Computer Controlled Cutting
Assignment
All the important links are Here
Learning outcomes
Group Assignments
Laser Cutter
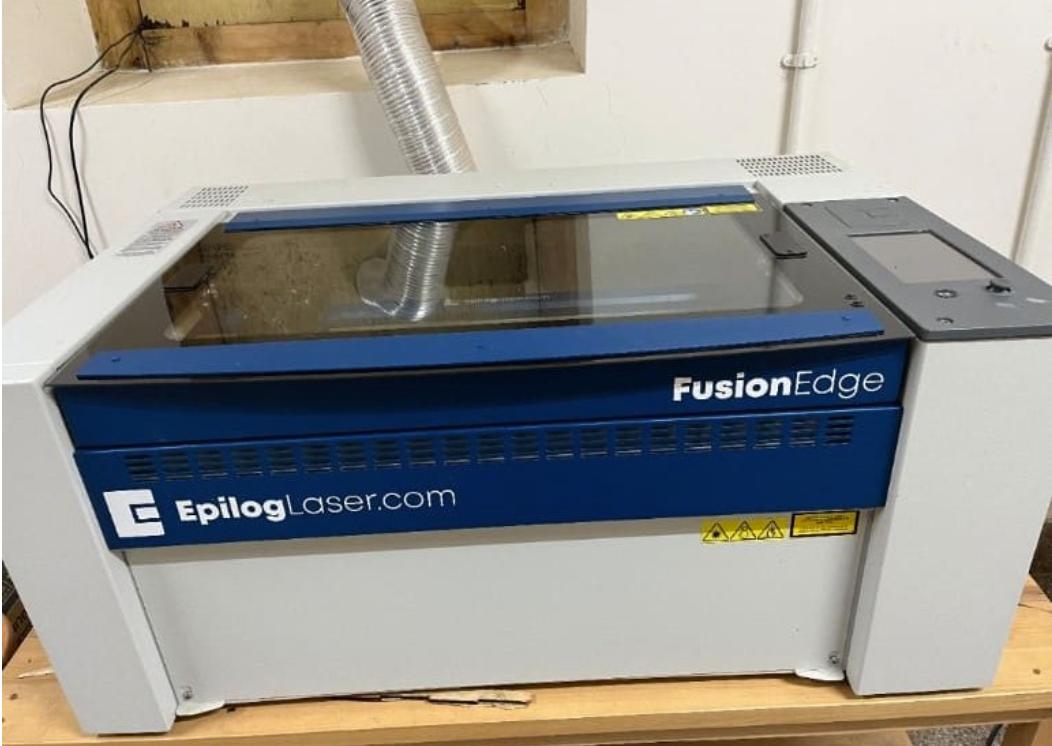
What is it and How it works
A laser cutter is a machine that uses a high-powered laser to cut materials such as wood, metal, and acrylic with precision and accuracy.A laser cutter works by focusing a high-powered laser beam onto a material's surface. This intense heat either melts, burns, or vaporizes the material, creating precise cuts or etchings. The machine follows a digital design or pattern, directing the laser along specific paths to create the desired shapes or designs with high accuracy and speed.
The laser printer I have at my lab is Epilog fusion edge 12/24
For a very detailed information on this laser printer, please have a look
Technical Description
- Model: Fusion Edge 24
- Description: The Fusion Edge 24 is a laser cutting and engraving machine designed for precision and versatility in various fabrication applications.
- Cutting Area: 24” x 12” (610 x 305 mm)
- Description: The cutting area refers to the maximum dimensions within which the laser can cut or engrave materials. In the case of the Fusion Edge 24, it can handle materials within a 24-inch by 12-inch area.
- Laser Type: Sealed CO2 Laser
- Description: This laser cutter utilizes a sealed CO2 laser as its cutting and engraving source. CO2 lasers are known for their efficiency and effectiveness in a wide range of materials, including wood, acrylic, plastic, and more.
- Laser Power: Up to 120 Watts
- Description: The Fusion Edge 24 offers laser power options that can range up to 120 watts. This range of power settings allows for precise control over the intensity of the laser beam, enabling users to work with different materials and achieve various cutting and engraving effects.
- Optional Accessories: Autofocus System
- Description: The Fusion Edge 24 offers an optional autofocus system for automatic focal adjustment. This feature enhances ease of use and ensures optimal focus for cutting and engraving tasks, particularly when working with materials of varying thicknesses or irregular surfaces.The autofocus system is shown in the "operating machine"part
- Importance: Autofocusing in laser cutting ensures precise and consistent results by adjusting the focal point of the laser beam to match the material's surface. It enhances accuracy, efficiency, and ease of use, making it crucial for achieving high-quality cuts and engravings across various materials and thicknesses.
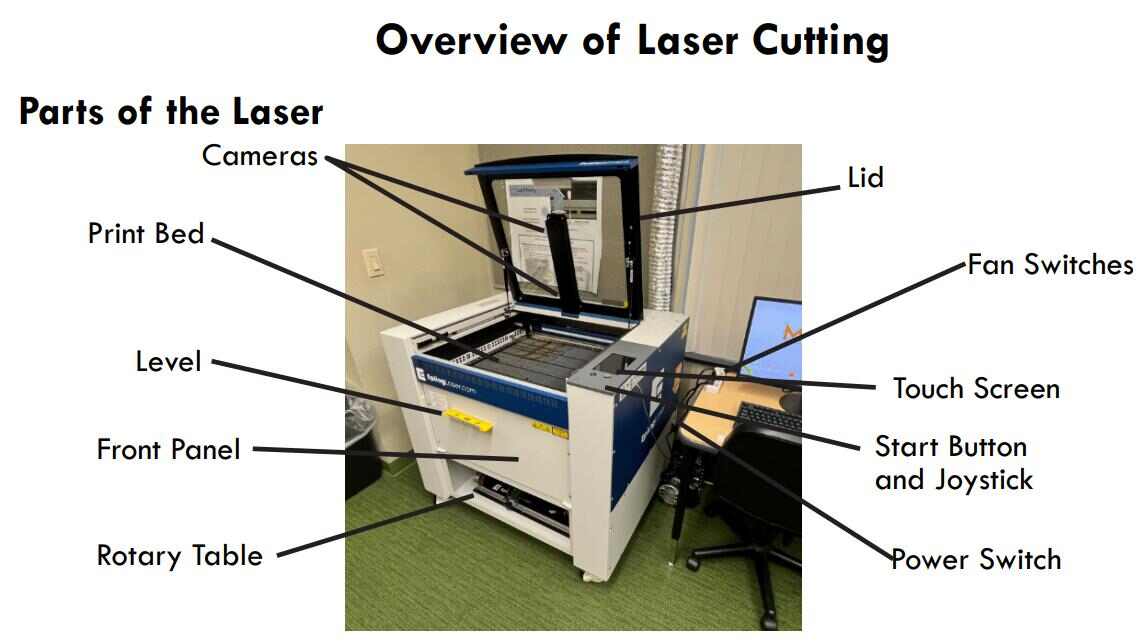
Operating the Machine
For a very detailed guide on operating and using the laser printer, I highly recommend you to go through this guide for its very informative description like the one below
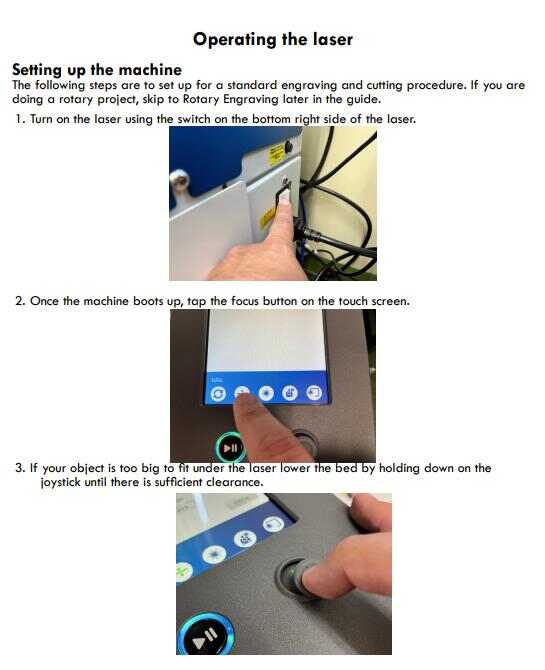
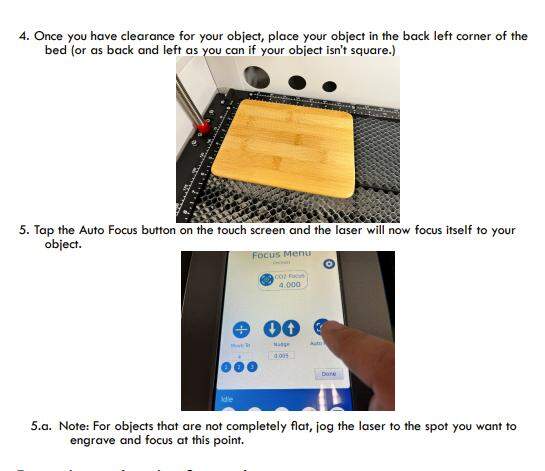
Laser Cutter Safety
Dos:
- Stay attentive: Never operate the laser cutter while unattended. Always monitor the machine during operation.
- Clean the machine: Regularly clean the laser system to prevent the buildup of cutting and engraving residue, which can create a fire hazard.
- Have a fire extinguisher: Keep a properly maintained and inspected fire extinguisher nearby. Consider using a Halotron extinguisher for clean and effective suppression.
- Connect to a vent: Always operate the laser cutter with a properly functioning exhaust system to remove smoke, debris, and harmful compounds generated during engraving or cutting.
Don'ts:
- Operate unvented: Never use the laser cutter without a properly operating vent to the outside or to a filtration unit.
- Run unattended: Never leave the laser cutter running without someone watching the system. This reduces the risk of fire in case of improper settings or mechanical/electrical failures.
- Vector cut unattended: Avoid laser cutting any material without supervision, especially during vector cutting, as the buildup of heat can pose a significant fire risk.
- Operate with open doors: Never operate the laser cutter with any covers or enclosures removed. The invisible laser beam is very dangerous.
Kerf
A kerf is the width of material removed during cutting, like laser cutting or sawing. It's the gap or groove created in the material as it's cut.