Grocubator
Small-medium size sprout and microgreen growing incubator
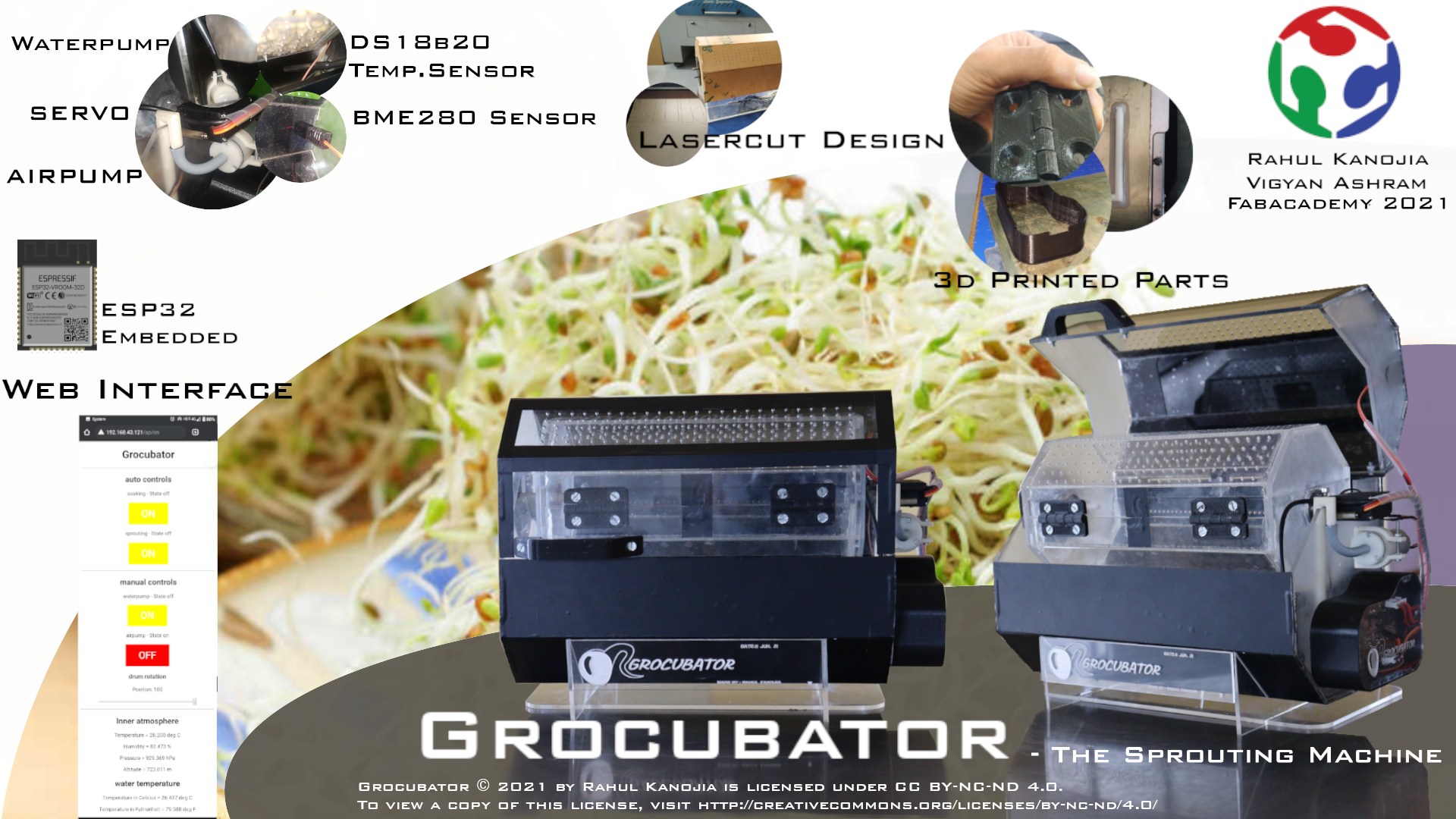
I am very happy with my work. I made something that have some application in our life and people like it.
This is almost ready product some improvement is needed to be call it a ready to sell product, on that I am working
Here my one minute presentation video covering my journey of How it Made "Grocubator"
What does it do?
It is more than just normal sprouter because it can incubate seed growth further more to microgreen. It can soak seed as well and recycle same water in entire process. It Prevent sprouts from spoiling and fungi infection. Does not give out unpleasant smell.
Some result of test performed with Black-Eye pea (chauli)
Result after one and half day including soaking period. I have soaked seed in Grocubator itself.
.jpg)
.jpg)
.jpg)
Result after two days. Sprout grown bigger...
.jpg)
.jpg)
.jpg)
Result after three days. Some sprout grown bigger and some started to show green leaves
.jpg)
.jpg)
.jpg)
Result after four days. more big more leaves.
.jpg)
.jpg)
.jpg)
Here after four days I took out all yield and kept it in a container and covered it for two more days. This was not part of experiment I took out to eat it but volume of food became almost 10 time so even after eating so much so much was left and that continued growing in container. Here the result after six days
.jpg)
Still many things are under study like how much and what type of seed will work well. How it work in different climate etc. So still there is scope of research and development.
Who's done what beforehand?
I mentioned in my principal and practices about origin of idea and prior work on project. I have done this fabacademy course in Fablab0 in vigyan ashram. Vigyan Ashram is Space full of things to experiment with. There is culture of problem solving using knowledge of science and technology.
Sprouting is traditional practices in every home kitchen. In my home too. So idea of process came from my own personal experience. No rocket Science
What did you design?
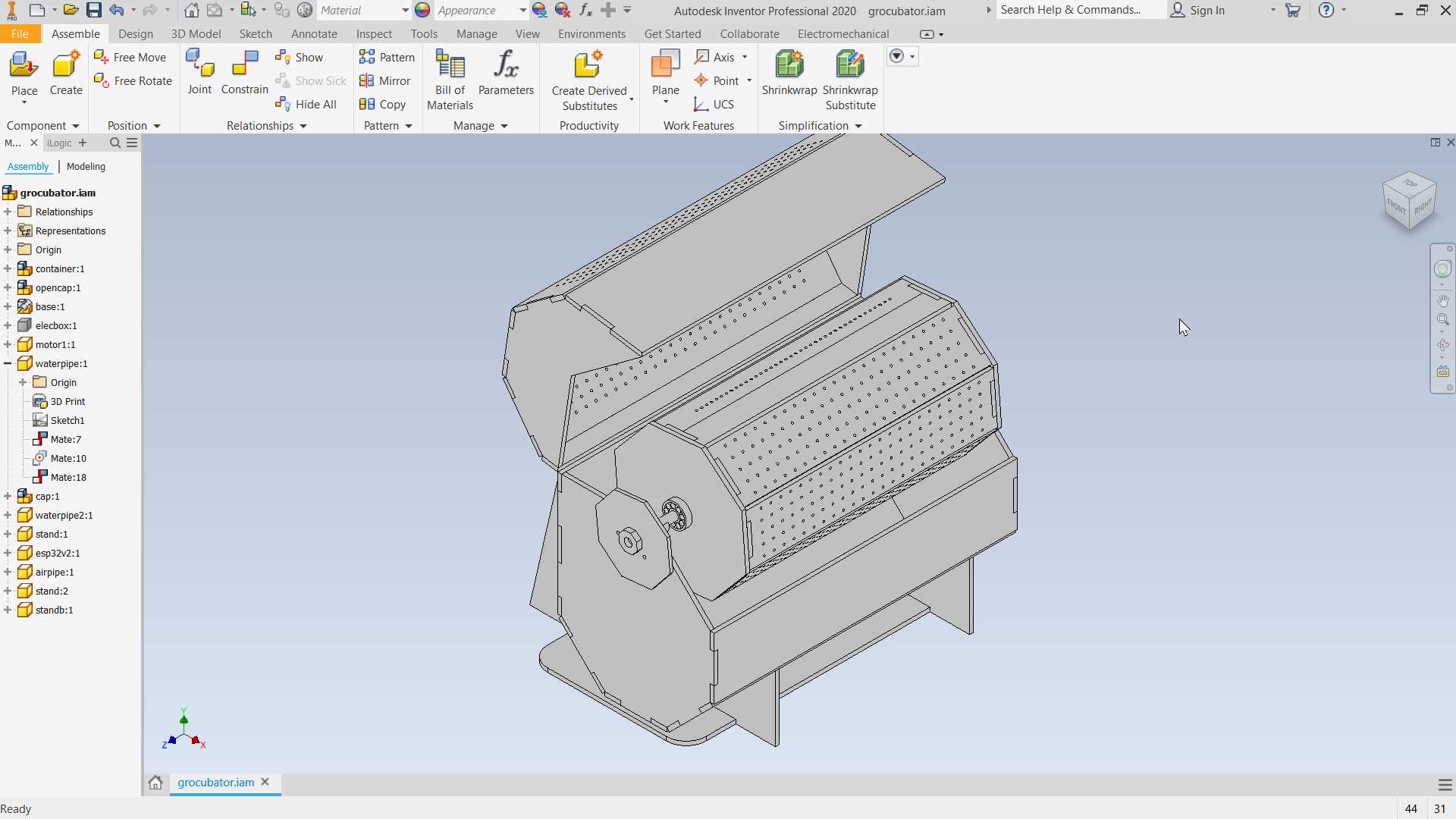
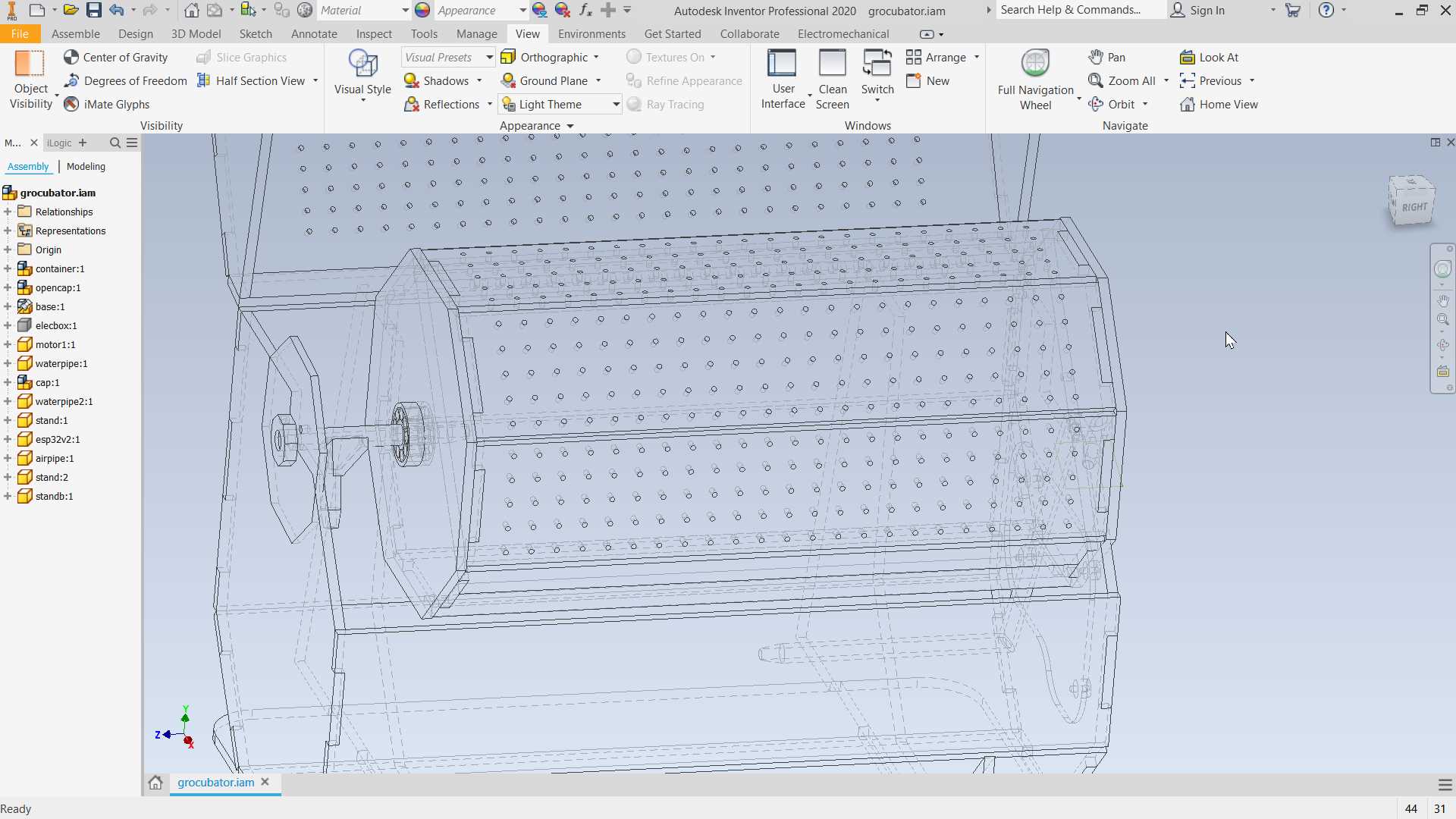
Problem with old method was excess water stay remain in batch that needed to be remove. I have designed rotating structure that make seeds to move which let excess water to come out. I have designed octagonal prism or cylinder that having hole on one side and completely pack from other side as you see in image. This special structure is also design to make seed soak water of sometime, then to remove water out and this structure also help in washing cycle that water seeds time to time.
.jpg)
.jpg)
.jpg)
prism or cylinder is rotated using servo motor from 0 to 180 deg. No full rotation is needed this is enough to keep fliping cylinder
It have waterpumping system that throw water inside the cylinder from down water storage and also have air bubbling system that keep DO level and pH of water maintained.
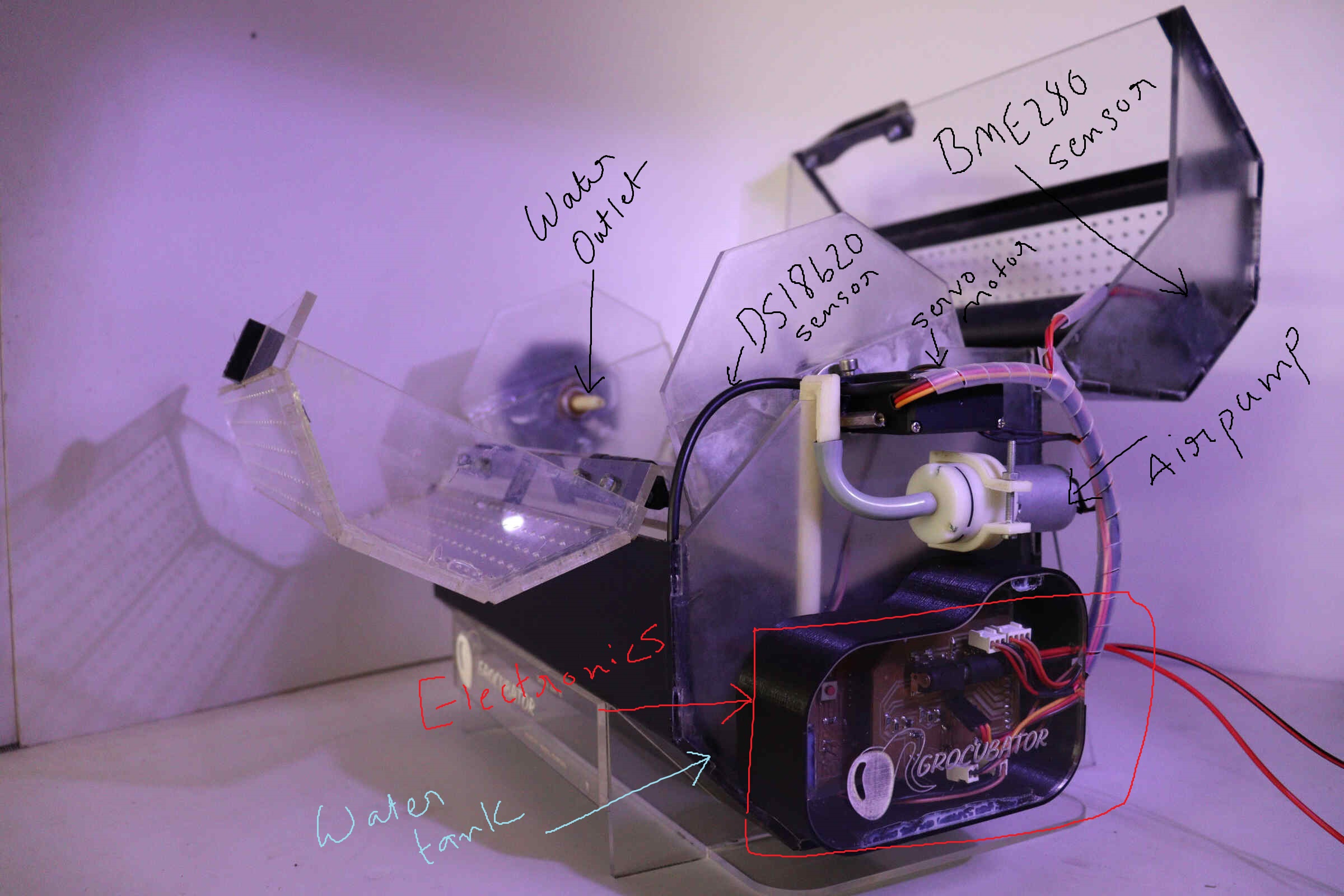
I have plan to add sensor control adaptation system. This system with will modified soaking, washing, and draining out cycle accordingly by sensing ambient climate and water temp. So I installed BME280 and DS18b20 sensor in it, to know more visit My Input device week. Actuators, Interface everthing is controlled by ESP32 chip and electronics that designed by me to make Grocubator smart. To know more about it visit Out device week and Interface and application week.
What materials and components were used? Where did they come from? and How much did they cost?
Cost of Raw materials
Sr. No. | Material |
---|---|
1 | 4mm Acrylic/Plexi Glass sheet. |
2 | PLA filament. |
3 | ABS filament. |
4 | FR1 Paper Phenolic Copper. |
So exact calcution and price of raw materials was bit difflicult So here I not added it in total
Cost of Electronics Components
Sr. No. | Component (rubo.in) | Price |
---|---|---|
1 | MG995 Servo Motor | 225 |
2 | Micro DC Air Pump 6VDC. | 339 |
3 | DC 3-6 V Mini Micro Submersible Water Pump. | 69 |
4 | GY-BME280-5V Temperature and Humidity Sensor. | 1199 |
5 | DS18B20 Water Proof Temperature Probe. | 95 |
6 | Espressif ESP32-WROOM-32D 4M 32Mbit Flash WiFi Bluetooth Module. | 329 |
2,256 |
Others cost of things like aquarium silicon sealant, chloroform to solvent weld acrylic parts, cyanoacrylate super glue to stick plastic parts, Vinyl paper for decoration, other electronic components like capcitor, resistor etc, tubes, nut-bolts, bearing etc
What parts and systems were made? What processes were used?
From structure to Electronic mother board to Software are made by me. Only Electronics sensor and actuator I have buyed. Main structure is made from clear acrylic/ plexi glass through Digital fabrication laser cutting. To stick all acrylic part I have used chloroform and to make it water tight I used food grade waterproof silicon or can be called aquarium silicon sealant.
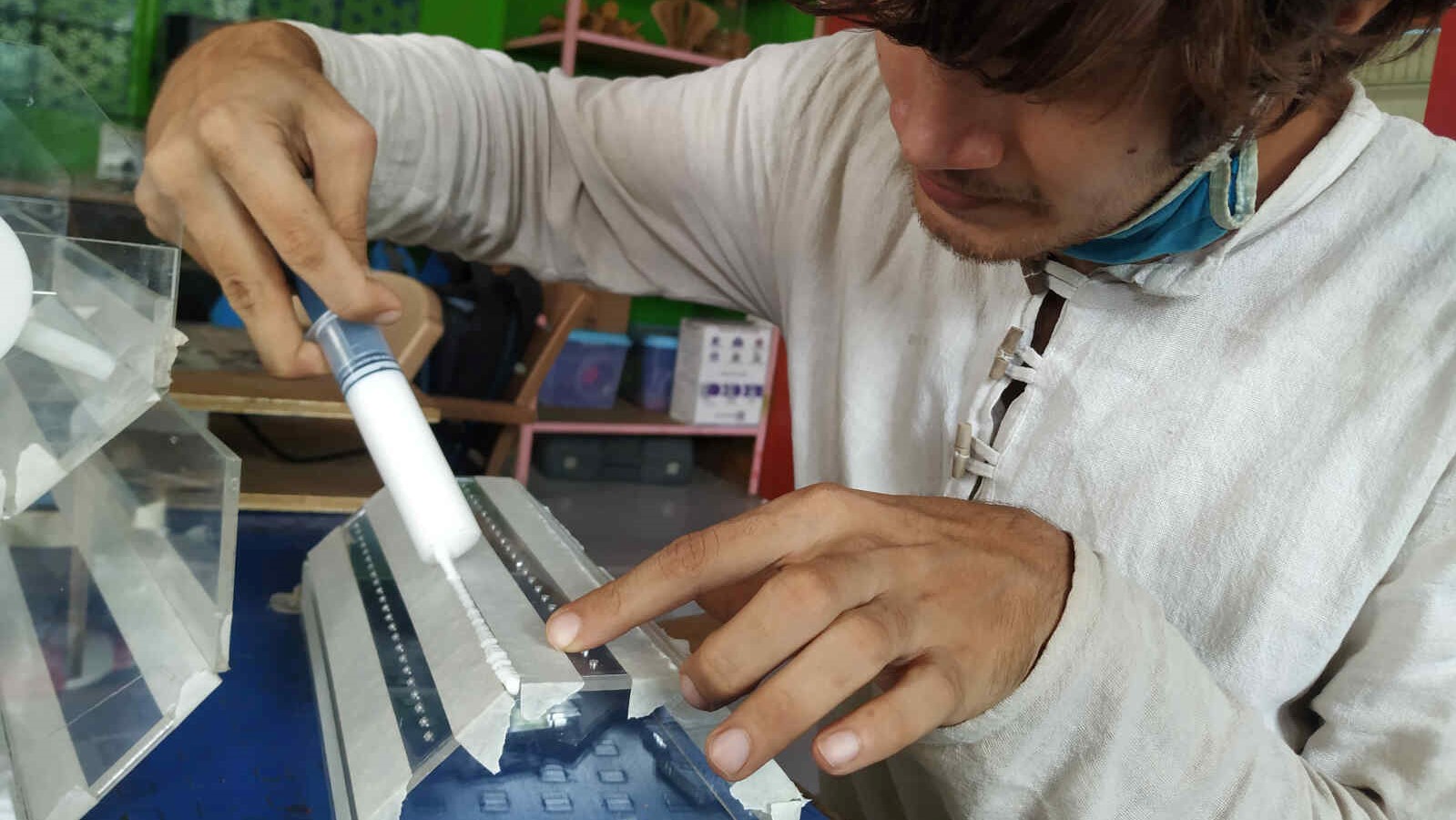
Some are 3d printed like hinge, buckle, tubes, clamp and cabinet for electronic using PLA and ABS both. Both are not food grade due to time limit and pademic situation I have used it but I prefer to use only food grade plastic filament.
.jpg)
.jpg)
.jpg)
I made two electronic boards that connected with eachother using headers. One is main board with esp32 that have control and another one is actuator driver and sensors board. I designed all in KiCAD and milled it on FRl PCB using SRM20.
.jpg)
.jpg)
.jpg)
What questions were answered?
This project was prototype to proof that this kind of design will work well to solve problem of sprout spoiling due to excess water and It proof that. It can be scale to any size to large purpose.
What worked? What didn't?
Design is working well enough but it can't be use in actual life because it is not made completely from food grade material. Because of covid pademic there was struggle for materials. but It can be recreated again with better materials
Final Presentation
What are the implications?
It is very useful gadget for kitchen use. It is almost a home kitchen appliances product. I wanted to take it further and finish it into ready to sell product.
Download Design files:
Here is my 3d design files grocubator.rar
For electronic design and Interface visit Input device week and Interface and application week