The Cardboard Whale That Came to Life
In the quiet hours of his workshop, a bold idea began to take shape. A life-size whale, majestic and mysterious, built entirely from an unlikely hero—cardboard. To many, cardboard was nothing more than a disposable material, but to him, it was a treasure waiting to reveal its potential. This wasn’t just any project; it was a culmination of passion, sustainability, and innovation.
The whale, an eight-meter-long masterpiece, would be a symbol of creativity and environmental consciousness. But it wouldn’t stop there. This whale would come to life, responding to the gentle touch of visitors and illuminating its mouth with soft LED lights, creating a magical interaction that bridged art and technology.
The Spark of Innovation
He began with a spiral development approach, iterating step by step to ensure the whale grew both in form and functionality. In phase one, the foundation was laid—a PIR (Passive Infrared) sensor paired with a servo mechanism brought the whale to life with subtle movements. Weeks of knowledge from electronic design, 3D printing, flatbed cutting, and embedded programming were poured into this phase, laying the groundwork for something extraordinary.
Phase two brought interactivity to the forefront. LED lights were carefully embedded along the whale’s mouth, synchronized to light up in rhythm with the strokes of a visitor’s hand. A simple pat beneath the whale’s eye would trigger a radiant glow, as if the creature itself responded to acts of kindness.
The Vision and the Journey
This wasn’t just a personal project—it was destined for a global stage. FAB23 in Bhutan, a prestigious annual gathering of creators and innovators, would serve as the whale’s grand debut. But the road to Bhutan wasn’t easy. Building a network of participants and gathering resources became a challenge. Still, the vision persisted: a collaborative sculpture embodying FAB’s spirit, created by attendees working together.
Drawing inspiration from renowned artists like Joseph DeLappe, Kiel Johnson, and Horst Kiechle, the project stood apart. Cardboard creations were everywhere, but none had been attempted at this scale in the history of the global FAB conference.
Designing a Gentle Giant
The whale wasn’t just art; it was a carefully engineered marvel. Using Blender, he designed the creature as a 3D model before unfolding it into hundreds of template pieces with Adobe Illustrator. Every cardboard panel was meticulously cut to size, transforming flat sheets into a three-dimensional masterpiece.
For participants and collaborators, smaller cardboard whales were produced as tokens of appreciation—easily die-cut and designed for replication.
The Heart of Creation
The project’s lifeblood lay in its processes. Flatbed cutting transformed cardboard sheets into precise components, while 3D printing added detail to the custom PCB case. CNC milling shaped the electronic boards, and embedded programming breathed life into the whale’s interactive features. Even the barcodes linking to instructional videos for mini-whales were crafted with care.
Facing the Questions
As the whale took shape, questions loomed: How many hours would it take to complete? Could such a massive sculpture be justified? Who would fund it? But with each step forward, answers emerged.
A Shared Triumph
The first prototype, built in Singapore, stood as a testament to the project’s success. Logistics to Bhutan were planned meticulously, and excitement grew as collaborators joined the journey. The ultimate goal was not just to unveil the whale but to create a shared experience—a group photo with FAB23 participants and the cardboard whale as a centerpiece of unity and creativity.
Perhaps the most ambitious dream was the open invitation to all participants: to contribute their ideas to the whale. Whether it was a projection mapping design, a mechanism to launch objects from its head, or playful doodles on its surface, this whale belonged to everyone.
And so, the gentle beast of the sea, reborn in cardboard, carried a message of hope, collaboration, and the boundless potential of imagination.
Presentation on 7 June 2023 (Wednesday)
I am no.4, the rest of the presentation schedule is here.
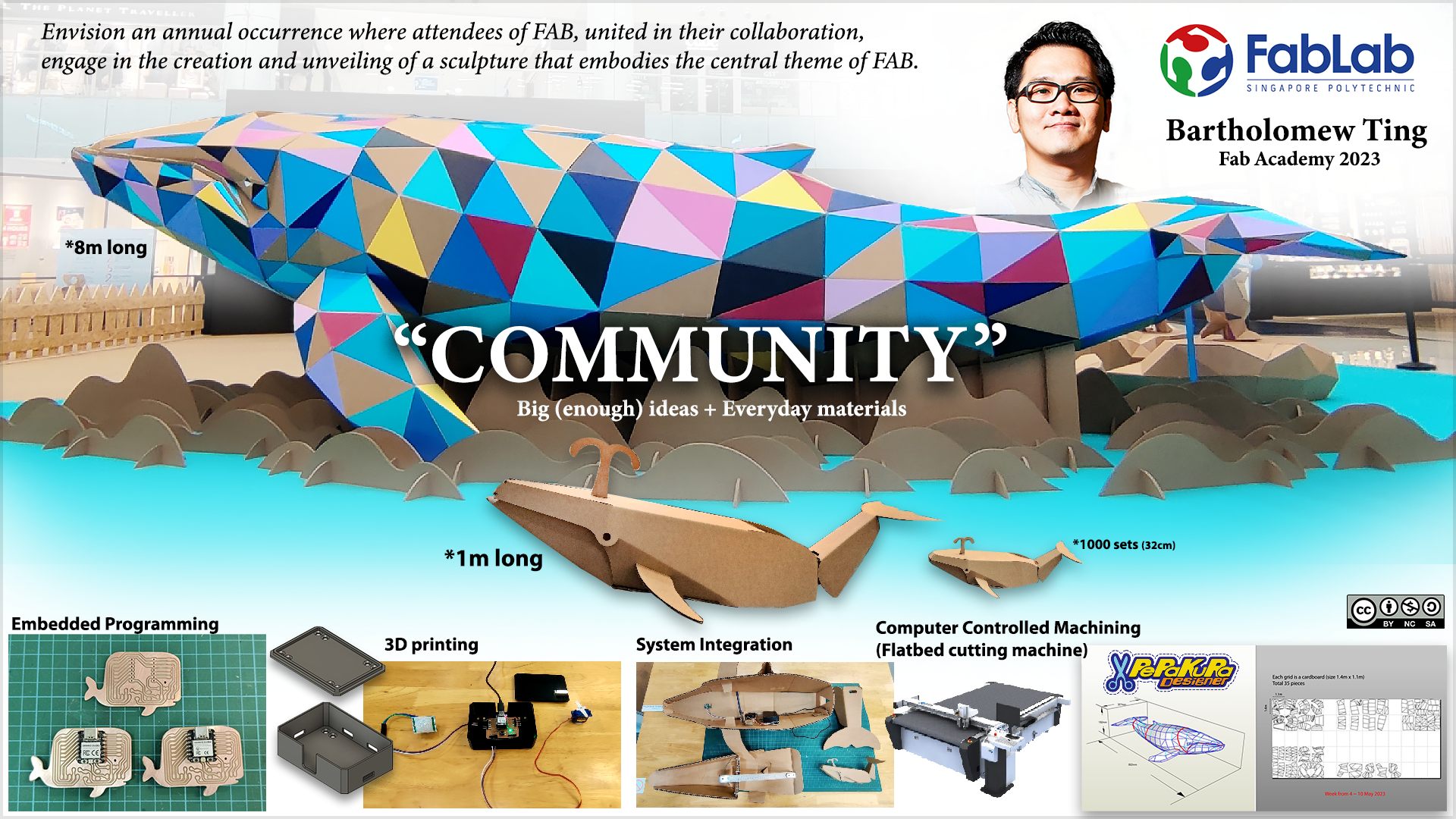
Table of contents
1. Questions
- What does it do?
- Who's done what beforehand?
- What have you designed?
- What materials and components were used?
- How much did they cost?
- What parts and systems are made?
- What processes have been used?
- What questions need to be answered?
- How will it be evaluated?
2. Materials and Components
3. Links
1.1 What does it do?
I often find myself pondering the underappreciated potential of cardboard as a versatile material. In this final project, I have constructed a remarkable life-size whale entirely from sustainable resources, specifically cardboard. The end result (that I aim for) is an awe-inspiring creation that truly comes to life.
In pursuit of continuous improvement and innovation, I have opted for a spiral development approach. As part of this methodology, (during phase one) I am incorporating a PIR (Passive Infrared) sensor to initiate a specific action performed by a servo mechanism. This integration of sensor and servo technology adds an interactive element to the project, enhancing its overall functionality and impact. For phase one, I have incorporated all the knowledge I learnt through out the weeks, from Electronic Design and Production, 3D printing, Flatbed cutting to Embedded programming and counting.
In phase 2 of the project, I incorporated interactivity by integrating LED lights along the mouth area of the 8m Whale. When a visitor gently pats the head of the Whale, specifically the area beneath the eyes, the LED strips illuminate in synchronization with the rhythm of the petting, creating an illusion of the Whale responding to acts of kindness.
1.2 Who's done what beforehand?
I am finding it challenging to articulate, but I am currently investing significant effort in seeking resources and building a network of participants for my final project at FAB23 in Bhutan.
Envision an annual occurrence where attendees of FAB, united in their collaboration, engage in the creation and unveiling of a sculpture that embodies the central theme of FAB.
Essentially, my focus is on ensuring the realization of my project physically at FAB23. I've been allocating excessive time and energy to searching for assistance and support.
Never-the-less, there are NO shortage of cardboard creation anywhere and everywhere, but no one has done it at the global FAB conference at this scale. Below are the artists whom have been my sources of inspiration over the years (not in particular order):
Joseph DeLappe, Kiel Johnson, & Horst Kiechle.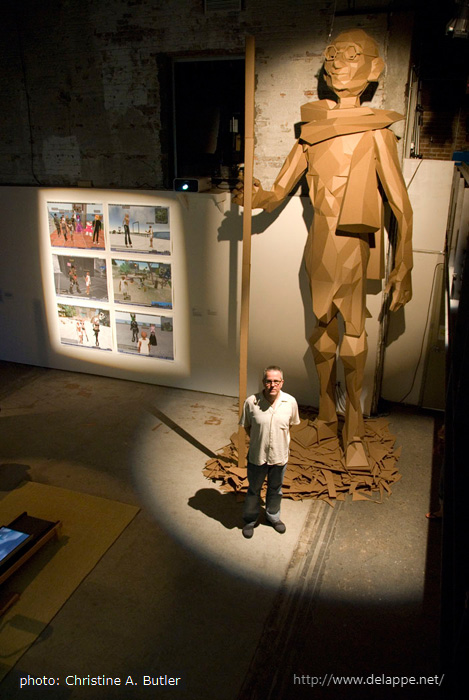
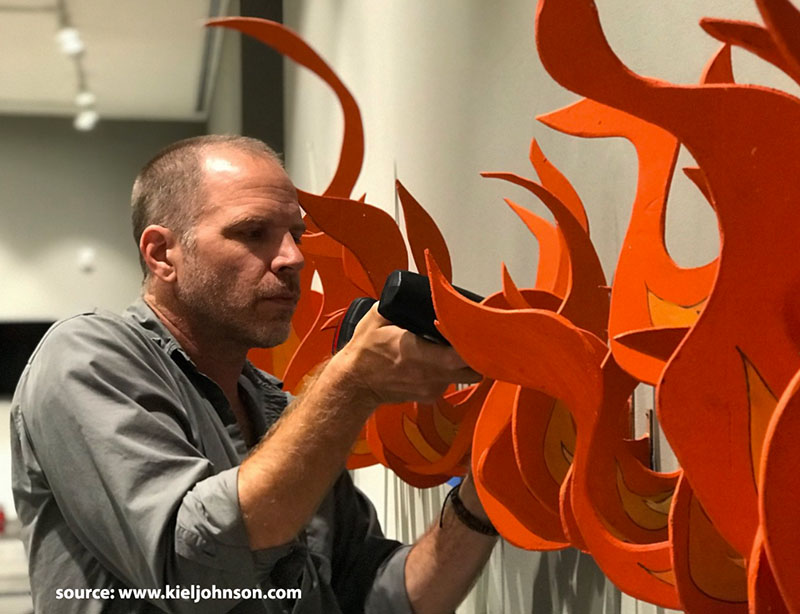
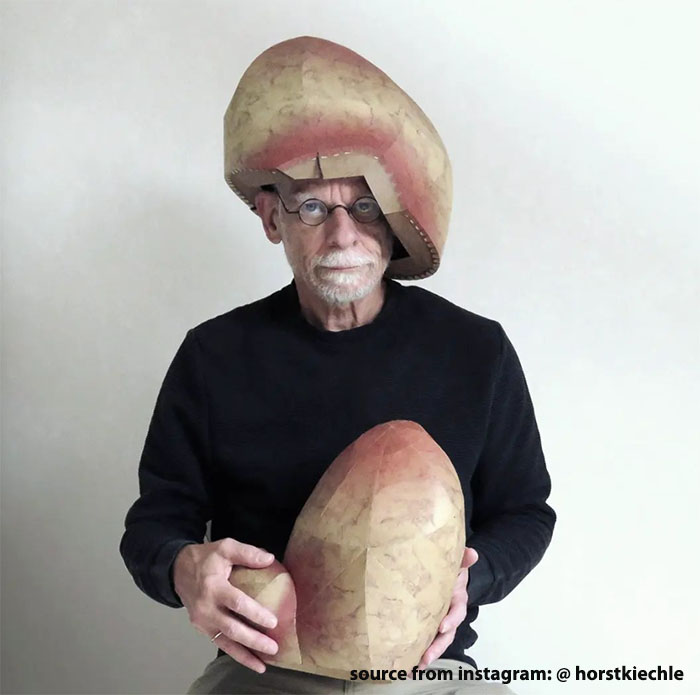
1.3 What have you designed?
With the sustainability theme in mind, I designed an endangered marine animal- a gentle beast in the sea. The effort included the creation of 3D model in Blender, unfolding the model and layout all the hundreds pieces of templates in Adobe illustrator to fit into the cardboard material size (1.4m x 1.1m).
I also make a small cardboard whales that is easily replicated and produced (die-cut) them in thousands (as a token of appreciation for participants in this project).
1.4 What parts and systems are made?
- An 8m long whale made out of cardboard that could last for minimum 5 years under indoor condition - 3D design
- Vinyl sticker for the Bar code (link to online instruction video) - 2D design
- Seeed Studio RP2040 on customized PCB - Embedded microcontroller
- Integration case
1.5 What processes have been used?
- Flatbed cutting for all the cardboard, for A-flute (5.5mm) and E-flute (1.8mm) - subtractive fabrication process
- 3D printing for the PCB case - Additive fabrication process
- Electronic Board CNC milling
- Embedding programming for the PIR sensor and actuators (Servo)
- Sticker printing and cutting for Bar code (Link to online instruction video for Mini Cardboard Whales)
1.6 What questions needed to be answered?
- How many manhour required to finish the sculptures?
- Is it necessary to build life-size?
- Who is paying?
1.7 How will it be evaluated?
- Implementation of Spiral Development: The initial "prototype" has been successfully created in Singapore. Contrary to common occurrences in life where actions do not align with words, this incident stands as a rare exception for me.
- To successfully arrange all the logistics to Bhutan.
- To get participants excited about building it together on the spot. A group photo of all FAB23 participants with the project would be bonus.
- Most challenging task, open collaboration (invitation) to all fellow students to do something on the whale (E.g. design a mechanism to shoot something from the head, projection mapping, doodling on the skin, etc)
2. Materials and components
Qty | Description | Price | Link | |
---|---|---|---|---|
SEEED STUDIO XIAO RP2040 ARDUINO | RP2040 XIAO RP2040 - ARM® Cortex®-M0+ MCU 32-Bit Embedded Evaluation Board | $7.81 | https://www.digikey.sg/en/products/detail/seeed-technology-co-ltd/102010428/14672129?s=N4IgTCBcDaIB4EsCGB7ABAJwA5gAwBZcQBdAXyA | |
SERVOMOTOR RC 4.8V | Positional Rotation DC Motor Servomotor, RC (Hobby) Incremental 4.8VDC | $5.24 | https://www.digikey.sg/en/products/detail/dfrobot/SER0006/7597224 | |
PIR Motion Sensor HC-SR501 | Detect movement or motion within the range of 7m | $3.60 | https://kuriosity.sg/products/pir-motion-sensor-hc-sr501?variant=44757201256761¤cy=SGD&utm_medium=product_sync&utm_source=google&utm_content=sag_organic&utm_campaign=sag_organic | |
Jumper Wire Male-Male 40x | 20cm long and come in a strip of 40 pieces (4 sets with 10 of each colour) | $3.60 | https://kuriosity.sg/products/jumper-wire-male-male-40x?_pos=2&_sid=51f4512cd&_ss=r | |
Heavy-duty Cardboard | Cardboard dimension 2.3m x 1.4m x 10mm | $28.00 | https://tri-wall.com.sg/aa.html | |
Daler Rowney Graduate Acrylic Colour | All colours come in a 500ml squeezable pot | $13.38 | https://artfriendonline.com/ProductDetails/FamilyDetails/DR_GRA_AC |
3. Link to files
- Full video walkthrough at Marina Square (By Minn Thonedra) (1 min 34 sec)
- Mini Whale Blender File (3D) (.blend)
- Mini Whale Pepakura File (.pdo)
- Mini Whale Illustrator File (.ai)
- Eagle Schematic file -.sch format
- Eagle Board file -.brd format
- PCB design
- PCB socket holes
- PCB socket outline
- G-code for PCB design
- G-code for PCB socket holes
- G-code for PCB outline
- Recommended reading: Bruce Mau’s Incomplete Manifesto. Read all but pay particular attention to #3, #23, #29, #35 & #37.