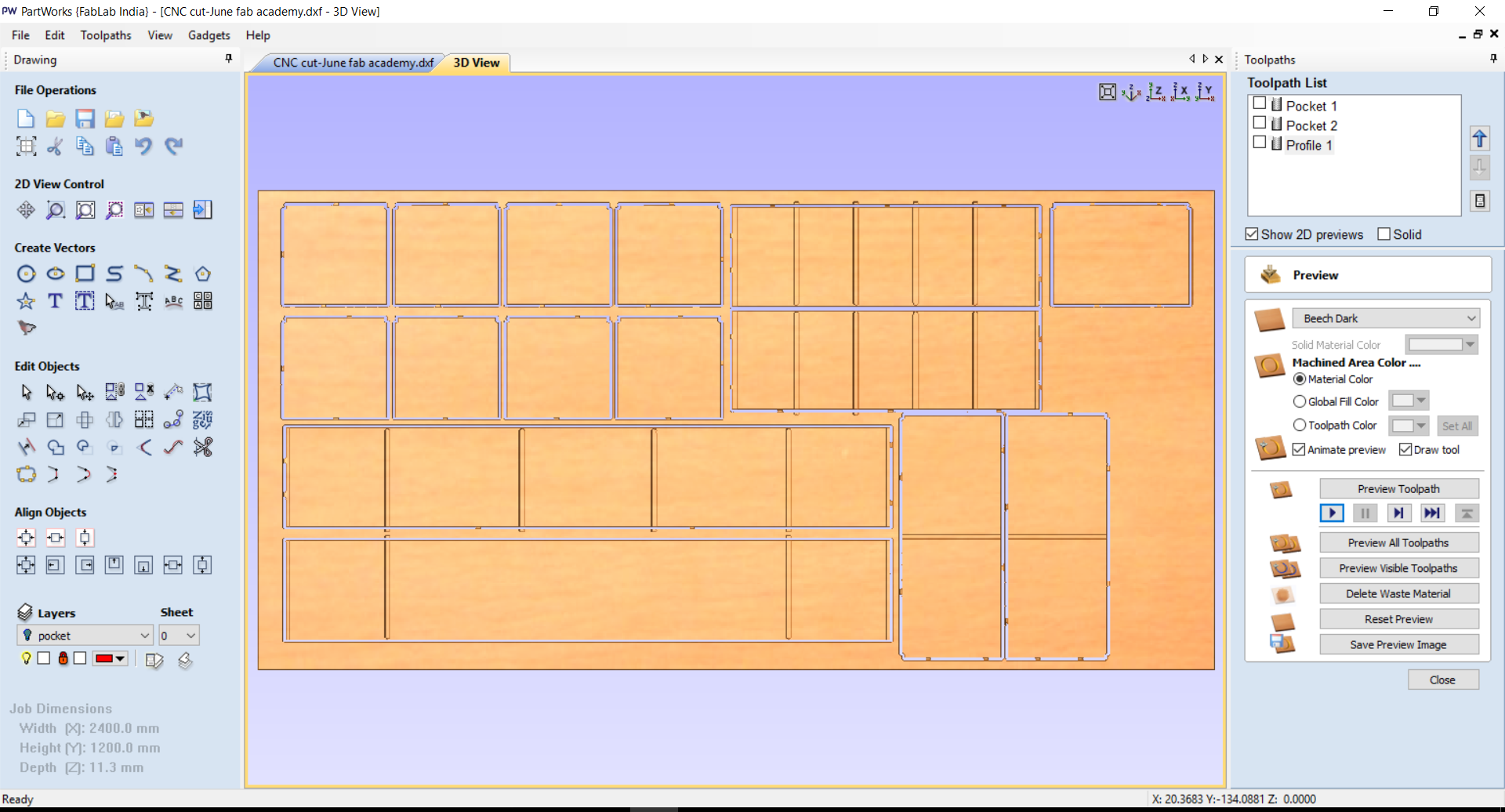
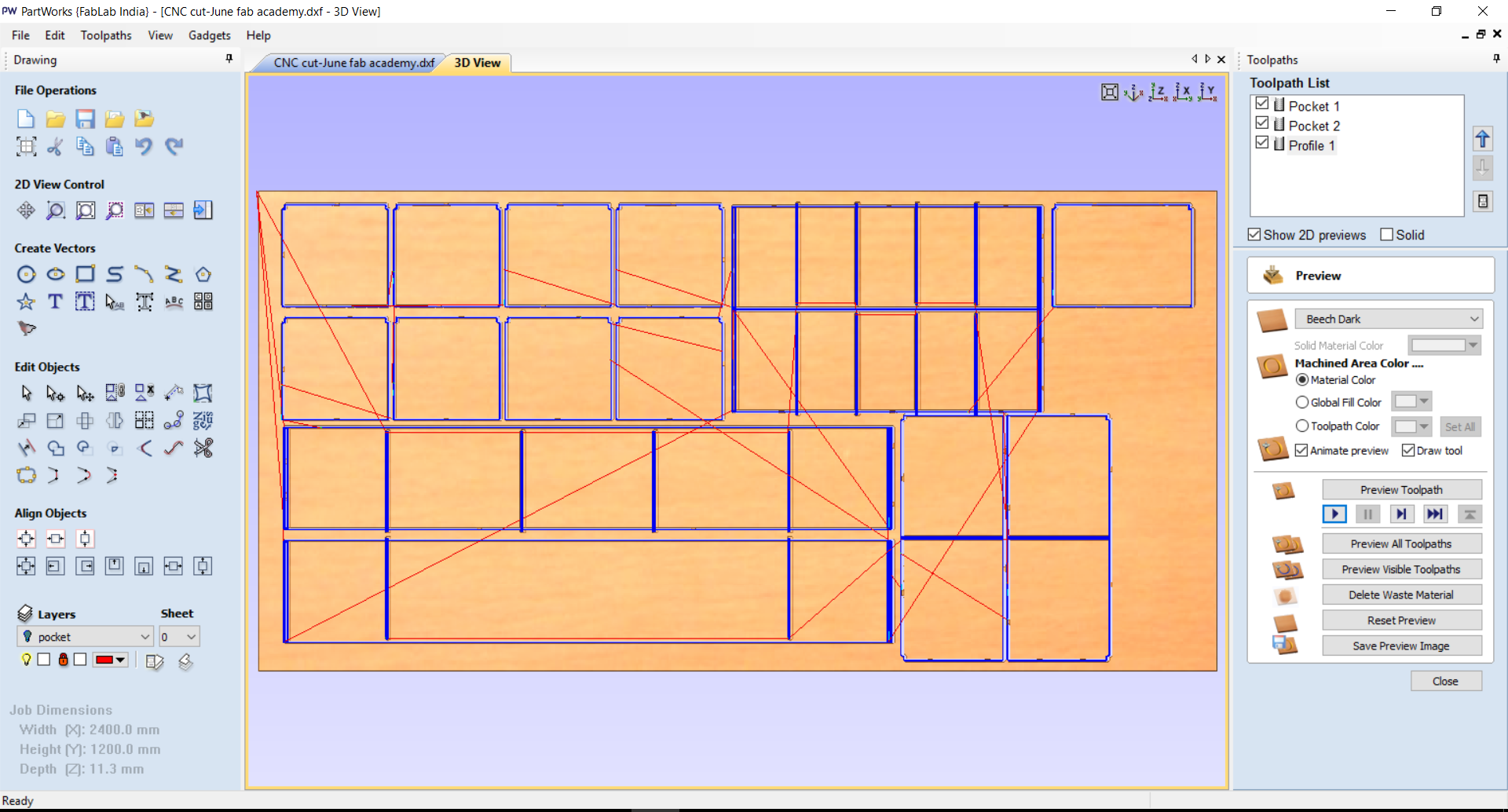
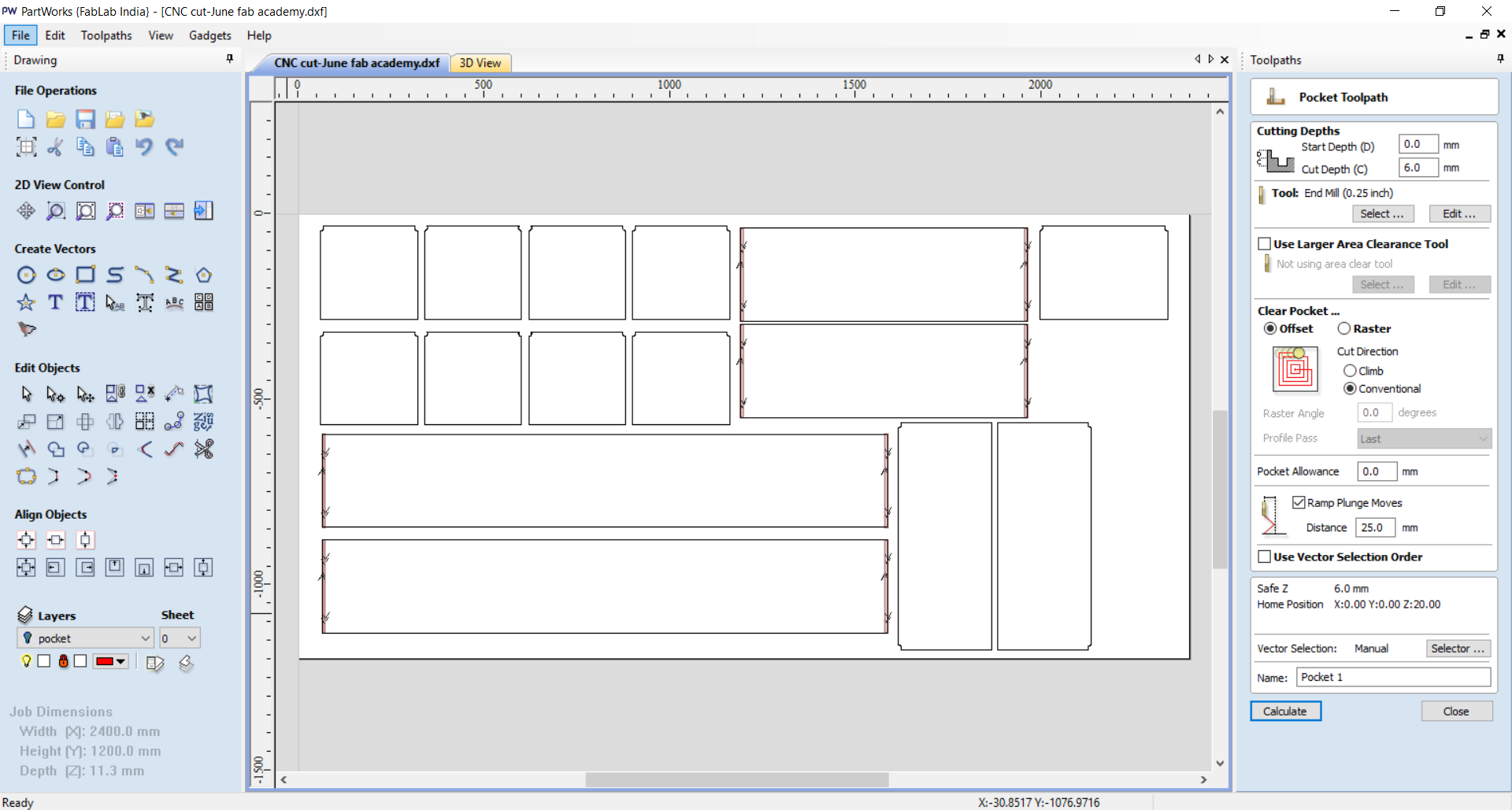
Shop Bot
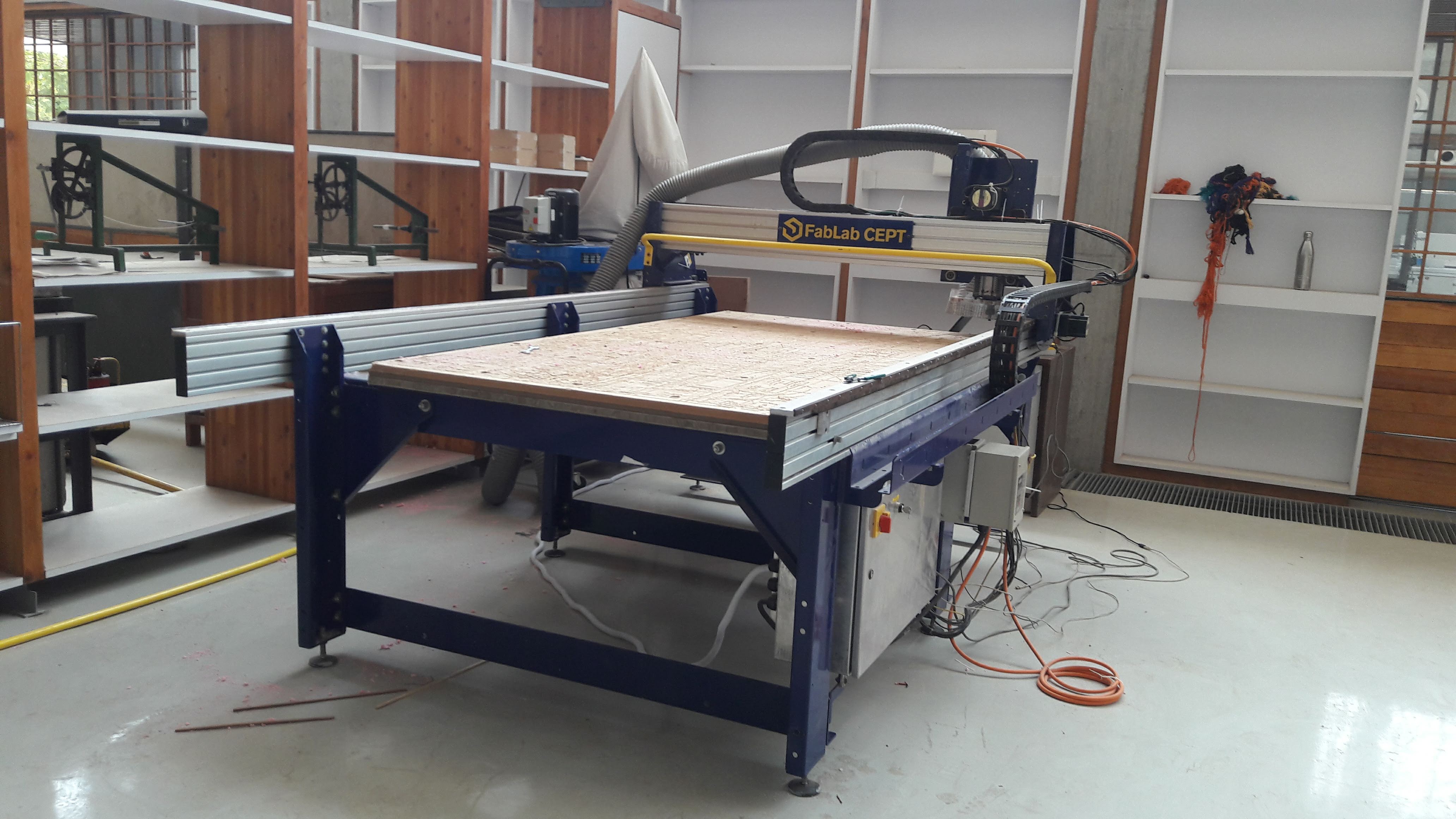
We have shop-bot in our lab. The machine was shifted at another place in the CEPT workshop so it had certain problem with the bed leveling
So for using the machine we had to level the bed again. For leveling the bed we need to level the sacrificial layer which is fixed in the machine.
There is a toolpath already available for leveling the bed, so first we did that. Dhruv Saidava, Gaurav Wadhva and Kishan helped me with the leveling of the sacrificial level.
For leveling we use 1/2 inch straignt cut bit.
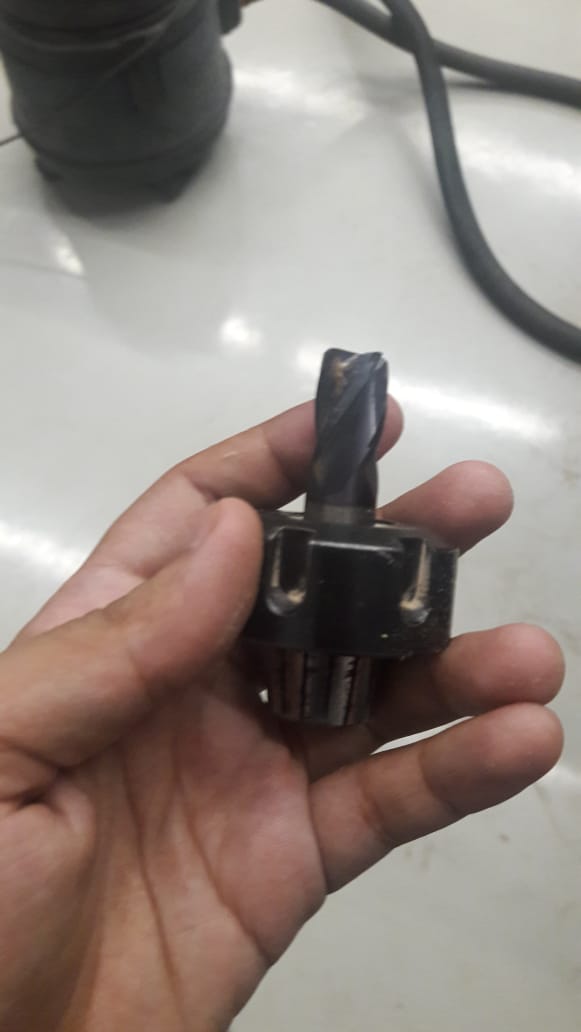
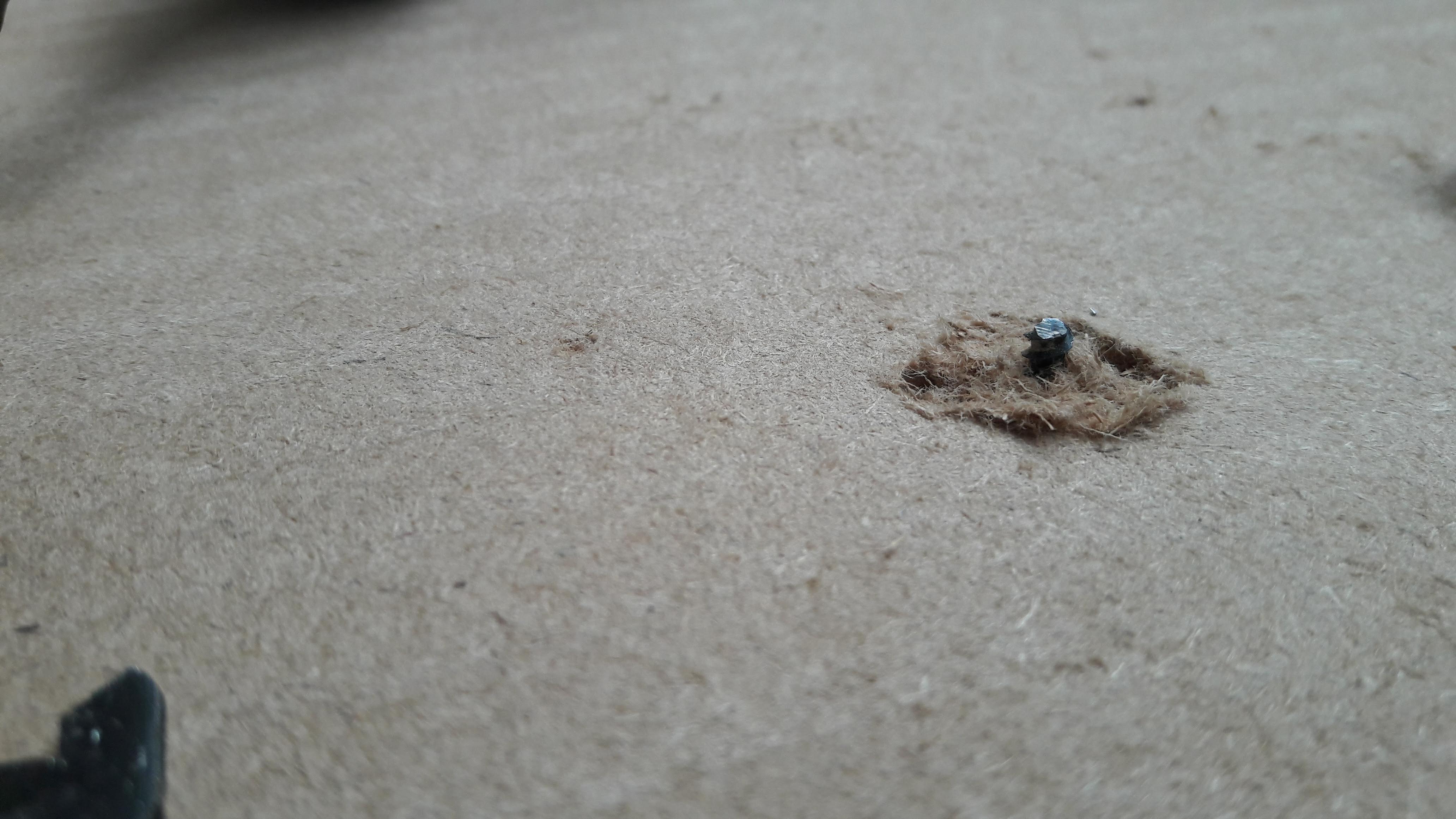
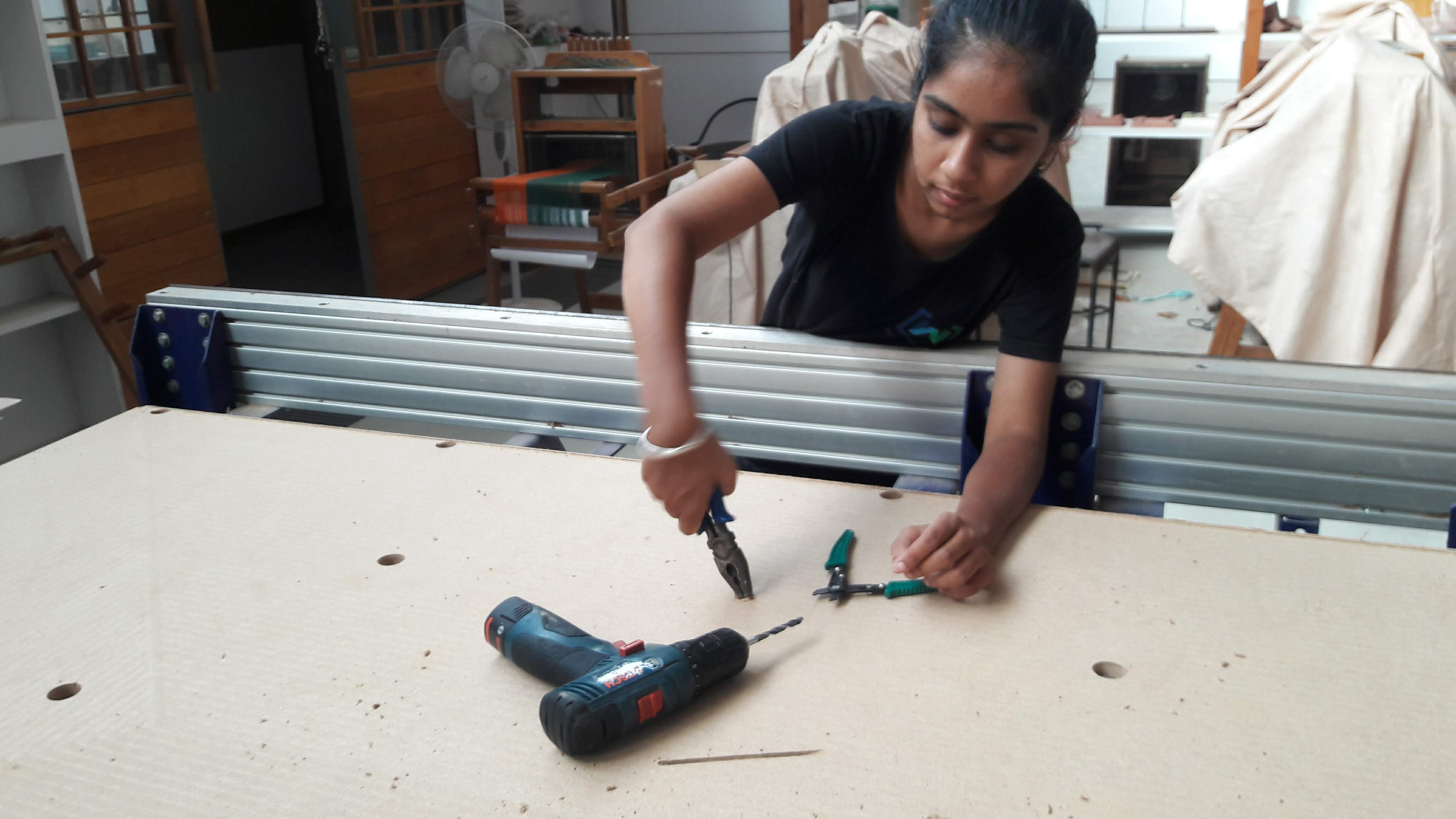
Now as the bed was leveled properly, I was now able to cut the design part. For cutting we use 1/4 inch 4 flute end mill.
Now as the bed was leveled properly, I was now able to cut the design part. For cutting we use 1/4 inch 4 flute end mill.
Additional keys for starting the machine and spindel rotation.
This is an emergency stop button, we can press the "stop" button in case of any emergency. It is necessary to hold it till the design get's completed.
For fixing the drill bit we need spanners to fix it.
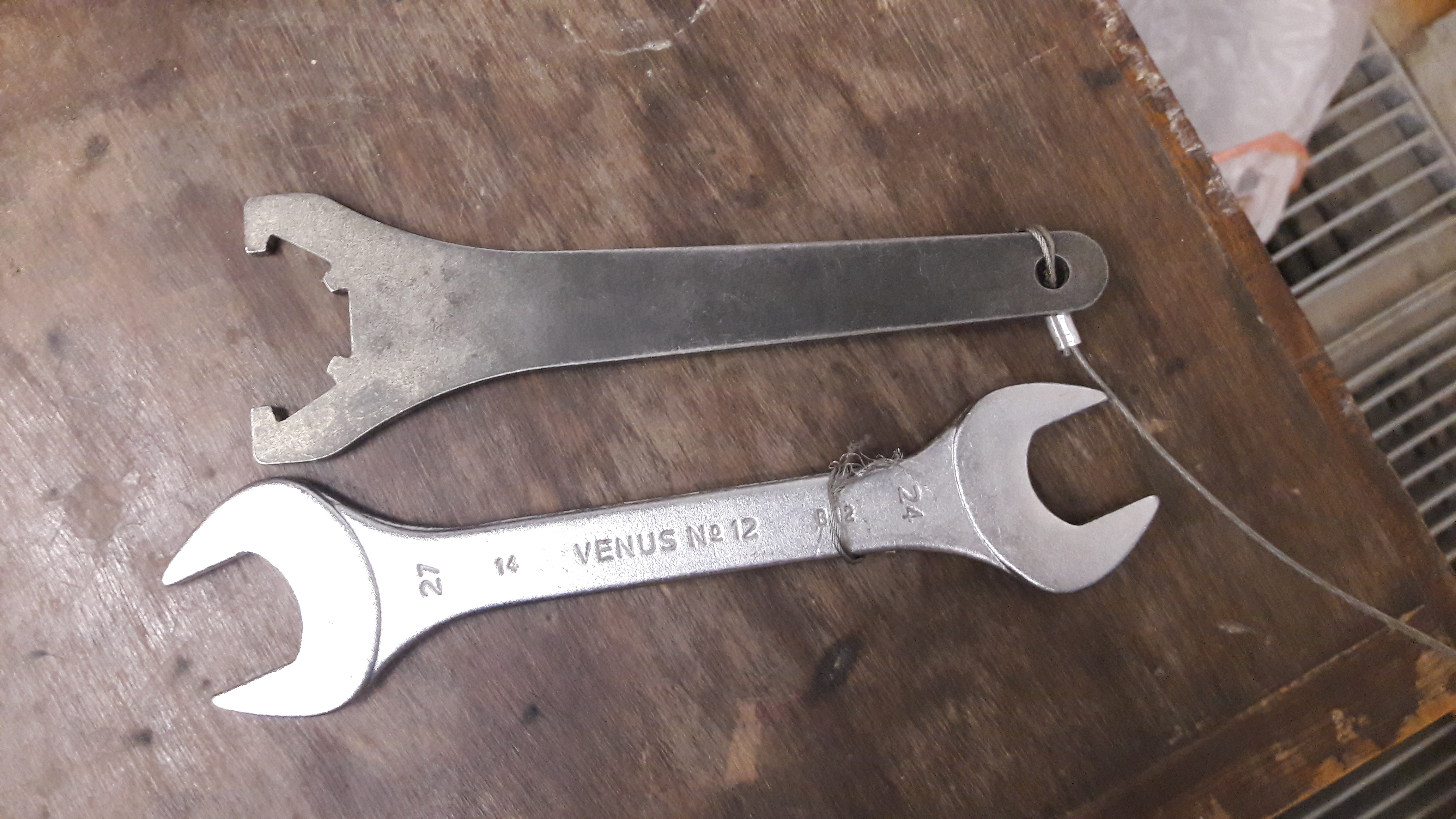
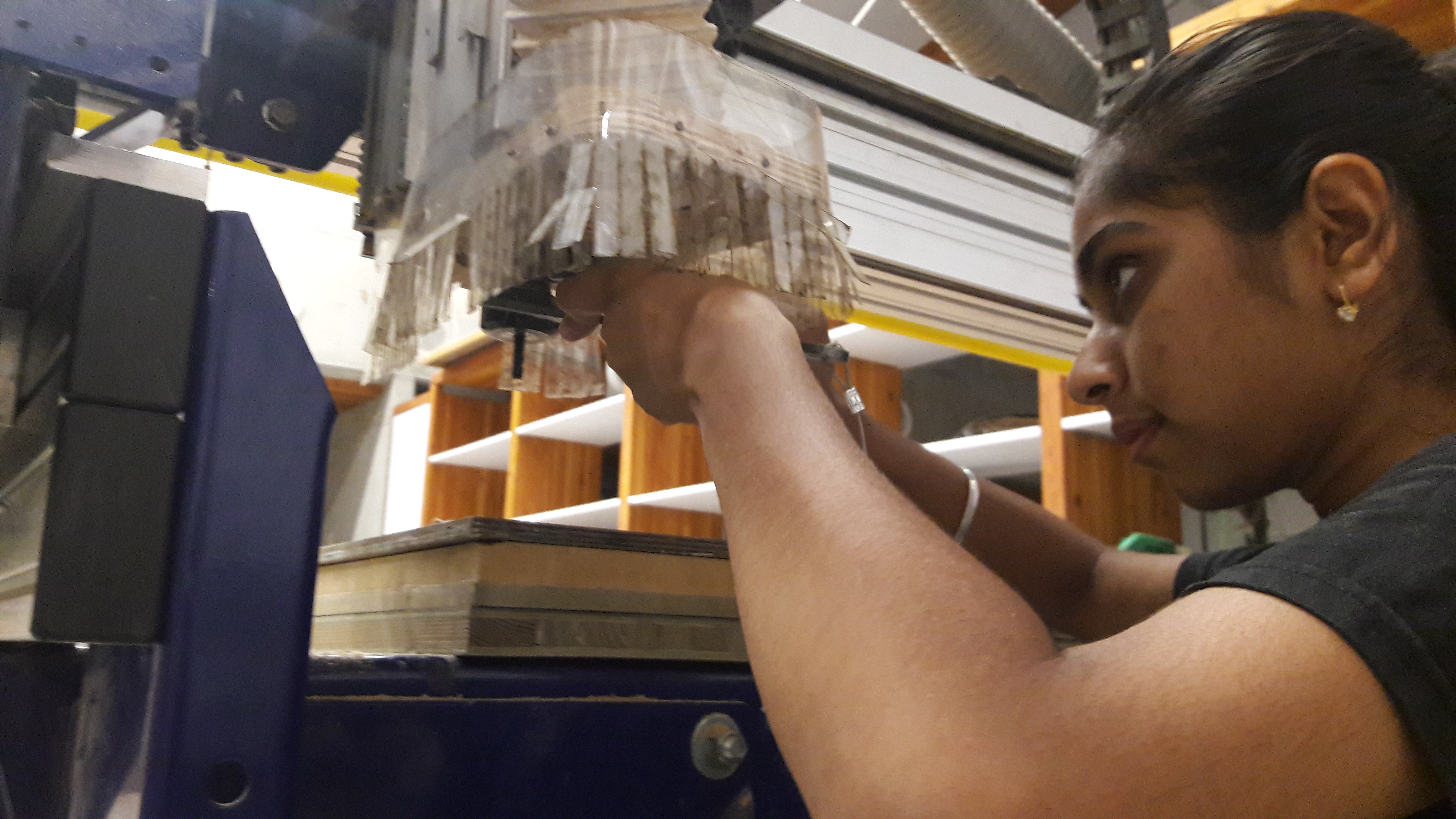
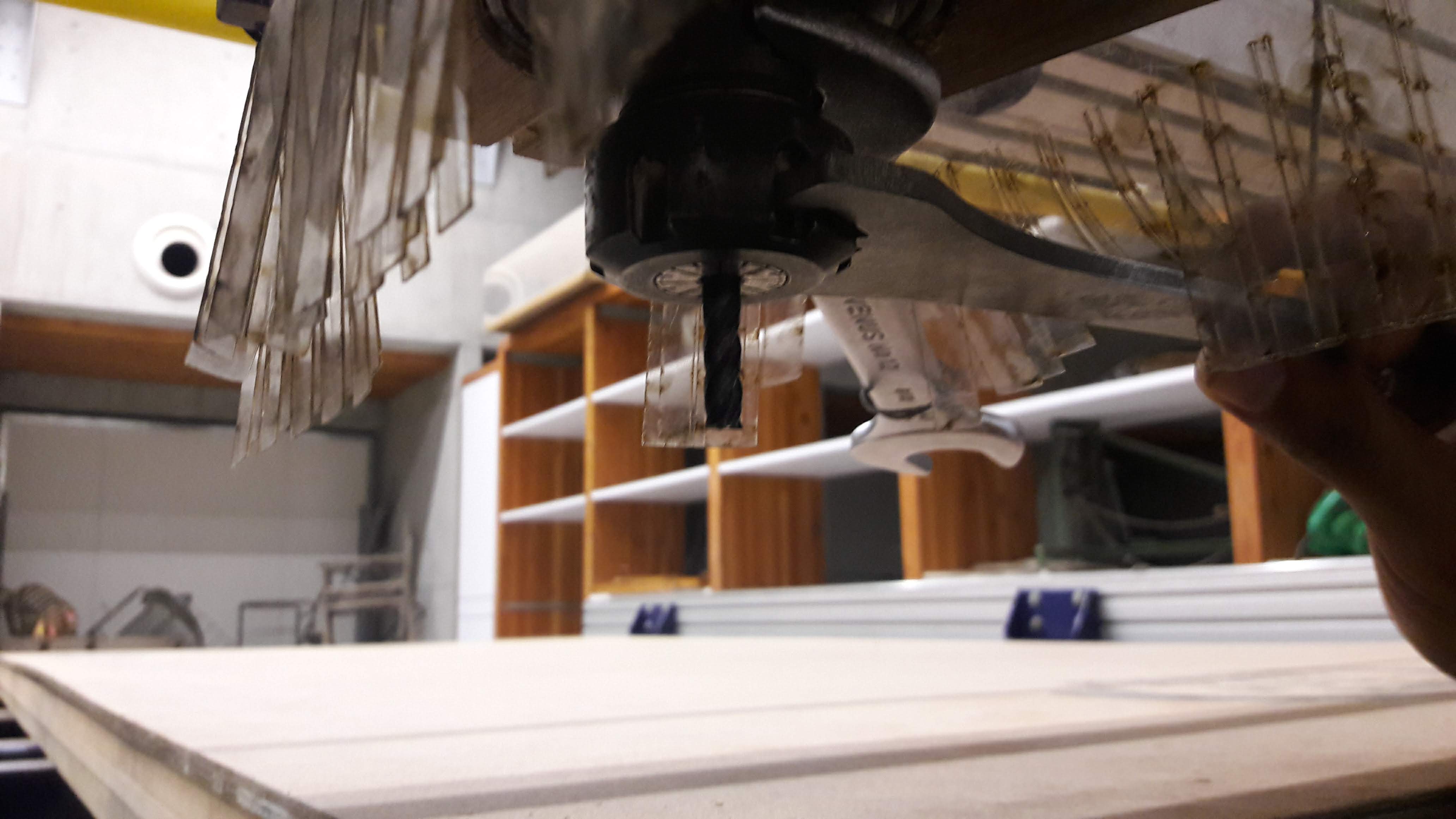
I am using 12mm plywood and for fixing it we have to screw the sheet on the sacrificial layer. Also it is very important to make sure that the vaccum is connected.
Now starting with the shopbot software.
- The red dialogue box is used to set the Origin. You can click on small yellow button to select X,Y,Z movement of the spindle.
- Once you have Set the Bit on the machine in the desired Origin Position, Check X,Y and Z axis to Set the Origin to that position.
- Select the file and move further
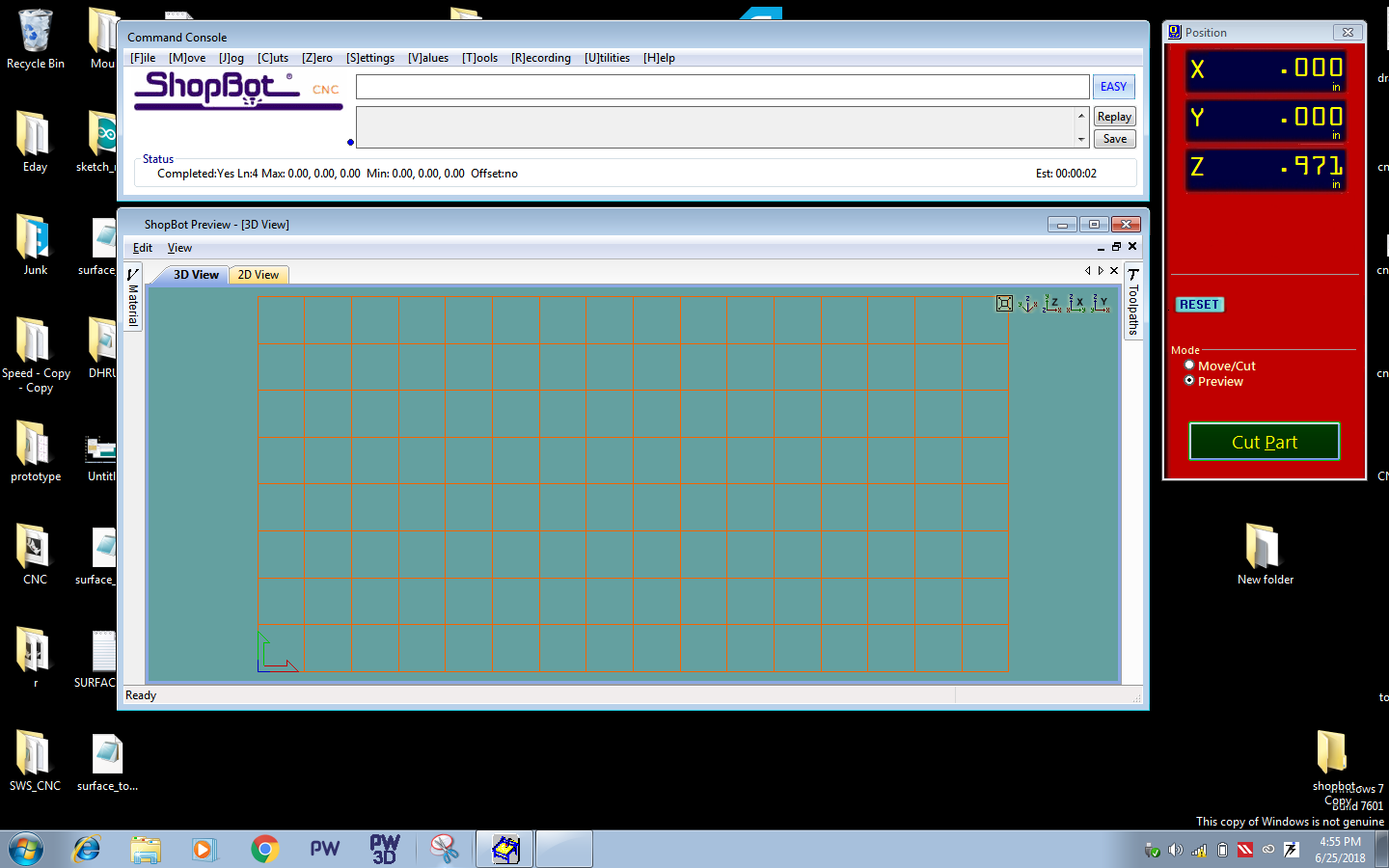
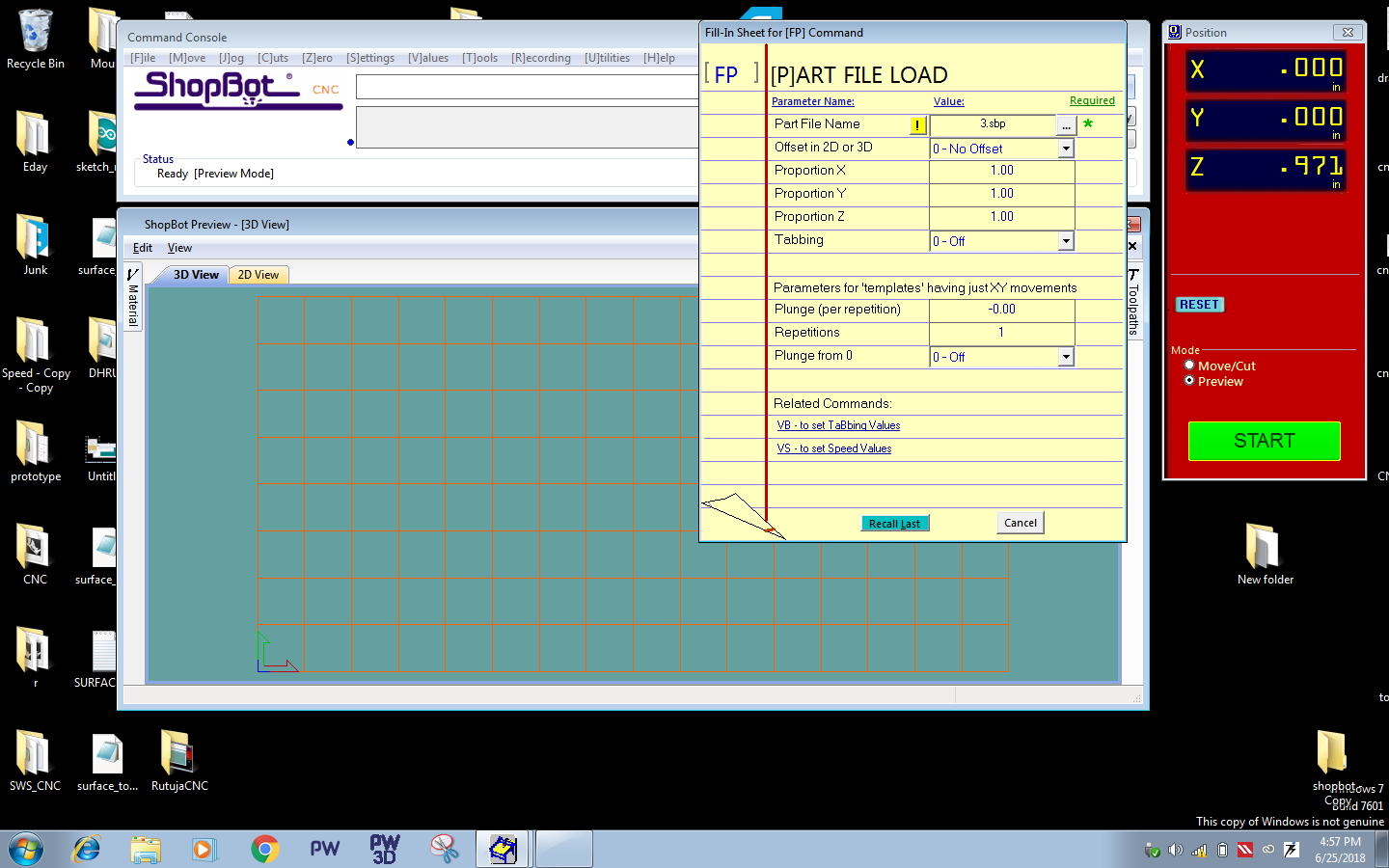
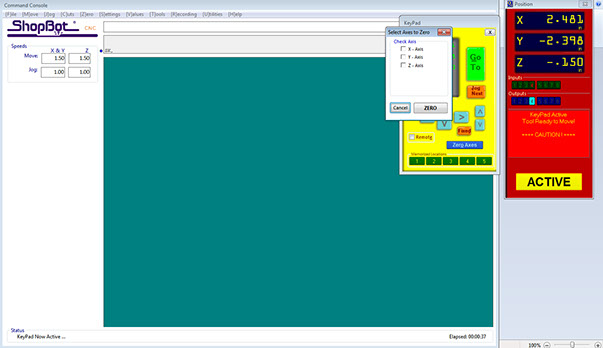
In shopbot it is not appropriate to remove the vaccum tube but I have done this for making sure the cutting is proper. I paused the machine to check the cutting.
For cut part I had set the following parameters:
- Cut Depth = 12.2mm
- 1/4th inch Up-cut bit
- Feed Rate = 1.5 inches/sec
- Plunge Rate = 1.5 inches/sec
- Spindle Rate = 12000 rpm
- Spindle Rate = 7000 rpm
- Cut Depth = 6mm
- Feed Rate = 1.5 inches/sec
- Spindle Rate = 12000 rpm
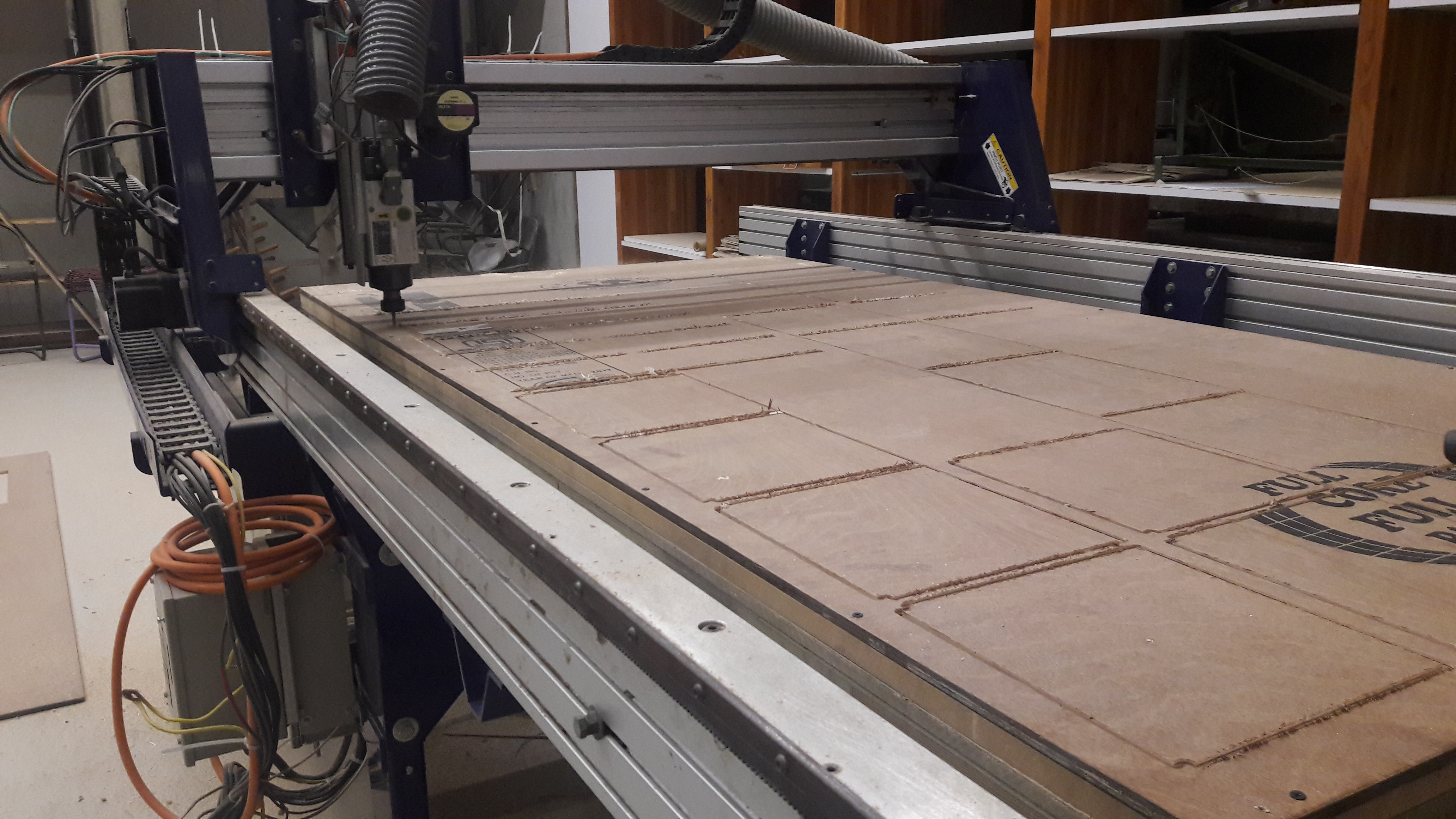
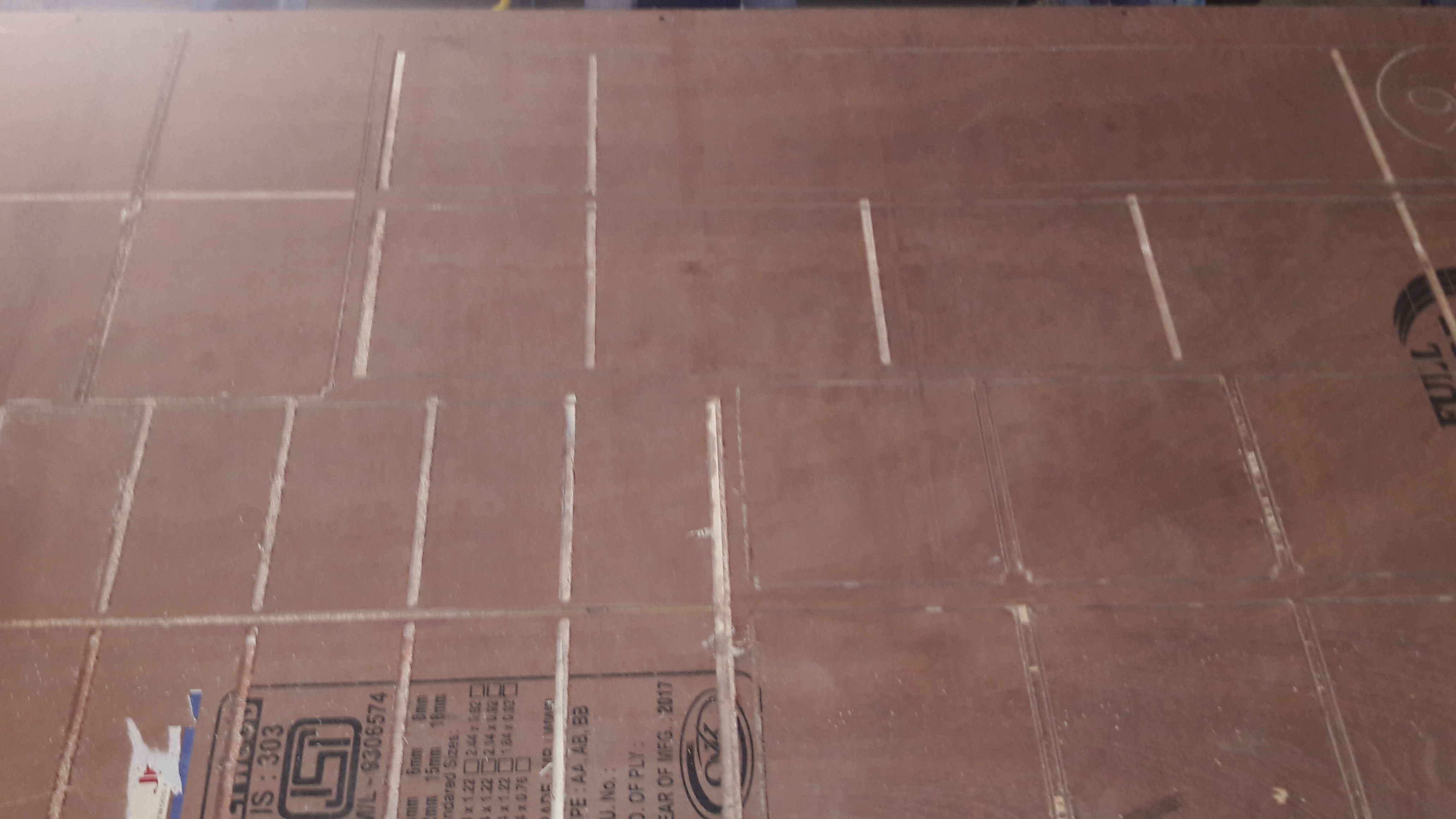
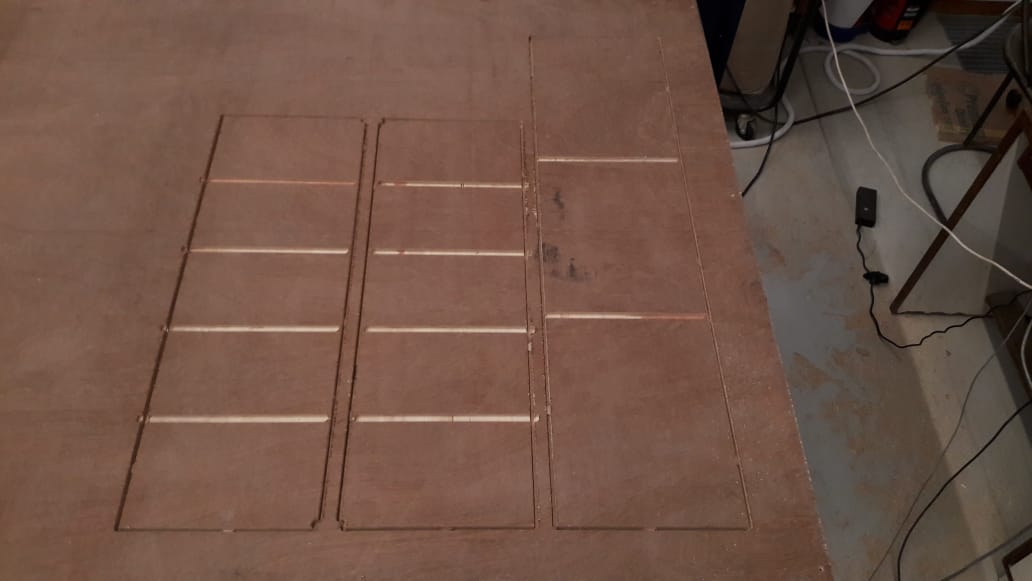
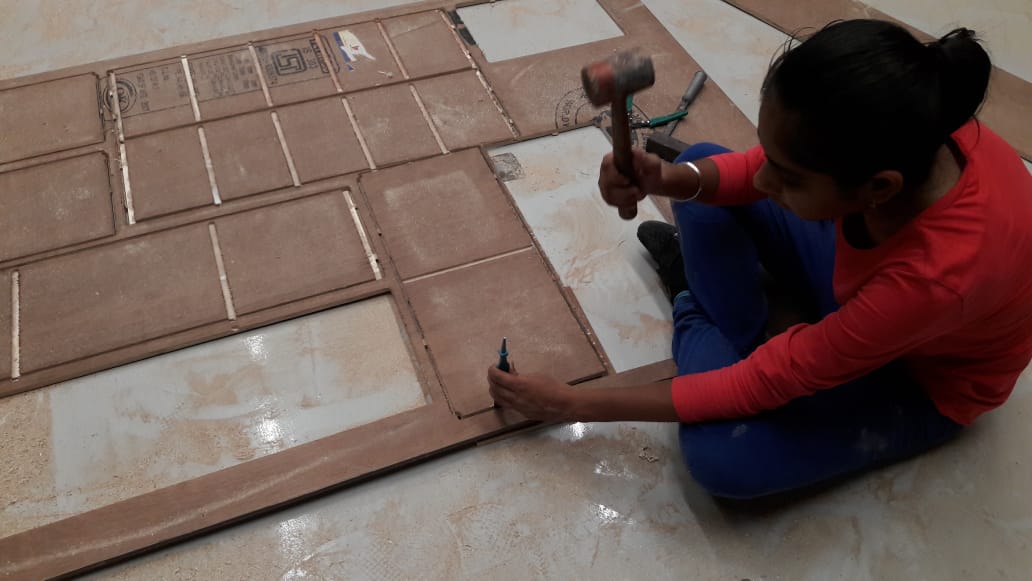
The final cut of the designTapan who is technician at fablab and 2015 fabacademy student helped me to design and also use CNC Machine. The design had some errors. The bas pocket was not given correct but I can be fixed properly.
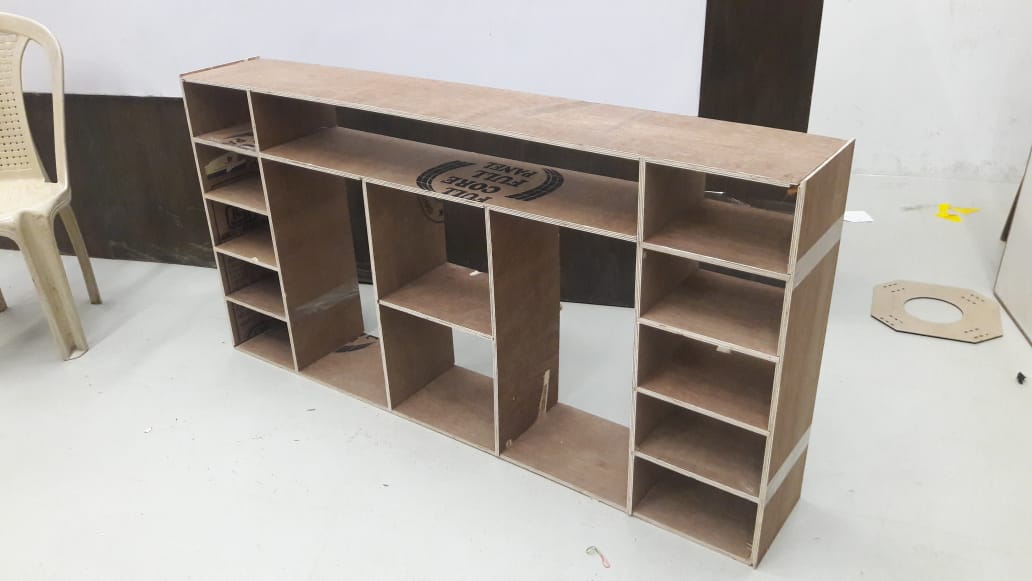
I arranged some of the things in the shelf and it became easy for all of us to work and it was not less messy this time.
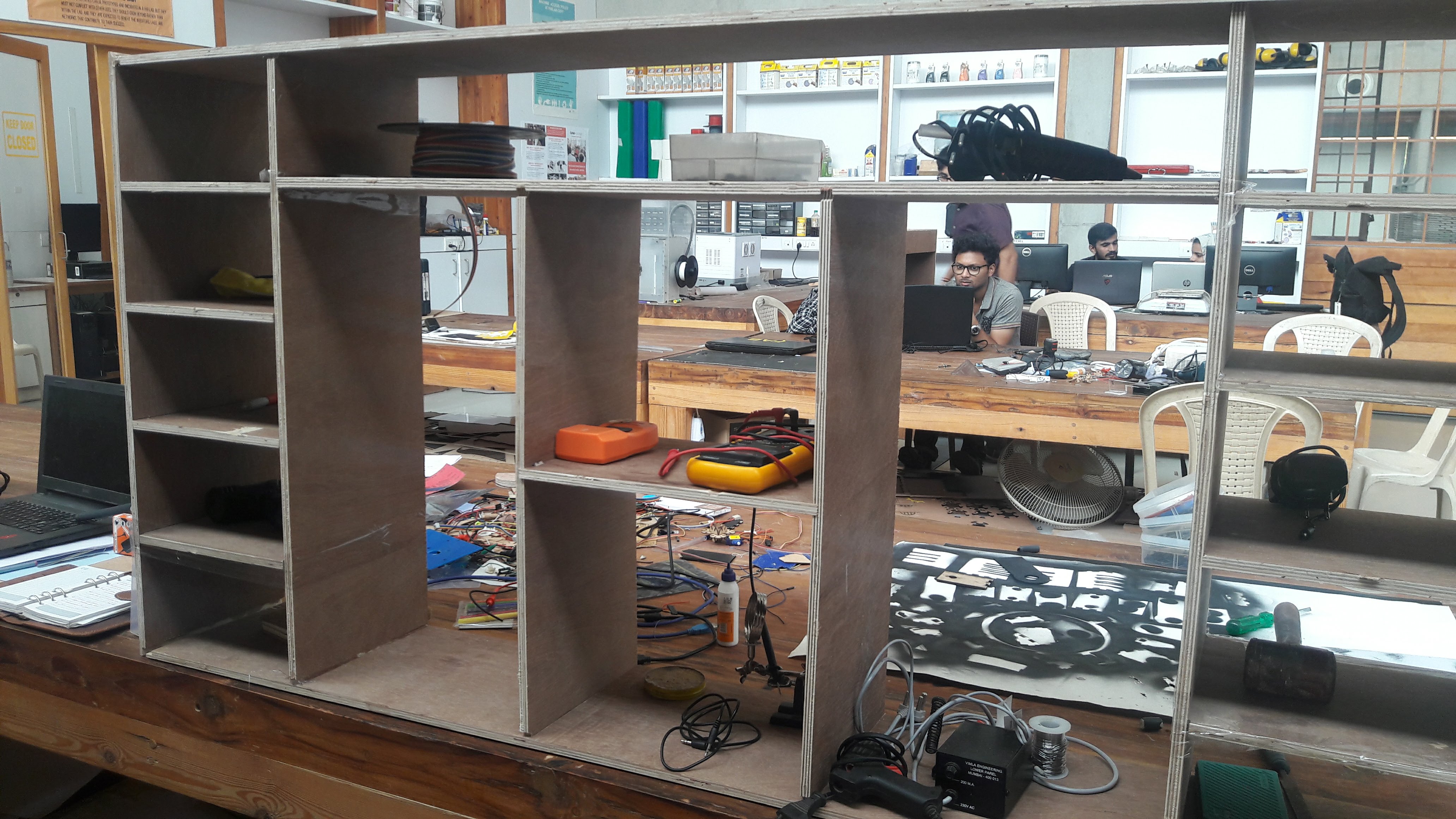
Group Assignment